Plaque défaillante bouillonnante. Colonnes à disques: concept, types, choix, production à faire soi-même
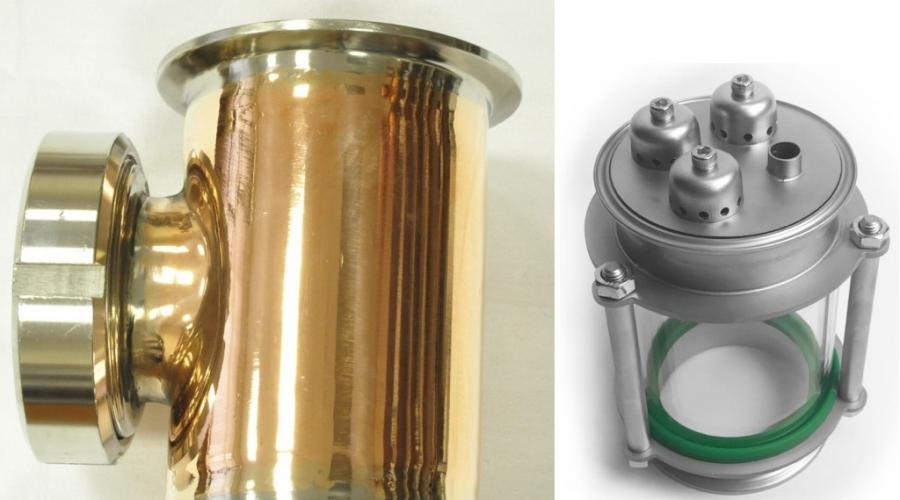
Lire aussi
(5 4 V 01 V 3/22 DESCRIPTION DE L'INVENTION TEPSTVO AUTHOR'S U 6ilial Voroshins SSRO.RELKA stvo S 2, 198 ) L'invention concerne la conception de chambres de tare défaillantes et peut être utilisée dans industrie chimique, en particulier dans le traitement des acides. Le but de l'invention est l'intensification du processus de transfert de masse en augmentant la surface de contact de phase et en réduisant la consommation de matière sans réduire la résistance mécanique. La plaque comprend une plaque 1 avec des trous 2 de tailles différentes, dont les parois latérales 3 sont réalisées sous la forme de pyramides tronquées tétraédriques avec des nervures arrondies et un alésage cylindrique dans la partie rétrécie, et les grandes bases des grands trous sont situées sur la face supérieure de la plaque. 4 ill. L'invention concerne les conceptions de plateaux défaillants d'appareils de transfert de masse et peut être utilisée dans l'industrie chimique, notamment dans le traitement des acides. Le but de l'invention est d'intensifier le processus de transfert de masse en augmentant le contact de phase surface et réduisant la consommation de matière sans réduire la résistance mécanique. 1 représente une plaque, vue de dessus ; En figue. 2 - le même, en bas en bas; En figue. 3 - coupe A-A sur la Fig. une; En figue. 4 - coupe B-B sur la Fig. 2. La plaque de rupture de bulles comprend une plaque 1 avec des trous 2 de différentes tailles, dont les parois latérales 3 sont réalisées sous la forme de pyramides tronquées à quatre côtés avec des nervures arrondies et un alésage cylindrique dans la partie rétrécie, ainsi qu'avec un chanfrein conique. Dans ce cas, les grandes bases des grands trous sont situées sur la face supérieure du plateau.Il est également conseillé de disposer des trous de différentes tailles en rangées alternées. Le gaz provenant de la plaque sous-jacente dans l'alésage cylindrique du trou pyramidal bouillonne à travers la couche de liquide formée, augmentant ainsi la surface de contact de phase. Les caractéristiques de conception de cette plaque permettent de l'utiliser plus pleinement surface de travail, La plaque peut être réalisée à partir d'un ferroalliage par coulée ou d'un fluoroplastique par pressage.Afin d'intensifier le processus de transfert de masse en augmentant la surface de contact de la fae et en réduisant la consommation de matière sans réduire la résistance mécanique, les parois latérales de la les trous sont réalisés sous la forme de pyramides tronquées tétraédriques avec des nervures arrondies et un alésage cylindrique dans la partie rétrécie, et les grandes bases des grands trous sont situées sur la face supérieure de la plaque .
Demande
3875425, 26.03.1985
BRANCHE DE RUBEZHANSK DE L'INSTITUT DE CONSTRUCTION DE MACHINES DE VOROSHILOVGRAD
ZINCHENKO Igor Maksimovitch
CIB / Balises
Code du lien
Plateau d'échec de bouillonnement
Brevets associés
L'entrée est équipée d'un couvercle technologique 11 avec une saillie 12, d'une hauteur non inférieure à l'épaisseur de paroi de l'entrée latérale, installé dans celle-ci avec un jeu minimal. le connecteur n'est pas démonté, Navire haute pression Fabriquer de la manière suivante Un corps 1 avec une ouverture latérale est fabriqué, un tuyau de dérivation est soudé, un couvercle de processus 11 est installé sur l'entrée latérale reçue.Le récipient est testé sous pression avec une pression dépassant la pression de service de 1,25 à 2 fois. Pour l'étanchéité...
La tige de la plus petite étape de travail est installée dans un ajustement libre, servant de guide pour la plus grande étape de travail L'outil proposé est représenté sur le dessin. L'étape 1 est installée avec la pièce de guidage dans le trou 3 de la pièce, puis l'étape 2 est mise sur la tige de l'étape 1 avec un trou borgne, et la pièce de guidage pénètre dans le trou 4 de la pièce.Sous l'action de la tige élément de force les deux étages se déplacent simultanément dans le sens de déplacement de la tige. En fin de course de travail de l'outil, l'étage 1 est séparé de l'étage 2 sous l'action de la gravité, ...
Les noyaux des transformateurs 12 et les bus 8 leur sont connectés, combinant les enroulements de 6 noyaux correspondant aux numéros 1. Les enroulements primaires 16 sont cousus dans le sens opposé aux noyaux des transformateurs 11 et dans le sens direct - les noyaux des transformateurs 12, et des bus 8 leur sont connectés, combinant des noyaux d'enroulement b correspondant aux numéros 2. Primaire. les noyaux des transformateurs 11 et 12 sont cousus dans le sens opposé avec les enroulements 16, et les pneus 8 leur sont connectés, en combinant les enroulements des noyaux b correspondant aux numéros 3. Les enroulements secondaires 17 sont les sorties des décodeurs 9 , et on leur connecte des amplificateurs de lecture 18. Le nombre de sorties des décodeurs 9 est de deux (généralement 1 impair, le dispositif fonctionne comme suit...
Comme prévu dans le précédent, j'ai testé l'insert poppet. En fait, un tel insert est l'une des variantes de la buse pour colonnes de purée.
Pourquoi pour les messieurs ? Qu'il est impossible d'avoir de l'alcool sur la colonne du plateau, dont cet insert fait partie ? En principe, bien sûr, vous pouvez aussi vous lancer dans l'alcool - c'est tout simplement très irrationnel. Rappelez-vous, dans l'un de ceux consacrés à la théorie de la rectification, j'ai écrit que pour obtenir de l'alcool, vous devez avoir au moins des plaques 50. Considérant que la hauteur de la plaque conditionnelle pour la buse SPN est d'environ 2 cm et la distance entre les les plateaux physiques sont approximativement égaux au diamètre avec une efficacité réelle d'environ 85 % (par rapport à un plateau théorique, de tels plateaux à tamis ne donnent pas un effet de séparation adéquat), alors la hauteur réellement comparable d'une telle colonne à plateaux sera de 2,5 à 3 fois supérieure à celle d'une colonne avec garnissage SPN, à chances égales. Il s'avère donc que la construction du RC sur plaques tamis est le lot de personnes obsédées par une passion pour les structures de plaques, mais sur le BK, où la tâche de séparation profonde n'est pas définie en principe (le but est le distillat) , l'utilisation de telles plaques est justifiée.
De plus, les assiettes présentent des avantages par rapport au SPN et aux débarbouillettes en Colombie-Britannique - les assiettes sont faciles à nettoyer et moins bouchées. L'essentiel est de choisir le bon diamètre et le bon nombre de trous et les dimensions de la plaque elle-même. Ici mon insertion entre en contradiction avec le Ces derniers temps dogme que les plaques d'un diamètre inférieur à 50 mm et rien à faire, mais que faire - j'ai un tuyau 38 avec un diamètre intérieur de 35 mm. A partir de là, nous procéderons.
Ainsi, un insert de 7 plaques de PTFE a été placé dans un tiroir vide d'une hauteur de 500 mm, la longueur totale de l'insert était de 270 mm. Dans chaque plaque, il y a 22 à 25 (et dans une seule il y en a 30) des trous d'un diamètre de 3 mm, percés au hasard pour un «tourbillon» de vapeur supplémentaire. Pourquoi exactement ? J'ai du mal à répondre - il m'a semblé que ce serait correct, même si je n'insiste pas sur cette opinion. D'ailleurs, les cymbales sont trop lâches et il était tout à fait possible de mettre au moins une cymbale de plus sur le même insert. L'ensemble du processus a été réalisé sur un plateau tournant avec un grand refroidisseur final, le CC a été dilué à environ 12%.
Les têtes ont d'abord été échantillonnées au rythme d'une goutte par seconde. Commence alors la sélection du corps. Un insert à plateaux permettait d'obtenir une température stable de la vapeur passant dans le condenseur à reflux. En faisant varier le taux de prélèvement (en pinçant le tube de prélèvement avec une pince d'Hoffmann), il a été possible d'influencer cette température. J'ai été assez satisfait des lectures du thermomètre au niveau de 79°C avec une sélection de 2,4 l/h. À la fin du processus, le débit a légèrement chuté à environ 2,1 l/h. Sur les lectures du thermomètre dans un cube de 96°C, j'ai arrêté la sélection d'un produit commercialisable et je suis passé aux résidus. De plus, la productivité a commencé à baisser plus sensiblement et à une température dans le cube d'environ 98 ° C, la sélection est devenue très petite. Les tentatives d'augmentation de la puissance et de la sélection n'ont pas abouti, car l'isoamyl a commencé à passer par le TCA. Ce point n'est pas tout à fait clair pour moi. Soit des gaz incondensables se sont formés, soit les performances du CT en mode reflux n'étaient pas suffisantes (ce qui est douteux aux puissances que j'ai données). Il reste une expérience à venir - vous devez soit piloter le CT en tant que déphlegmateur (peut-être que ses capacités sont insuffisantes, ce qui est étrange), soit répéter l'expérience avec l'insert sur le def déjà testé avec dimrot.
Sommaire . En sortie, un produit d'une résistance à 80° a été obtenu. Pas épais, mais pour les besoins de la construction de bourbon, il convient tout à fait. Il peut être considéré comme une variante d'un bec relativement simple pour les distillateurs à renfort. Il reste à comparer avec un petit échantillon de SPN et juste un côté de tiroir vraiment vide. Et, au fait, j'ai commis une erreur lors de l'expérience - je n'ai pas isolé le tsarga vide, qui est devenu un emballage. En général, le champ devant n'est pas labouré.
Fait intéressant, la forteresse n'a pas changé toute la bandoulière (même sur les têtes, il y avait le même 80 °) aux queues, mais elle a commencé à tomber très brusquement lors du déplacement vers les queues. Aussi, en général, c'est étrange pour les têtes. Je jouerai avec les cymbales, peut-être.
Colonnes à disques pour la distillation ont une petite capacité de renforcement et sont traditionnellement utilisés dans la production de whisky, cognac et autres boissons nobles. Pas un grand nombre de plaques vous permet d'économiser l'organoleptique des matières premières avec une stabilité et des performances élevées de l'appareil.
Matériel
Les colonnes en cuivre en forme de plat avec des fenêtres de visualisation, en raison de leur similitude, sont appelées flûtes, et celles fabriquées dans une vitrine en verre sont appelées cristal. Il est clair que ces noms ne sont qu'un stratagème marketing et n'ont rien à voir avec le design lui-même.
Le cuivre est un matériau coûteux, l'approche de son traitement est donc approfondie. Une flûte en laiton des principaux fabricants est une œuvre d'art et une source de fierté. Le coût du produit peut être absolument n'importe quel montant que l'acheteur est prêt à dépenser.
Un peu moins cher qu'une flûte dans un boîtier en acier inoxydable, et l'option la plus économique est dans un boîtier en verre.
Caractéristiques de conception et types de colonnes paraboliques
Les plus répandues sont les conceptions de colonnes modulaires basées sur des tés de dérivation ou des cylindres en verre borosilicaté. Naturellement, il s'agit d'un grand nombre de pièces de raccordement supplémentaires et d'un coût surestimé.
Une option plus simple consiste en des blocs prêts à l'emploi pour 5 à 10 assiettes. Ici le choix est plus large, et le prix est plus modéré. En règle générale, cette option est réalisée dans des vitrines.
Il y a absolument options budgétaires- juste des inserts pour les tiroirs existants.
Ils peuvent être recrutés à partir de composants dans n'importe quelle quantité requise.
La conception peut être différente, mais si de telles colonnes de plateaux sont utilisées avec des flacons métalliques, la visibilité du processus est perdue. Il est beaucoup plus difficile de comprendre dans quel mode la colonne fonctionne, ce qui est très important pour travailler avec des plaques.
Pour sceller chaque étage, de simples disques de silicone sont utilisés.
Naturellement, c'est moins fiable que joints dans les conceptions modulaires, mais en général, ils fonctionnent bien.
Comme alternative, il existe une conception modulaire simplifiée, où chaque étage est assemblé à partir de pièces simples et peu coûteuses, et toute la structure est assemblée avec des poteaux.
L'avantage des colonnes modulaires est principalement leur maintenabilité et leur ouverture aux modifications. Par exemple, il est facile de compléter la colonne au niveau requis avec une unité de fractionnement intermédiaire et un raccord pour thermomètre. Il ne vous reste plus qu'à changer la plaque.
Les colonnes de plateaux à tamis sont une option moins chère. Cela ne signifie pas que la qualité du produit avec son utilisation sera pire. Mais ils nécessitent un contrôle plus précis.
Les plateaux de trempage sont encore moins chers, mais leur plage de fonctionnement est très étroite, vous devez donc être prêt pour un contrôle précis de la chaleur avec des sources stabilisées en puissance. Fondamentalement, les plateaux défectueux sont utilisés au NSC.
Les matériaux les plus courants pour fabriquer des cymbales sont le cuivre, l'acier inoxydable et le PTFE. Toutes les combinaisons sont possibles. Le cuivre et l'acier inoxydable sont des matériaux familiers, le fluoroplastique est l'un des matériaux les plus inertes, comparable au platine. Mais sa mouillabilité est médiocre.
Si nous comparons une plaque en fluoroplastique avec une plaque en acier inoxydable, elle sera inondée beaucoup plus rapidement.
Le nombre de plateaux dans la colonne est généralement limité à 5 pour les distillats d'une force de 88-92 % et à 10 pour les distillats purifiés d'une force allant jusqu'à 94-95 %.
Les colonnes modulaires vous permettent de faire un ensemble le bon montant plaques de divers matériaux.
Différence entre la colonne remplie et la colonne de plateau
« J'ai une colonne remplie, ai-je besoin d'un plateau ? » – cette question se pose tôt ou tard à tout distillateur. Les deux colonnes mettent en œuvre la technologie de transfert de chaleur et de masse, mais il existe des différences significatives dans leur fonctionnement.
Nombre d'étapes de renforcement
La colonne remplie fonctionne en mode de séparation maximale à la capacité de pré-étranglement. En ajustant le taux de reflux, il est possible de changer le nombre de plateaux théoriques dans une large gamme : de zéro à l'infini (avec le condenseur à reflux complètement éteint et la colonne travaillant sur elle-même).
La colonne à plateaux est caractérisée par un nombre structurellement spécifié d'étages de séparation. Une plaque physique a une efficacité de 40 à 70 %. En d'autres termes, deux plateaux physiques donnent un étage de séparation (renforcement, plateau théorique). Selon le mode de fonctionnement, l'efficacité ne change pas au point d'affecter de manière significative le nombre d'étapes.
capacité de rétention
La colonne à garnissage avec sa faible capacité de rétention permet de bien purifier le distillat de la fraction de tête et de retenir en quelque sorte la fraction de queue.
La colonne de plateau a une capacité de rétention d'un ordre de grandeur supérieur. Cela l'empêche de faire un nettoyage aussi dur des "têtes", mais lui permet de contenir parfaitement les queues. C'est-à-dire, pour égaliser le distillat selon composition chimique. De plus, plus vous devez nettoyer le distillat des impuretés, plus vous devez mettre de plaques. Tâche simple, résoluble en pratique. Une fois que vous avez trouvé le nombre optimal d'assiettes pour vous-même et que vous n'y pensez plus.
Sensibilité aux actions de contrôle
La colonne à garnissage est très sensible à la différence de pression d'eau dans le condenseur à reflux ou aux variations de puissance de chauffage. Une légère modification de celles-ci entraîne parfois une modification du nombre d'étapes de renforcement, voire des dizaines de fois.
L'efficacité des plaques peut changer d'un maximum de 1,5 fois, et même alors avec un changement très important et ciblé de ces paramètres. On peut considérer qu'une colonne à plateaux accordée, en termes de pouvoir séparateur, ne répondra pratiquement pas aux petites chutes habituelles de pression ou de tension de l'eau.
Performance
Les performances d'une colonne à garnissage dépendent principalement de son diamètre. Diamètre optimal pour les buses modernes est de 40-50 mm, avec une augmentation supplémentaire du diamètre, la stabilité des processus diminue. Les effets près du mur et la formation de canaux commencent à se manifester. Les colonnes à disque ne souffrent pas de telles faiblesses. Leur diamètre et leur productivité peuvent être augmentés à n'importe quel valeur requise. Si seulement il y avait assez de puissance de chauffage.
Caractéristiques technologiques de l'obtention de distillats aromatiques
Lors de l'utilisation de colonnes garnies pour limiter le degré de renforcement, nous sommes obligés d'utiliser des côtés plus courts et un garnissage plus grand. Sinon, les esters qui donnent la saveur principale au distillat créeront des azéotropes avec les impuretés de la fraction de tête, puis s'envoleront rapidement hors du cube. Nous sélectionnons les «têtes» sous peu, le «corps» - à une vitesse accrue. Quant aux "queues", le petit nombre de buses et le court tsarga ne contiennent pas complètement le fuselage. Il est nécessaire de passer plus tôt à la sélection des fractions de queue ou de travailler avec de petits volumes cubiques.
La colonne à plateaux a une capacité de rétention relativement importante, il n'y a donc pas de questions sur la rétention de l'huile de fusel. Pour la sélection des "têtes" et du "corps", 5 à 10 plaques physiques donnent 3 à 5 étapes de renforcement. Cela permet une distillation selon les règles de la distillation conventionnelle. Calmement, sans risquer de priver le distillat d'arôme, sélectionnez les "têtes", et lors de la collecte du "corps", ne pensez pas à l'approche prématurée des "queues". La buée sur les plaques inférieures en fin de sélection vous indiquera clairement la nécessité de changer de contenant. Le degré de nettoyage peut être réglé en modifiant le nombre de plaques.
Cinq ou dix assiettes ne suffisent pas pour se rapprocher de l'alcool en termes de purification, mais il est réaliste d'entrer dans les exigences GOST pour le distillat.
L'utilisation de colonnes à plateaux dans la distillation des matières premières fruitières ou céréalières, notamment pour la poursuite du vieillissement en barriques, simplifie grandement la vie du distillateur.
Fondamentaux du dimensionnement des plateaux de colonne
Considérez les conceptions des assiettes les plus courantes à des fins domestiques.
Plaque ratée
À la base, il s'agit simplement d'une plaque avec des trous, qui peuvent être ronds, rectangulaires, etc.
Le flegme s'écoule dans des trous relativement grands vers la vapeur, ce qui détermine le principal inconvénient des plaques défaillantes - la nécessité d'un contrôle précis du mode de réglage.
Une légère diminution de la puissance de chauffage conduit au fait que tout le flegme tombe dans le cube, et une augmentation de la puissance verrouille le flegme sur la plaque et conduit à l'étouffement. Ces plateaux peuvent fonctionner de manière satisfaisante sur une plage de charge relativement étroite, où ils sont tout à fait compétitifs.
La simplicité de conception et les hautes performances des plateaux de trempage, ainsi que le chauffage habituel de la distillation domestique par des éléments chauffants avec une source d'alimentation stabilisée en tension, ont conduit à leur utilisation généralisée pour les colonnes de bière en continu (NBK), qui, en combinaison avec un borosilicate ou corps en verre de quartz, rend le réglage de la colonne simple et visuel.
Pour calculer le nombre et le diamètre des trous, les conditions de bullage sont prises en compte. Il a été déterminé expérimentalement que la surface totale des trous doit être égale à 15-30% de la surface de la plaque (section de tuyau). En général, pour BC action périodique le diamètre du trou de base d'environ 9-10% du diamètre de la colonne vous permet d'entrer dans la zone de travail.
Le diamètre des trous des plateaux de défaillance pour le NSC est sélectionné en fonction des propriétés de la matière première. Si, lors de la distillation de purée de sucre et de vin, des trous d'un diamètre de 5 à 6 mm suffisent, alors lors de la distillation de confitures de farine, un diamètre de trou de 7 à 8 mm est préférable. Cependant, les plateaux pour NSC ont leurs propres caractéristiques de calcul, puisque la densité de vapeur varie considérablement le long de la hauteur de la colonne, les dimensions doivent être calculées pour chaque plateau séparément, sinon leurs performances seront loin d'être optimales.
Plaque tamis avec trop-plein
Si les diamètres des trous dans la plaque défaillante sont inférieurs à 3 mm, alors même à une puissance relativement faible, le flegme sera bloqué sur la plaque même sans appareils supplémentaires le débordement sera inondé. Mais un plateau à tamis équipé de tels dispositifs élargit considérablement sa plage de fonctionnement.

1 - corps; 2 - plaque de tamis; 3 - tube de trop-plein; 4- verre
Au moyen de dispositifs de débordement sur ces plaques, le niveau maximum de reflux est réglé, ce qui vous permet d'éviter les inondations précoces et de travailler en toute confiance avec une charge de vapeur élevée. Cela n'empêche pas le flegme de se fondre complètement dans un cube lorsque le chauffage est éteint, et la colonne devra être redémarrée à zéro, comme d'habitude pour toutes les plaques défaillantes.
Dans un calcul simplifié de telles plaques, les relations suivantes sont prises en compte:
- la surface totale des trous est de 7 à 15% de la section transversale du tuyau;
- le rapport entre les diamètres des trous et le pas entre eux est d'environ 3,5 ;
- le diamètre des tuyaux de drainage est d'environ 20% du diamètre de la plaque.
Des joints hydrauliques doivent être installés dans les trous de vidange pour éviter la pénétration de vapeur. Les plaques de tamis doivent être installées strictement horizontalement pour permettre à la vapeur de passer à travers tous les trous et pour empêcher le reflux de les traverser.
assiettes coiffées
Si, au lieu de trous dans les plaques, nous fabriquons des tuyaux de vapeur plus hauts que les tuyaux de vidange et les recouvrons de bouchons à fentes, nous obtenons une toute nouvelle qualité. Ces plaques ne draineront pas les mucosités lorsque le chauffage est éteint. Le flegme divisé en fractions restera sur les assiettes. Par conséquent, pour continuer à travailler, il suffira d'allumer le chauffage.
De plus, de telles plaques ont une couche de reflux structurellement fixe en surface, elles fonctionnent dans une gamme plus large de puissances de chauffage (charges de vapeur) et de variations du taux de reflux (de l'absence complète au retour complet du reflux).
Il est également important que les plaques coiffées aient une efficacité relativement élevée - environ 0,6-0,7. Tout cela, ainsi que l'esthétique du processus, détermine la popularité des cymbales à capuchon.
Lors du calcul du construit, les proportions suivantes sont prises en compte :
- la surface des tubes à vapeur est d'environ 10% de la section de la colonne;
- la surface des fentes est de 70 à 80% de la surface des conduites de vapeur;
- zone de vidange 1/3 de la surface totale des conduites de vapeur (diamètre environ 18-20% du diamètre de la section de conduite);
- conception des plaques inférieures avec un haut niveau de reflux et grande section fentes pour qu'elles fonctionnent comme des dispositifs de retenue;
- les plaques supérieures sont fabriquées avec un niveau de reflux inférieur et une section coupée de sorte qu'elles fonctionnent comme une séparation.
Sur la base des graphiques donnés par Stabnikov, on voit qu'avec une couche de flegme de 12 mm (courbe 2) efficacité maximale atteint à une vitesse de vapeur de l'ordre de 0,3-0,4 m/s.
Pour une colonne de 2" avec un diamètre intérieur de 48 mm, la puissance nette de chauffage requise est de :
N = V * S / 750 ;
- V est la vitesse de la vapeur en m/s ;
- N est la puissance en kW, S est la section de la colonne en mm².
N \u003d 0,3 * 1808 / 750 \u003d 0,72 kW.
Vous pourriez penser que 0,72 kW détermine une petite performance. Peut-être, compte tenu de la puissance disponible, vaut-il la peine d'augmenter le diamètre de la colonne? C'est probablement vrai. Les diamètres courants des verres de quartz pour les dioptries sont de 80, 108 mm. Prenons 80 mm avec une épaisseur de paroi de 4 mm, un diamètre intérieur de 72 mm, une surface de section de 4069 mm². Recalculons la puissance - nous obtenons 1,62 kW. Eh bien, mieux pour la maison cuisinière à gaz correspond.
Après avoir choisi le diamètre de la colonne et la puissance calculée, nous déterminons la hauteur du tuyau de trop-plein et la distance entre les plaques. Pour ce faire, nous utilisons l'équation suivante :
V = (0,305 * H / (60 + 0,05 * H)) - 0,012 * Z (m/s);
- H est la distance entre les plaques ;
- Z est la hauteur du tube de débordement (c'est-à-dire l'épaisseur de la couche de reflux sur la plaque).
La vitesse de la vapeur est de 0,3 m/s, la hauteur de la plaque ne doit pas être inférieure à son diamètre. Pour les plaques inférieures, la hauteur de la couche de reflux est plus grande. Plus petit pour le haut.
Calculons les combinaisons les plus proches de hauteurs de plaque et de trop-plein, mm : 90-11 ; 100-14 ; 110-18 ; 120-21. Considérant que le verre standard a une hauteur de 100 mm, pour une conception modulaire, nous choisissons une paire de 100-14 mm. Naturellement, ce n'est que notre choix. Vous pouvez en prendre plus, alors la protection contre les embruns sera meilleure avec une augmentation de puissance.
Si la conception n'est pas modulaire, il y a plus de place pour la créativité. Vous pouvez fabriquer les plaques inférieures avec une plus grande capacité de rétention de 100-14 et la plaque supérieure avec une plus grande séparation - 90-11.
Nous choisissons des casquettes parmi les tailles standard et disponibles. Par exemple, des souches pour tuyau de cuivre 28 mm, tuyaux vapeur - tuyau 22 mm. La hauteur du tuyau de vapeur doit être supérieure à celle du tuyau de trop-plein, disons 17 mm. Les espaces pour le passage de la vapeur entre le capuchon et le tuyau de vapeur doivent avoir une section transversale plus grande que celle du tuyau de vapeur.
Des fentes pour le passage de la vapeur dans chaque bouchon sont nécessaires avec une section transversale d'environ 0,75 de la surface du tuyau de vapeur. La forme des fentes ne joue pas un rôle particulier, mais il est préférable de les rendre aussi étroites que possible afin que la vapeur se brise en bulles plus petites. Cela augmente la zone de contact entre les phases. L'augmentation du nombre de plafonds profite également au processus.
Modes de fonctionnement de la colonne à plateaux
Toutes les colonnes à bulles peuvent fonctionner dans plusieurs modes. À faible vitesse de vapeur ( batterie faible chauffage) le mode bulle se produit. La vapeur sous forme de bulles se déplace à travers la couche de flegme. La surface de contact de phase est minimale. Avec une augmentation de la vitesse de la vapeur (puissance de chauffage), les bulles individuelles à la sortie des fentes fusionnent en un jet continu, et après de courtes distances, en raison de la résistance de la couche bouillonnante, le jet se décompose en de nombreuses petites bulles. Une couche de mousse abondante se forme. La zone de contact est maximale. C'est le mode mousse.
Si nous continuons à augmenter le débit d'alimentation en vapeur, alors la longueur des jets de vapeur augmente, et ils atteignent la surface de la couche bouillonnante sans s'effondrer, formant une grande quantité d'éclaboussures. La surface de contact diminue, l'efficacité de la plaque diminue. Il s'agit d'un mode jet ou injection.
La transition d'un régime à un autre n'a pas de frontières claires. Par conséquent, même lors du calcul des colonnes industrielles, seules les vitesses de vapeur sont déterminées en fonction des limites inférieure et supérieure de travail. La vitesse de fonctionnement (puissance de chauffage) est simplement choisie dans cette plage. Pour les colonnes domestiques, un calcul simplifié est effectué pour une certaine puissance de chauffage moyenne, de sorte qu'il existe une possibilité d'ajustements pendant le fonctionnement.
Ceux qui souhaitent faire des calculs plus précis peuvent recommander le livre de A.G. Kasatkin "Procédés et appareils de base de l'industrie chimique".
PS Ce qui précède n'est pas une méthodologie complète pour calculer dimensions optimales chaque planche par rapport à un cas particulier et ne prétend pas être exacte ou scientifique. Mais encore, cela suffit pour faire une colonne de travail de vos propres mains ou pour comprendre les avantages et les inconvénients des colonnes proposées sur le marché.
Colonne à plateaux modulaires. Pratique sur l'automatisation BKU - 011M.
Couvercles coniques en cuivre. Une colonne de saveur cuivrée. Théorie et pratique.
Machine à alcool. Capuchon colonne HD/3-500 KKS-N. Partie 1. Nouveau en 2016.
Machine à alcool. Capuchon colonne HD/3-500 KKS-N. Partie 2. Nouveau en 2016.
Machine à alcool. Colonne à plateaux.
Qu'est-ce qu'une colonne à plateaux et pourquoi en a-t-on besoin... fixation prismatique) en fait des plaques. Avec l'aide d'une colonne à plateaux, nous n'obtiendrons pas d'alcool pur. Cependant, nous pouvons y obtenir la soi-disant sous-rectification avec une force de 90-95 vol. Autrement dit, ce n'est pas non plus de l'alcool, mais ce n'est plus un distillat. Un distillat très raffiné qui conserve encore les notes de la matière première d'origine. Cette technologie est utilisée depuis plus de cent ans et est activement utilisée par les distillateurs du monde entier. Notre pays dans ce sens dernières années pas une exception. Ces colonnes gagnent une immense popularité.
Analysons les principales différences entre les colonnes pour une compréhension correcte du choix d'une colonne particulière.
- Comme tous nos équipements, les colonnes à plateaux se distinguent par séries : HD/4 ou HD/3. Tout est simple ici. Si vous disposez déjà d'un équipement HD, le choix se fait en fonction de la série d'équipements correspondante. Si vous n'achetez que du matériel, vous devez comprendre la différence entre les séries HD / 4 et HD / 3. La série HD/4 est plus budgétaire, elle a un rapport qualité-prix optimal. La série HD/3 a un prix plus élevé mais aussi des performances plus élevées.
- Matériaux utilisés dans la fabrication des colonnes. Il s'agit soit d'acier inoxydable de qualité alimentaire, soit de verre de quartz. Dans ce dernier cas, vous avez la possibilité d'observer visuellement le processus, ce qui est un vrai plaisir. N'oubliez pas qu'en premier lieu, nous faisons ce passe-temps pour le plaisir.
- Les colonnes diffèrent également par leur hauteur et par le nombre de plaques qu'elles contiennent. La hauteur de la colonne est disponible en deux tailles : 375 et 750 mm, respectivement. Sur une colonne raccourcie, vous pouvez obtenir une "sous-rectification" avec une force de 91-92C, sur une colonne de 750 mm, vous pouvez obtenir une "sous-rectification" d'environ 95C. Étant donné que les colonnes à disques sont pliables, le nombre de plateaux dans la colonne peut être ajusté indépendamment par le distillateur.
- Type d'exécution de la plaque. Les plaques sont constituées de deux types: échec et capuchon. Il est difficile de dire sans équivoque laquelle des assiettes est la meilleure et sur quelles assiettes la boisson sera plus savoureuse. Le fait est que les plaques de panne sont bonnes si nous utilisons une puissance de chauffage stable, sans sauts dans le réseau. Si le réseau est instable, alors vous pouvez utiliser un stabilisateur de puissance de chauffage par exemple. Les plaques de type bouchon sont plus simples et n'importe quel chauffage peut être utilisé. Cependant, du fait de la complexité de fabrication de telles colonnes, elles sont plus onéreuses. Mais aussi plus esthétique au passage.
- Matériaux de fabrication d'assiettes. Les plaques défaillantes sont en PTFE inerte. Les cymbales Cap sont fabriquées en acier inoxydable ou en cuivre. L'inox est connu pour être inerte. Et par conséquent, la boisson obtenue à sa surface n'a pas de goûts supplémentaires caractéristiques, à l'exception de la matière première d'origine. Le cuivre, d'autre part, est censé absorber le soufre nocif libéré pendant le processus de distillation, débarrassant ainsi la boisson de odeurs désagréables et le goût. Les partisans du cuivre et de l'inox ont de nombreux adeptes. Chacun a ses propres arguments en faveur du matériau utilisé pour les assiettes.
Vous pouvez en savoir plus sur l'utilisation des colonnes de disque ici.