A quoi sert une colonne à distiller ? Comment est agencée la colonne de distillation et sur quel principe fonctionne-t-elle ? Classement des meilleurs avec descriptions et prix Principe de fonctionnement de l'appareil à colonne de distillation
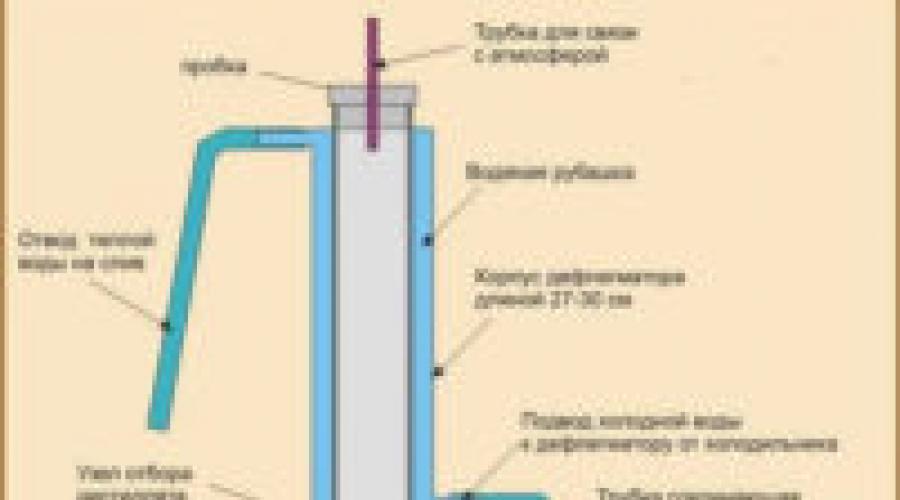
Lire aussi
Nous traitons tous en tremblant, avec beaucoup de fierté et d'amour ce qui est cultivé et produit par nos propres mains, qualifiant ces produits de respectueux de l'environnement. Il ne s'est pas éloigné de l'attrait pour le naturel et la pureté.
Le produit, bien sûr, est de haute qualité et en quantités raisonnables est utile. Cependant, la question de à propos de débarrasser le produit des impuretés nocives.
Savez-vous comment nettoyer le clair de lune ? Après tout, les huiles de fusel sont certainement contenues même dans un liquide «propre comme une larme», s'écoulant finement d'un tube ordinaire, dans lequel une colonne de distillation n'est pas fournie, dans un pot substitué.
La vodka prête à l'emploi, que nous achetons tous périodiquement dans les magasins, est exempte de substances dangereuses, tout d'abord - à partir d'huiles de fusel. Et le secret est assez simple.
Dans les usines produisant boissons alcoolisées, ils n'utilisent pas de distillation (comme dans moonshine), mais rectification, une méthode fondamentalement différente.
Par conséquent, le "kazenka" est exempt d'impuretés et a généralement un effet plus doux sur le corps. Bien sûr, nous parlons de vodka de haute qualité.
Considérez ce qu'est une colonne de distillation et pourquoi un quai Moonshine en a besoin. C'est d'abord une sorte superstructure au-dessus du réservoir de distillation, servant de filtre dans lequel ils se déposent. Schéma détaillé colonne de distillation est illustré ci-dessous.
Le principe de base de la colonne - nettoyage mécanique moonshine de diverses impuretés encore au stade de la production.
Lors de la distillation conventionnelle (distillation), tout l'alcool, ainsi que d'autres vapeurs, sont libérés de la purée pendant le chauffage, mélangés les uns aux autres afin de passer ensemble par le tube de sortie vers le réfrigérateur, puis transformer en un liquide dégoulinant dans un réservoir substitué.
La séparation de ces vapeurs en alcool et fusel dans des conditions ordinaires conditions de vie difficile.
Le résultat ne peut être atteint que partiellement par le contrôle régime de température, et séparation des "têtes" avec des "piles".
Et voici comment fonctionne une colonne de distillation: lors de la rectification, les vapeurs mixtes, montant, sont converties en un liquide qui coule dans des «plaques» spéciales, qui sont équipées d'une colonne de nettoyage de distillation d'un appareil de distillation.
Dans les mucosités (liquides dans les assiettes), il reste des composés volatils (bouillant à assez basses températures), et plus haut, dans le système de refroidissement, ceux à peine volatils montent, où ils se transforment en un liquide contenant de l'alcool - un clair de lune purifié.
Les huiles de fusel et autres composés nocifs restent dans le flegme, et l'alcool se condense librement et s'écoule dans les plats substitués.
Pour les appareils faits maison, le principe de fonctionnement de la colonne de distillation reste le même, mais la fonction de retardement des mucosités n'est pas assurée par des plaques, mais par de multiples petits ressorts de débarbouillettes de cuisine en acier inoxydable.
Comment faire à la maison ?
Il existe déjà des alambics Moonshine prêts à l'emploi avec une colonne de distillation qui peuvent être achetés via Internet. En règle générale, ils sont pratiques et de qualité suffisante, mais les prix des redresseurs en arrêtent beaucoup, même dans le but de produire un clair de lune d'une qualité exceptionnelle.
Alors, abandonnez et utilisez les méthodes "grand-père" pour nettoyer le produit : coton, charbon actif, filtres à café ? Bien sûr que non, les artisans folkloriques ont trouvé un moyen de sortir de cette situation.
Nous vous apprendrons à fabriquer vous-même une colonne de distillation, littéralement à partir de matériaux improvisés. Mais avant de procéder à la mise en œuvre de l'idée, pesez correctement le pour et le contre de cet appareil.
avantages rectification:
- Pratiquement nettoyage parfait moonshine des impuretés nocives.
- À l'aide de moonshine obtenu à partir d'un appareil équipé d'une colonne de purification de moonshine à faire soi-même, vous pouvez préparer diverses boissons de très haute qualité à forte teneur en alcool.
- La qualité du produit résultant sera conforme aux GOST pour la production industrielle.
- Ce n'est qu'à l'aide d'une colonne de distillation que vous pouvez obtenir produit final vraiment propre et de haute qualité. Avec une distillation ordinaire, même un tel résultat ne peut être atteint.
Les moins:
- Selon de nombreux vénérables moonshiners, après avoir traversé la colonne de distillation, le produit final est «émasculé», perdant non seulement l'huile de fusel, mais aussi la plupart des composants aromatiques (par exemple, le goût de confiture que vous y avez ajouté).
- Le processus de fabrication du produit final est plus long dans le temps, ce qui signifie qu'il nécessite également des coûts énergétiques importants (électricité, gaz, bois de chauffage).
- Vous avez besoin de la colonne elle-même, que vous devez acheter ou fabriquer vous-même.
Pour fabriquer une colonne de distillation de vos propres mains, il est nécessaire, après avoir compris le principe de fonctionnement, de faire un tel dispositif.
Rappelez-vous qu'une colonne de distillation pour un distillateur Moonshine nécessite des matières premières de qualité afin qu'il puisse remplir son objectif principal.
Tu auras besoin de:
- tuyau inoxydable d'un diamètre de 30 à 50 mm et d'une hauteur de 1,3 à 1,4 mètre. Il est souhaitable de supporter juste un tel diamètre afin d'atteindre le maximum bon fonctionnementéquipement. L'acier inoxydable est un matériau chimiquement inerte, il n'est pas sujet à la corrosion, n'émet pas d'odeurs étrangères et d'impuretés chimiques;
- beaucoup pensent qu'il est encore mieux de faire une colonne de distillation cuivre, mais cela est déjà à votre discrétion et selon vos possibilités ;
- éléments de liaison, ainsi que des tubes en silicone et/ou en cuivre ;
- isolation(un morceau de caoutchouc mousse fera l'affaire);
- serrer d'un compte-gouttes médical (pas nécessaire, mais ajoute de la commodité);
- 2 pinces à mailles métalliques- en fonction du diamètre intérieur du tuyau et des rondelles de butée pour ceux-ci ;
- éléments de contact, qui purifiera les vapeurs d'alcool des impuretés. Les petites perles de verre sont tout simplement excellentes à cet égard, mais la question est de savoir où les mettre le bon montant(ils doivent remplir aux 2/3 ou au moins à moitié l'intérieur de la colonne). Par conséquent, un remplaçant a été trouvé - tampons à récurer en métal d'un montant de 30 à 40 pièces.
Le choix des éponges à récurer à ressort métallique - Étape importante fabrication d'un redresseur. Tu peux aller faire les magazins uniquement avec aimant. L'acier inoxydable de qualité alimentaire (approuvé pour une utilisation dans l'industrie alimentaire) NE S'AIMAGNE PAS !
Sinon, vous pouvez acheter un gant de toilette qui rouillera à l'intérieur de la colonne, ou un en acier inoxydable technique qui libère des composés nocifs.
C'est en fait tout équipement optionel, étant donné que vous possédez déjà un distillateur Moonshine, comprenant un cube et un réfrigérateur.
Processus de fabrication
Quelle sera votre colonne de distillation à faire soi-même - vous décidez. Le principe de montage prévoit également plusieurs solutions possibles :
- Coupez le tuyau sélectionné en deux parties (supérieure - 0,5 - 1/3 de la hauteur totale).
- Les bords, ayant chanfreiné, s'amarrent. C'est possible - en utilisant un adaptateur ou une connexion filetée.
- Au bas du tuyau, il est nécessaire d'installer un treillis métallique pour que les particules de charge ne tombent pas dans le cube. Avec cette pièce, une colonne de distillation artisanale sera installée sur un cube de distillation.
- Coupez vos éponges en acier inoxydable existantes en petits morceaux d'environ un demi-centimètre. Remplir partie inférieure(rappelez-vous, il doit représenter au moins 0,5 de la hauteur totale du redresseur, mais pas plus de 2/3) avec des morceaux d'éponge métallique. Après cela, fermez le tuyau avec un filet et fixez-le avec une rondelle de butée.
- Fixez la partie inférieure du tuyau directement au réservoir, isolez la connexion.
- Le dispositif général de la colonne de distillation prévoit la présence d'une chemise d'eau, par conséquent, un carter d'eau avec deux buses d'entrée et de sortie pour le refroidissement est soudé hermétiquement à la partie supérieure du tuyau.
- Par le haut, le tuyau doit être fermé avec un couvercle ou soudé en faisant un trou pour le tube atmosphérique.
- Au-dessus de la jonction avec le tuyau inférieur de 1,5 à 2 cm, faites un trou pour le tuyau à travers lequel le distillat (moonshine) est évacué. En dessous, fixez une plaque sur laquelle le condensat s'accumulera - le flegme.
- Connectez les sections de tuyau les unes aux autres. Voici une colonne conçue pour nettoyer le clair de lune de vos propres mains et est prête.
Important! Le raccord de tuyau doit être étanche, mais pliable. Si vous le mettez sur un scellant, la possibilité de lavage disparaîtra remplissage interne et si nécessaire, remplacez-le.
Il est important que les morceaux de ressorts ne soient pas entrelacés les uns avec les autres, mais compacté de manière compacte. Ne poussez pas le remplisseur de force, secouez plutôt et tapotez le tuyau, en remplissant tout le segment.
La dernière étape est la connexion au réfrigérateur déjà dans l'alambic Moonshine. Il est pratique de le faire avec un tube en silicone, avec une pince compte-gouttes installée dedans. Ainsi, vous pouvez régler la vitesse du liquide à tout moment.
Vidéos utiles sur l'appareil et le bricolage
Le principe de fonctionnement de la colonne de distillation :
Nouvelle colonne de distillation "Prima", principe raccord rapide, voir:
Travaux pratiques sur la colonne depuis le moment du versement de l'alcool brut jusqu'à la séparation des résidus :
Après avoir examiné le dessin de la colonne de distillation, vous comprendrez comment l'assembler correctement. Et après l'avoir vérifié en action, vous comprendrez que vous produisez maintenant un clair de lune fort et parfaitement purifié. Partagez des informations avec vos amis réseaux sociaux!
§ 13.2 Colonnes de distillation : leur conception et leur fonctionnement
Comme mentionné ci-dessus, la rectification est effectuée dans un appareil spécial - colonnes de distillation ah, qui sont les principaux éléments des usines de distillation.
processus de rectification peut être effectuée périodiquement et en continu, quels que soient le type et la conception des colonnes de distillation. Considérez le processus de distillation continue, qui est utilisé pour séparer les mélanges liquides dans l'industrie.
Colonne de distillation- vertical appareil cylindrique avec soudure (ou corps préfabriqué), dans lequel des dispositifs d'échange de masse et de chaleur (plaques horizontales 2 ou buse). Au bas de la colonne (Fig. 13.3) il y a un cube 3, dans lequel le liquide du fond bout. Le chauffage dans le cube est effectué grâce à la vapeur sourde située dans le serpentin ou dans la chaudière à calandre. Une partie intégrante de la colonne de distillation est un déphlegmateur 7, destiné à condenser la vapeur sortant de la colonne.
La colonne à plaques de distillation fonctionne comme suit. Le cube est constamment chauffé et le liquide du fond bout. La vapeur formée dans le cube monte dans la colonne. Le mélange initial à séparer est préchauffé à ébullition. Il alimente la plaque nutritive 5, qui divise la colonne en deux parties : inférieure (exhaustive) 4 et supérieur (renforcement) 6. Le mélange initial de la plaque nutritive s'écoule vers les plaques sous-jacentes, interagissant sur son chemin avec la vapeur se déplaçant de bas en haut. Du fait de cette interaction, la vapeur s'enrichit en composant volatil, et le liquide qui s'écoule, étant appauvri en ce composant, s'enrichit en composant peu volatil. Dans la partie inférieure de la colonne, le processus d'extraction (épuisement) du composant volatil du mélange initial et sa transition vers la vapeur a lieu. Une partie du produit fini (rectifié) est acheminée vers le haut de la colonne pour l'irrigation.
Le liquide entrant en haut de la colonne pour l'irrigation et s'écoulant dans la colonne est appelé flegme. La vapeur, en interaction avec le reflux sur tous les plateaux de la partie supérieure de la colonne, est enrichie (renforcée) d'un composant volatil. La vapeur sortant de la colonne est envoyée au déphlegmateur 7, dans lequel elle est condensée. Le distillat obtenu est divisé en deux flux : l'un sous la forme d'un produit est envoyé pour un refroidissement supplémentaire et vers l'entrepôt de produits finis, l'autre est renvoyé vers la colonne en tant que reflux.
L'élément le plus important d'une colonne de distillation à plateaux est le plateau, car c'est sur lui que la vapeur interagit avec le liquide. Sur la fig. 13.4 montre un schéma de l'appareil et du fonctionnement plaque de chapeau. Elle a un cul 1, hermétiquement relié au corps de colonne 4, buses à vapeur 2 et tuyaux de vidange 5. Les buses à vapeur sont conçues pour laisser passer les vapeurs s'élevant de la plaque inférieure. À travers les tuyaux de drainage, le liquide s'écoule de la plaque sus-jacente à celle sous-jacente. Un capuchon est monté sur chaque buse vapeur 3, au moyen duquel les vapeurs sont dirigées dans le liquide, barbotées à travers celui-ci, refroidies et partiellement condensées. Le fond de chaque plateau est chauffé par les vapeurs du plateau sous-jacent. De plus, la condensation partielle de la vapeur dégage de la chaleur. En raison de cette chaleur, le liquide sur chaque plaque bout, formant ses propres vapeurs, qui se mélangent aux vapeurs de la plaque sous-jacente. Le niveau de liquide sur la plaque est maintenu au moyen de tuyaux de vidange.
Riz. 13.3. Schéma d'une colonne à distiller : / - corps ; 2 - assiettes ; 3 - cube; 4, 6 - parties exhaustives et renforçantes de la colonne ; 5 - assiette nutritive; 7 - déphlegmateur
Les processus se produisant sur la plaque peuvent être décrits comme suit (voir Fig. 13.4). Laissez les vapeurs de la composition L du plateau inférieur entrer dans le plateau, et le liquide de la composition À. En raison de l'interaction de la vapeur MAIS avec du liquide À(la vapeur, bouillonnant à travers le liquide, l'évapore partiellement et se condense partiellement) une nouvelle vapeur de la composition se forme DE et nouvelle composition fluide ré, étant en équilibre. A la suite du travail de la plaque, de la vapeur neuve DE plus riche en matières volatiles par rapport à la vapeur provenant de la plaque inférieure MAIS, c'est-à-dire sur une plaque de vapeur DE enrichi en matières volatiles. Nouveau liquide ré, au contraire, il s'est appauvri en matières volatiles par rapport au liquide issu du plateau supérieur À, c'est-à-dire que sur une assiette, le liquide est appauvri en composant volatil et enrichi en composant non volatil. Bref, le travail de la plaque se réduit à l'enrichissement de la vapeur et à l'appauvrissement du liquide en composant hautement volatil.
Riz. 13.4. Schéma de l'appareil et fonctionnement de la plaque chapeau : / - le fond de la plaque ; 2 - tuyau de vapeur;
3 - casquette; 4 - corps de colonne ; 5 - tuyau de vidange
Riz. 13.5. L'image du travail d'une plaque de distillation sur le schéma à-x : 1- courbe d'équilibre ;
2 - ligne de concentrations de travail
Une plaque sur laquelle un état d'équilibre est atteint entre les vapeurs qui en sortent et le liquide qui en descend est appelée théorique. Dans des conditions réelles, en raison de l'interaction à court terme de la vapeur avec le liquide sur les plaques, un état d'équilibre n'est pas atteint. La séparation du mélange sur une plaque réelle est moins intense que sur une plaque théorique. Donc, pour réaliser : le fonctionnement d'une plaque théorique nécessite plus d'une plaque réelle.
Sur la fig. 13.5 montre le fonctionnement d'un plateau de distillation à l'aide d'un schéma à-X. La plaque théorique correspond à un triangle rectangle hachuré, dont les jambes sont l'amplitude de l'augmentation de la concentration du composant volatil dans la vapeur, égale à moustache-y un , et l'amplitude de la diminution de la concentration du composant volatil dans le liquide, égale à X B - X ré . Les segments correspondant aux changements de concentration indiqués convergent vers la courbe d'équilibre. Cela suppose que les phases sortant de la plaque sont en équilibre. Cependant, en réalité, l'état d'équilibre n'est pas atteint, et les segments de l'évolution des concentrations n'atteignent pas la courbe d'équilibre. C'est-à-dire que la plaque de travail (réelle) correspondra à un triangle plus petit que celui illustré
En figue. 13.5.
Les conceptions des plateaux des colonnes de distillation sont très diverses. Considérons brièvement les principaux.
Colonnes avec calottes à bulles largement utilisé dans l'industrie. L'utilisation de bouchons assure un bon contact entre la vapeur et le liquide, un mélange efficace sur le plateau et un transfert de masse intensif entre les phases. La forme des bouchons peut être ronde, polyédrique et rectangulaire, des plaques - à un ou plusieurs bouchons.
Une plaque avec des capuchons rainurés est illustrée à la fig. 13.6. La vapeur de la plaque inférieure passe à travers les interstices et pénètre dans les auges supérieures (inversées), qui la dirigent vers les auges inférieures remplies de liquide. Ici, la vapeur bouillonne à travers le liquide, ce qui fournit un transfert de masse intensif. Le niveau de liquide sur le plateau est maintenu par un dispositif de débordement.
Les colonnes avec des plaques de tamis sont illustrées à la fig. 13.7. Les plaques comportent un grand nombre de trous de petit diamètre (de 0,8 à 3 mm). La pression de la vapeur et la vitesse de son passage à travers les trous doivent être en accord avec la pression du liquide sur la plaque : la vapeur doit vaincre la pression du liquide et l'empêcher de fuir à travers les trous vers la plaque sous-jacente. Les plateaux tamis nécessitent donc une régulation adaptée et sont très sensibles aux changements de régime. En cas de diminution de la pression de vapeur, le liquide des plaques de tamis descend. Les plateaux tamis sont sensibles aux impuretés (dépôts) qui peuvent obstruer les trous, créant des conditions propices à la formation pressions élevées. Tout cela limite leur application.
Colonnes garnies(Fig. 13.8) se distinguent par le fait que le rôle des plaques est joué par la soi-disant «buse». Des anneaux spéciaux en céramique (anneaux de Raschig), des boules, des tubes courts, des cubes, des corps en forme de selle, en forme de spirale, etc. en divers matériaux (porcelaine, verre, métal, plastique, etc.) sont utilisés comme buses.
La vapeur entre dans la partie inférieure de la colonne à partir d'une chaudière externe et remonte la colonne vers le liquide qui s'écoule. Se répartissant sur une grande surface formée de corps tassés, la vapeur entre intensément en contact avec le liquide, en échangeant des composants. La buse doit avoir grande surface par unité de volume, ont une faible résistance hydraulique, résistent aux effets chimiques du liquide et de la vapeur, ont une résistance mécanique élevée et ont un faible coût.
Les colonnes garnies ont une faible résistance hydraulique et sont faciles à utiliser : elles sont facilement vidées, lavées, soufflées et nettoyées.
La conception de la colonne de distillation a une structure plus complexe que celle d'un distillateur Moonshine conventionnel. De plus, contrairement à l'appareil, par exemple, avec une vapeur sèche, travailler avec une colonne implique une sorte de mode «préparatoire» avant le début de la distillation elle-même. Si vous avez de la chance (nous vous recommandons de choisir un appareil de la marque), vous trouverez probablement des instructions dans le kit correspondant. Assurez-vous d'étudier ce document important, car toutes les instructions pour travailler avec ce modèle particulier y seront données. En fait, l'utilisation d'une colonne de distillation est une affaire simple, l'essentiel est de comprendre exactement ce qui est fait et pourquoi.
Comment utiliser une colonne de distillation
Pour commencer, il convient de noter qu'il n'est pas tout à fait correct de distiller le moût immédiatement en mode rectification. Dans ce cas, peu importe. Vous risquez la buse qui, en très peu de temps, se «bouchera», ce qui rendra impossible le processus de nettoyage des vapeurs d'alcool. Cependant, presque toutes les colonnes de distillation domestiques sont capables de fonctionner en mode distillation, ce qui permettra d'obtenir de l'alcool brut au premier étage. Mais il peut déjà faire l'objet d'une rectification.
L'étape préparatoire est le mode de fonctionnement de la colonne "sur elle-même" pendant 15 à 20 minutes. Ceci est nécessaire à son échauffement, grâce auquel vous éviterez les pertes en alcool. Dans ce mode, il n'y a pas de sélection de fractions, un refroidissement maximal est fourni au condenseur à reflux, toutes les vapeurs s'y condensent et le soi-disant « flegme sauvage » s'écoule intégralement vers le cube de distillation.
Rappelez-vous toujours que le réglage de la température en ajoutant / diminuant le chauffage ou le refroidissement doit être effectué en douceur et progressivement, car le système est inertiel et l'établissement d'un nouveau régime de température stable à l'intérieur de la colonne ne se produit pas immédiatement, mais dans les 20 à 30 secondes.
Au début du travail de la colonne de distillation "pour vous-même", vous pouvez entendre un léger "soupir", et c'est normal. C'est l'air qui était dans la colonne avant que les vapeurs n'y arrivent. Au moment où la colonne entre en mode de fonctionnement (le début du processus d'échange de phase liquide-vapeur par masse et chaleur), la colonne peut commencer à émettre un léger bruit, ce qui est également la norme.
Lorsque la colonne s'est réchauffée, l'étape de rectification commence directement. Soyez propre éthanol sans impuretés étrangères, seule une colonne de distillation peut aider.
Comment utiliser la colonne de distillation en « mode travail » ?
Voici un petit guide :
- La température dans la partie supérieure de la colonne est réglée de telle manière (en ajustant le refroidissement du condenseur à reflux et en chauffant le cube) que les fractions de tête commencent à s'évaporer. En règle générale, il fait 65-68°C. Dans vous pouvez trouver des informations selon lesquelles les lectures du thermomètre peuvent donner un "peigne" insignifiant. Mais l'essentiel est que ce soit dans des limites étroites et, en général, le régime de température reste stable.
- Les têtes sont prélevées à un rythme ne dépassant pas une goutte par seconde. Sinon, les critères sont les mêmes que pour la distillation dans un distillateur classique (on peut calculer le volume des têtes, ou on peut naviguer à l'odeur).
- Après sélection des têtes, la température dans la colonne est portée à 77-78°C. La vitesse de sélection peut être légèrement augmentée ici. Augmentez légèrement le refroidissement et ajoutez de la chaleur.
- Dès que la température dans la colonne lors de la sélection du «corps» a commencé à grimper, il était temps de changer le réservoir de réception et de sélectionner les queues, si elles vous intéressent, bien sûr.
En général, il est clair qu'il n'est pas si difficile de travailler avec une colonne de distillation, il est important d'ajuster le régime de température à la fois ou deux, car la qualité des fractions sélectionnées en dépend davantage. Quant à l'utilisation de la boisson résultante, ici chaque propriétaire décide par lui-même: sera-t-il ou sera-t-il utilisé de l'éthanol pur à des fins médicales ou techniques.
La production à domicile de boissons fortes nécessite un équipement moderne en matériel de qualité. Dans les magasins, les fabricants proposent des modèles divisés en distillateurs et redresseurs. De nombreux distillateurs débutants sont tourmentés par la question: quoi de mieux pour le brassage à domicile - une colonne ou un moonshine still.
Le principe de fonctionnement n'est pas très différent, mais le produit final de la colonne de distillation est meilleur et plus propre, et il n'a pas d'égal en force, car il s'agit d'alcool presque pur. Pour savoir en quoi ces appareils diffèrent, quels sont leurs paramètres techniques, leurs nuances individuelles, s'il y a des lacunes, vous devez lire cet article.
Toute la procédure de distillation consiste en l'échange de chaleur qui se produit dans le produit, pendant le processus de refroidissement, la matière première est séparée et la substance purifiée apparaît à la sortie de l'appareil. À différentes températures de chauffage, vous obtenez différentes substances :
- t \u003d + 56 C - on obtient de l'acétone;
- t = +65 C - l'alcool méthylique peut être isolé ;
- et ce n'est qu'à t = +78 C que l'on obtient l'alcool rectifié ;
- si vous continuez à chauffer jusqu'au point d'ébullition de l'eau et au-dessus, par exemple jusqu'à 100 degrés, nous aurons à la sortie de l'eau aromatisée aux huiles de fusel et à toutes sortes d'impuretés.
La base de tout ce qui se passe dans la colonne de traitement est le contact des états liquide et vapeur diverses substances, à la suite de quoi diverses vapeurs sont libérées, qui se déposent dans le condenseur à reflux, et seules celles contenant de l'alcool passent.
Un chauffage supplémentaire se produit dans l'évaporateur, mais seulement jusqu'à +78 degrés, de sorte que toutes les impuretés nocives et l'eau se condensent et restent dans l'appareil. Dans différentes parties du produit, une interaction individuelle des vapeurs et du condensat se produit, et des fractions de différents niveaux de température tombent dans le condensat et s'écoulent vers la partie inférieure.
Une colonne est un appareil qui a une certaine hauteur, avec un récipient étendu sur toute sa longueur, de sorte qu'une température différente est obtenue : seules les vapeurs contenant de l'alcool atteignent le sommet, toutes les autres fractions se condensent, car la température est inférieure à celle nécessaire pour leur ébullition. Le goût et la force du produit final diffèrent considérablement selon meilleur côté de moonshine, passé par un distillateur standard.
Les modèles modernes de colonnes se distinguent par une très haute performance, et l'alcool résultant de la rectification n'a pas d'odeur de fusel et d'impuretés.
Quelle est la différence entre un alambic moonshine et une colonne de distillation
La différence la plus importante: un appareil standard pour le brassage domestique se compose d'un cube de distillation et d'un serpentin réfrigérant, où les vapeurs contenant de l'alcool se condensent. Dans certains modèles, il existe un cuiseur à vapeur, où une séparation de haute qualité des impuretés et une aromatisation des vapeurs ont lieu pour obtenir un alcool d'élite sous forme de brandy ou de whisky.
La colonne, en revanche, est un appareil assez complexe, elle est principalement destinée au nettoyage du clair de lune déjà obtenu afin d'éliminer toutes les plus petites inclusions étrangères et d'obtenir de l'alcool pur. La conception est en acier inoxydable, en cuivre ou en laiton, car des processus à haute température très complexes se déroulent à l'intérieur et la résistance à la corrosion doit être assez élevée.
La partie inférieure de la colonne s'appelle le tsarga, et la partie supérieure s'appelle le refroidisseur ou déphlegmateur, car c'est là que se produit la séparation finale des différents mucosités. Son couvercle contient un tube de communication avec environnement afin que la pression interne ne dépasse pas la valeur admissible. Nous avons déjà discuté de toutes les nuances du travail, nous l'omettons donc.
Le produit est installé sur une cuve ou un cube de distillation, et toutes les connexions doivent être parfaitement étanches. Tout en haut se trouve un tuyau d'évacuation des vapeurs d'alcool, la meilleure option lorsqu'il dispose également d'un réfrigérateur supplémentaire. La hauteur du produit est correcte, certains échantillons mesurent jusqu'à 2 m, donc cette conception peut ne pas convenir à l'intérieur : 2 m + réservoir + poêle. La meilleure option- chauffer le réservoir sur un réchaud spécial pour le clair de lune : il a de petites dimensions, comme un réchaud électrique de bureau.
Il n'est pas recommandé de distiller Braga à travers une colonne, bien qu'aujourd'hui les fabricants maîtrisent déjà la production d'échantillons améliorés capables de faire face à une telle application. Le verdict est simple : les alambics moonshine sont conçus pour distiller de l'alcool brut, et la colonne peut le purifier presque complètement des odeurs et des impuretés nocives.
Rappelles toi! Une colonne de distillation est utilisée pour obtenir de l'alcool pur, et si vous voulez faire du brandy, du brandy, où vous avez besoin de l'arôme et de la saveur spécifique du produit d'origine, utilisez uniquement du moonshine.
Types d'alambics et de colonnes de distillation Moonshine
Au total, il existe deux principaux types d'appareils pour le brassage domestique pratique dans le monde :
- Les vapeurs contenant de l'alcool sont évacuées sur le côté pour le refroidissement - directement dans le serpentin ou à travers le sécheur.
- Les vapeurs sont évacuées vers le haut dans un dispositif de distillation, où les impuretés sont séparées, nettoyage complet des odeurs et du refroidissement ultérieur.
Les appareils classiques sont divisés selon le système de refroidissement : à serpentin ou à flux direct, où l'élément de refroidissement est le corps du réfrigérateur.
Les colonnes sont divisées en fonction de la quantité de produit final obtenu :
- simple, assurant la séparation de la matière première en deux produits finaux - rectifié et sédiment ;
- complexe - ils assurent la séparation en plus de deux produits, des colonnes avec la sélection de fractions supplémentaires sous forme de bandes latérales et de bandes de décapage spéciales.
Il existe également une division selon le but, la pression, le principe de fonctionnement ou l'organisation des contacts au sein de la structure.
De plus, les colonnes sont divisées en complètes et incomplètes. Les produits incomplets sont divisés en deux types :
- Une colonne de lavage ou de distillation, qui fonctionne selon ce principe : la vapeur contenant de l'alcool entre dans le plateau supérieur, et sort du cube eau pure. La condensation tombe dans le réfrigérateur et le condenseur à reflux n'est pas installé.
- Dans les colonnes à alcool, tout se passe en miroir : la vapeur est amenée sous le plateau inférieur. L'alcool est éliminé de la partie supérieure et le résidu avec de l'eau est éliminé du fond, le déphlegmateur remplit la fonction d'alimentation du milieu liquide. De telles colonnes sont installées sur des alambiks.
Les premiers ne sont pas destinés à produire de l'alcool pur, et la deuxième option n'est pas utilisée pour produire de l'eau pure.
Caractéristiques des deux appareils
Tout le monde sait que le but principal d'un moonshine est d'obtenir un liquide contenant de l'alcool à partir de la purée par distillation et purification ultérieure. Les principaux paramètres techniques sont :
Le volume
C'est lui qui affecte l'échelle de production à la maison, donc le choix du produit est basé sur ce paramètre : plus il y a de moût, plus il y a de litres d'alcool brut qui est purifié diverses méthodes ou effectuer une redistillation.
Matériel
Fondamentalement, chaque détail modèles modernes sont en inox alimentaire ou médical. Les marques suivantes sont utilisées dans la production :
- L'AISI 304, en raison de ses propriétés de nettoyage assez élevées, est utilisé en médecine, dans les fermes laitières et les usines similaires ;
- l'acier de qualité 430 est de mauvaise qualité, mais les produits fabriqués à partir de celui-ci peuvent être chauffés sur des cuisinières à induction;
- alliages de cuivre et combinaisons d'acier différentes marques se trouvent dans de nombreux modèles d'alambics Moonshine de production nationale et étrangère.
À appareils maison l'aluminium est toujours utilisé, mais il est presque remplacé par des matériaux plus fiables. Les bobines sont en cuivre ou en laiton, seuls les appareils d'élite appelés alambiks, qui sont utilisés pour produire de l'alcool d'élite fait maison, sont entièrement en cuivre.
Appareils supplémentaires
Il s'agit notamment d'un thermomètre, d'un alcoomètre, d'un vaporisateur à vapeur sèche, d'un condenseur à reflux et d'autres qui aident à contrôler le processus de distillation. Une purification répétée donne un bon résultat, mais elle n'est pas effectuée dans le cas où vous avez besoin d'une boisson parfumée avec une odeur.
Caractéristiques techniques des colonnes à distiller universelles pour plus de clarté, il est préférable de présenter sous forme de petit tableau :
Tous les raccords d'étanchéité de la colonne sont en silicone alimentaire haute température avec période de garantie fonctionnement pendant au moins 10-20 ans, la température est autorisée jusqu'à +150°C.
Avantages et inconvénients
L'appareil standard pour la production de moonshine présente les avantages suivants:
- La conception la plus simple, le principe de fonctionnement est clair pour tous les utilisateurs, vous pouvez le fabriquer vous-même sans frais financiers importants.
- Un grand nombre de recettes sont fournies avec le modèle fini, mais vous pouvez les étendre considérablement en étudiant la recette sur Internet.
- Haute fiabilité d'une conception et de tous les matériaux.
- Faible coût, ce qui affecte particulièrement la grande disponibilité pour tous les segments de la population.
Les colonnes de distillation ont leurs avantages :
- Obtention d'un produit pur sans odeur ni impuretés.
- La résistance du produit final est bien supérieure à celle d'un appareil simple.
- Il est utilisé pour isoler un liquide contenant de l'alcool d'une purée à base de sucre, car c'est là qu'il y a beaucoup d'impuretés et d'odeurs.
En comparaison, l'appareil classique a plus de caractéristiques négatives :
- faible niveau de rendement;
- faible pourcentage de teneur en alcool - pas plus de 70%;
- faible degré de purification lors de la distillation primaire ;
- danger si les consignes de sécurité ne sont pas respectées.
Les colonnes de distillation n'ont qu'un seul inconvénient - la grande hauteur de la structure.
Quoi de mieux choisir
Si nous comparons la conception d'un produit classique pour le brassage domestique et d'une colonne de distillation, la différence est perceptible et ils sont utilisés à des fins différentes. Par conséquent, votre choix dépendra directement des objectifs, ainsi que de ce que vous allez dépasser :
- Pour la purée de vin, ainsi qu'à base de baies et de fruits, il est préférable d'utiliser du clair de lune.
- Pour la purée de sucre, il est préférable d'utiliser une colonne, car le produit final est propre et sans odeur.
Aujourd'hui, il existe des modèles de produits universels en vente qui peuvent fonctionner comme un simple distillateur ou comme une puissante colonne de distillation.
Les distillateurs expérimentés sont particulièrement demandés par les appareils fabriqués par des fabricants allemands dotés d'un tiroir supplémentaire vissé dans le distillateur. Par exemple, la colonne et l'appareil ont la même capacité de 2 l/h, mais le produit est bien différent :
- la densité ou résistance d'un produit classique n'est que de 60%, et celle d'une colonne est de 96% ;
- le niveau de purification du distillateur est 60 fois inférieur à celui de la colonne.
Les alambics Moonshine sont plus pratiques en raison de leurs dimensions, et les colonnes sont beaucoup plus hautes - les plus compactes mesureront environ un mètre de haut.
Si nous comparons les performances de différents produits, alors le classique produit 2 litres par heure d'alcool brut, et la colonne - 2 litres d'alcool pur à 96,6% ou en termes de moonshine à 60% - 6-7 litres. Par conséquent, lors de l'achat, vous devez décider de ce qui est le plus important pour vous - la pureté du produit final ou la simple utilisation du produit n'importe où. Les opportunités financières jouent également un rôle important.
conclusions
Si nous parlons de la pureté du produit final, alors les colonnes de distillation sont un cran au-dessus d'un simple distillateur Moonshine, mais grande importance a un côté financier. Chaque utilisateur choisit lui-même le modèle nécessaire, mais nous affirmons sans passion que les classiques du genre perdent encore Le progrès technique face à une colonne de distillation plus productive au regard des principaux indicateurs techniques.
§ 13.2 Colonnes de distillation : leur conception et leur fonctionnement
Comme mentionné ci-dessus, la distillation est effectuée dans un appareil spécial - les colonnes de distillation, qui sont les principaux éléments des installations de distillation.
processus de rectification peut être effectuée périodiquement et en continu, quels que soient le type et la conception des colonnes de distillation. Considérez le processus de distillation continue, qui est utilisé pour séparer les mélanges liquides dans l'industrie.
Colonne de distillation- vertical appareil cylindrique avec soudure (ou corps préfabriqué), dans lequel des dispositifs d'échange de masse et de chaleur (plaques horizontales 2 ou buse). Au bas de la colonne (Fig. 13.3) il y a un cube 3, dans lequel le liquide du fond bout. Le chauffage dans le cube est effectué grâce à la vapeur sourde située dans le serpentin ou dans la chaudière à calandre. Une partie intégrante de la colonne de distillation est un déphlegmateur 7, destiné à condenser la vapeur sortant de la colonne.
La colonne à plaques de distillation fonctionne comme suit. Le cube est constamment chauffé et le liquide du fond bout. La vapeur formée dans le cube monte dans la colonne. Le mélange initial à séparer est préchauffé à ébullition. Il alimente la plaque nutritive 5, qui divise la colonne en deux parties : inférieure (exhaustive) 4 et supérieur (renforcement) 6. Le mélange initial de la plaque nutritive s'écoule vers les plaques sous-jacentes, interagissant sur son chemin avec la vapeur se déplaçant de bas en haut. Du fait de cette interaction, la vapeur s'enrichit en composant volatil, et le liquide qui s'écoule, étant appauvri en ce composant, s'enrichit en composant peu volatil. Dans la partie inférieure de la colonne, le processus d'extraction (épuisement) du composant volatil du mélange initial et sa transition vers la vapeur a lieu. Une partie du produit fini (rectifié) est acheminée vers le haut de la colonne pour l'irrigation.
Le liquide entrant en haut de la colonne pour l'irrigation et s'écoulant dans la colonne est appelé flegme. La vapeur, en interaction avec le reflux sur tous les plateaux de la partie supérieure de la colonne, est enrichie (renforcée) d'un composant volatil. La vapeur sortant de la colonne est envoyée au déphlegmateur 7, dans lequel elle est condensée. Le distillat obtenu est divisé en deux flux : l'un sous la forme d'un produit est envoyé pour un refroidissement supplémentaire et vers l'entrepôt de produits finis, l'autre est renvoyé vers la colonne en tant que reflux.
L'élément le plus important d'une colonne de distillation à plateaux est le plateau, car c'est sur lui que la vapeur interagit avec le liquide. Sur la fig. 13.4 montre un schéma de l'appareil et du fonctionnement plaque de chapeau. Elle a un cul 1, hermétiquement relié au corps de colonne 4, buses à vapeur 2 et tuyaux de vidange 5. Les buses à vapeur sont conçues pour laisser passer les vapeurs s'élevant de la plaque inférieure. À travers les tuyaux de drainage, le liquide s'écoule de la plaque sus-jacente à celle sous-jacente. Un capuchon est monté sur chaque buse vapeur 3, au moyen duquel les vapeurs sont dirigées dans le liquide, barbotées à travers celui-ci, refroidies et partiellement condensées. Le fond de chaque plateau est chauffé par les vapeurs du plateau sous-jacent. De plus, la condensation partielle de la vapeur dégage de la chaleur. En raison de cette chaleur, le liquide sur chaque plaque bout, formant ses propres vapeurs, qui se mélangent aux vapeurs de la plaque sous-jacente. Le niveau de liquide sur la plaque est maintenu au moyen de tuyaux de vidange.
Riz. 13.3. Schéma d'une colonne à distiller : / - corps ; 2 - assiettes ; 3 - cube; 4, 6 - parties exhaustives et renforçantes de la colonne ; 5 - assiette nutritive; 7 - déphlegmateur
Les processus se produisant sur la plaque peuvent être décrits comme suit (voir Fig. 13.4). Laissez les vapeurs de la composition L du plateau inférieur entrer dans le plateau, et le liquide de la composition À. En raison de l'interaction de la vapeur MAIS avec du liquide À(la vapeur, bouillonnant à travers le liquide, l'évapore partiellement et se condense partiellement) une nouvelle vapeur de la composition se forme DE et nouvelle composition fluide ré, étant en équilibre. A la suite du travail de la plaque, de la vapeur neuve DE plus riche en matières volatiles par rapport à la vapeur provenant de la plaque inférieure MAIS, c'est-à-dire sur une plaque de vapeur DE enrichi en matières volatiles. Nouveau liquide ré, au contraire, il s'est appauvri en matières volatiles par rapport au liquide issu du plateau supérieur À, c'est-à-dire que sur une assiette, le liquide est appauvri en composant volatil et enrichi en composant non volatil. Bref, le travail de la plaque se réduit à l'enrichissement de la vapeur et à l'appauvrissement du liquide en composant hautement volatil.
Riz. 13.4. Schéma de l'appareil et fonctionnement de la plaque chapeau : / - le fond de la plaque ; 2 - tuyau de vapeur;
3 - casquette; 4 - corps de colonne ; 5 - tuyau de vidange
Riz. 13.5. L'image du travail d'une plaque de distillation sur le schéma à-x : 1- courbe d'équilibre ;
2 - ligne de concentrations de travail
Une plaque sur laquelle un état d'équilibre est atteint entre les vapeurs qui en sortent et le liquide qui en descend est appelée théorique. Dans des conditions réelles, en raison de l'interaction à court terme de la vapeur avec le liquide sur les plaques, un état d'équilibre n'est pas atteint. La séparation du mélange sur une plaque réelle est moins intense que sur une plaque théorique. Donc, pour réaliser : le fonctionnement d'une plaque théorique nécessite plus d'une plaque réelle.
Sur la fig. 13.5 montre le fonctionnement d'un plateau de distillation à l'aide d'un schéma à-X. La plaque théorique correspond à un triangle rectangle hachuré, dont les jambes sont l'amplitude de l'augmentation de la concentration du composant volatil dans la vapeur, égale à moustache-y un , et l'amplitude de la diminution de la concentration du composant volatil dans le liquide, égale à X B - X ré . Les segments correspondant aux changements de concentration indiqués convergent vers la courbe d'équilibre. Cela suppose que les phases sortant de la plaque sont en équilibre. Cependant, en réalité, l'état d'équilibre n'est pas atteint, et les segments de l'évolution des concentrations n'atteignent pas la courbe d'équilibre. C'est-à-dire que la plaque de travail (réelle) correspondra à un triangle plus petit que celui illustré
En figue. 13.5.
Les conceptions des plateaux des colonnes de distillation sont très diverses. Considérons brièvement les principaux.
Colonnes avec calottes à bulles largement utilisé dans l'industrie. L'utilisation de bouchons assure un bon contact entre la vapeur et le liquide, un mélange efficace sur le plateau et un transfert de masse intensif entre les phases. La forme des bouchons peut être ronde, polyédrique et rectangulaire, des plaques - à un ou plusieurs bouchons.
Une plaque avec des capuchons rainurés est illustrée à la fig. 13.6. La vapeur de la plaque inférieure passe à travers les interstices et pénètre dans les auges supérieures (inversées), qui la dirigent vers les auges inférieures remplies de liquide. Ici, la vapeur bouillonne à travers le liquide, ce qui fournit un transfert de masse intensif. Le niveau de liquide sur le plateau est maintenu par un dispositif de débordement.
Les colonnes avec des plaques de tamis sont illustrées à la fig. 13.7. Les plaques comportent un grand nombre de trous de petit diamètre (de 0,8 à 3 mm). La pression de la vapeur et la vitesse de son passage à travers les trous doivent être en accord avec la pression du liquide sur la plaque : la vapeur doit vaincre la pression du liquide et l'empêcher de fuir à travers les trous vers la plaque sous-jacente. Les plateaux tamis nécessitent donc une régulation adaptée et sont très sensibles aux changements de régime. En cas de diminution de la pression de vapeur, le liquide des plaques de tamis descend. Les plateaux tamis sont sensibles aux impuretés (précipitations) qui peuvent obstruer les trous, créant des conditions propices à la formation de pressions accrues. Tout cela limite leur application.
Colonnes garnies(Fig. 13.8) se distinguent par le fait que le rôle des plaques est joué par la soi-disant «buse». Des anneaux spéciaux en céramique (anneaux de Raschig), des boules, des tubes courts, des cubes, des corps en forme de selle, en forme de spirale, etc. en divers matériaux (porcelaine, verre, métal, plastique, etc.) sont utilisés comme buses.
La vapeur entre dans la partie inférieure de la colonne à partir d'une chaudière externe et remonte la colonne vers le liquide qui s'écoule. Se répartissant sur une grande surface formée de corps tassés, la vapeur entre intensément en contact avec le liquide, en échangeant des composants. La garniture doit avoir une grande surface par unité de volume, fournir une faible résistance hydraulique, être résistante aux effets chimiques du liquide et de la vapeur, avoir une résistance mécanique élevée et être d'un faible coût.
Les colonnes garnies ont une faible résistance hydraulique et sont faciles à utiliser : elles sont facilement vidées, lavées, soufflées et nettoyées.
Riz. 13.6. Plaque avec bouchons rainurés : un- Forme générale; b- coupé dans le sens de la longueur ; dans- schéma de la plaque
Riz. 13.7. Schéma du dispositif à plaque tamis: / - corps de colonne; 2 - assiette; 3 - tuyau de vidange ; 4 - serrure hydraulique ; 5 - trous
Riz. 13.8. Schéma d'une colonne de distillation à garnissage : 1 - Cadre; 2 - apport du mélange initial ; 3 - vapeur; 4 - irrigation ; 5 - treillis; 6 - buse; 7-élimination du produit à haut point d'ébullition j-. 8 - chaudière à distance