Der Produktionsprozess und die Grundprinzipien seiner Organisation. Organisation der Produktion
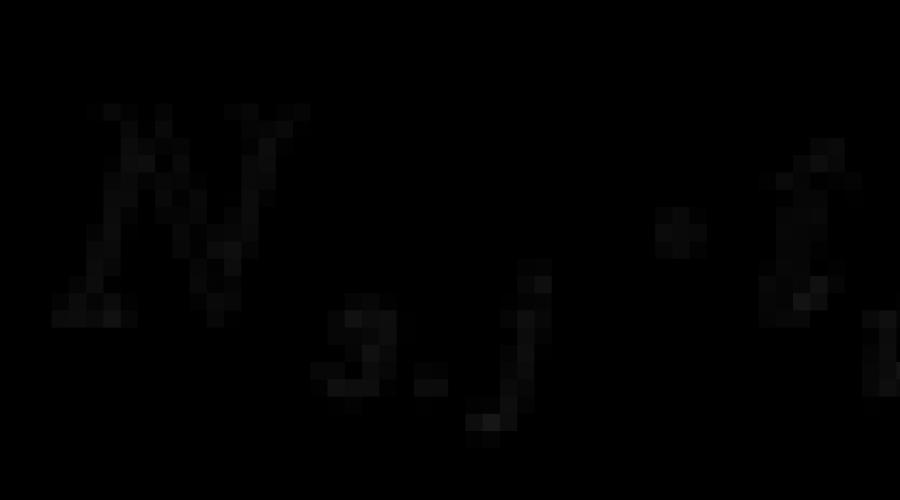
Der Produktionsprozess besteht aus Teilprozessen, die sich nach folgenden Merkmalen in Gruppen einteilen lassen:
Nach Ausführungsart: manuell, mechanisiert, automatisiert.
Nach Zweck und Rolle in der Produktion: Haupt-, Hilfs-, Service
Grundlegende Produktionsprozesse sind solche Prozesse, die in direktem Zusammenhang mit der Umwandlung des Arbeitsgegenstandes in fertige Produkte stehen. Im Maschinenbau beispielsweise ist das Ergebnis der Hauptprozesse die Herstellung von Maschinen, Apparaten und Instrumenten, die das Produktionsprogramm des Unternehmens bilden und seiner Spezialisierung entsprechen, sowie die Herstellung von Ersatzteilen für diese zur Lieferung an der Verbraucher. Die Gesamtheit solcher Teilprozesse bildet die Hauptproduktion.
Unterstützende Fertigungsprozesse sind Prozesse, die etwas schaffen die notwendigen Voraussetzungen um fertige Produkte herzustellen oder fertige Produkte herzustellen, die dann in der Hauptproduktion im Unternehmen selbst verbraucht werden. Zu den Hilfsprozessen gehören die Reparatur von Geräten, die Herstellung von Werkzeugen, Vorrichtungen, Ersatzteilen sowie Mechanisierungs- und Automatisierungsgeräte Eigenproduktion, Erzeugung aller Arten von Energie. Die Gesamtheit solcher Teilprozesse stellt die Hilfsproduktion dar.
Wartung von Produktionsprozessen – bei der Umsetzung solcher Prozesse werden keine Produkte hergestellt, sondern Dienstleistungen erbracht, die für die Umsetzung von Haupt- und Hilfsprozessen erforderlich sind. Zum Beispiel Transport, Lagerung, Ausgabe von Rohstoffen und Materialien aller Art, Kontrolle der Genauigkeit von Instrumenten, Auswahl und Fertigstellung von Teilen, technische Kontrolle der Produktqualität usw. Die Gesamtheit dieser Prozesse stellt die Dienstleistungsproduktion dar.
Hilfsprozess. Ein Prozess, der den normalen Ablauf des Hauptprozesses der Transformation des Arbeitsgegenstandes erleichtert und mit der Bereitstellung von Ausrüstung, Geräten, Schneid- und Messwerkzeugen sowie Brennstoff- und Energieressourcen für den Hauptprozess verbunden ist.
Serviceprozess. Ein Prozess, der sich nicht speziell auf ein bestimmtes Arbeitsthema bezieht und den normalen Ablauf von Haupt- und Hilfsprozessen durch die Bereitstellung von Transport- und Logistikdienstleistungen am „Eingang“ und „Ausgang“ der Organisation gewährleistet.
Die Hauptproduktionsprozesse finden in den Phasen Beschaffung, Verarbeitung, Montage und Prüfung statt.
Die Beschaffungsphase ist für die Herstellung von Rohteilen vorgesehen. Die Besonderheit der Entwicklung technologischer Prozesse in diesem Stadium besteht darin, dass die Rohlinge den Formen und Größen der Fertigteile näher kommen. Es zeichnet sich durch eine Vielfalt an Produktionsmethoden aus. Zum Beispiel das Schneiden oder Schneiden von Rohlingen aus einem Material, das Herstellen von Rohlingen durch Gießen, Stanzen, Schmieden usw.
Die Verarbeitungsstufe ist die zweite Stufe im Produktionsprozess. Gegenstand der Arbeit ist hier die Vorbereitung von Teilen. Die Arbeitsmittel in dieser Phase sind hauptsächlich Metallschneidemaschinen, Öfen zur Wärmebehandlung und Geräte zur chemischen Verarbeitung. Als Ergebnis dieser Phase erhalten die Teile Abmessungen, die einer bestimmten Genauigkeitsklasse entsprechen.
Die Montagephase ist der Teil des Produktionsprozesses, der zu Montageeinheiten oder fertigen Produkten führt. Gegenstand der Arbeit in dieser Phase sind Komponenten und Teile aus der eigenen Produktion sowie solche, die von außen bezogen werden (Komponenten). Montageprozesse zeichnen sich durch ein erhebliches Volumen aus handgefertigt Daher besteht die Hauptaufgabe des technologischen Prozesses in deren Mechanisierung und Automatisierung.
Die Testphase ist die letzte Phase des Produktionsprozesses, deren Zweck darin besteht, die erforderlichen Parameter des Endprodukts zu erhalten. Gegenstand der Arbeit sind hier fertige Produkte, die alle vorherigen Phasen durchlaufen haben.
Die Bestandteile der Stufen des Produktionsprozesses sind technologische Vorgänge.
Ein Produktionsvorgang ist eine elementare Handlung (Arbeit), die darauf abzielt, den Arbeitsgegenstand umzuwandeln und ein bestimmtes Ergebnis zu erzielen. Ein Fertigungsvorgang ist ein eigenständiger Teil des Fertigungsprozesses. Normalerweise wird es an einem Arbeitsplatz ohne Neukonfiguration der Ausrüstung und mit einem Satz derselben Werkzeuge durchgeführt.
5.1 Konzept des Produktionsprozesses
Der Produktionsprozess besteht aus einer Reihe miteinander verbundener Haupt-, Hilfs- und Serviceprozesse Arbeitskräfte und Werkzeuge zur Schaffung von Verbraucherwerten – nützliche Arbeitsgegenstände, die für die Produktion oder den persönlichen Konsum notwendig sind. Im Produktionsprozess beeinflussen Arbeiter mit Hilfe von Werkzeugen Arbeitsgegenstände und schaffen neue Fertigprodukte, zum Beispiel Maschinen, Computer, Fernseher, elektronische Geräte usw. Gegenstände und Werkzeuge stehen als materielle Elemente der Produktion in einer bestimmten Beziehung miteinander im Unternehmen Freund: Bestimmte Objekte können nur mit bestimmten Werkzeugen bearbeitet werden; Sie haben bereits an sich systemische Eigenschaften. Die lebendige Arbeit muss diese Dinge jedoch annehmen und damit den Prozess beginnen, sie in ein Produkt umzuwandeln. Somit ist der Produktionsprozess in erster Linie ein Arbeitsprozess, da die von einer Person bei seinem Input genutzten Ressourcen, sowohl Informationen als auch materielle Produktionsmittel, das Produkt früherer Arbeitsprozesse sind. Es gibt Haupt-, Hilfs- und Nebenproduktionsprozesse .
Hauptproduktionsprozesse- Dies ist der Teil der Prozesse, bei dem es zu einer direkten Veränderung der Formen/Größen, Eigenschaften, der inneren Struktur von Arbeitsgegenständen und ihrer Umwandlung in fertige Produkte kommt. In einem Werkzeugmaschinenbetrieb sind dies beispielsweise die Prozesse der Herstellung von Teilen und der Montage von Unterbaugruppen, Einheiten und dem Produkt als Ganzes daraus.
Zu Hilfsproduktionsprozessen umfassen solche Prozesse, deren Ergebnisse entweder direkt in den Hauptprozessen verwendet werden oder deren unterbrechungsfreien Betrieb gewährleisten Wirksame Umsetzung. Beispiele für solche Prozesse sind die Herstellung von Werkzeugen, Vorrichtungen, Formen, Mitteln zur Mechanisierung und Automatisierung der eigenen Produktion, Ersatzteile für die Reparatur von Geräten, die Erzeugung aller Arten von Energie im Unternehmen (elektrische Energie, Druckluft, Stickstoff usw.). .
Betreuung von Produktionsabläufen - Hierbei handelt es sich um Arbeitsprozesse zur Erbringung von Dienstleistungen, die für die Durchführung von Grund- und Hilfsproduktionsprozessen erforderlich sind. Zum Beispiel Transport von Sachwerten, Lagerarbeiten aller Art, technische Kontrolle der Produktqualität usw.
Grund-, Hilfs- und Serviceproduktionsprozesse weisen unterschiedliche Entwicklungs- und Verbesserungstendenzen auf. Dadurch können viele Produktionshilfsprozesse auf spezialisierte Anlagen verlagert werden, was in den meisten Fällen eine kostengünstigere Produktion gewährleistet. Mit zunehmendem Grad der Mechanisierung und Automatisierung von Haupt- und Nebenprozessen werden Dienstleistungsprozesse nach und nach zu einem integralen Bestandteil der Hauptproduktion und spielen eine organisierende Rolle in der automatisierten und insbesondere in der flexiblen automatisierten Produktion.
Die Haupt- und in einigen Fällen auch Nebenproduktionsprozesse finden in verschiedenen Stufen (oder Phasen) statt. Bühne- Dies ist ein separater Teil des Produktionsprozesses, bei dem der Arbeitsgegenstand in einen anderen qualitativen Zustand übergeht. Beispielsweise gelangt Material in ein Werkstück, ein Werkstück in ein Teil usw.
Die wesentlichen Produktionsprozesse erfolgen in den Stufen Beschaffung, Bearbeitung, Montage und Justierung.
Beschaffungsphase konzipiert für die Herstellung von Rohteilen. Es zeichnet sich durch sehr vielfältige Produktionsmethoden aus. Zum Beispiel das Schneiden oder Schneiden von Rohlingen aus Blechmaterial, die Herstellung von Rohlingen durch Gießen, Stanzen, Schmieden usw. Der Haupttrend bei der Entwicklung technologischer Prozesse in dieser Phase besteht darin, Rohlinge näher an die Formen und Größen fertiger Teile heranzuführen. Die Arbeitswerkzeuge in dieser Phase sind Schneidemaschinen, Press- und Stanzgeräte, Tafelscheren usw.
Verarbeitungsphase - die zweite in der Struktur des Produktionsprozesses – umfasst mechanische und thermische Behandlung. Gegenstand der Arbeit ist hier die Vorbereitung von Teilen. Die Arbeitsmittel in dieser Phase sind hauptsächlich verschiedene Metallschneidemaschinen, Öfen zur Wärmebehandlung und Geräte zur chemischen Verarbeitung. Als Ergebnis dieser Phase erhalten die Teile Abmessungen, die einer bestimmten Genauigkeitsklasse entsprechen.
Montagephase (Montage und Installation) - Hierbei handelt es sich um einen Produktionsprozess, bei dem Baugruppen (Kleinbaugruppen, Unterbaugruppen, Einheiten, Blöcke) oder Fertigprodukte entstehen. Gegenstand der Arbeit sind in diesem Stadium sowohl selbst hergestellte als auch von außen zugekaufte Teile und Baugruppen (Komponenten). Es gibt zwei wesentliche Organisationsformen der Versammlung: stationär und mobil. Von der stationären Montage spricht man, wenn ein Produkt an einem Arbeitsplatz hergestellt wird (Teilelieferung erfolgt). Bei der Umzugsmontage entsteht ein Produkt durch den Transport von einem Arbeitsplatz zum anderen. Die Arbeitsmittel sind hier nicht so vielfältig wie in der Verarbeitungsphase. Die wichtigsten sind alle Arten von Werkbänken, Ständern, Transport- und Führungsgeräten (Förderbänder, Elektroautos, Roboter usw.). Montageprozesse zeichnen sich in der Regel durch einen erheblichen manuellen Arbeitsaufwand aus, daher ist deren Mechanisierung und Automatisierung die Hauptaufgabe zur Verbesserung des technologischen Prozesses.
Anpassungs- und Anpassungsphase - endgültig in der Struktur des Produktionsprozesses, der durchgeführt wird, um die notwendigen technischen Parameter des Endprodukts zu erhalten. Gegenstand der Arbeit sind hier fertige Produkte oder deren einzelne Baugruppen, Werkzeuge, Universalinstrumente und spezielle Prüfstände.
Die Bestandteile der Stufen der Haupt- und Hilfsprozesse sind technologische Operationen. Die Aufteilung des Produktionsprozesses in Arbeitsgänge und dann in Techniken und Bewegungen ist notwendig, um technisch fundierte Standards für die Ausführungszeit von Arbeitsgängen zu entwickeln.
Betrieb - Teil des Produktionsprozesses, der in der Regel an einem Arbeitsplatz ohne Umstellung und von einem oder mehreren Arbeitern (Mannschaft) durchgeführt wird.
Je nach technischer Ausstattung des Produktionsprozesses werden Vorgänge unterschieden: manuell, manuell, maschinell, automatisch und Hardware.
Sowohl Haupt- als auch Hilfs- und manchmal auch Nebenproduktionsprozesse bestehen aus Haupt- und Hilfselementen – Operationen. Zu den wichtigsten gehören Vorgänge, die in direktem Zusammenhang mit Änderungen der Größe, Form, Eigenschaften, inneren Struktur eines Arbeitsgegenstandes oder der Umwandlung eines Stoffes in einen anderen sowie mit einer Änderung der Lage von Arbeitsgegenständen zueinander stehen . Zu den Hilfsvorgängen zählen Vorgänge, deren Durchführung zum Ablauf der Hauptvorgänge beiträgt, beispielsweise das Bewegen von Arbeitsgegenständen, die Qualitätskontrolle, den Aus- und Einbau, die Lagerung usw.
Organisatorisch werden Haupt- und Nebenproduktionsprozesse (ihre Abläufe) herkömmlicherweise in einfache und komplexe unterteilt.
Einfach sind Prozesse, bei denen Arbeitsgegenstände einer aufeinanderfolgenden Reihe miteinander verbundener Vorgänge unterzogen werden, wodurch teilweise fertige Arbeitsprodukte (Rohlinge, Teile, d. h. integrale Bestandteile des Produkts) entstehen.
Komplex sind Prozesse, bei denen durch Kombination privater Produkte fertige Arbeitsprodukte, also komplexe Produkte (Maschinen, Maschinen, Geräte etc.) entstehen.
Die Bewegung von Arbeitsgegenständen im Produktionsprozess erfolgt so, dass das Arbeitsergebnis eines Arbeitsplatzes zum Ausgangsgegenstand für einen anderen wird, d. h. jeder zeitlich und räumlich vorhergehende Arbeitsgegenstand gibt dem nächsten Arbeit. Dies wird durch die Organisation der Produktion sichergestellt.
Von der richtigen und rationale Organisation Produktionsprozesse (insbesondere die wichtigsten) hängen von den Ergebnissen der Produktions- und Wirtschaftstätigkeit des Unternehmens, den wirtschaftlichen Indikatoren seiner Arbeit, den Produktionskosten, dem Gewinn und der Rentabilität der Produktion, dem Umfang der laufenden Arbeiten und der Menge ab Betriebskapital.
5.2 Grundprinzipien der Organisation von Produktionsprozessen
Die Organisation des Produktionsprozesses in jedem Maschinenbauunternehmen (einschließlich der Herstellung radioelektronischer Instrumente), in jeder seiner Werkstätten oder an einem Standort basiert auf einer rationalen zeitlichen und räumlichen Kombination aller Grund-, Hilfs- und Wartungsprozesse. Dies ermöglicht die Herstellung von Produkten mit minimalen Lebens- und Materialkosten. Die Merkmale und Methoden dieser Kombination variieren je nach Produktionsbedingungen. Bei aller Vielfalt unterliegt die Organisation von Produktionsprozessen jedoch einigen allgemeinen Prinzipien: Differenzierung, Konzentration und Integration, Spezialisierung, Verhältnismäßigkeit, Geradlinigkeit, Kontinuität, Parallelität, Rhythmus, Automatismus, Prävention, Flexibilität, Optimalität, Elektronisierung, Standardisierung usw .
Das Prinzip der Differenzierung besteht darin, den Produktionsprozess in einzelne technologische Prozesse zu unterteilen, die wiederum in Vorgänge, Übergänge, Techniken und Bewegungen unterteilt sind. Gleichzeitig ermöglicht eine Analyse der Eigenschaften jedes Elements die Auswahl der besten Bedingungen dafür Implementierung, die eine Minimierung der Gesamtkosten aller Arten von Ressourcen gewährleistet. So hat sich die Linienfertigung aufgrund der immer tieferen Differenzierung der technologischen Prozesse über viele Jahre hinweg weiterentwickelt. Die Auswahl kurzfristiger Betriebe ermöglichte es, die Organisation und technologische Ausstattung der Produktion zu vereinfachen, die Fähigkeiten der Arbeitnehmer zu verbessern und ihre Arbeitsproduktivität zu steigern.
Eine übermäßige Differenzierung erhöht jedoch aufgrund der Monotonie und hohen Intensität der Produktionsprozesse die Ermüdung der Arbeiter bei manuellen Tätigkeiten. Eine große Anzahl von Einsätzen führt zu unnötigen Kosten für den Transport von Arbeitsgegenständen zwischen Arbeitsplätzen, deren Installation, Sicherung und Entfernung von Arbeitsplätzen nach Abschluss der Einsätze.
Beim Einsatz moderner, leistungsstarker flexibler Anlagen (CNC-Maschinen, Bearbeitungszentren, Roboter etc.) wird aus dem Prinzip der Differenzierung das Prinzip der Konzentration der Abläufe und Integration der Produktionsprozesse. Das Konzentrationsprinzip besteht darin, mehrere Arbeitsgänge an einem Arbeitsplatz durchzuführen (mehrspindlige, mehrschneidende CNC-Maschinen). Operationen werden umfangreicher, komplexer und werden in Kombination mit dem Teamprinzip der Arbeitsorganisation durchgeführt. Das Prinzip der Integration besteht darin, die wichtigsten Hilfs- und Serviceprozesse zu kombinieren.
Das Spezialisierungsprinzip ist eine Form der gesellschaftlichen Arbeitsteilung, die in systematischer Entwicklung die Aufteilung von Werkstätten, Abteilungen, Linien und einzelnen Arbeitsplätzen im Betrieb bestimmt. Sie stellen eine begrenzte Produktpalette her und zeichnen sich durch ein spezielles Produktionsverfahren aus.
Eine Reduzierung der Produktpalette führt in der Regel zu einer Verbesserung aller Wirtschaftsindikatoren, insbesondere zu einer Erhöhung der Auslastung des Anlagevermögens des Unternehmens, einer Senkung der Produktionskosten, einer verbesserten Produktqualität, Mechanisierung und Automatisierung von Herstellungsprozesse. Spezialgeräte arbeiten unter sonst gleichen Bedingungen produktiver.
Der Spezialisierungsgrad des Arbeitsplatzes wird durch den Konsolidierungskoeffizienten der Detailoperationen bestimmt ( Spi), an einem Arbeitsplatz für einen bestimmten Zeitraum (Monat, Quartal) durchgeführt,
Wo Mit PR- Anzahl der Arbeitsplätze (Ausrüstungseinheiten) des Produktionssystems; m doi - die Anzahl der Detailoperationen, die am i-ten Arbeitsplatz während einer Zeiteinheit (Monat, Jahr) durchgeführt wurden.
Mit einem Koeffizienten K sp= 1, eine enge Spezialisierung des Arbeitsplatzes wird gewährleistet, Voraussetzungen für eine effektive Organisation der Produktion werden geschaffen. Um einen Arbeitsplatz mit einem Detailvorgang vollständig auszulasten, muss die Bedingung erfüllt sein
,
Wo N. z.j- Produktionsvolumen von Teilen des J-ten Namens pro Zeiteinheit, zum Beispiel Stk./Monat;
t shti- Arbeitsintensität des Betriebs am i-ten Arbeitsplatz, min;
F eff- effektiver Zeitfonds am Arbeitsplatz, zum Beispiel Min./Monat.
Grundsatz der Verhältnismäßigkeit geht von der gleichen Durchsatzleistung aller Produktionsabteilungen aus, die Haupt-, Hilfs- und Serviceprozesse durchführen. Ein Verstoß gegen diesen Grundsatz führt zur Entstehung von Engpässen in der Produktion oder umgekehrt zur unvollständigen Auslastung einzelner Arbeitsplätze, Bereiche, Werkstätten und zu einer Verringerung der Effizienz des gesamten Unternehmens. Um die Verhältnismäßigkeit sicherzustellen, werden die Produktionskapazitätsberechnungen daher sowohl nach Produktionsstufen als auch nach Gerätegruppen und Produktionsbereichen durchgeführt. Wenn beispielsweise die Menge der produzierten Teile bekannt ist (N 3) und die Norm der Stückzeit (t Stück), Mit der Formel können Sie die Belastung einer bestimmten I-Gruppe von Geräten ermitteln
.
Bestimmen Sie als Nächstes den Durchsatz dieser Gerätegruppe
,
Anschließend werden Auslastung und Durchsatz der i-ten Gerätegruppe verglichen und der Auslastungsfaktor anhand der Formel ermittelt
Die bevorzugte Option ist wann K zi= 1 und Q i = P i .
Direktflussprinzip bedeutet eine solche Organisation des Produktionsprozesses, die die kürzesten Wege für den Durchgang von Teilen und Montageeinheiten durch alle Phasen und Vorgänge von der Einführung der Rohstoffe in die Produktion bis zur Produktion der fertigen Produkte gewährleistet. Der Fluss von Materialien, Halbzeugen und Montageeinheiten muss progressiv und kurz sein, ohne Gegen- oder Rückbewegungen. Dies wird durch eine entsprechende Planung der Geräteplatzierung entlang des technologischen Prozesses gewährleistet. Ein klassisches Beispiel für ein solches Layout ist eine Produktionslinie.
^ Kontinuitätsprinzip bedeutet, dass der Arbeiter ohne Ausfallzeiten arbeitet, die Geräte ohne Unterbrechungen arbeiten und Arbeitsgegenstände nicht am Arbeitsplatz liegen. Dieses Prinzip kommt in der Massen- oder Großserienproduktion am deutlichsten zum Ausdruck, wenn kontinuierliche Produktionsmethoden organisiert werden, insbesondere bei der Organisation kontinuierlicher Produktionslinien mit einem oder mehreren Subjekten. Dieses Prinzip sorgt für eine Verkürzung des Produktherstellungszyklus und trägt dadurch zu einer erhöhten Produktionsintensivierung bei.
Parallelprinzip beinhaltet die gleichzeitige Durchführung von Teilproduktionsprozessen und einzelnen Arbeitsgängen an ähnlichen Teilen und Teilen eines Produkts an verschiedenen Arbeitsplätzen, also die Erstellung vielfältiger Arbeiten zur Herstellung eines bestimmten Produkts. Parallelität in der Organisation des Produktionsprozesses wird in verschiedenen Formen verwendet: in der Struktur eines technologischen Vorgangs – Mehrwerkzeugbearbeitung (Mehrspindel-Mehrschneide-Halbautomaten) oder parallele Ausführung von Haupt- und Hilfselementen von Vorgängen; bei der Herstellung von Rohlingen und der Bearbeitung von Teilen (in Werkstätten Rohlinge und Teile in unterschiedlichen Bereitschaftsstadien); in der Einheits- und Generalversammlung. Das Parallelitätsprinzip sorgt für eine Verkürzung der Produktionszykluszeiten und eine Einsparung von Arbeitszeit.
^ Das Prinzip des Rhythmus gewährleistet die Freigabe gleicher oder steigender Produktmengen über gleiche Zeiträume und dementsprechend die Wiederholung dieser Zeiträume des Produktionsprozesses in allen seinen Phasen und Vorgängen. Bei einer engen Spezialisierung der Produktion und einer stabilen Produktpalette kann der Rhythmus direkt bezogen auf einzelne Produkte sichergestellt werden und wird durch die Anzahl der verarbeiteten bzw. produzierten Produkte pro Zeiteinheit bestimmt. Im Kontext einer breiten und sich verändernden Produktpalette des Produktionssystems kann der Arbeits- und Produktionsrhythmus nur anhand von Arbeits- oder Kostenindikatoren gemessen werden.
Automatisches Prinzip beinhaltet die maximale Ausführung von Vorgängen des Produktionsprozesses automatisch, das heißt ohne die direkte Beteiligung eines Arbeiters daran oder unter seiner Aufsicht und Kontrolle. Die Automatisierung von Prozessen führt zu einer Erhöhung des Produktionsvolumens von Teilen und Produkten, zu einer Steigerung der Arbeitsqualität, einer Senkung der menschlichen Arbeitskosten und dem Ersatz unattraktiver Handarbeit durch mehr geistige Arbeit hochqualifizierter Arbeitskräfte (Einsteller, Bediener). ), bis hin zur Abschaffung manueller Arbeit bei Arbeiten unter gefährlichen Bedingungen und zum Ersatz von Arbeitern durch Roboter. Besonders wichtig ist die Automatisierung von Serviceprozessen. Automatisierte Fahrzeuge und Lager übernehmen nicht nur Funktionen für den Transport und die Lagerung von Produktionsgegenständen, sondern können den Rhythmus der gesamten Produktion regeln. Der allgemeine Automatisierungsgrad von Produktionsprozessen wird durch den Anteil der Arbeit in der Haupt-, Hilfs- und Dienstleistungsindustrie am Gesamtarbeitsvolumen des Unternehmens bestimmt. Automatisierungsgrad (Bei Automatik) durch die Formel bestimmt
Wo T auto - die Komplexität der automatisch oder automatisiert ausgeführten Arbeiten;
T insgesamt- die Gesamtarbeitsintensität der Arbeit im Unternehmen (Werkstatt) für einen bestimmten Zeitraum.
Der Automatisierungsgrad kann sowohl insgesamt für das gesamte Unternehmen als auch für jeden Bereich separat berechnet werden.
Präventionsprinzip Dabei geht es um die Organisation der Gerätewartung mit dem Ziel, Unfälle und Ausfallzeiten technischer Systeme zu verhindern. Dies wird durch ein System der planmäßigen vorbeugenden Wartung (PPR) erreicht.
Das Prinzip der Flexibilität bietet effektive Organisation Arbeit, ermöglicht den Übergang zur Produktion anderer Produkte, die im Produktionsprogramm des Unternehmens enthalten sind, oder zur Produktion neuer Produkte bei der Beherrschung seiner Produktion. Es ermöglicht eine Reduzierung des Zeit- und Kostenaufwands für den Gerätewechsel bei der Herstellung von Teilen und Produkten einer breiten Palette. Dieses Prinzip erhält die größte Entwicklung unter Bedingungen einer hochorganisierten Produktion, in der CNC-Maschinen, Bearbeitungszentren (MCs) und rekonfigurierbare automatische Mittel zur Steuerung, Lagerung und Bewegung von Produktionsobjekten verwendet werden.
Optimalitätsprinzip ist, dass die Umsetzung aller Prozesse zur Herstellung von Produkten in einer bestimmten Menge und termingerecht mit größter Wirtschaftlichkeit bzw. mit geringstem Aufwand an Arbeits- und Materialressourcen erfolgt. Die Optimalität wird durch das Gesetz der Zeitersparnis bestimmt.
Elektronisierungsprinzip beinhaltet den weit verbreiteten Einsatz von CNC-Fähigkeiten auf Basis der Mikroprozessortechnologie, die es ermöglicht, grundlegend neue Maschinensysteme zu schaffen, die hohe Produktivität mit den Anforderungen an Flexibilität der Produktionsprozesse verbinden. Computer und Industrieroboter, die über künstliche Intelligenz verfügen, ermöglichen es, die komplexesten Funktionen in der Produktion anstelle eines Menschen auszuführen.
Der Einsatz von Mini- und Mikrocomputern mit erweiterter Funktionalität Software und CNC-Maschinen mit mehreren Werkzeugen ermöglichen es Ihnen, aufgrund des automatischen Werkzeugwechsels einen großen Satz oder sogar alle Bearbeitungsvorgänge von Teilen von einer Installation auf der Maschine aus durchzuführen. Der Schneidwerkzeugsatz für eine solche Maschine kann 100 bis 120 Einheiten erreichen, die im Revolver oder Werkzeugmagazin installiert und nach einem speziellen Programm ausgetauscht werden.
Prinzip der Standardisierung beinhaltet den weit verbreiteten Einsatz von Standardisierung, Vereinheitlichung, Typisierung und Normalisierung bei der Schaffung und Entwicklung neuer Geräte und neuer Technologien, was es ermöglicht, eine unangemessene Vielfalt bei Materialien, Geräten und technologischen Prozessen zu vermeiden und die Dauer des Zyklus stark zu verkürzen die Schaffung und Entwicklung neuer Geräte (SONT).
Bei der Gestaltung eines Produktionsprozesses oder Produktionssystems sollte die rationelle Anwendung der oben dargelegten Grundsätze berücksichtigt werden.
5.3 Produktionsarten und ihre technischen und wirtschaftlichen Merkmale
Die Organisation der Produktionsabläufe, die Wahl der rationellsten Methoden der Vorbereitung, Planung und Steuerung der Produktion werden maßgeblich von der Art der Produktion im Maschinenbaubetrieb bestimmt.
Unter der Art der Produktion wird eine Reihe von Merkmalen verstanden, die die organisatorischen und technischen Merkmale des Produktionsprozesses bestimmen, der an einem oder mehreren Arbeitsplätzen im Maßstab eines Standorts, einer Werkstatt oder eines Unternehmens durchgeführt wird. Die Art der Produktion bestimmt maßgeblich die Formen der Spezialisierung und die Art und Weise der Organisation von Produktionsprozessen.
Die Klassifizierung der Produktionsarten basiert auf folgenden Faktoren: Breite der Produktpalette, Produktionsvolumen, Grad der Konstanz der Produktpalette, Art der Arbeitsbelastung und deren Spezialisierung.
Nomenklatur Produkte ist die Anzahl der dem Produktionssystem zugeordneten Produktartikel und charakterisiert dessen Spezialisierung. Je breiter die Nomenklatur, desto weniger spezialisiert ist das System, und umgekehrt: Je enger es ist, desto höher ist der Spezialisierungsgrad. Durch die breite Produktpalette ergibt sich eine große Vielfalt an technologischen Prozessen und Abläufen, Geräten, Werkzeugen, Geräten und Arbeiterberufen.
Produktausstoßvolumen - Dabei handelt es sich um die Anzahl der Artikel einer bestimmten Art, die von einem Produktionssystem über einen bestimmten Zeitraum produziert werden. Das Produktionsvolumen und die Arbeitsintensität jedes Produkttyps haben einen entscheidenden Einfluss auf die Art der Spezialisierung dieses Systems.
Der Grad der Konsistenz der Nomenklatur - Dabei handelt es sich um die Wiederholbarkeit der Herstellung eines Produkts eines bestimmten Typs in aufeinanderfolgenden Zeiträumen. Wenn ein Produkt einer bestimmten Art in einem geplanten Zeitraum hergestellt wird, in anderen jedoch nicht, liegt kein Grad an Konstanz vor. Die regelmäßige Wiederholung der Produktion derartiger Produkte ist eine der Voraussetzungen für die Sicherstellung des Produktionsrhythmus. Die Regelmäßigkeit wiederum hängt von der Produktproduktionsmenge ab, da eine große Produktionsmenge gleichmäßig auf aufeinanderfolgende Planungszeiträume verteilt werden kann.
Art der Arbeitsbelastung bedeutet die Zuordnung bestimmter technologischer Prozessabläufe zu Arbeitsplätzen. Wenn einem Arbeitsplatz eine Mindestanzahl von Vorgängen zugeordnet ist, handelt es sich um eine enge Spezialisierung, und wenn einem Arbeitsplatz eine große Anzahl von Vorgängen zugeordnet sind (bei universeller Maschine), handelt es sich um eine breite Spezialisierung.
Abhängig von den oben genannten Faktoren werden drei Arten von Produktionsprozessen bzw. drei Arten der Produktion unterschieden: Einzel-, Serien- und Massenproduktion (Abb. 5.1).
Abbildung 5.1 – Klassifizierung der Produktionstypen
Die Hauptindikatoren zur Bestimmung der Produktionsart können die Spezialisierungskoeffizienten von Arbeitsplätzen sein ( K sp), Serialität (K ser) und Massencharakter (Zu m).
Berufsspezialisierungskoeffizient
Wo m d.o- die Anzahl der Detailoperationen im technologischen Prozess, die in einer bestimmten Abteilung (auf der Baustelle, in der Werkstatt) durchgeführt werden;
Mit PR- die Anzahl der Arbeitsplätze (Ausrüstungseinheiten) in dieser Abteilung.
Serialitätsfaktor
K grau =r/t Stk,
Wo R– Produktionszyklus der Produkte, min./Stück; r =F eff: N;
t Stk- durchschnittliche Stückzeit für technologische Prozessoperationen, min.
Wo, t Stk.i- Stückzeit für den i-ten Vorgang des technologischen Prozesses, min.
T - Anzahl der Operationen.
Der Massenkoeffizient wird durch die Formel bestimmt
.
Jede Produktionsart entspricht: dem Wert der angegebenen Koeffizienten, der Art der verwendeten Ausrüstung, Technologie und Organisationsformen der Produktion, Arten der Bewegung von Arbeitsgegenständen, der Produktionsstruktur des Unternehmens (Werkstatt, Standort) und anderen Merkmalen .
Einzelanfertigung gekennzeichnet durch eine breite Produktpalette und die Herstellung kleiner Mengen identischer Produkte, deren Nachproduktion in der Regel nicht vorgesehen ist. Dadurch ist eine dauerhafte Zuordnung von Vorgängen zu einzelnen Tätigkeiten, dem Spezialisierungskoeffizienten, nicht möglich K sp > 40 Detailoperationen pro Arbeitsplatz. Die Spezialisierung solcher Berufe ist nur auf sie zurückzuführen technologische Eigenschaften und Größen der verarbeiteten Produkte. In dieser Produktion kommen universelle Geräte und eine überwiegend sequentielle Art der Bewegung von Teilechargen durch technologische Prozessabläufe zum Einsatz. Fabriken verfügen über eine komplexe Produktionsstruktur und Werkstätten sind nach technologischen Grundsätzen spezialisiert.
Massenproduktion ist auf die Herstellung einer begrenzten Produktpalette in relativ kleinen Mengen und wiederholten Chargen (Serien) über einen bestimmten Zeitraum spezialisiert. Abhängig von der Anzahl der jedem Arbeitsplatz zugewiesenen Vorgänge, der Häufigkeit der Wiederholung von Produktchargen und ihrer Größe werden drei Untertypen (Typen) der Serienproduktion unterschieden: Kleinserie, Mittelserie und Großserie.
Die Produktion in kleinem Maßstab ist in der Regel einzigartig: Produkte werden in kleinen Serien mit einem breiten Sortiment hergestellt, die Wiederholbarkeit der Produkte im Anlagenprogramm ist entweder nicht vorhanden oder unregelmäßig und die Größe der Serie ist instabil; Das Unternehmen entwickelt ständig neue Produkte und stellt die Produktion bereits entwickelter Produkte ein. Den Arbeitsplätzen sind vielfältige Aufgaben zugeordnet, K sp= 20 - 40 Operationen ( K ser > 20; K m< 1). Die Ausstattung, Bewegungsarten, Spezialisierungsformen und Produktionsstruktur sind die gleichen wie bei der Einzelfertigung.
Für die Produktion im mittleren Maßstab ist es typisch, dass Produkte in relativ großen Serien mit begrenztem Sortiment hergestellt werden. Serien wiederholen sich mit einer gewissen Regelmäßigkeit hinsichtlich der Einführungsdauer und der Anzahl der Produkte in der Charge; Die jährliche Nomenklatur ist immer noch weiter gefasst als die Nomenklatur der Emission in jedem Monat. Arbeitsplätzen ist ein engeres Aufgabenspektrum zugeordnet: K sp= 10 - 20 Operationen ( K ser= 20; K m< 1). Die Ausrüstung ist universell und speziell, die Art der Bewegung der Arbeitsgegenstände ist parallel-sequentiell. Fabriken verfügen über eine entwickelte Produktionsstruktur, Beschaffungsbetriebe spezialisieren sich nach technologischen Grundsätzen und Maschinenmontagebetriebe schaffen fachspezifische Bereiche.
Die Großserienproduktion tendiert zur Massenproduktion. Produkte werden in großen Serien mit begrenztem Sortiment hergestellt, wobei die wichtigsten oder wichtigsten Produkte ständig und kontinuierlich hergestellt werden. Jobs haben eine engere Spezialisierung: K sp= 2 - 10 Operationen ( K ser = 10; K m< 1). Die Ausrüstung ist überwiegend speziell, die Bewegungsarten der Arbeitsgegenstände sind parallel-sequentiell und parallel. Fabriken verfügen über eine einfache Produktionsstruktur, Bearbeitungs- und Montagebetriebe sind fachlich spezialisiert und Beschaffungsbetriebe sind nach technologischen Grundsätzen spezialisiert.
Masse Die Produktion zeichnet sich durch die Produktion einer engen Produktpalette über einen langen Zeitraum und große Mengen sowie eine stabile Wiederholbarkeit aus. Den Arbeitsplätzen ist ein enger Aufgabenbereich zugeordnet: K sp< 1 операции (K ser< 2; K m> 1). Alle Produkte des Werksortiments werden gleichzeitig und parallel hergestellt. Die Nummern der Produktnamen im Jahres- und Monatsprogramm sind gleich. Die Ausstattung ist besonders, die Art der Bewegung der Arbeitsgegenstände ist parallel. Die Spezialisierung der Workshops und Bereiche erfolgt überwiegend fachspezifisch. Die Fabriken verfügen über eine einfache und klar definierte Produktionsstruktur.
Durch die Kombination der Mechanisierung und Automatisierung von Produktionsprozessen sowie der Belastung von Arbeitsplätzen (Geräten) mit den Bewegungsarten von Arbeitsgegenständen ist eine Serienproduktion in vier und eine Massenproduktion in drei Varianten möglich (Abb. 5.2).
Anhand der Produktionsart wird die Art des Unternehmens und seiner Geschäftsbereiche bestimmt. Jedes Unternehmen kann unterschiedliche Produktionsarten haben. Daher wird die Art des Unternehmens oder seiner Abteilung durch die vorherrschende Art der Endproduktion bestimmt.
Die Art der Produktion hat entscheidenden Einfluss auf die Besonderheiten ihrer Organisation, Führung und betrieblichen Produktionsplanung sowie auf technische und wirtschaftliche Kennzahlen. Reis. 5.2 - Klassifizierung der Produktionstypen
Wenn wir die Gesamtheit der Produktionsarten als Ganzes betrachten, beginnend bei der Einzelproduktion bis hin zur Massenproduktion, dann können wir auf dem Weg zur Massenproduktion Folgendes feststellen: a) die kontinuierliche Erweiterung des Umfangs leistungsstarker technologischer Prozesse , begleitet von Mechanisierung und Automatisierung der Produktion; b) Erhöhung des Anteils von Spezialausrüstung und spezieller technologischer Ausrüstung an der Gesamtzahl der Werkzeuge; V) allgemeine Steigerung technische Qualifikation der Arbeitnehmer sowie Einführung fortschrittlicher Arbeitsmethoden und -techniken.
Basierend auf diesen fortschreitenden Veränderungen werden beim Übergang von der Einzelproduktion zur Serienproduktion und dann zur Massenproduktion erhebliche Einsparungen bei der Sozialarbeit gewährleistet und als Ergebnis: erhöhte Arbeitsproduktivität, verbesserte Nutzung des Anlagevermögens des Unternehmens, reduzierte Materialkosten pro Produkt sowie reduzierte Produktionskosten, höhere Gewinne und Produktionsrentabilität.
Es ist jedoch zu beachten, dass der Einsatz von Gruppenmethoden zur Teilebearbeitung, Automatisierung und Elektronisierung von Produktionsprozessen es ermöglicht, Organisationsformen der Massenproduktion in der Serien- und sogar Einzelfertigung einzusetzen und hohe technische und wirtschaftliche Kennzahlen zu erreichen. Beispielsweise sorgt die Einführung flexibler Produktionskomplexe in einer einzigen Produktion für eine Steigerung der Arbeitsproduktivität um das 4- bis 6-fache, erhöht die Auslastung der Ausrüstung auf 0,92 bis 0,95, reduziert den Bedarf an Produktionsfläche um 40 bis 60 % und reduziert die Dauer des Produktionszyklus und verbessert alle technischen und wirtschaftlichen Indikatoren.
5.4 Rationale Organisation der Produktion
Eine der wichtigsten Anforderungen an die rationelle Organisation des Produktionsprozesses besteht darin, die kürzeste Dauer des Produktionszyklus für die Herstellung von Produkten sicherzustellen.
Unter Produktionszyklus versteht man den kalendarischen Zeitraum von der Produktion der Rohstoffe bis zur vollständigen Herstellung des fertigen Produkts. Die Dauer des Produktionszyklus für die Herstellung eines Produkts besteht aus der Arbeitszeit, der Zeit natürlicher Prozesse und der Zeit der Pausen.
Die Organisationsform der Produktion ist eine bestimmte zeitliche und räumliche Kombination von Elementen des Produktionsprozesses mit einem angemessenen Grad ihrer Integration, ausgedrückt durch ein System stabiler Verbindungen.
Je nach Art der temporären Struktur werden Organisationsformen mit sequentiellem, parallelem und parallel-sequentiellem Transfer von Arbeitsgegenständen in der Produktion unterschieden.
Die Organisationsform der Produktion mit sequentiellem Transfer von Arbeitsgegenständen ist eine Kombination von Elementen des Produktionsprozesses, die den Transport verarbeiteter Produkte über alle Produktionsbereiche in Chargen beliebiger Größe gewährleistet. Die Übergabe der Arbeitsgegenstände an jeden nachfolgenden Arbeitsgang erfolgt erst nach Abschluss der Bearbeitung der gesamten Charge im vorherigen Arbeitsgang. Diese Form ist in Bezug auf Änderungen im Produktionsprogramm am flexibelsten, sie ermöglicht eine ausreichende volle Nutzung der Ausrüstung, wodurch die Anschaffungskosten gesenkt werden können. Der Nachteil dieser Form der Produktionsorganisation ist die relativ lange Dauer des Produktionszyklus, da jedes Teil auf die Verarbeitung der gesamten Charge wartet, bevor es den nächsten Arbeitsgang durchführt.
Die Organisationsform der Produktion mit paralleler Übergabe von Arbeitsgegenständen basiert auf einer solchen Kombination von Elementen des Produktionsprozesses, die es ermöglicht, Arbeitsgegenstände einzeln und ohne Wartezeit von Betrieb zu Betrieb zu starten, zu verarbeiten und zu übergeben. Diese Organisation des Produktionsprozesses führt zu einer Reduzierung der Anzahl der zu bearbeitenden Teile und damit zu einem geringeren Platzbedarf für Lager und Gänge. Sein Nachteil ist der mögliche Ausfall von Geräten (Arbeitsplätzen) aufgrund unterschiedlicher Betriebsdauern.
Die Organisationsform der Produktion mit parallel-sequentiellem Transfer von Arbeitsgegenständen liegt zwischen sequentiellen und parallelen Formen und beseitigt deren inhärente Nachteile teilweise. Produkte werden in Transportchargen von Betrieb zu Betrieb transportiert. Gleichzeitig wird die Kontinuität des Geräte- und Arbeitseinsatzes gewährleistet und ein teilweise paralleler Durchlauf einer Teilecharge durch technologische Prozessabläufe ermöglicht.
Die räumliche Struktur der Produktionsorganisation wird durch die Menge der auf dem Arbeitsplatz konzentrierten technologischen Ausrüstung (Anzahl der Arbeitsplätze) und ihre Lage relativ zur Bewegungsrichtung der Arbeitsgegenstände im umgebenden Raum bestimmt. Abhängig von der Anzahl der technologischen Geräte (Arbeitsplätze) wird zwischen einem eingliedrigen Produktionssystem und der entsprechenden Struktur eines separaten Arbeitsplatzes und einem mehrgliedrigen System mit Werkstatt-, Linien- oder Zellenstruktur unterschieden. Mögliche Optionen für die räumliche Struktur der Produktionsorganisation sind in Abb. dargestellt. 5.3. Die Werkstattstruktur zeichnet sich durch die Schaffung von Bereichen aus, in denen Geräte (Arbeitsplätze) parallel zum Werkstückfluss angeordnet sind, was deren Spezialisierung auf der Grundlage technologischer Homogenität impliziert.
Abbildung 5.3. Optionen für die räumliche Struktur des Produktionsprozesses
Die Kombination räumlicher und zeitlicher Strukturen des Produktionsprozesses mit einem gewissen Grad an Integration von Teilprozessen bestimmt verschiedene Organisationsformen der Produktion: technologisch, subjektiv, direkt, punktuell, integriert (Abb. 5.4). Lassen Sie uns überlegen Charaktereigenschaften jeder von ihnen.
Reis. 5.4. Formen der Produktionsorganisation
Technologische Form Die Organisation des Produktionsprozesses ist gekennzeichnet Ladenstruktur Mit serielle Übertragung Gegenstände der Arbeit. Diese Organisationsform ist in Maschinenbaubetrieben weit verbreitet, da sie eine maximale Auslastung der Anlagen in der Kleinserienproduktion gewährleistet und an häufige Änderungen angepasst ist technologischer Prozess. Gleichzeitig hat der Einsatz einer technologischen Form der Organisation des Produktionsprozesses eine Reihe negativer Folgen. Eine große Anzahl von Teilen und deren wiederholte Bewegung während der Bearbeitung führen zu einer Erhöhung des Arbeitsvolumens und einer Erhöhung der Anzahl der Zwischenlagerplätze. Ein erheblicher Teil des Produktionszyklus besteht aus Zeitverlusten, die durch komplexe Kommunikation zwischen Standorten verursacht werden.
Subjektform der Organisation Die Produktion hat eine zelluläre Struktur mit parallel-sequentiellem (sequentiellem) Transfer von Arbeitsgegenständen in der Produktion. In der Regel sind am Fachgebiet alle für die Bearbeitung einer Teilegruppe vom Anfang bis zum Ende des technologischen Prozesses notwendigen Geräte installiert. Ist der verarbeitungstechnologische Kreislauf innerhalb der Site geschlossen, spricht man von subjektgeschlossen.
Durchgehende Organisationsform Produktion gekennzeichnet ist lineare Struktur mit stückweiser Übergabe von Arbeitsgegenständen. Diese Form gewährleistet die Umsetzung einer Reihe von Organisationsprinzipien: Spezialisierung, Direktheit, Kontinuität, Parallelität. Sein Einsatz führt zu einer Verkürzung der Dauer des Produktionszyklus, einem effizienteren Arbeitseinsatz aufgrund einer stärkeren Spezialisierung der Arbeitskräfte und einer Verringerung des Arbeitsvolumens.
Mit Punktform Produktionsorganisation, die Arbeit wird vollständig an einem Arbeitsplatz ausgeführt. Das Produkt wird dort hergestellt, wo sich sein Hauptbestandteil befindet.
Ein Beispiel ist die Montage eines Produkts, bei der sich ein Arbeiter darum bewegt. Die Organisation der Punktproduktion hat eine Reihe von Vorteilen: Sie bietet die Möglichkeit häufiger Änderungen im Design der Produkte und der Verarbeitungsreihenfolge sowie die Produktion von Produkten unterschiedlichster Bandbreite in Mengen, die durch den Produktionsbedarf bestimmt werden; Die mit dem Standortwechsel der Anlagen verbundenen Kosten werden reduziert und die Produktionsflexibilität erhöht.
Integriertes Formular Die Produktionsorganisation umfasst die Zusammenfassung von Haupt- und Nebenvorgängen zu einem einzigen integrierten Produktionsprozess mit zellulärer oder linearer Struktur mit sequentiellem, parallelem oder parallel-sequentiellem Transfer von Arbeitsgegenständen in der Produktion. Im Gegensatz zur bisherigen Praxis der getrennten Gestaltung der Prozesse der Lagerung, des Transports, der Verwaltung und der Verarbeitung in Bereichen mit integrierter Organisationsform ist es erforderlich, diese Teilprozesse zu einem einzigen Produktionsprozess zu verknüpfen. Dies wird durch die Kombination aller Arbeitsplätze mit Hilfe eines automatischen Transport- und Lagerkomplexes erreicht, bei dem es sich um eine Reihe miteinander verbundener automatischer Lagergeräte und Computergeräte handelt, die die Lagerung und Bewegung von Arbeitsgegenständen zwischen einzelnen Arbeitsplätzen organisieren sollen.
Der Fortschritt des Produktionsprozesses wird hier über einen Computer gesteuert, der das Funktionieren aller Elemente des Produktionsprozesses vor Ort nach folgendem Schema sicherstellt: Suche nach dem benötigten Werkstück im Lager – Transport des Werkstücks zur Maschine – Bearbeitung - Rückgabe des Teils an das Lager. Um zeitliche Abweichungen beim Transport und der Bearbeitung von Teilen auszugleichen, werden an einzelnen Arbeitsplätzen Pufferlager für zwischenbetriebliche und versicherungstechnische Reserven geschaffen. Die Schaffung integrierter Produktionsstandorte ist mit relativ hohen Einmalkosten verbunden, die durch die Integration und Automatisierung des Produktionsprozesses entstehen.
Der wirtschaftliche Effekt des Übergangs zu einer integrierten Form der Produktionsorganisation wird durch eine Verkürzung der Dauer des Produktionszyklus für die Herstellung von Teilen, eine Erhöhung der Ladezeit von Maschinen und eine verbesserte Regelung und Steuerung von Produktionsprozessen erreicht. In Abb. Abbildung 5.4 zeigt Anlagenlayoutdiagramme in Bereichen mit unterschiedlichen Formen der Produktionsorganisation.
Abbildung 5.4. Anordnungspläne von Geräten (Arbeitsplätzen) in Bereichen mit unterschiedlichen Formen der Produktionsorganisation:
a) technologisch; b) Betreff; c) geradeaus:
d) Punkt (für den Fall der Montage); e) integriert
Unter Fertigungsprozess wird als eine Reihe vielfältiger, aber miteinander verbundener Arbeitsprozesse und natürlicher Prozesse verstanden, die die Umwandlung von Rohstoffen in ein fertiges Produkt sicherstellen.
Der Produktionsprozess besteht aus Haupt-, Hilfs-, Service- und Nebenprozessen.
ZU hauptsächlich Dazu gehören Prozesse, die in direktem Zusammenhang mit der Umwandlung von Rohstoffen oder Materialien in Fertigprodukte stehen (Getreide zu Mehl, Zuckerrüben zu Zucker). Die Kombination dieser Prozesse im Unternehmen bildet die Hauptproduktion.
Bei Getreideempfangsbetrieben, die staatliche Getreideressourcen lagern, sollten zu den Hauptprozessen auch Prozesse im Zusammenhang mit der Annahme, Platzierung und Lagerung von Getreide gehören.
Zweck Hilfs- X Prozesse - technisch die Hauptprozesse bedienen, bestimmte Dienstleistungen erbringen: Energieversorgung, Herstellung von Werkzeugen und Geräten, Reparaturarbeiten.
Begleiter Prozesse erbringen materielle Dienstleistungen für die Haupt- und Nebenproduktion. Empfang, Platzierung, Lagerung von Rohstoffen, Materialien, Fertigprodukten, Brennstoffen, deren Transport von Lagerorten zu Verbrauchsorten usw.
Nebenwirkungen Prozesse tragen auch dazu bei, Rohstoffe in fertige Produkte umzuwandeln. Doch weder die Rohstoffe noch die daraus entstehenden Produkte gehören zu den Hauptprodukten des Unternehmens. Dies ist die Verarbeitung und Vervollständigung von Abfällen, die in der Hauptproduktion usw. anfallen.
Alle Prozesse sind in Stufen und die Stufen in einzelne Vorgänge unterteilt.
Produktionsphase- ein technologisch abgeschlossener Teil des Produktionsprozesses, der durch solche Veränderungen des Arbeitsgegenstandes gekennzeichnet ist, die seinen Übergang in einen anderen qualitativen Zustand bewirken (Reinigung von Zuckerrüben, Verpackung von Produkten).
Jede Stufe kombiniert Vorgänge, die technologisch miteinander verbunden sind, oder Vorgänge für einen bestimmten Zweck.
Das wichtigste primäre Glied im Produktionsprozess ist der Betrieb.
Fertigungsbetrieb- Dies ist ein Teil des Arbeits- oder Produktionsprozesses, der von einem oder einer Gruppe von Arbeitnehmern an einem separaten Ort mit demselben Arbeitsgegenstand und unter Verwendung derselben Arbeitsmittel ausgeführt wird.
Von Zweck Alle Operationen sind in drei Haupttypen unterteilt:
1) technologisch (grundlegend) – dabei handelt es sich um Vorgänge, bei denen Änderungen am Arbeitsgegenstand (seinem Zustand, seiner Form oder seinem Aussehen) vorgenommen werden (Milchtrennung, Getreidezerkleinerung usw.);
2) Kontrollvorgänge sind Vorgänge, die keine Änderungen am Arbeitsgegenstand bewirken, aber zur Durchführung technologischer Vorgänge (Wiegen usw.) beitragen;
3) Umzug – Vorgänge, die die Stellung des Arbeitssubjekts in der Produktion verändern (Beladen, Entladen, Transport).
Steuer- und Bewegungsvorgänge bilden zusammen eine Gruppe von Hilfsvorgängen.
Nach Ausführungsart (Mechanisierungsgrad) Folgende Operationen werden unterschieden:
- Maschine– von Maschinen unter der Aufsicht von Arbeitern ausgeführt (Rollen von Konserven, Reinigen von Milch, Zerkleinern von Produkten);
- Maschinenhandbuch– durch Maschinen unter direkter Beteiligung der Arbeiter ausgeführt (Mehl ausschlagen, Säcke nähen usw.);
- Handbuch Vorgänge – von Arbeitern ohne Beteiligung von Maschinen durchgeführt (Zufuhr von Rohstoffen zu Förderbändern, Stapeln von Säcken).
Verhältnis verschiedene Arten Die Arbeitsgänge bilden in ihrer Gesamtzahl die Struktur des Produktionsprozesses. In verschiedenen Verarbeitungsbetrieben ist es nicht dasselbe.
Organisation der Produktion im Zeitverlauf basieren auf folgenden Prinzipien:
Der Arbeitsrhythmus des Unternehmens und die Einheitlichkeit der Produktproduktion;
Verhältnismäßigkeit der Produktionseinheiten;
Parallelität (Gleichzeitigkeit) von Abläufen und Produktionsprozessen;
Kontinuität der Produktionsprozesse.
Das Prinzip des Rhythmus sorgt für den Betrieb des Unternehmens in einem geplanten Rhythmus (die Zeit zwischen der Freigabe identischer Produkte oder zweier identischer Produktchargen).
Der Grundsatz der Verhältnismäßigkeit Diese Produktionseinheiten gehen von der gleichen Produktivität pro Zeiteinheit aus.
Parallelprinzip Die Ausführung von Vorgängen und Prozessen basiert auf der gleichzeitigen Ausführung von Phasen, Stufen oder Teilen des Produktionsprozesses.
Kontinuitätsprinzip Der Produktionsprozess sorgt für die Beseitigung von Unterbrechungen bei der Verarbeitung von Arbeitsgegenständen. Die Kontinuität des Prozesses verhindert die Bildung von Lagerbeständen am Arbeitsplatz und reduziert die laufende Arbeit, was besonders wichtig in Unternehmen ist, in denen Rohstoffe nicht über einen längeren Zeitraum ohne Kühlung, Gefrieren und Konserven gelagert werden können (Obst- und Gemüsekonserven, Milch- und Fleischindustrie). .
Zweck Organisation des Produktionsprozesses im Weltraum besteht darin, seine rationelle Konstruktion im Laufe der Zeit sicherzustellen.
Die größte Effizienz bei der Organisation des Produktionsprozesses im Weltraum wird durch den Einsatz von Direktfluss, Spezialisierung, Zusammenarbeit und Kombination der Produktion erreicht.
Geradlinigkeit Der Produktionsprozess zeichnet sich dadurch aus, dass die Produkte in allen Phasen und Vorgängen der Produktion den kürzesten Weg zurücklegen. Im Unternehmensmaßstab sind Werkstätten auf dem Territorium so angeordnet, dass Fern-, Rück-, Gegen- und andere irrationale Transporte ausgeschlossen sind. Das heißt, Arbeitsplätze und Geräte befinden sich in einer technologischen Abfolge von Abläufen.
Innerbetriebliche Spezialisierung ist der Prozess der Trennung von Werkstätten und Bereichen für die Herstellung bestimmter Produkttypen, ihrer Teile oder die Umsetzung einzelner Stufen des technologischen Prozesses. Verarbeitende Unternehmen nutzen technologische, fachliche und funktionale Spezialisierung.
Technologische Spezialisierung Die Produktion umfasst die Isolierung eines engen Bereichs technologischer Vorgänge und die Durchführung von Vorgängen in separaten Werkstätten oder Produktionsbereichen.
Fachliche Spezialisierung Bei der Produktion handelt es sich um die Schaffung separater Linien mit einem vollständigen Produktionszyklus zur Herstellung eines oder mehrerer fertigungstechnisch ähnlicher Produkte.
Funktional nennt man die Spezialisierung aller Produktionsabteilungen auf die Ausführung einer oder eines begrenzten Funktionsumfangs.
Zusammenarbeit Die Produktion im Unternehmen wird von der Organisation durchgeführt Zusammenarbeit seine Produktbereiche. Das Prinzip der Produktionskooperation ist die Nutzung der Dienste einiger Werkstätten durch andere.
Die Suche nach rationalen Formen der Zusammenarbeit führt in manchen Fällen zur Entstehung kombinierter Industrien.
Kombination Bei der Produktion handelt es sich um die Verbindung verschiedener Produktionsanlagen in einem Unternehmen, die aufeinanderfolgende Stufen der Rohstoffverarbeitung darstellen oder im Verhältnis zueinander eine unterstützende Rolle spielen.
Der Produktionsprozess besteht aus einer Reihe gezielter Maßnahmen des Unternehmenspersonals, um Rohstoffe in fertige Produkte umzuwandeln.
Die Hauptkomponenten des Produktionsprozesses, die die Art der Produktion bestimmen, sind professionell geschultes Personal; Arbeitsmittel (Maschinen, Geräte, Gebäude, Bauwerke usw.); Arbeitsgegenstände (Rohstoffe, Materialien, Halbzeuge); Energie (elektrisch, thermisch, mechanisch, Licht, Muskel); Informationen (wissenschaftlich und technisch, kommerziell, operativ und produktionstechnisch, rechtlich, gesellschaftspolitisch).
Das professionell gemanagte Zusammenspiel dieser Komponenten bildet den konkreten Produktionsprozess und macht dessen Inhalt aus.
Der Produktionsprozess ist die Grundlage jedes Unternehmens. Der Inhalt des Produktionsprozesses hat entscheidenden Einfluss auf den Aufbau des Unternehmens und seiner Produktionseinheiten.
Der Hauptteil des Produktionsprozesses ist der technologische Prozess. Bei der Umsetzung des technologischen Prozesses kommt es zu Veränderungen der geometrischen Formen, Größen sowie physikalischen und chemischen Eigenschaften von Arbeitsgegenständen.
Entsprechend ihrer Bedeutung und Rolle in der Produktion werden Produktionsprozesse in Haupt-, Hilfs- und Wartungsprozesse unterteilt.
Die Hauptproduktionsprozesse sind diejenigen, bei denen die wichtigsten vom Unternehmen hergestellten Produkte hergestellt werden.
Zu den Hilfsprozessen zählen Prozesse, die den reibungslosen Ablauf der Hauptprozesse gewährleisten. Ihr Ergebnis sind Produkte, die im Unternehmen selbst eingesetzt werden. Zu den Hilfsprozessen gehören die Reparatur von Geräten, die Herstellung von Geräten, die Erzeugung von Dampf, Druckluft usw.
Unter Serviceprozessen versteht man solche Prozesse, bei deren Umsetzung Leistungen erbracht werden, die für das normale Funktionieren sowohl der Haupt- als auch der Hilfsprozesse erforderlich sind. Dies sind die Prozesse Transport, Lagerung, Kommissionierung von Teilen, Reinigung von Räumlichkeiten usw.
Der Produktionsprozess besteht aus vielen verschiedenen Vorgängen, die entsprechend in Haupt- (technologische) und Hilfsvorgänge unterteilt werden.
Ein technologischer Vorgang ist ein Teil des Produktionsprozesses, der an einem Arbeitsplatz an einem Produktionsobjekt (Teil, Einheit, Produkt) von einem oder mehreren Arbeitern durchgeführt wird.
Je nach Art und Verwendungszweck des Produkts sowie dem Grad der technischen Ausstattung werden die Vorgänge in manuelle, maschinelle, maschinelle und Hardware-Vorgänge eingeteilt.
Manuelle Vorgänge werden manuell mit einfachen Werkzeugen (manchmal mechanisiert) durchgeführt, zum Beispiel Handlackierung, Montage, Produktverpackung usw.
Maschinell-manuelle Arbeiten werden mit Maschinen und Mechanismen unter obligatorischer Beteiligung eines Arbeiters durchgeführt, zum Beispiel der Transport von Gütern mit Elektrofahrzeugen, die Bearbeitung von Teilen auf Maschinen mit manueller Zuführung.
Maschinenoperationen werden vollständig maschinell mit minimaler Beteiligung der Arbeiter am technologischen Prozess ausgeführt, zum Beispiel das Einsetzen von Teilen in die Bearbeitungszone und deren Entnahme am Ende der Bearbeitung, die Überwachung des Maschinenbetriebs, d. h. Arbeiter beteiligen sich nicht an technologischen Vorgängen, sondern kontrollieren sie nur.
Hardware-Operationen finden in speziellen Einheiten (Behälter, Bäder, Öfen usw.) statt. Der Werker überwacht die Funktionsfähigkeit der Geräte und Instrumentenwerte und nimmt bei Bedarf Anpassungen der Betriebsarten der Geräte entsprechend den Anforderungen der Technik vor. Hardware-Operationen sind in der Lebensmittel-, Chemie-, Metallurgie- und anderen Industrien weit verbreitet.
Die Organisation des Produktionsprozesses besteht darin, Menschen, Werkzeuge und Arbeitsgegenstände zu einem einzigen Prozess zur Herstellung materieller Güter zusammenzufassen und eine rationelle räumliche und zeitliche Kombination von Grund-, Hilfs- und Dienstleistungsprozessen sicherzustellen.
Die Wirtschaftlichkeit der rationellen Organisation des Produktionsprozesses drückt sich in einer Verkürzung der Dauer des Produktionszyklus von Produkten, einer Senkung der Produktionskosten, einer verbesserten Nutzung des Anlagevermögens und einer Erhöhung des Umlaufs des Betriebskapitals aus.
Die Art der Produktion wird durch die komplexen Merkmale technischer, organisatorischer und technischer Art bestimmt wirtschaftliche Merkmale Produktion aufgrund der Breite des Sortiments, der Regelmäßigkeit, Stabilität und des Produktionsvolumens. Der Hauptindikator, der die Art der Produktion charakterisiert, ist der Konsolidierungskoeffizient der Kz-Betriebe. Der Befür eine Gruppe von Arbeitsplätzen ist definiert als das Verhältnis der Anzahl aller verschiedenen technologischen Vorgänge, die im Laufe des Monats durchgeführt wurden oder durchgeführt werden sollen, zur Anzahl der Arbeitsplätze:
Kz = | Zu opi | ||||
K r. M. |
|||||
wobei Copi die Anzahl der ausgeführten Operationen ist i-ter Arbeiter Ort; Kr.m – die Anzahl der Arbeitsplätze auf der Baustelle oder in der Werkstatt.
Es gibt drei Arten der Produktion: Einzel-, Serien- und Massenproduktion.
Die Einzelfertigung zeichnet sich durch ein geringes Produktionsvolumen identischer Produkte aus, deren Nachfertigung und Reparatur in der Regel nicht vorgesehen ist. Der Konsolidierungsfaktor für die Stückproduktion liegt in der Regel über 40.
Unter Batch-Produktion versteht man die Herstellung oder Reparatur von Produkten in periodisch wiederholten Chargen. Abhängig von der Anzahl der Produkte in einer Charge oder Serie und dem Wert des Betrwerden Klein-, Mittel- und Großserienfertigung unterschieden.
Für die Produktion im kleinen Maßstab liegt der Bezwischen 21 und 40 (einschließlich), für die Produktion im mittleren Maßstab zwischen 11 und 20 (einschließlich) und für die Produktion im großen Maßstab zwischen 1 und 10 (einschließlich).
Die Massenproduktion zeichnet sich durch eine große Menge an Produkten aus, die über einen langen Zeitraum kontinuierlich hergestellt oder repariert werden, wobei an den meisten Arbeitsplätzen ein Arbeitsvorgang durchgeführt wird. Der Befür die Massenproduktion wird mit 1 angenommen.
Betrachten wir die technischen und wirtschaftlichen Merkmale jeder Produktionsart.
Die Einzel- und ähnliche Kleinserienfertigung zeichnet sich durch die Fertigung von Teilen eines großen Sortiments an Arbeitsplätzen ohne besondere Spezialisierung aus. Diese Produktion muss ausreichend flexibel und angepasst sein, um verschiedene Produktionsaufträge erfüllen zu können.
Technologische Prozesse in einzelnen Produktionsbedingungen werden in Form von Laufkarten für die Bearbeitung von Teilen für jeden Auftrag erweitert entwickelt; Die Standorte sind mit universellen Geräten und Vorrichtungen ausgestattet, die die Produktion von Teilen einer breiten Palette gewährleisten. Die Vielfalt der Tätigkeiten, die viele Arbeitnehmer ausüben müssen, erfordert unterschiedliche berufliche Fähigkeiten, weshalb im Betrieb hochqualifizierte Generalisten eingesetzt werden. In vielen Bereichen, insbesondere in der Pilotfertigung, wird die Berufszusammenlegung praktiziert.
Die Organisation der Produktion in einer einzigen Produktionsumgebung hat ihre eigenen Merkmale. Aufgrund der Vielfalt der Teile, der Reihenfolge und der Art ihrer Bearbeitung werden Produktionsbereiche nach einem technologischen Prinzip mit in homogenen Gruppen angeordneten Geräten aufgebaut. Bei dieser Produktionsorganisation durchlaufen Teile während des Herstellungsprozesses verschiedene Abschnitte. Daher ist es bei der Übertragung auf jeden nachfolgenden Vorgang (Abschnitt) erforderlich, die Fragen der Qualitätskontrolle der Verarbeitung, des Transports und der Festlegung von Arbeitsplätzen für die Durchführung des nächsten Vorgangs sorgfältig zu berücksichtigen. Zu den Merkmalen der Betriebsplanung und des Betriebsmanagements gehören die rechtzeitige Fertigstellung und Ausführung von Aufträgen, die Überwachung des Fortschritts jedes Detail im Betrieb,
Gewährleistung einer systematischen Auslastung von Standorten und Arbeitsplätzen. Bei der Organisation der Logistik treten große Schwierigkeiten auf. Eine breite Palette hergestellter Produkte und die Verwendung aggregierter Standards für den Materialverbrauch führen zu Schwierigkeiten bei der unterbrechungsfreien Versorgung, weshalb Unternehmen große Materialbestände ansammeln, was wiederum zu einer Erschöpfung des Betriebskapitals führt.
Merkmale der Organisation der Stückproduktion wirken sich auf die Wirtschaftsindikatoren aus. Unternehmen, in denen eine einzige Produktionsart vorherrscht, zeichnen sich durch eine relativ hohe Arbeitsintensität der Produkte und ein großes Volumen an unfertigen Arbeiten aufgrund der langen Lagerung von Teilen zwischen den Vorgängen aus. Die Kostenstruktur von Produkten ist durch einen hohen Lohnkostenanteil gekennzeichnet. Dieser Anteil beträgt in der Regel 20–25 %.
Die wesentlichen Chancen zur Verbesserung der technischen und wirtschaftlichen Kennzahlen der Einzelproduktion liegen in der technischen und organisatorischen Annäherung an die Serienproduktion. Der Einsatz von Serienproduktionsmethoden ist möglich, indem das Spektrum der hergestellten Teile für allgemeine Maschinenbauanwendungen eingeengt wird, Teile und Baugruppen vereinheitlicht werden, was uns ermöglicht, zur Organisation von Themenbereichen überzugehen; Ausbau der konstruktiven Kontinuität, um die Stückzahlen der Teile zu erhöhen; Gruppieren von Teilen, die in Design und Fertigungsreihenfolge ähnlich sind, um die Zeit für die Produktionsvorbereitung zu verkürzen und die Nutzung der Ausrüstung zu verbessern.
Bei der Serienfertigung handelt es sich um die Produktion eines begrenzten Teilespektrums in Chargen, die in bestimmten Zeitabständen wiederholt werden. Dadurch können Sie neben universellen auch spezielle Geräte verwenden. Bei der Gestaltung technologischer Prozesse werden die Ausführungsreihenfolge und die Ausrüstung jedes Vorgangs festgelegt.
Die Organisation der Massenproduktion zeichnet sich durch folgende Merkmale aus. Werkstätten bestehen in der Regel aus geschlossenen Bereichen, in denen Geräte im Rahmen eines standardmäßigen technologischen Prozesses platziert werden. Dadurch entstehen relativ einfache Verbindungen zwischen Arbeitsplätzen und die Voraussetzungen für die Organisation der direkten Bewegung von Teilen während ihres Herstellungsprozesses.
Aufgrund der fachlichen Spezialisierung der Sektionen empfiehlt es sich, eine Charge von Teilen parallel auf mehreren Maschinen zu bearbeiten, die nacheinander Operationen ausführen. Sobald der vorherige Arbeitsgang die Bearbeitung der ersten Teile abgeschlossen hat, werden diese an den nächsten Arbeitsgang übergeben, bis die gesamte Charge bearbeitet ist. Somit wird unter Bedingungen der Massenproduktion eine parallel-sequentielle Organisation des Produktionsprozesses möglich. Das ist seine Besonderheit.
Der Einsatz der einen oder anderen Organisationsform unter Massenproduktionsbedingungen hängt von der Arbeitsintensität und dem Produktionsvolumen der dem Standort zugeordneten Produkte ab. So werden große, arbeitsintensive Teile in hergestellt
große Mengen und einen ähnlichen technologischen Prozess haben, werden einem Standort zugeordnet, auf dem die Produktion mit variablem Durchfluss organisiert ist. Mittelgroße, multifunktionale und weniger arbeitsintensive Teile werden zu Chargen zusammengefasst. Bei regelmäßiger Wiederholung der Produktionsaufnahme werden Gruppenverarbeitungsbereiche organisiert. Kleine Teile mit geringem Arbeitsaufwand, wie z. B. genormte Stehbolzen und Bolzen, werden an einem speziellen Bereich befestigt. In diesem Fall ist es möglich, eine Direktflussproduktion zu organisieren.
Serienproduktionsunternehmen zeichnen sich durch eine deutlich geringere Arbeitsintensität und Herstellungskosten von Produkten aus als Einzelunternehmen. Bei der Massenfertigung erfolgt die Bearbeitung der Produkte im Vergleich zur Einzelfertigung mit weniger Unterbrechungen, was den Umfang der laufenden Arbeiten reduziert.
Aus organisatorischer Sicht ist die Einführung kontinuierlicher Produktionsmethoden die Hauptreserve zur Steigerung der Arbeitsproduktivität in der Serienproduktion.
Die Massenproduktion zeichnet sich durch höchste Spezialisierung aus und zeichnet sich durch die Produktion eines begrenzten Teilespektrums in großen Mengen aus. Massenproduktionswerkstätten sind mit modernster Ausrüstung ausgestattet, was eine nahezu vollständige Automatisierung der Teileproduktion ermöglicht. Automatische Produktionslinien haben sich hier durchgesetzt.
Technologische Bearbeitungsprozesse werden Schritt für Schritt sorgfältiger entwickelt. Jeder Maschine sind relativ wenige Arbeitsgänge zugeordnet, was eine möglichst vollständige Auslastung der Arbeitsplätze gewährleistet. Die Ausrüstung befindet sich in einer Kette entlang des technologischen Prozesses einzelner Teile. Die Arbeiter sind auf die Durchführung von ein oder zwei Arbeitsgängen spezialisiert. Die Teile werden Stück für Stück von Betrieb zu Betrieb weitergegeben. Unter Bedingungen der Massenproduktion nimmt die Bedeutung der Organisation des zwischenbetrieblichen Transports und der Instandhaltung von Arbeitsplätzen zu. Die ständige Überwachung des Zustands von Schneidwerkzeugen, -geräten und -geräten ist eine der Voraussetzungen für die Kontinuität des Produktionsprozesses, ohne die der Arbeitsrhythmus auf Baustellen und in Werkstätten unweigerlich gestört wird. Die Notwendigkeit, auf allen Produktionsebenen einen vorgegebenen Rhythmus einzuhalten, wird zu einem charakteristischen Merkmal der Organisation von Prozessen in der Massenproduktion.
Die Massenproduktion gewährleistet eine möglichst vollständige Nutzung der Ausrüstung, ein hohes Gesamtniveau der Arbeitsproduktivität und die niedrigsten Herstellungskosten der Produkte. In der Tabelle Tabelle 1.1 enthält Daten zu den Vergleichsmerkmalen verschiedener Produktionsarten.
Tabelle 1.1 Vergleichsmerkmale verschiedener Produktionsarten
Vergleichbar | Art der Produktion | |||||||
Zeichen | einzel | seriell | fest |
|||||
Nomenklatur | unbegrenzt | begrenzt |
||||||
Ausgangslautstärke | Nomenklatur | Nomenklatur | Nomenklatur |
|||||
Hergestellt nach | hergestellt | hergestellt in |
||||||
in Chargen | ||||||||
Mengen |
||||||||
Wiederholbarkeit | abwesend | periodisch | Konstante |
|||||
Anwendbarkeit | Universal- | teilweise besonders | meistens |
|||||
Ausrüstung | besonders |
|||||||
Konsolidierung | abwesend | begrenzt | eins zwei | Operationen |
||||
Operationen | Detailoperationen | zur Maschine | ||||||
Maschinen | ||||||||
Standort | ||||||||
Ausrüstung | homogene Maschinen | wird bearbeitet | technologisch |
|||||
konstruktiv | Verfahren | wird bearbeitet |
||||||
technologisch | ||||||||
homogene Teile | ||||||||
Artikel übertragen | sequentiell | parallel | parallel |
|||||
Wehen mit Operation | parallel | |||||||
für eine Operation | ||||||||
Organisationsform | technologisch | Thema | gerade |
|||||
Produktion | ||||||||
Verfahren |
1.4. Organisation des Produktionsprozesses
V Raum und Zeit
Der Aufbau einer rationellen Produktionsstruktur eines Unternehmens erfolgt in folgender Reihenfolge:
- die Zusammensetzung der Werkstätten des Unternehmens und ihre Kapazität werden in Größen festgelegt, die die angegebene Leistung gewährleisten;
- die Flächen für jede Werkstatt und jedes Lager werden berechnet, ihre räumliche Lage im Gesamtplan des Unternehmens wird bestimmt;
- alle Transportverbindungen innerhalb des Unternehmens werden geplant, ihre Interaktion mit nationalen (externen) Routen;
- Es werden die kürzesten Wege für den innerbetrieblichen Transport von Arbeitsgegenständen während des Produktionsprozesses aufgezeigt.
Zu den Produktionseinheiten gehören Werkstätten, Abteilungen, Labore, in denen die Hauptprodukte (vom Unternehmen hergestellt), Komponenten (von außen eingekauft), Materialien usw. hergestellt werden
Halbzeuge, Ersatzteile für Produktwartung und Reparaturen im laufenden Betrieb; verschiedene Arten von Energie werden für technologische Zwecke usw. erzeugt.
ZU Zu den Abteilungen, die die Mitarbeiter betreuen, gehören die Abteilungen Wohnungswesen und kommunale Dienstleistungen, deren Dienstleistungen, Fabrikküchen, Kantinen, Buffets, Kindergärten und Kindergärten, Sanatorien, Pensionen, Erholungsheime, Apotheken, medizinische Einheiten, freiwillige Sportvereine, technische Ausbildungsabteilungen und Bildungseinrichtungen, die sich mit der Verbesserung der Produktionsfähigkeiten, des kulturellen Niveaus der Arbeiter, der Ingenieurarbeiter befassen, und Büroangestellte.
Die wichtigste strukturelle Produktionseinheit eines Unternehmens (mit Ausnahme von Unternehmen mit betriebsloser Führungsstruktur) ist eine Werkstatt – eine administrativ separate Einheit, die einen bestimmten Teil des gesamten Produktionsprozesses (Produktionsphase) durchführt.
Die Werkstätten sind vollwertige Einheiten, die ihre Tätigkeit nach den Grundsätzen der wirtschaftlichen Buchführung ausüben. Im Maschinenbau werden Werkstätten üblicherweise in vier Gruppen eingeteilt: Haupt-, Hilfs-, Neben- und Hilfswerkstätten. In den Hauptwerkstätten werden Vorgänge zur Herstellung von zum Verkauf bestimmten Produkten durchgeführt. Die Hauptwerkstätten gliedern sich in Beschaffung, Bearbeitung und Montage.
ZU Rohlinge umfassen Gießereien, Schmieden und Stanzen, Schmieden und Pressen und manchmal Werkstätten für Schweißkonstruktionen; zur Verarbeitung
- Werkstätten für mechanische Bearbeitung, Holzbearbeitung, thermische, galvanische, Farb- und Lackschutz- und Dekorbeschichtung von Teilen sowie Montagewerkstätten – Werkstätten für die Gesamt- und Endmontage von Produkten, deren Lackierung, Lieferung von Ersatzteilen und abnehmbaren Geräten.
Hilfswerkstätten - Werkzeug, nicht standardmäßige Ausrüstung, Modell, Reparatur, Energie, Transport.
Nebenprodukte - Werkstätten für Recycling und Verarbeitung von Metallabfällen durch Gießen und Pressen von Spänen zu Briketts, Konsumgütergeschäfte. Nebentätigkeiten – Werkstätten, die Behälter für die Verpackung von Produkten und Schnittholz herstellen und die Konservierung von Produkten, die Verpackung, die Verladung und den Versand an den Verbraucher durchführen.
Zusätzlich zu diesen Werkstätten verfügt fast jedes Maschinenbauwerk über Produktionswerkstätten, Dienstleistungen und Abteilungen, die nichtindustrielle Einrichtungen (kommunale, kulturelle, Wohnungswesen usw.) bedienen.
Einen bestimmten Platz in der Struktur aller Maschinenbaubetriebe nehmen Lagerhallen, Sanitäranlagen und Kommunikationseinrichtungen ein (Stromnetze, Gas- und Luftleitungen, Heizung, Lüftung, gut ausgebaute Straßen für den Schienen- und gleislosen Verkehr usw.).
Eine besondere Rolle in der Produktionsstruktur des Vereins (Unternehmens) spielen Design, Technologieabteilungen,
Forschungsinstitute und Labore. Sie entwickeln Zeichnungen und technologische Prozesse, führen experimentelle Arbeiten durch, bringen Produktdesigns in volle Übereinstimmung mit den GOST-Anforderungen, technische Spezifikationen Es werden Versuchs- und Entwicklungsarbeiten durchgeführt. In diesen Abteilungen ist die Integration von Wissenschaft und Produktion besonders deutlich.
Die Werkstätten umfassen Haupt- und Nebenproduktionsbereiche.
Die Hauptproduktionsbereiche werden nach einem technologischen oder fachlichen Prinzip geschaffen. An Standorten, die nach dem Prinzip der technologischen Spezialisierung organisiert sind, werden technologische Operationen einer bestimmten Art durchgeführt. In einer Gießerei können beispielsweise Abteilungen in folgenden Technologiebereichen organisiert werden: Bodenvorbereitung, Herstellung von Kernen, Gießformen, Bearbeitung fertiger Gussteile usw., in einer Schmiede - Abteilungen zur Herstellung von Schmiederohlingen auf Hämmern und Pressen, Wärmebehandlung usw., in der mechanischen Abteilung - Drehen, Revolver, Fräsen, Schleifen, Metallbearbeitung und andere Bereiche; in der Montageabteilung - Bereiche der Einheits- und Endmontage von Produkten, Prüfung ihrer Teile und Systeme, Kontrolle und Prüfplatz, Lackierung usw.
An Standorten, die nach dem Prinzip der Fachspezialisierung organisiert sind, führen sie nicht einzelne Arbeitsgänge, sondern technologische Prozesse als Ganzes durch und erhalten letztendlich fertige Produkte für einen bestimmten Standort.
Zu den Hilfsabteilungen gehören die Abteilungen des Chefmechanikers und des Chefenergieingenieurs für die routinemäßige Reparatur und Wartung mechanischer Verarbeitungs- und Energieanlagen; ein Werkzeuglager mit einer Schärfwerkstatt, einem Transportdienst, einer Werkstatt für die Reparatur und Wartung technologischer Geräte usw.
Mit einem zentralisierten Service-Organisationssystem und aktuelle Reparaturen Das Unternehmen richtet in Werkstätten keine Nebenflächen ein.
Nebenwerkstätten und -bereiche werden nach den gleichen Kriterien organisiert wie die Werkstätten und -bereiche der Hauptproduktion.
Die ständige Aufmerksamkeit der Unternehmensleiter auf Umweltfaktoren ermöglicht rechtzeitige Änderungen in der Managementstruktur, um die Nachhaltigkeit des Unternehmens und seine flexible Reaktion auf Marktschwankungen zu fördern. Aus diesem Grund sollte die Organisation des Produktionsmanagements (territoriale, Transport-, Ressourcen-, Technologie- und andere Faktoren) als ein Handlungssystem betrachtet werden, das die Entwicklung des Unternehmens steuert.
Die Produktionsstruktur wird von mehreren Faktoren beeinflusst:
Branchenzugehörigkeit des Unternehmens - Produktpalette, Konstruktionsmerkmale, verwendete Materialien, Methoden zur Gewinnung und Bearbeitung von Werkstücken; Einfachheit des Designs und der Herstellbarkeit des Produkts; Niveau der Anforderungen an die Produktqualität; Art der Produktion, Grad ihrer Spezialisierung und Zusammenarbeit;
Zusammensetzung der Ausrüstung und technologischen Ausrüstung (universelle, spezielle, nicht standardmäßige Ausrüstung, Förderband oder automatische Linien):
- zentrale oder dezentrale Organisation der Gerätewartung, routinemäßiger Reparaturen und technologischer Geräte;
- die Fähigkeit der Produktion, sich schnell und ohne große Verluste an die Produktion neuer Produkte in einer veränderten Produktpalette anzupassen;
- die Art des Produktionsprozesses in den Haupt-, Hilfs-, Neben- und Hilfswerkstätten.
Die Produktionsstruktur von Unternehmen verschiedener Branchen weist ihre eigenen Merkmale auf, die sich aus der Art der Hauptproduktion ergeben.
In den meisten Fällen verfügen Textilfabriken über eine technologische Struktur mit gleichzeitiger Spezialisierung einzelner Abteilungen auf bestimmte Garnnummern und Rohstoffpositionen. Die meisten Fabriken verfügen über alle Stufen der Stoffproduktion: Spinnen, Weben, Veredeln. Einige Fabriken sind auf die Durchführung von ein oder zwei Schritten spezialisiert.
In Hüttenwerken herrscht die technologische Struktur vor. Es entstehen Kopier-, Hochofen-, Stahl- und Walzwerkstätten.
Gemeinsamkeiten in der Produktionsstruktur von Unternehmen verschiedener Branchen
- Organisation von Hilfs- und Servicebetrieben. Werkstätten für den leitenden Energieingenieur und leitenden Mechaniker sowie Transport- und Lagereinrichtungen gibt es in Unternehmen jeder Branche. In einem Maschinenbaubetrieb gibt es immer eine Werkzeugwerkstatt, in einer Textilfabrik gibt es Filz- und Schiffchenwerkstätten, die Werkzeuge für die Textilproduktion herstellen.
Die Frage der Auswahl und Verbesserung der Produktionsstruktur eines Unternehmens (Verbandes) muss sowohl beim Aufbau neuer Unternehmen als auch beim Umbau bestehender Unternehmen gelöst werden.
Die wichtigsten Möglichkeiten zur Verbesserung der Produktionsstruktur:
- Konsolidierung von Unternehmen und Werkstätten;
- Suche und Umsetzung eines weiterentwickelten Prinzips für den Bau von Werkstätten
Und produzierende Unternehmen;
- Aufrechterhaltung einer rationalen Beziehung zwischen den Haupt-, Hilfs- und Serviceabteilungen;
- ständige Arbeit an der Rationalisierung der Unternehmensstruktur;
- Integration einzelner Unternehmen, Schaffung leistungsstarker Industrie- und Wissenschafts- und Produktionsverbände basierend auf der Konzentration der Produktion;
- Gewährleistung der Verhältnismäßigkeit zwischen allen Teilen des Unternehmens;
- Änderung des Produktionsprofils, d. h. Art der Produktveröffentlichung, Spezialisierung und Zusammenarbeit; Entwicklung von Produktionskombinationen; Leistung strukturelle und technologische Homogenität
Produkte durch umfassende Vereinheitlichung und Standardisierung; Schaffung einer geschäftslosen Unternehmensführungsstruktur. Die Zusammenlegung von Betrieben und Werkstätten ermöglicht die Einführung neuer Hochleistungsgeräte in größerem Umfang, die ständige Verbesserung der Technik und die Verbesserung der Produktionsorganisation.
Die Identifizierung und Umsetzung von Reserven zur Verbesserung der Struktur von Werkstätten und Produktionsbereichen sind Faktoren für die kontinuierliche Verbesserung der Produktionsstruktur und die Steigerung der Produktionseffizienz.
Die Aufrechterhaltung eines rationellen Verhältnisses zwischen den Haupt-, Hilfs- und Servicewerkstätten und -bereichen sollte angestrebt werden spezifisches Gewicht Hauptwerkstätten nach der Anzahl der beschäftigten Arbeitnehmer, den Kosten des Anlagevermögens und der Größe der belegten Fläche.
Die Rationalisierung der Planung beinhaltet die Verbesserung des Masterplans des Unternehmens.
Die Qualität der Nutzung der verfügbaren Möglichkeiten, Ressourcen und günstigen Marktbedingungen im Unternehmen hängt mit dem Produktionsplanungsmechanismus zusammen. Die Erstellung eines optimalen Plans im Hinblick auf mögliche Veränderungen der Marktsituation ist der Schlüssel zur Verwirklichung der internen Nachhaltigkeit eines Unternehmens im externen wirtschaftlichen Umfeld. Deshalb sollten Sie bezahlen Besondere Aufmerksamkeit für Produktionsplanungsmaterial.
Der Masterplan ist einer der wichtigsten Teile des Projekts eines Industrieunternehmens und enthält eine umfassende Lösung für die Fragen der Planung und Landschaftsgestaltung des Territoriums, der Platzierung von Gebäuden, Bauwerken, der Verkehrskommunikation, der Versorgungsnetze sowie der Wirtschafts- und Verbraucherorganisation Dienstleistungssysteme sowie der Standort des Unternehmens in einem Industriegebiet (Knoten).
Der Masterplan stellt hohe Anforderungen, die wichtigsten davon sind:
1) Standort der Produktionseinheiten streng entlang des technologischen Prozesses – Lager für Rohstoffe, Materialien und Halbfabrikate, Beschaffung, Verarbeitung, Montagehallen, Lager für Fertigprodukte;
2) Platzierung von Nebengrundstücken und landwirtschaftlichen Betrieben in der Nähe der Hauptproduktionsstätten, die sie bedienen;
3) rationelle Anordnung der Bahngleise innerhalb des Unternehmens. Sie müssen sowohl mit den Räumlichkeiten der Lager für Rohstoffe, Materialien und Halbfabrikate als auch mit dem Lager für Fertigprodukte verbunden sein, wo die Produkte mit abnehmbarer Ausrüstung, Ersatzteilen, Konservierung, Verpackung, Verschließen, Verladung und Versand der Produkte aufgefüllt werden an den Verbraucher;
4) die größte Geradlinigkeit und die kürzesten Wege für den Transport von Rohstoffen, Materialien, Halbzeugen und Fertigprodukten;
5) Eliminierung von Gegen- und Rückströmen im Innen- und Außenbereich;
6) die am besten geeigneten Optionen für den Standort der externen Kommunikation des Unternehmens und deren Anbindung an Versorgungsnetze, Autobahnen, Eisenbahnen usw.
7) Platzierung von Laboren (Messtechnik, Chemie, Röntgenprüfung, Ultraschall usw.), deren Wartung sowie Wärmebehandlungsbetriebe und Schutzbeschichtungen von Teilen und Fertigprodukten.
Bei großen Unternehmen empfiehlt es sich, Werkstätten zu Gebäuden zusammenzufassen. Bei der Gestaltung von Unternehmen ist darauf zu achten
Kompaktheit des Gebäudes. Abhängig von der Art des Produkts Design-Merkmale Bauen Sie nach Möglichkeit mehrstöckige Gebäude. Wählen Sie rationelle Abstände zwischen Werkstätten, Werkstattblöcken und Gebäuden und beachten Sie dabei die hygienischen und technischen Bedingungen sowie Sicherheits- und Brandschutzanforderungen.
Der Masterplan muss außerdem die Möglichkeit einer Weiterentwicklung des Unternehmens vorsehen und eine Produktionsstruktur vorsehen, in der höchste Produktionsergebnisse bei geringsten Kosten erzielt werden können; Bedingungen für eine maximale Befriedigung der Interessen aller Mitarbeiter des Unternehmens schaffen.
Platzierung von Haupt-, Hilfs-, Neben- und Hilfswerkstätten
Und Gebiete, Servicebetriebe, Leitungsorgane, Transportwege auf dem Territorium des Unternehmens haben einen enormen Einfluss auf die Organisation der Produktion und ihrer Wirtschaft;
bestimmt die Richtung der Güterströme, die Länge der Bahnstrecken
Und gleislose Gleise sowie die effiziente Nutzung der Produktionsfläche.
Die Kompaktheit des Gebäudes, seine rationelle Dichte und die Anzahl der Stockwerke ermöglichen Einsparungen Kapital Investitionen, den Umfang der Bauarbeiten und des innerbetrieblichen Transports reduzieren, die Kommunikationslänge verkürzen, die Dauer des Produktionszyklus verkürzen, eine umfassende Mechanisierung und Automatisierung von Produktions- und Hilfsprozessen in größerem Maßstab einführen, den Zeitaufwand für fertige Produkte reduzieren das Lager, erhöhen die Arbeitsproduktivität, verbessern die Produktqualität und senken den Selbstkostenpreis.
Die Aufgabe von Mitarbeitern von Designinstituten, Ingenieur- und Technikarbeitern sowie Produktionsmitarbeitern Industrieunternehmen- Kontinuierliche Verbesserung der Produktionsstruktur, der Standorte der Werkstätten und Produktionsbereiche. In der Zeit des Wiederaufbaus, der technischen Umrüstung, der Unternehmenserweiterung und des Neubaus muss diesem Thema besondere Aufmerksamkeit gewidmet werden. Die Verbesserung des Masterplans des Werks ist Ausdruck des Anliegens, die Produktionseffizienz zu steigern und die Qualität der Produkte und Arbeitsbedingungen zu verbessern.
Die Analyse von Informationen über die Dynamik des internen Produktionsangebots eines Unternehmens und der Marktnachfrage nach seinen Produkten ist Voraussetzung für eine qualitative Bewertung seiner Nachhaltigkeit. Gleichzeitig kann die Aufmerksamkeit auf die Produktionswartung eines Unternehmens die Faktoren für die Fähigkeit oder Unfähigkeit des Unternehmens und eine nachhaltige Entwicklung in der Zukunft aufdecken. In diesem Fall kann der Mechanismus einer solchen Analyse darin bestehen, die Beziehung zwischen den Eigenschaften der Dienstleistung und den Zielen der Sicherstellung der allgemeinen Merkmale der Produktionsdienstleistung im Unternehmen festzulegen.
Die Organisationsform der Produktion ist eine bestimmte zeitliche und räumliche Kombination von Elementen des Produktionsprozesses mit einem angemessenen Grad ihrer Integration, ausgedrückt durch ein System stabiler Verbindungen.
Verschiedene zeitliche und räumliche Strukturstrukturen bilden eine Reihe grundlegender Formen der Produktionsorganisation. Die zeitliche Struktur der Produktionsorganisation wird durch die Zusammensetzung der Elemente des Produktionsprozesses und die Reihenfolge ihres zeitlichen Zusammenwirkens bestimmt. Je nach Art der temporären Struktur werden Organisationsformen mit sequentiellem, parallelem und parallel-sequentiellem Transfer von Arbeitsgegenständen in der Produktion unterschieden.
Die Organisationsform der Produktion mit sequentiellem Transfer von Arbeitsgegenständen ist eine Kombination von Elementen des Produktionsprozesses, die den Transport verarbeiteter Produkte über alle Produktionsbereiche in Chargen beliebiger Größe gewährleistet. Die Übergabe der Arbeitsgegenstände an jeden nachfolgenden Arbeitsgang erfolgt erst nach Abschluss der Bearbeitung der gesamten Charge im vorherigen Arbeitsgang. Diese Form ist in Bezug auf Änderungen im Produktionsprogramm am flexibelsten, sie ermöglicht eine ausreichende volle Nutzung der Ausrüstung, wodurch die Anschaffungskosten gesenkt werden können. Der Nachteil dieser Form der Produktionsorganisation ist die relativ lange Dauer des Produktionszyklus, da jedes Teil auf die Verarbeitung der gesamten Charge wartet, bevor es den nächsten Arbeitsgang durchführt.
Die Organisationsform der Produktion mit paralleler Übergabe von Arbeitsgegenständen basiert auf einer solchen Kombination von Elementen des Produktionsprozesses, die es ermöglicht, Arbeitsgegenstände einzeln und ohne Wartezeit von Betrieb zu Betrieb zu starten, zu verarbeiten und zu übergeben. Diese Organisation des Produktionsprozesses führt zu einer Reduzierung der Anzahl der zu bearbeitenden Teile und damit zu einem geringeren Platzbedarf für Lager und Gänge. Sein Nachteil ist der mögliche Ausfall von Geräten (Arbeitsplätzen) aufgrund unterschiedlicher Betriebsdauern.
Dazwischen liegt die Organisationsform der Produktion mit parallel-sequentiellem Transfer von Arbeitsgegenständen
serielle und parallele Formen und beseitigt teilweise deren inhärente Nachteile. Produkte werden in Transportchargen von Betrieb zu Betrieb transportiert. Gleichzeitig wird die Kontinuität des Geräte- und Arbeitseinsatzes gewährleistet und ein teilweise paralleler Durchlauf einer Teilecharge durch technologische Prozessabläufe ermöglicht.
Die räumliche Struktur der Produktionsorganisation wird durch die Menge der auf dem Arbeitsplatz konzentrierten technologischen Ausrüstung (Anzahl der Arbeitsplätze) und ihre Lage relativ zur Bewegungsrichtung der Arbeitsgegenstände im umgebenden Raum bestimmt. Abhängig von der Anzahl der technologischen Geräte (Arbeitsplätze) wird zwischen einem eingliedrigen Produktionssystem und der entsprechenden Struktur eines separaten Arbeitsplatzes und einem mehrgliedrigen System mit Werkstatt-, Linien- oder Zellenstruktur unterschieden. Mögliche Optionen für die räumliche Struktur der Produktionsorganisation sind in Abb. dargestellt. 1.2. Die Werkstattstruktur zeichnet sich durch die Schaffung von Bereichen aus, in denen Geräte (Arbeitsplätze) parallel zum Werkstückfluss angeordnet sind, was deren Spezialisierung auf der Grundlage technologischer Homogenität impliziert. Dabei wird eine am Standort ankommende Teilecharge an einen der freien Arbeitsplätze geschickt, wo sie den notwendigen Bearbeitungszyklus durchläuft und anschließend an einen anderen Standort (in die Werkstatt) überführt wird.
Reis. 1.2. Optionen für die räumliche Struktur des Produktionsprozesses
In einem Abschnitt mit einer linearen räumlichen Struktur befinden sich Geräte (Arbeitsplätze) entlang des technologischen Prozesses und eine Charge von in dem Abschnitt bearbeiteten Teilen wird sequentiell von einem Arbeitsplatz zum anderen übertragen.
Die zellulare Struktur der Produktionsorganisation vereint die Merkmale von Linear- und Werkstattorganisation. Die Kombination räumlicher und zeitlicher Strukturen des Produktionsprozesses mit einem gewissen Grad an Integration von Teilprozessen bestimmt verschiedene Organisationsformen der Produktion: technologisch, subjektiv, direkt, punktuell, integriert (Abb. 1.3). Schauen wir uns die charakteristischen Merkmale jedes einzelnen von ihnen an.
Reis. 1.3. Formen der Produktionsorganisation
Die technologische Form der Organisation des Produktionsprozesses ist durch eine Werkstattstruktur mit sequentieller Übergabe von Arbeitsgegenständen gekennzeichnet. Diese Organisationsform ist im Maschinenbau weit verbreitet, da sie in der Kleinserienfertigung eine maximale Anlagenauslastung gewährleistet und an häufige Veränderungen im technologischen Prozess angepasst ist. Gleichzeitig hat der Einsatz einer technologischen Form der Organisation des Produktionsprozesses eine Reihe negativer Folgen. Eine große Anzahl von Teilen und deren wiederholte Bewegung während der Bearbeitung führen zu einer Erhöhung des Arbeitsvolumens und einer Erhöhung der Anzahl der Zwischenlagerplätze. Ein erheblicher Teil des Produktionszyklus besteht aus Zeitverlusten, die durch komplexe Kommunikation zwischen Standorten verursacht werden.
Die Subjektform der Produktionsorganisation weist eine zelluläre Struktur mit parallel-sequentiellem (sequentiellem) Transfer von Arbeitsgegenständen in der Produktion auf. In der Regel sind am Fachgebiet alle für die Bearbeitung einer Teilegruppe vom Anfang bis zum Ende des technologischen Prozesses notwendigen Geräte installiert. Ist der verarbeitungstechnologische Kreislauf innerhalb der Site geschlossen, spricht man von subjektgeschlossen.
Die entsprechende Konstruktion der Abschnitte gewährleistet Geradheit und verkürzt die Dauer des Produktionszyklus für die Herstellung von Teilen. Im Vergleich zur technologischen Form ermöglicht die Objektform eine Reduzierung der Gesamtkosten für den Transport von Teilen und des Bedarfs an Produktionsfläche pro Produktionseinheit. Allerdings hat diese Form der Produktionsorganisation auch Nachteile. Der wichtigste Grund besteht darin, dass bei der Bestimmung der Zusammensetzung der auf der Baustelle installierten Ausrüstung die Notwendigkeit in den Vordergrund tritt, bestimmte Arten der Teilebearbeitung durchzuführen, was nicht immer eine vollständige Auslastung der Ausrüstung gewährleistet.
Darüber hinaus erfordern die Erweiterung und Aktualisierung der Produktpalette eine regelmäßige Neugestaltung der Produktionsbereiche und Änderungen in der Struktur des Geräteparks. Die Direktflussform der Produktionsorganisation zeichnet sich durch eine lineare Struktur mit stückweiser Übergabe von Arbeitsgegenständen aus. Diese Form gewährleistet die Umsetzung einer Reihe von Organisationsprinzipien: Spezialisierung, Direktheit, Kontinuität, Parallelität. Sein Einsatz führt zu einer Verkürzung der Dauer des Produktionszyklus, einem effizienteren Arbeitseinsatz aufgrund einer stärkeren Spezialisierung der Arbeitskräfte und einer Verringerung des Arbeitsvolumens.
Bei der Punktform der Produktionsorganisation wird die Arbeit vollständig an einem Arbeitsplatz ausgeführt. Das Produkt wird dort hergestellt, wo sich sein Hauptbestandteil befindet. Ein Beispiel ist die Montage eines Produkts, bei der sich ein Arbeiter darum bewegt. Die Organisation der Punktproduktion hat eine Reihe von Vorteilen: Sie bietet die Möglichkeit häufiger Änderungen im Design der Produkte und der Verarbeitungsreihenfolge sowie die Produktion von Produkten unterschiedlichster Bandbreite in Mengen, die durch den Produktionsbedarf bestimmt werden; Die mit dem Standortwechsel der Anlagen verbundenen Kosten werden reduziert und die Produktionsflexibilität erhöht.
Die integrierte Form der Produktionsorganisation beinhaltet die Zusammenfassung von Haupt- und Nebenvorgängen zu einem einzigen integrierten Produktionsprozess mit zellulärer oder linearer Struktur mit sequentiellem, parallelem oder parallel-sequentiellem Transfer von Arbeitsgegenständen in der Produktion. Im Gegensatz zur bisherigen Praxis der getrennten Gestaltung der Prozesse der Lagerung, des Transports, der Verwaltung und der Verarbeitung in Bereichen mit integrierter Organisationsform ist es erforderlich, diese Teilprozesse zu einem einzigen Produktionsprozess zu verknüpfen. Dies wird durch die Kombination aller Arbeitsplätze mit Hilfe eines automatischen Transport- und Lagerkomplexes erreicht, bei dem es sich um eine Reihe miteinander verbundener automatischer Lagergeräte und Computergeräte handelt, die die Lagerung und Bewegung von Arbeitsgegenständen zwischen einzelnen Arbeitsplätzen organisieren sollen.
Die Steuerung des Produktionsprozesses erfolgt hier über einen Computer, der das Funktionieren aller Elemente des Produktionsprozesses am Standort nach folgendem Schema sicherstellt: Suche
benötigtes Werkstück im Lager - Transport des Werkstücks zur Maschine - Bearbeitung - Rückführung des Teils ins Lager. Um zeitliche Abweichungen beim Transport und der Bearbeitung von Teilen auszugleichen, werden an einzelnen Arbeitsplätzen Pufferlager für zwischenbetriebliche und versicherungstechnische Reserven geschaffen. Die Schaffung integrierter Produktionsstandorte ist mit relativ hohen Einmalkosten verbunden, die durch die Integration und Automatisierung des Produktionsprozesses entstehen.
Der wirtschaftliche Effekt des Übergangs zu einer integrierten Form der Produktionsorganisation wird durch eine Verkürzung der Dauer des Produktionszyklus für die Herstellung von Teilen, eine Erhöhung der Ladezeit von Maschinen und eine verbesserte Regelung und Steuerung von Produktionsprozessen erreicht. In Abb. Abbildung 1.4 zeigt Anlagenlayoutdiagramme in Bereichen mit unterschiedlichen Formen der Produktionsorganisation.
Reis. 1.4. Anordnungspläne von Geräten (Arbeitsplätzen) in Bereichen mit unterschiedlichen Formen der Produktionsorganisation:
a) technologisch; b) Betreff; c) direkter Fluss; d) Punkt (für den Fall der Montage); e) integriert
Turovets O.G., Rodionov V.B., Bukhalkov M.I. Kapitel aus dem Buch „Organisation der Produktion und Unternehmensführung“
Verlag „INFRA-M“, 2007
10.1. Konzept des Produktionsprozesses
Die moderne Produktion ist ein komplexer Prozess der Umwandlung von Rohstoffen, Materialien, Halbfabrikaten und anderen Arbeitsgegenständen in fertige Produkte, die den Bedürfnissen der Gesellschaft entsprechen.
Als Gesamtheit aller in einem Unternehmen durchgeführten Handlungen von Menschen und Werkzeugen zur Herstellung bestimmter Produktarten wird bezeichnet Fertigungsprozess.
Der Hauptteil des Produktionsprozesses sind technologische Prozesse, die gezielte Maßnahmen zur Veränderung und Bestimmung des Zustands von Arbeitsgegenständen beinhalten. Bei der Umsetzung technologischer Prozesse kommt es zu Veränderungen der geometrischen Formen, Größen sowie der physikalischen und chemischen Eigenschaften von Arbeitsgegenständen.
Der Produktionsprozess umfasst neben technologischen auch nichttechnologische Prozesse, die nicht dazu dienen, die geometrischen Formen, Größen oder physikalischen und chemischen Eigenschaften von Arbeitsgegenständen zu verändern oder deren Qualität zu überprüfen. Zu diesen Prozessen gehören Transport, Lager, Be- und Entladen, Kommissionierung und einige andere Vorgänge und Prozesse.
Im Produktionsprozess werden Arbeitsprozesse mit natürlichen Prozessen kombiniert, bei denen Veränderungen an Arbeitsgegenständen unter dem Einfluss von Naturkräften ohne menschliches Eingreifen erfolgen (z. B. Trocknen lackierter Teile an der Luft, Abkühlen von Gussteilen, Alterung von Gussteilen usw. ).
Verschiedene Produktionsprozesse. Entsprechend ihrem Zweck und ihrer Rolle in der Produktion werden Prozesse in Haupt-, Hilfs- und Wartungsprozesse unterteilt.
Hauptsächlich werden Produktionsprozesse genannt, bei denen die Herstellung der vom Unternehmen hergestellten Hauptprodukte erfolgt. Das Ergebnis der Hauptprozesse im Maschinenbau ist die Herstellung von Maschinen, Apparaten und Instrumenten, die das Produktionsprogramm des Unternehmens bilden und seiner Spezialisierung entsprechen, sowie die Herstellung von Ersatzteilen für diese zur Lieferung an den Verbraucher.
ZU Hilfs- umfassen Prozesse, die den unterbrechungsfreien Ablauf grundlegender Prozesse gewährleisten. Ihr Ergebnis sind Produkte, die im Unternehmen selbst eingesetzt werden. Zu den Hilfsprozessen gehören die Reparatur von Geräten, die Herstellung von Geräten, die Erzeugung von Dampf und Druckluft usw.
Portion werden Prozesse genannt, bei deren Umsetzung Leistungen erbracht werden, die für das normale Funktionieren sowohl der Haupt- als auch der Hilfsprozesse notwendig sind. Hierzu zählen beispielsweise die Prozesse Transport, Lagerung, Auswahl und Montage von Teilen etc.
Unter modernen Bedingungen, insbesondere in der automatisierten Produktion, besteht die Tendenz zur Integration von Grund- und Wartungsprozessen. So werden in flexiblen automatisierten Komplexen Grund-, Kommissionierungs-, Lager- und Transportvorgänge in einem einzigen Prozess zusammengefasst.
Die Gesamtheit der Grundprozesse bildet die Hauptproduktion. Bei Maschinenbauunternehmen besteht die Hauptproduktion aus drei Phasen: Beschaffung, Verarbeitung und Montage. Bühne Produktionsprozess ist ein Komplex von Prozessen und Arbeiten, deren Durchführung den Abschluss eines bestimmten Teils des Produktionsprozesses charakterisiert und mit dem Übergang des Arbeitsgegenstandes von einem qualitativen Zustand in einen anderen verbunden ist.
ZU Beschaffung Zu den Phasen gehören die Prozesse zur Gewinnung von Werkstücken – Schneiden von Materialien, Gießen, Stanzen. wird bearbeitet Die Phase umfasst die Prozesse der Umwandlung von Rohlingen in Fertigteile: Bearbeitung, Wärmebehandlung, Lackieren und Galvanisieren usw. Montage Phase – der letzte Teil des Produktionsprozesses. Es umfasst die Montage von Komponenten und Fertigprodukten, die Einstellung und Fehlerbehebung von Maschinen und Instrumenten sowie deren Prüfung.
Der Aufbau und die gegenseitigen Verbindungen der Haupt-, Hilfs- und Nebenprozesse bilden die Struktur des Produktionsprozesses.
Organisatorisch werden Produktionsprozesse in einfache und komplexe unterteilt. Einfach werden Produktionsprozesse genannt, die aus nacheinander ausgeführten Aktionen bestehen einfaches Objekt Arbeit. Zum Beispiel der Produktionsprozess, bei dem ein Teil oder eine Charge identischer Teile hergestellt wird. Schwierig Ein Prozess ist eine Kombination einfacher Prozesse, die an vielen Arbeitsgegenständen ausgeführt werden. Beispielsweise der Prozess der Herstellung einer Baugruppe oder eines gesamten Produkts.
10.2. Wissenschaftliche Prinzipien der Organisation von Produktionsprozessen
Tätigkeiten im Zusammenhang mit der Organisation von Produktionsprozessen. Die vielfältigen Produktionsprozesse, die zur Entstehung industrieller Produkte führen, müssen ordnungsgemäß organisiert und sichergestellt werden effizientes Funktionieren um bestimmte Arten hochwertiger Produkte und in Mengen herzustellen, die den Bedürfnissen der Volkswirtschaft und der Bevölkerung des Landes entsprechen.
Die Organisation von Produktionsprozessen besteht darin, Menschen, Werkzeuge und Arbeitsgegenstände in einem einzigen Prozess zur Herstellung materieller Güter zu vereinen und eine rationelle räumliche und zeitliche Verknüpfung von Grund-, Hilfs- und Dienstleistungsprozessen sicherzustellen.
Die räumliche Kombination von Elementen des Produktionsprozesses und all seiner Spielarten erfolgt auf der Grundlage der Gestaltung der Produktionsstruktur des Unternehmens und seiner Unternehmensbereiche. In diesem Zusammenhang sind die wichtigsten Aktivitäten die Auswahl und Begründung der Produktionsstruktur des Unternehmens, d.h. Bestimmung der Zusammensetzung und Spezialisierung seiner konstituierenden Einheiten und Herstellung rationaler Beziehungen zwischen ihnen.
Bei der Entwicklung der Produktionsstruktur werden Konstruktionsberechnungen zur Bestimmung der Zusammensetzung des Geräteparks unter Berücksichtigung seiner Produktivität, Austauschbarkeit und der Möglichkeit einer effektiven Nutzung durchgeführt. Es werden auch rationelle Anordnungen der Abteilungen, der Platzierung von Geräten und Arbeitsplätzen entwickelt. Es werden organisatorische Voraussetzungen für den unterbrechungsfreien Betrieb der Geräte und der direkten Teilnehmer am Produktionsprozess – der Arbeiter – geschaffen.
Einer der Hauptaspekte bei der Bildung einer Produktionsstruktur besteht darin, das vernetzte Funktionieren aller Komponenten des Produktionsprozesses sicherzustellen: Vorbereitungsvorgänge, Hauptproduktionsprozesse und Wartung. Es ist notwendig, die rationalsten Organisationsformen und Methoden zur Durchführung bestimmter Prozesse für spezifische Produktions- und technische Bedingungen umfassend zu begründen.
Ein wichtiges Element der Organisation von Produktionsprozessen ist die Arbeitsorganisation der Arbeiter, die konkret die Verbindung der Arbeit mit den Produktionsmitteln umsetzt. Die Methoden der Arbeitsorganisation werden maßgeblich durch die Formen des Produktionsprozesses bestimmt. Dabei liegt der Schwerpunkt auf der Sicherstellung einer rationellen Arbeitsteilung und der darauf basierenden Festlegung der beruflichen und Qualifikationszusammensetzung der Arbeitnehmer, der wissenschaftlichen Gestaltung und optimalen Instandhaltung der Arbeitsplätze sowie der umfassenden Verbesserung und Verbesserung der Arbeitsbedingungen.
Die Organisation von Produktionsprozessen setzt auch die zeitliche Kombination ihrer Elemente voraus, die eine bestimmte Reihenfolge der Ausführung einzelner Vorgänge, eine rationelle Kombination der Zeit für die Ausführung verschiedener Arbeitsarten und die Festlegung kalendergeplanter Standards für die Bewegung bestimmt von Arbeitsgegenständen. Der normale zeitliche Ablauf der Prozesse wird auch durch die Reihenfolge der Produkteinführung und -freigabe, die Bildung der notwendigen Bestände (Reserven) und Produktionsreserven sowie die unterbrechungsfreie Versorgung der Arbeitsplätze mit Werkzeugen, Werkstücken und Materialien sichergestellt. Ein wichtiger Bereich dieser Tätigkeit ist die Organisation der rationellen Bewegung von Materialflüssen. Die Lösung dieser Aufgaben erfolgt auf der Grundlage der Entwicklung und Implementierung betrieblicher Produktionsplanungssysteme unter Berücksichtigung der Art der Produktion sowie technischer und organisatorischer Besonderheiten der Produktionsprozesse.
Schließlich kommt bei der Organisation von Produktionsprozessen in einem Unternehmen der Entwicklung eines Systems der Interaktion zwischen einzelnen Produktionseinheiten ein wichtiger Stellenwert zu.
Grundsätze der Organisation des Produktionsprozesses stellen die Ausgangspunkte dar, auf deren Grundlage Aufbau, Betrieb und Entwicklung von Produktionsprozessen erfolgen.
Prinzip Differenzierung Dabei geht es darum, den Produktionsprozess in einzelne Teile (Prozesse, Vorgänge) zu unterteilen und diese den entsprechenden Abteilungen des Unternehmens zuzuordnen. Dem Prinzip der Differenzierung steht das Prinzip gegenüber kombinieren, was die Vereinheitlichung aller oder eines Teils verschiedener Prozesse zur Herstellung bestimmter Produkttypen an einem Standort, einer Werkstatt oder einer Produktion bedeutet. Abhängig von der Komplexität des Produkts, dem Produktionsvolumen und der Art der verwendeten Ausrüstung kann der Produktionsprozess in einer Produktionseinheit (Werkstatt, Bereich) konzentriert oder auf mehrere Einheiten verteilt sein. So werden in Maschinenbauunternehmen mit einer bedeutenden Produktion ähnlicher Produkte eigenständige mechanische und Montagefertigungen und -werkstätten organisiert und für kleine Produktserien können einheitliche mechanische Montagewerkstätten geschaffen werden.
Die Grundsätze der Differenzierung und Kombination gelten auch für einzelne Arbeitsplätze. Eine Produktionslinie beispielsweise besteht aus einer differenzierten Reihe von Arbeitsplätzen.
Bei praktischen Aktivitäten zur Organisation der Produktion sollte bei der Anwendung der Prinzipien der Differenzierung oder Kombination dem Prinzip Vorrang eingeräumt werden, das die besten wirtschaftlichen und sozialen Merkmale des Produktionsprozesses gewährleistet. Somit ermöglicht die Fließproduktion, die sich durch einen hohen Differenzierungsgrad des Produktionsprozesses auszeichnet, eine Vereinfachung seiner Organisation, eine Verbesserung der Fähigkeiten der Arbeitnehmer und eine Steigerung der Arbeitsproduktivität. Eine übermäßige Differenzierung erhöht jedoch die Ermüdung der Arbeiter, eine große Anzahl von Vorgängen erhöht den Bedarf an Ausrüstung und Produktionsraum, führt zu unnötigen Kosten für bewegliche Teile usw.
Prinzip Konzentrationen bezeichnet die Konzentration bestimmter Produktionsbetriebe zur Herstellung technologisch homogener Produkte oder zur Erbringung funktional homogener Arbeiten an getrennten Arbeitsplätzen, Bereichen, Werkstätten oder Produktionsstätten des Unternehmens. Die Möglichkeit, ähnliche Arbeiten in getrennten Produktionsbereichen zu konzentrieren, wird durch folgende Faktoren bestimmt: die Gemeinsamkeit technologischer Methoden, die den Einsatz derselben Art von Ausrüstung erfordern; Fähigkeiten von Geräten, wie z. B. Bearbeitungszentren; Erhöhung des Produktionsvolumens bestimmter Produkttypen; die wirtschaftliche Machbarkeit der Konzentration der Produktion bestimmter Produkttypen oder der Durchführung ähnlicher Arbeiten.
Bei der Wahl der einen oder anderen Konzentrationsrichtung müssen die Vorteile jeder einzelnen davon berücksichtigt werden.
Durch die Konzentration technologisch homogener Arbeiten in einer Abteilung wird weniger Duplikat-Equipment benötigt, die Produktionsflexibilität erhöht sich, eine schnelle Umstellung auf die Produktion neuer Produkte wird möglich und die Anlagenauslastung steigt.
Durch die Konzentration technologisch homogener Produkte werden die Kosten für den Material- und Produkttransport gesenkt, die Dauer des Produktionszyklus verkürzt, das Produktionsmanagement vereinfacht und der Bedarf an Produktionsfläche reduziert.
Prinzip Spezialisierungen basiert auf der Begrenzung der Vielfalt der Elemente des Produktionsprozesses. Die Umsetzung dieses Prinzips besteht darin, jedem Arbeitsplatz und jeder Abteilung ein streng begrenztes Spektrum an Arbeiten, Vorgängen, Teilen oder Produkten zuzuordnen. Im Gegensatz zum Spezialisierungsprinzip geht das Universalisierungsprinzip von einer Produktionsorganisation aus, bei der jeder Arbeitsplatz bzw. jede Produktionseinheit mit der Herstellung von Teilen und Produkten verschiedenster Art oder der Durchführung heterogener Produktionsvorgänge beschäftigt ist.
Der Spezialisierungsgrad der Arbeitsplätze wird durch einen speziellen Indikator bestimmt – den BetrZU z.o, die durch die Anzahl der über einen bestimmten Zeitraum am Arbeitsplatz durchgeführten Detailoperationen gekennzeichnet ist. Ja, wenn ZU z.o = 1 gibt es eine enge Spezialisierung von Berufen, bei der eine Detailarbeit am Arbeitsplatz im Laufe eines Monats oder Quartals ausgeführt wird.
Die Art der Spezialisierung von Abteilungen und Stellen wird maßgeblich durch das Produktionsvolumen gleichnamiger Teile bestimmt. Nein Höchststufe Die Spezialisierung wird durch die Herstellung eines Produkttyps erreicht. Das typischste Beispiel für hochspezialisierte Industrien sind Fabriken zur Herstellung von Traktoren, Fernsehern und Autos. Durch die Vergrößerung des Produktionsspektrums verringert sich der Spezialisierungsgrad.
Ein hoher Spezialisierungsgrad von Abteilungen und Arbeitsplätzen trägt zur Steigerung der Arbeitsproduktivität aufgrund der Entwicklung der Arbeitsfähigkeiten der Arbeitnehmer, der Möglichkeit der technischen Ausstattung der Arbeitskräfte und der Minimierung der Kosten für die Neukonfiguration von Maschinen und Linien bei. Gleichzeitig verringert eine enge Spezialisierung die erforderlichen Qualifikationen der Arbeitnehmer, führt zu Monotonie der Arbeit und führt dadurch zu einer schnellen Ermüdung der Arbeitnehmer und schränkt ihre Initiative ein.
Unter modernen Bedingungen gibt es eine zunehmende Tendenz zur Universalisierung der Produktion, die durch die Anforderungen des wissenschaftlichen und technischen Fortschritts zur Erweiterung der Produktpalette, das Aufkommen multifunktionaler Geräte und die Aufgaben der Verbesserung der Arbeitsorganisation in der Produktion bestimmt wird Richtung der Erweiterung der Arbeitsfunktionen des Arbeitnehmers.
Prinzip Verhältnismäßigkeit besteht in einer natürlichen Kombination einzelner Elemente des Produktionsprozesses, die sich in einem bestimmten quantitativen Verhältnis zwischen ihnen ausdrückt. Proportionalität der Produktionskapazität setzt also die Gleichheit der Standortkapazitäten oder der Ausrüstungsauslastungsfaktoren voraus. Dabei entspricht der Durchsatz der Beschaffungswerkstätten dem Bedarf an Rohlingen in den mechanischen Werkstätten und der Durchsatz dieser Werkstätten entspricht dem Bedarf der Montagewerkstatt an den benötigten Teilen. Dies beinhaltet die Anforderung, in jeder Werkstatt über Ausrüstung, Platz und Arbeitskräfte in solchen Mengen zu verfügen, dass der normale Betrieb aller Abteilungen des Unternehmens gewährleistet ist. Zwischen der Hauptproduktion einerseits und den Hilfs- und Serviceeinheiten andererseits sollte das gleiche Durchsatzverhältnis bestehen.
Ein Verstoß gegen den Grundsatz der Verhältnismäßigkeit führt zu Ungleichgewichten, zur Entstehung von Produktionsengpässen, wodurch sich der Einsatz von Ausrüstung und Arbeitskräften verschlechtert, die Dauer des Produktionszyklus zunimmt und Rückstände zunehmen.
Die Verhältnismäßigkeit von Arbeitskräften, Raum und Ausrüstung wird bereits bei der Unternehmensplanung festgestellt und dann bei der Entwicklung jährlicher Produktionspläne durch sogenannte volumetrische Berechnungen geklärt – bei der Ermittlung von Kapazität, Mitarbeiterzahl und Materialbedarf. Proportionen werden auf der Grundlage eines Systems von Standards und Normen festgelegt, die die Anzahl der gegenseitigen Verbindungen zwischen verschiedenen Elementen des Produktionsprozesses bestimmen.
Der Grundsatz der Verhältnismäßigkeit beinhaltet die gleichzeitige Durchführung einzelner Vorgänge oder Teile des Produktionsprozesses. Ihr liegt die These zugrunde, dass Teile eines zerlegten Produktionsprozesses zeitlich zusammengeführt und gleichzeitig durchgeführt werden müssen.
Der Produktionsprozess einer Maschine besteht aus einer Vielzahl von Arbeitsgängen. Es liegt auf der Hand, dass die sequentielle Ausführung nacheinander zu einer Verlängerung des Produktionszyklus führen würde. Daher müssen einzelne Teile des Produktherstellungsprozesses parallel durchgeführt werden.
Parallelität wird erreicht: bei der Bearbeitung eines Teils auf einer Maschine mit mehreren Werkzeugen; gleichzeitige Bearbeitung verschiedene Teile eine Charge für einen bestimmten Vorgang an mehreren Arbeitsplätzen; gleichzeitige Bearbeitung gleicher Teile in verschiedenen Arbeitsgängen an mehreren Arbeitsplätzen; gleichzeitige Herstellung verschiedener Teile desselben Produkts an verschiedenen Arbeitsplätzen. Die Einhaltung des Parallelitätsprinzips führt zu einer Verkürzung der Dauer des Produktionszyklus und der Legezeit der Teile, wodurch Arbeitszeit gespart wird.
Unter Geradheit das Prinzip der Organisation des Produktionsprozesses verstehen, nach dem alle Phasen und Vorgänge des Produktionsprozesses unter bestimmten Bedingungen durchgeführt werden kürzester Weg Gegenstand der Arbeit vom Beginn des Prozesses bis zu seinem Ende. Das Prinzip der Direktströmung muss gewährleistet sein geradlinige Bewegung Arbeitsgegenstände im technologischen Prozess, wodurch verschiedene Arten von Schleifen und Rückbewegungen vermieden werden.
Eine vollständige Geradlinigkeit kann durch die räumliche Anordnung von Vorgängen und Teilen des Produktionsprozesses in der Reihenfolge der technologischen Vorgänge erreicht werden. Bei der Gestaltung von Betrieben ist außerdem darauf zu achten, dass Werkstätten und Dienstleistungen in einer Reihenfolge angeordnet sind, die einen Mindestabstand zwischen benachbarten Abteilungen gewährleistet. Sie sollten sich bemühen, sicherzustellen, dass Teile und Baugruppen verschiedener Produkte die gleiche oder eine ähnliche Abfolge von Phasen und Vorgängen im Produktionsprozess aufweisen. Bei der Umsetzung des Direktflussprinzips stellt sich auch das Problem der optimalen Anordnung von Geräten und Arbeitsplätzen.
Das Prinzip des Direktflusses manifestiert sich in stärkerem Maße in den Bedingungen der kontinuierlichen Produktion, bei der Schaffung fachbezogener Werkstätten und Abschnitte.
Die Einhaltung linearer Anforderungen führt zu einer Rationalisierung der Frachtströme, einer Reduzierung des Frachtumschlags und einer Reduzierung der Kosten für den Transport von Materialien, Teilen und Fertigprodukten.
Prinzip Rhythmik bedeutet, dass alle einzelnen Produktionsprozesse und ein einzelner Prozess zur Herstellung eines bestimmten Produkttyps nach festgelegten Zeiträumen wiederholt werden. Unterscheiden Sie zwischen Produktions-, Arbeits- und Produktionsrhythmus.
Der Produktionsrhythmus ist die Freisetzung gleicher oder gleichmäßig steigender (abnehmender) Produktmengen in gleichen Zeitabständen. Rhythmizität der Arbeit ist die Fertigstellung gleicher Arbeitsmengen (in Menge und Zusammensetzung) in gleichen Zeitintervallen. Rhythmische Produktion bedeutet die Aufrechterhaltung eines rhythmischen Outputs und Arbeitsrhythmus.
Rhythmisches Arbeiten ohne Ruckeln und Stürmen ist die Grundlage für eine Steigerung der Arbeitsproduktivität, eine optimale Auslastung der Geräte, eine vollständige Auslastung des Personals und eine Garantie für qualitativ hochwertige Produkte. Der reibungslose Betrieb eines Unternehmens hängt von einer Reihe von Bedingungen ab. Die Sicherstellung des Rhythmus ist eine komplexe Aufgabe, die eine Verbesserung der gesamten Produktionsorganisation im Unternehmen erfordert. Von größter Bedeutung sind die korrekte Organisation der betrieblichen Produktionsplanung, die Einhaltung der Verhältnismäßigkeit der Produktionskapazitäten, die Verbesserung der Produktionsstruktur, die ordnungsgemäße Organisation der Logistik und die technische Aufrechterhaltung der Produktionsprozesse.
Prinzip Kontinuität wird in solchen Organisationsformen des Produktionsprozesses umgesetzt, in denen alle seine Vorgänge kontinuierlich und ohne Unterbrechungen durchgeführt werden und alle Arbeitsgegenstände kontinuierlich von Betrieb zu Betrieb wechseln.
Das Prinzip der Kontinuität des Produktionsprozesses wird in automatischen und kontinuierlichen Produktionslinien vollständig umgesetzt, auf denen Arbeitsgegenstände hergestellt oder montiert werden, wobei Vorgänge von gleicher oder mehrfacher Dauer im Linienzyklus durchgeführt werden.
Im Maschinenbau überwiegen diskrete technologische Prozesse, daher ist eine Produktion mit einem hohen Grad an Synchronisation der Betriebsdauer hier nicht vorherrschend.
Die intermittierende Bewegung von Arbeitsgegenständen ist mit Pausen verbunden, die durch das Verlegen von Teilen in jedem Betrieb, zwischen Betrieben, Abschnitten und Werkstätten entstehen. Deshalb erfordert die Umsetzung des Kontinuitätsprinzips die Beseitigung oder Minimierung von Unterbrechungen. Die Lösung eines solchen Problems kann auf der Grundlage der Einhaltung der Grundsätze der Verhältnismäßigkeit und des Rhythmus erreicht werden; Organisation der parallelen Produktion von Teilen einer Charge oder verschiedener Teile eines Produkts; Schaffung solcher Organisationsformen von Produktionsprozessen, bei denen die Startzeit der Herstellung von Teilen in einem bestimmten Vorgang und die Endzeit des vorherigen Vorgangs synchronisiert werden usw.
Ein Verstoß gegen den Kontinuitätsgrundsatz führt in der Regel zu Arbeitsunterbrechungen (Ausfallzeiten von Arbeitskräften und Geräten), was zu einer Verlängerung der Dauer des Produktionszyklus und des Umfangs der laufenden Arbeiten führt.
Die Prinzipien der Produktionsorganisation wirken in der Praxis nicht isoliert, sondern sind in jedem Produktionsprozess eng miteinander verknüpft. Beim Studium der Organisationsprinzipien sollten Sie darauf achten Paarcharakter einige von ihnen, ihre Wechselbeziehung, gehen in ihr Gegenteil über (Differenzierung und Kombination, Spezialisierung und Universalisierung). Die Organisationsprinzipien entwickeln sich ungleichmäßig: Hin und wieder tritt ein Prinzip in den Vordergrund oder erlangt eine untergeordnete Bedeutung. Damit gehört die enge Spezialisierung der Berufe der Vergangenheit an, sie werden immer universeller. Das Prinzip der Differenzierung wird zunehmend durch das Prinzip der Kombination ersetzt, dessen Einsatz es ermöglicht, einen Produktionsprozess auf der Grundlage eines einzigen Flusses aufzubauen. Gleichzeitig nimmt unter Bedingungen der Automatisierung die Bedeutung der Grundsätze der Verhältnismäßigkeit, Kontinuität und Geradlinigkeit zu.
Der Grad der Umsetzung der Grundsätze der Produktionsorganisation hat eine quantitative Dimension. Daher müssen zusätzlich zu den aktuellen Methoden der Produktionsanalyse Formen und Methoden zur Analyse des Zustands der Produktionsorganisation und zur Umsetzung ihrer wissenschaftlichen Grundsätze entwickelt und in der Praxis angewendet werden. Methoden zur Berechnung des Umsetzungsgrades bestimmter Prinzipien der Organisation von Produktionsprozessen werden im Kapitel angegeben. 20.
Die Einhaltung der Grundsätze der Organisation von Produktionsprozessen ist von großer praktischer Bedeutung. Die Umsetzung dieser Grundsätze liegt in der Verantwortung aller Ebenen des Produktionsmanagements.
10.3. Räumliche Organisation von Produktionsprozessen
Produktionsstruktur des Unternehmens. Die räumliche Zusammenführung von Teilen des Produktionsprozesses wird durch die Produktionsstruktur des Unternehmens sichergestellt. Unter der Produktionsstruktur versteht man die Gesamtheit der dazu gehörenden Produktionseinheiten eines Unternehmens sowie die Formen der Beziehungen zwischen ihnen. Unter modernen Bedingungen kann der Produktionsprozess in zwei Varianten betrachtet werden:
- als Prozess der materiellen Produktion mit dem Endergebnis – kommerziellen Produkten;
- als Prozess der Designproduktion mit dem Endergebnis – einem wissenschaftlich-technischen Produkt.
Die Art der Produktionsstruktur eines Unternehmens hängt von der Art seiner Tätigkeiten ab, von denen die wichtigsten die folgenden sind: Forschung, Produktion, Forschung und Produktion, Produktion und Technik, Management und Wirtschaft.
Die Priorität der jeweiligen Tätigkeitsarten bestimmt die Struktur des Unternehmens, den Anteil der wissenschaftlichen, technischen und Produktionsabteilungen, das Verhältnis der Zahl der Arbeiter und Ingenieure.
Die Zusammensetzung der Abteilungen eines auf Produktionstätigkeiten spezialisierten Unternehmens wird durch die Gestaltungsmerkmale der hergestellten Produkte und der Technologie ihrer Herstellung, den Produktionsumfang, die Spezialisierung des Unternehmens und die bestehenden Kooperationsbeziehungen bestimmt. In Abb. Abbildung 10.1 zeigt ein Diagramm der Beziehungen zwischen Faktoren, die die Produktionsstruktur eines Unternehmens bestimmen.
Reis. 10.1. Schema der Beziehungen zwischen Faktoren, die die Produktionsstruktur eines Unternehmens bestimmen
Unter modernen Bedingungen hat die Eigentumsform einen großen Einfluss auf die Unternehmensstruktur. Der Übergang vom Staat zu anderen Eigentumsformen – Privateigentum, Aktienbesitz, Pacht – führt in der Regel zu einer Reduzierung unnötiger Verbindungen und Strukturen, der Zahl der Kontrollapparate und reduziert Doppelarbeit.
Derzeit sind verschiedene Formen der Unternehmensorganisation weit verbreitet; Es gibt kleine, mittlere und große Unternehmen, deren Produktionsstruktur jeweils entsprechende Merkmale aufweist.
Die Produktionsstruktur eines Kleinunternehmens ist einfach. In der Regel verfügt es über minimale oder gar keine internen strukturellen Produktionseinheiten. In kleinen Unternehmen ist der Führungsapparat unbedeutend, eine Kombination von Führungsfunktionen ist weit verbreitet.
Bei der Struktur mittelständischer Unternehmen handelt es sich um die Zuteilung von Werkstätten, im Falle einer Nicht-Werkstatt-Struktur von Abteilungen. Hier wird bereits das für die Funktionsfähigkeit des Unternehmens notwendige Minimum geschaffen, eigene Hilfs- und Serviceeinheiten, Abteilungen und Dienste des Führungsapparates.
Große Unternehmen der verarbeitenden Industrie verfügen über ein umfassendes Spektrum an Produktions-, Service- und Verwaltungsabteilungen.
Basierend auf der Produktionsstruktur wird ein Masterplan für das Unternehmen entwickelt. Der Masterplan bezieht sich auf die räumliche Anordnung aller Werkstätten und Dienstleistungen sowie Transportwege und Kommunikation auf dem Territorium des Unternehmens. Bei der Entwicklung eines Masterplans wird der direkte Fluss der Materialflüsse sichergestellt. Werkstätten müssen entsprechend der Reihenfolge des Produktionsprozesses angeordnet sein. Verbundene Dienste und Werkstätten müssen in unmittelbarer Nähe liegen.
Entwicklung der Produktionsstruktur von Verbänden. Die Produktionsstrukturen von Verbänden unter modernen Bedingungen unterliegen erheblichen Veränderungen. Produktionsverbände im verarbeitenden Gewerbe, insbesondere im Maschinenbau, zeichnen sich durch folgende Bereiche zur Verbesserung der Produktionsstrukturen aus:
- Konzentration der Produktion homogener Produkte oder der Ausführung ähnlicher Arbeiten in einzelnen Fachabteilungen des Vereins;
- Vertiefung der Spezialisierung struktureller Unternehmensbereiche - Produktionsstätten, Werkstätten, Niederlassungen;
- Integration in einheitliche Wissenschafts- und Produktionskomplexe der Arbeit an der Schaffung neuer Produkttypen, ihrer Entwicklung in der Produktion und der Organisation der Produktion in für den Verbraucher notwendigen Mengen;
- Zerstreuung der Produktion durch die Gründung hochspezialisierter Unternehmen unterschiedlicher Größe innerhalb des Verbandes;
- Überwindung der Segmentierung beim Aufbau von Produktionsprozessen und Schaffung einheitlicher Produktherstellungsabläufe ohne Trennung von Werkstätten und Abschnitten;
- Universalisierung der Produktion, die in der Herstellung von Produkten mit unterschiedlichen Zwecken besteht, die aus in Design und Technologie homogenen Einheiten und Teilen zusammengesetzt sind, sowie in der Organisation der Produktion verwandter Produkte;
- breite Entwicklung der horizontalen Zusammenarbeit zwischen Unternehmen, die verschiedenen Verbänden angehören, um die Produktionskosten durch Erhöhung des Produktionsumfangs ähnlicher Produkte und vollständige Auslastung der Kapazitäten zu senken.
Durch die Gründung und Entwicklung großer Verbände entstand eine neue Form der Produktionsstruktur, die durch die Zuteilung spezialisierter Produktionsstätten optimaler Größe gekennzeichnet ist, die auf dem Prinzip der Technologie- und Fachspezialisierung basieren. Diese Struktur sorgt auch für eine maximale Konzentration der Beschaffungs-, Hilfs- und Serviceprozesse. Die neue Form der Produktionsstruktur wurde Multiproduktion genannt. In den 80er Jahren fand es breite Anwendung in der Automobil-, Elektro- und anderen Industrie.
Der Automobilproduktionsverband Nischni Nowgorod beispielsweise umfasst ein Mutterunternehmen und sieben Zweigwerke. Das Mutterunternehmen umfasst zehn spezialisierte Produktionsstätten: Lkw, Pkw, Motoren, Lkw-Achsen, Metallurgie, Schmieden und Federn, Werkzeuge usw. Jede dieser Produktionen vereint eine Gruppe von Haupt- und Nebenwerkstätten, verfügt über eine gewisse Unabhängigkeit und pflegt enge Beziehungen mit anderen Unternehmensbereichen und genießt die für die Struktureinheiten des Vereins begründeten Rechte. Eine typische Produktionsstruktur ist in Abb. dargestellt. 10.2.
Im Volzhsky-Automobilwerk wurde eine Mehrproduktionsstruktur auf einem höheren Qualitätsniveau implementiert. Die Automobilproduktion konzentriert sich hier auf vier Hauptindustrien: Metallurgie, Pressen, mechanische Montage sowie Montage und Schmieden. Darüber hinaus wurden Hilfsproduktionsanlagen zugewiesen. Jeder von ihnen ist ein eigenständiges Werk mit einem geschlossenen Produktionskreislauf. Die Produktion umfasst Werkstätten. Aber die Werkstätten bei VAZ haben erhebliche Veränderungen erfahren. Sie werden von den Sorgen um die Sicherstellung der Produktion, Reparatur und Wartung von Geräten, Wartung und Reinigung von Räumlichkeiten usw. befreit Produktionswerkstatt VAZ bleibt nur noch die Aufgabe, die ihm zugewiesenen Produkte qualitativ hochwertig und termingerecht zu produzieren. Die Werkstattverwaltungsstruktur wird so weit wie möglich vereinfacht. Das sind der Werkstattleiter, seine beiden Schichtstellvertreter, Abteilungsleiter, Vorarbeiter und Vorarbeiter. Sämtliche Aufgaben der Versorgung, Produktionsvorbereitung und Instandhaltung werden zentral durch den Produktionsmanagementapparat gelöst.
Reis. 10.2. Typische Produktionsstruktur
In jeder Produktionsabteilung wurden folgende Abteilungen geschaffen: Design und Technologie, Design, Werkzeuge und Ausrüstung, Analyse und Planung von Gerätereparaturen. Hier wurden einheitliche Dienste für die Einsatzplanung, Logistik, Arbeitsorganisation und Löhne etabliert.
Die Produktion umfasst große Fachwerkstätten: Reparatur, Herstellung und Reparatur von Geräten, Transport- und Lagervorgänge, Reinigung von Räumlichkeiten und andere. Durch die Schaffung leistungsstarker Ingenieurdienstleistungen und Produktionsabteilungen in der Produktion, die jeweils die ihnen in ihrem Bereich übertragenen Aufgaben vollständig lösen, konnten auf grundlegend neuer Basis normale Bedingungen für den effektiven Betrieb der Hauptproduktionsabteilungen geschaffen werden.
Die Organisation der Workshops und Sektionen basiert auf den Prinzipien der Konzentration und Spezialisierung. Die Spezialisierung von Werkstätten und Produktionsbereichen kann nach Art der Arbeit – technologische Spezialisierung oder nach Art des hergestellten Produkts – Fachspezialisierung erfolgen. Beispiele für Produktionseinheiten mit technologischer Spezialisierung in einem Maschinenbauunternehmen sind Gießerei, thermische oder galvanische Werkstätten, Dreh- und Schleifabteilungen in einer mechanischen Werkstatt; Fachliche Spezialisierung - Karosserieteilewerkstatt, Wellenteilwerkstatt, Getriebefertigungswerkstatt usw.
Wenn ein vollständiger Zyklus der Herstellung eines Produkts oder Teils innerhalb einer Werkstatt oder eines Standorts durchgeführt wird, wird diese Abteilung als fachgebietsgeschlossen bezeichnet.
Bei der Organisation von Workshops und Sektionen ist es notwendig, die Vor- und Nachteile aller Spezialisierungsarten sorgfältig zu analysieren. Durch die technologische Spezialisierung wird eine hohe Anlagenauslastung sichergestellt, eine hohe Produktionsflexibilität bei der Entwicklung neuer Produkte und beim Wechsel von Produktionsanlagen erreicht. Gleichzeitig wird die betriebliche Produktionsplanung schwieriger, der Produktionszyklus verlängert sich und die Verantwortung für die Produktqualität sinkt.
Der Einsatz der Fachspezialisierung, die die Konzentration aller Arbeiten an der Herstellung eines Teils oder Produkts innerhalb einer Werkstatt oder eines Bereichs ermöglicht, erhöht die Verantwortung der Ausführenden für die Qualität der Produkte und die Erledigung der Aufgaben. Die Fachspezialisierung schafft die Voraussetzungen für die Organisation einer kontinuierlichen und automatisierten Produktion, gewährleistet die Umsetzung des Direktflussprinzips und vereinfacht Planung und Abrechnung. Allerdings ist es nicht immer möglich, eine vollständige Auslastung der Anlagen zu erreichen; die Umstrukturierung der Produktion zur Herstellung neuer Produkte erfordert hohe Kosten.
Fachlich geschlossene Werkstätten und Bereiche haben auch erhebliche wirtschaftliche Vorteile, deren Organisation es ermöglicht, die Dauer des Produktionszyklus für die Herstellung von Produkten durch den vollständigen oder teilweisen Wegfall von Gegen- oder Altersbewegungen zu verkürzen und zu vereinfachen das Planungssystem und die operative Steuerung des Produktionsfortschritts. Die praktische Erfahrung in- und ausländischer Unternehmen ermöglicht es uns, die folgende Gruppierung von Regeln anzugeben, die bei der Entscheidung über die Anwendung des Themas oder des technologischen Prinzips beim Bau von Werkstätten und Abteilungen beachtet werden sollten.
Thema Es wird empfohlen, das Prinzip in folgenden Fällen anzuwenden: bei der Herstellung von einem oder zwei Standardprodukten, mit einem großen Volumen und einem hohen Maß an Stabilität bei der Herstellung von Produkten, mit der Möglichkeit eines guten Gleichgewichts von Ausrüstung und Arbeit, mit a minimale Kontrollvorgänge und geringe Anzahl von Umstellungen; technologisch- bei der Herstellung einer großen Produktpalette mit relativ geringen Serienstückzahlen, der Unmöglichkeit, Ausrüstung und Arbeit in Einklang zu bringen, mit einer großen Anzahl von Kontrollvorgängen und einer erheblichen Anzahl von Umrüstungen.
Organisation von Produktionsstandorten. Die Organisation der Standorte wird durch die Art ihrer Spezialisierung bestimmt. Dabei geht es um die Lösung einer Vielzahl von Problemen, darunter die Auswahl der Produktionsanlagen; Berechnung der notwendigen Ausrüstung und ihrer Anordnung; Bestimmung der Größe von Chargen (Serien) von Teilen und der Häufigkeit ihrer Einführung und Produktion; Zuweisen von Arbeiten und Abläufen zu jedem Arbeitsplatz, Erstellen von Zeitplänen; Berechnung des Personalbedarfs; Entwurf eines Arbeitsplatzservicesystems. IN In letzter Zeit Es begannen sich Forschungs- und Produktionskomplexe in Verbänden zu bilden, die alle Phasen des Zyklus „Forschung – Entwicklung – Produktion“ integrierten.
Im St. Petersburger Verein „Svetlana“ wurden zum ersten Mal im Land vier Forschungs- und Produktionskomplexe geschaffen. Der Komplex ist eine einzelne Abteilung, die auf die Entwicklung und Produktion von Produkten eines bestimmten Profils spezialisiert ist. Es entsteht auf Basis der Konstruktionsbüros des Stammwerks. Neben dem Konstruktionsbüro umfasst es Hauptproduktionswerkstätten und spezialisierte Niederlassungen. Die wissenschaftlichen und Produktionsaktivitäten der Komplexe werden auf der Grundlage von Berechnungen vor Ort durchgeführt.
Forschungs- und Produktionskomplexe führen die gestalterische und technologische Vorbereitung der Produktion durch und ziehen die entsprechenden Abteilungen des Verbandes für die Durchführung von Arbeiten im Zusammenhang mit der Entwicklung neuer Produkte ein. Der Leiter des Konstruktionsbüros erhält das Recht zur ganzheitlichen Planung aller Phasen der Produktionsvorbereitung – von der Forschung bis zur Organisation der Serienproduktion. Er ist nicht nur für die Qualität und den Zeitplan der Entwicklung verantwortlich, sondern auch für die Entwicklung der Serienproduktion neuer Produkte und Produktionsaktivitäten Werkstätten und Filialen im Komplex enthalten.
Im Rahmen des Übergangs von Unternehmen zu Marktwirtschaft Es kommt zu einer Weiterentwicklung der Produktionsstruktur von Verbänden, die auf der Erhöhung der wirtschaftlichen Unabhängigkeit ihrer Mitgliedseinheiten beruht.
Als Beispiel für die Schaffung und Umsetzung einer neuen Organisationsform im Rahmen des Übergangs zum Markt kann man die Gründung einer Aktiengesellschaft nennen – eines Forschungs- und Produktionskonzerns im Energieverband (Woronesch). Auf der Grundlage der Unternehmensbereiche sind mehr als 100 unabhängige Forschungs- und Produktionskomplexe, Verbände und Unternehmen der ersten Ebene mit völliger rechtlicher Unabhängigkeit und Girokonten bei einer Geschäftsbank entstanden. Bei der Gründung unabhängiger Vereine und Unternehmen kamen zum Einsatz: verschiedene Eigentumsformen (Staat, Miete, gemischt, Aktiengesellschaft, Genossenschaft); vielfältige Organisationsstrukturen unabhängiger Unternehmen und Verbände, deren Zahl zwischen 3 und 2350 Personen variiert; vielfältige Tätigkeiten (Forschung und Produktion, Organisation und Wirtschaft, Produktion und Technik).
Der Konzern verfügt über 20 fachspezifische und funktionale Forschungs- und Produktionskomplexe, die Forschungs-, Design-, Technologieabteilungen und Produktionsanlagen vereinen und sich auf die Entwicklung und Produktion bestimmter Produkttypen oder die Durchführung technologisch homogener Arbeiten spezialisiert haben. Diese Komplexe entstanden durch die Reform von Pilot- und Serienanlagen und auf der Grundlage eines Forschungsinstituts. Je nach Anzahl und Umfang der Arbeit fungieren sie als Vereine erster Ebene, Betriebe oder Kleinbetriebe.
Forschungs- und Produktionskomplexe konnten ihre Vorteile während der Umstellungszeit unter den Bedingungen einer starken Änderung der Produktpalette voll ausspielen. Nach der Erlangung der Unabhängigkeit gründeten die Unternehmen freiwillig Verbände der ersten Ebene – Forschungs- und Produktionskomplexe oder Unternehmen – und gründeten einen Konzern, der gemäß der Charta zehn Hauptfunktionen zentralisierte. Das höchste Leitungsorgan des Konzerns ist die Gesellschafterversammlung. Die Koordinierung der Arbeiten zur Wahrnehmung zentraler Funktionen erfolgt durch den Vorstand und die Funktionsabteilungen des Konzerns unter Bedingungen völliger Selbstversorgung. Auch die Bereiche, die Service- und Supportfunktionen wahrnehmen, arbeiten auf vertraglicher Basis und verfügen über völlige rechtliche und wirtschaftliche Unabhängigkeit.
In Abb. dargestellt. 10.3 und die „zirkuläre“ Führungsstruktur des Konzerns entsprechen den Anforderungen der Gesetzgebung der Russischen Föderation. Der Vorstand koordiniert die zentralen Funktionen des Konzerns im Rahmen der Satzung nach der Idee des Runden Tisches.
Das zirkuläre (im Gegensatz zum bestehenden vertikalen) System der Organisation und des Produktionsmanagements basiert auf folgenden Grundsätzen:
Reis. 10.3. Zirkuläre Managementstruktur des Energia-Konzerns
- über den freiwilligen Zusammenschluss von Unternehmensaktionären zu gemeinsamen Aktivitäten, um durch den Verkauf von Produkten und Dienstleistungen auf einem wettbewerbsorientierten Markt maximale und stabile Gewinne zu erzielen und so die sozialen und wirtschaftlichen Interessen der Aktionäre zu befriedigen;
- freiwillige Zentralisierung eines Teils der Funktionen von Unternehmen bei der Organisation und Verwaltung der Produktion, verankert in der Satzung der Aktiengesellschaft;
- Kombination der Vorteile eines großen Unternehmens aufgrund von Spezialisierung, Zusammenarbeit und Produktionsumfang mit den Vorteilen kleiner Unternehmensformen und Motivation der Mitarbeiter durch Eigentumsbesitz;
- ein System technisch miteinander verbundener fachlicher und funktionaler Wissenschafts- und Produktionskomplexe unter Berücksichtigung der Vorteile von Spezialisierung und Zusammenarbeit;
- ein System vertraglicher Beziehungen zwischen Forschungs- und Produktionskomplexen und Unternehmen, unterstützt durch ein System zur Befriedigung selbsttragender Ansprüche, einschließlich der Regulierung des Lohnfonds;
- Verlagerung des Zentrums der aktuellen Arbeit zur Organisation und Verwaltung der Produktion von der höchsten Ebene vertikal auf die Ebene der Wissenschafts- und Produktionskomplexe und unabhängigen Unternehmen horizontal auf vertraglicher Basis mit Konzentration der Bemühungen der Geschäftsleitung auf vielversprechende Themen;
- Umsetzung der Wirtschaftsbeziehungen zwischen Unternehmen durch eine Geschäftsbank und ein Zentrum für interne Abrechnungen in relevanten Bereichen;
- Erhöhung der Garantien zur Lösung sozialer Probleme und zum Schutz sowohl unabhängiger Unternehmen als auch aller Aktionäre;
- Kombination und Entwicklung verschiedener Eigentumsformen auf der Ebene des Konzerns und unabhängiger Vereine und Unternehmen;
- Ablehnung der dominanten Rolle der höchsten Leitungsorgane mit der Umwandlung der Funktionen der Leitung und Koordinierung der Produktion in eine der Tätigkeitsarten der Aktionäre;
- Entwicklung eines Mechanismus, um die gegenseitigen Interessen unabhängiger Unternehmen und des Konzerns als Ganzes zu vereinen und die Gefahr eines Bruchs aufgrund der Zentrifugalkräfte des technologischen Prinzips beim Aufbau der Produktionsorganisation zu verhindern.
Die zirkuläre Struktur sorgt für eine grundlegende Veränderung der Aktivitäten fachspezifischer Forschungs- und Produktionskomplexe, die die führende Rolle bei der Planung und Sicherstellung der horizontalen Vernetzung der Aktivitäten funktionaler Forschungs- und Produktionskomplexe und Unternehmen auf vertraglicher Basis gemäß ihrer Nomenklatur übernehmen , unter Berücksichtigung von Marktveränderungen.
Die Planungs- und Versandabteilung innerhalb des Unternehmens Pribyl wurde umgestaltet und ein erheblicher Teil ihrer Funktionen und ihres Personals in fachspezifische Forschungs- und Produktionskomplexe verlagert. Die Aufmerksamkeit dieses Dienstes liegt auf strategischen Aufgaben und der Koordination der Arbeit von Komplexen und Unternehmen.
Concern Energia durchlief den Privatisierungsprozess durch Leasing und Korporatisierung, erhielt eine Eigentumsbescheinigung für das Eigentum und erhielt den Status eines Bundesforschungs- und Produktionszentrums.
10.4. Organisation von Produktionsabläufen im Zeitverlauf
Um ein rationelles Zusammenspiel aller Elemente des Produktionsprozesses zu gewährleisten und die geleistete Arbeit zeitlich und räumlich zu rationalisieren, ist es notwendig, einen Produktionszyklus des Produkts zu bilden.
Der Produktionszyklus ist ein Komplex von Grund-, Hilfs- und Serviceprozessen, die zeitlich auf eine bestimmte Weise organisiert sind und für die Herstellung eines bestimmten Produkttyps erforderlich sind. Das wichtigste Merkmal des Produktionszyklus ist seine Dauer.
Produktionszykluszeit- Hierbei handelt es sich um einen kalendarischen Zeitraum, in dem ein Material, Werkstück oder ein anderer verarbeiteter Gegenstand alle Vorgänge des Produktionsprozesses oder einen bestimmten Teil davon durchläuft und in fertige Produkte umgewandelt wird. Die Dauer des Zyklus wird in Kalendertagen oder Stunden ausgedrückt. Struktur des Produktionszyklus beinhaltet Arbeitszeit und Pausenzeit. Während der Arbeitszeit werden die eigentlichen technologischen Arbeiten sowie Vor- und Abschlussarbeiten durchgeführt. Zur Arbeitszeit zählen auch die Dauer von Kontroll- und Transportvorgängen sowie die Zeit natürlicher Prozesse. Die Zeit der Pausen wird durch das Arbeitsregime, die betriebsübergreifende Teileverfolgung und Mängel in der Arbeits- und Produktionsorganisation bestimmt.
Die Interoperationswartezeit wird durch Unterbrechungen bei der Chargen-, Warte- und Personalbesetzung bestimmt. Chargenbrüche treten bei der Herstellung von Produkten in Chargen auf und sind darauf zurückzuführen, dass die verarbeiteten Produkte so lange liegen bleiben, bis die gesamte Charge diesen Vorgang durchlaufen hat. In diesem Fall wird davon ausgegangen, dass es sich bei einer Produktionscharge um eine Gruppe von Produkten mit demselben Namen und derselben Standardgröße handelt, die innerhalb einer bestimmten Zeit mit derselben Vorbereitungs- und Endzeit in Produktion gehen. Wartepausen werden durch die uneinheitliche Dauer zweier benachbarter Vorgänge des technologischen Prozesses verursacht, und Kommissionierpausen entstehen durch die Notwendigkeit, zu warten, bis alle Rohlinge, Teile oder Baugruppen eines Produktsatzes hergestellt sind. Kommissionierunterbrechungen treten beim Übergang von einer Phase des Produktionsprozesses zu einer anderen auf.
In seiner allgemeinsten Form die Dauer des Produktionszyklus T q wird durch die Formel ausgedrückt
T ts = T t + Tn –3 + T e + T k + T tr + T Mo + T pr, (10.1)
Wo T t ist die Zeit der technologischen Operationen; Tn–3 – Zeit der Vorbereitungs- und Abschlussarbeiten; T e ist die Zeit natürlicher Prozesse; T k ist die Zeit der Kontrollvorgänge; T tr – Zeitpunkt des Transports von Arbeitsgegenständen; T Mo – Zeit der interoperativen Schlafenszeit (Pausen innerhalb der Schicht); T pr – Zeit der arbeitsplanbedingten Pausen.
Die Dauer der technologischen Operationen sowie der vorbereitenden und abschließenden Arbeiten bilden zusammen den Betriebszyklus T Polizist.
Betriebszyklus- Dies ist die Dauer des abgeschlossenen Teils des technologischen Prozesses, der an einem Arbeitsplatz durchgeführt wird.
Methoden zur Berechnung der Dauer des Produktionszyklus. Es ist zu unterscheiden zwischen dem Produktionszyklus einzelner Teile und dem Produktionszyklus einer Baugruppe oder eines Produkts als Ganzes. Der Produktionszyklus eines Teils wird üblicherweise als einfach bezeichnet, und der Produktionszyklus eines Produkts oder einer Baugruppe wird als komplex bezeichnet. Der Zyklus kann ein- oder mehrbetrieben sein. Die Zykluszeit eines Prozesses mit mehreren Arbeitsgängen hängt von der Art der Übergabe von Teilen von Arbeitsgang zu Arbeitsgang ab. Es gibt drei Arten der Bewegung von Arbeitsgegenständen im Prozess ihrer Herstellung: sequentiell, parallel und parallel-sequentiell.
Bei sequentielle Art der Bewegung die gesamte Teilecharge wird an den Folgevorgang übergeben, nachdem die Bearbeitung aller Teile im vorherigen Vorgang abgeschlossen ist. Die Vorteile dieser Methode sind das Fehlen von Betriebsunterbrechungen für Geräte und Arbeiter bei jedem Vorgang sowie die Möglichkeit ihrer hohen Belastung während der Schicht. Bei einer solchen Arbeitsorganisation ist der Produktionszyklus jedoch der größte, was sich negativ auf die technischen und wirtschaftlichen Indikatoren der Werkstatt oder des Unternehmens auswirkt.
Bei parallele Bewegungsart Die Übergabe der Teile an den nächsten Arbeitsgang per Transportcharge erfolgt unmittelbar nach Abschluss der Bearbeitung im vorherigen Arbeitsgang. In diesem Fall ist der kürzeste Zyklus gewährleistet. Die Einsatzmöglichkeiten einer parallelen Bewegungsart sind jedoch begrenzt, da Voraussetzung für deren Umsetzung die Gleichheit oder ein Vielfaches der Operationsdauer ist. Andernfalls sind Betriebsunterbrechungen von Geräten und Arbeitern unvermeidlich.
Bei parallel-sequentielle Bewegungsart Teile werden in Transportchargen oder einzeln von Betrieb zu Betrieb transportiert. In diesem Fall kommt es zu einer teilweisen Überlappung der Ausführungszeit benachbarter Vorgänge und der gesamte Stapel wird bei jedem Vorgang ohne Unterbrechungen verarbeitet. Arbeiter und Geräte arbeiten ohne Pausen. Der Produktionszyklus ist im Vergleich zu einem parallelen länger, aber kürzer als bei der sequentiellen Bewegung von Arbeitsgegenständen.
Taktberechnung für einen einfachen Produktionsprozess. Der betriebliche Produktionszyklus einer Teilecharge mit sequentieller Bewegungsart berechnet sich wie folgt:
(10.2)
Wo N— Anzahl der Teile in der Produktionscharge, Stk.; R op ist die Anzahl der technologischen Prozessoperationen; T PC ich— Standardzeit für die Durchführung jeder Operation, min; MIT r.m. ich— die Anzahl der Arbeitsplätze, die durch die Produktion einer Charge von Teilen in jedem Arbeitsgang belegt werden.
Das Diagramm der sequentiellen Bewegungsart ist in Abb. dargestellt. 10.4, A. Anhand der im Diagramm angegebenen Daten wird der Arbeitszyklus einer Charge bestehend aus drei Teilen berechnet, die an vier Arbeitsplätzen verarbeitet werden:
T c.seq = 3 (t Stück 1 + t Stück 2 + t Stück 3 + t Stück 4) = 3 (2 + 1 + 4 + 1,5) = 25,5 min.
Formel zur Berechnung der Dauer des Arbeitszyklus bei paralleler Bewegungsart:
(10.3)
wo ist die Ausführungszeit des längsten Vorgangs im technologischen Prozess, min.
Reis. 10.4, a. Produktionszyklusplan für die sequentielle Bewegung von Teilechargen
Der Bewegungsplan einer Charge von Teilen mit paralleler Bewegung ist in Abb. dargestellt. 10,4, geb. Anhand des Diagramms können Sie die Dauer des Arbeitszyklus bei Parallelbewegung ermitteln:
T c.pair = ( T Stück 1 + T Stück 2 + T Stück 3 + T Stück 4)+ (3 – 1) T Stk. 3 = 8,5 + (3 – 1) 4 = 16,5 Min.
Reis. 10,4, geb. Produktionszyklusplan für die parallel-sequentielle Bewegung von Teilechargen
Bei einer parallel-sequentiellen Bewegungsart kommt es zu einer teilweisen Überlappung der Ausführungszeit benachbarter Vorgänge. Es gibt zwei Arten der zeitlichen Kombination benachbarter Operationen. Wenn die Ausführungszeit des nachfolgenden Vorgangs länger ist als die Ausführungszeit des vorherigen Vorgangs, kann eine parallele Art der Teilebewegung verwendet werden. Wenn die Ausführungszeit des nachfolgenden Vorgangs kürzer ist als die Ausführungszeit des vorherigen, ist eine parallel-sequentielle Bewegungsart mit der maximal möglichen zeitlichen Kombination beider Vorgänge akzeptabel. Die maximalen kombinierten Vorgänge unterscheiden sich zum Zeitpunkt der Produktion des letzten Teils (bzw. der letzten Transportcharge) beim Folgevorgang voneinander.
Ein Diagramm der parallel-sequentiellen Bewegungsart ist in Abb. dargestellt. 10.4, V. In diesem Fall ist der Betriebszyklus um den Betrag der Kombination jedes benachbarten Operationspaares kürzer als bei einer sequentiellen Bewegungsart: der erste und zweite Betrieb - AB - (3 - l) T pcs2 ; zweite und dritte Operation - VG = А¢Б¢ – (3 –1) T pcs3 ; dritte und vierte Operation – DE – (3 – 1) T pcs4 (wo T pcs3 und T pcs4 haben eine kürzere Zeit T Stk. Karton aus jedem Operationspaar).
Formeln zur Berechnung
(10.4)
Bei der Durchführung von Operationen an parallelen Arbeitsplätzen:
Reis. 10.4, c. Zeitplan der Produktionszyklen mit paralleler Bewegung von Teilechargen
Beim Umladen von Produkten in Transportchargen:
(10.5)
Wo ist die Zeit, um den kürzesten Vorgang abzuschließen?
Ein Beispiel für die Berechnung der Zyklusdauer mithilfe der Formel (10.5):
T c.p.p = 25,5 – 2 (1 + 1 + 1,5) = 18,5 min.
Der Produktionszyklus zur Herstellung einer Charge von Teilen umfasst nicht nur den Betriebszyklus, sondern auch natürliche Prozesse und Pausen, die mit dem Betriebsmodus und anderen Komponenten verbunden sind. In diesem Fall wird die Zyklusdauer für die betrachteten Bewegungsarten durch die Formeln bestimmt:
Wo R op ist die Anzahl der technologischen Operationen; MIT r.m – die Anzahl der parallelen Arbeitsplätze, die bei der Herstellung einer Charge von Teilen bei jedem Vorgang belegt sind; T mo – interoperative Wartezeit zwischen zwei Operationen, h; T cm – Dauer einer Arbeitsschicht, h; D cm - Anzahl der Schichten; ZU v.n - geplanter Koeffizient der Einhaltung von Standards im Betrieb; ZU ln ist der Koeffizient zur Umrechnung der Arbeitszeit in Kalenderzeit; T e ist die Dauer natürlicher Prozesse.
Berechnung der Zykluszeit eines komplexen Prozesses
Der Produktionszyklus eines Produkts umfasst Zyklen der Herstellung von Teilen, der Montage von Komponenten und Fertigprodukten sowie von Testvorgängen. In diesem Fall wird allgemein davon ausgegangen, dass verschiedene Teile gleichzeitig hergestellt werden. Daher umfasst der Produktionszyklus des Produkts den Zyklus des arbeitsintensivsten (führenden) Teils von denen, die an die ersten Vorgänge der Montagewerkstatt geliefert werden. Die Dauer des Produktproduktionszyklus kann mit der Formel berechnet werden
T c.p = T c.d + T c.b, (10.9)
Wo T c.d - Dauer des Produktionszyklus für die Herstellung des Hauptteils, Kalendertage. Tage; T c.b - Dauer des Produktionszyklus der Montage- und Prüfarbeiten, Kalendertage. Tage
Reis. 10.5. Zyklus eines komplexen Prozesses
Kann verwendet werden, um die Zykluszeit eines komplexen Herstellungsprozesses zu bestimmen. grafische Methode. Zu diesem Zweck wird ein zyklischer Zeitplan erstellt. Die Produktionszyklen einfacher Prozesse, die in komplexe Prozesse eingebunden sind, sind vorab festgelegt. Gemäß dem zyklischen Zeitplan wird der Zeitraum des Fortschritts einiger Prozesse durch andere analysiert und die Gesamtdauer des Zyklus eines komplexen Prozesses zur Herstellung eines Produkts oder einer Produktcharge als die größte Summe der Zyklen miteinander verbundener einfacher Prozesse bestimmt und interoperative Pausen. In Abb. Abbildung 10.5 zeigt einen zyklischen Graphen eines komplexen Prozesses. In der Grafik sind von rechts nach links im Zeitmaßstab Zyklen von Teilprozessen dargestellt, beginnend mit der Prüfung bis hin zur Fertigung der Teile.
Möglichkeiten und Bedeutung zur Gewährleistung der Kontinuität des Produktionsprozesses und zur Reduzierung der Zykluszeiten
Ein hohes Maß an Kontinuität der Produktionsprozesse und eine Verkürzung der Dauer des Produktionszyklus sind von großer wirtschaftlicher Bedeutung: Der Umfang der laufenden Arbeiten wird reduziert und der Umschlag des Betriebskapitals beschleunigt, die Nutzung von Geräten und Produktionsflächen wird verbessert und die Produktionskosten werden gesenkt. Untersuchungen, die in einer Reihe von Unternehmen in Charkow durchgeführt wurden, zeigten, dass dort, wo die durchschnittliche Produktionszykluszeit 18 Tage nicht überschreitet, jeder ausgegebene Rubel 12 % mehr Produkte liefert als in Fabriken, in denen die Zykluszeit 19–36 Tage beträgt, und 61 % mehr als in einer Fabrik, in der die Produkte einen Zyklus von mehr als 36 Tagen haben.
Die Erhöhung der Kontinuität des Produktionsprozesses und die Verkürzung der Zykluszeit werden zum einen durch die Erhöhung des technischen Niveaus der Produktion und zum anderen durch organisatorische Maßnahmen erreicht. Beide Wege sind miteinander verbunden und ergänzen sich.
Die technische Verbesserung der Produktion geht in Richtung der Einführung neuer Technologien, fortschrittlicher Ausrüstung und neuer Fahrzeuge. Dies führt zu einer Verkürzung des Produktionszyklus, indem die Arbeitsintensität der Technologie- und Kontrollvorgänge selbst verringert und die Zeit für den Transport von Arbeitsgegenständen verkürzt wird.
Zu den organisatorischen Maßnahmen gehören:
- Minimierung von Unterbrechungen, die durch Interoperationsverfolgung und Batch-Unterbrechungen verursacht werden, durch den Einsatz paralleler und parallel-sequentieller Methoden der Bewegung von Arbeitsgegenständen und Verbesserung des Planungssystems;
- Erstellen von Zeitplänen für die Kombination verschiedener Produktionsprozesse, um eine teilweise zeitliche Überschneidung der damit verbundenen Arbeiten und Vorgänge sicherzustellen;
- Reduzierung der Wartepausen durch die Erstellung optimierter Produktionspläne für Produkte und die rationelle Einführung von Teilen in die Produktion;
- die Einführung von themen- und detailspezialisierten Werkstätten und Abteilungen, deren Schaffung die Länge der Intra-Shop- und Inter-Shop-Wege verkürzt und den Zeitaufwand für den Transport reduziert.