Lean Manufacturing ist ein System der gesamten Anlagenwartung. Total Productive Maintenance – TPM
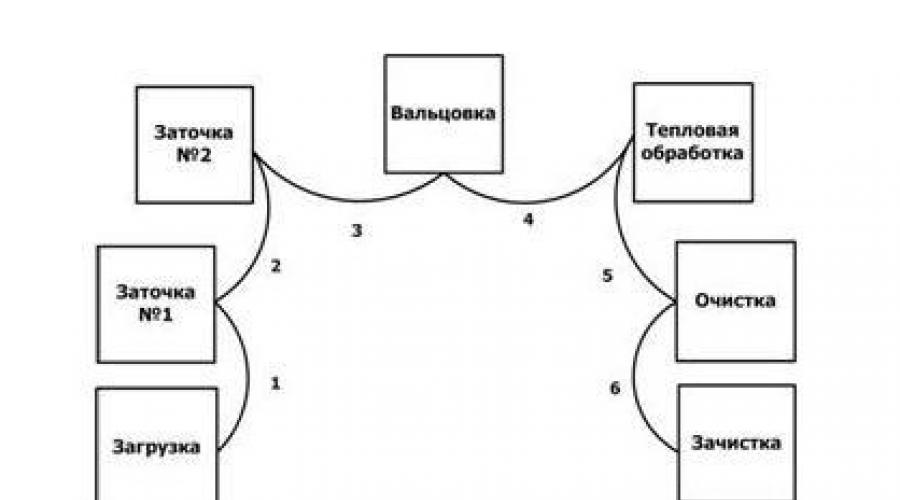
Lesen Sie auch
Das TPM-Konzept wurde Ende der 60er und Anfang der 70er Jahre in Japan bei Nippon Denso, einem Elektroausrüstungslieferanten der Toyota Corporation, entwickelt. Die berühmte Aussage des Toyota-Gründers „Stärke entsteht nicht durch Heilungsprozesse, sondern durch vorbeugende Wartung der Ausrüstung.“
TPM steht im weitesten Sinne für „Total Effective Maintenance“. In diesem Fall bezieht sich „universell“ auf das gesamte System effektive Pflege für das Gerät während seiner gesamten Lebensdauer. Dabei geht es auch um die Einbindung jedes einzelnen Mitarbeiters in den Prozess durch die Einbindung einzelner Bediener in die Instandhaltung. Darüber hinaus erfordert der Einsatz von TPM bestimmte Verpflichtungen seitens der Unternehmensleitung
Probleme, die TRM löst:
- Pannen
- Installation und Inbetriebnahme
- Leerlauf und kurze Stopps
- Geschwindigkeitsverlust
- Heirat und Nacharbeit
- Anlaufverluste
Im Total Equipment Maintenance-System geht es nicht um das Problem der Gerätestörung, sondern darum, die Wartung von Produktionsanlagen als Integration der Betriebs- und Wartungsprozesse zu verstehen. Ebenso die frühzeitige Einbindung des Wartungspersonals in die Entwicklung von Wartungsplänen und die genaue Erfassung des Gerätezustands. TPM spielt wichtige Rolle im Produktionsmanagement im Just-in-Time-System. Das Vorhandensein von Störungen führt zu Zeitverschwendung, die in der gesamten Wertschöpfungskette zunimmt.
Die Gründe für die Integration der Total Equipment Maintenance in die Lean Manufacturing (TPS)-Philosophie werden im Diagramm dargestellt.
Acht Prinzipien von TRM:
- Ständige Verbesserung
- Autonome Instandhaltung
- Planung Wartung
- Aus- und Weiterbildung: Verbesserung der Qualifikation der Mitarbeiter in der Bedienung und Wartung von Anlagen.
- Start Steuerung
- Qualitätsmanagement
- TPM in Verwaltungsbereichen: Abfälle und Abfälle werden in indirekten Produktionseinheiten eliminiert.
- Sicherheit, Umgebung und Gesundheitswesen
Autonome Instandhaltung - das wichtigste Prinzip TPM. Ihr Ziel ist es, Effizienzverluste, die durch Geräteausfälle, Kurzstopps, Defekte etc. entstehen, zu minimieren. Um dies zu erreichen, wird ein immer größerer Teil der notwendigen Wartungstätigkeiten (Reinigung, Schmierung, technische Inspektion der Geräte) vereinfacht, standardisiert und schrittweise durchgeführt die Aufgaben der Mitarbeiter auf das Feld übertragen. Dadurch werden die Mitarbeiter der Chefmechanikerabteilung von alltäglichen Routinetätigkeiten entlastet und haben mehr Zeit für die Entwicklung und Umsetzung von Verbesserungsmaßnahmen.
Das Total Productive Maintenance-Konzept ist die Grundlage für den Erfolg produzierender Unternehmen.
Durch die allgemeine Wartung von Geräten wird die Produktivität der Maschinen unter normalen Betriebsbedingungen maximiert und die Leistung über einen langen Zeitraum aufrechterhalten. Perfekt funktionierende Geräte, die repariert werden, bevor sie kaputt gehen, sparen Zeit, senken Kosten und motivieren die Mitarbeiter.
Oleg Levyakov
LIN (aus dem Englischen Lean – schlank, schlank) Produktion oder Logistik der „schlanken“ Produktion hat zu einem enormen Anstieg der Arbeitsproduktivität und des Produktionsvolumens geführt und bleibt in vielen Sektoren der Weltwirtschaft das wichtigste Produktionssystem.
Lean Manufacturing ist ein amerikanischer Name Toyota-Produktionssystem. Der Erfinder der Lean Manufacturing, Taiichi Ohno, begann bereits in den 1950er Jahren mit seinen ersten Experimenten zur Produktionsoptimierung. In der Nachkriegszeit lag Japan in Trümmern und das Land brauchte neue Autos. Das Problem bestand jedoch darin, dass die Nachfrage nicht groß genug war, um den Kauf einer leistungsstarken Produktionslinie nach dem Vorbild von Ford zu rechtfertigen. Es hat viel gekostet verschiedene Typen Pkw (Pkw, leichte und mittelschwere Lkw usw.), die Nachfrage nach einem bestimmten Pkw-Typ war jedoch gering. Die Japaner mussten lernen, effizient zu arbeiten und viele verschiedene Modelle zu entwickeln, obwohl die Nachfrage nach jedem Modell gering war. Dieses Problem hatte noch niemand gelöst, da Effizienz ausschließlich im Hinblick auf Massenproduktion verstanden wurde.
Lean Manufacturing beinhaltet die Einbindung jedes einzelnen Mitarbeiters in den Geschäftsoptimierungsprozess und maximale Kundenorientierung.
Der Ausgangspunkt der Lean Manufacturing ist der Kundennutzen. Aus Sicht des Endverbrauchers erlangt ein Produkt (eine Dienstleistung) erst dann seinen tatsächlichen Wert, wenn die direkte Verarbeitung und Produktion dieser Elemente erfolgt. Das Herzstück der schlanken Fertigung ist der Prozess der Verschwendungsbeseitigung, der auf Japanisch Muda genannt wird. Muda ist einer von ihnen japanische Wörter, was Verlust, Verschwendung bedeutet, also jede Aktivität, die Ressourcen verbraucht, aber keinen Wert schafft. Beispielsweise muss der Verbraucher das fertige Produkt oder seine Teile nicht auf Lager haben. Allerdings in traditionelles System Verwaltungskosten, Lagerkosten sowie alle mit Nachbesserungen, Mängeln und anderen indirekten Kosten verbundenen Kosten werden auf den Verbraucher umgelegt.
Gemäß dem Konzept des Lean Manufacturing lassen sich alle Aktivitäten eines Unternehmens wie folgt klassifizieren: Vorgänge und Prozesse, die für den Verbraucher einen Mehrwert schaffen, und Vorgänge und Prozesse, die für den Verbraucher keinen Mehrwert schaffen. Daher wird alles, was im Sinne einer schlanken Fertigung keinen Mehrwert für den Kunden darstellt, als Verschwendung eingestuft und muss beseitigt werden.
Die Hauptziele der Lean Manufacturing sind:
- Reduzierung der Kosten, einschließlich Arbeitskosten;
- Reduzierung der Produkterstellungszeit;
- Reduzierung der Produktions- und Lagerfläche;
- Garantie der Produktlieferung an den Kunden;
- maximale Qualität zu einem bestimmten Preis oder minimale Kosten zu einer bestimmten Qualität.
Wie oben erwähnt, begann die Geschichte des LIN-Systems mit der Firma Toyota. Sakishi Toyoda, einer der Gründer von Toyota, glaubte, dass der Produktionsverbesserung keine Grenzen gesetzt seien und dass sie unabhängig von der Marktlage und der Wettbewerbsfähigkeit des Unternehmens notwendig sei ständige Bewegung voranzutreiben und alle Produktionsprozesse zu verbessern. Das Ergebnis dieser Philosophie war die Kaizen-Strategie (kontinuierliche Verbesserung), die in Toyota-Unternehmen verfolgt wird. Sakishi Toyoda unterstützte große Investitionen in Forschungsunterlagen neue Autos zu bauen.
Kiishiro Toyoda, Sakishis Sohn, verstand, dass er etwas Ungewöhnliches tun musste, um erfolgreich mit amerikanischen Autogiganten (wie Ford) zu konkurrieren. Zunächst führte er in seinen Unternehmen das Konzept „just in time“ (Togo und Wartman) ein, das bedeutete, dass jedes Autoteil frühestens dann hergestellt werden musste, wenn es benötigt wurde. Daher verfügten die Japaner im Gegensatz zu den Amerikanern nicht über riesige Ersatzteillager, während die Japaner mehr Zeit und Ressourcen sparten. Die Methoden „Kaizen“ und „Togo und Wartman“ wurden zur Grundlage der Fertigungsphilosophie der Familie Toyoda.
Der nächste in der Dynastie, Eiji Toyoda, begann seine Aktivitäten mit der Entwicklung eines Fünfjahresplans zur Verbesserung der Produktionsmethoden. Zu diesem Zweck wurde Taichi Ono als Berater zu Toyota eingeladen, der „Kanban“-Karten einführte – „Bestandsbewegungen verfolgen“. Taichi Ohno brachte den Arbeitern ein detailliertes Verständnis der Methoden „Kaizen“ und „Togo und Wartman“ bei, modernisierte die Ausrüstung und legte den richtigen Arbeitsablauf fest. Wenn bei der Zusammenstellung der Produkte auf dem Förderband Probleme auftraten, hielt das Förderband sofort an, um etwaige Probleme schnell zu finden und zu beheben. Toyota setzt seine industrielle Qualitätsphilosophie seit zwanzig Jahren auch bei seinen Zulieferern um.
Soichiro Toyoda wurde 1982 Präsident und dann Vorstandsvorsitzender der Toyota Motor Corporation. Unter seiner Führung wurde Toyota internationales Unternehmen. Soishiro begann seine Arbeit zur Verbesserung der Qualität im Unternehmen mit dem Studium der Arbeiten des amerikanischen Qualitätsexperten E. Deming. Das Qualitätsmanagement in Toyota-Unternehmen ist klarer geworden und in allen Abteilungen des Unternehmens implementiert.
So wurde über mehrere Generationen des Toyota-Managements ein einzigartiges Qualitätssystem entwickelt, das die Grundlage des LIN-Systems bildete.
Die beliebtesten Lean-Manufacturing-Tools und -Methoden sind:
- Wertstromanalyse.
- Pull-Line-Produktion.
- Kanban.
- Kaizen – kontinuierliche Verbesserung.
- Das 5C-System ist eine Technologie zur Schaffung eines effektiven Arbeitsplatzes.
- SMED-System – Schneller Gerätewechsel.
- TPM-System (Total Productive Maintenance) – umfassende Gerätepflege.
- JIT-System (Just-In-Time – gerade pünktlich).
- Visualisierung.
- U-förmige Zellen.
Wertstromanalyse ist ein relativ einfaches und visuelles grafisches Diagramm, das die Material- und Informationsflüsse darstellt, die erforderlich sind, um dem Endverbraucher ein Produkt oder eine Dienstleistung bereitzustellen. Eine Wertstromkarte ermöglicht es, die Engpässe des Flusses sofort zu erkennen und auf der Grundlage ihrer Analyse alle unproduktiven Kosten und Prozesse zu identifizieren und einen Verbesserungsplan zu entwickeln. Die Wertstromanalyse umfasst die folgenden Schritte:
- Dokumentation der aktuellen Zustandskarte.
- Produktionsflussanalyse.
- Erstellen einer zukünftigen Zustandskarte.
- Entwicklung eines Verbesserungsplans.
Pull-Produktion(dt. Pull-Produktion) – ein Produktionsorganisationsschema, bei dem das Produktionsvolumen bei jedem Produktionsphase wird ausschließlich durch die Bedürfnisse der nachfolgenden Stufen (letztendlich durch die Bedürfnisse des Kunden) bestimmt.
Das Ideal ist „Single Piece Flow“, d.h. Der vorgelagerte Lieferant (oder interne Lieferant) produziert nichts, bis der nachgelagerte Verbraucher (oder interner Verbraucher) ihn dazu auffordert. Somit „zieht“ jeder nachfolgende Vorgang Produkte aus dem vorherigen.
Diese Art der Arbeitsorganisation steht auch in engem Zusammenhang mit der Linienverteilung und der Synchronisierung der Abläufe.
Kanban-System ist ein System, das die Organisation eines kontinuierlichen Materialflusses bei fehlenden Beständen gewährleistet: produktive Reserven werden in kleinen Chargen unter Umgehung des Lagers direkt an die benötigten Stellen im Produktionsprozess geliefert und die fertigen Produkte sofort an die Kunden versendet. Die Reihenfolge des Produktproduktionsmanagements ist umgekehrt: von der i-ten Stufe zur (i - 1)-ten.
Das Wesentliche des CANBAN-Systems ist, dass alles Produktionseinheiten Unternehmen werden mit materiellen Ressourcen nur in der Menge und rechtzeitig beliefert, die zur Erfüllung des Auftrags erforderlich sind. Die Bestellung von Fertigwaren wird an die letzte Stufe des Produktionsprozesses übermittelt, wo das erforderliche Volumen an unfertigen Erzeugnissen berechnet wird, das aus der vorletzten Stufe stammen sollte. Ebenso erfolgt ab der vorletzten Stufe eine Anfrage für die vorherige Produktionsstufe für eine bestimmte Anzahl von Halbzeugen. Das heißt, die Produktionsgröße an einem bestimmten Standort wird durch den Bedarf des nächsten Produktionsstandorts bestimmt.
Somit besteht zwischen jeweils zwei benachbarten Stufen des Produktionsprozesses eine doppelte Verbindung:
- Von der i-ten Stufe bis zur (i - 1)-ten Stufe wird die erforderliche Menge an laufender Arbeit angefordert („gezogen“);
- Von der (i – 1) Stufe werden materielle Ressourcen in der erforderlichen Menge an die i-te Stufe geschickt.
Die Mittel zur Übermittlung von Informationen im CANBAN-System sind spezielle Karten („Canban“, aus dem Japanischen übersetzt als Karte). Es werden zwei Arten von Karten verwendet:
- Produktionsauftragskarten, die die Anzahl der in einem früheren Produktionsstadium zu produzierenden Teile angeben. Produktionsauftragskarten werden von der i-ten Produktionsstufe an die (i-1)-te Stufe gesendet und sind die Grundlage für die Erstellung eines Produktionsprogramms für den (i-1)-ten Abschnitt;
- Auswahlkarten, die die Menge an Materialressourcen (Komponenten, Teile, Halbzeuge) angeben, die am vorherigen Verarbeitungs- (Montage-) Standort entnommen werden müssen. Auswahlkarten zeigen die Menge an materiellen Ressourcen, die der i-te Produktionsstandort tatsächlich vom (i - 1)-ten erhalten hat.
Auf diese Weise können Karten nicht nur innerhalb eines Unternehmens, das das CANBAN-System nutzt, zirkulieren, sondern auch zwischen diesem und seinen Niederlassungen sowie zwischen kooperierenden Unternehmen.
Unternehmen, die das CANBAN-System nutzen, erhalten Produktionsressourcen täglich oder sogar mehrmals am Tag, sodass der Bestand des Unternehmens 100–300 Mal im Jahr oder sogar noch häufiger vollständig aktualisiert werden kann, während in einem Unternehmen, das das CANBAN-System nutzt, das System vollständig aktualisiert werden kann MRP-Systeme oder MAP - nur 10-20 Mal im Jahr. Beispielsweise wurden bei der Toyota Motors Corporation 1976 dreimal täglich und 1983 alle paar Minuten Ressourcen an einen der Produktionsstandorte geliefert.
Der Wunsch, Lagerbestände zu reduzieren, wird auch zu einer Methode zur Identifizierung und Lösung von Produktionsproblemen. Die Anhäufung von Lagerbeständen und überhöhten Produktionsmengen ermöglicht es, häufige Geräteausfälle und -abschaltungen sowie Herstellungsfehler zu verbergen. Denn unter Bedingungen der Minimierung der Lagerbestände kann die Produktion aufgrund von Mängeln in der vorherigen Phase eingestellt werden technologischer Prozess, dann wird die Hauptanforderung des CANBAN-Systems neben der „Null-Inventar“-Anforderung zur „Null-Fehler“-Anforderung. Ohne die gleichzeitige Implementierung eines umfassenden Qualitätsmanagementsystems ist das CANBAN-System kaum umsetzbar.
Wichtige Elemente des CANBAN-Systems sind:
- ein Informationssystem, das nicht nur Karten, sondern auch Produktions-, Transport- und Lieferpläne umfasst, technologische Karten;
- System zur Regelung des Bedarfs und der beruflichen Personalrotation;
- System der totalen (TQM) und selektiven („Jidoka“) Produktqualitätskontrolle;
- Produktionsnivellierungssystem.
Hauptvorteile des CANBAN-Systems:
- kurzer Produktionszyklus, hoher Vermögensumschlag, einschließlich Lagerbestände;
- es fallen keine oder nur äußerst geringe Lagerkosten für Produktion und Lagerhaltung an;
- qualitativ hochwertige Produkte in allen Phasen des Produktionsprozesses.
Eine Analyse der weltweiten Erfahrungen mit der Verwendung des CANBAN-Systems hat gezeigt, dass dieses System eine Reduzierung der Produktionsbestände um 50 % und der Lagerbestände um 8 % bei einer deutlichen Beschleunigung des Umsatzes ermöglicht Betriebskapital und Verbesserung der Qualität der fertigen Produkte.
Die Hauptnachteile des Just-in-Time-Systems sind:
- die Schwierigkeit, eine hohe Konsistenz zwischen den Produktproduktionsstufen sicherzustellen;
- erhebliches Risiko einer Unterbrechung der Produktion und des Verkaufs von Produkten.
Kaizen- Dies ist eine Ableitung zweier Hieroglyphen – „Veränderung“ und „gut“ – wird normalerweise mit „Veränderung zum Besseren“ oder „kontinuierliche Verbesserung“ übersetzt.
Im übertragenen Sinne handelt es sich bei Kaizen um eine Philosophie und Managementmechanismen, die Mitarbeiter dazu ermutigen, Verbesserungen vorzuschlagen und diese zeitnah umzusetzen.
Es gibt fünf Hauptkomponenten von Kaizen:
- Interaktion;
- Persönliche Disziplin;
- Verbesserte Moral;
- Qualitätszirkel;
- Vorschläge zur Verbesserung;
5C-System – Technologie zur Schaffung eines effektiven Arbeitsplatzes
Unter dieser Bezeichnung versteht man ein System zur Herstellung von Ordnung, Sauberkeit und Stärkung der Disziplin. Das 5C-System umfasst fünf miteinander verbundene Prinzipien für die Organisation des Arbeitsplatzes. Der japanische Name für jedes dieser Prinzipien beginnt mit dem Buchstaben „S“. Ins Russische übersetzt – Sortieren, rationelle Anordnung, Reinigung, Standardisierung, Verbesserung.
- SORTIEREN: Notwendige Gegenstände – Werkzeuge, Teile, Materialien, Dokumente – von unnötigen trennen, um letztere zu entfernen.
- RATIONALE ANORDNUNG: Ordnen Sie den Rest rational an und platzieren Sie jeden Gegenstand an seinem Platz.
- REINIGUNG: Für Sauberkeit und Ordnung sorgen.
- STANDARDISIEREN: Behalten Sie die Genauigkeit bei, indem Sie die ersten drei S regelmäßig durchführen.
- VERBESSERUNG: etablierte Abläufe zur Gewohnheit machen und verbessern.
Schneller Wechsel (SMED – Single Minute Exchange of Die) wörtlich übersetzt als „Stempelwechsel in 1 Minute“. Das Konzept wurde vom japanischen Autor Shigeo Shingo entwickelt und revolutionierte Ansätze zur Umrüstung und Umrüstung. Durch die Implementierung des SMED-Systems kann der Werkzeugwechsel und das Nachjustieren in nur wenigen Minuten oder sogar Sekunden „mit einem Tastendruck“ erfolgen („OTED“-Konzept – „One Touch Exchange of Dies“).
Aufgrund zahlreicher statistische Forschung Es wurde festgestellt, dass sich die Zeit für die Durchführung verschiedener Vorgänge während des Umstellungsprozesses wie folgt verteilt:
- Vorbereitung von Materialien, Formen, Vorrichtungen usw. - dreißig%;
- Sichern und Entfernen von Matrizen und Werkzeugen – 5 %;
- Zentrierung und Platzierung des Werkzeugs - 15 %;
- Probebearbeitung und Anpassung - 50 %.
Als Ergebnis wurden die folgenden Prinzipien formuliert, um die Umrüstzeit um das Zehn- oder sogar Hundertfache zu verkürzen:
- Trennung von internen und externen Anpassungsvorgängen,
- Umwandlung innerer Handlungen in äußere,
- Verwendung von Funktionsklemmen oder vollständige Entfernung von Befestigungselementen,
- Verwendung zusätzlicher Geräte.
TPM-System (Total Productive Maintenance) – umfassende Gerätepflege Dient hauptsächlich dazu, die Qualität der Ausrüstung zu verbessern und sich auf das Maximum zu konzentrieren effiziente Nutzung dank eines umfassenden vorbeugenden Wartungssystems. Der Schwerpunkt dieses Systems liegt auf der Prävention und Früherkennung von Gerätedefekten, die zu schwerwiegenderen Problemen führen können.
TRM umfasst Bediener und Reparaturpersonal, die gemeinsam für eine höhere Zuverlässigkeit der Geräte sorgen. Die Grundlage von TPM ist die Erstellung eines Zeitplans für vorbeugende Wartung, Schmierung, Reinigung und allgemeine Inspektion. Dies sorgt für eine Steigerung des Total Equipment Efficiency Indikators.
JIT-System (Just-In-Time) – Materialverwaltungssystem in der Produktion, bei dem Komponenten aus einem früheren Betrieb (oder von einem externen Lieferanten) genau dann geliefert werden, wenn sie benötigt werden, aber nicht vorher. Dieses System führt zu einer starken Reduzierung des Volumens an unfertigen Arbeiten, Materialien und Fertigprodukten in den Lagern.
Das Just-in-Time-System beinhaltet einen spezifischen Ansatz für die Auswahl und Bewertung von Lieferanten, der auf der Zusammenarbeit mit einem engen Kreis von Lieferanten basiert, die aufgrund ihrer Fähigkeit ausgewählt werden, eine Just-in-Time-Lieferung von Komponenten zu gewährleisten. Gute Qualität. Gleichzeitig wird die Anzahl der Lieferanten um das Zwei- oder Mehrfache reduziert und mit den verbleibenden Lieferanten langfristige Wirtschaftsbeziehungen aufgebaut.
Visualisierung ist ein Mittel zur Kommunikation, wie Arbeit erledigt werden sollte. Hierbei handelt es sich um eine solche Anordnung von Werkzeugen, Teilen, Behältern und anderen Indikatoren für den Produktionszustand, bei der jeder auf den ersten Blick den Zustand des Systems erkennen kann – die Norm oder Abweichung.
Die am häufigsten verwendeten bildgebenden Verfahren sind:
- Gliederung.
- Farbcodierung.
- Verkehrszeichenmethode.
- Farbmarkierung.
- „Es war“ – „es wurde“.
- Grafische Arbeitsanweisungen.
U-förmige Zellen- Anordnung der Ausrüstung in Form des lateinischen Buchstabens „U“. In einer U-förmigen Zelle sind die Maschinen entsprechend der Arbeitsabfolge hufeisenförmig angeordnet. Bei dieser Geräteanordnung findet die letzte Bearbeitungsstufe in unmittelbarer Nähe statt Erstphase, sodass der Bediener nicht weit gehen muss, um den nächsten Produktionszyklus zu starten.
In einer Zeit intensiven Wettbewerbs und einer eskalierenden Krise haben Unternehmen auf der ganzen Welt keine andere Möglichkeit, als mithilfe der weltweit besten Managementtechnologien Produkte und Dienstleistungen zu schaffen, die die Kunden hinsichtlich Qualität und Preis maximal zufriedenstellen.
Verluste in jedem Fertigungsprozess- ein unvermeidliches Problem für viele Unternehmen, sowohl bei der Herstellung von Produkten als auch bei der Bereitstellung von Dienstleistungen. Verschwendung ist ein Zustand, der, gelinde gesagt, keinen Mehrwert für ein Produkt oder eine Dienstleistung darstellt. Um Verluste zu erkennen, müssen Sie diese zunächst erkennen. Es gibt acht Arten von Verlusten, durch die bis zu 85 % der Ressourcen eines Unternehmens verloren gehen:
- Ein Verlust kreatives Potenzial. Wenn ein Mitarbeiter wie ein Rädchen in einer Maschine behandelt wird, das jederzeit rausgeworfen oder ersetzt werden kann, wenn Beziehungen auf das Schema „Mit den Händen arbeiten und sich strikt an die Anweisungen des Chefs halten“ reduziert werden, nimmt das Interesse der Mitarbeiter an der Arbeit stetig ab. Experten halten diese Ordnung für überholt, sie zieht das Unternehmen zurück, was sich unmittelbar auf die Gewinne des Unternehmens auswirkt. In Japan beispielsweise gibt es in verschiedenen Unternehmen „Qualitätszirkel“, in denen jeder das Recht hat, Vorschläge zur Verbesserung der Prozessqualität zu äußern. Analysten glauben, dass im 21. Jahrhundert Unternehmen erfolgreich sein werden, die ein Gefühl der Beteiligung an der Produktionsverbesserung schaffen können.
- Überproduktion, die darin zum Ausdruck kommt, dass mehr Waren produziert werden als benötigt bzw. früher als der Kunde benötigt. Dadurch werden die Ressourcen, die für die Verbesserung der Qualität aufgewendet werden könnten, für die Steigerung der Quantität aufgewendet.
- Verzögerungen. Wenn Arbeiter untätig dastehen und auf Materialien, Werkzeuge, Ausrüstung und Informationen warten, ist das immer eine Folge schlechter Planung oder unzureichender Beziehungen zu Lieferanten oder unvorhergesehener Nachfrageschwankungen.
- Unnötiger Transport, wenn Materialien oder Produkte häufiger bewegt werden, als für einen kontinuierlichen Prozess erforderlich ist. Es ist wichtig, alles, was Sie brauchen, rechtzeitig und an den richtigen Ort zu liefern, und dafür muss das Unternehmen dies umsetzen gute Pläne Logistik.
- Übermäßiger Lagerbestand oder die Lagerung von mehr Produkten als verkauft wird und mehr Materialien als für den Prozess benötigt werden.
- Überverarbeitung. Die Produkte müssen von so hoher Qualität aus der Produktion kommen, dass Nacharbeiten und Modifikationen nach Möglichkeit entfallen, und die Qualitätskontrolle muss schnell und effektiv sein.
- Mängel, die unbedingt vermieden werden müssen, denn für die Bearbeitung von Kundenreklamationen werden zusätzliche Mittel aufgewendet: Muss ein fehlerhaftes Produkt repariert werden, kostet das zusätzliche Zeit, Mühe und Geld.
- Schlechte Bewegung oder schlechte Lieferung von Werkzeugen und Materialien innerhalb des Unternehmens, unnötige Bewegung der Mitarbeiter auf dem Gelände.
Laut einer Studie des Instituts für Integrierte Strategische Studien (ICSI) zur Verbreitung von Lean Manufacturing in Russland im März-April 2006 nutzten 32 % der 735 befragten russischen Industrieunternehmen japanische Erfahrungen. Eine Wiederholungsumfrage wurde im März-April 2008 durchgeführt. Anwendung von Lean Manufacturing auf Industrieunternehmen Russland in den Jahren 2006-2008.“ beim III. Russischen Lean-Forum „Lean Russia“. Unternehmen, die als erste Lean-Production-Methoden anwendeten: Gorky Automobile Plant (GAZ Group), RUSAL, EvrazHolding, Eurochem, VSMPO-AVISMA, KUMZ OJSC, Chelyabinsk Forging and Press Plant (ChKPZ OJSC), Sollers OJSC "("UAZ", „ZMZ“), KAMAZ, NefAZ, Sberbank of Russia OJSC usw.
TPM (Total Equipment Maintenance)(eng. Total Productive Maintenance, TPM) - Managementkonzept Produktionsausrüstung, mit dem Ziel, die Wartungseffizienz zu verbessern. Die Total Equipment Care-Methode basiert auf der Stabilisierung und kontinuierlichen Verbesserung der Wartungsprozesse, einem System der planmäßigen vorbeugenden Wartung, der Arbeit nach dem Prinzip „Null Fehler“ und der systematischen Beseitigung aller Verlustquellen.
TPM steht im weitesten Sinne für „Total Effective Maintenance“. Unter „Total“ versteht man nicht nur die produktive und kostengünstige Wartung, sondern auch das Gesamtsystem der effektiven Pflege der Geräte über deren gesamte Lebensdauer sowie die Einbeziehung jedes einzelnen Mitarbeiters und Mitarbeiters verschiedenen Abteilungen durch die Einbindung einzelner Betreiber in die Wartung. Darüber hinaus erfordert der Einsatz von TPM bestimmte Verpflichtungen seitens der Unternehmensleitung.
Im Total Equipment Maintenance-System geht es nicht um das ausschließliche Problem der Gerätewartung, sondern um ein umfassendes Verständnis der Wartung von Produktionsanlagen als Integration von Betriebs- und Wartungsprozessen, die frühzeitige Beteiligung des Wartungspersonals an der Geräteentwicklung Wartungspläne und genaue Aufzeichnung des Zustands der Ausrüstung für gezielte Wartung. in gutem Zustand. Insbesondere im Just-in-Time-Produktionsmanagement spielt TPM eine wichtige Rolle, da wartungsbedingte Eingriffe zu Zeitverschwendung führen, die sich entlang der gesamten Wertschöpfungskette erhöht.
Die Gründe für die Integration von Total Maintenance in die Lean Manufacturing (TPS)-Philosophie sind in Abbildung 1 dargestellt.
Diagramm 1. Einbindung von TPM in Lösungen zur Schadensverhütung.
Das Ziel der Implementierung von TPM ist die Beseitigung chronischer Verluste:
- Geräteausfall
- Hohe Umrüst- und Einstellzeiten
- Leerlauf und kleinere Mängel
- Reduzierte Leistung (Geschwindigkeit) des Gerätebetriebs
- Defekte Teile
- Verluste bei der Inbetriebnahme von Geräten.
Acht Prinzipien von TPM
- Kontinuierliche Verbesserung: Praxisgerechte Prävention der 7 Schadensarten.
- Selbstständige Wartung: Der Betreiber der Anlage muss selbständig Inspektions-, Reinigungs-, Schmier- und kleinere Wartungsarbeiten durchführen.
- Wartungsplanung: Sicherstellung der 100-prozentigen Verfügbarkeit der Geräte sowie Durchführung von Tätigkeiten Kaizen im Bereich Instandhaltung.
- Schulung und Schulung: Die Mitarbeiter müssen nach Bedarf geschult werden, um kompetent in der Bedienung und Wartung von Geräten zu werden.
- Einführungskontrolle: Implementierung einer vertikalen Einführungskurve für neue Produkte und Geräte.
- Qualitätsmanagement: Umsetzung des Ziels „Null Qualitätsmängel“ bei Produkten und Anlagen.
- TPM in Verwaltungsbereichen: Abfälle und Abfälle werden in indirekten Produktionseinheiten eliminiert.
- Arbeitssicherheit, Umwelt und Gesundheit: Die Anforderung, Unfälle im Unternehmen auf null zu reduzieren.
Autonome Wartung ist das wichtigste Prinzip von TPM. Ihr Ziel ist es, Effizienzverluste, die durch Geräteausfälle, Kurzstopps, Defekte etc. entstehen, zu minimieren. Um dies zu erreichen, wird ein immer größerer Teil der notwendigen Wartungstätigkeiten (Reinigung, Schmierung, technische Inspektion der Geräte) vereinfacht, standardisiert und schrittweise durchgeführt die Aufgaben der Mitarbeiter auf das Feld übertragen. Dadurch werden die Mitarbeiter der Chefmechanikerabteilung einerseits von alltäglichen Routinetätigkeiten entlastet, so dass ihnen mehr Zeit für die Entwicklung und Umsetzung von Verbesserungsmaßnahmen bleibt. Andererseits können Geräte (Geräte) nun mit der notwendigen technischen Wartung versorgt werden, die bisher mangels ausreichender Ressourcen nicht oder nicht rechtzeitig zur Verfügung gestellt werden konnten.
Das TPM-Konzept wurde in Japan in den späten 60er und frühen 70er Jahren bei Nippon Denso, einem Zulieferer für elektrische Ausrüstung der Toyota Corporation, im Zusammenhang mit der Gründung des Toyota Production System (TPS) entwickelt. In den frühen 90er Jahren des letzten Jahrhunderts TPM V verschiedene Optionen in Unternehmen auf der ganzen Welt implementiert. Der Gründer von TPS, Taiichi Ohno, sagte bekanntlich: „Die Stärke von Toyota liegt nicht in den Aushärtungsprozessen, sondern in der proaktiven Wartung der Ausrüstung.“ Die Erfahrung russischer und globaler Unternehmen bei der Implementierung und Nutzung des TPM-Systems finden Sie in Almanach „Produktionsmanagement“.
Die Implementierung der Total Equipment Maintenance in TPS wird in der in Abbildung 2 dargestellten Reihenfolge beschrieben.
Schema 2. Systematisches Vorgehen bei der Implementierung von TRM im Toyota-Produktionssystem.
Als effektives Lean-Manufacturing-Tool gilt die Total Equipment Maintenance-Methode In letzter Zeit wird in Russland in vielen Unternehmen aktiv umgesetzt - dem Reifenwerk Jaroslawl (SIBUR-Russische Reifenholding), dem mechanischen Werk Tschepetsk, dem Produktionswerk Tscheljabinsk Kunststofffenster(LLC „Etalon“), die Süßwarenfabrik JSC „Bolshevik“ in Moskau usw.
TPM (Total Productive Maintenance, TPM) ist ein Konzept, das darauf abzielt, die Leistung von Geräten durch Wartungstechniken zu verbessern, die darauf abzielen, Ausfälle im Betrieb zu verhindern. Die Total Equipment Maintenance-Methode basiert auf der Stabilisierung und kontinuierlichen Verbesserung der Wartungsprozesse, einem System der planmäßigen vorbeugenden Wartung, der Arbeit nach dem Prinzip „Null Fehler“ und der systematischen Beseitigung aller Verlustquellen. Die Behebung von TPM-Ausfällen und -Defekten erfordert die Beteiligung aller Managementebenen. Der Schwerpunkt sollte auf der Problempräventionsarbeit des Produktions- und Wartungspersonals liegen. TPM ist ein System, das eine ständige Unterstützung des Personals und eine direkte Beteiligung des Managements erfordert.
Das Ziel von TPM ist die Minimierung von Effizienzverlusten Produktionssystem und Schaffung eines Managementsystems, das kontinuierlich nach Verbesserungen strebt.
Das Ziel der Implementierung von TPM ist die Beseitigung chronischer Verluste:
· Geräteausfall;
· hohe Umrüstzeit;
· Leerlauf und kleinere Störungen;
· Reduzierung der Betriebsgeschwindigkeit der Ausrüstung;
· defekte Teile;
· Verluste bei der Inbetriebnahme von Geräten.
Das TPM-System basiert auf 8 Prinzipien, die in Abbildung 1 dargestellt sind.
1) Kontinuierliche Verbesserung: zielt darauf ab, 7 Arten von Verlusten zu verhindern;
2) Eigenständige Wartung: Der Anlagenbetreiber muss die Reinigungsarbeiten sowie kleinere Wartungsarbeiten selbstständig kontrollieren;
3) Wartungsplanung: Sicherstellung der vollständigen Einsatzbereitschaft der Ausrüstung sowie Durchführung von Wartungsarbeiten;
4) Personalschulung: Mitarbeiter müssen entsprechend den Anforderungen geschult werden, um ihre Qualifikationen für die Bedienung und Wartung von Geräten zu verbessern;
5) TPM für neue Prozesse: Umsetzung der Einführung neuer Prozesse;
6) Qualitätsmanagement: Umsetzung des Ziels „Null Qualitätsmängel“ bei Produkten und Geräten;
7) TPM in Verwaltungsbereichen: Abfall wird in indirekten Produktionseinheiten beseitigt;
8) Arbeitssicherheit: Unfälle im Unternehmen in „Null-Fehler“ umwandeln.
Abbildung 1 – TPM-Prinzipien
Abbildung 1 zeigt die TPM-Prinzipien, auf denen das gesamte System basiert. Jedes Prinzip trägt zur Bildung des Systems als Ganzes bei, sodass sie nicht einzeln, sondern nur in Kombination existieren können.
Trotz aller Schönheit dieses Systems gibt es viele Schwierigkeiten bei der Umsetzung. Besonders schwierig sind die ersten Schritte zur Umsetzung des Konzepts. Schauen wir uns die Hauptprobleme bei der Implementierung von TPM an.
Mangel an TPM-Managern. Leider stellen viele Unternehmen, die auf Lean Manufacturing umsteigen wollen, dabei fest, dass ihr Managementteam nicht über genügend Erfahrung verfügt. Daher muss die Geschäftsleitung zunächst bestimmte Spezialisten gewinnen, die über ausreichende Erfahrung in der Implementierung des Systems verfügen. Dabei kann es sich sowohl um eine einzelne Person als auch um ganze Teams handeln. Ihre Aufgaben werden darin bestehen, Pläne zu entwickeln, Schulungen für lokale Führungskräfte und direkt für normale Mitarbeiter durchzuführen und den gesamten Prozess zu koordinieren. Es gibt ganze Unternehmen, die Dienstleistungen in diesem Bereich anbieten.
Die nächste Herausforderung bei der Implementierung von TPM ist das Timing. Leider erfolgen solche Änderungen im Produktionsbetrieb nicht sofort und dieser Prozess kann lange dauern. Dies hat großen Einfluss auf die Reaktion sowohl der einfachen Mitarbeiter als auch der Geschäftsleitung, da jeder bestimmte Ergebnisse erwartet. In diesem Fall ist es notwendig, die Ergebnisse ständig aufzuzeichnen und anzuzeigen und zu vergleichen, was war und was geworden ist. Dann werden die Leute sehen, dass der Prozess voranschreitet und tatsächlich Ergebnisse hervorbringt.
Der nächste negative Punkt ist auf den ersten Blick die Investition zusätzlicher Materialkosten. Allerdings sollte ein kompetenter Manager, der sich für Veränderungen in seinem Unternehmen entscheidet, jederzeit zu zusätzlichen Investitionen bereit sein. Diese Investitionen werden sich im Laufe der Zeit in Form einer gesteigerten Produktionseffizienz sowie geringeren Materialkosten für Reparaturen und den Kauf von Ersatzteilen amortisieren. Es darf nicht sein, dass die vorhandenen Materialreserven nur für einen Teil des Projekts ausreichen, da diese Mittel sonst vergeblich genutzt werden könnten.
Das größte Problem besteht jedoch darin, dass es schwierig ist, die Einstellung der Arbeitnehmer zu ihrer Arbeit, ihrer Produktion und ihrer Ausrüstung zu ändern. Damit ist das Verhältnis zwischen Firmenmitarbeitern gemeint, die schon seit einigen Jahren für das Unternehmen arbeiten; sie gewöhnen sich daran bestehendes System Arbeit, Wartung, Management. Und es ist ganz natürlich, dass solche Menschen jede Veränderung negativ wahrnehmen. Und je älter die Mitarbeiter in der Produktion sind, desto schwieriger ist es, Veränderungen in ihrem Bewusstsein herbeizuführen.
Alle oben genannten Probleme sind in Tabelle 1 aufgeführt. Außerdem wurde jedes Problem anhand einer Umfrage unter mittleren Managern des technischen und Produktionspersonals auf einer Zehn-Punkte-Skala bewertet, anhand derer wir erkennen können, welche Probleme die meiste Aufmerksamkeit erfordern.
Tabelle 1 – Die häufigsten Probleme bei der Implementierung von TPM
Problemerkennung | Kritisch | Ursache des Auftretens | Heilmittel |
Mangel an qualifizierten Topmanagern | 9 | Mangel an Erfahrungsaustausch/Führungskräfteentwicklung | Fachkräfte von außen anziehen. Fortbildung für aktuelle Managementpersonal |
Langfristig | 7 | Schlechte Planung/mangelnde Ausführungskontrolle | Sorgfältige Planung. Sichtbarkeit von Zwischenergebnissen |
Zusätzliche Materialkosten | 8 | Mangel an Materialreserven | Sucht nach zusätzlichen Reserven |
Einstellung des Personals | 10 | Mangelnde Personalentwicklung/Sichtbarkeit der Ergebnisse | Ständiger Dialog mit dem Bedienpersonal. Anspruchsvoll/kontrollierend. Sichtbarkeit von Zwischenergebnissen |
In diesem Artikel wurden die Prinzipien von TPM erläutert. Auch die Hauptprobleme bei der Einführung des neuen Konzepts wurden diskutiert. Und nach der Analyse dieser Probleme wurden einige Optionen zu ihrer Lösung vorgeschlagen, wie zum Beispiel: Anwerbung von Top-Managern von außen, Suche nach zusätzlichen materiellen Ressourcen sowie Methoden zur Veränderung Unternehmenskultur und die Einstellung der Künstler zur Arbeit.
Liste der verwendeten Literatur:
- Horizontale Managementsysteme: Potenzial zur Modellierung von Geschäftsprozessen / A. A. Dolgaya. - Kaliningrad: Verlag der staatlichen Haushaltsbildungseinrichtung für höhere Berufsbildung „KSTU“, 2013. - 208 S.
- Chase, R. Produktions- und Betriebsmanagement / R. Chase. - 8. Aufl.: trans. aus dem Englischen - Moskau: Williams Publishing House, 2004. - 704 S.