Quel est le but de la gestion de la qualité. Méthodes de gestion de la qualité
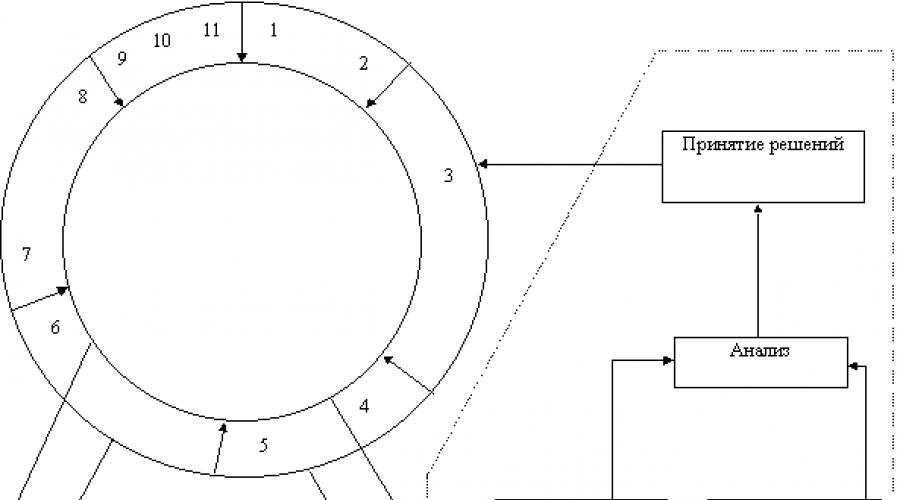
Lire aussi
CHAPITRE 3. FONDEMENTS MÉTHODOLOGIQUES DU MANAGEMENT DE LA QUALITÉ
3.1. Aspects de la qualité du produit
À théorie moderne et la pratique du management de la qualité, on distingue les cinq grandes étapes suivantes :
1. Décider « que produire ? » et élaboration de cahiers des charges. Par exemple. Lors de la sortie d'une voiture d'une marque ou d'une autre, il est important de décider: "pour qui est la voiture" (pour un cercle restreint de personnes très riches ou pour le grand public).
2. Vérification de l'état de préparation de la production et de la répartition des responsabilités organisationnelles.
3. Le processus de fabrication de produits ou de prestation de services.
4. Élimination des défauts et fourniture d'informations en retour afin d'apporter des modifications au processus de production et de contrôle qui permettent d'éviter les défauts identifiés à l'avenir.
5. Élaboration de plans qualité à long terme.
La mise en œuvre de ces étapes est impossible sans l'interaction de tous les services, organes de direction de l'entreprise. Cette interaction est appelée système unifié de gestion de la qualité. ce fournit approche systémiqueà la gestion de la qualité.
Examinons plus en détail le contenu des étapes de la gestion de la qualité.
Dans la première étape, la qualité fait référence à la mesure dans laquelle les produits ou services d'une entreprise répondent à ses spécifications internes. Cet aspect de la qualité est appelé qualité du respect des spécifications.
Lors de la deuxième étape, la qualité de la structure est évaluée. La qualité peut répondre aux spécifications de l'entreprise en matière de conception de produits, mais la conception elle-même peut être de qualité élevée ou médiocre.
Au troisième stade, la qualité signifie le degré auquel le travail ou le fonctionnement des services (biens) de l'entreprise satisfait les besoins réels des consommateurs.
À cet égard, l'expérience de la société Thermo King, qui est l'un des leaders reconnus dans le domaine des véhicules frigorifiques, mérite attention. Il s'agit d'une grande entreprise transnationale qui possède 13 usines dans différents pays du monde. En Russie, cette société est apparue dans les années 70, lorsqu'elle a commencé à coopérer avec la société Sovtransavto. L'objectif principal de l'entreprise est de créer une chaîne climatique fermée qui couvre les étapes de transport des produits des fabricants, des lieux de grandes installations de stockage, des entrepôts aux magasins, cafés et restaurants. Les produits de l'entreprise sont toute la gamme d'unités de réfrigération automobile, allant des petites voitures d'une capacité de charge de 350 à 500 kg. aux grandes semi-remorques, d'un volume de 90 mètres cubes. m., ainsi que les grands conteneurs maritimes impliqués dans le transport transnational entre les continents. Les unités Thermo King sont compactes, fiabilité maximale et économie. La base de l'organisation des activités de l'entreprise est de se concentrer sur l'utilisateur final et de lui créer les conditions les plus favorables lors de l'achat, de l'exploitation et de la réparation des équipements.
De manière caractéristique, l'équipement de "Thermo King" est plus cher que l'équipement de ses concurrents. Cependant, son succès en affaires est assuré par le niveau et la qualité du service.
Les produits de l'entreprise peuvent répondre à des spécifications internes (première étape) ; la conception du produit elle-même peut être exceptionnelle (deuxième étape) ; un service ou un produit peut ne pas convenir aux besoins spécifiques du consommateur. Nous avons considéré le contenu de trois étapes fondamentales, qui sont d'égale importance. Tout défaut dans l'un d'entre eux peut créer des problèmes de qualité.
Le système de gestion de la qualité des produits repose sur les catégories de gestion interdépendantes suivantes : objet, objectifs, facteurs, sujet, méthodes, fonctions, moyens, principe, type, type de critères, etc.
La gestion de la qualité des produits est comprise comme un processus constant, systématique et délibéré d'influence des facteurs et des conditions à tous les niveaux, garantissant la création de produits de qualité optimale et leur pleine utilisation.
Le système de gestion de la qualité des produits comprend les fonctions suivantes :
1. Fonctions de gestion stratégique, tactique et opérationnelle.
2. Fonctions de décision, de contrôle des actions, d'analyse et de comptabilité, d'information et de contrôle.
3. Fonctions spécialisées et communes à toutes les étapes cycle de la vie des produits.
4. Fonctions de gestion en fonction de facteurs et conditions scientifiques, techniques, industriels, économiques et sociaux.
Les fonctionnalités stratégiques incluent :
- prévision et analyse des indicateurs de qualité de base ;
- détermination des orientations des travaux de conception et d'ingénierie ;
- analyse des résultats obtenus en matière de qualité de la production ;
- analyse des informations sur les plaintes;
- analyse des informations sur la demande des consommateurs.
Caractéristiques tactiques :
- gestion de la production;
- maintien au niveau des indicateurs de qualité spécifiés ;
- interaction avec les objets gérés et l'environnement externe.
Le système de management de la qualité des produits est un ensemble d'organes de gestion et d'objets, d'activités, de méthodes et de moyens de gestion visant à établir, assurer et maintenir un haut niveau de qualité des produits.
En 1987, l'Organisation internationale de normalisation (ISO), avec la participation des États-Unis, du Canada et de l'Allemagne, a élaboré et approuvé cinq normes internationales de la série 9000 (sur les systèmes qualité), qui ont établi des exigences pour les systèmes d'assurance qualité des produits, y compris les le développement, la fabrication, l'organisation du contrôle et des essais des produits, leur exploitation, leur stockage et leur transport. Les normes internationales ISO 9000 pour les systèmes qualité comprennent cinq titres :
1. ISO 9000 « Normes générales de gestion de la qualité et d'assurance qualité. Lignes directrices pour la sélection et l'application ».
2. ISO 9001 « Système qualité. Un modèle d'assurance qualité dans la conception et/ou le développement, la production, l'installation et la maintenance.
3. ISO 9002 « Système qualité. Un modèle d'assurance qualité dans la production et l'installation ».
4. ISO 9003 « Système qualité. Modèle d'assurance qualité pour l'inspection et les essais finaux ».
5. ISO 9004 « Management général de la qualité et éléments d'un système qualité. Des lignes directrices".
Le système de gestion de la qualité des produits doit répondre aux exigences pour :
9001 - exigences pour le système de contrôle et d'essai des produits, certification de fiabilité.
9002 - exigences pour le système d'organisation de la production.
9003 - exigences pour un système de gestion de la qualité de la conception à l'exploitation.
Le système de management de la qualité comprend :
1. Tâches de gestion (politique qualité, organisation).
2. Système de documentation et de planification.
3. Documentation des exigences et de leur faisabilité.
4. Qualité pendant le développement (planification, compétence, documentation, vérification, résultat, changements).
5. Qualité lors de l'approvisionnement (documentation, contrôle).
6. Désignation des produits et possibilité de leur contrôle.
7. Qualité pendant la production (planification, instructions, qualification, contrôle).
8. Contrôle qualité (contrôles entrants, contrôle inter-opérationnel, contrôle final, documentation des tests).
9. Contrôle des installations d'essai.
10. Actions correctives.
11. Qualité du stockage, du mouvement, de l'emballage, de l'expédition.
12. Documentation de qualité.
13. Contrôle interne du système de maintien de la qualité.
14. Formation.
15. Candidature Méthodes statistiques.
16. Analyse de la qualité et des systèmes de mesures prises.
Des indicateurs de qualité contrôlés sont établis en fonction des spécificités du produit.
Exemple. Tableau de bord de la qualité.
Qualité des machines. Technique (puissance, précision, consommation de ressources spécifiques, fiabilité, etc.).
La qualité du travail. Raisons du mariage.
La qualité des produits. Industriel, consommateur, économique.
Qualité du projet. Nombre de correctifs en cours d'implémentation .
Qualité technologique. Nombre d'infractions.
Riz. 3.1. Niveaux de qualité
La politique qualité peut être formulée comme un principe d'activité ou un objectif à long terme et inclure :
- amélioration de la situation économique de l'entreprise;
- développer ou conquérir de nouveaux marchés ;
- l'atteinte d'un niveau technique de production supérieur au niveau des entreprises leaders ;
- se concentrer sur la satisfaction des exigences des consommateurs de certaines industries ou de certaines régions ;
- développement de produits dont la fonctionnalité est mise en œuvre sur de nouveaux principes ;
- amélioration des indicateurs les plus importants de la qualité des produits ;
- réduire le niveau de défectuosité des produits manufacturés;
- extension des garanties des produits ;
- développement des services.
Conformément à la norme ISO, le cycle de vie du produit comprend 11 étapes :
1. Marketing, recherche et étude de marché.
2. Conception et développement des exigences techniques, développement de produits.
3. Logistique.
4. Préparation et développement des processus de production.
5. Fabrication.
6. Contrôle, tests et enquêtes.
7. Emballage et stockage.
8. Ventes et distribution de produits.
9. Installation et fonctionnement.
10. Assistance et service technique.
11.Utilisation après essai.
Les étapes répertoriées sont présentées dans la littérature sur la gestion sous la forme d'une « boucle de qualité » fig. 3.2.
Ainsi, l'assurance qualité des produits est un ensemble d'activités planifiées et systématiquement réalisées qui créent les conditions nécessaires réaliser chaque étape de la boucle qualité pour s'assurer que les produits répondent aux exigences de qualité.
La gestion de la qualité comprend la prise de décision, qui est précédée par le contrôle, la comptabilité, l'analyse.
L'amélioration de la qualité est une activité continue visant à améliorer le niveau technique des produits, la qualité de leur fabrication, à améliorer les éléments de production et le système qualité.
Riz. 3.2. Assurance qualité
Le mécanisme de gestion de la qualité du produit est illustré à la fig. 3.3.
Sur la fig. 3.3 le système de gestion de la qualité est présenté sous une forme concentrée. Ici, tout d'abord, la politique de l'entreprise dans le domaine de la qualité est mise en évidence. le système qualité lui-même, y compris l'assurance, la gestion et l'amélioration de la qualité.
Dans la gestion moderne de la qualité, dix conditions fondamentales sont formulées :
1. Attitude envers le consommateur comme élément le plus important de ce processus.
2. Acceptation par la direction d'engagements à long terme pour mettre en œuvre le système de gestion de l'entreprise.
3. Croyance qu'il n'y a pas de limite à la perfection.
Riz. 3.3. Gestion de la qualité des produits
4. La confiance qu'il vaut mieux prévenir les problèmes que d'y répondre lorsqu'ils surviennent.
5. Intérêt, leadership et implication directe de la direction.
6. Norme de travail, exprimée par la formulation "zéro erreur".
7. Participation des salariés de l'entreprise, tant collective qu'individuelle.
8. Concentrez-vous sur l'amélioration des processus, pas sur les personnes.
9. Croyance que les fournisseurs deviendront vos partenaires s'ils comprennent vos tâches.
10. Reconnaissance du mérite.
Du point de vue du consommateur, la qualité du produit le degré de satisfaction des exigences des consommateurs.
Le consommateur de demain.
1. Donne la priorité à la qualité et le prix passe au second plan.
3. Nécessite une amélioration continue de la qualité.
4. Exige une assurance qualité dans le processus et refuse le contrôle final.
5. Sensibles dans leurs réactions au changement processus technologique.
6. Coopérer en cas d'assurance qualité.
7. Est un partisan des produits si la qualité est assurée
Le désir de la Russie de s'intégrer à la communauté mondiale, ainsi que le développement des relations de marché dans le pays, nécessitent une identification complète et complète des propriétés et une évaluation des indicateurs qui déterminent et caractérisent la qualité des produits et le niveau technique de production.
La composition et l'interrelation des principales exigences pour la production de produits dans la documentation réglementaire et technique sont présentées dans la fig. 3.4.
Riz. 3.4. Exigences de base pour le processus de production dans la documentation réglementaire et technique
Les meilleurs résultats dans la création et la production de produits compétitifs sont obtenus par les entreprises qui disposent d'informations complètes sur l'état et les capacités des processus de production, ainsi que sur le développement opportun d'actions de contrôle pour les améliorer.
Selon des experts nationaux et étrangers, la qualité des produits est définie dans la documentation de conception et technologique, et les deux doivent être évaluées en conséquence.
1) Vous devez commencer par le développement de la production de biens demandés, c'est-à-dire produire ce que quelqu'un achètera, et si vous améliorez ce produit, le nombre de ses acheteurs augmentera, la performance économique du l'entreprise s'améliorera et il sera possible de trouver des fonds pour les ventes prochaines étapes résoudre les problèmes de qualité.
Cependant, le produit demandé est le plus souvent un nouveau produit. Par conséquent, il est nécessaire de commencer par étudier la demande du marché et de la prendre en compte lors de la création et de la maîtrise de la production de nouveaux produits. Comme, par exemple, "Gazelle" de l'usine automobile de Gorki; "Bull" JSC "ZiL".
2) Vous devez disposer d'un revendeur, d'un réseau de vente, ainsi que d'une distribution de marchandises et d'informations à ce sujet. Si ce n'est pas le cas, aucune qualité de produit ne sauvera l'entreprise. Ainsi, par exemple, l'usine de Nizhny Novgorod JSC "Khokhloma painting" fabrique des produits de la plus haute qualité, mais, n'ayant pas de bon réseau de revendeurs, en particulier à l'étranger, est obligée de vendre des produits à des prix 5 à 10 fois inférieurs à ceux estimés par les experts étrangers. En conséquence, l'entreprise subit de lourdes pertes et connaît des difficultés financières.
3) Il est nécessaire de minimiser les coûts de production. Pour cela, il faut tout recalculer, repenser la base matérielle et technique de l'entreprise, abandonner tout le superflu et restructurer. Sans cela, cela ne vaut pas la peine de commencer une lutte pour la qualité, car l'entreprise peut mourir d'une autre maladie. Pour le confirmer, les exemples ne sont pas nécessaires, presque toutes les entreprises russes ont des coûts énormes. Ils sont si importants que les entreprises sont obligées de déformer les rapports. Par conséquent, il est presque impossible de calculer correctement le coût de la qualité et, par conséquent, de gérer l'économie de la qualité.
4) Vous devez apprendre à gérer les finances, et c'est un art, et pas facile à cela. Tout d'abord, il est nécessaire de déboguer le contrôle financier. Le manque de contrôle est la voie vers les pertes financières, leur pillage et la faillite de l'entreprise. Le principal facteur qui y contribue est le manque de entreprises industrielles leurs véritables propriétaires. Dans ces entreprises, les cadres supérieurs disposent pratiquement de la propriété et dépendent donc beaucoup de leur décence et de leur honnêteté. Néanmoins, des gestionnaires prévoyants sont intéressés par la mise en place d'un contrôle financier et travaillent dans ce sens.
Les quatre conditions préalables au bon fonctionnement des entreprises, mentionnées ci-dessus, sont prises en compte dans divers concepts de qualité, mais nous parlons ici de leur amélioration. Dans la majorité des entreprises russes, ces conditions doivent être créées pratiquement à partir de zéro. Et ce n'est qu'après que l'entreprise a en quelque sorte fait face à cette tâche qu'elle peut commencer à résoudre le problème de qualité en créant et en certifiant des systèmes de qualité qui répondent aux exigences des normes ISO 9000 et 05-9000, ainsi qu'au concept TOM. Dans le même temps, il est nécessaire de soulever la question de la réforme des entreprises, de leur restructuration et de la création de nouveaux éléments, sur la base d'une compréhension claire de la philosophie TOM et de l'accent mis sur le concept de qualité universelle. Ce n'est pas un hasard si les dernières grandes conférences internationales s'intitulaient « La qualité est l'étoile directrice de monde meilleur" (Israël, Jérusalem, 1996), "La qualité est la clé de XXIe siècle"(Japon, Yokohama, 1996).
3.2. Contrôle de qualité
Le contrôle qualité, quelle que soit la perfection des méthodes utilisées à cet effet, consiste avant tout à séparer les bons produits des mauvais. Naturellement, la qualité du produit n'augmente pas en raison du rejet des produits de mauvaise qualité. Notez que dans les entreprises de l'industrie électronique, en raison de la taille miniature des produits, il est souvent impossible de réparer un défaut. Par conséquent, les entreprises modernes ne se concentrent pas sur la détection du mariage, mais sur sa prévention, sur un contrôle minutieux du processus de production et mènent leurs activités conformément au concept de «régulation de la qualité».
jouer un rôle important dans la garantie de la qualité du produit Méthodes statistiques.
Le but des méthodes de contrôle statistique est d'exclure les variations aléatoires de la qualité du produit. De tels changements sont causés par des causes spécifiques qui doivent être identifiées et éliminées. Les méthodes statistiques de contrôle de la qualité sont divisées en :
- contrôle d'acceptation statistique sur un attribut alternatif ;
- contrôle d'acceptation sélectif pour différentes caractéristiques de qualité ;
- normes de contrôle d'acceptation statistique;
- système de plans économiques;
- les plans d'échantillonnage continu ;
- méthodes de régulation statistique des processus technologiques.
Il est à noter que le contrôle statistique et la régulation de la qualité des produits sont bien connus dans notre pays. Dans ce domaine, nos scientifiques ont une priorité incontestable. Qu'il suffise de rappeler les travaux d'A.N. Kolmogorov sur des évaluations impartiales de la qualité des produits acceptés sur la base des résultats du contrôle sélectif, l'élaboration d'une norme de contrôle d'acceptation utilisant des critères économiques.
De nombreuses évaluations de la qualité des produits découlent de la nature même de la collecte d'informations.
Exemple. L'usine contrôle un lot de produits, parmi lesquels il y a ceux qui conviennent et ceux qui ne conviennent pas. La proportion de mariage dans ce lot est inconnue. Cependant, ce n'est pas une quantité indéfinie dans le vrai sens du terme. Si rien n'empêche de vérifier tous les produits d'un lot donné, le pourcentage de rebuts peut être déterminé avec précision. Si, en contrôlant l'échantillon prélevé sur le parti, il n'est possible de ne recueillir que des informations incomplètes, il y a une sélection accidentelle qui peut déformer l'image réelle.
Le problème se pose, comment estimer la valeur de telle ou telle caractéristique de cette population à partir d'un échantillon pris dans la population ? Ce problème peut survenir dans diverses situations.
1. En prenant un lot de produits sur la base des résultats de l'échantillon, le pourcentage de défauts est estimé w dans ce lot de produits.
2. Il y a du matériel. La loi de répartition des résultats du travail de l'équipement détermine dans une certaine mesure la capacité de l'équipement à effectuer ce travail au moment considéré.
Chacun des types de méthodes de contrôle statistique de la qualité a ses propres avantages et inconvénients. Par exemple, l'échantillonnage d'acceptation pour des caractéristiques variables a l'avantage de nécessiter une taille d'échantillon plus petite. L'inconvénient de cette méthode est qu'un plan de contrôle séparé est nécessaire pour chaque caractéristique contrôlée. Si chaque élément est testé par rapport à cinq caractéristiques de qualité, cinq plans de test distincts doivent être en place.
En règle générale, les plans d'échantillonnage pour acceptation sont conçus de manière à ce qu'il y ait peu de chance de rejeter par erreur un bon produit, ou qu'il y ait peu de "risque du fabricant". La plupart des plans d'échantillonnage sont conçus de manière à ce que le "risque du producteur" soit
Si, avec un plan d'échantillonnage établi, le "niveau de qualité acceptable" correspond au taux de rejet attendu p dans la population générale, on estime que la probabilité de rejeter les bons produits diffère peu de 0,05. Par conséquent, le niveau de qualité acceptable et un correspondent à la méthode du plan d'échantillonnage. Il est également important que le plan d'échantillonnage pour acceptation soit établi de manière à ce que la probabilité d'accepter des produits de mauvaise qualité soit faible, c'est-à-dire qu'il y ait peu de "risque pour le consommateur". La frontière entre les bons et les mauvais produits s'appelle fraction admissible de défauts dans un lot. Examinons plus en détail les méthodes les plus courantes de contrôle statistique de la qualité.
3.3. Contrôle d'acceptation statistique par attribut
La principale caractéristique d'un lot de produits sur une base alternative est la proportion générale de produits défectueux.
D est le nombre d'articles défectueux dans un lot de N articles.
Dans la pratique du contrôle statistique, la part générale q est inconnue et doit être estimée à partir des résultats du contrôle d'un échantillon aléatoire de n éléments, dont m sont défectueux.
Un plan de contrôle statistique est un système de règles qui spécifie les méthodes de sélection des éléments à tester et les conditions dans lesquelles un lot doit être accepté, rejeté ou continué à être testé.
Il existe les types de plans suivants pour le contrôle statistique d'un lot de produits sur une base alternative :
Les plans en une étape sont plus simples en termes d'organisation du contrôle de la production. Les plans de contrôle en deux étapes, multi-étapes et séquentiels permettent, à taille d'échantillon identique, une plus grande précision des décisions, mais ils sont plus complexes sur le plan organisationnel.
La tâche du contrôle sélectif d'acceptation est en fait réduite à tester statistiquement l'hypothèse que la proportion de produits défectueux q dans le lot est égale à la valeur admissible q o , c'est-à-dire H 0 : :q = q 0 .
Une tâche bon choix Le plan de contrôle statistique est de rendre improbables les erreurs de type I et de type II. Rappelons que les erreurs du premier type sont associées à la possibilité de rejeter à tort un lot de produits ; les erreurs du deuxième type sont associées à la possibilité de sauter par erreur un lot défectueux
3.4. Normes de contrôle d'acceptation statistique
Pour l'application réussie des méthodes statistiques de contrôle de la qualité des produits grande importance dispose de lignes directrices et de normes pertinentes qui devraient être accessibles à un large éventail d'ingénieurs et de techniciens. Les normes de contrôle d'acceptation statistique offrent la possibilité de comparer objectivement les niveaux de qualité des lots d'un même type de produit à la fois dans le temps et entre différentes entreprises.
Arrêtons-nous sur les exigences de base des normes de contrôle d'acceptation statistique.
Tout d'abord, la norme doit contenir suffisamment grand nombre plans avec des caractéristiques opérationnelles différentes. Ceci est important, car cela vous permettra de choisir des plans de contrôle, en tenant compte des caractéristiques de la production et des exigences des clients en matière de qualité des produits. Il est souhaitable que différents types de plans soient spécifiés dans la norme : plans de contrôle en une étape, en deux étapes, en plusieurs étapes, séquentiels, etc.
Les principaux éléments des normes de contrôle d'acceptation sont :
1. Tableaux des plans d'échantillonnage utilisés dans le cours normal de la production, ainsi que des plans pour un contrôle renforcé dans des conditions de désordre et pour faciliter le contrôle lors de l'obtention d'une qualité élevée.
2. Règles de choix des plans, en tenant compte des caractéristiques de contrôle.
3. Règles pour la transition du contrôle normal au contrôle renforcé ou léger et la transition inverse pendant le cours normal de la production.
4.Méthodes de calcul des estimations ultérieures des indicateurs de qualité du processus maîtrisé.
En fonction des garanties apportées par les plans de contrôle de réception, on distingue les modalités suivantes d'élaboration des plans :
Le premier système de plans de contrôle d'acceptation statistique, qui a trouvé une large application dans l'industrie, a été développé par Dodge et Rohlig. Les plans de ce système prévoient le contrôle complet des produits des lots rejetés et le remplacement des produits défectueux par de bons.
Répandu dans de nombreux pays norme américaine MIL-STD-LO5D. La norme nationale GOST-18242-72 est proche de la construction américaine et contient des plans pour le contrôle d'acceptation en une étape et en deux étapes. La norme est basée sur le concept d'un niveau de qualité acceptable (ARQ) q 0, qui est considéré comme la part maximale autorisée par le consommateur de produits défectueux dans un lot fabriqué au cours du cours normal de la production. La probabilité de rejeter un lot avec une proportion de produits défectueux égale à q 0 pour les plans standards est faible et diminue à mesure que la taille de l'échantillon augmente. Pour la plupart des forfaits ne dépasse pas 0,05.
Lors de tests de produits sur plusieurs terrains, la norme recommande de classer les défauts en trois classes : critiques, majeurs et mineurs.
3.5. Cartes de contrôle
L'un des principaux outils du vaste arsenal de méthodes statistiques de contrôle de la qualité est cartes de contrôle. Il est généralement admis que l'idée de la carte de contrôle appartient au célèbre statisticien américain Walter L. Shewhart. Il a été exprimé en 1924 et décrit en détail en 1931. . Initialement, ils étaient utilisés pour enregistrer les résultats des mesures des propriétés requises des produits. Le paramètre dépassant le champ de tolérance indiquait la nécessité d'arrêter la production et d'ajuster le processus en fonction des connaissances du spécialiste qui gère la production.
Cela a donné des informations sur quand qui, sur quel équipement, a reçu le mariage dans le passé. .
Cependant, dans ce cas, la décision d'ajustement a été prise alors que le mariage était déjà obtenu. Par conséquent, il était important de trouver une procédure qui accumulerait des informations non seulement pour une étude rétrospective, mais aussi pour une utilisation dans la prise de décision. Cette proposition a été publiée par le statisticien américain I. Page en 1954. Les cartes utilisées dans la prise de décision sont dites cumulatives.
La carte de contrôle (Figure 3.5) se compose d'une ligne centrale, de deux limites de contrôle (au-dessus et en dessous de la ligne centrale) et de valeurs caractéristiques (score de qualité) tracées sur la carte pour représenter l'état du processus.
Dans certaines périodes de temps, n produits fabriqués sont sélectionnés (tous à la suite ; sélectivement ; périodiquement à partir d'un flux continu, etc.) et le paramètre contrôlé est mesuré.
Les résultats de mesure sont appliqués à la carte de contrôle, et en fonction de cette valeur, une décision est prise de corriger le processus ou de continuer le processus sans ajustements.
Un signal concernant un éventuel ajustement du processus technologique peut être:
- point dépassant les limites de contrôle (point 6); (le processus est hors de contrôle);
- la localisation d'un groupe de points successifs proches d'une frontière de contrôle, mais ne la dépassant pas (11, 12, 13, 14), ce qui indique une violation du niveau de réglage de l'équipement ;
- forte dispersion des points (15, 16, 17, 18, 19, 20) sur la carte de contrôle par rapport à la ligne médiane, ce qui indique une diminution de la précision du processus technologique.
Riz. 3.5. carte de contrôle
S'il y a un signal d'une violation du processus de production, la cause de la violation doit être identifiée et éliminée.
Ainsi, les cartes de contrôle sont utilisées pour identifier une cause spécifique, et non aléatoire.
Une cause certaine doit être comprise comme l'existence de facteurs qui permettent l'étude. Bien sûr, de tels facteurs doivent être évités.
La variation due à des causes aléatoires est nécessaire, elle se produit inévitablement dans tout processus, même si l'opération technologique est réalisée à l'aide de méthodes et de matières premières standard. L'exclusion des causes aléatoires de variation est techniquement impossible ou économiquement irréalisable.
Souvent, lors de la détermination des facteurs influençant tout indicateur de performance caractérisant la qualité, des schémas d'Ishikawa sont utilisés.
Ils ont été proposés par un professeur de l'Université de Tokyo Kaoru Ishikawa en 1953 lors de l'analyse opinions différents ingénieurs. Sinon, le schéma d'Ishikawa est appelé un diagramme de cause à effet, un diagramme en arête de poisson, un arbre, etc.
Il se compose d'un indicateur de qualité caractérisant le résultat et d'indicateurs factoriels (Fig. 3.6).
Riz. 3.6. Structure du diagramme de cause à effet
La construction des diagrammes comprend les étapes suivantes :
- sélection d'un indicateur de performance caractérisant la qualité d'un produit (processus, etc.) ;
- sélection des principales raisons affectant le score de qualité. Ils doivent être placés dans des rectangles ("gros os");
- sélection des causes secondaires (« middle bones ») influençant les principales ;
- sélection (description) des causes de l'ordre tertiaire ("petits os") qui affectent les secondaires ;
- classer les facteurs selon leur importance et mettre en évidence les plus importants.
Les diagrammes de cause à effet ont des applications universelles. Ainsi, ils sont largement utilisés pour mettre en évidence les facteurs les plus importants affectant, par exemple, la productivité du travail.
Il est à noter que le nombre de défauts importants est insignifiant et qu'ils sont généralement causés par un petit nombre de raisons. Ainsi, en découvrant les causes de l'apparition de quelques défauts essentiels, presque toutes les pertes peuvent être éliminées.
Ce problème peut être résolu à l'aide de diagrammes de Pareto.
Il existe deux types de diagrammes de Pareto :
1. Selon les résultats des activités. Ils servent à identifier le problème principal et reflètent les résultats indésirables des activités (défauts, échecs, etc.);
2. Pour des raisons (facteurs). Ils reflètent les causes des problèmes qui surviennent pendant la production.
Il est recommandé de construire de nombreux diagrammes de Pareto, en utilisant diverses manières de classer à la fois les résultats et les raisons conduisant à ces résultats. Le meilleur graphique doit être considéré comme celui qui révèle quelques facteurs essentiels, ce qui est l'objectif de l'analyse de Pareto.
La construction des diagrammes de Pareto comprend les étapes suivantes :
1. Choix du type de graphique (selon les résultats des activités ou pour des raisons (facteurs).
2. Classification des résultats (causes). Bien sûr, toute classification a un élément de convention, cependant, la plupart des unités observées de toute population ne devraient pas tomber dans la ligne « autre ».
3. Détermination de la méthode et de la période de collecte des données.
4. Élaboration d'une liste de contrôle pour l'enregistrement des données énumérant les types d'informations collectées. Il doit fournir un espace libre pour l'enregistrement graphique des données.
5. Classement des données obtenues pour chaque caractéristique testée par ordre d'importance. Le groupe "autre" doit être indiqué à la dernière ligne, quelle que soit la taille du nombre.
6. Construire un diagramme à barres (Fig. 3.7).
Figure 3.7. Relation entre les types de défauts et le nombre de produits défectueux
La construction de diagrammes de PARETO en combinaison avec un diagramme de causes et d'effets est d'un intérêt considérable.
L'identification des principaux facteurs affectant la qualité des produits permet de relier les indicateurs de qualité de la production à tout indicateur caractérisant la qualité des consommateurs.
Pour un tel couplage, il est possible d'utiliser une analyse de régression.
Par exemple, à la suite d'observations spécialement organisées des résultats du port de chaussures et du traitement statistique ultérieur des données obtenues, il a été constaté que la durée de vie des chaussures (y) dépend de deux variables: la densité du matériau de la semelle en g /cm 3 (x1) et la force d'adhérence de la semelle avec le dessus de la chaussure en kg/cm 2 (x2). La variation de ces facteurs de 84,6 % explique la variation de l'attribut résultant (facteur de correction multiple R = 0,92), et l'équation de régression est :
y = 6,0 + 4,0 * x1 + 12 * x2
Ainsi, déjà dans le processus de production, connaissant les caractéristiques des facteurs x1 et x2, il est possible de prédire la durée de vie des chaussures. En améliorant les paramètres ci-dessus, vous pouvez augmenter la période de port de chaussures. Sur la base de la durée de vie requise des chaussures, il est possible de choisir des niveaux technologiquement acceptables et économiquement optimaux de caractéristiques de qualité de fabrication.
La pratique la plus répandue consiste à caractériser la qualité du procédé étudié en évaluant la qualité du résultat de ce procédé, dans ce cas on parle de contrôle qualité des produits, des pièces obtenues dans une opération particulière. Les plus répandues sont les méthodes de contrôle discontinues, et les plus efficaces sont celles basées sur la théorie de la méthode d'observation par échantillonnage.
Prenons un exemple.
A l'usine d'ampoules, l'atelier produit des ampoules.
Pour vérifier la qualité des lampes, un ensemble de 25 pièces est sélectionné et testé sur un stand spécial (changements de tension, le stand est soumis à des vibrations, etc.). Toutes les heures, prenez des lectures sur la durée de combustion des lampes. Les résultats suivants sont obtenus:
Tout d'abord, vous devez créer une série de distribution.
Durée de combustion (x) |
fréquence (f) |
En % du total |
Intérêt accru |
|||
Ensuite, vous devez définir
1) durée moyenne de combustion des lampes :
heures;
2) La mode (option que l'on retrouve le plus souvent dans les séries statistiques). Il est égal à 6 ;
3) Médiane (une valeur située au milieu de la ligne. Il s'agit de la valeur de la ligne qui divise son nombre en deux parties égales). La médiane est également de 6.
Construisons une courbe de distribution (polygone) (Fig. 3.8).
Riz. 3.8. Répartition des lampes par durée de combustion
Définissons le périmètre :
R \u003d X max - X min \u003d 4 heures.
Il caractérise les limites de changement d'un trait variable. Signifie une déviation absolue:
heures.
Il s'agit de la mesure moyenne de l'écart de chaque valeur de caractéristique par rapport à la moyenne .
Écart-type:
heures.
Calculez les coefficients de variation :
1) dans la portée :
;
2) selon l'écart absolu moyen :
;
3) par le rapport quadratique moyen :
.
En termes de qualité des produits, les coefficients de variation doivent être réduits au minimum.
L'usine ne s'intéressant pas à la qualité des lampes témoins, mais de toutes les lampes, se pose la question du calcul de l'erreur d'échantillonnage moyenne :
heures,
qui dépend de la variabilité de l'attribut () et du nombre d'unités sélectionnées (n).
Erreur d'échantillonnage limite = t*. Le nombre de confiance t montre que l'écart ne dépasse pas un multiple de l'erreur d'échantillonnage. Avec une probabilité de 0,954, on peut affirmer que la différence entre l'échantillon et le général ne dépassera pas deux valeurs de l'erreur d'échantillonnage moyenne, c'est-à-dire que dans 954 cas, l'erreur de représentativité n'ira pas au-delà de 2
Ainsi, avec une probabilité de 0,954, le temps de combustion moyen devrait être d'au moins 5,6 heures et d'au plus 6,4 heures. Du point de vue de la qualité des produits, il faut s'efforcer de réduire ces écarts.
En règle générale, dans le contrôle statistique de la qualité, le niveau de qualité acceptable, qui est déterminé par le nombre de produits ayant réussi le contrôle et dont la qualité était inférieure à la qualité minimale acceptable, varie de 0,5 % à 1 % des produits. Toutefois, pour les entreprises qui cherchent à fabriquer des produits uniquement la plus haute qualité ce niveau peut ne pas être suffisant. Par exemple, Toyota vise à réduire le taux de défaut à zéro, en gardant à l'esprit que bien que des millions de voitures soient produites, chaque client n'en achète qu'une seule. C'est pourquoi, parallèlement aux méthodes statistiques de contrôle qualité, l'entreprise a développé des moyens simples de contrôle qualité de toutes les pièces fabriquées (TQM). Le contrôle statistique de la qualité est principalement utilisé dans les services de l'entreprise, où les produits sont fabriqués par lots. Par exemple, 50 ou 100 pièces entrent dans le plateau d'un processus automatique à grande vitesse après traitement, dont seules la première et la dernière passent l'inspection. Si les deux pièces sont exemptes de défauts, toutes les pièces sont considérées comme bonnes. Cependant, si la dernière pièce s'avère défectueuse, la première pièce défectueuse du lot sera retrouvée et l'ensemble du défaut sera supprimé. Pour s'assurer qu'aucun lot n'échappe au contrôle, la presse s'éteint automatiquement après le traitement du lot suivant de flans. L'application de l'échantillonnage statistique a un effet global lorsque chaque opération de production est effectuée de manière stable grâce au débogage minutieux des équipements, à l'utilisation de matières premières de qualité, etc.
3.6. La valeur de la normalisation
Il a été noté plus haut qu'en conditions modernes la gestion de la qualité repose en grande partie sur la normalisation. La normalisation est un mode de gestion normatif. Son impact sur l'objet s'effectue par l'établissement de normes et de règles, formalisées sous la forme document normatif et juridiquement contraignant.
Une norme est un document normatif et technique qui établit les exigences de base pour la qualité d'un produit.
Un rôle important dans la gestion de la qualité appartient aux conditions techniques (TS).
Les spécifications sont un document réglementaire et technique qui établit des normes supplémentaires aux normes nationales et, en leur absence, des exigences indépendantes pour les indicateurs de qualité des produits, ainsi que celles assimilées à ce document. description technique, recette, échantillon de référence. Les exigences prévues dans les spécifications techniques ne peuvent être inférieures à celles des normes nationales.
Le système de gestion de la qualité des produits est basé sur une normalisation complète.
Les normes déterminent la procédure et les méthodes de planification de l'amélioration de la qualité des produits à toutes les étapes du cycle de vie, établissent les exigences relatives aux moyens et aux méthodes de surveillance et d'évaluation de la qualité des produits. La gestion de la qualité des produits est effectuée sur la base des normes nationales, internationales, industrielles et des entreprises.
La normalisation par l'État agit comme un moyen de protéger les intérêts de la société et des consommateurs spécifiques et s'applique à tous les niveaux de gouvernement.
La série ISO 9000 garantit au consommateur le droit d'influencer plus activement la qualité des produits ; apporter cadre législatif qui prévoit le rôle actif du consommateur dans le processus de fabrication de produits de qualité.
ISO 9000 est utilisée pour définir les différences et les relations entre les concepts clés dans le domaine de la qualité et comme guide pour la sélection et l'application des normes ISO pour les systèmes de qualité, qui sont utilisées en interne par l'entreprise pour résoudre les tâches de gestion de la qualité (ISO 9004) .
Dans notre pays, le système national de normalisation de la Fédération de Russie (SSS) a été formé, qui comprend cinq normes principales ?
1. GOST R 1.0-92 Système de normalisation d'État de la Fédération de Russie. Dispositions de base.
2. GOST R 1.2-92 Système national de normalisation de la Fédération de Russie. La procédure d'élaboration des normes d'État.
3. GOST R 1.3-92 Système d'État de la Fédération de Russie. L'ordre de coordination, d'approbation et d'enregistrement des conditions techniques.
4. GOST R 1.4-92 Système d'État de la Fédération de Russie. Normes d'entreprise. Dispositions générales.
5. GOST R 1.5-92 Système d'État de la Fédération de Russie. Exigence généraleà la construction, la présentation, la conception et le contenu des normes.
Il existe trois normes nationales en Russie :
1. GOST 40.9001-88 "Système qualité. Un modèle d'assurance qualité dans la conception et/ou le développement, la production, l'installation et la maintenance.
2. GOST 40.9002.-88 "Système qualité. Un modèle d'assurance qualité dans la production et l'installation ».
3. GOST 40.9003-88 "Système qualité. Modèle d'assurance qualité pour l'inspection et les essais finaux ».
Les normes d'État de la Fédération de Russie comprennent les dispositions suivantes :
- les exigences relatives à la qualité des produits, des travaux, des services, à la sécurité de la vie, de la santé et des biens, à la protection de l'environnement, exigences obligatoires précautions de sécurité et assainissement industriel;
- exigences de compatibilité et d'interchangeabilité des produits;
- les méthodes de contrôle des exigences de qualité des produits, travaux et services qui assurent leur sécurité pour la vie, la santé des personnes et des biens, la protection de l'environnement, la compatibilité et l'interchangeabilité des produits ;
- propriétés de consommation et d'exploitation de base des produits, exigences en matière d'emballage, d'étiquetage, de transport et de stockage, d'élimination ;
- des dispositions garantissant l'unité technique dans le développement, la production, l'exploitation des produits et la fourniture des services, des règles garantissant la qualité, la sécurité et la utilisation rationnelle tous les types de ressources, termes, définitions et désignations et autres règles et réglementations techniques générales.
Il est important pour toute entreprise de se conformer aux normes établies et de maintenir un système de qualité à un niveau approprié.
La gestion de la qualité nécessite une approche systématique.
Le système de management de la qualité est un ensemble d'organes de gestion et d'objets, d'activités, de méthodes et de moyens de gestion visant à établir, assurer et maintenir un haut niveau de qualité des produits.
Le système de gestion de la qualité doit être conforme aux normes ISO 9000.
Le contrôle qualité implique l'identification des produits défectueux.
Un rôle important dans le contrôle de la qualité est joué par les méthodes statistiques, dont l'utilisation est requise dans les normes ISO 9000 lors de l'évaluation des systèmes de gestion de la qualité.
Dans le contrôle de la qualité, les cartes de contrôle sont utilisées avec succès. Une carte de contrôle se compose d'une ligne centrale, de deux limites de contrôle (au-dessus et en dessous de la ligne centrale) et de valeurs caractéristiques (score de qualité) tracées sur la carte pour représenter l'état du processus. Les cartes de contrôle servent à identifier une cause précise (non aléatoire).
Le schéma d'Ishikawa (diagramme des causes et des résultats) est composé d'un indicateur de qualité caractérisant le résultat et d'indicateurs factoriels.
Les diagrammes de Pareto sont utilisés pour identifier quelques défauts essentiels et leurs causes.
Questions de révision
- Lister les principales méthodes de contrôle statistique de la qualité.
- A quoi servent les cartes de contrôle Shewhart ?
- A quoi servent les diagrammes de cause à effet (diagrammes d'Ishikawa) ?
- Quelles sont les étapes de construction des diagrammes de Pareto ?
- Comment lier les indicateurs de qualité de consommation et de production ?
- Énumérez les cinq étapes principales de la gestion de la qualité.
- Quelles sont les fonctions d'un système de management de la qualité ?
- À quelles exigences un système de management de la qualité doit-il répondre ?
- Quels sont les objectifs de la politique qualité.
- Quelles sont les étapes du cycle de vie du produit ?
- A quoi servent les méthodes de contrôle statistique ?
- Nommer les caractéristiques d'un lot de produits dans le contrôle par un signe alternatif.
- Quelles tâches le contrôle d'acceptation statistique sur un attribut alternatif résout-il ?
- Parlez-nous des normes de contrôle d'acceptation statistique.
- Qu'entend-on par système de plans économiques et quelle est leur signification ?
- A quoi servent les plans d'échantillonnage continu ?
- Quel rôle jouent les cartes de contrôle dans le système des méthodes de management de la qualité ?
- À quelles fins les cartes de contrôle de U.A. Shewhart ?
- À quoi servent les diagrammes de cause à effet du schéma d'Ishikawa) ?
- Quelles sont les étapes de construction des diagrammes de Pareto ?
- Quel est le rôle de la normalisation dans la gestion de la qualité ?
- Quelles sont les normes incluses dans système d'état normalisation de la Fédération de Russie?
La gestion de la qualité en tant que processus La tâche de la gestion de la qualité se résume à l'assurance qualité. Par assurance qualité, nous entendrons le processus ou le résultat de la formation des caractéristiques requises du produit lors de sa création, ainsi que le maintien de ces caractéristiques pendant le stockage, le transport et le fonctionnement du produit. Le concept d'assurance qualité est plus large que le concept de gestion de la qualité, voir Système d'assurance qualité du produit Par gestion de la qualité, nous comprendrons l'impact sur le processus de production avec ...
Partager le travail sur les réseaux sociaux
Si cette oeuvre ne vous convient pas, il y a une liste d'oeuvres similaires en bas de page. Vous pouvez également utiliser le bouton de recherche
Conférence 5 La gestion de la qualité en tant que processus
La tâche de gestion de la qualité est réduite à l'assurance de la qualité.
Par assurance qualité, nous entendons le processus ou le résultat de la formation des caractéristiques requises du produit lors de sa création, et aussi conserver ces caractéristiques pendant le stockage le transport et l'exploitation des produits.
Qualité requiseest assurée par l'efficacité de toutes les activités nécessaires utilisant des techniques,administratifet les facteurs humains.
Le concept d'assurance qualité est plus large, que le concept de gestion de la qualité(voir Fig.1) .
Riz. une. Système d'assurance qualité des produits
Dans le cadre de la gestion de la qualité, nous comprendrons l'impact sur le processus de production afin d'assurer la qualité requise du produit.(prestations de service ) . Dans cette notion il y a trois éléments :sujet de gestion (qui influence) , objet de contrôle(sur le quelle est la direction de l'impact) et le mécanisme lui-même.
Objet de contrôle défini processus de fabrication.
Matière Système de qualité
Considérez le mécanisme, c'est à dire. technologie de contrôle.
La gestion de la qualité est assurée par la mise en œuvre de fonctions de gestion.D'après les sections précédentes, on saitque sont ils, en règle générale : planification, motivation, organisation, contrôle, information, développement d'événementsprise de décision et mise en œuvre des activités.
Ces fonctions de direction générale dans la gestion de la qualité sont représentées de la manière suivante:
- Politique de qualité;
- Planification de la qualité;
- Formation et motivation du personnel;
- Organisation d'un travail de qualité;
- Contrôle de qualité;
- Informations sur la qualité des produits,besoins du marché et progrès scientifiques et technologiques;
- Développement des mesures nécessaires;
- Prise de décision par la direction de l'entreprise;
- Mise en œuvre des activités;
- Interaction avec l'environnement extérieur résoudre les problèmes de qualité avec les fournisseurs, consommateurs organismes gouvernementaux
Ces fonctions sont étroitement liées les unes aux autres et leur mise en œuvre cohérente est un processus de gestion de la qualité des produits.
Le processus doit couvrir toutes les étapes du cycle de vie du produit.Il peut être représenté comme une boucle de qualité.
Norme internationale ISO 8402 définit : "boucle de qualité" modèle conceptuel des activités interdépendantes,affectant la qualité à différentes étapes depuis l'identification des besoins jusqu'à l'évaluation de leur satisfaction» . (voir Fig.2) .
La boucle de qualité doit montrer commentet à travers quelles activitésimpact sur la qualité à différentes étapes du cycle de vie du produit.
Ça devrait être noté,et si les résultatsun contrôle de la qualité et une analyse des informations reçues seront préparés,approuvé par la direction et mis en œuvretoutes les activités nécessairesalors le prochain cycle de contrôle doit être répétéà un niveau supérieur.Par conséquent, la boucle de qualité se transforme en ce que l'on appelle « spirale de qualité» avec une qualité de produit améliorée après chaque cycle de contrôle réussi.
Riz. 2. Boucle de qualité ( selon le cycle de vie) .
Dans la norme internationale de terminologie(ISO 8402) Deux aspects de la gestion de la qualité sont identifiés : 1. Général" gestion de la qualité; 2 ) la gestion de la qualité en tant qu'activité opérationnelle.Répartition des fonctions parles aspects identifiés de la gestion sont présentés comme suit(Voir Fig.3) :
Riz. 3. Aspects et fonctions de la gestion de la qualité
fonction "prise de décision" inclus dans les deux aspects de la gestion,selon quede quelles solutions parles-tu :stratégique ou opérationnel. Les fonctions de la gestion générale de la qualité ajustent le processus de production au mode souhaité,qui est en outre soutenu par la gestion de la qualité opérationnelle.
Il convient de noter le cycle bien connu du Dr Deming RDCA, sinon cercle de Deming, qui prévoit la mise en œuvre 4 étapes de travail
planification (PlanP);
réalisation de travaux action (Faire D );
contrôle des résultats(Vérifier C);
action corrective(Action - A );
Il convient de soulignerque la dernière étape du cycle de Deming est une action corrective.Le travail du cycle peut être effectuéjusqu'à ce que le résultat prévu soit atteint.
De cette façon, Contrôle de qualité c'est le processus d'influencer la production et les activités en général afin d'assurer la qualité.
Assurance qualité- le processus de formation de la qualité requise sous l'influence de trois facteurs principaux: technique, administratif, Humain; Contrôle de qualité- partie d'un administratif.
fonction managériale « développement d'activités» prévoit l'adoption de mesures visant à améliorerbase matérielle de production,améliorer l'organisation du travail et activer le personnel.
Considérant ce qui précède un concept plus complet: "Boucle de qualité - c'est un modèle d'impact sur le système qualitéà toutes les étapes du cycle de vie des produits et services.Cet impact est réalisé de manière cyclique par implémentation séquentielle des fonctions suivantes :politique et planification de la qualité.Formation et motivation du personnel,organisation d'un travail de qualité,développement des mesures nécessaires,prise de décisions par la direction de l'entreprise et leur mise en œuvre aux étapes appropriées du travail» .
Pour mise en œuvre du processus d'amélioration continue des activités, il est nécessaire de remplir un certain nombre de conditions,qui sont consonants 14 ces déclarations de Deming,liés à la gestion du poste de responsable qualité :
- Créer un objectif holistique d'amélioration du produit ou du service.
- L'étude d'une nouvelle philosophie.
- Établir la relation entre le contrôle du produit et l'atteinte d'une qualité supérieure.Besoin de statistiques de processus et d'ingrédients critiques entrants(détails) .
- Acquisition de matières premières et de matériaux uniquement auprès de fournisseurs dont la qualité des produits est reconnue.Cessation de la pratique d'encouragement des affaires,basé uniquement sur le prix.
- Application de méthodes statistiques pour identifier les faiblesses et l'amélioration continue du système.
- Une approche moderne de l'apprentissage en milieu de travail.
- Application méthodes modernes guides.
- Négligence de la peur.
- Exclusion de nombreux Buts.
- Révision des normes de travail pour améliorer la qualité.
- Éliminer les barrières entre les départements.
- Présentation du programmeapprendre de nouvelles compétences.
Création de la structure de direction générale,capable de se déplacer quotidiennement dans le sens de la précédente 13
Autres travaux connexes susceptibles de vous intéresser.vshm> |
|||
12568. | Gestion de la qualité des produits chez OAO Lamzur | 137.21Ko | |
L'amélioration de la qualité des produits est la direction la plus importante pour le développement intensif de l'économie, source de croissance économique et d'efficacité de la production sociale. Dans ces conditions, l'importance d'une gestion intégrée de la qualité des produits et de l'efficacité de la production augmente. Les systèmes de gestion de la qualité opérant dans diverses entreprises sont individuels. Néanmoins, la science et la pratique mondiales se sont formées caractéristiques communes de ces systèmes, ainsi que les méthodes et principes applicables à chacun d'eux. | |||
19809. | Gestion de la qualité des produits dans l'entreprise | 112.34Ko | |
Amélioration du système qualité de l'entreprise JSC Winzavod Issyk. Introduction L'un des domaines prioritaires pour le développement de l'économie kazakhe conformément à la stratégie de développement de la République du Kazakhstan jusqu'en 2020 est le développement innovant, qui est impensable sans une augmentation sérieuse de la qualité des produits. L'un des facteurs les plus importants de la croissance de l'efficacité de la production est l'amélioration de la qualité des produits ou des services fournis. Amélioration de la qualité des produits... | |||
12616. | Gestion de la qualité dans les systèmes de production et technologiques | 181.56Ko | |
La production de chaussures a été largement mécanisée, c'est-à-dire que la plupart des opérations de fabrication de chaussures, qui étaient auparavant effectuées à la main, sont désormais effectuées sur des machines semi-automatiques ou automatiques; des unités avec plusieurs opérations et lignes agrégées ont été introduites. Dans toutes les grandes usines, les produits semi-finis du processus de fabrication de chaussures sont transportés sur des convoyeurs, ce qui assure une bonne organisation du travail. | |||
2042. | Management de la qualité : sujet et objectifs du cours | 18.79Ko | |
Parlant du problème de la qualité, il convient de noter que le consommateur soutient toujours ce concept. C'est avec l'aide de méthodes modernes de gestion de la qualité que les principales entreprises étrangères ont atteint des positions de leader sur divers marchés. Les entreprises russes sont encore à la traîne dans le domaine de l'application des méthodes modernes de gestion de la qualité. Pendant ce temps, l'amélioration de la qualité apporte des opportunités vraiment colossales. | |||
16209. | -Petersburg State University of Economics and Finance Education Quality Management o | 11.56Ko | |
Vice-recteur Saint-Pétersbourg Université d'Étatéconomie et finances Gestion de la qualité de l'éducation la base d'un développement innovant de l'économie La composante la plus importante du développement économique et social du pays est son potentiel intellectuel, qui est directement déterminé par la qualité de l'éducation. La conformité des qualifications des salariés aux besoins des activités d'innovation scientifique ou de production est déterminée par la conformité des contenus et des formes du primaire supérieur. enseignement professionnel ces exigences... | |||
20937. | Audit du sous-système "Gestion des achats" du système de management de la qualité de RU NPP Agrinol LLC | 172.54Ko | |
programme de vérification. Préparer et réaliser un audit de l'adéquation du système de management de la qualité. Détermination des objectifs des critères et de la portée de l'audit d'adéquation. Plan d'audit de l'adéquation du système de management de la qualité. | |||
17473. | Le concept et la classification des coûts de production et de vente des produits. Gestion de la qualité des produits | 31.86Ko | |
Gestion de la qualité des produits Théorie générale gestion et gestion de la qualité Schéma universel de gestion de la qualité des produits. Catégorie gestion de la qualité des produits. Organismes de gestion de la qualité des produits. | |||
21342. | Le processus de gestion de votre propre capital et comment mener efficacement cette gestion | 31.52Ko | |
Le rôle du capital de l'entreprise ainsi que son utilisation efficace dans diverses relations économiques est toujours important. Cela est dû au fait que la principale source de profit pour toute entreprise de la richesse nationale du pays est l'utilisation habile, raisonnable et assez complète du capital de l'entreprise avec la découverte opportune de moyens de l'augmenter et de moyens de l'augmenter . utilisation efficace. En combinaison avec le travail humain, une efficacité maximale dans l'utilisation du capital est atteinte. Le principal problème de toute entreprise qui doit... | |||
3504. | Le processus le plus simple (Poisson), ses propriétés, ses conséquences. Processus de Poisson complexe (Poisson composite), ses caractéristiques probabilistes | 27.97Ko | |
Le processus de Poisson le plus simple et ses propriétés en sont les conséquences. Poisson composé Processus de Poisson composé et ses caractéristiques probabilistes. les fonds arrivent t temps Nt valeur aléatoire nombre de sinistres N= somme des indicateurs d'événements EN = np = ν Nt est un processus de Poisson avec ses valeurs yavl. Le processus de Poisson le plus simple (figure du bas) un processus à incréments indépendants a les propriétés suivantes : 1 stationnarité c'est-à-dire | |||
613. | Le processus chimique de la combustion. Facteurs qui assurent le processus de combustion. Principes de base de l'extinction des incendies | 10.69Ko | |
procédé chimique brûlant. Facteurs qui assurent le processus de combustion. Pour que le processus de combustion se produise, trois facteurs sont nécessaires : une substance combustible, un oxydant et une source d'inflammation. Complets avec un excès d'oxygène, les produits de combustion ne sont pas capables de s'oxyder davantage. |
La gestion de la qualité des produits est comprise comme un processus constant, systématique et ciblé d'influence des facteurs et des conditions à tous les niveaux, garantissant la création de produits de qualité optimale et leur pleine utilisation1.
Jusqu'à récemment, lors de la résolution de problèmes de qualité, les entreprises se concentraient sur le niveau technique de la qualité des produits sans tenir compte des besoins du marché.
Dans le même temps, il convient de noter que le système national de gestion de la qualité a apporté une contribution significative au développement d'approches de gestion de la qualité des produits dans le monde entier. Dans ce numéro, l'expérience nationale est prise en compte dans l'élaboration de normes internationales pour les systèmes de qualité.
Le système qualité réglementé par la norme internationale ISO 9004 couvre l'ensemble du cycle de vie d'un produit, de sa conception à son élimination, et s'applique à des éléments du système tels que le marketing, la logistique, les ventes, le service.
Une approche systématique de la gestion de la qualité des produits implique une interaction claire de tous les départements et organes de direction de l'entreprise.
Le système de management de la qualité des produits est un ensemble d'organes de gestion et d'objets, d'activités, de méthodes et de moyens de gestion visant à établir, assurer et maintenir un haut niveau de qualité des produits. Le système de gestion de la qualité des produits comprend les fonctions suivantes :
- Fonctions de gestion stratégique, tactique et opérationnelle.
- Fonctions de décision, de contrôle des actions, d'analyse et de comptabilité, d'information et de contrôle.
- Les fonctions sont spécialisées et communes à toutes les étapes du cycle de vie du produit.
- Fonctions de gestion en fonction de facteurs et conditions scientifiques, techniques, industriels, économiques et sociaux.
Conformément aux normes internationales de la série ISO 9000, une politique qualité et un système qualité lui-même sont distingués, comprenant la fourniture, l'amélioration et la gestion de la qualité des produits.
La politique qualité peut être formulée comme une ligne d'action ou un objectif à long terme et peut inclure :
- amélioration de la situation économique de l'entreprise;
- développer ou conquérir de nouveaux marchés ;
- l'atteinte d'un niveau technique de production supérieur au niveau des entreprises leaders ;
- se concentrer sur la satisfaction des exigences des consommateurs de certaines industries ou régions;
- développement de produits dont la fonctionnalité est mise en œuvre sur de nouveaux principes ;
- amélioration des indicateurs les plus importants de la qualité des produits ;
- réduire le niveau de défectuosité des produits manufacturés;
- extension des garanties des produits ;
- développement des services.
Conformément aux normes ISO, le cycle de vie du produit, appelé boucle qualité, comprend 11.
À l'aide de la boucle de qualité, la relation entre le fabricant de produits et le consommateur, avec l'ensemble du système qui apporte une solution au problème de la gestion de la qualité des produits, est réalisée.
Ainsi, l'assurance qualité produit est un ensemble d'activités planifiées et systématiques qui créent les conditions nécessaires à la mise en place de chaque étape de la "boucle qualité" afin que les produits répondent aux exigences qualité.
Dans un environnement concurrentiel, les entreprises pourront se développer avec succès en introduisant une gestion systémique de la qualité des produits. À l'heure actuelle, la demande croissante d'amélioration de la qualité des produits est l'un des traits caractéristiques développement du marché mondial.
Gestion de la qualité totale (totale) (TQC) effectuée par les entreprises Europe de l'Ouest, USA et Japon, implique trois conditions obligatoires.
- La qualité comme principal objectif stratégique les activités sont reconnues par la haute direction des entreprises. Dans le même temps, des tâches spécifiques sont définies et des fonds sont alloués pour leur solution. Étant donné que les exigences de qualité sont déterminées par le consommateur, il ne peut y avoir de niveau de qualité constant. La qualité doit constamment augmenter, car la qualité est un objectif en constante évolution.
- Les activités d'amélioration de la qualité devraient toucher tous les services sans exception. L'expérience montre que 80 à 90% des activités ne sont pas contrôlées par les services qualité et fiabilité. Attention particulière est donnée à l'amélioration de la qualité à des stades tels que la R & D, en raison d'une forte réduction du temps de création de nouveaux produits.
- Un processus d'apprentissage continu (axé sur un lieu de travail spécifique) et une motivation accrue du personnel.
Le développement moderne du système de gestion de la qualité a été le résultat de la transition de la gestion de la qualité totale (TQC) à la gestion de la qualité totale (TQM).
Si TQC est la gestion de la qualité afin de répondre aux exigences établies, alors TQM est également la gestion des objectifs et des exigences elles-mêmes. TQM comprend également l'assurance qualité, qui est interprétée comme un système de mesures qui donne au consommateur confiance dans la qualité des produits.
Le système TQM est un système complet axé sur l'amélioration continue de la qualité, la minimisation des coûts de production et la livraison juste à temps. L'idéologie principale de TQM est basée sur le principe - il n'y a pas de limite à l'amélioration. En ce qui concerne la qualité, il y a un objectif fixé - le désir de « 0 défaut », de « 0 coûts improductifs », de livraisons juste à temps. Dans le même temps, on se rend compte qu'il est impossible d'atteindre ces limites, mais il faut constamment s'y efforcer et ne pas s'arrêter aux résultats obtenus. Cette idéologie a un terme spécial - "amélioration continue de la qualité" (amélioration de la qualité).
Le système TQM utilise des méthodes de gestion de la qualité adéquates aux objectifs. L'une des principales caractéristiques du système est l'utilisation de formes et de méthodes collectives de recherche, d'analyse et de résolution de problèmes, une participation constante à l'amélioration de la qualité de toute l'équipe.
Une place particulière dans la pratique mondiale de la gestion de la qualité des produits est occupée par les cercles de qualité en tant que forme d'incitation des employés de l'entreprise à participer consciemment au processus d'amélioration de la qualité des produits, de l'image de l'entreprise et de leur propre bien-être. Les cercles de qualité sont apparus pour la première fois au Japon en 1962 et sont devenus un facteur important d'amélioration de la qualité et de la compétitivité des produits, ce qui a grandement contribué à l'avancement du Japon parmi les leaders du marché mondial des biens. Depuis la fin des années 70. le mouvement de création de cercles de qualité s'est généralisé dans de nombreux pays du monde (Hongrie, USA, France, Allemagne, Suède, Yougoslavie, etc.). Leur large diffusion a été facilitée par une propagande active, de nombreuses publications, l'organisation de conférences et de séminaires.
Un cercle de qualité est un petit groupe (de 3 à 12 personnes) d'ouvriers ou d'employés d'un unité de production qui se réunissent régulièrement (une fois par semaine) et pendant une heure (pendant les heures de travail ou non) discutent des problèmes survenus dans leur travail. Les forces collectives sous la direction du chef trouvent des moyens de résoudre les problèmes de production et de les mettre en œuvre eux-mêmes ou avec l'aide de spécialistes.
Les principaux objectifs des cercles de qualité sont :
- faciliter la contribution à la croissance et au développement de l'entreprise ;
- créer une atmosphère dans laquelle le respect de chaque membre de l'effectif est démontré ;
- activation de l'utilisation du facteur humain.
Ces dernières années, dans les pays développés, l'influence de la société sur les entreprises s'est accrue et les entreprises ont commencé à prendre de plus en plus en compte les intérêts de la société. Cela a conduit aux normes ISO 14000, qui établissent des exigences pour les systèmes de qualité en termes de protection de l'environnement et de sécurité des produits.
La certification ISO 14000 des systèmes qualité devient aussi populaire que la certification ISO 9000. L'influence de la composante humaniste de la qualité s'est considérablement accrue. L'attention des chefs d'entreprise à répondre aux besoins de leur personnel augmente.
B. Gribov, V. Gryzinov
Le concept de qualité et de gestion de la qualité
Qualité - il s'agit d'un ensemble de caractéristiques d'une entité relatives à sa capacité à satisfaire à des exigences explicites ou implicites. La qualité des produits est récemment devenue de plus en plus importante en raison de l'intégration du marché, progrès scientifique et technologique et, par conséquent, les demandes toujours croissantes des consommateurs. Il existe de nombreux paramètres qui déterminent la qualité d'un produit, et pour chacun ils sont différents, il est devenu nécessaire de développer une telle tendance en matière de gestion que la gestion de la qualité.
Contrôle de qualité - c'est l'activité de gestion de toutes les étapes du cycle de vie du produit, ainsi que l'interaction avec l'environnement externe .
La qualité des produits (services) est un certain ensemble de propriétés des produits (services) qui sont potentiellement ou réellement capables de répondre aux besoins requis dans une certaine mesure lorsqu'ils sont utilisés conformément à leur destination, y compris l'élimination ou la destruction.
La gestion de la qualité des produits (services) est un processus délibéré d'influence des objets de gestion, effectué lors de la création et de l'utilisation des produits (services), afin d'établir, d'assurer et de maintenir son niveau de qualité requis qui répond aux exigences des consommateurs et de la société en tant que ensemble.
Historique du développement des systèmes de management de la qualité
ÉTAPE 1.
première étoile correspond aux premières étapes de l'approche systémique, lorsque le premier système est apparu - Système Taylor(1905). Il a établi des exigences pour la qualité des produits (pièces) sous la forme de champs de tolérance ou de certains modèles adaptés aux limites de tolérance supérieure et inférieure - calibres de réussite et de non-réussite.
Pour assurer le bon fonctionnement du système Taylor, les premiers professionnels de la qualité ont été introduits - les inspecteurs (en Russie - les contrôleurs techniques).
Le système de motivation prévoyait des amendes pour les défauts et le mariage, ainsi que le licenciement. Le système de formation a été réduit à formation professionnelle et une formation pour travailler avec la mesure et équipement de contrôle.
Les relations avec les fournisseurs et les consommateurs ont été construites sur la base des exigences établies dans Caractéristiques(TU) dont la mise en œuvre a été vérifiée lors du contrôle de réception (entrée et sortie).
Toutes les caractéristiques ci-dessus du système Taylor en ont fait un système de gestion de la qualité pour chaque produit individuel.
ETAPE 2.
Deuxième étoile. Le système de Taylor offrait un excellent mécanisme pour gérer la qualité de chaque produit spécifique (pièce, unité d'assemblage), mais la production est un processus. Et il est vite devenu évident qu'il fallait gérer les processus. En 1924, un groupe dirigé par le Dr R.L. gestion de la qualité statistique. Il s'agit de l'élaboration des cartes de contrôle par Walter Schuhart, des premiers concepts et tableaux de contrôle de la qualité de l'échantillonnage, développés par H. Dodge et H. Romig. Ces travaux ont été le début des méthodes statistiques de gestion de la qualité, qui plus tard, grâce au Dr E. Deming, se sont largement répandues au Japon et ont eu un impact très important sur la révolution économique de ce pays. Les systèmes de qualité sont devenus plus complexes car ils ont inclus des services utilisant des méthodes statistiques. Les problèmes dans le domaine de la qualité résolus par les concepteurs, les technologues et les ouvriers sont devenus plus compliqués, car ils devaient comprendre ce que sont les variations et la variabilité, et également savoir quelles méthodes peuvent être utilisées pour parvenir à leur réduction. Une spécialité est apparue : un ingénieur qualité qui doit analyser la qualité et les défauts des produits, construire des cartes de contrôle, etc.
En général, l'accent a été déplacé de l'inspection et de la détection des défauts vers la prévention en identifiant les causes des défauts et en les éliminant sur la base de l'étude des processus et de leur gestion. La motivation au travail est devenue plus complexe, puisqu'il a été désormais tenu compte de la précision avec laquelle le processus est mis en place, de la manière dont certaines cartes de contrôle, de régulation et de contrôle sont analysées. Une formation aux méthodes statistiques d'analyse, de régulation et de contrôle s'est ajoutée à la formation professionnelle.
La relation fournisseur-consommateur est également devenue plus complexe. Les tables standard pour le contrôle d'acceptation statistique ont commencé à y jouer un rôle important.
ÉTAPE 3
Troisième étoile. Dans les années 50, le concept de gestion de la qualité totale - TQC a été mis en avant. . Son auteur était le scientifique américain A. Feigenbaum. Les systèmes TQC ont évolué au Japon en mettant davantage l'accent sur l'utilisation de méthodes statistiques et l'implication du personnel dans les cercles de qualité. Les Japonais eux-mêmes ont longtemps souligné qu'ils utilisaient l'approche TQSC, où S est statistique (statistique).
A ce stade, désigné par la troisième étoile, des systèmes qualité documentés sont apparus, établissant la responsabilité et l'autorité, ainsi que l'interaction dans le domaine de la qualité de l'ensemble de la gestion de l'entreprise, et pas seulement des spécialistes des services qualité.
Les systèmes de motivation ont commencé à se déplacer vers le facteur humain. Les incitations financières ont diminué, le moral a augmenté. Les principaux motifs d'un travail de qualité étaient le travail d'équipe, la reconnaissance des réalisations par les collègues et la direction, le souci de l'entreprise pour l'avenir de l'employé, son assurance et le soutien de sa famille.
De plus en plus d'attention est accordée à l'éducation. Au Japon et en Corée, les travailleurs étudient en moyenne de quelques semaines à un mois, y compris en autoformation. Bien sûr, l'introduction et le développement du concept TQC dans différents pays La paix a été réalisée de manière inégale. Le Japon est devenu un leader incontesté dans ce domaine, bien que toutes les idées principales de TQC soient nées aux États-Unis et en Europe. En conséquence, les Américains et les Européens ont dû apprendre des Japonais. Cependant, cette formation s'est également accompagnée d'innovations.Il convient de noter que le stade de développement d'une gestion systémique et intégrée de la qualité n'est pas passé par l'Union soviétique. De nombreux systèmes domestiques sont nés ici, et l'un des meilleurs est le système KANASPI (qualité, fiabilité, ressource dès les premiers produits), qui était certainement en avance sur son temps. Bon nombre des principes de CANARSPI sont toujours pertinents aujourd'hui. L'auteur du système était l'ingénieur en chef de l'usine d'aviation de Gorky T.F. Seifi. Il a été l'un des premiers à comprendre le rôle de l'information et des connaissances dans la gestion de la qualité, a déplacé l'accent de l'assurance qualité de la production vers la conception et a attaché une grande importance aux tests. Il est juste de considérer T. F. Seifi comme un spécialiste exceptionnel dans le domaine de la gestion de la qualité, et son nom devrait être à côté de noms tels que A. Feigenbaum, G. Taguchi, E. Schilling, H. Wadsworth.
ÉTAPE 4
4ème
étoile. Dans les années 1970 et 1980, la transition de la gestion de la qualité totale à la gestion de la qualité totale (TQM) a commencé. À cette époque, une série de nouvelles normes internationales pour les systèmes de qualité ISO 9000 (1987) sont apparues, qui ont eu un impact très important sur la gestion et l'assurance qualité. Si TQC est la gestion de la qualité afin de répondre aux exigences établies, alors TQM est également la gestion des objectifs et des exigences elles-mêmes.
TQM comprend également l'assurance qualité, qui est interprétée comme un système de mesures qui donne confiance aux consommateurs dans la qualité des produits.
Noter:
TQC-Gestion de la qualité totale ;
QA-assurance qualité ;
QPolicy-Politique Qualité ;
QPIanning-Planification de la qualité ;
QI - Amélioration de la qualité.
Le système TQM est un système complet axé sur l'amélioration continue de la qualité, la minimisation des coûts de production et la livraison juste à temps. La philosophie de base de TQM est basée sur le principe - il n'y a pas de limite à l'amélioration. En ce qui concerne la qualité, l'objectif fixé est la volonté de 0 défaut, de coûts - 0 coûts improductifs, de livraisons - juste à temps.
En même temps, on se rend compte qu'il est impossible d'atteindre ces limites, mais il faut constamment s'y efforcer et ne pas s'arrêter aux résultats obtenus. Cette philosophie a un terme spécial - "amélioration continue de la qualité" (amélioration de la qualité). Le système TQM utilise des méthodes de gestion de la qualité adéquates aux objectifs. L'une des principales caractéristiques du système est l'utilisation de formes et de méthodes collectives de recherche, d'analyse et de résolution de problèmes, une participation constante à l'amélioration de la qualité de toute l'équipe. Dans TQM, le rôle d'une personne et de la formation du personnel augmente considérablement. La motivation atteint un état où les gens sont tellement passionnés par le travail qu'ils refusent une partie de leurs vacances, restent tard au travail, continuent de travailler à la maison. Un nouveau type de travailleur est apparu : les bourreaux de travail.
La formation devient totale et continue, accompagnant les salariés tout au long de leur carrière. Les formes d'éducation évoluent de manière significative, devenant de plus en plus actives. Ainsi, on utilise des jeux d'entreprise, des tests spéciaux, des méthodes informatiques, etc.. L'apprentissage devient aussi une partie de la motivation. Car une personne bien formée se sent plus en confiance dans une équipe, est capable d'assumer un rôle de leadership et a des avantages professionnels. Développer et utiliser des techniques de développement spéciales la créativité ouvriers.
La certification des systèmes qualité pour la conformité aux normes ISO 9000 a été très largement intégrée dans la relation entre les fournisseurs et les consommateurs.
L'objectif principal des systèmes de qualité construits sur la base de la série de normes ISO 9000 est de fournir la qualité des produits requise par le client et de lui fournir la preuve de la capacité de l'entreprise à le faire. En conséquence, le mécanisme du système, les méthodes et moyens appliqués sont axés sur cet objectif. Cependant, dans la série ISO 9000, le réglage cible pour l'efficacité économique exprimé très faiblement, et la rapidité des livraisons est tout simplement absente.
Mais malgré le fait que le système ne résout pas tous les problèmes nécessaires pour assurer la compétitivité, la popularité du système se développe comme une avalanche, et occupe aujourd'hui une place forte dans le mécanisme du marché. Un signe externe indiquant si l'entreprise dispose d'un système de qualité conforme aux normes de la série ISO 9000 est un certificat de système de gestion de la qualité.
En conséquence, dans de nombreux cas, la disponibilité d'un certificat de système de gestion de la qualité pour une entreprise est devenue l'une des principales conditions de son admission aux appels d'offres pour la participation à divers projets. Le certificat pour le système de gestion de la qualité a trouvé une large application dans le secteur des assurances : puisque le certificat témoigne de la fiabilité de l'entreprise, il est souvent assorti de conditions d'assurance préférentielles : S'il existe un certificat pour un système de gestion de la qualité, les paiements d'assurance sont réduits de 25 à 50%, le % de prêt lors de l'émission de prêts est réduit de 1,5 à 2,0 fois.
Le processus de gestion de la qualité est complexe et multidimensionnel. Il implique tous les salariés de l'entreprise, des cadres supérieurs aux ouvriers ordinaires. Naturellement, le rôle principal dans ce processus appartient à la haute direction, car ce sont eux qui élaborent la stratégie et les tactiques de l'organisation, fixent les objectifs, etc. C'est la direction générale qui développe des solutions visant à améliorer la qualité des marchandises et surveille leur mise en œuvre à toutes les étapes du cycle de vie du produit.
Cependant, sans la grande motivation de chaque employé, l'entreprise ne peut pas s'attendre à produire des produits vraiment de haute qualité. Par conséquent, chaque entreprise cherche à impliquer autant que possible ses employés dans le processus de travail pour la pleine réalisation de leurs capacités intellectuelles, créatives et autres.
Mécanisme de gestion de la qualité
Le processus de gestion de la qualité ne commence pas à atelier de fabrication. Premièrement, les structures compétentes de l'entreprise (en règle générale, il s'agit du service marketing) étudient l'état du marché et font une prévision de ses besoins. Sur la base des informations reçues, les spécialistes concernés développent et lancent de nouveaux produits, tout en améliorant constamment la gamme existante de produits et services.La qualité du produit fini dépend directement des matières premières et des caractéristiques techniques de l'équipement, ainsi que du niveau de compétence des employés. Par conséquent, l'entreprise doit accorder une attention particulière au travail avec les fournisseurs, au soutien matériel de la production et recertifier régulièrement les employés.
Directement dans le processus de production, les divisions concernées de l'entreprise surveillent la conformité de la qualité des produits manufacturés aux normes prévues : les produits sont testés, les défauts de production sont identifiés et prévenus.
À toutes les étapes de la production, il y a un rapport interne constant sur la qualité des biens produits. Sur la base de ces rapports, la direction de l'entreprise fournit un soutien juridique, informationnel, logistique et financier pour garantir la qualité prévue du produit.
Normes de gestion de la qualité
L'assurance qualité est décrite dans la série de normes ISO 9000:2005. Ce document a été élaboré par l'Organisation internationale de normalisation sur la base des principes de la qualité totale. Les normes ISO ne décrivent pas la qualité réelle des produits et n'en constituent pas la garantie. Le but du document est d'aider le fabricant à standardiser le système de gestion par l'audit interne, les actions correctives, l'approche processus de la gestion de la production. En Russie, il existe des versions nationales des normes ISO élaborées par l'Institut russe de recherche pour la certification.Conformément aux exigences de l'ISO, une entreprise dans son travail doit être guidée par le consommateur et la satisfaction maximale de ses besoins et attentes. Le principe le plus important gestion de la qualité - approche processus, qui consiste à gérer le processus de création de biens et de services, et pas seulement les produits finis. Dans le même temps, il est important d'utiliser une approche systématique, car la production se compose de différentes étapes, étapes, éléments qui s'ajoutent à un système dynamique complexe. La plus grande efficacité dans le processus de gestion de la qualité est atteint précisément dans le cas d'une vue systématique des processus de production.