Types de plaques de distillation. Plateau Colonne de Distillation
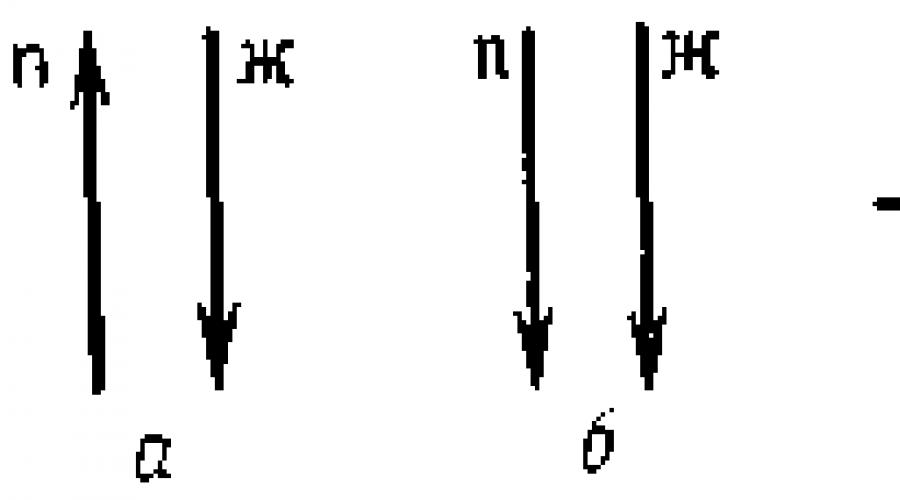
Lire aussi
Des appareils sont utilisés pour effectuer le processus de rectification. divers modèles principalement de type colonne. Selon le type de dispositifs de contact, on distingue les dispositifs à buse, à plaque et à film. Le domaine d'application de certains appareils est déterminé par les propriétés des mélanges à séparer, le débit, etc.
Riz. 6.9.1. Appareils à colonne des principaux types:
a - emballage ; b - plaque; dans - film; 1 - corps de l'appareil ; 2 - distributeur ; 3 - réseau restrictif; 4 - buse; 5 - grille de support; 6 - plaque; 7 - dispositif de transfert ; 8 - surface de contact.
Riz. 6.9.2. Les principaux schémas de circulation des flux de vapeur et de liquide dans la zone de contact:
a - contre-courant; b - flux vers l'avant ; c - courant croisé.
Selon la méthode d'organisation du mouvement relatif des flux de contact de liquide et de vapeur, les dispositifs de contact se distinguent par un mouvement de phase à contre-courant, à flux direct et à flux croisé (Fig. 6.9.2). Quel que soit le schéma de mouvement d'écoulement dans un dispositif de contact séparé (étape de contact), en règle générale, un contre-courant de vapeur et de liquide est effectué dans tout l'appareil.
Colonnes garnies ont trouvé une application dans les cas où il est nécessaire d'assurer une faible rétention de liquide dans la colonne, une faible perte de charge, ainsi que pour une production à petite échelle. Des types de garnissage (anneaux Pall, métal perforé, filets, etc.) ont été créés, qui se sont avérés assez efficaces dans les colonnes de grand diamètre.
Les principaux types de buses. Les buses sont des corps solides diverses formes, qui sont chargés dans le corps de colonne en vrac ou posés d'une certaine manière. La surface développée des garnissages provoque une importante surface de contact entre la vapeur et le liquide. De nombreuses modifications constructives des corps garnis sont connues, dont les principaux types sont représentés sur les Fig. 6.9.3.
Anneaux Raschig en divers matériaux, ce qui garantit la polyvalence de leur utilisation pratique. Cependant, les anneaux Raschig ont des performances relativement faibles et une résistance relativement élevée. Ce dernier limite leur utilisation pour procédés sous vide. Création de diverses modifications des anneaux Raschig - anneaux Pall, anneaux Borade et autres ont permis d'obtenir de meilleures performances qu'avec les anneaux Raschig.
Riz. 6.9.3. Éléments de buses irrégulières :
1-4 - Anneaux Raschig, Lessing, Pall et anneaux à cloisons cruciformes; 5, 6 - ressorts ronds et trièdres; 7, 9 – Buses Intallox en céramique et en métal embouti ; 8 - Buse Berl
En raison de la nécessité de créer des garnissages à faible résistance hydraulique, diverses options de garnissage régulier de corps de garnissage, de garnissages en blocs, ainsi que de garnissages à partir de mailles de différentes conceptions ont été développées.
Les garnissages réguliers comprennent les garnissages dont la disposition des éléments dans le volume de la colonne est soumise à un certain ordre géométrique qui crée des canaux ordonnés pour le passage des éléments. Des exemples de telles buses sont illustrés à la Figure 6.9.4.
Éléments d'une tuyère plan-parallèle 1 peuvent être constitués de planches, de verre, de plaques de métal ou de treillis.
Buse Sulzer 2 se compose de couches alternées de treillis ondulé ou de tôle perforée, avec des ondulations dans les couches adjacentes tournées dans la direction opposée.
Buse Goodlow 3 (parfois appelée buse de Panchenkov) est une spirale enroulée à partir d'un bas en maille. Dans une colonne, de tels emballages torsadés sont empilés en couches. Le flux de vapeur qui les traverse passe à travers les fentes entre les couches de maille.
Buse pack inclinée 4
représente des emballages rectangulaires à partir de couches de mailles de bonneterie qui y sont posées, qui sont installées à un angle de 45 à 60 ° les unes par rapport aux autres (ou verticalement).
Riz. 6.9.4. Pièces jointes régulières :
1 - plan parallèle; 2 - Sulzer ; 3 - Goodlow ; 4 - lot avec sections inclinées
Les principales caractéristiques dimensionnelles des garnissages sont la surface spécifique et le volume libre. Sous la surface spécifique de la buse F comprendre la surface totale de tous les corps emballés dans une unité de volume de l'appareil. L'unité SI est m 3 /m 3. Plus la surface spécifique du garnissage est grande, plus son efficacité est élevée, mais plus la résistance hydraulique est élevée et plus la productivité est faible.
Par volume libre du garnissage ε on entend le volume total de vides entre les corps garnis par unité de volume de l'appareil. L'unité SI est m 3 /m 3. Plus le volume libre de la buse est grand, plus ses performances sont élevées, moins de résistance et d'efficacité. Avec une augmentation de la taille des corps emballés, la productivité augmente, mais en même temps l'efficacité de séparation diminue.
Riz. 6.9.5. Distributeurs de liquide :
7 - plaque perforée; 2 - plaque avec tuyaux de dérivation; 3 - plaque avec réflecteurs à jet inclinés; 4 - liqueur mère de pulvérisation sous pression
Pour éviter que le liquide ne se répande sur les parois de la colonne, le garnissage est chargé dans la colonne en couches séparées de 1,5 à 3 m de haut Des distributeurs de différentes conceptions sont installés entre les couches du garnissage (Fig. 6.9.5).
La buse est posée sur les grilles et plaques de distribution porteuses. La section libre de tels dispositifs doit être la plus grande possible et se rapprocher de la valeur du volume libre du garnissage. Pour que la buse fonctionne efficacement, la surface de l'élément de buse doit être bien mouillée par le liquide.
Hydraulique à colonne garnie. En fonction des charges de la colonne en vapeur et en liquide, la nature de l'interaction entre elles change, ce qui détermine la vitesse limite de vapeur dans la colonne à garnissage. A certaines valeurs de charges de vapeur et de liquide, la quantité de liquide retenue dans le garnissage et la résistance hydraulique de la couche de garnissage augmentent fortement. Ce mode est appelé inondation de la colonne et est considéré comme la limite supérieure de son fonctionnement stable.
Colonnes à disques. Dans les colonnes à plateaux, la vapeur (ou le gaz) traverse une couche de liquide sur le plateau. Dans ce cas, la vapeur est décomposée en petites bulles et jets, qui se déplacent à grande vitesse dans le liquide. Un système gaz-liquide se forme, appelé mousse. Le fonctionnement de la colonne à plateaux est illustré sur la figure.
Riz. 6.9.7. Types principaux plaques de distillation:
I - défaillance du réseau ; II - le maillage a échoué ; III - tamis à flux croisés; IV - bouchon (a, b, c - capsule, tunnel et bouchons rainurés); V - à partir d'éléments en forme de S; VI - vanne (a, b, c, d); VII - jet (a, b); VIII - vortex (a - dispositif de l'élément vortex); 1 - corps de colonne ; 2 - toile (base) de la plaque; 3 - trous pour le passage des vapeurs ; 4 - tuyaux de trop-plein; 5 - poches de segment de vidange; 6 - plaques de drainage (cloisons); 7 - buses à vapeur; 8 - casquettes; 9 - soupapes; 10 - limiteurs de levée de soupapes; 11, 12 - coudes en forme de la bande de plaque; 13 - encoches de l'élément vortex ; 14 - réflecteurs (p et l - sens de circulation de la vapeur et du liquide)
Les principaux modèles de plaques de distillation sont représentés schématiquement sur la fig. 6.9.7.
Le plus simple d'entre eux est plaque défaillante du réseau(Fig. 6.9.7, je), dont la bande présente des rangées de fentes géométriquement ordonnées (d'une taille d'environ 10 x 150 mm), à travers lesquelles la vapeur passe vers le haut, bouillonnant à travers la couche de liquide sur la plaque, et à travers lesquelles une partie du liquide en excès s'écoule (tombe) dans jets sur la plaque sous-jacente.
Une telle plaque est très sensible aux variations de la charge liquide, avec des variations de 20 à 30% par rapport à celle calculée, la plaque peut soit s'étouffer, soit ne pas retenir une couche de liquide sur la toile. Le même effet se produira également lorsque la charge fluctue par paires.
Plaque ondulée perforée(Fig. 6.9.7, II) est un réseau amélioré. Sa toile n'a pas de lacunes, mais des trous d'un diamètre de 10-15 mm. Le profil en coupe de la toile est sinusoïdal. Cela permet de séparer les zones de passage de vapeur prépondérantes (coudes supérieurs de la plaque) et de vidange de liquide (coudes inférieurs de l'âme de la plaque). La couche de liquide sur le plateau est maintenue au-dessus des plis supérieurs et donc la vapeur bouillonne à travers cette couche. Le plateau est conçu pour les colonnes de petit diamètre et est utilisé dans les colonnes de stabilisation de l'essence et de séparation des gaz d'hydrocarbures.
Les deux plaques ( je et II En figue. 6.9.7.) sont défaillants, et la colonne avec de tels plateaux fonctionne en mode contre-courant de vapeur et de liquide. Le reste de ceux représentés sur la Fig. 6.9.7 les plaques sont à flux croisés, c'est-à-dire le liquide sur eux ne se déplace pas vers le flux de vapeur, mais perpendiculairement ou sous un angle proche d'un droit.
Selon l'importance de la charge liquide, son écoulement de plaque à plaque est effectué par un, deux ou plusieurs flux (Fig. 6.9.8).
Riz. 6.9.8. Schémas des écoulements de liquide sur plaques avec dispositifs de débordement :
a - monothread ; b - double flux ; c - trois flux ; g - quatre flux ; e - avec un mouvement annulaire du liquide; e - avec mouvement unidirectionnel de liquide sur des plaques adjacentes ; g, h - type cascade; et - avec une cloison de drainage en forme de faucille.
Le plus simple de ces types de plaques est tamis (perforé) plaque tangentielle. Sa toile présente des trous d'un diamètre de 4 à 12 mm sur toute la surface, à l'exception de deux segments opposés, où se trouvent les tuyaux de drainage. Ces tuyaux sont surélevés au-dessus de la tôle du plateau à une hauteur de 20 à 40 mm (la hauteur du drain est la hauteur de la couche de liquide bouillonnant sur le plateau), et leur autre extrémité (inférieure) n'atteint pas la tôle du plateau de 30 –50 mm soit. Afin d'empêcher le flux de vapeur de pénétrer dans le tuyau de vidange, son extrémité inférieure est immergée dans une couche de liquide d'une hauteur maximale de 50 mm, créée par une barre de retenue devant la partie perforée de la plaque. Le joint hydraulique qui en résulte empêche les vapeurs de pénétrer dans le tuyau d'évacuation. Le dispositif de trop-plein peut être non seulement sous la forme de tuyaux de drainage, mais également sous la forme d'une cloison segmentée (VI, riz. 6.9.7), qui coupe un volume segmentaire de l'espace de vapeur, à travers lequel le liquide s'écoule d'une plaque à l'autre.
À tuyaux de vidange(ou segment) le niveau de liquide est généralement plus élevé que le niveau sur le plateau sous-jacent d'une quantité qui équilibre la résistance hydraulique du plateau. Par conséquent, la distance entre les plaques ne peut pas être inférieure à cette colonne de liquide dans le déversoir.
D'autre part, la distance entre les plaques (le pas des plaques) est en fait définie en tenant compte des facteurs suivants :
· séparation des projections de liquide du flux de vapeur sortant de la couche bouillonnante, et réduction due à cet entraînement de liquide sur la plaque sus-jacente ;
la possibilité d'un accès humain à l'espace entre les plateaux lors de la réparation et de l'inspection des plateaux.
Sur la base de ces conditions documents normatifs le pas de plateaux est fixé en fonction du diamètre de la colonne de 300 à 900 mm.
Plaques de tamis (voir Fig. 6.9.7, III) utilisé dans des colonnes de petit diamètre (jusqu'à 2,0-2,5 m). Actuellement, des variantes de plaques de tamis sont souvent utilisées, dont la toile est en métal déployé. Le flux de vapeur traversant une telle nappe s'écarte de la verticale et à la sortie de la couche bouillonnante est dirigé selon un angle de 40-60° par rapport à l'horizontale. Afin d'intensifier le travail de la plaque sur le trajet de la vapeur sortant de la couche bouillonnante, des éléments déflecteurs constitués de la même tôle perforée sont installés en oblique. En heurtant ces éléments, le mélange vapeur-liquide est séparé : le liquide descend de l'élément en film jusqu'à la zone de barbotage, et la vapeur passe à travers les fentes dans l'espace inter-plateaux. De telles plaques ont une très faible résistance hydraulique (0,1-0,2 kPa) et offrent une efficacité suffisamment élevée des processus de transfert de masse.
Riz. 6.9.9 Schéma de fonctionnement de la feuille d'une plaque à partir d'une feuille perforée :
1 - corps de colonne ; 2 - parois de la poche de vidange; 3 - toile de plaque; 4 - éléments de garde-boue à partir d'une tôle perforée
L'inconvénient de ces plateaux (ainsi que d'autres variantes du plateau à tamis) est qu'au moindre manque d'horizontalité ou renflements ou bosses locaux dans la bande du plateau, il fonctionne de manière inégale sur toute la surface - le liquide tombe aux points sous-jacents, et la vapeur glisse sans faire de bulles aux points sus-jacents. En conséquence, l'efficacité de la plaque est réduite.
L'un des plus anciens types de plaques en termes de durée d'utilisation et de masse est encore plaque coiffée(voir figure 6.9.7, IV) avec des bouchons ronds (capsules). Sa différence avec les précédents est que chaque trou pour le passage des vapeurs a un tuyau de dérivation 7 une certaine hauteur, sur laquelle le capuchon est fixé 8 avec des fentes pour le passage de la vapeur sur tout son bord inférieur. Un tel dispositif vous permet de faire entrer le flux de vapeur dans la couche de liquide sur la plaque parallèle à son plan et fragmenté en de nombreux petits jets. De plus, les contre-jets des bouchons adjacents, en collision, créent des turbulences dans la zone inter-bouchons, ce qui entraîne une efficacité accrue du plateau. En effet, dans la grande majorité des cas, le rendement moyen une telle plaque s'avère en pratique être la plus grande - 0,6-0,8.
Il existe un grand nombre de modifications de la plaque de capuchon, qui diffèrent par la conception ou la forme des capuchons. Trois de ces modifications sont illustrées à la Fig. 6.9.7 (IV, a ; IV, b et IV, c).
Le premier d'entre eux est la plaque à capuchons ronds décrite ci-dessus. Une telle plaque est universelle, elle a trouvé une application dans diverses colonnes - des colonnes de séparation des gaz aux colonnes atmosphériques et sous vide. Dans ce dernier cas, il est rarement utilisé en raison de la forte consommation de métal de la plaque, de la complexité de fabrication et d'installation.
Deuxième modification (IV, b) - il s'agit d'une plaque avec des bouchons rectangulaires (tunnel) moulés ou estampés, qui était utilisée dans les années 1930 et 1940 dans les colonnes de la Foster-Wheeler Company (USA) pour séparer le mazout en fractions pétrolières.
Troisième modification (IV, c) - il s'agit d'une plaque rainurée dont la caractéristique est l'absence d'âme de plaque. Remplacées par des gouttières en acier 2, entre lesquels se forment des espaces pour le passage des vapeurs. Les fentes sont recouvertes de bouchons 8, ayant des fentes le long de leurs bords, la longueur de chaque capuchon correspond à la longueur de l'espace entre les rainures. Le liquide se déplace le long des gouttières jusqu'au drain; et les vapeurs bouillonnent à travers les fentes des bouchons.
Dans les années 60 et 70, deux nouveaux types de plateaux sont venus remplacer les plateaux cap et rainurés dans le raffinage du pétrole - à partir d'éléments en forme de S (V) et vanne ( VI).
Originalité plaques à partir d'éléments en forme de S consiste dans le fait que son voile et ses bouchons forment les mêmes éléments (dans la section - un profil en forme de S), mais chaque bouchon a des fentes pour le passage des vapeurs d'un seul côté, c'est-à-dire par unité de surface de barbotage du plateau, le flux de vapeur est introduit dans le liquide par un "front" de jets écrasés plus petit (par rapport à un plateau rainuré). Contrairement à un plateau rainuré, le liquide sur ce plateau se déplace à travers les bouchons du tunnel, les inondant.
Les plateaux constitués d'éléments en forme de S sont très répandus dans toutes les colonnes, à l'exception de celles à vide (en raison de la résistance hydraulique accrue), en raison de la faible consommation de métal, de la facilité de fabrication (emboutissage) et d'installation, combinées à un rendement élevé (rendement moyen 0 . 4–0,7).
Pas haute efficacité plaques d'éléments en forme de S est en partie liée, avec une plus faible proportion de jets de vapeur écrasés par unité de surface de barbotage. Par conséquent, une plaque combinée de ce type est apparue, dans laquelle, le long du plan supérieur des bouchons avec un pas de 100-120 mm, il y a des trous de section rectangulaire, bloqués par des vannes qui s'ouvrent dans la direction du liquide. Cela augmente l'effet de bouillonnement, réduit la résistance hydraulique de la plaque et, par conséquent, augmente son efficacité.
Clapets de soupape(Fig. 6.9.7, vi) selon le principe de l'appareil, il est plus proche des perforés, mais contrairement à eux, ils vous permettent d'ajuster la zone d'écoulement des trous pour les vapeurs. Pour ce faire, au-dessus de chaque trou (diamètre de 30 à 50 mm) se trouve un dispositif (valve) qui, en fonction de la quantité de vapeur sous leur pression, monte (ou tourne) au-dessus du trou, modifiant ainsi la zone d'écoulement pour vapeur.
Cependant, il existe de nombreuses conceptions différentes de disques de soupape, différant par la conception des soupapes.
Sur la fig. 6.9.7, VI 4 dispositions de vannes les plus typiques sont illustrées : un B - vannes avec butées supérieures (un - tournant, b- soupape à champignon montant verticalement); c, d- vannes avec limiteurs de levée inférieurs - "jambes" (dans - avec trois pieds de même hauteur ; G - avec trois pieds de hauteurs différentes : un - court et deux - long). Soupape de pépin (dans) s'élève verticalement sous la pression de la vapeur jusqu'à ce que les membres de ses pattes reposent contre la toile de l'assiette. Dans ce cas, la section transversale pour le passage des vapeurs sera maximale et le mouvement des vapeurs et des liquides sera strictement à flux croisé.
Riz. 6.9.10. Fragment de la section et schéma de fonctionnement de la plaque à flux droit croisé de la vanne:
a, b, c - vue latérale de la section à faible (contre-courant), moyenne (courant croisé) et augmentation (flux direct) chargement du plateau par paires, respectivement ; d – vue de dessus des vannes ; e - vue de la valve du côté de la jambe courte ; 7 - assiette en tissu; 2 - trous pour vannes; 3 - soupapes; 4 - jambes courtes; 5 - jambes longues (les flèches indiquent les directions de mouvement du liquide et de la vapeur)
La vanne à différentes pattes (Fig. 6.9.10) sous l'action du flux de vapeur, s'élève d'abord du côté de la patte courte (puisque le centre de gravité d'une telle vanne est déplacé vers les pattes longues) jusqu'à ce qu'elle repose contre la toile. Dans cette position (Fig. 6.9.10, un) le flux de vapeur est introduit sous un angle par rapport au plan de la plaque vers le flux de liquide en mouvement, c'est-à-dire la plaque fonctionne à contre-courant. Avec une augmentation ultérieure de la quantité de vapeur, la valve monte du côté des jambes longues (plus précisément, elle tourne autour du point d'arrêt - la jambe courte), et lorsque les plans de la valve et de la lame de la plaque deviennent parallèles ( position "b" En figue. 6.9.10), le clapet, comme dans le cas de la vanne Glitch, fonctionne en mode de flux croisé de liquide et de vapeur. Si la quantité de vapeur continue de croître, la valve tourne davantage autour du point d'arrêt et, à la fin, repose contre la toile avec les trois pattes (" dans" sur la Fig. 6.9.10), en prenant une position inclinée, dans laquelle la plus grande zone d'écoulement des vapeurs est située le long du liquide, c'est-à-dire que la plaque fonctionne dans ce cas comme un écoulement direct.
Les plateaux à clapet cumulent de nombreux avantages (faible consommation de métal, facilité de montage, barbotage homogène sur une large plage de charge vapeur et liquide, etc.) qui leur ont permis de devenir le type de plateau le plus répandu des années 1970 à nos jours . Ces plateaux sont utilisés dans presque tous les types de colonnes de raffinage du pétrole - de la séparation des gaz au vide.
plaques à jet(Fig. 6.9.7, VII) sont une toile de 3 à 5 mm d'épaisseur, dans laquelle des trous sont estampés configuration différente avec une courbure des pétales à un certain angle. Les variantes les plus typiques de ces plaques sont illustrées sur la figure: un - aux pétales recourbés en forme de rectangles aux angles arrondis, b- sous la forme de renflements coniques (type "cabine de prompteur") avec des trous dans une direction. Le bullage sur de tels plateaux s'effectue en mode courant croisé, dans lequel l'énergie dynamique du flux de vapeur est utilisée pour intensifier le mouvement du liquide le long du plateau.
Les plateaux à jet sont conçus pour être utilisés dans les cas où la charge de la colonne sur le flux de vapeur est assez élevée, ils ont donc trouvé plus d'utilisation dans les colonnes de séparation des gaz. En raison de l'introduction de vapeur dans la couche de liquide sous un angle par rapport au plan du plateau, l'entraînement des gouttelettes de liquide sur le plateau sus-jacent est bien inférieur à celui des plateaux à écoulement transversal.
plaque tourbillonnaire(Fig. 6.9.7, VII)- un exemple de plateau avec un mélange intense de vapeur et de liquide sur le plateau avec un entraînement de gouttelettes réduit. Sur la toile d'une telle plaque en cercles d'un diamètre de 100-120 mm, des trous à pétales courbés sont estampés dans des directions radiales. (VIII, a), et au centre de ces cercles sur les goujons se trouvent des coupelles de chicane du même diamètre (100-120 mm), au fond desquelles se trouvent 6 à 8 trous d'un diamètre de 5 à 6 mm. Ces éléments de vortex sur la toile sont disposés en damier avec un pas de 140-180 mm.
Le flux de vapeur, passant à travers les fentes à un angle de 40 à 60° par rapport au plan du plateau, tourbillonne dans le mélange avec le liquide s'écoulant le long de la bande du plateau, et ce mélange vapeur-liquide, frappant les coupelles de chicane, est séparé au-dessus d'eux . Le flux de vapeur va plus loin dans l'espace entre les plateaux, et la majeure partie du liquide tombe dans les coupelles et s'écoule à nouveau à travers les trous de celles-ci dans la zone de la couche bouillonnante tourbillonnante.
Un tel plateau à l'échelle expérimentale a montré une faible résistance hydraulique, combinée à une efficacité de transfert de masse élevée, ce qui répond aux exigences de base des plateaux de colonne sous vide.
Pour tous les types de plaques considérés, les facteurs qui déterminent la portée de leur application et l'efficacité du travail sont :
· résistance hydraulique ;
uniformité et intensité du bouillonnement sur la surface de la plaque ;
La plage de charges de vapeur et de liquide dans laquelle le plateau fonctionne normalement (sans défaillance de liquide et entraînement intense de gouttelettes).
Colonne de distillation (colonne de fractionnement)- un appareil vertical cylindrique, équipé de dispositifs internes de transfert de chaleur et de masse et d'unités auxiliaires, conçu pour séparer les mélanges liquides à deux ou plusieurs composants en fractions, chacune contenant des substances à points d'ébullition proches.
Les colonnes de distillation sont divisées en :
selon le nombre de produits reçus :
Simple les colonnes de distillation assurent la séparation du mélange initial (matière première) en deux produits : le produit rectifié (distillat), qui est retiré du haut de la colonne à l'état de vapeur, et le résidu (produit de rectification liquide inférieur)
Complexe les colonnes de distillation séparent la charge en plus de deux produits. Il existe des colonnes complexes avec la sélection de fractions supplémentaires de la colonne sous la forme de bandes latérales et de colonnes dans lesquelles des produits supplémentaires sont extraits de produits spéciaux. colonnes de décapage (décapage).
sur rendez-vous:
1) pour la distillation atmosphérique et sous vide d'huile et de mazout
2) pour la distillation secondaire de l'essence
3) pour stabiliser l'huile, le condensat de gaz, l'essence instable
4) pour le fractionnement des raffineries, des huiles et des gaz naturels
5) pour la distillation des solvants dans les procédés de raffinage du pétrole
6) pour la séparation des produits des fours tubulaires et des procédés catalytiques pour le traitement du pétrole et du gaz, etc.
par pression :
ce sont des colonnes, dans la partie supérieure desquelles la pression est légèrement supérieure à la pression atmosphérique (0,1 ... 0,2 MPa). La pression au bas de la colonne, en règle générale, dépend de la résistance de son périphériques internes et peut largement dépasser la pression atmosphérique. De telles colonnes sont utilisées dans la distillation d'huile stabilisée ou épurée en fractions combustibles et en mazout.
fonctionner sous vide (ou vide profond). En d'autres termes, la pression y est inférieure à la pression atmosphérique (un vide est créé), ce qui permet de réduire la température de fonctionnement du procédé et d'éviter la décomposition du produit. Ces colonnes sont destinées au fractionnement du mazout en gazole sous vide (vide profond) ou en fractions pétrolières étroites et en goudron.
sont utilisés dans la stabilisation ou l'étêtage du pétrole, la stabilisation des essences gazeuses, des essences de distillation du pétrole et des procédés secondaires et le fractionnement des gaz de raffinerie ou de pétrole associés.
selon le principe d'action :
sont utilisés sur des installations à faible productivité, si nécessaire, sélection un grand nombre fractions et séparation haute définition. La matière première initiale est coulée dans un cube d'une hauteur égale aux 2/3 de son diamètre. Le chauffage est effectué avec de la vapeur sourde. Dans la première période de fonctionnement de l'unité de distillation, on prend le composant le plus volatil du mélange, par exemple la tête benzénique, puis les composants à point d'ébullition plus élevé (benzène, toluène, etc.). Les composants à point d'ébullition le plus élevé du mélange restent dans le cube, formant un résidu de TVA. A la fin du processus de rectification, ce résidu est refroidi et pompé. Le cube est à nouveau rempli de matières premières et la rectification reprend. La périodicité du processus est due à une plus grande consommation de chaleur, une productivité du travail plus faible et moins utilisation efficaceéquipement.
Installations avec colonnes action continue dépourvu des inconvénients des colonnes action périodique. Dans de telles colonnes, la charge chauffée est introduite dans une colonne de distillation, où elle est séparée en phases liquide et vapeur. À la suite de la distillation, l'isopentane est prélevé du haut de la colonne comme produit principal et du bas de la colonne - le n-pentane comme résidu.
selon la méthode de transfert de fluide inter-étage :
1) avec dispositifs de débordement (avec un, deux ou plus)
2) sans dispositifs de débordement (type de panne)
selon le mode d'organisation du contact des phases vapeur-gaz et liquide :
Ces colonnes sont utilisées, par exemple, pour séparer l'eau lourde. Les plaques sont des boucliers coniques avec un angle d'inclinaison de 40°. Les plateaux fixes 4 sont fixés le long de la périphérie au corps de la colonne 1, les mobiles 3 sont fixés au centre à l'arbre 5 et tournent avec lui. Des plaques tournantes alternent avec des plaques fixes. Tous les 1,5 m de hauteur, l'arbre est recouvert de roulements à billes 6 fonctionnant sans lubrification. Pour faciliter l'installation, la colonne est assemblée à partir de tsargs (pièces / sur brides). Les mucosités descendent d'en haut le long du plateau fixe 4 et débordent au centre sur le plateau tournant sous-jacent 3. Sous l'influence de la force centrifuge, les mucosités se déplacent le long du plateau tournant jusqu'à sa périphérie et débordent sur le plateau fixe sous forme de un film annulaire continu. Les vapeurs se déplacent sur les mucosités à contre-courant.
Dans les colonnes à garnissage, le contact entre le gaz (vapeur) et le liquide s'effectue à la surface de corps garnis spéciaux, ainsi que dans l'espace libre entre eux.
La buse est un corps en matériaux inertes, elle est conçue pour créer une plus grande surface de contact entre le liquide qui y coule et le flux de vapeur montant et pour les mélanger intensément. La buse est généralement en matériau résistant à la corrosion (céramique, porcelaine, verre).
La buse est placée sur des plaques équipées de deux trous de deux types: petit - pour le débit d'irrigation (mucosités) et grand - pour le passage de la vapeur. La couche de garnissage est divisée en plusieurs petites couches de 1 à 1,5 m de haut, en les séparant par de l'espace libre.
Plus les anneaux de garnissage sont fins, meilleur est le contact entre les vapeurs et les mucosités, mais plus la résistance hydraulique au mouvement des vapeurs dans la colonne est élevée. à certains Valeur limite Le chargement de la colonne garnie, c'est-à-dire à haute vitesse de vapeur ou de liquide, peut être observé "starter" de la buse lorsque le flux de liquide s'arrête et que son éjection de la colonne commence. Le principal inconvénient des colonnes à garnissage est la formation de zones « mortes » dans le garnissage, à travers lesquelles ni vapeur ni flegme ne passent, ce qui aggrave le contact entre les phases de transfert de masse et réduit l'efficacité de la séparation.
Les conceptions de garnitures utilisées dans les appareils industriels pour le traitement du pétrole et du gaz et la pétrochimie peuvent être divisées en deux groupes - garnitures irrégulières (en vrac) et régulières.
En tant que buses irrégulières (en vrac), des corps solides de différentes formes sont utilisés, chargés dans le corps en vrac. En conséquence, une structure spatiale complexe est formée dans la colonne, fournissant une surface de contact de phase significative.
Les anneaux Raschig, qui sont des sections de tuyaux dont la hauteur est égale au diamètre extérieur, sont largement utilisés parmi les buses coulées en vrac. Faible coût et la facilité de fabrication des anneaux Raschig en font l'un des types d'appâts les plus courants. Parallèlement aux anneaux cylindriques lisses en métal, en céramique ou en porcelaine, des buses avec des surfaces extérieures et (ou) intérieures nervurées ont été développées. Pour intensifier le processus de transfert de masse, des conceptions de buses cylindriques à chicanes ont été développées.
Appât à anneaux Raschig (1 - anneau simple; 2 - anneaux en vrac; 3 - appâts réguliers)
L'utilisation industrielle a maintenant trouvé une autre buse annulaire - les anneaux Pall. Lors de la fabrication de tels anneaux sur les parois latérales, deux rangées de découpes rectangulaires décalées l'une par rapport à l'autre sont réalisées, dont les pétales sont repliés à l'intérieur de la buse. La conception des anneaux Pall par rapport aux anneaux Raschig permet d'augmenter le débit et de réduire la résistance hydraulique.
L'accessoire, connu sous le nom de selles Intallox, est l'accessoire en céramique le plus courant aujourd'hui. Sa surface fait partie d'un tore. Les sièges Intallox sont mécaniquement solides, offrent un placement uniforme des buses et une bonne auto-distribution des fluides.
Dans les colonnes à plateaux, le contact entre les phases se produit lorsqu'une vapeur (gaz) traverse une couche de liquide située sur le dispositif de contact (plateau).
Plaque de distillation représente une cloison horizontale dans la colonne, sur la plaque il y a une couche de liquide qui coule dans la colonne (irrigation), à travers laquelle barbotent les vapeurs montant d'en bas.
Dans le livre Skoblo A.I., Molokanov Yu.K., Vladimirov A.I., Shchelkunov V.A. Les appareils à colonne "Procédés et appareils pour le traitement du pétrole et du gaz et la pétrochimie" selon le type de dispositifs de contact interne sont divisés en plateau, garni et film (les auteurs de cette publication se réfèrent à des appareils à film dans lesquels les phases sont en contact sur la surface d'un mince film de liquide s'écoulant sur une surface verticale ou inclinée).
Le dispositif d'une colonne de distillation est assez compliqué et il est peu probable qu'il soit possible de le simuler à la maison. Mais sur des sites Internet spécialisés, vous pouvez acheter une installation fonctionnelle à un prix très raisonnable, qui ne nécessitera encore qu'un rééquipement mineur de votre moonshine.
La conversion ne concernera que le réservoir de l'évaporateur - il est nécessaire d'installer une bride d'un diamètre approprié pour que la colonne puisse être fixée strictement verticalement. S'il n'y avait pas de thermomètre sur le réservoir, vous devrez l'installer. Sans mesurer la température sur l'évaporateur, il est extrêmement difficile de contrôler le fonctionnement de la colonne, et, en principe, c'est impossible du tout.
Comment fonctionne la colonne
La colonne est un échangeur de chaleur et de masse dans lequel se déroulent des processus physiques et chimiques complexes. Ils sont basés sur la différence des points d'ébullition de divers liquides et la capacité de chaleur latente des transitions de phase. Cela semble très mystérieux, mais en pratique, cela semble un peu plus simple.
La théorie est très simple - de la vapeur contenant de l'alcool et diverses impuretés bouillant à différentes températures, qui diffèrent de plusieurs degrés, monte et se condense dans la partie supérieure de la colonne. Le liquide résultant s'écoule et rencontre en chemin une nouvelle portion de vapeur chaude. Les liquides dont le point d'ébullition est plus élevé se réévaporent. Et ceux qui n'avaient pas assez d'énergie thermique restent à l'état liquide.
La colonne de distillation est constamment dans un état d'équilibre dynamique de vapeur et de liquide, dans de nombreux cas, il est difficile de séparer les phases liquide et gazeuse - tout bout et bout. Mais en termes de densité, en fonction de la hauteur, toutes les substances sont très clairement séparées - légères en haut, puis plus lourdes et tout en bas - huiles de fusel, autres impuretés à point d'ébullition élevé, eau. La séparation par fractions s'effectue très rapidement, et cet état se maintient quasi indéfiniment, sous réserve du régime de température dans la colonne.
À une hauteur correspondant à la teneur maximale en vapeurs d'alcool, un tuyau d'admission est installé, à travers lequel la vapeur est libérée et pénètre dans le condenseur (réfrigérateur), d'où l'alcool s'écoule dans le récipient de collecte. La colonne de distillation pour le moonshine fonctionne toujours très lentement - la sélection, en règle générale, est effectuée au goutte à goutte, mais en même temps, elle est assurée haut niveau nettoyage.
La colonne fonctionne à ou légèrement au-dessus de la pression atmosphérique. Pour ce faire, une vanne atmosphérique ou simplement un tube ouvert est installé au point haut - les vapeurs qui n'ont pas eu le temps de se condenser quittent la colonne. En règle générale, ils ne contiennent pratiquement pas d'alcool.
Les états des composants vapeur-liquide à différentes hauteurs de la colonne
Le graphique montre les états fixes des composants vapeur-liquide à différentes hauteurs de la colonne, qui peuvent être contrôlés par la température en un point donné. La partie horizontale du graphique correspond à la concentration maximale de la substance. La séparation n'a pas de limites claires - la ligne verticale correspond à un mélange des fractions inférieure et supérieure. Comme on peut le voir, le volume des zones limites est beaucoup plus petit que celui des fractions, ce qui donne un certain jeu dans le régime de température.
Appareil à colonne de distillation
La base de la colonne est tuyau vertical acier inoxydable ou cuivre. D'autres métaux, notamment l'aluminium, ne conviennent pas à cette fin. Le tuyau est isolé de l'extérieur avec un matériau à faible conductivité thermique - les fuites d'énergie peuvent perturber l'équilibre établi et réduire l'efficacité des processus d'échange de chaleur.
Un prérefroidisseur déflegmateur est monté dans la partie supérieure de la colonne. Il s'agit généralement d'un serpentin en ligne ou externe qui refroidit environ 1/8 à 1/10 de la hauteur de la colonne. Vous pouvez également trouver des colonnes de distillation avec une chemise d'eau ou des refroidisseurs à billes complexes sur Internet. Outre le prix, ils n'affectent rien d'autre. La serpentine classique fait parfaitement son travail.
Rubrique "Bébé"
Le rapport entre la quantité de condensat prélevée et le nombre total de reflux retournant au réservoir est appelé nombre de reflux. Ceci est une caractéristique d'un modèle de colonne particulier et décrit ses capacités de fonctionnement.
Plus le taux de reflux est faible, plus la colonne est efficace. A F=1, la colonne fonctionne comme un clair de lune ordinaire.
Les installations industrielles ont une capacité fractionnaire de séparation élevée, leur nombre est donc compris entre 1,1 et 1,4. Pour une colonne domestique Moonshine, F \u003d 3-5 est optimal.
Types de colonnes
Une colonne de distillation pour un moonshine encore pour augmenter les points de contact entre la vapeur et le liquide, où se produisent les processus d'échange de chaleur et de diffusion, est alimentée en charges qui augmentent considérablement la zone de contact. Taper structure interne les colonnes sont divisées en plateau et emballées. La classification par performance ou taille ne montre pas de réelles possibilités.
Pour augmenter la surface de contact, un fin treillis en acier inoxydable torsadé en spirale, de petites boules lâches, des anneaux de Raschig et de petites spirales de fil sont placés à l'intérieur de la colonne. Ils sont bien emballés ou remplis jusqu'à une hauteur allant jusqu'aux ¾ de la longueur de la colonne, sans atteindre le point de consommation d'alcool.
Le thermomètre doit être situé dans une zone exempte de buses et indiquer la température réelle du fluide. Le thermomètre est choisi électronique, car ayant le moins d'inertie. Dans certains modèles de colonnes, les dixièmes de degré jouent un rôle. Pour obtenir de l'alcool pur dans la zone de sélection, la température doit être maintenue dans la plage de 72,5 à 77 C.
Une colonne de distillation à plaques est beaucoup plus difficile à fabriquer - la conception de plaques à capuchon ou à tamis, qui sont des cloisons horizontales à l'intérieur, à travers lesquelles le liquide s'écoule avec un certain retard. Une zone de bullage est créée sur chacun des plateaux, ce qui augmente le taux d'extraction des vapeurs d'alcool du reflux. Parfois, les colonnes de distillation sont appelées renforcement - elles atteignent un rendement en alcool de près de cent pour cent avec un minimum d'additifs étrangers.
La colonne fonctionne à pression atmosphérique, pour communiquer avec environnement externe la colonne est équipée d'une vanne spéciale ou d'un tube ouvert dans la partie supérieure de la structure. Ce fait détermine l'une des caractéristiques d'une colonne de distillation pour un distillateur Moonshine - à différentes pressions atmosphériques, cela fonctionne différemment. Régime de température varie de quelques degrés (différence sur le thermomètre de la cuve et de la colonne). Le rapport est établi expérimentalement. Pour cette raison, avec une colonne d'élément chauffant.
Après avoir acheté une colonne de distillation fonctionnelle ou en la construisant vous-même, vous pouvez obtenir de l'alcool de haute pureté sans trop de difficulté. La colonne est particulièrement efficace dans la distillation du moonshine obtenu à partir d'un distillateur conventionnel.
Colonne à plateaux modulaires. Pratique sur l'automatisation BKU - 011M.
Couvercles coniques en cuivre. Une colonne de saveur cuivrée. Théorie et pratique.
Machine à alcool. Capuchon colonne HD/3-500 KKS-N. Partie 1. Nouveau en 2016.
Machine à alcool. Capuchon colonne HD/3-500 KKS-N. Partie 2. Nouveau en 2016.
Machine à alcool. Colonne à plateaux.
Qu'est-ce qu'une colonne à plateaux et pourquoi en a-t-on besoin... fixation prismatique) en fait des plaques. Avec l'aide d'une colonne à plateaux, nous n'obtiendrons pas d'alcool pur. Cependant, nous pouvons y obtenir la soi-disant sous-rectification avec une force de 90-95 vol. Autrement dit, ce n'est pas non plus de l'alcool, mais ce n'est plus un distillat. Un distillat très raffiné qui conserve encore les notes de la matière première d'origine. Cette technologie est utilisée depuis plus de cent ans et est activement utilisée par les distillateurs du monde entier. Notre pays en ce sens n'a pas fait exception ces dernières années. Ces colonnes gagnent une immense popularité.
Analysons les principales différences entre les colonnes pour une compréhension correcte du choix d'une colonne particulière.
- Comme tous nos équipements, les colonnes à plateaux se distinguent par séries : HD/4 ou HD/3. Tout est simple ici. Si vous disposez déjà d'un équipement HD, le choix se fait en fonction de la série d'équipements correspondante. Si vous n'achetez que du matériel, vous devez comprendre la différence entre les séries HD / 4 et HD / 3. La série HD/4 est plus budgétaire, elle a un rapport qualité-prix optimal. La série HD/3 a un prix plus élevé mais aussi des performances plus élevées.
- Matériaux utilisés dans la fabrication des colonnes. Il s'agit soit d'acier inoxydable de qualité alimentaire, soit de verre de quartz. Dans ce dernier cas, vous avez la possibilité d'observer visuellement le processus, ce qui est un vrai plaisir. N'oubliez pas qu'en premier lieu, nous faisons ce passe-temps pour le plaisir.
- Les colonnes diffèrent également par leur hauteur et par le nombre de plaques qu'elles contiennent. La hauteur de la colonne est disponible en deux tailles : 375 et 750 mm, respectivement. Sur une colonne raccourcie, vous pouvez obtenir une "sous-rectification" avec une force de 91-92C, sur une colonne de 750 mm, vous pouvez obtenir une "sous-rectification" d'environ 95C. Étant donné que les colonnes à disques sont pliables, le nombre de plateaux dans la colonne peut être ajusté indépendamment par le distillateur.
- Type d'exécution de la plaque. Les plaques sont constituées de deux types: échec et capuchon. Il est difficile de dire sans équivoque laquelle des assiettes est la meilleure et sur quelles assiettes la boisson sera plus savoureuse. Le fait est que les plaques de panne sont bonnes si nous utilisons une puissance de chauffage stable, sans sauts dans le réseau. Si le réseau est instable, alors vous pouvez utiliser un stabilisateur de puissance de chauffage par exemple. Les plaques de type bouchon sont plus simples et n'importe quel chauffage peut être utilisé. Cependant, du fait de la complexité de fabrication de telles colonnes, elles sont plus onéreuses. Mais aussi plus esthétique au passage.
- Matériaux de fabrication d'assiettes. Les plaques défaillantes sont en PTFE inerte. Les cymbales Cap sont fabriquées en acier inoxydable ou en cuivre. L'inox est connu pour être inerte. Et par conséquent, la boisson obtenue à sa surface n'a pas de goûts supplémentaires caractéristiques, à l'exception de la matière première d'origine. Le cuivre, d'autre part, est censé absorber le soufre nocif libéré pendant le processus de distillation, débarrassant ainsi la boisson de odeurs désagréables et le goût. Les partisans du cuivre et de l'inox ont de nombreux adeptes. Chacun a ses propres arguments en faveur du matériau utilisé pour les assiettes.
En savoir plus sur le travail avec colonnes de plat vous pouvez ici.
À appareil à colonne Les raffineries utilisent actuellement des dizaines de conceptions de dispositifs de contact qui diffèrent par leurs caractéristiques et leurs indicateurs techniques et économiques. A côté des barquettes de première génération (bouchon, rainuré), toujours en activité dans les anciennes installations de production, les CU en S, à clapet (lamellaire, disque) et autres types de CU se sont généralisées dans les installations AVT.
casquette

Tamis

treillis

Avec des éléments en forme de S

Soupape (disque)

Portée de différents types de plaques
Principales fonctionnalités de comparaison
Il n'est pas rare que des cymbales soient utilisées dans différentes sections d'une section différents types. Cela s'explique par le fait que les charges de vapeur et de liquide le long de la hauteur des colonnes d'huile, en particulier celles travaillant avec des extractions latérales, diffèrent considérablement (parfois d'un ordre de grandeur). Lors de la comparaison d'appareils de contact divers types Les principaux indicateurs sont généralement les suivants :
- Performance.
- résistance hydraulique.
- Efficacité (efficacité) - caractérise le degré d'approximation du processus de séparation réel sur la plaque par rapport au théoriquement réalisable (plaque théorique).
- Plage de variation admissible des charges de fonctionnement (vapeur et liquide), qui est déterminée par le rapport entre la charge maximale admissible et la charge minimale admissible.
- Le gradient du niveau de liquide sur la largeur de la bande du plateau, qui est déterminé par le fait que le liquide est introduit sur le plateau à partir d'une extrémité du plateau (section) et retiré de l'autre. Lorsque le liquide s'écoule le long de la tôle, il surmonte une certaine résistance hydraulique, de sorte que la hauteur de la couche de liquide au niveau de la poche de réception dépasse le niveau correspondant au niveau de la poche de vidange. La présence d'un gradient conduit à une violation de l'uniformité de la répartition de la vapeur sur la largeur de la couche bouillonnante et, par conséquent, à une diminution de l'efficacité du HR.
- La hauteur de la distance inter-plaques, qui doit assurer le fonctionnement normal du joint hydraulique pour assurer un écoulement garanti du fluide du plateau supérieur vers le plateau inférieur.
- Garantir des performances à long terme lorsque vous travaillez sur des supports contaminés et sujets à la formation de goudron ou d'autres dépôts.
- Consommation de métal.
- Prix.
- Facilité d'installation et de réparation, conception simple.
Buses à flux croisés (CTH)
Calcul de la dissipation thermique par irrigation à distance
Pour les colonnes complexes fonctionnant avec une irrigation à circulation froide à distance, qui incluent les colonnes AVT, une autre caractéristique spécifique devient très importante: la valeur de l'évacuation de la chaleur du flux de vapeur interne par irrigation froide - Q, (kW / m 3). Dans cette caractéristique, la quantité d'évacuation de chaleur obtenue est rapportée à 1 m 3 de couche bouillonnante ou à 1 m 3 de garnissage. Dans la littérature domestique cette caractéristique est rarement prise en compte alors qu'elle conditionne largement l'efficacité de l'irrigation circulante.
La quantité de chaleur retirée de l'irrigation par circulation dans un échangeur de chaleur externe est déterminée par :
Q=L(Hn-Hk)
Toute cette quantité de chaleur est dépensée à l'intérieur de la colonne pour condenser une partie de l'irrigation à la vapeur, et l'enthalpie du débit de liquide atteint la valeur Hn. Dans la procédure de calcul technologique, qui, en règle générale, est effectuée selon des "plaques théoriques", le processus d'échange de chaleur sera terminé dès le premier KU. En fait, c'est l'efficacité réelle du processus d'évacuation de la chaleur à la cogénération qui déterminera le nombre de plaques réelles sur lesquelles ce processus sera effectué.
Sélection de la conception optimale des dispositifs de contact
Il n'y a pas de conception KU qui surpasse toutes les autres conceptions à tous égards. Chacune des conceptions a ses propres avantages et inconvénients et son propre domaine d'utilisation rationnelle. Selon le processus particulier valeur la plus élevée peuvent acquérir certaines caractéristiques de ce qui précède. Ainsi, le choix du HR pour les colonnes de l'unité atmosphérique est le plus influencé par les indicateurs de productivité, d'efficacité et de la valeur admissible de la plage de charge de fonctionnement, dans laquelle la haute efficacité des plateaux est assurée. Pour les colonnes d'un bloc à vide, la résistance hydraulique de la HV est mise en avant en premier lieu, puisqu'elle va déterminer l'intensité du processus de décomposition des hydrocarbures lourds dans la zone de chauffe, et donc, dans une large mesure, la qualité de fractions commerciales, bien que dans ce cas, bien sûr, d'autres caractéristiques doivent également être prises en compte. Les types les plus courants de KU sont présentés dans la figure.
Au fait, lisez aussi cet article : Rectification d'huile dans une colonne
Dans les colonnes atmosphériques, diverses modifications de la vanne KU avec disque, vannes rectangulaires et trapézoïdales, ainsi que des plateaux combinés en forme de S avec vannes, ont fait leurs preuves. Dans les colonnes à vide, il est intéressant d'utiliser des vannes à disque du type à éjection, qui se caractérisent par la plus faible résistance hydraulique parmi tous les types de CU.
Riz. 3.1. Types courants de bouchons et de valves :
Casquettes : a - rondes ; b - hexagonale; c - rectangulaire; g - rainuré; e - en forme de S ; soupapes : e - rectangulaires ; g - rond avec un limiteur inférieur; h - rond avec un limiteur supérieur; et - lest ; k - flux croisé d'éjection de disque ; l - écoulement transversal des plaques ; m - Bouchon en forme de S avec valve.
Désignations : 1 - disque disque ; 2 - soupape; 3 - limiteur ; 4 - ballast.
Dispositifs de débordement pour plaques
Pour organiser le débordement du fluide de travail de la plaque sus-jacente à la plaque sous-jacente, des dispositifs de débordement spéciaux sont utilisés dans la KU, notamment une cloison de vidange et une poche (Fig. 3.2). À grandes valeurs charges spécifiques sur le liquide (mesurées par le débit de la phase - m 3 / heure rapporté à 1 m 2 de la section de la colonne ou à 1 m de la longueur de la paroi du drain), ce qui est typique pour les gros tonnages colonnes des installations AT-AVT, les structures multi-flux du KU sont utilisées pour réduire le gradient de niveau de liquide (de 2 à 4 filets). Les poches de drainage peuvent également être utilisées pour fournir des flux intermédiaires au KU (irrigation froide) et/ou pour détourner des extractions latérales (Fig. 3.3). Dans ce dernier cas, la capacité volumétrique de la poche est augmentée en augmentant la distance entre les plateaux, ce qui augmente la fiabilité de la pompe de pompage.
Riz. 3.2. Disposition des unités pour l'écoulement de liquide de plateau à plateau et l'injection d'irrigation pour les plateaux à simple flux (a) et à double flux (b) : 1 - corps de colonne ; 2 - sections de plaques; 3, 4 - collecteurs d'admission de liquide dans les plaques supérieure et intermédiaire; 5, 6 - poches de vidange
Au fait, lisez aussi cet article : colonne à vide
L'échange masse-chaleur entre les phases en interaction (vapeur-liquide) a lieu sur le KU dans la couche bouillonnante : une structure qui se forme lorsque le flux de vapeur s'écoule de petits trous ou fentes pratiqués dans la plaque ou dans des dispositifs spéciaux (bouchons ), dans la couche liquide sous une légère surpression. Cette structure est un ensemble de bulles dont la taille se mesure en millimètres. Des bulles de vapeur sont générées lors de la sortie de gaz, flottent dans la couche liquide en raison de la différence de densité des phases liquide et vapeur et s'effondrent à la limite supérieure de la couche bouillonnante. La taille des bulles est déterminée par les propriétés des phases vapeur et liquide (densité, viscosité, tension superficielle, ...), la conception du HPC et les conditions hydrodynamiques de l'interaction des phases. La surface totale de transfert de masse dans la couche bouillonnante se mesure en dizaines voire centaines de m 2 de surface pour 1 m 3 de volume de la couche bouillonnante.
Riz. 3.3. Nœuds pour la sortie des bandes latérales (liquide) de la colonne : 1 - corps de colonne ; 2 - assiettes; 3 - poche de drainage surdimensionnée ; 4 - plaque combinée (aveugle); 5, 6 - buses pour le passage des vapeurs et l'élimination des liquides; 7 - tuyau d'équilibrage
Les types de dispositifs de contact considérés sont parmi les plus courants pour les conditions de fonctionnement des unités AT-AVT. À ce jour, d'autres conceptions CG efficaces ont été développées qui peuvent être intéressantes pour résoudre les problèmes de conception. Dans le même temps, il convient de noter qu'il est impossible de distinguer une conception universelle adaptée à toutes les conditions de fonctionnement. Chaque problème de conception spécifique doit être résolu en tenant compte de la technologie de production basée sur la généralisation de l'expérience des installations connexes.
VOUS SEREZ INTERESSE PAR :
Types de fours tubulaires
Types et conception des roulements
Types et but des rebouilleurs de différentes conceptions