Cartes de contrôle. Cartes X et R
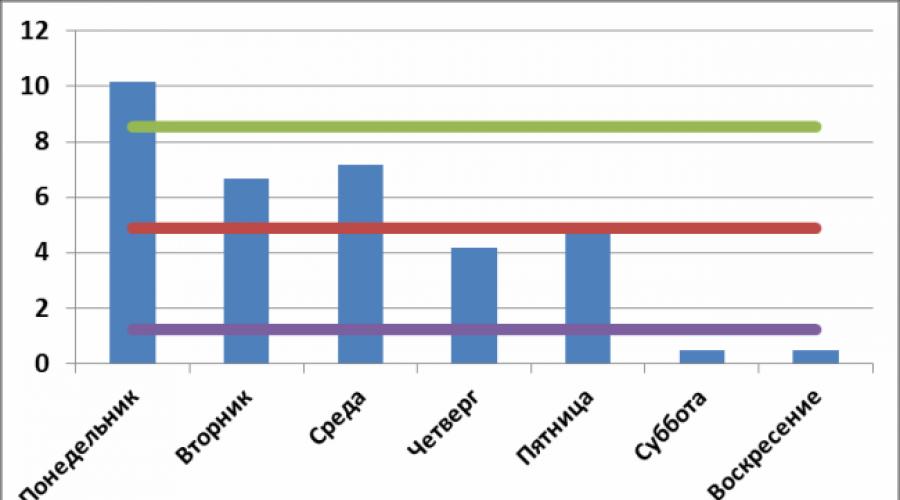
Lire aussi
J'ai récemment posté le mien ici, où assez langage clair, dans des endroits abusant d'un langage grossier, sous un rire de 20 minutes d'auditeurs, il a expliqué comment séparer les variations systémiques des variations causées par des raisons particulières.
Maintenant, je veux analyser en détail un exemple de construction d'une carte de contrôle de Shewhart basée sur des données réelles. En tant que données réelles, j'ai pris des informations historiques sur les tâches personnelles terminées. J'ai ces informations grâce à l'adaptation du modèle d'efficacité personnelle Getting Things de David Allen (j'ai aussi un vieux diaporama à ce sujet en trois parties : Partie 1, Partie 2, Partie 3 + tableau Excel avec des macros pour analyser les tâches depuis Outlook).
L'énoncé de tâche ressemble à ceci. J'ai une distribution du nombre moyen de tâches terminées en fonction du jour de la semaine (ci-dessous dans le graphique) et je dois répondre à la question : "y a-t-il quelque chose de spécial à propos du lundi ou est-ce juste une erreur système ?"
Répondons à cette question à l'aide de la carte de contrôle de Shewhart, principal outil de contrôle statistique des processus.
Ainsi, le critère de Shewhart pour la présence d'une cause spéciale de variation est assez simple : si un point dépasse les limites de contrôle, calculées d'une manière spéciale, alors il indique une cause spéciale. Si le point se situe dans ces limites, l'écart est dû aux propriétés générales du système lui-même. En gros, c'est l'erreur de mesure.
La formule de calcul des limites de contrôle ressemble à ceci :
Où
- la valeur moyenne des valeurs moyennes pour le sous-groupe,
- portée moyenne,
- un certain coefficient d'ingénierie en fonction de la taille du sous-groupe.
Toutes les formules et les coefficients tabulaires peuvent être trouvés, par exemple, dans GOST 50779.42-99, où l'approche de la gestion statistique est brièvement et clairement énoncée (honnêtement, je ne m'attendais pas moi-même à ce qu'il y ait un tel GOST. Le sujet de la gestion statistique et sa place dans l'optimisation des affaires est décrite plus en détail dans le livre de D. Wheeler).
Dans notre cas, nous regroupons le nombre de tâches terminées par jour de la semaine - ce seront les sous-groupes de notre échantillon. J'ai pris des données sur le nombre de tâches terminées pour 5 semaines de travail, c'est-à-dire que la taille du sous-groupe est de 5. En utilisant le tableau 2 de GOST, nous trouvons la valeur du coefficient d'ingénierie :
Le calcul de la valeur moyenne et de la plage (différence entre les valeurs minimale et maximale) pour un sous-groupe (dans notre cas, par jour de la semaine) est une tâche assez simple, dans mon cas, les résultats sont les suivants :
La ligne centrale de la carte de contrôle sera la moyenne des moyennes du groupe, c'est-à-dire :
Nous calculons également la portée moyenne :
Nous savons maintenant que la limite de contrôle inférieure pour le nombre de tâches terminées sera égale à :
C'est-à-dire que les jours où j'accomplis moins de tâches en moyenne sont particuliers du point de vue du système.
De même, on obtient la limite supérieure de contrôle :
Tracez maintenant la ligne médiane (rouge), la limite de contrôle supérieure (verte) et la limite de contrôle inférieure (violette) sur le graphique :
Et, ô miracle ! Nous voyons trois groupes clairement distincts hors des limites de contrôle, dans lesquels il existe des causes de variation clairement non systémiques !
Je ne travaille pas le samedi et le dimanche. Fait. Et lundi était un jour vraiment spécial. Et maintenant, vous pouvez réfléchir et rechercher ce qui est vraiment spécial le lundi.
Cependant, si le nombre moyen de tâches achevées le lundi se situait dans les limites de contrôle et même s'il se démarquait fortement par rapport à d'autres points, alors du point de vue de Shewhart et Deming, il serait inutile de rechercher des caractéristiques le lundi, car ce comportement est déterminé uniquement par des causes générales. . Par exemple, j'ai construit une carte de contrôle pendant encore 5 semaines à la fin de l'année dernière :
Et il semble qu'il y ait une sorte de sentiment que lundi se démarque d'une manière ou d'une autre, mais selon le critère de Shewhart, ce n'est qu'une fluctuation ou une erreur dans le système lui-même. Selon Shewhart, dans ce cas, vous pouvez explorer les causes particulières des lundis pendant une durée arbitrairement longue - elles n'existent tout simplement pas. Du point de vue de l'office statistique, sur ces données, le lundi n'est pas différent de n'importe quel autre jour ouvrable (même le dimanche).
40. 7 Outils de contrôle qualité. Les cartes de contrôle de Shewhart sur une base alternative : types, méthodes de construction, analyse, recommandations.
Carte de la proportion de produits défectueux (p-map). La p-map calcule la proportion de produits défectueux dans l'échantillon. Il est utilisé lorsque la taille de l'échantillon est variable.
Carte du nombre d'articles défectueux (np-map). La np-map compte le nombre d'articles défectueux dans l'échantillon. Il est utilisé lorsque la taille de l'échantillon est constante.
Carte du nombre de défauts dans l'échantillon (s-map). Dans la c-map, le nombre de défauts dans l'échantillon est compté.
Carte du nombre de défauts par article (u-map). L'u-map compte le nombre de défauts par article dans l'échantillon.
41. Contrôle d'acceptation statistique : le concept, les niveaux de défectuosité, les risques du fournisseur et du consommateur.
Contrôle statistique d'acceptation, un ensemble de méthodes statistiques permettant de surveiller la production de masse afin d'identifier sa conformité aux exigences spécifiées. P. s. à.- un moyen efficace d'assurer la bonne qualité de la production de masse.
P. s. à. est effectué sur la base d'un système (standard) de règles de contrôle qui prescrivent l'utilisation d'un plan de contrôle spécifique en fonction du nombre de produits dans le lot contrôlé, des résultats du contrôle des lots précédents, de la complexité du contrôle, etc. . La principale méthode de sélection des éléments à inspecter est la sélection aléatoire (sans retour), dans laquelle les éléments sont sélectionnés au hasard pour l'inspection, et toutes les compositions possibles de l'échantillon ont la même probabilité.
Si, selon les résultats du contrôle, les produits sont classés pour le meilleur et pour le pire, alors ils disent que le contrôle est effectué sur une base alternative. En pratique P. s. à. plans en une étape largement utilisés pour le contrôle sur une base alternative, déterminés en fixant le nombre n d'éléments sélectionnés pour le contrôle (n est la taille de l'échantillon), et ainsi de suite. nombre d'acceptation c, dont la signification est la suivante : si d - le nombre de produits défectueux trouvés dans l'échantillon - est supérieur à c, alors le lot est rejeté, mais si d £ c, alors il est accepté. Parfois, il est avantageux d'utiliser les plans en deux étapes de P. avec. k) sur une base alternative, déterminée par les volumes n1 et n2 des premier et deuxième échantillons. Si d1 est le nombre d'articles défectueux trouvés dans le premier échantillon - pas plus de c1, alors le lot est accepté, mais si d1 ³ r1(r1 > c1), alors il est rejeté. Quand c1< d1 < r1, берётся вторая выборка, включающая n2. изделий. Если же общее число d1 + d2 дефектных объектов, обнаруженных в первой и второй выборках, не более c2, то партия принимается, если же d1 + d2 >c2, alors il est rejeté. Dans certains cas, il est recommandé d'utiliser des plans de contrôle en plusieurs étapes, des plans séquentiels (voir Analyse séquentielle), etc.
Pour certaines conditions de production, le rejet d'un lot entraîne une vérification complète de tous les produits du lot afin d'en éliminer tous les produits défectueux, pour d'autres cela signifie la destruction des produits ou leur utilisation comme matière première pour la re-production (métal les produits sont refondus), etc. Lors de l'utilisation de P. avec. j. La décision d'accepter ou de rejeter est basée sur le contrôle d'une partie seulement des produits sélectionnés au hasard. Il existe donc toujours une probabilité non nulle d'accepter des lots contenant des produits défectueux. Lorsque le contrôle du produit est destructif (essais de traction, etc.), P. s. est la seule méthode possible de contrôle d'acceptation. Si les propriétés des produits ne changent pas pendant le contrôle, alors, en principe, un contrôle continu est possible. Des contrôles ponctuels approfondis des produits peuvent donner des résultats plus objectifs qu'un contrôle complet inévitablement moins approfondi (en raison de l'augmentation de la charge de travail).
Si les articles sont sélectionnés pour inspection sur la base d'une sélection aléatoire, la réponse opérationnelle du plan d'inspection peut être calculée comme étant égale à la probabilité P(D) d'accepter un lot contenant D articles défectueux.
Dans les standards de P. avec. A. indique quels types de plans il est conseillé d'utiliser pour contrôler la production de masse. Passer d'inspections avec des plans en une seule étape à des inspections plus complexes peut réduire le risque de fausse acceptation de lots contenant grand nombre objets défectueux (Fig.). Cependant, les plans autres que ceux en une seule étape sont plus difficiles tant en termes de mise en œuvre qu'en termes de méthodes pour obtenir des estimations statistiques basées sur eux pour le niveau de qualité de la production de masse.
Le problème de la surveillance actuelle de la qualité du produit dans le processus de sa production a toujours été aigu pour les fabricants. Si la surveillance de la qualité est comprise non seulement comme une vérification directe de l'adéquation d'un produit manufacturé, mais aussi comme une observation des tendances des changements de qualité, alors la tâche à accomplir semble être assez laborieuse.
Pour résoudre ces problèmes dans l'environnement de fabrication d'aujourd'hui, les responsables du contrôle qualité utilisent des techniques et des procédures basées sur analyses statistiques caractéristiques du produit.
L'un de ces outils est indispensable pour le suivi de la qualité en ligne. cartes de contrôle (ou cartes de contrôle de Shewhart), visualiser caractéristiques statistiques recherché processus de production.
Dans ce document, des exemples modèles de cartes de contrôle sont examinés et, sur la base de ceux-ci, des méthodes de détection des violations de la qualité sont démontrées.
L'approche générale du contrôle continu de la qualité est assez simple. Au cours du processus de production, des mesures aléatoires des produits sont effectuées. Après cela, des diagrammes de la variabilité des valeurs d'échantillon des spécifications prévues dans les échantillons sont construits sur le graphique (carte), et le degré de leur proximité avec les valeurs spécifiées est pris en compte. Si les graphiques montrent que les valeurs échantillonnées sont en tendance, ou si les valeurs échantillonnées sont en dehors des limites spécifiées, le processus est alors considéré comme hors de contrôle et les actions nécessaires sont prises pour trouver la cause du trouble. .
Critères de la série sert à mettre en évidence les tendances systématiques dans l'emplacement des points de la carte de contrôle, ce qui peut indiquer un désordre dans le processus contrôlé.
Commande par fonction continue
Pour le contrôle qualité en continu (analyse de la variabilité des paramètres), des cartes X-bar, R ou S sont généralement utilisées.
Les valeurs moyennes de l'échantillon sont tracées sur la carte X-bar afin de contrôler l'écart de la variable continue par rapport à la moyenne.
Les valeurs des plages d'échantillons sont tracées sur la carte R de contrôle pour contrôler le degré de variabilité du paramètre continu, et des graphiques des écarts-types et des variances des échantillons sont tracés sur les cartes S et S2, respectivement.
Image 1
Cet exemple (voir Figure 1) illustre les cartes de contrôle d'un "bon" processus. Les points sur les deux cartes de contrôle sont dans les limites de contrôle. Dans le même temps, aucun changement systématique (tendance) ni aucun autre signe de perte de contrôle du processus ne sont observés : les points des deux cartes fluctuent de manière uniforme (au moins sur la base d'une analyse visuelle) par rapport aux lignes médianes correspondantes.
La valeur moyenne du sixième échantillon est assez proche de la limite de contrôle inférieure, cependant, dans le contexte d'une image généralement positive, ce n'est pas un événement alarmant. La contrôlabilité du processus est également confirmée par un bon ajustement des histogrammes des moyennes d'échantillons observés et des plages de la distribution normale théorique (histogrammes sur le côté gauche de la figure).
Figure 2
Dans l'exemple suivant, la figure ci-dessus montre les "mauvaises" cartes de contrôle. On voit clairement que le procédé est mal maîtrisé : les moyennes d'échantillonnage des 1er et 4ème échantillons sont en dehors des limites de contrôle. Le fait que six des sept moyennes d'échantillons se trouvent du même côté de la ligne médiane est également alarmant.
De plus, l'histogramme de la distribution des moyennes de l'échantillon (graphique supérieur gauche) indique une discordance dans le processus de production, montrant une nette différence dans la distribution des moyennes par rapport à la normale.
Il convient également de noter qu'avec des valeurs aberrantes explicites sur la carte X-bar, les valeurs des plages d'échantillonnage (R-map) se situent dans les limites de contrôle.
figure 3
À cet exemple les cartes de contrôle (voir Figure 3) montrent la situation inverse. Les valeurs moyennes des échantillons (points sur la carte X-bar) se situent dans les limites de contrôle, alors qu'il existe une valeur aberrante sur la carte R-range (la plage du deuxième échantillon est supérieure à la limite de contrôle supérieure). Grandes valeurs dans un échantillon avec une plage critique, ils diminuent avec de petites valeurs, ce qui fait que la valeur moyenne de l'échantillon se situe dans la plage normale. Il convient également de noter un léger décalage systématique sur la carte moyenne, mais avec un petit nombre d'échantillons et une plage critique de valeurs, un tel décalage peut être considéré comme non significatif à ce stade de l'étude.
En conséquence, dans une telle situation, des mesures sont nécessaires pour réduire la propagation des valeurs du paramètre à l'étude, puis procéder à une analyse plus approfondie des moyennes de l'échantillon.
Figure 4
Dans l'exemple suivant (voir Figure 4), vous pouvez à nouveau observer la présence de valeurs aberrantes sur la carte X-bar et leur absence sur la carte des plages. Cependant, le résultat le plus révélateur dans cet exemple est la présence d'une tendance perceptible sur les deux cartes : positive sur la carte moyenne et négative sur la carte des plages. Une diminution systématique des valeurs des plages d'échantillonnage signifie la convergence du processus (diminution de la dispersion des valeurs). Il semblerait que ce soit une évolution positive. Mais, avec une tendance positive dans les valeurs des moyennes, le processus converge très probablement vers une valeur située en dehors des limites de contrôle. En conséquence, dans un court laps de temps, toutes les mesures du paramètre à l'étude peuvent être en dehors des valeurs de spécification.
Contrôle qualité par attribut
Un autre type de cartes de contrôle sont les cartes par attribut (attribut) - par exemple, par le nombre de pièces défectueuses dans un lot, par le nombre d'écarts des caractéristiques du produit par rapport à la norme par échantillon.
L'avantage des cartes de contrôle basées sur les attributs est la possibilité d'obtenir rapidement idée générale sur divers aspects de la qualité du produit analysé; c'est-à-dire que, sur la base de divers critères de qualité, l'ingénieur peut immédiatement accepter ou rejeter le produit.
Les cartes de contrôle attributives permettent parfois de se passer d'instruments de précision coûteux et de procédures de mesure chronophages. De plus, ce type de carte de contrôle est plus compréhensible pour les gestionnaires qui ne comprennent pas les subtilités des méthodes de contrôle de la qualité. Ainsi, à l'aide de ces cartes, il est possible de démontrer de manière plus convaincante à la direction qu'il existe des problèmes de qualité des produits.
Cependant, par rapport aux cartes de contrôle des attributs, les cartes pour les variables continues sont plus sensibles. De ce fait, les cartes de contrôle des variables continues peuvent indiquer l'existence d'un problème de détérioration avant l'apparition de vrais produits défectueux dans le flux de produits, qui sont identifiés à l'aide de la carte de contrôle par attribut.
Les cartes de contrôle des variables continues peuvent être considérées comme des précurseurs de problèmes de détérioration de la qualité, avertissant de leur présence bien avant que le taux de défauts n'augmente fortement dans le processus de fabrication.
Pour contrôler la qualité des produits par attribut, les types de cartes suivants sont généralement utilisés :
- C-carte
- Carte U
- carte np
- Carte P
Lors de l'utilisation de cartes C et U, on suppose que les défauts dans les performances contrôlées des produits sont relativement rares et les limites de contrôle pour ces types de cartes sont calculées sur la base des propriétés de la distribution de Poisson (distribution des événements rares).
À leur tour, les limites de contrôle pour les cartes Np et P sont calculées en fonction de la distribution binomiale et non de la distribution des événements rares. Par conséquent, ce type de carte doit être utilisé lorsque la découverte d'un défaut n'est pas un événement rare (par exemple, survient dans plus de 5 % des articles testés).
Dans le même temps, les cartes C et Np affichent le nombre de défauts (dans un lot, par jour, par machine), et les cartes U et P affichent la fréquence relative des défauts, c'est-à-dire le rapport de le nombre de défauts détectés au nombre d'unités de production testées.
Figure 5
La figure ci-dessus est un exemple de P-map par attribut. Sur la base de l'analyse visuelle du graphique, on peut conclure que ce processus est contrôlable : il n'y a pas de valeurs en dehors des limites de contrôle (valeurs aberrantes), il n'y a pas de tendance perceptible et il n'y a pas de tendances systématiques dans l'emplacement des points. Sur la carte.
Figure 6
Contrairement au graphique précédent, cette P-map (voir Figure 6) montre un "mauvais" processus. Dans les sixième et septième échantillons, plus de 80 % de produits défectueux sont trouvés, ce qui est supérieur aux limites de contrôle prédéfinies. Naturellement, un pourcentage aussi élevé de rejet de produit indique la présence de sérieux problèmes de qualité dans ce processus de production.
Figure 7
La P-map suivante (voir Figure 7) fournit également un exemple de "mauvais" processus. De plus, en plus de la valeur aberrante du dernier échantillon (80 % de défauts), on observe une augmentation systématique du pourcentage de produits défectueux.
Semblable aux méthodes démontrées, une analyse de la qualité visuelle est effectuée sur la base d'autres cartes par attribut. Voici quelques exemples de contrôles de qualité actuels basés sur la charte C.
Figure 8
Cette C-map montre un processus de fabrication bien contrôlé : la quantité de produits défectueux dans chaque échantillon est dans les limites de contrôle.
Figure 9
Et dans cet exemple (voir Figure 9), il y a une valeur aberrante sur la C-map (premier échantillon). Cependant, les statistiques correspondantes pour le reste des échantillons se situent dans les limites de contrôle. Ainsi, sur la base de cette carte, en excluant le premier échantillon, on peut considérer que le processus est contrôlable. Si l'échantillon du problème reflète le début du vrai processus technologique, alors, très probablement, sa qualité insatisfaisante est associée au réglage initial du processus. Dans ce cas, il est recommandé de procéder à une analyse complémentaire de la qualité des produits fabriqués à stade initial et, en excluant la valeur aberrante existante, reconnaître le processus comme gérable.
Sommaire
En conclusion, je voudrais souligner à nouveau haute efficacité application des cartes de contrôle dans la gestion de la qualité. Utilisant des moyens appropriés graphique, l'œil humain est capable de détecter des signes de dégradation de la qualité et des tendances inquiétantes dans la production en ligne.
Dans le même temps, un package d'analyse puissant, tel que STATISTIQUES, est capable d'assumer presque tout le travail de détection des signes d'un désordre de processus technologique en mode en ligne, ne laissant à l'opérateur que l'analyse des critères les plus sophistiqués pour le contrôle visuel de la qualité (petites tendances).
Avant de procéder à la construction directe des cartes de contrôle, familiarisons-nous avec les principales étapes de la tâche. Ainsi, compte tenu du fait que différents auteurs poursuivent leurs propres objectifs, décrivant la construction des cartes de contrôle, la vision originale des étapes de construction des cartes de contrôle de Shewhart sera présentée ci-dessous.
Algorithme de construction des cartes de contrôle de Shewhart :
I. Analyse de processus.
Tout d'abord, il est nécessaire de poser une question sur le problème existant, car, en l'absence de ceux-ci, l'analyse n'aura pas de sens. Pour plus de clarté, vous pouvez utiliser le diagramme cause-effet d'Ishikawa (mentionné plus haut, ch. 2). Pour sa compilation, il est recommandé d'impliquer des employés de différents départements et d'utiliser réflexion. Après une analyse approfondie du problème et la découverte des facteurs qui l'influencent, nous passons à la deuxième étape.
II. Sélection de processus.
Après avoir clarifié à l'étape précédente les facteurs influençant le processus, après avoir dessiné un squelette détaillé du «poisson», il est nécessaire de choisir le processus qui fera l'objet de recherches ultérieures. Cette étape est très importante car choisir les mauvais indicateurs rendra l'ensemble de la carte de contrôle moins efficace du fait de l'examen d'indicateurs non significatifs. À ce stade, il convient de réaliser que le choix du processus et de l'indicateur appropriés détermine le résultat de l'ensemble de l'étude et les coûts qui y sont associés.
Voici quelques exemples d'indicateurs possibles :
Tableau 1. L'utilisation des cartes de contrôle dans les organisations de services
Source Evans J. Gestion de la qualité : manuel. Allocation/J. Evans.-M. : Unity-Dana, 2007.
Dans ce cas, l'indicateur doit être choisi en fonction de objectif principal entreprises, à savoir répondre aux besoins des clients. Lorsque le processus et l'indicateur qui le caractérise sont sélectionnés, vous pouvez procéder à la collecte des données.
III. Collecte de données.
Le but de cette étape est de collecter des données sur le processus. Pour ce faire, il est nécessaire de concevoir la manière la plus appropriée de collecter des données, de savoir qui et à quelle heure prendra les mesures. Si le processus n'est pas doté de moyens techniques pour automatiser la saisie et le traitement des données, il est possible d'utiliser l'un des sept des moyens simples Ishikawa - listes de contrôle. Les fiches de contrôle sont en fait des fiches d'enregistrement du paramètre étudié. Leur avantage réside dans la facilité d'utilisation et la facilité de formation des employés. S'il y a un ordinateur sur le lieu de travail, il est possible de saisir des données à l'aide des produits logiciels appropriés.
En fonction des spécificités de l'indicateur, la fréquence, le moment de la collecte et la taille de l'échantillon sont déterminés pour assurer la représentativité des données. Les données collectées constituent la base d'opérations et de calculs ultérieurs.
Après avoir collecté des informations, le chercheur doit décider de la nécessité de regrouper les données. Le regroupement détermine souvent les performances des cartes de contrôle. Ici, à l'aide de l'analyse déjà effectuée à l'aide du diagramme de cause à effet, il est possible d'établir des facteurs par lesquels il sera possible de regrouper les données de la manière la plus rationnelle. Il convient de noter que les données au sein d'un groupe doivent avoir peu de variabilité, sinon les données peuvent être mal interprétées. De plus, si le processus est divisé en parties par stratification, chaque partie doit être analysée séparément (exemple : la fabrication des mêmes pièces par des ouvriers différents).
Changer la façon dont le groupement changera les facteurs qui forment la variation au sein du groupe. Il est donc nécessaire d'étudier les facteurs influençant l'évolution de l'indicateur afin de pouvoir appliquer le bon regroupement.
IV. Calcul des valeurs de la carte de contrôle.
Les cartes de contrôle de Shewhart sont divisées en quantitatives et qualitatives (alternatives) en fonction de la mesurabilité de l'indicateur étudié. Si la valeur de l'indicateur est mesurable (température, poids, taille, etc.), des cartes de la valeur de l'indicateur, des plages et des doubles cartes de Shewhart sont utilisées. Au contraire, si l'indicateur ne permet pas l'utilisation de mesures numériques, utilisez des types de carte pour une fonctionnalité alternative. En effet, les indicateurs étudiés sur cette base sont définis comme satisfaisant ou non aux exigences. D'où l'utilisation de cartes pour la proportion (nombre) de défauts et le nombre de conformités (incohérences) par unité de production.
Pour tout type de cartes de Shewhart, il est supposé définir les lignes centrale et de contrôle, où la ligne centrale (CL-limite de contrôle) représente en fait la valeur moyenne de l'indicateur, et les limites de contrôle (UCL-limite de contrôle supérieure ; LCL- limite de contrôle inférieure) sont les valeurs de tolérance admissibles.
Les valeurs des limites de contrôle supérieure et inférieure sont déterminées par les formules pour différents types graphiques, comme on peut le voir sur le schéma de l'annexe 1. Pour les calculer, afin de remplacer des formules encombrantes, des coefficients issus de tables spéciales sont utilisés pour construire des cartes de contrôle, où la valeur du coefficient dépend de la taille de l'échantillon (annexe 2) . Si la taille de l'échantillon est grande, on utilise des cartes qui fournissent les informations les plus complètes.
A ce stade, le chercheur doit calculer les valeurs de CL, UCL, LCL.
V. Construction d'une carte de contrôle.
Nous sommes donc arrivés au processus le plus intéressant - une réflexion graphique des données obtenues. Ainsi, si les données ont été saisies dans un ordinateur, puis en utilisant l'environnement du programme Statistica ou Excel, vous pouvez afficher rapidement les données sous forme graphique. Cependant, il est possible de construire une carte de contrôle et, sans programmes spéciaux, puis, le long de l'axe OY des cartes de contrôle, nous traçons les valeurs de l'indicateur de qualité, et le long de l'axe OX, les points temporels d'enregistrement du valeurs, dans l'ordre suivant :
1. tracer la ligne médiane (CL) sur la carte de contrôle
2. dessiner des bordures (UCL; LCL)
3. Nous reflétons les données obtenues au cours de l'étude en appliquant un marqueur approprié au point d'intersection de la valeur de l'indicateur et du moment de son enregistrement. Il est recommandé d'utiliser différents types de marqueurs pour les valeurs situées à l'intérieur et à l'extérieur des limites de tolérance.
4. En cas d'utilisation de cartes doubles, répétez les étapes 1 à 3 pour la deuxième carte.
VI. Vérification de la stabilité et de la contrôlabilité du processus.
Cette étape est conçue pour nous montrer pourquoi la recherche a été menée - si le processus est stable. La stabilité (contrôlabilité statistique) est comprise comme un état dans lequel la répétabilité des paramètres est garantie. Ainsi, le processus ne sera stable que si les cas suivants ne se produisent pas.
Considérez les principaux critères d'instabilité du processus :
1. Dépasser les limites de contrôle
2. Série - un certain nombre de points, invariablement d'un côté de la ligne médiane - (en haut) en bas.
Une série de sept points est considérée comme anormale. De plus, la situation doit être considérée comme anormale si :
a) au moins 10 points sur 11 se trouvent du même côté de la ligne médiane ;
b) au moins 12 points sur 14 se trouvent du même côté de la ligne médiane ;
c) au moins 16 points sur 20 sont du même côté de la ligne médiane.
3. tendance - une courbe continuellement croissante ou décroissante.

4. s'approcher des limites de contrôle. Si 2 ou 3 points sont très proches des limites de contrôle, cela indique une distribution anormale.

5. en s'approchant de la ligne médiane. Si les valeurs sont concentrées près de la ligne centrale, cela peut indiquer un mauvais choix de méthode de regroupement, ce qui rend la plage trop large et conduit à un mélange de données avec différentes distributions.

6. périodicité. Lorsque, après certains intervalles de temps égaux, la courbe va soit "décroître", soit "monter".

VII. Analyse des cartes de contrôle.
Les actions ultérieures sont basées sur la conclusion concernant la stabilité ou l'instabilité du processus. Si le processus ne répond pas aux critères de stabilité, l'influence des facteurs non aléatoires doit être réduite et, en collectant de nouvelles données, une carte de contrôle doit être construite. Mais, si le procédé répond aux critères de stabilité, il est nécessaire d'évaluer les capabilités du procédé (Cp). Plus la dispersion des paramètres dans les limites de tolérance est faible, plus la valeur de l'indicateur de capabilité du processus est élevée. L'indicateur reflète le rapport entre la largeur du paramètre et le degré de sa dispersion. Kruglov M.G., Shishkov G.M. La gestion de la qualité telle qu'elle est / M.G. Kruglov, G.M. Shishkov.- M.: Eksmo, 2006. L'indice d'opportunité est calculé comme, où peut être calculé comme.

Si l'indice calculé est inférieur à 1, le chercheur doit améliorer le processus, soit arrêter la production du produit, soit modifier les exigences du produit. Avec valeur d'index :
Épouser<1 возможности процесса неприемлемы,
Cð=1 le processus est à la limite des capacités requises,
Cp>1 le processus satisfait le critère de possibilité.

S'il n'y a pas de décalage par rapport à la ligne centrale Cp=Cpk , où. Ces deux indicateurs sont toujours utilisés ensemble pour déterminer l'état du processus, donc en génie mécanique, il est considéré comme la norme, ce qui signifie que la probabilité de non-conformité ne dépasse pas 0,00006.
Maintenant, après avoir considéré l'algorithme de construction des cartes de contrôle, nous allons analyser un exemple spécifique.
Tâche : la teneur en chrome des pièces moulées en acier est contrôlée. Les mesures sont effectuées dans quatre maillots de bain. Le tableau 2 montre les données de 15 sous-groupes. Vous devez construire une carte.
Solution : Comme on sait déjà à l'avance quel type de carte doit être construit, nous calculons les valeurs
numéro de sous-groupe |
||||||

L'étape suivante consiste à calculer où, selon le schéma ci-dessus également. Maintenant, ayant les valeurs de la ligne centrale, la valeur moyenne de l'indicateur et l'écart moyen, nous trouverons les valeurs des limites de contrôle des cartes.
Où est selon le tableau des coefficients de calcul des lignes des cartes de contrôle et est égal à 0,729. Alors UCL=0.880 , LCL=0.596.
Pour les valeurs, les limites de contrôle inférieure et supérieure sont déterminées par les formules :
où et se trouvent selon le tableau des coefficients de calcul des lignes des cartes de contrôle et sont respectivement égaux à 0,000 et 2,282. Alors UCL=0,19*2,282=0,444 et LCL=0,19*0,000=0.
Construisons des cartes de contrôle pour les moyennes et les plages de cet échantillon à l'aide d'Excel :


Comme nous pouvons le vérifier, les cartes de contrôle n'ont pas révélé de valeurs non aléatoires, de limites hors contrôle, de séries ou de tendances. Cependant, le graphique des valeurs moyennes tend vers la position centrale, ce qui peut indiquer à la fois des limites de tolérance mal choisies, une distribution anormale et une instabilité du processus. Pour s'en assurer, nous calculons l'indice de capabilité du processus. , où vous pouvez calculer comment, selon le tableau des coefficients, nous trouvons une valeur égale à ;


Puisque l'indice calculé<1, что свидетельствует о неприемлемости возможностей процесса, его статистической неуправляемости и не стабильности. Необходимо провести усовершенствования процесса, установить контроль над его протеканием, с целью уменьшения влияния не случайных факторов.