Grundsätze der Organisation des Produktionsprozesses. Der Produktionsprozess ist eine Gesamtheit von miteinander in Beziehung stehenden Haupt-, Hilfs- und Dienstleistungsprozessen von Arbeits- und Naturprozessen
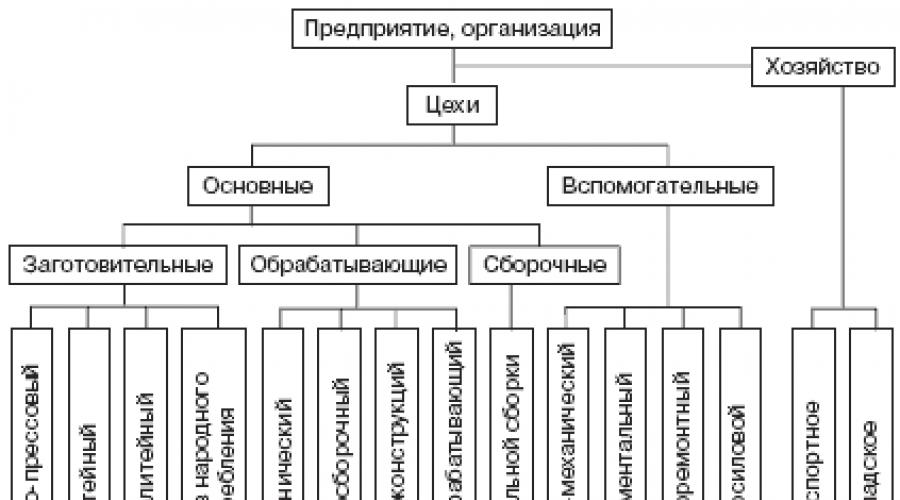
Lesen Sie auch
Turovets O.G., Rodionov V.B., Bukhalkov M.I. Kapitel aus dem Buch "Organisation der Produktion und Unternehmensführung"
Verlag "INFRA-M", 2007
10.1. Das Konzept des Produktionsprozesses
Die moderne Produktion ist ein komplexer Prozess der Umwandlung von Rohstoffen, Materialien, Halbfertigprodukten und anderen Arbeitsgegenständen in fertige Produkte, die den Bedürfnissen der Gesellschaft entsprechen.
Die Gesamtheit aller Handlungen von Menschen und Werkzeugen, die im Unternehmen zur Herstellung bestimmter Arten von Produkten ausgeführt werden, wird als bezeichnet Fertigungsprozess.
Der Hauptteil des Produktionsprozesses sind technologische Prozesse, die gezielte Aktionen zur Veränderung und Bestimmung des Zustands von Arbeitsgegenständen beinhalten. Im Zuge der Umsetzung technologischer Prozesse verändern sich die geometrischen Formen, Größen sowie physikalischen und chemischen Eigenschaften der Arbeitsgegenstände.
Er umfasst neben dem technologischen Produktionsprozess auch nichttechnologische Prozesse, die nicht darauf abzielen, die geometrischen Formen, Größen oder physikalisch-chemischen Eigenschaften der Arbeitsgegenstände zu verändern oder deren Qualität zu überprüfen. Zu solchen Prozessen gehören Transport, Lagerung, Be- und Entladen, Kommissionierung und einige andere Vorgänge und Prozesse.
Im Produktionsprozess werden Arbeitsprozesse mit natürlichen kombiniert, bei denen die Veränderung der Arbeitsgegenstände unter dem Einfluss der Naturkräfte ohne menschliches Zutun erfolgt (z. B. Trocknen von lackierten Teilen an der Luft, Abkühlen von Gussteilen, Altern von Gussteilen). , usw.).
Varianten von Produktionsprozessen. Prozesse werden nach ihrem Zweck und ihrer Rolle in der Produktion in Haupt-, Hilfs- und Serviceprozesse eingeteilt.
Hauptsächlich werden Produktionsprozesse genannt, bei denen die Herstellung der Hauptprodukte des Unternehmens durchgeführt wird. Das Ergebnis der Hauptprozesse im Maschinenbau ist die Herstellung von Maschinen, Apparaten und Instrumenten, die das Produktionsprogramm des Unternehmens ausmachen und seiner Spezialisierung entsprechen, sowie die Herstellung von Ersatzteilen für diese zur Lieferung an den Verbraucher.
ZU Hilfs- umfassen Prozesse, die den ununterbrochenen Ablauf grundlegender Prozesse sicherstellen. Ihr Ergebnis sind die im Unternehmen selbst eingesetzten Produkte. Hilfsmittel sind die Prozesse zur Reparatur von Geräten, die Herstellung von Geräten, die Erzeugung von Dampf und Druckluft usw.
Portion Prozesse werden aufgerufen, während deren Implementierung die für das normale Funktionieren sowohl des Haupt- als auch des Hilfsprozesses erforderlichen Dienste ausgeführt werden. Dazu gehören beispielsweise die Prozesse des Transports, der Lagerhaltung, der Auswahl und Kommissionierung von Teilen usw.
Unter modernen Bedingungen, insbesondere in der automatisierten Produktion, besteht die Tendenz zur Integration der Haupt- und Serviceprozesse. In flexiblen automatisierten Komplexen werden also Haupt-, Kommissionier-, Lager- und Transportvorgänge in einem einzigen Prozess kombiniert.
Die Menge der Grundprozesse bildet die Hauptproduktion. In Maschinenbauunternehmen besteht die Hauptproduktion aus drei Phasen: Beschaffung, Verarbeitung und Montage. Bühne Der Produktionsprozess ist ein Komplex von Prozessen und Arbeiten, deren Ausführung den Abschluss eines bestimmten Teils des Produktionsprozesses kennzeichnet und mit dem Übergang des Arbeitsgegenstands von einem qualitativen Zustand in einen anderen verbunden ist.
ZU Beschaffung Phasen umfassen die Prozesse zur Gewinnung von Rohlingen - Schneidmaterialien, Gießen, Stanzen. wird bearbeitet Die Phase umfasst die Prozesse der Umwandlung von Rohlingen in fertige Teile: Bearbeitung, Wärmebehandlung, Lackierung und Galvanisierung usw. Montage Stufe - der letzte Teil des Produktionsprozesses. Es umfasst die Montage von Einheiten und Fertigprodukten, die Einstellung und Fehlerbeseitigung von Maschinen und Instrumenten sowie deren Prüfung.
Die Zusammensetzung und Verflechtung der Haupt-, Hilfs- und Dienstprozesse bilden die Struktur des Produktionsprozesses.
Organisatorisch werden Produktionsprozesse in einfache und komplexe Prozesse eingeteilt. Einfach Produktionsprozesse genannt, die aus nacheinander ausgeführten Handlungen an einem einfachen Arbeitsgegenstand bestehen. Zum Beispiel der Produktionsprozess der Herstellung eines einzelnen Teils oder einer Charge identischer Teile. Schwierig Prozess ist eine Kombination einfacher Prozesse, die an einer Vielzahl von Arbeitsobjekten durchgeführt werden. Zum Beispiel der Prozess der Herstellung einer Baugruppe oder eines ganzen Produkts.
10.2. Wissenschaftliche Prinzipien der Organisation von Produktionsprozessen
Tätigkeiten zur Organisation von Produktionsprozessen. Vielfältige Produktionsprozesse, die zur Herstellung von Industrieprodukten führen, müssen ordnungsgemäß organisiert werden, um ihr effektives Funktionieren zu gewährleisten, um bestimmte Arten von Produkten von hoher Qualität und in Mengen herzustellen, die den Bedürfnissen der Volkswirtschaft und der Bevölkerung des Landes entsprechen .
Die Organisation von Produktionsprozessen besteht darin, Menschen, Werkzeuge und Arbeitsgegenstände zu einem einzigen Prozess zur Herstellung materieller Güter zusammenzufassen, sowie eine räumlich und zeitlich rationelle Verknüpfung der Haupt-, Hilfs- und Dienstleistungsprozesse sicherzustellen.
Die räumliche Kombination von Elementen des Produktionsprozesses und all seiner Varianten erfolgt auf der Grundlage der Bildung der Produktionsstruktur des Unternehmens und seiner konstituierenden Einheiten. Die wichtigsten Aktivitäten in dieser Hinsicht sind die Auswahl und Begründung der Produktionsstruktur des Unternehmens, d.h. Bestimmung der Zusammensetzung und Spezialisierung seiner konstituierenden Einheiten und Herstellung rationaler Beziehungen zwischen ihnen.
Während der Entwicklung der Produktionsstruktur werden Konstruktionsberechnungen im Zusammenhang mit der Bestimmung der Zusammensetzung des Geräteparks unter Berücksichtigung seiner Produktivität, Austauschbarkeit und der Möglichkeit einer effektiven Nutzung durchgeführt. Rationelle Planung von Abteilungen, Platzierung von Ausrüstung und Arbeitsplätzen werden ebenfalls entwickelt. Es werden organisatorische Bedingungen für den reibungslosen Betrieb von Geräten und direkten Teilnehmern am Produktionsprozess - Arbeitern - geschaffen.
Einer der Hauptaspekte bei der Bildung der Produktionsstruktur ist die Sicherstellung des miteinander verbundenen Funktionierens aller Komponenten des Produktionsprozesses: vorbereitende Operationen, grundlegende Produktionsprozesse, Wartung. Es ist notwendig, die rationellsten Organisationsformen und Methoden zur Umsetzung bestimmter Prozesse für bestimmte Produktions- und technische Bedingungen umfassend zu begründen.
Ein wichtiges Element in der Organisation von Produktionsprozessen ist die Organisation der Arbeit der Arbeiter, die die Verbindung der Arbeitskraft mit den Produktionsmitteln konkret verwirklicht. Die Methoden der Arbeitsorganisation werden weitgehend durch die Formen des Produktionsprozesses bestimmt. Dabei sollte der Fokus darauf liegen, eine rationelle Arbeitsteilung zu gewährleisten und auf dieser Grundlage die fachliche und qualifizierte Zusammensetzung der Arbeitskräfte, die wissenschaftliche Organisation und optimale Erhaltung der Arbeitsplätze sowie die allseitige Verbesserung und Verbesserung der Arbeitsbedingungen zu bestimmen.
Die Organisation von Produktionsprozessen impliziert auch eine zeitliche Kombination ihrer Elemente, die eine bestimmte Reihenfolge für die Ausführung einzelner Vorgänge, eine rationale Kombination der Zeit für die Ausführung verschiedener Arten von Arbeiten und die Festlegung von Kalender- und Planungsstandards für die Bewegung von festlegt Gegenstände der Arbeit. Der normale zeitliche Ablauf der Prozesse wird auch durch die Reihenfolge der Produkteinführungsfreigabe, die Bildung der erforderlichen Lager (Reserven) und Produktionsreserven, die ununterbrochene Versorgung der Arbeitsplätze mit Werkzeugen, Rohlingen, Materialien sichergestellt. Eine wichtige Richtung dieser Tätigkeit ist die Organisation der rationellen Bewegung von Materialströmen. Diese Aufgaben werden auf der Grundlage der Entwicklung und Implementierung von Systemen zur betrieblichen Produktionsplanung unter Berücksichtigung der Produktionsart und der technischen und organisatorischen Besonderheiten der Produktionsprozesse gelöst.
Schließlich wird im Zuge der Organisation von Produktionsprozessen in einem Unternehmen der Entwicklung eines Systems für das Zusammenwirken einzelner Produktionseinheiten ein wichtiger Stellenwert eingeräumt.
Grundsätze der Organisation des Produktionsprozesses sind die Ausgangspunkte, auf deren Basis Aufbau, Betrieb und Entwicklung von Produktionsprozessen erfolgen.
Prinzip Differenzierung beinhaltet die Aufteilung des Produktionsprozesses in einzelne Teile (Prozesse, Arbeitsgänge) und deren Zuordnung zu den entsprechenden Abteilungen des Unternehmens. Das Differenzierungsprinzip steht dem Prinzip entgegen Kombinationen, d. h. die Kombination aller oder eines Teils verschiedener Prozesse zur Herstellung bestimmter Arten von Produkten innerhalb desselben Standorts, derselben Werkstatt oder Produktion. Abhängig von der Komplexität des Produkts, dem Produktionsvolumen und der Art der verwendeten Ausrüstung kann der Produktionsprozess in einer Produktionseinheit (Werkstatt, Abschnitt) konzentriert oder auf mehrere Einheiten verteilt werden. So werden in Maschinenbauunternehmen mit einer bedeutenden Produktion der gleichen Art von Produkten unabhängige mechanische und Montagewerkstätten organisiert, und mit kleinen Chargen hergestellter Produkte können einheitliche mechanische Montagewerkstätten geschaffen werden.
Die Grundsätze der Differenzierung und Kombination gelten auch für einzelne Jobs. Eine Produktionslinie ist beispielsweise eine differenzierte Reihe von Arbeitsplätzen.
Bei praktischen Tätigkeiten zur Organisation der Produktion sollte bei der Anwendung der Prinzipien der Differenzierung oder Kombination dem Prinzip Vorrang eingeräumt werden, das die besten wirtschaftlichen und sozialen Eigenschaften des Produktionsprozesses liefert. Somit ermöglicht die Inline-Produktion, die durch einen hohen Differenzierungsgrad des Produktionsprozesses gekennzeichnet ist, eine Vereinfachung seiner Organisation, eine Verbesserung der Fähigkeiten der Arbeiter und eine Steigerung der Arbeitsproduktivität. Eine übermäßige Differenzierung erhöht jedoch die Ermüdung der Mitarbeiter, eine große Anzahl von Arbeitsgängen erhöht den Bedarf an Ausrüstung und Produktionsfläche, führt zu unnötigen Kosten für bewegliche Teile usw.
Prinzip Konzentration bezeichnet die Konzentration bestimmter Produktionsbetriebe zur Herstellung technologisch einheitlicher Produkte oder zur Erbringung funktional einheitlicher Arbeiten an getrennten Arbeitsplätzen, Abteilungen, Werkstätten oder Produktionsstätten des Unternehmens. Die Zweckmäßigkeit der Konzentration homogener Arbeit in getrennten Produktionsbereichen beruht auf folgenden Faktoren: der Gemeinsamkeit technologischer Methoden, die die Verwendung derselben Art von Ausrüstung erfordern; Ausrüstungsmöglichkeiten, wie Bearbeitungszentren; eine Steigerung der Produktion bestimmter Arten von Produkten; die wirtschaftliche Machbarkeit der Konzentration der Produktion bestimmter Arten von Produkten oder der Durchführung ähnlicher Arbeiten.
Bei der Wahl der einen oder anderen Konzentrationsrichtung müssen die Vorteile jeder von ihnen berücksichtigt werden.
Mit der Konzentration technologisch einheitlicher Arbeit in der Unterabteilung wird weniger Duplizierausrüstung benötigt, die Flexibilität der Produktion steigt und es wird möglich, schnell auf die Produktion neuer Produkte umzustellen, und die Belastung der Ausrüstung steigt.
Durch die Konzentration technologisch einheitlicher Produkte werden die Transportkosten für Materialien und Produkte reduziert, die Dauer des Produktionszyklus verkürzt, die Verwaltung des Produktionsprozesses vereinfacht und der Bedarf an Produktionsfläche verringert.
Prinzip Spezialisierungen basierend auf der Begrenzung der Vielfalt der Elemente des Produktionsprozesses. Zur Umsetzung dieses Prinzips wird jedem Arbeitsplatz und jeder Abteilung ein streng begrenztes Spektrum an Arbeiten, Arbeitsgängen, Teilen oder Produkten zugeordnet. Im Gegensatz zum Spezialisierungsprinzip impliziert das Universalisierungsprinzip eine solche Produktionsorganisation, bei der jeder Arbeitsplatz oder jede Produktionseinheit mit der Herstellung von Teilen und Produkten einer breiten Palette oder der Durchführung heterogener Produktionsvorgänge beschäftigt ist.
Der Spezialisierungsgrad der Arbeitsplätze wird durch einen speziellen Indikator bestimmt - den Konsolidierungskoeffizienten der Operationen ZU z.o., die durch die Anzahl der am Arbeitsplatz für einen bestimmten Zeitraum durchgeführten Detailoperationen gekennzeichnet ist. Ja, bei ZU z.o = 1 gibt es eine enge Spezialisierung von Arbeitsplätzen, in denen während des Monats, des Quartals eine Detailoperation am Arbeitsplatz durchgeführt wird.
Die Art der Spezialisierung von Abteilungen und Arbeitsplätzen wird maßgeblich durch das Produktionsvolumen gleichnamiger Teile bestimmt. Nein Höchststufe Die Spezialisierung erfolgt bei der Herstellung einer Produktart. Das typischste Beispiel für hochspezialisierte Industrien sind Fabriken zur Herstellung von Traktoren, Fernsehern und Autos. Eine Erweiterung des Produktionsspektrums verringert den Spezialisierungsgrad.
Ein hoher Spezialisierungsgrad von Abteilungen und Arbeitsplätzen trägt zur Steigerung der Arbeitsproduktivität bei, da sich die Arbeitsfähigkeiten der Arbeitnehmer entwickeln, die Möglichkeit der technischen Ausrüstung der Arbeitskräfte besteht und die Kosten für die Neukonfiguration von Maschinen und Linien minimiert werden. Gleichzeitig verringert eine enge Spezialisierung die erforderlichen Qualifikationen der Arbeitnehmer, führt zu Arbeitsmonotonie und führt folglich zu einer schnellen Ermüdung der Arbeitnehmer und schränkt ihre Initiative ein.
Unter modernen Bedingungen nimmt die Tendenz zur Universalisierung der Produktion zu, was durch die Anforderungen des wissenschaftlichen und technologischen Fortschritts zur Erweiterung der Produktpalette, das Aufkommen multifunktionaler Geräte und die Aufgaben zur Verbesserung der Arbeitsorganisation in der Richtung bestimmt wird der Erweiterung der Arbeitsfunktionen des Arbeiters.
Prinzip Verhältnismäßigkeit besteht in einer regelmäßigen Kombination einzelner Elemente des Produktionsprozesses, die sich in einem bestimmten quantitativen Verhältnis zueinander ausdrückt. Die Proportionalität in Bezug auf die Produktionskapazität impliziert also die Gleichheit der Kapazitäten der Abschnitte oder der Auslastungsfaktoren der Ausrüstung. Dabei entspricht der Durchsatz der Beschaffungswerkstätten dem Rohlingsbedarf in den Maschinenwerkstätten und der Durchsatz dieser Werkstätten dem Bedarf der Montagewerkstatt an den benötigten Teilen. Dies impliziert die Anforderung, dass in jeder Werkstatt Ausrüstung, Platz und Arbeitskräfte in einer solchen Menge vorhanden sein müssen, dass der normale Betrieb aller Abteilungen des Unternehmens gewährleistet ist. Zwischen der Hauptproduktion einerseits und den Neben- und Serviceeinheiten andererseits soll das gleiche Durchsatzverhältnis bestehen.
Ein Verstoß gegen den Grundsatz der Verhältnismäßigkeit führt zu Missverhältnissen, dem Auftreten von Produktionsengpässen, wodurch sich der Einsatz von Ausrüstung und Arbeitskräften verschlechtert, die Dauer des Produktionszyklus zunimmt und der Rückstand zunimmt.
Die Verhältnismäßigkeit von Arbeitskräften, Raum und Ausrüstung wird bereits bei der Gestaltung des Unternehmens festgelegt und dann bei der Entwicklung der jährlichen Produktionspläne durch die Durchführung sogenannter volumetrischer Berechnungen verfeinert - bei der Bestimmung von Kapazitäten, der Anzahl der Mitarbeiter und des Bedarfs Materialien. Proportionen werden auf der Grundlage eines Systems von Normen und Normen festgelegt, die die Anzahl der gegenseitigen Beziehungen zwischen verschiedenen Elementen des Produktionsprozesses bestimmen.
Der Grundsatz der Verhältnismäßigkeit impliziert die gleichzeitige Ausführung einzelner Vorgänge oder Teile des Produktionsprozesses. Es basiert auf der Prämisse, dass die Teile eines zerstückelten Produktionsprozesses zeitlich kombiniert und gleichzeitig ausgeführt werden müssen.
Der Produktionsprozess zur Herstellung einer Maschine besteht aus einer Vielzahl von Arbeitsgängen. Es liegt auf der Hand, dass eine sequentielle Ausführung nacheinander zu einer Verlängerung der Dauer des Produktionszyklus führen würde. Daher müssen die einzelnen Teile des Produktherstellungsprozesses parallel durchgeführt werden.
Parallelität erreicht: bei Bearbeitung eines Teils auf einer Maschine mit mehreren Werkzeugen; gleichzeitige Bearbeitung verschiedener Teile einer Charge für einen bestimmten Arbeitsgang an mehreren Arbeitsplätzen; gleichzeitige Bearbeitung gleicher Teile für verschiedene Arbeitsgänge an mehreren Arbeitsplätzen; Gleichzeitige Produktion verschiedener Teile desselben Produkts an verschiedenen Arbeitsplätzen. Die Einhaltung des Parallelitätsprinzips führt zu einer Reduzierung der Produktionszyklusdauer und des Zeitaufwands für Teile, um Arbeitszeit zu sparen.
Unter direkten Fluss ein solches Prinzip der Organisation des Produktionsprozesses verstehen, nach dem alle Stufen und Operationen des Produktionsprozesses unter den Bedingungen des kürzesten Weges des Arbeitsgegenstands vom Beginn des Prozesses bis zu seinem Ende durchgeführt werden. Das Prinzip des direkten Flusses erfordert die Sicherstellung der geradlinigen Bewegung der Arbeitsgegenstände im technologischen Prozess, wobei verschiedene Arten von Schleifen und Rückbewegungen eliminiert werden.
Volle Unmittelbarkeit kann durch räumliche Anordnung von Arbeitsgängen und Teilen des Produktionsprozesses in der Reihenfolge der technologischen Arbeitsgänge erreicht werden. Bei der Gestaltung von Unternehmen ist es auch erforderlich, die Anordnung von Werkstätten und Dienstleistungen in einer Reihenfolge zu erreichen, die einen Mindestabstand zwischen benachbarten Einheiten vorsieht. Es sollte angestrebt werden sicherzustellen, dass die Teile und Baugruppen verschiedener Produkte die gleiche oder ähnliche Abfolge von Stufen und Arbeitsgängen des Produktionsprozesses aufweisen. Bei der Umsetzung des Direktflussprinzips stellt sich auch das Problem der optimalen Anordnung von Geräten und Arbeitsplätzen.
Das Prinzip des direkten Flusses manifestiert sich in stärkerem Maße in den Bedingungen der Inline-Produktion bei der Schaffung von themengeschlossenen Werkstätten und Abschnitten.
Die Einhaltung der Anforderungen des direkten Flusses führt zu einer Rationalisierung der Frachtströme, einer Reduzierung des Frachtumsatzes und einer Reduzierung der Kosten für den Transport von Materialien, Teilen und Fertigprodukten.
Prinzip Rhythmus bedeutet, dass alle einzelnen Produktionsprozesse und ein einzelner Prozess zur Herstellung eines bestimmten Produkttyps nach festgelegten Zeiträumen wiederholt werden. Unterscheiden Sie den Rhythmus von Output, Arbeit, Produktion.
Der Freisetzungsrhythmus ist die Freisetzung der gleichen oder gleichmäßig ansteigenden (abnehmenden) Produktmenge in gleichen Zeitintervallen. Der Arbeitsrhythmus ist die Ausführung gleicher Arbeitsmengen (in Menge und Zusammensetzung) für gleiche Zeitintervalle. Der Produktionsrhythmus bedeutet die Einhaltung des Produktionsrhythmus und des Arbeitsrhythmus.
Rhythmisches Arbeiten ohne Ruckeln und Stürme ist die Basis für steigende Arbeitsproduktivität, optimale Geräteauslastung, vollen Personaleinsatz und Garant für qualitativ hochwertiges Output. Der reibungslose Betrieb des Unternehmens hängt von einer Reihe von Bedingungen ab. Die Sicherstellung des Rhythmus ist eine komplexe Aufgabe, die die Verbesserung der gesamten Produktionsorganisation im Unternehmen erfordert. Von größter Bedeutung sind die richtige Organisation der betrieblichen Produktionsplanung, die Beachtung der Verhältnismäßigkeit der Produktionskapazitäten, die Verbesserung der Produktionsstruktur, die ordnungsgemäße Organisation der materiellen und technischen Versorgung und Aufrechterhaltung der Produktionsprozesse.
Prinzip Kontinuität Sie verwirklicht sich in solchen Organisationsformen des Produktionsprozesses, in denen alle seine Operationen kontinuierlich und ohne Unterbrechungen durchgeführt werden und alle Arbeitsgegenstände ständig von Operation zu Operation wandern.
Das Prinzip der Kontinuität des Produktionsprozesses wird vollständig auf automatischen und kontinuierlichen Produktionslinien verwirklicht, auf denen Arbeitsgegenstände hergestellt oder montiert werden, die Arbeitsgänge von gleicher Dauer oder einem Vielfachen der Taktzeit der Linie haben.
Im Maschinenbau überwiegen diskrete technologische Prozesse, daher ist hier eine Produktion mit einem hohen Grad an Synchronisation der Betriebsdauer nicht vorherrschend.
Die diskontinuierliche Bewegung von Arbeitsgegenständen ist mit Pausen verbunden, die durch die Alterung von Teilen bei jedem Arbeitsgang zwischen Arbeitsgängen, Abschnitten, Werkstätten entstehen. Deshalb erfordert die Umsetzung des Kontinuitätsprinzips die Beseitigung oder Minimierung von Unterbrechungen. Die Lösung eines solchen Problems kann auf der Grundlage der Beachtung der Grundsätze der Verhältnismäßigkeit und des Rhythmus erreicht werden; Organisation der parallelen Produktion von Teilen einer Charge oder verschiedener Teile eines Produkts; Schaffung solcher Organisationsformen von Produktionsprozessen, bei denen die Startzeit der Herstellung von Teilen für einen bestimmten Vorgang und die Endzeit des vorherigen Vorgangs synchronisiert werden usw.
Die Verletzung des Kontinuitätsprinzips führt in der Regel zu Arbeitsunterbrechungen (Ausfallzeiten von Arbeitern und Ausrüstung), zu einer Verlängerung der Dauer des Produktionszyklus und der Größe der laufenden Arbeiten.
Die Prinzipien der Produktionsorganisation wirken in der Praxis nicht isoliert, sie sind in jedem Produktionsprozess eng miteinander verflochten. Beim Studium der Organisationsprinzipien sollte darauf geachtet werden Paar Charakter einige von ihnen, ihre Verknüpfung, gehen in ihr Gegenteil über (Differenzierung und Kombination, Spezialisierung und Universalisierung). Die Organisationsprinzipien entwickeln sich ungleichmäßig: In der einen oder anderen Periode tritt ein Prinzip in den Vordergrund oder gewinnt an sekundärer Bedeutung. Die enge Spezialisierung der Berufe gehört damit der Vergangenheit an, sie werden immer universeller. Das Prinzip der Differenzierung wird zunehmend durch das Prinzip der Kombination ersetzt, dessen Nutzung es ermöglicht, einen Produktionsprozess auf der Basis eines einzigen Stroms aufzubauen. Gleichzeitig nimmt unter den Bedingungen der Automatisierung die Bedeutung der Prinzipien der Proportionalität, der Kontinuität und des direkten Flusses zu.
Der Umsetzungsgrad der Grundsätze der Produktionsorganisation hat eine quantitative Dimension. Daher sollten zusätzlich zu den bestehenden Methoden der Produktionsanalyse Formen und Methoden zur Analyse des Zustands der Produktionsorganisation und zur Umsetzung ihrer wissenschaftlichen Prinzipien entwickelt und in der Praxis angewendet werden. Methoden zur Berechnung des Umsetzungsgrades einiger Prinzipien der Organisation von Produktionsprozessen werden in Kap. 20.
Die Einhaltung der Grundsätze der Organisation von Produktionsprozessen ist von großer Bedeutung praktischer Wert. Die Umsetzung dieser Grundsätze ist Aufgabe aller Ebenen des Produktionsmanagements.
10.3. Räumliche Organisation von Produktionsprozessen
Die Produktionsstruktur des Unternehmens. Die Kombination von Teilen des Produktionsprozesses im Weltraum wird durch die Produktionsstruktur des Unternehmens bereitgestellt. Unter der Produktionsstruktur versteht man die Gesamtheit der Produktionseinheiten des Unternehmens, die Teil davon sind, sowie die Formen der Beziehungen zwischen ihnen. Unter modernen Bedingungen kann der Produktionsprozess in seinen zwei Varianten betrachtet werden:
- als Prozess der Materialherstellung mit dem Endergebnis - marktfähige Produkte;
- als Prozess der Designproduktion mit dem Endergebnis - einem wissenschaftlich-technischen Produkt.
Die Art der Produktionsstruktur des Unternehmens hängt von der Art seiner Aktivitäten ab, von denen die wichtigsten folgende sind: Forschung, Produktion, Forschung und Produktion, Produktion und Technik, Management und Wirtschaft.
Die Priorität der relevanten Aktivitäten bestimmt die Struktur des Unternehmens, den Anteil der wissenschaftlichen, technischen und Produktionseinheiten, das Verhältnis der Anzahl der Arbeiter und Ingenieure.
Die Zusammensetzung der Abteilungen eines auf Produktionstätigkeiten spezialisierten Unternehmens wird durch die Konstruktionsmerkmale der hergestellten Produkte und die Technologie ihrer Herstellung, den Produktionsumfang, die Spezialisierung des Unternehmens und die bestehenden genossenschaftlichen Beziehungen bestimmt. Auf Abb. 10.1 zeigt ein Diagramm der Beziehung von Faktoren, die die Produktionsstruktur des Unternehmens bestimmen.
Reis. 10.1. Schema der Wechselbeziehungen von Faktoren, die die Produktionsstruktur eines Unternehmens bestimmen
Unter modernen Bedingungen hat die Eigentumsform einen großen Einfluss auf die Struktur des Unternehmens. Der Übergang vom Staat zu anderen Eigentumsformen – Privat, Aktiengesellschaft, Pacht – führt in der Regel zu einer Reduzierung überflüssiger Verknüpfungen und Strukturen, der Größe des Kontrollapparates und zu einer Reduzierung von Doppelarbeit.
Gegenwärtig sind verschiedene Formen der Unternehmensorganisation weit verbreitet; Es gibt kleine, mittlere und große Unternehmen, deren Produktionsstruktur die entsprechenden Merkmale aufweist.
Die Produktionsstruktur eines kleinen Unternehmens ist einfach. Sie verfügt in der Regel über eine minimale oder gar keine internen strukturellen Produktionseinheiten. In kleinen Unternehmen ist der Verwaltungsapparat unbedeutend und die Kombination von Führungsfunktionen weit verbreitet.
Die Struktur mittelständischer Unternehmen setzt die Zuordnung von Werkstätten in ihrer Zusammensetzung und bei einer Nicht-Ladenstruktur von Abteilungen voraus. Hier werden bereits das für das Funktionieren des Unternehmens erforderliche Minimum, eigene Hilfs- und Serviceeinheiten, Abteilungen und Dienste des Verwaltungsapparates geschaffen.
Große Unternehmen der verarbeitenden Industrie umfassen die gesamte Bandbreite der Produktions-, Dienstleistungs- und Verwaltungsabteilungen.
Auf der Grundlage der Produktionsstruktur wird ein Gesamtplan des Unternehmens entwickelt. Der Masterplan bezieht sich auf die räumliche Anordnung aller Geschäfte und Dienstleistungen sowie Verkehrswege und Kommunikationen auf dem Territorium des Unternehmens. Bei der Entwicklung eines Masterplans wird der direkte Materialfluss sichergestellt. Die Werkstätten sollten entsprechend dem Ablauf des Produktionsprozesses angesiedelt sein. Dienstleistungen und miteinander verbundene Werkstätten müssen in unmittelbarer Nähe platziert werden.
Entwicklung der Produktionsstruktur von Verbänden. Die Produktionsstrukturen von Verbänden unter modernen Bedingungen unterliegen erheblichen Veränderungen. Produktionsverbände im produzierenden Gewerbe, insbesondere im Maschinenbau, zeichnen sich durch folgende Bereiche zur Verbesserung der Produktionsstrukturen aus:
- Konzentration der Produktion gleichartiger Produkte oder Erbringung gleichartiger Arbeiten in einzelnen Fachabteilungen des Vereins;
- Vertiefung der Spezialisierung der strukturellen Abteilungen von Unternehmen - Industrien, Werkstätten, Branchen;
- Integration in einheitliche Forschungs- und Produktionskomplexe der Arbeit zur Schaffung neuer Produkttypen, ihrer Entwicklung in der Produktion und der Organisation der Produktion in den für den Verbraucher erforderlichen Mengen;
- Streuung der Produktion durch Gründung hochspezialisierter Unternehmen unterschiedlicher Größe im Rahmen des Verbandes;
- Überwindung der Segmentierung beim Aufbau von Produktionsprozessen und Schaffung einheitlicher Produktionsabläufe ohne Zuweisung von Werkstätten, Standorten;
- Universalisierung der Produktion, die in der Herstellung von Produkten für unterschiedliche Zwecke besteht, die aus in Design und Technologie homogenen Komponenten und Teilen vervollständigt werden, sowie in der Organisation der Produktion verwandter Produkte;
- breite Entwicklung der horizontalen Zusammenarbeit zwischen Unternehmen, die verschiedenen Verbänden angehören, um die Produktionskosten durch Erhöhung des Produktionsumfangs der gleichen Art von Produkten und volle Kapazitätsauslastung zu senken.
Die Gründung und Entwicklung großer Verbände hat eine neue Form der Produktionsstruktur ins Leben gerufen, die sich durch die Zuordnung spezialisierter Industrien optimaler Größe in ihrer Zusammensetzung auszeichnet, die auf dem Prinzip der technologischen und fachlichen Spezialisierung aufbauen. Eine solche Struktur sorgt auch für eine maximale Konzentration von Beschaffungs-, Hilfs- und Serviceprozessen. Die neue Form der Produktionsstruktur hieß Multiproduktion. In den 1980er Jahren war es in der Automobil-, Elektro- und anderen Industrien weit verbreitet.
Der Verband der Automobilproduktion Nischni Nowgorod beispielsweise umfasst eine Muttergesellschaft und sieben Tochterwerke. Der Stammbetrieb verfügt über zehn spezialisierte Produktionsstätten: LKW, PKW, Motoren, LKW-Achsen, Hüttenwesen, Schmieden und Federn, Werkzeugbau usw. Jede dieser Branchen vereint eine Gruppe von Haupt- und Hilfswerkstätten, hat eine gewisse Eigenständigkeit, behält sich diese vor enge Beziehungen mit anderen Unternehmensbereichen und genießt die für die Struktureinheiten des Verbandes festgelegten Rechte. Eine typische Produktionsstruktur ist in Abb. 1 dargestellt. 10.2.
Auf einem höheren Qualitätsniveau wurde im Wolga-Automobilwerk eine Multi-Produktionsstruktur implementiert. Die Herstellung von Automobilen konzentriert sich hier auf vier Hauptindustrien: Metallurgie, Pressen, mechanische Montage sowie Montage und Schmieden. Darüber hinaus wurden auch Nebenproduktionsanlagen identifiziert. Jedes von ihnen ist ein eigenständiges Werk mit einem geschlossenen Produktionskreislauf. Die Struktur der Produktion umfasst Werkstätten. Doch die Werkstätten im VAZ haben sich stark verändert. Sie sind von den Sorgen befreit, die Produktion, Reparatur und Wartung von Geräten, Wartung und Reinigung von Räumlichkeiten usw. sicherzustellen. Die einzige Aufgabe, die der VAZ-Produktionswerkstatt bleibt, besteht darin, die ihr zugewiesenen Produkte qualitativ und termingerecht herzustellen. Die Shop-Verwaltungsstruktur wird so weit wie möglich vereinfacht. Das sind der Werkstattleiter, seine beiden Schichtstellvertreter, die Abteilungsleiter, Meister, Meister. Alle Aufgaben der Bereitstellung, Produktionsvorbereitung und Wartung werden zentral vom Produktionsmanagementapparat gelöst.
Reis. 10.2. Typische Produktionsstruktur
In jeder Produktion wurden Abteilungen geschaffen: Design und Technologie, Design, Werkzeug und Ausrüstung, Analyse und Planung der Reparatur der Ausrüstung. Hier werden erzogen Einzelleistungen Arbeits- und Disposition, Logistik, Arbeits- und Lohnorganisation.
Die Produktionsstruktur umfasst große spezialisierte Werkstätten: Reparatur, Herstellung und Reparatur von Geräten, Transport- und Lagerarbeiten, Reinigung von Räumlichkeiten und andere. Die Schaffung leistungsfähiger Ingenieurleistungen und Produktionseinheiten in der Produktion, die jeweils die ihnen übertragenen Aufgaben auf ihrem Gebiet vollständig lösen, hat dies grundlegend ermöglicht neue Grundlage erstellen normale Bedingungen für den effizienten Betrieb der Hauptproduktionshallen.
Die Organisation der Workshops und Sektionen basiert auf den Prinzipien der Konzentration und Spezialisierung. Die Spezialisierung von Werkstätten und Produktionsstätten kann nach Art der Arbeit erfolgen - technologische Spezialisierung oder nach Art der hergestellten Produkte - fachliche Spezialisierung. Beispiele für Produktionseinheiten technologischer Spezialisierung in einem Maschinenbauunternehmen sind Gießereien, Wärme- oder Galvanikbetriebe, Dreh- und Schleifabteilungen in einer Maschinenhalle; fachliche Spezialisierung - eine Werkstatt für Karosserieteile, ein Wellenabschnitt, eine Werkstatt für die Herstellung von Getrieben usw.
Wenn ein vollständiger Zyklus der Herstellung eines Produkts oder Teils innerhalb einer Werkstatt oder eines Standorts durchgeführt wird, wird diese Unterteilung als subjektgeschlossen bezeichnet.
Bei der Organisation von Workshops und Standorten ist es notwendig, die Vor- und Nachteile aller Arten von Spezialisierungen sorgfältig zu analysieren. Durch die technologische Spezialisierung wird eine hohe Geräteauslastung sichergestellt, eine hohe Produktionsflexibilität bei der Beherrschung neuer Produkte und dem Wechsel von Produktionsanlagen erreicht. Gleichzeitig wird die Betriebs- und Produktionsplanung erschwert, der Produktionszyklus verlängert und die Verantwortung für die Produktqualität reduziert.
Die Nutzung der fachlichen Spezialisierung, die es Ihnen ermöglicht, alle Arbeiten auf die Produktion eines Teils oder Produkts im Rahmen eines Workshops oder Abschnitts zu konzentrieren, erhöht die Verantwortung der Ausführenden für die Produktqualität und die Aufgabenerfüllung. Die fachliche Spezialisierung schafft die Voraussetzungen für die Organisation der Inline- und automatisierten Fertigung, sichert die Umsetzung des Direktflussprinzips, vereinfacht die Planung und Abrechnung. Allerdings ist hier nicht immer eine Vollauslastung der Anlagen möglich, die Umstrukturierung der Produktion für die Produktion neuer Produkte erfordert große Aufwendungen.
Gegenstandsgeschlossene Werkstätten und Sektionen haben auch erhebliche wirtschaftliche Vorteile, deren Organisation es ermöglicht, die Dauer des Produktionszyklus von Herstellungsprodukten durch den vollständigen oder teilweisen Wegfall entgegenkommender oder altersbedingter Bewegungen zu verkürzen, zu vereinfachen System der Planung und Betriebsführung des Produktionsprozesses. Die praktische Erfahrung in- und ausländischer Unternehmen ermöglicht es uns, die folgende Gruppierung von Regeln anzugeben, die bei der Entscheidung über die Anwendung des fachlichen oder technologischen Prinzips des Baus von Werkstätten und Abschnitten zu beachten sind.
Thema Das Prinzip wird in folgenden Fällen empfohlen: mit der Freigabe von einem oder zwei Standardprodukten, mit einem großen Volumen und einem hohen Grad an Stabilität bei der Herstellung von Produkten, mit der Möglichkeit eines guten Gleichgewichts von Ausrüstung und Arbeitskräften, mit einem Minimum an Steuervorgängen und einer geringen Anzahl von Umstellungen; technologisch- mit der Freigabe einer großen Produktpalette, mit ihrer relativ geringen Serialisierung, mit der Unmöglichkeit, Ausrüstung und Personal auszugleichen, mit einer großen Anzahl von Kontrollvorgängen und einer erheblichen Anzahl von Umstellungen.
Organisation von Produktionsstätten. Die Organisation der Standorte wird durch die Art ihrer Spezialisierung bestimmt. Es geht um die Lösung einer Vielzahl von Aufgaben, darunter die Auswahl der Produktionsanlagen; Berechnung der erforderlichen Ausrüstung und ihrer Anordnung; Festlegung der Größe von Losen (Serien) von Teilen und der Häufigkeit ihrer Markteinführung; Zuordnung von Arbeiten und Vorgängen zu jedem Arbeitsplatz, Bauzeitpläne; Berechnung des Personalbedarfs; Entwurf eines Systems für Wartungsarbeitsplätze. In jüngster Zeit begannen sich Forschungs- und Produktionskomplexe in Verbänden zu bilden, die alle Phasen des Zyklus "Forschung - Entwicklung - Produktion" integrieren.
Zum ersten Mal im Land wurden im St. Petersburger Verein "Svetlana" vier Forschungs- und Produktionskomplexe geschaffen. Der Komplex ist eine einzelne Abteilung, die sich auf die Entwicklung und Produktion von Produkten mit einem bestimmten Profil spezialisiert hat. Es wird auf Basis der Konstruktionsbüros des Hauptwerkes erstellt. Neben dem Konstruktionsbüro gehören Hauptproduktionsstätten und spezialisierte Niederlassungen dazu. Die wissenschaftliche und Produktionstätigkeit der Komplexe wird auf der Grundlage der Berechnung vor Ort durchgeführt.
Wissenschafts- und Produktionskomplexe führen Design und technologische Vorbereitung der Produktion durch und beziehen die entsprechenden Abteilungen des Verbandes mit ein, um Arbeiten im Zusammenhang mit der Entwicklung neuer Produkte durchzuführen. Dem Leiter des Konstruktionsbüros wurden die Rechte zur durchgängigen Planung aller Stufen der Vorserienfertigung übertragen – von der Recherche bis zur Organisation der Serienfertigung. Er ist nicht nur für die Qualität und das Timing der Entwicklung verantwortlich, sondern auch für die Entwicklung der Serienproduktion neuer Produkte und der Produktionsaktivitäten der zum Komplex gehörenden Geschäfte und Filialen.
Im Rahmen des Übergangs von Unternehmen zur Marktwirtschaft erfolgt eine Weiterentwicklung der Produktionsstruktur von Verbänden auf der Grundlage einer Erhöhung der wirtschaftlichen Selbständigkeit ihrer konstituierenden Einheiten.
Als Beispiel für die Schaffung und Umsetzung einer neuen Organisationsform beim Übergang zur Marktwirtschaft kann die Gründung einer Aktiengesellschaft - eines Forschungs- und Produktionsunternehmens im Verband Energia (Woronesch) - angeführt werden. Auf der Grundlage der Abteilungen des Konzerns wurden mehr als 100 unabhängige Forschungs- und Produktionskomplexe, Assoziationen und Unternehmen der ersten Ebene mit voller rechtlicher Unabhängigkeit und Abrechnungskonten in einer Geschäftsbank geschaffen. Bei der Gründung unabhängiger Vereine und Unternehmen wurde Folgendes verwendet: verschiedene Eigentumsformen (Staat, Miete, gemischt, Aktiengesellschaft, Genossenschaft); verschiedene Organisationsstrukturen von unabhängigen Unternehmen und Verbänden, deren Anzahl zwischen 3 und 2350 Personen variiert; vielfältige Tätigkeiten (wissenschaftlich und produktiv, organisatorisch und wirtschaftlich, produktiv und technisch).
Der Konzern verfügt über 20 thematische und funktionale Forschungs- und Produktionskomplexe, die Forschung, Design, technologische Abteilungen und Produktionseinrichtungen vereinen, die auf die Entwicklung und Produktion bestimmter Produkttypen oder die Durchführung technologisch homogener Arbeiten spezialisiert sind. Diese Komplexe wurden durch die Reformierung von Versuchs- und Serienanlagen und auf der Grundlage eines Forschungsinstituts geschaffen. Je nach Anzahl und Umfang der Arbeit fungieren sie als Vereine der ersten Ebene, Unternehmen oder Kleinunternehmen.
Forschungs- und Produktionskomplexe zeigten ihre Vorteile während der Umstellungsphase unter den Bedingungen einer starken Änderung der Produktpalette. Nach der Erlangung der Unabhängigkeit organisierten die Unternehmen freiwillig Vereinigungen der ersten Ebene - Forschungs- und Produktionskomplexe oder -firmen - und gründeten einen Konzern, der 10 Hauptfunktionen gemäß der Charta zentralisierte. Oberstes Organ des Konzerns ist die Gesellschafterversammlung. Die Koordinierung der Arbeiten zur Umsetzung zentralisierter Funktionen wird vom Vorstand und den Funktionsabteilungen des Konzerns unter Bedingungen der vollständigen Selbstversorgung durchgeführt. Teilbereiche, die Service- und Unterstützungsfunktionen wahrnehmen, arbeiten ebenfalls auf vertraglicher Basis und sind rechtlich und wirtschaftlich vollständig selbstständig.
In Abb. gezeigt. 10.3 und die so genannte "zirkuläre" Managementstruktur des Konzerns erfüllt die Anforderungen der Gesetzgebung der Russischen Föderation. Der Vorstand koordiniert die zentralen Funktionen des Konzerns im Rahmen der Satzung nach der Idee eines runden Tisches.
Das kreisförmige (im Gegensatz zum bestehenden vertikalen) System der Organisation und des Managements der Produktion basiert auf den folgenden Prinzipien:
Reis. 10.3. Zirkuläre Managementstruktur von Energia Concern
- über die Freiwilligkeit des Zusammenschlusses von Anteilseignerunternehmen für gemeinsame Aktivitäten, um durch den Verkauf von Produkten und Dienstleistungen auf einem Wettbewerbsmarkt maximale und stabile Gewinne zu erzielen, um die sozialen und wirtschaftlichen Interessen der Anteilseigner zu erfüllen;
- freiwillige Zentralisierung eines Teils der Unternehmensfunktionen für die Organisation und Verwaltung der Produktion, verankert in der Satzung der Aktiengesellschaft;
- Kombination der Vorteile eines großen Unternehmens aufgrund von Spezialisierung, Zusammenarbeit und Produktionsumfang mit den Vorteilen kleiner Unternehmensformen und Motivation der Mitarbeiter durch Eigentum;
- ein System fachlicher und funktionaler Forschungs- und Produktionskomplexe, die auf technologischer Basis miteinander verbunden sind, unter Berücksichtigung der Vorteile der Spezialisierung und Zusammenarbeit;
- ein System vertraglicher Beziehungen zwischen Forschungs- und Produktionskomplexen und Firmen, unterstützt durch ein System zur Befriedigung selbsttragender Ansprüche, einschließlich der Regulierung des Lohnfonds;
- Übertragung des Zentrums der laufenden Arbeit zur Organisation und Verwaltung der Produktion von der obersten Ebene vertikal auf die Ebene der Forschungs- und Produktionskomplexe und unabhängigen Unternehmen auf vertraglicher Basis mit Fokussierung der Bemühungen des Top-Managements auf vielversprechende Themen;
- Durchführung von Wirtschaftsbeziehungen zwischen Unternehmen durch eine Geschäftsbank und ein internes Abwicklungszentrum in den relevanten Bereichen;
- Erhöhung der Garantien zur Lösung sozialer Probleme und zum Schutz sowohl unabhängiger Unternehmen als auch aller Anteilseigner;
- Kombination und Entwicklung verschiedener Eigentumsformen auf Ebene des Konzerns und unabhängiger Vereine und Unternehmen;
- Verzicht auf die dominierende Rolle der obersten Leitungsgremien mit der Umwandlung der Funktionen der Leitung und Koordinierung der Produktion in eine der Tätigkeitsvarianten der Aktionäre;
- Ausarbeitung des Mechanismus zur Vereinigung der gegenseitigen Interessen der unabhängigen Unternehmen und des Konzerns als Ganzes und Vermeidung der Gefahr eines Bruchs des technologischen Prinzips des Aufbaus der Produktionsorganisation durch Fliehkräfte.
Die kreisförmige Struktur sieht eine grundlegende Änderung der Aktivitäten von Subjektforschungs- und Produktionskomplexen vor, die die Führung bei der Planung übernehmen und die horizontale Verknüpfung der Aktivitäten von funktionalen Forschungs- und Produktionskomplexen und Unternehmen auf Vertragsbasis gemäß ihrer Nomenklatur übernehmen Kontoveränderungen auf dem Markt.
Die Planungs- und Dispositionsabteilung im Rahmen der Firma Pribyl wurde umgestaltet und ein bedeutender Teil ihrer Funktionen und ihres Personals in Fachforschungs- und Produktionskomplexe verlegt. Die Aufmerksamkeit dieses Dienstes konzentriert sich auf strategische Aufgaben und die Koordination der Arbeit von Komplexen und Firmen.
Concern Energia durchlief den Prozess der Privatisierung durch Pacht und Körperschaft und erhielt eine Eigentumsurkunde für das Eigentum, es erhielt den Status eines föderalen Forschungs- und Produktionszentrums.
10.4. Termingerechte Organisation der Produktionsabläufe
Um das rationelle Zusammenspiel aller Elemente des Produktionsprozesses zu gewährleisten und die durchgeführten Arbeiten zeitlich und räumlich zu rationalisieren, ist es notwendig, den Produktionszyklus des Produkts zu bilden.
Der Produktionszyklus ist ein Komplex von Haupt-, Hilfs- und Serviceprozessen, die zeitlich auf eine bestimmte Weise organisiert sind und für die Herstellung eines bestimmten Produkttyps erforderlich sind. Das wichtigste Merkmal Produktionszyklus ist seine Dauer.
Produktionszykluszeit- dies ist ein kalendarischer Zeitraum, in dem das Material, Werkstück oder ein anderer bearbeiteter Gegenstand alle Arbeitsgänge des Produktionsprozesses oder einen bestimmten Teil davon durchläuft und zu fertigen Produkten wird. Die Zyklusdauer wird in Kalendertagen oder Stunden ausgedrückt. Struktur des Produktionszyklus einschließlich Arbeitszeit und Pausen. Während der Arbeitszeit werden die eigentlichen technologischen Operationen sowie vorbereitende und abschließende Arbeiten durchgeführt. Zur Verarbeitungszeit gehören auch die Dauer von Kontroll- und Transportvorgängen sowie die Zeit von Naturvorgängen. Die Pausenzeit ist bedingt durch die Arbeitsweise, die überbetriebliche Teilelagerung und Mängel in der Arbeits- und Produktionsorganisation.
Die Zeit zwischen den Arbeitsgängen wird durch die Pausen des Stapelns, Wartens und Kommissionierens bestimmt. Teilabrisse treten bei der Herstellung von Produkten in Chargen auf und sind darauf zurückzuführen, dass verarbeitete Produkte so lange liegen bleiben, bis die gesamte Charge diesen Vorgang durchlaufen hat. In diesem Fall wird davon ausgegangen, dass eine Produktionscharge eine Gruppe von Produkten gleichen Namens und gleicher Größe ist, die für eine bestimmte Zeit mit der gleichen Vor- und Endphase in Produktion genommen werden. Wartepausen werden durch die uneinheitliche Dauer zweier benachbarter Arbeitsgänge des technologischen Prozesses verursacht, und Kommissionierpausen werden durch die Notwendigkeit verursacht, auf den Zeitpunkt zu warten, an dem alle in einem Produktsatz enthaltenen Rohlinge, Teile oder Baugruppen hergestellt sind. Kommissionierpausen treten beim Übergang von einer Stufe des Produktionsprozesses zu einer anderen auf.
In der allgemeinsten Form die Dauer des Produktionszyklus T ts wird durch die Formel ausgedrückt
T c = T t+ T n –3 + T e+ T bis + T tr + T mo + T Bsp. (10.1)
Wo T t ist die Zeit der technologischen Operationen; T n-3 - Zeit der Vor- und Abschlussarbeiten; T e ist die Zeit der natürlichen Prozesse; T k ist die Zeit der Kontrolloperationen; T tr ist die Zeit des Transports von Arbeitsgegenständen; T mo — Zeit der interoperativen Einbettung (Pausen zwischen den Schichten); T pr - die Zeit der Arbeitspausen.
Die Dauer der technologischen Operationen und Vor- und Abschlussarbeiten bildet zusammen einen Arbeitszyklus T Polizist.
Betriebszyklus- Dies ist die Dauer des abgeschlossenen Teils des technologischen Prozesses, der an einem Arbeitsplatz durchgeführt wird.
Methoden zur Berechnung der Dauer des Produktionszyklus. Es muss zwischen dem Produktionszyklus einzelner Teile und dem Produktionszyklus einer Baugruppe oder eines Produkts als Ganzes unterschieden werden. Der Produktionszyklus eines Teils wird normalerweise als einfach bezeichnet, und das Produkt oder die Montageeinheit wird als komplex bezeichnet. Der Zyklus kann ein- und mehrstufig sein. Die Zykluszeit eines mehrstufigen Prozesses hängt davon ab, wie Teile von Arbeitsgang zu Arbeitsgang übergeben werden. Es gibt drei Arten der Bewegung von Arbeitsgegenständen im Prozess ihrer Herstellung: sequentiell, parallel und parallel-sequentiell.
Bei sequentielle Art der Bewegung Die gesamte Charge von Teilen wird zum nächsten Arbeitsgang übertragen, nachdem die Bearbeitung aller Teile im vorherigen Arbeitsgang abgeschlossen ist. Die Vorteile dieser Methode sind das Fehlen von Betriebsunterbrechungen der Ausrüstung und des Arbeiters bei jeder Operation, die Möglichkeit ihrer hohen Belastung während der Schicht. Der Produktionszyklus mit einer solchen Arbeitsorganisation ist jedoch der größte, was sich negativ auf die technische und wirtschaftliche Leistung der Werkstatt und des Unternehmens auswirkt.
Bei parallele Bewegung Teile werden unmittelbar nach dem Ende ihrer Bearbeitung in der vorherigen Operation von einem Transportbatch an die nächste Operation übergeben. In diesem Fall am meisten kurzer Zyklus. Die Einsatzmöglichkeiten einer parallelen Bewegungsart sind jedoch begrenzt, da Voraussetzung für deren Realisierung die Gleichheit oder Vielfachheit der Operationsdauer ist. Andernfalls sind Unterbrechungen im Betrieb von Geräten und Arbeitern unvermeidlich.
Bei parallel-sequentieller Bewegungstyp Teile von Betrieb zu Betrieb, sie werden durch Transportpartien oder stückweise transportiert. In diesem Fall gibt es eine teilweise Kombination der Ausführungszeit benachbarter Operationen, und der gesamte Stapel wird bei jeder Operation ohne Unterbrechungen verarbeitet. Arbeiter und Ausrüstung arbeiten ohne Unterbrechung. Der Produktionszyklus ist im Vergleich zu einem parallelen länger, aber kürzer als bei einer sequentiellen Bewegung von Arbeitsgegenständen.
Berechnung des Zyklus eines einfachen Produktionsprozesses. Der betriebliche Produktionszyklus einer Teilecharge mit sequentieller Bewegungsart errechnet sich wie folgt:
(10.2)
Wo N- die Anzahl der Teile in der Produktionscharge, Stück; R op ist die Anzahl der technologischen Prozessoperationen; T PC ich— Zeitlimit für jeden Vorgang, min; MIT RM ich- die Anzahl der Arbeitsplätze, die von der Herstellung einer Teilecharge für jeden Arbeitsgang belegt werden.
Das Schema des sequentiellen Bewegungstyps ist in Abb. 1 dargestellt. 10.4, A. Nach den Daten des Diagramms wird der Arbeitszyklus einer Charge aus drei Teilen berechnet, die an vier Arbeitsplätzen verarbeitet werden:
T c.seq = 3 (t Stk. 1 + t Stk. 2 + t Stk. 3 + t Stk. 4) = 3 (2 + 1 + 4 + 1,5) = 25,5 min.
Die Formel zur Berechnung der Dauer des Betriebszyklus für eine parallele Bewegungsart:
(10.3)
wo ist die Ausführungszeit der Operation, die längste im technologischen Prozess, min.
Reis. 10.4, a. Zeitplan der Produktionszyklen für die sequentielle Bewegung von Teilechargen
Das Diagramm der Bewegung einer Charge von Teilen mit paralleler Bewegung ist in Abb. 10.4, b. Gemäß dem Zeitplan können Sie die Dauer des Betriebszyklus mit paralleler Bewegung bestimmen:
T c.par = ( T Stk. 1+ T Stk. 2+ T Stk. 3+ T Stk 4)+ (3 – 1) T Stk. 3 \u003d 8,5 + (3 - 1) 4 \u003d 16,5 min.
Reis. 10.4, b. Zeitplan der Produktionszyklen mit parallel-sequentieller Bewegung von Teilechargen
Bei einer parallel-sequentiellen Bewegungsart kommt es zu einer teilweisen Überlappung der Ausführungszeit benachbarter Operationen. Es gibt zwei Arten von Kombinationen zeitlich benachbarter Operationen. Wenn die Ausführungszeit des nachfolgenden Vorgangs länger ist als die Ausführungszeit des vorherigen Vorgangs, können Sie die parallele Art der Teilebewegung anwenden. Ist die Ausführungszeit der nachfolgenden Operation kleiner als die Ausführungszeit der vorherigen, so ist eine parallel-sequentielle Bewegungsart bei maximal möglicher Überlappung der Ausführungszeit beider Operationen akzeptabel. In diesem Fall unterscheiden sich die maximalen kombinierten Arbeitsgänge um den Zeitpunkt der Herstellung des letzten Teils (bzw. des letzten Transportloses) beim nachfolgenden Arbeitsgang.
Ein Diagramm eines parallel-sequentiellen Bewegungstyps ist in Abb. 1 dargestellt. 10.4, v. In diesem Fall ist der Arbeitszyklus um den Betrag der Kombination jedes benachbarten Paars von Operationen kleiner als bei einer sequentiellen Art von Bewegung: die erste und zweite Operation - AB - (3 - l) T Stück2 ; zweite und dritte Operation - VG \u003d A ¢ B ¢ - (3 -1) T pcs3 ; dritte und vierte Operation - DE - (3 - 1) T pcs4 (wo T pcs3 und T pcs4 haben kürzere Zeit T Stückkern aus jedem Operationspaar).
Formeln zur Berechnung
(10.4)
Beim Ausführen von Operationen auf parallelen Workstations:
Reis. 10.4, c. Zeitplan der Produktionszyklen mit paralleler Bewegung von Teilechargen
Bei Übergabe von Produkten durch Transportunternehmen:
(10.5)
wo ist die Zeit, um die kürzeste Operation abzuschließen.
Ein Beispiel für die Berechnung der Zyklusdauer nach Formel (10.5):
T c.p-p \u003d 25,5 - 2 (1 + 1 + 1,5) \u003d 18,5 min.
Der Produktionszyklus zur Herstellung einer Charge von Teilen umfasst nicht nur den Betriebszyklus, sondern auch mit der Betriebsweise verbundene natürliche Prozesse und Pausen und andere Komponenten. In diesem Fall wird die Dauer des Zyklus für die betrachteten Bewegungsarten durch die Formeln bestimmt:
Wo R op ist die Anzahl der technologischen Operationen; MIT rm - die Anzahl paralleler Jobs, die von der Herstellung einer Charge von Teilen für jeden Vorgang belegt werden; T mo — Zeit des interoperativen Dekubitus zwischen zwei Operationen, h; T cm ist die Dauer einer Arbeitsschicht, h; D cm ist die Anzahl der Schichten; ZU v.n - der geplante Übereinstimmungskoeffizient mit den Normen im Betrieb; ZU Lane - Umrechnungskoeffizient der Arbeitszeit in Kalenderzeit; T e ist die Dauer natürlicher Prozesse.
Berechnung der Zykluszeit eines komplexen Prozesses
Der Produktionszyklus eines Produkts umfasst die Zyklen der Herstellung von Teilen, der Montage von Einheiten und Endprodukten sowie der Testvorgänge. Dabei wird davon ausgegangen, dass verschiedene Teile gleichzeitig gefertigt werden. Daher wird der Zyklus des arbeitsintensivsten (führenden) Teils von denjenigen, die an die ersten Arbeitsgänge der Montagewerkstatt geliefert werden, in den Produktionszyklus des Produkts einbezogen. Die Dauer des Produktionszyklus des Produkts kann anhand der Formel berechnet werden
T cp = T c.d + T cb, (10.9)
Wo T ts.d - die Dauer des Produktionszyklus für die Herstellung des führenden Teils, Kalender. Tage; T ts.b - die Dauer des Produktionszyklus von Montage- und Testarbeiten, Kalendern. Tage
Reis. 10.5. Komplexer Prozessablauf
Mit einem grafischen Verfahren kann die Zykluszeit eines komplexen Fertigungsprozesses ermittelt werden. Dazu wird ein zyklischer Zeitplan erstellt. Die Produktionszyklen einfacher Prozesse, die in den komplexen eingeschlossen sind, werden vorläufig festgelegt. Gemäß dem Zyklusplan wird die Durchlaufzeit einiger Prozesse durch andere analysiert und die Gesamtdauer des Zyklus eines komplexen Prozesses zur Herstellung eines Produkts oder einer Produktcharge als größte Summe von Zyklen miteinander verbundener einfacher Prozesse bestimmt und Betriebspausen. Auf Abb. 10.5 zeigt ein Zyklusdiagramm eines komplexen Prozesses. In der Grafik von rechts nach links sind die Zyklen von Teilprozessen auf einer Zeitskala aufgetragen, beginnend mit dem Testen und endend mit der Herstellung von Teilen.
Wege und Bedeutung, um die Kontinuität des Produktionsprozesses zu gewährleisten und die Durchlaufzeit zu reduzieren
Ein hohes Maß an Kontinuität der Produktionsprozesse und eine Verkürzung der Dauer des Produktionszyklus sind von großer wirtschaftlicher Bedeutung: Der Umfang der laufenden Arbeiten wird reduziert und der Umschlag des Betriebskapitals beschleunigt, die Nutzung von Ausrüstung und Produktionsflächen wird verbessert , und die Produktionskosten werden reduziert. Studien, die in einer Reihe von Unternehmen in Charkow durchgeführt wurden, haben gezeigt, dass bei einer durchschnittlichen Dauer des Produktionszyklus von nicht mehr als 18 Tagen jeder ausgegebene Rubel 12 % mehr Produktion liefert als in Fabriken mit einer Zyklusdauer von 19 bis 36 Tagen und 61 % mehr als in einer Fabrik, in der Produkte einen Zyklus von mehr als 36 Tagen haben.
Eine Erhöhung der Kontinuität des Produktionsprozesses und eine Verkürzung der Zyklusdauer werden zum einen durch die Anhebung des technischen Produktionsniveaus und zum anderen durch Maßnahmen organisatorischer Art erreicht. Beide Wege sind miteinander verbunden und ergänzen sich.
Die technische Verbesserung der Produktion geht in Richtung der Einführung neuer Technologien, fortschrittlicher Ausrüstung und neuer Fahrzeuge. Dies führt zu einer Verkürzung des Produktionszyklus, indem die Arbeitsintensität der eigentlichen technologischen und Kontrollvorgänge verringert wird, wodurch die Zeit zum Bewegen von Arbeitsobjekten verkürzt wird.
Zu den organisatorischen Maßnahmen sollten gehören:
- Minimierung von Unterbrechungen, die durch zwischenbetriebliche Warte- und Stapelunterbrechungen verursacht werden, durch die Verwendung von parallelen und parallel-sequentiellen Verfahren zur Bewegung von Arbeitsgegenständen und Verbesserung des Planungssystems;
- Erstellung von Zeitplänen für die Kombination verschiedener Produktionsprozesse, die eine teilweise Überschneidung der Zeit für die Durchführung verwandter Arbeiten und Operationen ermöglichen;
- Reduzierung von Wartezeiten auf der Grundlage der Erstellung optimierter Zeitpläne für die Herstellung von Produkten und der rationellen Einführung von Teilen in die Produktion;
- Die Einführung von thematisch abgeschlossenen und auf Details spezialisierten Werkstätten und Abteilungen, deren Schaffung die Länge der Wege innerhalb der Geschäfte und zwischen den Geschäften verkürzt, reduziert die für den Transport aufgewendete Zeit.
Der Produktionsprozess ist eine Reihe von miteinander verbundenen Haupt-, Hilfs- und Dienstleistungsprozessen von Arbeit und Arbeitswerkzeugen, um Verbraucherwerte zu schaffen - nützliche Arbeitsgegenstände, die für den industriellen oder persönlichen Verbrauch erforderlich sind. Im Produktionsprozess wirken Arbeiter mit Hilfe von Werkzeugen auf Arbeitsgegenstände ein und schaffen neue Endprodukte, z. B. Werkzeugmaschinen, Computer, Fernseher, radioelektronische Geräte usw. Arbeitsgegenstände und -werkzeuge sind materielle Elemente von Produktion, stehen im Unternehmen in einer bestimmten Beziehung zueinander, eine andere: bestimmte Artikel können nur mit bestimmten Werkzeugen bearbeitet werden; sie haben bereits an sich systemische Eigenschaften. Die lebendige Arbeit muss diese Dinge jedoch annehmen und damit den Prozess beginnen, sie in ein Produkt zu verwandeln. Der Produktionsprozess ist also in erster Linie ein Arbeitsprozess, da die von einer Person bei seinem Input eingesetzten Ressourcen, sowohl Informationen als auch materielle Produktionsmittel, das Produkt vorangegangener Arbeitsprozesse sind. Unterscheiden Sie Haupt-, Neben- und Nebenproduktionsprozesse (Abb. 1).
Die Hauptproduktionsprozesse sind der Teil der Prozesse, bei denen es zu einer direkten Änderung der Formen, Größen, Eigenschaften, der inneren Struktur von Arbeitsgegenständen und ihrer Umwandlung in fertige Produkte kommt. Beispielsweise in einem Werkzeugmaschinenbetrieb sind dies die Prozesse der Teilefertigung und der Montage von Unterbaugruppen, Baugruppen und dem Gesamtprodukt daraus.
Zu den Produktionsnebenprozessen zählen solche Prozesse, deren Ergebnisse entweder direkt in den Hauptprozessen verwendet werden oder deren reibungslosen Ablauf gewährleisten Wirksame Umsetzung. Beispiele für solche Prozesse sind die Herstellung von Werkzeugen, Vorrichtungen, Matrizen, Mitteln zur Mechanisierung und Automatisierung der eigenen Produktion, Ersatzteilen für die Reparatur von Geräten, Erzeugung aller Arten von Energie im Unternehmen (Strom, Druckluft, Stickstoff usw.).
Disind Arbeitsprozesse zur Erbringung von Dienstleistungen, die für die Durchführung der Haupt- und Hilfsproduktionsprozesse erforderlich sind. Beispielsweise Transporte von Sachwerten, Lagertätigkeiten aller Art, technische Kontrolle der Produktqualität etc.
Die Haupt-, Neben- und Diweisen unterschiedliche Entwicklungs- und Verbesserungstendenzen auf. Dadurch können viele Nebenproduktionsprozesse auf spezialisierte Anlagen verlagert werden, was in den meisten Fällen deren kostengünstigere Produktion sicherstellt. Mit zunehmendem Mechanisierungs- und Automatisierungsgrad der Haupt- und Nebenprozesse werden Serviceprozesse allmählich zu einem integralen Bestandteil der Hauptproduktion und spielen eine organisierende Rolle in der automatisierten und insbesondere in der flexiblen automatisierten Produktion.
Die Haupt- und in einigen Fällen Nebenproduktionsprozesse finden in verschiedenen Stufen (oder Phasen) statt. Eine Stufe ist ein gesonderter Teil des Produktionsprozesses, wenn das Arbeitsobjekt in einen anderen qualitativen Zustand übergeht. Zum Beispiel geht das Material in das Werkstück, das Werkstück geht in das Teil usw.
Die Hauptproduktionsprozesse finden in folgenden Phasen statt: Beschaffung, Verarbeitung, Montage und Anpassung.
Die Beschaffungsphase ist für die Fertigung von Rohteilen vorgesehen. Es zeichnet sich durch sehr unterschiedliche Herstellungsverfahren aus. B. Schneiden oder Schneiden von Werkstücken aus Blattmaterial, Herstellung von Rohlingen durch Gießen, Stanzen, Schmieden usw. Der Haupttrend in der Entwicklung technologischer Prozesse in diesem Stadium besteht darin, Rohlinge näher an die Formen und Größen fertiger Teile zu bringen. Die Werkzeuge der Arbeit in diesem Stadium sind Schneidemaschinen, Press- und Stanzeinrichtungen, Schlagscheren usw.
Die Verarbeitungsstufe – die zweite in der Struktur des Produktionsprozesses – umfasst die mechanische und thermische Bearbeitung. Gegenstand der Arbeit sind hier die Rohteile. Die Arbeitswerkzeuge in diesem Stadium sind hauptsächlich verschiedene Metallschneidemaschinen, Öfen für die Wärmebehandlung und Apparate für die chemische Verarbeitung. Als Ergebnis dieses Schrittes erhalten die Teile Abmessungen entsprechend der angegebenen Genauigkeitsklasse.
Die Montagephase (Montage-Montage) ist ein Produktionsprozess, der zu Montageeinheiten (kleine Montageeinheiten, Unterbaugruppen, Einheiten, Blöcke) oder fertigen Produkten führt. Arbeitsgegenstand sind in dieser Stufe sowohl Teile und Baugruppen aus eigener Herstellung als auch fremdbezogene (Bauteile). Es gibt zwei Hauptorganisationsformen der Montage: stationär und mobil. Stationäre Montage liegt vor, wenn das Produkt an einem Arbeitsplatz gefertigt wird (Teile beigestellt werden). Bei der mobilen Montage entsteht das Produkt während des Transports von einem Arbeitsplatz zum anderen. Die Arbeitswerkzeuge sind hier nicht so vielfältig wie in der Verarbeitungsphase. Die wichtigsten sind alle Arten von Werkbänken, Ständern, Transport- und Führungsvorrichtungen (Förderbänder, Elektroautos, Roboter usw.). Montageprozesse sind in der Regel durch einen erheblichen manuellen Arbeitsaufwand gekennzeichnet, daher ist ihre Mechanisierung und Automatisierung die Hauptaufgabe zur Verbesserung des technologischen Prozesses.
Die Anpassungs- und Anpassungsphase ist die letzte in der Struktur des Produktionsprozesses, die durchgeführt wird, um die notwendigen technischen Parameter des Endprodukts zu erhalten. Arbeitsgegenstand sind hier fertige Produkte oder deren einzelne Baugruppen, Werkzeuge, universelle Instrumentierung und spezielle Prüfstände.
Die konstituierenden Elemente der Stufen der Haupt- und Hilfsprozesse sind technologische Operationen. Die Aufteilung des Produktionsprozesses in Operationen und dann in Techniken und Bewegungen ist notwendig für die Entwicklung technisch fundierter Normen für die Ausführung von Operationen.
Ein Arbeitsgang ist ein Teil des Produktionsprozesses, der in der Regel an einem Arbeitsplatz ohne Umrüstung und von einem oder mehreren Arbeitern (Team) durchgeführt wird.
Je nach technischem Ausstattungsgrad des Produktionsprozesses werden Arbeitsgänge unterschieden: manuell, maschinell, maschinell, automatisch und maschinell.
Sowohl die Haupt- als auch die Hilfs- und manchmal dienenden Produktionsprozesse bestehen aus Haupt- und Hilfselementen - Operationen. Zu den wichtigsten gehören Operationen, die in direktem Zusammenhang mit der Änderung der Größe, Form, Eigenschaften, der inneren Struktur des Arbeitsgegenstands oder der Umwandlung einer Substanz in eine andere sowie der Änderung der Position der Arbeitsgegenstände relativ zueinander stehen. Hilfsoperationen umfassen Operationen, deren Durchführung zum Fluss der Hauptoperationen beiträgt, z. B. Bewegung von Arbeitsgegenständen, Qualitätskontrolle, Aus- und Einbau, Lagerung usw.
Organisatorisch werden die Haupt- und Hilfsproduktionsprozesse (ihre Operationen) herkömmlicherweise in einfache und komplexe unterteilt.
Als einfach werden Prozesse bezeichnet, bei denen Arbeitsgegenstände einer aufeinanderfolgenden Reihe von miteinander verbundenen Operationen unterzogen werden, wodurch teilweise fertige Arbeitsprodukte (Rohlinge, Teile, dh integrale Teile des Produkts) erhalten werden.
Als komplex werden Prozesse bezeichnet, bei denen durch Kombination von Teilprodukten fertige Arbeitsprodukte, also komplexe Produkte (Maschinen, Maschinen, Geräte etc.) entstehen.
Die Bewegung von Arbeitsgegenständen im Produktionsprozess erfolgt so, dass das Arbeitsergebnis eines Arbeitsplatzes zum Ausgangsgegenstand eines anderen wird, d. h. jeder zeitlich und räumlich vorangegangene dem nächsten, diesem, Arbeit gibt wird durch die Organisation der Produktion sichergestellt.
Von der korrekten und rationellen Organisation der Produktionsprozesse (insbesondere der Hauptprozesse) hängen die Ergebnisse der Produktions- und Wirtschaftstätigkeit des Unternehmens, die wirtschaftliche Leistung seiner Arbeit, die Produktionskosten, der Gewinn und die Rentabilität der Produktion sowie die Höhe ab laufende Arbeiten und die Höhe des Betriebskapitals.
2. GRUNDPRINZIPIEN DER ORGANISATION DES PRODUKTIONSPROZESSES
Die Organisation des Produktionsprozesses in jedem produzierenden Unternehmen (einschließlich funkelektronischer Instrumentierung) in jeder seiner Werkstätten an einem Standort basiert auf einer zeitlich und räumlich rationalen Kombination aller Haupt-, Hilfs- und Serviceprozesse. Auf diese Weise können Sie Produkte zu minimalen Lebenshaltungskosten und materialisierten Arbeitskräften herstellen. Merkmale und Verfahren einer solchen Kombination sind bei unterschiedlichen Produktionsbedingungen unterschiedlich. Die Organisation von Produktionsprozessen unterliegt jedoch bei aller Vielfalt bestimmten allgemeinen Prinzipien: Differenzierung, Konzentration und Integration, Spezialisierung, Proportionalität, direkter Fluss, Kontinuität, Parallelität, Rhythmus, Automatismus, Prävention, Flexibilität, Optimalität, Elektronisierung, Standardisierung, usw.
Das Differenzierungsprinzip beinhaltet die Aufteilung des Produktionsprozesses in separate technologische Prozesse, die wiederum in Operationen, Übergänge, Techniken und Bewegungen unterteilt sind. Gleichzeitig ermöglicht die Analyse der Merkmale jedes Elements die Auswahl der besten Bedingungen für seine Implementierung, wodurch die Minimierung der Gesamtkosten aller Arten von Ressourcen sichergestellt wird. So entwickelt sich die Inline-Fertigung seit vielen Jahren durch die immer tiefere Ausdifferenzierung technologischer Prozesse. Die Vergabe kurzfristiger Operationen ermöglichte es, die Organisation und technologische Ausstattung der Produktion zu vereinfachen, die Fähigkeiten der Arbeiter zu verbessern und ihre Produktivität zu steigern.
Eine zu starke Differenzierung erhöht jedoch die Ermüdung der Arbeiter in manuellen Tätigkeiten aufgrund der Monotonie und hohen Intensität von Produktionsprozessen. Eine große Anzahl von Arbeitsgängen führt zu überhöhten Kosten für das Verschieben von Arbeitsgegenständen zwischen den Arbeitsplätzen, deren Installation, Befestigung und Entfernung von den Arbeitsplätzen nach dem Ende des Arbeitsgangs.
Beim Einsatz moderner flexibler Hochleistungsmaschinen (CNC-Maschinen, Bearbeitungszentren, Roboter usw.) wird das Prinzip der Differenzierung auf das Prinzip der Betriebskonzentration und Integration von Produktionsprozessen übertragen. Das Prinzip der Konzentration beinhaltet die Durchführung mehrerer Arbeitsgänge an einem Arbeitsplatz (Mehrspindel-Mehrschneidemaschinen mit CNC). Die Operationen werden umfangreicher, komplexer und werden in Kombination mit dem Brigadeprinzip der Arbeitsorganisation durchgeführt. Das Prinzip der Integration besteht darin, die wesentlichen Support- und Serviceprozesse zu vereinen.
Das Spezialisierungsprinzip ist eine Form der gesellschaftlichen Arbeitsteilung, die, sich systematisch entwickelnd, die Zuordnung von Werkstätten, Abteilungen, Linien und einzelnen Arbeitsplätzen im Unternehmen bestimmt. Sie stellen eine begrenzte Produktpalette her und zeichnen sich durch ein besonderes Produktionsverfahren aus.
Eine Reduzierung der Produktpalette führt in der Regel zu einer Verbesserung aller Wirtschaftsindikatoren, insbesondere zu einer Erhöhung des Nutzungsgrads des Anlagevermögens eines Unternehmens, einer Senkung der Produktionskosten und einer Verbesserung in der Produktqualität, Mechanisierung und Automatisierung von Produktionsprozessen. Spezialgeräte arbeiten bei sonst gleichen Bedingungen produktiver.
Der Spezialisierungsgrad des Arbeitsplatzes wird durch den Konsolidierungskoeffizienten der Detailoperationen (Kspi) bestimmt, die an einem Arbeitsplatz für einen bestimmten Zeitraum (Monat, Quartal) durchgeführt werden:
(1)
wobei Spr die Anzahl der Arbeitsplätze (Ausrüstungsteile) des Produktionssystems ist;
mto - die Anzahl der Detailoperationen, die am 1. Arbeitsplatz während einer Zeiteinheit (Monat, Jahr) durchgeführt wurden.
Mit dem Koeffizienten Ksp = 1 wird eine enge Spezialisierung des Arbeitsplatzes sichergestellt, es werden Voraussetzungen für eine effektive Organisation der Produktion geschaffen. Um einen Arbeitsplatz mit einer Detailoperation vollständig zu belasten, ist es erforderlich, dass die Bedingung :
(2)
wo ist das Volumen der Startteile des j-ten Artikels pro Zeiteinheit, zum Beispiel Stück/Monat;
- die Komplexität des Betriebs am 1. Arbeitsplatz, min;
- effektive Arbeitszeit des Arbeitsplatzes, z. B. min / Monat.
Das Verhältnismäßigkeitsprinzip geht von einem gleichen Durchsatz aller Produktionseinheiten aus, die die Haupt-, Hilfs- und Dienstleistungsprozesse ausführen. Ein Verstoß gegen dieses Prinzip führt zum Auftreten von "Engpässen" in der Produktion oder umgekehrt zur unvollständigen Auslastung einzelner Arbeitsplätze, Bereiche, Werkstätten und zu einer Verringerung der Effizienz des gesamten Unternehmens. Zur Wahrung der Verhältnismäßigkeit werden daher Produktionskapazitätsberechnungen sowohl nach Produktionsstufen als auch nach Gerätegruppen und Produktionsbereichen durchgeführt. Zum Beispiel, wenn das Produktionsvolumen der Teile (Ne) und die Stückzeitrate (tsht) bekannt sind. Sie können die Belastung eines bestimmten definieren ich- Gerätegruppe nach Formel
(4)
Vergleichen Sie dann die Last und den Durchsatz ich Gerätegruppe und bestimmen Sie deren Belastungsfaktor nach der Formel
Die bevorzugte Option ist wann
Und .
Das Prinzip des direkten Flusses bedeutet eine solche Organisation des Produktionsprozesses, die die kürzesten Wege für den Durchgang von Teilen und Montageeinheiten durch alle Phasen und Vorgänge von der Einführung der Rohstoffe in die Produktion bis zur Freigabe der fertigen Produkte bietet. Der Material-, Halbzeug- und Montagefluss muss vorwärts und möglichst kurz sein, ohne Gegen- und Rückbewegungen. Dies wird durch die entsprechende Anordnung der Geräteplatzierung entlang des technologischen Prozesses sichergestellt. Ein klassisches Beispiel für ein solches Layout ist die Produktionslinie.
Das Prinzip der Kontinuität bedeutet, dass der Arbeiter ohne Ausfallzeiten arbeitet, die Ausrüstung ohne Unterbrechungen arbeitet, die Arbeitsgegenstände nicht am Arbeitsplatz liegen. Dieses Prinzip manifestiert sich am vollständigsten in der Massen- oder Großproduktion bei der Organisation von Fließproduktionsverfahren, insbesondere bei der Organisation von kontinuierlichen Einzel- und Mehrsubjekt-Produktionslinien. Dieses Prinzip sorgt für eine Verkürzung des Herstellungszyklus des Produkts und trägt dadurch zu einer Steigerung der Intensivierung der Produktion bei.
Das Prinzip der Parallelität impliziert die gleichzeitige Ausführung von Teilproduktionsprozessen und Einzeloperationen an ähnlichen Teilen und Teilen des Produkts an verschiedenen Arbeitsplätzen, d. H. Die Schaffung einer breiten Front der Arbeit an der Herstellung dieses Produkts. Die Parallelität in der Organisation des Produktionsprozesses wird in verschiedenen Formen verwendet: in der Struktur der technologischen Operation - Multi-Tool-Bearbeitung (mehrspindlige, mehrschneidige halbautomatische Maschinen) oder parallele Ausführung der Haupt- und Hilfselemente der Operationen; bei der Herstellung von Rohlingen und der Bearbeitung von Teilen (in den Werkstätten Rohlinge und Teile in verschiedenen Stadien der Bereitschaft); in der Knoten- und Generalversammlung. Das Prinzip der Parallelität verkürzt die Dauer des Produktionszyklus und spart Arbeitszeit.
Das Rhythmusprinzip gewährleistet die Freigabe gleicher oder zunehmender Produktmengen für gleiche Zeiträume und dementsprechend die Wiederholung dieser Perioden des Produktionsprozesses in allen seinen Phasen und Operationen. Bei einer engen Spezialisierung der Produktion und einem stabilen Produktsortiment kann der Rhythmus direkt in Bezug auf einzelne Produkte sichergestellt werden und wird durch die Anzahl der verarbeiteten oder produzierten Produkte pro Zeiteinheit oder Wertindikatoren bestimmt.
Das Prinzip der Automatik geht davon aus, dass die maximale Leistung der Vorgänge des Produktionsprozesses automatisch erfolgt, dh ohne direkte Beteiligung des Arbeiters daran oder unter seiner Aufsicht und Kontrolle. Die Automatisierung von Prozessen führt zu einer Steigerung des Outputs von Teilen, Produkten, einer Steigerung der Arbeitsqualität, einer Senkung der Kosten menschlicher Arbeit, dem Ersatz unattraktiver Handarbeit durch mehr intellektuelle Arbeit hochqualifizierter Arbeitnehmer (Einsteller, Bediener), die Eliminierung manueller Arbeit bei Arbeitsplätzen mit schädlichen Bedingungen und der Ersatz von Arbeitern durch Roboter. Besonders wichtig ist die Automatisierung von Serviceprozessen. Automatisierte Fahrzeuge und Lager übernehmen nicht nur Funktionen für den Transport und die Lagerung von Produktionsanlagen, sondern können den Rhythmus der gesamten Produktion regulieren. Der allgemeine Automatisierungsgrad von Produktionsprozessen wird durch den Anteil der Arbeit in der Haupt-, Hilfs- und Dienstleistungsindustrie am Gesamtarbeitsvolumen des Unternehmens bestimmt. Der Automatisierungsgrad (Uavt) wird durch die Formel bestimmt
Uavt \u003d T aut: T gesamt, (6)
wo T aut - die Komplexität der automatisch oder automatisiert ausgeführten Arbeit;
Тtot ist die gesamte Arbeitsintensität der Arbeit im Unternehmen (Werkstatt) für einen bestimmten Zeitraum.
Der Automatisierungsgrad kann als Summe für das gesamte Unternehmen und für jeden Bereich separat berechnet werden.
Das Prinzip der Prävention beinhaltet die Organisation der Gerätewartung mit dem Ziel, Unfälle und Ausfallzeiten technischer Anlagen zu vermeiden. Dies wird durch ein System der vorbeugenden Wartung (PPR) erreicht.
Das Prinzip der Flexibilität gewährleistet eine effiziente Arbeitsorganisation, ermöglicht den mobilen Übergang zur Produktion anderer Produkte, die im Produktionsprogramm des Unternehmens enthalten sind, oder zur Produktion neuer Produkte, wenn die Produktion beherrscht wird. Es sorgt für eine Reduzierung von Zeit und Kosten für den Gerätewechsel bei der Produktion von Teilen und Produkten einer breiten Palette. Dieses Prinzip ist am weitesten unter Bedingungen einer hochorganisierten Produktion entwickelt, wo CNC-Maschinen, Bearbeitungszentren (MC), rekonfigurierbare automatische Mittel zur Steuerung, Lagerung und Bewegung von Produktionsobjekten verwendet werden.
Das Prinzip der Optimalität besagt, dass die Durchführung aller Prozesse zur Herstellung von Produkten in vorgegebener Menge und termingerecht mit größtmöglicher Wirtschaftlichkeit bzw. mit geringstem Arbeits- und Materialeinsatz erfolgt. Optimalität beruht auf dem Gesetz der Zeitökonomie.
Das Prinzip der Elektronisierung impliziert die weit verbreitete Nutzung von CNC-Fähigkeiten auf der Grundlage der Verwendung von Mikroprozessortechnologie, die es ermöglicht, grundlegend neue Maschinensysteme zu schaffen, die hohe Leistung mit den Anforderungen an Flexibilität in Produktionsprozessen verbinden. Computer und Industrieroboter mit künstlicher Intelligenz ermöglichen es, komplexeste Funktionen in der Produktion anstelle von Menschen auszuführen.
Die Verwendung von Mini- und Mikrocomputern mit fortschrittlicher Software und Multi-Tool-CNC-Maschinen ermöglicht es Ihnen, aufgrund des automatischen Werkzeugwechsels einen großen Satz oder sogar die gesamte Bearbeitung von Teilen von einer ihrer Installationen auf der Maschine durchzuführen. Ein Satz Schneidwerkzeuge für eine solche Maschine kann 100 bis 120 Einheiten erreichen, die in einem Revolver oder Werkzeugmagazin installiert und gemäß einem speziellen Programm ersetzt werden.
Das Prinzip der Standardisierung impliziert den weit verbreiteten Einsatz bei der Schaffung und Entwicklung neuer Technologien und der neuen Technologie der Standardisierung, Vereinheitlichung, Typisierung und Normalisierung, die es ermöglichen, eine unangemessene Vielfalt an Materialien, Geräten und technologischen Prozessen zu vermeiden und die Dauer drastisch zu verkürzen des Zyklus der Schaffung und Entwicklung neuer Technologien (SONT).
Bei der Gestaltung eines Produktionsprozesses oder Produktionssystems sollte von der rationalen Anwendung der oben skizzierten Prinzipien ausgegangen werden.
3. ORGANISATORISCHE STRUKTUR DES PRODUKTIONSPROZESSES DER MODERNEN ORGANISATION
Bei der Umwandlung von Produktionsgegenständen in ein bestimmtes Produkt durchlaufen sie viele Haupt-, Hilfs- und Dienstleistungsprozesse, die zeitlich parallel, parallel-sequentiell oder zeitlich nacheinander ablaufen, je nach der auf Unternehmensebene, Produktionsart, Ebene entstandenen Produktionsstruktur der Spezialisierung von Produktionseinheiten, Organisationsformen von Produktionsprozessen und anderen Faktoren. Die Gesamtheit dieser Prozesse, die die Herstellung eines Produkts sicherstellen, wird allgemein als Produktionszyklus bezeichnet, dessen Hauptmerkmale seine Dauer und Struktur sind (2).
Die Dauer des Produktionszyklus zur Herstellung von Produkten (unabhängig von der Anzahl der gleichzeitig hergestellten Teile oder Produkte) ist ein kalendarischer Zeitraum, in dem Rohstoffe, Grundstoffe, Halbfabrikate und fertige Komponenten in fertige Produkte umgewandelt werden, oder mit anderen Worten, es ist ein Zeitraum vom Beginn des Produktionsprozesses bis zur Freigabe des fertigen Produkts oder der Charge von Teilen, Baugruppen. Beispielsweise beginnt der Produktionszyklus eines einfachen Prozesses mit der Fertigung eines Rohteils (Rohlingslos) und endet mit der Freigabe eines Fertigteils (Teilelos). Der Produktionszyklus eines komplexen Prozesses besteht aus einer Reihe einfacher Prozesse und beginnt mit der Einführung des ersten Werkstücks des Teils und endet mit der Freigabe des fertigen Produkts oder der Montageeinheit.
Die Dauer des Produktionszyklus wird in der Regel in Kalendertagen oder -stunden (bei geringer Arbeitsintensität der Produkte) ausgedrückt.
Die Kenntnis der Dauer des Produktionszyklus für die Herstellung aller Arten von Produkten (von der Herstellung von Rohlingen, Teilen bis zur Montage von Produkten) ist erforderlich: 1) um das Produktionsprogramm des Unternehmens und seiner Abteilungen zu erstellen; 2) um den Zeitpunkt des Beginns des Produktionsprozesses (Start) entsprechend dem Zeitpunkt seines Abschlusses (Freigabe) zu bestimmen; 3) für Berechnungen des Normalwerts der unfertigen Erzeugnisse.
Die Dauer des Produktionszyklus hängt von der Arbeitszeit und den natürlichen Prozessen sowie von den Pausenzeiten im Produktionsprozess ab (Abb. 2). Während Arbeitsprozessen werden technologische und nicht-technologische Operationen durchgeführt.
Die Ausführungszeit technologischer Operationen im Produktionszyklus ist der technologische Zyklus (TC). Die Ausführungszeit eines Arbeitsgangs, in der ein Teil, eine Charge gleicher Teile oder mehrere unterschiedliche Teile gefertigt werden, wird als Arbeitszyklus (Oben) bezeichnet.
Die Struktur und Dauer des Produktionszyklus hängen von der Art der Produktion, dem Organisationsgrad des Produktionsprozesses und anderen Faktoren ab.
Bei der Berechnung der Dauer des Produktionszyklus zur Herstellung eines Produkts werden nur diejenigen Zeiten berücksichtigt, die für Transport- und Kontrollvorgänge, natürliche Prozesse und Pausen aufgewendet werden, die nicht vom Betriebszyklus überlappt werden.
Die Verkürzung der Dauer des Produktionszyklus ist von großer wirtschaftlicher Bedeutung. Je kürzer die Dauer des Produktionszyklus ist, desto mehr Produkte pro Zeiteinheit können unter sonst gleichen Bedingungen in einem bestimmten Unternehmen, in einer Werkstatt oder auf einem Gelände hergestellt werden; je höher die Nutzung des Anlagevermögens des Unternehmens; desto geringer ist der Bedarf des Unternehmens Betriebskapital in laufende Arbeiten investiert; je höher die Gesamtkapitalrendite usw.
In der Fabrikpraxis wird der Produktionszyklus gleichzeitig in drei Richtungen reduziert: Die Zeit der Arbeitsprozess wird reduziert, die Zeit der natürlichen Prozesse wird reduziert und verschiedene Unterbrechungen werden vollständig eliminiert oder minimiert.
Praktische Maßnahmen zur Verkürzung des Produktionszyklus ergeben sich aus den Grundsätzen des Aufbaus des Produktionsprozesses und vor allem aus den Grundsätzen der Verhältnismäßigkeit, Parallelität und Kontinuität.
Die Verkürzung der Arbeitszeit in Bezug auf die Betriebszyklen wird durch die Verbesserung der technologischen Prozesse sowie durch die Verbesserung der Herstellbarkeit des Produktdesigns erreicht.
Entsprechend dem oben diskutierten Inhalt des Produktionsprozesses als Gesamtheit von Haupt-, Hilfs- und Dienstleistungsprozessen für Produktionszwecke unterscheidet jeder produzierende Betrieb zwischen Haupt-, Hilfs- und Nebenbetrieben und Dienstleistungsbetrieben. Ihre Zusammensetzung sowie die Formen der Produktionsbeziehungen zwischen ihnen werden üblicherweise als Produktionsstruktur des Unternehmens bezeichnet (Abb. 3).
Zusammen mit der Produktion unterscheiden Sie die allgemeine Struktur des Unternehmens. Letztere umfassen neben Produktionswerkstätten und Dienstleistungseinrichtungen für industrielle Zwecke verschiedene allgemeine Werksdienstleistungen sowie Einrichtungen und Unternehmen im Zusammenhang mit Investitionsbau, Umweltschutz und kulturellen und sozialen Dienstleistungen für Arbeitnehmer, z. B. Wohnungs- und Kommunaldienste, Nebenbetriebe, Kantinen, Apotheken, medizinische Einrichtungen, Kindergärten, Vereine usw.
Die Konstruktionsmerkmale der hergestellten Produkte und die technologischen Methoden ihrer Herstellung bestimmen weitgehend die Zusammensetzung und Art der Produktionsprozesse, die Art der Zusammensetzung der technologischen Ausrüstung, die berufliche Zusammensetzung der Arbeitnehmer, die wiederum die Zusammensetzung der Werkstätten und anderer Produktionseinheiten bestimmt, und folglich die Produktionsstruktur des Unternehmens.
Das Produktionsvolumen beeinflusst die Differenzierung der Produktionsstruktur, die Komplexität der Intraproduktionsbeziehungen zwischen den Geschäften. Je größer das Produktionsvolumen, desto größer sind in der Regel die Werkstätten des Unternehmens und desto enger ihre Spezialisierung. So können in großen Unternehmen mehrere Werkstätten innerhalb jeder Produktionsstufe eingerichtet werden.
Neben dem Volumen hat die Produktpalette einen entscheidenden Einfluss auf die Produktionsstruktur. Es hängt davon ab, ob Werkstätten und Abteilungen für die Herstellung von streng definierten Produkten oder vielfältigeren angepasst werden sollen. Je schmaler die Produktpalette, desto einfacher die Struktur des Unternehmens.
Spezialisierungsformen von Produktionseinheiten bestimmen die spezifische Zusammensetzung von technologisch und fachspezifischen Fachwerkstätten, Unternehmensteilen, deren Standort u industrielle Beziehungen zwischen ihnen, was der wichtigste Faktor bei der Bildung der Produktionsstruktur ist.
Die Produktionsstruktur eines Unternehmens kann sich lange nicht ändern, sie ist dynamisch, da Unternehmen immer erleben: die Vertiefung der gesellschaftlichen Arbeitsteilung, die Entwicklung von Technologie und Technologie, die Erhöhung des Organisationsgrades der Produktion, die Entwicklung von Spezialisierung und Zusammenarbeit, Kombination von Wissenschaft und Produktion, Verbesserung des Service des Produktionsteams. All dies macht es notwendig, es zu verbessern.
Die Struktur des Unternehmens sollte die zeitlich und räumlich richtige Kombination aller Teile des Produktionsprozesses gewährleisten.
Die Produktionsstruktur eines Unternehmens bestimmt die Arbeitsteilung zwischen seinen Betrieben und Dienstleistungsbetrieben, d. h. die innerbetriebliche Spezialisierung und Koproduktion, und bestimmt auch die zwischenbetriebliche Spezialisierung der Produktion.
Die Spezialisierungsformen der Hauptwerkstätten der produzierenden Unternehmen hängen von den Phasen ab, in denen die Produktionsprozesse stattfinden, nämlich: Beschaffung, Verarbeitung und Montage. Dementsprechend nimmt die Spezialisierung folgende Formen an: technologisch, fachlich oder fachtechnisch.
Bei der technologischen Form der Spezialisierung wird ein bestimmter Teil des technologischen Prozesses in den Werkstätten durchgeführt, der aus mehreren gleichartigen Operationen mit sehr unterschiedlichen Werkstücken besteht. Gleichzeitig wird in den Werkstätten die gleiche Art von Ausrüstung installiert, manchmal sogar in der Größenordnung. Gießerei, Schmieden, thermische, galvanische usw. können als Beispiel für technologische Spezialisierungsworkshops dienen; unter Bearbeitungswerkstätten - Drehen, Fräsen, Schleifen usw. In solchen Werkstätten wird in der Regel das gesamte Spektrum an Rohlingen oder Teilen hergestellt, oder wenn es sich um eine Montagewerkstatt handelt, werden alle von der Anlage hergestellten Produkte darin montiert ( Abb. 4).
Die technologische Form der Werkstattspezialisierung hat ihre Vor- und Nachteile. Mit einer kleinen Vielfalt an Arbeitsgängen und Geräten wird das technische Management erleichtert und es werden mehr Möglichkeiten geschaffen, die Beladung der Geräte zu regulieren, den Erfahrungsaustausch zu organisieren, rationelle technologische Produktionsmethoden anzuwenden (z. B. Spritzgießen, Kokillen- und Schleuderguss usw. ). Die technologische Form der Spezialisierung bietet eine größere Produktionsflexibilität bei der Beherrschung der Produktion neuer Produkte und der Erweiterung der Produktpalette, die ohne wesentliche Änderung der bereits verwendeten Ausrüstung und technologischen Prozesse hergestellt werden.
Allerdings hat diese Form der Spezialisierung auch erhebliche Nachteile. Es erschwert und verteuert die werksinterne Zusammenarbeit und schränkt die Verantwortung der Abteilungsleiter für die Umsetzung nur eines bestimmten Teils des Produktionsprozesses ein.
Bei der Nutzung der technologischen Form der Spezialisierung in den Beschaffungs- und Verarbeitungsbetrieben entstehen komplexe, langgestreckte Wege für die Bewegung von Arbeitsgegenständen mit ihrer wiederholten Rückkehr zu denselben Betrieben. Dies verstößt gegen das Direktflussprinzip, erschwert die Arbeitskoordination der Werkstätten und führt zu einer Verlängerung des Produktionszyklus und damit zu einer Erhöhung der unfertigen Erzeugnisse.
Nach dem technologischen Prinzip werden Werkstätten hauptsächlich in Unternehmen der Einzel- und Kleinproduktion gebildet, die eine vielfältige und instabile Produktpalette herstellen. Mit der Entwicklung der Spezialisierung der Produktion sowie der Standardisierung und Vereinheitlichung von Produkten und deren Teilen wird das technologische Prinzip der Bildung von Werkstätten in der Regel durch das Fach ergänzt, auf dessen Grundlage die Hauptwerkstätten geschaffen werden der Herstellung eines bestimmten Produkts oder eines Teils davon durch jeden von ihnen.
Die fachliche Form der Shop-Spezialisierung ist typisch für Betriebe mit enger fachlicher Spezialisierung. In den Werkstätten werden die ihnen zugeordneten Teile oder Produkte eines engen Sortiments vollständig hergestellt, beispielsweise ein Produkt, mehrere homogene Produkte oder strukturell und technologisch homogene Teile (Bild 5).
Betriebe mit einer Fachrichtung zeichnen sich durch eine Vielzahl von Ausstattungen und Werkzeugen, aber ein schmales Teile- oder Produktsortiment aus. Die Ausrüstung wird entsprechend dem technologischen Prozess ausgewählt und in Abhängigkeit von der Reihenfolge der durchgeführten Operationen angeordnet, d. H. Es wird das Prinzip des direkten Durchflusses verwendet. Eine solche Bildung von Werkstätten ist am typischsten für Serien- und Massenproduktionsunternehmen.
Die fachliche Form der Shop-Spezialisierung hat neben der technologischen auch ihre Vor- und Nachteile. Erstere umfassen eine einfache Koordinierung der Arbeit von Werkstätten, da alle Arbeitsgänge zur Herstellung eines bestimmten Produkts (Teils) in einer Werkstatt konzentriert sind. All dies führt zu einer stabilen Wiederholbarkeit des Produktionsprozesses, zu einer Erhöhung der Verantwortung des Betriebsleiters für die termingerechte Freigabe von Produkten, der erforderlichen Menge und Qualität, zur Vereinfachung der betrieblichen Produktionsplanung, zu einer Reduzierung der Produktion Zyklus, zur Verringerung der Anzahl und Vielfalt der Wege für den Transport von Arbeitsgegenständen, zur Verringerung des Zeitverlusts für die Neueinstellung der Ausrüstung, zur Verringerung der Übergangszeiten und zur Beseitigung der Alterung zwischen den Werkstätten, Schaffung günstiger Bedingungen für die die Einführung von Inline-Produktionsmethoden, integrierte Mechanisierung und Automatisierung von Produktionsprozessen.
Die Erfahrung der Unternehmen zeigt, dass die oben genannten Vorteile bei der Gegenstandsform der Spezialisierung der Werkstätten zu einer Erhöhung der Arbeitsproduktivität der Arbeiter und des Produktionsrhythmus, zu einer Senkung der Produktionskosten, einer Steigerung des Gewinns und der Rentabilität und zu einer Erhöhung der Produktionskosten führen Verbesserung anderer technischer und wirtschaftlicher Indikatoren.
Allerdings hat diese Form der Spezialisierung auch einige ganz erhebliche Nachteile. Der wissenschaftliche und technologische Fortschritt führt zu einer Erweiterung des Warenangebots und einer Zunahme der Vielfalt der eingesetzten Geräte, und bei einer engen fachlichen Spezialisierung sind die Geschäfte nicht in der Lage, das erforderliche Warensortiment ohne deren kostspieligen Umbau herzustellen.
Die Schaffung von Werkstätten, die auf die Herstellung eines begrenzten Spektrums von Arbeitsgegenständen spezialisiert sind, ist nur bei großen Produktionsmengen sinnvoll. Nur in diesem Fall ist die Verladung der Ausrüstung ausreichend abgeschlossen, und die mit dem Übergang zur Produktion einer anderen Anlage verbundene Umstellung der Ausrüstung verursacht keine großen Zeitverluste. In den Werkstätten ist es möglich, einen geschlossenen (abgeschlossenen) Produktionskreislauf durchzuführen. Solche Workshops werden themengeschlossen genannt. Sie kombinieren manchmal Beschaffungs- und Verarbeitungs- oder Verarbeitungs- und Montageschritte (z. B. eine mechanische Montagehalle).
Technologische und fachliche Spezialisierungsformen in ihrer reinen Form werden selten genutzt. Am häufigsten verwenden viele Unternehmen des verarbeitenden Gewerbes eine gemischte (fachtechnische) Spezialisierung, bei der Beschaffungswerkstätten nach einer technologischen Form gebaut und Verarbeitungs- und Montagewerkstätten zu fachgeschlossenen Werkstätten oder Abschnitten zusammengefasst werden.
Unter der Produktionsstruktur des Shops versteht man die Zusammensetzung seiner konstituierenden Produktionsstätten, Hilfs- und Serviceeinheiten sowie die Beziehung zwischen ihnen. Diese Struktur bestimmt die Arbeitsteilung zwischen den Abteilungen der Werkstatt, d. h. innerbetriebliche Spezialisierung und kooperative Produktion.
Die Produktionsstätte als eine nach dem einen oder anderen Merkmal zusammengefasste Gruppe von Arbeitsplätzen ist eine strukturelle Einheit der Werkstatt, die einer eigenen Verwaltungseinheit zugeordnet ist und von einem Meister mit mindestens 25 Arbeitern in einer Schicht geleitet wird.
Der Arbeitsplatz, der das primäre Strukturelement des Standorts ist, ist ein Teil des Produktionsbereichs, der einem Arbeiter oder einem Team von Arbeitern zugewiesen ist und auf dem sich Werkzeuge und andere Arbeitsmittel befinden, einschließlich Werkzeuge, Vorrichtungen, Handhabungs- und anderer Geräte, nach Art der an diesem Arbeitsplatz ausgeführten Arbeiten.
Die Bildung von Produktionsstätten sowie Werkstätten kann auf einer technologischen oder fachlichen Spezialisierung beruhen.
Bei technologischer Spezialisierung werden Sektionen mit homogener Ausstattung (Gruppenanordnung von Maschinen) ausgestattet.
AUFGABE
Wie ändert sich die Dauer des Produktionszyklus, wenn die sequentielle Bewegung durch eine seriell-parallele Bewegung ersetzt wird, wenn eine Charge von 3 Teilen beim ersten Vorgang bearbeitet wird - 30 Minuten, beim zweiten - 18 Minuten, beim dritten - 45 Minuten?
Geben Sie eine anschauliche Erklärung.
Antworten
Anzahl der Operationen m = 3
Der Produktionsprozess ist eine Reihe von zielgerichteten Maßnahmen des Personals des Unternehmens zur Umwandlung von Rohstoffen und Materialien in fertige Produkte.
Die Hauptkomponenten des Produktionsprozesses, die die Art der Produktion bestimmen, sind professionell ausgebildetes Personal; Arbeitsmittel (Maschinen, Ausrüstung, Gebäude, Bauwerke usw.); Arbeitsgegenstände (Rohstoffe, Materialien, Halbfabrikate); Energie (elektrisch, thermisch, mechanisch, Licht, Muskel); Informationen (wissenschaftlich-technisch, kaufmännisch, betrieblich und produktionstechnisch, rechtlich, gesellschaftspolitisch).
Das professionell gesteuerte Zusammenspiel dieser Komponenten bildet einen spezifischen Produktionsprozess und macht dessen Inhalt aus.
Der Produktionsprozess ist die Grundlage eines jeden Unternehmens. Der Inhalt des Produktionsprozesses hat einen entscheidenden Einfluss auf den Aufbau des Unternehmens und seiner Produktionseinheiten.
Der Hauptteil des Produktionsprozesses ist der technologische Prozess. Während der Durchführung des technologischen Prozesses ändern sich die geometrischen Formen, Größen und physikalischen und chemischen Eigenschaften der Arbeitsgegenstände.
Die Produktionsprozesse werden nach ihrer Bedeutung und Rolle in der Produktion unterteilt in: Haupt-, Hilfs- und Dienstleistungsprozesse.
Die wichtigsten werden als Produktionsprozesse bezeichnet, bei denen die Herstellung der vom Unternehmen hergestellten Hauptprodukte durchgeführt wird.
Nebenprozesse umfassen Prozesse, die den unterbrechungsfreien Ablauf der Hauptprozesse sicherstellen. Ihr Ergebnis sind die im Unternehmen selbst eingesetzten Produkte. Hilfsmittel sind die Prozesse zur Reparatur von Geräten, zur Herstellung von Geräten, zur Erzeugung von Dampf, Druckluft usw.
Als Dienstprozesse werden solche bezeichnet, bei deren Durchführung die für das normale Funktionieren sowohl der Haupt- als auch der Hilfsprozesse erforderlichen Dienste ausgeführt werden. Dies sind die Prozesse des Transports, der Lagerhaltung, der Teilekommissionierung, der Reinigung von Räumen usw.
Der Produktionsprozess besteht aus vielen verschiedenen Operationen, die jeweils in Haupt- (technologische) und Hilfsoperationen unterteilt sind.
Ein technologischer Vorgang ist ein Teil des Produktionsprozesses, der an einem Arbeitsplatz an einem Produktionsgegenstand (Teil, Baugruppe, Produkt) von einem oder mehreren Arbeitern ausgeführt wird.
Je nach Art und Zweck der Produkte, dem Grad der technischen Ausstattung, werden die Arbeitsgänge in manuelle, maschinell-manuelle, maschinelle und Hardware unterteilt.
Manuelle Operationen werden manuell mit einfachen Werkzeugen (manchmal mechanisiert) durchgeführt, wie z. B. manuelles Lackieren, Zusammenbau, Produktverpackung usw.
Maschinell-manuelle Arbeiten werden mit Hilfe von Maschinen und Mechanismen unter obligatorischer Beteiligung eines Arbeiters durchgeführt, zum Beispiel der Transport von Waren mit Elektroautos, die Bearbeitung von Teilen auf Werkzeugmaschinen mit manueller Ablage.
Die Maschinenoperationen werden vollständig von der Maschine mit minimaler Beteiligung der Arbeiter am technologischen Prozess ausgeführt, z. B. das Installieren von Teilen in der Bearbeitungszone und das Entfernen nach Abschluss der Bearbeitung, die Überwachung des Maschinenbetriebs, d.h. Arbeiter beteiligen sich nicht an technologischen Vorgängen, sondern kontrollieren sie nur.
Hardwareoperationen finden in speziellen Einheiten (Behälter, Bäder, Öfen usw.) statt. Der Werker überwacht die Funktionsfähigkeit der Geräte und Instrumentenablesungen und passt gegebenenfalls die Betriebsarten der Einheiten entsprechend den Anforderungen der Technologie an. Hardware-Operationen sind in der Lebensmittel-, Chemie-, Metallurgie- und anderen Industrien weit verbreitet.
Die Organisation des Produktionsprozesses besteht darin, Menschen, Werkzeuge und Arbeitsgegenstände zu einem einzigen Produktionsprozess materieller Güter zusammenzufassen sowie eine räumlich und zeitlich rationelle Kombination der Haupt-, Hilfs- und Dienstleistungsprozesse sicherzustellen.
Die wirtschaftliche Effizienz der rationellen Organisation des Produktionsprozesses äußert sich in der Verkürzung der Dauer des Produktionszyklus von Produkten, in der Senkung der Produktionskosten, in der besseren Nutzung des Anlagevermögens und in der Erhöhung des Umlaufs des Betriebskapitals.
Die Art der Produktion wird durch ein komplexes Merkmal technischer, organisatorischer u wirtschaftliche Merkmale Produktion aufgrund der Breite der Nomenklatur, der Regelmäßigkeit, der Stabilität und des Produktionsvolumens. Der Hauptindikator, der die Art der Produktion charakterisiert, ist der Konsolidierungskoeffizient der Operationen Kz. Der Afür eine Gruppe von Arbeitsplätzen ist definiert als das Verhältnis der Anzahl aller verschiedenen technologischen Arbeitsgänge, die während des Monats durchgeführt wurden oder durchgeführt werden sollen, zur Anzahl der Arbeitsplätze:
KZ = | Zu Opi | ||||
Kr. M. |
|||||
wobei Kopi die Anzahl der durchgeführten Operationen ist i-ter Arbeiter Ort; Kr.m - die Anzahl der Arbeitsplätze auf der Website oder im Geschäft.
Es gibt drei Arten der Produktion: Einzel-, Serien- und Massenproduktion.
Die Einzelproduktion ist gekennzeichnet durch ein geringes Produktionsvolumen identischer Produkte, deren Nachfertigung und Reparatur in der Regel nicht vorgesehen sind. Das Pinning-Verhältnis für eine einzelne Produktion liegt normalerweise über 40.
Die Serienfertigung ist gekennzeichnet durch die Herstellung oder Reparatur von Produkten in sich periodisch wiederholenden Chargen. Abhängig von der Anzahl der Produkte in einer Charge oder Serie und dem Wert des Konsolidierungskreises der Betriebe wird zwischen Klein-, Mittel- und Großserienfertigung unterschieden.
Für die Kleinproduktion beträgt der Konsolidierungskoeffizient 21 bis 40 (einschließlich), für die mittlere Produktion - von 11 bis 20 (einschließlich) und für die Großproduktion - von 1 bis 10 (einschließlich).
Die Massenproduktion ist gekennzeichnet durch eine große Menge an Produkten, die über einen langen Zeitraum kontinuierlich hergestellt oder repariert werden, während der die meisten Arbeitsplätze einen Arbeitsgang ausführen. Der Koeffizient der Fixierungsvorgänge für die Massenproduktion wird mit 1 angenommen.
Berücksichtigen Sie die technischen und wirtschaftlichen Merkmale jeder Produktionsart.
Die Einzel- und Kleinserienfertigung in deren Nähe ist gekennzeichnet durch die Fertigung von Teilen einer großen Bandbreite an Arbeitsplätzen ohne spezielle Fachrichtung. Diese Produktion muss ausreichend flexibel und an die Ausführung verschiedener Produktionsaufträge angepasst sein.
Technologische Prozesse unter den Bedingungen der Stückfertigung werden in Form von Routenplänen für die Bearbeitung von Teilen für jeden Auftrag erweitert entwickelt; Abschnitte sind mit universellen Geräten und Werkzeugen ausgestattet, die die Herstellung einer breiten Palette von Teilen gewährleisten. Die große Vielfalt der Aufgaben, die viele Arbeitnehmer ausführen müssen, erfordert unterschiedliche berufliche Fähigkeiten, sodass hochqualifizierte allgemeine Arbeitnehmer im Betrieb eingesetzt werden. In vielen Bereichen, insbesondere in der Pilotfertigung, wird eine Berufskombination praktiziert.
Die Organisation der Produktion unter den Bedingungen der Stückproduktion hat ihre eigenen Merkmale. Aufgrund der Vielfalt der Teile, der Reihenfolge und der Methoden ihrer Verarbeitung werden Produktionsstätten nach dem technologischen Prinzip mit der Anordnung der Ausrüstung in homogenen Gruppen aufgebaut. Bei dieser Produktionsorganisation durchlaufen die Teile im Fertigungsprozess verschiedene Abschnitte. Daher müssen bei der Übertragung auf jeden nachfolgenden Vorgang (Abschnitt) die Fragen der Qualitätskontrolle der Verarbeitung, des Transports und der Bestimmung von Jobs für den nächsten Vorgang sorgfältig berücksichtigt werden. Merkmale der Betriebsplanung und -verwaltung sind die rechtzeitige Kommissionierung und Ausführung von Aufträgen, die Überwachung des Fortschritts jedes Details im Betrieb,
Gewährleistung des systematischen Ladens von Websites und Jobs. Große Schwierigkeiten ergeben sich bei der Organisation der materiellen und technischen Versorgung. Eine breite Palette von Fertigprodukten, die Verwendung von erhöhten Verbrauchsraten von Materialien erschweren die ununterbrochene Versorgung, weshalb Unternehmen große Materialvorräte anhäufen, was wiederum zu einer Schwächung des Betriebskapitals führt.
Merkmale der Organisation der Stückproduktion wirken sich auf die wirtschaftliche Leistung aus. Für Unternehmen, in denen eine einzige Produktionsart vorherrscht, sind eine relativ hohe Arbeitsintensität der Produkte und ein großes Volumen an unfertigen Erzeugnissen aufgrund der langen Lagerzeiten von Teilen zwischen den Vorgängen charakteristisch. Die Kostenstruktur von Produkten ist durch einen hohen Kostenanteil für z Löhne. Dieser Anteil beträgt in der Regel 20-25%.
Die wichtigsten Möglichkeiten zur Verbesserung der technischen und wirtschaftlichen Kennziffern einer Einzelproduktion sind mit ihrer technischen und organisatorischen Annäherung an die Serienproduktion verbunden. Die Verwendung von Serienproduktionsmethoden ist möglich mit einer Einengung des Spektrums hergestellter Teile für allgemeine Maschinenbauanwendungen, einer Vereinheitlichung von Teilen und Baugruppen, die es ermöglichen, zur Organisation von Fachgebieten überzugehen; Erweiterung der konstruktiven Kontinuität, um die Chargen von Startteilen zu erhöhen; Gruppieren von Teilen, die in Konstruktion und Fertigungsreihenfolge ähnlich sind, um die Zeit für die Vorbereitung der Produktion zu verkürzen und die Nutzung der Ausrüstung zu verbessern.
Die Serienfertigung ist gekennzeichnet durch die Produktion eines begrenzten Teilespektrums in Chargen, die sich in regelmäßigen Abständen wiederholen. Dies ermöglicht Ihnen die Verwendung zusammen mit dem Universal Spezialausrüstung. Bei der Gestaltung technologischer Prozesse sehen sie die Reihenfolge der Ausführung und Ausrüstung für jeden Vorgang vor.
Die folgenden Merkmale sind typisch für die Organisation der Serienfertigung. Geschäfte haben in ihrer Zusammensetzung in der Regel thematisch geschlossene Bereiche, auf denen im Laufe eines typischen technologischen Prozesses Geräte platziert werden. Dadurch entstehen relativ einfache Verbindungen zwischen Arbeitsplätzen und es werden Voraussetzungen geschaffen, um den direkten Teilefluss im Herstellungsprozess zu organisieren.
Die fachliche Spezialisierung der Sektionen macht es sinnvoll, eine Charge von Teilen parallel auf mehreren Maschinen zu bearbeiten, die aufeinanderfolgende Arbeitsgänge ausführen. Sobald der vorherige Arbeitsgang die ersten Teile fertig bearbeitet hat, werden diese vor dem Ende der Bearbeitung der gesamten Charge in den nächsten Arbeitsgang überführt. Somit wird es unter den Bedingungen der Massenproduktion möglich, den Produktionsprozess parallel und sequentiell zu organisieren. Das ist sein Erkennungsmerkmal.
Die Verwendung der einen oder anderen Organisationsform unter den Bedingungen der Massenproduktion hängt von der Arbeitsintensität und dem Produktionsvolumen der dem Standort zugewiesenen Produkte ab. Somit können große, arbeitsintensive Teile in gefertigt werden
in großen Mengen und mit einem ähnlichen technologischen Prozess werden sie einem Standort zugeordnet, auf dem die Produktion mit variablem Durchfluss organisiert wird. Teile mittlerer Größe, multifunktional und weniger arbeitsintensiv werden in Chargen zusammengefasst. Wird ihr Produktionsstart regelmäßig wiederholt, werden Chargenverarbeitungsbereiche organisiert. Kleine, arbeitsarme Teile, wie z. B. normalisierte Stehbolzen, Bolzen, werden an einem spezialisierten Abschnitt befestigt. In diesem Fall ist die Organisation einer Direktflussproduktion möglich.
Serienproduktionsunternehmen zeichnen sich durch eine deutlich geringere Arbeitsintensität und Kosten der Herstellung von Produkten aus als in einem einzigen. In der Serienfertigung werden Produkte im Vergleich zur Einzelfertigung mit weniger Unterbrechungen verarbeitet, was das Volumen der laufenden Arbeiten reduziert.
Aus organisatorischer Sicht ist die Hauptreserve zur Steigerung der Arbeitsproduktivität in der Massenproduktion die Einführung von Massenproduktionsmethoden.
Die Massenproduktion ist am spezialisiertesten und zeichnet sich durch die Produktion eines begrenzten Teilespektrums in großen Mengen aus. Massenproduktionswerkstätten sind mit modernster Ausrüstung ausgestattet, die eine nahezu vollständige Automatisierung der Teileherstellung ermöglicht. Automatische Produktionslinien sind hier weit verbreitet.
Technologische Prozesse der Bearbeitung werden sorgfältiger entwickelt, durch Übergänge. Jeder Maschine wird eine relativ kleine Anzahl von Arbeitsgängen zugewiesen, was ein möglichst vollständiges Laden von Jobs gewährleistet. Die Ausrüstung befindet sich in einer Kette entlang des technologischen Prozesses der einzelnen Teile. Arbeiter spezialisieren sich darauf, ein oder zwei Operationen durchzuführen. Details werden Stück für Stück von Betrieb zu Betrieb übertragen. Unter den Bedingungen der Massenproduktion nimmt die Bedeutung der Organisation des interoperativen Transports und der Instandhaltung von Arbeitsplätzen zu. Die ständige Überwachung des Zustands des Schneidwerkzeugs, der Vorrichtungen und der Ausrüstung ist eine der Bedingungen für die Gewährleistung der Kontinuität des Produktionsprozesses, ohne die der Arbeitsrhythmus auf den Baustellen und in den Werkstätten zwangsläufig gestört wird. Die Notwendigkeit, einen bestimmten Rhythmus in allen Phasen der Produktion einzuhalten, wird zu einem charakteristischen Merkmal der Organisation von Prozessen in der Massenproduktion.
Die Massenproduktion bietet die umfassendste Nutzung der Ausrüstung, ein hohes Gesamtniveau an Arbeitsproduktivität und die niedrigsten Kosten für die Herstellung von Produkten. Im Tisch. 1.1 enthält Daten zu den vergleichenden Merkmalen verschiedener Produktionsarten.
Tabelle 1.1 Vergleichsmerkmale verschiedener Produktionsarten
Verglichen | Art der Produktion | |||||||
Zeichen | Singular | seriell | fest |
|||||
Nomenklatur | unbegrenzt | begrenzt |
||||||
Ausgabevolumen | Nomenklatur | Nomenklatur | Nomenklatur |
|||||
gefertigt gem | hergestellt | hergestellt in |
||||||
Parteien | ||||||||
Mengen |
||||||||
Wiederholbarkeit | abwesend | Zeitschrift | Konstante |
|||||
Anwendbarkeit | Universal- | teilweise speziell | meistens |
|||||
Ausrüstung | speziell |
|||||||
Verankerung | abwesend | begrenzt | eins zwei | Operationen |
||||
Operationen | Bedienungsdetail | auf der Maschine | ||||||
Maschinen | ||||||||
Standort | ||||||||
Ausrüstung | homogene Maschinen | wird bearbeitet | technologisch |
|||||
konstruktiv | Verfahren | wird bearbeitet |
||||||
technologisch | ||||||||
homogene Teile | ||||||||
Übertragung von Gegenständen | konsistent | parallel | parallel |
|||||
Arbeit aus dem Betrieb | parallel | |||||||
für Chirurgie | ||||||||
Organisationsform | technologisch | Thema | geradlinig |
|||||
Produktion | ||||||||
Verfahren |
1.4. Organisation des Produktionsprozesses
v Raum und Zeit
Der Aufbau einer rationellen Produktionsstruktur des Unternehmens erfolgt in der folgenden Reihenfolge:
- die Zusammensetzung der Werkstätten des Unternehmens, ihre Kapazität in Größen, die eine bestimmte Produktion von Produkten gewährleisten, werden festgelegt;
- die Flächen für jede Werkstatt und jedes Lager werden berechnet, ihre räumliche Anordnung wird im Masterplan des Unternehmens festgelegt;
- alle Verkehrsverbindungen innerhalb des Unternehmens sind geplant, ihr Zusammenwirken mit nationalen (unternehmensexternen) Strecken;
- die kürzesten Transportwege von Arbeitsgegenständen zwischen den Werkstätten im Laufe des Produktionsprozesses werden skizziert.
Die Produktionseinheiten umfassen Werkstätten, Abteilungen, Labors, in denen die Hauptprodukte (vom Unternehmen hergestellt), Komponenten (von außen zugekauft), Materialien u
Halbfabrikate, Ersatzteile für die Produktwartung und -reparatur während des Betriebs; verschiedene Arten von Energie werden für technologische Zwecke erzeugt usw.
ZU Zu den Unterabteilungen, die den Arbeitnehmern dienen, gehören Wohnungs- und Kommunalabteilungen, ihre Dienstleistungen, Küchenfabriken, Kantinen, Kantinen, Kindergärten und Kindertagesstätten, Sanatorien, Pensionen, Erholungsheime, Apotheken, medizinische Einheiten, freiwillige Sportvereine, technische Ausbildungsabteilungen und Bildungseinrichtungen, die an der Verbesserung der Produktionsfähigkeiten, des kulturellen Niveaus von Arbeitern, Ingenieuren und technischen Arbeitern beteiligt sind , Mitarbeiter.
Die wichtigste strukturelle Produktionseinheit eines Unternehmens (mit Ausnahme von Unternehmen mit einer Nicht-Ladenverwaltungsstruktur) ist eine Werkstatt - ein administrativ getrenntes Glied, das einen bestimmten Teil des gesamten Produktionsprozesses (Produktionsphase) durchführt.
Werkstätten sind vollwertige Unterabteilungen, die ihre Tätigkeit nach den Grundsätzen der Kostenrechnung ausüben. Im Maschinenbau werden Werkstätten üblicherweise in vier Gruppen eingeteilt: Haupt-, Hilfs-, Neben- und Hilfswerkstätten. In den Hauptwerkstätten werden Arbeiten zur Herstellung von zum Verkauf bestimmten Produkten durchgeführt. Die Hauptwerkstätten gliedern sich in Beschaffung, Bearbeitung und Montage.
ZU Rohlinge umfassen Gießereien, Schmieden und Stanzen, Schmieden und Pressen, manchmal Werkstätten für Schweißkonstruktionen; zur Verarbeitung
- Bearbeitung, Holzbearbeitung, thermische, galvanische Beschichtung, Schutz- und Dekorationsbeschichtung von Teilen, Montagewerkstätten - Gesamt- und Endmontage von Produkten, deren Lackierung, Komplettierung mit Ersatzteilen und abnehmbaren Geräten.
Hilfswerkstätten - Werkzeug, nicht standardmäßige Ausrüstung, Modell, Reparatur, Energie, Transport.
Nebenprodukte - Geschäfte für Recycling und Verarbeitung von Metallabfällen durch Gießen und Pressen von Spänen zu Briketts, Geschäfte für Konsumgüter. Hilfswerkstätten, die Behälter für Produktverpackungen und Schnittholz herstellen, Produkte konservieren, verpacken, verladen und an den Verbraucher versenden.
Neben diesen Werkstätten verfügt fast jeder Maschinenbaubetrieb über Produktionswerkstätten, Dienstleistungen und Abteilungen für nichtindustrielle Einrichtungen (kommunale, kulturelle und private Einrichtungen, Wohnungen usw.).
Einen bestimmten Platz in der Struktur aller Maschinenbaubetriebe nehmen Lager, sanitäre Einrichtungen und Kommunikationsmittel (Stromnetze, Gas- und Luftleitungen, Heizung, Lüftung, gut instand gehaltene Schienen und spurlose Transportstraßen usw.) ein.
Eine besondere Rolle in der Produktionsstruktur des Vereins (Unternehmens) spielen Design, technologische Abteilungen,
Forschungsinstitute und Labors. Sie entwickeln Zeichnungen, technologische Prozesse, führen experimentelle Arbeiten durch, bringen Produktdesigns in Übereinstimmung mit den Anforderungen von GOST, technischen Spezifikationen und führen experimentelle und Entwicklungsarbeiten durch. In diesen Untergliederungen manifestiert sich die Integration von Wissenschaft und Produktion besonders stark.
Die Werkstätten umfassen Haupt- und Nebenproduktionsstätten.
Die Hauptproduktionsstätten werden nach dem technologischen oder fachlichen Prinzip gebildet. In Bereichen, die nach dem Prinzip der technologischen Spezialisierung organisiert sind, werden technologische Operationen bestimmter Art durchgeführt. In einer Gießerei können beispielsweise Abschnitte in folgenden technologischen Bereichen organisiert werden: Landvorbereitung, Herstellung von Stäben, Gussformen, Bearbeitung fertiger Gussteile usw. in einer Schmiede - Abschnitte zur Herstellung von geschmiedeten Rohlingen auf Hämmern und Pressen, Wärmebehandlung usw. in mechanischen - Dreh-, Revolver-, Fräs-, Schleif-, Schlosser- und anderen Abschnitten, in Montage - Abschnitten der Knoten- und Endmontage von Produkten, Prüfung ihrer Teile und Systeme, Kontroll- und Prüfstation, Lackierung , usw.
In nach dem Prinzip der fachlichen Spezialisierung organisierten Bereichen werden nicht einzelne Arten von Operationen durchgeführt, sondern technologische Prozesse als Ganzes, wodurch fertige Produkte für diesen Bereich erhalten werden.
Zu den Hilfskräften gehören die Abteilungen des Chefmechanikers und des Chefenergietechnikers für die laufende Reparatur und Wartung von Maschinen- und Energieanlagen; eine Werkzeug- und Vertriebskammer mit einer Schleifwerkstatt, einem Transportdienst, einer Werkstatt für die Reparatur und Wartung von technologischen Geräten usw.
Bei einem zentralisierten System zur Organisation von Wartungsarbeiten und laufenden Reparaturen im Unternehmen werden keine Hilfsabteilungen in den Geschäften erstellt.
Hilfsbetriebe und Abteilungen sind nach den gleichen Kriterien organisiert wie die Betriebe und Abteilungen der Hauptproduktion.
Der ständige Appell der Unternehmensleitung an die Faktoren Außenumgebung ermöglicht Ihnen eine zeitnahe Änderung der Führungsstruktur, um zur Stabilität des Unternehmens und seiner flexiblen Reaktion auf Marktschwankungen im Marktumfeld beizutragen. Aus diesem Grund sollte die Organisation des Produktionsmanagements (Territorial-, Transport-, Ressourcen-, technologische und andere Faktoren) als ein System von Maßnahmen betrachtet werden, das die Entwicklung eines Unternehmens leitet.
Die Produktionsstruktur wird durch eine Reihe von Faktoren beeinflusst:
Branchenzugehörigkeit des Unternehmens - Produktpalette, Konstruktionsmerkmale, verwendete Materialien, Methoden zur Gewinnung und Verarbeitung von Rohlingen; Einfachheit des Designs und Herstellbarkeit des Produkts; die Höhe der Anforderungen an die Produktqualität; Art der Produktion, Grad ihrer Spezialisierung und Zusammenarbeit;
Zusammensetzung der Ausrüstung und technologischen Ausrüstung (Universal-, Spezial-, Nicht-Standard-Ausrüstung, Förder- oder automatische Linien):
- zentrale oder dezentrale Organisation der Gerätewartung, ihrer laufenden Reparatur und technologischen Ausrüstung;
- die Fähigkeit der Produktion, schnell und ohne große Verluste reorganisiert zu werden, um neue Produkte in einer geänderten Produktpalette herzustellen;
- die Art des Produktionsprozesses in den Haupt-, Hilfs-, Neben- und Nebenbetrieben.
Die Produktionsstruktur eines Unternehmens in verschiedenen Branchen hat ihre eigenen Merkmale, die sich aus der Art der Hauptproduktion ergeben.
In Textilfabriken arbeitet meist eine technologische Struktur mit gleichzeitiger Spezialisierung einzelner Sektionen auf bestimmte Garnnummern und Rohartikel. Die größte Anzahl von Fabriken verfügt über alle Stufen der Stoffherstellung: Spinnen, Weben, Veredeln. Einige Fabriken spezialisieren sich auf ein oder zwei Stufen.
In Hüttenwerken überwiegt die technologische Struktur. Pilot-, Hochofen-, Stahl- und Walzwerk werden errichtet.
Allgemein in der Produktionsstruktur von Unternehmen in verschiedenen Branchen
- Organisation von Hilfs- und Dienstleistungsbetrieben. Geschäfte des Chef-Energieingenieurs und Chef-Mechanikers, Transport- und Lagereinrichtungen sind in Unternehmen jeder Branche verfügbar. Im Maschinenbauwerk gibt es immer eine Werkzeugmacherei, in der Textilfabrik gibt es Fäll- und Pendelwerkstätten, die Werkzeuge für die Textilproduktion herstellen.
Die Frage der Auswahl und Verbesserung der Produktionsstruktur eines Unternehmens (Verband) sollte sowohl beim Aufbau neuer Unternehmen als auch beim Wiederaufbau bestehender Unternehmen angegangen werden.
Die wichtigsten Möglichkeiten zur Verbesserung der Produktionsstruktur:
- Vergrößerung von Betrieben und Werkstätten;
- Suche und Umsetzung eines perfekteren Prinzips des Bauens von Werkstätten
Und produzierende Unternehmen;
- Einhaltung eines rationellen Verhältnisses zwischen Haupt-, Hilfs- und Servicewerkstätten;
- ständige Arbeit zur Rationalisierung der Unternehmensplanung;
- Integration einzelner Unternehmen, Schaffung mächtiger Industrie- und Forschungs- und Produktionsverbände aufgrund der Konzentration der Produktion;
- Gewährleistung der Verhältnismäßigkeit zwischen allen Teilen des Unternehmens;
- Änderung des Produktionsprofils, d. h. Art der Leistung, Spezialisierung und Zusammenarbeit; Entwicklung der kombinierten Produktion; Leistung konstruktive und technologische Homogenität
Produkte durch breite Vereinheitlichung und Standardisierung; Schaffung einer nicht werkstättenbezogenen Unternehmensverwaltungsstruktur. Die Vergrößerung von Betrieben und Werkstätten ermöglicht die Einführung neuer Hochleistungsmaschinen in größerem Maßstab, die ständige Verbesserung der Technologie und die Verbesserung der Produktionsorganisation.
Die Identifizierung und Umsetzung von Reserven zur Verbesserung der Struktur von Shops und Produktionsstätten sind Faktoren für die kontinuierliche Verbesserung der Produktionsstruktur und die Steigerung der Produktionseffizienz.
Die Einhaltung eines rationellen Verhältnisses zwischen Haupt-, Hilfs- und Dienstleistungsbetrieben und -standorten sollte verstärkt angestrebt werden spezifisches Gewicht Hauptwerkstätten nach der Anzahl der beschäftigten Arbeiter, den Kosten des Anlagevermögens, der Größe der belegten Flächen.
Die Rationalisierung der Planung impliziert die Verbesserung des Masterplans des Unternehmens.
Die Qualität der Nutzung vorhandener Möglichkeiten, Ressourcen und eines günstigen Marktumfeldes ist im Unternehmen mit dem Mechanismus der Produktionsplanung verbunden. Die Erstellung eines optimalen Plans im Hinblick auf eine mögliche Änderung der Marktsituation ist der Schlüssel zur Umsetzung der internen Stabilität des Unternehmens im externen wirtschaftlichen Umfeld. Deshalb sollten Sie dem Produktionsplanungsmaterial besondere Aufmerksamkeit schenken.
Der Masterplan ist einer der wichtigsten Teile des Projekts eines Industrieunternehmens und enthält eine umfassende Lösung für die Fragen Planung und Landschaftsgestaltung, Platzierung von Gebäuden, Strukturen, Verkehrskommunikation, Ingenieurnetze, Organisation von Haushalts- und Verbraucherdienstsystemen, sowie der Standort des Unternehmens in einem Industriegebiet (Knoten).
Der Masterplan unterliegt hohen Anforderungen, von denen die wichtigsten sind:
1) der Standort von Produktionseinheiten streng im Laufe des technologischen Prozesses - Lager für Rohstoffe, Materialien und Halbfabrikate, Beschaffungs-, Verarbeitungs-, Montagehallen, Lager für Fertigprodukte;
2) Platzierung von Hilfsstandorten, landwirtschaftlichen Betrieben in der Nähe der Hauptproduktionsstätten, die sie bedienen;
3) rationelle Anordnung von Gleisen innerhalb des Unternehmens. Sie müssen sowohl mit den Räumlichkeiten der Lager für Rohstoffe, Materialien und Halbfertigprodukte als auch mit dem Lager der Fertigprodukte verbunden sein, wo die Produkte mit abnehmbaren Geräten, Ersatzteilen, Konservierung, Verpackung, Verschließung, Verladung und Versand von Produkten vervollständigt werden an den Verbraucher;
4) größte Geradlinigkeit und kürzeste Transportwege von Rohstoffen, Materialien, Halbfabrikaten und Fertigprodukten;
5) Ausschluss von Gegen- und Rückströmen im Innen- und Außenbereich;
6) die zweckmäßigsten Optionen, um die externe Kommunikation des Unternehmens zu lokalisieren und sie mit Ingenieurnetzen, Autobahnen, Eisenbahnen usw. zu verbinden.
7) Praktikum in Werkstättenblöcken von Laboratorien (Meß-, Chemie-, Röntgenkontrolle, Ultraschall usw.), die ihnen dienen, sowie Geschäfte für Wärmebehandlung und Schutzbeschichtung von Teilen, Fertigprodukten.
Bei großen Unternehmen empfiehlt es sich, Werkstätten zu Gebäuden zusammenzufassen. Bei der Gestaltung von Unternehmen ist Vorsicht geboten
Kompaktheit bauen. Abhängig von der Art des Produkts und seinen Designmerkmalen ist es möglich, mehrstöckige Gebäude zu bauen. Wählen Sie vernünftige Abstände zwischen Geschäften, Geschäftsblöcken und Gebäuden und beachten Sie dabei die sanitären und technischen Bedingungen sowie die Sicherheits- und Brandschutzanforderungen.
Auch der Masterplan sollte die Möglichkeit vorsehen weitere Entwicklung Unternehmen und stellen eine solche Produktionsstruktur bereit, in der die höchsten Produktionsergebnisse zu den niedrigsten Kosten erzielt werden können; Bedingungen für die maximale Befriedigung der Interessen aller Mitarbeiter des Unternehmens schaffen.
Platzierung der Haupt-, Hilfs-, Neben- und Hilfswerkstätten
Und Standorte, die landwirtschaftliche Betriebe, Regierungen und Transportwege auf dem Territorium des Unternehmens bedienen, haben einen enormen Einfluss auf die Organisation der Produktion und seine Wirtschaft.
bestimmt die Richtung der Güterströme, die Länge der Gleise
Und spurlose Gleise sowie die Effizienz der Nutzung von Produktionsflächen.
Die Kompaktheit des Gebäudes, seine rationelle Dichte und Anzahl der Stockwerke ermöglichen Einsparungen Kapital Investitionen, Volumen reduzieren Bauarbeiten und innerbetrieblicher Transport, Verkürzung der Kommunikationsdauer, Verkürzung der Dauer des Produktionszyklus, Einführung einer umfassenden Mechanisierung und Automatisierung von Produktions- und Hilfsprozessen in größerem Maßstab, Verkürzung der Verweildauer der fertigen Produkte im Lager, Steigerung der Arbeitsproduktivität, Verbesserung der Produktqualität, Reduzierung der Kosten.
Die Aufgabe der Mitarbeiter von Designinstituten, Ingenieuren und Technikern sowie Produktionsmitarbeitern von Industrieunternehmen ist die ständige Verbesserung der Produktionsstruktur, des Standorts von Werkstätten und Produktionsstätten. In der Zeit des Umbaus, der technischen Umrüstung, der Betriebserweiterung und des Neubaus muss diesem Thema besondere Aufmerksamkeit geschenkt werden. Die Verbesserung des Masterplans der Anlage ist Ausdruck der Sorge um die Steigerung der Produktionseffizienz, die Verbesserung der Produktqualität und der Arbeitsbedingungen.
Die Analyse von Informationen über die Dynamik der internen Unterstützung der Produktion des Unternehmens und die Nachfrage nach seinen Produkten auf dem Markt ist eine Voraussetzung für eine qualitative Bewertung seiner Nachhaltigkeit. Gleichzeitig kann die Beachtung der Aufrechterhaltung der Produktion im Unternehmen die Faktoren der Fähigkeit oder Unfähigkeit des Unternehmens und der nachhaltigen Entwicklung in der Zukunft aufdecken. Gleichzeitig kann der Mechanismus einer solchen Analyse die Fixierung der Beziehung zwischen den Eigenschaften der Dienstleistung und den Zielen sein, die allgemeinen Merkmale der Produktionsdienstleistung im Unternehmen sicherzustellen.
Die Organisationsform der Produktion ist eine bestimmte zeitliche und räumliche Kombination der Elemente des Produktionsprozesses mit einem angemessenen Grad ihrer Integration, ausgedrückt durch ein System stabiler Beziehungen.
Verschiedene zeitliche und räumliche Strukturkonstruktionen bilden eine Reihe von Grundformen der Organisation der Produktion. Die temporäre Struktur der Produktionsorganisation wird durch die Zusammensetzung der Elemente des Produktionsprozesses und die Reihenfolge ihres zeitlichen Zusammenwirkens bestimmt. Je nach Art der temporären Struktur werden Organisationsformen mit sequentiellem, parallelem und parallel-sequentiellem Transfer von Arbeitsgegenständen in der Produktion unterschieden.
Die Organisationsform der Produktion mit sequentiellem Transfer von Arbeitsgegenständen ist eine solche Kombination von Elementen des Produktionsprozesses, die die Bewegung verarbeiteter Produkte in allen Produktionsbereichen in Chargen beliebiger Größe sicherstellt. Die Arbeitsgegenstände für jeden nachfolgenden Arbeitsgang werden erst nach Abschluss der Bearbeitung des gesamten Stapels an den vorherigen Arbeitsgang übergeben. Diese Form ist am flexibelsten in Bezug auf Änderungen, die im Produktionsprogramm auftreten, ermöglicht es Ihnen, die Ausrüstung vollständig zu nutzen, wodurch die Anschaffungskosten gesenkt werden können. Der Nachteil dieser Organisationsform der Produktion liegt in der relativ langen Dauer des Produktionszyklus, da jedes Teil vor der Durchführung des nächsten Arbeitsgangs der Bearbeitung der gesamten Charge vorweggenommen wird.
Die Organisationsform der Produktion mit paralleler Überführung von Arbeitsgegenständen basiert auf einer solchen Kombination von Elementen des Produktionsprozesses, die es ermöglicht, Arbeitsgegenstände Stück für Stück und ohne Wartezeiten zu starten, zu bearbeiten und von Betrieb zu Betrieb zu überführen. Diese Organisation des Produktionsprozesses führt zu einer Reduzierung der zu bearbeitenden Teile, einer Reduzierung des Platzbedarfs für Lager und Gänge. Sein Nachteil ist die mögliche Ausfallzeit von Geräten (Arbeitsplätzen) aufgrund von Unterschieden in der Betriebsdauer.
Dazwischen liegt die Organisationsform der Produktion mit parallel-sequentiellem Transfer von Arbeitsgegenständen
serielle und parallele Formen und eliminiert teilweise ihre inhärenten Nachteile. Produkte von Betrieb zu Betrieb werden von Transportparteien transportiert. Dies gewährleistet die Kontinuität des Einsatzes von Ausrüstung und Arbeitskräften, es ist möglich, den Durchgang einer Teilecharge durch die Arbeitsgänge des technologischen Prozesses teilweise parallel zu führen.
Die räumliche Struktur der Produktionsorganisation wird durch die Menge der auf der Baustelle konzentrierten technologischen Ausrüstung (die Anzahl der Arbeitsplätze) und ihren Standort im Verhältnis zur Bewegungsrichtung der Arbeitsgegenstände im umgebenden Raum bestimmt. Je nach Anzahl der technologischen Ausstattung (Arbeitsplätze) gibt es einen Single-Link Produktionssystem und die ihm entsprechende Struktur eines separaten Arbeitsplatzes und einer Mehrgelenkanlage mit Werkstatt-, Linien- oder Zellenstruktur. Mögliche Optionen für die räumliche Struktur der Produktionsorganisation sind in Abb. 1 dargestellt. 1.2. Die Werkstattstruktur ist gekennzeichnet durch die Schaffung von Standorten, an denen sich Geräte (Arbeitsplätze) parallel zum Werkstückfluss befinden, was deren Spezialisierung auf der Grundlage technologischer Homogenität impliziert. In diesem Fall wird eine am Standort ankommende Teilecharge zu einem der freien Arbeitsplätze geschickt, wo der erforderliche Bearbeitungszyklus durchlaufen wird, und anschließend an einen anderen Standort (in die Werkstatt) verbracht.
Reis. 1.2. Varianten der räumlichen Struktur des Produktionsprozesses
An einem Standort mit linearer Raumstruktur werden im Laufe des technologischen Prozesses Anlagen (Arbeitsplätze) angesiedelt und eine Charge von am Standort bearbeiteten Teilen sequentiell von einem Arbeitsplatz zum anderen transferiert.
Die zellulare Struktur der Produktionsorganisation vereint die Merkmale eines Linien- und Shopfloors. Die Kombination von räumlichen und zeitlichen Strukturen des Produktionsprozesses auf einer bestimmten Ebene der Integration von Teilprozessen bestimmt verschiedene Organisationsformen der Produktion: technologisch, subjektiv, direkt fließend, punktuell, integriert (Abb. 1.3). Betrachten Sie die charakteristischen Merkmale von jedem von ihnen.
Reis. 1.3. Organisationsformen der Produktion
Die technologische Form der Organisation des Produktionsprozesses ist durch eine Ladenstruktur mit konsequentem Transfer von Arbeitsgegenständen gekennzeichnet. Diese Organisationsform ist in Maschinenbaubetrieben weit verbreitet, da sie eine maximale Anlagenauslastung in der Kleinserienfertigung sicherstellt und an häufige Änderungen im technologischen Prozess angepasst ist. Gleichzeitig hat der Einsatz einer technologischen Organisationsform des Produktionsprozesses eine Reihe negativer Folgen. Eine große Anzahl von Teilen und deren wiederholte Bewegung während der Bearbeitung führen zu einer Erhöhung des Arbeitsvolumens und einer Erhöhung der Anzahl von Zwischenlagern. Ein wesentlicher Teil des Produktionszyklus ist der Zeitverlust durch komplexe bereichsübergreifende Kommunikation.
Die Subjektform der Organisation der Produktion hat eine zellulare Struktur mit einer parallel-sequentiellen (sequentiellen) Übertragung von Arbeitsgegenständen in der Produktion. Auf dem Fachgebiet ist in der Regel die gesamte Ausrüstung installiert, die für die Bearbeitung einer Gruppe von Teilen vom Anfang bis zum Ende des technologischen Prozesses erforderlich ist. Ist der technologische Verarbeitungskreislauf innerhalb des Bereichs geschlossen, spricht man von subjektgeschlossen.
Die gegenständliche Konstruktion von Abschnitten stellt die Geradheit sicher und reduziert die Dauer des Produktionszyklus für die Herstellung von Teilen. Im Vergleich mit der technologischen Form erlaubt das Thema eins, die Gesamtkosten für den Transport von Teilen, den Bedarf an Produktionsfläche pro Produktionseinheit zu reduzieren. Allerdings hat diese Organisationsform der Produktion auch Nachteile. Der Hauptgrund ist, dass bei der Bestimmung der Zusammensetzung der auf der Baustelle installierten Ausrüstung die Notwendigkeit bestimmter Arten der Bearbeitung von Teilen im Vordergrund steht, was nicht immer eine volle Auslastung der Ausrüstung gewährleistet.
Darüber hinaus erfordern die Erweiterung der Palette der hergestellten Produkte und ihre Erneuerung eine regelmäßige Neuentwicklung der Produktionsstätten und Änderungen in der Struktur des Geräteparks. Direktflussform der Organisation der Produktion ist gekennzeichnet durch lineare Struktur mit stückweisem Transfer von Arbeitsgegenständen. Diese Form gewährleistet die Umsetzung einer Reihe von Organisationsprinzipien: Spezialisierung, Direktfluss, Kontinuität, Parallelität. Seine Anwendung führt zu einer Verkürzung der Dauer des Produktionszyklus, mehr effiziente Nutzung Arbeitskräfte aufgrund einer stärkeren Spezialisierung der Arbeitskräfte, wodurch das Volumen der laufenden Arbeiten verringert wird.
Bei einer punktuellen Organisationsform der Produktion wird die Arbeit vollständig an einem Arbeitsplatz verrichtet. Das Produkt wird dort hergestellt, wo sich sein Hauptteil befindet. Ein Beispiel ist die Montage eines Produkts, um das herum sich der Arbeiter bewegt. Die Organisation der Punktproduktion hat eine Reihe von Vorteilen: Sie bietet die Möglichkeit häufiger Änderungen des Produktdesigns und der Verarbeitungsreihenfolge, der Herstellung von Produkten verschiedener Nomenklatur in der Menge, die durch den Produktionsbedarf bestimmt wird; Kosten für den Standortwechsel von Anlagen werden reduziert, die Produktionsflexibilität wird erhöht.
Eine integrierte Organisationsform der Produktion beinhaltet die Zusammenfassung von Haupt- und Nebentätigkeiten zu einem einzigen integrierten Produktionsprozess mit zellularer oder linearer Struktur mit sequentiellem, parallelem oder parallel-sequentiellem Transfer von Arbeitsgegenständen in der Produktion. Im Gegensatz zur bisherigen Praxis der getrennten Gestaltung der Prozesse Lagern, Transportieren, Verwalten, Verarbeiten in Bereichen mit integrierter Organisationsform ist es erforderlich, diese Teilprozesse zu einem einzigen Produktionsprozess zu verknüpfen. Dies wird erreicht, indem alle Arbeitsplätze mit Hilfe eines automatischen Transport- und Lagerkomplexes kombiniert werden, bei dem es sich um eine Reihe miteinander verbundener, automatischer und speicherbarer Geräte sowie Computerausrüstung handelt, die zur Organisation der Lagerung und Bewegung von Arbeitsgegenständen zwischen einzelnen Arbeitsplätzen bestimmt ist.
Die Verwaltung des Produktionsprozesses erfolgt hier über einen Computer, der das Funktionieren aller Elemente des Produktionsprozesses am Standort nach folgendem Schema sicherstellt: Suche
das benötigte Werkstück im Lager - Transport des Werkstücks zur Maschine - Bearbeitung - Rückführung des Teils ins Lager. Um zeitliche Abweichungen beim Transport und der Bearbeitung von Teilen auszugleichen, werden an einzelnen Arbeitsplätzen Pufferlager für Betriebs- und Versicherungsreserven gebildet. Die Schaffung integrierter Produktionsstandorte ist mit relativ hohen Einmalkosten verbunden, die durch die Integration und Automatisierung des Produktionsprozesses entstehen.
Der wirtschaftliche Effekt beim Übergang zu einer integrierten Produktionsorganisation wird durch die Reduzierung der Produktionszyklusdauer für Fertigungsteile, die Erhöhung der Beschickungszeit von Werkzeugmaschinen und die Verbesserung der Regelung und Steuerung von Produktionsprozessen erreicht. Auf Abb. 1.4 zeigt die Anordnung der Geräte in Bereichen mit verschiedene Form Organisation der Produktion.
Reis. 1.4. Anordnungen von Einrichtungen (Arbeitsplätzen) an Standorten mit unterschiedlichen Formen der Produktionsorganisation:
a) technologisch; b) Thema; c) geradeaus; d) Punkt (für den Montagefall); e) integriert
- Dies ist eine zielgerichtete, schrittweise Umwandlung von Rohstoffen und Materialien in ein fertiges Produkt mit einer bestimmten Eigenschaft, das zum Verzehr oder zur Weiterverarbeitung geeignet ist. Der Produktionsprozess beginnt mit seinem Projekt und endet an der Schnittstelle von Produktion und Konsum, wonach der Konsum der hergestellten Produkte erfolgt.
Die technischen und organisatorischen und wirtschaftlichen Merkmale des Produktionsprozesses werden nicht durch die Art des Produkts, das Produktionsvolumen, die Art und Art der verwendeten Ausrüstung und Technologie sowie den Spezialisierungsgrad bestimmt.
Der Produktionsprozess in Unternehmen ist in zwei Arten unterteilt: Haupt- und Hilfs. Die Hauptprozesse sind in direktem Zusammenhang mit der Umwandlung von Arbeitsgegenständen in fertige Produkte. Zum Beispiel Erz im Hochofen schmelzen und in Metall verwandeln oder Mehl zu Teig und dann zu fertig gebackenem Brot verarbeiten.
Helferprozesse: Arbeitsgegenstände bewegen, Geräte reparieren, Räume reinigen usw. Diese Arten von Arbeiten tragen nur zum Ablauf grundlegender Prozesse bei, sind aber selbst nicht direkt daran beteiligt.
Der Hauptunterschied zwischen Hilfsprozessen und den Hauptprozessen ist der Unterschied zwischen Verkaufsort und Verbrauchsort. Die Produkte der Hauptproduktion, in denen die Hauptproduktionsprozesse durchgeführt werden, werden gemäß den abgeschlossenen Lieferverträgen an Verbraucher verkauft. Dieses Produkt hat einen eigenen Markennamen, eine eigene Kennzeichnung, und es wird ein Marktpreis dafür festgelegt.
Produkte der Hilfsproduktion, in denen Hilfsprozesse und Dienstleistungen durchgeführt werden, werden innerhalb des Unternehmens verbraucht. Die Kosten für Wartung und Nebenarbeiten werden vollständig auf die Kosten des Hauptprodukts angerechnet, das nebenbei an die Verbraucher verkauft wird.
Fertigungsbetrieb
Der Produktionsprozess gliedert sich in viele elementare technologische Vorgänge, die als Arbeitsgänge bezeichnet werden. Fertigungsbetrieb ist Teil des Herstellungsprozesses. In der Regel wird sie an einem Arbeitsplatz ohne Neueinstellung der Ausrüstung und mit einem Satz gleicher Werkzeuge durchgeführt. Wie der Produktionsprozess selbst werden die Arbeitsgänge in Haupt- und Hilfsbetriebe unterteilt.
Um die Herstellungskosten von Produkten zu senken, die Organisation und Zuverlässigkeit des Produktionsprozesses zu verbessern, wird eine Reihe der folgenden Regeln und Methoden verwendet:- Spezialisierung von Standorten, Arbeitsplätzen;
- Kontinuität und Geradlinigkeit des technologischen Prozesses;
- Parallelität und Proportionalität der Produktionsvorgänge.
Spezialisierung
Die Spezialisierung liegt darin, dass jeder Werkstatt, jedem Bereich, jedem Arbeitsplatz ein technologisch homogenes oder fest definiertes Produktspektrum zugeordnet ist. Die Spezialisierung ermöglicht es in der Praxis, die Prinzipien der Kontinuität und des direkten Flusses anzuwenden - die wirtschaftlich vorteilhaftesten Methoden zur Organisation der Produktion.
Kontinuität- Dies ist eine Reduzierung oder Reduzierung auf null Unterbrechungen bei der Produktion von Fertigprodukten, außerdem beginnt jeder nachfolgende Vorgang desselben Prozesses unmittelbar nach dem Ende des vorherigen, wodurch die Zeit für die Herstellung von Produkten verkürzt und die Ausfallzeiten von Geräten und Arbeitsplätzen verringert werden .
Geradheit charakterisiert die Bewegung von Arbeitsgegenständen im Laufe des Produktionsprozesses und sorgt für jedes Produkt kürzester Weg nach Arbeitsplätzen.
Eine solche Bewegung zeichnet sich durch die Eliminierung aller Rück- und Gegenbewegungen im Produktionsprozess aus, was zur Reduzierung der Transportkosten beiträgt.
Die Regel der Parallelität impliziert die gleichzeitige Ausführung verschiedener Operationen bei der Herstellung desselben Produkts. Diese Regel ist besonders in der Serien- und Massenproduktion weit verbreitet.
Die Regel der Parallelität beinhaltet:- parallele (gleichzeitige) Produktion verschiedener Baugruppen und Teile, die zur Vervollständigung (Montage) des Endprodukts bestimmt sind;
- Gleichzeitige Ausführung verschiedener technologischer Operationen bei der Bearbeitung identischer Teile und Baugruppen auf einer Vielzahl von parallelen Geräten.
Unter dem Gesichtspunkt der Kosteneinsparung ist es sehr wichtig, bestimmte Proportionen der Kapazität (Produktivität) des Geräteparks zwischen Werkstätten und Abteilungen, die an der Herstellung von Produkten arbeiten, zu beachten.
Produktionszyklus
Der abgeschlossene Kreis der Produktionsvorgänge vom ersten bis zum letzten bei der Herstellung von Produkten wird als bezeichnet Produktionszyklus.
Aufgrund der Tatsache, dass der Produktionsprozess in Zeit und Raum abläuft, kann der Produktionszyklus daher durch die Länge des Bewegungswegs des Produkts und seiner Komponenten und die Zeit, während der das Produkt den gesamten Bearbeitungsweg durchläuft, gemessen werden . Die Länge des Produktionszyklus ist keine Linie, sondern ein breites Band, auf dem Maschinen, Geräte, Inventar usw. platziert sind, daher wird in der Praxis in den meisten Fällen nicht die Länge des Weges bestimmt, sondern die Fläche und das Volumen der Räumlichkeiten, in denen sich die Produktion befindet.
Das Intervall der Kalenderzeit vom Beginn des ersten Produktionsvorgangs bis zum Ende des letzten wird als Zeitdauer des Produktionszyklus des Produkts bezeichnet. Die Dauer des Zyklus wird in Tagen, Stunden, Minuten, Sekunden gemessen, abhängig von der Art des Produkts und der Verarbeitungsphase, für die der Zyklus gemessen wird.
Die Dauer des Produktionszyklus umfasst drei Phasen:- Bearbeitungszeit (Arbeitszeitraum)
- Produktionswartungszeit
- geht kaputt.
Arbeitsperiode- Dies ist der Zeitraum, in dem entweder vom Arbeiter selbst oder von Maschinen und Mechanismen unter seiner Kontrolle ein direkter Einfluss auf das Arbeitsobjekt ausgeübt wird, sowie die Zeit natürlicher Prozesse, die im Produkt ohne Beteiligung von auftreten Menschen und Technik.
Zeit der natürlichen Prozesse- Dies ist die Arbeitszeit, in der das Arbeitsobjekt seine Eigenschaften ohne direkten Einfluss einer Person oder von Mechanismen ändert. Zum Beispiel Lufttrocknung eines lackierten Produkts oder Kühlung eines erhitzten Produkts, Wachstum auf den Feldern und Reifung von Pflanzen, Fermentation bestimmter Produkte usw.
Die Wartungszeit umfasst:- Produktqualitätskontrolle;
- Kontrolle der Betriebsarten von Maschinen und Geräten, deren Einstellung und Einstellung, kleinere Reparaturen;
- Reinigung des Arbeitsplatzes;
- Transport von Rohlingen, Materialien, Annahme und Reinigung von bearbeiteten Produkten.
Pausen- das ist die Zeit, in der das Arbeitsobjekt nicht beeinflußt wird und sich seine qualitativen Eigenschaften nicht ändern, das Produkt aber noch nicht fertig ist und der Produktionsprozess noch nicht abgeschlossen ist. Zwischen Pausen unterscheiden: reguliert und nicht reguliert.
Geplante Pausen werden in überbetrieblich (innerschichtlich) und überschichtig (verbunden mit der Betriebsweise) unterteilt.
Ungeplante Pausen verbunden mit Ausfallzeiten von Ausrüstung und Arbeitern aus unvorhergesehenen Gründen (Rohstoffmangel, Maschinenausfall, Fehlzeiten von Arbeitern usw.). Im Produktionsablauf werden ungeplante Pausen in Form eines Korrekturfaktors eingerechnet oder nicht berücksichtigt.
Produktionsarten
Die Dauer des Produktionszyklus hängt maßgeblich von der Bewegungsreihenfolge der Arbeitsgegenstände im Zuge ihrer Verarbeitung und der Art der Produktion ab.
Die Reihenfolge der Bewegung von Produkten und Komponenten im Produktionsprozess entspricht dem Volumen und der Häufigkeit der Produktion. Es wird durch die gleichen Zeichen bestimmt.
Derzeit ist es üblich, zwischen folgenden Produktionsarten zu unterscheiden:- gemischt.
- kleinteilig
- mittlere Serie
- großflächig.
Die Massen- und Massenproduktion von Produkten ermöglicht es Ihnen, eine kontinuierliche synchrone Bewegung von Produkten im Prozess ihrer Verarbeitung zu organisieren. Bei einer solchen Organisation bewegen sich alle Komponenten, aus denen das fertige Produkt zusammengesetzt wird, kontinuierlich von der ersten bis zur letzten technologischen Operation. Die in Bewegungsrichtung zu Einheiten und Baugruppen zusammengesetzten Einzelteile bewegen sich in zusammengesetzter Form weiter, bis sie das fertige Produkt bilden. Diese Methode der Organisation der Produktion wird genannt im Einklang.
Die Fließmethode der Produktionsorganisation basiert auf der zeitlich koordinierten rhythmischen Wiederholung der Haupt- und Hilfsproduktionsvorgänge, die an spezialisierten Stellen entlang des technologischen Prozesses durchgeführt werden. Unter den Bedingungen der Inline-Produktion werden Proportionalität, Kontinuität und Rhythmus des Produktionsprozesses erreicht.
Fließband
Das Hauptglied der Massenproduktion ist Fließband. Unter einer Produktionslinie wird eine Kombination aus einer bestimmten Anzahl von Arbeitsplätzen verstanden, die sich entlang des technologischen Prozesses befinden und dazu bestimmt sind, die ihnen zugewiesenen Arbeitsgänge abwechselnd auszuführen. Produktionslinien werden in kontinuierliche, intermittierende und freie Taktlinien unterteilt..
kontinuierliche Produktionslinie- Dies ist ein Förderer, auf dem das Produkt für alle Arbeitsgänge kontinuierlich verarbeitet (oder montiert) wird, ohne zwischen den Arbeitsgängen zu verfolgen. Die Bewegung der Produkte auf dem Förderer erfolgt parallel und synchron.
Diskontinuierliche Produktionslinie bezeichnet eine Linie, auf der die Beförderung von Produkten für den Betrieb nicht streng geregelt ist. Es passiert zeitweise. Solche Linien zeichnen sich durch die Isolierung technologischer Vorgänge und erhebliche Abweichungen in der Dauer verschiedener Vorgänge vom durchschnittlichen Zyklus aus. Thread-Synchronisation erreicht verschiedene Wege, auch zu Lasten interoperativer Rückstände (Reserven).
Produktionslinien im freien Rhythmus werden Linien genannt, auf denen der Transfer einzelner Teile oder Produkte (ihrer Chargen) mit einigen Abweichungen vom berechneten (festgelegten) Arbeitsrhythmus durchgeführt werden kann. Gleichzeitig wird zum Ausgleich dieser Abweichungen und zur Sicherstellung eines unterbrechungsfreien Arbeitens am Arbeitsplatz ein überbetrieblicher Warenvorrat (Reserve) angelegt.
Grundsätze der Organisation des Produktionsprozesses. Der Produktionsprozess ist eine Gesamtheit von miteinander in Beziehung stehenden Haupt-, Hilfs- und Dienstleistungsprozessen von Arbeits- und Naturprozessen
Herstellungsprozess ist eine Gesamtheit von miteinander verbundenen Grund-, Hilfs- und Dienstleistungsarbeitsprozessen und natürlichen Prozessen, durch die Rohstoffe in fertige Produkte oder Dienstleistungen umgewandelt werden. Die Produktionsprozesse in jedem Unternehmen werden je nach ihrer Rolle bei der Herstellung von Produkten unterteilt in Haupt-, Hilfs- und Wartung. Als Ergebnis der Umsetzung der Hauptprozesse werden Rohstoffe und Materialien in fertige Produkte umgewandelt.
Hilfs umfassen Prozesse, deren Zweck und Zweck es ist, eine reibungslose und effiziente Umsetzung der Grundlagen des Produktionsprozesses zu gewährleisten (Herstellung von Werkzeugen, Reparatur von Betriebsmitteln).
Zum Servieren Prozesse umfassen Prozesse im Zusammenhang mit der Erbringung von Produktionsdienstleistungen für die Hauptproduktion (Material- und technische Versorgung, technische Kontrolle usw.).
Die Zusammensetzung und Beziehung der Haupt-, Neben- und Dienstprozesse bilden sich Struktur des Produktionsprozesses. Prozesse bestehen aus Aktivitäten.
Betrieb bezeichnet Teil des technischen Prozesses, der an einem Gegenstand an einem Arbeitsplatz durchgeführt wird. Operationen wiederum in Übergänge unterteilt, Handlungen und Bewegungen. Operationen können mit oder ohne menschliches Eingreifen durchgeführt werden. Operationen können maschinell-manuell, maschinell, manuell, instrumentell, automatisiert und natürlich sein..
Bei manuellen Operationen werden Prozesse ohne die Hilfe von Maschinen und Mechanismen ausgeführt. Maschinell-manuelle Operationen werden von Maschinen und Mechanismen unter aktiver Beteiligung der Arbeiter ausgeführt. Hardwareoperationen werden in speziellen Geräten durchgeführt. Automatisierte Operationen werden an automatischen Geräten ohne aktives Eingreifen des Arbeiters ausgeführt. Naturbetriebe sind Vorgänge, die in der Produktion unter dem Einfluss natürlicher Prozesse (Trocknung) stattfinden.
Kernstück des Produktionsprozesses eines jeden Unternehmens ist eine räumlich und zeitlich sinnvolle Verknüpfung der Haupt-, Hilfs- und Dienstleistungsprozesse. Organisation Herstellungsprozesse im Unternehmen basiert auf dem Folgenden allgemeine Grundsätze.
1. Das Spezialisierungsprinzip bedeutet eine Verringerung der Vielfalt von Jobs, Operationen, Verarbeitungsmodi und anderen Elementen der Prozesse. Diese wiederum wird durch die Vielfalt der Produktpalette bestimmt. Die Spezialisierung ist eine der Formen der Arbeitsteilung, die die Zuordnung und Prüfung von Unternehmen und einzelnen Arbeitsplätzen bestimmt.
2. Der Grundsatz der Verhältnismäßigkeit beinhaltet die Einhaltung des richtigen Verhältnisses von Produktionskapazitäten und -flächen zwischen einzelnen Arbeitsplätzen, Abteilungen, Werkstätten. Die Verletzung der Verhältnismäßigkeit führt zur Bildung von Engpässen, dh zur Überlastung einiger Arbeitsplätze und zur Unterbelastung anderer, wodurch die Produktionskapazitäten nicht voll ausgelastet werden, die Ausrüstung stillsteht, was zu einer Verschlechterung der Leistung des Unternehmens führt.
3. Das Prinzip der Parallelität gekennzeichnet durch die Gleichzeitigkeit von Arbeitsgängen, Teilen des Produktionsprozesses. Parallelität kann während der Ausführung der Operation selbst, während des Ablaufs benachbarter Operationen, der Durchführung der Haupt-, Hilfs- und Dienstprozesse stattfinden.
4. Prinzip des direkten Durchflusses bedeutet die räumliche Zusammenführung von Arbeitsgängen und Prozessteilen, ausgenommen die Rückbewegung von Arbeitsgegenständen im Verarbeitungsprozess. Dadurch wird sichergestellt, dass das Produkt alle Phasen und Vorgänge des Produktionsprozesses auf dem kürzesten Weg durchläuft. Die Hauptbedingung für den direkten Fluss ist die räumliche Platzierung der Ausrüstung im Laufe des technologischen Prozesses sowie die miteinander verbundene Lage von Gebäuden und Bauwerken auf dem Territorium des Unternehmens.
5. Kontinuitätsprinzip des Produktionsprozesses bedeutet die Kontinuität der Bewegung von Arbeitsgegenständen in der Produktion ohne Ausfallzeiten und Warten auf die Verarbeitung sowie die Kontinuität der Arbeit von Arbeitern und Ausrüstung. Dies erreicht rationelle Nutzung Anlagen und Produktionsbereiche. Der Produktionsprozess von Produkten wird beschleunigt, Nebenkosten werden eliminiert und die Arbeitsproduktivität erhöht.
6. Das Prinzip des Rhythmus Die Produktion zeichnet sich durch eine gleichmäßige Ausgabe von Produkten für gleiche Zeitintervalle und die entsprechende Einheitlichkeit der an jedem Standort am Arbeitsplatz ausgeführten Arbeiten aus. Die Hauptbedingungen für die Gewährleistung des Rhythmus sind strikte Einhaltung Technologie- und Arbeitsdisziplin, rechtzeitige Bereitstellung von Materialien, Halbfabrikaten und Strom usw. Je höher der Spezialisierungsgrad, desto eher kann der Produktionsrhythmus sichergestellt werden.
8.2. Berechnung der Dauer des Produktionszyklus
bei verschiedene Arten Bewegung von Arbeitsgegenständen
Einer der wichtigsten Indikatoren für die Qualität der Organisation des Produktionsprozesses ist der Produktionszyklus. Als Produktionszyklus wird der kalendarische Zeitraum bezeichnet, in dem der Produktionsprozess zur Herstellung eines Produkts oder eines Teils davon durchgeführt wird. Das Konzept des Produktionszyklus kann der Herstellung einer Charge von Produkten oder Teilen zugeordnet werden.
Der Produktionszyklus umfasst:
1. Betriebszeit welches beinhaltet:
¾ technologische Operationen;
¾ Transportvorgänge;
¾ Kontrolloperationen;
¾ Montagearbeiten;
¾ natürliche Prozesse.
2. Pausen, die stattfinden:
¾ während der Arbeitszeit und werden aufgeteilt:
¾ Interoperative Pausen;
¾ Zykluspausen;
¾ Pausen aus organisatorischen Gründen;
¾ außerhalb der Arbeitszeit.
Pausen bestehen aus einer Pause, die mit der Arbeitszeit verbunden ist (Pausen zwischen Schichten, Mittagspausen, arbeitsfreien Tagen), Unterbrechungen zwischen den Zyklen, die auftreten, wenn Produkte von Werkstatt zu Werkstatt, von Standort zu Standort, interbetrieblich, verbunden mit Erwartungen und Alterung verbunden werden von Teilen beim Transfer von einem Arbeitsplatz zum anderen.
Der Produktionszyklus hängt von der Art der hergestellten Produkte, dem organisatorischen und technischen Niveau der Produktion ab. Das Zeitverhältnis zur Durchführung der einzelnen Grundelemente des Zyklus bestimmt dessen Struktur.
Die Dauer der technologischen Operationen im Produktionszyklus wird genannt technologischer Zyklus. Sein konstituierendes Element ist der Betriebszyklus, der allgemein für eine Charge von Teilen nach der Formel (8.1) berechnet wird:
wo - die Größe der Teilecharge;
- normale Betriebszeit;
Der technologische Zyklus hängt von der Kombination der Ausführungszeit bestimmter Zyklen ab, die durch die Reihenfolge der Übergabe von Arbeitsgegenständen im Produktionsprozess bestimmt wird. Unterscheiden drei Bewegungsarten Arbeit im Produktionsprozess:
1) konsistent;
2) serien-parallel;
3) parallel.
Bei sequentielle Form Bewegung einer Charge von Teilen, jeder vorherige Vorgang wird erst zugeordnet, nachdem die Bearbeitung aller Teile der Charge bei der vorherigen Operation abgeschlossen ist. Gleichzeitig liegt jedes Teil an jedem Arbeitsplatz und wartet zunächst auf seine Bearbeitungswarteschlange und wartet dann auf die Beendigung der Bearbeitung aller anderen Teile in diesem Vorgang. Die Dauer des technologischen Zyklus mit der sequentiellen Bewegung von Arbeitsgegenständen kann durch die Formel (8.2) bestimmt werden:
, (8.2)
wo ist die Anzahl der Operationen im Prozess;
- Losgröße von Teilen;
- normale Betriebszeit;
- Anzahl der Jobs pro Vorgang.
Die sequentielle Art der Bewegung von Arbeitsgegenständen ist die einfachste, hat aber gleichzeitig lange Unterbrechungen aufgrund von Leerlaufteilen, die auf die Verarbeitung warten. Infolgedessen ist der Zyklus sehr lang, was den Umfang der laufenden Arbeiten und den Bedarf an Betriebskapital erhöht. Die sequentielle Art der Bewegung von Arbeitsgegenständen ist charakteristisch für eine einzelne Kleinproduktion.
Bei serien-parallel B. in Form der Bewegung von Arbeitsgegenständen, beginnt der Folgevorgang früher, als die Bearbeitung der gesamten Teilecharge im vorherigen Vorgang endet. Die Chargen werden nicht vollständig, sondern in Teilen (Transportchargen) an den Folgebetrieb übergeben. In diesem Fall gibt es eine teilweise Überlappung in der Ausführungszeit benachbarter Betriebszyklen.
Die Dauer des technologischen Zyklus zur Bearbeitung einer Charge von Teilen mit einer sequentiell parallelen Art der Bewegung von Arbeitsgegenständen kann durch die Formel (8.3) bestimmt werden:
, (8.3)
wo - die Größe des Transferlos;
- Anzahl der Operationen im Prozess;