Le processus de production et les principes de base de son organisation. Organisation de la fabrication
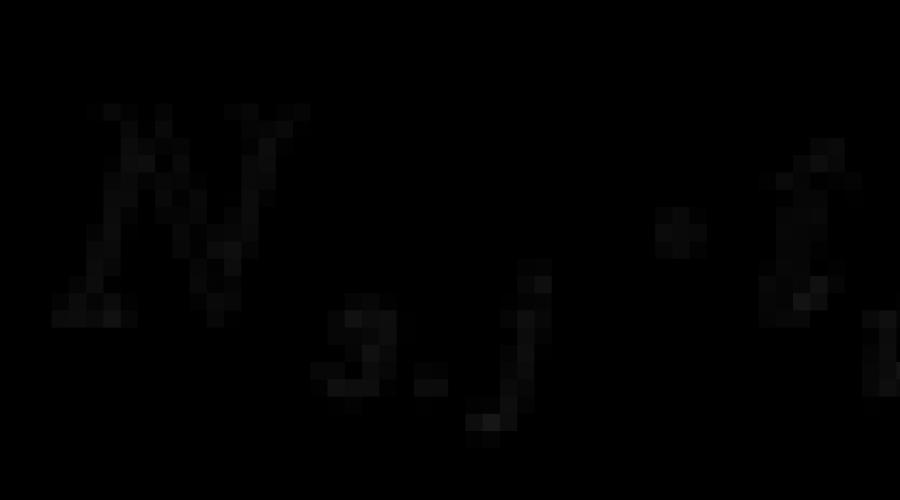
Lire aussi
Le processus de production se compose de processus partiels, qui peuvent être divisés en groupes selon les critères suivants :
Selon le mode d'exécution : manuel, mécanisé, automatisé.
Par objectif et rôle dans la production: principal, auxiliaire, servant
Les principaux processus de production sont les processus directement liés à la transformation de l'objet de travail en produits finis. Par exemple, en génie mécanique, le résultat des principaux processus est la production de machines, d'appareils et d'instruments qui composent le programme de production de l'entreprise et correspondent à sa spécialisation, ainsi que la fabrication de pièces de rechange pour leur livraison à le consommateur. L'ensemble de ces procédés partiels constitue la production principale.
Les processus de fabrication auxiliaires sont des processus qui créent les conditions nécessaires pour créer des produits finis, ou créer des produits finis, qui sont ensuite consommés dans la production principale de l'entreprise elle-même. Auxiliaires sont les processus de réparation d'équipements, de fabrication d'outils, de montages, de pièces de rechange, de mécanisation et d'automatisation. propre production, production de tous types d'énergie. L'ensemble de ces processus partiels constitue une production auxiliaire.
Entretien des processus de production - lors de la mise en œuvre de ces processus, les produits ne sont pas fabriqués, mais les services nécessaires à la mise en œuvre des processus principaux et auxiliaires sont effectués. Par exemple, le transport, l'entreposage, la délivrance de tous types de matières premières et de matériaux, le contrôle de la précision des instruments, la sélection et l'assemblage des pièces, le contrôle technique de la qualité des produits, etc. L'ensemble de ces processus constitue la production de services.
Processus d'assistance. Un processus qui contribue au déroulement normal du processus principal de transformation de l'objet de travail et est associé à la fourniture du processus principal avec des équipements, des installations, des outils de coupe et de mesure, des ressources en carburant et en énergie.
processus de service. Un processus qui n'est pas spécifiquement lié à ce sujet de travail, assurant le flux normal des processus principaux et auxiliaires en fournissant des services de transport, des services logistiques à "l'entrée" et à la "sortie" de l'organisation.
Les principaux processus de production se déroulent dans les étapes suivantes : étapes d'approvisionnement, de transformation, d'assemblage et de test.
L'étape d'approvisionnement est destinée à la production de pièces brutes. Une caractéristique du développement des processus technologiques à ce stade est le rapprochement des ébauches avec les formes et les tailles des pièces finies. Il se caractérise par une variété de méthodes de production. Par exemple, découpe ou découpe d'ébauches de pièces à partir d'un matériau, fabrication d'ébauches par coulée, emboutissage, forgeage, etc.
L'étape de transformation est la deuxième au cours du processus de production. Le sujet du travail ici est les pièces brutes. Les outils de travail à ce stade sont principalement des machines à couper les métaux, des fours pour le traitement thermique et des appareils pour le traitement chimique. A l'issue de cette étape, les pièces sont dimensionnées correspondant à la classe de précision spécifiée.
L'étape d'assemblage fait partie du processus de production, à la suite de laquelle des unités d'assemblage ou des produits finis sont obtenus. L'objet de la main-d'œuvre à ce stade sont les composants et les pièces de notre propre production, ainsi que ceux reçus de l'extérieur (produits composants). Les processus d'assemblage se caractérisent par un volume important Fait main Par conséquent, la tâche principale du processus technologique est leur mécanisation et leur automatisation.
L'étape de test est l'étape finale du processus de production, dont le but est d'obtenir les paramètres nécessaires du produit fini. Le sujet du travail ici sont les produits finis qui ont passé toutes les étapes précédentes.
Les éléments constitutifs des étapes du processus de production sont des opérations technologiques.
Une opération de production est une action élémentaire (travail) visant à transformer l'objet de travail et à obtenir un résultat donné. L'opération de production est une partie distincte du processus de production. Habituellement, il est effectué sur un lieu de travail sans réajustement de l'équipement et est effectué à l'aide d'un ensemble des mêmes outils.
5.1 Le concept de processus de production
Le processus de production est un ensemble de processus principaux, auxiliaires et processus de service travail et outils de travail afin de créer des valeurs de consommation - objets de travail utiles nécessaires à la consommation industrielle ou personnelle. Dans le processus de production, les travailleurs influencent les objets de travail à l'aide d'outils et créent de nouveaux produits finis, par exemple des machines-outils, des ordinateurs, des téléviseurs, des appareils radio-électroniques, etc. Les objets et outils de travail, étant des éléments matériels de production, sont dans une certaine relation les uns avec les autres dans l'entreprise, un autre: des éléments spécifiques ne peuvent être traités que par certains outils; ils ont déjà en eux-mêmes des propriétés systémiques. Cependant, le travail vivant doit embrasser ces choses et commencer ainsi le processus de les transformer en un produit. Ainsi, le processus de production est avant tout un processus de travail, puisque les ressources utilisées par une personne à son entrée, tant l'information que les moyens matériels de production, sont le produit de processus de travail antérieurs. Distinguer les processus de production principaux, auxiliaires et de service .
Principaux processus de production- c'est cette partie des processus au cours de laquelle il y a un changement direct dans les formes / tailles, les propriétés, la structure interne des objets de travail et leur transformation en produits finis. Par exemple, dans une usine de machines-outils, il s'agit des processus de fabrication de pièces et d'assemblage de sous-ensembles, d'assemblages et du produit dans son ensemble.
Aux processus de production auxiliaires inclure de tels processus, dont les résultats sont utilisés soit directement dans les processus principaux, soit pour assurer leur bon déroulement et mise en œuvre efficace. Des exemples de tels processus sont la fabrication d'outils, de montages, de matrices, de moyens de mécanisation et d'automatisation de leur propre production, de pièces de rechange pour la réparation d'équipements, de la production de tous les types d'énergie dans l'entreprise (électricité, air comprimé, azote, etc.).
Processus de production de services - ce sont des processus de travail pour la fourniture de services nécessaires à la mise en œuvre des processus de production principaux et auxiliaires. Par exemple, transport de biens matériels, opérations d'entrepôt de toutes sortes, contrôle technique de la qualité des produits, etc.
Les processus de production principaux, auxiliaires et de service ont des tendances de développement et d'amélioration différentes. Ainsi, de nombreux processus de production auxiliaires peuvent être transférés vers des usines spécialisées, ce qui, dans la plupart des cas, assure leur production plus rentable. Avec une augmentation du niveau de mécanisation et d'automatisation des processus principaux et auxiliaires, les processus de service deviennent progressivement partie intégrante de la production principale, jouant un rôle organisateur dans la production automatisée et surtout dans la production automatisée flexible.
Les processus de production principaux et, dans certains cas, auxiliaires, se déroulent en différentes étapes (ou phases). Organiser- il s'agit d'une partie distincte du processus de production, lorsque l'objet du travail passe dans un autre état qualitatif. Par exemple, le matériau entre dans la pièce, la pièce dans une pièce, etc.
Les principaux processus de production se déroulent dans les étapes suivantes : approvisionnement, transformation, assemblage et réglage.
Phase de récolte conçu pour la production de pièces brutes. Elle se caractérise par des modes de production très divers. Par exemple, découper ou découper des ébauches de pièces à partir de tôles, fabriquer des ébauches par coulée, emboutissage, forgeage, etc. La principale tendance dans le développement des procédés technologiques à ce stade est de rapprocher les ébauches des formes et des tailles des pièces finies. Les outils de travail à ce stade sont les machines de découpe, les équipements de pressage et d'estampage, les cisailles à guillotine, etc.
Étape de traitement - le second dans la structure du processus de production - comprend le traitement mécanique et thermique. Le sujet du travail ici est les pièces brutes. Les outils de travail à ce stade sont principalement diverses machines à couper les métaux, des fours pour le traitement thermique et des appareils pour le traitement chimique. A l'issue de cette étape, les pièces sont dimensionnées correspondant à la classe de précision spécifiée.
Phase d'assemblage (montage et installation) - il s'agit d'un processus de production, qui aboutit à des unités d'assemblage (petites unités d'assemblage, sous-ensembles, assemblages, blocs) ou produits finis. Les objets de travail à ce stade sont les pièces et assemblages de leur propre fabrication, ainsi que ceux reçus de l'extérieur (produits composants). Il existe deux principales formes d'organisation de l'assemblage : fixe et mobile. L'assemblage stationnaire correspond à la fabrication du produit sur un lieu de travail (les pièces sont fournies). Avec l'assemblage mobile, le produit est créé en le déplaçant d'un lieu de travail à un autre. Les outils de travail ici ne sont pas aussi diversifiés qu'au stade de la transformation. Les principaux sont toutes sortes d'établis, de supports, de dispositifs de transport et de guidage (convoyeurs, voitures électriques, robots, etc.). Les processus d'assemblage, en règle générale, sont caractérisés par une quantité importante de travail effectué manuellement, de sorte que leur mécanisation et leur automatisation sont la tâche principale de l'amélioration du processus technologique.
Étape d'ajustement et d'ajustement ― finale dans la structure du processus de production, qui est réalisée afin d'obtenir les paramètres techniques nécessaires du produit fini. Le sujet du travail ici est les produits finis ou leurs unités d'assemblage individuelles, les outils, l'instrumentation universelle et les bancs d'essai spéciaux.
Les éléments constitutifs des étapes des processus principaux et auxiliaires sont des opérations technologiques. La division du processus de production en opérations, puis en techniques et mouvements, est nécessaire au développement de normes techniquement solides pour l'exécution des opérations.
Opération - partie du processus de production qui, en règle générale, est effectuée sur un lieu de travail sans réajustement et par un ou plusieurs travailleurs (équipe).
Selon le degré d'équipement technique du processus de production, les opérations sont distinguées: manuelles, mécanisées, mécaniques, automatiques et matérielles.
Les processus de production principaux et auxiliaires, et parfois auxiliaires, consistent en des éléments principaux et auxiliaires - des opérations. Les principales comprennent les opérations directement liées à la modification de la taille, de la forme, des propriétés, de la structure interne de l'objet de travail ou de la transformation d'une substance en une autre, ainsi qu'à la modification de l'emplacement des objets de travail les uns par rapport aux autres. Les opérations auxiliaires comprennent les opérations dont la mise en œuvre contribue au flux des principales, par exemple le déplacement des objets de travail, le contrôle de la qualité, l'enlèvement et l'installation, le stockage, etc.
En termes d'organisation, les processus de production principaux et auxiliaires (leurs opérations) sont classiquement divisés en simples et complexes.
Simple on appelle processus dans lesquels les objets de travail sont soumis à une série successive d'opérations interconnectées, à la suite desquelles des produits de travail partiellement finis (ébauches, pièces, c'est-à-dire parties intégrantes du produit) sont obtenus.
complexe on appelle processus dans lesquels des produits finis du travail sont obtenus en combinant des produits privés, c'est-à-dire des produits complexes (machines, machines, appareils, etc.) sont obtenus.
Le mouvement des objets de travail dans le processus de production s'effectue de telle manière que le résultat du travail d'un lieu de travail devient l'objet initial d'un autre, c'est-à-dire que chacun précédent dans le temps et l'espace donne du travail au suivant, ce est assurée par l'organisation de la production.
de correct et organisation rationnelle les processus de production (en particulier les principaux) dépendent des résultats de la production et des activités économiques de l'entreprise, des indicateurs économiques de son travail, du coût de production, du profit et de la rentabilité de la production, de la quantité de travail en cours et de la quantité de fonds de roulement.
5.2 Principes de base de l'organisation des processus de production
L'organisation du processus de production dans toute entreprise de construction de machines (y compris l'instrumentation radioélectronique), dans l'un de ses ateliers, sur un site repose sur une combinaison rationnelle dans le temps et dans l'espace de tous les processus principaux, auxiliaires et de service. Cela vous permet de produire des produits au coût de la vie et de la main-d'œuvre matérialisés minimes. Les caractéristiques et les méthodes d'une telle combinaison sont différentes dans différentes conditions de production. Cependant, dans toute leur diversité, l'organisation des processus de production est soumise à certains principes généraux : différenciation, concentration et intégration, spécialisation, proportionnalité, flux direct, continuité, parallélisme, rythme, automaticité, prévention, flexibilité, optimalité, électronisation, standardisation, etc.
Le principe de différenciation implique la division du processus de production en processus technologiques distincts, eux-mêmes divisés en opérations, transitions, techniques et mouvements.Dans le même temps, une analyse des caractéristiques de chaque élément vous permet de choisir les meilleures conditions pour sa mise en œuvre, en minimisant les coûts totaux de tous les types de ressources. Ainsi, la production en ligne se développe depuis de nombreuses années du fait de la différenciation toujours plus poussée des procédés technologiques. L'attribution d'opérations à court terme a permis de simplifier l'organisation et l'équipement technologique de la production, d'améliorer les compétences des travailleurs et d'augmenter leur productivité.
Cependant, une différenciation excessive augmente la fatigue des travailleurs dans les opérations manuelles en raison de la monotonie et de la forte intensité des processus de production. Un grand nombre d'opérations entraîne des coûts excessifs pour déplacer les objets de travail entre les travaux, les installer, les réparer et les retirer des travaux après la fin des opérations.
Lors de l'utilisation d'équipements flexibles modernes et performants (machines à commande numérique, centres d'usinage, robots, etc.), le principe de différenciation se transforme en principe de concentration des opérations et d'intégration des processus de production. Le principe de concentration implique la réalisation de plusieurs opérations sur un même poste de travail (machines multibroches multicoupes à commande numérique). Les opérations deviennent plus volumineuses, complexes et sont effectuées en combinaison avec le principe de brigade de l'organisation du travail. Le principe de l'intégration est de combiner les principaux processus de support et de service.
Le principe de spécialisation est une forme de division du travail social qui, se développant systématiquement, détermine la répartition des ateliers, des sections, des lignes et des emplois individuels dans l'entreprise. Ils fabriquent une gamme limitée de produits et se distinguent par un processus de production particulier.
Une réduction de la gamme de produits manufacturés entraîne généralement une amélioration de tous les indicateurs économiques, en particulier une augmentation du niveau d'utilisation des immobilisations d'une entreprise, une réduction du coût de production, une amélioration dans la qualité des produits, la mécanisation et l'automatisation des processus de production. L'équipement spécialisé, toutes choses égales par ailleurs, fonctionne de manière plus productive.
Le niveau de spécialisation du lieu de travail est déterminé par le coefficient de consolidation des opérations de détail ( Dormir) effectué sur un lieu de travail pendant une certaine période de temps (mois, trimestre),
où Cpr- le nombre d'emplois (équipements) du système de production ; moi je - le nombre d'opérations de détail effectuées sur le i-ème lieu de travail pendant une unité de temps (mois, année).
Avec un coefficient Kcn= 1 spécialisation étroite du lieu de travail est assurée, les conditions préalables sont créées pour une organisation efficace de la production. Pour charger complètement un poste de travail avec une opération de détail, il est nécessaire que la condition
,
où N cj- le volume de lancement de pièces du jième nom par unité de temps, par exemple, pièces / mois;
t pièces- intensité de travail de l'opération au ième lieu de travail, min;
F ef- fonds de temps effectif du lieu de travail, par exemple, min/mois.
Le principe de proportionnalité suppose un débit égal de toutes les unités de production qui exécutent les processus principaux, auxiliaires et de service. La violation de ce principe conduit à l'émergence de "goulets d'étranglement" dans la production ou, au contraire, au chargement incomplet de travaux individuels, de sections, d'ateliers, à une diminution de l'efficacité de l'ensemble de l'entreprise. Par conséquent, pour assurer la proportionnalité, les calculs de capacité de production sont effectués à la fois par étapes de production et par groupes d'équipements et zones de production. Par exemple, si le volume de production de pièces est connu (N 3) et l'heure normale (t pièces), il est possible de déterminer la charge d'un certain i-ème groupe d'équipements par la formule
.
Ensuite, déterminez le débit de ce groupe d'équipements
,
après cela, la charge et le débit du i-ème groupe d'équipements sont comparés et son facteur de charge est déterminé par la formule
L'option préférée est lorsque K zі= 1 et Q je = P je .
Principe du flux direct signifie une telle organisation du processus de production, qui fournit les chemins les plus courts pour le passage des pièces et des unités d'assemblage à travers toutes les étapes et opérations depuis le lancement des matières premières en production jusqu'à la sortie des produits finis. Le flux de matériaux, de produits semi-finis et d'unités d'assemblage doit être aller et le plus court possible, sans mouvements de contre et de retour. Ceci est assuré par la disposition appropriée du placement des équipements tout au long du processus technologique. Un exemple classique d'une telle disposition est la ligne de production.
^ Principe de continuité signifie que le travailleur travaille sans temps d'arrêt, que l'équipement fonctionne sans interruption, que les objets du travail ne se trouvent pas sur le lieu de travail. Ce principe se manifeste le plus pleinement dans la production de masse ou à grande échelle dans l'organisation des méthodes de production en flux, en particulier dans l'organisation de lignes de production continues à un ou plusieurs sujets. Ce principe permet une réduction du cycle de fabrication du produit et contribue ainsi à une augmentation de l'intensification de la production.
Le principe du parallélisme implique l'exécution simultanée de processus de production partiels et d'opérations individuelles sur des pièces similaires et des pièces du produit sur différents lieux de travail, c'est-à-dire la création d'un large front de travail sur la fabrication de ce produit. Le parallélisme dans l'organisation du processus de production est utilisé sous diverses formes: dans la structure de l'opération technologique - traitement multi-outils (machines semi-automatiques multibroches à coupe multiple) ou exécution parallèle des éléments principaux et auxiliaires des opérations; dans la fabrication des ébauches et le traitement des pièces (dans les ateliers, ébauches et pièces à différents stades de préparation) ; dans l'assemblée nodale et générale. Le principe de parallélisme réduit la durée du cycle de production et fait gagner du temps de travail.
^ Le principe du rythme assure la libération de volumes identiques ou croissants de produits pendant des périodes de temps égales et, par conséquent, la répétition pendant ces périodes du processus de production à toutes ses étapes et opérations. Avec une spécialisation étroite de la production et une gamme stable de produits, le rythme peut être assuré directement par rapport aux produits individuels et est déterminé par le nombre de produits transformés ou fabriqués par unité de temps. Dans le contexte d'une gamme large et changeante de produits fabriqués par le système de production, le rythme du travail et la production ne peuvent être mesurés qu'à l'aide d'indicateurs de main-d'œuvre ou de coût.
Le principe d'automaticité assume automatiquement la performance maximale des opérations du processus de production, c'est-à-dire sans la participation directe du travailleur ou sous sa supervision et son contrôle. L'automatisation des processus entraîne une augmentation de la production de pièces, de produits, une augmentation de la qualité du travail, une réduction du coût du travail humain, le remplacement d'un travail manuel peu attrayant par un travail plus intellectuel de travailleurs hautement qualifiés (ajusteurs, opérateurs), l'élimination du travail manuel dans les emplois aux conditions préjudiciables et le remplacement des travailleurs par des robots. L'automatisation des processus de service est particulièrement importante. Les véhicules et les entrepôts automatisés remplissent des fonctions non seulement pour le transfert et le stockage des installations de production, mais peuvent réguler le rythme de l'ensemble de la production. Le niveau général d'automatisation des processus de production est déterminé par la part du travail dans les industries principales, auxiliaires et de services, dans le volume total de travail de l'entreprise. Niveau d'automatisation (En automatique) déterminé par la formule
où Aut- la complexité du travail effectué de manière automatique ou automatisée ;
T totale- l'intensité de travail totale du travail dans l'entreprise (atelier) pendant une certaine période de temps.
Le niveau d'automatisation peut être calculé comme un total pour l'ensemble de l'entreprise et pour chaque division séparément.
Le principe de prévention implique l'organisation de la maintenance des équipements visant à prévenir les accidents et l'indisponibilité des systèmes techniques. Ceci est réalisé grâce à un système de maintenance préventive (PPR).
Principe de flexibilité fournit organisation efficace travaux, permet de passer mobile à la production d'autres produits inclus dans le programme de production de l'entreprise, ou à la production de nouveaux produits dans le développement de sa production. Il offre une réduction du temps et des coûts de changement d'équipement dans la production de pièces et de produits d'une large gamme. Ce principe est le plus développé dans des conditions de production hautement organisées, où des machines CNC, des centres d'usinage (MC), des moyens automatiques reconfigurables de contrôle, de stockage et de déplacement des objets de production sont utilisés.
Principe d'optimalité consiste dans le fait que la mise en œuvre de tous les processus de production de produits en une quantité donnée et dans les délais est réalisée avec la plus grande efficacité économique ou avec les coûts de main-d'œuvre et de ressources matérielles les plus bas. L'optimalité est due à la loi d'économie du temps.
Le principe de l'électronisation implique l'utilisation généralisée des capacités CNC basées sur l'utilisation de la technologie des microprocesseurs, ce qui vous permet de créer des systèmes de machines fondamentalement nouveaux qui combinent des performances élevées avec les exigences de flexibilité des processus de production. ordinateurs et robots industriels, avec l'intelligence artificielle, vous permettent d'effectuer les fonctions les plus complexes en production à la place d'une personne.
L'utilisation de mini- et micro-ordinateurs avec des Logiciel et les machines CNC multi-outils permettent d'effectuer un grand ensemble voire l'intégralité de l'usinage des pièces depuis l'une de leurs installations sur la machine grâce au changement d'outil automatique. Un ensemble d'outils de coupe pour une telle machine peut atteindre 100 à 120 unités, qui sont installées dans une tourelle ou un magasin d'outils et remplacées selon un programme spécial.
Le principe de standardisation implique l'utilisation généralisée dans la création et le développement de nouvelles technologies et de nouvelles technologies de normalisation, d'unification, de typification et de normalisation, ce qui permet d'éviter une diversité déraisonnable dans les matériaux, les équipements, les procédés technologiques et de réduire drastiquement la durée du cycle de création et le développement de nouvelles technologies (SONT).
Lors de la conception d'un processus de production ou d'un système de production, il convient de partir de l'utilisation rationnelle des principes énoncés ci-dessus.
5.3 Types de production et leurs caractéristiques techniques et économiques
L'organisation des processus de production, le choix des méthodes de préparation les plus rationnelles, la planification et le contrôle de la production sont largement déterminés par le type de production dans une entreprise de construction de machines.
Le type de production s'entend comme un ensemble d'éléments qui déterminent les caractéristiques organisationnelles et techniques du processus de production réalisé sur un ou plusieurs postes de travail à l'échelle d'un site, d'un atelier, d'une entreprise. Le type de production détermine en grande partie les formes de spécialisation et les modes d'organisation des processus de production.
La classification des types de production est basée sur les facteurs suivants : l'étendue de la nomenclature, le volume de la production, le degré de constance de la nomenclature, la nature de la charge de travail et leur spécialisation.
Nomenclature produit est le nombre d'articles affectés au système de production, et caractérise sa spécialisation. Plus la nomenclature est large, moins le système est spécialisé et, à l'inverse, plus il est étroit, plus le degré de spécialisation est élevé. Une large gamme de produits manufacturés détermine une grande variété de processus technologiques et d'opérations, d'équipements, d'outils, d'équipements et de professions de travailleurs.
Sortie de produit - est le nombre d'articles d'un certain type produits par le système de production pendant une certaine période de temps. Le volume de la production et la complexité de chaque type de produit ont une influence déterminante sur la nature de la spécialisation de ce système.
Le degré de constance de la nomenclature - est la répétabilité de la fabrication d'un produit d'un type donné dans des périodes de temps successives. Si, au cours d'une période de temps planifiée, un produit de ce type est fabriqué et qu'il n'est pas produit dans d'autres, il n'y a aucun degré de constance. La répétition régulière de la sortie de produits de ce type est l'une des conditions préalables pour assurer le rythme de la production. À son tour, la régularité dépend du volume de production, puisqu'un grand volume de production peut être réparti uniformément sur des périodes de planification successives.
La nature de la charge de travail désigne l'affectation de certaines opérations du processus technologique aux lieux de travail. Si le nombre minimum d'opérations est affecté au lieu de travail, il s'agit d'une spécialisation étroite, et si un grand nombre d'opérations sont affectées au lieu de travail (si la machine est universelle), cela signifie une large spécialisation.
En fonction des facteurs ci-dessus, il existe trois types de processus de production ou trois types de production: unique, en série et en masse (Fig. 5.1).
Figure 5.1 - Classification des types de production
Les principaux indicateurs pour déterminer le type de production peuvent être les coefficients de spécialisation des emplois ( Kcn), sérialité (K ser) et caractère de masse (Km).
Coefficient de spécialisation professionnelle
où m d.o.- le nombre d'opérations de détail du procédé technologique réalisées dans cette unité (sur chantier, en atelier) ;
Cpr- le nombre d'emplois (équipements) dans cette unité.
Facteur série
K ser \u003d r / t pcs,
où r– cycle de libération des produits, min./pcs. ; r = F eff : N ;
t pièces- temps moyen à la pièce pour les opérations du processus technologique, min.
où, t pièces.- temps à la pièce pour la ième opération du processus technologique, min.
t- nombre d'opérations.
Le coefficient de masse est déterminé par la formule
.
A chaque type de production correspond : la valeur des coefficients indiqués, le type d'équipement utilisé, la technologie et les formes d'organisation de la production, les types de mouvements d'objets de travail, la structure de production de l'entreprise (atelier, site) et autres caractéristiques.
Fabrication unique caractérisée par une large gamme de produits et la production de petits volumes de produits identiques, dont la reproduction, en règle générale, n'est pas prévue. Cela rend impossible l'affectation permanente d'opérations à des emplois individuels, le coefficient de spécialisation K sp > 40 opérations de détail par poste de travail. La spécialisation de ces emplois n'est due qu'à leur caractéristique technologique et les dimensions des produits transformés. Dans cette production, un équipement universel est utilisé et, pour l'essentiel, un type séquentiel de mouvement de lots de pièces à travers les opérations du processus technologique. Les usines ont une structure de production complexe et les ateliers sont spécialisés selon le principe technologique.
Production de masse se spécialise dans la fabrication d'une gamme limitée de produits en volumes relativement petits et en lots (séries) qui se répètent après un certain temps. En fonction du nombre d'opérations affectées à chaque lieu de travail, de la régularité de répétition des lots de produits et de leur taille, on distingue trois sous-types (types) de production de masse : petite, moyenne et grande échelle.
La production à petite échelle a tendance à être monobloc : les produits sont fabriqués en petits lots d'une large gamme, la répétabilité des produits dans le programme de l'usine est soit absente, soit irrégulière, et les tailles de lots sont instables ; l'entreprise développe constamment de nouveaux produits et arrête la production de ceux déjà maîtrisés. Les emplois sont affectés à un large éventail d'opérations, Kcn= 20 - 40 opérations ( K ser > 20; K m< une). L'équipement, les types de mouvements, les formes de spécialisation et la structure de production sont les mêmes que dans la production unitaire.
Il est typique pour la production à moyenne échelle que la production de produits soit réalisée en séries assez importantes d'une gamme limitée; les séries sont répétées avec une régularité connue en fonction de la période de lancement et du nombre de produits du lot ; la nomenclature annuelle est encore plus large que la nomenclature de l'émission de chaque mois. Une gamme plus restreinte d'opérations est affectée aux tâches : Kcn= 10 - 20 opérations ( K ser= 20; K m< une). L'équipement est universel et spécial, le type de mouvement des objets de travail est parallèle-séquentiel. Les usines ont une structure de production développée, les magasins d'approvisionnement se spécialisent selon le principe technologique et les ateliers de montage de machines créent des sections fermées.
La production à grande échelle gravite vers la production de masse. Les produits sont fabriqués en grandes séries d'une gamme limitée, et les principaux ou les plus importants sont fabriqués en permanence et en continu. Les emplois ont une spécialisation plus étroite : Kcn= 2 - 10 opérations ( K ser = 10; K m< une). L'équipement est principalement spécial, les types de mouvements d'objets de travail sont parallèles-séquentiels et parallèles. Les usines ont une structure de production simple, les ateliers de transformation et d'assemblage sont spécialisés selon le principe du sujet et les achats - selon le principe technologique.
Masse la production se caractérise par la libération d'une gamme étroite de produits sur une longue période de temps et un grand volume, une répétabilité stable. Une gamme étroite d'opérations est affectée aux tâches : Kcn< 1 операции (K ser< 2; K m> 1). Tous les produits de la nomenclature de l'usine sont fabriqués simultanément et en parallèle. Le nombre de noms de produits dans les programmes annuels et mensuels est le même. L'équipement est spécial, le type de mouvement des objets de travail est parallèle. Les magasins et les sections sont spécialisés principalement selon le principe du sujet. Les usines ont une structure de production simple et bien définie.
En combinaison avec la mécanisation et l'automatisation des processus de production, ainsi que le chargement des emplois (équipements) avec des types de mouvement d'objets de travail, vous pouvez obtenir une production de masse en quatre et une production de masse en trois options (Fig. 5.2).
En fonction du type de production, le type d'entreprise et ses divisions sont établis. Chaque entreprise peut avoir différents types de production. Par conséquent, le type d'entreprise ou sa division est déterminé par le type prédominant de production finale.
Le type de production a une influence déterminante sur les caractéristiques de son organisation, de sa gestion et de sa planification opérationnelle de la production, ainsi que sur les indicateurs techniques et économiques. Riz. 5.2 - Classification des types de production
Si nous considérons l'ensemble des types de production dans leur ensemble, en commençant par un seul et en terminant par la production de masse, alors à mesure que nous nous dirigeons vers la production de masse, nous pouvons noter: a) l'expansion continue de la portée des processus technologiques performants , accompagné par la mécanisation et l'automatisation de la production ; b) une augmentation de la part des équipements spéciaux et des équipements technologiques spéciaux dans le nombre total d'outils de travail; dans) augmentation générale qualification technique des travailleurs, ainsi que l'introduction de méthodes et de techniques de travail avancées.
Sur la base de ces changements progressifs, lors du passage de la production unitaire à la production de masse et ensuite à la production de masse, d'importantes économies de travail social sont assurées et, par conséquent : une augmentation de la productivité du travail, une amélioration de l'utilisation des immobilisations d'une entreprise, une réduction des coûts matériels par produit, ainsi qu'une réduction des coûts de production, et une augmentation des bénéfices et de la rentabilité de la production.
Cependant, il convient de noter que l'utilisation de méthodes de groupe pour le traitement des pièces, des moyens d'automatisation et d'électronisation des processus de production permet d'appliquer des formes organisationnelles de production de masse en série et même en production unique et d'atteindre des indicateurs techniques et économiques élevés. Par exemple, l'introduction de complexes de production flexibles dans une seule production augmente la productivité du travail de 4 à 6 fois, augmente le taux d'utilisation des équipements à 0,92-0,95, réduit le besoin d'espace de production de 40 à 60%, réduit la durée du cycle de production et améliore tout indicateurs techniques et économiques.
5.4 Organisation rationnelle de la production
L'une des exigences les plus importantes pour l'organisation rationnelle du processus de production est d'assurer la durée la plus courte du cycle de production pour la fabrication des produits.
Le cycle de production est compris comme une période calendaire allant du moment où les matières premières sont mises en production jusqu'à ce que le produit fini soit entièrement fabriqué. La durée du cycle de production pour la fabrication de tout produit comprend la période de travail, le temps des processus naturels et le temps des pauses.
La forme d'organisation de la production est une certaine combinaison dans le temps et dans l'espace des éléments du processus de production avec un niveau approprié de son intégration, exprimée par un système de relations stables.
Selon le type de structure temporaire, on distingue les formes d'organisation avec transfert séquentiel, parallèle et parallèle-séquentiel des objets de travail dans la production.
La forme d'organisation de la production avec le transfert séquentiel des objets de travail est une telle combinaison d'éléments du processus de production, qui assure le mouvement des produits transformés dans toutes les zones de production en lots de taille arbitraire. Les objets de travail pour chaque opération ultérieure ne sont transférés qu'après l'achèvement du traitement de l'ensemble du lot lors de l'opération précédente. Ce formulaire est le plus flexible par rapport aux changements qui surviennent dans le programme de production, vous permet d'utiliser pleinement l'équipement, ce qui permet de réduire le coût de son achat. L'inconvénient de cette forme d'organisation de la production réside dans la durée relativement longue du cycle de production, puisque chaque pièce, avant d'effectuer l'opération suivante, se trouve en anticipation du traitement de l'ensemble du lot.
La forme d'organisation de la production avec le transfert parallèle d'objets de travail est basée sur une telle combinaison d'éléments du processus de production qui vous permet de démarrer, de traiter et de transférer des objets de travail d'une opération à l'autre et sans attendre. Cette organisation du processus de production conduit à une réduction du nombre de pièces à traiter, à une réduction de l'espace requis pour les entrepôts et les allées. Son inconvénient est le temps d'arrêt possible des équipements (emplois) en raison des différences de durée des opérations.
La forme d'organisation de la production avec transfert parallèle-séquentiel d'objets de travail est intermédiaire entre les formes sérielles et parallèles et élimine partiellement leurs défauts inhérents. Les produits d'une opération à l'autre sont transférés par les transporteurs. Cela garantit la continuité de l'utilisation des équipements et de la main-d'œuvre, il est possible de paralléliser partiellement le passage d'un lot de pièces à travers les opérations du processus technologique.
La structure spatiale de l'organisation de la production est déterminée par la quantité d'équipements technologiques concentrés sur le chantier (le nombre d'emplois) et sa localisation par rapport au sens de déplacement des objets de travail dans l'espace environnant. En fonction du nombre d'équipements technologiques (emplois), on distingue un système de production à un seul lien et la structure correspondante d'un lieu de travail séparé et un système à plusieurs liens avec un atelier, une structure linéaire ou cellulaire. Les options possibles pour la structure spatiale de l'organisation de la production sont présentées dans la fig. 5.3. La structure de l'atelier se caractérise par la création de sites où les équipements (emplois) sont implantés parallèlement au flux des pièces, ce qui implique leur spécialisation sur la base de l'homogénéité technologique.
Figure 5.3. Variantes de la structure spatiale du processus de production
La combinaison des structures spatiales et temporelles du processus de production à un certain niveau d'intégration des processus partiels détermine diverses formes d'organisation de la production: technologique, sujet, flux direct, ponctuel, intégré (Fig. 5.4). Envisager traits de caractère chacun d'eux.
Riz. 5.4. Formes d'organisation de la production
forme technologique l'organisation du processus de production est caractérisée structure de l'atelier Avec transmission en série objets de travail. Cette forme d'organisation est largement répandue dans les usines de fabrication de machines, car elle assure une utilisation maximale des équipements dans la production à petite échelle et est adaptée aux changements fréquents de processus technologique. Dans le même temps, l'utilisation d'une forme technologique d'organisation du processus de production a un certain nombre de conséquences négatives. Un grand nombre de pièces et leurs mouvements répétés lors du traitement entraînent une augmentation du volume d'encours et une augmentation du nombre de points de stockage intermédiaires. Une partie importante du cycle de production est la perte de temps due à une communication intersectionnelle complexe.
Forme d'objet de l'organisation la production a une structure cellulaire avec un transfert parallèle-séquentiel (séquentiel) d'objets de travail dans la production. Sur le sujet, en règle générale, tous les équipements nécessaires au traitement d'un groupe de pièces du début à la fin du processus technologique sont installés. Si le cycle de traitement technologique est fermé dans le domaine, il est dit sujet-fermé.
Forme d'organisation directe la production se caractérise structure linéaire avec transfert pièce par pièce des objets de travail. Cette forme assure la mise en œuvre d'un certain nombre de principes d'organisation : spécialisation, flux direct, continuité, parallélisme. Son application entraîne une réduction de la durée du cycle de production, une utilisation plus efficace de la main-d'œuvre grâce à une plus grande spécialisation de la main-d'œuvre et une diminution du volume des travaux en cours.
Avec forme de points organisation de la production, le travail est entièrement effectué sur un seul lieu de travail. Le produit est fabriqué là où se trouve sa partie principale.
Un exemple est l'assemblage d'un produit avec le travailleur qui se déplace autour de lui. L'organisation de la production ponctuelle présente de nombreux avantages: elle offre la possibilité de changements fréquents dans la conception des produits et la séquence de traitement, la fabrication de produits de différentes nomenclatures dans la quantité déterminée par les besoins de production; les coûts associés au changement d'emplacement des équipements sont réduits, la flexibilité de la production est accrue.
Formulaire intégré l'organisation de la production implique la combinaison d'opérations principales et auxiliaires en un seul processus de production intégré à structure cellulaire ou linéaire avec transfert en série, parallèle ou parallèle-série d'objets de travail dans la production. Contrairement à la pratique existante de conception séparée des processus d'entreposage, de transport, de gestion, de traitement dans des zones à forme d'organisation intégrée, il est nécessaire de lier ces processus partiels en un seul processus de production. Ceci est réalisé en combinant tous les emplois à l'aide d'un complexe de transport et de stockage automatique, qui est un ensemble de dispositifs interconnectés, automatiques et de stockage, d'équipements informatiques conçus pour organiser le stockage et le mouvement des objets de travail entre les différents emplois.
La gestion du processus de production est ici effectuée à l'aide d'un ordinateur, qui assure le fonctionnement de tous les éléments du processus de production sur le site selon le schéma suivant: recherche de la pièce nécessaire dans l'entrepôt - transport de la pièce à la machine - traitement - retour de la pièce à l'entrepôt. Pour compenser les écarts de temps lors du transport et du traitement des pièces, des entrepôts tampons de réserves inter-opérationnelles et d'assurance sont créés sur les lieux de travail individuels. La création de sites de production intégrés est associée à des coûts ponctuels relativement élevés causés par l'intégration et l'automatisation du processus de production.
L'effet économique de la transition vers une forme intégrée d'organisation de la production est obtenu en réduisant la durée du cycle de production pour la fabrication de pièces, en augmentant le temps de chargement des machines-outils et en améliorant la régulation et le contrôle des processus de production. Sur la fig. 5.4 montre la disposition des équipements dans des zones avec différentes formes d'organisation de la production.
Figure 5.4. Agencements d'équipements (postes de travail) sur des sites avec différentes formes d'organisation de la production :
a) technologique ; b) sujet ; c) direct :
d) point (pour le cas du montage) ; e) intégré
En dessous de processus de production est compris comme un ensemble de processus de travail et de processus naturels divers mais interconnectés qui assurent la transformation des matières premières en un produit fini.
Le processus de production comprend des processus principaux, auxiliaires, de service et secondaires.
À principale comprennent les processus directement liés à la transformation de matières premières ou de matériaux en produits finis (céréales en farine, betteraves sucrières en sucre). L'ensemble de ces processus dans l'entreprise constitue la production principale.
Dans les entreprises de réception de céréales qui stockent les ressources céréalières de l'État, les processus associés à la réception, au placement et au stockage des céréales doivent également être considérés comme les principaux.
Objectif auxiliaire X processus - entretenir techniquement les principaux processus, leur fournir certains services: fourniture d'énergie, production d'outils et d'accessoires, travaux de réparation.
Portion les processus fournissent des services matériels aux industries principales et auxiliaires. Réception, placement, stockage des matières premières, des matériaux, des produits finis, du carburant, leur transport des lieux de stockage aux lieux de consommation, etc.
Effets secondaires les procédés contribuent également à la transformation des matières premières en produits finis. Mais ni les matières premières ni les produits obtenus ne sont les principaux produits de l'entreprise. Il s'agit du traitement et du raffinement des déchets obtenus dans la production principale, etc.
Tous les processus sont divisés en étapes et les étapes sont divisées en opérations distinctes.
Étape de fabrication- une partie technologiquement achevée du processus de production, caractérisée par de tels changements dans l'objet du travail qui provoquent sa transition vers un autre état qualitatif (nettoyage de la betterave à sucre, emballage du produit).
Chaque étape combine des opérations qui sont technologiquement liées les unes aux autres, ou des opérations ayant un objectif spécifique.
Le principal maillon principal du processus de production est l'opération.
Opération de fabrication- c'est une partie du processus de travail ou de production, effectuée par un ou un groupe de travailleurs dans un lieu séparé, avec le même objet de travail, en utilisant les mêmes moyens de travail.
Par rendez-vous Toutes les opérations sont divisées en trois types principaux:
1) technologique (de base) - ce sont des opérations au cours desquelles des modifications sont apportées à l'objet du travail (son état, sa forme ou son apparence) (séparation du lait, broyage du grain, etc.);
2) contrôle - ce sont des opérations qui n'introduisent aucune modification dans l'objet du travail, mais contribuent à la réalisation d'opérations technologiques (pesée, etc.);
3) déménagement - opérations qui modifient la position de l'objet de travail dans la production (chargement, déchargement, transport).
Les opérations de contrôle et de déplacement forment ensemble un groupe d'opérations auxiliaires.
Selon le mode d'exécution (degré de mécanisation) distinguer les opérations suivantes :
- machine- effectués par des machines sous la surveillance de travailleurs (enroulement de conserves, nettoyage du lait, broyage des produits);
- machine-manuel- réalisée par des machines avec la participation directe des ouvriers (mise en sac de farine, couture de sacs, etc.) ;
- manuel opérations - effectuées par des travailleurs sans la participation de machines (fourniture de matières premières aux convoyeurs, empilage de sacs).
Rapport diverses sortes opérations dans leur nombre total est la structure du processus de production. Ce n'est pas la même chose dans les différentes entreprises de transformation.
Organisation de la production dans le temps construire sur les principes suivants :
Le rythme de l'entreprise et l'uniformité du rendement ;
Proportionnalité des unités de production ;
Parallélisme (simultanéité) des opérations et des processus de production ;
Continuité des processus de production.
Le principe du rythme prévoit le travail de l'entreprise au rythme prévu (le temps entre la sortie de produits identiques ou de deux lots de produits identiques).
Principe proportionnel Ces unités de production supposent la même productivité par unité de temps.
Le principe du parallélisme l'exécution des opérations et des processus repose sur l'exécution simultanée de phases, d'étapes ou de parties du processus de production.
Principe de continuité le processus de production prévoit l'élimination des interruptions dans le traitement des objets de travail. La continuité du processus élimine la création d'un stock sur le lieu de travail, réduit les travaux en cours, ce qui est particulièrement important dans les entreprises où les matières premières et les matériaux ne peuvent pas être stockés pendant une longue période sans refroidissement, congélation, mise en conserve (conserves de fruits et légumes, laiterie, industries de la viande).
objectif organisation du processus de production dans l'espace est d'assurer sa construction rationnelle dans le temps.
La plus grande efficacité dans l'organisation du processus de production dans l'espace est obtenue grâce à l'utilisation du flux direct, de la spécialisation, de la coopération et de la combinaison de la production.
Flux direct du processus de production, se caractérise par le fait qu'à toutes les phases et opérations de production, les produits suivent le chemin le plus court. A l'échelle de l'entreprise, les ateliers sont implantés sur le territoire de manière à exclure les transports longue distance, aller-retour, venant en sens inverse et autres irrationnels. C'est-à-dire que les emplois et les équipements sont situés dans la séquence technologique des opérations.
Spécialisation en usine est un processus de séparation des ateliers et des sites pour la production de certains types de produits, de leurs pièces ou la mise en œuvre d'étapes individuelles du processus technologique. Les entreprises de transformation appliquent une spécialisation technologique, thématique et fonctionnelle.
Spécialisation technologique la production implique l'attribution d'une gamme étroite d'opérations technologiques et la réalisation d'opérations dans des ateliers ou des sites de production séparés.
Spécialisation matière la production implique la création de lignes séparées avec un cycle de production complet pour la production d'un ou plusieurs produits similaires dans la technologie de fabrication.
fonctionnel appelé la spécialisation de toutes les divisions de production dans l'exercice d'une ou d'une gamme limitée de fonctions.
la coopération la production dans l'entreprise est réalisée par l'organisation travail conjoint ses divisions de produits. Le principe de la coproduction est l'utilisation des services de certains ateliers par d'autres.
La recherche de formes rationnelles de coopération conduit dans un certain nombre de cas à la création d'industries combinées.
combinaison la production implique la connexion dans une même entreprise d'industries différentes, qui sont des étapes successives dans la transformation des matières premières ou jouent un rôle auxiliaire les unes par rapport aux autres.
Le processus de production est un ensemble d'actions délibérées du personnel de l'entreprise pour la transformation des matières premières et des matériaux en produits finis.
Les principales composantes du processus de production qui déterminent la nature de la production sont le personnel professionnellement formé ; moyens de travail (machines, équipements, bâtiments, structures, etc.); objets de travail (matières premières, matériaux, produits semi-finis); énergie (électrique, thermique, mécanique, lumineuse, musculaire) ; informations (scientifiques et techniques, commerciales, opérationnelles et de production, juridiques, socio-politiques).
L'interaction professionnellement contrôlée de ces composants forme un processus de production spécifique et constitue son contenu.
Le processus de production est la base de toute entreprise. Le contenu du processus de production a un impact décisif sur la construction de l'entreprise et de ses unités de production.
La partie principale du processus de production est le processus technologique. Au cours de la mise en œuvre du processus technologique, les formes géométriques, les tailles et les propriétés physiques et chimiques des objets de travail changent.
Selon leur importance et leur rôle dans la production, les processus de production sont divisés en : principaux, auxiliaires et de service.
Les principaux sont appelés processus de production, au cours desquels la production des principaux produits fabriqués par l'entreprise est réalisée.
Les processus auxiliaires comprennent les processus qui assurent le flux ininterrompu des processus principaux. Leur résultat est les produits utilisés dans l'entreprise elle-même. Auxiliaires sont les processus de réparation d'équipements, de fabrication d'équipements, de génération de vapeur, d'air comprimé, etc.
Les processus de service sont appelés ceux, au cours de la mise en œuvre desquels les services nécessaires au fonctionnement normal des processus principaux et auxiliaires sont exécutés. Ce sont les processus de transport, d'entreposage, de cueillette de pièces, de nettoyage des salles, etc.
Le processus de production comprend de nombreuses opérations différentes, qui sont respectivement divisées en opérations principales (technologiques) et auxiliaires.
Une opération technologique est une partie du processus de production effectuée sur un lieu de travail sur un objet de production (pièce, assemblage, produit) par un ou plusieurs travailleurs.
Selon le type et la destination des produits, le degré d'équipement technique, les opérations sont classées en manuel, machine-manuel, machine et matériel.
Les opérations manuelles sont effectuées manuellement à l'aide d'outils simples (parfois mécanisés), tels que la peinture manuelle, l'assemblage, l'emballage des produits, etc.
Les opérations manuelles à la machine sont effectuées à l'aide de machines et de mécanismes avec la participation obligatoire d'un travailleur, par exemple le transport de marchandises sur des voitures électriques, le traitement de pièces sur des machines-outils avec classement manuel.
Les opérations de la machine sont entièrement effectuées par la machine avec une participation minimale des travailleurs au processus technologique, par exemple, installer des pièces dans la zone d'usinage et les retirer une fois le traitement terminé, surveiller le fonctionnement des machines, c'est-à-dire les travailleurs ne participent pas aux opérations technologiques, mais les contrôlent seulement.
Les opérations matérielles ont lieu dans des unités spéciales (cuves, bains, fours, etc.). Le travailleur surveille l'état de fonctionnement de l'équipement et des lectures d'instruments et, au besoin, apporte des ajustements aux modes de fonctionnement des unités conformément aux exigences de la technologie. Les opérations de quincaillerie sont répandues dans les industries alimentaires, chimiques, métallurgiques et autres.
L'organisation du processus de production consiste à combiner les personnes, les outils et les objets de travail en un seul processus de production de biens matériels, ainsi qu'à assurer une combinaison rationnelle dans l'espace et dans le temps des processus principaux, auxiliaires et de service.
L'efficacité économique de l'organisation rationnelle du processus de production s'exprime dans la réduction de la durée du cycle de production des produits, dans la réduction des coûts de production, dans l'amélioration de l'utilisation des immobilisations et dans l'augmentation de la rotation du fonds de roulement.
Le type de production est déterminé par une caractéristique complexe de facteurs techniques, organisationnels et caractéristiques économiques production, en raison de l'étendue de la nomenclature, de la régularité, de la stabilité et du volume de la production. Le principal indicateur caractérisant le type de production est le coefficient de consolidation des opérations Kz. Le coefficient de consolidation des opérations pour un groupe d'emplois est défini comme le rapport du nombre d'opérations technologiques toutes différentes effectuées ou à effectuer au cours du mois sur le nombre d'emplois :
Kz = | à op | ||||
Kr. M. |
|||||
où Kopi est le nombre d'opérations effectuées sur i-ème travailleur place; Kr.m - le nombre d'emplois sur le site ou dans le magasin.
Il existe trois types de production : unique, en série, en masse.
La production unique se caractérise par un petit volume de production de produits identiques, dont la refabrication et la réparation ne sont généralement pas fournies. Le taux d'épinglage pour une seule production est généralement supérieur à 40.
La production en série se caractérise par la fabrication ou la réparation de produits en lots périodiquement répétés. En fonction du nombre de produits d'un lot ou d'une série et de la valeur du coefficient de consolidation des opérations, on distingue la production à petite, moyenne et grande échelle.
Pour la production à petite échelle, le coefficient de consolidation des opérations est de 21 à 40 (inclus), pour la production à moyenne échelle - de 11 à 20 (inclus), pour la production à grande échelle - de 1 à 10 (inclus).
La production de masse se caractérise par un grand volume de production de produits qui sont fabriqués ou réparés en continu pendant une longue période, au cours de laquelle la plupart des lieux de travail effectuent une opération de travail. Le coefficient des opérations de fixage pour la production de masse est supposé égal à 1.
Considérez les caractéristiques techniques et économiques de chaque type de production.
La production unique et à petite échelle qui lui est proche se caractérise par la fabrication de pièces d'une large gamme sur des lieux de travail qui n'ont pas de spécialisation spécifique. Cette production doit être suffisamment flexible et adaptée à l'exécution des différents ordres de fabrication.
Les processus technologiques dans les conditions de la production unitaire sont développés sur une base élargie sous forme de feuilles de route pour le traitement des pièces pour chaque commande; Les sections sont équipées d'équipements et d'outillages universels, ce qui assure la fabrication d'une large gamme de pièces. La grande variété d'emplois que de nombreux travailleurs doivent accomplir exige qu'ils aient des compétences professionnelles différentes, de sorte que des travailleurs généraux hautement qualifiés sont utilisés dans les opérations. Dans de nombreux domaines, en particulier dans la production pilote, une combinaison de professions est pratiquée.
L'organisation de la production dans les conditions de la production unitaire a ses propres caractéristiques. En raison de la variété des pièces, de l'ordre et des méthodes de traitement, les sites de production sont construits selon le principe technologique avec la disposition des équipements en groupes homogènes. Avec cette organisation de la production, les pièces du processus de fabrication passent par différentes sections. Par conséquent, lors de leur transfert vers chaque opération ultérieure (section), il est nécessaire d'examiner attentivement les problèmes de contrôle de la qualité du traitement, du transport et de la détermination des tâches pour l'opération suivante. Les caractéristiques de la planification et de la gestion opérationnelles sont la sélection et l'exécution en temps opportun des commandes, le suivi de la progression de chaque détail des opérations,
assurer le chargement systématique des chantiers et des travaux. De grandes difficultés surgissent dans l'organisation de l'approvisionnement matériel et technique. Une large gamme de produits manufacturés, l'utilisation de taux de consommation élargis de matériaux créent des difficultés d'approvisionnement ininterrompu, c'est pourquoi les entreprises accumulent d'importants stocks de matériaux, ce qui, à son tour, conduit à l'amortissement du fonds de roulement.
Les caractéristiques de l'organisation de la production unitaire affectent les performances économiques. Pour les entreprises à prédominance d'un seul type de production, une intensité de main-d'œuvre relativement élevée des produits et un volume important de travaux en cours en raison des longues périodes de stockage des pièces entre les opérations sont typiques. La structure des coûts des produits se caractérise par une part élevée des coûts salariaux. Cette part est généralement de 20 à 25 %.
Les principales possibilités d'amélioration des indicateurs techniques et économiques d'une seule production sont associées à son rapprochement en termes de niveau technique et organisationnel du niveau de série. L'utilisation de méthodes de production en série est possible avec un rétrécissement de la gamme de pièces fabriquées pour les applications générales de construction mécanique, unification des pièces et des assemblages, ce qui permet de procéder à l'organisation des domaines; expansion de la continuité constructive pour augmenter les lots de pièces de lancement ; regrouper des pièces similaires dans leur conception et leur fabrication afin de réduire le temps de préparation de la production et d'améliorer l'utilisation des équipements.
La production en série se caractérise par la production d'une gamme limitée de pièces par lots, répétés à intervalles réguliers. Cela vous permet d'utiliser avec l'équipement spécial universel. Lors de la conception des processus technologiques, ils prévoient l'ordre d'exécution et l'équipement pour chaque opération.
Les caractéristiques suivantes sont typiques pour l'organisation de la production en série. Les magasins, en règle générale, ont dans leur composition des zones fermées, des équipements sur lesquels sont placés au cours d'un processus technologique typique. En conséquence, des connexions relativement simples entre les lieux de travail apparaissent et des conditions préalables sont créées pour organiser le mouvement direct des pièces au cours de leur fabrication.
La spécialisation thématique des sections rend opportun de traiter un lot de pièces en parallèle sur plusieurs machines qui effectuent des opérations successives. Dès que l'opération précédente a fini de traiter les premières pièces, elles sont transférées à l'opération suivante avant la fin du traitement de l'ensemble du lot. Ainsi, dans les conditions de la production de masse, il devient possible d'organiser le processus de production en parallèle et séquentiellement. C'est sa particularité.
L'utilisation de l'une ou l'autre forme d'organisation dans les conditions de la production de masse dépend de l'intensité de travail et du volume de production des produits affectés au site. Ainsi, les grandes pièces à forte intensité de main-d'œuvre fabriquées en
en grand nombre et ayant un processus technologique similaire, ils sont affectés à un site avec l'organisation d'une production à flux variable sur celui-ci. Les pièces de taille moyenne, multi-opérationnelles et à faible intensité de main-d'œuvre sont combinées par lots. Si leur mise en production se répète régulièrement, des zones de traitement par lots sont organisées. Les petites pièces à faible main-d'œuvre, telles que les goujons normalisés, les boulons, sont fixées à une section spécialisée. Dans ce cas, l'organisation d'une production en flux direct est possible.
Les entreprises de production en série se caractérisent par une intensité de main-d'œuvre et un coût de fabrication des produits nettement inférieurs à ceux d'une seule. Dans la production en série, par rapport à la production à la pièce, les produits sont traités avec moins d'interruptions, ce qui réduit le volume de travail en cours.
Du point de vue de l'organisation, la principale réserve pour augmenter la productivité du travail dans la production de masse est l'introduction de méthodes de production de masse.
La production de masse est la plus spécialisée et se caractérise par la production d'une gamme limitée de pièces en grande quantité. Les ateliers de production en série sont équipés des équipements les plus avancés, ce qui permet une automatisation quasi complète de la fabrication des pièces. Les lignes de production automatiques sont largement utilisées ici.
Les processus technologiques d'usinage sont développés plus soigneusement, par transitions. Chaque machine se voit attribuer un nombre relativement restreint d'opérations, ce qui garantit le chargement le plus complet des travaux. L'équipement est situé dans une chaîne le long du processus technologique des pièces individuelles. Les travailleurs se spécialisent dans l'exécution d'une ou deux opérations. Les détails sont transférés d'une opération à l'autre pièce par pièce. Dans les conditions de la production de masse, l'importance d'organiser le transport inter-opérationnel et l'entretien des lieux de travail augmente. La surveillance constante de l'état de l'outil de coupe, des outillages, des équipements est l'une des conditions pour assurer la continuité du processus de production, sans quoi le rythme de travail sur les chantiers et dans les ateliers est inévitablement perturbé. La nécessité de maintenir un rythme donné à toutes les étapes de la production devient un trait distinctif de l'organisation des processus dans la production de masse.
La production de masse offre l'utilisation la plus complète de l'équipement, un niveau global élevé de productivité du travail et le coût de fabrication des produits le plus bas. En tableau. 1.1 présente des données sur les caractéristiques comparatives de divers types de production.
Tableau 1.1 Caractéristiques comparatives des différents types de production
Par rapport | Type de fabrication | |||||||
panneaux | singulier | en série | massif |
|||||
Nomenclature | illimité | limité |
||||||
volume de sortie | nomenclature | nomenclature | nomenclature |
|||||
fabriqué selon | fabriqué | fabriqué en |
||||||
des soirées | ||||||||
quantités |
||||||||
Répétabilité | disparu | périodique | constant |
|||||
Applicabilité | universel | en partie spécial | la plupart |
|||||
équipement | spécial |
|||||||
Ancrage | disparu | limité | un deux | opérations |
||||
opérations | opération-détail | sur la machine | ||||||
Machines | ||||||||
Emplacement | ||||||||
équipement | machines homogènes | En traitement | technologique |
|||||
de manière constructive | traiter | En traitement |
||||||
technologiquement | ||||||||
parties homogènes | ||||||||
Transfert d'articles | cohérent | parallèle | parallèle |
|||||
travail d'exploitation | parallèle | |||||||
pour la chirurgie | ||||||||
Forme d'organisation | technologique | matière | rectiligne |
|||||
production | ||||||||
traiter |
1.4. Organisation du processus de fabrication
dans l'espace et le temps
La construction d'une structure de production rationnelle de l'entreprise s'effectue dans l'ordre suivant:
- la composition des ateliers de l'entreprise, leur capacité en tailles assurant une production donnée de produits sont établies ;
- les surfaces de chaque atelier et entrepôt sont calculées, leurs aménagements spatiaux sont déterminés dans le plan directeur de l'entreprise;
- toutes les liaisons de transport au sein de l'entreprise sont planifiées, leur interaction avec les itinéraires nationaux (externes à l'entreprise);
- les itinéraires les plus courts de déplacement inter-ateliers des objets de travail au cours du processus de production sont esquissés.
Les unités de production comprennent des ateliers, des sections, des laboratoires dans lesquels les principaux produits (fabriqués par l'entreprise), composants (achetés à l'extérieur), matériaux et
produits semi-finis, pièces de rechange pour l'entretien et la réparation des produits pendant le fonctionnement ; divers types d'énergie sont produits à des fins technologiques, etc.
À les subdivisions au service des salariés comprennent les logements et les services communaux, leurs services, usines de cuisine, cantines, cantines, jardins d'enfants et crèches, sanatoriums, pensions, maisons de repos, dispensaires, unités médicales, sociétés sportives volontaires, départements de formation technique et établissements d'enseignement impliqués dans l'amélioration des compétences de production, le niveau culturel des travailleurs, des ingénieurs et des techniciens , des employés.
La principale unité de production structurelle d'une entreprise (à l'exception des entreprises dont la structure de gestion n'est pas un magasin) est un atelier - un lien administrativement séparé qui exécute une certaine partie du processus de production global (étape de production).
Les ateliers sont des subdivisions à part entière, ils exercent leurs activités selon les principes de la comptabilité analytique. En génie mécanique, les ateliers sont généralement divisés en quatre groupes : principal, auxiliaire, secondaire et auxiliaire. Dans les ateliers principaux sont réalisées les opérations de fabrication des produits destinés à la vente. Les principaux ateliers sont répartis entre l'approvisionnement, la transformation et l'assemblage.
À les ébauches comprennent les fonderies, forgeage et emboutissage, forgeage et emboutissage, parfois ateliers de structures soudées ; au traitement
- usinage, travail du bois, thermique, galvanoplastie, revêtements protecteurs et décoratifs de pièces, ateliers d'assemblage - assemblage global et final de produits, leur peinture, complétant avec des pièces de rechange et des équipements amovibles.
Ateliers auxiliaires - outillage, matériel hors normes, maquette, réparation, énergie, transport.
Sous-produits - magasins de recyclage et de traitement des déchets métalliques par moulage et pressage de copeaux en briquettes, magasins de biens de consommation. Auxiliaires - ateliers qui fabriquent des conteneurs pour l'emballage des produits, du bois scié, effectuent la conservation des produits, leur emballage, leur chargement et leur expédition au consommateur.
En plus de ces ateliers, presque toutes les usines de construction de machines disposent d'ateliers de production, de services et de services desservant des installations non industrielles (municipales, culturelles et ménagères, logements, etc.).
Une certaine place dans la structure de toutes les usines de construction de machines est occupée par l'entreposage, les installations sanitaires et les communications (réseaux électriques, gazoducs et gazoducs, chauffage, ventilation, voies ferrées et voies de transport sans voies bien entretenues, etc.).
Un rôle particulier dans la structure de production de l'association (entreprise) est joué par la conception, les divisions technologiques,
instituts et laboratoires de recherche. Ils développent des dessins, des processus technologiques, effectuent des travaux expérimentaux, mettent les conceptions de produits en pleine conformité avec les exigences de GOST, Caractéristiques, des travaux de conception expérimentale et expérimentale sont en cours. Dans ces subdivisions, l'intégration de la science à la production se manifeste avec une force particulière.
Les ateliers comprennent des sites de production principaux et auxiliaires.
Les principaux sites de production sont créés selon le principe technologique ou thématique. Dans les domaines organisés selon le principe de spécialisation technologique, des opérations technologiques d'un certain type sont effectuées. Dans une fonderie, par exemple, des sections peuvent être organisées dans les domaines technologiques suivants : préparation du terrain, production de barres, moules de coulée, traitement des pièces moulées finies, etc., dans un atelier de forgeage - sections pour la fabrication d'ébauches forgées sur marteaux et presses, traitement thermique, etc., dans les sections mécaniques - tournage, tourelle, fraisage, meulage, serrurerie et autres, dans l'assemblage - sections de l'assemblage nodal et final des produits, test de leurs pièces et systèmes, station de contrôle et de test, peinture , etc.
Dans les domaines organisés selon le principe de la spécialisation des sujets, ce ne sont pas des types d'opérations individuels qui sont effectués, mais des processus technologiques dans leur ensemble, en conséquence, des produits finis pour ce domaine sont obtenus.
Les auxiliaires comprennent les sections du chef mécanicien et du chef mécanicien pour la réparation et l'entretien courants des équipements d'usinage et de puissance ; un garde-manger d'outillage et de distribution avec un atelier de meulage, un service de transport, un atelier de réparation et d'entretien d'équipements technologiques, etc.
Avec un système centralisé d'organisation des services et réparation en coursà l'entreprise, les sections auxiliaires dans les magasins ne sont pas créées.
Les ateliers et sections auxiliaires sont organisés selon les mêmes critères que les ateliers et sections de la production principale.
L'appel constant des dirigeants de l'entreprise aux facteurs environnementaux permet de modifier la structure de gestion en temps opportun afin de contribuer à la stabilité de l'entreprise et à sa réponse flexible aux fluctuations du marché dans l'environnement du marché. C'est pourquoi l'organisation de la gestion de la production (facteurs territoriaux, transports, ressources, technologiques et autres) doit être considérée comme un système d'actions qui guide le développement d'une entreprise.
La structure de production est influencée par un certain nombre de facteurs :
Affiliation industrielle de l'entreprise - la gamme de produits, ses caractéristiques de conception, les matériaux utilisés, les méthodes d'obtention et de traitement des ébauches; simplicité de conception et fabricabilité du produit; le niveau d'exigences en matière de qualité des produits ; type de production, niveau de sa spécialisation et coopération;
composition des équipements et équipements technologiques (équipements universels, spéciaux, hors-normes, lignes de convoyage ou automatiques) :
- organisation centralisée ou décentralisée de la maintenance des équipements, de leur réparation courante et des équipements technologiques ;
- la capacité de la production à se réorganiser rapidement et sans pertes importantes pour produire de nouveaux produits dans une gamme de produits modifiée ;
- la nature du processus de production dans les ateliers principaux, auxiliaires, secondaires et auxiliaires.
La structure de production d'une entreprise dans diverses industries a ses propres caractéristiques découlant de la nature de la production principale.
Dans les usines textiles, dans la plupart des cas, une structure technologique fonctionne avec la spécialisation simultanée de sections individuelles pour certains numéros de fils et articles bruts. Le plus grand nombre d'usines a toutes les étapes de la production de tissus : filature, tissage, finition. Certaines usines se spécialisent en une ou deux étapes.
Dans les usines métallurgiques, la structure technologique prévaut. Des ateliers pilotes, de hauts fourneaux, d'aciérie et de laminage sont en cours d'installation.
Général dans la structure de production des entreprises de diverses industries
- organisation de fermes auxiliaires et de service. Les ateliers du chef ingénieur en énergie et du chef mécanicien, les installations de transport et de stockage sont disponibles dans l'entreprise de n'importe quelle industrie. À l'usine de construction de machines, il y a toujours un atelier d'outillage, à l'usine textile, il y a des ateliers d'abattage et de navette qui fabriquent des outils pour la production textile.
La question du choix et de l'amélioration de la structure de production d'une entreprise (association) doit être abordée à la fois dans la construction de nouvelles entreprises et dans la reconstruction d'entreprises existantes.
Les principaux moyens d'améliorer la structure de production:
- agrandissement d'entreprises et d'ateliers;
- recherche et mise en œuvre d'un principe plus parfait de construction d'ateliers
et entreprises manufacturières;
- respect d'un rapport rationnel entre les magasins principaux, auxiliaires et de service;
- travail constant de rationalisation de la planification des entreprises ;
- l'intégration d'entreprises individuelles, la création de puissants pôles industriels et les associations de recherche et de production basées sur la concentration de la production ;
- assurer la proportionnalité entre toutes les parties de l'entreprise;
- modification du profil de production, c'est-à-dire nature de la production, spécialisation et coopération; développement de la production combinée; réalisation homogénéité constructive et technologique
produits en raison d'une large unification et normalisation; création d'une structure de gestion d'entreprise hors atelier. L'agrandissement des entreprises et des ateliers permet d'introduire à plus grande échelle de nouvelles machines performantes, d'améliorer constamment la technologie et d'améliorer l'organisation de la production.
L'identification et la mise en place de réserves d'amélioration de la structure des ateliers et des sites de production sont des facteurs d'amélioration continue de la structure de production, augmentant l'efficacité de la production.
Le respect d'un rapport rationnel entre les ateliers et sites principaux, auxiliaires et de service doit viser à accroître gravité spécifique principaux ateliers par le nombre d'ouvriers employés, le coût des immobilisations, la taille des surfaces occupées.
La rationalisation de la planification implique l'amélioration du schéma directeur de l'entreprise.
La qualité de l'utilisation des opportunités disponibles, des ressources et d'un environnement de marché favorable est associée dans l'entreprise au mécanisme de planification de la production. Construire un plan optimal du point de vue d'un éventuel changement de la situation du marché est la clé de la mise en œuvre de la stabilité interne de l'entreprise dans l'environnement économique externe. C'est pourquoi vous devez faire attention Attention particulière pour le matériel de planification de la production.
Le plan directeur est l'une des parties les plus importantes du projet d'une entreprise industrielle, contenant une solution globale aux problèmes de planification et d'aménagement paysager, de placement des bâtiments, des structures, des communications de transport, des réseaux d'ingénierie, de l'organisation des systèmes de services aux ménages et aux consommateurs, ainsi que la localisation de l'entreprise dans une zone industrielle (nœud).
Le schéma directeur est soumis à des exigences élevées dont les principales sont :
1) la localisation des unités de production strictement au cours du processus technologique - entrepôts de matières premières, matériaux et produits semi-finis, approvisionnement, transformation, ateliers d'assemblage, entrepôts de produits finis;
2) placement de sites annexes, fermes à proximité des principaux ateliers de production qu'ils desservent ;
3) disposition rationnelle des voies ferrées au sein de l'entreprise. Ils doivent être reliés à la fois aux locaux des entrepôts de matières premières, matériaux et produits semi-finis, et à l'entrepôt de produits finis, où les produits sont complétés par des équipements amovibles, des pièces de rechange, la conservation, l'emballage, le bouchage, le chargement, l'envoi des produits au consommateur ;
4) la plus grande rectitude et les voies de transport les plus courtes des matières premières, des matériaux, des produits semi-finis et des produits finis ;
5) exclusion des flux de compteur et de retour tant à l'intérieur qu'à l'extérieur ;
6) les options les plus rapides pour localiser les communications externes de l'entreprise et les connecter aux réseaux d'ingénierie, aux autoroutes, aux chemins de fer, etc.
7) placement dans des blocs d'ateliers de laboratoires (mesure, chimie, contrôle par rayons X, ultrasons, etc.), les desservant, ainsi que des ateliers de traitement thermique et de revêtements protecteurs de pièces, produits finis.
Dans les grandes entreprises, il est conseillé de combiner les ateliers dans les bâtiments. Lors de la conception des entreprises, il faut veiller
compacité du bâtiment. Selon la nature du produit, il caractéristiques de conception si possible, construisez des bâtiments à plusieurs étages. Choisir des distances rationnelles entre les magasins, les blocs de magasins et les bâtiments, en respectant les conditions sanitaires et techniques, les exigences de sécurité et de sécurité incendie.
Le plan directeur doit également prévoir la possibilité d'un développement ultérieur de l'entreprise et fournir une telle structure industrielle dans laquelle les résultats de production les plus élevés peuvent être atteints au moindre coût; créer les conditions d'une satisfaction maximale des intérêts de tous les employés de l'entreprise.
Placement des ateliers principaux, auxiliaires, secondaires et auxiliaires
et les sites desservant les exploitations agricoles, les administrations, les voies de transport sur le territoire de l'entreprise ont un impact énorme sur l'organisation de la production, son économie ;
détermine le sens des flux de marchandises, la longueur des voies ferrées
et pistes sans rail, ainsi que l'efficacité de l'utilisation des zones de production.
La compacité du bâtiment, sa densité rationnelle et son nombre d'étages permettent d'économiser investissements en capital réduire le volume des travaux de construction et du transport intra-usine, réduire la durée des communications, raccourcir la durée du cycle de production, introduire une mécanisation et une automatisation complètes de la production et des processus auxiliaires à plus grande échelle, réduire le temps passé par les produits finis dans le entrepôt, augmenter la productivité du travail, améliorer la qualité des produits, réduire le prix de revient.
La tâche des employés des instituts de conception, des ingénieurs et des techniciens et des ouvriers de production entreprises industrielles- l'amélioration continue de la structure de production, de la localisation des ateliers et des sites de production. Une attention particulièrement sérieuse à cette question doit être accordée pendant la période de reconstruction, de rééquipement technique, d'expansion de l'entreprise et de nouvelle construction. L'amélioration du schéma directeur de l'usine est une manifestation du souci d'augmenter l'efficacité de la production, d'améliorer la qualité des produits et les conditions de travail.
L'analyse des informations sur la dynamique du soutien interne de la production de l'entreprise et la demande de ses produits sur le marché est une condition pour une évaluation qualitative de sa durabilité. Dans le même temps, prêter attention au maintien de la production dans l'entreprise peut révéler les facteurs de capacité ou d'incapacité de l'entreprise et de développement durable à l'avenir. Dans le même temps, le mécanisme d'une telle analyse peut être la fixation de la relation entre les propriétés du service et les objectifs d'assurer les caractéristiques générales du service de production dans l'entreprise.
La forme d'organisation de la production est une certaine combinaison dans le temps et dans l'espace des éléments du processus de production avec un niveau approprié de son intégration, exprimée par un système de relations stables.
Diverses constructions structurelles temporelles et spatiales forment un ensemble de formes fondamentales d'organisation de la production. La structure temporaire de l'organisation de la production est déterminée par la composition des éléments du processus de production et l'ordre de leur interaction dans le temps. Selon le type de structure temporaire, on distingue les formes d'organisation avec transfert séquentiel, parallèle et parallèle-séquentiel des objets de travail dans la production.
La forme d'organisation de la production avec le transfert séquentiel des objets de travail est une telle combinaison d'éléments du processus de production, qui assure le mouvement des produits transformés dans toutes les zones de production en lots de taille arbitraire. Les objets de travail pour chaque opération ultérieure ne sont transférés qu'après l'achèvement du traitement de l'ensemble du lot lors de l'opération précédente. Ce formulaire est le plus flexible par rapport aux changements qui surviennent dans le programme de production, vous permet d'utiliser pleinement l'équipement, ce qui permet de réduire le coût de son achat. L'inconvénient de cette forme d'organisation de la production réside dans la durée relativement longue du cycle de production, puisque chaque pièce, avant d'effectuer l'opération suivante, se trouve en anticipation du traitement de l'ensemble du lot.
La forme d'organisation de la production avec le transfert parallèle d'objets de travail est basée sur une telle combinaison d'éléments du processus de production qui vous permet de démarrer, de traiter et de transférer des objets de travail d'une opération à l'autre et sans attendre. Cette organisation du processus de production conduit à une réduction du nombre de pièces à traiter, à une réduction de l'espace requis pour les entrepôts et les allées. Son inconvénient est le temps d'arrêt possible des équipements (emplois) en raison des différences de durée des opérations.
La forme d'organisation de la production avec transfert parallèle-séquentiel des objets de travail est intermédiaire entre
formes en série et en parallèle et élimine partiellement leurs inconvénients inhérents. Les produits d'une opération à l'autre sont transférés par les transporteurs. Cela garantit la continuité de l'utilisation des équipements et de la main-d'œuvre, il est possible de paralléliser partiellement le passage d'un lot de pièces à travers les opérations du processus technologique.
La structure spatiale de l'organisation de la production est déterminée par la quantité d'équipements technologiques concentrés sur le chantier (le nombre d'emplois) et sa localisation par rapport au sens de déplacement des objets de travail dans l'espace environnant. En fonction du nombre d'équipements technologiques (emplois), on distingue un système de production à un seul lien et la structure correspondante d'un lieu de travail séparé et un système à plusieurs liens avec un atelier, une structure linéaire ou cellulaire. Les options possibles pour la structure spatiale de l'organisation de la production sont présentées dans la fig. 1.2. La structure de l'atelier se caractérise par la création de sites où les équipements (emplois) sont implantés parallèlement au flux des pièces, ce qui implique leur spécialisation sur la base de l'homogénéité technologique. Dans ce cas, un lot de pièces arrivant sur le site est envoyé vers l'un des postes de travail libres, où se déroule le cycle de traitement nécessaire, après quoi il est transféré vers un autre site (vers l'atelier).
Riz. 1.2. Variantes de la structure spatiale du processus de production
Sur un site à structure spatiale linéaire, des équipements (emplois) sont localisés au cours du processus technologique et un lot de pièces traitées sur le site est transféré d'un emploi à un autre de manière séquentielle.
La structure cellulaire de l'organisation de la production combine les caractéristiques d'un linéaire et d'un atelier. La combinaison des structures spatiales et temporelles du processus de production à un certain niveau d'intégration des processus partiels détermine diverses formes d'organisation de la production: technologique, sujet, flux direct, ponctuel, intégré (Fig. 1.3). Considérez les caractéristiques de chacun d'eux.
Riz. 1.3. Formes d'organisation de la production
La forme technologique de l'organisation du processus de production se caractérise par une structure d'atelier avec un transfert cohérent d'objets de travail. Cette forme d'organisation est largement répandue dans les usines de fabrication de machines, car elle assure une utilisation maximale des équipements dans la production à petite échelle et est adaptée aux changements fréquents du processus technologique. Dans le même temps, l'utilisation d'une forme technologique d'organisation du processus de production a un certain nombre de conséquences négatives. Un grand nombre de pièces et leurs mouvements répétés lors du traitement entraînent une augmentation du volume d'encours et une augmentation du nombre de points de stockage intermédiaires. Une partie importante du cycle de production est la perte de temps due à une communication intersectionnelle complexe.
La forme sujet de l'organisation de la production a une structure cellulaire avec un transfert parallèle-séquentiel (séquentiel) d'objets de travail dans la production. Sur le sujet, en règle générale, tous les équipements nécessaires au traitement d'un groupe de pièces du début à la fin du processus technologique sont installés. Si le cycle de traitement technologique est fermé dans le domaine, il est dit sujet-fermé.
La construction en objet des profilés assure la rectitude et réduit la durée du cycle de production pour la fabrication des pièces. En comparaison avec la forme technologique, le sujet permet de réduire le coût total de transport des pièces, le besoin d'espace de production par unité de production. Cependant, cette forme d'organisation de la production présente également des inconvénients. Le principal est que lors de la détermination de la composition de l'équipement installé sur le site, la nécessité de certains types de traitement de pièces est mise en évidence, ce qui ne fournit pas toujours une charge complète de l'équipement.
De plus, l'élargissement de la gamme de produits fabriqués, son renouvellement nécessitent des réaménagements périodiques des sites de production, des modifications de la structure du parc matériel. La forme d'organisation de la production en flux direct se caractérise par une structure linéaire avec un transfert pièce par pièce des objets de travail. Cette forme assure la mise en œuvre d'un certain nombre de principes d'organisation : spécialisation, flux direct, continuité, parallélisme. Son application entraîne une réduction de la durée du cycle de production, une utilisation plus efficace de la main-d'œuvre grâce à une plus grande spécialisation de la main-d'œuvre et une diminution du volume des travaux en cours.
Avec une forme ponctuelle d'organisation de la production, le travail est entièrement effectué sur un seul lieu de travail. Le produit est fabriqué là où se trouve sa partie principale. Un exemple est l'assemblage d'un produit avec le travailleur qui se déplace autour de lui. L'organisation de la production ponctuelle présente de nombreux avantages: elle offre la possibilité de changements fréquents dans la conception des produits et la séquence de traitement, la fabrication de produits de différentes nomenclatures dans la quantité déterminée par les besoins de production; les coûts associés au changement d'emplacement des équipements sont réduits, la flexibilité de la production est accrue.
Une forme intégrée d'organisation de la production implique la combinaison d'opérations principales et auxiliaires en un seul processus de production intégré à structure cellulaire ou linéaire avec transfert séquentiel, parallèle ou parallèle-séquentiel d'objets de travail dans la production. Contrairement à la pratique existante de conception séparée des processus d'entreposage, de transport, de gestion, de traitement dans des zones à forme d'organisation intégrée, il est nécessaire de lier ces processus partiels en un seul processus de production. Ceci est réalisé en combinant tous les emplois à l'aide d'un complexe de transport et de stockage automatique, qui est un ensemble de dispositifs interconnectés, automatiques et de stockage, d'équipements informatiques conçus pour organiser le stockage et le mouvement des objets de travail entre les différents emplois.
La gestion du processus de production est ici réalisée à l'aide d'un ordinateur, qui assure le fonctionnement de tous les éléments du processus de production sur le site selon le schéma suivant : recherche
la pièce nécessaire dans l'entrepôt - transport de la pièce à la machine - traitement - retour de la pièce à l'entrepôt. Pour compenser les écarts de temps lors du transport et du traitement des pièces, des entrepôts tampons de réserves inter-opérationnelles et d'assurance sont créés sur les lieux de travail individuels. La création de sites de production intégrés est associée à des coûts ponctuels relativement élevés causés par l'intégration et l'automatisation du processus de production.
L'effet économique de la transition vers une forme intégrée d'organisation de la production est obtenu en réduisant la durée du cycle de production pour la fabrication de pièces, en augmentant le temps de chargement des machines-outils et en améliorant la régulation et le contrôle des processus de production. Sur la fig. 1.4 montre la disposition des équipements dans des zones avec différentes formes d'organisation de la production.
Riz. 1.4. Agencements d'équipements (postes de travail) sur des sites avec différentes formes d'organisation de la production :
a) technologique ; b) sujet ; c) direct ; d) point (pour le cas du montage) ; e) intégré
Turovets O.G., Rodionov V.B., Bukhalkov M.I. Chapitre du livre "Organisation de la production et gestion d'entreprise"
Maison d'édition "INFRA-M", 2007
10.1. Le concept de processus de production
La production moderne est un processus complexe de conversion de matières premières, de matériaux, de produits semi-finis et d'autres objets de travail en produits finis qui répondent aux besoins de la société.
La totalité de toutes les actions des personnes et des outils effectuées dans l'entreprise pour la fabrication de types de produits spécifiques est appelée processus de production.
La partie principale du processus de production est constituée de processus technologiques qui contiennent des actions délibérées pour modifier et déterminer l'état des objets de travail. Au cours de la mise en œuvre des processus technologiques, les formes géométriques, les tailles et les propriétés physiques et chimiques des objets de travail changent.
Outre le processus de production technologique, il comprend également les processus non technologiques qui ne visent pas à modifier les formes géométriques, les tailles ou les propriétés physiques et chimiques des objets de travail ou à vérifier leur qualité. Ces processus comprennent le transport, le stockage, le chargement et le déchargement, la cueillette et certaines autres opérations et processus.
Dans le processus de production, les processus de travail sont combinés avec des processus naturels, dans lesquels le changement d'objets de travail se produit sous l'influence des forces de la nature sans intervention humaine (par exemple, séchage des pièces peintes à l'air, refroidissement des pièces moulées, vieillissement des pièces moulées , etc.).
Variétés de processus de production. Selon leur objectif et leur rôle dans la production, les processus sont divisés en principaux, auxiliaires et services.
Principal sont appelés processus de production au cours desquels s'effectue la fabrication des principaux produits fabriqués par l'entreprise. Le résultat des principaux processus de génie mécanique est la production de machines, d'appareils et d'instruments qui composent le programme de production de l'entreprise et correspondent à sa spécialisation, ainsi que la fabrication de pièces de rechange pour eux à livrer au consommateur.
À auxiliaire inclure des processus qui assurent le flux ininterrompu des processus de base. Leur résultat est les produits utilisés dans l'entreprise elle-même. Auxiliaires sont les processus de réparation d'équipements, de fabrication d'équipements, de génération de vapeur et d'air comprimé, etc.
portion les processus sont appelés, au cours de la mise en œuvre desquels les services nécessaires au fonctionnement normal des processus principaux et auxiliaires sont exécutés. Ceux-ci incluent, par exemple, les processus de transport, d'entreposage, de sélection et de prélèvement des pièces, etc.
Dans les conditions modernes, en particulier dans la production automatisée, il existe une tendance à intégrer les processus principaux et de service. Ainsi, dans des complexes automatisés flexibles, les opérations principales, de prélèvement, d'entreposage et de transport sont combinées en un seul processus.
L'ensemble des processus de base constitue la production principale. Dans les entreprises d'ingénierie, la production principale comprend trois étapes : l'approvisionnement, la transformation et l'assemblage. Organiser Le processus de production est un ensemble de processus et de travaux dont l'exécution caractérise l'achèvement d'une certaine partie du processus de production et est associée au passage de l'objet de travail d'un état qualitatif à un autre.
À approvisionnement les étapes comprennent les processus d'obtention des ébauches - matériaux de coupe, moulage, estampage. Traitement l'étape comprend les processus de conversion des flans en pièces finies A : Usinage, traitement thermique, peinture et galvanoplastie, etc. Assembléeétape - la dernière partie du processus de production. Il comprend l'assemblage des unités et des produits finis, le réglage et le débogage des machines et des instruments, ainsi que leurs tests.
La composition et les interconnexions des processus principaux, auxiliaires et de service forment la structure du processus de production.
En termes d'organisation, les processus de production sont divisés en simples et complexes. Simple sont appelés processus de production, consistant en des actions séquentiellement effectuées sur objet simple travail. Par exemple, le processus de production consistant à fabriquer une pièce unique ou un lot de pièces identiques. Difficile processus est une combinaison de processus simples effectués sur une variété d'objets de travail. Par exemple, le processus de fabrication d'une unité d'assemblage ou d'un produit complet.
10.2. Principes scientifiques d'organisation des processus de production
Activités d'organisation des processus de production. Les divers processus de production, qui aboutissent à la création de produits industriels, doivent être correctement organisés, en leur fournissant fonctionnement efficace afin de produire des types spécifiques de produits de haute qualité et en quantités qui répondent aux besoins de l'économie nationale et de la population du pays.
L'organisation des processus de production consiste à combiner les personnes, les outils et les objets de travail en un seul processus de production de biens matériels, ainsi qu'à assurer une combinaison rationnelle dans l'espace et dans le temps des processus principaux, auxiliaires et de service.
La combinaison spatiale des éléments du processus de production et de toutes ses variétés est mise en œuvre sur la base de la formation de la structure de production de l'entreprise et de ses unités constitutives. À cet égard, les activités les plus importantes sont le choix et la justification de la structure de production de l'entreprise, c'est-à-dire détermination de la composition et de la spécialisation de ses unités constitutives et établissement de relations rationnelles entre elles.
Lors du développement de la structure de production, des calculs de conception sont effectués pour déterminer la composition du parc d'équipements, en tenant compte de sa productivité, de son interchangeabilité et de la possibilité d'une utilisation efficace. La planification rationnelle des divisions, le placement des équipements, les emplois sont également en cours de développement. Des conditions organisationnelles sont créées pour le bon fonctionnement des équipements et des participants directs au processus de production - les travailleurs.
L'un des principaux aspects de la formation de la structure de production est d'assurer le fonctionnement interconnecté de tous les composants du processus de production: opérations préparatoires, processus de production de base, maintenance. Il est nécessaire de justifier de manière exhaustive les formes et méthodes d'organisation les plus rationnelles pour la mise en œuvre de certains processus pour des conditions de production et techniques spécifiques.
Un élément important dans l'organisation des processus de production est l'organisation du travail des travailleurs, qui réalise concrètement la combinaison de la force de travail avec les moyens de production. Les modes d'organisation du travail sont largement déterminés par les formes du processus de production. À cet égard, l'accent devrait être mis sur la garantie d'une division rationnelle du travail et la détermination sur cette base de la composition professionnelle et des qualifications des travailleurs, de l'organisation scientifique et de l'entretien optimal des lieux de travail, ainsi que de l'amélioration et de l'amélioration globales des conditions de travail.
L'organisation des processus de production implique également une combinaison de leurs éléments dans le temps, qui détermine un certain ordre pour effectuer les opérations individuelles, une combinaison rationnelle du temps pour effectuer divers types de travail et la détermination de normes de calendrier et de planification pour le mouvement des objets de travail. Le déroulement normal des processus dans le temps est également assuré par l'ordre de lancement-libération des produits, la création des stocks nécessaires (réserves) et des réserves de production, l'approvisionnement ininterrompu des lieux de travail en outils, ébauches, matériaux. Une direction importante de cette activité est l'organisation du mouvement rationnel des flux de matières. Ces tâches sont résolues sur la base du développement et de la mise en œuvre de systèmes de planification opérationnelle de la production, en tenant compte du type de production et des caractéristiques techniques et organisationnelles des processus de production.
Enfin, au cours de l'organisation des processus de production dans une entreprise, une place importante est accordée au développement d'un système d'interaction des unités de production individuelles.
Principes d'organisation du processus de production sont les points de départ sur la base desquels la construction, l'exploitation et le développement des processus de production sont réalisés.
Principe différenciation implique la division du processus de production en parties distinctes (processus, opérations) et leur affectation aux départements concernés de l'entreprise. Le principe de différenciation s'oppose au principe combinaisons, c'est-à-dire la combinaison de tout ou partie de procédés divers pour la fabrication de certains types de produits au sein d'un même site, atelier ou production. Selon la complexité du produit, le volume de production, la nature des équipements utilisés, le processus de production peut être concentré dans une seule unité de production (atelier, section) ou dispersé sur plusieurs unités. Ainsi, dans les entreprises de construction de machines, avec une production importante du même type de produits, une production mécanique et d'assemblage indépendante, des ateliers sont organisés et, avec de petits lots de produits manufacturés, des ateliers d'assemblage mécanique unifiés peuvent être créés.
Les principes de différenciation et de combinaison s'appliquent également aux emplois individuels. Une chaîne de production, par exemple, est un ensemble différencié d'emplois.
Dans les activités pratiques d'organisation de la production, la priorité dans l'utilisation des principes de différenciation ou de combinaison doit être donnée au principe qui fournira les meilleures caractéristiques économiques et sociales du processus de production. Ainsi, la production en ligne, qui se caractérise par un degré élevé de différenciation du processus de production, permet de simplifier son organisation, d'améliorer les compétences des travailleurs et d'augmenter la productivité du travail. Cependant, une différenciation excessive augmente la fatigue des travailleurs, un grand nombre d'opérations augmente le besoin d'équipement et d'espace de production, entraîne des coûts inutiles pour les pièces mobiles, etc.
Principe concentration signifie la concentration de certaines opérations de production pour la fabrication de produits technologiquement homogènes ou l'exécution d'un travail fonctionnellement homogène dans des lieux de travail, des sections, des ateliers ou des installations de production séparés de l'entreprise. L'opportunité de concentrer un travail homogène dans des zones de production distinctes est due aux facteurs suivants: la communauté des méthodes technologiques qui nécessitent l'utilisation du même type d'équipement; les capacités des équipements, tels que les centres d'usinage ; une augmentation de la production de certains types de produits; la faisabilité économique de concentrer la production de certains types de produits ou d'effectuer des travaux similaires.
Lors du choix de l'un ou l'autre sens de concentration, il est nécessaire de prendre en compte les avantages de chacun d'eux.
Avec la concentration de travaux technologiquement homogènes dans la subdivision, une plus petite quantité d'équipements de duplication est nécessaire, la flexibilité de la production augmente et il devient possible de passer rapidement à la production de nouveaux produits, et la charge sur l'équipement augmente.
Avec la concentration de produits technologiquement homogènes, les coûts de transport des matériaux et des produits sont réduits, la durée du cycle de production est réduite, la gestion du processus de production est simplifiée et le besoin d'espace de production est réduit.
Principe spécialisations basée sur la limitation de la variété des éléments du processus de production. La mise en œuvre de ce principe consiste à affecter à chaque lieu de travail et à chaque division une gamme strictement limitée de travaux, d'opérations, de pièces ou de produits. Contrairement au principe de spécialisation, le principe d'universalisation implique une telle organisation de la production, dans laquelle chaque lieu de travail ou unité de production est engagé dans la fabrication de pièces et de produits d'une large gamme ou dans l'exécution d'opérations de production hétérogènes.
Le niveau de spécialisation des emplois est déterminé par un indicateur spécial - le coefficient de consolidation des opérations À z.o, qui se caractérise par le nombre d'opérations de détail effectuées sur le lieu de travail pendant une certaine période de temps. Oui, à À z.o = 1 il existe une spécialisation étroite des lieux de travail, dans laquelle au cours du mois, du trimestre, une opération de détail est effectuée sur le lieu de travail.
La nature de la spécialisation des départements et des emplois est largement déterminée par le volume de production des pièces du même nom. Naï haut niveau la spécialisation se produit dans la production d'un type de produit. L'exemple le plus typique d'industries hautement spécialisées sont les usines de production de tracteurs, de téléviseurs, de voitures. Une augmentation de la gamme de production réduit le niveau de spécialisation.
Un degré élevé de spécialisation des départements et des lieux de travail contribue à la croissance de la productivité du travail en raison du développement des compétences professionnelles des travailleurs, de la possibilité d'équipement technique du travail, de la minimisation des coûts de reconfiguration des machines et des lignes. Dans le même temps, une spécialisation étroite réduit les qualifications requises des travailleurs, entraîne la monotonie du travail et, par conséquent, conduit à une fatigue rapide des travailleurs et limite leur initiative.
Dans les conditions modernes, la tendance à l'universalisation de la production augmente, ce qui est déterminé par les exigences du progrès scientifique et technologique pour élargir la gamme de produits, l'émergence d'équipements multifonctionnels et les tâches d'amélioration de l'organisation du travail dans le sens d'élargir les fonctions de travail du travailleur.
Principe proportionnalité consiste en une combinaison régulière d'éléments individuels du processus de production, qui s'exprime dans un certain rapport quantitatif entre eux. Ainsi, la proportionnalité en termes de capacité de production implique l'égalité des capacités des sections ou des facteurs de charge des équipements. Dans ce cas, le débit des ateliers d'approvisionnement correspond aux besoins en ébauches des ateliers d'usinage, et le débit de ces ateliers correspond aux besoins de l'atelier d'assemblage en pièces nécessaires. Cela implique l'exigence de disposer dans chaque atelier d'équipements, d'espace et de main-d'œuvre en quantité suffisante pour assurer le fonctionnement normal de tous les départements de l'entreprise. Le même rapport de débit doit exister entre la production principale, d'une part, et les unités auxiliaires et de service, d'autre part.
La violation du principe de proportionnalité entraîne des disproportions, l'apparition de goulots d'étranglement dans la production, à la suite desquels l'utilisation de l'équipement et de la main-d'œuvre se détériore, la durée du cycle de production augmente et l'arriéré augmente.
La proportionnalité dans la main-d'œuvre, l'espace, l'équipement est déjà établie lors de la conception de l'entreprise, puis affinée lors de l'élaboration des plans de production annuels en effectuant des calculs dits volumétriques - lors de la détermination des capacités, du nombre d'employés et du besoin de matériaux. Les proportions sont établies sur la base d'un système de normes et de normes qui déterminent le nombre de relations mutuelles entre les différents éléments du processus de production.
Le principe de proportionnalité implique l'exécution simultanée d'opérations individuelles ou de parties du processus de production. Il est basé sur la prémisse que les parties d'un processus de production démembré doivent être combinées dans le temps et exécutées simultanément.
Le processus de fabrication d'une machine consiste en un grand nombre d'opérations. Il est bien évident que les exécuter séquentiellement les uns après les autres entraînerait une augmentation de la durée du cycle de production. Par conséquent, les différentes parties du processus de fabrication du produit doivent être réalisées en parallèle.
Parallélisme atteint : lors de l'usinage d'une pièce sur une machine avec plusieurs outils ; traitement simultané différents détails un lot pour une opération donnée sur plusieurs postes de travail ; traitement simultané des mêmes pièces pour diverses opérations sur plusieurs postes de travail ; production simultanée de différentes parties du même produit sur différents lieux de travail. Le respect du principe de parallélisme entraîne une réduction de la durée du cycle de production et du temps passé sur les pièces, pour gagner du temps de travail.
En dessous de flux direct comprendre un tel principe d'organisation du processus de production, selon lequel toutes les étapes et opérations du processus de production sont effectuées dans des conditions le chemin le plus court sujet du travail depuis le début du processus jusqu'à sa fin. Le principe du flux direct nécessite de s'assurer mouvement rectiligne objets de travail dans le processus technologique, élimination de divers types de boucles et de mouvements de retour.
La directivité totale peut être obtenue par l'agencement spatial des opérations et des parties du processus de production dans l'ordre des opérations technologiques. Il est également nécessaire, lors de la conception des entreprises, de réaliser l'emplacement des ateliers et des services dans une séquence qui prévoit une distance minimale entre les unités adjacentes. Il convient de s'efforcer de garantir que les pièces et les unités d'assemblage de différents produits présentent la même séquence ou une séquence similaire d'étapes et d'opérations du processus de production. Lors de la mise en œuvre du principe de flux direct, se pose également le problème de l'agencement optimal des équipements et des travaux.
Le principe de flux direct se manifeste davantage dans les conditions de production en ligne, lors de la création d'ateliers et de sections à sujet fermé.
Le respect des exigences de flux direct entraîne une rationalisation des flux de fret, une réduction du chiffre d'affaires du fret et une réduction du coût de transport des matériaux, des pièces et des produits finis.
Principe rythme signifie que tous les processus de production distincts et un processus unique pour la production d'un certain type de produit sont répétés après des périodes de temps définies. Distinguer le rythme de sortie, de travail, de production.
Le rythme de libération est la libération d'une quantité identique ou uniformément croissante (décroissante) de produits pendant des intervalles de temps égaux. Le rythme de travail est l'exécution de quantités égales de travail (en quantité et en composition) pendant des intervalles de temps égaux. Le rythme de production signifie le respect du rythme de production et du rythme de travail.
Un travail rythmé sans à-coups ni tempêtes est la base d'une augmentation de la productivité du travail, d'une utilisation optimale des équipements, d'une utilisation complète du personnel et d'une garantie de production de haute qualité. Le bon fonctionnement de l'entreprise dépend d'un certain nombre de conditions. Assurer le rythme est une tâche complexe qui nécessite l'amélioration de toute l'organisation de la production de l'entreprise. L'organisation correcte de la planification opérationnelle de la production, le respect de la proportionnalité des capacités de production, l'amélioration de la structure de production, la bonne organisation de l'approvisionnement matériel et technique et la maintenance des processus de production sont d'une importance primordiale.
Principe continuité Il est réalisé dans de telles formes d'organisation du processus de production, dans lesquelles toutes ses opérations sont effectuées en continu, sans interruption, et tous les objets de travail se déplacent continuellement d'une opération à l'autre.
Le principe de la continuité du processus de production est pleinement mis en œuvre sur des lignes de production automatiques et continues, sur lesquelles des objets de travail sont fabriqués ou assemblés, ayant des opérations de même durée ou un multiple du temps de cycle de la ligne.
En génie mécanique, les processus technologiques discrets prédominent et, par conséquent, la production avec un degré élevé de synchronisation de la durée des opérations n'est pas prédominante ici.
Le mouvement discontinu des objets de travail est associé à des ruptures qui surviennent du fait du vieillissement des pièces à chaque opération, entre opérations, sections, ateliers. C'est pourquoi la mise en œuvre du principe de continuité nécessite l'élimination ou la minimisation des interruptions. La solution d'un tel problème peut être obtenue sur la base du respect des principes de proportionnalité et de rythme ; organisation de la production parallèle de pièces d'un lot ou de différentes pièces d'un même produit ; création de telles formes d'organisation des processus de production, dans lesquelles l'heure de début de fabrication des pièces pour une opération donnée et l'heure de fin de l'opération précédente sont synchronisées, etc.
La violation du principe de continuité, en règle générale, provoque des interruptions de travail (temps d'arrêt des travailleurs et des équipements), entraîne une augmentation de la durée du cycle de production et de la taille des travaux en cours.
Les principes d'organisation de la production dans la pratique ne fonctionnent pas isolément, ils sont étroitement liés dans chaque processus de production. Lors de l'étude des principes d'organisation, il convient de prêter attention à caractère de paire certains d'entre eux, leur interconnexion, la transition vers leur contraire (différenciation et combinaison, spécialisation et universalisation). Les principes d'organisation se développent inégalement : à une époque ou à une autre, tel principe passe au premier plan ou passe au second plan. Ainsi, la spécialisation étroite des emplois appartient au passé, ils deviennent de plus en plus universels. Le principe de différenciation est de plus en plus remplacé par le principe de combinaison, dont l'utilisation permet de construire un processus de production sur la base d'un flux unique. Dans le même temps, dans les conditions d'automatisation, l'importance des principes de proportionnalité, de continuité, de flux direct augmente.
Le degré de mise en œuvre des principes d'organisation de la production a une dimension quantitative. Par conséquent, en plus des méthodes d'analyse de la production existantes, des formulaires et des méthodes d'analyse de l'état de l'organisation de la production et de mise en œuvre de ses principes scientifiques devraient être développés et appliqués dans la pratique. Des méthodes de calcul du degré de mise en œuvre de certains principes d'organisation des processus de production seront données au chap. vingt.
Le respect des principes d'organisation des processus de production revêt une grande importance pratique. La mise en œuvre de ces principes est l'affaire de tous les niveaux de gestion de la production.
10.3. Organisation spatiale des processus de production
La structure de production de l'entreprise. La combinaison des parties du processus de production dans l'espace est assurée par la structure de production de l'entreprise. Par structure de production, on entend l'ensemble des unités de production de l'entreprise qui en font partie, ainsi que les formes de relations entre elles. Dans les conditions modernes, le processus de production peut être considéré dans ses deux variétés :
- en tant que processus de production matérielle avec le résultat final - des produits commercialisables ;
- comme un processus de production de conception avec le résultat final - un produit scientifique et technique.
La nature de la structure de production de l'entreprise dépend des types de ses activités, dont les principales sont les suivantes : recherche, production, recherche et production, production et technique, gestion et économie.
La priorité des activités concernées détermine la structure de l'entreprise, la part des unités scientifiques, techniques et de production, le rapport du nombre d'ouvriers et d'ingénieurs.
La composition des divisions d'une entreprise spécialisée dans les activités de production est déterminée par les caractéristiques de conception des produits fabriqués et la technologie de sa fabrication, l'échelle de production, la spécialisation de l'entreprise et les liens de coopération établis. Sur la fig. 10.1 montre un diagramme de la relation des facteurs qui déterminent la structure de production de l'entreprise.
Riz. 10.1. Schéma des interrelations des facteurs qui déterminent la structure de production d'une entreprise
Dans les conditions modernes, la forme de propriété a une grande influence sur la structure de l'entreprise. Le passage de l'État à d'autres formes de propriété - privée, par actions, bail - conduit, en règle générale, à réduire les liens et les structures superflus, la taille de l'appareil de contrôle et réduit la duplication du travail.
A l'heure actuelle, diverses formes d'organisation des entreprises se sont généralisées; il existe des petites, moyennes et grandes entreprises, la structure de production de chacune d'elles a les caractéristiques correspondantes.
La structure de production d'une petite entreprise est simple. En règle générale, il a un minimum ou pas du tout d'unités de production structurelles internes. Dans les petites entreprises, l'appareil administratif est insignifiant et la combinaison des fonctions de gestion est largement utilisée.
La structure des entreprises moyennes suppose l'affectation d'ateliers dans leur composition, et dans le cas d'une structure hors atelier, de sections. Ici, le minimum nécessaire pour assurer le fonctionnement de l'entreprise, ses propres unités auxiliaires et de service, départements et services de l'appareil de gestion est déjà en cours de création.
Les grandes entreprises de l'industrie manufacturière comprennent l'ensemble des départements de production, de service et de gestion.
Sur la base de la structure de production, un plan général de l'entreprise est élaboré. Le plan directeur fait référence à l'aménagement spatial de tous les commerces et services, ainsi qu'aux voies de transport et aux communications sur le territoire de l'entreprise. Lors de l'élaboration d'un plan directeur, le flux direct des flux de matériaux est assuré. Les ateliers doivent être situés en fonction de la séquence du processus de production. Les services et ateliers interconnectés doivent être placés à proximité.
Développement de la structure de production des associations. Les structures de production des associations dans les conditions modernes subissent des changements importants. Les associations de production de l'industrie manufacturière, notamment en génie mécanique, se caractérisent par les axes d'amélioration des structures de production suivants :
- concentration de la production de produits homogènes ou exécution du même type de travail dans des divisions spécialisées uniques de l'association ;
- approfondissement de la spécialisation des divisions structurelles des entreprises - industries, ateliers, succursales;
- intégration dans des complexes unifiés de recherche et de production de travaux sur la création de nouveaux types de produits, leur développement en production et l'organisation de la production dans les quantités nécessaires au consommateur;
- dispersion de la production basée sur la création d'entreprises hautement spécialisées de différentes tailles dans le cadre de l'association ;
- dépasser la segmentation dans la construction des processus de production et la création de flux de production unifiés sans affectation d'ateliers, de sites ;
- la mondialisation de la production, qui consiste à produire des produits à des fins différentes, complétés à partir de composants et de pièces homogènes dans leur conception et leur technologie, ainsi qu'à organiser la production de produits connexes ;
- large développement de la coopération horizontale entre les entreprises appartenant à différentes associations afin de réduire les coûts de production en augmentant l'échelle de production du même type de produits et en utilisant la pleine capacité.
La création et le développement de grandes associations ont donné vie à une nouvelle forme de structure de production, caractérisée par l'attribution dans leur composition d'industries spécialisées de taille optimale, construites sur le principe de la spécialisation technologique et disciplinaire. Une telle structure permet également une concentration maximale des processus d'approvisionnement, auxiliaires et de service. La nouvelle forme de structure de production s'appelait la multiproduction. Dans les années 1980, il était largement utilisé dans les industries automobile, électrique et autres.
L'association de Nizhny Novgorod pour la production d'automobiles, par exemple, comprend une société mère et sept usines affiliées. L'entreprise chef de file dispose de dix unités de production spécialisées : camions, voitures, moteurs, essieux de camions, métallurgie, forge-ressort, outillage, etc. Chacune de ces industries réunit un ensemble d'ateliers principaux et auxiliaires, jouit d'une certaine indépendance, entretient des liens étroits avec autres subdivisions de l'entreprise et jouit des droits établis pour les unités structurelles de l'association. Une structure de production typique est illustrée à la fig. 10.2.
À un niveau de qualité supérieur, une structure multi-production a été mise en place à l'usine automobile de la Volga. La fabrication d'automobiles y est concentrée dans quatre industries principales : la métallurgie, la presse, l'assemblage mécanique et l'assemblage et la forge. En outre, des installations de production auxiliaires ont également été identifiées. Chacun d'eux est une usine indépendante avec un cycle de production fermé. La structure de production comprend des ateliers. Mais les ateliers du VAZ ont subi des changements importants. Ils sont libérés des soucis d'assurer la production, la réparation et l'entretien des équipements, l'entretien et le nettoyage des locaux, etc. atelier de fabrication VAZ s'est retrouvé avec la seule tâche - produire les produits qui lui étaient assignés avec une haute qualité et dans les délais. La structure de gestion de la boutique est simplifiée au maximum. Ce sont le chef d'atelier, ses deux adjoints d'équipe, les chefs de section, contremaîtres, contremaîtres. Toutes les tâches d'approvisionnement, de préparation de la production et d'entretien sont résolues de manière centralisée par l'appareil de gestion de la production.
Riz. 10.2. Structure de production typique
Dans chaque production, des départements ont été créés : conception et technologie, conception, outillage et équipement, analyse et planification de la réparation des équipements. Ici, des services unifiés pour la planification et la répartition des opérations, la logistique, l'organisation du travail et les salaires ont été formés.
La structure de production comprend de grands ateliers spécialisés : réparation, fabrication et réparation d'équipements, opérations de transport et de stockage, nettoyage des locaux et autres. La création de puissants services d'ingénierie et de divisions de production en production, chacun d'entre eux résolvant pleinement les tâches qui leur sont assignées dans son domaine, a permis, sur une base fondamentalement nouvelle, de créer des conditions normales pour le fonctionnement efficace des principaux ateliers de production. .
L'organisation des ateliers et des sections est basée sur les principes de concentration et de spécialisation. La spécialisation des ateliers et des sites de production peut s'effectuer par type de travail - spécialisation technologique ou par type de produits manufacturés - spécialisation disciplinaire. Des exemples d'unités de production de spécialisation technologique dans une entreprise de construction de machines sont les ateliers de fonderie, de thermodéposition ou de galvanoplastie, les sections de tournage et de meulage dans un atelier d'usinage; spécialisation du sujet - un atelier de pièces de carrosserie, une section d'arbres, un atelier de fabrication de boîtes de vitesses, etc.
Si un cycle complet de fabrication d'un produit ou d'une pièce est réalisé au sein d'un atelier ou d'un site, cette subdivision est dite sujet-fermé.
Lors de l'organisation d'ateliers et de sites, il est nécessaire d'analyser attentivement les avantages et les inconvénients de tous les types de spécialisation. Avec la spécialisation technologique, une charge élevée d'équipements est assurée, une grande flexibilité de production est obtenue lors de la maîtrise de nouveaux produits et de l'évolution des installations de production. Dans le même temps, la planification des opérations et de la production devient plus difficile, le cycle de production est allongé et la responsabilité de la qualité des produits est réduite.
L'utilisation de la spécialisation par sujet, vous permettant de concentrer tout le travail sur la production d'une pièce ou d'un produit dans le cadre d'un atelier, d'une section, augmente la responsabilité des artistes interprètes ou exécutants pour la qualité du produit et l'exécution des tâches. La spécialisation par sujet crée les conditions préalables à l'organisation de la production en ligne et automatisée, assure la mise en œuvre du principe de flux direct, simplifie la planification et la comptabilité. Cependant, ici, il n'est pas toujours possible d'atteindre une charge complète d'équipements, la restructuration de la production pour la production de nouveaux produits nécessite des dépenses importantes.
Les ateliers et les sections fermées à sujet présentent également des avantages économiques importants, dont l'organisation permet de réduire la durée du cycle de production des produits de fabrication du fait de l'élimination totale ou partielle des mouvements entrants ou liés à l'âge, de simplifier la système de planification et de gestion opérationnelle du processus de production. L'expérience pratique des entreprises nationales et étrangères nous permet de donner le groupement suivant de règles à suivre lors de la décision sur l'application du sujet ou du principe technologique de la construction d'ateliers et de sections.
matière il est recommandé d'appliquer le principe dans les cas suivants : avec la sortie d'un ou deux produits standards, avec un volume important et une grande stabilité dans la production des produits, avec la possibilité d'un bon équilibre des équipements et de la main-d'œuvre, avec un minimum d'opérations de contrôle et un petit nombre de basculements ; technologique- avec la sortie d'une large gamme de produits, avec leur sérialisation relativement faible, avec l'impossibilité d'équilibrer matériels et effectifs, avec un grand nombre d'opérations de contrôle et un nombre important de changements.
Organisation des sites de production. L'organisation des sites est déterminée par le type de leur spécialisation. Cela implique de résoudre un grand nombre de tâches, y compris la sélection des installations de production ; calcul de l'équipement nécessaire et de sa disposition; déterminer la taille des lots (séries) de pièces et la fréquence de leur lancement-libération ; affecter les travaux et les opérations à chaque lieu de travail, établir des horaires ; calcul des besoins en personnel; conception d'un système de desserte des lieux de travail. À Ces derniers temps des complexes de recherche et de production ont commencé à se constituer en associations, intégrant toutes les étapes du cycle "Recherche - développement - production".
Pour la première fois dans le pays, quatre complexes de recherche et de production ont été créés au sein de l'association de Saint-Pétersbourg "Svetlana". Le complexe est une division unique spécialisée dans le développement et la production de produits d'un certain profil. Il est créé sur la base des bureaux d'études de l'usine principale. Outre le bureau d'études, il comprend les principaux ateliers de production et des filiales spécialisées. L'activité scientifique et de production des complexes est réalisée sur la base d'un calcul à la ferme.
Les complexes scientifiques et de production réalisent la conception et la préparation technologique de la production, impliquant les divisions concernées de l'association pour effectuer des travaux liés au développement de nouveaux produits. Le chef du bureau d'études s'est vu accorder les droits de planification de bout en bout de toutes les étapes de la pré-production - de la recherche à l'organisation de la production en série. Il est responsable non seulement de la qualité et du calendrier de développement, mais également du développement de la production en série de nouveaux produits et activités de production commerces et succursales inclus dans le complexe.
Dans le cadre de la transition des entreprises vers économie de marché il y a un développement ultérieur de la structure de production des associations sur la base de l'augmentation de l'indépendance économique de leurs unités constituantes.
Comme exemple de création et de mise en œuvre d'une nouvelle forme d'organisation dans la transition vers une économie de marché, on peut citer la création d'une société par actions - une entreprise de recherche et de production au sein de l'association Energia (Voronezh). Plus de 100 complexes de recherche et de production indépendants, des associations de premier niveau et des entreprises dotées d'une indépendance juridique complète et de comptes de règlement dans une banque commerciale ont été créés sur la base des divisions de l'entreprise. Lors de la création d'associations et d'entreprises indépendantes, les éléments suivants ont été utilisés : une variété de formes de propriété (étatique, locative, mixte, par actions, coopérative) ; variété de structures organisationnelles d'entreprises indépendantes et d'associations, dont le nombre varie de 3 à 2350 personnes; variété d'activités (scientifiques et productives, organisationnelles et économiques, productives et techniques).
L'entreprise compte 20 complexes de recherche et de production thématiques et fonctionnels qui combinent la recherche, la conception, les divisions technologiques et les installations de production spécialisées dans le développement et la production de certains types de produits ou la réalisation de travaux technologiquement homogènes. Ces complexes ont été créés en reformant des usines expérimentales et en série et sur la base d'un institut de recherche. Selon le nombre et le volume de travail, elles fonctionnent comme des associations de premier niveau, des entreprises ou des petites entreprises.
Les complexes de recherche et de production ont pleinement montré leurs avantages pendant la période de conversion dans les conditions d'un changement radical de la gamme de produits. Après l'obtention de l'indépendance, les entreprises se sont volontairement organisées en associations de premier niveau - complexes ou entreprises de recherche et de production - et se sont constituées en une entité centralisant 10 fonctions principales conformément à la Charte. L'organe directeur suprême de l'entreprise est l'assemblée des actionnaires. La coordination des travaux de mise en œuvre des fonctions centralisées est assurée par le conseil d'administration et les directions fonctionnelles de l'entreprise, travaillant dans des conditions de pleine autonomie. Les subdivisions exerçant des fonctions de service et de support travaillent également sur une base contractuelle et jouissent d'une totale indépendance juridique et économique.
Montré sur la fig. 10.3 et appelée la structure de gestion "circulaire" de l'entreprise répond aux exigences de la législation de la Fédération de Russie. Le conseil d'administration coordonne les fonctions centralisées de l'entreprise dans le cadre des statuts selon l'idée d'une table ronde.
Le système circulaire (par opposition au système vertical existant) d'organisation et de gestion de la production repose sur les principes suivants :
Riz. 10.3. Structure de gestion circulaire d'Energia Concern
- sur le caractère volontaire de l'association des entreprises actionnaires pour des activités communes afin d'obtenir des bénéfices maximaux et stables grâce à la vente de produits et services sur un marché concurrentiel pour répondre aux intérêts sociaux et économiques des actionnaires ;
- centralisation volontaire d'une partie des fonctions des entreprises pour l'organisation et la gestion de la production, inscrite dans la Charte de la société par actions;
- combiner les avantages d'une grande entreprise, en raison de la spécialisation, de la coopération et de l'échelle de production, avec les avantages des formes de petites entreprises et la motivation des employés par la propriété de la propriété ;
- un système de complexes de recherche et de production thématiques et fonctionnels interconnectés sur une base technologique, en tenant compte des avantages de la spécialisation et de la coopération;
- un système de relations contractuelles entre les complexes de recherche et de production et les entreprises, soutenu par un système de satisfaction des créances autosuffisantes, y compris la régulation du fonds salarial ;
- transférer le centre des travaux en cours sur l'organisation et la gestion de la production du niveau supérieur verticalement au niveau des complexes de recherche et de production et des entreprises indépendantes horizontalement sur une base contractuelle en concentrant les efforts de la direction générale sur des questions prometteuses ;
- la mise en place de relations économiques entre entreprises par l'intermédiaire d'une banque commerciale et d'un centre de règlement interne dans les zones concernées ;
- accroître les garanties pour résoudre les problèmes sociaux et protéger à la fois les entreprises indépendantes et tous les actionnaires;
- combinaison et développement de diverses formes de propriété au niveau de l'entreprise et des associations et entreprises indépendantes ;
- renoncement au rôle dominant des organes suprêmes de gouvernance avec la transformation des fonctions de gestion et de coordination de la production en une des variétés d'activité des actionnaires ;
- élaborer le mécanisme permettant de combiner les intérêts mutuels des entreprises indépendantes et de l'entreprise dans son ensemble et de prévenir le danger d'une rupture due aux forces centrifuges du principe technologique de construction de l'organisation de la production.
La structure circulaire prévoit une modification fondamentale des activités des complexes thématiques de recherche et de production, qui prennent la tête de la planification et assurent l'interconnexion horizontale des activités des complexes fonctionnels de recherche et de production et des entreprises sur une base contractuelle selon leur nomenclature, en tenant compte compte des changements sur le marché.
Le service de planification et de répartition dans le cadre de la société Pribyl a été transformé et une partie importante de ses fonctions et de son personnel a été transférée dans des complexes de recherche et de production. L'attention de ce service est centrée sur les tâches stratégiques et la coordination du travail des complexes et des entreprises.
Concern Energia a suivi le processus de privatisation par bail et transformation en société et a reçu un certificat de propriété de la propriété, il a reçu le statut de Centre fédéral de recherche et de production.
10.4. Organisation des processus de production dans le temps
Pour assurer l'interaction rationnelle de tous les éléments du processus de production et rationaliser le travail effectué dans le temps et dans l'espace, il est nécessaire de former le cycle de production du produit.
Le cycle de production est un ensemble de processus principaux, auxiliaires et de service organisés d'une certaine manière dans le temps, nécessaires à la fabrication d'un certain type de produit. La caractéristique la plus importante du cycle de production est sa durée.
Temps de cycle de fabrication- il s'agit d'une période calendaire au cours de laquelle le matériau, la pièce à usiner ou un autre élément traité passe par toutes les opérations du processus de production ou une certaine partie de celui-ci et se transforme en produits finis. La durée du cycle est exprimée en jours calendaires ou en heures. Structure du cycle de production comprend les heures de travail et les pauses. Pendant la période de travail, les opérations technologiques proprement dites et les travaux préparatoires et finaux sont effectués. La période de travail comprend également la durée des opérations de contrôle et de transport et le temps des processus naturels. Le temps des pauses est dû au mode de travail, au stockage interopérationnel des pièces et aux lacunes dans l'organisation du travail et de la production.
Le temps entre les opérations est déterminé par les pauses de mise en lots, d'attente et de cueillette. Les ruptures de partition se produisent lorsque les produits sont fabriqués par lots et sont dues au fait que les produits transformés restent jusqu'à ce que le lot entier soit passé par cette opération. Dans ce cas, on suppose qu'un lot de production est un ensemble de produits de même nom et de même taille, lancés en production pour un certain temps avec la même période préparatoire et finale. Les pauses d'attente sont causées par la durée incohérente de deux opérations adjacentes du processus technologique, et les pauses de préparation sont causées par la nécessité d'attendre le moment où toutes les ébauches, pièces ou unités d'assemblage incluses dans un ensemble de produits sont fabriquées. Les pauses de cueillette se produisent lors du passage d'une étape du processus de production à une autre.
Sous sa forme la plus générale, la durée du cycle de production J ts est exprimé par la formule
J c = J t+ Tn –3 + J e+ Jà + J tr + J mois + J exemple, (10.1)
où J t est le temps des opérations technologiques ; Tn-3 - le temps des travaux préparatoires et finaux ; J e est le temps des processus naturels ; J k est le temps des opérations de contrôle ; J tr est le temps de transport des objets de travail ; J mo - temps de couchage interopératoire (pauses intra-équipe); J pr - le temps des pauses dues au mode de travail.
La durée des opérations technologiques et des travaux préparatoires et finaux dans l'ensemble forme un cycle d'exploitation J flic.
Cycle de fonctionnement- il s'agit de la durée de la partie achevée du processus technologique, réalisée sur un lieu de travail.
Méthodes de calcul de la durée du cycle de production. Il est nécessaire de faire la distinction entre le cycle de production de pièces individuelles et le cycle de production d'une unité d'assemblage ou d'un produit dans son ensemble. Le cycle de production d'une pièce est généralement appelé simple, et le produit ou l'unité d'assemblage est appelé complexe. Le cycle peut être mono-opérationnel et multi-opérationnel. Le temps de cycle d'un processus en plusieurs étapes dépend de la manière dont les pièces sont transférées d'une opération à l'autre. Il existe trois types de mouvement d'objets de travail dans le processus de leur fabrication: séquentiel, parallèle et parallèle-séquentiel.
À type de mouvement séquentiel le lot entier de pièces est transféré à l'opération suivante une fois que le traitement de toutes les pièces à l'opération précédente est terminé. Les avantages de cette méthode sont l'absence d'interruptions dans le fonctionnement de l'équipement et du travailleur à chaque opération, la possibilité de leur charge élevée pendant le quart de travail. Mais le cycle de production avec une telle organisation du travail est le plus important, ce qui affecte négativement les performances techniques et économiques de l'atelier, de l'entreprise.
À mouvement parallèle les pièces sont transférées à l'opération suivante par un lot de transport immédiatement après la fin de son traitement à l'opération précédente. Dans ce cas, le cycle le plus court est fourni. Mais les possibilités d'utiliser un type de mouvement parallèle sont limitées, car une condition préalable à sa mise en œuvre est l'égalité ou la multiplicité de la durée des opérations. Sinon, des interruptions dans le fonctionnement des équipements et des travailleurs sont inévitables.
À type de mouvement parallèle-séquentiel les pièces d'opération en opération, elles sont transférées par des transporteurs ou à la pièce. Dans ce cas, il y a une combinaison partielle du temps d'exécution des opérations adjacentes, et le lot entier est traité à chaque opération sans interruption. Les ouvriers et les équipements travaillent sans interruption. Le cycle de production est plus long par rapport à un cycle parallèle, mais plus court qu'avec un mouvement séquentiel d'objets de travail.
Calcul du cycle d'un processus de production simple. Le cycle de production opérationnel d'un lot de pièces à mouvement de type séquentiel se calcule comme suit :
(10.2)
où n- le nombre de pièces du lot de fabrication, pièces ; r op est le nombre d'opérations du processus technologique ; t PC je— délai pour chaque opération, min ; DE r.m. je- le nombre d'emplois occupés par la fabrication d'un lot de pièces pour chaque opération.
Le schéma du type de mouvement séquentiel est illustré à la fig. 10.4, un. Selon les données indiquées dans le diagramme, le cycle de fonctionnement d'un lot composé de trois pièces traitées sur quatre postes de travail est calculé :
T c.seq = 3 (t pièces 1 + t pièces 2 + t pièces 3 + t pièces 4) = 3 (2 + 1 + 4 + 1,5) = 25,5 min.
La formule de calcul de la durée du cycle de fonctionnement pour un type de mouvement parallèle :
(10.3)
où est le temps d'exécution de l'opération, le plus long du processus technologique, min.
Riz. 10.4, un. Calendrier des cycles de production pour le mouvement séquentiel de lots de pièces
Le graphique du mouvement d'un lot de pièces avec un mouvement parallèle est illustré à la Fig. 10.4, b. Selon le planning, vous pouvez déterminer la durée du cycle de fonctionnement avec mouvement parallèle :
J c.par = ( t pièces 1+ t pièces 2+ t pièces 3+ t pièces 4)+ (3 – 1) t pièces 3 \u003d 8,5 + (3 - 1) 4 \u003d 16,5 min.
Riz. 10.4, b. Calendrier des cycles de production avec mouvement parallèle-séquentiel de lots de pièces
Avec un type de mouvement parallèle-séquentiel, il y a un chevauchement partiel dans le temps d'exécution des opérations adjacentes. Il existe deux types de combinaison d'opérations adjacentes dans le temps. Si le temps d'exécution de l'opération suivante est supérieur au temps d'exécution de l'opération précédente, vous pouvez appliquer le type de mouvement parallèle des pièces. Si le temps d'exécution de l'opération suivante est inférieur au temps d'exécution de la précédente, alors un type de mouvement parallèle-séquentiel est acceptable avec le chevauchement maximal possible dans le temps d'exécution des deux opérations. Dans ce cas, les opérations combinées maximales diffèrent les unes des autres par le moment de la fabrication de la dernière pièce (ou du dernier lot de transport) lors de l'opération suivante.
Un schéma d'un type de mouvement parallèle-séquentiel est illustré à la fig. 10.4, dans. Dans ce cas, le cycle de fonctionnement sera inférieur à celui d'un type de mouvement séquentiel, par la quantité de combinaison de chaque paire d'opérations adjacentes : les première et deuxième opérations - AB - (3 - l) t pièce2 ; deuxième et troisième opérations - VG \u003d A¢B¢ - (3 -1) t pc3 ; troisième et quatrième opérations - DE - (3 - 1) t pcs4 (où t pc3 et t pcs4 a moins de temps t morceau de noyau de chaque paire d'opérations).
Formules de calcul
(10.4)
Lors de l'exécution d'opérations sur des postes de travail parallèles :
Riz. 10.4, ch. Planning des cycles de production avec mouvement parallèle des lots de pièces
Lors du transfert de produits par des transporteurs :
(10.5)
où est le temps nécessaire pour effectuer l'opération la plus courte.
Un exemple de calcul de la durée du cycle selon la formule (10.5):
J c.p-p \u003d 25,5 - 2 (1 + 1 + 1,5) \u003d 18,5 min.
Le cycle de production pour la fabrication d'un lot de pièces comprend non seulement le cycle de fonctionnement, mais également les processus naturels et les ruptures liées au mode de fonctionnement, et d'autres composants. Dans ce cas, la durée du cycle pour les types de mouvement considérés est déterminée par les formules :
où r op est le nombre d'opérations technologiques ; DE r.m - le nombre d'emplois parallèles occupés par la fabrication d'un lot de pièces pour chaque opération ; t mo — temps de décubitus interopératoire entre deux opérations, h ; J cm est la durée d'un poste de travail, h; ré cm est le nombre d'équipes ; À v.n - le coefficient de conformité prévu avec les normes d'exploitation; À voie - coefficient de conversion du temps de travail en temps calendaire; J e est la durée des processus naturels.
Calcul du temps de cycle d'un processus complexe
Le cycle de production d'un produit comprend les cycles de fabrication des pièces, d'assemblage des unités et des produits finis, et des opérations de test. Dans ce cas, on suppose que différentes pièces sont fabriquées en même temps. Par conséquent, le cycle de la pièce la plus exigeante en main-d'œuvre (principale) parmi celles fournies aux premières opérations de l'atelier d'assemblage est inclus dans le cycle de production du produit. La durée du cycle de production du produit peut être calculée par la formule
J cp = J cd + J cb, (10.9)
où J ts.d - la durée du cycle de production pour la fabrication de la pièce principale, calendes. journées; J ts.b - la durée du cycle de production des travaux d'assemblage et de test, les calendriers. journées
Riz. 10.5. Cycle de processus complexe
Pour déterminer la durée du cycle d'un processus de production complexe peut être utilisé méthode graphique. Pour cela, un planning cyclique est établi. Les cycles de production des processus simples inclus dans le complexe sont préalablement établis. Selon le programme de cycle, le délai d'exécution de certains processus par d'autres est analysé et la durée totale du cycle d'un processus complexe pour la production d'un produit ou d'un lot de produits est déterminée comme la plus grande somme de cycles de processus simples interconnectés. et pauses interopérationnelles. Sur la fig. 10.5 montre un graphique de cycle d'un processus complexe. Sur le graphique de droite à gauche, les cycles des processus partiels sont tracés sur une échelle de temps, en commençant par les essais et en terminant par la fabrication des pièces.
Moyens et sens d'assurer la continuité du processus de production et de réduire le temps de cycle
Un degré élevé de continuité des processus de production et une réduction de la durée du cycle de production revêtent une grande importance économique : la taille des travaux en cours est réduite et la rotation du fonds de roulement est accélérée, l'utilisation des équipements et des zones de production est améliorée , et le coût de production est réduit. Des études menées dans un certain nombre d'entreprises à Kharkov ont montré que lorsque la durée moyenne du cycle de production ne dépasse pas 18 jours, chaque rouble dépensé fournit 12 % de production en plus que dans les usines où la durée du cycle est de 19 à 36 jours, et 61 % plus que dans une usine où les produits ont un cycle de plus de 36 jours.
Une augmentation du niveau de continuité du processus de production et une réduction de la durée du cycle sont obtenues, d'une part, en élevant le niveau technique de production, et d'autre part, par des mesures de nature organisationnelle. Les deux voies sont interconnectées et se complètent.
L'amélioration technique de la production va dans le sens de l'introduction de nouvelles technologies, d'équipements de pointe et de nouveaux véhicules. Cela conduit à une réduction du cycle de production en réduisant l'intensité de travail des opérations technologiques et de contrôle réelles, en réduisant le temps de déplacement des objets de travail.
Les mesures organisationnelles devraient inclure :
- minimiser les interruptions causées par l'attente interopérationnelle et les interruptions de traitement par lots grâce à l'utilisation de méthodes parallèles et parallèles-séquentielles de déplacement des objets de travail et à l'amélioration du système de planification ;
- construction d'horaires pour combiner divers processus de production, offrant un chevauchement partiel dans le temps d'exécution des travaux et opérations connexes;
- réduction des temps d'attente basée sur la construction de plannings optimisés pour la fabrication des produits et le lancement rationnel des pièces en production ;
- la mise en place d'ateliers et de sections thématiques et pointillistes, dont la création réduit la longueur des trajets intra- et inter-ateliers, réduit les temps de transport.