Methoden zur Organisation von Produktionsprozessen. Prinzipien der rationellen Organisation des Produktionsprozesses
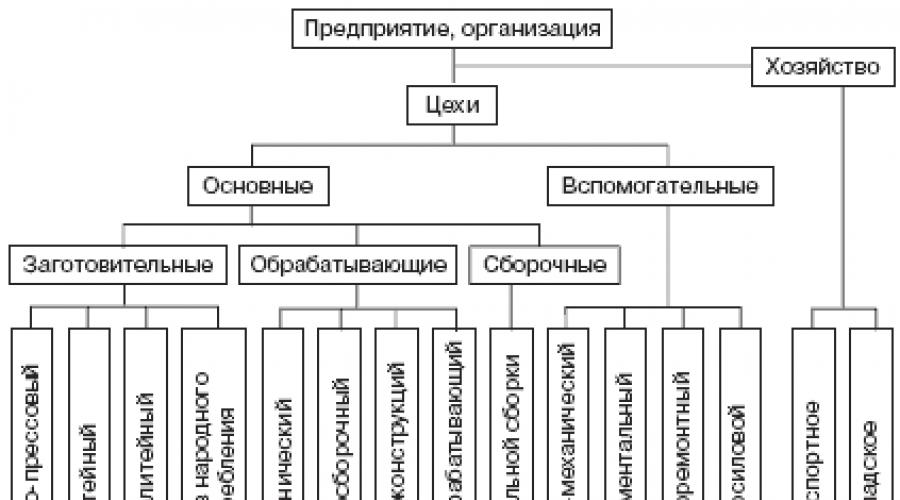
2. Grundprinzipien der Organisation des Produktionsprozesses
Bei der Organisation der oben genannten und anderer Produktionsprozesse orientieren sie sich an einer Reihe von Grundsätzen der Organisationstheorie. Die Prinzipien sind verallgemeinerte, gut etablierte und weit verbreitete Techniken und Methoden, die bei der Organisation jedes Systems, einschließlich der Organisation von Produktionsprozessen, verwendet werden. Zu den wichtigsten Grundsätzen der Organisation des Produktionsprozesses gehören die folgenden.
Das Prinzip der Spezialisierung setzt eine strikte Arbeitsteilung innerhalb des Unternehmens voraus. In diesem Fall ist eine betriebsinterne Spezialisierung vorgesehen, die die Massenproduktion von Produkten eines begrenzten Sortiments in separaten strukturellen Produktionsabteilungen (Werkstätten) des Unternehmens oder durch die Durchführung streng definierter Phasen des technologischen Prozesses an Arbeitsplätzen gewährleistet. Die Spezialisierung kann objektbezogen (für fertige Produkte als Ganzes), detailliert (für die Herstellung einzelner Teile) und operativ (für die Umsetzung eines separaten Vorgangs des technologischen Prozesses) sein.
Die Spezialisierung der Produktion sorgt einerseits für eine Steigerung der Effizienz, kann andererseits aber auch negative Folgen haben. Eine Erhöhung des Spezialisierungsgrades führt zu einer Verbesserung der Wirtschaftsindikatoren aufgrund einer Steigerung der Produktion gleichnamiger Produkte, unter anderem durch die Entstehung größerer Möglichkeiten zur Automatisierung von Produktionsprozessen und einer Steigerung der Produktivität der Arbeitnehmer, die dieselben streng spezialisierten Tätigkeiten ausführen Funktionen sowie durch Verbesserung der Qualität der hergestellten Produkte. Gleichzeitig ist die Spezialisierung häufig mit der Monotonie und Monotonie der von den Arbeitnehmern ausgeführten Arbeitsfunktionen verbunden, was dazu führt, dass sie ihre technologische Belastung erhöhen, ihre Fähigkeiten verlieren, das Interesse an der Arbeit verlieren und infolgedessen die Arbeitsproduktivität und das Personal verringern Umsatz.
Der Grad der innerbetrieblichen Spezialisierung wird durch das Produktionsprogramm des Unternehmens bestimmt; er wird durch Faktoren wie Standardisierung, Normalisierung und Vereinheitlichung von Produktdesigns, Typisierung technologischer Prozesse und ihrer Parameter beeinflusst. Das Spezialisierungsprinzip und seine Einhaltung bestimmen maßgeblich die erfolgreiche Umsetzung anderer Prinzipien der Organisation von Produktionsprozessen.
Grundsatz der Verhältnismäßigkeit geht von einer relativ gleichen Produktivität pro Zeiteinheit der miteinander verbundenen Unternehmensbereiche aus. Die Nichteinhaltung des Grundsatzes der Verhältnismäßigkeit führt zu Ungleichgewichten, wodurch sich der Einsatz von Ausrüstung und Arbeitskräften verschlechtert, die Dauer des Produktionszyklus zunimmt und Rückstände zunehmen. Ein Verstoß gegen den Grundsatz der Verhältnismäßigkeit führt zum Entstehen sogenannter Engpässe in einer bestimmten Technologiekette, die einerseits das Wachstum der Produktionsmengen hemmen und andererseits zu einer Unterauslastung und Verschlechterung der Nutzung der in anderen Gliedern installierten Ausrüstung führen diese Kette.
Durch die Ausweitung der bei der Analyse der Auslastung der Produktionskapazität einer Werkstatt (Unternehmens) identifizierten Engpässe und die darauf aufbauende Profilbildung kann eine Erhöhung der Verhältnismäßigkeit der Produktionsprozesse erreicht werden. Die Beseitigung von Engpässen unter Wahrung des Grundsatzes der Verhältnismäßigkeit führt zur Einhaltung der notwendigen Verhältnisse zwischen einzelnen Stufen in einer bestimmten Werkstatt oder zwischen einzelnen Werkstätten (Produktionen) des Unternehmens. Dadurch wird die Wirtschaftlichkeit des Unternehmens durch die Umsetzung der sich in diesem Fall ergebenden Möglichkeiten zur Steigerung des Produktionsvolumens und des Produktabsatzes, zur Verbesserung der Nutzung vorhandener Geräte und zur Steigerung der Arbeitsproduktivität gesteigert.
Parallelprinzip beinhaltet die gleichzeitige Ausführung einzelner Vorgänge oder Teile Fertigungsprozess. Dieses Prinzip basiert auf dem Prinzip, dass Teile des Produktionsprozesses zeitlich zusammengefasst und gleichzeitig durchgeführt werden müssen. Die Einhaltung des Parallelitätsprinzips führt zu einer Verkürzung der Dauer des Produktionszyklus und damit zu einer Einsparung von Arbeitszeit.
Direktflussprinzip beinhaltet eine solche Organisation des Produktionsprozesses, die den kürzesten Weg für den Transport von Arbeitsgegenständen von der Einführung der Rohstoffe bis zum Erhalt der fertigen Produkte gewährleistet. Die Einhaltung des Direktflussprinzips führt zu einer Straffung der Frachtströme, einer Reduzierung des Frachtumschlags und einer Reduzierung der Kosten für den Transport von Materialien, Teilen und Fertigprodukten. Der direkte Ablauf wird durch die rationelle Platzierung von Werkstätten, Abschnitten, Arbeitsplätzen im Arbeitsablauf und einzelnen Etappen erreicht, d.h. während des technologischen Prozesses.
Das Prinzip des Rhythmus bedeutet, dass der gesamte Produktionsprozess und seine Bestandteile zur Herstellung einer bestimmten Produktmenge in regelmäßigen Abständen wiederholt werden. Es gibt Rhythmik der Produktion, Rhythmik der Arbeit und Rhythmik der Produktion.
Der Produktionsrhythmus ist die Freisetzung gleicher oder gleichmäßig steigender (abnehmender) Produktmengen über gleiche Zeiträume. Rhythmizität der Arbeit ist die Fertigstellung gleicher Arbeitsmengen (in Menge und Zusammensetzung) in gleichen Zeitintervallen. Rhythmische Produktion bedeutet die Aufrechterhaltung einer rhythmischen Leistung und rhythmischen Arbeit.
Dies ist eines der wichtigsten Prinzipien der Organisation von Produktionsprozessen. Das bedeutet, dass alle einzelnen Schritte und der gesamte Produktionsprozess zur Herstellung einer bestimmten Anzahl von Produkten nach genau festgelegten Zeiträumen wiederholt werden, d. h. Der Rhythmus drückt sich in der gleichmäßigen Produktion von Produkten oder der Bewegung von Arbeitsgegenständen in gleichen Abständen auf allen Stufen der technologischen Kette sowie in der regelmäßigen Wiederholbarkeit einzelner Vorgänge aus.
Die Einhaltung des Rhythmusprinzips ist bei kooperativen Lieferungen von Partnern sowie im Hinblick auf die Erfüllung vertraglicher Verpflichtungen zur Lieferung von Produkten innerhalb streng festgelegter Fristen gemäß dem Vertrag von besonderer Bedeutung. Dieses Prinzip der Organisation des Produktionsprozesses schließt die Möglichkeit der Umsetzung des sogenannten Stormings aus, wenn das Erreichen eines solchen Ziels hinsichtlich der Produktionsmenge auf das Ende des Kalenderzeitraums (die letzten zehn Tage des Monats, Im vergangenen Monat Quartal usw.) mit allen daraus resultierenden negativen Folgen.
Der Indikator, der den Grad der Umsetzung dieses Prinzips am besten charakterisiert, ist der Produktionsrhythmus, d.h. Herstellung der gleichen Produktmenge über gleiche Zeiträume. Der Rhythmuskoeffizient wird durch das Verhältnis des tatsächlichen Produktionsvolumens für einen beliebigen Kalenderzeitraum (Jahrzehnt, Monat) innerhalb (nicht höher) des geplanten Ziels zum durch dieses Ziel vorgesehenen Produktionsvolumen bestimmt.
Kontinuitätsprinzip Dabei geht es darum, Unterbrechungen im Produktionsprozess von Fertigprodukten zu reduzieren oder zu beseitigen. Dieses Prinzip setzt eine Organisation des Produktionsprozesses voraus, bei der Stopps auf ein Minimum reduziert werden. erforderliche Werte oder gar Unterbrechungen bei der Anwesenheit des Arbeitsgegenstandes (Rohstoffe, Halbzeuge) in der Verarbeitung entfallen vollständig. Das Prinzip der Kontinuität des Produktionsprozesses trägt dazu bei, Unterbrechungen beim Einsatz menschlicher Arbeitskräfte zu reduzieren Produktionsausrüstung, die auf allen Hierarchieebenen beachtet werden müssen: von jedem Arbeitsplatz, Standort, jeder Werkstatt bis hin zum Unternehmen als Ganzes. Dabei handelt es sich um die Übergabe von Arbeitsgegenständen von einem Betrieb an einen anderen ohne Verzögerungen und Ausfallzeiten von Geräten und Arbeitskräften. Die Umsetzung des Kontinuitätsprinzips, das eine Einsparung der Arbeitszeit der Arbeitnehmer garantiert und die Zeit im „Leerlauf“ der Geräte verkürzt, sorgt für eine Steigerung der Wirtschaftlichkeit der Produktion. Der Grad der Kontinuität des Produktionsprozesses kann anhand der folgenden Indikatoren beurteilt werden:
Geräteauslastungsrate im Laufe der Zeit, Bewertung des Grads der Kontinuität bei der Verwendung von Arbeitswerkzeugen;
Der Kontinuitätskoeffizient des Produktionsprozesses, bestimmt durch das Verhältnis der Zeit, die zum Abschluss aller Phasen des technologischen Prozesses erforderlich ist, zur Dauer des Produktionszyklus.
Redundanzprinzip in der Organisation der Produktion setzt voraus, dass das Produktionssystem über berechtigte (Mindest-)Reserven und Sicherheitsbestände verfügt, die zur Aufrechterhaltung der Beherrschbarkeit und Stabilität des Systems erforderlich sind. Tatsache ist, dass verschiedene Störungen im normalen Ablauf des Produktionsprozesses, die durch die Einwirkung vieler, zum Teil schwer oder gar nicht vorhersehbarer Faktoren entstehen, durch Managementmethoden beseitigt werden, aber den Aufwand zusätzlicher Produktionsressourcen erfordern . Deshalb durch Organisieren Produktionssystem, ist es notwendig, für solche Vorräte und Reserven zu sorgen, beispielsweise Versicherungs-(Garantie-)Bestände an Rohstoffen und Energiereserven des Unternehmens und seiner einzelnen Geschäftsbereiche. Im Einzelfall wird die erforderliche Redundanz des Produktionssystems auf Basis praktischer Erfahrungen, statistischer Muster ermittelt oder mit ökonomisch-mathematischen Methoden minimiert.
Das Prinzip der technischen Ausrüstung (Automatik) Der Schwerpunkt liegt auf der Mechanisierung und Automatisierung des Produktionsprozesses sowie auf der Beseitigung manueller, monotoner und schwerer Arbeit, die für die menschliche Gesundheit schädlich ist. Da sind viele technologische Prozesse Herstellung besonders komplexer und arbeitsintensiver Produktarten, deren Umsetzung ohne Automatisierung grundsätzlich nicht möglich ist, d.h. technisch nicht machbar. Einige Produktionsprozesse sind zwar grundsätzlich manuell durchführbar, führen aber durch Automatisierung zu einer Erhöhung des technischen Produktionsniveaus und auf dieser Grundlage zu einer Verringerung der Arbeitsintensität der Produktion, einer Verringerung der Verletzungen der Arbeitnehmer und einer Erhöhung der Qualität der hergestellten Produkte. Die Lösung wirtschaftlicher Probleme durch die Automatisierung von Produktionsprozessen ist trotz der relativ hohen Kapitalintensität (der Notwendigkeit, große Investitionen anzuziehen) der Automatisierung darauf ausgerichtet, einen erheblichen wirtschaftlichen Effekt zu erzielen und damit zu erreichen kurze Zeit Return on Investment und eine deutliche Steigerung der Wirtschaftlichkeit automatisierter Produktionsprozesse. Die gesellschaftlichen Folgen der Umsetzung des Prinzips der Automatisierung und Mechanisierung von Produktionsprozessen äußern sich erstens in einer Veränderung der Art der Arbeit der Arbeitnehmer, zweitens in einer deutlichen Erhöhung der Entlohnung ihrer Arbeit, drittens in einer Verbesserung der Arbeitsbedingungen, insbesondere in gefährlichen Industrien, viertens bei der Erhöhung der Sicherheit, einschließlich der Umweltsicherheit, der Produktion.
Das Prinzip der Flexibilität Bei der Organisation von Produktionsprozessen besteht darin, dass die Produktion teilweise so organisiert werden muss, dass sie sich schnell an die Anforderungen des Marktes anpassen kann, um neue Produkte herzustellen. Unter Flexibilität ist die Fähigkeit eines Produktionsprozesses zu verstehen:
Änderungen im Produktsortiment, Produktionsvolumen;
Notwendige Änderungen der Prozessparameter;
Fähigkeit der Haupt- und Hilfsausrüstung, auf andere Arbeitsarten umzustellen;
Notwendige Änderungen im Qualifikationsniveau und -profil der Arbeitskräfte.
Optimalitätsprinzip Mit der Organisation von Produktionsprozessen ist in erster Linie die Notwendigkeit ihrer Optimierung verbunden, die sich in der Möglichkeit ausdrückt, für jede einzelne Produktion solche Organisationsprinzipien auszuwählen, die in ihrer Kombination ein Höchstmaß an wirtschaftlicher Effizienz gewährleisten.
Turovets O.G., Rodionov V.B., Bukhalkov M.I. Kapitel aus dem Buch „Organisation der Produktion und Unternehmensführung“
Verlag „INFRA-M“, 2007
10.1. Konzept des Produktionsprozesses
Die moderne Produktion ist ein komplexer Prozess der Umwandlung von Rohstoffen, Materialien, Halbfabrikaten und anderen Arbeitsgegenständen in fertige Produkte, die den Bedürfnissen der Gesellschaft entsprechen.
Als Gesamtheit aller in einem Unternehmen durchgeführten Handlungen von Menschen und Werkzeugen zur Herstellung bestimmter Produktarten wird bezeichnet Fertigungsprozess.
Der Hauptteil des Produktionsprozesses sind technologische Prozesse, die gezielte Maßnahmen zur Veränderung und Bestimmung des Zustands von Arbeitsgegenständen beinhalten. Bei der Umsetzung technologischer Prozesse kommt es zu Veränderungen der geometrischen Formen, Größen sowie der physikalischen und chemischen Eigenschaften von Arbeitsgegenständen.
Der Produktionsprozess umfasst neben technologischen auch nichttechnologische Prozesse, die nicht darauf abzielen, die geometrischen Formen, Größen oder physikalischen und chemischen Eigenschaften von Arbeitsgegenständen zu verändern oder deren Qualität zu überprüfen. Zu diesen Prozessen gehören Transport, Lager, Be- und Entladen, Kommissionierung und einige andere Vorgänge und Prozesse.
Im Produktionsprozess werden Arbeitsprozesse mit natürlichen Prozessen kombiniert, bei denen Veränderungen an Arbeitsgegenständen unter dem Einfluss von Naturkräften ohne menschliches Eingreifen erfolgen (z. B. Trocknen lackierter Teile an der Luft, Abkühlen von Gussteilen, Alterung von Gussteilen usw. ).
Verschiedene Produktionsprozesse. Entsprechend ihrem Zweck und ihrer Rolle in der Produktion werden Prozesse in Haupt-, Hilfs- und Wartungsprozesse unterteilt.
Hauptsächlich werden Produktionsprozesse genannt, bei denen die Herstellung der vom Unternehmen hergestellten Hauptprodukte erfolgt. Das Ergebnis der Hauptprozesse im Maschinenbau ist die Herstellung von Maschinen, Apparaten und Instrumenten, die das Produktionsprogramm des Unternehmens bilden und seiner Spezialisierung entsprechen, sowie die Herstellung von Ersatzteilen für diese zur Lieferung an den Verbraucher.
ZU Hilfs- umfassen Prozesse, die den unterbrechungsfreien Ablauf grundlegender Prozesse gewährleisten. Ihr Ergebnis sind Produkte, die im Unternehmen selbst eingesetzt werden. Zu den Hilfsprozessen gehören die Reparatur von Geräten, die Herstellung von Geräten, die Erzeugung von Dampf und Druckluft usw.
Portion werden Prozesse genannt, bei deren Umsetzung Leistungen erbracht werden, die für das normale Funktionieren sowohl der Haupt- als auch der Hilfsprozesse notwendig sind. Hierzu zählen beispielsweise die Prozesse Transport, Lagerung, Auswahl und Montage von Teilen etc.
IN moderne Verhältnisse Insbesondere in der automatisierten Fertigung gibt es einen Trend zur Integration von Kern- und Serviceprozessen. So werden in flexiblen automatisierten Komplexen Grund-, Kommissionierungs-, Lager- und Transportvorgänge in einem einzigen Prozess zusammengefasst.
Die Gesamtheit der Grundprozesse bildet die Hauptproduktion. Bei Maschinenbauunternehmen besteht die Hauptproduktion aus drei Phasen: Beschaffung, Verarbeitung und Montage. Bühne Produktionsprozess ist ein Komplex von Prozessen und Arbeiten, deren Durchführung den Abschluss eines bestimmten Teils des Produktionsprozesses charakterisiert und mit dem Übergang des Arbeitsgegenstandes von einem qualitativen Zustand in einen anderen verbunden ist.
ZU Beschaffung Zu den Phasen gehören die Prozesse zur Gewinnung von Werkstücken – Schneiden von Materialien, Gießen, Stanzen. wird bearbeitet Die Phase umfasst die Prozesse der Umwandlung von Rohlingen in Fertigteile: Bearbeitung, Wärmebehandlung, Lackieren und Galvanisieren usw. Montage Phase – der letzte Teil des Produktionsprozesses. Es umfasst die Montage von Komponenten und Fertigprodukten, die Einstellung und Fehlerbehebung von Maschinen und Instrumenten sowie deren Prüfung.
Der Aufbau und die gegenseitigen Verbindungen der Haupt-, Hilfs- und Nebenprozesse bilden die Struktur des Produktionsprozesses.
Organisatorisch werden Produktionsprozesse in einfache und komplexe unterteilt. Einfach werden Produktionsprozesse genannt, die aus nacheinander ausgeführten Aktionen bestehen einfaches Objekt Arbeit. Zum Beispiel der Produktionsprozess, bei dem ein Teil oder eine Charge identischer Teile hergestellt wird. Schwierig Ein Prozess ist eine Kombination einfacher Prozesse, die an vielen Arbeitsgegenständen ausgeführt werden. Beispielsweise der Prozess der Herstellung einer Baugruppe oder eines gesamten Produkts.
10.2. Wissenschaftliche Prinzipien der Organisation von Produktionsprozessen
Tätigkeiten im Zusammenhang mit der Organisation von Produktionsprozessen. Die vielfältigen Produktionsprozesse, die zur Entstehung industrieller Produkte führen, müssen ordnungsgemäß organisiert und sichergestellt werden effizientes Funktionieren um bestimmte Arten hochwertiger Produkte und in Mengen herzustellen, die den Bedürfnissen der Volkswirtschaft und der Bevölkerung des Landes entsprechen.
Die Organisation von Produktionsprozessen besteht darin, Menschen, Werkzeuge und Arbeitsgegenstände in einem einzigen Prozess zur Herstellung materieller Güter zu vereinen und eine rationelle räumliche und zeitliche Verknüpfung von Grund-, Hilfs- und Dienstleistungsprozessen sicherzustellen.
Die räumliche Kombination von Elementen des Produktionsprozesses und all seiner Spielarten erfolgt auf der Grundlage der Gestaltung der Produktionsstruktur des Unternehmens und seiner Unternehmensbereiche. In diesem Zusammenhang sind die wichtigsten Aktivitäten die Auswahl und Begründung der Produktionsstruktur des Unternehmens, d.h. Bestimmung der Zusammensetzung und Spezialisierung seiner konstituierenden Einheiten und Herstellung rationaler Beziehungen zwischen ihnen.
Bei der Entwicklung der Produktionsstruktur werden Konstruktionsberechnungen zur Bestimmung der Zusammensetzung des Geräteparks unter Berücksichtigung seiner Produktivität, Austauschbarkeit und der Möglichkeit einer effektiven Nutzung durchgeführt. Es werden auch rationelle Anordnungen der Abteilungen, der Platzierung von Geräten und Arbeitsplätzen entwickelt. Es werden organisatorische Voraussetzungen für den unterbrechungsfreien Betrieb der Geräte und der direkten Teilnehmer am Produktionsprozess – der Arbeiter – geschaffen.
Einer der Hauptaspekte bei der Bildung einer Produktionsstruktur besteht darin, das vernetzte Funktionieren aller Komponenten des Produktionsprozesses sicherzustellen: Vorbereitungsvorgänge, Hauptproduktionsprozesse, Wartung. Es ist notwendig, die rationalsten Organisationsformen und Methoden zur Durchführung bestimmter Prozesse für spezifische Produktions- und technische Bedingungen umfassend zu begründen.
Ein wichtiges Element der Organisation von Produktionsprozessen ist die Arbeitsorganisation der Arbeiter, die konkret die Verbindung der Arbeit mit den Produktionsmitteln umsetzt. Die Methoden der Arbeitsorganisation werden maßgeblich durch die Formen des Produktionsprozesses bestimmt. Dabei liegt der Schwerpunkt auf der Sicherstellung einer rationellen Arbeitsteilung und der darauf basierenden Festlegung der beruflichen und Qualifikationszusammensetzung der Arbeitnehmer, der wissenschaftlichen Gestaltung und optimalen Instandhaltung der Arbeitsplätze sowie der umfassenden Verbesserung und Verbesserung der Arbeitsbedingungen.
Zur Organisation von Produktionsprozessen gehört auch die zeitliche Kombination ihrer Elemente, die eine bestimmte Reihenfolge der Ausführung einzelner Vorgänge, eine rationelle Kombination der Ausführungszeit, bestimmt verschiedene Arten Arbeiten, Festlegung von Kalender- und Planungsstandards für den Transport von Arbeitsgegenständen. Der normale zeitliche Ablauf der Prozesse wird auch durch die Reihenfolge der Produkteinführung und -freigabe, die Bildung der notwendigen Bestände (Reserven) und Produktionsreserven sowie die unterbrechungsfreie Versorgung der Arbeitsplätze mit Werkzeugen, Werkstücken und Materialien sichergestellt. Ein wichtiger Bereich dieser Tätigkeit ist die Organisation der rationellen Bewegung von Materialflüssen. Die Lösung dieser Aufgaben erfolgt auf der Grundlage der Entwicklung und Implementierung betrieblicher Produktionsplanungssysteme unter Berücksichtigung der Art der Produktion sowie technischer und organisatorischer Besonderheiten der Produktionsprozesse.
Schließlich kommt bei der Organisation von Produktionsprozessen in einem Unternehmen der Entwicklung eines Systems der Interaktion zwischen einzelnen Produktionseinheiten ein wichtiger Stellenwert zu.
Grundsätze der Organisation des Produktionsprozesses stellen die Ausgangspunkte dar, auf deren Grundlage Aufbau, Betrieb und Entwicklung von Produktionsprozessen erfolgen.
Prinzip Differenzierung Dabei geht es darum, den Produktionsprozess in einzelne Teile (Prozesse, Vorgänge) zu unterteilen und diese den entsprechenden Abteilungen des Unternehmens zuzuordnen. Dem Prinzip der Differenzierung steht das Prinzip gegenüber kombinieren, was die Vereinheitlichung aller oder eines Teils verschiedener Prozesse zur Herstellung bestimmter Produkttypen an einem Standort, einer Werkstatt oder einer Produktion bedeutet. Abhängig von der Komplexität des Produkts, dem Produktionsvolumen und der Art der verwendeten Ausrüstung kann der Produktionsprozess in einer Produktionseinheit (Werkstatt, Bereich) konzentriert oder auf mehrere Einheiten verteilt sein. So werden in Maschinenbaubetrieben mit einer bedeutenden Produktion ähnlicher Produkte unabhängige mechanische und Montagefertigungen und -werkstätten organisiert und für kleine Produktserien können einheitliche mechanische Montagewerkstätten geschaffen werden.
Die Grundsätze der Differenzierung und Kombination gelten auch für einzelne Arbeitsplätze. Eine Produktionslinie beispielsweise besteht aus einer differenzierten Reihe von Arbeitsplätzen.
IN praktische Tätigkeiten Bei der Organisation der Produktion sollte bei der Anwendung der Prinzipien der Differenzierung oder Kombination dem Prinzip Vorrang eingeräumt werden, das die besten wirtschaftlichen und sozialen Merkmale des Produktionsprozesses gewährleistet. Somit ermöglicht die Fließproduktion, die sich durch einen hohen Differenzierungsgrad des Produktionsprozesses auszeichnet, eine Vereinfachung seiner Organisation, eine Verbesserung der Fähigkeiten der Arbeitnehmer und eine Steigerung der Arbeitsproduktivität. Eine übermäßige Differenzierung erhöht jedoch die Ermüdung der Arbeiter, eine große Anzahl von Vorgängen erhöht den Bedarf an Ausrüstung und Produktionsraum, führt zu unnötigen Kosten für bewegliche Teile usw.
Prinzip Konzentrationen bezeichnet die Konzentration bestimmter Produktionsbetriebe zur Herstellung technologisch homogener Produkte oder zur Erbringung funktional homogener Arbeiten an getrennten Arbeitsplätzen, Bereichen, Werkstätten oder Produktionsstätten des Unternehmens. Die Möglichkeit, ähnliche Arbeiten in getrennten Produktionsbereichen zu konzentrieren, wird durch folgende Faktoren bestimmt: die Gemeinsamkeit technologischer Methoden, die den Einsatz derselben Art von Ausrüstung erfordern; Fähigkeiten von Geräten, wie z. B. Bearbeitungszentren; Erhöhung des Produktionsvolumens bestimmter Produkttypen; die wirtschaftliche Machbarkeit der Konzentration der Produktion bestimmter Produkttypen oder der Durchführung ähnlicher Arbeiten.
Bei der Wahl der einen oder anderen Konzentrationsrichtung müssen die Vorteile jeder einzelnen davon berücksichtigt werden.
Durch die Konzentration technologisch homogener Arbeiten in einer Abteilung wird weniger Duplikat-Equipment benötigt, die Produktionsflexibilität erhöht sich, eine schnelle Umstellung auf die Produktion neuer Produkte wird möglich und die Anlagenauslastung steigt.
Durch die Konzentration technologisch homogener Produkte werden die Kosten für den Material- und Produkttransport gesenkt, die Dauer des Produktionszyklus verkürzt, das Produktionsmanagement vereinfacht und der Bedarf an Produktionsfläche reduziert.
Prinzip Spezialisierungen basiert auf der Begrenzung der Vielfalt der Elemente des Produktionsprozesses. Die Umsetzung dieses Prinzips besteht darin, jedem Arbeitsplatz und jeder Abteilung ein streng begrenztes Spektrum an Arbeiten, Vorgängen, Teilen oder Produkten zuzuordnen. Im Gegensatz zum Spezialisierungsprinzip setzt das Universalisierungsprinzip eine Produktionsorganisation voraus, in der jeder Arbeitsplatz oder eine Produktionseinheit beschäftigt sich mit der Herstellung einer breiten Palette von Teilen und Produkten oder mit der Durchführung unterschiedlicher Fertigungsvorgänge.
Der Spezialisierungsgrad der Arbeitsplätze wird durch einen speziellen Indikator bestimmt – den BetrZU z.o, die durch die Anzahl der über einen bestimmten Zeitraum am Arbeitsplatz durchgeführten Detailoperationen gekennzeichnet ist. Ja, wenn ZU z.o = 1 gibt es eine enge Spezialisierung von Berufen, bei der eine Detailarbeit am Arbeitsplatz im Laufe eines Monats oder Quartals ausgeführt wird.
Die Art der Spezialisierung von Abteilungen und Stellen wird maßgeblich durch das Produktionsvolumen gleichnamiger Teile bestimmt. Die Spezialisierung erreicht ihren höchsten Grad bei der Herstellung eines Produkttyps. Das typischste Beispiel für hochspezialisierte Industrien sind Fabriken zur Herstellung von Traktoren, Fernsehern und Autos. Durch die Vergrößerung des Produktionsspektrums verringert sich der Spezialisierungsgrad.
Ein hoher Spezialisierungsgrad von Abteilungen und Arbeitsplätzen trägt zur Steigerung der Arbeitsproduktivität aufgrund der Entwicklung der Arbeitsfähigkeiten der Arbeitnehmer, der Möglichkeit der technischen Ausstattung der Arbeitskräfte und der Minimierung der Kosten für die Neukonfiguration von Maschinen und Linien bei. Gleichzeitig verringert eine enge Spezialisierung die erforderlichen Qualifikationen der Arbeitnehmer, führt zu Monotonie der Arbeit und führt dadurch zu einer schnellen Ermüdung der Arbeitnehmer und schränkt ihre Initiative ein.
Unter modernen Bedingungen besteht eine zunehmende Tendenz zur Universalisierung der Produktion, die durch die Anforderungen bestimmt wird wissenschaftlicher und technischer Fortschritt Erweiterung der Produktpalette, Entstehung multifunktionaler Geräte, Aufgaben der Verbesserung der Arbeitsorganisation in Richtung Expansion Arbeitsfunktionen Arbeiter.
Prinzip Verhältnismäßigkeit besteht in einer natürlichen Kombination einzelner Elemente des Produktionsprozesses, die sich in einem bestimmten quantitativen Verhältnis zwischen ihnen ausdrückt. Proportionalität der Produktionskapazität setzt also die Gleichheit der Standortkapazitäten oder der Ausrüstungsauslastungsfaktoren voraus. In diesem Fall entspricht der Durchsatz der Beschaffungswerkstätten dem Bedarf an Rohlingen in den mechanischen Werkstätten und der Durchsatz dieser Werkstätten entspricht dem Bedarf der Montagewerkstatt an den benötigten Teilen. Dies beinhaltet die Anforderung, in jeder Werkstatt über Ausrüstung, Platz und Arbeitskräfte in solchen Mengen zu verfügen, dass der normale Betrieb aller Abteilungen des Unternehmens gewährleistet ist. Zwischen der Hauptproduktion einerseits und den Hilfs- und Serviceeinheiten andererseits sollte das gleiche Durchsatzverhältnis bestehen.
Ein Verstoß gegen den Grundsatz der Verhältnismäßigkeit führt zu Ungleichgewichten, zur Entstehung von Produktionsengpässen, wodurch sich der Einsatz von Ausrüstung und Arbeitskräften verschlechtert, die Dauer des Produktionszyklus zunimmt und Rückstände zunehmen.
Die Verhältnismäßigkeit von Arbeitskräften, Raum und Ausrüstung wird bereits bei der Unternehmensplanung festgestellt und dann bei der Entwicklung jährlicher Produktionspläne durch sogenannte volumetrische Berechnungen geklärt – bei der Ermittlung von Kapazität, Mitarbeiterzahl und Materialbedarf. Proportionen werden auf der Grundlage eines Systems von Standards und Normen festgelegt, die die Anzahl der gegenseitigen Verbindungen zwischen verschiedenen Elementen des Produktionsprozesses bestimmen.
Der Grundsatz der Verhältnismäßigkeit beinhaltet die gleichzeitige Durchführung einzelner Vorgänge oder Teile des Produktionsprozesses. Ihr liegt die These zugrunde, dass Teile eines zerlegten Produktionsprozesses zeitlich zusammengeführt und gleichzeitig durchgeführt werden müssen.
Der Produktionsprozess einer Maschine besteht aus einer Vielzahl von Arbeitsgängen. Es liegt auf der Hand, dass die sequentielle Ausführung nacheinander zu einer Verlängerung des Produktionszyklus führen würde. Daher müssen einzelne Teile des Produktherstellungsprozesses parallel durchgeführt werden.
Parallelität wird erreicht: bei der Bearbeitung eines Teils auf einer Maschine mit mehreren Werkzeugen; gleichzeitige Bearbeitung verschiedene Teile eine Charge für einen bestimmten Vorgang an mehreren Arbeitsplätzen; gleichzeitige Bearbeitung gleicher Teile in verschiedenen Arbeitsgängen an mehreren Arbeitsplätzen; gleichzeitige Herstellung verschiedener Teile desselben Produkts an verschiedenen Arbeitsplätzen. Die Einhaltung des Parallelitätsprinzips führt zu einer Verkürzung der Dauer des Produktionszyklus und der Legezeit der Teile, wodurch Arbeitszeit gespart wird.
Unter Geradheit das Prinzip der Organisation des Produktionsprozesses verstehen, nach dem alle Phasen und Vorgänge des Produktionsprozesses unter den Bedingungen des kürzesten Weges des Arbeitsgegenstandes vom Beginn des Prozesses bis zu seinem Ende durchgeführt werden. Das Prinzip der Direktströmung muss gewährleistet sein geradlinige Bewegung Arbeitsgegenstände im technologischen Prozess, wodurch verschiedene Arten von Schleifen und Rückbewegungen vermieden werden.
Eine vollständige Geradlinigkeit kann durch die räumliche Anordnung von Vorgängen und Teilen des Produktionsprozesses in der Reihenfolge der technologischen Vorgänge erreicht werden. Bei der Gestaltung von Betrieben ist außerdem darauf zu achten, dass Werkstätten und Dienstleistungen in einer Reihenfolge angeordnet sind, die einen Mindestabstand zwischen benachbarten Abteilungen gewährleistet. Sie sollten sich bemühen, sicherzustellen, dass Teile und Baugruppen verschiedener Produkte die gleiche oder eine ähnliche Abfolge von Phasen und Vorgängen im Produktionsprozess aufweisen. Bei der Umsetzung des Direktflussprinzips stellt sich auch das Problem der optimalen Anordnung von Geräten und Arbeitsplätzen.
Das Prinzip des Direktflusses manifestiert sich in stärkerem Maße in den Bedingungen der kontinuierlichen Produktion, bei der Schaffung fachbezogener Werkstätten und Abschnitte.
Die Einhaltung linearer Anforderungen führt zu einer Rationalisierung der Frachtströme, einer Reduzierung des Frachtumschlags und einer Reduzierung der Kosten für den Transport von Materialien, Teilen und Fertigprodukten.
Prinzip Rhythmik bedeutet, dass alle einzelnen Produktionsprozesse und ein einzelner Prozess zur Herstellung eines bestimmten Produkttyps nach festgelegten Zeiträumen wiederholt werden. Unterscheiden Sie zwischen Produktions-, Arbeits- und Produktionsrhythmus.
Der Produktionsrhythmus ist die Freisetzung gleicher oder gleichmäßig steigender (abnehmender) Produktmengen in gleichen Zeitabständen. Rhythmizität der Arbeit ist die Fertigstellung gleicher Arbeitsmengen (in Menge und Zusammensetzung) in gleichen Zeitintervallen. Rhythmische Produktion bedeutet die Aufrechterhaltung eines rhythmischen Outputs und Arbeitsrhythmus.
Rhythmisches Arbeiten ohne Ruckeln und Stürmen ist die Grundlage für eine Steigerung der Arbeitsproduktivität, eine optimale Auslastung der Geräte, eine vollständige Auslastung des Personals und eine Garantie für qualitativ hochwertige Produkte. Der reibungslose Betrieb eines Unternehmens hängt von einer Reihe von Bedingungen ab. Die Sicherstellung des Rhythmus ist eine komplexe Aufgabe, die eine Verbesserung der gesamten Produktionsorganisation im Unternehmen erfordert. Von größter Bedeutung sind die korrekte Organisation der betrieblichen Produktionsplanung, die Einhaltung der Verhältnismäßigkeit der Produktionskapazitäten, die Verbesserung der Produktionsstruktur, die ordnungsgemäße Organisation der Logistik und die technische Aufrechterhaltung der Produktionsprozesse.
Prinzip Kontinuität wird in solchen Organisationsformen des Produktionsprozesses umgesetzt, in denen alle seine Vorgänge kontinuierlich und ohne Unterbrechungen durchgeführt werden und alle Arbeitsgegenstände kontinuierlich von Betrieb zu Betrieb wechseln.
Das Prinzip der Kontinuität des Produktionsprozesses wird in automatischen und kontinuierlichen Produktionslinien vollständig umgesetzt, auf denen Arbeitsgegenstände hergestellt oder montiert werden, wobei Vorgänge von gleicher oder mehrfacher Dauer im Linienzyklus durchgeführt werden.
Im Maschinenbau überwiegen diskrete technologische Prozesse, daher ist eine Produktion mit einem hohen Grad an Synchronisation der Betriebsdauer hier nicht vorherrschend.
Die intermittierende Bewegung von Arbeitsgegenständen ist mit Pausen verbunden, die durch das Verlegen von Teilen in jedem Betrieb, zwischen Betrieben, Abschnitten und Werkstätten entstehen. Deshalb erfordert die Umsetzung des Kontinuitätsprinzips die Beseitigung oder Minimierung von Unterbrechungen. Die Lösung eines solchen Problems kann auf der Grundlage der Einhaltung der Grundsätze der Verhältnismäßigkeit und des Rhythmus erreicht werden; Organisation der parallelen Produktion von Teilen einer Charge oder verschiedener Teile eines Produkts; Schaffung solcher Organisationsformen von Produktionsprozessen, bei denen die Startzeit der Herstellung von Teilen in einem bestimmten Vorgang und die Endzeit des vorherigen Vorgangs synchronisiert werden usw.
Ein Verstoß gegen den Kontinuitätsgrundsatz führt in der Regel zu Arbeitsunterbrechungen (Ausfallzeiten von Arbeitskräften und Geräten), was zu einer Verlängerung des Produktionszyklus und des Umfangs der laufenden Arbeiten führt.
Die Prinzipien der Produktionsorganisation wirken in der Praxis nicht isoliert, sondern sind in jedem Produktionsprozess eng miteinander verknüpft. Beim Studium der Organisationsprinzipien sollten Sie darauf achten Paarcharakter einige von ihnen, ihre Wechselbeziehung, gehen in ihr Gegenteil über (Differenzierung und Kombination, Spezialisierung und Universalisierung). Die Organisationsprinzipien entwickeln sich ungleichmäßig: Hin und wieder tritt ein Prinzip in den Vordergrund oder erlangt eine untergeordnete Bedeutung. Damit gehört die enge Spezialisierung der Berufe der Vergangenheit an, sie werden immer universeller. Das Prinzip der Differenzierung wird zunehmend durch das Prinzip der Kombination ersetzt, dessen Einsatz es ermöglicht, einen Produktionsprozess auf der Grundlage eines einzigen Flusses aufzubauen. Gleichzeitig nimmt unter Bedingungen der Automatisierung die Bedeutung der Grundsätze der Verhältnismäßigkeit, Kontinuität und Geradlinigkeit zu.
Der Grad der Umsetzung der Grundsätze der Produktionsorganisation hat eine quantitative Dimension. Daher müssen zusätzlich zu den aktuellen Methoden der Produktionsanalyse Formen und Methoden zur Analyse des Zustands der Produktionsorganisation und zur Umsetzung ihrer wissenschaftlichen Grundsätze entwickelt und in der Praxis angewendet werden. Methoden zur Berechnung des Umsetzungsgrades bestimmter Prinzipien der Organisation von Produktionsprozessen werden im Kapitel angegeben. 20.
Die Einhaltung der Grundsätze der Organisation von Produktionsprozessen ist von großer praktischer Bedeutung. Die Umsetzung dieser Grundsätze liegt in der Verantwortung aller Ebenen des Produktionsmanagements.
10.3. Räumliche Organisation von Produktionsprozessen
Produktionsstruktur des Unternehmens. Die räumliche Zusammenführung von Teilen des Produktionsprozesses wird durch die Produktionsstruktur des Unternehmens sichergestellt. Unter der Produktionsstruktur versteht man die Gesamtheit der dazu gehörenden Produktionseinheiten eines Unternehmens sowie die Formen der Beziehungen zwischen ihnen. Unter modernen Bedingungen kann der Produktionsprozess in zwei Varianten betrachtet werden:
- als Prozess der materiellen Produktion mit dem Endergebnis – kommerziellen Produkten;
- als Prozess der Designproduktion mit dem Endergebnis – einem wissenschaftlich-technischen Produkt.
Die Art der Produktionsstruktur eines Unternehmens hängt von der Art seiner Tätigkeiten ab, von denen die wichtigsten die folgenden sind: Forschung, Produktion, Forschung und Produktion, Produktion und Technik, Management und Wirtschaft.
Die Priorität der jeweiligen Tätigkeitsarten bestimmt die Struktur des Unternehmens, den Anteil der wissenschaftlichen, technischen und Produktionsabteilungen, das Verhältnis der Zahl der Arbeiter und Ingenieure.
Die Zusammensetzung der Abteilungen eines auf Produktionstätigkeiten spezialisierten Unternehmens wird durch die Gestaltungsmerkmale der hergestellten Produkte und der Technologie ihrer Herstellung, den Produktionsumfang, die Spezialisierung des Unternehmens und die bestehenden Kooperationsbeziehungen bestimmt. In Abb. Abbildung 10.1 zeigt ein Diagramm der Beziehungen zwischen Faktoren, die die Produktionsstruktur eines Unternehmens bestimmen.
Reis. 10.1. Schema der Beziehungen zwischen Faktoren, die die Produktionsstruktur eines Unternehmens bestimmen
Unter modernen Bedingungen hat die Eigentumsform einen großen Einfluss auf die Unternehmensstruktur. Der Übergang vom Staat zu anderen Eigentumsformen – Privateigentum, Aktienbesitz, Pacht – führt in der Regel zu einer Reduzierung unnötiger Verbindungen und Strukturen, der Zahl der Kontrollapparate und reduziert Doppelarbeit.
Derzeit sind verschiedene Formen der Unternehmensorganisation weit verbreitet; Es gibt kleine, mittlere und große Unternehmen, deren Produktionsstruktur jeweils entsprechende Merkmale aufweist.
Die Produktionsstruktur eines Kleinunternehmens ist einfach. In der Regel verfügt es über minimale oder gar keine internen strukturellen Produktionseinheiten. In kleinen Unternehmen ist der Führungsapparat unbedeutend, eine Kombination von Führungsfunktionen ist weit verbreitet.
Bei der Struktur mittelständischer Unternehmen handelt es sich um die Zuteilung von Werkstätten, im Falle einer Nicht-Werkstatt-Struktur von Abteilungen. Hier wird bereits das für die Funktionsfähigkeit des Unternehmens notwendige Minimum geschaffen, eigene Hilfs- und Serviceeinheiten, Abteilungen und Dienste des Führungsapparates.
Große Unternehmen der verarbeitenden Industrie verfügen über ein umfassendes Spektrum an Produktions-, Service- und Verwaltungsabteilungen.
Basierend auf der Produktionsstruktur wird ein Masterplan für das Unternehmen entwickelt. Der Masterplan bezieht sich auf die räumliche Anordnung aller Werkstätten und Dienstleistungen sowie Transportwege und Kommunikation auf dem Territorium des Unternehmens. Bei der Entwicklung eines Masterplans wird der direkte Fluss der Materialflüsse sichergestellt. Werkstätten müssen entsprechend der Reihenfolge des Produktionsprozesses angeordnet sein. Verbundene Dienste und Werkstätten müssen in unmittelbarer Nähe liegen.
Entwicklung der Produktionsstruktur von Verbänden. Die Produktionsstrukturen von Verbänden unter modernen Bedingungen unterliegen erheblichen Veränderungen. Produktionsverbände im verarbeitenden Gewerbe, insbesondere im Maschinenbau, zeichnen sich aus durch die folgenden Anweisungen Verbesserung der Produktionsstrukturen:
- Konzentration der Produktion homogener Produkte oder der Ausführung ähnlicher Arbeiten in einzelnen Fachabteilungen des Vereins;
- Vertiefung der Spezialisierung struktureller Unternehmensbereiche - Produktionsstätten, Werkstätten, Niederlassungen;
- Integration in einheitliche Wissenschafts- und Produktionskomplexe der Arbeit an der Schaffung neuer Produkttypen, ihrer Entwicklung in der Produktion und der Organisation der Produktion in für den Verbraucher notwendigen Mengen;
- Zerstreuung der Produktion durch die Gründung hochspezialisierter Unternehmen unterschiedlicher Größe innerhalb des Verbandes;
- Überwindung der Segmentierung beim Aufbau von Produktionsprozessen und Schaffung einheitlicher Produktherstellungsabläufe ohne Trennung von Werkstätten und Abschnitten;
- Universalisierung der Produktion, die in der Herstellung von Produkten mit unterschiedlichen Zwecken besteht, die aus in Design und Technologie homogenen Einheiten und Teilen zusammengesetzt sind, sowie in der Organisation der Produktion verwandter Produkte;
- breite Entwicklung der horizontalen Zusammenarbeit zwischen Unternehmen, die verschiedenen Verbänden angehören, um die Produktionskosten durch Erhöhung des Produktionsumfangs ähnlicher Produkte und vollständige Auslastung der Kapazitäten zu senken.
Durch die Gründung und Entwicklung großer Verbände entstand eine neue Form der Produktionsstruktur, die durch die Zuteilung spezialisierter Produktionsstätten optimaler Größe gekennzeichnet ist, die auf dem Prinzip der Technologie- und Fachspezialisierung basieren. Diese Struktur sorgt auch für eine maximale Konzentration der Beschaffungs-, Hilfs- und Serviceprozesse. Die neue Form der Produktionsstruktur wurde Multiproduktion genannt. In den 80er Jahren fand es breite Anwendung in der Automobil-, Elektro- und anderen Industrie.
Der Automobilproduktionsverband Nischni Nowgorod beispielsweise umfasst ein Mutterunternehmen und sieben Zweigwerke. Das Mutterunternehmen umfasst zehn spezialisierte Produktionsstätten: Lkw, Pkw, Motoren, Lkw-Achsen, Metallurgie, Schmieden und Federn, Werkzeugproduktion usw. Jede dieser Produktionen vereint eine Gruppe von Haupt- und Nebenwerkstätten, verfügt über eine gewisse Unabhängigkeit und behält enge Beziehungen mit anderen Unternehmensbereichen und genießt die für die Struktureinheiten des Vereins begründeten Rechte. Typische Struktur Die Produktion ist in Abb. dargestellt. 10.2.
Im Volzhsky-Automobilwerk wurde eine Mehrproduktionsstruktur auf einem höheren Qualitätsniveau implementiert. Die Automobilproduktion konzentriert sich hier auf vier Hauptindustrien: Metallurgie, Pressen, mechanische Montage sowie Montage und Schmieden. Darüber hinaus wurden Hilfsproduktionsanlagen zugewiesen. Jeder von ihnen ist ein eigenständiges Werk mit einem geschlossenen Produktionskreislauf. Die Produktion umfasst Werkstätten. Aber die Werkstätten bei VAZ haben erhebliche Veränderungen erfahren. Sie werden von den Sorgen um die Sicherstellung der Produktion, die Reparatur und Wartung von Geräten, die Instandhaltung und Reinigung von Räumlichkeiten usw. befreit. Der VAZ-Produktionswerkstatt bleibt nur noch die Aufgabe, die ihr zugewiesenen Produkte qualitativ hochwertig und termingerecht herzustellen. Die Werkstattverwaltungsstruktur wird so weit wie möglich vereinfacht. Das sind der Werkstattleiter, seine beiden Schichtstellvertreter, Abteilungsleiter, Vorarbeiter und Vorarbeiter. Sämtliche Aufgaben der Versorgung, Produktionsvorbereitung und Instandhaltung werden zentral durch den Produktionsmanagementapparat gelöst.
Reis. 10.2. Typische Produktionsstruktur
In jeder Produktionsabteilung wurden folgende Abteilungen geschaffen: Design und Technologie, Design, Werkzeuge und Ausrüstung, Analyse und Planung von Gerätereparaturen. Sie wurden hier ausgebildet einheitliche Dienstleistungen Einsatzplanung und Disposition, Logistik, Arbeitsorganisation und Löhne.
Die Produktion umfasst große Fachwerkstätten: Reparatur, Herstellung und Reparatur von Geräten, Transport- und Lagervorgänge, Reinigung von Räumlichkeiten und andere. Die Schaffung leistungsstarker Ingenieurdienstleistungen und Produktionsabteilungen in der Produktion, die jeweils die ihnen in ihrem Bereich zugewiesenen Aufgaben vollständig lösen, hat dies grundsätzlich ermöglicht neue Basis normale Bedingungen schaffen für effiziente Arbeit Hauptproduktionswerkstätten.
Die Organisation der Workshops und Sektionen basiert auf den Prinzipien der Konzentration und Spezialisierung. Die Spezialisierung von Werkstätten und Produktionsbereichen kann nach Art der Arbeit – technologische Spezialisierung oder nach Art des hergestellten Produkts – Fachspezialisierung erfolgen. Beispiele für Produktionseinheiten mit technologischer Spezialisierung in einem Maschinenbauunternehmen sind Gießerei, thermische oder galvanische Werkstätten, Dreh- und Schleifabteilungen in einer mechanischen Werkstatt; Fachliche Spezialisierung - Karosserieteilewerkstatt, Wellenteilwerkstatt, Getriebefertigungswerkstatt usw.
Wenn ein vollständiger Zyklus der Herstellung eines Produkts oder Teils innerhalb einer Werkstatt oder eines Standorts durchgeführt wird, wird diese Abteilung als fachgebietsgeschlossen bezeichnet.
Bei der Organisation von Workshops und Sektionen ist es notwendig, die Vor- und Nachteile aller Spezialisierungsarten sorgfältig zu analysieren. Durch die technologische Spezialisierung wird eine hohe Anlagenauslastung sichergestellt, eine hohe Produktionsflexibilität bei der Entwicklung neuer Produkte und beim Wechsel von Produktionsanlagen erreicht. Gleichzeitig wird die betriebliche Produktionsplanung schwieriger, der Produktionszyklus verlängert sich und die Verantwortung für die Produktqualität sinkt.
Der Einsatz der Fachspezialisierung, die die Konzentration aller Arbeiten an der Herstellung eines Teils oder Produkts innerhalb einer Werkstatt oder eines Bereichs ermöglicht, erhöht die Verantwortung der Ausführenden für die Qualität der Produkte und die Erledigung der Aufgaben. Die Fachspezialisierung schafft die Voraussetzungen für die Organisation einer kontinuierlichen und automatisierten Produktion, gewährleistet die Umsetzung des Direktflussprinzips und vereinfacht Planung und Abrechnung. Allerdings ist es nicht immer möglich, eine vollständige Auslastung der Anlagen zu erreichen; die Umstrukturierung der Produktion zur Herstellung neuer Produkte erfordert hohe Kosten.
Fachlich geschlossene Werkstätten und Bereiche haben auch erhebliche wirtschaftliche Vorteile, deren Organisation es ermöglicht, die Dauer des Produktionszyklus für die Herstellung von Produkten durch den vollständigen oder teilweisen Wegfall von Gegen- oder Altersbewegungen zu verkürzen und zu vereinfachen das Planungssystem und die operative Steuerung des Produktionsfortschritts. Die praktische Erfahrung in- und ausländischer Unternehmen ermöglicht es uns, die folgende Gruppierung von Regeln anzugeben, die bei der Entscheidung über die Anwendung des Themas oder des technologischen Prinzips beim Bau von Werkstätten und Abteilungen beachtet werden sollten.
Thema Es wird empfohlen, das Prinzip in folgenden Fällen anzuwenden: bei der Herstellung von einem oder zwei Standardprodukten, mit einem großen Volumen und einem hohen Maß an Stabilität bei der Herstellung von Produkten, mit der Möglichkeit eines guten Gleichgewichts von Ausrüstung und Arbeit, mit a minimale Kontrollvorgänge und geringe Anzahl von Umstellungen; technologisch- bei der Herstellung einer großen Produktpalette mit relativ geringen Serienstückzahlen, der Unmöglichkeit, Ausrüstung und Arbeit in Einklang zu bringen, mit einer großen Anzahl von Kontrollvorgängen und einer erheblichen Anzahl von Umrüstungen.
Organisation von Produktionsstandorten. Die Organisation der Standorte wird durch die Art ihrer Spezialisierung bestimmt. Dabei geht es um die Lösung einer Vielzahl von Problemen, darunter die Auswahl der Produktionsanlagen; Berechnung notwendige Ausrüstung und sein Layout; Bestimmung der Größe von Chargen (Serien) von Teilen und der Häufigkeit ihrer Einführung und Produktion; Zuweisung von Arbeiten und Abläufen zu jedem Arbeitsplatz, Erstellung von Zeitplänen; Berechnung des Personalbedarfs; Entwurf eines Arbeitsplatzservicesystems. IN In letzter Zeit Es begannen sich Forschungs- und Produktionskomplexe in Verbänden zu bilden, die alle Phasen des Zyklus „Forschung – Entwicklung – Produktion“ integrierten.
Im St. Petersburger Verein „Svetlana“ wurden zum ersten Mal im Land vier Forschungs- und Produktionskomplexe geschaffen. Der Komplex ist eine einzelne Abteilung, die auf die Entwicklung und Produktion von Produkten eines bestimmten Profils spezialisiert ist. Es entsteht auf Basis der Konstruktionsbüros des Stammwerks. Neben dem Konstruktionsbüro umfasst es Hauptproduktionswerkstätten und spezialisierte Niederlassungen. Die wissenschaftlichen und Produktionsaktivitäten der Komplexe werden auf der Grundlage von Berechnungen vor Ort durchgeführt.
Forschungs- und Produktionskomplexe führen die gestalterische und technologische Vorbereitung der Produktion durch und ziehen die entsprechenden Abteilungen des Verbandes für die Durchführung von Arbeiten im Zusammenhang mit der Entwicklung neuer Produkte ein. Der Leiter des Konstruktionsbüros erhält das Recht zur ganzheitlichen Planung aller Phasen der Produktionsvorbereitung – von der Forschung bis zur Organisation der Serienproduktion. Er ist nicht nur für die Qualität und den Zeitplan der Entwicklung verantwortlich, sondern auch für die Entwicklung der Serienproduktion neuer Produkte und Produktionsaktivitäten Werkstätten und Filialen im Komplex enthalten.
Im Rahmen des Übergangs von Unternehmen zu Marktwirtschaft es passiert weitere Entwicklung die Produktionsstruktur von Verbänden, die auf der Erhöhung der wirtschaftlichen Unabhängigkeit ihrer Mitgliedseinheiten basiert.
Als Beispiel für die Schaffung und Umsetzung einer neuen Organisationsform unter den Bedingungen des Übergangs zum Markt können wir die Gründung anführen Aktiengesellschaft— Wissenschafts- und Produktionskonzern im Verein „Energia“ (Woronesch). Auf der Grundlage der Unternehmensbereiche sind mehr als 100 unabhängige Forschungs- und Produktionskomplexe, Verbände und Unternehmen der ersten Ebene mit völliger rechtlicher Unabhängigkeit und Girokonten bei einer Geschäftsbank entstanden. Bei der Gründung unabhängiger Vereine und Unternehmen kamen zum Einsatz: verschiedene Eigentumsformen (Staat, Miete, gemischt, Aktiengesellschaft, Genossenschaft); vielfältige Organisationsstrukturen unabhängiger Unternehmen und Verbände, deren Zahl zwischen 3 und 2350 Personen variiert; vielfältige Tätigkeiten (Forschung und Produktion, Organisation und Wirtschaft, Produktion und Technik).
Der Konzern verfügt über 20 fachspezifische und funktionale Forschungs- und Produktionskomplexe, die Forschungs-, Design-, Technologieabteilungen und Produktionsanlagen vereinen und sich auf die Entwicklung und Produktion bestimmter Produkttypen oder die Durchführung technologisch homogener Arbeiten spezialisiert haben. Diese Komplexe entstanden durch die Reform von Pilot- und Serienanlagen und auf der Grundlage eines Forschungsinstituts. Je nach Anzahl und Umfang der Arbeit fungieren sie als Vereine erster Ebene, Betriebe oder Kleinbetriebe.
Forschungs- und Produktionskomplexe konnten ihre Vorteile während der Umstellungszeit unter den Bedingungen einer starken Änderung der Produktpalette voll ausspielen. Nach der Erlangung der Unabhängigkeit gründeten die Unternehmen freiwillig Verbände der ersten Ebene – Forschungs- und Produktionskomplexe oder Unternehmen – und gründeten einen Konzern, der gemäß der Charta zehn Hauptfunktionen zentralisierte. Das höchste Leitungsorgan des Konzerns ist die Gesellschafterversammlung. Die Koordinierung der Arbeiten zur Wahrnehmung zentraler Funktionen erfolgt durch den Vorstand und die Funktionsabteilungen des Konzerns unter Bedingungen völliger Selbstversorgung. Auch die Bereiche, die Service- und Supportfunktionen wahrnehmen, arbeiten auf vertraglicher Basis und verfügen über volle rechtliche und wirtschaftliche Unabhängigkeit.
In Abb. dargestellt. 10.3 und die „zirkuläre“ Führungsstruktur des Konzerns entspricht den gesetzlichen Anforderungen Russische Föderation. Der Vorstand koordiniert die zentralen Funktionen des Konzerns im Rahmen der Satzung nach der Idee des Runden Tisches.
Das zirkuläre (im Gegensatz zum bestehenden vertikalen) System der Organisation und des Produktionsmanagements basiert auf folgenden Grundsätzen:
Reis. 10.3. Zirkuläre Managementstruktur des Energia-Konzerns
- über die Freiwilligkeit der Unternehmensvereinigung für Gemeinsame Aktivitäten um durch den Verkauf von Produkten und Dienstleistungen auf einem wettbewerbsorientierten Markt maximale und stabile Gewinne zu erzielen und so den sozialen und wirtschaftlichen Interessen der Aktionäre gerecht zu werden;
- freiwillige Zentralisierung eines Teils der Funktionen von Unternehmen bei der Organisation und Verwaltung der Produktion, verankert in der Satzung der Aktiengesellschaft;
- Kombination der Vorteile eines großen Unternehmens aufgrund von Spezialisierung, Zusammenarbeit und Produktionsumfang mit den Vorteilen kleiner Unternehmensformen und Motivation der Mitarbeiter durch Eigentumsbesitz;
- ein System technisch miteinander verbundener fachlicher und funktionaler Wissenschafts- und Produktionskomplexe unter Berücksichtigung der Vorteile von Spezialisierung und Zusammenarbeit;
- ein System vertraglicher Beziehungen zwischen Forschungs- und Produktionskomplexen und Unternehmen, unterstützt durch ein System zur Befriedigung selbsttragender Ansprüche, einschließlich der Regulierung des Lohnfonds;
- Verlagerung des Zentrums der aktuellen Arbeit zur Organisation und Verwaltung der Produktion von der höchsten Ebene vertikal auf die Ebene der Wissenschafts- und Produktionskomplexe und unabhängigen Unternehmen horizontal auf vertraglicher Basis mit Konzentration der Bemühungen der Geschäftsleitung auf vielversprechende Themen;
- Umsetzung der Wirtschaftsbeziehungen zwischen Unternehmen durch eine Geschäftsbank und ein Zentrum für interne Abrechnungen in relevanten Bereichen;
- Erhöhung der Garantien zur Lösung sozialer Probleme und zum Schutz sowohl unabhängiger Unternehmen als auch aller Aktionäre;
- Kombination und Entwicklung verschiedener Eigentumsformen auf der Ebene des Konzerns und unabhängiger Vereine und Unternehmen;
- Ablehnung der dominanten Rolle der höchsten Leitungsorgane mit der Umwandlung der Funktionen der Leitung und Koordinierung der Produktion in eine der Tätigkeitsarten der Aktionäre;
- Entwicklung eines Mechanismus, um die gegenseitigen Interessen unabhängiger Unternehmen und des Konzerns als Ganzes zu vereinen und die Gefahr eines Bruchs aufgrund der Zentrifugalkräfte des technologischen Prinzips beim Aufbau der Produktionsorganisation zu verhindern.
Die zirkuläre Struktur sorgt für eine grundlegende Veränderung der Aktivitäten fachspezifischer Forschungs- und Produktionskomplexe, die die führende Rolle bei der Planung und Sicherstellung der horizontalen Vernetzung der Aktivitäten funktionaler Forschungs- und Produktionskomplexe und Unternehmen auf vertraglicher Basis gemäß ihrer Nomenklatur übernehmen , unter Berücksichtigung von Marktveränderungen.
Die Planungs- und Versandabteilung innerhalb des Unternehmens Pribyl wurde umgestaltet und ein erheblicher Teil ihrer Funktionen und ihres Personals in fachspezifische Forschungs- und Produktionskomplexe verlagert. Die Aufmerksamkeit dieses Dienstes liegt auf strategischen Aufgaben und der Koordination der Arbeit von Komplexen und Unternehmen.
Concern Energia durchlief den Privatisierungsprozess durch Leasing und Korporatisierung, erhielt eine Eigentumsbescheinigung für das Eigentum und erhielt den Status eines Bundesforschungs- und Produktionszentrums.
10.4. Organisation von Produktionsabläufen im Zeitverlauf
Um ein rationelles Zusammenspiel aller Elemente des Produktionsprozesses zu gewährleisten und die geleistete Arbeit zeitlich und räumlich zu rationalisieren, ist es notwendig, einen Produktionszyklus des Produkts zu bilden.
Der Produktionszyklus ist ein Komplex von Grund-, Hilfs- und Serviceprozessen, die zeitlich auf eine bestimmte Weise organisiert sind und für die Herstellung eines bestimmten Produkttyps erforderlich sind. Das wichtigste Merkmal des Produktionszyklus ist seine Dauer.
Produktionszykluszeit- Hierbei handelt es sich um einen kalendarischen Zeitraum, in dem ein Material, Werkstück oder ein anderer verarbeiteter Gegenstand alle Vorgänge des Produktionsprozesses oder einen bestimmten Teil davon durchläuft und in fertige Produkte umgewandelt wird. Die Dauer des Zyklus wird in Kalendertagen oder Stunden ausgedrückt. Struktur des Produktionszyklus beinhaltet Arbeitszeit und Pausenzeit. Während der Arbeitszeit werden die eigentlichen technologischen Arbeiten sowie Vor- und Abschlussarbeiten durchgeführt. Zur Arbeitszeit zählen auch die Dauer von Kontroll- und Transportvorgängen sowie die Zeit natürlicher Prozesse. Die Zeit der Pausen wird durch das Arbeitsregime, die betriebsübergreifende Teileverfolgung und Mängel in der Arbeits- und Produktionsorganisation bestimmt.
Die Interoperationswartezeit wird durch Unterbrechungen bei der Chargen-, Warte- und Personalbesetzung bestimmt. Chargenbrüche treten bei der Herstellung von Produkten in Chargen auf und sind darauf zurückzuführen, dass die verarbeiteten Produkte so lange liegen bleiben, bis die gesamte Charge diesen Vorgang durchlaufen hat. In diesem Fall wird davon ausgegangen, dass es sich bei einer Produktionscharge um eine Gruppe von Produkten mit demselben Namen und derselben Standardgröße handelt, die innerhalb einer bestimmten Zeit mit derselben Vorbereitungs- und Endzeit in Produktion gehen. Wartepausen entstehen durch die uneinheitliche Dauer zweier benachbarter Vorgänge des technologischen Prozesses, Kommissionierpausen entstehen durch die Notwendigkeit, zu warten, bis alle Rohlinge, Teile oder Baugruppen eines Produktsatzes hergestellt sind. Kommissionierunterbrechungen treten beim Übergang von einer Phase des Produktionsprozesses zu einer anderen auf.
In den meisten Gesamtansicht Dauer des Produktionszyklus T q wird durch die Formel ausgedrückt
T ts = T t + Tn –3 + T e + T k + T tr + T Mo + T pr, (10.1)
Wo T t ist die Zeit der technologischen Operationen; Tn–3 – Zeit der Vorbereitungs- und Abschlussarbeiten; T e ist die Zeit natürlicher Prozesse; T k ist die Zeit der Kontrollvorgänge; T tr – Zeitpunkt des Transports von Arbeitsgegenständen; T Mo – Zeit der interoperativen Schlafenszeit (Pausen innerhalb der Schicht); T pr – Zeit der arbeitsplanbedingten Pausen.
Die Dauer der technologischen Operationen sowie der vorbereitenden und abschließenden Arbeiten bilden zusammen den Betriebszyklus T Polizist.
Betriebszyklus- Dies ist die Dauer des abgeschlossenen Teils des technologischen Prozesses, der an einem Arbeitsplatz durchgeführt wird.
Methoden zur Berechnung der Dauer des Produktionszyklus. Es ist zu unterscheiden zwischen dem Produktionszyklus einzelner Teile und dem Produktionszyklus einer Baugruppe oder eines Produkts als Ganzes. Der Produktionszyklus eines Teils wird üblicherweise als einfach bezeichnet, und der Produktionszyklus eines Produkts oder einer Baugruppe wird als komplex bezeichnet. Der Zyklus kann ein- oder mehrbetrieben sein. Die Zykluszeit eines Prozesses mit mehreren Arbeitsgängen hängt von der Art der Übergabe von Teilen von Arbeitsgang zu Arbeitsgang ab. Es gibt drei Arten der Bewegung von Arbeitsgegenständen im Prozess ihrer Herstellung: sequentiell, parallel und parallel-sequentiell.
Bei sequentielle Art der Bewegung die gesamte Teilecharge wird an den Folgevorgang übergeben, nachdem die Bearbeitung aller Teile im vorherigen Vorgang abgeschlossen ist. Die Vorteile dieser Methode sind das Fehlen von Betriebsunterbrechungen für Geräte und Arbeiter bei jedem Vorgang sowie die Möglichkeit ihrer hohen Belastung während der Schicht. Bei einer solchen Arbeitsorganisation ist der Produktionszyklus jedoch der größte, was sich negativ auf die technischen und wirtschaftlichen Indikatoren der Werkstatt oder des Unternehmens auswirkt.
Bei parallele Bewegungsart Die Übergabe der Teile an den nächsten Arbeitsgang per Transportcharge erfolgt unmittelbar nach Abschluss der Bearbeitung im vorherigen Arbeitsgang. In diesem Fall ist der kürzeste Zyklus gewährleistet. Allerdings sind die Möglichkeiten der parallelen Bewegungsart begrenzt Voraussetzung seine Umsetzung ist gleich oder ein Vielfaches der Betriebsdauer. Andernfalls sind Betriebsunterbrechungen von Geräten und Arbeitern unvermeidlich.
Bei parallel-sequentielle Bewegungsart Teile werden in Transportchargen oder einzeln von Betrieb zu Betrieb transportiert. In diesem Fall kommt es zu einer teilweisen Überlappung der Ausführungszeit benachbarter Vorgänge und der gesamte Stapel wird bei jedem Vorgang ohne Unterbrechungen verarbeitet. Arbeiter und Geräte arbeiten ohne Pausen. Der Produktionszyklus ist im Vergleich zu einem parallelen länger, aber kürzer als bei der sequentiellen Bewegung von Arbeitsgegenständen.
Taktberechnung für einen einfachen Produktionsprozess. Der betriebliche Produktionszyklus einer Teilecharge mit sequentieller Bewegungsart berechnet sich wie folgt:
(10.2)
Wo N— Anzahl der Teile in der Produktionscharge, Stk.; R op ist die Anzahl der technologischen Prozessoperationen; T PC ich— Standardzeit für die Durchführung jeder Operation, min; MIT r.m. ich— die Anzahl der Arbeitsplätze, die durch die Produktion einer Charge von Teilen in jedem Arbeitsgang belegt werden.
Das Diagramm der sequentiellen Bewegungsart ist in Abb. dargestellt. 10.4, A. Anhand der im Diagramm angegebenen Daten wird der Arbeitszyklus einer Charge bestehend aus drei Teilen berechnet, die an vier Arbeitsplätzen verarbeitet werden:
T c.seq = 3 (t Stück 1 + t Stück 2 + t Stück 3 + t Stück 4) = 3 (2 + 1 + 4 + 1,5) = 25,5 min.
Formel zur Berechnung der Dauer des Arbeitszyklus bei paralleler Bewegungsart:
(10.3)
wo ist die Ausführungszeit des längsten Vorgangs im technologischen Prozess, min.
Reis. 10.4, a. Produktionszyklusplan für die sequentielle Bewegung von Teilechargen
Der Bewegungsplan einer Charge von Teilen mit paralleler Bewegung ist in Abb. dargestellt. 10,4, geb. Anhand des Diagramms können Sie die Dauer des Arbeitszyklus bei Parallelbewegung ermitteln:
T c.pair = ( T Stück 1 + T Stück 2 + T Stück 3 + T Stück 4)+ (3 – 1) T Stk. 3 = 8,5 + (3 – 1) 4 = 16,5 Min.
Reis. 10,4, geb. Produktionszyklusplan für die parallel-sequentielle Bewegung von Teilechargen
Bei einer parallel-sequentiellen Bewegungsart kommt es zu einer teilweisen Überlappung der Ausführungszeit benachbarter Vorgänge. Es gibt zwei Arten der zeitlichen Kombination benachbarter Operationen. Wenn die Ausführungszeit des nachfolgenden Vorgangs länger ist als die Ausführungszeit des vorherigen Vorgangs, kann eine parallele Art der Teilebewegung verwendet werden. Wenn die Ausführungszeit des nachfolgenden Vorgangs kürzer ist als die Ausführungszeit des vorherigen, ist eine parallel-sequentielle Bewegungsart mit der maximal möglichen zeitlichen Kombination beider Vorgänge akzeptabel. Die maximalen kombinierten Vorgänge unterscheiden sich zum Zeitpunkt der Produktion des letzten Teils (bzw. der letzten Transportcharge) beim Folgevorgang voneinander.
Ein Diagramm der parallel-sequentiellen Bewegungsart ist in Abb. dargestellt. 10.4, V. In diesem Fall ist der Betriebszyklus um den Betrag der Kombination jedes benachbarten Operationspaares kürzer als bei einer sequentiellen Bewegungsart: der erste und zweite Betrieb - AB - (3 - l) T pcs2 ; zweite und dritte Operation - VG = А¢Б¢ – (3 –1) T pcs3 ; dritte und vierte Operation – DE – (3 – 1) T pcs4 (wo T pcs3 und T pcs4 haben eine kürzere Zeit T Stk. Karton aus jedem Operationspaar).
Formeln zur Berechnung
(10.4)
Bei der Durchführung von Operationen an parallelen Arbeitsplätzen:
Reis. 10.4, c. Zeitplan der Produktionszyklen mit paralleler Bewegung von Teilechargen
Beim Umladen von Produkten in Transportchargen:
(10.5)
Wo ist die Zeit, um den kürzesten Vorgang abzuschließen?
Ein Beispiel für die Berechnung der Zyklusdauer mithilfe der Formel (10.5):
T c.p.p = 25,5 – 2 (1 + 1 + 1,5) = 18,5 min.
Der Produktionszyklus zur Herstellung einer Charge von Teilen umfasst nicht nur den Betriebszyklus, sondern auch natürliche Prozesse und Pausen, die mit dem Betriebsmodus und anderen Komponenten verbunden sind. In diesem Fall wird die Zyklusdauer für die betrachteten Bewegungsarten durch die Formeln bestimmt:
Wo R op ist die Anzahl der technologischen Operationen; MIT r.m – die Anzahl der parallelen Arbeitsplätze, die bei der Herstellung einer Charge von Teilen bei jedem Vorgang belegt sind; T mo – interoperative Wartezeit zwischen zwei Operationen, h; T cm – Dauer einer Arbeitsschicht, h; D cm - Anzahl der Schichten; ZU v.n - geplanter Koeffizient der Einhaltung von Standards im Betrieb; ZU ln ist der Koeffizient zur Umrechnung der Arbeitszeit in Kalenderzeit; T e ist die Dauer natürlicher Prozesse.
Berechnung der Zykluszeit eines komplexen Prozesses
Der Produktionszyklus eines Produkts umfasst Zyklen der Herstellung von Teilen, der Montage von Komponenten und Fertigprodukten sowie von Testvorgängen. In diesem Fall wird allgemein davon ausgegangen, dass verschiedene Teile gleichzeitig hergestellt werden. Daher umfasst der Produktionszyklus des Produkts den Zyklus des arbeitsintensivsten (führenden) Teils von denen, die an die ersten Vorgänge der Montagewerkstatt geliefert werden. Die Dauer des Produktproduktionszyklus kann mit der Formel berechnet werden
T c.p = T c.d + T c.b, (10.9)
Wo T c.d - Dauer des Produktionszyklus für die Herstellung des Hauptteils, Kalendertage. Tage; T c.b - Dauer des Produktionszyklus der Montage- und Prüfarbeiten, Kalendertage. Tage
Reis. 10.5. Zyklus eines komplexen Prozesses
Mit einer grafischen Methode kann die Zykluszeit eines komplexen Fertigungsprozesses ermittelt werden. Zu diesem Zweck wird ein zyklischer Zeitplan erstellt. Die Produktionszyklen einfacher Prozesse, die in komplexe Prozesse eingebunden sind, sind vorab festgelegt. Gemäß dem zyklischen Zeitplan wird der Zeitraum des Fortschritts einiger Prozesse durch andere analysiert und die Gesamtdauer des Zyklus eines komplexen Prozesses zur Herstellung eines Produkts oder einer Produktcharge als die größte Summe der Zyklen miteinander verbundener einfacher Prozesse bestimmt und interoperative Pausen. In Abb. Abbildung 10.5 zeigt einen zyklischen Graphen eines komplexen Prozesses. In der Grafik sind von rechts nach links im Zeitmaßstab Zyklen von Teilprozessen aufgetragen, beginnend mit der Prüfung bis hin zur Fertigung der Teile.
Möglichkeiten und Bedeutung zur Gewährleistung der Kontinuität des Produktionsprozesses und zur Reduzierung der Zykluszeiten
Ein hohes Maß an Kontinuität der Produktionsprozesse und eine Verkürzung der Produktionszyklusdauer sind von großer wirtschaftlicher Bedeutung: Der Umfang der laufenden Arbeiten wird reduziert und der Umsatz beschleunigt Betriebskapital, die Nutzung von Ausrüstung und Produktionsraum wird verbessert und die Produktionskosten werden gesenkt. Untersuchungen, die in einer Reihe von Unternehmen in Charkow durchgeführt wurden, zeigten, dass dort, wo die durchschnittliche Produktionszykluszeit 18 Tage nicht überschreitet, jeder ausgegebene Rubel 12 % mehr Produkte liefert als in Fabriken, in denen die Zykluszeit 19–36 Tage beträgt, und 61 % mehr als in einer Fabrik, in der die Produkte einen Zyklus von mehr als 36 Tagen haben.
Die Erhöhung der Kontinuität des Produktionsprozesses und die Verkürzung der Zykluszeit werden zum einen durch die Erhöhung des technischen Niveaus der Produktion und zum anderen durch organisatorische Maßnahmen erreicht. Beide Wege sind miteinander verbunden und ergänzen sich.
Die technische Verbesserung der Produktion geht in Richtung Umsetzung neue Technologie, fortschrittliche Ausstattung und neu Fahrzeug. Dies führt zu einer Verkürzung des Produktionszyklus, indem die Arbeitsintensität der Technologie- und Kontrollvorgänge selbst verringert und die Zeit für den Transport von Arbeitsgegenständen verkürzt wird.
Zu den organisatorischen Maßnahmen gehören:
- Minimierung von Unterbrechungen, die durch Interoperationsverfolgung und Batch-Unterbrechungen verursacht werden, durch den Einsatz paralleler und parallel-sequentieller Methoden der Bewegung von Arbeitsgegenständen und Verbesserung des Planungssystems;
- Erstellen von Zeitplänen für die Kombination verschiedener Produktionsprozesse, um eine teilweise zeitliche Überschneidung der damit verbundenen Arbeiten und Vorgänge sicherzustellen;
- Reduzierung der Wartepausen durch die Erstellung optimierter Produktionspläne für Produkte und die rationelle Einführung von Teilen in die Produktion;
- die Einführung von themen- und detailspezialisierten Werkstätten und Abteilungen, deren Schaffung die Länge der Intra-Shop- und Inter-Shop-Wege verkürzt und den Zeitaufwand für den Transport reduziert.
Konzept des Produktionsprozesses. Die moderne Produktion ist ein komplexer Prozess der Umwandlung von Rohstoffen, Materialien, Halbfabrikaten und anderen Arbeitsgegenständen in fertige Produkte, die den Bedürfnissen der Gesellschaft entsprechen.
Als Gesamtheit aller in einem Unternehmen durchgeführten Handlungen von Menschen und Werkzeugen zur Herstellung bestimmter Produktarten wird bezeichnet Fertigungsprozess.
Der Hauptteil des Produktionsprozesses sind technologische Prozesse, die gezielte Maßnahmen zur Veränderung und Bestimmung des Zustands von Arbeitsgegenständen beinhalten. Bei der Umsetzung technologischer Prozesse kommt es zu Veränderungen der geometrischen Formen, Größen sowie der physikalischen und chemischen Eigenschaften von Arbeitsgegenständen.
Verschiedene Produktionsprozesse.
Entsprechend ihrem Zweck und ihrer Rolle in der Produktion werden Prozesse in Haupt-, Hilfs- und Wartungsanlagen sowie Nebenanlagen unterteilt.
Hauptsächlich werden Produktionsprozesse genannt, bei denen die Herstellung der vom Unternehmen hergestellten Hauptprodukte erfolgt. Beispielsweise sind Wärmekraftwerke die Hauptproduktionsstätte, da sie Brennstoffenergie in thermische und elektrische Energie umwandeln.
Die Pünktlichkeit und qualitativ hochwertige Ausführung der Hauptproduktion hängt maßgeblich davon ab, wie die Arbeit der Hilfs- und Dienstleistungsproduktion organisiert ist, der die Aufgabe untergeordnet ist, die Hauptproduktionsbetriebe besser mit Materialien, Geräten etc. zu versorgen.
Unter modernen Bedingungen, insbesondere in der automatisierten Produktion, ist dies der Fall Trend zur Integration Haupt- und Serviceprozesse. So werden in flexiblen automatisierten Komplexen Grund-, Kommissionierungs-, Lager- und Transportvorgänge in einem einzigen Prozess zusammengefasst.
Die Gesamtheit der Grundprozesse bildet die Hauptproduktion.
Hilfsproduktionsunternehmen sind Unternehmen, die zwar nicht in direktem Zusammenhang mit der Herstellung des Hauptprodukts stehen, aber den Normalbetrieb der Hauptproduktion bedienen und Voraussetzungen dafür schaffen. Zu den Hilfsproduktionsunternehmen zählen Unternehmen, die Produkte herstellen, die von der Hauptproduktion verbraucht werden, und dadurch zur Produktion von Endprodukten beitragen und den normalen Betrieb der Hauptproduktion sicherstellen. Im Energiesektor umfasst die Hilfsproduktion Reparaturunternehmen sowie Unternehmen, die nicht standardmäßige Geräte und Ersatzteile für Energiegeräte herstellen.
Dienstleistungsunternehmen sind für die Betreuung von Haupt- und Nebenunternehmen organisiert. Der Dist ein Arbeitsprozess, bei dem keine Produkte entstehen. Zu den Dienstleistungsunternehmen zählen Unternehmen, die sich mit der Lieferung von Materialien und Ersatzteilen befassen, Labore, Design- und Forschungsinstitute, Transportunternehmen usw.
In jüngster Zeit taucht im Energiesektor das Konzept der „Dienstleistungsunternehmen“ auf, das sowohl Hilfs- als auch Dienstleistungsunternehmen vereint. Es wird vorgeschlagen, Unternehmen, die Dienstleistungen für die Reparatur, Installation, Anpassung und Modernisierung von Industrieanlagen und technologischen Netzwerken erbringen (z. B. Reparaturbetriebe, Anlagenbaubetriebe, Kraftverkehrsunternehmen usw.), in die Dienstleistungsgruppe einzubeziehen.
Zu den Nicht-Kernunternehmen zählen landwirtschaftliche Betriebe, deren Produkte und Dienstleistungen nicht zu den Hauptaktivitäten des Unternehmens gehören. Zu ihren Aufgaben gehört die Befriedigung der Haushaltsbedürfnisse des Personals des Unternehmens (Unterkünfte, Kindergärten, Sanatorien, Nebenlandwirtschaft usw.).
Wissenschaftliche Prinzipien der Organisation von Produktionsprozessen.
Die Organisation von Produktionsprozessen besteht darin, Menschen, Werkzeuge und Arbeitsgegenstände zu einem einzigen Prozess zur Herstellung materieller Güter zusammenzufassen und eine rationelle räumliche und zeitliche Verknüpfung von Grund-, Hilfs- und Dienstleistungsprozessen sicherzustellen.
Die räumliche Kombination von Elementen des Produktionsprozesses und all seiner Spielarten erfolgt auf der Grundlage der Gestaltung der Produktionsstruktur des Unternehmens und seiner Unternehmensbereiche. In diesem Zusammenhang sind die wichtigsten Aktivitäten die Auswahl und Begründung der Produktionsstruktur des Unternehmens, d.h. Bestimmung der Zusammensetzung und Spezialisierung seiner konstituierenden Einheiten und Herstellung rationaler Beziehungen zwischen ihnen.
Während der Entwicklung Produktionsstruktur werden Konstruktionsberechnungen im Zusammenhang mit der Bestimmung der Zusammensetzung des Geräteparks unter Berücksichtigung seiner Produktivität, Austauschbarkeit und der Möglichkeit einer effektiven Nutzung durchgeführt. Es werden auch rationelle Anordnungen der Abteilungen, der Platzierung von Geräten und Arbeitsplätzen entwickelt. Es werden organisatorische Voraussetzungen für den unterbrechungsfreien Betrieb der Geräte und der direkten Teilnehmer am Produktionsprozess – der Arbeiter – geschaffen
Einer der Hauptaspekte bei der Bildung einer Produktionsstruktur besteht darin, das vernetzte Funktionieren aller Komponenten des Produktionsprozesses sicherzustellen: Vorbereitungsvorgänge, Hauptproduktionsprozesse und Wartung. Es ist notwendig, die rationalsten Organisationsformen und Methoden zur Durchführung bestimmter Prozesse für spezifische Produktions- und technische Bedingungen umfassend zu begründen.
Ein wichtiges Element der Organisation Produktionsprozesse - die Arbeitsorganisation der Arbeiter, insbesondere die Verwirklichung des Zusammenhangs der Arbeit mit den Produktionsmitteln. Die Methoden der Arbeitsorganisation werden maßgeblich durch die Formen des Produktionsprozesses bestimmt. Dabei liegt der Schwerpunkt auf der Sicherstellung einer rationellen Arbeitsteilung und der darauf basierenden Festlegung der beruflichen und Qualifikationszusammensetzung der Arbeitnehmer, der wissenschaftlichen Gestaltung und optimalen Instandhaltung der Arbeitsplätze sowie der umfassenden Verbesserung und Verbesserung der Arbeitsbedingungen.
Die Organisation von Produktionsprozessen setzt auch eine zeitliche Kombination ihrer Elemente voraus, die eine bestimmte Reihenfolge der Durchführung einzelner Vorgänge, eine rationelle Kombination der Zeit für die Durchführung verschiedener Arten von Arbeiten und die Festlegung kalendergeplanter Standards für die Bewegung von Arbeiten bestimmt Gegenstände der Arbeit. Der normale zeitliche Ablauf der Prozesse wird auch durch die Reihenfolge der Produkteinführung und -freigabe, die Bildung der notwendigen Bestände (Reserven) und Produktionsreserven sowie die unterbrechungsfreie Versorgung der Arbeitsplätze mit Werkzeugen, Werkstücken und Materialien sichergestellt. Ein wichtiger Bereich dieser Tätigkeit ist die Organisation der rationellen Bewegung von Materialflüssen. Die Lösung dieser Aufgaben erfolgt auf der Grundlage der Entwicklung und Implementierung betrieblicher Produktionsplanungssysteme unter Berücksichtigung der Art der Produktion sowie technischer und organisatorischer Besonderheiten der Produktionsprozesse.
Schließlich kommt bei der Organisation von Produktionsprozessen in einem Unternehmen der Entwicklung eines Systems der Interaktion zwischen einzelnen Produktionseinheiten ein wichtiger Stellenwert zu.
Grundsätze der Organisation des Produktionsprozesses stellen die Ausgangspunkte dar, auf deren Grundlage Aufbau, Betrieb und Entwicklung von Produktionsprozessen erfolgen.
Prinzip Differenzierung Dabei geht es darum, den Produktionsprozess in einzelne Teile (Prozesse, Vorgänge) zu unterteilen und diese den entsprechenden Abteilungen des Unternehmens zuzuordnen. Dem Prinzip der Differenzierung steht das Prinzip gegenüber Kombinationen, Dies bedeutet die Vereinheitlichung aller oder eines Teils verschiedener Prozesse zur Herstellung bestimmter Produkttypen an einem Standort, einer Werkstatt oder einer Produktion.
Abhängig von der Komplexität des Produkts, dem Produktionsvolumen und der Art der verwendeten Ausrüstung kann der Produktionsprozess in einer Produktionseinheit (Werkstatt, Bereich) konzentriert oder auf mehrere Einheiten verteilt sein. So werden beispielsweise in Maschinenbauunternehmen mit einer bedeutenden Produktion ähnlicher Produkte eigenständige mechanische und Montagefertigungen und -werkstätten organisiert und für kleine Produktserien können einheitliche mechanische Montagehallen geschaffen werden.
Die Grundsätze der Differenzierung und Kombination gelten auch für einzelne Arbeitsplätze. Eine Produktionslinie beispielsweise besteht aus einer differenzierten Reihe von Arbeitsplätzen.
In der Praxis Bei der Organisation der Produktion sollte bei der Anwendung der Prinzipien der Differenzierung oder Kombination dem Prinzip Vorrang eingeräumt werden, das die besten wirtschaftlichen und sozialen Merkmale des Produktionsprozesses gewährleistet. Somit ermöglicht die Fließproduktion, die sich durch einen hohen Differenzierungsgrad des Produktionsprozesses auszeichnet, eine Vereinfachung seiner Organisation, eine Verbesserung der Fähigkeiten der Arbeitnehmer und eine Steigerung der Arbeitsproduktivität. Eine übermäßige Differenzierung erhöht jedoch die Ermüdung der Arbeiter, eine große Anzahl von Vorgängen erhöht den Bedarf an Ausrüstung und Produktionsraum, führt zu unnötigen Kosten für bewegliche Teile usw.
Prinzip Konzentrationen bedeutet Konzentration bestimmter Produktionsbetriebe zur Herstellung technologisch homogener Produkte oder zur Erbringung funktional homogener Arbeiten an einzelnen Arbeitsplätzen, Bereichen, Werkstätten oder Produktionsstätten des Unternehmens. Die Möglichkeit, ähnliche Arbeiten in getrennten Produktionsbereichen zu konzentrieren, wird durch folgende Faktoren bestimmt: die Gemeinsamkeit technologischer Methoden, die den Einsatz derselben Art von Ausrüstung erfordern; Fähigkeiten von Geräten, wie z. B. Bearbeitungszentren; Erhöhung des Produktionsvolumens bestimmter Produkttypen; die wirtschaftliche Machbarkeit der Konzentration der Produktion bestimmter Produkttypen oder der Durchführung ähnlicher Arbeiten.
Bei der Wahl der einen oder anderen Konzentrationsrichtung müssen die Vorteile jeder einzelnen davon berücksichtigt werden.
Durch die Konzentration technologisch homogener Arbeiten in einer Abteilung wird weniger Duplikat-Equipment benötigt, die Produktionsflexibilität erhöht sich, eine schnelle Umstellung auf die Produktion neuer Produkte wird möglich und die Anlagenauslastung steigt.
Durch die Konzentration technologisch homogener Produkte werden die Kosten für den Material- und Produkttransport gesenkt, die Dauer des Produktionszyklus verkürzt, das Produktionsmanagement vereinfacht und der Bedarf an Produktionsfläche reduziert.
Prinzip Spezialisierungen basierend auf die Begrenzung der Vielfalt der Elemente des Produktionsprozesses. Die Umsetzung dieses Prinzips besteht darin, jedem Arbeitsplatz und jeder Abteilung ein streng begrenztes Spektrum an Arbeiten, Vorgängen, Teilen oder Produkten zuzuordnen. Im Gegensatz zum Spezialisierungsprinzip geht das Universalisierungsprinzip von einer Produktionsorganisation aus, bei der jeder Arbeitsplatz bzw. jede Produktionseinheit mit der Herstellung von Teilen und Produkten verschiedenster Art oder der Durchführung heterogener Produktionsvorgänge beschäftigt ist.
Der Spezialisierungsgrad der Arbeitsplätze wird durch einen speziellen Indikator bestimmt – den BetrZu z.o, die durch die Anzahl der über einen bestimmten Zeitraum am Arbeitsplatz durchgeführten Detailoperationen gekennzeichnet ist. Ja, wenn K z.o= 1 Es gibt eine enge Spezialisierung von Arbeitsplätzen, bei der während eines Monats oder Quartals eine Detailoperation am Arbeitsplatz durchgeführt wird.
Die Art der Spezialisierung von Abteilungen und Stellen wird maßgeblich durch das Produktionsvolumen gleichnamiger Teile bestimmt. Die Spezialisierung erreicht ihren höchsten Grad bei der Herstellung eines Produkttyps. Das typischste Beispiel für hochspezialisierte Industrien sind Fabriken zur Herstellung von Traktoren, Fernsehern und Autos. Durch die Vergrößerung des Produktionsspektrums verringert sich der Spezialisierungsgrad.
Ein hoher Spezialisierungsgrad von Abteilungen und Arbeitsplätzen trägt zur Steigerung der Arbeitsproduktivität aufgrund der Entwicklung der Arbeitsfähigkeiten der Arbeitnehmer, der Möglichkeit der technischen Ausstattung der Arbeitskräfte und der Minimierung der Kosten für die Neukonfiguration von Maschinen und Linien bei. Gleichzeitig verringert eine enge Spezialisierung die erforderlichen Qualifikationen der Arbeitnehmer, führt zu Monotonie der Arbeit und führt dadurch zu einer schnellen Ermüdung der Arbeitnehmer und schränkt ihre Initiative ein.
Unter modernen Bedingungen gibt es eine zunehmende Tendenz zur Universalisierung der Produktion, die durch die Anforderungen des wissenschaftlichen und technischen Fortschritts zur Erweiterung der Produktpalette, das Aufkommen multifunktionaler Geräte und die Aufgaben der Verbesserung der Arbeitsorganisation in der Produktion bestimmt wird Richtung der Erweiterung der Arbeitsfunktionen des Arbeitnehmers.
Prinzip Verhältnismäßigkeit Ist in einer natürlichen Kombination einzelner Elemente des Produktionsprozesses, die sich in einem bestimmten quantitativen Verhältnis zwischen ihnen ausdrückt. Proportionalität der Produktionskapazität setzt also die Gleichheit der Standortkapazitäten oder der Ausrüstungsauslastungsfaktoren voraus. Dabei entspricht der Durchsatz der Beschaffungswerkstätten dem Rohlingsbedarf der mechanischen Werkstätten und der Durchsatz dieser Werkstätten dem Bedarf der Montagewerkstatt an den benötigten Teilen. Dies beinhaltet die Anforderung, in jeder Werkstatt über Ausrüstung, Platz und Arbeitskräfte in solchen Mengen zu verfügen, dass der normale Betrieb aller Abteilungen des Unternehmens gewährleistet ist. Zwischen der Hauptproduktion einerseits und den Hilfs- und Serviceeinheiten andererseits sollte das gleiche Durchsatzverhältnis bestehen.
Ein Verstoß gegen den Grundsatz der Verhältnismäßigkeit führt zu Ungleichgewichten, zur Entstehung von Produktionsengpässen, wodurch sich der Einsatz von Ausrüstung und Arbeitskräften verschlechtert, die Dauer des Produktionszyklus zunimmt und Rückstände zunehmen.
Verhältnismäßigkeit in der Belegschaft, Flächen, Geräte werden bereits bei der Planung des Unternehmens installiert und dann bei der Entwicklung jährlicher Produktionspläne durch sogenannte volumetrische Berechnungen spezifiziert – bei der Ermittlung der Kapazität, der Mitarbeiterzahl und des Materialbedarfs. Proportionen werden auf der Grundlage eines Systems von Standards und Normen festgelegt, die die Anzahl der gegenseitigen Verbindungen zwischen verschiedenen Elementen des Produktionsprozesses bestimmen.
Der Grundsatz der Verhältnismäßigkeit beinhaltet die gleichzeitige Durchführung einzelner Vorgänge oder Teile des Produktionsprozesses. Ihr liegt die These zugrunde, dass Teile eines zerlegten Produktionsprozesses zeitlich zusammengeführt und gleichzeitig durchgeführt werden müssen.
Organisation von Produktionsabläufen im Zeitverlauf.
Um ein rationelles Zusammenspiel aller Elemente des Produktionsprozesses zu gewährleisten und die geleistete Arbeit zeitlich und räumlich zu rationalisieren, ist es notwendig, einen Produktionszyklus des Produkts zu bilden.
Der Produktionszyklus wird aufgerufen ein Komplex von Grund-, Hilfs- und Serviceprozessen, die zeitlich auf eine bestimmte Weise organisiert sind und für die Herstellung eines bestimmten Produkttyps erforderlich sind. Das wichtigste Merkmal des Produktionszyklus ist seine Dauer.
Dauer des Produktionszyklus - Das der kalendarische Zeitraum, in dem ein Material, ein Werkstück oder ein sonstiger verarbeiteter Gegenstand alle Vorgänge des Produktionsprozesses oder einen bestimmten Teil davon durchläuft und in ein fertiges Produkt umgewandelt wird. Die Dauer des Zyklus wird in Kalendertagen oder Stunden ausgedrückt.
Struktur des Produktionszyklus beinhaltet Arbeitszeit und Pausenzeit. Während der Arbeitszeit werden die eigentlichen technologischen Arbeiten sowie Vor- und Abschlussarbeiten durchgeführt. Zur Arbeitszeit gehören auch die Dauer von Kontroll- und Transportvorgängen sowie die Zeit natürlicher Prozesse (einschließlich der Zeit arbeitsplanbedingter Pausen).
In seiner allgemeinsten Form die Dauer des Produktionszyklus T c ausgedrückt durch die Formel:
T a = T t + T n -3 + T e + T k + T Tr + T mo + T Pr,
wobei T t die Zeit der technologischen Operationen ist; T n -3- Zeit der Vor- und Abschlussarbeiten; T e - Zeit natürlicher Prozesse; T k - Zeitpunkt der Kontrolloperationen; T Tr- Zeitpunkt des Transports von Arbeitsgegenständen; T mo- betriebsübergreifende Schlafenszeit (interschichtige Pausen); T Pr,- Zeit der Pausen aufgrund des Arbeitsplans.
Die Dauer der technologischen Vorgänge sowie der vorbereitenden und abschließenden Arbeiten bildet zusammen den Betriebszyklus T c.op.
Betriebszyklus- Dies ist die Dauer des abgeschlossenen Teils des technologischen Prozesses, der an einem Arbeitsplatz durchgeführt wird.
ARTEN, FORMEN UND METHODEN DER PRODUKTIONSORGANISATION
Produktionsarten und ihre technischen und wirtschaftlichen Merkmale.
Die Art der Produktion wird durch eine umfassende Beschreibung der technischen, organisatorischen und wirtschaftlichen Merkmale der Produktion bestimmt, bestimmt durch die Breite der Produktpalette, Regelmäßigkeit, Stabilität und Produktionsmenge. Der Hauptindikator, der die Art der Produktion charakterisiert, ist der BeK z.
Der Befür eine Gruppe von Arbeitsplätzen ist definiert als das Verhältnis der Anzahl aller verschiedenen technologischen Vorgänge, die im Laufe des Monats durchgeführt wurden oder durchgeführt werden sollen, zur Anzahl der Arbeitsplätze:
K op i - Anzahl der durchgeführten Operationen ich-ter Arbeitsplatz; Zu r.m— die Anzahl der Arbeitsplätze auf der Baustelle oder in der Werkstatt.
Es gibt drei Arten der Produktion: Einzel-, Serien- und Massenproduktion.
Einzelanfertigung gekennzeichnet durch eine geringe Produktionsmenge identischer Produkte, deren Nachfertigung und Reparatur in der Regel nicht vorgesehen ist. Der Konsolidierungsfaktor für die Stückproduktion liegt in der Regel über 40.
Massenproduktion gekennzeichnet durch die Herstellung oder Reparatur von Produkten in sich periodisch wiederholenden Chargen. Abhängig von der Anzahl der Produkte in einer Charge oder Serie und dem Wert des Betrwerden Klein-, Mittel- und Großserienfertigung unterschieden.
Für die Produktion im kleinen Maßstab beträgt der Betriebskonsolidierungsfaktor 21 bis 40 (einschließlich), für die Produktion im mittleren Maßstab: 11 bis 20 (einschließlich), für die Produktion im großen Maßstab: 1 bis 10 (einschließlich).
Massenproduktion gekennzeichnet ein großes Produktionsvolumen von Produkten, die über einen längeren Zeitraum kontinuierlich hergestellt oder repariert werden, wobei an den meisten Arbeitsplätzen ein Arbeitsvorgang durchgeführt wird. Der Befür die Massenproduktion wird mit 1 angenommen.
Betrachten wir die technischen und wirtschaftlichen Merkmale jeder Produktionsart.
Die Einzel- und ähnliche Kleinserienfertigung zeichnet sich durch die Fertigung von Teilen eines großen Sortiments an Arbeitsplätzen ohne besondere Spezialisierung aus. Diese Produktion muss ausreichend flexibel und angepasst sein, um verschiedene Produktionsaufträge erfüllen zu können.
Technologische Prozesse unter Bedingungen der Einzelproduktion werden sie in Form von Streckenkarten zur Bearbeitung von Teilen für jeden Auftrag erweitert entwickelt; Die Standorte sind mit universellen Geräten und Vorrichtungen ausgestattet, die die Produktion von Teilen einer breiten Palette gewährleisten. Die Vielfalt der Tätigkeiten, die viele Arbeitnehmer ausüben müssen, erfordert unterschiedliche berufliche Fähigkeiten, weshalb im Betrieb hochqualifizierte Generalisten eingesetzt werden. In vielen Bereichen, insbesondere in der Pilotfertigung, wird die Berufszusammenlegung praktiziert.
Organisation der Produktion unter Bedingungen der Einzelproduktion hat seine eigenen Eigenschaften. Aufgrund der Vielfalt der Teile, der Reihenfolge und der Art ihrer Bearbeitung werden Produktionsbereiche nach einem technologischen Prinzip mit in homogenen Gruppen angeordneten Geräten aufgebaut. Bei dieser Produktionsorganisation durchlaufen Teile während des Herstellungsprozesses verschiedene Abschnitte.
Daher ist es bei der Übertragung auf jeden nachfolgenden Vorgang (Abschnitt) erforderlich, die Fragen der Qualitätskontrolle der Verarbeitung, des Transports und der Festlegung von Arbeitsplätzen für die Durchführung des nächsten Vorgangs sorgfältig zu berücksichtigen. Zu den Merkmalen der Betriebsplanung und -steuerung gehören die rechtzeitige Fertigstellung und Erfüllung von Aufträgen, die Überwachung des Fortschritts jedes Teils durch den Betrieb und die Sicherstellung der systematischen Auslastung von Bereichen und Arbeitsplätzen. Bei der Organisation der Logistik treten große Schwierigkeiten auf.
Merkmale der Organisation Die Stückproduktion wirkt sich auf die Wirtschaftsindikatoren aus. Unternehmen, in denen eine einzige Produktionsart vorherrscht, zeichnen sich durch eine relativ hohe Arbeitsintensität der Produkte und ein großes Volumen an unfertigen Arbeiten aufgrund der langen Lagerung von Teilen zwischen den Vorgängen aus. Die Kostenstruktur von Produkten ist durch einen hohen Lohnkostenanteil gekennzeichnet. Dieser Anteil beträgt in der Regel 20 – 25 %.
Die wesentlichen Chancen zur Verbesserung der technischen und wirtschaftlichen Kennzahlen der Einzelproduktion liegen in der technischen und organisatorischen Annäherung an die Serienproduktion. Der Einsatz von Serienproduktionsmethoden ist möglich, indem das Spektrum der hergestellten Teile für allgemeine Maschinenbauanwendungen eingeengt wird, Teile und Baugruppen vereinheitlicht werden, was uns ermöglicht, zur Organisation von Themenbereichen überzugehen; Ausbau der konstruktiven Kontinuität, um die Stückzahlen der Teile zu erhöhen; Gruppieren von Teilen, die in Design und Fertigungsreihenfolge ähnlich sind, um die Zeit für die Produktionsvorbereitung zu verkürzen und die Nutzung der Ausrüstung zu verbessern.
Massenproduktion gekennzeichnet durch die Produktion einer begrenzten Anzahl von Teilen in Chargen, die in bestimmten Abständen wiederholt werden. Dies ermöglicht die Verwendung zusammen mit dem Universalgerät Spezialausrüstung. Bei der Gestaltung technologischer Prozesse werden die Ausführungsreihenfolge und die Ausrüstung jedes Vorgangs festgelegt.
Die folgenden Merkmale sind charakteristisch für die Organisation der Serienproduktion: Werkstätten enthalten in der Regel geschlossene Bereiche, in denen Geräte im Rahmen eines standardmäßigen technologischen Prozesses platziert werden. Dadurch entstehen relativ einfache Verbindungen zwischen Arbeitsplätzen und die Voraussetzungen für die Organisation der direkten Bewegung von Teilen während ihres Herstellungsprozesses.
Serienproduktionsunternehmen zeichnen sich durch eine deutlich geringere Arbeitsintensität und Herstellungskosten von Produkten aus als Einzelunternehmen. Bei der Massenfertigung erfolgt die Bearbeitung der Produkte im Vergleich zur Einzelfertigung mit weniger Unterbrechungen, was den Umfang der laufenden Arbeiten reduziert.
Massenproduktion ist anders die größte Spezialisierung und zeichnet sich durch die Produktion eines begrenzten Teilespektrums in großen Stückzahlen aus. Massenproduktionswerkstätten sind mit modernster Ausrüstung ausgestattet, was eine nahezu vollständige Automatisierung der Teileproduktion ermöglicht. Automatische Produktionslinien haben sich hier durchgesetzt. Unter Bedingungen der Massenproduktion nimmt die Bedeutung der Organisation des zwischenbetrieblichen Transports und der Instandhaltung von Arbeitsplätzen zu.
Die ständige Überwachung des Zustands von Schneidwerkzeugen, -geräten und -geräten ist eine der Voraussetzungen für die Kontinuität des Produktionsprozesses, ohne die der Arbeitsrhythmus auf Baustellen und in Werkstätten unweigerlich gestört wird. Die Notwendigkeit, auf allen Produktionsebenen einen vorgegebenen Rhythmus einzuhalten, wird zu einem charakteristischen Merkmal der Organisation von Prozessen in der Massenproduktion.
Die Massenproduktion gewährleistet eine möglichst vollständige Nutzung der Ausrüstung, ein hohes Gesamtniveau der Arbeitsproduktivität und die niedrigsten Herstellungskosten der Produkte. In der Tabelle 1 präsentiert Daten zu Vergleichsmerkmale verschiedene Arten Produktion.
Organisationsformen der Produktion.
Die Organisationsform der Produktion ist eine bestimmte zeitliche und räumliche Kombination von Elementen des Produktionsprozesses mit einem angemessenen Grad ihrer Integration, ausgedrückt durch ein System stabiler Verbindungen.
Verschiedene zeitliche und räumliche Strukturstrukturen bilden eine Reihe grundlegender Formen der Produktionsorganisation.
Temporäre Struktur der Organisation Die Produktion wird durch die Zusammensetzung der Elemente des Produktionsprozesses und die Reihenfolge ihres Zusammenwirkens im Zeitverlauf bestimmt. Je nach Art der temporären Struktur werden Organisationsformen mit sequentiellem, parallelem und parallel-sequentiellem Transfer von Arbeitsgegenständen in der Produktion unterschieden.
Die Organisationsform der Produktion mit sequentiellem Transfer von Arbeitsgegenständen ist eine Kombination von Elementen des Produktionsprozesses, die den Transport verarbeiteter Produkte über alle Produktionsbereiche in Chargen beliebiger Größe gewährleistet. Dieses Formular ist am flexibelsten in Bezug auf Änderungen, die im Produktionsprogramm auftreten.
Tabelle 1.
Vergleichbare Eigenschaften | Art der Produktion | ||
Einzel | Seriell | Masse | |
Nomenklatur und Produktionsvolumen Wiederholbarkeit der Produktion Verwendete Ausrüstung Zuordnung von Arbeitsgängen zu Maschinen Standort der Ausrüstung Übertragung von Arbeitsgegenständen von Betrieb zu Betrieb Organisationsform des Produktionsprozesses | Unbegrenzte Auswahl an auf Bestellung gefertigten Teilen. Abwesend. Universell. Abwesend. Durch Gruppen ähnlicher Maschinen. Sequentielle Technologie | Breites Spektrum an in Chargen hergestellten Teilen. Periodisch Universell, teilweise speziell. Es wird eine begrenzte Anzahl von Detailoperationen eingerichtet. In Gruppen wird für die Verarbeitung von strukturell und technologisch homogenen Teilen parallel-sequentielles Subjekt, Gruppe, flexibles Subjekt eingerichtet | Begrenztes Teilespektrum, das in großen Mengen hergestellt wird. Konstant Meist speziell. Ein oder zwei Arbeitsgänge pro Maschine. Entlang des technologischen Prozesses der Bearbeitung von Teilen. Parallel. Gerade |
Vergleichende Eigenschaften verschiedener Produktionsarten ermöglichen eine vollständige Ausnutzung der Ausrüstung, wodurch die Anschaffungskosten gesenkt werden können. Der Nachteil dieser Form der Produktionsorganisation ist die relativ lange Dauer des Produktionszyklus, da jedes Teil auf die Verarbeitung der gesamten Charge wartet, bevor es den nächsten Arbeitsgang durchführt.
Form der Produktionsorganisation mit paralleler Übertragung von Arbeitsgegenständen basiert auf einer solchen Kombination von Elementen des Produktionsprozesses, die es Ihnen ermöglicht, Arbeitsgegenstände einzeln und ohne Wartezeit von Betrieb zu Betrieb zu starten, zu verarbeiten und zu übertragen. Diese Organisation des Produktionsprozesses führt zu einer Reduzierung der Anzahl der zu bearbeitenden Teile und damit zu einem geringeren Platzbedarf für Lager und Gänge. Sein Nachteil ist mögliche Ausfallzeit Geräte (Arbeitsplätze) aufgrund von Unterschieden in der Betriebsdauer.
Die Organisationsform der Produktion mit parallel-sequentiellem Transfer von Arbeitsgegenständen liegt zwischen sequentiellen und parallelen Formen und beseitigt deren inhärente Nachteile teilweise. Produkte werden in Transportchargen von Betrieb zu Betrieb transportiert. Gleichzeitig wird die Kontinuität des Geräte- und Arbeitseinsatzes gewährleistet und ein teilweise paralleler Durchlauf einer Teilecharge durch technologische Prozessabläufe ermöglicht.
Raumstruktur Die Organisation der Produktion wird durch die Anzahl der auf dem Arbeitsplatz konzentrierten technologischen Ausrüstung (Anzahl der Arbeitsplätze) und ihre Lage relativ zur Bewegungsrichtung der Arbeitsgegenstände im umgebenden Raum bestimmt.
Abhängig von der Anzahl der technologischen Geräte (Arbeitsplätze) wird zwischen einem eingliedrigen Produktionssystem und der entsprechenden Struktur eines separaten Arbeitsplatzes und einem mehrgliedrigen System mit Werkstatt-, Linien- oder Zellenstruktur unterschieden. Möglichkeiten Die räumliche Struktur der Produktionsorganisation ist in Abb. dargestellt. 5.
Geschäft Struktur gekennzeichnet ist die Schaffung von Bereichen, in denen Geräte (Arbeitsplätze) parallel zum Werkstückfluss angeordnet sind, was deren Spezialisierung auf der Grundlage technologischer Homogenität voraussetzt. Dabei wird eine am Standort ankommende Teilecharge an einen der freien Arbeitsplätze geschickt, wo sie den notwendigen Bearbeitungszyklus durchläuft und anschließend an einen anderen Standort (in die Werkstatt) überführt wird.
Reis. 5. Optionen für die räumliche Struktur des Produktionsprozesses
Auf der Website mit linear räumliche Struktur, Geräte (Arbeitsplätze) befinden sich entlang des technologischen Prozesses und eine Charge der am Standort bearbeiteten Teile wird sequentiell von einem Arbeitsplatz zum anderen transportiert.
Mobilfunk Die Struktur der Produktionsorganisation vereint die Merkmale von Linear und Werkstatt.
Die Kombination räumlicher und zeitlicher Strukturen des Produktionsprozesses mit einem gewissen Grad an Integration von Teilprozessen bestimmt verschiedene Organisationsformen der Produktion: technologisch, subjektiv, direkt, punktuell, integriert (Abb. 6). Schauen wir uns die charakteristischen Merkmale jedes einzelnen von ihnen an.
Reis. 6. Organisationsformen der Produktion
Technologisch Die Organisationsform des Produktionsprozesses ist durch eine Werkstattstruktur mit sequentieller Übergabe von Arbeitsgegenständen gekennzeichnet. Diese Organisationsform ist im Maschinenbau weit verbreitet, da sie in der Kleinserienfertigung eine maximale Anlagenauslastung gewährleistet und an häufige Veränderungen im technologischen Prozess angepasst ist.
Gleichzeitig Anwendung Es gibt viele technologische Formen der Organisation des Produktionsprozesses negative Konsequenzen: Eine große Anzahl von Teilen und deren wiederholte Bewegung während der Verarbeitung führen zu einer Erhöhung des Arbeitsvolumens und einer Erhöhung der Anzahl der Zwischenlagerplätze. Ein erheblicher Teil des Produktionszyklus besteht aus Zeitverlusten, die durch komplexe Kommunikation zwischen den Standorten verursacht werden.
Die Subjektform der Produktionsorganisation weist eine zelluläre Struktur mit parallel-sequentiellem (sequentiellem) Transfer von Arbeitsgegenständen in der Produktion auf. In der Regel sind am Fachgebiet alle für die Bearbeitung einer Teilegruppe vom Anfang bis zum Ende des technologischen Prozesses notwendigen Geräte installiert. Ist der verarbeitungstechnologische Kreislauf innerhalb der Site geschlossen, spricht man von subjektgeschlossen.
Im Vergleich zur technologischen Form Mit diesem Thema können Sie die Gesamtkosten für den Transport von Teilen und den Bedarf an Produktionsfläche pro Produktionseinheit reduzieren. Gleichzeitig diese Form Die Organisation der Produktion bei der Festlegung der Zusammensetzung der am Standort installierten Geräte stellt die Notwendigkeit in den Vordergrund, bestimmte Arten der Teilebearbeitung durchzuführen, was nicht immer eine vollständige Auslastung der Geräte gewährleistet. Darüber hinaus erfordern die Erweiterung und Aktualisierung der Produktpalette eine regelmäßige Neugestaltung der Produktionsbereiche und Änderungen in der Struktur des Geräteparks.
Direkter Fluss Form der Organisation Produktion gekennzeichnet ist lineare Struktur mit stückweiser Übergabe von Arbeitsgegenständen. Diese Form gewährleistet die Umsetzung einer Reihe von Organisationsprinzipien: Spezialisierung, Direktheit, Kontinuität, Parallelität. Sein Einsatz führt zu einer Verkürzung der Dauer des Produktionszyklus, einem effizienteren Arbeitseinsatz aufgrund einer stärkeren Spezialisierung der Arbeitskräfte und einer Verringerung des Arbeitsvolumens.
Bei Punkt bilden Produktionsorganisation, die Arbeit wird vollständig an einem Arbeitsplatz ausgeführt. Das Produkt wird dort hergestellt, wo sich sein Hauptbestandteil befindet. Ein Beispiel ist die Montage eines Produkts, bei der sich ein Arbeiter darum bewegt. Die Organisation der Punktproduktion hat eine Reihe von Vorteilen: Sie bietet die Möglichkeit häufiger Änderungen im Design der Produkte und der Verarbeitungsreihenfolge sowie die Produktion von Produkten unterschiedlichster Bandbreite in Mengen, die durch den Produktionsbedarf bestimmt werden; Die mit dem Standortwechsel der Anlagen verbundenen Kosten werden reduziert und die Produktionsflexibilität erhöht.
Die Form der Produktionsorganisation beinhaltet die Zusammenfassung von Haupt- und Nebenvorgängen zu einem einzigen integrierten Produktionsprozess mit zellulärer oder linearer Struktur mit sequentiellem, parallelem oder parallel-sequentiellem Transfer von Arbeitsgegenständen in der Produktion.
Erstellung integrierter Produktionsstandorte sind mit relativ hohen Einmalkosten verbunden, die durch die Integration und Automatisierung des Produktionsprozesses entstehen. Der wirtschaftliche Effekt des Übergangs zu einer integrierten Form der Produktionsorganisation wird durch eine Verkürzung der Dauer des Produktionszyklus für die Herstellung von Teilen, eine Erhöhung der Ladezeit von Maschinen und eine verbesserte Regelung und Steuerung von Produktionsprozessen erreicht. In Abb. Abbildung 7 zeigt Anlagenlayoutdiagramme in Bereichen mit unterschiedlichen Formen der Produktionsorganisation.
Je nach Können Zur Nachjustierung für die Produktion neuer Produkte lassen sich die oben genannten Formen der Produktionsorganisation in flexible (veränderbare) und starre (nicht nachjustierbare) Formen unterteilen. Starre Formen der Produktionsorganisation umfassen die Verarbeitung von Teilen einer Art (z. B. eine kontinuierliche Form der Organisation des Produktionsprozesses).
Flexible Formen ermöglichen es, den Übergang zur Produktion neuer Produkte ohne Änderung der Zusammensetzung der Komponenten des Produktionsprozesses mit geringem Zeit- und Arbeitsaufwand sicherzustellen.
Die am weitesten verbreiteten Formen der Produktionsorganisation in Maschinenbauunternehmen sind derzeit flexible Punktproduktion, flexible Subjekt- und Flussformen.
Reis. 7. Anlagenanordnungen (Arbeitsplätze) in Bereichen mit unterschiedlichen Formen der Produktionsorganisation:
a - technologisch; b - Betreff; c - direkter Fluss;
g - Punkt (für den Montagefall); d - integriert
Bei der flexiblen Punktproduktion handelt es sich um die räumliche Struktur eines separaten Arbeitsplatzes ohne weitere Verlagerung von Arbeitsgegenständen während des Produktionsprozesses. Das Teil wird komplett in einer Position bearbeitet. Die Anpassung an die Veröffentlichung neuer Produkte erfolgt durch Änderung des Betriebszustands des Systems.
Flexible Fachorganisationsform Die Produktion zeichnet sich durch die Fähigkeit aus, Teile innerhalb eines bestimmten Bereichs ohne Unterbrechung für Umrüstungen automatisch zu verarbeiten. Der Übergang zur Produktion neuer Produkte erfolgt durch Neuanpassung technischer Mittel und Neuprogrammierung der Steuerung. Die flexible, lineare Form der Produktionsorganisation zeichnet sich durch eine schnelle Umstellung auf die Bearbeitung neuer Teile innerhalb eines vorgegebenen Bereichs durch den Austausch von Werkzeugen und Vorrichtungen sowie die Neuprogrammierung des Steuerungssystems aus. Es basiert auf einer strikt dem technologischen Prozess entsprechenden Reihenanordnung der Geräte mit stückweiser Übergabe der Arbeitsgegenstände.
Entwicklung von Organisationsformen der Produktion unter modernen Bedingungen.
Unter dem Einfluss des wissenschaftlichen und technologischen Fortschritts im Maschinenbau und Maschinenbau kommt es zu erheblichen Veränderungen durch die Mechanisierung und Automatisierung von Produktionsprozessen. Dadurch werden objektive Voraussetzungen für die Entwicklung neuer Formen der Produktionsorganisation geschaffen, beispielsweise der blockmodularen Form.
Die Schaffung einer Produktion mit einer blockmodularen Form der Produktionsorganisation erfolgt durch die Konzentration des gesamten Komplexes der technologischen Ausrüstung, die für die kontinuierliche Produktion einer begrenzten Produktpalette erforderlich ist, an einem Standort und die Zusammenführung einer Gruppe von Arbeitern zur Herstellung des Endprodukts und überträgt ihnen einen Teil der Funktionen der Planung und Steuerung der Produktion vor Ort.
Ökonomische Basis Die Schaffung solcher Industrien sind kollektive Formen der Arbeitsorganisation. Die Hauptanforderungen für die Organisation des Produktions- und Arbeitsprozesses sind in diesem Fall: Schöpfung autonomes System technische und instrumentelle Aufrechterhaltung der Produktion; Erreichen der Kontinuität des Produktionsprozesses auf der Grundlage der Berechnung des rationellen Ressourcenbedarfs unter Angabe von Intervallen und Lieferterminen; Sicherstellung der passenden Kapazität der Bearbeitungs- und Montageabteilungen; Berücksichtigung etablierter Kontrollierbarkeitsstandards bei der Ermittlung der Mitarbeiterzahl; Auswahl einer Gruppe von Arbeitnehmern unter Berücksichtigung der vollständigen Austauschbarkeit.
Umsetzung der vorgegebenen Anforderungen ist nur mit einer umfassenden Lösung der Fragen der Arbeitsorganisation, der Produktion und des Managements möglich. Der Übergang zu einer blockmodularen Produktionsorganisation erfolgt in mehreren Schritten. In der Phase der Vorprojekterhebung wird entschieden, ob die Erstellung solcher Einheiten unter den gegebenen Produktionsbedingungen sinnvoll ist. Es wird eine Analyse der strukturellen und technologischen Homogenität der Produkte durchgeführt und die Möglichkeit der Zusammenstellung von „Familien“ von Teilen für die Verarbeitung innerhalb der Produktionszelle bewertet.
Anschließend wird die Möglichkeit ermittelt, den gesamten Komplex der technologischen Vorgänge zur Herstellung einer Teilegruppe in einem Bereich zu konzentrieren; die Anzahl der Arbeitsplätze, die für die Einführung der Gruppenbearbeitung von Teilen geeignet sind, wird festgelegt; Basierend auf dem angestrebten Automatisierungsgrad werden Zusammensetzung und Inhalt der Grundvoraussetzungen für die Organisation des Produktions- und Arbeitsprozesses festgelegt.
In der Strukturentwurfsphase werden die Zusammensetzung und Beziehungen der Hauptkomponenten des Produktionsprozesses festgelegt.
Auf der Stufe der organisatorischen und wirtschaftlichen Gestaltung werden technische und organisatorische Lösungen kombiniert und Wege zur Umsetzung der Prinzipien der Tarifverträge und der Selbstverwaltung in autonomen Teams aufgezeigt.
Die zweite Richtung in der Entwicklung von Formen der Produktionsorganisation ist der Übergang zur Montage komplexer Einheiten im Tischverfahren, der Verzicht auf die Bandmontage durch die Organisation eines Mini-Flows.
Eine weitere Entscheidung der Organisation Bei der kontinuierlichen Produktion handelt es sich um die Aufrechterhaltung des Fördersystems unter Einbeziehung vorbereitender Vorgänge. In diesem Fall arbeiten die Monteure nach eigenem Ermessen entweder im Haupt- oder im Vorbereitungsbetrieb. Diese Ansätze zur Entwicklung der kontinuierlichen Form der Produktionsorganisation sorgen nicht nur für eine Steigerung der Arbeitsproduktivität und eine verbesserte Qualität, sondern geben den Monteuren auch ein Gefühl der Arbeitszufriedenheit und beseitigen die Monotonie der Arbeit.
Methoden zur Organisation der Produktion.
Methoden zur Organisation der Produktion sind eine Reihe von Methoden, Techniken und Regeln zur rationellen Kombination der Hauptelemente des Produktionsprozesses in Raum und Zeit in den Phasen Betrieb, Gestaltung und Verbesserung der Produktionsorganisation.
Methode zur Organisation der individuellen Produktion wird unter Bedingungen einer Einzelproduktion oder Produktion in kleinen Chargen verwendet und setzt Folgendes voraus: mangelnde Spezialisierung am Arbeitsplatz; der Einsatz vielseitig einsetzbarer Geräte, deren Anordnung in Gruppen entsprechend funktionaler Zweck; sequentielle Bewegung von Teilen von Betrieb zu Betrieb in Chargen.
Die Bedingungen für die Wartung von Arbeitsplätzen unterscheiden sich insofern, als dass die Arbeiter fast ständig einen Satz Werkzeuge und eine kleine Anzahl universeller Geräte verwenden; lediglich ein regelmäßiger Austausch stumpfer oder abgenutzter Werkzeuge ist erforderlich. Im Gegensatz dazu erfolgt die Anlieferung von Teilen an Arbeitsplätze und die Anpassung von Teilen bei der Ausgabe neuer Arbeiten und der Abnahme fertiger Arbeiten mehrmals während der Schicht. Daher besteht Bedarf an einer flexiblen Organisation der Transportdienstleistungen für Arbeitsplätze.
ORGANISATION DER PRODUKTION UND WIRTSCHAFTLICHEN AKTIVITÄTEN IM ENERGIEBEREICH
Betrachtet man die Vorgehensweise zur Wahrnehmung der Funktionen und Teilfunktionen des Energiemanagements eines Unternehmens, so ist zum einen zu beachten, dass diese alle Tätigkeitsbereiche durchdringen und zum anderen in diesen Bereichen bestimmte vorrangige Elemente aufweisen. Die an der Schnittstelle der Bereiche gebildeten funktionalen Management-Subsysteme sind eine Art „Inhaltsverzeichnis“ der gesamten organisatorischen und wirtschaftlichen Arbeit des Energiedienstes. Einige von ihnen erhalten mehr Aufmerksamkeit, andere weniger als ¾ aufgrund des sehr großen Umfangs der Managementarbeit im Energiesektor.
Wenn man nämlich die Anzahl der Funktionen und Unterfunktionen (es sind 17) mit der Anzahl der Bereiche (es sind 12) multipliziert, erhält man 204 „Überschriften“ – eine Reihe von Aufgaben in der allgemeinen Liste der Managementaufgaben des Energiedienstes. In jedem dieser Komplexe wird die Anzahl der Aufgaben durch die Anzahl der Energiearten, Energieanlagen (Produktionen, Werkstätten, Standorte und sogar einzelne Energie- und Energienutzungsanlagen) und andere Indikatoren bestimmt. Dadurch beläuft sich die Gesamtzahl der Verwaltungsaufgaben und -arbeiten auf mehrere Tausend.
Als Beispiel für diese Vielfalt empfiehlt es sich, die Organisation der Struktur in den Haupttätigkeitsbereichen aufzulisten und kurz zu betrachten:
¾ Organisation der Energieverbrauchsstruktur;
¾ Organisation der Struktur der Energienutzung.
¾ Organisation des Aufbaus von Energieanlagen und des Verfahrens für deren Betrieb.
¾ Organisation der Struktur der Stromversorgungsarten und des Betriebs von Energieanlagen.
¾ Organisation der Struktur im System der Zuverlässigkeit der Stromversorgung und des Betriebs von Energieanlagen.
¾ Organisation der Struktur der betrieblichen Energieüberwachung.
¾ Organisation der Struktur der Reparaturwartung von Energieanlagen.
¾ Organisation der Arbeitsstruktur und des Energiepersonals.
¾ Organisation der Struktur der materiellen und technischen Versorgung des Energiesektors.
¾ Organisation der Struktur der wirtschaftlichen Arbeit im Energiesektor.
¾ Organisation einer Struktur zur Entwicklung der Energieerzeugung.
Energieeffizienz Die Existenz eines Unternehmens hängt maßgeblich vom Perfektionsgrad der Organisationsstruktur des Eab. Die Qualität der Organisationsstruktur wird in erster Linie durch die Fähigkeit bestimmt, Führungsfunktionen in allen Tätigkeitsbereichen optimal wahrzunehmen. Daher werden hier Produktions- und Verwaltungsabteilungen geschaffen, deren Aufgaben die Arbeit an einer Funktion („Planung“ – Planungsabteilung, „Buchhaltung“ – Buchhaltung, „Rationierung“ – Normungsbüro usw.) in einer (oder mehreren) umfassen. Tätigkeitsbereiche („Reparaturservice“ – Reparaturwerkstatt, „Energienutzung“ – Energiemanagementbüro etc.) sowie in funktionale Subsysteme(„Kontrolle und Regulierung des Energieverbrauchs“ – Energieversanddienst usw.).
Unternehmen verschiedener Branchen nutzen zentralisierte, dezentrale und gemischte Managementsysteme. In manchen Fällen entsteht ein sogenanntes „Personal“-Programm, das meist als vorübergehende Maßnahme zur Lösung spezifischer Probleme organisiert wird.
Mit zentraler Steuerung Der Energiedienst, der vom leitenden Energietechniker des Unternehmens geleitet wird, umfasst Energietechniker, die allgemeine Anlagen- und Werkstattausrüstungen warten. Zwischen dem Chef-Energieingenieur, seinem Verwaltungsapparat (Abteilung des Chef-Energieingenieurs) und allen Energieingenieuren des Unternehmens werden lineare Führungsbeziehungen direkter Unterordnung hergestellt. Dieses Managementschema ist typisch für kleine und mittlere Unternehmen mit einem unterentwickelten Energiesektor.
Bei der dezentralen Bewirtschaftung deckt die Energiedienstleistung nur den allgemeinen Anlagenteil des Energiesektors ab. Das Energiepersonal der Werkstätten ist der Leitung seiner Werkstätten unterstellt und hat nur funktionale Verbindungen mit dem Energiedienst – in Fragen des Betriebs und der Reparatur von Werkstättenenergieanlagen, der Energieversorgung, des Energieverbrauchs und des Energieverbrauchs in der Werkstatt. Dieses Schema wird in großen Unternehmen mit komplexem Energiemanagement eingesetzt.
Das gemischte System sieht eine teilweise Dezentralisierung der Verwaltung vor, bei der die Energieingenieure einiger Werkstätten und Dienste der Leitung ihrer Abteilungen und in einigen Fällen dem Energiedienst des Unternehmens unterstellt sind.
Die Verwendung des einen oder anderen Schemas, Der mehr oder weniger starke Grad der Zentralisierung des Energiemanagements in Unternehmen wird auf der Grundlage der örtlichen Gegebenheiten und unter Berücksichtigung der Größe des Energiesektors bestimmt. In der Industrie gibt es unterschiedliche Ansätze zur Organisation der Energiemanagementstruktur, nach zahlreichen Vorgaben wurden Kategorien des Energiemanagements entwickelt.
Die gebräuchlichsten Kategorisierungssysteme sind wie folgt.
Pro 20 Millionen kWh Jahresstromverbrauch wird ein Punkt vergeben. Die Gesamtmenge beträgt 50.000 Tonnen Treibstoffäquivalent. pro Jahr, für alle 500 Stück. elektrische Maschinen.
Die Gesamtpunktzahl wird mit einem Koeffizienten von 0,27 Personen/Punkt multipliziert und das Ergebnis der Abteilung des leitenden Energieingenieurs bestimmt die Kategorie der Energiedienstleistung und die Anzahl der Abteilungen (durch Rundung).
In Chemieunternehmen ist die Kategorisierung auch mit der Berechnung von Punkten in Abhängigkeit vom Strom-, Wärme- und Wasserverbrauch verbunden.
Eine Kategorie höher(einschließlich „Null“, nicht kategorisch) bezieht sich auf eine Energiedienstleistung, die eines von umfasst folgenden Objekten: Wärmekraftwerke, Kesselhäuser, Kühlung, Kompressor, Luftzerlegung, Wasserstoff-Sauerstoff-Stationen; Abhitzekessel; Wasserzirkulationssysteme; eigene Wasserversorgungsquellen - Wasserentnahmen, artesische Brunnen und andere. Eine ungefähre Struktur für die Verwaltung einer Energiedienstleistung der Kategorie I oder II ist in Abb. dargestellt. 8.
Chefenergieingenieur
![]() |
Chefabteilung des Chief Power Engineer Chief
Elektriker, Heizungsbauer
Buchhaltungssektor, Sektorsektorlabor
Standardisierung der Energieüberwachung von PPR sowie Prüfung und Planung sowie Zuverlässigkeit von Ersatzteilen für Energieressourcen von Anlagen
Elektrowerkstatt - Elektrowerkstatt - Dampfwerkstatt - Wasserkommunikationswerkstatt Reparaturversorgung, Dampf- und Wärmeversorgung und Versorgungswerkstatt, BHKW-Kanalisation
Reis. 8. Ungefähres Schema zur Verwaltung des Energiedienstes Industrieunternehmen 1. und 2. Kategorie
Einige Experten schlagen vor Legen Sie die Kategorie des Energiesektors und die Anzahl der Führungskräfte darin in Abhängigkeit von einer Reihe von Produktionsfaktoren gemäß den Regressionsabteilungen fest. Anzahl der Führungskräfte ( L aup) wird in Abhängigkeit von der Anzahl der Produktionsmitarbeiter im Unternehmen berechnet ( L pr), Anzahl der Arbeitnehmer im Energiesektor ( L e); Kosten der Produktionsanlagen ( F), ihr aktiver Teil ( F a) und separat Stromversorgungsgeräte (F e); Gesamtmenge der verbrauchten Energie, umgewandelt in Standardbrennstoff ( IN); die Gesamtzahl der Einheiten der Energieausrüstung, angegeben in Einheiten der Reparierbarkeit ( R sl).
Die Standardanzahl an Führungskräften wird je nach Einflussgrad eines bestimmten Faktors nach einer von vier Formeln berechnet:
L aup = 0,208F 0.9102
L aup= 0,0223 L e0 ,19 F a0 ,414
L aup= 0,023L pr 0,542 F a 0,414
L aup = 2 + 0,9F. e + 0,55R sl+ 0,01 V.
Es wird vorgeschlagen, diese Formeln zur Bestimmung der Anzahl der Ingenieure in Energieabteilungen zu verwenden.
Unter Marktbedingungen organisatorische Struktur Das Energiemanagement in Unternehmen sollte zwei neue Qualitäten haben:
Größte Klarheit beim Aufbau von Produktions- und Funktionseinheiten für die erfolgreiche Umsetzung der Zielfunktion;
Die Erweiterung der Wirtschaftseinheiten aufgrund eines starken Anstiegs des Wirtschaftsarbeitsvolumens.
Ungefähres Diagramm Die Steuerung des Energiemanagements des Unternehmens unter Bedingungen wirtschaftlicher Unabhängigkeit ist in Abb. dargestellt. 9.
Die Hauptaufgaben der Funktionseinheiten des Energiedienstes, traditionell und zur wirtschaftlichen Unterstützung der wirtschaftlichen Unabhängigkeit eingeführt, ergeben sich in den meisten Fällen aus ihren Namen. Für einige davon empfiehlt es sich, einige Erläuterungen zu geben.
Die Hauptaufgabe Energiewirtschaftsbüro Es sollte eine Energiesparpolitik im Unternehmen geben, eine Analyse des Energieverbrauchs in Produktionsprozessen durchführen und organisatorische und technische Maßnahmen zur Energieeinsparung entwickeln.
Reis. 9. Ungefähres Schema des Energiemanagements in einem Industrieunternehmen unter den Bedingungen einer wirtschaftlich unabhängigen Energiedienstleistung
Aufgaben des Büros für Normung und Energiebilanzen:
Schaffung eines Systems zur Rationierung des Energieverbrauchs in Produktionsprozessen auf der Grundlage einer gemeinsam mit dem Wirtschaftsbüro durchgeführten Analyse des Energieverbrauchs;
Entwicklung technologischer Standards für die energieintensivsten Vorgänge, Prozesse, Grenzwerte, Zwischenprodukte pro Rohstoffeinheit oder Fertigprodukt im gesamten Sortiment;
Entwicklung von Energieverbrauchsstandards für sanitäre und technische Zwecke in Abhängigkeit von klimatischen und saisonalen Faktoren;
Rationierung des Energieverbrauchs in Hilfsprozesse und Produktion, Verluste in der Energiekommunikation und Energieausrüstung, Eigenbedarf des Energiesektors;
Entwicklung allgemeiner Produktion – Werkstatt und Fabrik – Standards für den Energieverbrauch für Produkte, Arbeiten und Dienstleistungen.
Hier soll es stattfinden Energieversorgungsplanung durch Entwicklung geplanter (aktueller) und langfristiger Energiebilanzen für alle gewerblichen (selbstversorgenden) Verbraucher innerhalb und außerhalb des Unternehmens.
Das Büro für Energiebuchhaltung, -kontrolle und -überwachung sollte sich mit der Aufrechterhaltung und Verbesserung der betrieblichen und statistischen (aktuellen) Buchhaltung der Produktion, Verteilung und des Verbrauchs von Energieressourcen und der damit verbundenen Berichterstattung befassen. betriebliche (zusammen mit dem Dispositionsdienst) und laufende Kontrolle und Regelung der Energieversorgung, werksinterne Energieüberwachung.
Das Wirtschaftsplanungsbüro (Abteilung) hat die Aufgabe, die Produktions- und Wirtschaftsaktivitäten des Energiesektors (mit Ausnahme der Produktion und des Verbrauchs von Energieressourcen) sowie die Geschäftsbeziehungen zu Unternehmensbereichen und externen Verbrauchern zu planen.
Das Finanzbüro (die Finanzabteilung) muss Finanztransaktionen zur Finanzierung der Produktion und wirtschaftlichen Aktivitäten von Energiedienstleistungen sowie Finanztransaktionen mit Lieferanten durchführen.
STRUKTUR UND MERKMALE DER ENERGIEERZEUGUNG
Die Energieerzeugung ist ein technologischer Prozess, der drei Phasen umfasst: Produktion, Umwandlung, Energieverbrauch.
Dieser technologische Prozess basiert auf physikalischen Gesetzen, aus denen sich zwei Hauptmerkmale ergeben: erzwungene Kontinuität und Automatismus; zeitliches Zusammentreffen von Energieerzeugung und -verbrauch.
Aus diesen beiden Hauptmerkmalen ergibt sich Folgendes:
a) Bei diesem Prozess besteht eine absolute Proportionalität zwischen Energieerzeugung und -verbrauch, d. h. es gibt keine lokalen Ansammlungen von Halbfabrikaten und Produkten;
b) Produktrückweisungen und Rücknahme vom Verzehr sind ausgeschlossen;
c) es gibt kein Verkaufsproblem, Überbestände sind ausgeschlossen;
d) Es besteht keine Notwendigkeit, Produkte zu lagern.
Ein wichtiges Merkmal der Energieerzeugung liegt auch darin, dass Energieunternehmen eng mit Industrie, Bau, Verkehr, Kommunikation, Landwirtschaft und öffentlichen Versorgungsbetrieben verbunden sind – mit der Gesamtheit der verschiedenen Empfänger elektrischer Energie. Und dies wiederum gibt die strikte Abhängigkeit der Energieerzeugung, insbesondere der elektrischen Energie, vom Verbrauchsregime vor.
Ein sehr charakteristisches Merkmal der Energieerzeugung ist die Variabilität ihres Regimes sowohl im Jahresverlauf als auch im Tagesverlauf. Diese Variabilität beruht einerseits auf natürlichen und klimatischen Faktoren (Temperaturschwankungen, Veränderungen des natürlichen Lichts), andererseits auf den Besonderheiten des technologischen Prozesses verschiedener Unternehmen und Branchen.
Diese Merkmale der Energieerzeugung bestimmen, wie wichtig es ist, ein ausreichendes Maß an Zuverlässigkeit des Energiesektors sicherzustellen, um eine unterbrechungsfreie Stromversorgung der Verbraucher sicherzustellen.
Ein wesentliches Merkmal der Energieerzeugung liegt auch in der relativ schnellen Entwicklung von Notfallsituationen, in dem Einfluss, den ein ausgefallenes Element auf die mit ihm verbundenen Elemente hat.
Wie oben erwähnt, besteht bei der Energieerzeugung eine strikte Abhängigkeit des Produktionsmodus vom Verbrauchsmodus.
Daher spielen Lastdiagramme, die zeigen, wie sich der Verbrauch im Laufe der Zeit verändert, eine wichtige Rolle bei der Planung und wirtschaftlichen Analyse der Energieerzeugung. Je nach Zeitintervall werden Tages- (Winter, Sommer) und Jahrespläne unterschieden.
Die Belastung des Energieverbrauchers ändert sich ständig und erreicht zu einem bestimmten Zeitpunkt ihren Höchstwert ( R max) und kleinste ( R min) Werte. Die maximale und minimale Belastung sind die wichtigsten Punkte in der Grafik. Die Fläche des Diagramms drückt in einem bestimmten Maßstab die erzeugte Energiemenge aus.
Der Bereich, der durch horizontale Linien begrenzt wird, die durch das Maximum verlaufen R maximal und durchschnittlich R Der Mittwoch des Lastwertes wird als Spitzenteil des täglichen Lastplans bezeichnet, der Rest des Lastplans wird als Basis bezeichnet. Das absolute Indikatoren Ladeplan. Lastdiagramme werden auch durch relative Indikatoren charakterisiert:
1. Dichtekoeffizient (Füllkoeffizient). G, definiert als das Verhältnis der durchschnittlichen Belastung R Durchschnitt bis Maximum:
G = R Mi / R max, wobei max die maximale Belastung MW ist.
2) Mindestlastkoeffizient α min, definiert als Verhältnis von Minimum zu Maximum:
α = R Mindest/ R max , wo
Indikatoren der Tages-Charts elektrische Belastung des Stromnetzes G und α min hängen von der Zusammensetzung und Betriebsart der Energieverbraucher ab. α min kann theoretisch von 0 bis 1 schwanken (die gesamte Belastung erfolgt über den Tag hinweg kontinuierlich). In der Praxis liegt α min zwischen 0,3 (einschichtige Verbraucher und Beleuchtung überwiegen) bis 0,9 (energieintensive Verbraucher mit kontinuierlicher Produktion überwiegen).
Der Dichte-(Füllungs-)Indikator des täglichen Stromlastplans liegt normalerweise innerhalb G= 0,5 ÷ 0,95.
Bei einem niedrigeren Wert überwiegt die elektrische Kapazität industrieller Verbraucher.
Leistungsreservierung.
Reservekapazitäten sind erforderlich, um ausgefallene Einheiten zu ersetzen, die routinemäßig zur Reparatur ausgeliefert werden, und um den Bedarf an Produktionskapazitäten zu decken.
Bei Erzeugungs-, Umwandlungs- und Übertragungsanlagen werden die Kapazitätsreserven entsprechend unterschieden: Reparatur, Notfall, Last (erforderlich zum Ausgleich unregelmäßiger Laständerungen aus zufälligen Gründen für Energiesysteme). Die Kombination aus Not- und Lastreserve wird als Betriebsreserve bezeichnet. Die elektrische Leistungsreserve ist für den Energiepool einheitlich und einheitlich. Seine Größe richtet sich nach der maximalen Belastung des Energiespeichers (in der Regel für Wintertage).
Der wirtschaftliche Aspekt des Problems liegt in der Rechtfertigung der optimalen Gangreserve. Durch die Erhöhung der Leistungsreserve in Stromverbindungen wird der Schaden des Verbrauchers durch eine Notunterversorgung mit elektrischer Energie verringert, jedoch steigen die Kosten für die Erzeugung und Aufrechterhaltung der Leistungsreserve. Statistiken zeigen, dass die notwendige und ausreichende Leistungsreserve des Stromversorgungssystems etwas mehr als 15 % der maximalen Last betragen sollte (einschließlich Notfall – 4–5 %, Reparatur – 8–9 %, Last – 3–4 %).
BETRIEBLICHES ENERGIEMANAGEMENT DES UNTERNEHMENS
Die meisten Managementfunktionen verfügen über Unterfunktionen, die sich auf den betrieblichen Zeitpunkt beziehen – Betriebsbuchhaltung, Betriebsanalyse, Betriebsplanung, Betriebssteuerung und -regulierung. Zusammengenommen bilden sie (eine Organisation), wobei vor allem die betriebliche Buchhaltung, Kontrolle und Regulierung hervorzuheben sind. Daher wird oft der gesamte Prozess der Betriebsführung so genannt – Betriebsabrechnung und -kontrolle, deren Umsetzung in den Dienst des Energiesektors fällt. Die Hauptaufgabe der Betriebsführung sollte auch die Arbeit des Betriebspersonals an jedem Arbeitsplatz umfassen, das Energie und energieverbrauchende technologische Geräte wartet.
Gleichzeitig sollte ihre Aufgabe sein bei der optimalen Steuerung von Prozessen nicht nur im Hinblick auf technologische, sondern auch im Hinblick auf Energieindikatoren. Es empfiehlt sich, die Vorgehensweise einer solchen Betriebsführung am Beispiel der optimalen Regelung des Betriebs einer technologischen Anlage nach den Kriterien der rationellen Energienutzung zu betrachten. Die operative Führung gemäß den Aufgaben eines jeden Führungszyklus muss dem Standardprozess der Vorbereitung, Entscheidungsfindung und Umsetzung von Entscheidungen zur Zielerreichung entsprechen. In diesem Fall entstehen Informationsverbindungen zwischen dem Objekt und dem Subjekt der Verwaltung, und der Verwaltungsprozess selbst besteht in der sequentiellen Ausführung streng definierter Funktionen.
Das Betriebsmanagement umfasst die folgenden Hauptphasen:
a) im Rahmen der Betriebsabrechnung werden Daten über den Verbrauch und die Nutzung von Energieressourcen durch das Kontrollobjekt erfasst; Solche Daten sind quantitative und qualitative (parametrische) Indikatoren des Energieverbrauchs;
b) Aus den Abrechnungsdaten werden Indikatoren ausgewählt, die den Rationalitätsgrad der Energienutzung bestimmen, d.h. unterliegt der betrieblichen Kontrolle;
c) ausgewählte Indikatoren werden im Vergleich zu Standardwerten analysiert, beispielsweise mit dem aktuellen Energieverbrauch;
d) Wenn die tatsächlichen Indikatoren von den normativen abweichen, wird eine Lösung zur Korrektur dieser Situation und ein Satz ausgewählt Standardlösungen im Vorfeld bei der Vorbereitung operativer Planungsoptionen vorbereitet;
d) beabsichtigte Option optimale Lösung bei Bedarf wird dies mit übergeordneten Führungskräften vereinbart und anschließend der Befehl zur Durchführung erteilt – ein Akt der Betriebsführung;
f) Maßnahmen werden ergriffen, um den Prozess operativ zu regulieren, um das Ziel zu erreichen – indem die tatsächlichen Indikatoren mit den gewünschten, normativen in Einklang gebracht werden;
g) es wird ein neuer Betriebsbuchhaltungsakt durchgeführt, um zu prüfen, ob das gewünschte Ergebnis erreicht wurde;
Damit ist ein Zyklus beendet Kontrolle und die nächste beginnt - kontrolliert
Die Organisation der Produktion ist eine Reihe von Maßnahmen, die auf die rationelle Verknüpfung von Arbeitsprozessen mit den materiellen Elementen der Produktion in Raum und Zeit abzielen, um die Effizienz zu steigern, d. h. gesetzte Ziele in kürzester Zeit bei bestmöglicher Nutzung der Produktionsressourcen zu erreichen . Die Hauptziele der Produktionsorganisation sind:
- 1) Bereitstellung der notwendigen Produktionsfaktoren (Rohstoffe, Ausrüstung, Arbeitskräfte) für die Produktionsaufgabe;
- 2) Einhaltung der notwendigen Verhältnisse zwischen den Produktionsfaktoren (Bildung wirtschaftlich gerechtfertigter Vorräte und Reserven, Beseitigung von Überschüssen usw.);
- 3) Gewährleistung eines ausgewogenen Produktionsprozesses (Konsistenz, Kontinuität, Synchronizität usw.);
- 4) termingerechte Erledigung der Aufgabe, Herstellung von Produkten entsprechender Qualität und Quantität.
Daher sind die aktuellen Aufgaben der Produktionsorganisation:
- - Schaffung der notwendigen Proportionen im Produktionspotenzial des Unternehmens;
- - Schaffung eines rationalen Gleichgewichts zwischen Arbeitsplätzen und Arbeitskräften relevanter Berufe und Qualifikationen;
- - Koordinierung der Zeit für die Durchführung von Arbeiten in Werkstätten, Bereichen, Arbeitsplätzen;
- - Verteilung der Arbeitsaufgaben zwischen den Mitarbeitern;
- - Schaffung von Arbeitsanreizen;
- - Organisation der Versorgung der Arbeitsplätze mit Produktionsfaktoren (Geräte, Werkzeuge, Rohstoffe etc.).
Wie aus der Formulierung der Aufgaben hervorgeht, besteht die wichtigste Richtung der Produktionsorganisation darin, Arbeitsplätze zu organisieren, Aufgaben an die Arbeitnehmer zu verteilen und Bedingungen für die Erledigung dieser Aufgaben zu schaffen. Effektive Organisation Arbeit ist ohne die Entwicklung grundlegender Prinzipien für die Organisation des Produktionsprozesses als Ganzes unmöglich. Schauen wir uns diese Prinzipien genauer an. Zu den wichtigsten Grundsätzen der Organisation des Produktionsprozesses gehören:
Spezialisierung. Dieses Prinzip der Organisation von Produktionsprozessen setzt eine strikte Arbeitsteilung innerhalb des Unternehmens voraus. Bestimmt Produktionsstrukturen, Bereiche, Arbeiter führen die ihnen zugewiesenen Spezialfunktionen aus. Wenn sich Produktionsaufgaben ändern, ist die Unternehmensleitung bestrebt, die Spezialisierung aufrechtzuerhalten. Beispielsweise wird in der Tischlerei die Lackiererei auch dann weiter lackieren, wenn sich das Möbelsortiment ändert. Die Spezialisierung kann objektbezogen (für fertige Produkte als Ganzes), detailliert (für die Herstellung einzelner Teile) und operativ (für die Umsetzung eines separaten Vorgangs des technologischen Prozesses) sein. Die Spezialisierung hat eine Reihe von Vorteilen. Durch die Aufteilung der Produktion in separate Spezialvorgänge können Sie den Prozess automatisieren. Darüber hinaus ermöglicht die Ausübung homogener Funktionen den Mitarbeitern, ihre Fähigkeiten zu verbessern und trägt zu einer gesteigerten Produktivität bei. Die Qualität der Produkte verbessert sich. In der Bekleidungsindustrie wird beispielsweise die Betriebs- und Detailspezialisierung verwendet, bei der sich jede Näherin auf das Nähen von Taschen, Manschetten, Kragen usw. spezialisiert. Gleichzeitig ist die Spezialisierung häufig mit der Monotonie und Einheitlichkeit der von den Arbeitern ausgeführten Arbeitsfunktionen verbunden . Dies kann dazu führen, dass das Interesse an Aktivitäten verloren geht, was zu Arbeitsmüdigkeit führt. Dadurch kann es zu Personalfluktuationen kommen.
Kontinuität. Dieses Prinzip setzt eine solche Organisation des Produktionsprozesses voraus, bei der Stopps auf die minimal erforderlichen Werte reduziert werden oder sogar Unterbrechungen bei Anwesenheit des Arbeitsgegenstandes (Rohstoffe, Halbzeuge) in der Verarbeitung vollständig eliminiert werden. Dabei handelt es sich um die Übergabe von Arbeitsgegenständen von einem Betrieb an einen anderen ohne Verzögerungen und Ausfallzeiten von Geräten und Arbeitskräften. Die Umsetzung des Kontinuitätsprinzips trägt dazu bei, die Arbeitszeit der Arbeitnehmer zu sparen und die Zeit, in der die Geräte „im Leerlauf“ laufen, zu verkürzen. Dies sorgt für eine erhöhte Wirtschaftlichkeit der Produktion. Gleichzeitig ist eine Verabsolutierung des Kontinuitätsprinzips unmöglich. Insbesondere benötigt der Arbeitnehmer Pausen für kurze Ruhezeiten, Mittagessen usw. Die Kontinuität der Produktion zwingt die Unternehmensleitung dazu, die Arbeit in Nachtschichten zu organisieren, was sich negativ auf die Gesundheit der Arbeitnehmer auswirkt, die Arbeitsproduktivität verringert und eine Erhöhung der Arbeitskosten erfordert . Dauerbetrieb Geräte tragen zu Ausfällen und Unfällen bei. Bei der Organisation der Produktion sollte man sich um eine optimale Beschäftigung von Arbeitskräften und Ausrüstung bemühen.
Rhythmus. Dabei handelt es sich um die regelmäßige Wiederholung bestimmter Vorgänge. Beispielsweise ist alle 15 Minuten der Zusammenbau eines Kühlschranks abgeschlossen, alle 2 Minuten näht eine Näherin eine Manschette an einen Ärmel, alle 35 Minuten ist eine Ladung Brot fertig gebacken. Alle einzelnen Schritte und der gesamte Produktionsprozess zur Herstellung einer bestimmten Anzahl von Produkten werden nach genau festgelegten Zeiträumen wiederholt. Der Rhythmus drückt sich in der gleichmäßigen Produktion von Produkten oder der Bewegung von Arbeitsgegenständen in gleichen Abständen auf allen Stufen der technologischen Kette aus. Rhythmus ist wichtig bei der Zusammenarbeit bei Lieferungen und bei der Erfüllung von Verträgen über die Lieferung von Produkten innerhalb streng festgelegter Fristen. Zum Beispiel Lieferung und Montage Plattenhaus in 2 Wochen. Dies ermöglicht Planungsarbeiten sowohl für Lieferanten als auch für Verbraucher von Produkten. Die Umsetzung des Rhythmusprinzips erleichtert einerseits die Lösung des Problems der Produktionsorganisation. Dies wird zur Hauptaufgabe des Leiters. Andererseits besteht der Wunsch, den Rhythmus um jeden Preis sicherzustellen. Werden Lieferfristen für fertige Produkte nicht eingehalten, sind die Arbeitnehmer daher gezwungen, Überstunden und Wochenenden zu leisten.
Der Rhythmizitätskoeffizient wird durch das Verhältnis des tatsächlichen Produktionsvolumens für einen beliebigen Kalenderzeitraum (Jahrzehnt, Monat) zum geplanten Ziel für diesen Zeitraum bestimmt. Bei der Erledigung einer Aufgabe ohne Abweichungen ist dieser Koeffizient gleich eins.
Verhältnismäßigkeit. Dieses Prinzip der Organisation des Produktionsprozesses setzt die Einhaltung der notwendigen Proportionen, bestimmter Beziehungen zwischen den einzelnen Produktionsstufen sowie zwischen den Haupt-, Hilfs- und Dienstleistungsprozessen voraus. Auch bei der Durchführung einzelner Vorgänge wird auf Verhältnismäßigkeit geachtet. Beim Bau eines Hauses ist dies beispielsweise unbedingt erforderlich eine bestimmte Menge von Badezimmer. Bei der Produktion von 120 Hemden müssen 240 Ärmel genäht werden. Der Kern dieser Verhältnismäßigkeit besteht vor allem darin, genaue Proportionen in der Größe der Produktionskapazität und der Verfügbarkeit von Ausrüstung in Werkstätten und Bereichen einzuhalten. Handelt es sich dabei beispielsweise um das Nähen von 120 Hemden pro Monat, dann muss die Stoffzuschnittkapazität diesem Volumen entsprechen. Wenn Bauarbeiter während einer Arbeitsschicht 23 Tonnen Mörtel verbrauchen, muss die Kapazität der Mörtel-Beton-Einheit diesem Wert entsprechen. Selbstverständlich müssen bei Abweichungen von den Normen Reserven vorgehalten werden. So kann die Nachfrage nach der Lösung in einem bestimmten Zeitraum beispielsweise auf bis zu 30 Tonnen steigen. Das Wesen der Verhältnismäßigkeit beruht auf dem Vorhandensein realer Möglichkeiten zur Herstellung einer bestimmten Produktmenge pro Zeiteinheit in allen Phasen des Produktionsprozesses. Ein Verstoß gegen den Grundsatz der Verhältnismäßigkeit führt zur Entstehung sogenannter Engpässe in einer bestimmten Technologiekette, die das Wachstum der Produktionsmengen begrenzen. Ungleichgewichte führen auch zu Unterlasten und einer Verschlechterung der Nutzung von Geräten, die in anderen Gliedern dieser Kette installiert sind. Die Aufgabe des Produktionsorganisators besteht darin, Engpässe durch die Anschaffung neuer Geräte und eine rationelle Organisation der Produktion (z. B. Erhöhung der Schichtzahl) zu beseitigen.
Parallelität. Das Prinzip der Parallelität in der Organisation von Produktionsprozessen beinhaltet die gleichzeitige Ausführung einzelner Phasen des technologischen Prozesses, die zeitliche Kombination der Ausführung von Haupt- und Nebenvorgängen. Dieses Prinzip bedeutet Folgendes:
- - gleichzeitige Verarbeitung mehrerer Einheiten derselben Produkte in verschiedenen Arbeitsgängen (z. B. werden mehrere Sofas gleichzeitig hergestellt);
- - gleichzeitige Durchführung homogener Arbeitsgänge an verschiedenen Arbeitsplätzen (mehrere Näherinnen sind damit beschäftigt, Kragen für Hemden zu nähen). Die Erhöhung des Parallelitätsgrades der Vorgänge führt zu einer Verkürzung der Dauer des Produktionszyklus und spart Arbeitszeit. Darüber hinaus ermöglicht Ihnen das Parallelitätsprinzip, die benötigte Produktmenge in kürzerer Zeit zu produzieren. Beim Bau eines Hauses sind also mehrere Maurer daran beteiligt, Ziegel in die Wände zu legen.
Die Aufgabe der Produktionsorganisatoren besteht darin, Personal für parallele Vorgänge einzusetzen, um die Aufgabe termingerecht zu erledigen.
Direktheit. Dies ist der Grundsatz, nach dem bei der Organisation des Produktionsprozesses auf möglichst kurze Bewegungswege der Arbeitsgegenstände während des Produktionsprozesses geachtet werden muss. Die Bewegung des hergestellten Teils (oder Produkts) durch Arbeitsplätze, Abschnitte und Werkstätten sollte möglichst geradlinig erfolgen und ohne Rück- oder Gegenbewegungen erfolgen. Der direkte Ablauf wird durch die rationelle Platzierung von Werkstätten, Abschnitten, Arbeitsplätzen im Arbeitsablauf und einzelnen Etappen, also entlang des technologischen Prozesses, erreicht. Wenn sich eine Näherin beispielsweise auf das Annähen von Knöpfen spezialisiert hat, wird ihr Arbeitsplatz nach den Arbeitern liegen, die früher mit Arbeiten beschäftigt sind. Der Verpackungsbereich liegt in der Regel im Anschluss an die Hauptproduktionsbereiche. Montagebereiche sind so angeordnet, dass die Wege zu den Zulieferbereichen möglichst kurz sind. Aufgabe des Produktionsorganisators ist daher die rationelle Platzierung von Standorten und Werkstätten entsprechend der technologischen Kette.
Automatik. Dieses Prinzip setzt eine solche Organisation des Produktionsprozesses voraus, die einen möglichst hohen Grad an Automatisierung bzw. Mechanisierung erreicht. Die Automatisierung des Produktionsprozesses soll eine Reihe von Problemen technischer, wirtschaftlicher und sozialer Natur lösen. Bestimmte Produktionsarten sind gefährlich für die menschliche Gesundheit und werden daher in erster Linie automatisiert – dies ist die Produktion von chemischen Reagenzien, Kernenergie usw. Die wirtschaftlichen Vorteile der Automatisierung bestehen darin, dass die Produktionsleistung steigt, die Kosten sinken und die Arbeitsproduktivität steigt. Die sozialen Folgen der Automatisierung und Mechanisierung der Produktion sind mit der Verbesserung der Arbeitsbedingungen, der Erhöhung der Löhne, der Steigerung der Attraktivität des Arbeitsplatzes, der Verbesserung der Qualifikationen, der Verringerung von Gesundheitsrisiken usw. verbunden. Der Nachteil des Prozesses der Automatisierung und Mechanisierung der Produktion ist die Zunahme seine Kapitalintensität und Investitionskosten. Daher ist es bei kleinen Produktionsmengen manchmal wirtschaftlicher, einen manuellen Stapel zu verwenden. Beispielsweise ist es günstiger, einen kleinen Graben von Hand auszuheben, als mit leistungsstarken Baumaschinen. Daher sollten in der Massenproduktion die Arbeitsabläufe so weit wie möglich mit Maschinen und Geräten ausgestattet sein. Es ist jedoch zu bedenken, dass eine übermäßige Spezialisierung dieser Ausrüstung zu erhöhten Produktionskosten führen kann. Wenn Geräte sporadisch genutzt werden und nicht genutzt werden, steigen die Produktionskosten.
Beispiel 10. Es wurde eine Verpackungsmaschine im Wert von 2 Millionen Rubel gekauft. und eine Produktivität von 10.000 Paketen pro Monat, 100.000 pro Jahr. Die Standardlebensdauer beträgt 5 Jahre. Die Standardverpackungskosten betragen 4 Rubel. für 1 Produkt. Das Unternehmen muss nur 1.000 Produkte pro Monat verpacken. Folglich sind die Verpackungskosten in einem Produkt zehnmal höher als der Standard (40 Rubel). In dieser Situation kann es erforderlich sein, die Produkte manuell zu verpacken. Aber wenn die Kosten für die manuelle Verpackung mehr als 40 Rubel betragen. (zum Beispiel 50 Rubel) wird diese Maschine auch dann profitabel sein, wenn sie unterbelastet ist.
Die angegebenen Arten und Prinzipien der Organisation des Produktionsprozesses sind in Abb. dargestellt. 8.
Lassen Sie uns weiterhin die Prinzipien der Organisation des Produktionsprozesses charakterisieren.
Flexibilität. Das Prinzip der Flexibilität bei der Organisation von Produktionsprozessen besteht darin, dass die Produktion teilweise so organisiert werden muss, dass sie auf Marktanforderungen reagiert und sich schnell an die Produktion neuer Produkte anpasst. Flexibilität äußert sich in Änderungen der Produktpalette und des Produktionsvolumens; Prozessparameter ändern; die Fähigkeit der Haupt- und Hilfsgeräte, umzuschalten
andere Arten von Arbeit; Veränderungen im Niveau und Profil der Qualifikationen der Arbeitskräfte.
Reis. 8. Produktionsprozess und Grundsätze seiner Organisation
Optimalität. Dies ist die Wahl solcher Formen der Produktionsorganisation, die ein Höchstmaß an Wirtschaftlichkeit bieten. Dabei handelt es sich um die Wahl der optimalen Art der Führung, der optimalen Größe der Abteilungen und Strukturen, der optimalen technologischen Verbindungen zwischen den Abteilungen usw. Beispielsweise kann ein Unternehmen beim Einkauf von Rohstoffen eine Vorauszahlung leisten oder nach Erhalt der Produkte von der Firma bezahlen Anbieter. Bei der Entscheidung für die Zahlungsart sollten Sie von der Höhe der Rabatte ausgehen verschiedene Optionen Abrechnungen, die Möglichkeit der Verwendung von Zahlungsaufschüben usw.
Schauen wir uns nun konkrete Möglichkeiten zur Organisation der Produktion an. Abhängig von der Technologie der Branchen, der Unternehmensart und der Stellung des Unternehmens in der Branchenstruktur unterscheiden sich diese Methoden. Nennen wir einige davon:

Reis. 9. Möglichkeit zur Platzierung von Arbeitsplätzen in der Bekleidungsproduktion
- 3. Auf der Grundlage technologischer Karten Entwicklung von Aufgaben für Hauptproduktions-, Hilfs- und Wartungsarbeiten.
- 4. Die Aufgabe an die Darsteller kann in Form von Einzel- und Gruppenaufgaben erfolgen, begleitet von Netzwerk- und Bandplänen zur Erledigung der Arbeit. In Abb. Abbildung 10 zeigt beispielhaft einen Streifenplan für die Ausführung landwirtschaftlicher Arbeiten. Der Bandplan wird in Fällen verwendet, in denen Darsteller homogene Vorgänge ausführen. Mit dem Streifenplan können Sie den Übergang des Darstellers zu einem neuen Objekt planen. In Abb. Abbildung 10 zeigt einen Plan für die Aussaat und das Pflügen von Feldern. Abhängig von der Fläche des Feldes und dem Relief ist die Position der landwirtschaftlichen Maschinen auf den Feldern unterschiedlich.
Ein Beispiel für eine Aufgabe finden Sie in der Tabelle. 23. Diese Aufgaben können in Form von Anordnungen, in Form von Arbeitsplänen, Anordnungen und Weisungen für die Institution etc. erfolgen. Jede Institution wählt ihre eigene Aufgabenform. Das Hauptprinzip ist die Konsistenz der Aufgaben über Abteilungen und Abteilungen hinweg. In Fällen, in denen Mitarbeiter täglich homogene Arbeiten verrichten, erfolgt keine Aufgabenerteilung. Sie kommen zum Einsatz, wenn zusätzliche Arbeitsvolumina oder neue Arbeiten hinzukommen.
Produktionsmitarbeiter und Führungskräfte im Dienstleistungssektor können ihre Aufgaben auf der Grundlage von Stellenbeschreibungen wahrnehmen.
Reis. 10. Streifenplan zum Pflügen von Feldern
Tabelle 23
Beispiel einer Bodenbelagsaufgabe Keramikfliesen mit Musterdesign
Name technologischer Prozesse |
Dienstprogramm Arbeiter |
Fliesenleger, 4. Klasse (3 Personen) |
|
Benetzen Sie die Basis mit Wasser |
|||
Sortieren von Kacheln nach Größe und Farbe |
|||
Installation von „Beacons“ |
|||
Installation einer Schicht vorgefertigter Lösung |
|||
Verlegen von Fliesen nach einer Vorlage nach einem vorgegebenen Muster |
|||
Fliesen verlegen |
|||
Nahtfüllung |
|||
Reinigen und Abwischen der Beschichtung |
|||
Gesamtfläche - 100 m2 |
|||
Arbeitszeit: 8 Arbeitsschichten |
Abhängig von der Art der Bewegung von Arbeitsgegenständen gibt es Linien- (kontinuierliche), Batch- und Einzelmethoden zur Organisation von Produktionsprozessen.
Die Fließproduktion entlang des technologischen Prozesses ist durch die kontinuierliche und sequentielle Bewegung von Arbeitsgegenständen von einem Betrieb zum anderen gekennzeichnet.
Bei Batch- und Einzelverfahren (diskontinuierlich) wird das verarbeitete Produkt nach jedem Arbeitsgang vom technologischen Prozess abgeschaltet und wartet auf den nächsten Arbeitsgang. In diesem Fall sind die Dauer des Produktionszyklus sowie der Umfang der laufenden Arbeiten und des Betriebskapitals relativ groß; zusätzliche Bereiche zur Lagerung von Halbzeugen.
Als fortschrittlichste Methode zur Organisation des Produktionsprozesses gilt die Fließmethode. Seine Hauptmerkmale sind:
- · hochgradig Kontinuität;
- · Lage der Arbeitsplätze während der technologischen Bearbeitung;
- · hohes Maß an Rhythmus.
Die organisatorische Grundlage des Fließverfahrens ist die Produktionslinie, die über die wichtigsten Parameter wie Takt und Fließgeschwindigkeit verfügt.
Im Takt des Flusses ist die durchschnittliche geschätzte Zeit, nach der ein Produkt oder eine Transportcharge von Produkten in den Fluss eingeführt oder aus dem Fluss freigegeben wird:
Wo, T F-- Arbeitszeitfonds für den Abrechnungszeitraum (Schicht, Tag usw.);
ZU Und- Auslastungsgrad der Ausrüstung unter Berücksichtigung von Ausfallzeiten und Unterbrechungen;
IN P- Volumen der geplanten Produkte für den Abrechnungszeitraum in natürlichen Einheiten (Stück, Meter usw.).
Die Durchflussrate charakterisiert die Arbeitsintensität der Arbeitnehmer und wird durch die Formel bestimmt:
Anzahl der laufenden Jobs:
wobei m die Anzahl der Operationen ist;
wo ist die Standardbetriebszeit;
Wo ist die Komplexität der Herstellung des Produkts?
Bei der Organisation von Produktionsprozessen orientieren wir uns an einer Reihe von Grundsätzen. Die Prinzipien sind verallgemeinerte, gut etablierte und weit verbreitete Techniken und Methoden, die bei der Organisation jedes Systems, einschließlich der Organisation von Produktionsprozessen, verwendet werden. Zu den wichtigsten Grundsätzen der Organisation des Produktionsprozesses gehören die folgenden.
Spezialisierung . Dieses Prinzip der Organisation von Produktionsprozessen setzt eine strikte Arbeitsteilung innerhalb des Unternehmens voraus. In diesem Fall ist eine betriebsinterne Spezialisierung vorgesehen, die die Massenproduktion von Produkten eines begrenzten Sortiments in separaten strukturellen Produktionsabteilungen des Unternehmens oder durch die Durchführung streng definierter Phasen des technologischen Prozesses an Arbeitsplätzen gewährleistet.
Die Spezialisierung kann objektbezogen (für fertige Produkte als Ganzes), detailliert (für die Herstellung einzelner Teile) und operativ (für die Umsetzung eines separaten Vorgangs des technologischen Prozesses) sein. Die Spezialisierung der Produktion sorgt einerseits für eine Steigerung der Effizienz, kann andererseits aber auch negative Folgen haben. Eine Erhöhung des Spezialisierungsgrades führt zu einer Verbesserung der Wirtschaftsindikatoren aufgrund einer Steigerung der Produktion gleichnamiger Produkte, unter anderem durch die Entstehung größerer Möglichkeiten zur Automatisierung von Produktionsprozessen und einer Steigerung der Produktivität der Arbeitnehmer, die dieselben streng spezialisierten Tätigkeiten ausführen Funktionen sowie durch Verbesserung der Qualität der hergestellten Produkte. Gleichzeitig ist die Spezialisierung häufig mit der Monotonie und Monotonie der von den Arbeitnehmern ausgeführten Arbeitsfunktionen verbunden, was dazu führt, dass sie ihre technologische Belastung erhöhen, ihre Fähigkeiten verlieren, das Interesse an der Arbeit verlieren und infolgedessen die Arbeitsproduktivität und das Personal verringern Umsatz. Der Grad der Spezialisierung wird durch das Produktionsprogramm des Unternehmens bestimmt; er wird von Faktoren wie Standardisierung, Normalisierung und Vereinheitlichung von Produktdesigns, Typisierung technologischer Prozesse und ihrer Parameter beeinflusst. Das Spezialisierungsprinzip und seine Einhaltung bestimmen maßgeblich die erfolgreiche Umsetzung anderer Prinzipien der Organisation von Produktionsprozessen.
Kontinuität . Dieses Prinzip setzt eine solche Organisation des Produktionsprozesses voraus, bei der Stopps auf die minimal erforderlichen Werte reduziert werden oder sogar Unterbrechungen bei Anwesenheit des Arbeitsgegenstandes (Rohstoffe, Halbzeuge) in der Verarbeitung vollständig eliminiert werden. Das Prinzip der Kontinuität des Produktionsprozesses trägt dazu bei, Unterbrechungen beim Einsatz menschlicher Arbeitskraft und Produktionsanlagen zu reduzieren, die auf allen Hierarchieebenen beachtet werden müssen: von jedem Arbeitsplatz, Standort, jeder Werkstatt bis hin zum gesamten Unternehmen. Dabei handelt es sich um die Übergabe von Arbeitsgegenständen von einem Betrieb an einen anderen ohne Verzögerungen und Ausfallzeiten von Geräten und Arbeitskräften. Die Umsetzung des Kontinuitätsprinzips, das eine Einsparung der Arbeitszeit der Arbeitnehmer garantiert und die Zeit im „Leerlauf“ der Geräte verkürzt, sorgt für eine Steigerung der Wirtschaftlichkeit der Produktion. Der Grad der Kontinuität des Produktionsprozesses kann anhand der folgenden Indikatoren beurteilt werden:
- - Koeffizient der Nutzlast der Ausrüstung im Laufe der Zeit, der den Grad der Kontinuität der Nutzung von Arbeitswerkzeugen beurteilt;
- - Kontinuitätskoeffizient des Produktionsprozesses, bestimmt durch das Verhältnis der Zeit, die zum Abschluss aller Phasen des technologischen Prozesses erforderlich ist, zur Dauer des Produktionszyklus:
Wo, T R- Dauer der Arbeitszeit;
T ts- die Gesamtdauer des Prozesses, einschließlich der Ausfallzeiten für die Verlegung des Arbeitsgegenstandes zwischen Arbeitsplätzen, an Arbeitsplätzen usw.
Rhythmus . Dies ist eines der wichtigsten Prinzipien der Organisation von Produktionsprozessen. Das bedeutet, dass alle einzelnen Schritte und der gesamte Produktionsprozess zur Herstellung einer bestimmten Anzahl von Produkten nach genau festgelegten Zeiträumen wiederholt werden. Rhythmus drückt sich in der gleichmäßigen Produktion von Produkten oder der Bewegung von Arbeitsgegenständen in gleichen Abständen auf allen Stufen der technologischen Kette sowie in der regelmäßigen Wiederholbarkeit einzelner Vorgänge aus.
Die Einhaltung des Rhythmusprinzips ist bei kooperativen Lieferungen sowie im Hinblick auf die Erfüllung vertraglicher Verpflichtungen zur Lieferung von Produkten innerhalb der streng festgelegten Fristen gemäß dem Vertrag von besonderer Bedeutung. Dieses Prinzip der Organisation des Produktionsprozesses schließt die Möglichkeit der Umsetzung des sogenannten Stormings aus, wenn das Erreichen eines solchen Ziels hinsichtlich der Produktionsmenge auf das Ende des Kalenderzeitraums (die letzten zehn Tage des Monats, der letzte) verschoben wird Monat des Quartals usw.) mit allen daraus resultierenden negativen Konsequenzen.
Der Indikator, der den Grad der Umsetzung dieses Prinzips am besten charakterisiert, ist der Produktionsrhythmus, d.h. Herstellung der gleichen Produktmenge über gleiche Zeiträume. Der Rhythmuskoeffizient wird durch das Verhältnis des tatsächlichen Produktionsvolumens für einen beliebigen Kalenderzeitraum (Jahrzehnt, Monat) innerhalb (nicht höher) des geplanten Ziels zum durch dieses Ziel vorgesehenen Produktionsvolumen bestimmt.
Wo, V F- das tatsächliche Arbeitsvolumen, das für den analysierten Zeitraum (Jahrzehnt, Monat, Quartal) innerhalb des Plans durchgeführt wurde;
V pl- Geplanter Arbeitsumfang.
Verhältnismäßigkeit . Dieses Prinzip der Organisation des Produktionsprozesses setzt die Einhaltung der notwendigen Proportionen, bestimmter Beziehungen zwischen den einzelnen Produktionsstufen sowie zwischen den Haupt-, Hilfs- und Dienstleistungsprozessen voraus. Der Kern dieser Verhältnismäßigkeit besteht vor allem darin, genaue Proportionen zwischen der Höhe der Produktionskapazität sowohl der einzelnen Werkstätten der Hauptproduktion als auch der Kapazität der Produktionsbereiche innerhalb derselben Werkstatt aufrechtzuerhalten. Das Wesen der Verhältnismäßigkeit beruht auf dem Vorhandensein realer Möglichkeiten zur Herstellung einer bestimmten Produktmenge pro Zeiteinheit in allen Phasen des Produktionsprozesses. Ein Verstoß gegen den Grundsatz der Verhältnismäßigkeit führt zum Entstehen sogenannter Engpässe in einer bestimmten Technologiekette, die einerseits das Wachstum der Produktionsmengen hemmen und andererseits zu einer Unterauslastung und Verschlechterung der Nutzung der in anderen Gliedern installierten Ausrüstung führen dieser Kette.
Durch die Ausweitung der bei der Analyse der Auslastung der Produktionskapazität einer Werkstatt (Unternehmens) identifizierten Engpässe und die darauf aufbauende Profilbildung kann eine Erhöhung der Verhältnismäßigkeit der Produktionsprozesse erreicht werden. Die Beseitigung von Engpässen unter Wahrung des Grundsatzes der Verhältnismäßigkeit führt zur Einhaltung der notwendigen Verhältnisse zwischen einzelnen Stufen in einer bestimmten Werkstatt oder zwischen einzelnen Werkstätten (Produktionen) des Unternehmens. Dadurch wird die Wirtschaftlichkeit des Unternehmens durch die Umsetzung der sich in diesem Fall ergebenden Möglichkeiten zur Steigerung des Produktionsvolumens und des Produktabsatzes, zur Verbesserung der Nutzung vorhandener Geräte und zur Steigerung der Arbeitsproduktivität gesteigert.
Die Verhältnismäßigkeit wird durch die Formel bestimmt:
Wo, M Mindest- Mindestdurchsatz oder Betriebsparameter
Orte in der technologischen Kette (z. B. Macht, Art der Arbeit, Umfang und Qualität der Informationen usw.);
M max-- maximale Fähigkeit.
Parallelität . Das Prinzip der Parallelität in der Organisation von Produktionsprozessen beinhaltet die gleichzeitige Ausführung einzelner Phasen des technologischen Prozesses, die zeitliche Kombination der Ausführung von Haupt- und Nebenvorgängen. Dieses Prinzip manifestiert sich unter der Bedingung der gleichzeitigen Verarbeitung mehrerer Einheiten derselben Produkte in verschiedenen Arbeitsgängen und der Durchführung aller Arbeitsgänge zur Herstellung einer oder mehrerer Produktarten an verschiedenen Arbeitsplätzen. Die Erhöhung des Parallelitätsgrades der Vorgänge führt zu einer Verkürzung der Dauer des Produktionszyklus und spart Arbeitszeit.
Der Parallelitätskoeffizient kann nach folgender Formel berechnet werden:
wobei Tc.steam, Tc.seq die Dauer des Prozesses für parallele und sequentielle Kombinationen von Vorgängen ist.
Geradlinigkeit . Dies ist der Grundsatz, nach dem bei der Organisation des Produktionsprozesses auf möglichst kurze Bewegungswege der Arbeitsgegenstände während des Produktionsprozesses geachtet werden muss. Die Bewegung des hergestellten Teils (oder Produkts) durch Arbeitsplätze, Abschnitte und Werkstätten sollte möglichst geradlinig erfolgen und ohne Rück- oder Gegenbewegungen erfolgen. Der direkte Ablauf wird durch die rationelle Platzierung von Werkstätten, Abschnitten, Arbeitsplätzen im Arbeitsablauf und einzelnen Etappen erreicht, d.h. während des technologischen Prozesses.
Der Geradheitskoeffizient kann durch die Formel bestimmt werden
wobei t Transport die Dauer der Transportvorgänge ist;
t technischer Zyklus - Dauer des technologischen Zyklus.
Automatik . Dieses Prinzip setzt eine solche Organisation des gesamten Produktionsprozesses und seiner einzelnen Phasen voraus, die einen möglichst hohen Grad an Automatisierung bzw. Mechanisierung gewährleistet. Zur Herstellung besonders komplexer und arbeitsintensiver Produktarten gibt es viele technologische Verfahren, deren Umsetzung ohne deren Automatisierung grundsätzlich nicht möglich ist, d.h. technisch nicht machbar. Einige Produktionsprozesse sind zwar grundsätzlich manuell durchführbar, führen aber durch Automatisierung zu einer Erhöhung des technischen Produktionsniveaus und auf dieser Grundlage zu einer Verringerung der Arbeitsintensität der Produktion, einer Verringerung der Verletzungen der Arbeitnehmer und einer Erhöhung der Qualität der hergestellten Produkte. Die Lösung wirtschaftlicher Probleme durch die Automatisierung von Produktionsprozessen ist trotz der relativ hohen Kapitalintensität (der Notwendigkeit, große Investitionen anzuziehen) der Automatisierung darauf ausgerichtet, einen erheblichen wirtschaftlichen Effekt zu erzielen und dadurch eine kurze Kapitalrendite zu erzielen und a deutliche Steigerung der Wirtschaftlichkeit automatisierter Produktionsprozesse. Die gesellschaftlichen Folgen der Umsetzung des Prinzips der Automatisierung und Mechanisierung von Produktionsprozessen äußern sich erstens in einer Veränderung der Art der Arbeit der Arbeitnehmer, zweitens in einer deutlichen Erhöhung der Entlohnung ihrer Arbeit, drittens in einer Verbesserung der Arbeitsbedingungen, insbesondere in gefährlichen Industrien, viertens bei der Erhöhung der Sicherheit, einschließlich der Umweltsicherheit, der Produktion.
Flexibilität . Das Prinzip der Flexibilität bei der Organisation von Produktionsprozessen besteht darin, dass die Produktion teilweise so organisiert werden muss, dass sie sich als Reaktion auf Marktanforderungen schnell an die Produktion neuer Produkte anpassen kann. Unter Flexibilität ist die Fähigkeit eines Produktionsprozesses zu verstehen:
- - Änderungen im Produktsortiment, Produktionsvolumen;
- - notwendige Änderungen der Prozessparameter;
- - die Fähigkeit der Haupt- und Hilfsausrüstung, auf andere Arbeitsarten umzustellen;
- - notwendige Änderungen des Qualifikationsniveaus und -profils der Arbeitskräfte.
Optimalität . Mit diesem Prinzip der Organisation von Produktionsprozessen ist in erster Linie die Notwendigkeit verbunden, diese zu optimieren, was sich in der Möglichkeit ausdrückt, für jede einzelne Produktion solche Organisationsprinzipien auszuwählen, die in ihrer Kombination ein Höchstmaß an Wirtschaftlichkeit gewährleisten.
Eine Möglichkeit, die aufgeführten Prinzipien der rationellen Organisation von Produktionsprozessen zu verbessern, besteht darin, die Wiederholbarkeit von Prozessen und Abläufen zu erhöhen. Ihre möglichst vollständige Umsetzung wird durch eine optimale Kombination folgender Faktoren erreicht:
- Produktionsumfang;
- · Komplexität der Nomenklatur und Produktpalette;
- · Art des Betriebs der Technologie- und Transportausrüstung;
- · Aggregatzustand und Form der Ausgangsmaterialien;
- · Art und Reihenfolge der technologischen Auswirkungen auf das Thema Arbeit usw.