Poka-Yoke-Beispiele in der Mechanik. Methoden zur Narrensicherheit werden in der Reihenfolge zunehmender Wirksamkeit in drei Stufen unterteilt.
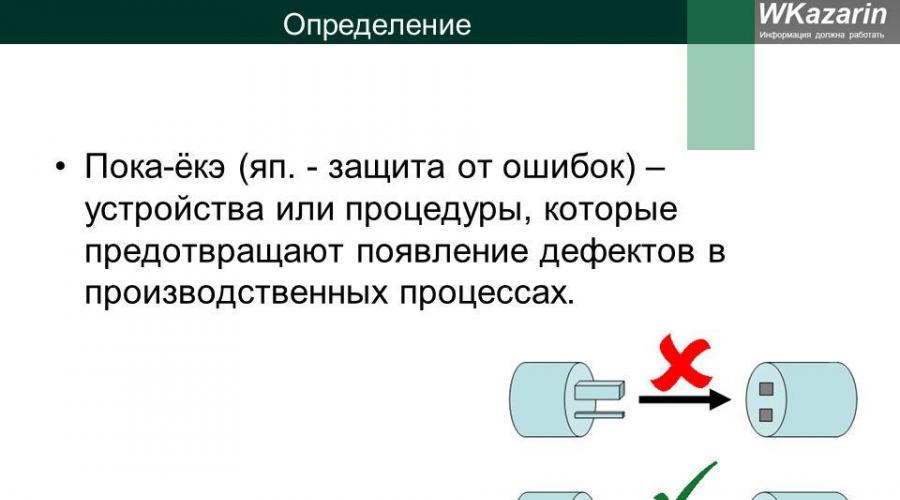
Lesen Sie auch
Definition Poka-Yoke (japanisch – Fehlerschutz) – Geräte oder Verfahren, die das Auftreten von Fehlern in Produktionsprozessen verhindern.
Poka-Yoke. Beispiel 2. Eine Fotozelle, die ausgelöst wird, wenn eine Person eine unsichtbare Kontrolllinie überquert (oder umgekehrt, nicht überquert). Beispielsweise muss ein Monteur unbedingt ein bestimmtes Teil entnehmen und verwenden.
Arten menschlicher Fehler Vergesslichkeit Unverständnis für die Gründe Unterschätzung Unerfahrenheit Zurückhaltung Unaufmerksamkeit Langsamkeit Mangel an Standards Überraschung Absicht
Fehlerquellen Fehlbedienung Bearbeitungsfehler Teilepositionierungsfehler Fehlende Teile Falsche Teile Bearbeitung des falschen Teils Falsche Bedienung Einrichtungsfehler Falsche Geräteinstallation Verwendung falscher Werkzeuge oder Vorrichtungen Fukushima-1.
Beispiellösung: Gussverarbeitung Problem: Unbearbeitete Teile Lösung: Auswechseln der Rutsche, um fehlerhafte Teile zu identifizieren Prozessbeschreibung: Gussteile werden auf einer automatischen Maschine bearbeitet und durch die Rutsche in den nächsten Prozess überführt. Vor der Verbesserung: Wenn ein unbearbeitetes Teil durch die Rutsche gelangt, Die nächste Maschine im Prozess stoppt ungewöhnlich und kann beschädigt werden. Zeichnung aus dem Buch „Poka-Yoke. Verbesserung der Produktqualität durch Vermeidung von Fehlern“
Ein Beispiel für eine Lösung eines Problems: Gussbearbeitung Nach der Verbesserung: Um ein unbearbeitetes Teil zu stoppen, wurde eine Methode entwickelt, die den Unterschied in seinem berücksichtigt Geometrische Figur vom verarbeiteten Teil. Die Rutsche wurde so modifiziert, dass das Rohteil in einem in der Rutsche installierten Block stoppt und nicht in die nächste Maschine fließt. Dadurch konnten Maschinenausfälle verhindert werden. Zeichnung aus dem Buch „Poka-Yoke. Verbesserung der Produktqualität durch Vermeidung von Fehlern“
Die Präsentation „ABC“ ist im Abschnitt „Ressourcen“ veröffentlicht. Lean Manufacturing. Was ist Poka-Yoke? Poka-Yoke (oder Poka-Yoke) sind Geräte oder Verfahren, die das Auftreten von Fehlern in Herstellungsprozessen verhindern. Die Präsentation gibt eine Definition, listet die Arten menschlicher Fehler und Fehlerquellen auf und liefert mehrere Beispiele.
Unten im Text der Notiz finden Sie den Begleittext.
Darüber hinaus wird diese Präsentation im Videoformat mit meinen Kommentaren auf gepostet Youtube.com und Rutube.ru.
Ich bitte Sie, Ihre Kommentare und Vorschläge auf den YouTube- und Rutube-Websites, direkt auf der Videoseite oder über das Formular auf meiner Website abzugeben, damit ich sie in Zukunft berücksichtigen kann.
Abschrift des Begleittextes
Poka-Yoke (was auf Japanisch „Fehlervermeidung“ bedeutet) sind Geräte oder Verfahren, die das Auftreten von Fehlern in Herstellungsprozessen verhindern.
Schauen wir uns ein paar Beispiele an.
Beispiel Nr. 1. Die Form des Produkts ist so, dass es nicht zur Handhabung oder Verwendung in einer falschen Position (verkehrt herum oder verkehrt herum) installiert werden kann. Sie haben es mit einer 3-Zoll-Diskette zu tun, die nur in einer Position vollständig in das Laufwerk eingeschoben werden kann.
Beispiel Nr. 2. Eine Fotozelle, die ausgelöst wird, wenn eine Person eine unsichtbare Kontrolllinie überquert (oder umgekehrt nicht überschreitet). Beispielsweise muss ein Monteur unbedingt ein bestimmtes Teil entnehmen und verwenden.
Fehler entstehen durch menschliches Versagen.
Es gibt 10 Arten menschlicher Fehler, die zu Fehlern führen. Das:
- Vergesslichkeit,
- Missverständnis der Gründe (das Auftreten von etwas)
- Unterschätzung einer Situation (oder Unfähigkeit, ein Objekt zu identifizieren)
- Unerfahrenheit
- Zurückhaltung (Abläufe und Regeln zu befolgen)
- Unaufmerksamkeit
- Langsamkeit (bei der Entscheidungsfindung)
- Mangel an Standards
- Überraschung
- absichtlich einen Fehler machen (oder sabotieren)
Die Fehlerquellen sind folgende Sachverhalte:
- verpasste Operation
- Verarbeitungsfehler
- Fehler bei der Teilepositionierung
- fehlendes Detail
- falscher Teil
- Bearbeitung des falschen Teils
- Fehlbedienung am richtigen Teil
- Konfigurationsfehler
- falsche Installation von Geräten und
- Verwendung des falschen Werkzeugs oder der falschen Vorrichtung
Schauen wir uns ein Beispiel für die Lösung eines Problems an.
Das Problem liegt in den Rohteilen. Die angewandte Lösung bestand darin, die Rutsche zu modifizieren, um fehlerhafte Teile zu identifizieren.
Sehen Sie das Bild an.
Gussteile werden auf einer automatischen Maschine bearbeitet und über eine Rutsche dem nächsten Prozess übergeben.
Vor der Verbesserung geschah Folgendes: Wenn ein unbearbeitetes Teil die Rutschen passiert, stürzt die nächste Maschine im Prozess ab und kann beschädigt werden.
Um ein unbearbeitetes Teil anzuhalten, wurde eine Methode entwickelt, die den Unterschied seiner geometrischen Form zum bearbeiteten Teil berücksichtigt. Die Rutsche wurde so modifiziert, dass das unbearbeitete Teil in einem in der Rutsche installierten Block stoppt und nicht auf der nächsten Maschine landet. Dadurch konnten Maschinenausfälle verhindert werden.
Die Entstehungsgeschichte des „Poke-Eka“-Systems
Im Jahr 1961 analysiert Produktionsstruktur Shingo, ein Unternehmen von Yamaha Electric, entwickelte die Baka-Yoke-Methode (narrensicher). Er kam zu dem Schluss, dass das allgemein anerkannte statistische Kontrollsystem Mängel nicht verhindert. Natürlich ließe sich mit seiner Hilfe die Wahrscheinlichkeit des Auftretens des nächsten Defekts vorhersagen, dies wäre jedoch nur eine Tatsachenfeststellung. Shingo beschloss, Kontrollen in den Prozess selbst zu integrieren. Schließlich ist die Ehe das Ergebnis menschlicher Fehler. Fehler sind natürlich unvermeidlich, aber sie können durch die Entwicklung von Maschinen und Werkzeugen mit Feedback verhindert werden. Der Versuch, ein Teil falsch einzulegen, führte sofort zu einem Arbeitsstopp. Ein Alarmsignal wurde auch empfangen, wenn ein Mitarbeiter vergaß, eine Operation durchzuführen. Nachdem ein Fehler aufgetreten war, wurde dieser identifiziert, identifiziert und ein erneutes Auftreten vollständig verhindert. So trennte Shigeo Shingo Ursache von Wirkung – Fehler von Defekt und garantiert so 100 % Produktqualität. Schließlich erfolgte die Qualitätskontrolle nicht mehr durch Probenentnahme am QD-Tisch, sondern ausnahmslos bei allen Produkten direkt an der Maschine. Die Ergebnisse waren sofort sichtbar. Zum Beispiel im Jahr 1977 Produktionswerkstätten Das Unternehmen Matsushita Electric, bei dem das Shingo-System eingeführt wurde, arbeitete 7 Monate lang ohne Mängel. S. Shingo begann zu Recht, im In- und Ausland den Titel „Mr. Improvement“ zu verwenden.
Der Bezeichnung „narrensicher“ konnte man zwar nicht widerstehen. Eines Tages, als Shingo den Arbeitern eine neue Methode vorstellte, rief einer der Arbeiter: „Ich bin kein Dummkopf!“ Ich musste mich entschuldigen und der Methode einen neuen Namen geben: das Poka-Yoke-System (Schutz vor Fehlern oder 0-Fehler). Dieses System verbessert die Effizienz erheblich Fertigungsprozess, was dazu beiträgt, Abfall zu reduzieren, Kosten und Zeitverschwendung zu reduzieren.
Das Konzept der Bye-bye-Methode
Die Null-Fehler-Fertigung basiert auf einer Fehlervermeidungsmethode namens Poka-Yoke. Das „Poka-eka“-System lässt sich ins Russische mit „narrer Widerstand“ übersetzen.
Die Grundidee besteht darin, den Prozess zu stoppen, sobald ein Fehler erkannt wird, die Ursache zu ermitteln und zu verhindern, dass die Fehlerquelle erneut auftritt. Daher ist keine statistische Stichprobe erforderlich. Ein wesentlicher Bestandteil des Verfahrens besteht darin, dass die Prüfung der Fehlerquelle als aktiver Teil des Fertigungsprozesses durchgeführt wird, um Fehler zu erkennen, bevor sie zu Mängeln werden. Bei der Entdeckung eines Fehlers wird entweder die Produktion gestoppt, bis der Fehler behoben ist, oder der Prozess wird angepasst, um das Auftreten des Fehlers zu verhindern. Dies geschieht in jeder Phase des Prozesses durch die Überwachung potenzieller Fehlerquellen. Auf diese Weise werden Mängel an der Quelle erkannt und behoben und nicht erst zu einem späteren Zeitpunkt. Möglich wird dieser Prozess selbstverständlich durch den Einsatz von Werkzeugen und Mechanismen mit unmittelbarer Rückmeldung (der Einsatz von Personal wird dabei aufgrund der Fehlbarkeit vermieden). Der Einsatz von Personal ist jedoch unerlässlich, um potenzielle Fehlerquellen zu identifizieren. Im Alter von 40 Jahren lernte Shingo und nutzte es weitgehend statistische Methoden Qualitätskontrolle, aber 20 Jahre später, 1977, sagte er, er sei endlich von ihrem Bann befreit. Dies geschah, als er mit eigenen Augen beobachtete, wie am Fließband gearbeitet wurde Regen-Rinne In der Fabrik Waschmaschinen Das Matsushita-Unternehmen in Shizuoka, das 23 Mitarbeiter beschäftigte, konnte einen Monat lang ununterbrochen ohne einen einzigen Defekt arbeiten, dank der Installation von Poka-Yeke-Geräten, die das Auftreten von Defekten verhinderten. Shingo argumentiert, dass Nullfehler durch den Einsatz der Quellcodeverwaltung und des Poka-Yeke-Systems erreicht werden können. Zusammen bilden sie „Zero Quality Control“.
Dieses Konzept von „Null Fehlern“ unterscheidet sich von dem, was normalerweise mit dem Namen des amerikanischen Mentors Philip Crosby verbunden wird. Das Shingo-Konzept legt Wert darauf, durch den Einsatz von Gut Null Fehler zu erreichen Ingenieurausbildung Produktion und Erforschung von Produktionsprozessen, und nicht durch Appelle und Slogans, die mit Qualitätskampagnen amerikanischer und westeuropäischer Unternehmen verbunden sind. Shingo selbst zeigt sich ebenso wie Deming und Juran besorgt über diesen amerikanischen Ansatz und argumentiert, dass die Veröffentlichung von Fehlerstatistiken irreführend sei und dass es stattdessen notwendig sei, nach den fehlerhaften Elementen des Herstellungsprozesses zu suchen, die die meisten Produktfehler verursachen.
Das „Bye-bye“-System ist die Grundlage einer fehlerfreien Produktion.
Die meisten Produktionsfehler entstehen durch eine erhöhte Variabilität der Prozesseigenschaften, die wiederum folgende Ursachen haben kann:
* falsch entwickelte Standards oder dokumentierte Verfahren;
ѕ Verwendung von minderwertiger oder veralteter Ausrüstung;
* Verwendung ungeeigneter Materialien;
* Werkzeugverschleiß;
* Bedienerfehler.
Für alle diese Fehlerursachen, mit Ausnahme der letzten, können Korrektur- und Vorbeugungsmaßnahmen ergriffen werden. Es ist ziemlich schwierig, Bedienfehler zu verhindern.
Die zugrunde liegende Ideologie von Poke-Eka ist die Tatsache, dass es für Menschen ganz natürlich ist, im Arbeitsprozess Fehler zu machen. Und das ist kein Indikator für mangelnde Professionalität des Betreibers. Der Zweck von Poke-Ek besteht darin, Wege zu finden, um sich vor unbeabsichtigten Fehlern zu schützen. Eine Liste typischer Bedienhandlungen, die zu Störungen führen, ist in der Tabelle aufgeführt.
Die Poke-Eka-Methode basiert auf sieben Prinzipien:
1 Verwenden Sie robustes Design, um effiziente Prozesse zu erstellen.
2 Arbeiten Sie im Team: Nur so können Sie das Wissen Ihrer Mitarbeiter optimal nutzen.
3 Fehler beseitigen, auch durch robustes Design: Dadurch wird die Anzahl der Fehler näher an Null gebracht;
4 Beseitigen Sie die Grundursachen von Fehlern mithilfe der 5-Warum-Methode.
5 Sofort handeln, alle möglichen Ressourcen nutzen;
6 nicht wertschöpfende Aktivitäten eliminieren;
7 Verbesserungen umsetzen und sofort über weitere Verbesserungen nachdenken.
Bei der Verwendung von Poke-Eka verlassen sie sich nicht darauf, dass die Bediener selbst den Fehler finden. Daher werden bei der Ausführung von Arbeiten Berührungssensoren und andere Geräte verwendet. Dies trägt dazu bei, vom Bediener übersehene Fehler effektiv zu erkennen.
Die Poke-Ek-Methode sollte sowohl bei der Eingangskontrolle als auch während des gesamten Prozesses angewendet werden. Die Wirkung ihrer Umsetzung hängt davon ab, in welcher Phase des Prozesses – Eingangskontrolle oder Kontrolle während des Prozesses – diese Methode angewendet wurde. In diesem Fall können bei festgestellten Inkonsistenzen Warnsignale empfangen oder sogar die Anlage gestoppt werden.
Die Einführung der Poke-ek-Methode bei der Eingabekontrolle wird als proaktiver Ansatz bezeichnet. In diesem Fall wird ein Fehler erkannt, bevor bestimmte Vorgänge ausgeführt wurden, Warnsignale verwendet werden oder sogar die Anlage an der Ausgangssteuerung gestoppt werden kann.
Der Ansatz, bei dem die Poke-Eka-Methode auf andere Phasen des Produktionsprozesses angewendet wird, wird als reaktiv bezeichnet. In diesem Fall wird diese Methode verwendet:
* sofort nach Abschluss des Vorgangs;
* während der Arbeit des Bedieners;
* bei Überweisung nach nächste Stufe Verfahren.
Der reaktive Ansatz ist effektiv, weil er verhindert, dass fehlerhafte Produkte in die nächste Prozessstufe weitergeleitet werden, erreicht aber dennoch nicht so viel hochgradig Schutz vor Fehlern, wie es beim proaktiven Ansatz der Fall ist. Der Einsatz von Poke-Ek-Methoden bei der Suche nach Fehlerursachen liefert keine guten Ergebnisse, ist aber gleichzeitig deutlich effektiver als die selektive Kontrolle.
Es gibt noch andere Ansätze zur Anwendung der Poke-Eka-Methode: Kontrolle und Warnung. Bei einem Überwachungsansatz wird das Gerät automatisch angehalten, wenn ein Defekt erkannt wird. Der Warnansatz basiert auf dem Einsatz verschiedener Signalmittel (Licht- und Tonsignale), die den Bediener darüber informieren möglicher Fehler. Das Abschalten von Anlagen ist im präventiven Ansatz oft keine Option.
Die in Poke-Eka verwendeten Geräte werden entsprechend der ihrer Funktionsweise zugrunde liegenden Methode unterteilt in:
* Kontakt;
* Lektüre;
* sequentielle Bewegung.
Alle drei Gerätetypen können sowohl im Kontrollansatz als auch im Präventionsansatz eingesetzt werden.
Das Funktionsprinzip von Geräten mit Kontaktmethode basiert auf der Feststellung, ob das empfindliche Element Kontakt mit dem zu prüfenden Objekt hat. Ein Beispiel für solche Geräte sind Endschalter. Bei einer Kontaktunterbrechung wird beispielsweise ein akustisches Signal ausgelöst.
Zu den Geräten, die im Kontaktverfahren arbeiten, gehören auch Sender und Empfänger, Lichtschranken, piezoelektrische Sensoren usw. Die Geräte müssen nicht unbedingt Hightech sein. Einfache passive Geräte sind manchmal die besten. Sie verhindern, dass Teile während des Prozesses falsch platziert werden.
Lesegeräte werden verwendet, wenn es in einem Prozess eine feste Anzahl von Vorgängen und in einem Produkt eine feste Anzahl von Teilen gibt. Der Sensor zählt die Teile mehrmals und gibt das Produkt nur dann an den nächsten Prozess weiter, wenn die Anzahl der Teile stimmt.
Der dritte Gerätetyp sind Sensoren, die feststellen, ob ein Prozessvorgang abgeschlossen ist. Wird der Vorgang nicht abgeschlossen oder fehlerhaft ausgeführt, signalisiert der Sensor, dass das Gerät angehalten werden sollte. Viele Sensoren und fotoelektrische Geräte, die an einen Gerätetimer angeschlossen sind, arbeiten nach diesem Prinzip. Der Einsatz solcher Geräte ist am effektivsten, wenn im Prozess viele Teile verwendet werden, die in Form und Größe einander ähneln.
Durch die konsequente Anwendung der Poke-Eka-Methode kann die Fehlerquote der Bediener deutlich reduziert werden, was zur Kostensenkung und Steigerung der Kundenzufriedenheit beiträgt.
Eines Tages beobachtete ich es zufällig ähnliche Situation: Das Projekt war schlecht vorbereitet und wurde sehr überstürzt gestartet. Dadurch erwies sich das etablierte Verfahren als völlig untauglich für die Massenproduktion, was sich negativ auf die Beziehung zum Kunden auswirkte. Um den Kunden nicht völlig zu „verlieren“, war sofortiges Handeln erforderlich. Als erstes begann die Unternehmensleitung mit der Neuorganisation der Abteilung, insbesondere wurde beschlossen, den Abteilungsleiter zu ersetzen. Wahrscheinlich, Es lohnt sich, mich zu korrigieren: Ich habe gesagt, dass ich die Möglichkeit hatte, diese Situation zu beobachten, und zwar erst von dem Moment an, als ich dieser Abteilung zugewiesen wurde. Mit anderen Worten, ich musste die Situation nicht beobachten, sondern „ausschaufeln“. Aber darum geht es jetzt nicht...
Es gibt ein solches Konzept Englische Sprache„Kick-off-Meeting“ kann unterschiedlich übersetzt werden – von „Planungstreffen“ bis „Nachbesprechung“. In diesem Fall handelte es sich um eine Einführungsrede des neuen Chefs, in der er dazu aufrief, die aktuelle Situation zu durchbrechen so schnell wie möglich Bringen Sie das Qualitätsniveau auf das vom Kunden geforderte Niveau. Lassen Sie mich die Situation kurz skizzieren: 38 % Prozessausbeute (CFTY) und Verzögerung von 3 Produktlieferungen (mehr als 10.000 Einheiten Fertigprodukte). In dem Teil der Rede, der die Ingenieure betraf, äußerte der neu ernannte Chef einen sehr interessanten Satz:
- „Nehmen Sie zum Beispiel Alex. Bei der Erstellung des Installationsentwurfs stützte er sich auf seine Erfahrung, Ausbildung und sein Wissen über den Zweck des Geräts. Aber wenn er die Chance gehabt hätte, 12 Stunden lang als Bediener in einer Schicht mit ihm zusammenzuarbeiten, hätte er vielleicht noch ein paar zusätzliche Änderungen vorgenommen. Vielleicht sollten wir Sie eine Schicht arbeiten lassen? Immerhin während lange Arbeit Es wird sicherlich zu ungewöhnlichen Situationen kommen ...“
Hier ist ein interessanter Punkt: Ein Mensch ist kein Roboter, egal wie man ihm beibringt, aber bei längerer Arbeit treten unweigerlich Fehler oder ungewöhnliche Situationen auf, die zu Fehlern führen. Es scheint sinnlos, das Phänomen des menschlichen Faktors zu bekämpfen – jeder Prozess, an dem eine Person beteiligt ist, ist anfällig für Bedienfehler. Sie können jedoch die Häufigkeit solcher Fehler auf ein Minimum reduzieren oder versuchen, sie zu reduzieren. Erstellen Sie einen Prozess oder eine Ergänzung dazu, der das Auftreten von Fehlern verhindert.
Zum Beispiel beim Stricken von Autokabelbäumen: Alle Verbindungen sind so konstruiert, dass es äußerst schwierig ist, die Drähte zu verwechseln. Mit SIM-Karte Mobiltelefon Eine der Ecken ist „abgeschnitten“, was eine fehlerhafte Montage unmöglich macht. Kabelanschlüsse befinden sich im Inneren Systemeinheit persönlicher Computer haben verschiedene Formen Dadurch entfällt die Möglichkeit, für die Datenübertragung Strom an den Kabelstecker anzuschließen und umgekehrt.
Was haben die obigen Beispiele gemeinsam? – Systemkonfiguration, die menschliche Fehler eliminiert – Fehlerschutz – Poka Yoke.
Poka Yoke ist eine Philosophie des Qualitätsmanagements und der kontinuierlichen Prozessverbesserung, die darauf abzielt, die Möglichkeit menschlicher Fehler auszuschließen. Poka Yoke ist ein japanischer Ausdruck, der wörtlich „Fehlerschutz“ bedeutet.
Die praktische Umsetzung des Poka-Yoke-Prinzips kann von zwei Seiten betrachtet werden:
- Einerseits, und das ist der bevorzugte Weg, ist der Fehlerschutz ein System, bei dem das Auftreten eines Fehlers ausgeschlossen ist;
- Andererseits handelt es sich um ein System, das verhindert, dass ein fehlerhaftes Produkt den nächsten Betrieb, die nächste Station, den nächsten Standort, die nächste Linie oder den nächsten Kunden erreicht
Es sollte klargestellt werden, dass die Einführung einer 100 %-Kontrolle das Hinzufügen einer separaten Station oder eines separaten Betriebs bedeutet bestehenden Prozess und ist keine Umsetzung des Poka-Yoke-Prinzips. Oftmals erfordert eine solche Lösung zusätzliche Kosten, erhöht den Ressourcenaufwand für die Herstellung von Produkten und erhöht deren Kosten. Im Gegensatz zur zusätzlichen Kontrolle erfordert die Anwendung des Fehlersicherheitsprinzips zur Verhinderung des Eintritts eines fehlerhaften Produkts keine zusätzlichen Ressourcen und hat keinen Einfluss auf die Produktionskosten.
Lass uns nehmen echtes Beispiel aus der Praxis. Von Zeit zu Zeit trat bei Autoscheinwerfern, die im Förderbandverfahren zusammengebaut wurden, der gleiche Defekt auf – ein Kratzer auf der Linse. Es stellte sich heraus, dass der Scheinwerfer an einer der U-förmigen Vorrichtungen auf dem Förderband zerkratzt war. Dies geschah nur in Fällen, in denen der Scheinwerfer falsch auf dem Sockel montiert wurde – die unterdrückte Kante ragte höher heraus, als sie sollte, und beim Bewegen entlang des Förderbands blieb sie an der oben genannten Vorrichtung hängen.
Wie kann dieser Mangel behoben werden?
- Kaufen Sie ein automatisches Gerät, das den Scheinwerfer auf der Basis installiert.
- Sorgen Sie dafür, dass alle Bediener die Position des Scheinwerfers regelmäßig kontrollieren.
- Beauftragen Sie eine separate Person mit der Überwachung der Position der Scheinwerfer auf dem Sockel.
Es gibt viele Lösungen und sie sind alle unterschiedlich, aber eines haben sie gemeinsam: den Wunsch, dem Prozess etwas hinzuzufügen. Etwas, das zusätzliche Kosten verursacht und möglicherweise die Produktivität der Linie verringert.
Durch die Umsetzung des Poka-Yoke-Prinzips konnte dieser Mangel behoben werden: Auf dem Gerät wurde eine Platte aus weichem Material angebracht, die jedoch hart genug war, um das Produkt nicht zu verfehlen, was Kratzer auf den Scheinwerfern verursachte. Die Platte wurde einfach an den U-förmigen Rahmen des Geräts geschraubt und stoppte das Teil lediglich, sodass es nicht weiter passieren konnte.
Ein weiteres Beispiel: Alle Multimedia-Produkte verfügen über eine gewisse Speicherkapazität. Der „Speicher“-Teil des Produkts wird getrennt vom gesamten Produkt hergestellt und programmiert. Der Gerätekonfigurationsprozess besteht aus den folgenden Schritten:
- Geräteprüfung;
- „Low-Level“-Programmierung;
- Überprüfung des Programmcodes;
- Installation eines Sicherheitscodes;
- Funktionstest des Geräts (Simulation des Betriebs unter realen Bedingungen).
Alle diese Schritte werden automatisch innerhalb von 40 – 70 s durchgeführt. und sind für den Bediener nicht wahrnehmbar. Der Bediener sieht lediglich grüne oder rote Indikatoren, die den erfolgreichen oder fehlgeschlagenen Abschluss des Vorgangs anzeigen. Geleitet vom Befehl des Programmierers sortiert der Bediener die bearbeiteten Teile direkt vor Ort in „gut“ und „schlecht“. Bitte beachten Sie, dass es dem Bediener möglich ist, einen Fehler zu machen und das Teil in den falschen Behälter zu legen.
Am Endmontageort werden der Seriencode des Produkts und der Speicherblock gescannt. Wenn ein Teil den Programmierer nicht passiert, erscheint auf dem Bildschirm des Bedieners eine Fehlermeldung auf rotem Hintergrund, die Sie auffordert, das Teil auszutauschen. Die Verbindung zweier Maschinen mit einer Datenbank dient als System, um zu verhindern, dass minderwertige Teile in das Produkt gelangen.
Leider ist Poka Yoke nur eine Qualitätssicherungsphilosophie und beinhaltet keine praktische Empfehlungen um bestimmte Prozesse zu verbessern. Dennoch werden wir versuchen, die grundlegenden Postulate und Prinzipien der Umsetzung dieser Technik zu formulieren.
Die Anwendung des Ansatzes kann in mehrere Phasen unterteilt werden:
- Festlegung der Prioritäten von Problemen – diese Phase ist der bedingte Beginn des Prozesses. In dieser Phase geht es darum, alle bestehenden Probleme zu ordnen und die Bemühungen auf die am häufigsten auftretenden Probleme zu lenken.
- Analyse durchführen – so schnell wie möglich bedeutendes Problem, sollten die Ursachen ihres Auftretens herausgefunden werden. Beim Poka-Yoke-Ansatz werden Änderungen vorgenommen, die den Fehler vollständig beseitigen. Die Umsetzung eines solchen Vorgehens ist nur bei der Bekämpfung der Fehlerursachen möglich. Demnach gilt das Prinzip des Fehlerschutzes nur dann, wenn die Bemühungen darauf abzielen, den Fehler/die Ursache zu verhindern, und nicht den Mangel – die Folge des Fehlers.
- Umsetzung von Änderungen – es ist äußerst schwierig, die kreative Phase des Prozesses zu beschreiben, aber es ist sehr wichtig, ein Merkmal dieser Phase zu beachten: die Einbindung der Mitarbeiter. Wie bei vielen anderen Qualitätssicherungsansätzen „japanischen Stils“ ist der entscheidende Erfolgsfaktor die aktive Einbindung des Personals in den Prozess der kontinuierlichen Verbesserung. Daher spielen in dieser Phase die Mitarbeiter, die direkt an diesem bestimmten Vorgang beteiligt sind, die Hauptrolle. Dieser Ansatz hat zwei unbestreitbare Vorteile: Erstens kennt nur der Bediener alle Feinheiten der Arbeit an einem bestimmten Arbeitsplatz, zweitens ist die Umsetzung von Änderungen durch die direkte Beteiligung der Arbeitnehmer viel einfacher und schneller.
Es gibt drei Hauptwege (oder Richtungen) zur Einführung von Veränderungen:
- Den Prozess so verändern, dass die fehlerhafte Probe vom Bediener eindeutig bemerkt wird. Ein Beispiel ist eine Checkliste, die der Betreiber für jedes Produkt ausfüllt. Dieses Beispiel Sehr effektiv beim Zusammenbau komplexer Produkte durch eine Person, insbesondere von Formen, sowie in Verpackungslinien für Produkte wie Haushaltsgeräte.
- Schaffung von Bedingungen, unter denen ein fehlerhaftes Muster nicht zum nächsten Schritt des Prozesses gelangen kann, wie beispielsweise der oben beschriebene Fall bei der Erstellung einer gemeinsamen Datenbank für den Programmierer und die Teilescanstation.
- Einen Prozess schaffen, bei dem Fehler ausgeschlossen sind. Ein hervorragendes Beispiel ist oben für die Montage von Autoscheinwerfern beschrieben – Kratzer auf den Linsen falsch montierter Scheinwerfer können einfach nicht auftreten. Ein solcher Scheinwerfer wird den potenziellen Gefahrenbereich nicht betreten können.
Es gibt viele Anwendungsbereiche des Prinzips des Fehlerschutzes, konzentrieren wir uns auf einen davon – die menschliche Sicherheit. IN moderne Gesellschaft Wir nutzen viele Geräte und Geräte, die uns beim Arbeiten oder Entspannen helfen. Der Nutzen all dieser Gegenstände grenzt an die enorme Gefahr, die sie für das Leben und die Gesundheit des Benutzers darstellen können. Nachfolgend finden Sie Beispiele dafür, wie der Poka-Yoke-Ansatz umgesetzt wurde, um die Sicherheit menschlichen Lebens zu gewährleisten:
- Kindersicherung an Autotüren: Eine Tür mit dieser Option kann nicht von innen geöffnet werden.
- Doppelverschlüsse auf Tablettenfläschchen und Haushaltschemikalien verhindern versehentliches Öffnen und Zugriff durch Kinder.
- Flammensensoren in der Nähe Gasbrenner Küchenherde: Wenn die Flamme im Brenner erlischt, wird die Gaszufuhr automatisch unterbrochen.
- Der Mikrowellenherd stoppt automatisch, wenn die Tür geöffnet wird. Dies verhindert die Belastung durch schädliche Wellen und die Möglichkeit einer Schädigung der Gliedmaßen.
- Manuelles Drücken mit zwei Tasten: Der Bediener muss beide Hände verwenden, um zwei Tasten zu drücken. Dadurch ist eine Gesundheitsschädigung des Bedieners ausgeschlossen.
- Zusätzliche Komponenten auf Leiterplatten, empfindlich gegenüber Entladungen: Wenn eine Ladung auf dem Gehäuse oder einer anderen Oberfläche auftritt, brennt die Komponente durch, wodurch verhindert wird, dass der Benutzer einen elektrischen Schlag erhält.
- Ein hervorragendes Beispiel für die Umsetzung des Prinzips zeigt das Video: Eine Kreiselsäge stoppt bei der geringsten Berührung mit den Fingern einer Person.
Die Philosophie des Qualitätsmanagements, die auf der Eliminierung von Fehlermöglichkeiten im System basiert, zielt nicht nur darauf ab, die Fehlerhaftigkeit des Prozesses zu reduzieren, sondern auch Lösungen zu finden, die keine nennenswerten Kosten verursachen. Diese Funktion unterscheidet Poka Yoke von anderen Methoden zur Prozessverbesserung. Die Methodik zur Anwendung des Ansatzes ist nicht auf einen bestimmten Satz von Werkzeugen oder Methoden beschränkt, was ihn universell und leicht auf jeden Bereich menschlicher Tätigkeit anwendbar macht.