Principes d'organisation du processus de production. Principes et méthodes d'organisation du processus de production
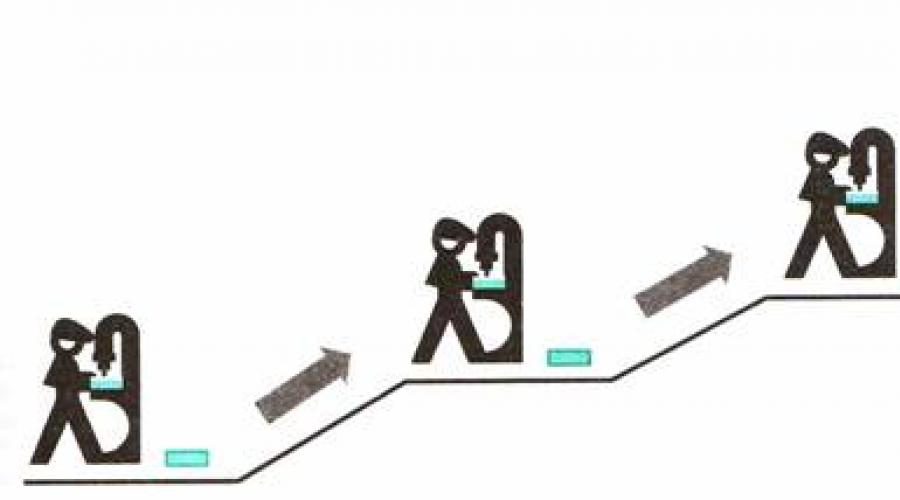
100 roubles bonus pour la première commande
Sélectionnez le type de travail Thèse Travaux de cours Résumé Mémoire de maîtrise Rapport sur la pratique Article Rapport Revue Test Monographie Résolution de problèmes Plan d'affaires Réponses aux questions Travail créatif Essai Dessin Travaux Traduction Présentations Dactylographie Autre Augmenter l'unicité du texte Mémoire de maîtrise Travaux de laboratoire Aide en ligne
Découvrez le prix
Organisation processus de production dans toute entreprise de construction de machines, dans l'un de ses ateliers, sur un site, elle repose sur une combinaison rationnelle dans le temps et dans l'espace de tous les processus principaux, auxiliaires et de service. Cela permet de fabriquer des produits avec un coût de la vie et une main-d'œuvre matérielle minimes. Les caractéristiques et les méthodes de cette combinaison varient selon les différentes conditions de production. Cependant, dans toute leur diversité, l'organisation des processus de production est soumise à certaines conditions. principes généraux: différenciation, concentration et intégration, spécialisation, proportionnalité, rectitude, continuité, parallélisme, rythme, automaticité, prévention, flexibilité, optimalité, électronisation, standardisation, etc.
Principe différenciation implique de diviser le processus de production en processus technologiques distincts, eux-mêmes divisés en opérations, transitions, techniques et mouvements. Parallèlement, l'analyse des caractéristiques de chaque élément permet de choisir meilleures conditions pour sa mise en œuvre, en garantissant la minimisation des coûts totaux de tous les types de ressources. Ainsi, la production en ligne s'est développée depuis de nombreuses années en raison d'une différenciation de plus en plus profonde des processus technologiques. La sélection d'opérations à court terme a permis de simplifier l'organisation et l'équipement technologique de la production, d'améliorer les compétences des travailleurs et d'augmenter leur productivité du travail.
Cependant, une différenciation excessive augmente la fatigue des travailleurs lors des opérations manuelles en raison de la monotonie et de la forte intensité des processus de production. Un grand nombre d'opérations entraîne des coûts inutiles pour déplacer les objets de travail entre les lieux de travail, les installer, les sécuriser et les retirer des lieux de travail une fois les opérations terminées.
Lors de l'utilisation d'équipements flexibles modernes et performants (machines CNC, centres d'usinage, robots, etc.), le principe de différenciation se transforme en principe de concentration des opérations et d’intégration des processus de production. Principe de concentration consiste à réaliser plusieurs opérations sur un même poste de travail (machines CNC multibroches et multi-coupes). Les opérations deviennent plus volumineuses, plus complexes et sont réalisées en combinaison avec le principe d'équipe de l'organisation du travail. Principe d'intégration consiste à combiner les principaux processus auxiliaires et de service.
Principe spécialisations est une forme de division du travail social qui, se développant systématiquement, détermine la répartition des ateliers, des sections, des lignes et des emplois individuels dans l'entreprise. Ils fabriquent une gamme limitée de produits et se distinguent par un processus de production spécial.
En règle générale, la réduction de la gamme de produits entraîne une amélioration de tous les indicateurs économiques, en particulier une augmentation du niveau d'utilisation des immobilisations de l'entreprise, une réduction des coûts de production, une amélioration de la qualité des produits, une mécanisation et une automatisation de la production. processus. Les équipements spécialisés, toutes choses égales par ailleurs, fonctionnent de manière plus productive.
Principe de proportionnalité suppose un débit égal de tous les départements de production effectuant des processus principaux, auxiliaires et de service. La violation de ce principe conduit à l'émergence de goulots d'étranglement dans la production ou, à l'inverse, à une utilisation incomplète des postes de travail individuels, des sections, des ateliers et à une diminution de l'efficacité de l'ensemble de l'entreprise. Par conséquent, pour garantir la proportionnalité, les calculs de capacité de production sont effectués à la fois par étapes de production et par groupes d'équipements et zones de production.
Principe du flux direct désigne une telle organisation du processus de production qui garantit les chemins les plus courts pour le passage des pièces et des unités d'assemblage à travers toutes les étapes et opérations depuis le lancement des matières premières en production jusqu'à la sortie des produits finis. Les flux de matières, de produits semi-finis et d'unités d'assemblage doivent être progressifs et les plus courts, sans mouvements de contre-courant ou de retour. Ceci est assuré par une planification appropriée du placement des équipements le long du parcours. processus technologique. Un exemple classique d’un tel agencement est une ligne de production.
Principe de continuité signifie que le travailleur travaille sans temps d'arrêt, que l'équipement fonctionne sans interruption et que les objets de travail ne se trouvent pas sur le lieu de travail. Ce principe se manifeste le plus pleinement dans la production de masse ou à grande échelle lors de l'organisation de méthodes de production continue, en particulier lors de l'organisation de lignes de production continues mono- et multi-objets. Ce principe assure une réduction du cycle de fabrication des produits et contribue ainsi à une intensification accrue de la production.
Principe parallèle implique l'exécution simultanée de processus de production partiels et d'opérations individuelles sur des pièces similaires et des parties d'un produit sur différents lieux de travail, c'est-à-dire la création d'un large éventail de travaux pour la fabrication d'un produit donné. Le parallélisme dans l'organisation du processus de production est utilisé sous diverses formes : dans la structure d'une opération technologique - usinage multi-outils (machines semi-automatiques multibroches multi-coupes) ou exécution parallèle d'éléments principaux et auxiliaires d'opérations ; dans la fabrication d'ébauches et le traitement des pièces (en ateliers, ébauches et pièces à différents stades de préparation) ; en unité et en assemblée générale. Le principe de parallélisme assure une réduction des temps de cycle de production et un gain de temps de travail.
Le principe du rythme assure la libération de volumes égaux ou croissants de produits sur des périodes de temps égales et, par conséquent, la répétition de ces périodes du processus de production à toutes ses étapes et opérations. Avec une spécialisation étroite de la production et une gamme de produits stable, le rythme peut être assuré directement par rapport aux produits individuels et est déterminé par le nombre de produits transformés ou fabriqués par unité de temps. Dans le contexte d'une gamme large et changeante de produits fabriqués par le système de production, le rythme du travail et de la production ne peut être mesuré qu'à l'aide d'indicateurs de main-d'œuvre ou de coût.
Principe automatique implique l'exécution maximale des opérations du processus de production automatiquement, c'est-à-dire sans la participation directe d'un travailleur à celui-ci ou sous sa supervision et son contrôle. L'automatisation des processus conduit à une augmentation du volume de production de pièces et de produits, à une augmentation de la qualité du travail, à une réduction des coûts de main-d'œuvre humaine, au remplacement du travail manuel peu attrayant par un travail plus intellectuel de travailleurs hautement qualifiés (ajusteurs, opérateurs ), à l'élimination du travail manuel dans les travaux comportant des conditions dangereuses et au remplacement des travailleurs par des robots. L'automatisation des processus de service est particulièrement importante. automatique Véhicules et les entrepôts remplissent des fonctions non seulement de transfert et de stockage des objets de production, mais peuvent également réguler le rythme de toute production. Le niveau général d'automatisation des processus de production est déterminé par la part du travail dans les industries principales, auxiliaires et de services dans le volume total de travail de l'entreprise.
Principe de prévention consiste à organiser la maintenance des équipements visant à prévenir les accidents et les temps d'arrêt systèmes techniques. Ceci est réalisé grâce à un système de maintenance préventive programmée (PPR).
Le principe de flexibilité fournit organisation efficace travail, permet de passer mobile à la production d'autres produits inclus dans le programme de production de l'entreprise, ou à la production de nouveaux produits lors de la maîtrise de sa production. Il permet de réduire le temps et les coûts de changement d'équipement lors de la production de pièces et de produits d'une large gamme. Ce principe reçoit le plus grand développement dans des conditions de production hautement organisées, où sont utilisés des machines CNC, des centres d'usinage (MC) et des moyens automatiques reconfigurables de contrôle, de stockage et de déplacement des objets de production.
Principe d'optimalité est que la mise en œuvre de tous les processus de production de produits dans une quantité donnée et dans les délais est réalisée avec le plus grand l'efficacité économique ou avec le moins de main-d'œuvre et de ressources matérielles. L'optimalité est déterminée par la loi du gain de temps.
Principe d'électronisation implique l'utilisation généralisée des capacités CNC basées sur l'utilisation de la technologie des microprocesseurs, ce qui permet de créer des systèmes de machines fondamentalement nouveaux combinant une productivité élevée avec les exigences de flexibilité des processus de production. ordinateur et robots industriels, possédant une intelligence artificielle, permettent d'effectuer les fonctions les plus complexes de la production à la place d'une personne.
Principe de normalisation implique le recours généralisé à la standardisation, à l'unification, à la typification et à la normalisation dans la création et le développement de nouveaux équipements et de nouvelles technologies, ce qui permet d'éviter une diversité déraisonnable des matériaux, des équipements et des procédés technologiques et de réduire fortement la durée du cycle de la création et le développement de nouveaux équipements (SONT).
Lors de la conception d'un processus de production ou d'un système de production, l'utilisation rationnelle des principes énoncés ci-dessus doit être prise en compte.
Sous processus de production est compris comme un ensemble de processus de travail divers mais interconnectés et processus naturels assurer la transformation des matières premières en produit fini.
Le processus de production comprend des processus principaux, auxiliaires, de service et secondaires.
À principal Il s'agit notamment des procédés directement liés à la transformation de matières premières ou de matériaux en produits finis (céréales en farine, betteraves sucrières en sucre). La combinaison de ces processus dans l'entreprise constitue la production principale.
Dans les entreprises de réception de céréales qui stockent les ressources céréalières de l'État, les principaux processus devraient également inclure les processus liés à la réception, au placement et au stockage des céréales.
But auxiliaire X procédés - entretenir techniquement les principaux procédés, leur fournir certains services : approvisionnement en énergie, production d'outils et d'appareils, travaux de réparation.
Préposés les processus fournissent des services matériels à la production principale et auxiliaire. Réception, placement, stockage des matières premières, matériaux, produits finis, carburants, leur transport depuis les lieux de stockage vers les lieux de consommation, etc.
Effets secondaires Les processus contribuent également à transformer les matières premières en produits finis. Mais ni les matières premières ni les produits obtenus n'appartiennent aux principaux produits de l'entreprise. Il s'agit du traitement et de la finalisation des déchets obtenus dans la production principale, etc.
Tous les processus sont divisés en étapes et les étapes en opérations individuelles.
Étape de production- une partie technologiquement complète du processus de production, caractérisée par de tels changements dans le sujet du travail qui provoquent sa transition vers un état qualitatif différent (nettoyage des betteraves sucrières, produits d'emballage).
Chaque étape combine des opérations technologiquement liées les unes aux autres, ou des opérations dans un but précis.
Le maillon principal du processus de production est l’exploitation.
Opération de fabrication- cela fait partie du processus de travail ou de production, effectué par un ou un groupe de travailleurs dans un lieu distinct, avec le même sujet de travail, en utilisant les mêmes moyens de travail.
Par but Toutes les opérations sont divisées en trois types principaux :
1) technologique (de base) - ce sont des opérations au cours de l'exécution desquelles le sujet du travail (son état, sa forme ou apparence) des modifications sont apportées (séparation du lait, broyage des grains, etc.) ;
2) les opérations de contrôle sont des opérations qui n'apportent aucune modification au sujet du travail, mais contribuent à la mise en œuvre d'opérations technologiques (pesage, etc.) ;
3) déplacement – opérations qui modifient la position du sujet du travail dans la production (chargement, déchargement, transport).
Les opérations de contrôle et de déplacement constituent ensemble un groupe d'opérations auxiliaires.
Par mode d'exécution (degré de mécanisation) On distingue les opérations suivantes :
- machine– effectués par des machines sous la surveillance d'ouvriers (rouler des conserves, nettoyer le lait, hacher des produits) ;
- manuel de la machine– réalisé par des machines avec la participation directe des ouvriers (battage de la farine, couture de sacs, etc.) ;
- manuel opérations - effectuées par des travailleurs sans la participation de machines (approvisionnement en matières premières des convoyeurs, empilage des sacs).
Rapport divers types les opérations dans leur nombre total constituent la structure du processus de production. Ce n'est pas la même chose dans les différentes usines de transformation.
Organisation de la production dans le temps sont construits sur la base des principes suivants :
Le rythme de travail de l’entreprise et l’uniformité de la production des produits ;
Proportionnalité des unités de production ;
Parallélisme (simultanéité) des opérations et des processus de production ;
Continuité des processus de production.
Le principe du rythme prévoit le fonctionnement de l'entreprise selon un rythme planifié (le délai entre la sortie de produits identiques ou de deux lots de produits identiques).
Le principe de proportionnalité Ces unités de production supposent la même productivité par unité de temps.
Principe parallèle l'exécution des opérations et des processus repose sur l'exécution simultanée de phases, d'étapes ou de parties du processus de production.
Principe de continuité le processus de production prévoit l'élimination des interruptions dans le traitement des objets de travail. La continuité du processus élimine la création de stocks sur les lieux de travail et réduit les travaux en cours, ce qui est particulièrement important dans les entreprises où les matières premières ne peuvent pas être stockées longtemps sans réfrigération, congélation, mise en conserve (conserves de fruits et légumes, industries laitières, de viande). .
But organisation du processus de production dans l'espace est d’assurer sa construction rationnelle dans le temps.
La plus grande efficacité dans l'organisation du processus de production dans l'espace est obtenue grâce à l'utilisation du flux direct, de la spécialisation, de la coopération et de la combinaison de la production.
Rectitude processus de production, se caractérise par le fait qu'à toutes les phases et opérations de production, les produits subissent chemin le plus court. À l'échelle de l'entreprise, les ateliers sont implantés sur le territoire de manière à exclure les transports longue distance, aller-retour, au comptoir et autres transports irrationnels. C'est-à-dire que les lieux de travail et les équipements sont situés dans une séquence technologique d'opérations.
Spécialisation en usine est le processus de séparation des ateliers et des zones pour la production de certains types de produits, de leurs pièces ou la mise en œuvre d'étapes individuelles du processus technologique. Les entreprises de transformation utilisent une spécialisation technologique, thématique et fonctionnelle.
Spécialisation technologique la production implique d'isoler une gamme étroite d'opérations technologiques et d'effectuer des opérations dans des ateliers ou des zones de production séparés.
Spécialisation du sujet la production implique la création de lignes distinctes avec un cycle de production complet pour la production d'un ou plusieurs produits similaires en termes de technologie de fabrication.
Fonctionnel est appelé la spécialisation de tous les départements de production pour remplir une ou une gamme limitée de fonctions.
Coopération la production dans l'entreprise est réalisée par l'organisation collaboration ses divisions de produits. Le principe de la coopération productive est l'utilisation des services de certains ateliers par d'autres.
La recherche de formes rationnelles de coopération conduit dans certains cas à la création d'industries combinées.
Combinaison la production implique la connexion dans une entreprise de différentes installations de production, représentant des étapes successives de transformation des matières premières ou jouant un rôle de soutien les unes par rapport aux autres.
Tout type d'activité industrielle nécessite une construction compétente du processus de production, compris comme la procédure de transformation du sujet du travail (matières premières, matériaux, produits semi-finis) en quelque chose de nécessaire à la société.
L'organisation présuppose une combinaison rationnelle de ses éléments : le travail (activités des personnes), (outils de production), processus naturels(chimique, physique, biologique), visant à modifier les propriétés de l'objet de travail - sa forme, sa taille, sa qualité ou son état.
Principes d'organisation rationnelle du processus de production.
Les processus de production existants sont extrêmement divers, mais ils reposent sur bonne organisation Il existe certains principes qui permettent d'optimiser l'activité industrielle.
Le principe de différenciation. Conformément à ce principe, l'organisation du processus de production doit être réalisée de manière à ce que les processus ou opérations spécifiques qui constituent la base du schéma de production soient attribués aux divisions individuelles de l'entreprise.
Le principe de combinaison. Il s'agit de l'unification de tout ou partie des opérations de nature différente au sein d'une même unité de production (atelier, section, unité).
À première vue, ces principes se contredisent. Lequel d'entre eux doit être préféré détermine la complexité du produit fabriqué et sa faisabilité pratique.
Le principe de concentration. Ce principe signifie l'unification au sein d'un même domaine de production de travaux sur la fabrication de produits homogènes ou la mise en œuvre d'opérations d'exécution identiques. Son utilisation permet d'utiliser plus efficacement un type d'équipement (sa charge augmente), augmentant ainsi la flexibilité des processus technologiques.
Le principe de spécialisation. Il s'agit d'attribuer à chaque zone de travail un nombre précisément limité d'opérations, de travaux et de produits. Le niveau de spécialisation est déterminé par la nature des pièces produites, ainsi que par le volume quantitatif de leur production. Plus le niveau de spécialisation d’une entreprise est élevé, meilleures sont les compétences des travailleurs et plus la productivité du travail est élevée. Dans le même temps, la possibilité d'automatiser les augmentations de production et les coûts associés au changement d'équipement sont réduits. L'inconvénient est la monotonie du travail et la fatigue rapide des personnes.
Le principe d’universalisation est à l’opposé du principe de spécialisation. L'organisation du processus de production, basée sur ce principe, implique la production de divers produits (ou la mise en œuvre de processus hétérogènes) au sein d'une même unité de travail. La production d'une large gamme de pièces nécessite un personnel assez hautement qualifié et la participation d'équipements multifonctionnels.
Le principe de proportionnalité. Une gestion compétente du processus de production est indissociable du maintien des proportions entre les quantités de produits fabriqués par les différents départements de l'entreprise. les zones doivent correspondre à la charge de l'équipement et être comparables entre elles.
Le principe du parallélisme. Il s'agit de la production (transformation) simultanée de divers produits, ce qui permet de gagner du temps consacré à la production du produit final.
Principe du flux direct. Le processus de production doit être organisé de manière à ce que le trajet d'une étape de transformation à l'autre soit le plus court possible.
Le principe du rythme est que tous les processus de production visant à produire des pièces intermédiaires et à produire des produits finaux sont soumis à une répétition périodique. Suivre ce principe nous permet d’assurer un flux de production fluide, sans délais manqués ni temps d’arrêt forcés.
Le principe de continuité suppose un flux uniforme du sujet de travail d'une opération à l'autre sans arrêts ni retards.
Le principe de flexibilité assure une adaptation rapide des sites de production aux changements des réalités de production liés à la transition vers la production de nouveaux types de produits.
Les principes énumérés sont appliqués conformément à leur opportunité pratique. Sous-estimer leur rôle conduit à une augmentation des coûts de production et, par conséquent, à une diminution de la compétitivité des produits manufacturés.
Modalités d'organisation de la production. Le mode d'organisation de la production est un ensemble de méthodes, de techniques et de règles permettant la combinaison rationnelle des principaux éléments de la production
Méthode d'organisation de la production est un ensemble de méthodes, de techniques et de règles pour la combinaison rationnelle des principaux éléments du processus de production dans l'espace et dans le temps aux étapes d'exploitation, de conception et d'amélioration de l'organisation de la production.
Le choix du mode d'organisation de la production est déterminé par la stratégie d'organisation de la production (orientée processus ou orientée produit), le type de production, l'intensité de travail du produit et la nature de sa technologie de production. Lors du choix d'une entreprise stratégie de production orientée processus, dans des conditions de production unique, à petite échelle et en série, ils sont principalement utilisés méthodes sans flux organisation du processus de production. Choix pour une période de temps stratégies d'organisation de la production un ou plusieurs produits ( Composants des produits), axé sur le produit, permet de construire des processus de production selon méthode d'organisation de la production continue.
Mode d'organisation de la production individuelle utilisé dans des conditions de production unique ou de production en petits lots et suppose : un manque de spécialisation sur le lieu de travail ; l'utilisation d'équipements largement universels, leur disposition en groupes selon leur objectif fonctionnel ; mouvement séquentiel des pièces d'une opération à l'autre par lots.
Conditions d'utilisation lieux de travail : les mêmes ensembles d'outils sont utilisés presque constamment et non un grand nombre de appareils universels; remplacement périodique des outils émoussés ou usés ; plusieurs fois au cours du quart de travail, les pièces sont transportées vers les postes de travail et les pièces sont envoyées lorsque de nouveaux travaux sont délivrés et que les travaux terminés sont acceptés, il existe donc un besoin pour une organisation flexible des services de transport pour les lieux de travail.
Mode d'organisation groupée de la production est utilisé dans le cas d'une gamme limitée de produits structurellement et technologiquement homogènes fabriqués en lots répétitifs. L'essence de la méthode est de concentrer sur un site différents types d'équipements technologiques pour traiter un groupe de pièces selon un processus technologique unifié (standard ou groupé).
Figure 10. Localisation des postes de travail (équipements) sur les chantiers
Avec diverses formes organisation de production :
UN– technologique ; b- sujet; V- tout droit;
g– point (pour le cas de montage) ; d- intégré
Signes caractéristiques organisation collective de la production : spécialisation détaillée des unités de production ; lancer la production de pièces par lots selon des calendriers spécialement élaborés ; passage parallèle-séquentiel de lots de pièces à travers les opérations ; exécution dans les centres de travail (sur chantiers, en ateliers) d'un ensemble de travaux technologiquement achevés.
Méthode d'organisation de la production synchronisée. Intègre un certain nombre de fonctions traditionnelles d'organisation des processus de production : planification opérationnelle, contrôle des stocks, gestion de la qualité des produits.
L'essence de la méthode est le refus de produire des produits en grands lots et la création d'une production multi-articles en flux continu, dans laquelle, à toutes les étapes du cycle de production, l'unité ou la pièce requise est livrée sur le lieu de production. opération ultérieure. juste à temps" - exactement au bon moment.
L'utilisation principe de traction dans la gestion de l'avancement de la production - un système de gestion de production « pull » (Fig. 11) : le planning de production est établi uniquement pour le site d'assemblage ; Aucune pièce n'est produite avant d'être nécessaire à l'assemblage final. Ainsi, la zone d'assemblage détermine la quantité et l'ordre de lancement des pièces en production.
Figure 11. Système de gestion de production « Pull » – analogue à la gravité
L’objectif de l’organisation et de la gestion de la production est d’améliorer constamment le travail en éliminant toutes les activités inutiles. Sous inutile, ou action inutile fait référence à tous les processus et objets de gestion de la production qui n'augmentent pas la valeur pour le consommateur des produits. Cet objectif est atteint grâce à la création de lignes de production groupées, multi-sujets et à l'utilisation d'un système de gestion de production « pull ».
Règles de base pour organiser le processus de production : fabriquer des produits en petits lots ; formation de séries de pièces et utilisation de technologies de groupe afin de réduire le temps de configuration des équipements ; transformer les matériaux de stockage et les produits semi-finis en entrepôts tampons ; transition vers une structure de production sans atelier - divisions thématiques ; transfert des fonctions de gestion opérationnelle du processus de production aux exécutants directs.
Le processus de production est contrôlé selon les éléments suivants des principes: le volume, la nomenclature et le calendrier de la tâche sont déterminés par le site (lieu de travail) de la prochaine étape de production ; le rythme de production est fixé par la section qui clôture le processus de production ; la reprise du cycle de production sur le site ne commence que si la commande correspondante est reçue ; l'ouvrier commande le nombre de flans (composants) nécessaires à la réalisation de la tâche reçue, en tenant compte des délais de livraison des pièces (unités d'assemblage) ; la livraison des composants (pièces, unités d'assemblage) sur le lieu de travail est effectuée dans les délais et dans les quantités précisés dans la demande ; les composants, unités et pièces sont fournis au moment de l'assemblage, les pièces individuelles - au moment de l'assemblage des unités, les ébauches nécessaires - au début de la fabrication des pièces ; Seuls les produits de haute qualité sont transférés hors du site.
Une carte est utilisée comme moyen de communiquer des informations sur les besoins en pièces détachées. Kanban».
En figue. La figure 12 montre un schéma d'organisation de la production synchronisée sur le site de broyage.
1. Dès que le prochain lot de pièces est traité sur le site de broyage, le conteneur libéré avec une carte de consommation est envoyé vers un entrepôt intermédiaire.
2. À l'entrepôt, la carte de consommation est retirée du conteneur et placée dans une boîte de collecte spéciale, et le conteneur auquel est attachée la carte de production est acheminé vers la zone de forage.
3. La carte de production sert de signal pour démarrer la production. Il joue le rôle d'une tenue, sur la base de laquelle les pièces sont fabriquées dans la quantité requise.
4. Les pièces de chaque commande terminée sont chargées dans un conteneur vide, une carte de production y est attachée et le conteneur plein est envoyé vers un lieu de stockage temporaire.
5. Depuis l'entrepôt intermédiaire, un conteneur contenant des pièces à usiner et une carte de consommation, qui est attachée à la place d'une carte de production, arrive à la zone de broyage.
Efficacité du système utilisant des cartes " Kanban» est assuré par le respect des règles suivantes :
Riz. 12. Schéma d'organisation de la production synchronisée au niveau de la section de broyage :
I - schéma d'itinéraire du processus de production ;
II - schéma de déplacement des conteneurs avec cartes " Kanban»
La production des pièces ne commence que si une carte de production a été reçue. Il vaut mieux permettre que la production soit suspendue plutôt que de produire des pièces dont on n’a pas besoin ;
Pour chaque conteneur il existe strictement une fiche d'expédition et une fiche de production ; le nombre de conteneurs pour chaque type de pièce est déterminé par calcul.
La méthode de production synchronisée implique l'introduction systèmes intégrés de gestion de la qualité, qui repose sur le respect de certains principes, parmi lesquels : le contrôle qualité pendant le processus de production à toutes les étapes du processus de production, sur chaque lieu de travail ; visibilité des résultats de mesure des indicateurs de qualité ; le respect des exigences de qualité ; correction indépendante des défauts sur les lieux d'apparition ; contrôle qualité continu des produits finis; amélioration continue de la qualité.
La responsabilité de la qualité est redistribuée et devient universelle : chaque unité organisationnelle, dans le cadre de sa compétence, est chargée d'assurer la qualité ; La responsabilité principale incombe aux fabricants de produits eux-mêmes.
Méthode d'organisation de la production automatisée. Utilisation en organisation et gestion de production divers moyens automatisation des processus de travail. L'objectif principal de l'utilisation d'un tel système est d'assurer une réponse rapide de l'entreprise aux commandes des consommateurs et une vitesse de production élevée.
Les principales options pour organiser la production automatisée :
production informatisée (fabrication assistée par ordinateur - FAO). L'utilisation d'ordinateurs dans la gestion du processus de fabrication des produits, du traitement au contrôle automatique de la qualité. Base technique MOI-MÊME se compose de machines et de robots à commande numérique ;
système de production flexible (système de fabrication flexible - FMS). Il s'agit d'un ensemble de mécanismes conçus pour un processus de production cyclique et capables de produire une large gamme de produits similaires. FMS ordinateur de surveillance et de contrôle, moyens de chargement et de déchargement automatiques des matériaux, ainsi que d'autres équipements logiciels automatisés. Les dispositifs de contrôle reprogrammables permettent à ces systèmes de produire une large gamme de produits similaires ;
fabrication intégrée par ordinateur (fabrication intégrée par ordinateur - CIM). C'est un système qui relie les uns aux autres grâce à réseau informatique divers domaines activités de l'entreprise - conception technique, planification et contrôle de la production, systèmes de production flexibles. Système ICM permet d'établir les plannings de production et les achats de matériels, assure la gestion des moyens de production, des ventes et de la distribution.
QUESTIONS ET TÂCHES DU TEST
1. Comment une stratégie d’organisation d’entreprise aide-t-elle une organisation d’entreprise à réaliser sa mission ?
2. Qu'entend-on par structure de production d'une entreprise ?
3. Quelle est la structure de production d'une entreprise avec un cycle technologique complet ?
4. Quelle est la composition des principaux ateliers de l'entreprise ?
5. Quelle est la composition des services auxiliaires de l’entreprise ?
6. Quelle est la composition des installations de services de l’entreprise ?
7. Quels facteurs déterminent la structure de production d'une entreprise ?
8. Énumérez les principales exigences pour la planification des processus.
9. Quels sont les principes de base du placement rationnel des divisions de production d'une entreprise ?
10. Énumérer les formes de spécialisation et d'organisation des divisions de l'entreprise ?
11. Élargir les concepts de spécialisation technologique et disciplinaire.
12. Qu'entend-on par spécialisation thématique et technologique des domaines au sein des ateliers ?
13. Quelle est la structure de production des ateliers et sections de l'entreprise ?
14. Décrivez les principaux types de schémas de production, expliquez les différences entre eux.
15. Proposer des solutions aux problèmes associés à chaque type d'aménagement.
16. Donnez des exemples pratiques de chaque type d’aménagement.
17. Établir une correspondance entre les types d'aménagement et les formes de spécialisation des divisions de l'entreprise.
18. Expliquez l'essence du placement des équipements selon le principe de la technologie de groupe.
19. Liste les conditions nécessaires, dans lequel il convient d'organiser des cellules technologiques.
20. Quelles sont les principales orientations pour améliorer la structure de production de l'entreprise ?
21. Quelle est la structure de production de MIREA ? Décris-la.
Concept du processus de production. La production moderne est un processus complexe de transformation de matières premières, de matériaux, de produits semi-finis et d'autres éléments de travail en produits finis répondant aux besoins de la société.
L'ensemble de toutes les actions des personnes et des outils effectuées dans une entreprise pour la fabrication de types spécifiques de produits est appelée processus de production.
La partie principale du processus de production est constituée de processus technologiques qui contiennent des actions ciblées pour modifier et déterminer l'état des objets de travail. Lors de la mise en œuvre des processus technologiques, des changements se produisent formes géométriques, tailles et propriétés physiques et chimiques des objets de travail.
Variétés de processus de production.
Selon leur objectif et leur rôle dans la production, les processus sont divisés en : installations principales, auxiliaires et de service et non essentielles.
Principal sont appelés processus de production au cours desquels s'effectue la production des principaux produits fabriqués par l'entreprise. Par exemple, centrales thermiques constituent la principale production, car ils convertissent l’énergie combustible en énergie thermique et électrique.
La rapidité et la qualité de l'exécution de la production principale dépendent en grande partie de la manière dont est organisé le travail de la production auxiliaire et des services, qui sont subordonnés à la tâche de mieux fournir aux principales entreprises de production des matériaux, des équipements, etc.
Dans les conditions modernes, notamment dans la production automatisée, il existe tendance à l'intégration processus principaux et de service. Ainsi, dans des complexes automatisés flexibles, les opérations de base, de préparation de commandes, d'entrepôt et de transport sont combinées en un seul processus.
L'ensemble des processus de base constitue la production principale.
Les entreprises de production auxiliaires sont des entreprises qui, bien qu'elles ne soient pas directement liées à la fabrication du produit principal, servent et créent les conditions nécessaires au fonctionnement normal de la production principale. Les entreprises de production auxiliaires comprennent les entreprises qui fabriquent des produits consommés par la production principale et contribuent ainsi à la production de produits finaux et assurent le fonctionnement normal de la production principale. Dans le secteur de l'énergie, la production auxiliaire comprend les entreprises de réparation, ainsi que les entreprises qui produisent des équipements non standard et des pièces de rechange pour les équipements énergétiques.
Les entreprises de services sont organisées pour desservir les entreprises principales et auxiliaires. Le processus de production de services est un processus de travail à la suite duquel aucun produit n'est créé. Les entreprises de services comprennent les entreprises impliquées dans la fourniture de matériaux et de pièces de rechange, les laboratoires, les instituts de conception et de recherche, les entreprises de transport, etc.
DANS Dernièrement Dans le secteur de l'énergie, est apparu le concept d'« entreprises de services », qui combine à la fois des entreprises auxiliaires et des entreprises de services. Il est proposé d'inclure dans le groupe de services les entreprises qui fournissent des services de réparation, d'installation, d'ajustement et de modernisation d'équipements industriels et de réseaux technologiques (par exemple, les entreprises de réparation, les usines de fabrication d'équipements, les entreprises de transport automobile, etc.).
Les entreprises non essentielles comprennent les exploitations agricoles dont les produits et services ne sont pas inclus dans les activités principales de l'entreprise. Leurs fonctions comprennent la satisfaction des besoins domestiques du personnel de l'entreprise (logements, jardins d'enfants, sanatoriums, auxiliaires agriculture etc.).
Principes scientifiques d'organisation des processus de production.
L'organisation des processus de production consiste à combiner des personnes, des outils et des objets de travail en un seul processus de production de biens matériels, ainsi qu'à assurer une combinaison rationnelle dans l'espace et dans le temps des processus de base, auxiliaires et de service..
La combinaison spatiale des éléments du processus de production et de toutes ses variétés est mise en œuvre sur la base de la formation de la structure de production de l'entreprise et de ses divisions. À cet égard, les activités les plus importantes sont la sélection et la justification de la structure de production de l'entreprise, c'est-à-dire déterminer la composition et la spécialisation de ses unités constitutives et établir des relations rationnelles entre elles.
Pendant le développement structure de production, des calculs de conception sont effectués pour déterminer la composition du parc d'équipements, en tenant compte de sa productivité, de son interchangeabilité et de la possibilité d'une utilisation efficace. Des agencements rationnels des départements, l'emplacement des équipements et des lieux de travail sont également en cours d'élaboration. Des conditions organisationnelles sont créées pour le fonctionnement ininterrompu des équipements et des participants directs au processus de production - les travailleurs
L'un des principaux aspects de la formation d'une structure de production est d'assurer le fonctionnement interconnecté de toutes les composantes du processus de production : opérations préparatoires, principaux processus de production, Entretien. Il est nécessaire de justifier de manière exhaustive les formes et méthodes organisationnelles les plus rationnelles pour réaliser certains processus pour des conditions de production et techniques spécifiques.
Un élément important de l'organisation processus de production - l'organisation du travail des travailleurs, réalisant spécifiquement le lien entre le travail et les moyens de production. Les méthodes d'organisation du travail sont largement déterminées par les formes du processus de production. À cet égard, l'accent devrait être mis sur la garantie d'une division rationnelle du travail et la détermination sur cette base de la composition professionnelle et des qualifications des travailleurs, de l'organisation scientifique et de l'entretien optimal des lieux de travail, ainsi que de l'amélioration globale des conditions de travail.
L'organisation des processus de production présuppose également une combinaison de leurs éléments dans le temps, qui détermine un certain ordre d'exécution des opérations individuelles, une combinaison rationnelle du temps pour effectuer divers types de travaux et la détermination de normes planifiées par calendrier pour le mouvement des objets de travail. Le déroulement normal des processus dans le temps est également assuré par l'ordre de lancement et de libération des produits, la création des stocks (réserves) et des réserves de production nécessaires et l'approvisionnement ininterrompu des lieux de travail en outils, pièces et matériaux. Un domaine important de cette activité est l'organisation du mouvement rationnel des flux de matières. Ces tâches sont résolues sur la base du développement et de la mise en œuvre de systèmes opérationnels de planification de la production, en tenant compte du type de production et des caractéristiques techniques et organisationnelles des processus de production.
Enfin, lors de l'organisation des processus de production dans une entreprise, une place importante est accordée au développement d'un système d'interaction entre les unités de production individuelles.
Principes d'organisation du processus de production représentent les points de départ sur la base desquels s'effectuent la construction, l'exploitation et le développement des processus de production.
Principe différenciation implique de diviser le processus de production en parties distinctes (processus, opérations) et de les attribuer aux départements concernés de l'entreprise. Le principe de différenciation s'oppose au principe des combinaisons, ce qui signifie l'unification de tout ou partie de divers processus de production de certains types de produits au sein d'un même site, atelier ou production.
Selon la complexité du produit, le volume de production et la nature de l'équipement utilisé, le processus de production peut être concentré dans une seule unité de production (atelier, zone) ou dispersé dans plusieurs unités. Ainsi, par exemple, dans les entreprises de construction de machines, avec une production importante de produits similaires, une production et des ateliers indépendants de mécanique et d'assemblage sont organisés, et pour de petits lots de produits, des ateliers d'assemblage mécanique unifiés peuvent être créés.
Les principes de différenciation et de combinaison s'appliquent également aux lieux de travail individuels. Une chaîne de production, par exemple, est un ensemble différencié d’emplois.
DANS activités pratiques dans l'organisation de la production, la priorité dans l'utilisation des principes de différenciation ou de combinaison doit être donnée au principe qui garantira les meilleures caractéristiques économiques et sociales du processus de production. Ainsi, la production en flux, caractérisée par un haut degré de différenciation du processus de production, permet de simplifier son organisation, d'améliorer les compétences des travailleurs et d'augmenter la productivité du travail. Cependant, une différenciation excessive augmente la fatigue des travailleurs, un grand nombre d'opérations augmente le besoin en équipements et en espace de production, entraîne des coûts inutiles pour les pièces mobiles, etc.
Principe concentrations moyens concentration de certaines opérations de production pour la fabrication de produits technologiquement homogènes ou l'exécution de travaux fonctionnellement homogènes sur des lieux de travail, zones, ateliers ou installations de production individuels de l'entreprise. La faisabilité de concentrer un travail homogène dans des domaines de production distincts est due aux facteurs suivants : méthodes technologiques, entraînant la nécessité d'utiliser le même type d'équipement ; capacités des équipements, tels que les centres d'usinage ; augmenter les volumes de production de certains types de produits ; la faisabilité économique de concentrer la production de certains types de produits ou d'effectuer un travail similaire.
Lors du choix d'une direction ou d'une autre de concentration, il est nécessaire de prendre en compte les avantages de chacune d'elles.
En concentrant un travail technologiquement homogène dans un département, moins d'équipements de duplication sont nécessaires, la flexibilité de la production augmente et il devient possible de passer rapidement à la production de nouveaux produits, et l'utilisation des équipements augmente.
En concentrant des produits technologiquement homogènes, les coûts de transport des matériaux et des produits sont réduits, la durée du cycle de production est réduite, la gestion de la production est simplifiée et le besoin d'espace de production est réduit.
Principe spécialisations basé sur la limitation de la variété des éléments du processus de production. La mise en œuvre de ce principe implique d'attribuer à chaque lieu de travail et à chaque service une gamme strictement limitée de travaux, d'opérations, de pièces ou de produits. Contrairement au principe de spécialisation, le principe d'universalisation présuppose une organisation de la production dans laquelle chacun lieu de travail ou division de production engagés dans la fabrication de pièces et de produits d'une large gamme ou effectuant diverses opérations de production.
Le niveau de spécialisation des emplois est déterminé par un indicateur spécial - le coefficient de consolidation des opérations Pour z.o, qui se caractérise par le nombre d'opérations de détail effectuées sur le lieu de travail sur une certaine période de temps. Oui quand K z.o= 1 il existe une spécialisation étroite des lieux de travail, dans laquelle une opération détaillée est effectuée sur le lieu de travail pendant un mois ou un trimestre.
La nature de la spécialisation des départements et des emplois est largement déterminée par le volume de production des pièces du même nom. Plus haut niveau la spécialisation est obtenue en produisant un type de produit. L’exemple le plus typique d’industries hautement spécialisées sont les usines de production de tracteurs, de téléviseurs et de voitures. L'augmentation de la gamme de production réduit le niveau de spécialisation.
Un degré élevé de spécialisation des départements et des emplois contribue à la croissance de la productivité du travail grâce au développement des compétences professionnelles des travailleurs, à la possibilité d'équipement technique du travail et à la minimisation des coûts de reconfiguration des machines et des lignes. Dans le même temps, une spécialisation étroite réduit les qualifications requises des travailleurs, provoque la monotonie du travail et, par conséquent, entraîne une fatigue rapide des travailleurs et limite leur initiative.
Dans les conditions modernes, il existe une tendance croissante à l'universalisation de la production, qui est déterminée par les exigences progrès scientifique et technologiqueélargir la gamme de produits, l'émergence d'équipements multifonctionnels, les tâches d'amélioration de l'organisation du travail dans le sens de l'expansion fonctions de travail ouvrier.
Principe proportionnalité est dans une combinaison naturelle d'éléments individuels du processus de production, qui s'exprime dans une certaine relation quantitative entre eux. Ainsi, la proportionnalité des capacités de production présuppose l’égalité des capacités des sites ou des facteurs de charge des équipements. Dans ce cas, le débit des ateliers d'approvisionnement correspond au besoin en ébauches des ateliers de mécanique, et le débit de ces ateliers correspond aux besoins de l'atelier de montage en pièces nécessaires. Cela implique la nécessité de disposer dans chaque atelier d'équipements, d'espace et de main-d'œuvre en quantités suffisantes pour assurer le fonctionnement normal de tous les départements de l'entreprise. Le même rapport de débit doit exister entre la production principale, d'une part, et les unités auxiliaires et de service, d'autre part.
La violation du principe de proportionnalité entraîne des déséquilibres, l'émergence de goulots d'étranglement dans la production, ce qui entraîne une détérioration de l'utilisation des équipements et de la main-d'œuvre, une augmentation de la durée du cycle de production et une augmentation des retards.
Proportionnalité dans l'effectif, les zones, les équipements sont installés dès la conception de l'entreprise, puis spécifiés lors de l'élaboration des plans de production annuels en effectuant des calculs dits volumétriques - lors de la détermination de la capacité, du nombre d'employés et du besoin en matériaux. Les proportions sont établies sur la base d'un système de standards et de normes qui déterminent le nombre de connexions mutuelles entre les différents éléments du processus de production.
Le principe de proportionnalité implique l'exécution simultanée d'opérations individuelles ou de parties du processus de production. Elle repose sur la proposition selon laquelle les parties d’un processus de production démembré doivent être combinées dans le temps et exécutées simultanément.
Organisation des processus de production dans le temps.
Pour assurer une interaction rationnelle de tous les éléments du processus de production et rationaliser le travail effectué dans le temps et dans l'espace, il est nécessaire de former un cycle de production du produit.
Le cycle de production est appelé un complexe de processus de base, auxiliaires et de service organisés d'une certaine manière dans le temps, nécessaires à la fabrication d'un certain type de produit. La caractéristique la plus importante du cycle de production est sa durée.
Durée du cycle de production - Ce la période calendaire pendant laquelle un matériau, une pièce ou un autre article transformé passe par toutes les opérations du processus de production ou une certaine partie de celui-ci et est transformé en un produit fini. La durée du cycle est exprimée en jours ou en heures calendaires.
Structure du cycle de production comprend le temps de travail et le temps de pause. Pendant la période de travail, les opérations technologiques proprement dites et les travaux préparatoires et finaux sont effectués. La période de travail comprend également la durée des opérations de contrôle et de transport et le temps des processus naturels (y compris le temps des pauses dues à l'horaire de travail).
Dans sa forme la plus générale, la durée du cycle de production T c exprimé par la formule :
T a = T t + T n -3 + T e + T k + T Tr + T mo + T Pr,
où T t est le temps des opérations technologiques ; T n -3- le temps des travaux préparatoires et finaux ; T e - temps des processus naturels; T k - heure des opérations de contrôle ; T Tr- le temps de transport des objets de travail ; T mo- l'heure du coucher interopérationnelle (pauses intra-équipe) ; T Pr,- temps de pauses en raison de l'horaire de travail.
La durée des opérations technologiques et des travaux préparatoires et finaux forme ensemble le cycle de fonctionnement T c.op.
Cycle de fonctionnement- c'est la durée de la partie achevée du processus technologique effectuée sur un lieu de travail.
TYPES, FORMES ET MÉTHODES D'ORGANISATION DE LA PRODUCTION
Types de production et leurs caractéristiques techniques et économiques.
Le type de production est déterminé par les caractéristiques complexes des aspects techniques, organisationnels et caractéristiques économiques production, en raison de l'étendue de la gamme, de la régularité, de la stabilité et du volume de production. Le principal indicateur caractérisant le type de production est le coefficient de consolidation des opérations Kz.
Le coefficient de consolidation des opérations pour un groupe d'emplois est défini comme le rapport entre le nombre de toutes les différentes opérations technologiques réalisées ou à réaliser au cours du mois et le nombre d'emplois :
K op je - nombre d'opérations effectuées sur je-ème lieu de travail ; À r.m— le nombre d'emplois sur le chantier ou en atelier.
Il existe trois types de production : unique, en série, en série.
Production unique caractérisé par un petit volume de production de produits identiques, dont la reproduction et la réparation ne sont généralement pas prévues. Le facteur de consolidation pour la production unitaire est généralement supérieur à 40.
Production de masse caractérisé par la fabrication ou la réparation de produits en lots périodiquement répétés. Selon le nombre de produits d'un lot ou d'une série et la valeur du coefficient de consolidation des opérations, on distingue la production à petite, moyenne et grande échelle.
Pour la production à petite échelle, le facteur de consolidation des opérations est de 21 à 40 (inclus), pour la production à moyenne échelle : de 11 à 20 (inclus), pour la production à grande échelle : de 1 à 10 (inclus).
Production de masse caractérisé un grand volume de production de produits fabriqués ou réparés en continu sur une longue période de temps, au cours de laquelle une opération de travail est effectuée sur la plupart des lieux de travail. Le coefficient de consolidation des opérations de production en série est pris égal à 1.
Considérons les caractéristiques techniques et économiques de chaque type de production.
La production unique et similaire à petite échelle se caractérise par la production de pièces d'une large gamme sur des lieux de travail qui n'ont pas de spécialisation spécifique. Cette production doit être suffisamment flexible et adaptée pour répondre aux différentes commandes de production.
Processus technologiques dans des conditions de production unique, ils sont élaborés agrandis sous forme de feuilles de route pour le traitement des pièces pour chaque commande ; Les sites sont équipés d'équipements et d'accessoires universels qui assurent la production de pièces d'une large gamme. La grande variété d'emplois que de nombreux travailleurs doivent occuper exige qu'ils possèdent des compétences professionnelles différentes, c'est pourquoi des généralistes hautement qualifiés sont utilisés dans les opérations. Dans de nombreux domaines, notamment dans la production pilote, le cumul des métiers est pratiqué.
Organisation de la production dans des conditions de production unique, il a ses propres caractéristiques. En raison de la diversité des pièces, de l'ordre et des modalités de leur traitement, les zones de production sont construites selon un principe technologique avec des équipements disposés en groupes homogènes. Avec cette organisation de la production, les pièces passent par différentes sections au cours du processus de fabrication.
Par conséquent, lors de leur transfert vers chaque opération (section) suivante, il est nécessaire d'examiner attentivement les questions de contrôle de la qualité du traitement, du transport et de la détermination des lieux de travail pour effectuer l'opération suivante. Les caractéristiques de la planification et de la gestion opérationnelles comprennent l'exécution et l'exécution des commandes dans les délais, le suivi de la progression de chaque pièce tout au long des opérations, et la garantie du chargement systématique des zones et des lieux de travail. De grandes difficultés surviennent dans l'organisation de la logistique.
Caractéristiques de l'organisation la production unitaire affecte les indicateurs économiques. Les entreprises à prédominance d'un seul type de production se caractérisent par une intensité de main-d'œuvre relativement élevée des produits et un volume important de travaux en cours en raison du long stockage des pièces entre les opérations. La structure des coûts des produits se caractérise par une part élevée des coûts salariaux. Cette part est généralement de 20 à 25 %.
Les principales opportunités d'amélioration des indicateurs techniques et économiques de la production individuelle sont liées à son rapprochement de la production en série en termes de niveau technique et organisationnel. L'utilisation de méthodes de production en série est possible en rétrécissant la gamme de pièces fabriquées pour des applications générales de construction de machines, en unifiant les pièces et les assemblages, ce qui permet de passer à l'organisation des domaines ; étendre la continuité constructive pour augmenter les lots de lancement de pièces ; regrouper des pièces similaires dans leur conception et leur ordre de fabrication pour réduire le temps de préparation de la production et améliorer l'utilisation des équipements.
Production de masse caractérisé par la production d'une gamme limitée de pièces en lots répétés à certains intervalles. Cela vous permet d'utiliser avec l'universel équipement spécial. Lors de la conception des processus technologiques, l'ordre d'exécution et l'équipement de chaque opération sont fournis.
Les caractéristiques suivantes sont caractéristiques de l'organisation de la production en série : les ateliers contiennent, en règle générale, des zones fermées où les équipements sont placés au cours d'un processus technologique standard. En conséquence, des connexions relativement simples apparaissent entre les postes de travail et les conditions préalables sont créées pour organiser le mouvement direct des pièces au cours de leur processus de fabrication.
Les entreprises de production en série se caractérisent par une intensité de main-d'œuvre et un coût de fabrication des produits nettement inférieurs à ceux des entreprises individuelles. Dans la production de masse, par rapport à la production individuelle, les produits sont traités avec moins d'interruptions, ce qui réduit le volume de travail en cours.
La production de masse est différente la plus grande spécialisation et se caractérise par la production d'une gamme limitée de pièces en grande quantité. Les ateliers de production de masse sont dotés des équipements les plus avancés, permettant une automatisation quasi complète de la production des pièces. Les lignes de production automatiques se sont généralisées ici. Dans des conditions de production de masse, l'importance d'organiser le transport interopérationnel et l'entretien des lieux de travail augmente.
La surveillance constante de l'état des outils, appareils et équipements de coupe est l'une des conditions pour assurer la continuité du processus de production, sans laquelle le rythme de travail sur les chantiers et dans les ateliers sera inévitablement perturbé. La nécessité de maintenir un rythme donné à tous les niveaux de production devient trait distinctif organisation des processus dans la production de masse.
La production de masse garantit l'utilisation la plus complète des équipements, un niveau global élevé de productivité du travail et le coût de fabrication des produits le plus bas. Dans le tableau 1 présente des données sur caractéristiques comparatives divers types production.
Formes d'organisation de la production.
La forme d'organisation de la production est une certaine combinaison dans le temps et dans l'espace d'éléments du processus de production avec un niveau approprié de son intégration, exprimé par un système de connexions stables.
Diverses structures structurelles temporelles et spatiales forment un ensemble de formes fondamentales d'organisation de la production.
Structure temporaire de l'organisation la production est déterminée par la composition des éléments du processus de production et l'ordre de leur interaction dans le temps. Sur la base du type de structure temporaire, les formes d'organisation se distinguent par le transfert séquentiel, parallèle et parallèle-séquentiel des objets de travail dans la production.
La forme d'organisation de la production avec transfert séquentiel d'objets de travail est une combinaison d'éléments du processus de production qui assure le mouvement des produits transformés à travers toutes les zones de production par lots de taille arbitraire. Cette forme est la plus flexible par rapport aux changements qui surviennent dans le programme de production,
Tableau 1.
Caractéristiques comparables | Type de fabrication | ||
Célibataire | En série | Masse | |
Nomenclature et volume de production Répétabilité de la production Équipement utilisé Affectation des opérations aux machines Localisation des équipements Transfert des objets de travail d'une opération à l'autre Forme d'organisation du processus de production | Gamme illimitée de pièces fabriquées sur commande Absente Universelle Absente Par groupes de machines similaires Séquentielle Technologique | Large gamme de pièces fabriquées par lots Périodique Universel, en partie spécial Un nombre limité d'opérations de détail est établi En groupes pour le traitement de pièces structurellement et technologiquement homogènes Parallèle-séquentiel Sujet, groupe, sujet flexible | Gamme limitée de pièces fabriquées en grandes quantités Constante Généralement spéciales Une ou deux opérations par machine Tout au long du processus technologique de traitement des pièces Parallèle Linéaire |
Les caractéristiques comparatives des différents types de production permettent d'utiliser pleinement l'équipement, ce qui permet de réduire le coût de son acquisition. L'inconvénient de cette forme d'organisation de la production est la durée relativement longue du cycle de production, puisque chaque pièce attend que l'ensemble du lot soit traité avant d'effectuer l'opération suivante.
Forme d'organisation de la production avec transfert parallèle d'objets de travail est basé sur une telle combinaison d'éléments du processus de production qui vous permet de lancer, de traiter et de transférer des objets de travail d'une opération à l'autre individuellement et sans attendre. Cette organisation du processus de production entraîne une réduction du nombre de pièces traitées, réduisant ainsi le besoin d'espace nécessaire au stockage et aux allées. Son inconvénient est temps d'arrêt possibleéquipements (postes de travail) en raison des différences dans la durée des opérations.
La forme d'organisation de la production avec transfert parallèle-séquentiel d'objets de travail est intermédiaire entre les formes séquentielles et parallèles et élimine partiellement leurs inconvénients inhérents. Les produits sont transférés d'une opération à l'autre par lots de transport. Dans le même temps, la continuité d'utilisation des équipements et de la main-d'œuvre est assurée, et un passage partiellement parallèle d'un lot de pièces à travers les opérations du processus technologique est possible.
Structure spatiale L'organisation de la production est déterminée par le nombre d'équipements technologiques concentrés sur le chantier (le nombre de postes de travail) et par sa localisation par rapport au sens de déplacement des objets de travail dans l'espace environnant.
Selon le nombre d'équipements technologiques (postes de travail), il existe des liaisons simples Système de production et la structure correspondante d'un lieu de travail séparé et d'un système multi-liens avec une structure d'atelier, linéaire ou cellulaire. Les options possibles pour la structure spatiale de l'organisation de la production sont présentées dans la Fig. 5.
Boutique la structure est caractérisée la création d'espaces dans lesquels les équipements (postes de travail) sont implantés parallèlement au flux des pièces, ce qui suppose leur spécialisation sur la base de l'homogénéité technologique. Dans ce cas, un lot de pièces arrivant sur le site est envoyé vers l'un des postes de travail libres, où il subit le cycle de traitement nécessaire, après quoi il est transféré vers un autre site (à l'atelier).
Riz. 5. Options pour la structure spatiale du processus de production
Sur le site avec linéaire structure spatiale, les équipements (postes de travail) sont localisés tout au long du processus technologique et un lot de pièces traitées sur le site est transféré d'un lieu de travail à un autre de manière séquentielle.
Cellulaire la structure de l'organisation de la production combine les caractéristiques du linéaire et de l'atelier.
La combinaison des structures spatiales et temporelles du processus de production avec un certain niveau d'intégration des processus partiels détermine diverses formes d'organisation de la production : technologique, thématique, à flux direct, ponctuelle, intégrée (Fig. 6). Regardons les traits caractéristiques de chacun d'eux.
Riz. 6. Formes d'organisation de la production
Technologique La forme d'organisation du processus de production est caractérisée par une structure d'atelier avec le transfert séquentiel des objets de travail. Cette forme d'organisation est répandue dans les usines de construction de machines, car elle garantit une utilisation maximale des équipements dans la production à petite échelle et est adaptée aux changements fréquents du processus technologique.
En même temps, l'application la forme technologique d'organisation du processus de production a un certain nombre de conséquences négatives : un grand nombre de pièces et leur mouvement répété au cours du processus de transformation entraînent une augmentation du volume des travaux en cours et une augmentation du nombre de points de stockage intermédiaires ; une partie importante du cycle de production est constituée de pertes de temps causées par des communications complexes entre les sites.
La forme sujette d'organisation de la production a une structure cellulaire avec un transfert parallèle-séquentiel (séquentiel) d'objets de travail dans la production. En règle générale, tous les équipements nécessaires au traitement d'un groupe de pièces du début à la fin du processus technologique sont installés sur le site. Si le cycle technologique de traitement est fermé au sein du site, il est dit sujet fermé.
Par rapport à la forme technologique le sujet permet de réduire les coûts globaux de transport des pièces et le besoin d'espace de production par unité de production. En même temps ce formulaire L'organisation de la production lors de la détermination de la composition des équipements installés sur le site met en évidence la nécessité de procéder à certains types de transformation des pièces, qui ne garantissent pas toujours la pleine utilisation des équipements. De plus, l'élargissement de la gamme de produits et leur mise à jour nécessitent un réaménagement périodique des zones de production et des modifications dans la structure du parc d'équipements.
Flux direct forme d'organisation la production est caractérisée structure linéaire avec transfert fragmentaire d'objets de travail. Cette forme assure la mise en œuvre d'un certain nombre de principes d'organisation : spécialisation, franchise, continuité, parallélisme. Son utilisation entraîne une réduction de la durée du cycle de production, une utilisation plus efficace de la main-d'œuvre grâce à une plus grande spécialisation de la main-d'œuvre et une réduction du volume de travail en cours.
À indiquer formulaire organisation de la production, le travail est entièrement effectué sur un seul lieu de travail. Le produit est fabriqué là où se trouve sa partie principale. Un exemple est l’assemblage d’un produit avec un ouvrier se déplaçant autour de lui. L'organisation de la production ponctuelle présente de nombreux avantages : elle offre la possibilité de changements fréquents dans la conception des produits et la séquence de transformation, de fabrication de produits d'une gamme diversifiée dans des quantités déterminées par les besoins de production ; Les coûts associés au changement d'emplacement des équipements sont réduits et la flexibilité de la production est augmentée.
La forme d'organisation de la production implique la combinaison d'opérations principales et auxiliaires en un seul processus de production intégré avec une structure cellulaire ou linéaire avec transfert séquentiel, parallèle ou parallèle-séquentiel d'objets de travail dans la production.
Création d'intégration les sites de production sont associés à des coûts ponctuels relativement élevés causés par l’intégration et l’automatisation du processus de production. L'effet économique de la transition vers une forme intégrée d'organisation de la production est obtenu en réduisant la durée du cycle de production de fabrication de pièces, en augmentant le temps de chargement des machines et en améliorant la régulation et le contrôle des processus de production. En figue. La figure 7 montre des schémas de disposition des équipements dans des zones présentant différentes formes d'organisation de la production.
Selon capacité au réajustement pour la production de nouveaux produits, les formes d'organisation de la production ci-dessus peuvent être divisées en flexibles (modifiables) et rigides (non réajustables). Les formes rigides d'organisation de la production impliquent le traitement de pièces d'un type (par exemple, une forme continue d'organisation du processus de production).
Des formes flexibles permettent d'assurer la transition vers la production de nouveaux produits sans modifier la composition des composants du processus de production avec peu de temps et de main d'œuvre.
Les formes d'organisation de la production les plus répandues dans les entreprises de construction de machines sont actuellement la production ponctuelle flexible, les formes flexibles de sujets et de flux.
Riz. 7. Aménagements des équipements (postes de travail) dans des zones avec différentes formes d'organisation de la production :
a - technologique ; b - sujet ; c - flux direct ;
g - point (pour le cas d'assemblage) ; d - intégré
La production ponctuelle flexible implique la structure spatiale d'un lieu de travail séparé sans autre transfert d'objets de travail pendant le processus de production. La pièce est entièrement traitée dans une seule position. L'adaptation à la sortie de nouveaux produits s'effectue en modifiant l'état de fonctionnement du système.
Forme d'organisation thématique flexible la production se caractérise par la capacité de traiter automatiquement des pièces dans une certaine plage sans interruption pour le changement. La transition vers la production de nouveaux produits s'effectue par un réajustement des moyens techniques et une reprogrammation du système de contrôle. La forme flexible et linéaire de l'organisation de la production se caractérise par un réajustement rapide pour traiter de nouvelles pièces dans une plage donnée en remplaçant les outillages et les montages et en reprogrammant le système de contrôle. Il repose sur une disposition en rangées d'équipements qui correspond strictement au processus technologique, avec transfert pièce par pièce des objets de travail.
Développement de formes d'organisation de la production dans les conditions modernes.
Sous l'influence des progrès scientifiques et technologiques en matière d'ingénierie et de technologie du génie mécanique, des changements importants se produisent en raison de la mécanisation et de l'automatisation des processus de production. Cela crée des conditions objectives pour le développement de nouvelles formes d'organisation de la production, par exemple la forme modulaire en blocs.
La création d'une production avec une forme d'organisation de la production modulaire en blocs s'effectue en concentrant sur un site l'ensemble des équipements technologiques nécessaires à la production continue d'une gamme limitée de produits et en réunissant un groupe de travailleurs pour fabriquer le produit final. , leur transférant une partie des fonctions de planification et de gestion de la production sur le site.
Base économique La création de telles industries est une forme collective d'organisation du travail. Les principales exigences pour organiser le processus de production et de travail dans ce cas sont : la création système autonome maintenance technique et instrumentale de la production; assurer la continuité du processus de production sur la base du calcul du besoin rationnel de ressources, en indiquant les intervalles et les dates de livraison ; assurer la capacité correspondante des départements d'usinage et d'assemblage ; prendre en compte les normes de contrôlabilité établies lors de la détermination du nombre d'employés ; sélection d'un groupe de travailleurs en tenant compte d'une interchangeabilité totale.
Mise en œuvre des exigences spécifiées n’est possible qu’avec une solution globale aux problèmes d’organisation du travail, de production et de gestion. Le passage à une forme d'organisation de la production modulaire en blocs s'effectue en plusieurs étapes. Au stade de l'enquête d'avant-projet, une décision est prise sur l'opportunité de créer de telles unités dans les conditions de production données. Une analyse de la conception et de l'homogénéité technologique des produits est réalisée et une évaluation est faite de la possibilité de constituer des « familles » de pièces à traiter au sein de la cellule de production.
Ensuite, la possibilité de concentrer l'ensemble des opérations technologiques pour la production d'un groupe de pièces dans une seule zone est déterminée ; le nombre de postes de travail adaptés à la mise en place du traitement groupé des pièces est établi ; la composition et le contenu des exigences de base pour l'organisation du processus de production et de travail sont déterminés en fonction du niveau d'automatisation prévu.
Au stade de la conception structurelle, la composition et les relations entre les principaux composants du processus de production sont déterminées.
Au stade de la conception organisationnelle et économique, des solutions techniques et organisationnelles sont combinées et des moyens de mettre en œuvre les principes de la convention collective et de l'autonomie gouvernementale en équipes autonomes sont esquissés.
La deuxième direction dans l'évolution des formes d'organisation de la production est le passage à l'assemblage d'unités complexes par la méthode au banc, l'abandon du montage par convoyeurs grâce à l'organisation d'un mini-flux.
Une autre décision de l'organisation la production continue consiste à entretenir le système de convoyeur avec l'inclusion d'opérations préparatoires. Dans ce cas, les monteurs, à leur discrétion, travaillent soit aux opérations principales, soit aux opérations préparatoires. Ces approches du développement d'une forme continue d'organisation de la production garantissent non seulement une augmentation de la productivité du travail et une qualité améliorée, mais donnent également aux assembleurs un sentiment de satisfaction du travail et éliminent la monotonie du travail.
Modalités d'organisation de la production.
Les méthodes d'organisation de la production sont un ensemble de méthodes, de techniques et de règles permettant la combinaison rationnelle des principaux éléments du processus de production dans l'espace et dans le temps aux étapes d'exploitation, de conception et d'amélioration de l'organisation de la production.
Mode d'organisation de la production individuelle utilisé dans des conditions de production unique ou de production en petits lots et suppose : un manque de spécialisation sur le lieu de travail ; l'utilisation d'équipements largement universels, leur disposition en groupes selon leur objectif fonctionnel ; mouvement séquentiel des pièces d'une opération à l'autre par lots.
Les conditions d'entretien des lieux de travail sont différentes dans la mesure où les travailleurs utilisent presque constamment un seul ensemble d'outils et un petit nombre d'appareils universels ; seul le remplacement périodique des outils émoussés ou usés est requis. En revanche, la livraison des pièces aux postes de travail et l'ajustement des pièces lors de la délivrance de nouveaux travaux et de l'acceptation des travaux finis ont lieu plusieurs fois au cours du quart de travail. Il est donc nécessaire d’organiser de manière flexible les services de transport sur les lieux de travail.
ORGANISATION DE LA PRODUCTION ET DES ACTIVITÉS ÉCONOMIQUES DANS LE SECTEUR DE L'ÉNERGIE
Considérant la procédure d'exercice des fonctions et sous-fonctions de gestion énergétique d'une entreprise, il convient de noter, d'une part, qu'elles imprègnent tous les domaines d'activité et, d'autre part, qu'elles comportent certains éléments prioritaires dans ces domaines. Les sous-systèmes de gestion fonctionnelle formés à l'intersection des zones sont une sorte de « table des matières » de l'ensemble du travail organisationnel et économique du service énergétique. Certains d'entre eux reçoivent plus d'attention, d'autres - moins des ¾ en raison du très grand volume de travail de gestion dans le secteur de l'énergie.
En effet, si vous multipliez le nombre de fonctions et sous-fonctions (il y en a 17) par le nombre de domaines (il y en a 12), vous obtenez 204 « rubriques » - un ensemble de tâches dans la liste générale des travaux de gestion du service énergétique. Dans chacun de ces complexes, le nombre de tâches est déterminé par le nombre de types d'énergie, d'installations énergétiques (productions, ateliers, sites et même installations individuelles d'énergie et consommatrices d'énergie) et d'autres indicateurs. En conséquence, le nombre total de tâches et de travaux de gestion s'élève à plusieurs milliers.
A titre d'exemple de cette diversité, il convient d'énumérer et d'évoquer brièvement l'organisation de la structure dans les principaux domaines d'activité :
¾ Organisation de la structure de consommation énergétique ;
¾ Organisation de la structure des usages énergétiques.
¾ Organisation de la structure des équipements électriques et des modalités de leur fonctionnement.
¾ Organisation de la structure des modes d'alimentation électrique et fonctionnement des équipements électriques.
¾ Organisation de la structure du système de fiabilité de l'alimentation électrique et de fonctionnement des équipements électriques.
¾ Organisation de la structure de supervision énergétique en usine.
¾ Organisation de la structure de maintenance de réparation des équipements électriques.
¾ Organisation de la structure du travail et du personnel de l'énergie.
¾ Organisation de la structure d'approvisionnement matériel et technique du secteur de l'énergie.
¾ Organisation de la structure du travail économique dans le secteur de l'énergie.
¾ Organisation d'une structure de développement de la production d'énergie.
Efficacité énergétique d'une entreprise dépend en grande partie du degré de perfection de la structure organisationnelle de la gestion des services énergétiques. La qualité de la structure organisationnelle est déterminée principalement par la capacité à exercer de manière optimale les fonctions de gestion dans tous les domaines d'activité. Ainsi sont créées ici des divisions de production et de gestion, dont les tâches incluent le travail sur une fonction (« planification » - service de planification, « comptabilité » - comptabilité, « rationnement » - bureau de normalisation, etc.), en un (ou plusieurs) domaines d'activité (« service de réparation » - atelier de réparation, « utilisation de l'énergie » - bureau de gestion de l'énergie, etc.), ainsi que dans sous-systèmes fonctionnels(« contrôle et régulation des consommations d'énergie » - service de dispatching d'énergie, etc.).
Les entreprises de divers secteurs utilisent des systèmes de gestion centralisés, décentralisés et mixtes. Dans certains cas, un dispositif dit « du personnel » apparaît, généralement organisé comme une mesure temporaire pour résoudre des problèmes spécifiques.
Avec contrôle centralisé Le service énergétique, dirigé par l'ingénieur électricien en chef de l'entreprise, comprend des ingénieurs électriciens qui assurent l'entretien des équipements électriques généraux des usines et des magasins. Des liens de gestion linéaires de subordination directe sont établis entre le chef électricien, son appareil administratif (service du chef électricien) et tous les ingénieurs électriciens de l'entreprise. Ce schéma de gestion est typique des petites et moyennes entreprises dont le secteur énergétique est sous-développé.
Avec une gestion décentralisée, le service énergétique ne couvre que la partie générale des installations du secteur de l'énergie. Le personnel énergétique des magasins est subordonné à la direction de leurs magasins et n'a que des liens fonctionnels avec le service énergétique - sur les questions d'exploitation et de réparation des équipements électriques des magasins, de l'approvisionnement en énergie, de la consommation d'énergie et de l'utilisation de l'énergie dans le magasin. Ce schéma est utilisé dans les grandes entreprises ayant une gestion énergétique complexe.
Le schéma mixte prévoit une décentralisation partielle de la gestion, dans laquelle les ingénieurs électriciens de certains ateliers et services sont subordonnés à la direction de leurs départements, et dans certains cas, au service énergétique de l'entreprise.
L'utilisation de l'un ou l'autre schéma, un degré plus ou moins grand de centralisation de la gestion de l'énergie dans les entreprises est déterminé en fonction des conditions locales, en tenant compte de la taille du secteur énergétique. Dans l'industrie, il existe différentes approches pour organiser la structure de gestion de l'énergie, selon de nombreuses dispositions, des catégories de gestion de l'énergie ont été développées.
Les systèmes de catégorisation les plus courants sont les suivants.
Un point est attribué pour chaque tranche de 20 millions de kWh de consommation électrique annuelle. La quantité totale est de 50 000 tonnes d'équivalent carburant. par an, pour 500 pièces. machines électriques.
Le nombre total de points est multiplié par un coefficient de 0,27 personne/point et le résultat du service du chef électricien détermine la catégorie du service énergétique et le nombre de services (par arrondi).
Dans les entreprises chimiques, la catégorisation est également associée au calcul de points en fonction du volume de consommation d'électricité, de chaleur et d'eau.
Une catégorie plus élevée(y compris « zéro », non catégorique) désigne un service énergétique qui comprend l'un des objets suivants: centrales thermiques, chaufferies, réfrigération, compresseur, séparation d'air, stations hydrogène-oxygène ; chaudières à chaleur résiduelle; systèmes de circulation d'eau; propres sources d'approvisionnement en eau - prises d'eau, puits artésiens et autres. Une structure approximative de gestion d'un service énergétique classé en catégorie I ou II est présentée dans la Fig. 8.
Ingénieur en chef de l'énergie
![]() |
Chef du département du chef de l'ingénieur en chef de l'énergie
électricien chauffagiste
Secteur Comptabilité, Secteur Laboratoire Secteur
Standardisation de la supervision énergétique des PPR et des tests et planification et fiabilité des pièces de rechange pour les ressources énergétiques des installations
Atelier d'électricité - Atelier d'électricité - Atelier de vapeur - Atelier de communication d'eau Réparation, fourniture de vapeur et de chaleur et Atelier d'approvisionnement, assainissement CHP
Riz. 8. Schéma approximatif de gestion du service énergétique sur entreprise industrielle 1ère et 2ème catégories
Certains experts suggèrentétablir la catégorie du secteur de l'énergie et le nombre de cadres qui y sont affectés en fonction d'un certain nombre de facteurs de production selon les départements de régression. Nombre de cadres ( Laup) est calculé en fonction du nombre d'ouvriers de production dans l'entreprise ( L pr), nombre de travailleurs dans le secteur de l'énergie ( L e); coût des actifs de production ( F), leur partie active ( FA) et alimenter séparément les équipements (Fe); quantité totale d'énergie consommée convertie en carburant standard ( DANS); le nombre total d'unités d'équipement électrique, exprimé en unités de réparabilité ( R sl).
Le nombre standard de cadres est calculé à l'aide de l'une des quatre formules en fonction du degré d'influence d'un facteur particulier :
Laup = 0,208F 0.9102
Laup= 0,0223 L e0,19 F a0,414
Laup= 0,023L pr 0,542 F à 0,414
Laup = 2 + 0,9F e + 0,55R sl+ 0,01 V.
Il est proposé d'utiliser ces formules pour déterminer le nombre d'ingénieurs dans les départements de l'énergie.
Dans les conditions du marché structure organisationnelle la gestion de l'énergie dans les entreprises doit avoir deux nouvelles qualités :
La plus grande clarté dans la construction d'unités de production et fonctionnelles pour la mise en œuvre réussie de la fonction cible ;
L'expansion des unités économiques due à une forte augmentation du volume de travail économique.
Schéma approximatif la gestion de la gestion énergétique de l'entreprise dans des conditions d'indépendance économique est illustrée à la Fig. 9.
Les tâches principales des unités fonctionnelles du service énergétique, traditionnelles et introduites pour le soutien économique de l'indépendance économique, découlent dans la plupart des cas de leurs noms. Pour un certain nombre d'entre eux, il convient de donner quelques explications.
La tâche principale bureau économique de l'énergie Il devrait y avoir une politique d'économie d'énergie dans l'entreprise, une analyse de la consommation d'énergie dans les processus de production et le développement de mesures organisationnelles et techniques pour économiser l'énergie.
Riz. 9. Schéma approximatif de gestion de l'énergie dans une entreprise industrielle dans les conditions d'un service énergétique économiquement indépendant
Tâches du Bureau de normalisation et des bilans énergétiques :
Création d'un système de rationnement de la consommation d'énergie dans les processus de production basé sur une analyse de la consommation d'énergie réalisée conjointement avec le bureau économique ;
Élaboration de normes technologiques pour les opérations, procédés, limites, produits intermédiaires les plus énergivores, par unité de matières premières ou de produits finis sur l'ensemble de sa gamme ;
Élaboration de normes de consommation d'énergie pour les besoins sanitaires et techniques en fonction des facteurs climatiques et saisonniers ;
Rationnement des coûts énergétiques dans les processus et la production auxiliaires, pertes dans les communications énergétiques et les équipements énergétiques, et besoins propres du secteur énergétique ;
Élaboration de normes de production générale - atelier et usine - de consommation d'énergie pour les produits, travaux et services.
C'est ici que ça devrait avoir lieu planification de l'approvisionnement énergétique en développant des bilans énergétiques planifiés (actuels) et à long terme pour tous les consommateurs commerciaux (autosuffisants) à l'intérieur et à l'extérieur de l'entreprise.
Le Bureau de comptabilité, de contrôle et de surveillance de l'énergie devrait s'engager dans le maintien et l'amélioration de la comptabilité opérationnelle et statistique (actuelle) de la production, de la distribution et de la consommation des ressources énergétiques et des rapports associés ; contrôle et régulation opérationnels (en collaboration avec le service de répartition) et permanents de l'approvisionnement en énergie, supervision énergétique au sein de l'usine.
Le bureau (département) de planification économique est conçu pour planifier la production et les activités économiques du secteur énergétique (à l'exception de la production et de la consommation de ressources énergétiques), les relations commerciales avec les divisions de l'entreprise et les consommateurs externes.
Le bureau (département) financier doit effectuer des transactions financières pour financer la production et les activités économiques des services énergétiques, ainsi que des transactions financières avec les fournisseurs.
STRUCTURE ET CARACTÉRISTIQUES DE LA PRODUCTION D'ÉNERGIE
La production d'énergie est un processus technologique qui comprend trois phases : production, transformation, consommation d'énergie.
Ce processus technologique est basé sur des lois physiques, d'où découlent deux caractéristiques principales : la continuité forcée et l'automaticité ; coïncidence entre le moment de la production d’énergie et sa consommation.
De ces deux caractéristiques principales découlent les éléments suivants :
a) dans ce processus, il existe une proportionnalité absolue entre la production et la consommation d'énergie, c'est-à-dire il n'y a pas d'accumulation locale de produits et produits semi-finis ;
b) le rejet du produit et le retrait de la consommation sont exclus ;
c) il n'y a pas de problème de vente, le surstockage est impossible ;
d) il n'est pas nécessaire de stocker les produits.
Une caractéristique importante de la production d’énergie réside également dans le fait que les entreprises énergétiques sont étroitement liées à l'industrie, à la construction, aux transports, aux communications, à l'agriculture et aux services publics - avec l'ensemble des différents récepteurs d'énergie électrique. Et ceci, à son tour, prédétermine la stricte dépendance de la production d’énergie, notamment électrique, du régime de consommation.
Très caractéristique la production d'énergie est la variabilité de son régime aussi bien tout au long de l'année que pendant la journée. Cette variabilité repose, d'une part, sur des facteurs naturels et climatiques (fluctuations de température, changements de lumière naturelle), d'autre part, sur les particularités du processus technologique des diverses entreprises et industries.
Ces caractéristiques de la production d'énergie déterminent la pertinence d'assurer un niveau de fiabilité suffisant du secteur énergétique afin d'assurer une alimentation électrique ininterrompue aux consommateurs.
Une caractéristique essentielle de la production d'énergie réside également dans l'évolution relativement rapide des situations d'urgence, dans l'influence qu'un élément défaillant exerce sur les éléments travaillant en liaison avec lui.
Comme mentionné ci-dessus, dans la production d'énergie, il existe une stricte dépendance du mode de production au mode de consommation.
Par conséquent, les graphiques de charge, qui montrent l’évolution de la consommation au fil du temps, jouent un rôle important dans la planification et l’analyse économique de la production d’énergie. Selon l'intervalle de temps, on distingue les horaires journaliers (hiver, été) et annuels.
La charge du consommateur d'énergie change continuellement, atteignant le plus haut à un certain moment ( R. max) et le plus petit ( R. min) valeurs. La charge maximale et minimale sont les points les plus importants du graphique. L'aire du graphique exprime, sur une certaine échelle, la quantité d'énergie produite.
La zone délimitée par des lignes horizontales passant par le maximum R. maximum et moyenne R. La mer de la valeur de charge est appelée la partie de pointe du programme de charge quotidien, le reste du programme de charge est appelé la base. Ce sont des indicateurs graphiques de charge absolue. Les graphiques de charge sont également caractérisés par des indicateurs relatifs :
1. Coefficient de densité (remplissage) g, défini comme le rapport de la charge moyenne R. moyenne au maximum :
g = R. Mer / R. max, où max est la charge maximale, MW.
2) Coefficient de charge minimum α min, défini comme le rapport du minimum au maximum :
α = R. min/ R. maximum, où
Indicateurs de graphiques journaliers charge électrique du système électrique g et α min dépendent de la composition et du mode de fonctionnement des consommateurs d'énergie. α min peut théoriquement fluctuer de 0 à 1 (la charge entière est continue tout au long de la journée). En pratique, α min varie de 0,3 (les consommateurs en une seule équipe et l'éclairage prédominent) à 0,9 (les consommateurs énergivores avec une production continue prédominent).
L'indicateur de densité (remplissage) du programme de charge électrique quotidien se situe généralement dans g= 0,5÷0,95.
À une valeur inférieure, la capacité électrique des consommateurs industriels prévaut.
Réservation de puissance.
Une capacité de réserve est nécessaire pour remplacer les unités en panne et régulièrement retirées pour réparation, ainsi que pour répondre aux besoins en capacité de production.
Pour les installations de production, de transformation et de transport, les réserves de capacité sont distinguées en conséquence : réparation, urgence, charge (nécessaire pour compenser les changements irréguliers de charge pour des raisons aléatoires aux systèmes électriques). La combinaison des réserves d'urgence et de charge est appelée réserve opérationnelle. La réserve d'énergie électrique est commune, uniforme pour le pool énergétique. Sa taille est déterminée en fonction de la charge maximale du pool énergétique (généralement pour les journées d'hiver).
L’aspect économique du problème réside dans la justification de la quantité optimale de réserve de marche. En augmentant la réserve d'énergie dans les interconnexions électriques, les dommages causés au consommateur par un sous-approvisionnement d'urgence en énergie électrique sont réduits, mais les coûts de création et de maintien de l'énergie de réserve augmentent. Les statistiques montrent que la réserve de puissance nécessaire et suffisante du système électrique devrait être légèrement supérieure à 15 % de la charge maximale (y compris urgence - 4 à 5 %, réparation - 8 à 9 %, charge - 3 à 4 %).
GESTION OPÉRATIONNELLE DE L'ÉNERGIE DE L'ENTREPRISE
La plupart des fonctions de gestion ont des sous-fonctions liées au moment opérationnel - comptabilité opérationnelle, analyse opérationnelle, planification opérationnelle, contrôle opérationnel et régulation. Ensemble, ils forment (une organisation), les plus remarquables étant la comptabilité opérationnelle, le contrôle et la réglementation. Par conséquent, l'ensemble du processus de gestion opérationnelle est souvent appelé ainsi - comptabilité et contrôle opérationnels, dont la mise en œuvre est au service du secteur de l'énergie. La tâche principale de la gestion opérationnelle devrait également inclure le travail du personnel opérationnel sur chaque lieu de travail assurant l'entretien de l'énergie et des équipements technologiques consommateurs d'énergie.
En même temps, leur tâche devrait être dans la gestion optimale des processus non seulement en termes d'indicateurs technologiques, mais aussi en termes d'indicateurs énergétiques. Il convient d'envisager la procédure d'une telle gestion opérationnelle à l'aide de l'exemple d'une régulation optimale du fonctionnement d'une installation technologique selon les critères d'utilisation rationnelle de l'énergie. La gestion opérationnelle conformément aux tâches de tout cycle de gestion doit correspondre au processus standard de préparation, de prise et de mise en œuvre des décisions pour atteindre les objectifs. Dans ce cas, des connexions d'informations apparaissent entre l'objet et le sujet de gestion, et le processus de gestion lui-même consiste en l'exécution séquentielle de fonctions strictement définies.
La gestion opérationnelle comprend les principales étapes suivantes :
a) lors de la comptabilité opérationnelle, les données sur la consommation et l'utilisation des ressources énergétiques par l'objet de contrôle sont enregistrées ; Ces données sont des indicateurs quantitatifs et qualitatifs (paramétriques) de la consommation d'énergie ;
b) à partir des données comptables, des indicateurs sont sélectionnés qui déterminent le degré de rationalité de l'utilisation de l'énergie, c'est-à-dire soumis au contrôle opérationnel ;
c) les indicateurs sélectionnés sont analysés par rapport à des valeurs standard, par exemple avec le taux actuel de consommation d'énergie ;
d) si les indicateurs réels s'écartent des indicateurs normatifs, une solution est sélectionnée visant à corriger cette situation, et un ensemble de solutions standard est préparé à l'avance lors de la préparation des options de planification opérationnelle ;
e) l'option envisagée pour la solution optimale, si nécessaire, est convenue avec les responsables de haut rang, puis un ordre est donné pour sa mise en œuvre - un acte de gestion opérationnelle ;
f) des mesures sont prises pour réguler opérationnellement le processus visant à atteindre l'objectif - en alignant les indicateurs réels sur les indicateurs normatifs souhaités ;
g) un nouvel acte comptable opérationnel est réalisé pour vérifier si le résultat souhaité a été atteint ;
Ceci termine un cycle contrôle et le suivant commence - contrôlé