Les plateaux à valves dans une colonne de distillation présentent des avantages. Conceptions de colonnes de distillation
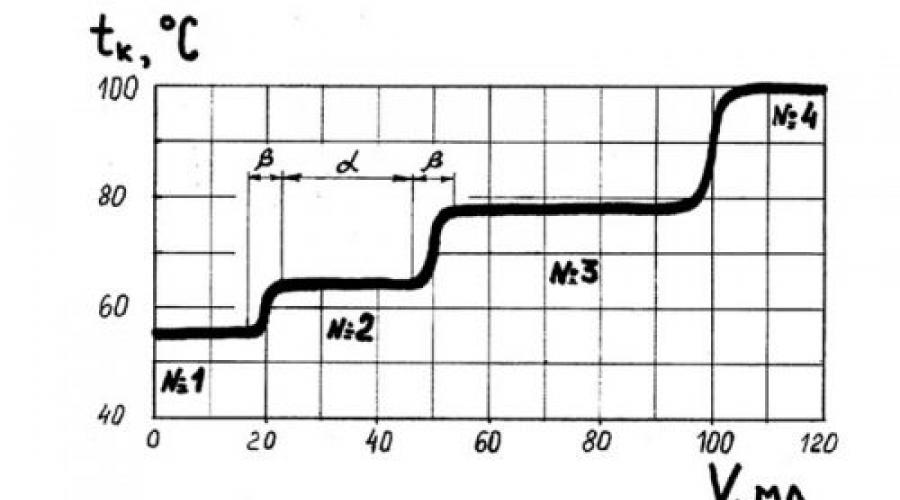
Lire aussi
La structure d'une colonne de distillation est assez complexe et il est peu probable qu'il soit possible de la simuler à la maison. Mais sur des sites Internet spécialisés, vous pouvez acheter une installation fonctionnelle à un prix très raisonnable, qui ne nécessitera encore qu'un rééquipement mineur de votre moonshine.
La conversion n'affectera que le réservoir de l'évaporateur - il est nécessaire d'installer une bride d'un diamètre approprié pour que la colonne puisse être fixée strictement verticalement. S’il n’y avait pas de thermomètre sur le réservoir, vous devrez en installer un. Sans mesurer la température sur l'évaporateur, il est extrêmement difficile de contrôler le fonctionnement de la colonne, voire impossible du tout.
Comment fonctionne une colonne ?
La colonne est un échangeur de chaleur et de masse dans lequel se produisent des processus physiques et chimiques complexes. Ils sont basés sur la différence des températures d'ébullition de divers liquides et sur la capacité thermique latente des transitions de phase. Cela semble très mystérieux, mais en pratique, cela semble un peu plus simple.
La théorie est très simple : de la vapeur contenant de l'alcool et diverses impuretés, qui bout à des températures différentes de plusieurs degrés, monte et se condense en haut de la colonne. Le liquide résultant s'écoule et rencontre en cours de route une nouvelle portion de vapeur chaude. Les liquides dont le point d'ébullition est plus élevé s'évaporent à nouveau. Et ceux qui manquent d’énergie thermique restent à l’état liquide.
Colonne de distillation est constamment dans un état d'équilibre dynamique de vapeur et de liquide ; dans de nombreux cas, il est difficile de séparer les phases liquide et gazeuse - tout bouillonne et bout. Mais selon la densité, selon l'altitude, toutes les substances sont très clairement divisées - légères en haut, puis plus lourdes, et tout en bas - les huiles de fusel, d'autres impuretés à point d'ébullition élevé, l'eau. La séparation en fractions s'effectue très rapidement, et cet état est maintenu quasiment indéfiniment, sous réserve des conditions de température dans la colonne.
À une hauteur correspondant à la teneur maximale en vapeur d'alcool, un tuyau d'admission est installé, à travers lequel la vapeur est libérée et pénètre dans le condenseur (réfrigérateur), d'où l'alcool s'écoule dans un récipient collecteur. La colonne de distillation d'un clair de lune fonctionne encore très lentement - la sélection, en règle générale, se fait goutte à goutte, mais en même temps elle est assurée haut niveau nettoyage.
La colonne fonctionne à la pression atmosphérique, ou légèrement au-dessus. Pour ce faire, une vanne atmosphérique ou simplement un tube ouvert est installé au point haut - les vapeurs qui n'ont pas eu le temps de se condenser quittent la colonne. En règle générale, ils ne contiennent pratiquement pas d'alcool.
États des composants vapeur-liquide à différentes hauteurs de la colonne
Le graphique montre les états fixes des composants vapeur-liquide à différentes hauteurs de la colonne, qui peuvent être contrôlés par la température en un point donné. La partie horizontale du graphique correspond à la concentration maximale de la substance. La division n'a pas de limites claires - la ligne verticale correspond à un mélange des fractions inférieure et supérieure. Comme vous pouvez le constater, le volume des zones limites est beaucoup plus petit que celui des zones fractionnaires, ce qui donne un certain contrecoup dans le régime de température.
Conception de la colonne de distillation
La base de la colonne est tuyau vertical en acier inoxydable ou en cuivre. D'autres métaux, notamment l'aluminium, ne conviennent pas à cet effet. Le tuyau est isolé de l'extérieur avec un matériau à faible conductivité thermique - les fuites d'énergie peuvent perturber l'équilibre établi et réduire l'efficacité des processus d'échange thermique.
Un pré-refroidisseur à reflux est monté en haut de la colonne. Il s'agit généralement d'un serpentin interne ou externe qui refroidit environ 1/8 à 1/10 de la hauteur de la colonne. Vous pouvez également trouver sur Internet des colonnes de distillation avec une chemise d'eau ou des réfrigérateurs sphériques complexes. Hormis le prix, ils n’affectent rien d’autre. La bobine classique remplit parfaitement ses tâches.
Chronique "Bébé"
Le rapport entre la quantité de condensat collectée et la quantité totale de reflux retournant au réservoir est appelé taux de reflux. Il s'agit d'une caractéristique d'un modèle de colonne individuel et décrit ses capacités de fonctionnement.
Plus le taux de reflux est faible, plus la colonne est productive. Lorsque Ф=1, la colonne fonctionne comme un alambic Moonshine ordinaire.
Les installations industrielles ont une capacité de séparation fractionnée élevée, leur nombre est donc de 1,1 à 1,4. Pour une colonne de clair de lune domestique, la valeur optimale est Ф = 3-5.
Types de colonnes
La colonne de distillation d'un alambic Moonshine est équipée de charges qui augmentent considérablement la zone de contact pour augmenter les points de contact entre la vapeur et le liquide, où se produisent les processus d'échange de chaleur et de diffusion. En fonction du type de structure interne, les colonnes sont divisées en plaques et garnies. La classification par performances ou par hauteur ne montre pas de réelles capacités.
Pour augmenter la surface de contact, un fin treillis en acier inoxydable torsadé en spirale, de petites billes lâches, des anneaux de Raschig et de petites spirales métalliques sont placés à l'intérieur de la colonne. Ils sont emballés hermétiquement ou remblayés jusqu'à une hauteur pouvant atteindre les ¾ de la longueur de la colonne, sans atteindre le point de prise d'alcool.
Le thermomètre doit être situé dans une zone exempte de buses et indiquer la température réelle de l'environnement. Un thermomètre électronique est sélectionné comme ayant la moindre inertie. Dans certains modèles de colonnes, les dixièmes de degré jouent un rôle. Pour obtenir de l'alcool pur dans la zone de sélection, la température doit être maintenue entre 72,5 et 77 C.
Une colonne de distillation à plateaux est beaucoup plus difficile à fabriquer - la conception est constituée de plateaux à capuchon ou à tamis, qui sont des cloisons horizontales à l'intérieur, à travers lesquelles le liquide s'écoule avec un certain retard. Une zone de bullage est créée sur chacune des plaques, augmentant le degré d'extraction des vapeurs d'alcool du reflux. Parfois, les colonnes de distillation sont appelées colonnes de renforcement - elles atteignent un rendement en alcool de près de cent pour cent avec un minimum d'additifs étrangers.
La colonne fonctionne à pression atmosphérique pour communiquer avec environnement externe la colonne est équipée d'une vanne spéciale ou d'un tube ouvert au sommet de la structure. Ce fait détermine l'une des caractéristiques de la colonne de distillation pour un alambic Moonshine : elle fonctionne différemment à différentes pressions atmosphériques. Le régime de température varie de quelques degrés (la différence entre le thermomètre du réservoir et celui de la colonne). La relation est établie expérimentalement. Pour cette raison, avec une colonne d'éléments chauffants.
En achetant une colonne de distillation fonctionnelle ou en la construisant vous-même, vous pouvez obtenir de l'alcool hautement purifié sans trop de difficultés. La colonne est particulièrement efficace lors de la distillation du clair de lune obtenu à partir d'un distillateur conventionnel.
Le but de l'article est d'analyser les aspects théoriques et certains aspects pratiques du fonctionnement d'une colonne de distillation domestique destinée à produire de l'alcool éthylique, ainsi que de dissiper les mythes les plus répandus sur Internet et de clarifier les points sur lesquels les vendeurs d'équipements sont « silencieux ». à propos de.
Rectification de l'alcool– séparation d'un mélange contenant de l'alcool à plusieurs composants en fractions pures (éthyle et alcool méthylique s, eau, huiles de fusel, aldéhydes et autres) ayant des points d'ébullition différents, par évaporation répétée du liquide et condensation de la vapeur sur des dispositifs de contact (plaques ou buses) dans des dispositifs spéciaux à tour à contre-courant.
D'un point de vue physique, la rectification est possible, car initialement la concentration des composants individuels du mélange dans les phases vapeur et liquide est différente, mais le système tend à s'équilibrer - la même pression, la même température et la même concentration de toutes les substances dans chaque phase. Au contact d'un liquide, la vapeur s'enrichit de composants hautement volatils (à faible point d'ébullition), et le liquide, à son tour, s'enrichit de composants non volatils (à haut point d'ébullition). Simultanément à l'enrichissement, un échange de chaleur se produit.


Le moment de contact (interaction des flux) de la vapeur et du liquide est appelé processus de transfert de chaleur et de masse.
En raison des différentes directions de mouvement (la vapeur monte et le liquide descend), une fois que le système atteint l'équilibre dans la partie supérieure de la colonne de distillation, il est possible de sélectionner séparément les composants pratiquement purs qui faisaient partie du mélange. D'abord, les substances à point d'ébullition plus bas (aldéhydes, éthers et alcools) sortent, puis celles à point d'ébullition élevé (huiles de fusel).
État d'équilibre. Apparaît à la limite même de la séparation de phases. Cela ne peut être réalisé que si deux conditions sont simultanément remplies :
- Pression égale de chaque composant individuel du mélange.
- La température et la concentration des substances dans les deux phases (vapeur et liquide) sont les mêmes.
Plus le système atteint souvent l'équilibre, plus le transfert de chaleur et de masse et la séparation du mélange en composants individuels sont efficaces.
Différence entre distillation et rectification
Comme vous pouvez le voir sur le graphique, à partir d'une solution d'alcool à 10 % (purée), vous pouvez obtenir 40 % de clair de lune, et la deuxième distillation de ce mélange donnera un distillat à 60 degrés, et la troisième – 70 %. Les intervalles suivants sont possibles : 10-40 ; 40-60 ; 60-70 ; 70-75 et ainsi de suite jusqu'à un maximum de 96 %.
Théoriquement, pour obtenir de l'alcool pur, 9 à 10 distillations consécutives sont nécessaires sur un alambic Moonshine. Dans la pratique, la distillation de liquides contenant de l'alcool avec une concentration supérieure à 20-30 % est explosive et, en raison de la dépense importante d'énergie et de temps, elle n'est pas économiquement rentable.
De ce point de vue, la rectification de l'alcool consiste en un minimum de 9 à 10 distillations simultanées, par étapes, qui se produisent sur différents éléments de contact de la colonne (buses ou plateaux) sur toute la hauteur.
Différence | Distillation | Rectification |
Organoleptiques de la boisson | Préserve l'arôme et le goût des matières premières d'origine. | Le résultat est un alcool pur, inodore et insipide (le problème a une solution). |
Force de sortie | Cela dépend du nombre de distillations et de la conception de l'appareil (généralement 40 à 65 %). | Jusqu'à 96%. |
Degré de fractionnement | Faible, les substances même avec des points d'ébullition différents se mélangent, cela ne peut pas être corrigé. | Des substances hautement pures peuvent être isolées (uniquement avec des points d'ébullition différents). |
Possibilité de supprimer produits dangereux | Faible ou moyen. Pour améliorer la qualité, un minimum de deux distillations sont nécessaires, dont au moins une divisée en fractions. | Élevé, avec la bonne approche, toutes les substances nocives sont supprimées. |
Pertes d'alcool | Grand. Même avec la bonne approche, vous pouvez extraire jusqu'à 80 % du montant total tout en conservant une qualité acceptable. | Faible. Théoriquement, il est possible d’extraire tout l’alcool éthylique sans perte de qualité. En pratique, au moins 1 à 3 % de pertes. |
Complexité de la technologie pour la mise en œuvre à domicile | Faible et moyen. Même les appareils les plus primitifs avec bobine conviennent. Des améliorations d'équipement sont possibles. La technologie de distillation est simple et directe. Un clair de lune ne prend généralement pas beaucoup de place lorsqu’il est en état de marche. | Haut. Requis équipement spécial, ce qui est impossible à produire sans connaissances et expérience. Le processus est plus difficile à comprendre ; une préparation préalable, au moins théorique, est nécessaire. La colonne prend plus de place (surtout en hauteur). |
Danger (par rapport à l'autre), les deux processus présentent des risques d'incendie et d'explosion. | Grâce à la simplicité de l'alambic Moonshine, la distillation est un peu plus sûre ( Avis subjectif auteur de l'article). | En raison d'équipements complexes, lors du travail avec lesquels il existe un risque de commettre plus d'erreurs, la rectification est plus dangereuse. |
Fonctionnement d'une colonne de distillation
Colonne de distillation– un dispositif conçu pour séparer un mélange liquide à plusieurs composants en fractions distinctes en fonction du point d'ébullition. Il s'agit d'un cylindre de section constante ou variable, à l'intérieur duquel se trouvent des éléments de contact - plaques ou buses.
De plus, presque chaque colonne dispose d'unités auxiliaires pour fournir le mélange initial (alcool brut), surveiller le processus de rectification (thermomètres, automatisation) et sélectionner le distillat - un module dans lequel la vapeur d'une certaine substance extraite du système est condensée puis prélevée. dehors.


Alcool brut– un produit de distillation de purée selon la méthode de distillation classique, qui peut être « versé » dans une colonne de distillation. En fait, il s'agit d'un clair de lune d'une force de 35 à 45 degrés.
Reflux– de la vapeur condensée dans le déflegmateur, s'écoulant le long des parois de la colonne.
Taux de reflux– le rapport entre la quantité de mucosités et la masse de distillat prélevé. Il y a trois flux dans une colonne de distillation d'alcool : la vapeur, le reflux et le distillat (le but final). Au début du processus, le distillat n'est pas soutiré afin qu'un reflux suffisant apparaisse dans la colonne pour le transfert de chaleur et de masse. Ensuite, une partie de la vapeur d'alcool est condensée et extraite de la colonne, et la vapeur d'alcool restante continue de créer un flux de reflux, assurant un fonctionnement normal.
Pour que la plupart des installations fonctionnent, le taux de reflux doit être d'au moins 3, c'est-à-dire que 25 % du distillat est prélevé, le reste est nécessaire dans la colonne d'irrigation des éléments de contact. Règle générale: plus l'alcool est échantillonné lentement, plus la qualité est élevée.
Dispositifs de contact de la colonne de distillation (plaques et buses)
Ils sont responsables de la séparation répétée et simultanée du mélange en liquide et vapeur, suivie de la condensation de la vapeur en liquide, atteignant ainsi un état d'équilibre dans la colonne. Toutes choses égales par ailleurs, plus il y a de dispositifs de contact dans la conception, plus la rectification est efficace en termes de purification de l'alcool, car la surface d'interaction de phase augmente, ce qui intensifie tout le transfert de chaleur et de masse.
Planche théorique– un cycle consistant à quitter l’état d’équilibre et à y parvenir à nouveau. Pour obtenir un alcool de haute qualité, un minimum de 25 à 30 assiettes théoriques sont nécessaires.
Plaque physique- un appareil vraiment fonctionnel. La vapeur traverse la couche de liquide présente dans la plaque sous forme de nombreuses bulles, créant une grande surface de contact. Dans la conception classique, la plaque physique fournit environ la moitié des conditions nécessaires pour atteindre un état d’équilibre. Par conséquent, pour le fonctionnement normal d'une colonne de distillation, deux fois plus de plaques physiques sont nécessaires que le minimum théorique (calculé) - 50 à 60 pièces.
Buses Souvent, les plaques sont installées uniquement sur des installations industrielles. Dans les colonnes de distillation de laboratoire et à domicile, des buses sont utilisées comme éléments de contact - fil de cuivre (ou d'acier) spécialement torsadé ou treillis pour lave-vaisselle. Dans ce cas, le reflux s'écoule en un mince filet sur toute la surface de la buse, offrant ainsi une surface de contact maximale avec la vapeur.


Il existe de nombreux modèles. L'inconvénient des attaches métalliques faites maison est l'endommagement possible du matériau (noircissement, rouille) ; les analogues d'usine sont exempts de tels problèmes.
Propriétés de la colonne de distillation
Matériel et tailles. Le cylindre de la colonne, les buses, le cube et les distillateurs doivent être fabriqués en alliage de qualité alimentaire, inoxydable, sûr lorsqu'il est chauffé (se dilate uniformément). Dans les conceptions faites maison, les canettes et les autocuiseurs sont le plus souvent utilisés sous forme de cube.
La longueur minimale du tuyau d'une colonne de distillation domestique est de 120 à 150 cm et son diamètre est de 30 à 40 mm.
Système de chauffage. Lors du processus de rectification, il est très important de contrôler et d’ajuster rapidement la puissance de chauffage. Par conséquent, la solution la plus efficace consiste à chauffer à l’aide d’éléments chauffants montés dans la partie inférieure du cube. Apport de chaleur par cuisinière à gaz déconseillé car il ne permet pas de modifier rapidement la plage de température (forte inertie du système).
Contrôle de processus. Lors de la rectification, il est important de suivre les instructions du fabricant de la colonne, qui doivent indiquer les caractéristiques de fonctionnement, la puissance de chauffage, le taux de reflux et les performances du modèle.


Il est très difficile de contrôler le processus de rectification sans deux appareils simples : un thermomètre (aide à déterminer le degré de chauffage correct) et un alcoomètre (mesure le titre de l'alcool obtenu).
Performance. Cela ne dépend pas de la taille de la colonne, puisque plus le tiroir (tuyau) est haut, plus il y a de plaques physiques à l'intérieur, donc meilleur est le nettoyage. La productivité est affectée par la puissance de chauffage, qui détermine la vitesse des flux de vapeur et de reflux. Mais s'il y a un excès de puissance fournie, la colonne s'étouffe (cesse de fonctionner).
La productivité moyenne des colonnes de distillation domestique est de 1 litre par heure avec une puissance de chauffe de 1 kW.
Effet de pression. Le point d'ébullition des liquides dépend de la pression. Pour une rectification réussie de l'alcool, la pression au sommet de la colonne doit être proche de la pression atmosphérique - 720-780 mmHg. Sinon, à mesure que la pression diminue, la densité de vapeur diminuera et le taux d'évaporation augmentera, ce qui pourrait provoquer un débordement de la colonne. Quand aussi hypertension artérielle le taux d'évaporation diminue, rendant l'appareil inefficace (il n'y a pas de séparation du mélange en fractions). Pour maintenir la bonne pression, chaque colonne de distillation d'alcool est équipée d'un tube de communication avec l'atmosphère.
A propos de la possibilité d'un montage maison. Théoriquement, une colonne de distillation n’est pas un dispositif très complexe. Les conceptions sont mises en œuvre avec succès par des artisans à domicile.
Mais dans la pratique, sans comprendre les fondements physiques du processus de rectification, les calculs corrects des paramètres de l'équipement, la sélection des matériaux et l'assemblage de haute qualité des composants, l'utilisation d'une colonne de distillation artisanale se transforme en une activité dangereuse. Une seule erreur peut entraîner un incendie, une explosion ou des brûlures.
En termes de sécurité, les colonnes fabriquées en usine qui ont réussi les tests (avec documentation à l'appui) sont plus fiables et sont également accompagnées d'instructions (qui doivent être détaillées). Le risque d'une situation critique se résume à seulement deux facteurs : un montage correct et un fonctionnement conforme aux instructions, mais il s'agit d'un problème avec presque tous les appareils électroménagers, et pas seulement les colonnes ou les alambics Moonshine.
Principe de fonctionnement d'une colonne de distillation
Le cube est rempli au maximum aux 2/3 de son volume. Avant de mettre l'installation en marche, veiller à vérifier l'étanchéité des raccords et du montage, éteindre l'unité de sélection de distillat et alimenter en eau de refroidissement. Ce n'est qu'après cela que vous pourrez commencer à chauffer le cube.
La concentration optimale du mélange contenant de l'alcool introduit dans la colonne est de 35 à 45 %. Autrement dit, avant la rectification, une distillation du moût est nécessaire. Le produit obtenu (alcool brut) est ensuite traité dans une colonne, obtenant un alcool presque pur.
Cela signifie qu'une colonne de distillation domestique ne remplace pas complètement un alambic Moonshine classique (distillateur) et ne peut être considérée que comme une étape de purification supplémentaire qui remplace mieux la redistillation (deuxième distillation), mais neutralise les propriétés organoleptiques de la boisson.
Pour être honnête, je note que la plupart des modèles modernes de colonnes de distillation nécessitent un fonctionnement en mode alambic Moonshine. Pour passer à la distillation, il suffit de fermer la connexion avec l'atmosphère et d'ouvrir l'unité de sélection du distillat.
Si les deux raccords sont fermés en même temps, la colonne chauffée peut exploser en raison d'une surpression ! Ne faites pas de telles erreurs !
Dans les installations industrielles action continue Souvent, la purée est distillée immédiatement, mais cela est possible en raison de sa taille gigantesque et de ses caractéristiques de conception. Par exemple, la norme est un tuyau de 80 mètres de haut et 6 mètres de diamètre, dans lequel sont installés beaucoup plus d'éléments de contact que sur les colonnes de distillation pour la maison.


Après la mise sous tension, le liquide contenu dans le cube est porté à ébullition par le chauffage. La vapeur résultante monte dans la colonne, puis entre dans le condenseur à reflux, où elle se condense (un reflux apparaît) et retourne sous forme liquide le long des parois des tuyaux jusqu'à la partie inférieure de la colonne, au retour entrant en contact avec la vapeur montante sur les plateaux. ou des buses. Sous l'action du réchauffeur, le reflux redevient de la vapeur, et la vapeur en haut est à nouveau condensée par le condenseur à reflux. Le processus devient cyclique, les deux flux étant continuellement en contact l’un avec l’autre.
Après stabilisation (la vapeur et le reflux suffisent pour un état d'équilibre), les fractions pures (séparées) ayant le point d'ébullition le plus bas (alcool méthylique, acétaldéhyde, éthers, alcool éthylique) s'accumulent dans la partie supérieure de la colonne, et celles ayant le point d'ébullition le plus élevé ( huiles de fusel) s'accumulent au fond. Au fur et à mesure de la sélection, les fractions inférieures montent progressivement dans la colonne.
Dans la plupart des cas, une colonne dans laquelle la température ne change pas pendant 10 minutes est considérée comme stable (la sélection peut commencer). temps totaléchauffement – 20-60 minutes). Jusqu’à ce moment, l’appareil fonctionne « sur lui-même », créant des flux de vapeur et des reflux qui tendent à l’équilibre. Après stabilisation, commence la sélection de la fraction de tête, contenant des substances nocives : éthers, aldéhydes et alcool méthylique.
Une colonne de distillation n’élimine pas la nécessité de séparer le produit en fractions. Comme dans le cas d'un alambic Moonshine classique, il faut assembler la « tête », le « corps » et la « queue ». La seule différence est la pureté du résultat. Lors de la rectification, les fractions ne sont pas "lubrifiées" - les substances dont les points d'ébullition sont proches, mais différents d'au moins un dixième de degré, ne se croisent pas. Par conséquent, lorsque le "corps" est sélectionné, on obtient de l'alcool presque pur. Lors d'une distillation conventionnelle, il est physiquement impossible de séparer le produit en fractions constituées d'une seule substance, quelle que soit la conception utilisée.
Si la colonne est réglée sur le mode de fonctionnement optimal, il n'y a aucune difficulté à sélectionner le « corps », puisque la température est tout le temps stable.
Lors de la rectification, les fractions inférieures (« queues ») sont sélectionnées en fonction de la température ou de l'odeur, mais contrairement à la distillation, ces substances ne contiennent pas d'alcool.
Retour des propriétés organoleptiques à l'alcool. Souvent, des « queues » sont nécessaires pour redonner « l’âme » à l’alcool rectifié – l’arôme et le goût de la matière première d’origine, par exemple une pomme ou un raisin. Une fois le processus terminé, une certaine quantité des résidus collectés est ajoutée à de l'alcool pur. La concentration est calculée empiriquement en expérimentant avec une petite quantité de produit.
L’avantage de la rectification est la possibilité d’extraire la quasi-totalité de l’alcool contenu dans le liquide sans perdre sa qualité. Cela signifie que les « têtes » et les « queues » obtenues dans un alambic Moonshine peuvent être traitées dans une colonne de distillation et produire de l'alcool éthylique sans danger pour la santé.
Inondation de la colonne de distillation
Chaque modèle a une vitesse maximale de mouvement de la vapeur, après quoi le flux de reflux dans le cube ralentit d'abord puis s'arrête complètement. Le liquide s'accumule dans la partie distillation de la colonne et une « inondation » se produit - l'arrêt du processus de transfert de chaleur et de masse. Il y a une forte chute de pression à l'intérieur et des bruits parasites ou des gargouillis apparaissent.
Raisons du noyage de la colonne de distillation :
- dépassement de la puissance de chauffage autorisée (le plus courant) ;
- colmatage du fond de l'appareil et remplissage excessif du cube ;
- pression atmosphérique très basse (typique des hautes montagnes) ;
- la tension du réseau est supérieure à 220 V - en conséquence, la puissance des éléments chauffants augmente ;
- erreurs de conception et dysfonctionnements.
RectificUNtion(du latin tardif rectificatio - redressage, correction), une des méthodes de séparation des mélanges liquides, basée sur la répartition différente des composants du mélange entre les phases liquide et vapeur. Lors de la rectification, des flux de vapeur et de liquide, se déplaçant dans des directions opposées (à contre-courant), se contactent à plusieurs reprises dans des appareils spéciaux (colonnes de distillation), et une partie de la vapeur (ou du liquide) sortant de l'appareil est restituée après condensation (pour la vapeur) ou évaporation (pour les liquides). Ce mouvement à contre-courant des flux en contact s'accompagne de processus d'échange thermique et de transfert de masse, qui à chaque étape de contact procèdent (à la limite) à un état d'équilibre ; dans ce cas, les flux de vapeur ascendants sont continuellement enrichis de composants plus volatils, et le liquide qui s'écoule - de composants moins volatils. Utilisant la même quantité de chaleur que lors de la distillation, la rectification permet d'obtenir une plus grande extraction et un enrichissement du composant ou du groupe de composants souhaité. La rectification est largement utilisée à l'échelle industrielle, préparative et en laboratoire, souvent en combinaison avec d'autres procédés de séparation, tels que l'absorption, l'extraction et la cristallisation.
Selon les lois de Raoult et de Dalton, dans des conditions d'équilibre thermodynamique, la concentration de tout jeème composant d'une paire K je fois différent de sa concentration dans le liquide, et le coefficient de distribution K je=p je */p
(Où p je * —
pression de vapeur saturée je-ième composant ; R- pression totale). Rapport du coefficient de distribution de deux composants quelconques K je Et Kj est appelée volatilité relative et est désignée par un ij. Plus un je de l’unité, plus il est facile de séparer ces composants par rectification. Dans certains cas, il est possible d'augmenter un je résultant de l'introduction dans le mélange à séparer d'un nouveau composant (appelé agent de séparation), qui forme un mélange azéotropique avec certains composants du système. Dans le même but, un solvant est introduit, bouillant à une température beaucoup plus élevée que les composants du mélange d'origine. Les procédés de rectification correspondants sont dits azéotropiques ou extractifs. Valeur un je dépend de la pression : en règle générale, lorsque la pression diminue, je augmente. Rectification à basses pressions- vide - particulièrement adapté à la séparation de substances thermiquement instables.
Colonne de distillation
Équipement de rectification
Au cours du processus de distillation (distillation simple), le tétrachlorure de titane, contenant des impuretés solides, est chauffé jusqu'au point d'ébullition dans des cubes évaporateurs spéciaux. Les vapeurs résultantes pénètrent dans le condenseur et les résidus solides s'accumulent dans le cube évaporateur. Lors de la distillation, il n'est pas possible d'obtenir du TiCl 4 suffisamment pur, c'est pourquoi un processus plus complexe est utilisé - la rectification.
La rectification est réalisée dans une installation de rectification comprenant une colonne de distillation, un condenseur à reflux, un réfrigérateur-condenseur, un réchauffeur du mélange d'alimentation et des collecteurs pour le distillat et les résidus.
Colonne de distillation
1 - tuyau de trop-plein ; 2 - assiette; 3 - corps; 4 - évaporateur cubique
Le condenseur à reflux, le réfrigérateur-condenseur et le réchauffeur sont des échangeurs de chaleur classiques. L'appareil principal de l'installation est une colonne de distillation, dans laquelle les vapeurs du liquide distillé montent par le bas, et le liquide s'écoule vers les vapeurs par le haut, amenées à la partie supérieure de l'appareil sous forme de reflux. Dans la plupart des cas, les produits finaux sont un distillat (une vapeur d'un composant hautement volatil condensée dans un condenseur à reflux, quittant le haut de la colonne) et un fond (un composant moins volatil, s'écoulant sous forme liquide depuis le bas de la colonne). ).
Les chaudières des installations de distillation de faible capacité sont réalisées sous forme de serpentins installés directement dans le cube, mais le plus souvent la chaudière est montée sous la forme d'un échangeur de chaleur à distance, placé verticalement à proximité du cube et relié à celui-ci par deux tuyaux. . Cubes de colonnes action périodique diffèrent par leur capacité suffisante pour accepter une charge simultanée de produit. Les colonnes continues ne nécessitent pas un grand volume de liquide de fond et l'évaporateur qu'elles contiennent peut être Partie inférieure colonnes de 1,0 à 2,5 m de haut.
Dans la production de TiC1 4, des colonnes de distillation à plaques et à garnissage sont utilisées pour éliminer les impuretés à bas et à haut point d'ébullition. Les colonnes à garnissage avec anneaux Raschig en céramique sont inefficaces et nécessitent un remplacement fréquent de la garniture. DANS colonnes de plats Deux types de dispositifs de contact sont utilisés : des plaques grillagées et des plaques tamisées avec trop-plein. Les dispositifs à disque du premier type sont faciles à fabriquer et restent toujours les principaux de l'industrie du titane. Ils sont fabriqués par estampage, avec des fentes de même taille percées. Pour nettoyer les impuretés difficiles à éliminer, il est conseillé d'utiliser des plaques grillagées de 2 à 4 mm d'épaisseur avec une section libre de 16 à 22 % et une taille de fente de 4 x 60 mm. La distance entre les plateaux dépend du diamètre de la colonne. Lors de l'assemblage, chaque plaque est installée dans le corps de la colonne et l'espace est éliminé à l'aide d'un film d'étanchéité en plastique fluoré.
Les plateaux tamis avec trop-plein n'ont pas encore fait l'objet de tests industriels à long terme, mais l'expérience de leur utilisation dans des domaines connexes montre qu'ils se caractérisent par une efficacité plus élevée. sur une large gamme de changements de charge. Les plaques d'un diamètre de 400 à 3 600 mm ont un diamètre de trou de 3 à 8 mm, la section de perforation libre pour les colonnes d'un diamètre de 400 à 1 200 mm est de 3 à 14 %. Par rapport aux plaques de tamisage, les plaques de tamisage sont plus complexes et demandent plus de main-d'œuvre à fabriquer.
Le chauffage du cube évaporateur est électrique ; à cet effet, des radiateurs ouverts en bandes ou en nichrome rond sont utilisés ; La puissance du cube est déterminée par le nombre et la puissance des éléments chauffants individuels. Un appareil situé verticalement se caractérise par une production de vapeur stable, mais s'obstrue rapidement par des particules solides et est plus difficile à entretenir. Dans les appareils horizontaux, la production constante de vapeur est assurée par un trop-plein spécial.
La condensation de vapeur se produit dans les condenseurs à reflux, qui sont utilisés comme échangeurs de chaleur à calandre refroidis à l'eau ou comme serpentins plats refroidis par air du type AVM (appareil refroidi par air à faible débit). Les coefficients de transfert thermique sont respectivement de 210-294 et 42-84 kJ/(m 2 h °C).
Les condenseurs à reflux à calandre sont difficiles à fabriquer, ont une durée de vie courte (jusqu'à 1 an) et il existe un risque que de l'eau pénètre dans les produits du procédé. La durée de vie des condenseurs à reflux d'air est de 10 à 12 ans. Pour augmenter la surface de transfert de chaleur, les tuyaux AVM ont des nervures, ce qui permet d'augmenter la surface de transfert de chaleur de 10 à 20 fois.
Buses et plaques
Le but des plateaux et de la buse est de développer la surface interfaciale et d'améliorer le contact entre le liquide et la vapeur. Les plaques sont généralement équipées d'un dispositif de débordement de liquide. Constructions trois types les plaques de trop-plein sont illustrées dans la figure ci-dessous.
Schéma des plaques avec dispositif de trop-plein :
a - type de bouchon (1 - base avec une couche de liquide ; 2 - tuyaux pour le passage de la vapeur ; 3 - bouchons ;
4, 5 - dispositifs de trop-plein); b - à partir d'éléments en forme de S (6) ; c - tamis.
Types de buses
1 — Anneaux de Raschig ; 2 — anneaux en spirale ; 3 — anneaux avec cloison; 4 - Pahl sonne.
Dans les colonnes à garnissage et à disques, l'énergie cinétique de la vapeur est utilisée pour surmonter la résistance hydraulique des dispositifs de contact et pour créer un système vapeur-liquide dispersé dynamique avec une grande surface interfaciale. Il existe également des colonnes de distillation à alimentation mécanique en énergie, dans lesquelles un système dispersé est créé par la rotation d'un rotor monté le long de l'axe de la colonne. Les appareils rotatifs ont une perte de charge plus faible en hauteur, ce qui est particulièrement important pour les colonnes à vide.
Selon la méthode de mise en œuvre, une distinction est faite entre la rectification continue et périodique. Dans le premier cas, le mélange à séparer est introduit en continu dans une colonne de distillation et deux ou plusieurs fractions, enrichies en certains composants et appauvries en d'autres, sont continuellement retirées de la colonne. L'organigramme d'un appareil de distillation continue typique - une colonne pleine - est présenté dans la figure ci-dessous ( UN).
Diagrammes de flux de colonne de distillation
a - rectification continue ; b - rectification périodique ; 1 - section de renfort ;
2 - rubrique exhaustive ; 3 - cube de colonnes ; 4 - condenseur à reflux.
Une colonne complète se compose de 2 sections - renforcement ( 1 ) et exhaustif ( 2 ). Le mélange initial (généralement au point d'ébullition) est introduit dans la colonne, où il est mélangé avec ce qu'on appelle. le liquide extrait et s'écoule vers les dispositifs de contact (plaques ou buse) de la section d'échappement à contre-courant du flux de vapeur ascendant. Ayant atteint le fond de la colonne, le flux liquide, enrichi en composants hautement volatils, est introduit dans le cube de la colonne ( 3 ). Ici, le liquide est partiellement évaporé en chauffant avec un liquide de refroidissement approprié, et la vapeur pénètre à nouveau dans la section d'échappement. La vapeur sortant de cette section (appelée vapeur de stripping) entre dans la section de renforcement. Après l'avoir traversé, la vapeur enrichie en composants volatils pénètre dans le condenseur à reflux ( 4 ), où il est généralement complètement condensé avec un réfrigérant approprié. Le liquide obtenu est divisé en 2 flux : distillat et reflux. Le distillat est un flux de produit, et le reflux va irriguer la section de renforcement, à travers les dispositifs de contact dont il s'écoule. Une partie du liquide est retirée du cube de la colonne sous la forme de ce qu'on appelle. fonds (également flux de produits).
Le rapport entre la quantité de reflux et la quantité de distillat est noté R. et s'appelle le rapport de reflux. Ce numéro est caractéristique importante rectification : plus R., plus les coûts d’exploitation du procédé sont élevés. Les coûts minimaux requis de chaleur et de froid associés à l'exécution de toute tâche de séparation spécifique peuvent être déterminés à l'aide du concept de taux de reflux minimum, qui est déterminé par calcul en supposant que le nombre de dispositifs de contact ou la hauteur totale de la buse , tend vers l’infini.
Si le mélange initial doit être divisé en continu en un nombre de fractions supérieur à deux, une connexion de colonnes en série ou en série parallèle est utilisée.
Avec rectification périodique ( b) le mélange liquide initial est simultanément chargé dans le cube de colonne dont la capacité correspond à la productivité souhaitée. Les vapeurs du cube pénètrent dans la colonne et montent jusqu'au condenseur à reflux, où elles sont condensées. Dans la période initiale, tous les condensats retournent dans la colonne, ce qui correspond à ce qu'on appelle. mode d'irrigation complet. Le condensat est ensuite divisé en reflux et distillat. Au fur et à mesure que le distillat est sélectionné (soit avec un taux de reflux constant, soit avec son changement), les composants hautement volatils sont d'abord retirés de la colonne, puis les composants modérément volatils, etc. La ou les fractions requises sont sélectionnées dans la collection appropriée. . L'opération se poursuit jusqu'à ce que le mélange initialement chargé soit complètement traité.
Récemment, beaucoup de gens ne font pas confiance à la qualité de l'alcool proposé par les magasins et le coût de ces produits est élevé. Par conséquent, souvent dans les cuisines à côté de divers appareils ménagers vous pouvez encore voir le clair de lune. Après tout, les boissons alcoolisées faites maison sont respectueuses de l'environnement et moins nocives pour la santé en quantités raisonnables. Cependant, tous les distillateurs sont confrontés à un problème : purifier l'alcool des impuretés nocives et Odeur désagréable. Les propriétaires expérimentés et économiques utilisent pour cela une colonne de distillation. Eh bien, afin de suivre le rythme des distillateurs plus avancés, les débutants doivent apprendre ce qu'est une colonne de distillation dans un alambic Moonshine.
La colonne de rectification permet la production de boissons contenant de l'alcool, telles que la vodka, le whisky, les liqueurs hautement purifiées et à fort titre (jusqu'à 97 %). La structure d'une colonne de distillation classique est la suivante :
- Cube d'évaporation.
- Une colonne avec une buse spéciale dans laquelle se déroulent les processus de transfert de chaleur et de masse (tsarga).
- Déphlegmateur.
- Unité de collecte de distillat.
Cube d'évaporation
Le cube d'évaporation est un récipient dans lequel la purée est chauffée. Au cours du processus, il s’évapore et la vapeur monte dans la colonne. Au sommet du redresseur, le liquide est divisé en fractions distinctes.
Le cube d'évaporation se chauffe sur tout type de plaque. Et certains de ses modèles nécessitent un appareil de chauffage. Un cube acheté doit être équipé d'un thermomètre, qui permet de contrôler le chauffage de la purée. Le cube d'évaporation est absolument hermétique. Lors de l'ébullition, il est important que le liquide et la vapeur restent à l'intérieur. Le cube ne peut pas être rempli de purée à plus des 2/3 de son volume, sinon le liquide éclaboussera hors du récipient.
Tsarga
Les processus suivants se produisent dans cette partie de la colonne de distillation :
- La purée contenue dans le cube s'évapore sous l'influence de la chaleur et remonte dans la colonne. Un réfrigérateur y est installé.
- Le réfrigérant à reflux assure la condensation des vapeurs d'alcool et la production d'un distillat.
- Le distillat descend dans la colonne d'alcool. À ce moment, il entre en collision avec la vapeur – transfert de chaleur et de masse.
- À la suite de ce processus, la partie évaporée de la fraction remonte dans la colonne. Ici, il se condense puis passe dans le canal de sélection.
N'oubliez pas que si vous augmentez la hauteur de la colonne, le transfert de chaleur et de masse s'effectue plus activement. Il en résulte une production d'alcool plus rectifiée.
Buse de redressement
La buse de rectification comporte deux parties :
- Unité de sélection d'alcool. Dans une colonne de distillation industrielle, cette partie est équipée d'un voyant, qui permet de déterminer le taux de sélection d'alcool.
- Déphlegmateur. Parfois, cette partie est appelée le réfrigérateur. Le condenseur à reflux est situé en tête de la colonne de distillation. Il est nécessaire de collecter les vapeurs de clair de lune et de les transformer en mucosités, qui sont libérées vers le bas. Ici, il est enrichi de vapeur d’alcool. Une fois que les mucosités sont entrées dans l'unité de sélection, la partie évaporée en sort.
La colonne de distillation a une structure simple, le principe de son fonctionnement peut donc être facilement expliqué. Ce mécanisme agit comme un filtre dans lequel les huiles de fusel se déposent. Il y a une interaction constante de vapeur d'alcool et de liquide, en d'autres termes, une rectification. Une fois que la purée s'est réchauffée à 70 degrés dans le cube d'évaporation, l'alcool commence à s'évaporer. Il monte dans le tuyau et aboutit dans le condenseur à reflux. Dans cette partie, la recondensation se produit avec la vapeur lorsqu'elle est refroidie avec de l'eau. Le condensat (reflux) s'écoule et retrouve la vapeur chaude. Un échange se produit entre les deux composants - le processus de saturation des mucosités en vapeur et de la vapeur en liquide, qui a basse températureébullition.
La condensation finale de la vapeur se produit au réfrigérateur. Le résultat est de l'alcool purifié, qui s'écoule dans un récipient récepteur. Au sommet de la colonne de distillation se trouve une vanne atmosphérique. Il est nécessaire pour que les vapeurs qui ne contiennent pas d'alcool et ne soient pas sujettes à la condensation quittent le mécanisme.
La rectification continue se produit grâce à des éléments de contact spéciaux - des plaques physiques dans les colonnes de distillation achetées et des éponges métalliques ou des billes de verre dans des échantillons fabriqués à la main. Ces pièces sont nécessaires pour augmenter l'efficacité de l'interaction entre la vapeur et le reflux.
Types de colonnes
Il existe les types de colonnes de distillation suivants :
- Type de disque. De telles unités ont des plaques à l'intérieur qui sont installées à une certaine distance. Des transferts de chaleur et de masse s'y effectuent. Les colonnes de distillation de ce type sont coûteuses et assez encombrantes. Mais ils ont le principal avantage : les factions sont séparées avec précision.
- Type de pièce jointe. Le mécanisme comporte deux types de fixation en cuivre. Le premier est une dispersion de petits éléments en acier inoxydable remplissant la colonne. Leur placement inégal complique le passage des vapeurs et l'écoulement des mucosités. Le deuxième type est une buse Panchenkov, qui effectue un transfert efficace de chaleur et de masse.
Est-il possible de fabriquer soi-même une colonne de distillation à part entière ?
Il y en a des confortables et de haute qualité en vente alambics au clair de lune avec une colonne de distillation. Mais leur coût est élevé. Par conséquent, les hommes qui savent travailler les métaux peuvent fabriquer eux-mêmes l’unité. Pour créer une colonne, les matériaux qui n'entrent pas dans réactions chimiques avec de l'alcool et ne libèrent pas divers éléments nocifs pour la santé humaine dans le temps. Pour créer l'unité, vous aurez besoin de :
- Un récipient du volume requis sous forme de cube de distillation. Il peut s'agir de n'importe quel récipient en cuivre ou en émail. L'acier inoxydable fonctionnera également. S'il y a un faible rendement en alcool, utilisez un autocuiseur.
- Corps de colonne en forme de tiroir ou de tuyau. Dans les rayons des magasins, vous pouvez rapidement trouver un tiroir de 15 centimètres prêt à l'emploi. Achetez plusieurs pièces et connectez-les. Ou vous pouvez facilement fabriquer cette pièce à partir d'un tuyau en acier inoxydable d'un diamètre de 0,5 centimètre et d'une épaisseur de paroi de 1,5 à 2 millimètres. Un filetage est réalisé des deux côtés de celui-ci : le bas est fixé au cube, et le haut est relié au condenseur à reflux. Le tiroir doit mesurer au moins un mètre de hauteur, sinon les fractions nocives ne seront pas éliminées et les huiles de fusel se retrouveront dans le distillat. Le résultat sera un produit de mauvaise qualité. Si vous réalisez un tuyau d'une longueur supérieure à 1,5 mètre, le temps de rectification augmentera, mais l'efficacité restera la même.
- Déphlegmateur pour refroidir et condenser la vapeur. Il peut être gainé ou direct. Fabriqué à partir de deux tuyaux entre lesquels circule l’eau. Le condenseur à reflux Dimroth est considéré comme plus efficace. Le corps devient un tuyau, à l'intérieur duquel se trouve un mince tube en forme de spirale. Il y circule eau froide. Déphlegmateur à coque et tube- à partir de plusieurs tuyaux. Dans le plus grand, ils attachent les petits. La vapeur s'y condense.
- Buses pour le tiroir. Ils augmentent la surface sur laquelle s’écoulent les mucosités. Cela signifie que les impuretés nocives se déposent et ne finissent pas dans l'alcool fait maison. Des buses en forme de billes en céramique ou d'éponges de cuisine découpées en acier inoxydable doivent remplir complètement le tiroir. Une buse Panchenkov est également utilisée. Elle est la meilleure option.
- Unité de sélection de distillat.
- Réfrigérateur. Cette pièce est fabriquée de la même manière qu'un condenseur à reflux à double enveloppe. Mais des tubes de plus petit diamètre sont pris. Le réfrigérateur dispose de passages pour l'eau. Il entre dans le trou inférieur et depuis le trou supérieur, le liquide est dirigé à travers des tubes vers le déflegmateur.
- Petites pièces pour relier les pièces.
- Thermomètre.
La méthode de rectification a à la fois des partisans et des opposants. Il présente les aspects positifs suivants :
- Le résultat est un alcool fort Haute qualité, qui ne contient pas d'impuretés nocives pour la santé humaine. Ce sera une excellente base pour toute boisson alcoolisée.
- Vous pouvez préparer du clair de lune avec les propriétés organoleptiques souhaitées.
- L'appareil est assez simple à construire soi-même.
Les distillateurs notent les inconvénients suivants :
- L'ensemble du processus de rectification prend beaucoup de temps. Un seul litre de distillat est obtenu par heure.
- Les conceptions de fabrication sont coûteuses.
Cependant, étant donné les avantages incontestables de la colonne, elle vaut toujours la peine d'être achetée. Et puis il n'y aura aucune plainte concernant la qualité du clair de lune.
Plaque multi-capsules avec des capuchons ronds - le plus courant (Fig. 7.68). Il comporte une tôle avec des trous pour les tuyaux de vapeur, qui sont fixés à la tôle.
Des capuchons sont installés au-dessus des buses, le plus souvent d'un diamètre de 60 et 80 mm. Les bouchons ont des fentes d'une hauteur de 15, 20 ou 30 mm Pour créer le niveau de liquide requis, des tubes de trop-plein situés le long du diamètre ou des cloisons de trop-plein segmentées sont utilisés. Les fentes des bouchons doivent être immergées dans le liquide, de sorte que les tubes de trop-plein et les cloisons dépassent au-dessus de la plaque jusqu'à une certaine hauteur. La vapeur entre par le tuyau de vapeur, passe par les fentes et bouillonne à travers la couche de liquide. Lorsque la vapeur et le liquide interagissent, une mousse finement poreuse se forme et des composants sont échangés entre les phases. Il y a un flux croisé de liquide et de vapeur sur la plaque. Ces plaques appartiennent au groupe des dispositifs à contact à bulles. Le liquide s'écoule d'assiette en assiette à travers des dispositifs de trop-plein (verres). La vapeur passe vers vous de bas en haut.
Les dispositifs de contact à capuchon ont une large plage de fonctionnement stable, un coefficient relativement élevé action utile(0,5-0,7), mais ont une résistance hydraulique élevée et peuvent être utilisés pour traiter un liquide pur. L'inconvénient est également la consommation importante de métal et la complexité de fabrication.
Plaque de capuchon simple fonctionne de la même manière qu'un multi-cap. Les plateaux à capuchon unique fonctionnent bien dans les colonnes de petit diamètre. À mesure que le diamètre augmente, leur efficacité diminue.
Les plaques multi-bouchons sont utilisées dans les colonnes des installations de distillation : épuration, alcool, fusel, purification finale. Ils sont également utilisés dans la partie concentration des installations de distillation pour produire de l’alcool brut. Dans les installations modernes, les colonnes d'épuration disposent de 39 à 40 plateaux multi-bouchons et les colonnes d'alcool de 71 à 74.
Les colonnes de purée de l'installation de distillation et la partie d'épuisement de la colonne de l'installation de distillation sont équipées de plateaux mono-capuchon. Ils peuvent être utilisés pour distiller de la purée et d’autres liquides contenant des matières en suspension.
Plaque grillagée est l'un des dispositifs de contact à disque les plus simples (Fig. 7.69.). Il s'agit d'un disque métallique perforé avec des trous d'un diamètre de 2 à 12 mm, placés sur le plan de la plaque le long des sommets des triangles équilatéraux. La plaque est fixée horizontalement dans la colonne. Pour maintenir un certain niveau de liquide dans les colonnes de petit diamètre, on utilise des tubes de trop-plein dont les extrémités inférieures sont immergées dans des verres solides. Dans les colonnes de plus grand diamètre, des cloisons de trop-plein segmentées sont utilisées. La vapeur qui monte dans la colonne traverse les trous du plateau et se répartit dans la couche de liquide sous forme de bulles et de filets. Dans ce cas, un transfert de masse se produit entre les phases. Les plaques grillagées ont une section libre (le plan des trous) plus grande que les plaques à capuchon, c'est pourquoi leur débit de vapeur est de 30 à 40 % plus élevé que celui des plaques à capuchon. Le niveau de liquide sur le plateau est maintenu par une certaine pression dans la colonne. Lorsque la pression diminue, le liquide peut s'écouler à travers les trous sur tout le plan de la plaque ou de ses parties individuelles, ce qui altère le transfert de masse. Cela peut également se produire si les plaques ne sont pas positionnées avec précision (mal alignées).
Les plaques grillagées sont efficaces, faciles à fabriquer, ont une faible consommation de métal, mais nécessitent une installation horizontale précise.
Les plaques grillagées sont utilisées dans les colonnes de purée grand diamètre(> 1400 mm).
Plaques de contact défaillantes.Dans ces plaques, la vapeur et le liquide passent par les mêmes trous, ils ont donc une section libre plus grande que celles en maille (12-20%). Ces structures ne nécessitent pas de dispositifs de trop-plein et disposent d'une grande zone de travail.
Treillis plaques défaillantes sont fabriqués à partir de tôles d'acier ou de cuivre de 3 à 5 mm d'épaisseur. Les fentes sont embouties ou fraisées avec une largeur de 2 à 6 mm et une longueur de 60 à 200 mm. Sur les plaques adjacentes, les fentes sont perpendiculaires entre elles. De telles plaques sont de conception simple, leur débit de liquide est supérieur à celui des plaques à mailles, mais elles ont une plage étroite de fonctionnement stable. Les plaques de rupture en treillis sont recommandées pour une utilisation dans les colonnes de purée.
Plaque d'échelle(Fig. 7.70) est constitué d'une tôle dans laquelle des écailles arquées sont estampées en forme de damier. L'angle d'inclinaison est de 15 à 20°. La modification de la section libre de la plaque (recommandée 8-15 %) est obtenue en modifiant le nombre d'éclats. La plaque comporte des segments d'entrée et de sortie encastrés. Un tuyau de trop-plein est fixé au segment de drainage. Le flux de vapeur qui se déplace dans la colonne change de sens de déplacement lors du passage à travers les écailles dont les fentes sont orientées vers le mouvement du liquide. Le flux de vapeur dirigé augmente la vitesse du liquide, qui monte vers le drain. En mode jet de fonctionnement, la vapeur turbulise intensément le flux de liquide, une partie importante du mélange vapeur-liquide s'élève au-dessus de la plaque et se déplace dans l'espace inter-plaque. Les plaques en forme d'écaille fonctionnent à des vitesses de vapeur élevées et à une faible élimination des éclaboussures et ont haute efficacité(efficacité 0,5-0,7) .
Ce type de plaques est recommandé pour une utilisation dans les colonnes de purée d'un diamètre supérieur à 1,4 m lors de la distillation de purée à partir de matières premières de céréales broyées et de pommes de terre. La colonne de brassage avec plaques en forme d'écaille se caractérise par une large plage de fonctionnement stable, une productivité 20 à 40 % supérieure à celle typique. colonnes de purée, contribue à améliorer la qualité de l’alcool.
Plateaux à valves. La plaque métallique plate de la plaque comporte des trous ronds ou carrés fermés par des valves. Les vannes à disque et rectangulaires sont fabriquées en conséquence (Fig. 7.71). Lorsque la vapeur se déplace de bas en haut dans la colonne, les vannes montent légèrement, la vapeur passe par la fente formée et entre en contact avec le liquide qui se trouve sur le plateau. À mesure que la quantité de vapeur augmente, la valve monte plus haut. La zone d'écoulement augmente, mais la vitesse de la vapeur ne change pas. La hauteur de levée des soupapes est de 6 à 8 mm et est limitée par un support limiteur. Les plateaux à valves sont également équipés de dispositifs de trop-plein et peuvent fonctionner dans des modes d'interaction de phase à flux transversal et à flux direct. Dans ce dernier cas, les vannes ont des butées de longueurs différentes.
Au stade actuel, les plateaux à vannes sont équipés de colonnes de purée et d'épuration. Les dispositifs à contact vortex sont utilisés dans les installations de rectification pour le traitement des matières premières secondaires de vinification et la distillation de mélanges d'huile.