So erstellen Sie ein Warenwirtschaftssystem. MRP II-Standard
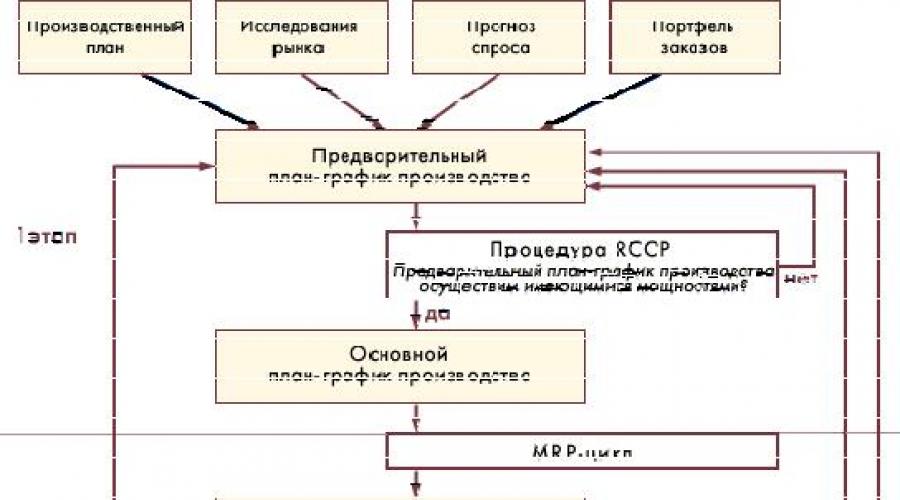
Lesen Sie auch
Seite 1 von 3
Eines der beliebtesten Logistikkonzepte der Welt, auf dessen Grundlage es entwickelt wurde und betrieben wird große Menge Mikrologistiksystemen ist das Konzept der „Anforderungs-/Ressourcenplanung“ (RP). Dem RP-Konzept wird häufig das Just-in-Time-Logistikkonzept gegenübergestellt, d. h. darauf aufbauend Push-Logistikkonzepte (im Gegensatz zum JIT-Ansatz).
Die grundlegenden Mikrologistiksysteme, die auf dem Konzept der „Bedarfs-/Ressourcenplanung“ in Produktion und Versorgung basieren, sind die Systeme „Materialien/Fertigungsbedarf/Ressourcenplanung“ (MRP I/MRP II) und in der Distribution (Distribution) – Systeme zur „Produkt-/Ressourcenverteilungsplanung“ (Verteilungsbedarf/Ressourcenplanung, DRP I, DRP II).
MRP-Systeme werden praktisch bei der Organisation von Produktions- und Technologieprozessen sowie beim Einkauf von Materialressourcen eingesetzt. Gemäß der Definition des amerikanischen Forschers J. Orlisky, einem der Hauptentwickler des MRP-I-Systems, besteht das „Materialbedarfsplanungssystem (MRP-System) im engeren Sinne aus einer Reihe logisch zusammenhängender Verfahren, Schlüsselregeln und.“ Anforderungen, die den Produktionsplan in eine zeitlich synchronisierte „Anforderungskette“ umwandeln, sowie die geplante Abdeckung dieser Anforderungen für jede Bestandseinheit an Komponenten, die zur Einhaltung des Zeitplans erforderlich sind... Das MRP-System plant die Reihenfolge der Anforderungen neu und Abdeckung aufgrund von Änderungen im Produktionsplan, in der Lagerstruktur oder in den Produkteigenschaften.“
MRP-Systeme befassen sich mit Materialien, Komponenten, Halbzeugen und deren Teilen, deren Nachfrage von der Nachfrage nach bestimmten Fertigprodukten abhängt. Obwohl das Logistikkonzept selbst, das die Grundlage des MRP-I-Systems bildet, schon vor längerer Zeit (seit Mitte der 1950er Jahre) entwickelt wurde, konnte es erst mit dem Aufkommen von Hochgeschwindigkeitscomputern umgesetzt werden üben. Gleichzeitig kam es zu einer Revolution im Mikroprozessor- und Informationstechnologie hat das schnelle Wachstum verschiedener Anwendungen von MRP-Systemen in der Wirtschaft stimuliert.
Die Hauptziele von MRP-Systemen:
– Deckung des Bedarfs an Materialien, Komponenten und Produkten für die Produktionsplanung und Lieferung an Verbraucher;
– Aufrechterhaltung eines niedrigen Bestands an Materialressourcen, unfertigen Produkten und Fertigprodukten;
– Planung von Produktionsabläufen, Lieferplänen, Einkaufsvorgängen.
Bei der Erreichung dieser Ziele stellt das MRP-System den Fluss der geplanten Menge an Materialressourcen und Produktbeständen über den Planungshorizont sicher. Das MRP-System ermittelt zunächst, wie viele Endprodukte in welchem Zeitraum produziert werden müssen. Das System ermittelt dann die Uhrzeit und erforderliche Menge Materialressourcen, um den Produktionsplan einzuhalten. In Abb. Abbildung 1 zeigt ein Blockdiagramm des MRP I-Systems.
Der Input des MRP-I-Systems sind Verbraucherbestellungen, unterstützt durch Nachfrageprognosen für die Fertigprodukte des Unternehmens, die im Produktionsplan enthalten sind (Freigabepläne für Fertigprodukte). Wie bei Mikrologistiksystemen, die auf den Prinzipien des Just-in-Time-Konzepts basieren, ist auch bei MRP I die Kundennachfrage der entscheidende Faktor.
Die Datenbank der Materialressourcen enthält alle notwendigen Informationen über die Nomenklatur und die wichtigsten Parameter (Eigenschaften) von Rohstoffen, Materialien, Komponenten, Halbzeugen usw., die für die Herstellung (Montage) von Fertigprodukten oder deren Teilen erforderlich sind. Darüber hinaus enthält es die Normen für den Verbrauch materieller Ressourcen pro Produktionseinheit sowie Aufzeichnungen über die Zeitpunkte der Lieferung der entsprechenden materiellen Ressourcen an die Produktionsabteilungen des Unternehmens.
Die Datenbank identifiziert auch Zusammenhänge zwischen einzelnen Eingaben Produktionseinheiten auf die verwendeten Materialressourcen und auf das Endprodukt. Die Bestandsdatenbank informiert das System und das Managementpersonal über das Vorhandensein und die Größe von Produktions-, Versicherungs- und anderen notwendigen Beständen an Materialressourcen in den Lagereinrichtungen des Unternehmens sowie über deren Nähe zu einem kritischen Niveau und die Notwendigkeit ihrer Auffüllung. Darüber hinaus enthält diese Datenbank Informationen über Lieferanten und Parameter für die Bereitstellung materieller Ressourcen.
MRP-SYSTEM
MRP-Klassensystem (Materialbedarfsplanung)– ein System, das nach einem durch die MRP-Methodik regulierten Algorithmus arbeitet und es Ihnen ermöglicht, die Versorgung des Produktionsprozesses mit Komponenten optimal zu regulieren, die Bestände im Lager und die Produktionstechnologie selbst zu kontrollieren.
Das MRP-Klassensystem basiert auf der Planung des Materialbedarfs einer Abteilung eines Unternehmens und der Organisation als Ganzes.
Das Hauptziel von MRP ist Sicherstellung der Verfügbarkeit der benötigten Menge an benötigten Materialien und Komponenten zu jedem Zeitpunkt innerhalb des Planungszeitraums sowie einer möglichen Reduzierung der Dauerbestände und damit der Entladung des Lagers.
Zwecke der Verwendung des MPR-Standards:
Planung der Lieferung aller Komponenten, um Produktionsausfälle zu vermeiden und Lagerbestände zu minimieren;
Reduzierung der Lagerbestände an Komponentenmaterialien, zusätzlich zur offensichtlichen Entladung von Lagerhäusern;
Die Reduzierung der Lagerkosten bietet eine Reihe unbestreitbarer Vorteile. Der wichtigste davon ist die Minimierung der eingefrorenen Mittel, die in den Materialeinkauf investiert werden.
Eingabeelemente des MRP-Moduls sind die folgenden Informationsressourcen.
Beschreibung des Materialzustands (Inventory Status File) – ist das Haupteingabeelement des MRP-Moduls. Es sollte möglichst vollständige Informationen über alle Arten von Rohstoffen und Komponentenmaterialien enthalten, die für die Herstellung des Endprodukts erforderlich sind. Für jedes Material muss außerdem der Status angegeben werden, ob es vorrätig, im Lager, in laufenden Bestellungen oder nur in Planung ist, sowie Beschreibungen, Bestände, Standort, Preis, mögliche Lieferverzögerungen und Lieferantendetails ;
Produktionsprogramm (Master Production Schedule) – ein optimierter Zeitverteilungsplan für die Produktion der erforderlichen Charge fertiger Produkte für den geplanten Zeitraum oder Zeitraumbereich;
Liste der Komponenten des Endprodukts A(Stücklistendatei) – eine Liste der Materialien und deren Mengen, die zur Herstellung des Endprodukts erforderlich sind. Darüber hinaus enthält es eine Beschreibung des Aufbaus des Endprodukts.
Funktionsprinzip des MRP-Moduls.
Für jeden Zeitraum entsteht ein vollständiger Bedarf an Materialien. Es handelt sich um eine integrierte Tabelle, die den Bedarf an jedem Material zu jedem bestimmten Zeitpunkt angibt.
Es wird die Nettonachfrage berechnet (wie viele Materialien müssen zu einem bestimmten Zeitpunkt bestellt (oder produziert, im Falle der internen Produktion von Komponenten) werden?
Der Nettomaterialbedarf wird in den entsprechenden Bestellplan für die benötigten Materialien umgewandelt. und bei Bedarf werden Änderungen an bereits bestehenden Plänen vorgenommen.
Die Ergebnisse des MRP-Moduls sind:
Bestellplan Geplanter Bestellplan – Wie viel von jedem Material muss in jedem im Planungszeitraum berücksichtigten Zeitraum bestellt werden?
Änderungen am Bestellplan (Änderungen in Planaufträgen) – Änderungen an zuvor geplanten Aufträgen .
Das MRP-Konzept weist einen schwerwiegenden Fehler auf. Bei der Berechnung des Materialbedarfs werden nicht berücksichtigt:
Produktionskapazitäten, ihre Auslastung;
Arbeitskosten usw.
Daher in den 80ern. Das Closed-Loop-MRP-System wurde umgewandelt Produktionsressourcenplanungssystem), das benannt wurde MRPII.
Dabei handelt es sich um ein System der gemeinsamen Planung von Beständen und Produktionsressourcen, gekennzeichnet durch:
geschäftliche Planung;
Verkaufsplanung;
Produktionsplanung;
Planung des Materialbedarfs;
Produktionskapazitätsplanung;
verschiedene Steuerungssysteme.
Der MRPII-Standard wurde in den USA entwickelt und wird von der American Production and Inventory Control Society (APICS) unterstützt.
Anforderungen an MRPII-Klassensysteme – müssen eine bestimmte Menge dieser Grundfunktionen erfüllen:
Vertriebs- und Betriebsplanung.
Nachfragemanagement.
Erstellen eines Produktionsplans (Master Production Scheduling).
Planung des Materialbedarfs(Materialbedarfsplanung).
Produktspezifikationen (Stückliste).
KontrolleLager(Inventartransaktions-Subsystem).
Geplante Lieferungen (Subsystem für geplante Wareneingänge).
Levelmanagement Produktionswerkstatt(Shop-Flow-Steuerung).
Kapazitätsplanung(Kapazitätsbedarfsplanung).
Eingabe-/Ausgabesteuerung.
Material- und technische Versorgung (Einkauf).
Planung der Ressourcenzuteilung(Vertriebsregressplanung).
Planung und Steuerung von Produktionsabläufen (Tooling Planning and Control).
Finanzverwaltung(Finanzielle Planung).
Simulation.
Leistungsmessung.
Die Essenz des MRPII-Konzepts : Prognose, Planung und Produktionssteuerung erfolgen über den gesamten Produktlebenszyklus, vom Einkauf der Rohstoffe bis zum Versand der Produkte an den Verbraucher.
Durch den Einsatz von MRPII-Systemen sollte Folgendes umgesetzt werden:
zeitnaher Erhalt von Informationen über die aktuellen Ergebnisse der Unternehmenstätigkeit, sowohl im Allgemeinen als auch mit allen Einzelheiten zu einzelnen Aufträgen, Ressourcenarten und der Umsetzung von Plänen;
langfristige, operative und detaillierte Planung der Unternehmensaktivitäten mit der Möglichkeit, geplante Daten basierend auf betrieblichen Informationen anzupassen;
Optimierung der Produktions- und Materialflüsse mit einer deutlichen Reduzierung der Nichtproduktionskosten und einer tatsächlichen Reduzierung der Materialressourcen in Lagern;
Spiegelbild der finanziellen Tätigkeit des Unternehmens als Ganzes.
Beispiele für MRPII-Klassensysteme:
Microsoft Dynamics
Galaxy 7.1
Nachteile von MRP-II:
Orientierung nur auf Bestellung,
schlechte Integration von Design und Design,
schlechte Integration des technologischen Prozesssystems,
schlechte Integration von Personalplanung und Finanzmanagement.
[Kurzes Konzept von ERP – Enterprise Resource Planning.
ERP basiert auf dem Prinzip, ein einziges Data Warehouse (Repository) zu erstellen, das alle Geschäftsinformationen enthält, die von einer Organisation im Rahmen der Geschäftsabwicklung gesammelt werden, einschließlich Finanzinformationen, Daten im Zusammenhang mit der Produktion, der Personalverwaltung und anderen Informationen. Dadurch entfällt die Notwendigkeit, Daten von System zu System zu übertragen. Darüber hinaus wird jeder Teil der von einer bestimmten Organisation gespeicherten Informationen gleichzeitig allen Mitarbeitern mit entsprechenden Befugnissen zugänglich gemacht. Das ERP-Konzept ist im Fertigungssektor sehr bekannt geworden, da die Ressourcenplanung kürzere Durchlaufzeiten, geringere Lagerbestände und ein verbessertes Kundenfeedback bei gleichzeitiger Reduzierung des Verwaltungsaufwands ermöglicht hat. Der ERP-Standard ermöglichte es, alle Unternehmensressourcen zu bündeln und damit Auftragsverwaltung, Finanzen usw. hinzuzufügen.]
Als weitere, insbesondere finanzielle, in die Liste der bei der Planung berücksichtigten Ressourcen aufgenommen wurden, tauchte der Begriff ERP (Enterprise Resource Planning) auf – Ressourcenplanung auf Unternehmensebene.
Der Unterschied zwischen MRP II- und ERP-Konzepten besteht darin, dass ersteres produktionsorientiert ist, während letzteres geschäftsorientiert ist. Beispielsweise werden Kreditbedingungen von Kunden für den Versand fertiger Produkte von ERP abgedeckt, nicht jedoch von MRP II. OLAP-Tools, Entscheidungsunterstützungstools – gehören zu ERP-, aber nicht zu MRP/MRP II-Systemen.
Die Grundkonzepte des Produktionsmanagements (einschließlich des Begriffs „ERP“) können als durchaus etabliert gelten. Der anerkannte „De-facto-Standard“ in diesem Bereich ist die Terminologie der American Production and Inventory Control Society (APICS). Grundlegende Begriffe und Definitionen finden Sie im APICS-Wörterbuch, das regelmäßig im Zuge der Weiterentwicklung von Managementtheorie und -praxis aktualisiert wird. Diese Veröffentlichung enthält die vollständigste und genaueste Definition eines ERP-Systems.
Laut APICS Dictionary kann der Begriff „ERP-System“ (Enterprise Resource Planning) in zwei Bedeutungen verwendet werden.
Erstens handelt es sich um ein Informationssystem zur Identifizierung und Planung aller Unternehmensressourcen, die für Vertrieb, Produktion, Einkauf und Buchhaltung im Rahmen der Erfüllung von Kundenaufträgen erforderlich sind.
Zweitens (im allgemeineren Kontext) handelt es sich um eine Methodik zur effektiven Planung und Verwaltung aller Unternehmensressourcen, die für Vertrieb, Produktion, Einkauf und Buchhaltung zur Ausführung von Kundenaufträgen in den Bereichen Produktion, Vertrieb und Dienstleistungserbringung erforderlich sind.
Unternehmensressourcen, die für Vertrieb, Produktion, Einkauf und Buchhaltung bei der Ausführung von Kundenaufträgen in den Bereichen Produktion, Vertrieb und Dienstleistungserbringung erforderlich sind.
Somit kann der Begriff ERP nicht nur ein Informationssystem bedeuten, sondern auch die entsprechende Managementmethodik, die von diesem Informationssystem implementiert und unterstützt wird.
Hauptfunktionen des ERP-Systems:
Die meisten modernen ERP-Systeme sind modular aufgebaut, was dem Kunden die Möglichkeit gibt, nur die Module auszuwählen und zu implementieren, die er wirklich benötigt. Module verschiedener ERP-Systeme können sich sowohl im Namen als auch im Inhalt unterscheiden. Es gibt jedoch eine Reihe von Funktionen, die als typisch für Softwareprodukte der ERP-Klasse gelten können.
Diese typischen Funktionen sind:
Einhaltung von Design- und Technologiespezifikationen. Solche Spezifikationen definieren die Zusammensetzung des Endprodukts sowie die Materialressourcen und Arbeitsgänge, die zu seiner Herstellung erforderlich sind (einschließlich Routing);
Nachfragemanagement und Erstellung von Verkaufs- und Produktionsplänen. Diese Funktionen sind für die Bedarfsprognose und Produktionsplanung konzipiert;
Planung des Materialbedarfs. Ermöglicht die Bestimmung der Mengen verschiedener Arten von Materialressourcen (Rohstoffe, Materialien, Komponenten), die zur Erfüllung des Produktionsplans erforderlich sind, sowie von Lieferzeiten, Losgrößen usw.;
Bestandsverwaltung und Einkaufsaktivitäten. Ermöglicht die Organisation der Vertragsverwaltung, die Implementierung eines zentralisierten Beschaffungsschemas, die Sicherstellung der Buchhaltung und Optimierung der Lagerbestände usw.;
Produktionskapazitätsplanung. Mit dieser Funktion können Sie die Verfügbarkeit der verfügbaren Kapazität überwachen und deren Auslastung planen. Beinhaltet eine groß angelegte Kapazitätsplanung (zur Beurteilung der Machbarkeit von Produktionsplänen) und eine detailliertere Planung bis hin zu einzelnen Arbeitsplätzen;
Finanzfunktionen. Zu dieser Gruppe gehören Finanzbuchhaltungsfunktionen, Managementbuchhaltung sowie operatives Finanzmanagement; \Projektmanagementfunktionen. Sorgen Sie für die Planung von Projektaufgaben und Ressourcen, die für deren Umsetzung erforderlich sind.
Die Hauptidee des MRP-Systems, die Hauptelemente von MRP, MRP II (Manufactory Resource Planning), die Logik des MRP II-Systems, konzentrierten sich auf die (diskrete) Montageproduktion. Entwicklung von MRP II: Erweiterung auf „Nicht- „diskrete“ Produktionsarten. Merkmale der Implementierung von MRP-II-Systemen
1.MRP (Materialbedarfsplanung)
In den 60er Jahren wurde durch die Bemühungen der Amerikaner Joseph Orlicky und Oliver Weight eine Methode zur Berechnung der für die Produktion benötigten Materialien entwickelt, die sogenannte MRP (Material Requirements Planning). notwendige Materialien). Dank der gezielten Arbeit der American Association for Inventory and Production Management (APICS) hat sich die MRP-Methode in der gesamten westlichen Welt verbreitet und wird in einigen Ländern (einschließlich Russland) sogar als Standard behandelt, obwohl sie keiner ist .
In welchen Fällen ist der Einsatz von MRP-Systemen sinnvoll?
Zunächst ist festzuhalten, dass MRP-Systeme für den Einsatz in Produktionsbetrieben entwickelt wurden. Wenn das Unternehmen über eine diskrete Produktionsart verfügt (Assemble to Order – ATO, Make to Order – MTO, Make to Warehouse – MTS, Serial – RPT), d. h. Wenn für hergestellte Produkte eine Stückliste und Produktzusammensetzung vorliegt, ist der Einsatz eines MRP-Systems logisch und angemessen. Verfügt das Unternehmen über eine Prozessproduktion (Prozessindustrie, Continuous-Batch-Processing), ist der Einsatz der MRP-Funktionalität bei einem langen Produktionszyklus gerechtfertigt.
MRP-Systeme werden selten zur Planung des Materialbedarfs in Dienstleistungs-, Transport-, Handels- und anderen Nicht-Produktionsorganisationen verwendet, obwohl die Ideen von MRP-Systemen möglicherweise mit einigen Annahmen auf Nicht-Produktionsunternehmen angewendet werden können, deren Aktivitäten Planungsmaterialien über einen relativen Zeitraum erfordern lange Zeit.
MRP-Systeme basieren auf der Materialplanung zur optimalen Organisation der Produktion und beinhalten direkt Funktionen zur Beschreibung und Planung der Auslastung von Produktionskapazitäten CRP (Capacity Resources Planning) und zielen darauf ab, optimale Bedingungen für die Umsetzung des Produktionsplans zur Produktfreigabe zu schaffen.
2. Die Grundidee des MRP-Systems
Die Grundidee von MRP-Systemen besteht darin, dass jede Buchhaltungseinheit
Materialien oder Komponenten, die zur Herstellung eines Produkts benötigt werden, müssen zum richtigen Zeitpunkt und in der richtigen Menge verfügbar sein.
Der Hauptvorteil von MRP-Systemen ist die Bildung einer Abfolge von Produktionsabläufen mit Materialien und Komponenten, die eine rechtzeitige Produktion von Komponenten (Halbzeugen) zur Umsetzung des Hauptproduktionsplans für die Herstellung von Fertigprodukten gewährleistet.
3. Grundelemente der MRP
Die Hauptelemente eines MRP-Systems können in Elemente unterteilt werden, die Informationen bereitstellen (Software-Implementierung der algorithmischen Basis von MRP) und Elemente, die das Ergebnis der Funktionsweise der Software-Implementierung darstellen
Abbildung 1 – Elemente des MRP-Systems
In vereinfachter Form werden die Ausgangsinformationen für das MRP-System durch folgende Elemente repräsentiert:
1) Master-Produktionsplan (MPS)
Der Hauptproduktionsplan wird in der Regel erstellt, um den Bestand an Fertigprodukten aufzufüllen oder Kundenaufträge zu erfüllen.
In der Praxis scheint die Entwicklung der EVP eine Planungsschleife zu sein. Zunächst wird ein Entwurf erstellt, um die Möglichkeit einer Sicherstellung der Umsetzung im Hinblick auf materielle Ressourcen und Kapazitäten zu prüfen.
Das MRP-System detailliert die operative Planung in Bezug auf Materialkomponenten. Sollte der benötigte Artikel und seine quantitative Zusammensetzung nicht im freien oder bereits bestellten Bestand vorhanden sein, oder im Falle unbefriedigender geplanter Lieferungen von Materialien und Komponenten, muss der OPP entsprechend angepasst werden.
Nach den erforderlichen Iterationen wird der betriebliche Prozess als gültig genehmigt und auf dieser Grundlage werden Produktionsaufträge gestartet.
2) Stückliste und Produktzusammensetzung
Eine Stückliste ist eine Nomenklaturliste von Materialien und deren Mengen für die Produktion einer bestimmten Einheit oder eines Endprodukts. Zusammen mit der Zusammensetzung des Produkts ermöglicht die Stückliste die Erstellung einer vollständigen Liste der fertigen Produkte, der Menge der Materialien und Komponenten für jedes Produkt und einer Beschreibung der Struktur des Produkts (Baugruppen, Teile, Komponenten, Materialien usw.). ihre Beziehungen).
Bei der Stückliste und der Produktzusammensetzung handelt es sich um Datenbanktabellen, deren Informationen die relevanten Daten korrekt wiedergeben. Wenn sich die physische Zusammensetzung des Produkts ändert, muss der Status der Tabellen rechtzeitig angepasst werden.
3) Lagerstatus
Der aktuelle Stand der Lagerbestände spiegelt sich in den entsprechenden Tabellen wider, in denen alle erforderlichen Merkmale der Buchhaltungseinheiten aufgeführt sind. Jede Abrechnungseinheit
Unabhängig von der Verwendung in einem oder mehreren Endprodukten darf es nur einen identifizierenden Datensatz mit einem eindeutigen Code haben. Typischerweise enthält ein Datensatz zur Identifizierung einer Buchhaltungseinheit eine große Anzahl von Parametern und Merkmalen, die vom MRP-System verwendet werden und wie folgt klassifiziert werden können:
Allgemeine Daten: Code, Beschreibung, Typ, Größe, Gewicht usw.
Bestandsdaten: Bestandseinheit, Lagereinheit, freier Bestand, optimaler Bestand, geplant für Bestellung, bestellter Bestand, zugewiesener Bestand, Chargen-/Serienattribut usw.
Einkaufs- und Verkaufsdaten: Einkaufs-/Verkaufseinheit, Hauptlieferant,
Daten zu Produktion und Fertigungsaufträgen etc.
Die Aufzeichnungen der Buchhaltungseinheiten werden immer dann aktualisiert, wenn Bestandstransaktionen durchgeführt werden, z. B. für den Kauf geplant, zur Lieferung bestellt, aktiviert, Ausschuss usw.
Basierend auf den MRP-Eingabedaten führt das System die folgenden Grundoperationen durch:
Basierend auf dem operativen Planungsprozess wird für jeden Planungszeitraum die quantitative Zusammensetzung der Endprodukte ermittelt;
Die Zusammensetzung der Endprodukte umfasst Ersatzteile, die nicht im Lieferumfang enthalten sind
Für OPP und Ersatzteile wird der Gesamtbedarf an Materialressourcen anhand der Stückliste und der Zusammensetzung des Produkts ermittelt, verteilt nach Planungszeiträumen;
Der gesamte Materialbedarf wird basierend auf dem Bestandsstatus für jeden Planungszeitraum angepasst;
Aufträge zur Wiederauffüllung der Lagerbestände werden unter Berücksichtigung der notwendigen Vorlaufzeiten generiert.
Die Ergebnisse des MRP-Systems sind:
Zeitplan für die Bereitstellung von Materialressourcen für die Produktion – die Menge jeder Buchhaltungseinheit an Materialien und Komponenten für jeden Zeitraum, um die betriebliche Produktion sicherzustellen. Zur Umsetzung des Lieferplans erstellt das System einen auf Zeiträumen basierenden Bestellplan, der zur Auftragserteilung an Lieferanten von Materialien und Komponenten oder zur Planung verwendet wird selbstgemacht;
Änderungen im Lieferplan – Anpassungen des zuvor erstellten Produktionslieferplans;
Eine Reihe von Berichten, die zur Verwaltung des Produktionsversorgungsprozesses erforderlich sind.
Eine der Komponenten des Integrierten Informationssysteme Das Unternehmensmanagement der MRP-Klasse ist ein Produktionskapazitätsplanungssystem
Die Hauptaufgabe des CRP-Systems besteht darin, die Machbarkeit von MPS im Hinblick auf die Beladung von Ausrüstung entlang produktionstechnologischer Routen unter Berücksichtigung von Umrüstzeiten, erzwungenen Stillstandszeiten, Unterauftragsarbeiten usw. zu überprüfen. Die Eingangsinformationen für CRP sind der Zeitplan für Produktionsaufträge und Aufträge für die Lieferung von Materialien und Komponenten, der gemäß den technologischen Routen in die Beladung von Ausrüstung und Arbeitspersonal umgewandelt wird.
Typische Funktionalität von MRP-Systemen:
Beschreibung der Planungseinheiten und Planungsebenen
Beschreibung der Planungsvorgaben
Erstellung des Hauptproduktionsplans
Produktmanagement (Beschreibung von Materialien, Komponenten und fertigen Produkteinheiten)
Bestandsverwaltung
Produktkonfigurationsmanagement (Produktzusammensetzung)
Führen einer Stückliste
Berechnung des Materialbedarfs
Bildung von MRP-Bestellungen
Generierung von MRP-Transferaufträgen
Arbeitsplätze (Beschreibung der Struktur von Produktionsarbeitsplätzen mit Kapazitätsermittlung)
Maschinen und Mechanismen (Beschreibung Produktionsausrüstung mit Ermittlung der Normleistung)
Produktionsvorgänge, die im Zusammenhang mit Arbeitsplätzen und Ausrüstung durchgeführt werden
Prozessrouten stellen eine Abfolge von Vorgängen dar, die über einen bestimmten Zeitraum an bestimmten Geräten in einem bestimmten Arbeitsplatz ausgeführt werden
Berechnung des Kapazitätsbedarfs zur Ermittlung der kritischen Last und zur Entscheidungsfindung
4.MRP II (Manufaktur-Ressourcenplanung)
In den 80er Jahren wurden die Grundprinzipien der MRP- (Material Requirements Planning) und CRP- (Capacity Requirements Planning) Methoden entwickelt
Kapazitätsbedarfsplanung), Closed Loop MRP (Bedarfsplanung).
Materialien in einem geschlossenen Kreislauf) wurden in einer einzigen Planungsmethodik zusammengefasst - MRP II (Manufactory Resource Planning, Fertigungsressourcenplanung).
Die römische Zahl „II“ im Namen der neuen MRP II-Methodik entstand aufgrund der Ähnlichkeit der Abkürzungen Manufactory Resource Planning und Material Requirements Planning und
weist auf mehr hin hohes Niveau Planung im Vergleich zur Materialbedarfsplanung. Manchmal wird es weggelassen, wenn aus dem Kontext klar ist, um welches System es sich handelt.
Die MRP II-Methodik beschreibt die End-to-End-Planung und das Kettenmanagement
„Verkauf – Produktion – Lager – Versorgung.“ Im Gegensatz zu früheren Planungsmethoden liegt der Schwerpunkt auf der operativen Planung und dem Management des gesamten Produktionsprozesses und nicht seiner einzelnen Fragmente.
Die MRP II-Methodik zielt auf die Lösung folgender Hauptaufgaben ab:
1. Erstellen Sie einen grundlegenden Produktionsplan (Volumen-
Kalenderplan, Master Production Schedule (MPS), der beschreibt, was und in welcher Menge das Unternehmen in jeder Periode des Planungssegments produzieren wird. Einerseits sollte dieser Plan das bestehende Auftragsportfolio möglichst umfassend berücksichtigen und Marktforschung Nachfrage zu erfüllen, um Kundenbedürfnisse zeitnah zu erfüllen, aber auch keine überschüssigen Produkte zu produzieren, die anschließend lange im Lager liegen und auf ihren Käufer warten. Andererseits muss der erstellte Plan angesichts der aktuellen Vermögensstruktur des Unternehmens (Produktionskapazität, Personal, finanzielle Unterstützung) umsetzbar sein. Einen Kompromiss zwischen Zufriedenheit finden Marktnachfrage und die Machbarkeit eines solchen Produktionsprogramms ist sehr wichtige Aufgabe, und es wird erfolgreich mit der MRP II-Methodik gelöst.
2. Erstellen Sie Betriebspläne, die die Umsetzung des genehmigten Produktionsprogramms offenbaren: Produktionsarbeitsplan, Zeitplan für die Rohstoffbeschaffung, Plan für die Verwendung von Bargeld. Nach diesen Plänen ist das gesamte Produktionstätigkeit Unternehmen. Allerdings bietet MRP II einen Mehrwert für diese Pläne, da die Methodik die wichtige Aufgabe der Optimierung des Ressourcenverbrauchs berücksichtigt. Bei der Planung geht es nämlich darum, die verbrauchten Ressourcen (Geld, Materialien, Produktionskapazität) optimal über den gesamten Planungsabschnitt zu verteilen. Einerseits ist es notwendig, die Einhaltung des Hauptproduktionsplans und eine unterbrechungsfreie Produktion sicherzustellen Fertigungsprozess und verhindern andererseits die Entstehung überhöhter Lagerbestände. Um dieses Ziel zu erreichen, ist eine integrierte Planung des Ressourcenbedarfs erforderlich, d. h. Planungsbedarfe auf der Ebene aller am Produktionsprozess beteiligten Abteilungen (Produktion, Lager, Versorgung und Vertrieb) unter Berücksichtigung des komplexen Beziehungssystems zwischen diesen Abteilungen.
Die Implementierung der MRP II-Methodik in ein spezifisches Informationssystem setzt das Vorhandensein von Rückmeldungen voraus, die über die Qualität der Umsetzung der erstellten Pläne informieren und gegebenenfalls Anpassungen dieser Pläne ermöglichen.
Ursprünglich wurde die MRP II-Methodik für die (diskrete) Montageproduktion entwickelt. Ein klassisches Beispiel für diskrete Fertigung ist der Maschinenbau. Ohne auf Details einzugehen, kann die diskrete Fertigung wie folgt definiert werden: Es handelt sich um die Produktion oder den Zusammenbau eines Endprodukts, basierend auf einer hierarchischen Beschreibung der Zusammensetzung des Produkts. Anschließend wurden ähnliche Planungsprinzipien und -methoden für andere Produktionsarten entwickelt.
5. Funktionslogik des MRP II-Systems mit Schwerpunkt auf der Montage (diskreten) Produktion
Der Betrieb des MRP II-Systems ist klar in drei Stufen unterteilt. Die ersten beiden umfassen die Umsetzung der MRP-II-Methodik und enden mit der Genehmigung von Plänen. Letzteres geschieht parallel zum eigentlichen Produktionsprozess und umfasst die Überwachung der Umsetzung der erstellten Pläne und die zeitnahe Anpassung des Produktionsprozesses bei Bedarf:
Figur 2
1) Basierend auf Bestellungen unabhängiger Nachfrage wird der Hauptproduktionsplan erstellt.
·Auf der Grundlage des Produktionsplans, der Marktforschung, der Nachfrageprognose und des Produktauftragsportfolios wird ein vorläufiger Produktionsplan für die Endprodukte erstellt.
· Das RCCP-Verfahren (Rough Cut Capacity Planning, vorläufige Kapazitätsplanung) wird gestartet – eine schnelle Überprüfung der Machbarkeit des erstellten Plans im Hinblick auf verfügbare Kapazitäten und vorhandene Technologie Produktion. Bei diesem Verfahren wird ein Fluss von Aufträgen abhängiger Nachfrage zwischen den am Produktionsprozess beteiligten Abteilungen des Unternehmens erstellt und die Durchführbarkeit dieser Aufträge in vorab identifizierten kritischen Produktionsbereichen (d. h. in Arbeitszentren, die die Schichtproduktion begrenzen oder bestimmen) überprüft Produkte).
·Wenn der vorläufige Produktionsplan für Endprodukte als realistisch realisierbar angesehen wird, wird er zum Hauptproduktionsplan. Andernfalls werden Änderungen am vorläufigen Zeitplan vorgenommen und dieser erneut mit dem RCCP-Verfahren getestet.
2) Basierend auf dem angenommenen Produktionsplan werden die Anforderungen an Materialien, Kapazität und finanzielle Ressourcen geplant.
·Ein Standard-MRP-Zyklus wird gestartet, dessen Hauptergebnis ein Auftragsplan für den Einkauf/die Produktion von Materialien und Komponenten ist.
·Der CRP-Zyklus wird gestartet, der einen Produktionsarbeitsplan bereitstellt, der alle weiteren Produktionsaktivitäten beschreibt.
·Anhand dieser beiden Dokumente wird der Finanzierungsbedarf (Financial Requirements Planning – FRP) für die Durchführung von Produktionsaktivitäten beurteilt. Das heißt, es werden Betriebskosten für Materialeinkauf, Produktionsbedarf, Gehälter des Produktionspersonals etc. berechnet und diese Kosten über den gesamten Planungshorizont verteilt.
3) Gemäß den erstellten Zeitplänen beginnen die eigentlichen Produktionsaktivitäten. Gleichzeitig übernimmt das MRP II-System die operative Steuerung des Produktionsprozesses: Es überwacht die Umsetzung geplanter Aufgaben und nimmt bei Bedarf Anpassungen bestehender Pläne vor.
·Die Erledigung geplanter Aufgaben wird zeitnah im MRP II-System registriert. System, basierend auf dem Vergleich von tatsächlichen und Standardindikatoren, analysiert den Fluss wirtschaftlicher Prozess. Um beispielsweise die Umsetzung von CRP-Plänen zu überwachen, überwacht das MRP II-System die Produktivität jeder Produktionseinheit über den gesamten Planungszeitraum. Die tatsächliche Produktivität wird mit dem Standardproduktivitätsindikator verglichen und wenn die Abweichung einen vorgegebenen akzeptablen Wert überschreitet, signalisiert das System dem Management, dringend in die Arbeit dieser Produktionseinheit einzugreifen und Maßnahmen zur Verbesserung der Produktivität zu ergreifen. Solche Maßnahmen können beispielsweise die Gewinnung zusätzlicher Arbeitskräfte oder die Erhöhung der Regelbetriebszeit einer schwächelnden Produktionseinheit sein. Ebenso überwacht das System den Verbrauch von Materialien und Komponenten durch Produktionseinheiten und zeichnet die Abweichung der tatsächlichen und Standardverbrauchsindikatoren für jede Produktionseinheit auf. Dadurch können Sie schnell eine Situation diagnostizieren, in der eine Produktionseinheit aufgrund unzureichender Materialversorgung nicht die geplante Produktivität erreicht.
·Durch die Analyse des Fortschritts des Produktionsprozesses generiert das MRP II-System täglich Schichtzuweisungen für Arbeitsplätze (Vorgangslisten), die an die Leiter der Arbeitsplätze gesendet werden. Schichtzuweisungen spiegeln die Abfolge der Arbeitsvorgänge an Rohstoffen und Komponenten in jeder Produktionskapazitätseinheit und die Dauer dieser Vorgänge wider. Im Gegensatz zum vom CRP-Modul generierten Produktionsarbeitsplan berücksichtigen diese Werkstattaufgaben automatisch die Verringerung/Erhöhung der Produktionsgeschwindigkeit
Einheiten: Schichtaufträge können sowohl aus irgendeinem Grund verspätete Produktionsaufträge (reduzierte Verarbeitungsgeschwindigkeit) als auch für spätere Planungszeiträume geplante Produktionsaufträge (erhöhte Verarbeitungsgeschwindigkeit) enthalten.
·In gleicher Weise regelt das MRP-II-System durch die Generierung angepasster täglicher Aufgaben für den Einkauf/die Lieferung von Rohstoffen und Komponenten die Arbeit der Versorgungs-, Verkaufs- und Lagerstrukturen des Unternehmens.
6. Entwicklung von MRP II: Erweiterung auf „nicht-diskrete“ Produktionsarten
Wie oben erwähnt, wurden die MRP II-Methodik und die MRP II-Systeme ursprünglich für die Montageindustrie entwickelt. Allerdings sind über 40 % der Industrieunternehmen weltweit Unternehmen mit einer anderen Produktionsart –
Verfahren.
Nach der von der Gartner Group vorgeschlagenen Klassifizierung lässt sich die gesamte Produktionsvielfalt auf drei Haupttypen reduzieren:
1) Designproduktion;
2) diskrete Produktion;
3) Prozessproduktion.
Die Projektproduktion ist eine einmalige einmalige Produktion (z. B. Raketentechnik, Schiffbau), deren Technologie nicht vorbestimmt ist.
Hauptsächlich Kennzeichen Unter diskreter Produktion versteht man das Vorhandensein zählbarer Einheiten hergestellter Produkte, die wiederum aus einzelnen Komponenten zusammengesetzt sind. Daher ist in der diskreten Fertigung die Grundlage für die Herstellung (Montage) des Endprodukts eine hierarchische Beschreibung der Zusammensetzung des Produkts (d. h. das Design oder die Fertigungsspezifikation des Endprodukts). Ein klassisches Beispiel für diskrete Fertigung ist der Maschinenbau.
In der diskreten Industrie gibt es mehrere deutlich unterschiedliche Arten der Produktionsorganisation:
·Produktion zum Lager (Make-To-Stock – MTS): Das Produktionsvolumen wird auf der Grundlage der „optimalen Auslastung der Produktionskapazität“ geplant; es wird davon ausgegangen, dass alle produzierten Produkte verkauft werden;
· Auftragsfertigung (Make-To-Order – MTO): Das Produktionsvolumen wird auf der Grundlage der eingegangenen Bestellungen für Produkte geplant, und es gibt:
Auftragsentwicklung (Engineering-To-Order – ETO), wenn Sie mit dem Design des bestellten Produkts, der Entwicklung von Design und technologischer Dokumentation beginnen müssen;
o Montage auf Bestellung (Assembling-To-Order – ATO), bei der die bereits im Unternehmen vorhandene Konstruktions- und Technologiedokumentation für verschiedene Komponenten verwendet wird, jedoch je nach Kundenauftrag geringfügige Abweichungen in der Zusammensetzung des Produkts zulässig sind (In diesem Fall wird davon ausgegangen, dass alle Erstkomponenten im Lager verfügbar sind.)
Die Prozessproduktion besteht aus einer Reihe technologischer Prozesse (z. B. Mischen, Lösen, Erhitzen), die zu keinem Zeitpunkt unterbrochen werden können. Zusätzlich zum Endprodukt entstehen bei der Prozessfertigung typischerweise viele Nebenprodukte und verwandte Produkte.
Technologischer Prozess ist in der Regel in mehrere Stufen unterteilt, die durch das Rezept beschrieben werden. Am Ausgang desselben Prozesses können unterschiedliche Produkte erhalten werden, abhängig beispielsweise von der Konzentration der Ausgangskomponenten. Temperaturregime, Katalysatoren. Einige Prozesse können rekursiv wiederholt werden (Recycle).
Prozessindustrien zeichnen sich durch untrennbare interne Verbindungen zwischen ihnen aus verschiedene Arten Produkte, die in einem Prozess hergestellt werden. Beispielsweise werden bei der Ölraffinierung in einer Anlage gleichzeitig Erdölprodukte von Gasöl und Benzin bis hin zu Heizöl und Bitumen hergestellt, deren Zusammensetzung nicht verändert werden kann.
Entsprechend der Eigenschaft der Diskretion/Kontinuität in der Zeit der Freigabe des Endprodukts werden unter den verarbeitenden Industrien jeweils sich wiederholende Industrien unterschieden (z. B. Pharmazie, Lebensmittelindustrie, Zellstoff- und Papierproduktion, chemische Industrie) und kontinuierlich (z. B. Energie, Öl- und Gasförderung, Petrochemie, Primärmetallurgie).
Jede Produktionsart hat ihre eigene spezifische Planung und Verwaltung. Wenn sie bei der Planung diskreter Produktionen von den volumetrischen Indikatoren von Produktionsplänen und einer genau definierten Zusammensetzung des Endprodukts ausgehen, stützen sie sich bei der Projektproduktion auf eine Liste der Arbeiten zum Projekt und ihrer Beziehungen (d. h. sie erstellen so- sogenannte Netzwerkdiagramme). In der Prozessindustrie stehen Kapazitätsauslastungsindikatoren und technologische Prozessvariabilität an erster Stelle.
Ursprünglich für die diskrete Fertigung entwickelt, entsprach die MRP II-Methodik nicht den Besonderheiten anderer Produktionsarten. Versuche, das zugrunde liegende mathematische Modell für die Anwendung beispielsweise in der Prozessfertigung „anzupassen“, führten zu so unrealistischen Ergebnissen wie negativen Produktionszeiten und negativem Ressourcenverbrauch. Aufgrund der grundlegenden Unterschiede zwischen der diskreten und der Prozessindustrie konnte dieser Ansatz keine Wirkung entfalten. Daher wurden originelle mathematische Modelle und Algorithmen zur Lösung des Problems der Ressourcenplanung für die Prozess- und Designproduktion erstellt, die die Grundlage für die Erstellung von MRP-II-Systemen bildeten, die sich auf „nicht-diskrete“ Produktionsarten konzentrierten.
Charakteristisches Merkmal Bei klassischen MRP-II-Systemen handelt es sich um eine Spezialisierung auf eine bestimmte (eine oder mehrere) Produktionsart. Allerdings in In letzter Zeit Hersteller von MRP II-Systemen modifizieren ihre Produkte, erweitern die Funktionalität und übertragen sie auf neue Plattformen. Dies ist auf den harten Wettbewerb auf dem Markt für Informationsmanagementsysteme und damit auf den Wunsch nach maximaler Kundenzufriedenheit zurückzuführen.
Als Ergebnis der Weiterentwicklung der MRP-II-Systeme entstand eine neue Klasse von Systemen (Enterprise Resource Planning, Corporate Resource Planning).
7.Merkmale der Implementierung von MRP-II-Systemen
Derzeit wird in Russland mit Hilfe von MRP-II-Systemen häufig versucht, veraltete Buchhaltungs- oder hausgemachte Informationssysteme durch ein leistungsfähigeres, moderneres und modischeres Unternzu ersetzen.
Die Ergebnisse einer solchen Implementierung sind nicht schwer vorherzusagen: Nach einem Jahr, zwei, drei Jahren Implementierung wird das System funktionieren, aber in der Regel wird es schlechter sein als das alte. Was nicht verwunderlich ist, da es sich hierbei um ein anderes System handelt, von dem die gleichen Ergebnisse verlangt werden wie vom alten.
Einer der ausländischen Berater sprach darüber ähnliche Situation wie folgt: „Ein MRP-II-Klassensystem ist nur so effektiv wie das Personal und die Geschäftsprozesse des Unternehmens.“ Je weniger Komplikationen es in diesen Prozessen gibt (also weniger Aktivitäten, die letztendlich nicht den Gewinn des Unternehmens steigern), desto effektiver wird das MRP-II-System sein. Viele Unternehmen haben versucht und versuchen heute, ihre bestehenden Geschäftsprozesse mithilfe des implementierten MRP-II-Klassensystems zu beschreiben. Mit dieser Implementierung „automatisieren“ sie lediglich die derzeitige Art und Weise, ein Unternehmen zu betreiben, ohne sie überhaupt zu verbessern. Erinnern goldene Regel: Wenn Sie weiterhin so arbeiten, wie Sie es getan haben, werden Sie bekommen, was Sie bekommen haben.“
Am Ende gilt die Umsetzung als gescheitert und das System selbst, genauer gesagt das Fehlen der gewünschten Funktionalität darin, wird für den Misserfolg verantwortlich gemacht.
Warum? Die Antwort ist einfach. Trotz der Tatsache, dass es auf dem russischen Markt viele Unternehmen gibt, die gerne ein MRP-II-System an ein Unternehmen verkaufen, wird eine erfolgreiche Implementierung nicht ohne die harte Arbeit des gesamten Unternehmensteams möglich sein. MRP-II ist nicht Computer Programm. Dies ist ein betriebswirtschaftliches Konzept, das durch den Computer ermöglicht wird. Aus diesem Grund hängen die Faktoren, die den Erfolg oder Misserfolg der Implementierung von MRP-II-Systemen beeinflussen, weitgehend von den Anstrengungen zur Implementierung des Systems ab. Die Erfahrung mit der Implementierung von MRP-II-Systemen auf der ganzen Welt (Russland ist keine Ausnahme) legt nahe, dass Sie zunächst auf die folgenden Punkte achten sollten:
Umsetzungsziele mit Unternehmenszielen verknüpfen;
Verwendung eines Teamansatzes;
Änderungsmanagement;
Ausbildung;
Qualifizierte Berater gewinnen.
Umsetzungsziele
Bevor ein Projekt zur Implementierung des MRP-II-Systems geplant wird, müssen zunächst die globalen Ziele des Unternehmens formuliert werden, um festzulegen, wohin das Unternehmen in einem Jahr, zwei, fünf oder mehr gehen möchte. Dementsprechend sollten Sie die Größe des Unternehmens, das Verkaufsvolumen in Rubel und in physischer Hinsicht, die Anzahl der Mitarbeiter und die erforderliche Ausrüstung planen. Der Plan sollte wertmäßige Verkaufsmengen nach Produktgruppen, Informationen darüber, wie sie hergestellt werden, unter ausschließlicher Nutzung der Fähigkeiten des Unternehmens oder auf andere Weise usw. enthalten. Diese Schätzungen dienen als Grundlage für die Entwicklung der Struktur des Unternehmens oder der Unternehmensgruppe. mit deren Hilfe die gesetzten Ziele erreicht werden. Anschließend sollten Ziele auf einer detaillierteren Ebene definiert werden, woraufhin mit der Planung der Ressourcen begonnen werden kann, die zur Sicherstellung eines bestimmten Produktionsniveaus erforderlich sind. Als nächstes müssen Sie den Zustand des Unternehmens heute realistisch einschätzen.
Basierend auf den gewonnenen Basisinformationen muss der Bedarf an zusätzlichen Ressourcen ermittelt werden, um das Umsatzwachstum des Unternehmens sicherzustellen. Dadurch wird das zukünftige Informationssystem die Unternehmensführung übersichtlicher machen, die Effizienz der Organisation steigern, Ressourcen sparen und letztendlich das Geschäft auf ein neues Niveau heben, ohne zusätzliche Investitionen anzuziehen.
Team-Ansatz
Die Implementierung des MRP-II-Systems erfordert erhebliche Anstrengungen und Ressourcen des Unternehmens. Und es sind die Manager des Unternehmens, die für die Verteilung dieser Ressourcen sorgen müssen: Generaldirektor(Präsident) des Unternehmens sowie Leiter (Direktoren) der Hauptabteilungen. Da es sich bei Systemen der MRP-II-Klasse in der Regel um integrierte Systeme handelt, ist eines davon typische Ergebnisse Bei der Umsetzung gilt Folgendes: Abteilungen, die sich traditionell nicht gegenseitig vertrauten und um Ressourcen konkurrierten, sind gezwungen, ihre Anstrengungen zu bündeln, um die Umsetzungsziele zu erreichen. Dies wird durch den Teamansatz bei der Implementierung solcher Systeme erleichtert.
Änderungsmanagement
Die Einführung des MRP-II-Systems und damit verbundene Veränderungen in den Geschäftsprozessen des Unternehmens können bei einem erheblichen Teil des Unternehmenspersonals Angst auslösen. Dies ist eine natürliche Angst vor Veränderungen, ein Widerwillen, das aufzugeben, was in der Vergangenheit, wenn auch schlecht, funktioniert hat, und das völlig Unbekannte und Beängstigende Neue zu akzeptieren. Der beste Weg, diese Angst zu überwinden, ist die Schulung des Personals. Nur wenn man versteht, was in Zukunft genau von ihnen verlangt wird und was sie als Gegenleistung erhalten (z. B. wird ihre Arbeit effizienter, Arbeitsplätze bleiben erhalten, das Unternehmen gelangt in eine neue Entwicklungsstufe usw.) , wird das Personal in der Lage sein, effektiv am Projekt zu arbeiten, Methoden und Wesen der Funktionsweise des Unternehmens zu ändern und zu nutzen notwendige Werkzeuge(Wissen). Es ist wichtig anzumerken, dass es hier nicht so sehr um die Schulung im Umgang mit einem Informationssystem geht, sondern vielmehr um die Frage, wie man mit einem Informationssystem umgeht Allgemeinbildung: MRP-II-Konzepte, Change Management, Management Accounting etc.
Ausbildung
Die Einführung neuer Geräte oder Informationssysteme erfordert die Schulung des Personals für die Interaktion mit ihnen sowie die Verfügbarkeit geeigneter Unterstützung und Unterstützung. Das heißt, eine ständige Aus- und Weiterbildung des Personals, eine Verbesserung oder Entwicklung neuer Verfahren sind notwendig.
Einsatz von Beratern
Der Berater hilft bei der Festlegung von Zielen, der Planung der Umsetzung und des Projektmanagements und sorgt für die Schulung des Personals. Ein guter Berater „holt“ so viel aus dem System heraus, wie das Unternehmen nutzen kann. Aber er wird niemals die Verantwortung für die Endergebnisse der Umsetzung übernehmen. Das Unternehmen und jeder seiner Mitarbeiter müssen selbst Eigentümer des betreffenden Teils des Systems werden und die Verantwortung für dessen Funktionieren übernehmen.
Vorlesung 10. Enterprise-Resource-Planning-Systeme – ERP (ERP, Enterprise Resource Planning)
Allgemeines Verständnis von ERP. Entstehungsgeschichte von ERP-Systemen Konzept und Funktionen von ERP-Systemen. Produktion: vor dem Aufkommen von ERP, mit dem Aufkommen von ERP. Implementierungserfahrung: Vor- und Nachteile
MRP-System als Ganzes:
Beschreibung der Planungseinheiten und Planungsebenen;
Beschreibung der Planungsvorgaben;
Erstellung des Hauptproduktionsplans.
MRP-Subsystem:
Produktmanagement (Beschreibung von Materialien, Komponenten und fertigen Produkteinheiten);
Bestandsverwaltung;
Produktkonfigurationsmanagement (Produktzusammensetzung);
Führen einer Stückliste;
Berechnung des Materialbedarfs;
Bildung von MRP-Bestellungen;
Bildung von MRP-Bewegungsaufträgen.
CRP-Subsystem:
Arbeitsplätze (Beschreibung der Struktur von Produktionsarbeitsplätzen mit Kapazitätsermittlung);
Maschinen und Mechanismen (Beschreibung der Produktionsausrüstung mit Bestimmung der Standardkapazität);
Produktionsvorgänge, die im Zusammenhang mit Arbeitsplätzen und Ausrüstung durchgeführt werden;
Prozessrouten, die eine Abfolge von Vorgängen darstellen, die über einen bestimmten Zeitraum an bestimmten Geräten in einem bestimmten Arbeitsplatz ausgeführt werden;
Berechnung des Kapazitätsbedarfs zur Ermittlung der kritischen Last und zur Entscheidungsfindung.
19. MRPII-Klassensysteme. Unterschiede zu MRP, Struktur des MRPII-Systems, Vorteile der Verwendung von MRPII-Systemen.
Allerdings hat das MRP-Konzept einen gravierenden Nachteil. Tatsache ist, dass bei der Berechnung des Materialbedarfs im Rahmen dieses Konzepts weder die verfügbare Produktionskapazität noch deren Auslastung noch die Arbeitskosten berücksichtigt werden. Dieser Mangel wurde im MRPII-Konzept (Manufacturing Resource Planning) behoben. MRPII ermöglichte die Berücksichtigung und Planung aller Produktionsressourcen des Unternehmens – Rohstoffe, Betriebsstoffe, Ausrüstung, Personal usw.
Mit der Entwicklung des MRPII-Konzepts wurde nach und nach die Möglichkeit hinzugefügt, auch andere Unternehmenskosten zu berücksichtigen. So entstand das Konzept des ERP (Enterprise Resource Planning), manchmal auch Enterprise Resource Planning genannt
Das MRPII-System sollte aus folgenden Funktionsmodulen bestehen (Abbildung 3):
Modul zur Geschäftsentwicklungsplanung bestimmt die Mission des Unternehmens: seine Marktnische, Bewertung und Bestimmung des Gewinns, finanzielle Ressourcen. Tatsächlich gibt er in finanzieller Hinsicht an, was das Unternehmen produzieren und verkaufen will, und schätzt, wie viel Geld in die Entwicklung und Weiterentwicklung des Produkts investiert werden muss, um die geplante Gewinnhöhe zu erreichen. Das Ausgabeelement dieses Moduls ist somit ein Businessplan.
Vertriebsplanungsmodul schätzt (normalerweise in Einheiten des fertigen Produkts), wie groß das Volumen und die Dynamik des Umsatzes sein müssen, damit der festgelegte Geschäftsplan erfüllt werden kann. Änderungen im Verkaufsplan werden zweifellos zu Änderungen in den Ergebnissen anderer Module führen.
Produktionsplanungsmodul genehmigt den Produktionsplan für alle Arten von Fertigprodukten und deren Eigenschaften. Jeder Produkttyp innerhalb der Produktlinie verfügt über ein eigenes Produktionsprogramm. Somit stellt der Satz von Produktionsprogrammen für alle Arten von hergestellten Produkten den Produktionsplan des gesamten Unternehmens dar.
Modul zur Materialbedarfsplanung(oder Arten von Dienstleistungen) legt auf der Grundlage des Produktionsprogramms für jede Art von Fertigprodukt den erforderlichen Zeitplan für den Einkauf und/oder die interne Produktion aller Materialkomponenten dieses Produkts und dementsprechend für deren Montage fest.
Modul zur Kapazitätsplanung wandelt den Produktionsplan in endgültige Einheiten der Arbeitskapazitätsauslastung um (Maschinen, Arbeiter, Labore usw.)
Die Entwicklung von Unternehmensinformationssystemen erfolgte in mehreren Schritten. Um die Produktion optimal zu verwalten, hat APICS – American Production and Inventory Control Society (American Society for Production and Inventory Control) Grundsätze für die Verwaltung von Unternehmensbeständen entwickelt. Diese Prinzipien liegen dem Konzept der MRP (Material Requirements Planning – Planung des Bedarfs des Unternehmens an materiellen Ressourcen) zugrunde.
In der ersten Phase in den 1970er Jahren. Es wurden Systeme implementiert, die dem MRP-Enterprise-Management-Standard entsprachen. Die Einführung von Systemen, die diese Methodik implementieren, ermöglichte es, Produktion, Planung und Bestandsverwaltung in einem einzigen Geschäftsprozess zu integrieren. Allerdings berücksichtigten diese Systeme Produktionskapazitäten, deren Auslastung, Arbeitsressourcen etc. nicht, weshalb das Konzept von MRP II (MRP – Manufacturing Resources Planning) – einem Pro– entstand. Anschließend wurde dieses Konzept entwickelt, und zwar am Ende des 20. Jahrhunderts. gekennzeichnet durch das Aufkommen von ERP-Systemen - Enterprise Resource Planning-Systemen (Enterprise Resource Planning), die auf dem Prinzip der Erstellung eines einzigen Data Warehouse basieren, das alle Geschäftsinformationen enthält, die von der Organisation im Prozess der Geschäftsabwicklung gesammelt werden, einschließlich Finanzinformationen, Daten im Zusammenhang mit Produktionsmanagement, Personalmanagement und anderen Informationen. Darüber hinaus wird jeder Teil der von der Organisation gespeicherten Informationen gleichzeitig allen Mitarbeitern mit entsprechenden Befugnissen zugänglich gemacht.
MRP-Konzept:
Minimierung der Kosten im Zusammenhang mit Lagerbeständen und in verschiedenen Produktionsbereichen. Diesem Konzept liegt das Konzept einer Produktspezifikation (Bill of Material – BOM) zugrunde, die die Abhängigkeit des Bedarfs an Rohstoffen, Halbfabrikaten etc. vom Produktionsplan für Fertigprodukte (unter Berücksichtigung der Zeit) aufzeigt. . Basierend auf dem Produktionsplan, den Produktspezifikationen und unter Berücksichtigung der Merkmale der Technologiekette wird der Produktionsbedarf an Materialien berechnet (notwendigerweise an bestimmte Fristen gebunden). Das MRP-Konzept bildete die Grundlage für den Aufbau sogenannter MRP-Systeme.
MRPII-Konzept:
Effektives Management alle Ressourcen produzierendes Unternehmen, Prognosen, Planung und Produktionssteuerung werden durchgehend durchgeführt Lebenszyklus Produkte, angefangen beim Einkauf der Rohstoffe bis hin zum Versand der Produkte an den Verbraucher. Das MRP-Konzept weist einen schwerwiegenden Fehler auf. Bei der Berechnung des Materialbedarfs werden Produktionskapazitäten, deren Auslastung, Arbeitskosten etc. nicht berücksichtigt. Daher in den 80ern. Das Closed-Loop-MRP-System wurde in ein Pronamens MRPII umgewandelt. Ziel: Sicherstellung der Planung der Unternehmensaktivitäten in physischen Einheiten, finanzieller Kennzahlen in monetärer Hinsicht, Modellierung der Fähigkeiten des Unternehmens, Beantwortung der Frage „Was passiert, wenn?“
APICS-Standard für MRPII-Klassensysteme enthält eine Beschreibung von 16 Gruppen von Systemfunktionen:
Vertriebs- und Produktionsplanung.
Nachfragemanagement.
Erstellung eines Produktionsplans.
Planung des Materialbedarfs.
Produktspezifikationen.
Lagerverwaltung.
Geplante Lieferungen.
Management auf der Ebene der Produktionswerkstatt.
Planung des Kapazitätsbedarfs.
Ein-/Ausreisekontrolle.
Logistik.
Planung der Ressourcenzuteilung.
Planung und Verwaltung von Werkzeugen.
Finanzverwaltung.
Modellieren.
Auswertung der Leistungsergebnisse.
Sie ermöglichen die Integration von Planungsfunktionen, einschließlich der Koordination verschiedener Managementprozesse in Zeit und Raum. Der vorgestellte Modulsatz ist nicht redundant und bleibt daher hauptsächlich in Systemen nachfolgender Generationen erhalten.
Unternehmensmanagementsystem ERP:
In den frühen 90ern. Das Analyseunternehmen Gartner Group hat ein neues Konzept eingeführt. Systeme der MRPII-Klasse in Integration mit dem Finanzplanungsmodul FRP (Finance Requirements Planning) werden ERP-Systeme (Enterprise Resource Planning) genannt. Manchmal wird auch der Begriff unternehmensweite Ressourcenplanung verwendet. ERP macht die Übertragung von Daten von einem System in ein anderes überflüssig und stellt außerdem die gleichzeitige Verfügbarkeit von Informationen für eine beliebige Anzahl von Unternehmensmitarbeitern mit entsprechenden Befugnissen sicher.
Hauptmodule von ERP-Systemen:
Finanzverwaltung;
Materialwirtschaft;
Produktionskontrolle;
Projektmanagement;
Kontrolle Service;
Qualitätskontrolle;
Personalmanagement.
Zusätzliche ERP-Module (APICS-Standard):
Supply Chain Management – SCM (Supply Chain Management);
Verbesserte Planung und Zusammensetzung Produktionspläne– APS (Advanced Planning and Scheduling);
Kundenbeziehungsmanagement – CRM (Customer Relationship Management);
E-Commerce– EC (Elektronischer Handel);
Produktdatenmanagement – PDM (Produktdatenmanagement) oder PLM (Produktlebenszyklusmanagement);
Business-Intelligence-Add-on, das Tools im Bereich intelligenter Business Analytics (Aufbau von Data Warehouses, OLAP, Data Mining, Visualisierung und Reporting) und weitere Module umfasst.
Hauptrichtungen der ERP-Entwicklung:
Vertiefung der ERP-Funktionalität.
Erstellung spezialisierter Branchenlösungen.
Verbesserung der Module zur Verwaltung unternehmensübergreifender Geschäftsprozesse.
Entwicklung von Architektur (SOA – Serviceorientierte Architektur) und Anwendungsintegrationstools.
Beispiele für ERP-Systeme:
Oracle E-Business Suite
SAP Business One
1C:Enterprise 8.0
Microsoft Dynamics
und andere.
Enterprise Resource and Relationship Management System ERP II (CSRP):
ERP II (Enterprise Resource & Relationship Processing – „Management von Unternehmensressourcen und -beziehungen“, vorgeschlagen von der Gartner Group) ist das Ergebnis der Entwicklung der ERP-Methodik und -Technologie hin zu einer engeren Interaktion zwischen einem Unternehmen und seinen Kunden und Gegenparteien. Gleichzeitig werden die Managementinformationen des Unternehmens nicht nur für interne Zwecke genutzt, sondern dienen auch dem Aufbau kooperativer Beziehungen mit anderen Organisationen. In vereinfachter Form handelt es sich bei ERP II um ein verbessertes ERP-System, in das Produkte der Klassen SCM (Supplier Relationship Management) und CRM (Customer Relationship Management) integriert sind, sowie ein Unternehmens-Internetportal, über das die Mitarbeiter des Unternehmens alles Notwendige erhalten können Informationen und schnelle Interaktion untereinander, mit Partnern und Kunden.
Das ERP II-Konzept zielt darauf ab, Außenbeziehungen zu automatisieren und ein sogenanntes „virtuelles Unternehmen“ zu schaffen, das das Zusammenspiel von Produktion, Lieferanten, Partnern und Verbrauchern widerspiegelt und aus autonom agierenden Unternehmen oder einem temporären Zusammenschluss von Unternehmen besteht, die an demselben Projekt arbeiten. Programm usw. Das ERP II-System verfügt auch über die Funktionen Finanzmanagement, Buchhaltung, Verkaufs- und Einkaufsmanagement, Beziehungen zu Debitoren und Gläubigern, Personalmanagement, Produktion, Bestandsverwaltung und ermöglicht die Verwaltung von Kundenbeziehungen, Lieferketten und Handel über das Internet.