MRP-Prozess. Informationstechnologie Management
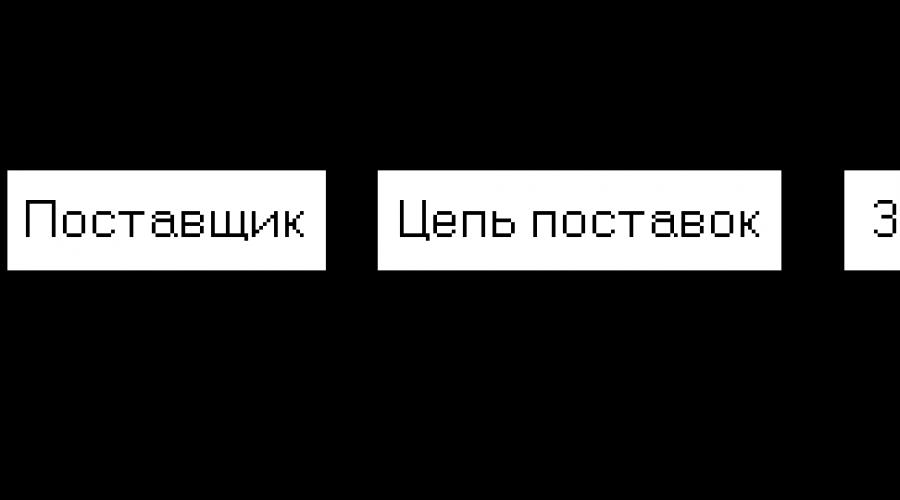
Lesen Sie auch
Einführung
Das MRP-1-System ist eines der beliebtesten weltweit und basiert auf dem logistischen Konzept der „Anforderungs-/Ressourcenplanung“. Dieses System arbeitet mit Materialien, Komponenten, Halbzeugen und deren Teilen, deren Nachfrage von der Nachfrage nach bestimmten Fertigprodukten abhängt.
Die Hauptziele dieses Systems sind die Deckung des Bedarfs an Materialressourcen für die Planung der Produktion und Lieferung an Verbraucher, die Aufrechterhaltung eines niedrigen Bestands an Materialressourcen, unfertigen Erzeugnissen und Fertigwaren sowie die Planung von Produktionsabläufen, Lieferplänen und Einkaufsvorgängen.
Die Grundidee von MRP-Systemen besteht darin, dass jede Abrechnungseinheit von Materialien oder Komponenten, die zur Herstellung eines Produkts benötigt werden, zum richtigen Zeitpunkt und in der richtigen Menge verfügbar sein muss.
Die Notwendigkeit, den Bedarf an MR zu planen, ergibt sich aus der Tatsache, dass die meisten Probleme im Produktionsprozess mit der Verzögerung oder Vorverlegung des Eingangs von Bauteilen, Rohstoffen und Materialien verbunden sind, wodurch in der Regel Parallel zu einer Abnahme der Produktionseffizienz kommt es in den Lagern zu einem Überschuss (Mangel) an Materialien, die früher oder später als zum geplanten Termin eingehen. Um solchen Problemen vorzubeugen, wurde eine Methodik zur Planung des Materialbedarfs MRP I (Material Requirements Planning) entwickelt. Es wurden Computerprogramme erstellt, die es ermöglichen, die Versorgung mit MR optimal zu regulieren, die Bestände im Lager und die Produktionstechnik selbst zu kontrollieren.
Die Hauptaufgabe von MRP I besteht darin, die Verfügbarkeit der benötigten Menge an benötigten Materialien (Komponenten) zu jedem Zeitpunkt innerhalb des Planungszeitraums sicherzustellen, zusammen mit einer möglichen Reduzierung der aktuellen Bestände und damit der Entladung der Lager.
Allgemeines Konzept des MRP-Systems I.
Eines der weltweit populärsten Logistikkonzepte, auf dessen Grundlage eine Vielzahl mikrologistischer Systeme entwickelt und betrieben wurde, ist das Konzept der „Anforderungs-/Ressourcenplanung“ (RP). Das Konzept steht oft im Gegensatz zum Just-in-Time-Logistikkonzept, d. h. Push-Logistiksysteme basieren darauf.
Basierend auf dem festgelegten Produktionsplan des MRP I-Systems implementieren sie einen zeitbasierten Phasenansatz zur Wertermittlung und Regulierung des Lagerbestands. Da dadurch wiederum die Menge der erforderlichen Materialressourcen für die Produktion oder Montage einer bestimmten Menge an Fertigprodukten generiert wird, handelt es sich bei MRP I um ein typisches „Push“-System, von dem ein vergrößertes Diagramm gegeben wird.
MRP I als „Push“-System;
MR – materielle Ressourcen;
NP – in Arbeit;
GP – Fertigprodukte
Grundlegende mikrologistische Systeme, die auf dem Konzept der „Bedarfs-/Ressourcenplanung“ basieren, sind in der Produktion und Versorgung Systeme der „Materialien/Fertigungsbedarfs-/Ressourcenplanung, MRP I / MRP II“ und in der Distribution (Distribution) Systeme „Produkt/Ressource“. „Verteilungsplanung“ (Verteilungsbedarfe/Ressourcenplanung, DRP I / DRP II).
Typische praktische Anwendungen für MRP-I-Systeme finden sich in produzierenden Unternehmen. technologische Prozesse zusammen mit dem Kauf materieller Ressourcen. Nach der Definition des amerikanischen Forschers J. Orlisky, einem der Hauptentwickler des MRP-I-Systems, besteht das „Materialbedarfsplanungssystem (MRP-System) im engeren Sinne aus einer Reihe logisch zusammenhängender Verfahren, entscheidender Regeln und Anforderungen.“ die den Produktionsplan in eine „Kette von Anforderungen“ übersetzen, die zeitlich synchronisiert sind, sowie die geplante Abdeckung dieser Anforderungen für jede Bestandseinheit an Komponenten, die zur Einhaltung des Zeitplans erforderlich sind ...
Das MRP-System plant die Reihenfolge der Bedarfe und Deckungen neu, wenn sich entweder der Produktionsplan, die Bestandsstruktur oder die Produkteigenschaften ändern.“
MRP-Systeme verwalten Materialien, Komponenten, Halbzeuge und deren Teile, deren Nachfrage von der Nachfrage nach bestimmten Fertigprodukten abhängt. Obwohl das Logistikkonzept selbst, das die Grundlage des MRP-I-Systems bildet, schon vor längerer Zeit (seit Mitte der 1950er Jahre) entwickelt wurde, konnte es erst mit dem Aufkommen von Hochgeschwindigkeitscomputern umgesetzt werden üben. Gleichzeitig hat die Revolution in der Mikroprozessor- und Informationstechnologie das explosionsartige Wachstum verschiedener Anwendungen von MRP-Systemen in der Wirtschaft stimuliert. Die Hauptziele von MRP-Systemen sind:
* Steigerung der Effizienz der Qualitätsplanung des Ressourcenbedarfs;
* Planung des Produktionsprozesses, Lieferplans, Beschaffung;
* Verringerung der Lagerbestände an Materialressourcen, unfertigen Erzeugnissen und Fertigprodukten;
* Verbesserung der Kontrolle über die Lagerbestände;
* verringern Logistikkosten;
* Deckung des Bedarfs an Materialien, Komponenten und Produkten.
MRP I ermöglichte es, die Planungen und Maßnahmen der logistischen Systemeinheiten in Versorgung, Produktion und Vertrieb im gesamten Unternehmen unter Berücksichtigung der ständigen Veränderungen in der realen Welt zu koordinieren. Zeitskala („online“). Es ist nun möglich, mittel- und langfristige Liefer-, Produktions- und Verkaufspläne im MRP zu koordinieren sowie eine laufende Regulierung und Kontrolle der Bestandsverwendung durchzuführen.
Bei der Erreichung dieser Ziele stellt das MRP-System den Fluss der geplanten Mengen an Materialressourcen und Produktbeständen über den Planungshorizont sicher. Das System im MRP ermittelt zunächst, wie viel und in welchem Zeitrahmen das Endprodukt produziert werden muss. Das System ermittelt dann die Uhrzeit und benötigte Mengen Materialressourcen, um den Produktionsplan einzuhalten. Es wird ein Blockdiagramm des MRP I-Systems dargestellt. Es enthält die folgenden Informationen:
Blockdiagramm des MRP I-Systems
1. Verbraucherbestellungen, Prognose der Nachfrage nach Fertigprodukten, Produktionsplan – MRP-I-Eingabe.
2. Datenbank zu Materialressourcen – Nomenklatur und Parameter von Rohstoffen, Halbzeugen usw.; Normen des Verbrauchs materieller Ressourcen pro Produktionseinheit; Zeitpunkt ihrer Lieferung für den Produktionsbetrieb.
3. Bestandsdatenbank – das Volumen der Produktions-, Versicherungs- und sonstigen Bestände an Materialressourcen in Lagerhäusern; Übereinstimmung der Barreserven mit der erforderlichen Menge; Lieferanten; Versorgungsparameter.
4. Softwarepaket MRP-I – das erforderliche Gesamtvolumen der anfänglichen Materialressourcen, abhängig von der Nachfrage; Anforderungskette (Bedarf) an materiellen Ressourcen unter Berücksichtigung der Lagerbestände; Bestellungen für Mengen an Inputmaterialressourcen für die Produktion.
5. Die Ausgabemaschine stellt eine Reihe von Ausgabedokumenten grafisch dar: Bestellungen für Materialressourcen von Lieferanten, Anpassungen des Produktionsplans, Lieferpläne für Materialressourcen, Status MRP-I-Systeme.
Die Eingabe des MRP-I-Systems sind Verbraucherbestellungen, unterstützt durch Nachfrageprognosen für die Fertigprodukte des Unternehmens, die im Produktionsplan (Freigabepläne für Fertigprodukte) enthalten sind. Wie bei Mikrologistiksystemen, die auf den Prinzipien des Just-in-Time-Konzepts basieren, ist auch bei MRP-I die Kundennachfrage der entscheidende Faktor.
Die MRP-I-Informationsunterstützung umfasst die folgenden Daten:
* Produktionsplan gemäß der angegebenen Nomenklatur für ein bestimmtes Datum;
* Daten zu Materialien, die spezifische Namen der benötigten Teile, Rohstoffe, Montageeinheiten enthalten und deren Menge pro Einheit des fertigen Produkts angeben;
* Daten zu den Beständen der für die Produktion notwendigen Materialressourcen, Lieferzeiten von Bestellungen usw.
Die Datenbank zu Materialressourcen enthält alle erforderlichen Informationen über die Nomenklatur und die wichtigsten Parameter (Eigenschaften) von Rohstoffen, Materialien, Komponenten, Halbzeugen usw., die für die Herstellung (Montage) von Fertigprodukten oder deren Teilen erforderlich sind. Darüber hinaus enthält es Standards für den Verbrauch materieller Ressourcen pro Produktionseinheit sowie Dateien über die Zeitpunkte der Lieferung der entsprechenden materiellen Ressourcen an die Produktionsabteilungen des Unternehmens. Die Datenbank identifiziert auch Zusammenhänge zwischen einzelnen Inputs von Produktionseinheiten hinsichtlich der verbrauchten Materialressourcen und im Verhältnis zum Endprodukt. Die Bestandsdatenbank informiert das System und das Managementpersonal über das Vorhandensein und die Größe von Produktions-, Versicherungs- und anderen erforderlichen Beständen an Materialressourcen im Lager des Unternehmens sowie über deren Nähe zu einem kritischen Niveau und die Notwendigkeit ihrer Auffüllung. Darüber hinaus enthält diese Datenbank Informationen über Lieferanten und Parameter für die Bereitstellung materieller Ressourcen.
Einführung. 3
1. Merkmale des MRP-Systems, Entstehungsgeschichte. 4
2. Ziele des MRP-Systems, Elemente des Systems. 7
3. Ergebnisse des MRP-Systems. 11
Abschluss. 16
Ziele…………………………………………………………………………………….17
Liste der verwendeten Literatur... 21
Einführung
Der zunehmende Wettbewerb am Markt und das dynamische Wachstum des Unternehmens selbst erhöhen die Anforderungen an das Ressourcenplanungssystem in Handelsunternehmen erheblich. Wenn sich Probleme im Working Capital Management jedoch nicht vermeiden lassen, sind eine ganze Reihe von Maßnahmen zu deren Lösung erforderlich.
Das Einkaufssystem ist ein nicht weniger wichtiger Geschäftsprozess als der Vertrieb. Richtiger wäre es zu sagen, dass diese beiden Prozesse untrennbar miteinander verbunden sind und daher nur ihre koordinierte Optimierung den gewünschten Effekt erzielen kann. Aus der Beziehung zwischen Verkaufsplänen und Wareneinkäufen wird eine Handelsbilanz erstellt, die die Bewegungsbilanz widerspiegelt Geld aus Handelsaktivitäten. Das heißt, Zahlungen an Lieferanten für gekaufte Waren und Quittungen von Käufern für an sie gelieferte Waren. Durch die automatische Erstellung von Handelsbilanzen können Sie die Umsetzung von Plänen unter dem Gesichtspunkt des Cashflows schnell analysieren sowie verschiedene Pläneszenarien anpassen und erarbeiten.
Die Automatisierung des Beschaffungsprozesses erfordert die Erstellung eines operativen Beschaffungsplans, wenn Kunden Waren bestellen und die Waren die Untergrenze des Standards erreichen. Als Einkaufsmanagementmethoden werden viele Methoden eingesetzt, die effektivste Methode ist jedoch MRP.
Ziel dieser Arbeit ist die Organisation der Beschaffung im MRP-System.
Im Rahmen des erklärten Ziels wurden folgende Aufgaben gestellt:
1. Beschreiben Sie das MRP-System und seine Entstehungsgeschichte;
2. Identifizieren Sie die Ziele des MRP-Systems und die Elemente des Systems.
3. Charakterisieren Sie die erzielten Ergebnisse des MRP-Systems.
1. Merkmale des MRP-Systems, Entstehungsgeschichte
Das MRP-1-System ist eines der beliebtesten weltweit und basiert auf dem Logistikkonzept der „Anforderungs-/Ressourcenplanung“. Dieses System arbeitet mit Materialien, Komponenten, Halbzeugen und deren Teilen, deren Nachfrage von der Nachfrage nach bestimmten Fertigprodukten abhängt. Die Hauptziele dieses Systems sind die Deckung des Bedarfs an Materialressourcen für die Planung der Produktion und Lieferung an Verbraucher, die Aufrechterhaltung eines niedrigen Bestands an Materialressourcen, unfertigen Erzeugnissen und Fertigwaren sowie die Planung von Produktionsabläufen, Lieferplänen und Einkaufsvorgängen.
Das MRP-II-System, ein Bedarfs-/Ressourcenplanungssystem der zweiten Generation, ist ein integriertes Mikrologistiksystem, das Finanzplanung und Logistikabläufe kombiniert. Dieses System ist wirksames Werkzeug Planung zur Umsetzung der strategischen Ziele des Unternehmens in den Bereichen Logistik, Marketing, Produktion, Finanzen, Planung und Verwaltung der organisatorischen Ressourcen des Unternehmens, um ein Mindestmaß an Lagerbeständen zu erreichen und gleichzeitig alle Phasen des Produktionsprozesses zu kontrollieren. Der Vorteil von MRP-2-Systemen gegenüber MRP-1-Systemen: bessere Befriedigung der Verbrauchernachfrage, erreicht durch Verkürzung der Produktionszyklen, Reduzierung der Lagerbestände, bessere Organisation Lieferungen, schnelle Reaktion auf Nachfrageänderungen, größere Planungsflexibilität, was zur Reduzierung der Logistikkosten für die Bestandsverwaltung beiträgt.
In den USA durchgeführte Studien haben gezeigt, dass der Einsatz des MRP-II-Logistiksystems die Lagerbestände um durchschnittlich 17 % reduzieren, die Produktionsrentabilität um 10 % steigern und den Einkauf von Rohstoffen und Ausrüstung um 7 % reduzieren kann. Gleichzeitig steigt das Dienstleistungsvolumen für Verbraucher um 16 %.
Die Ziele der Bedarfs-/Ressourcenplanung bestehen darin, den Lagerbestand zu reduzieren, einen hohen Prozentsatz der Leistungserbringung aufrechtzuerhalten, Lieferpläne sowie Produktions- und Einkaufsaktivitäten zu koordinieren. Diese Ziele sind gleichzeitig erreichbar, was ein Vorteil dieser Systeme ist.
Grundlegende Mikrologistik-Subsysteme, die auf dem Konzept der „Bedarfs-/Ressourcenplanung“ basieren, sind in der Produktion und Versorgung Systeme der „Material-/Fertigungsbedarfs-/Ressourcenplanung, MRP I/MRP II“ und im Vertrieb (Distribution) „Produkt-/Ressourcenverteilungsplanung“. ”-Systeme (Verteilungsanforderungen/Ressourcenplanung, DRPI/DRPII).
In den frühen 60ern. Aufgrund der wachsenden Beliebtheit von Computersystemen entstand die Idee, diese zur Planung von Produktionsprozessen einzusetzen. Die Notwendigkeit hierfür ergab sich aus der Tatsache, dass der Großteil der Verzögerungen im Produktionsprozess mit Verzögerungen beim Eingang einzelner Komponenten verbunden ist, was in der Regel mit einer Abnahme der Produktionseffizienz einhergeht ein Überschuss an Materialien in Lagern, die pünktlich oder früher als geplant eintrafen. Darüber hinaus kommt es durch ein Ungleichgewicht in der Versorgung mit Bauteilen zu zusätzlichen Komplikationen bei der Zustandserfassung und -verfolgung während des Produktionsprozesses, d bereits montiertes Fertigprodukt.
Aus diesem Grund wurde die MRP-Methodik (Material Requirements Planning) entwickelt. Die Implementierung eines nach dieser Methodik arbeitenden Systems ist Computer Programm, mit dem Sie die Versorgung des Produktionsprozesses mit Komponenten optimal regulieren und sowohl die Bestände im Lager als auch die Produktionstechnologie selbst steuern können. Das Hauptziel der MRP besteht darin, die Verfügbarkeit der erforderlichen Menge an benötigten Materialien und Komponenten zu jedem Zeitpunkt innerhalb des Planungszeitraums sicherzustellen, zusammen mit einer möglichen Reduzierung der festen Bestände und damit der Entladung des Lagers.
Mit anderen Worten: Das MRP-System ermöglicht es Ihnen, die Produktionskapazität optimal auszulasten und gleichzeitig genau so viele Rohstoffe einzukaufen, wie zur Erfüllung des aktuellen Auftragsplans erforderlich und im entsprechenden Produktionszyklus verarbeitet werden können.
So können Sie durch die Planung des aktuellen Materialbedarfs Lager mit Rohstoffen und Komponenten (sie werden in genau der Menge eingekauft, die in einem Produktionszyklus verarbeitet und direkt an die Produktionswerkstätten geliefert werden kann) sowie Lager mit Fertigprodukten entladen (Die Produktion erfolgt in strikter Übereinstimmung mit akzeptierter Plan Bestellungen und Produkte im Zusammenhang mit der aktuellen Bestellung müssen termingenau produziert werden).
Die ideale Umsetzung des MRP-Konzepts ist in der Realität nicht umsetzbar. Beispielsweise aufgrund möglicher Lieferverzögerungen aus verschiedenen Gründen und anschließendem Produktionsstopp. Deshalb stellen Dispositionssysteme für jeden Fall einen gewissen Sicherheitsbestand an Rohstoffen und Komponenten bereit.
2. Ziele des MRP-Systems, Elemente des Systems
Die Hauptziele von MRP-Systemen sind:
Befriedigung des Bedarfs an Materialien, Komponenten und Produkten zur Planung der Produktion und Lieferung an Kunden;
Aufrechterhaltung eines niedrigen Bestands an Materialressourcen, unfertigen Produkten und Fertigprodukten;
Planung von Produktionsabläufen, Lieferplänen und Einkaufsvorgängen.
Bei der Erreichung dieser Ziele stellt das MRP-System den Fluss geplanter Mengen an Materialressourcen und Produktbeständen für die geplante Zukunft sicher. Das MRP-System ermittelt zunächst, in welchem Zeitrahmen und in welcher Menge Endprodukte produziert werden müssen. Anschließend werden die Zeit und die erforderlichen Mengen an Materialressourcen zur Erfüllung des Produktionsplans bestimmt. Die Eingabe dieses Systems sind Verbraucherbestellungen, unterstützt durch Nachfrageprognosen für die Fertigprodukte des Unternehmens, die im Produktionsplan (Freigabepläne für Fertigprodukte) enthalten sind. Wie bei Mikrologistiksystemen, die auf den Prinzipien des Just-in-Time-Konzepts basieren, steht bei MRPI die Verbrauchernachfrage im Vordergrund.
Das MRPI-Softwarepaket basiert auf systematisierten Produktionsplänen (Endproduktfreigabepläne) (MPS – Master Production Schedule-Modul) in Abhängigkeit von der Verbrauchernachfrage und umfassenden Informationen aus Datenbanken über Materialressourcen und deren Bestände. Die in den Softwaremodulen des Systems eingebetteten Algorithmen übersetzen zunächst den Bedarf an Fertigprodukten in die benötigte Gesamtmenge an Ausgangsmaterialressourcen. Die Programme berechnen dann den Bedarf an Einsatzmaterialressourcen, Halbfertigprodukten und unfertigen Mengen auf der Grundlage von Informationen über die entsprechenden Lagerbestände und geben Bestellungen für Mengen an Einsatzmaterialressourcen für Produktionsbereiche (Montagebereiche) von Fertigprodukten auf. Die Bestellungen richten sich nach dem in Nomenklatur und Volumen spezifizierten Bedarf an materiellen Ressourcen sowie dem Zeitpunkt ihrer Lieferung an die entsprechenden Arbeitsplätze und Lager.
Nach Abschluss der erforderlichen Berechnungen wird im Informations- und Rechenzentrum des Unternehmens ein Ausgabesatz von Maschinendiagrammen des MRPI-Systems generiert, der in dokumentarischer Form an Produktions- und Logistikmanager übermittelt wird, um Entscheidungen über die Versorgung der Produktionsstandorte und Lager des Unternehmens mit dem zu treffen notwendigen Ressourcen.
Zu den wichtigsten Eingabeelementen des MRP-Systems gehören:
Die Beschreibung des Materialzustands (Inventory Status File) ist das Haupteingabeelement des MRP-Programms. Es sollte möglichst vollständige Informationen über alle Materialien und Komponenten enthalten, die für die Herstellung des Endprodukts erforderlich sind. Dieses Element muss den Status jedes Materials angeben und bestimmen, ob es vorrätig, im Lager, in aktuellen Bestellungen oder nur für die Bestellung geplant ist, sowie eine Beschreibung, seinen Lagerbestand, Standort, Preis, mögliche Lieferverzögerungen und Lieferanten Einzelheiten. Diese Informationen müssen für jedes am Produktionsprozess beteiligte Material separat bereitgestellt werden;
Ein Produktionsprogramm (Master-Produktionsplan) ist ein optimierter Zeitplan zur Zuweisung von Zeit für die Produktion der erforderlichen Charge des Fertigprodukts B über einen geplanten Zeitraum oder eine Reihe von Zeiträumen. Zunächst wird ein Probeproduktionsprogramm erstellt, anschließend durch zusätzliches Durchlaufen des CRP-Systems (Capacity Requirements Planning) auf Machbarkeit geprüft und festgestellt, ob die Produktionskapazität für die Umsetzung ausreicht. Wird das Produktionsprogramm als machbar erachtet, wird es automatisch zum Hauptprogramm umgeformt und wird zum Eingabeelement des MRP-Systems. Dies ist notwendig, da der Bedarf an Produktionsressourcen für das MRP-System transparent ist, das auf der Grundlage des Produktionsprogramms einen Materialbedarfsplan erstellt. Wenn jedoch Materialien nicht verfügbar sind oder es aus CPR-Sicht nicht möglich ist, den Auftragsplan zu erfüllen, der zur Unterstützung des umzusetzenden Produktionsprogramms erforderlich ist, weist das MRP-System darauf hin, dass Anpassungen erforderlich sind;
Die Stücklistendatei ist eine Liste der Materialien und ihrer Mengen, die zur Herstellung des Produkts erforderlich sind. Somit verfügt jedes Endprodukt über eine eigene Liste von Komponenten. Darüber hinaus enthält es eine Beschreibung des Aufbaus des Endprodukts, also vollständige Informationen zur Technologie seiner Montage. Es ist äußerst wichtig, die Genauigkeit aller Einträge in diesem Element beizubehalten und sie entsprechend anzupassen, wenn Änderungen an der Struktur und/oder Produktionstechnologie des Endprodukts vorgenommen werden.
Denken Sie daran, dass jedes der oben genannten Eingabeelemente eine Computerdatendatei ist, die vom MRP-Programm verwendet wird. Derzeit werden MRP-Systeme auf den unterschiedlichsten Hardwareplattformen implementiert und sind als Module in den meisten Finanz- und Wirtschaftssystemen enthalten. Sein Arbeitszyklus besteht aus den folgenden Hauptphasen:
1. Zunächst ermittelt das MRP-System anhand der Analyse des angenommenen Produktionsprogramms den optimalen Produktionsplan für den geplanten Zeitraum.
3. In diesem Schritt wird auf der Grundlage des genehmigten Produktionsprogramms und der Bestellungen für nicht darin enthaltene Komponenten der Gesamtbedarf für jedes einzelne Material gemäß der Komponentenliste des Endprodukts berechnet.
Nettobedarf = Gesamtbedarf - Lagerbestand - Sicherheitsbestand Reservierung für andere Zwecke,
wobei der Nettobedarf der Bedarf an der Beschaffung materieller Ressourcen ist;
Gesamtnachfrage – der Bedarf an materiellen Ressourcen zur Erfüllung eines bestimmten Produktionsprogramms;
vorhandener Bestand – zur Produktion materieller Ressourcen freigegeben;
Reservierung für andere Zwecke – materielle Ressourcen werden für die Anpassung des Produktionsprogramms reserviert.
4. Aus dem Gesamtbedarf wird unter Berücksichtigung der Materialart der Nettobedarf für jeden Zeitraum nach der angegebenen Formel berechnet. Wenn der Nettobedarf für ein Material größer als Null ist, erstellt das System automatisch eine Bestellung für das Material.
5. Alle Bestellungen, die vor dem aktuellen Planungszeitraum erstellt wurden, werden überprüft und gegebenenfalls geändert, um vorzeitige Lieferungen und Lieferverzögerungen von Lieferanten zu verhindern.
Durch diese Änderungen wird automatisch die Materialstatusbeschreibung geändert, sodass für jedes einzelne Material ein Bestellplan für den gesamten Planungszeitraum erstellt wird, dessen Durchsetzung zur Unterstützung des Produktionsprogramms erforderlich ist.
3. Ergebnisse des MRP-Systems
Die Hauptergebnisse des MRP-Systems sind:
Der Plan für geplante Bestellungen legt fest, wie viel von jedem Material in jedem im Planungszeitraum berücksichtigten Zeitraum bestellt werden muss. Der Bestellplan dient als Leitfaden für die weitere Zusammenarbeit mit Lieferanten und legt insbesondere das Produktionsprogramm für die interne Fertigung von Komponenten (sofern vorhanden) fest;
Änderungen in Planaufträgen sind Modifikationen an zuvor geplanten Aufträgen. Bestellungen können storniert, geändert oder verzögert oder verschoben werden.
Darüber hinaus generiert das A/HR-System einige zusätzliche Ergebnisse in Form von Berichten, deren Zweck es ist, Manager auf „Engpässe“ während des Planungszeitraums aufmerksam zu machen;
Der Zweck des Ausnahmeberichts besteht darin, den Benutzer im Voraus über erforderliche Zeiträume im Planungszeitraum zu informieren besondere Aufmerksamkeit und wo ein Eingreifen des externen Managements erforderlich sein kann. Typische Beispiele für Situationen, die in diesem Bericht berücksichtigt werden sollten, können unerwartet verspätete Bestellungen von Komponenten, überschüssige Komponenten in Lagern usw. sein;
Der Performance Report ist der Hauptindikator für den korrekten Betrieb des MRP-Systems und informiert den Benutzer über kritische Situationen, die während des Planungsprozesses aufgetreten sind (z. B. vollständige Erschöpfung der Sicherheitsbestände einzelner Komponenten), sowie über alle Systemfehler die während des Betriebs des MRP-Programms entstehen;
Beim Planungsbericht handelt es sich um Informationen, die dazu dienen, Prognosen über mögliche zukünftige Änderungen der Produktmengen und -eigenschaften zu erstellen und den langfristigen Materialbedarf zu planen.
Durch den Einsatz eines MRP-Systems zur Planung des Produktionsbedarfs können Sie somit den Zeitpunkt des Eingangs jedes Materials optimieren, wodurch die Lagerkosten erheblich gesenkt und die Produktionsabrechnung erleichtert werden.
Mikrologistiksysteme, die auf dem MRP/-Ansatz basieren, haben Nachteile und Einschränkungen, zu denen die wichtigsten gehören:
Ein erheblicher Aufwand an Berechnungen, Vorbereitung und Vorverarbeitung einer großen Menge an Ausgangsinformationen, was die Dauer des Produktionszeitraums und des Logistikzyklus verlängert;
Ein Anstieg der Logistikkosten für die Auftragsabwicklung und den Transport, da das Unternehmen bestrebt ist, die Lagerbestände zu reduzieren oder auf die Produktion von Fertigprodukten in kleinen Mengen mit hoher Frequenz umzustellen;
Unempfindlichkeit gegenüber kurzfristigen Nachfrageänderungen, da diese auf der Kontrolle und Auffüllung der Lagerbestände an festen Bestellpunkten basieren;
Aufgrund seiner Größe und Überlastung kommt es zu einer erheblichen Anzahl von Ausfällen im System.
Diese Mängel überlagern sich mit dem allgemeinen Mangel, der allen Mikrologistiksystemen vom Typ „Push“ (Push-Systeme) innewohnt, zu denen auch MRPI-Systeme gehören, nämlich eine unzureichend strenge Nachfrageverfolgung mit der obligatorischen Anwesenheit von Sicherheitsbeständen.
Ein Push-Mikrologistiksystem zeichnet sich durch die Herstellung von Teilen, Komponenten, Halbzeugen und deren Montage zu Fertigprodukten nach einem streng definierten Produktionsplan aus. Dadurch werden Materialressourcen und das Volumen der laufenden Arbeiten sozusagen von einem Glied des produktionsinternen Logistiksystems zum anderen „geschoben“ und das fertige Produkt gelangt dann in das Vertriebsnetz. In einem solchen System ist es nur durch die Schaffung von Überproduktions- und (oder) Sicherheitsbeständen zwischen den üblicherweise aufgerufenen Gliedern des Logistiksystems möglich, Störungen im Produktionsprozess zu verhindern und Nachfrageänderungen zu berücksichtigen Pufferbestände. Ihre Anwesenheit verlangsamt den Umschlag des Betriebskapitals des Unternehmens, erhöht die Kosten für Fertigprodukte, gewährleistet jedoch eine größere Stabilität des Logistiksystems bei starken Nachfrageschwankungen und Unzuverlässigkeit der Lieferanten materieller Ressourcen im Vergleich zu auf Gerechtigkeit basierenden Logistiksystemen -in-time-Konzept.
MRPI-Systeme werden vor allem dann eingesetzt, wenn die Nachfrage nach Inputmaterialien stark von der Verbrauchernachfrage nach Endprodukten abhängt. Das MRPI-System kann mit einem breiten Spektrum an Materialressourcen arbeiten (sortimentübergreifende Ausgangsmaterialflüsse). Der Einsatz von MRPI-Systemen ermöglicht es Unternehmen, die gleichen Ziele wie beim Einsatz der JIT-Technologie zu erreichen, insbesondere eine Verkürzung der Dauer des gesamten Logistikzyklus und die Beseitigung überschüssiger Lagerbestände, wenn die Zeit für die Entscheidungsfindung bei der Verwaltung von Produktionsabläufen fehlt und Einkaufsressourcen ist vergleichbar mit der Häufigkeit von Nachfrageänderungen.
Die festgestellten Mängel und die begrenzte Nutzung von MRP I erforderten die Entwicklung einer zweiten Generation dieser Systeme, die als MRPII-System bezeichnet wurde. Dabei handelt es sich um integrierte Mikrologistiksysteme, die Finanzplanung und Logistikabläufe umfassen. MRPII-Systeme sind ein effektives unternehmensinternes Planungstool, mit dem Sie das Logistikkonzept der Integration funktionaler Unternehmensbereiche bei der Steuerung von Materialflüssen in die Praxis umsetzen können. Der Vorteil dieser Systeme gegenüber MRPI-Systemen besteht in einer umfassenderen Befriedigung der Verbrauchernachfrage, die durch eine Verkürzung der Produktionszyklen, eine Reduzierung der Lagerbestände, eine bessere Organisation der Lieferungen und eine schnellere Reaktion auf Nachfrageänderungen erreicht wird. MRP II-Systeme bieten eine größere Planungsflexibilität und senken die Logistikkosten für die Bestandsverwaltung.
Das MRPI-System ist die Hauptkomponente des MRPII-Systems. Wichtiger Platz Das MRPII-System ist mit Algorithmen zur Prognose der Nachfrage, des Bedarfs an Materialressourcen und der Lagerbestände ausgestattet. Im Vergleich zum MRPI-System wird zusätzlich eine Reihe von Aufgaben gelöst, um den Bestand an Materialressourcen, das Volumen der laufenden Arbeiten und Fertigprodukte am Computer zu überwachen und zu regulieren: Auswahl einer Strategie zur Bestandsauffüllung, Berechnung kritischer Punkte und Bestellung Punkte, Analyse der Bestandsstruktur nach der ABC-Methode, Überbestände usw.
Moderne Mikroprozessortechnik und Software ermöglichte es, Mikrologistiksysteme auf Basis des MRPII-Schemas in Echtzeit („online“) mit täglichen Datenbankaktualisierungen in der Praxis zu testen, was die Effizienz der Planung und Verwaltung von Materialflüssen deutlich steigerte.
In vielen Ländern wurde versucht, kombinierte MRPII-KANBAN-Systeme zu schaffen, um die Mängel, die jedem dieser Systeme innewohnen, gegenseitig zu beseitigen. Typischerweise werden solche kombinierten MRPII-Systeme für die Planung und Prognose von Bedarf, Verkauf und Einkauf verwendet, und das KANBAN-System wird für die operative Produktionssteuerung verwendet. Einige westliche Forscher nennen dieses integrierte Mikrologistiksystem MRP III.
Aus betrieblicher Sicht kann das Logistikkonzept der „Bedarfs-/Ressourcenplanung“ auch in Distributionssystemen eingesetzt werden, welches die Grundlage für die Schaffung externer mikrologistischer „Produkt-/Ressourcenplanungs“-Systeme (DRP) war. DRP-Systeme sind die Erweiterung der Logik des Aufbaus von MRP-Systemen auf die Vertriebskanäle von Fertigprodukten. Obwohl diese Systeme auf einem gemeinsamen Logistikkonzept der „Bedarfs-/Ressourcenplanung“ basieren, unterscheiden sie sich gleichzeitig erheblich.
MRP-Systeme werden durch einen Produktionsplan bestimmt, der vom Hersteller des Endprodukts geregelt und kontrolliert wird. Die Funktionsweise von DRP-Systemen basiert auf der Verbrauchernachfrage, die nicht vom Unternehmen kontrolliert wird. Daher zeichnen sich MRP-Systeme in der Regel durch eine größere Stabilität aus, im Gegensatz zu DRP-Systemen, die unter Bedingungen der Nachfrageunsicherheit arbeiten. Das ist ungewiss Außenumgebung verhängt Zusätzliche Anforderungen und Einschränkungen bei der Bestandsverwaltungspolitik für Fertigprodukte in Vertriebsnetzen. Gleichzeitig steuern MRP-Systeme den Lagerbestand innerhalb der Produktionseinheiten. DRP-Systeme planen und regulieren die Lagerbestände an den Standorten und Lagern des Unternehmens im eigenen Vertriebsnetz oder bei Großhändlern.
Abschluss
Die Zukunft liegt natürlich in der vollständigen Automatisierung des Speicherns und Abrufens von Informationen und der größtmöglichen Automatisierung der Entscheidungsfindung auf Basis dieser Informationen. Der Grad der Automatisierung der Entscheidungsfindung hängt von vielen Faktoren ab, beispielsweise von den technischen und finanziellen Möglichkeiten des Unternehmens, der Marktstabilität, den Besonderheiten der Unternehmensaktivitäten usw. Heutzutage können komplexe Probleme der Finanzbuchhaltung und -planung auftreten lässt sich am effektivsten durch die Einführung von MRP-Systemen in der Unternehmensklasse lösen.
Solche Systeme ermöglichen es, Beziehungen zwischen verschiedenen Funktionsbereichen im Unternehmen herzustellen, große Informationsmengen zu speichern, einen schnellen Zugriff darauf zu ermöglichen, Informationen in der für die Entscheidungsfindung erforderlichen Form darzustellen usw., aber gleichzeitig auch deren Umsetzung erfordert erhebliche finanzielle Investitionen.
Im Rahmen der Zielsetzung wurden folgende Aufgaben gestellt und gelöst:
1. die Merkmale des MRP-Systems und seine Entstehungsgeschichte werden dargelegt;
2. die Ziele des MRP-Systems und Elemente des Systems werden angegeben;
3. Die Merkmale der erzielten Ergebnisse des MRP-Systems werden angegeben.
Aufgaben
Problem 1
Bestimmen Sie anhand der ABC-Analyse die Parameter von Beständen, die keiner Bestandskontrolle (Klasse) bedürfen, wenn folgende Daten bekannt sind:
Lagerbezeichnung |
|||||
Nachfragevolumen (Stück) |
|||||
Preis, reiben.) |
Lassen Sie uns den Anteil jeder Aktie am Gesamtvolumen (5900 Stück) ermitteln. A1=1,69 %; A2=5,08 %; A3=16,95 %; B1=8,47 %; B3=67,8 %.
Berechnen wir diesen Anteil mit einer kumulierten Summe (dieser Vorgang ist technischer Natur und dient der bequemeren weiteren Bestimmung der Grenzen für ABC-Gruppen). Wir verwenden die traditionelle Einteilung in drei Gruppen nach dem Indikator „Anteil an der Gesamtsumme“: A – bis zu 50 %, B – 50–80 % und C – 80–100 %. Diese Verteilung entspricht voll und ganz den Zielen eines Lagers eines Großhandelsunternehmens bzw Einzelhandelsnetzwerk. Es stellt sich heraus, dass die Aktie B3 in Gruppe A fällt, die Aktie A3 in Gruppe B, die Aktien A1, A2, B1 in Gruppe C.
Aufgabe 2.
Das Unternehmen benötigt 1.200 Bohrmaschinen pro Jahr. Die Kosten für die Bestellung betragen 50 Rubel und die Lagerkosten betragen 40 % der Kosten für eine Bohrmaschine, was 300 Rubel entspricht. Bestimmen Sie die wirtschaftliche Größe des Auftrags, die Anzahl der Aufträge pro Jahr und den Zeitraum zwischen zwei Aufträgen, wenn die Anzahl der Arbeitstage 250 beträgt.
1. Rz = 1200*300=360000 Rubel.
2. OR = Quadratwurzel von (2*Zt*TZ1)/TZ2,
wobei Zt das erforderliche Wareneinkaufsvolumen pro Jahr ist;
TK1 – die Höhe der laufenden Kosten für Platzierung, Lieferung;
TZ2 – Lagerkosten.
ODER = kor. Quadrat. von (2*1200*50)/120 = 347/120=3 mal.
3. Zeitraum zwischen zwei Bestellungen = 250/3=83 Tage.
Aufgabe 3.
Zwei Unternehmen A und B, die 200 Kilometer voneinander entfernt liegen, verkaufen die gleiche Art von Produkt. Unternehmen A verkauft Waren zu einem Preis von 60 Rubel. Firma B zum Preis von 85 Rubel. Bestimmen Sie die Marktgrenzen für jedes Unternehmen. Lassen Sie Unternehmen A ein Großhandelslager in einer Entfernung von 50 km errichten. Der Transport kostete 12 Rubel. pro km. Die Kosten für die Lagerung von Waren in einem Lagerhaus betragen 15 Rubel. für eine Einheit. Definieren Sie neue Marktgrenzen.
1. Marktgrenzen für Unternehmen A = 60/200 = 300 m.
Marktgrenzen für Unternehmen B = 85 / 200 = 425m.
2. Ra = 60+15 = 75 Rubel.
Neue Grenzen für Unternehmen A = 75/50+0,3 = 1,5+0,3 = 1,8 km.
Durch die Eröffnung eines neuen Großhandelslagers erweiterte Unternehmen A seine Marktgrenzen, obwohl der Preis dadurch auf 75 Rubel erhöht werden musste.
Problem 4
Bestimmen Sie den Produktionsort der Ware anhand folgender Ausgangsdaten:
Die Tarife für den Gütertransport sind gleich: (in Rubel/Tonne) für K1 – 10; K2 – 8; P1 – 5; P2 – 9.
Die Liefermengen (in Tonnen) sind gleich: für K1 - 250; K2 – 150; P1 – 200; P2-200.
Ihre Koordinaten sind in der Tabelle angegeben:
1. Ermitteln Sie die Entfernung, die Kunden und Lieferanten zum gewünschten Unternehmen zurücklegen.
Sk1 = 250/10 = 25 km.
2. Berücksichtigen wir die Situation, wenn die Rohstoffe in der gewünschten Anlage, nennen wir sie Anlage, ankommen und dann das fertige Produkt beim Kunden ankommt.
Suchen wir einen Punkt zwischen K1 und P1, er ist gleich ((150+50/2) +(200+150/2). Wir erhalten einen Punkt mit den Koordinaten (100;175).
Nun finden wir auf die gleiche Weise den Punkt zwischen K2 und P2, er ist gleich (375; 450).
Bestimmen wir nun die Koordinaten der benötigten Anlage ((100+375/2)+(175+450/2)). Wir erhalten einen Punkt mit den Koordinaten (238; 313).
Aufgabe 5.
Der Produktionsleiter legt den Mindestumsatz für einen Tag fest, um die Produktion aufrechtzuerhalten. Bestimmen Sie die Höhe des Umsatzes, wenn die in der Tabelle angegebenen Daten bekannt sind (FC = 10.000 Rubel):
Produktpreis - 50 Rubel;
Verkaufsvolumen - 500 Stück.
Variable Kosten - 30 Rubel.
Vvyr. = 10000 / (50-30) = 500 Rubel.
Das daraus resultierende Umsatzvolumen wird lediglich zur Deckung der Kosten und nicht zur Erzielung eines Gewinns ausreichen.
Aufgabe 6.
Der Produktionsleiter legt den Mindestumsatz für 1 Tag fest, um die Produktion von 4 Gütern aufrechtzuerhalten. Bestimmen Sie das Umsatzvolumen, wenn die folgenden Daten bekannt sind, die in der Tabelle bei FC = 20.000 Rubel angegeben sind.
Warenpreis (in Rubel) |
||||
Verkaufsvolumen (in Einheiten) |
||||
Variable Kosten (in Rubel) |
Vvyr. = 20000 / 20-30 = -2000 Stück.
Vvyr. = 20000 / 10-30 = -1000 Stück.
Vvyr. = 20000 / 5-30 = -800 Stück.
Vvyr. = 20000 / 15-30 = -1333Stk.
Der Unternehmensleiter muss dringend Maßnahmen ergreifen, um die aktuelle Situation zu verbessern. In diesem Fall können wir entweder eine Preiserhöhung empfehlen, die in Zukunft zum Verlust von Kunden führen kann, wenn der festgelegte Preis über den Marktpreisen liegt, oder eine Kostensenkung.
Literaturverzeichnis
1. Gadzhinsky A.M. Logistik. Lehrbuch für Universitäten. M., 2001.-259 S.
2. Logistik. Bildungsdorf / Ed. B.A. Anikina.- M.: INFRA-M, 2000.-375 S.
3. Nerush Yu.M. Kommerzielle Logistik. M.: Banken und Börsen, UNITY, 2002.-213 S.
4. Workshop zum Thema Logistik. Lehrbuch Gestellt. B.A. Anikina, M.: INFRA - M, 2002.-198p.
5. Smekhov A.A. Grundlagen der Transportlogistik. M.: Verkehr, 2000.-245 S.
Logistik. Bildungsdorf / Ed. B.A. Anikina.- M.: INFRA-M, 2000.-178 S.
Gadzhinsky A.M. Logistik. Lehrbuch für Universitäten. M., 2001.-85p.
Nerush Yu.M. Kommerzielle Logistik. M.: Banken und Börsen, UNITY, 2002.-123p.
Workshop zum Thema Logistik. Lehrbuch Gestellt. B.A. Anikina, M.: INFRA - M, 2002.-28p.
Smekhov A.A. Grundlagen der Transportlogistik. M.: Verkehr, 2000.-214 S.
Einleitung (Zweck)………………………………………………………………3-5
1. Methodik zur Planung des Materialbedarfs eines Unternehmens (MRP). Hauptziele von MRP-Systemen. Grundlegende Bestimmungen des MRP-Konzepts……………………………………………………………………………………..6-8
2.MRP II-Standard. Die Essenz des MRPII-Konzepts………………………….8-10
3. ERP-Systeme. Hauptfunktionsblöcke eines ERP-Systems. Vergleichende Analyse von MRP- und ERP-Systemen……………………………………..10-15
4. APS-Systeme. Struktur des APS-Modells. Grundkonzepte von APS-Systemen……………………………………………………………………………………...15-18
5. CSRP-Systeme: Enterprise Resource Planning, synchronisiert mit den Anforderungen und Erwartungen des Käufers…………………………………….18-21
6. BPM-Systeme……………………………………………………………..21-23
7. Microsoft Dynamics-Software: Microsoft Dynamics AX, Microsoft Dynamics NAV. Methoden zur Implementierung von Systemen der Microsoft Business Solutions-Gruppe…………………………………………………………...23-26
8. Einheitliches Modell zur Organisation der Implementierung von IT-Lösungen in der Microsoft Solutions Framework (MSF)-Methodik……………………….….27-29
9. Oracle-Geschäftsanwendungen: Oracle E-Business Suite für die effektive Verwaltung von Unternehmensaktivitäten………………...29-31
10. Methoden der Oracle Corporation: PJM (Projektmanagementmethode), OBM (Oracle-Geschäftsmodelle), CDM (kundenspezifische Entwicklungsmethode), AIM (Anwendungsimplementierungsmethode)…………………………………... 31 -34
Fazit…………………………………………………………...35-36
Referenzliste………………………………………………………......37
Einführung
Der wichtigste Faktor für die Schaffung eines langfristigen Wettbewerbsvorteils und die Steigerung der Investitionsattraktivität des Unternehmens sind heute optimale betriebswirtschaftliche Strategien. Effektives Management ist eine Ressource wie Geld oder Sachwerte. Diese Ressource hilft dabei, dynamisch auf die sich ständig ändernde Marktsituation zu reagieren, alle Aspekte der Unternehmensaktivitäten zu kontrollieren, „Engpässe“ schnell zu erkennen und die Anstrengungen genau dort zu konzentrieren, wo sie am meisten benötigt werden dieser Moment. Wir hören ständig, dass russische Unternehmen nicht mit westlichen Herstellern konkurrieren können, dass unsere Technologien nicht so weit entwickelt sind und dass die Qualität russischer Produkte denen ihrer ausländischen Pendants zu minderwertig ist. Das Problem besteht darin, dass russische Manager mit mindestens zwei Problemen im Management konfrontiert wurden: Es stellte sich heraus, dass die Indikatoren und Verfahren, die zuvor zur Analyse und Planung der Aktivitäten des Unternehmens verwendet wurden (z. B. die Menge der produzierten Produkte), dies nicht zulassen sie erfolgreich zu konkurrieren; Das Aufkommen von Wettbewerbern erschwert nicht nur die Erzielung der üblichen Mehrgewinne, sondern reduziert sie manchmal sogar auf Null. IN moderne Verhältnisse effektives Management repräsentiert wertvolle Ressource Organisation sowie finanzielle, materielle, personelle und andere Ressourcen. Folglich wird die Steigerung der Effizienz der Managementaktivitäten zu einem der Bereiche zur Verbesserung der Aktivitäten des gesamten Unternehmens. Der offensichtlichste Weg, die Effizienz des Arbeitsprozesses zu steigern, ist seine Automatisierung. Aber was beispielsweise für einen streng formalisierten Produktionsprozess gilt, ist für einen so eleganten Bereich wie das Management keineswegs so offensichtlich. Bei der Entwicklung von Informationssystemen (IS) ist es notwendig, den produktiven Teil des Unternehmens anzustreben und nicht nur die Möglichkeit zu schaffen, einen primitiven Informationssatz zu erstellen, Geschäftsprozesse und andere Implementierungsattribute zu optimieren, sondern auch die Fähigkeit zur analytischen Verarbeitung bereitzustellen Informationen auf der Ebene von Produkteigenschaften, Technologien, Ressourcen usw. Es ist kein Geheimnis, dass der Automatisierungsansatz oft so lautet: Wir müssen alles automatisieren, und deshalb kaufen wir ein leistungsstarkes integriertes System und implementieren es alle Module Modul. Doch erst später stellt sich heraus, dass der resultierende Effekt weit hinter den Erwartungen zurückbleibt und das Geld verschwendet wurde. Manchmal ist es notwendig, nur wenige spezialisierte und kostengünstige Anwendungen zu implementieren und diese auf Basis einer Integrationsplattform zu verknüpfen oder bei Bedarf die Funktionalität eines ERP-Systems zu nutzen. Alle diese Probleme können und sollten in der Entwurfsphase gelöst werden, d. h. die Auswahl der Automatisierungstools bewusst angehen und die Kosten mit der erwarteten Wirkung vergleichen. In diesem Fall sollten Sie sich nicht an den Grundsatz „Je mehr Funktionen, desto besser“ halten. Je mehr ein System „kann“, desto teurer ist es und die Wahrscheinlichkeit ist groß, dass nicht alle Funktionen genutzt werden und es sich nicht amortisiert. Derzeit wird intensiv an der Einführung betrieblicher Informationssysteme (KIS) gearbeitet. Auf den Seiten von Zeitschriften und im Internet können Sie sehen große Menge Materialien, die diesen oder jenen Nachwuchs von Monstern verherrlichen und so weiter. Gleichzeitig ist die Spanne sowohl bei den Preisen, den Ausführungsbedingungen als auch bei den erbrachten Leistungen sehr groß. Neben allem anderen werden verschiedene betriebswirtschaftliche Ideologien wie MRP, MRP2, ERP usw. verwendet. Das Schwierigste ist das Bauen einheitliches System, das den Bedürfnissen der Mitarbeiter aller Abteilungen gerecht wird. Jede Abteilung kann über eine eigene Software verfügen, die für ihre eigenen Betriebseigenschaften optimiert ist. Ein Informationssystem kann sie alle in einem integrierten Programm kombinieren, das auf einer einzigen Datenbank arbeitet, sodass alle Abteilungen einfacher Informationen austauschen und miteinander kommunizieren können. Dieser integrierte Ansatz verspricht sich sehr zu lohnen, wenn es den Unternehmen gelingt, das System korrekt zu installieren.
1. Methodik zur Planung des Materialbedarfs eines Unternehmens (MRP). Hauptziele von MRP-Systemen. Grundlegende Bestimmungen des MRP-Konzepts
Das MRP-1-System ist eines der beliebtesten weltweit und basiert auf dem Logistikkonzept der „Anforderungs-/Ressourcenplanung“. Dieses System arbeitet mit Materialien, Komponenten, Halbzeugen und deren Teilen, deren Nachfrage von der Nachfrage nach bestimmten Fertigprodukten abhängt. Die Hauptziele dieses Systems sind die Deckung des Bedarfs an Materialressourcen für die Planung der Produktion und Lieferung an Verbraucher, die Aufrechterhaltung eines niedrigen Bestands an Materialressourcen, unfertigen Erzeugnissen und Fertigwaren sowie die Planung von Produktionsabläufen, Lieferplänen und Einkaufsvorgängen. Das MRP-II-System, ein Bedarfs-/Ressourcenplanungssystem der zweiten Generation, ist ein integriertes Mikrologistiksystem, das Finanzplanung und Logistikabläufe kombiniert. Dieses System ist ein wirksames Planungsinstrument zur Verwirklichung der strategischen Ziele des Unternehmens in den Bereichen Logistik, Marketing, Produktion, Finanzen, Planung und Verwaltung der Organisationsressourcen des Unternehmens, um einen Mindestbestand an Lagerbeständen zu erreichen und gleichzeitig alle Phasen des Produktionsprozesses zu kontrollieren . Der Vorteil von MRP-2-Systemen gegenüber MRP-1-Systemen: bessere Befriedigung der Verbrauchernachfrage, erreicht durch Verkürzung der Produktionszykluszeiten, Reduzierung der Lagerbestände, bessere Organisation der Lieferungen, schnelle Reaktion auf Nachfrageänderungen, größere Planungsflexibilität, was zur Reduzierung der Logistikkosten beiträgt für die Bestandsverwaltung. Grundlegende Mikrologistik-Subsysteme, die auf dem Konzept der „Bedarfs-/Ressourcenplanung“ basieren, sind in der Produktion und Versorgung Systeme der „Material-/Fertigungsbedarfs-/Ressourcenplanung, MRP I/MRP II“ und im Vertrieb (Distribution) „Produkt-/Ressourcenverteilungsplanung“. ”-Systeme (Verteilungsanforderungen/Ressourcenplanung, DRPI/DRPII). Aus diesem Grund wurde die MRP-Methodik (Material Requirements Planning) entwickelt. Die Implementierung eines nach dieser Methodik arbeitenden Systems ist ein Computerprogramm, das es Ihnen ermöglicht, die Versorgung des Produktionsprozesses mit Komponenten optimal zu regulieren und dabei sowohl den Lagerbestand im Lager als auch die Produktionstechnik selbst zu steuern. Das Hauptziel der MRP besteht darin, die Verfügbarkeit der erforderlichen Menge an benötigten Materialien und Komponenten zu jedem Zeitpunkt innerhalb des Planungszeitraums sicherzustellen, zusammen mit einer möglichen Reduzierung der festen Bestände und damit der Entladung des Lagers. Mit anderen Worten: Das MRP-System ermöglicht es Ihnen, die Produktionskapazität optimal auszulasten und gleichzeitig genau so viele Rohstoffe einzukaufen, wie zur Erfüllung des aktuellen Auftragsplans erforderlich und im entsprechenden Produktionszyklus verarbeitet werden können. So können Sie durch die Planung des aktuellen Materialbedarfs Lager mit Rohstoffen und Komponenten (sie werden in genau der Menge eingekauft, die in einem Produktionszyklus verarbeitet und direkt an die Produktionswerkstätten geliefert werden kann) sowie Lager mit Fertigprodukten entladen (Die Produktion erfolgt in strikter Übereinstimmung mit den angenommenen Planaufträgen, und Produkte im Zusammenhang mit dem aktuellen Auftrag müssen termingerecht produziert werden.)
Die ideale Umsetzung des MRP-Konzepts ist in der Realität nicht umsetzbar. Beispielsweise aufgrund möglicher Lieferverzögerungen aus verschiedenen Gründen und anschließendem Produktionsstopp. Deshalb stellen Dispositionssysteme für jeden Fall einen gewissen Sicherheitsbestand an Rohstoffen und Komponenten bereit.
Die Hauptziele von MRP-Systemen sind:
Befriedigung des Bedarfs an Materialien, Komponenten und Produkten zur Planung der Produktion und Lieferung an Kunden;
Aufrechterhaltung eines niedrigen Bestands an Materialressourcen, unfertigen Produkten und Fertigprodukten;
Planung von Produktionsabläufen, Lieferplänen und Einkaufsvorgängen.
Bei der Erreichung dieser Ziele stellt das MRP-System den Fluss geplanter Mengen an Materialressourcen und Produktbeständen für die geplante Zukunft sicher. Das MRP-System ermittelt zunächst, in welchem Zeitrahmen und in welcher Menge Endprodukte produziert werden müssen. Anschließend werden die Zeit und die erforderlichen Mengen an Materialressourcen zur Erfüllung des Produktionsplans bestimmt. Die Eingabe dieses Systems sind Verbraucherbestellungen, unterstützt durch Nachfrageprognosen für die Fertigprodukte des Unternehmens, die im Produktionsplan (Freigabepläne für Fertigprodukte) enthalten sind. Wie bei Mikrologistiksystemen, die auf den Prinzipien des Just-in-Time-Konzepts basieren, steht bei MRPI die Verbrauchernachfrage im Vordergrund.
Das MRPI-Softwarepaket basiert auf systematisierten Produktionsplänen (Endproduktfreigabepläne) (MPS – Master Production Schedule-Modul) in Abhängigkeit von der Verbrauchernachfrage und umfassenden Informationen aus Datenbanken über Materialressourcen und deren Bestände. Die in den Softwaremodulen des Systems eingebetteten Algorithmen übersetzen zunächst den Bedarf an Fertigprodukten in die benötigte Gesamtmenge an Ausgangsmaterialressourcen. Die Programme berechnen dann den Bedarf an Einsatzmaterialressourcen, Halbfertigprodukten und unfertigen Mengen auf der Grundlage von Informationen über die entsprechenden Lagerbestände und geben Bestellungen für Mengen an Einsatzmaterialressourcen für Produktionsbereiche (Montagebereiche) von Fertigprodukten auf. Die Bestellungen richten sich nach dem in Nomenklatur und Volumen spezifizierten Bedarf an materiellen Ressourcen sowie dem Zeitpunkt ihrer Lieferung an die entsprechenden Arbeitsplätze und Lager.
MRP II-Standard. Die Essenz des MRPII-Konzepts
Der MRP II-Standard (Manufacturing Resource Planning) (Abb. 7) ermöglichte die Entwicklung einer auf den Einsatz von Unternehmensinformationssystemen ausgerichteten Planungstechnologie, die die Aufgaben des industriellen Unternehmensmanagements auf operativer Ebene vollständig umreißt. Die wichtigste Funktion von MRPII besteht darin, denjenigen, die Entscheidungen im Bereich des Finanzmanagements treffen, alle notwendigen Informationen zur Verfügung zu stellen. MRP informiert über den Zeitpunkt von Bestellungen und hilft bei der Planung von Zahlungen an Lieferanten. MRP I/CRP liefert Informationen über die Anzahl der wichtigsten Produktionsmitarbeiter, die Höhe der Stundensätze und Zeitvorgaben für die Durchführung technologischer Vorgänge (in der Beschreibung technologischer Routen), über mögliche Überstunden usw., die das Unternehmen annehmen muss Zahlungsverpflichtungen Löhne. Schließlich meldet MRP das Volumen und den Zeitpunkt der Produktlieferungen an Kunden, was Cashflow-Prognosen ermöglicht.
Ausgearbeitete detaillierte Pläne, die der Ausführung unterliegen, werden durch die Berechnung der Produktkosten, die Abrechnung von Verkäufen, Lieferungen und Produktionsvorgängen in den Kosten berücksichtigt. Die errechneten Ist-Kosten werden mit den Plan- (bzw. Norm-)Kosten verglichen und Abweichungen dienen als Grundlage für die Abnahme Managemententscheidungen bezogen auf die folgenden Planungszeiträume.
Die Integration wird durch die Vereinheitlichung aller wesentlichen Funktionsbereiche des Unternehmens auf operativer Ebene (innerhalb eines Planungshorizonts von bis zu einem Jahr) in Bezug auf Material- und Finanzströme im Unternehmen gewährleistet. MRP II deckt Unternehmensfunktionen wie Produktionsplanung, Produktionsversorgung, Produktverkäufe, Produktionsplanausführung, Kostenrechnung, Lagerbuchhaltung, Bedarfsmanagement usw. ab. Gemäß dem „MRPII-Standardsystem“ in einem darauf basierenden Informationssystem MRP-Standard II müssen folgende 16 Gruppen von Funktionen implementiert werden:
Vertriebs- und Betriebsplanung.
Nachfragemanagement.
Erstellen eines Produktionsplans (Master Production Scheduling).
Materialbedarfsplanung.
Stückliste.
Lagerverwaltung (Inventory Transaction Subsystem).
Geplante Lieferungen (Subsystem für geplante Wareneingänge).
Levelmanagement Produktionswerkstatt(Shop-Flow-Steuerung).
Kapazitätsbedarfsplanung.
Eingabe-/Ausgabesteuerung.
Logistik (Einkauf).
Planung von Vertriebsressourcen.
Planung und Steuerung von Produktionsabläufen (Tooling Planning and Control).
Finanzielle Planung.
Simulation.
Leistungsmessung.
Das auf der Grundlage von MRPII implementierte IS ist für die effektive Planung aller Unternehmensressourcen (einschließlich Finanz- und Personalressourcen) konzipiert. Der Kern des MRPII-Konzepts besteht darin, dass die Prognose, Planung und Steuerung der Produktion über den gesamten Lebenszyklus von Produkten erfolgt, vom Einkauf der Rohstoffe bis zum Versand der Produkte an den Verbraucher. Die Aufgabe von Informationssystemen des MRP Klasse II ist die optimale Gestaltung des Materialflusses (Rohstoffe), Halbzeuge (Komponenten) und Fertigprodukte. Das System zielt darauf ab, die wichtigsten vom Unternehmen implementierten Prozesse zu integrieren: Planung und Kontrolle der Planumsetzung, Kosten, Lieferung, Produktion, Verkauf, Bestandsverwaltung, Belastung des Anlagevermögens usw. Ein solches System integriert eine große Anzahl von Modulen, die Ergebnisse davon werden vom MRPII-System im Allgemeinen analysiert, was seine Flexibilität in Bezug auf verschiedene gewährleistet externe Faktoren- zum Beispiel aktuelle Nachfrage nach Produkten, Preisangebote usw. (Abb. 1.)
3. ERP-Systeme. Hauptfunktionsblöcke eines ERP-Systems. Vergleichende Analyse von MRP- und ERP-Systemen
ERP-Systeme sind Computersysteme, die dazu dienen, die Geschäftstransaktionen einer Organisation zu verarbeiten und eine umfassende und operative (Echtzeit-)Planung, Produktion und Kundenbetreuung zu ermöglichen. Insbesondere ERP-Systeme haben die folgenden Eigenschaften:
Dabei handelt es sich um vorgefertigte Software, die für eine Client-Server-Umgebung entwickelt wurde, sowohl traditionell als auch basierend auf Internet-Technologien;
diese Systeme integrieren die meisten Geschäftsprozesse;
Sie wickeln die meisten Geschäftstransaktionen der Organisation ab.
diese Systeme nutzen eine Datenbank des gesamten Unternehmens, in der jede Datenprobe in der Regel einmal gespeichert wird;
Sie bieten Zugriff auf Echtzeitdaten:
In einigen Fällen ermöglichen diese Systeme die Integration der Verarbeitung von Geschäftsvorfällen und Planungsaktivitäten (z. B. Produktionsplanung).
Darüber hinaus verfügen ERP-Systeme zunehmend über zusätzliche Eigenschaften wie:
Unterstützung mehrerer Währungen und Sprachen (was für multinationale Unternehmen sehr wichtig ist);
Unterstützung für bestimmte Branchen (SAP unterstützt beispielsweise eine große Anzahl von Branchen, darunter Öl und Gas, Gesundheitswesen, Chemie und Banken);
die Möglichkeit zur Konfiguration (Anpassung) ohne Programmierung (z. B. durch Installation von „Schaltern“).
Lassen Sie uns die wichtigsten Vorteile der Implementierung und Nutzung eines ERP-Systems auflisten:
ERP-Systeme integrieren die Aktivitäten eines Unternehmens. Enterprise-Resource-Planning-Prozesse sind funktionsübergreifend und zwingen das Unternehmen dazu, über traditionelle, funktionale und lokale Grenzen hinauszugehen. Darüber hinaus sind häufig verschiedene Geschäftsprozesse eines Unternehmens miteinander verknüpft. Darüber hinaus werden Daten, die bisher auf verschiedenen heterogenen Systemen lagen, nun in einem einzigen System integriert. ERP-Systeme nutzen „Best Practices“. Es gibt mehr als tausend Enterprise-Resource-Planning-Systeme die besten Wege Organisation von Geschäftsprozessen. Diese Best Practices können genutzt werden, um die Leistung von Unternehmen zu verbessern. Die Auswahl und Einführung von ERP-Systemen erfordert die Umsetzung solcher Best Practices. ERP-Systeme ermöglichen eine organisatorische Standardisierung. Enterprise-Resource-Planning-Systeme ermöglichen eine organisatorische Standardisierung zwischen verschiedenen geografisch getrennten Einheiten. Dadurch können Abteilungen mit nicht standardmäßigen Prozessen mit anderen Abteilungen mit effektiven Prozessen gleichgesetzt werden. Darüber hinaus kann das Unternehmen nach außen als eine einheitliche Organisation auftreten. Anstatt unterschiedliche Dokumente zu erhalten, wenn ein Unternehmen mit verschiedenen Niederlassungen oder Betrieben eines bestimmten Unternehmens zu tun hat, kann dieses Unternehmen der Welt als ein gemeinsames Image präsentiert werden, was zu einer Verbesserung seines Images führt. ERP-Systeme beseitigen Informationsasymmetrien. Enterprise-Resource-Planning-Systeme speichern alle Informationen in derselben Masterdatenbank und beseitigen so zahlreiche Informationsinkonsistenzen. Dies führt zu mehreren Ergebnissen. Erstens bietet es eine bessere Kontrolle. Wenn ein Benutzer seine Arbeit nicht erledigt, sieht der andere, dass etwas nicht getan wurde. Zweitens eröffnet es den Zugang zu Informationen für diejenigen, die sie benötigen; Im Idealfall stehen verbesserte Informationen für die Entscheidungsfindung zur Verfügung. Drittens sind Informationen nicht mehr Gegenstand der Vermittlung, da sie sowohl dem Management als auch den Mitarbeitern des Unternehmens zugänglich werden. Viertens kann die Organisation „flach“ werden: Da Informationen weithin verfügbar sind, besteht kein Bedarf an zusätzlichen geringwertigen Arbeitskräften, deren Haupttätigkeit darin besteht, Informationen für die Verteilung an das Management und die Mitarbeiter des Unternehmens vorzubereiten. ERP-Systeme stellen Informationen in Echtzeit bereit. In herkömmlichen Systemen werden große Mengen an Informationen auf Papier erfasst und dann an einen anderen Teil der Organisation übertragen, wo sie entweder neu formatiert (normalerweise aggregiert) oder in ein Computerformat übertragen werden. Bei ERP-Systemen werden viele Informationen an der Quelle gesammelt und direkt in den Computer eingegeben. Dadurch werden die Informationen sofort für andere verfügbar. ERP-Systeme ermöglichen den gleichzeitigen Zugriff auf dieselben Daten für Planung und Steuerung. Enterprise-Resource-Planning-Systeme verwenden eine einzige Datenbank, in der die meisten Informationen nur einmal eingegeben werden. Da die Daten in Echtzeit verfügbar sind, haben praktisch alle Benutzer in einer Organisation Zugriff auf dieselben Informationen zur Planung und Steuerung. Dies kann im Vergleich zu zu einer konsistenteren Planung und Verwaltung führen traditionelle Systeme. ERP-Systeme fördern die Kommunikation und Zusammenarbeit innerhalb einer Organisation. Enterprise-Resource-Planning-Systeme fördern auch die Kommunikation und Zusammenarbeit innerhalb einer Organisation (zwischen verschiedenen funktionalen und geografisch getrennten Einheiten). Das Vorhandensein miteinander verbundener Prozesse führt dazu, dass funktionale und geografisch getrennte Abteilungen interagieren und zusammenarbeiten. Die Standardisierung von Prozessen fördert auch die Zusammenarbeit, da es weniger Reibungsverluste zwischen den Prozessen gibt. Darüber hinaus fördert eine einzige Datenbank die Interoperabilität, indem sie jede geografisch getrennte und funktionale Abteilung mit den benötigten Informationen versorgt. ERP-Systeme erleichtern die Kommunikation und Zusammenarbeit zwischen Organisationen. Ein ERP-System bietet eine Informationsautobahn für die Organisation der Interaktion und Zusammenarbeit mit anderen Organisationen. Unternehmen öffnen ihre Datenbanken zunehmend für Partner, um die Beschaffung und andere Aktivitäten zu erleichtern. Zu dieses System hat funktioniert, es wird ein einheitliches Archiv benötigt, das Partner nutzen können; und ERP-Systeme können verwendet werden, um einen solchen Austausch zu erleichtern.
Lasst uns ausführen Vergleichsmerkmale Systeme zweier Klassen - ERP und MRPII. Es sei gleich darauf hingewiesen, dass sowohl bei MRPII-Systemen als auch bei ERP-Systemen die Produktion im Vordergrund steht. Sie entwickeln sich natürlich als Reaktion auf die Marktanforderungen weiter: Neue Funktionen werden hinzugefügt, Lösungen werden auf neue Technologieplattformen übertragen. Allerdings bleiben Produktionssubsysteme im Mittelpunkt der betrachteten Systeme und die Unterschiede zwischen MRPII/ERP-Systemen liegen gerade im Bereich der Produktionsplanung. Diese Unterschiede hängen mit der Tiefe der Planungsumsetzung zusammen, die auf die Ausrichtung dieser Systeme auf unterschiedliche Marktsegmente zurückzuführen ist. ERP-Systeme werden für große multifunktionale und geografisch verteilte Produktionsunternehmen (z. B. Holdinggesellschaften, TNCs, Finanzindustriekonzerne usw.) erstellt. MRPII-Systeme richten sich an den Markt der mittelständischen Unternehmen, die nicht die volle Leistungsfähigkeit von ERP-Systemen benötigen. Eigentlich ist der Unterschied zwischen MRPII- und ERP-Systemen bereits an der Bezeichnung erkennbar: einerseits Enterprise Resources Planning, andererseits Manufacturing Resources Planning. Die wesentlichen Unterschiede zwischen ERP und MRP II lassen sich durch folgende Formel ausdrücken: ERP = MRPII + Umsetzung aller Produktionsarten + Integration der Ressourcenplanung für verschiedene Bereiche der Unternehmenstätigkeit + bereichsübergreifende Planung.
Wir können die wesentlichen Unterschiede zwischen ERP-Systemen und MRP-II-Systemen formulieren:
─ Einsatzmöglichkeit in verschiedenen Unternehmenstypen;
─ Unterstützung bei der Ressourcenplanung in verschiedenen Bereichen der Unternehmenstätigkeit (nicht nur Produktion);
─ die Fähigkeit, Ressourcen eines komplexen, branchenübergreifenden Unternehmens oder Konzerns zu planen und zu verwalten;
─ ERP-Systeme konzentrieren sich im Gegensatz zu MRP II auf die Verwaltung eines „virtuellen Unternehmens“. Ein virtuelles Unternehmen, das die Interaktion von Produktion, Lieferanten, Partnern und Verbrauchern widerspiegelt, kann aus autonom operierenden Unternehmen oder einem Konzern oder einem geografisch verteilten Unternehmen oder einem temporären Zusammenschluss von Unternehmen bestehen, die an einem Projekt, einem Regierungsprogramm usw. arbeiten;
─ Dem ERP werden Verwaltungsmechanismen hinzugefügt Transnationale Unternehmen, einschließlich Unterstützung für mehrere Zeitzonen, Sprachen, Währungen, Buchhaltungs- und Berichtssysteme;
─ In ERP wird im Gegensatz zu MRP II den Finanzsubsystemen mehr Aufmerksamkeit geschenkt.
ERP fügt Mechanismen zur Verwaltung multinationaler Unternehmen hinzu, einschließlich der Unterstützung mehrerer Zeitzonen, Sprachen, Währungen sowie Buchhaltungs- und Berichtssysteme. Darüber hinaus ermöglichen ERP-Systeme eine effektive Planung der finanziellen Kosten für Projekte zur Erneuerung der Ausrüstung und Investitionen in die Produktion neuer Produkte, was in MRP-Systemen nicht möglich war. Zum ersten Mal stellten diese Systeme eine vollständige Palette automatischer Kostenmanagementtools bereit. ERP-Systeme haben von MRP-Systemen die Fähigkeit übernommen, den Status von Produktionsressourcen und Lagerbeständen zu verfolgen. Dies ermöglicht es, betriebliche Informationen über den Zeitpunkt bestimmter Lieferungen, Preise einzelner Bestellungen usw. zu erhalten eine notwendige Bedingung Einsatz elektronischer Beschaffungssysteme.
ERP-Systeme bieten die Möglichkeit einer vollständigen End-to-End-Buchhaltung und Kontrolle von Informationen im Zusammenhang mit dem Durchgang einer Bestellung über die folgende Kette: Antrag des Käufers > Berechnung geplanter Indikatoren (Kosten, Produktions- und Lieferzeit) > Auftragserteilung - Produktionsauftrag (Reservierung von Produktionskapazität) > Erstellung von Aufträgen für die Lieferung von Komponenten > Abrechnung des Komponenteneingangs, gegenseitige Abrechnung mit Lieferanten > Abrechnung der Abschreibung von Komponenten für die Produktion im Zusammenhang mit einem Produktionsauftrag > Abrechnung der Merkmale des Produktionsauftrags > Abrechnung der Freigabe von Fertigprodukten > Abrechnung der Lieferung von Fertigprodukten, gegenseitige Abrechnung mit dem Kunden > Vergleich von Plan- und Ist-Kennzahlen.
Zu diesem Zweck ist Folgendes vorgesehen:
Automatische Berechnung der möglichen Fertigstellungszeit und -kosten jedes neuen Auftrags unter Berücksichtigung der aktuellen Ausrüstungsauslastung, Verfügbarkeit und Lieferzeiten der Komponenten;
Automatische Generierung von Kaufanfragen auf Basis von Daten zu Lagerbeständen und geplantem Verbrauch für das gesamte Komponentenspektrum;
Automatische Generierung eines Produktionsauslastungsplans.
Als Basis für die Internetlösungen eines Unternehmens sollten ERP-Systeme in Betracht gezogen werden, die eine Ressourcenplanung und eine integrierte Steuerung aller Geschäftsprozesse ermöglichen. Das Fehlen eines zuverlässigen internen Planungs- und Kontrollsystems, das mit einem externen (Front-Office-)Internet-Commerce-System integriert ist, verurteilt ein Unternehmen zum Scheitern in der New Economy. Gleichzeitig können nicht alle ERP- und MRPII-Systeme Lösungen für ein prozessorientiertes Produktionsplanungs- und -managementsystem anbieten. Die Unterschiede zwischen den beiden Systemen (MRP II und ERP) ergeben sich aus ihrer funktionaler Zweck. MRP-Systeme sind ausschließlich für den Einsatz in Industrieunternehmen konzipiert. ERP-Systeme sind nicht auf die Sphäre beschränkt industrielle Produktion Sie können in Handels- und Dienstleistungsorganisationen, Banken, Versicherungen, Bildungseinrichtungen usw. eingesetzt werden.
©2015-2019 Website
Alle Rechte liegen bei ihren Autoren. Diese Seite erhebt keinen Anspruch auf Urheberschaft, stellt die Nutzung jedoch kostenfrei zur Verfügung.
Erstellungsdatum der Seite: 08.08.2016
Die Notwendigkeit, Managementprozesse zu automatisieren, wurde erstmals Ende der 60er und Anfang der 70er Jahre erkannt, als klar wurde, dass die Führung eines Großkonzerns denselben Gesetzen unterliegt wie jede bürokratische Struktur.
In einem der Parkinson-Gesetze heißt es: „Die Größe einer Organisation hat nichts mit der Menge ihrer Arbeit zu tun.“ Mit anderen Worten: Mit zunehmender Zahl des Führungspersonals sinkt die Effizienz seiner Arbeit auf Null (Abb. 19.1).
Reis. 19.1. Abhängigkeit der Effizienz von der Personalzahl
In diesem Zusammenhang wurde eine Idee geboren: die Arbeit von Managern mithilfe eines automatisierten Systems zu organisieren, ähnlich wie ein Fließband die Arbeit von Arbeitern organisiert. Daraus entstand das Konzept des regulären Managements, das sich nicht auf talentierte Einzelpersonen, sondern auf formal beschriebene Verfahren stützt, die die Arbeit jedes Managers effektiv machen.
Empfehlungsstandards- eine Beschreibung der allgemeinsten Regeln, nach denen die Planung und Steuerung verschiedener Phasen des Produktionsprozesses durchgeführt werden sollte: Bedarf an Rohstoffen, Einkäufe, Kapazitätsauslastung, Ressourcenzuteilung usw.
Lasst uns zuerst geben Kurzbeschreibung Methoden/Systeme:
- MPS (Master Planning Schedule)- Bekannte Methodik „Umfangsplanung“. Es ist die Grundlage für fast alle planorientierten Methoden. Es wird hauptsächlich in der Fertigung eingesetzt, kann aber auch in anderen Geschäftsbereichen, beispielsweise im Vertrieb, eingesetzt werden.
- MRP (Materialbedarfsplanung) - Automatisierte Planung des Rohstoffbedarfs für die Produktion. Eine Methode zur Planung des Bedarfs an Materialressourcen, die darin besteht, den endgültigen Ressourcenbedarf anhand der Daten des Produktionsvolumenplans zu ermitteln. Schlüsselkonzept Methodik ist das Konzept der „Explosion“, d.h. Zusammenführen der Baumzusammensetzung eines Produkts in eine lineare Liste (Stückliste), nach der der Bedarf geplant und Komponenten bestellt werden. Seine verbesserte Version, Closed Loop MRP (Materialbedarfsplanung im geschlossenen Kreislauf), ermöglichte es, Beschaffungspläne dynamisch anzupassen, wenn ungewöhnliche Abweichungen davon auftreten.
In den späten 60er Jahren begannen große Unternehmen mit vielen automatisierten Arbeitsplätzen nach einer Möglichkeit zu suchen, die Verwaltung von Produktionsprozessen zu vereinfachen. Der erste Schritt auf diesem Weg war die Entstehung der Idee eines einheitlichen Datenmodells in der gesamten Organisation. So entstand das Konzept der MRP-Systeme (Material Requirements Planning) – automatisierte Planung des Bedarfs an Rohstoffen und Materialien für die Produktion. Die wichtigste Errungenschaft von MRP-Systemen ist die Minimierung der mit der Lagerhaltung verbundenen Kosten.
Auf Basis der MRP-Methodik implementierte Softwaresysteme ermöglichten es, die Komponentenversorgung für die Produktion optimal zu regeln, Lagerbestände und die Produktionstechnik selbst zu steuern. Darüber hinaus ist es durch den Einsatz von MRP-Systemen möglich, das Volumen der permanenten Bestände zu reduzieren.
Zunächst wurde mit Hilfe von MRP-Systemen einfach ein Auftragsplan für einen bestimmten Zeitraum auf Basis des genehmigten Produktionsprogramms erstellt. Damit wurde den wachsenden Bedürfnissen der Unternehmen nicht vollständig entsprochen. Um die Planungseffizienz Ende der 70er Jahre zu verbessern. In MRP-Systemen wurde die Idee der Abbildung eines geschlossenen Kreislaufs (Closed Loop Material Requirement Planning) umgesetzt, was die Erstellung eines Produktionsprogramms und dessen Steuerung auf Werkstattebene impliziert.
Zu den Grundfunktionen der Planung der Produktionskapazität und der Planung des Materialbedarfs wurden zusätzliche Funktionen hinzugefügt (z. B. Überwachung der Übereinstimmung der Menge der produzierten Produkte mit der Anzahl der im Montageprozess verwendeten Komponenten, Erstellung regelmäßiger Berichte über Auftragsverzögerungen und -mengen). und Dynamik von Produktverkäufen, Lieferanten usw.) . Die während des Betriebs des modifizierten MRP-Systems erstellten Berichte wurden analysiert und in weiteren Planungsphasen berücksichtigt, wobei (falls erforderlich) das Produktionsprogramm und der Auftragsplan geändert wurden (wodurch Planungsflexibilität in Bezug auf externe Faktoren wie die Nachfragehöhe gewährleistet wurde). , der aktuelle Stand der Dinge bei Komponentenlieferanten usw.).
- CRP (Kapazitätsbedarfsplanung) - Produktionsressourcenplanung. Dieses Konzept ähnelt MRP, operiert jedoch anstelle eines einzelnen Konzepts der Produktzusammensetzung mit Konzepten wie „Bearbeitungszentrum“, „Maschine“, „Arbeitsressourcen“, weshalb die technische Umsetzung von CRP komplexer ist. Aufgrund des engen logischen Zusammenhangs in der Planung wird es normalerweise in Verbindung mit MRP verwendet. MRP/CRP-Methoden werden in automatisierten Kontrollsystemen produzierender Unternehmen eingesetzt.
- FRP (Finanzbedarfsplanung) - Finanzielle Ressourcenplanung.
- MRP II (Manufacturing Resources Planning) - Planung und Verwaltung aller Produktionsressourcen des Unternehmens: Rohstoffe, Materialien, Ausrüstung, Arbeitskosten. Produktionsplanung. Integrierte Methodik einschließlich MRP/CRP und typischerweise MPS und FRP. Bei der Verwendung dieser Methodik ist zwangsläufig eine Analyse der finanziellen Ergebnisse des Produktionsplans erforderlich.
Das MRP-II-Klassensystem zielt darauf ab, alle vom Unternehmen implementierten Hauptprozesse zu integrieren, wie z. B. Lieferung, Lagerbestände, Produktion, Verkauf und Vertrieb, Planung, Kontrolle über die Planumsetzung, Kosten, Finanzen, Anlagevermögen usw.
Der MRP II-Standard unterteilt den Umfang einzelner Funktionen (Prozeduren) in zwei Ebenen: erforderlich und optional. Damit Software als MRP II eingestuft werden kann, muss sie eine bestimmte Anzahl notwendiger (Kern-)Funktionen (Prozeduren) ausführen. Einige Softwareanbieter haben unterschiedliche Implementierungen des optionalen Teils der Verfahren in diesem Standard übernommen.
Das MRPII-Framework deckt alle wichtigen Funktionen der Produktionsplanung von oben bis unten ab. Der Aufbau von Funktionsmodulen und deren Beziehungen sind aus regelungstheoretischer Sicht eingehend belegt. Sie ermöglichen die Integration von Planungsfunktionen, einschließlich ihrer Koordination über zeitliche und räumliche Unterschiede hinweg. Es ist wichtig zu beachten, dass der vorgestellte Modulsatz nicht redundant ist, weshalb er hauptsächlich in Systemen nachfolgender Generationen erhalten bleibt. Darüber hinaus bleiben viele Konzepte, Methoden und Algorithmen, die in MRPII-Funktionsmodule eingebettet sind, lange Zeit unverändert und werden als Elemente in Systeme der nächsten Generation einbezogen.
Jede Ebene der MRPII-Planung ist durch Parameter wie den Detaillierungsgrad des Plans, den Planungshorizont, die Art der Bedingungen und Einschränkungen gekennzeichnet. Bei gleichem MRPII-Planungsniveau können diese Parameter je nach Art des Produktionsprozesses in einem weiten Bereich variieren; es ist auch möglich, in jedem einzelnen Unternehmen einen bestimmten Satz von MRPII-Funktionsmodulen zu verwenden.
Kurze Merkmale der MRPII-Funktionsmodule:
- Geschäftliche Planung. Der Prozess der Erstellung eines Unternehmensplans auf höchstem Niveau. Langfristige Planung, der Plan wird unter Kostengesichtspunkten erstellt. Der am wenigsten formalisierte Entscheidungsprozess.
- Verkaufs- und Aktivitätsplanung. Der Geschäftsplan wird in Verkaufspläne für die wichtigsten Produkttypen (normalerweise 5 bis 10) umgewandelt. In diesem Fall dürfen Produktionskapazitäten nicht oder nicht in Summe berücksichtigt werden. Der Plan ist mittelfristiger Natur.
- Produktionsplanung. Der Verkaufsplan nach Produkttypen wird in einen volumetrischen oder volumetrischen Kalenderplan für die Produktion von Produkttypen umgewandelt. Typ bezieht sich hier auf Familien homogener Produkte. In dieser Hinsicht fungieren Produkte erstmals als Planungs- und Abrechnungseinheiten, die Vorstellungen über sie sind jedoch durchschnittlicher Natur. Wir können beispielsweise über alle im Werk produzierten Personenkraftwagen mit Frontantrieb sprechen, ohne die Modelle anzugeben. Oftmals wird dieses Modul mit dem vorherigen kombiniert.
- Erstellung eines Produktionsplans. Der Produktionsplan wird in einen Produktionsplan umgewandelt. In der Regel handelt es sich dabei um einen mittelfristigen Mengenkalenderplan, der die Mengen bestimmter Produkte (oder Chargen) mit dem Zeitpunkt ihrer Produktion festlegt.
- Planung des Bedarfs an materiellen Ressourcen. Bei der Planung auf dieser Ebene wird der zur Sicherstellung des Produktionsplans erforderliche Materialbedarf quantitativ und zeitlich ermittelt.
- Produktionskapazitätsplanung. In der Regel führt dieses Modul Berechnungen durch, um verfügbare und benötigte Produktionskapazitäten zu ermitteln und zu vergleichen. Mit geringfügigen Modifikationen kann dieses Modul nicht nur für Produktionsanlagen, sondern auch für andere Arten von Produktionsressourcen verwendet werden, die den Anlagendurchsatz beeinflussen können. Solche Berechnungen werden in der Regel nach der Planerstellung auf fast allen vorherigen Ebenen durchgeführt, um die Zuverlässigkeit des Planungssystems zu erhöhen. Manchmal ist die Lösung dieses Problems in einem Modul der entsprechenden Stufe enthalten.
- Operatives Produktionsmanagement. Hier werden Einsatzpläne und Zeitpläne erstellt. Als Planungsbuchhaltungseinheiten können Teile (Batch), tiefe Montageeinheiten, Teil-(Batch-)Operationen usw. fungieren. Der von der Planung abgedeckte Zeitraum ist klein (von mehreren Tagen bis zu einem Monat).
Der lange Prozess der Einführung von MRPII ermöglichte einerseits eine Steigerung der Effizienz von Unternehmen und zeigte andererseits eine Reihe von Mängeln auf, die diesem System innewohnen, darunter:
Die Fokussierung des Unternehmensmanagementsystems ausschließlich auf bestehende Aufträge, was es schwierig machte, lang-, mittelfristige und teilweise auch kurzfristige Entscheidungen zu treffen;
Schlechte Integration in Produktdesign- und Engineering-Systeme, was besonders wichtig für Unternehmen ist, die komplexe Produkte herstellen;
Schlechte Integration in Prozessdesign- und Produktionsautomatisierungssysteme;
Unzureichende Sättigung des Managementsystems mit Kostenmanagementfunktionen;
Mangelnde Integration in Finanz- und Personalmanagementprozesse.
ERP (Enterprise Resources Planning) - Unternehmensressourcenmanagement. Zu den Eigenschaften von MRPII wurden Finanzressourcenmanagement und Marketing hinzugefügt. Das ERP-Konzept ist das erste, das auf die Unternehmensführung abzielt und nicht nur auf die Produktion, wie MRP. Geschäftsplanungskonzept. ERP bezieht sich auf ein „integriertes“ System, das die von den MPS-MRP/CRP-FRP-Konzepten bereitgestellten Funktionen ausführt. Ein wichtiger Unterschied zur MRPII-Methodik ist die Möglichkeit der „dynamischen Analyse“ und „dynamischen Planmodifikation“ entlang der gesamten Planungskette.
Die spezifischen Fähigkeiten der ERP-Methodik hängen maßgeblich von der Softwareimplementierung ab. Das ERP-Konzept ist vager als MRPII. Wenn MRPII einen klaren Fokus auf produzierende Unternehmen hat, dann ist die ERP-Methodik im Handel, im Dienstleistungssektor und im Finanzsektor anwendbar. Laut APICS Dictionary kann der Begriff „ERP-System“ (Enterprise Resource Planning) in zwei Bedeutungen verwendet werden.
Erstens handelt es sich um ein Informationssystem zur Identifizierung und Planung aller Unternehmensressourcen, die für Vertrieb, Produktion, Einkauf und Buchhaltung im Rahmen der Erfüllung von Kundenaufträgen erforderlich sind.
Zweitens (im allgemeineren Kontext) handelt es sich um eine Methodik zur effektiven Planung und Verwaltung aller Unternehmensressourcen, die für Vertrieb, Produktion, Einkauf und Buchhaltung zur Ausführung von Kundenaufträgen in den Bereichen Produktion, Vertrieb und Dienstleistungserbringung, Unternehmen erforderlich sind Ressourcen, die für Vertrieb, Produktion, Einkauf und Buchhaltung bei der Ausführung von Kundenaufträgen in den Bereichen Produktion, Vertrieb und Dienstleistungserbringung erforderlich sind.
Somit kann der Begriff ERP nicht nur ein Informationssystem bedeuten, sondern auch die entsprechende Managementmethodik, die von diesem Informationssystem implementiert und unterstützt wird.
Hauptfunktionen des ERP-Systems:
Die meisten modernen ERP-Systeme sind modular aufgebaut, was dem Kunden die Möglichkeit gibt, nur die Module auszuwählen und zu implementieren, die er wirklich benötigt. Module verschiedener ERP-Systeme können sich sowohl im Namen als auch im Inhalt unterscheiden. Es gibt jedoch eine Reihe von Funktionen, die als typisch für Softwareprodukte der ERP-Klasse gelten können.
Diese typischen Funktionen sind:
Einhaltung gestalterischer und technologischer Vorgaben. Solche Spezifikationen definieren die Zusammensetzung des Endprodukts sowie die Materialressourcen und Arbeitsgänge, die zu seiner Herstellung erforderlich sind (einschließlich Routing);
Bedarfsmanagement und Erstellung von Verkaufs- und Produktionsplänen. Diese Funktionen sind für die Bedarfsprognose und Produktionsplanung konzipiert;
Planung des Materialbedarfs. Ermöglicht die Bestimmung der Mengen verschiedener Arten von Materialressourcen (Rohstoffe, Materialien, Komponenten), die zur Erfüllung des Produktionsplans erforderlich sind, sowie von Lieferzeiten, Losgrößen usw.;
Bestands- und Einkaufsmanagement. Ermöglicht die Organisation der Vertragsverwaltung, die Implementierung eines zentralisierten Beschaffungsschemas, die Sicherstellung der Buchhaltung und Optimierung der Lagerbestände usw.;
Planung der Produktionskapazität. Mit dieser Funktion können Sie die Verfügbarkeit der verfügbaren Kapazität überwachen und deren Auslastung planen. Beinhaltet eine groß angelegte Kapazitätsplanung (zur Beurteilung der Machbarkeit von Produktionsplänen) und eine detailliertere Planung bis hin zu einzelnen Arbeitsplätzen;
Finanzielle Funktionen. Diese Gruppe umfasst die Funktionen der Finanzbuchhaltung, des Management Accounting sowie des operativen Finanzmanagements;
Projektmanagementfunktionen. Sorgen Sie für die Planung von Projektaufgaben und Ressourcen, die für deren Umsetzung erforderlich sind. Systeme dieser Klasse konzentrieren sich eher auf die Arbeit mit Finanzinformationen, um Probleme bei der Verwaltung großer Unternehmen mit geografisch verteilten Ressourcen zu lösen. Dazu gehört alles, was nötig ist, um Ressourcen zu beschaffen, Produkte herzustellen, zu transportieren und Kundenaufträge zu bezahlen. Zusätzlich zu den aufgeführten funktionalen Anforderungen implementiert ERP auch neue Ansätze für den Einsatz von Grafiken, den Einsatz relationaler Datenbanken, CASE-Technologien zu deren Entwicklung, die Architektur von Client-Server-Computersystemen und deren Umsetzung als offene Systeme.
ERP ist somit eine verbesserte Modifikation von MRPII. Sein Ziel ist es, die Verwaltung aller Unternehmensressourcen zu integrieren, und nicht nur der materiellen, wie es bei MRPII der Fall war.
Ein weiteres Merkmal von ERP besteht darin, dass es im Wesentlichen die in MRPII übernommenen Produktionsplanungsansätze beibehält. Der Hauptgrund dafür war, dass beim anfänglichen Übergang von MRPII zu ERP die Rechenleistung nicht ausreichte, um den breiten Einsatz von Modellierungs- und Optimierungsmethoden zu unterstützen. Rechnerische Einschränkungen haben beispielsweise dazu geführt, dass Planungslösungen durch zyklische Wiederholung zweier Schritte gebildet werden. Im ersten Schritt wird ein Plan erstellt, ohne Einschränkungen der Produktionskapazität zu berücksichtigen. Im zweiten Schritt wird die Gültigkeit überprüft. Der Vorgang wird wiederholt, bis der bei der nächsten Iteration erhaltene Plan gültig ist.
Im ERP können Entscheidungen zur Aufnahme eines Produkts in den Produktionsplan nicht nur auf der Grundlage der tatsächlichen Nachfrage, sondern auch auf der Grundlage der Bedarfsprognose und im Zusammenhang mit der Umsetzung getroffen werden große Projekte und Programme. Dies erweitert natürlich den Anwendungsbereich des Steuerungssystems und macht es flexibler und reaktionsfähiger auf Änderungen in der externen Umgebung.
CSRP (Customer Synchronized Resources Planning) - Das Management konzentriert sich auf die Interaktion mit Kunden: Dazu gehören die Annahme von Aufträgen, die Entwicklung von Plänen, Projekten und Aufgaben sowie technischer Support. Praktisch: CSRP=ERP+CRM. Mit dem Käufer synchronisierte Ressourcenplanung. CSRP umfasst einen vollständigen Zyklus – vom Design eines zukünftigen Produkts unter Berücksichtigung der Kundenanforderungen bis hin zur Garantie und Service nach dem Verkauf. Der Kern von CSRP besteht darin, den Käufer in das Unternehmensmanagementsystem zu integrieren. In diesem Fall ist es nicht die Vertriebsabteilung, sondern der Käufer selbst, der einen Auftrag zur Herstellung von Produkten erteilt, für die ordnungsgemäße Ausführung des Auftrags verantwortlich ist und gegebenenfalls die Einhaltung der Produktions- und Lieferfristen überwacht. Ein Unternehmen kann die Nachfrageentwicklung seiner Produkte sehr genau überwachen.
CSRP ist die erste Geschäftsmethodik, die kundenorientierte Unternehmensaktivitäten in den Mittelpunkt des Unternehmensmanagementsystems integriert.
Das CSRP legt eine Geschäftsmethodik fest, die auf aktuellen Kundeninformationen basiert. CSRP verlagert den Fokus des Unternehmens von der Planung weg von den Produktionsanforderungen hin zur Planung weg von Kundenaufträgen. Kundeninformationen und -dienstleistungen sind im Kern der Organisation verankert. Produktionsplanungsaktivitäten werden nicht einfach erweitert, sondern entfernt und durch Kundenanfragen ersetzt, die von kundenorientierten Teilen der Organisation übertragen werden.
CSRP definiert den Kundenservice neu und erweitert ihn über den reinen Telefonsupport und Abrechnungen hinaus. Beim Einsatz des CSRP-Modells wird der Kundenservice zum Rückgrat des gesamten Unternehmens, zur Kommandozentrale der Organisation. Das Customer Support Center ist für die Übermittlung wichtiger Kundeninformationen an die Führungszentren der Organisation verantwortlich.
Die Vorteile einer erfolgreichen Anwendung von CSRP sind eine Steigerung der Warenqualität, eine Verkürzung der Lieferzeit, eine Steigerung des Produktwertes für den Käufer usw. und infolgedessen eine Senkung der Produktionskosten. Noch wichtiger ist jedoch die Schaffung einer Infrastruktur, die dazu geeignet ist, Produkte zu schaffen, die die Bedürfnisse des Käufers erfüllen, die Feedback-Kommunikation mit Käufern zu verbessern und den Käufern den besten Service zu bieten. Es ist nicht die Produktionseffizienz, die einen vorübergehenden Wettbewerbsvorteil verschafft, sondern die Fähigkeit, Produkte zu entwickeln, die die Kundenbedürfnisse erfüllen und erfüllen bester Service. Die Fähigkeit, Kundennutzen zu schaffen, wird zu Umsatzwachstum und nachhaltigen Wettbewerbsvorteilen führen.
Bei der Verwendung des CSRP-Geschäftsmodells werden traditionelle Geschäftsprozesse dahingehend überarbeitet, Kunden zu bedienen und Produkte zu schaffen, die ihre Bedürfnisse erfüllen. Die Implementierung von CSRP-Anwendungen drängt Unternehmensleiter zu Veränderungen. Der nach innen gerichtete Fokus traditioneller Fertigungsstrukturen, segmentiert nach Abteilung und Funktionalität, wird neu nach außen ausgerichtet. Mit CSRP können Sie einen bidirektionalen freien Informationsfluss zwischen Käufer und Hersteller aufbauen.
ERPII (Enterprise Resource and Relationship Processing) - Verwaltung interner Ressourcen und externer Beziehungen des Unternehmens. Neuüberarbeitung des ERP-Konzepts. Wir können davon ausgehen, dass ERPII = ERP + CRM + SCM. Die Hauptidee von ERP II besteht darin, über die Aufgaben der Optimierung der internen Prozesse der Organisation hinauszugehen: neben der Integration traditioneller ERP-Systeme auch Unternehmensbereiche wie Finanzmanagement, Buchhaltung, Vertriebs- und Einkaufsmanagement, Beziehungen mit Debitoren und Kreditoren, Personalmanagement, Produktion, Bestandsverwaltung, Systeme der Klasse ERP II ermöglichen Ihnen die Verwaltung von Kundenbeziehungen, Lieferketten und die Abwicklung des Handels über das Internet.
Das renommierte Beratungsunternehmen Gartner Group verkündete 1999 das Ende der Ära der ERP-Systeme. Es wurde durch das Konzept von ERP II – Enterprise Resource and Relationship Processing, Verwaltung interner Ressourcen und externer Beziehungen des Unternehmens – ersetzt.
Nach der Definition der Gartner Group ist ERP II die Geschäftsstrategie eines Unternehmens, das einer bestimmten Branche angehört, und eine Reihe von Schlüsselanwendungen für diese Branche, die Kunden und Aktionären von Unternehmen dabei helfen, den Geschäftswert durch effektive IT-Unterstützung und -Optimierung zu steigern betriebliche und finanzielle Prozesse sowohl innerhalb Ihres Unternehmens als auch nach außen – im Rahmen der Zusammenarbeit mit anderen Unternehmen.
SCM (Supply Chain Management)- Lieferantenbeziehungsmanagement. Lieferkettenmanagement. Das SCM-Konzept wurde zur Optimierung des Supply Chain Managements erfunden und kann durch eine optimale Strukturierung logistischer Lieferketten Transport- und Betriebskosten deutlich senken. Das SCM-Konzept wird in den meisten Systemen der ERP- und MRPII-Klasse unterstützt.
CRM (Kundenbeziehungsmanagement) - Kundenbeziehungsmanagement. Verfolgung der Geschichte der Beziehungsentwicklung, Koordinierung multilateraler Kommunikation, zentrale Steuerung des Vertriebs und kundenorientiertes Marketing. Das Konzept, automatisierte Kundendienstsysteme für das Unternehmen aufzubauen. CRM umfasst die Sammlung, Verarbeitung und Analyse nicht nur von Finanz- und Buchhaltungsinformationen, sondern auch anderer Informationen über die Beziehungen zu Kunden. Dies steigert die Produktivität der Manager, verbessert den Kundenservice und steigert den Umsatz.
PLM (Produktlebenszyklusmanagement)- Produktlebenszyklusmanagement.
CAD/CAM/CAE/PDM (Computergestütztes Design/Computergestützte Fertigung/Computergestütztes Engineering/Projektdatenmanagement)- Automatisierte Systeme: Design/technologische Vorbereitung der Produktion/technische Berechnungen/Dokumentenfluss.
MES (Management Execution System) - Ausführungsmanagementsystem (Produktionsaufgaben) oder Versandsystem. Für die Definition von MES-Systemen gibt es mehrere Formulierungen. MES ist ein Informations- und Kommunikationssystem für die Produktionsumgebung eines Unternehmens (APICS-Definition). MES- automatisiertes System Management und Optimierung Produktionsaktivitäten, die in Echtzeit: initiiert, überwacht, optimiert, dokumentiert Herstellungsprozesse vom Beginn der Auftragsabwicklung bis zur Freigabe der fertigen Produkte (MESA International-Definition). MES ist ein integriertes Informations- und Computersystem, das Werkzeuge und Methoden für das Produktionsmanagement in Echtzeit vereint.
SCADA (Supervisory Control And Data Acquisition System)- ein System zur Datenerfassung und operativen Versandsteuerung technologischer Prozesse. Ich möchte betonen, dass der Name zwei Hauptfunktionen enthält, die dem SCADA-System zugewiesen sind: Sammeln von Daten über den gesteuerten technologischen Prozess; Steuerung des technologischen Prozesses, durchgeführt von verantwortlichen Personen auf der Grundlage der gesammelten Daten und Regeln (Kriterien), deren Umsetzung die größte Effizienz und Sicherheit des technologischen Prozesses gewährleistet.
Einführung
Die neue wirtschaftliche Situation stellt Unternehmen vor Herausforderungen, die sie bisher nicht bedacht hatten. Unter den meisten wichtige Aufgaben Herausforderungen, denen sich Industrieunternehmen unter modernen Bedingungen gegenübersehen, lassen sich unterscheiden:
- verstärkter Wettbewerb,
- die Anforderung, Produkte nach aktuellen Kundenaufträgen und nicht nach langfristigen Plänen zu produzieren,
- die Notwendigkeit einer schnellen Entscheidungsfindung in einer schwierigen wirtschaftlichen Situation,
- Stärkung der Verbindungen zwischen Lieferanten, Herstellern und Käufern.
Im Wettbewerb gewinnt nur derjenige, der schneller als andere auf Veränderungen im Geschäft reagiert und mehr akzeptiert. richtige Entscheidungen. Es ist Informationstechnologie, die Managern hilft Industrieunternehmen bei der Bewältigung dieser Probleme komplexe Aufgaben. Länder Marktwirtschaft verfügen über umfangreiche Erfahrung in der Erstellung und Entwicklung von Informationstechnologien für Industrieunternehmen. Eine der weltweit am weitesten verbreiteten Methoden des Produktions- und Vertriebsmanagements ist der in den USA entwickelte und von der American Production and Inventory Control Society (APICS) unterstützte MRP II-Standard (Manufacturing Resource Planning). APICS veröffentlicht regelmäßig das MRP II Standard System-Dokument, das die grundlegenden Anforderungen an Fertigungsinformationssysteme beschreibt. Die letzte Ausgabe dieses Systems von Industriestandards wurde 1989 veröffentlicht.
Bei MRP II handelt es sich um eine Reihe bewährter, solider Management- und Kontrollprinzipien, Modelle und Verfahren zur Leistungsverbesserung. Wirtschaftstätigkeit Unternehmen. Die Idee von MRP II basiert auf mehreren einfache Prinzipien, zum Beispiel die Aufteilung der Nachfrage in abhängige und unabhängige. Das MRP II-Standardsystem enthält eine Beschreibung von 16 Gruppen von Systemfunktionen:
- Vertriebs- und Betriebsplanung.
- Nachfragemanagement.
- Master-Produktionsplanung.
- Materialbedarfsplanung.
- Stückliste (Produktspezifikationen).
- Subsystem für Bestandstransaktionen (Lagerverwaltung).
- Subsystem für geplante Eingänge.
- Shop Flow Control (Management auf Ebene der Produktionswerkstatt).
- Kapazitätsbedarfsplanung.
- Eingabe-/Ausgabesteuerung.
- Einkauf (Material- und technische Versorgung).
- Planung von Vertriebsressourcen.
- Werkzeugplanung und -steuerung (Planung und Steuerung von Produktionsabläufen).
- Finanzplanung (Finanzmanagement).
- Simulation.
- Leistungsmessung.
Mit der gesammelten Erfahrung in der Modellierung von Produktions- und Nichtproduktionsabläufen werden diese Konzepte ständig verfeinert und decken nach und nach immer mehr Funktionen ab.
Der MRP II-Standard durchlief bei seiner Entstehung mehrere Entwicklungsstufen:
- 60-70 Jahre - Planung des Materialbedarfs, basierend auf Daten über Lagerbestände und Zusammensetzung der Produkte (Materialbedarfsplanung)
- 70-80 Jahre - Planung des Materialbedarfs in einem geschlossenen Kreislauf (Closed Loop Material Requirement Planning), einschließlich der Erstellung eines Produktionsprogramms und dessen Steuerung auf Werkstattebene,
- Ende der 80er-90er Jahre – basierend auf Daten von Lieferanten und Verbrauchern, Prognose, Planung und Produktionssteuerung,
- 90er Jahre – Planung von Verteilungs- und Ressourcenbedarfen auf Unternehmensebene – Enterprise Resource Planning und Distributed Requirements Planning.
Die Aufgabe von Informationssystemen der Klasse MRP II ist die optimale Gestaltung des Flusses von Materialien (Rohstoffen), Halbzeugen (auch in der Produktion) und Fertigprodukten. Das MRP-II-Klassensystem zielt darauf ab, alle vom Unternehmen implementierten Hauptprozesse zu integrieren, wie z. B. Lieferung, Lagerbestände, Produktion, Verkauf und Vertrieb, Planung, Kontrolle über die Planumsetzung, Kosten, Finanzen, Anlagevermögen usw.
Der MRP II-Standard unterteilt den Umfang einzelner Funktionen (Prozeduren) in zwei Ebenen: erforderlich und optional. Damit Software als MRP II eingestuft werden kann, muss sie eine bestimmte Anzahl notwendiger (Kern-)Funktionen (Prozeduren) ausführen. Einige Softwareanbieter haben unterschiedliche Implementierungen des optionalen Teils der Verfahren in diesem Standard übernommen.
Ergebnisse der Verwendung integrierter Systeme des MRP II-Standards:
- Einholung operativer Informationen über die aktuellen Ergebnisse der Unternehmenstätigkeit, sowohl allgemein als auch mit vollständigen Einzelheiten zu einzelnen Aufträgen, Ressourcenarten, Umsetzung von Plänen;
- langfristige, betriebliche und detaillierte Planung des Unternehmens mit der Möglichkeit, die Plandaten anhand betrieblicher Informationen anzupassen;
- Lösung von Problemen der Optimierung von Produktions- und Materialflüssen;
- echte Reduzierung der Materialressourcen in Lagerhäusern;
- Planung und Kontrolle des gesamten Produktionszyklus mit der Möglichkeit, ihn zu beeinflussen, um eine optimale Effizienz bei der Nutzung von Produktionskapazitäten, allen Arten von Ressourcen und der Erfüllung der Kundenbedürfnisse zu erreichen;
- Automatisierung der Arbeit der Vertragsabteilung mit vollständiger Kontrolle über Zahlungen, Versand von Produkten und Fristen für die Erfüllung vertraglicher Verpflichtungen;
- finanzielle Widerspiegelung der gesamten Unternehmenstätigkeit;
- erhebliche Reduzierung der Nichtproduktionskosten;
- Schutz von Investitionen in die Informationstechnologie;
- die Möglichkeit einer schrittweisen Einführung des Systems unter Berücksichtigung der Investitionspolitik eines bestimmten Unternehmens.
MRP II basiert auf einer Planhierarchie. Die Pläne der unteren Ebenen hängen von den Plänen der höheren Ebenen ab, d.h. planen Höchststufe Bietet Eingaben, Ziele und/oder eine Art einschränkenden Rahmen für Pläne auf niedrigerer Ebene. Darüber hinaus sind diese Pläne so miteinander verbunden, dass sich die Ergebnisse untergeordneter Pläne umgekehrt auf übergeordnete Pläne auswirken.
Wenn die Ergebnisse eines Plans unrealistisch sind, müssen der Plan oder übergeordnete Pläne überarbeitet werden. Auf diese Weise ist es möglich, Angebot und Nachfrage von Ressourcen auf einer bestimmten Planungsebene und Ressourcen auf höheren Planungsebenen zu koordinieren.
STRATEGISCHE PLANUNG
Strategische Planung- Das ist langfristige Planung. Es wird in der Regel für einen Zeitraum von einem bis fünf Jahren erstellt. Es basiert auf makroökonomischen Indikatoren wie Wirtschaftstrends, technologischen Veränderungen, Marktbedingungen und Wettbewerb. Die strategische Planung erstreckt sich in der Regel auf jedes Jahr des Fünfjahresplans und stellt Ziele (Ziele) auf höchster Ebene dar.
GESCHÄFTLICHE PLANUNG
Ein Businessplan ist in der Regel ein Jahresplan, der ebenfalls jährlich erstellt wird. Manchmal wird es mehrmals im Jahr überarbeitet. In der Regel handelt es sich dabei um das Ergebnis einer Sitzung des Führungsteams, in der Planungen für Verkäufe, Investitionen, Entwicklung des Anlagevermögens sowie Kapitalbedarf und Budgetierung zusammengetragen werden. Diese Informationen werden in monetärer Form bereitgestellt. Der Geschäftsplan legt Umsatz- und Produktionsziele sowie weitere untergeordnete Pläne fest.
PLANUNG DES VERKAUFS UND DES PRODUKTIONSVOLUMENS
Wenn der Geschäftsplan zusammenfassende Daten zu monatlichen Verkaufsmengen (in Geldbeträgen) bereitstellt, werden diese Informationen im Verkaufs- und Produktionsmengenplan in 10-15 Produktgruppen unterteilt. Das Ergebnis ist ein Produktionsplan, der monatlich überarbeitet wird und dabei den Plan des Vormonats, Ist-Ergebnisse und Businessplandaten berücksichtigt.
Der Vertriebs- und Produktionsplan umfasst in der Regel folgende Elemente:
- Umsatzvolumen
- Produktion
- Reserven
- In Arbeit
- Sendung
Von diesen Elementen sind Verkaufsvolumen und Versand Prognosen, da Dabei handelt es sich um externe Daten, die nicht direkt kontrolliert werden können. Die Produktionsmenge wird geplant; es handelt sich dabei um eine interne Kennzahl, die direkt gesteuert werden kann. Bestands- und Work-in-Process-Pläne werden indirekt durch die Manipulation von Daten aus Verkaufsprognosen, Versandprognosen und/oder Produktionsvolumenplänen gesteuert.
Lagerbestände und unfertige Erzeugnisse werden je nach Art der vom Unternehmen hergestellten oder verkauften Produkte unterschiedlich verwaltet. Insbesondere für Unternehmen, die Produkte zur Lagerung herstellen, ist das geplante Lagervolumen ein wichtiger Faktor. Für Unternehmen, die auftragsbezogen produzieren, ist der geplante Umfang der unfertigen Arbeiten ein wichtiger Faktor.
Im Mittelpunkt der Vertriebs- und Produktionsplanung steht der Produktionsplan. Obwohl man ihn Produktionsplan nennt, ist er im Prinzip mehr als nur ein Produktionsplan. Es erfordert die Verfügbarkeit der notwendigen Ressourcen im gesamten Unternehmen. Wenn die Marketingabteilung einen Umsatzschub für eine bestimmte Produktpalette plant, müssen Ingenieure dafür sorgen, dass die erforderliche Menge an Ausrüstung verfügbar ist; die MTS-Abteilung muss zusätzliche Materiallieferungen bereitstellen (Verfügbarkeit neuer Lieferanten); Die Personalabteilung muss die Verfügbarkeit zusätzlicher Arbeitskräfte sicherstellen und neue Arbeitsschichten organisieren. Darüber hinaus muss die Verfügbarkeit der erforderlichen Kapitalmenge (zur Deckung des zusätzlichen Ressourcen- und Reservevolumens) sichergestellt werden.
RESSOURCENPLANUNG
Der Produktionsplan wird unrealistisch, wenn die Verfügbarkeit der erforderlichen Ressourcenmenge nicht gewährleistet ist. Bei der Ressourcenplanung handelt es sich um eine langfristige Planung, die es Ihnen ermöglicht, die erforderliche (zur Erfüllung des Produktionsplans) und verfügbare Menge wichtiger Ressourcen wie Personen, Ausrüstung, Gebäude und Strukturen abzuschätzen. Wenn der Bedarf an zusätzlichen Ressourcen in der erforderlichen Menge besteht, muss der Geschäftsplan möglicherweise überarbeitet werden.
Die Ressourcenplanung betrifft nur Schlüsselressourcen und wird für die Dauer des Produktionsplans (normalerweise ein Jahr) erstellt. Eine Ressource kann als Schlüssel betrachtet werden, wenn ihr Wert groß genug ist, ihre Lieferzeit lang genug ist oder wenn andere Ressourcen von ihr abhängen. Ressourcen können entweder extern (Lieferantenfähigkeiten) oder intern (Ausrüstung, Lagerraum, Geld) sein.
HAUPTPRODUKTIONSPLAN (MPSP)
Die Aufgabe des Leiters der Planungsabteilung besteht darin, den Produktionsplan in einen konkreten Produktionsplan umzusetzen. Dieser Plan ist der GPPP – ein Produktionsplan, der einer Zeitskala überlagert ist. GPGP zeigt, was wann und in welchen Mengen produziert wird.
Weil Der Produktionsplan wird in Einheiten wie Rubel, Stunden, Tonnen ausgedrückt. Um den GPGP zu erhalten, müssen einige Schritte zur Umgestaltung des Produktionsplans unternommen werden. Geplante Mengenindikatoren für eine Sortimentsgruppe müssen für jedes Produkt dieser Gruppe separat in geplante Mengen und Konditionen umgerechnet werden. Je nach Art und Menge der produzierten Produkte kann GPGP in Wochen-, Tages- und sogar Schichtpläne unterteilt werden.
Einer der Hauptzwecke von MRP besteht darin, einen Puffer bereitzustellen: MRP unterscheidet Prognosen und Bedarfe der Vertriebsabteilung von MRP (Materialbedarfsplanung). Die Philosophie besteht darin, dass Prognosen und Verkaufsaufträge (Kundenaufträge) die Nachfrage (oder Lieferungen) zum Ausdruck bringen, während der WPI darstellt, was basierend auf der bestehenden Nachfrage tatsächlich produziert wird. Gemäß GPGP ist es möglich, Produkte in Zeiten geringer Nachfrage herzustellen und umgekehrt. Dies kann bei der Herstellung von Produkten auftreten, deren Nachfrage saisonabhängig ist.
NACHFRAGE GPGP
Der Planungsleiter muss alle Quellen unabhängiger Nachfrage berücksichtigen. Eigenbedarf ist ein vorhersehbarer Bedarf, in der Regel der Bedarf an Fertigprodukten und Ersatzteilen. Sie unterscheidet sich grundlegend von der abhängigen Nachfrage (Nachfrage, die auf der Grundlage von Daten zur Produktzusammensetzung berechnet werden kann). Quellen der unabhängigen Nachfrage: Produktionsplan, prognostiziertes Versandvolumen, Kundenaufträge (in Produktion oder Montage auf Bestellung), Nachfrage nach Ersatzteilen, werksübergreifende Nachfrage und Sicherheitsbestand.
Das Hauptproblem bei der Erstellung des GPGP besteht darin, zu bestimmen, welche Produkte/Komponenten von der Planungsabteilung geplant und welche automatisch (vom MRP-System) durchgeführt werden sollen. Die von der Planungsabteilung geplanten Produkte müssen unter menschlicher Kontrolle geplant werden. Vom MRP-System geplante Artikel, d. h. automatisch, erfordern keinen solchen Grad an Kontrolle (sie hängen vom GPGP ab). Die Festlegung, wie die Planung für einen bestimmten Produkttyp durchgeführt werden soll, hängt von den Produkttypen und technologischen Prozessen ab. Normalerweise sehr geringe Menge Produkte müssen von der Planungsabteilung gesteuert werden.
ALLGEMEINE KAPAZITÄTSPLANUNG
Wie die Ressourcenplanung ist auch die Gesamtkapazitätsplanung langfristig und basiert auf Schlüsselressourcen. Bei diesem Prozess werden GPWP-Daten anstelle von Produktionsplandaten verwendet. Wenn GPPP also in Volumen- und Zeitmerkmalen ausgedrückt wird, wird die allgemeine Kapazitätsplanung verwendet, um einen detaillierteren Plan zu erstellen, der bei der Beurteilung des durchschnittlichen Bedarfs des gesamten Unternehmens sowie bei der Schätzung des GPPP sehr nützlich sein kann.
Dispositions- oder Materialbedarfsplanung
In der Vergangenheit ging es bei der Materialbedarfsplanung (MRP) um die Bestandskontrolle und -auffüllung. Im Rahmen von MRP II (Enterprise Resource Planning) wurde der Einsatz auf die Kapazitätsbedarfsplanung, Priorisierung und Schließung der gesamten Planungskette ausgeweitet.
MRP beantwortet vier Hauptfragen:
- Was werden wir produzieren?
- Was brauchen wir dafür?
- Was haben wir bereits?
- Was müssen wir besorgen?
GPGP beantwortet die erste Frage „Was werden wir produzieren?“ Um die vom GPGP gesetzten Ziele zu erreichen, wird eine Planung aller Produktions- und Vertriebsaktivitäten durchgeführt. Weil GPGP ist ein Diagramm, das auch Fragen wie „Wie viel“ und „Wann“ beantwortet.
Die zweite Frage lautet: „Was brauchen wir dafür?“ fragt im Wesentlichen: „Welche Artikel/Komponenten müssen wir produzieren (oder kaufen), um die GPGP-Pläne zu erfüllen?“ Um diese Frage zu beantworten, müssen wir zwei Dinge wissen: GPGP und korrekte Daten zur Zusammensetzung des Produkts (Produktstruktur, Produktformel). Mithilfe von GPGP- und Produktzusammensetzungsdaten kann das System bestimmen, was, wie viel und wann benötigt wird, um das zu produzieren, was wir benötigen.
Die Frage „Was haben wir schon?“ lässt sich in zwei Fragen unterteilen: „Was haben wir bereits zur Hand?“ und „Was erwarten wir von Bestellungen?“ Die Antwort auf die erste Frage ist der verfügbare Bestand im Lager, die Antwort auf die zweite Frage ist das geplante Volumen der Wareneingänge aus der Produktion und von den Lieferanten. Zusammengenommen liefern diese Daten nicht nur Informationen über die Menge des vorhandenen Lagerbestands, sondern ermöglichen dem System auch, die erwartete Menge des Lagerbestands abzuschätzen. Um die letzte Frage zu beantworten, müssen Sie die Antworten auf die vorherigen drei kennen. Indem wir das nehmen, was produziert werden muss (Bruttobedarf), und das wegnehmen, was wir bereits haben (im Lager und geplante Zugänge), finden wir heraus, was wir zusätzlich erhalten müssen (Nettobedarf).
CRP oder Kapazitätsbedarfsplanung
Aber die erforderliche Menge an notwendigen Materialien bedeutet nichts, ohne über ausreichend freie Arbeitszeit zu verfügen. CRP (oder Kapazitätsbedarfsplanung) ist eine Planung auf mittlerer Ebene, die Daten aus geplanten MRP-Aufträgen und Produktionsaufträgen verwendet, um die erforderliche Menge an Arbeitszeit (sowohl Arbeitskräfte als auch technische Ressourcen) zu bestimmen.
Ressourcenplanung und Gesamtkapazitätsplanung sind die höchste Planungsebene, die zur Planung von Ressourcen wie physischer Ausrüstung verwendet wird. CRP ist eine detailliertere Planung. Der Arbeitsaufwand wird auf der Grundlage des technologischen Herstellungswegs des Produkts berechnet, der genau bestimmt, wie dieser Produkttyp hergestellt wird. Ein technologischer Weg ähnelt einer Gebrauchsanweisung – eine Reihe von Schritten (oder technischen Vorgängen), die abgeschlossen werden müssen, um etwas herzustellen. Jeder technische Vorgang wird an einem Arbeitsplatz ausgeführt, der aus einer oder mehreren Personen und/oder Geräten bestehen kann.
DRP- ODER VERTEILUNGSANFORDERUNGSPLANUNG
Wenn Materialien vom Lieferanten zum Verbraucher gelangen, durchlaufen sie eine Lieferkette (oder einen Marktkanal). Wenn wir dies grafisch darstellen, stellt die Lieferkette den Fluss von Angebot und Nachfrage zwischen Lieferanten und einigen Abteilungen des Unternehmens des Kunden, zwischen diesen Abteilungen und Kunden oder zwischen verschiedenen Abteilungen desselben Unternehmens dar. DRP (Distribution Requirements Planning) koordiniert Nachfrage, Angebot und Ressourcen zwischen den Abteilungen eines oder mehrerer Unternehmen.
In einer Lieferkette kann es zwei oder mehr Ebenen von Produktions- und/oder Vertriebseinheiten geben. Diese Abteilungen können unterschiedlich stark voneinander abhängig sein; Der wichtige Punkt ist, dass eine Abteilung Produkte an eine andere Abteilung liefern kann.
Beispielsweise stellt ein Unternehmen Waren auf dem Gebiet einer Abteilung her und verkauft sie über ein separates Verkaufslager.
Ein anderes Unternehmen verfügt möglicherweise über ein zentrales Vertriebszentrum, das Produkte an die Lager regionaler Niederlassungen liefert.
Und das dritte Beispiel: Das Unternehmen verfügt über Produktionsstätten in zwei Städten.
Bei der Planung von Materialangebot und -nachfrage zwischen Abteilungen werden drei Hauptfragen beantwortet:
- Was müssen wir (von anderen Abteilungen) bekommen?
- Was werden wir (an andere Abteilungen) liefern?
- Was können wir liefern?
Obwohl diese Fragen denen der Materialbedarfsplanung (MRP) ähneln, gibt es einen grundlegenden Unterschied. Im MRP reicht es aus zu wissen, was und wann Nachfrage und Angebot erwartet werden. Wenn es mehrere Abteilungen gibt, zwischen denen Produkte ständig bewegt werden, muss DRP wissen, wo (von welcher Abteilung) die Nachfrage/das Angebot entstanden ist.
Die Antwort auf die Frage „Was müssen wir bekommen?“ schafft Bedarf an Materialien, die von einer anderen Abteilung geliefert werden müssen. DRP berechnet alle diese Anforderungen vollständig (nach dem Start von MRP).
Auf die Frage „Was liefern wir?“ Die Antwort ergibt sich aus der Bewertung aller Nachfragequellen für ein Produkt, einschließlich Kundenbestellungen, Versandprognosen, Teilebedarf, Sicherheitsbestand und werksübergreifender Nachfrage.
Anhand von Daten zu werksübergreifenden Anfragen und Vertriebsaufträgen werden Nachfrage und Angebot zwischen den Abteilungen überwacht. Basierend auf Daten über den Bedarf einer Abteilung an Materialien, die von einer anderen Abteilung geliefert werden, erstellt DRP Anfragen zwischen diesen Abteilungen.
Die Antwort auf die letzte Frage „Was können wir liefern“ hängt von der Verfügbarkeit von Materialien (Lieferung) und Transportmitteln (Ressourcen) ab. Wenn die Nachfrage das Angebot übersteigt, kann DRP verwendet werden, um Materialien in einem bestimmten Verhältnis mehreren Abteilungen zuzuweisen.