CNC-Holzfräsmaschine zum Selbermachen. Welche Arten von selbstgebauten Maschinen und Geräten gibt es? Do-it-yourself-Produktion für eine Heimwerkstatt. Abmessungen einer CNC-Maschine mit eigenen Händen
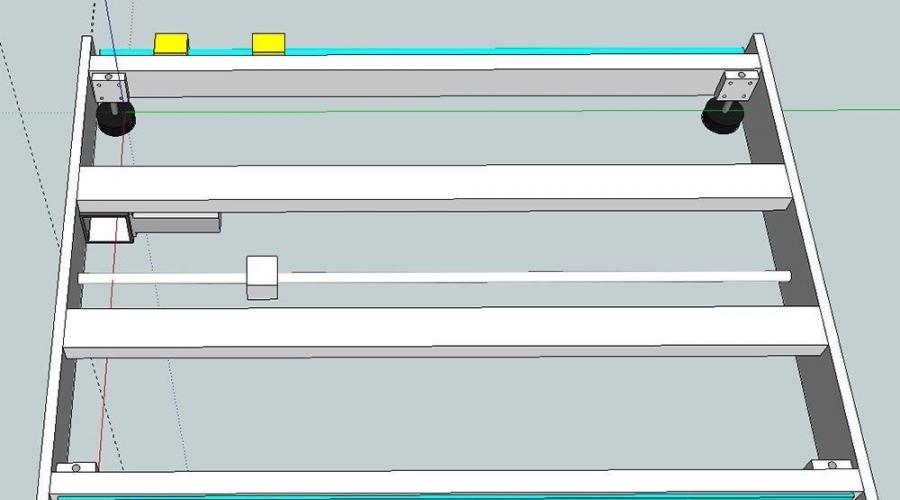
Lesen Sie auch
Er beschrieb ausführlich den gesamten Prozess der Entwicklung einer CNC-Maschine zur Bearbeitung von Holz und anderen Materialien, beginnend mit dem Design.
1. Design
Bevor Sie eine Maschine bauen, müssen Sie zumindest eine Skizze von Hand zeichnen oder noch besser, eine genauere dreidimensionale Zeichnung mit einem CAD-Programm anfertigen. Der Autor des Projekts verwendete Google Sketchup, ein recht einfaches Programm (kostenlos für 30 Tage). Für ein komplexeres Projekt können Sie Autocad wählen.
Der Hauptzweck der Zeichnung besteht darin, dies herauszufinden erforderliche Abmessungen Ersatzteile, bestellen Sie diese online und stellen Sie sicher, dass alle beweglichen Teile der Maschine zusammenpassen.
Wie Sie sehen können, verwendete der Autor keine detaillierten Zeichnungen mit markierten Löchern für die Befestigung; er markierte die Löcher während des Baus der Maschine, aber dieser ursprüngliche Entwurf erwies sich als ausreichend.
Gesamtabmessungen der Maschine: 1050 x 840 x 400 mm.
Achsenweg: X 730 mm, Y 650 mm, Z 150 mm
Die Länge der Führungen und der Kugelumlaufspindel hängt von der Größe der gewünschten Maschine ab.
Bei der Konstruktion einer CNC-Maschine stellen sich mehrere Fragen, deren Antwort vom Endergebnis abhängt.
Für welchen CNC-Maschinentyp möchten Sie sich entscheiden?
Mit beweglichem Tisch oder mit beweglichem Portal? Bei Werkzeugmaschinen werden häufig bewegliche Tischkonstruktionen eingesetzt kleine Größe, bis zu 30x30 cm. Sie sind einfacher zu bauen und können steifer gemacht werden als Maschinen mit beweglichem Portal. Der Nachteil des Verschiebens des Tisches besteht darin, dass bei gleicher Schnittfläche die Gesamtfläche der Maschine doppelt so groß ist wie bei einer Ausführung mit beweglichem Portal. Bei diesem Projekt beträgt die Bearbeitungsfläche ca. 65x65 cm, daher wurde ein bewegliches Portal gewählt.
Was möchten Sie mit einer CNC-Maschine bearbeiten?
In diesem Projekt war die Maschine hauptsächlich für Sperrholz vorgesehen, Hartholz Holz und Kunststoffe sowie für Aluminium.
Woraus wird die Maschine gebaut?
Dies hängt hauptsächlich vom Material ab, das auf der Maschine verarbeitet wird. Idealerweise sollte das Material, aus dem die Maschine hergestellt wurde, sein stärker als das Material, die maschinell verarbeitet werden oder zumindest nicht weniger haltbar sind. Wenn Sie Aluminium schneiden möchten, muss die Maschine daher aus Aluminium oder Stahl zusammengebaut werden.
Welche Achslänge benötigen Sie?
Nach dem ursprünglichen Plan sollte die CNC-Maschine Sperrholz und MDF verarbeiten, die in den Niederlanden in den Abmessungen 62 x 121 cm hergestellt werden. Daher muss für Y der Durchgangsabstand mindestens 620 mm betragen. Die Hublänge entlang der X-Achse beträgt 730 mm, da die Maschine sonst den gesamten Raum einnehmen würde. Daher ist die X-Achse kürzer als die Länge der Sperrholzplatte (1210 mm), aber es ist möglich, die Hälfte zu bearbeiten, dann die Platte nach vorne zu bewegen und den Rest zu bearbeiten. Mit diesem Trick ist es möglich, Teile auf der Maschine zu bearbeiten, die deutlich größer sind als die Länge der X-Achse. Für die Z-Achse wurden 150 mm gewählt, um künftig eine vierte Achse nutzen zu können.
Welche Art von linearer Bewegung werden Sie verwenden?
Es gibt viele Optionen für ein Linearbewegungssystem und die Qualität der Arbeit hängt weitgehend von seiner Wahl ab. Daher ist es sinnvoll, in das beste System zu investieren, das Sie sich leisten können. Der Autor des Projekts entschied, dass lineare Schienen die beste Option seien, für die er genug Geld habe. Wenn Sie eine 3-Achsen-CNC-Fräse bauen, müssen Sie einen Bausatz kaufen, der aus drei Sätzen Linearführungen und zwei Linearlagern pro Führung besteht.
Welches Vorschubantriebssystem werden Sie für jede Achse verwenden?
Die wichtigsten Optionen für den Vorschubantrieb sind: Zahnriemen, Zahnstangengetriebe und Spindel-Mutter-Übertragung. Bei selbstgebauten CNC-Maschinen wird am häufigsten ein Schrauben-Mutter-Getriebe mit Kugelumlaufspindel verwendet. Die Mutter wird am beweglichen Teil der Maschine befestigt, die Schraube ist an beiden Enden befestigt. Die Schraube ist am Motor befestigt. Wenn sich die Motoren drehen, bewegt sich die Mutter mit dem daran befestigten beweglichen Maschinenteil entlang der Spindel und setzt die Maschine in Bewegung.
Die Kugelumlaufspindel dieser Maschine dient zum Antrieb der X- und Y-Achsen. Kugelumlaufspindellager sorgen für einen sehr ruhigen Lauf, es gibt kein Spiel und die Schnittqualität und -geschwindigkeit steigt.
Die Z-Achse verwendet eine hochwertige M10-Stange aus Edelstahl mit einer selbstgebauten Delrin-Mutter.
Motor- und Steuerungstyp
Typischerweise verwenden selbstgebaute CNC-Maschinen Schrittmotoren. Servoantriebe werden hauptsächlich für industrielle CNC-Maschinen mit hoher Leistung eingesetzt, sie sind teurer und erfordern teurere Steuerungen. Hier kommen 3Nm Schrittmotoren zum Einsatz.
Spindeltyp
Das Projekt verwendet einen Standard-Kress und verfügt über einen guten 43-mm-Klemmflansch sowie einen eingebauten Geschwindigkeitsregler (die meisten Spindeln verfügen jedoch über letzteres).
Wenn Sie wirklich komplexe Schnitte durchführen möchten, sollten Sie auf wassergekühlte Spindeln achten – sie sind teurer als Standardspindeln, machen aber viel weniger Lärm, können bei niedrigen Drehzahlen ohne Überhitzung und mit einer Vielzahl von Materialien arbeiten.
Kosten
Diese CNC-Maschine kostete ca. 1.500 Euro. Eine vorgefertigte CNC-Fräsmaschine mit ähnlichen Spezifikationen kostet viel mehr, Sie können also Geld sparen, indem Sie die Maschine selbst bauen.
2. Komponenten zum Erstellen einer CNC-Maschine
Elektrische Ausrüstung und Elektronik:
- 3 Schrittmotoren 3 Nm Nema 23;
- 3 Schrittmotortreiber DM556 Leadshine;
- 36-V-Stromversorgung für CNC-Maschinen;
- Schnittstellenkarte 5-Achsen-CNC-Breakout-Board zur Steuerung von Schrittmotortreibern;
- 5V-Stromversorgung für Schnittstellenplatine;
- Ein-/Ausschalter mit zwei Positionen;
- Geschirmtes 4-adriges 18-AWG-Litzenkabel;
- 3 Touch-Endschalter;
- Spindel: Kress FME 800 (Bosch Colt oder Dewalt Compact Router funktionieren auch).
Auf Wunsch:
- Schrank/Gehäuse für elektrische Geräte;
- beweglicher Kabelkanal aus Kunststoff;
- 4-polige Kabelstecker.
Mechanische Teile:
- Linearführungen: für X - SBR 20 für Y und Z - SBR 16;
- Kugelumlaufspindel für X und Y – 16 mm Durchmesser, 5 mm Steigung4
- als Übertragungsschraube für die Z-Achse: Stahlstift mit M10-Gewinde mit selbstgebauter Delrin-Mutter;
- Aluminiumprofil: 30x60 mm, in 100 mm lange Stücke geschnitten;
- Aluminiumplatte 15 mm dick;
- Leistungsstarke Anti-Vibrations-Nivellierfüße.
Programme:
- CAD/CAM-Programm CamBam;
- Programm zur Steuerung einer CNC-Maschine Mach3
Die Maschine besteht hauptsächlich aus 15 mm dicken Aluminiumplatten und 30 x 60 mm großen Aluminiumprofilen. Die Arbeiten wurden mit Bohr- und Drehmaschinen durchgeführt. Platten und Profile wurden auf Maß zugeschnitten bestellt.
3. X-Achse
Das Grundgestell besteht aus 4 Teilen Aluminiumprofil Querschnitt 30x60 mm und zwei Seitenwände 15 mm dick. Am Ende der Profile befinden sich zwei Löcher mit einem Durchmesser von 6,8 mm, in die Löcher wird mit einem Gewindebohrer ein M8-Gewinde eingebracht.
Gewindeschneiden an den Enden von Aluminiumprofilen
Um sicherzustellen, dass die Löcher der Endplatten übereinstimmen, wurden beim Bohren beide Platten zusammengeklemmt. In der Mitte jeder Platte sind 4 Löcher gebohrt, um die Lagerstützen zu installieren, und in einer der Seitenplatten sind vier zusätzliche Löcher zur Montage des Motors angebracht.
Zur Befestigung der Nivellierfüße wurden vier Blöcke aus Aluminiumstücken (50x50x20) angefertigt. Die Blöcke werden mit vier M5-Schrauben mit Möbel-Nutensteinen an den Außenprofilen verschraubt.
Linearführungen passen direkt auf Aluminiumprofile. Für die X-Achse wurden Schienen mit einem Durchmesser von 20 mm verwendet. Vorgebohrte Löcher in der Basis der Linearführungen passen genau zu den Nuten in den Aluminiumprofilen. Zur Montage wurden M5-Schrauben und Möbel-Nutensteine verwendet.
4. Portalseitenplatten
Die Seitenplatten des Portals sind nahezu identisch, in einer davon sind jedoch zusätzlich vier Löcher zur Montage des Motors gebohrt. Das gesamte Portal besteht aus 15 mm starken Aluminiumplatten. Um sicherzustellen, dass die Löcher genau an der richtigen Stelle waren, wurden an sorgfältig markierten Stellen mit einem Tischlocher Aussparungen gestanzt und mit einer Bohrmaschine entlang dieser Markierungen zunächst mit einem Bohrer kleineren Durchmessers, dann mit dem erforderlichen Bohrer Löcher gebohrt .
Aufgrund der Konstruktionsweise des Portals mussten wir Löcher in die Enden der Seitenplatten bohren und M8-Gewinde in die Löcher bohren.
5. Portalmontage
Das Portal ist montiert und installiert
Der Rest des Portals wird in gleicher Weise wie die Seitenteile gefertigt. Der schwierigste Teil bestand darin, die linearen Schienen richtig auszurichten, die mit der Kante der Platte übereinstimmen mussten. Beim Markieren der genauen Position der Löcher habe ich zwei Aluminiumprofile gegen die Seiten der Platte gedrückt, um die Führungen auszurichten. IN gebohrte Löcher M5-Gewindeschnitt. Bei der Befestigung der Führungen am Portal ist darauf zu achten, dass der Abstand zwischen den Führungen über die gesamte Länge gleich ist, die Führungen müssen parallel sein.
An der Seitenwand des Portals sind Linearlager angebracht.
Mehrere Eckwinkel sorgen für zusätzliche Steifigkeit der Struktur.
In die Platte an der Unterseite des Portals sind 6 Löcher gebohrt, um sie an den Seitenplatten zu befestigen. Ich musste in der Mitte zwei Löcher bohren, um den Mutternhalter zu befestigen.
6. Y-Achsen-Schlitten
Der Y-Achsen-Schlitten besteht aus einer einzigen Platte, an der Linearlager befestigt sind. Das Bohren der Löcher war recht einfach, erforderte jedoch große Präzision. An dieser Platte sind Lager für die Y-Achse und die Z-Achse befestigt. Da die Linearlager nahe beieinander liegen, können sie bereits bei der kleinsten Bewegung blockieren. Der Schlitten sollte leicht von einer Seite zur anderen gleiten können. Die Schienen und Lager müssen angepasst werden. Zur Ausrichtung kamen hochpräzise digitale Instrumente zum Einsatz. Nachdem die Antriebsmutterhalterung für die Y-Achse fertig war, mussten zur Befestigung zwei zusätzliche Löcher in die Platte gebohrt werden.
7. Z-Achse
Die Z-Achsen-Linearführungen (Schienen) werden am beweglichen Teil der Z-Achsen-Baugruppe befestigt. Die Schienen mussten einige Millimeter vom Rand der Platte versetzt werden. Um sie auszurichten, wurden zwei Kunststoffstücke der erforderlichen Dicke als Abstandshalter verwendet. Es war mit Sicherheit bekannt, dass die Kanten der Aluminiumplatte parallel waren, daher fügte der Autor Plastikstücke zwischen die an der Kante der Platte befestigten Aluminiumseiten und die Schienen ein, bewegte die Schienen auf den erforderlichen gleichen Abstand und markierte dann die Positionen der Löcher, bohrte sie und schnitt die Innengewinde.
Um die obere Platte an der Z-Achsen-Baugruppe zu befestigen, werden drei Löcher in das Ende der Montageplatte gebohrt. Es war nicht möglich, den Schrittmotor direkt auf der Platte zu befestigen, daher musste ich eine separate Halterung für den Motor aus Kunststoff anfertigen (siehe Punkt 12).
Zwei Lagergehäuseblöcke bestehen aus dem gleichen Kunststoff. Die Antriebsschraube ist eine Stahlstange mit einem M10-Gewinde. Die Zahnriemenscheibe wird gebohrt, mit einem M10-Gewinde versehen und einfach oben an der Antriebsschraube verschraubt. Die Befestigung erfolgt durch drei Stellschrauben. Die Delrin-Antriebsmutter wird am Y-Achsen-Schlitten befestigt.
Die Delrin-Antriebsmutter wird am Y-Achsen-Schlitten befestigt.
Die Spindelhalterung wurde vorbestellt und verfügt über einen 43-mm-Klemmring, der zu dem im Projekt verwendeten Kress passt.
Wenn Sie eine wassergekühlte Spindel verwenden möchten, liegt dieser häufig eine vorgefertigte Halterung bei. Sie können die Halterungen auch separat kaufen, wenn Sie einen Dewalt- oder Bosch-Lauf verwenden möchten, oder sie in 3D drucken.
8. Zahnriemen und Riemenscheiben
Oft werden die Motoren außen an der Maschine oder auf einem separaten Ständer montiert. In diesem Fall können die Motoren über eine flexible Kupplung direkt mit der Kugelumlaufspindel verbunden werden. Da sich die Maschine jedoch in einem kleinen Raum befindet, wären externe Motoren im Weg.
Aus diesem Grund sind die Motoren im Inneren des Autos untergebracht. Da es unmöglich war, die Motoren direkt mit den Kugelumlaufspindeln zu verbinden, mussten wir 9 mm breite HTD5m-Zahnriemen und Riemenscheiben verwenden.
Wenn Sie einen Riemenantrieb verwenden, können Sie den Motor über ein Untersetzungsgetriebe mit der Antriebsspindel verbinden. So können Sie kleinere Motoren verwenden und trotzdem das gleiche Drehmoment, aber eine geringere Drehzahl erzielen. Da die Motoren recht groß gewählt wurden, war es nicht nötig, die Gänge zu reduzieren, um mehr Leistung zu erhalten.
9. Motorlager
Die Motorhalterungen bestehen aus quadratischen Aluminiumrohrstücken, die individuell auf die erforderliche Länge zugeschnitten werden. Sie können auch ein Stahlrohr nehmen und quadratische Stücke daraus schneiden. Die Motorhalterungen für die X- und Y-Achse müssen aus- und einfahrbar sein, um die Zahnriemen zu spannen. Die Schlitze wurden auf einer Drehmaschine hergestellt und auf einer Seite der Halterung ein großes Loch gebohrt, Sie können dies aber auch auf einer Bohrmaschine tun.
Das große Loch auf einer Seite der Halterung wurde mit einer Endsäge ausgeschnitten. Dadurch sitzt der Motor bündig mit der Oberfläche ab und gewährleistet außerdem die Zentrierung der Welle. Der Motor wird mit M5-Schrauben befestigt. Auf der anderen Seite der Halterung befinden sich vier Schlitze, damit der Motor hin und her gleiten kann.
10. Lagerstützblöcke
Stützblöcke für die X- und Y-Achse bestehen aus 50-mm-Aluminiumstangen runder Abschnitt— Daraus wurden vier Stücke mit einer Dicke von jeweils 15 mm geschnitten. Nach dem Markieren und Bohren der vier Befestigungslöcher wurde ein großes Loch in die Mitte des Werkstücks gebohrt. Anschließend wurde ein Hohlraum für die Lager geschaffen. Die Lager sollten gedrückt und die Blöcke an den End- und Seitenplatten verschraubt werden.
11. Z-Achsen-Antriebsmutterhalterung
Anstelle einer Kugelumlaufspindel für die Z-Achse wurde eine M10-Gewindestange und eine selbstgemachte Mutter aus einem Stück Delrin verwendet. Delrin-Polyformaldehyd ist für diesen Zweck gut geeignet, da es selbstschmierend ist und sich mit der Zeit nicht abnutzt. Wenn Sie zum Gewindeschneiden einen Gewindebohrer guter Qualität verwenden, ist das Spiel minimal.
12. Halterungen für Antriebsmuttern auf der X- und Y-Achse
Die Antriebshalterung für die X- und Y-Achse besteht aus Aluminium. Kugelumlaufmuttern haben zwei kleine Flansche mit drei Löchern auf jeder Seite. Ein Loch auf jeder Seite dient zur Befestigung der Mutter am Halter. Der Halter wird mit großer Präzision auf einer Drehmaschine bearbeitet. Nachdem Sie die Muttern am Portal und am Y-Achsen-Schlitten befestigt haben, können Sie versuchen, diese Teile von einer Seite zur anderen zu bewegen, indem Sie die Kugelumlaufspindel von Hand drehen. Bei falschen Abmessungen der Halter kommt es zum Verklemmen der Mutter.
Y-Achsen-Montage.
13. Z-Achsen-Motorhalterung
Die Z-Achsen-Motorhalterung unterscheidet sich von den anderen. Es ist aus 12 mm dickem Acryl geschnitten. Die Riemenspannung kann durch Lösen der beiden Schrauben oben und Verschieben der gesamten Motorhalterung eingestellt werden. Im Moment funktioniert die Acrylhalterung super, aber in Zukunft denke ich darüber nach, sie durch eine Aluminiumhalterung zu ersetzen, da sich die Acrylplatte beim Spannen des Riemens leicht verbiegt.
14. Arbeitsfläche
Am besten wäre ein Aluminiumtisch mit T-Nuten, der aber teuer ist. Der Autor des Projekts hat sich für eine perforierte Tischplatte entschieden, weil diese ins Budget passt und viele Möglichkeiten zum Aufspannen des Werkstücks bietet.
Der Tisch besteht aus einem Stück 18 mm starkem Birkensperrholz und wird mit M5-Schrauben und T-Nutensteinen an Aluminiumprofilen befestigt. Es wurden 150 Sechskantmuttern M8 gekauft. Für diese Muttern wurde mit einem CAD-Programm ein Netz mit sechseckigen Ausschnitten gezeichnet. Die CNC-Maschine schneidet dann alle diese Löcher für die Muttern.
Auf einem Stück Birkensperrholz wurde ein 25 mm dickes Stück MDF montiert. Dies ist eine austauschbare Oberfläche. Mit einem großen Fräser wurden die Löcher in beide Teile geschnitten. Die Löcher im MDF sind genau auf die Mitte der zuvor geschnittenen sechseckigen Löcher ausgerichtet. Anschließend wurde das MDF-Stück entfernt und alle Muttern in die Löcher im Sperrholz eingebaut. Die Löcher waren etwas kleiner als die Muttern, daher wurden die Muttern mit einem Hammer hineingetrieben. Nach der Fertigstellung kehrte das MDF an seinen Platz zurück.
Die Tischoberfläche verläuft parallel zur X- und Y-Achse und ist völlig eben.
15. Elektronik
Folgende Komponenten kommen zum Einsatz:
- Hauptnetzteil mit Ausgangsspannung 48 V DC und Ausgangsstrom 6,6 A;
- 3 Schrittmotortreiber Leadshine M542 V2.0;
- 3 Schrittmotoren 3Nm Hybrid Nema 23;
- Schnittstellenkarte;
- Relais – 4–32 V Gleichstrom, 25 A/230 V Wechselstrom;
- Hauptschalter;
- Stromversorgung für Schnittstellenplatine 5V DC;
- Netzteil für Kühlventilatoren 12V DC;
- 2 Cooler Master Sleeve Bearing 80-mm-Lüfter;
- 2 Steckdosen – für Spindel und Staubsauger;
- Not-Aus-Taster und Endschalter (noch nicht verbaut).
Wenn Sie nicht viel Geld für den Einzelkauf der Ausrüstung ausgeben möchten, können Sie diese auch im Set kaufen. Vor der Bestellung sollten Sie sich überlegen, welche Schrittmotorgröße Sie benötigen. Wenn Sie eine kleine Maschine zum Schneiden von Holz und Kunststoff bauen, liefern Nema 23-Schrittmotoren mit 1,9 Nm ausreichend Leistung. Hier wurden 3-Nm-Motoren gewählt, da die Maschine selbst recht groß und schwer ist und auch Materialien wie Aluminium verarbeitet werden sollten.
Für kleine Motoren können Sie eine Platine für drei Motoren kaufen, besser ist es jedoch, separate Treiber zu verwenden. Die kundenspezifischen Treiber von Leadshine verfügen über einen Mikroschrittmodus für maximale Laufruhe und reduzierte Schrittmotorvibrationen. Die Treiber in diesem Design können maximal 4,2 A und bis zu 125 Mikroschritte verarbeiten.
An den Hauptstromeingang ist eine 5-V-Gleichspannungsquelle angeschlossen. Die Ventilatoren verfügen über eine Steckdose im Inneren des Gehäuses, daher wird für die Stromversorgung ein handelsüblicher 12-Volt-Wandadapter verwendet. Der Hauptstrom wird mit einem großen Schalter ein- und ausgeschaltet.
Das 25A-Relais wird von einem Computer über einen Leistungsschalter gesteuert. Die Eingangsklemmen des Relais sind mit den Ausgangsklemmen des Leistungsschalters verbunden. Das Relais ist mit zwei verbunden Steckdosen, die den Kress und den Staubsauger antreiben, um die Späne aufzusaugen. Wenn der G-Code mit dem Befehl M05 endet, werden sowohl der Staubsauger als auch die Spindel automatisch ausgeschaltet. Um sie zu aktivieren, können Sie F5 drücken oder den G-Code-Befehl M03 verwenden.
16. Elektronikschrank
Elektrische Geräte brauchen einen guten Schrank. Der Autor hat die ungefähren Abmessungen und Positionen aller Komponenten auf ein Blatt Papier gezeichnet und versucht, sie so anzuordnen, dass alle Anschlüsse beim Anschließen der Drähte leicht erreichbar sind. Wichtig ist auch, dass eine ausreichende Luftzirkulation durch das Gehäuse gewährleistet ist, da Schrittmotorsteuerungen sehr heiß werden können.
Laut Plan sollten alle Kabel an der Rückseite des Gehäuses angeschlossen werden. Es wurden spezielle 4-Draht-Stecker verwendet, um die Trennung der Elektronik von der Maschine zu ermöglichen, ohne die Kabelklemmen zu lösen. Für die Stromversorgung der Spindel und des Staubsaugers wurden zwei Steckdosen bereitgestellt. Steckdosen sind mit Relais verbunden, um die Spindel basierend auf Mach3-Befehlen automatisch ein- und auszuschalten. An der Vorderseite des Schranks hätte ein großer Schalter sein sollen.
Teile für den Schrank werden auf der CNC-Maschine selbst geschnitten
Als nächstes wurden nach der groben Auslegung der Teile die Karosserieteile in einem CAD-Programm entworfen. Anschließend werden an der bereits montierten Maschine selbst alle Seiten und der Boden ausgeschnitten. Oben auf dem Schrank befindet sich ein Deckel, in der Mitte befindet sich ein Stück Plexiglas. Nach der Montage wurden alle Komponenten im Inneren verbaut.
17. Software
Mach3
Für den Betrieb einer CNC-Maschine sind drei Arten von Software erforderlich.
- CAD-Programm zum Erstellen von Zeichnungen.
- CAM-Programm zum Erstellen von Werkzeugwegen und G-Code-Ausgabe.
- Und ein Steuerungsprogramm, das den G-Code liest und den Router steuert.
Dieses Projekt verwendet ein einfaches Programm namens CamBam. Es verfügt über grundlegende CAD-Funktionen und ist für die meisten DIY-Projekte geeignet. Gleichzeitig handelt es sich um ein CAM-Programm. Bevor CamBam Flugbahnen erstellen kann, müssen Sie mehrere Parameter festlegen. Beispiele für Parameter: Durchmesser des verwendeten Werkzeugs, Schnitttiefe, Tiefe pro Durchgang, Schnittgeschwindigkeit usw. Sobald der Werkzeugweg erstellt ist, können Sie einen G-Code ausgeben, der der Maschine mitteilt, was zu tun ist.
Zeichnung erstellt in CamBam
Die Controller-Software verwendet Mach3. Mach3 überträgt Signale über den Parallelport des Computers an die Schnittstellenkarte. Mach3-Befehle stellen das Schneidwerkzeug auf Null und starten Schneidprogramme. Sie können damit auch die Spindeldrehzahl und die Schnittgeschwindigkeit steuern. Mach3 verfügt über mehrere integrierte Assistenten, mit denen Sie einfache G-Code-Dateien ausgeben können.
Von CamBam erstellter Werkzeugweg
18. Benutzung der Maschine
Als erstes wurden mehrere Klammern zur Befestigung der zu bearbeitenden Materialien auf dem Arbeitstisch hergestellt. Und das erste „große“ Projekt war ein Elektronikschrank (Punkt 15).
Als erstes wurden mehrere Proben angefertigt verschiedene Arten Zahnräder, Schachteln für Gitarrenplektren.
Staubfänger
Es stellte sich heraus, dass die CNC-Maschine viel Staub produziert und sehr laut ist. Um das Staubproblem zu lösen, wird ein Staubsammler hergestellt, an den ein Staubsauger angeschlossen werden kann.
3-Achsen-CNC-Fräser
Benutzermaschine SörenS7.
Ohne eine CNC-Fräse bleiben viele Projekte unrealisiert. Der Autor kam zu dem Schluss, dass alle Maschinen, die billiger als 2000 Euro sind, nicht die von ihm benötigte Größe der Arbeitsfläche und Genauigkeit bieten können.
Was war erforderlich:
- Arbeitsbereich 900 x 400 x 120 mm;
- relativ leise Spindel, die eine hohe Leistung bei niedrigen Drehzahlen garantiert;
- möglichst hohe Härte (zur Verarbeitung). Aluminiumteile);
- hohe Genauigkeit;
- USB-Schnittstelle;
- kosten weniger als 2000 Euro.
Diese Anforderungen wurden bei der dreidimensionalen Gestaltung berücksichtigt. Das Hauptaugenmerk lag darauf, sicherzustellen, dass alle Teile zusammenpassen.
Daher wurde die Entscheidung getroffen, eine Oberfräse mit einem Aluminium-Strangpressrahmen, 15-mm-Kugelumlaufspindeln und NEMA 23-Schrittmotoren mit einer Nennleistung von 3 A zu bauen, die perfekt in das handelsübliche Montagesystem passt.
Alle Teile passen perfekt, eine Anfertigung zusätzlicher Sonderteile ist nicht erforderlich.
1. Rahmenherstellung
Die X-Achse war in wenigen Minuten zusammengebaut.
Die Linearführungen der HRC-Serie sind von sehr hoher Qualität und sofort nach der Installation ist klar, dass sie einwandfrei funktionieren.
Dann trat das erste Problem auf: Die Antriebsschrauben passten nicht in die Lageraufnahmen. Daher wurde beschlossen, die Propeller mit Trockeneis zu kühlen, um die Größe zu reduzieren.
2. Einbau der Antriebsschrauben
Nachdem die Enden der Schrauben mit Eis gekühlt wurden, passen sie perfekt in die Halterungen.
3: Elektrisch
Der Zusammenbau des mechanischen Teils ist abgeschlossen, jetzt sind die elektrischen Komponenten dran.
Da der Autor Arduino gut kannte und die volle Kontrolle über USB ermöglichen wollte, fiel die Wahl auf Arduino Uno mit CNC Shield-Erweiterungsplatine und DRV8825-Schrittmotortreibern. Die Installation war überhaupt nicht schwierig und nach der Einstellung der Parameter begann die Steuerung der Maschine über einen PC.
Da der DRV8825 jedoch hauptsächlich mit 1,9 A und 36 V arbeitet (und sehr heiß wird), überspringt er einen Schritt, da dies auch der Fall ist geringer Strom. Langfristiges Mahlen bei hohen Temperaturen würde kaum gelingen.
Als nächstes wurden die günstigen Tb6560-Treiber an die Erweiterungsplatine angeschlossen. Die Nennspannung erwies sich für dieses Board als nicht sehr geeignet. Es wurde versucht, ein 36V-Netzteil zu verwenden.
Dadurch arbeiten zwei Treiber normal, der dritte hält der höheren Spannung jedoch nicht stand und dreht den Schrittmotorrotor nur in eine Richtung.
Ich musste den Treiber erneut wechseln.
Der tbV6600 hat gut funktioniert. Es ist fast vollständig von einem Aluminiumkühler umschlossen und lässt sich einfach aufstellen. Jetzt arbeiten die Schrittmotoren auf der X- und Y-Achse mit einem Strom von 2,2 A und auf der Z-Achse mit 2,7 A.
Es galt, die Stromversorgung der Schrittmotoren und des Frequenzumrichters vor kleinen Aluminiumspänen zu schützen. Es gibt viele Lösungen, wenn der Konverter weit von der Fräsmaschine entfernt platziert ist. Das Hauptproblem besteht darin, dass diese Geräte viel Wärme erzeugen und benötigen aktive Kühlung. Es wurde eine originelle Lösung gefunden: Die Verwendung von 30 cm langen Strumpfhosen als Schutzhülle ist günstig und praktisch und sorgt für ausreichend Luftzirkulation.
4. Spindel
Die Wahl der richtigen Spindel ist nicht einfach. Die erste Idee war, eine Standard-Kress1050-Spindel zu verwenden, aber diese hat nur 1050 Watt bei 21.000 U/min, sodass ich bei niedrigeren Drehzahlen nicht viel Leistung erwarten konnte.
Zum Trockenfräsen von Aluminium- und Stahlteilen sind 6000-12000 U/min erforderlich. Gekauft wurde eine Drei-Kilowatt-VFD-Spindel mit Wechselrichter, die bei Lieferung aus China 335 Euro kostete.
Dies ist eine ziemlich leistungsstarke Spindel und einfach zu installieren. Es ist schwer – es wiegt 9 kg, aber der starke Rahmen hält seinem Gewicht stand.
5. Der Zusammenbau ist abgeschlossen
Die Maschine macht ihren Job gut, ich musste an den Schrittmotortreibern herumbasteln, aber insgesamt ist das Ergebnis zufriedenstellend. 1.500 Euro wurden ausgegeben und eine Maschine gebaut, die genau den Bedürfnissen des Erstellers entspricht.
Das erste Fräsprojekt war ein geformter Aussparungsschnitt in POM.
6: Modifikation zum Aluminiumfräsen
Schon bei der Verarbeitung von POM stellte sich heraus, dass das Drehmoment am Y-Support zu hoch war und sich die Maschine bei hohen Belastungen entlang der Y-Achse durchbiegte, sodass der Autor eine zweite Führung anschaffte und das Portal entsprechend rüstete.
Danach normalisierte sich alles wieder. Der Umbau kostete 120 Euro.
Jetzt können Sie auch Aluminium fräsen. Die AlMg4,5Mn-Legierung lieferte ohne Kühlung sehr gute Ergebnisse.
7. Schlussfolgerung
Um Ihre eigene CNC-Maschine zu bauen, müssen Sie kein Genie sein, alles liegt in unseren Händen.
Wenn alles gut geplant ist, ist es nicht notwendig, jede Menge Ausrüstung und Ausrüstung zu haben ideale Bedingungen Zum Arbeiten benötigen Sie lediglich etwas Geld, einen Schraubenzieher, einen Griff und eine Bohrmaschine.
Ein Monat wurde für die Entwicklung des Entwurfs mithilfe eines CAD-Programms sowie für die Bestellung und den Kauf von Komponenten aufgewendet, vier Monate für die Montage. Der Bau der zweiten Maschine hätte viel weniger Zeit in Anspruch genommen, da der Autor keine Erfahrung mit Werkzeugmaschinen hatte und viel über Mechanik und Elektronik lernen musste.
8. Zubehör
Elektrisch:
Alle elektrischen Teile wurden bei eBay gekauft.
- Arduino GRBL + CNC Shield: ca. 20 Euro
- Schrittmotortreiber: 12 Euro pro Stück.
- Netzteil: 40 Euro
- Schrittmotoren: ca. 20 Euro pro Stück
- Spindel+Wechselrichter: 335 Euro
Mechanik:
Linearlager ARC 15 FN
Foto: www.dold-mechatronik.de
Linearführungen AR/HR 15 - ZUSCHNITT
Foto: www.dold-mechatronik.de
Kugelumlaufspindeln SFU1605-DM:
- 2x 1052mm
- 1x 600mm
- 1x 250mm
Foto: www.dold-mechatronik.de
Kugelumlaufspindellagerhalter FLB20-3200 inklusive NEMA23-Motorhalter:
Foto: www.dold-mechatronik.de
Kugelumlaufspindelunterstützung LLB20
Foto: www.dold-mechatronik.de
Schrittmotor-Spindel-Kupplungen: aus China für 2,5 Euro pro Stück.
Rahmen:
Basisprofile 160x16 I-Typ Nut 8
Foto: www.dold-mechatronik.de
Profile für X-Achse 30x60 B-Typ Nut 8
Foto: www.dold-mechatronik.de
Y-Achsen-Schrittmotor-Montageprofile 30x60 B-Typ-Mutter 8
Foto: www.dold-mechatronik.de
Portal:
Profil 30x60 B-Typ Mutter 8 für X-Achsen-Linearlager 100 mm
Rückplatte: 5 mm dicke Aluminiumplatte, 600 x 200.
Profil 30x60x60 B-Typ Mutter 8 für Y: 2 Stk.
Foto: www.dold-mechatronik.de
Profil 30x30 B-Typ Mutter 8
für Z:
Montageplatte – 5 mm dicke Aluminiumplatte, Abmessungen 250 x 160
Gleitplatte zur Spindelmontage - Aluminiumplatte 5 mm dick, Abmessungen 200x160
9. Programm
Nach langer Suche nach einer Softwarelösung fiel die Wahl auf das komfortable Programm Estlcam, dessen Lizenz 50 Euro kostet. Die Testversion des Programms verfügt über alle Funktionen der lizenzierten Version, arbeitet jedoch langsamer.
Diese Software ist in der Lage, Arduino neu zu programmieren und verfügt über viele Funktionen, einschließlich der Möglichkeit, Schrittmotoren direkt zu steuern.
Beispiel: Um nach der Kante eines Teils zu suchen, müssen Sie Drähte an die Kontakte des Arduino-Mikrocomputers und an das Werkstück anschließen. Wenn das Werkstück keinen Strom leitet, können Sie mit Folie eine temporäre leitfähige Beschichtung erzeugen.
Anschließend nähert sich das Programm dem Teil von verschiedenen Seiten und bestimmt dessen Grenzen im Moment des Kontakts.
10. Upgrade
An der Y- und Z-Achse wurden provisorische Kunststoffhalterungen angebracht. Der Kunststoff war stark genug, aber die Heftklammern konnten trotzdem brechen. Daher hat der Autor Aluminiumhalterungen zum Austausch gefräst. Das Ergebnis ist auf dem Foto zu sehen.
11. Maschine in Betrieb
Nach etwas Übung liefert die Maschine bereits sehr gute Ergebnisse für ein selbstgemachtes Produkt.
Diese Bilder zeigen ein Teil aus der AlMg4,5Mn-Legierung. Es ist komplett gefräst. Das zweite Foto zeigt das Ergebnis der Maschine, ohne weitere Bearbeitung mit anderen Mitteln.
Es wurde ein VHM 6 mm 3-schneidiger Schaftfräser verwendet. Beim Einsatz von 4- und 6-mm-Fräsern erzielt die Maschine recht ordentliche Ergebnisse. Für seine Ausstattungsklasse natürlich.
CNC-Tisch
Zum Nachtisch - keine Maschine, aber nützlich und interessantes hausgemachtes Produkt für die Maschine, nämlich ein langlebiger und geräumiger Rahmen mit Regalen. Wenn Sie noch keine CNC-Maschine besitzen, können Sie frühzeitig eine bauen und diese als Werkbank nutzen.
Evan und Caitlin, Websitebesitzer EvanAndKatelyn.com , haben ihren CNC-Maschinentisch aktualisiert, um ihm mehr Funktionalität und Platz zu verleihen.
Das Produkt wurde vollständig durch Schraubverbindungen und ohne Verwendung von Klebstoff zusammengebaut, um die Möglichkeit einer einfachen Änderung und Aufrüstung zu gewährleisten.
Verwendete Werkzeuge und Komponenten:
- Stopp-Taste;
- Rollenschloss;
- Senker und Bits;
- Bohren;
- Elektronischer Schraubenzieher;
- Gesehen;
- X-Carve-Maschine;
- Hartmetallbeschichteter Viertelzoll-Schaftfräser;
- Viertelzoll-Hartmetall-Kugelkopffräser mit 4 Schneiden;
- Gehörschutz.
Schritt 1: Vorbereitung
Schritt eins besteht darin, alles vom alten Tisch zu entfernen, angefangen bei der Maschine bis hin zu einer Menge anderer dort liegender Dinge, und ihn teilweise zu zerlegen. Bis auf zwei große Regale 120 x 120 cm, die verstärkt wurden und die Basis für einen neuen Tisch bildeten, wurde alles komplett abgebaut.
Schritt 2: Verstärken Sie die Regale
An den vier Innenecken wurden Eckwinkel und entlang des an der Unterseite verlaufenden Querträgers L-förmige Winkel verwendet.
Auf dem Foto unten: Vergleich eines verstärkten Regals mit einem unfertigen.
Schritt 3: Schneiden Sie den Überschuss ab
Ursprünglich gab es 4 Regale, die über die Tischplatte hinausragten, da über der Maschine ein zusätzlicher Regalboden vorgesehen war. Diese Idee wurde verworfen und beschlossen, zwei der vier Racks wegzulassen.
Sie wurden mit Eckwinkeln verstärkt.
Darauf platzierten sie ein Regal und verstärkten es mit noch mehr Halterungen.
Krafttest.
Schritt 4: Stecktafel – Symbolleiste
Das aktualisierte Möbelstück musste so viel Stauraum wie möglich bieten, und eines der Details, das seine Möglichkeiten erweiterte, war eine perforierte Platte, in deren Löchern Werkzeughalter befestigt sind. Die Ecken wurden mit einer Stichsäge an der Platte ausgeschnitten.
Schritt 5: Untere Regale
Für die Lagerung im unteren Teil war es notwendig, so viel Platz wie möglich zu lassen, weil... Hier werden Tischkreissäge und Trommelschleifer aufbewahrt. Außerdem wurde viel Platz für die Lagerung von Materialien benötigt, daher wurde beschlossen, ein Regal hinzuzufügen, es jedoch leicht herausnehmbar zu machen. Holzklötze und eine für die Beine vorbereitete Sperrholzplatte waren praktisch.
Die Beine wurden mit Eckwinkeln an der Sperrholzplatte befestigt, in die das entstandene Regal eingesetzt wurde Unterteil. Es lässt sich leicht entfernen, wenn erneut Stauraum in voller Höhe benötigt wird.
Schritt 6: Obere Regale
Das alte Bett hatte oben eine Ablage für den Computer, der die Maschine bediente, und für verschiedene Kleinigkeiten. Da noch Platz frei war, beschlossen sie, unter diesem Regal noch einen zu machen. Es half auch dabei, die Steckdosen und die Verkabelung der Maschine abzudecken.
Das obere Regal wurde auf die Enden der Regale aufgesetzt und verschraubt.
Im zweiten Regal haben wir mit einer Stichsäge die Ecken für die Beine ausgeschnitten.
Und sie haben es auch mit Ecken gesichert.
Schritt 7: Der letzte Schliff
Am Ende wurde ein Schild mit der Aufschrift „Ruf mich an“ aufgeschraubt, das später durch einen von Abonnenten auf YouTube erfundenen Namen ersetzt wird.
Schließlich wurde alles, was im Vorgänger enthalten war, wieder auf den Tisch gelegt.
Es gibt viele beeindruckende Projekte selbstgebauter Maschinen, oft verblüffen die Autoren mit ihrem Können und genialen Lösungen. Wie ein Hobby Selbstmontage Eine CNC-Maschine oder ein 3D-Drucker ist vielen anderen Hobbys überlegen – sowohl im Hinblick auf die Nützlichkeit des erzielten Ergebnisses, weil man auf der Maschine viele wunderbare Dinge tun kann, als auch im Hinblick auf die Vorteile des Prozesses selbst – das ist nicht nur der Fall spannend, aber auch Bildungsaktivität, was zur Entwicklung technischer Fähigkeiten beiträgt.
Wir listen keine einzelnen Modelle auf, da es viele davon gibt und für alle Zwecke, Aufgaben und vorhandenen Installations- und Betriebsbedingungen die Ausrüstung individuell ausgewählt werden muss, bei der Ihnen Spezialisten weiterhelfen. Kontaktiere uns!
Wir senden Ihnen das Material per E-Mail zu
Mit einer guten Ausstattung werden komplexe technologische Prozesse zugänglich. Spezialgeräte mit Elektroantrieb vereinfachen die Bearbeitung von Holzzuschnitten erheblich. Der Erwerb ist jedoch mit erheblichen Investitionen verbunden. Um dieses Problem erfolgreich zu lösen, sollten Sie die Materialien in diesem Artikel sorgfältig studieren. Hier sprechen wir darüber, wie Sie selbst funktionale Holzbearbeitungsmaschinen für Ihre Heimwerkstatt bauen können.
Einige Muster selbstgebauter Geräte sind in ihren Verbrauchereigenschaften nicht schlechter als Fabrikprodukte
Bevor wir uns direkt der technischen Ausstattung zuwenden, sind einige allgemeine Bemerkungen zu den entsprechenden Fachräumen zu machen:
- Praktisch ist es, wenn sich die Werkstatt in einem separaten Gebäude befindet. Dies setzt ausreichend Platz, das Fehlen unnötiger Sorgen und die Möglichkeit einer vollständigen Ausstattung mit anderen technischen Systemen voraus.
- Wenn das Zimmer in , oder ist Erdgeschoss, es muss gut vom Wohngebiet isoliert sein.
- Die Fläche einer Standardwerkstatt sollte nicht weniger als 6-7 Quadratmeter betragen. Höhe – ausreichend für freien Durchgang und maximale Höhe des angehobenen Werkzeugs (ab 2,5 m).
- Hier kommen hochwertige Lüftungs-, Heizungs- und Beleuchtungssysteme zum Einsatz. Jedes Engineering-System sollte separat betrachtet werden, um übermäßige Kosten im Betrieb zu vermeiden.
- Sie müssen sicherstellen, dass die elektrische Leistung für alle Holzbearbeitungsmaschinen in Ihrer Heimwerkstatt ausreicht.
Zu Ihrer Information! Wenn das Gerät über elektronische Komponenten verfügt, sind spezielle Schutzschalter im Stromkreis sinnvoll, um Schäden durch Überspannungen zu vermeiden. Schutzerdung. Es ist darauf zu achten, dass die Netzparameter den Eigenschaften der Leistungsteile entsprechen (220 V, einphasig; 380 V, dreiphasig).
Die Verwendung einer solchen Quelle verringert die Ermüdung und trägt zur Aufrechterhaltung einer guten Sehkraft bei. Es ist vorzuziehen, ein LED-Gerät zu installieren. Sie erwärmt die Umgebung nicht wie eine normale Glühlampe. Im Gegensatz zu seinem Gegenstück zur Gasentladung ist es schwierig, es durch mechanische Einwirkung zu beschädigen.
Holzbearbeitungsmaschinen für die Heimwerkstatt und Spezialgeräte: Grunddefinitionen, Fertigungstechnologien
- Jede Maschine ist für die Durchführung einer begrenzten Anzahl von Arbeitsvorgängen mit Werkstücken bestimmter Größen ausgelegt.
- In der Regel ist das Arbeiten mit Spezialgeräten komfortabler als mit Universalmodellen.
- Es ist einfacher, eine Holzbearbeitungsmaschine mit eigenen Händen herzustellen, wenn Sie zunächst eine genaue Liste der Anforderungen an ihre Eigenschaften erstellen. Übermäßige Leistung ist nicht erforderlich. Das erforderliche Drehmoment kann über ein Getriebe bereitgestellt werden.
- Auf die gleiche Weise wird durch den Einbau des entsprechenden Getriebemechanismus die Drehzahl der Arbeitswelle verändert. Für eine präzisere Bearbeitung ist eine stufenlose Anpassung sinnvoll diesen Parameter in einem breiten Spektrum.
- Um die Kosten zu senken, können Sie bei der Konstruktion einen elektrischen Bohrmotor mit defektem Gehäuse und andere Arbeitsteile defekter Geräte verwenden.
- Die komplexesten mechanischen und elektronischen Komponenten müssen separat erworben werden. Die Kosten für die Reproduktion einiger Technologien zu Hause übersteigen die Kosten für fertige Produkte.
- Die Lebensdauer elektrisch angetriebener Geräte erhöht sich, wenn diese vor Überlastungen geschützt werden. Insbesondere ist es sinnvoll, mit einem automatischen System ausgestattet zu sein, das den Strom abschaltet, wenn der Motor überhitzt.
Wichtig! Sicherheitsaspekte sollten nicht vernachlässigt werden. Die Antriebsscheiben sind mit Abdeckungen abgedeckt. Vor den Arbeitsgeräten sind Folien aus transparentem Kunststoff angebracht.
Für rationelle Nutzung Freiraum, Wand- und Deckenregale, Regale, Haken und spezielle Halter sind nützlich. Der genaue Installationsort der entsprechenden Geräte wird unter Berücksichtigung der Besonderheiten technologischer Prozesse, der Platzierung von Maschinen und Werkbänken ausgewählt.
Verwandter Artikel:
Unser Testbericht hilft Ihnen bei der Auswahl und Herstellung selbstgebauter Maschinen und Geräte für Ihre Heimwerkstatt sowie beim Verständnis der Technologie ihrer Herstellung.
Erstellen Sie eine Holzdrehmaschine für Ihre Heimwerkstatt
Technische Parameter der entsprechenden Produkte sowie Beschreibungen finden Sie im Internet.
Der Hauptteil ist das Bett (1). Weitere Teile des Produkts sind daran befestigt. Es gewährleistet nicht nur die Integrität des Power-Frames, sondern auch eine gute Stabilität auf der Oberfläche. Die Zimmereimaschine ist für die Bearbeitung relativ leichter Werkstücke konzipiert, daher kann dieser Teil aus Hartholz gefertigt werden.
Im Mittelteil befindet sich eine Stütze mit Ständer Handschneider(2). Stattdessen kann ein Halter zur starren Fixierung des Werkzeugs montiert werden. Das Werkstück wird zwischen Vorderteil (3) und Reitstock (4) befestigt. Es dreht sich mittels eines Elektromotors (6). Um das Drehmoment an der Achse zu verändern, werden bei dieser Konstruktion ein Riementrieb und eine Riemenscheibe (5) verwendet. Der Träger und der Reitstock bewegen sich horizontal entlang einer speziellen Welle (7), die im Inneren des Rahmens installiert ist.
Wichtig! Diese Zeichnungen können zur Herstellung einer Arbeitsmaschine verwendet werden. Man muss nur bedenken, dass hier alle Maße in Zoll angegeben sind.
Mit diesem Projekt können Sie mit Ihren eigenen Händen eine Holzdrehmaschine herstellen. Sie müssen es lediglich durch ein spezielles Gerät ergänzen, das darauf ausgelegt ist, stets identische Produkte herzustellen.
Um es an der richtigen Stelle zu befestigen, müssen Sie einen speziellen Ständer erstellen. IN in diesem Beispiel Es wurde 10 mm Sperrholz verwendet, aus dem eine Plattform mit den Maßen 480×180 mm ausgeschnitten wurde. Die angegebenen Abmessungen können unter Berücksichtigung realer Parameter geändert werden. Löcher in das Sperrholz werden so geschnitten, dass Befestigungsschrauben und Werkzeuge hindurchpassen können. Zur starren Befestigung werden Holzklötze mit Schrauben entlang der Kontur der Plattform befestigt.
Dieses Design besticht durch seine Einfachheit und Zugänglichkeit Komponenten, angemessene Kosten. Einige Nachteile sind jedoch zu beachten:
- Zum Bewegen des Fräsers müssen Sie zwei Hände benutzen. Dies ist notwendig, um ausreichend Kraft zu erzeugen und ein Verklemmen zu verhindern.
- Der minimale Radius, entlang dem Biegungen von Teilen erzeugt werden, wird durch den Durchmesser des Werkzeugs (Fräsers) begrenzt.
- Zur Bearbeitung von Werkstücken aus verschiedene Rassen Holz erfordert eine genaue Einstellung der Wellendrehzahl, in diesem Beispiel ist eine solche Möglichkeit jedoch nicht gegeben.
Dieses Beispiel verdeutlicht, dass selbst ein Design, das durch Zeit und praktische Erfahrung getestet wurde, durch sorgfältiges Studium der Ausrüstung und des technologischen Prozesses verbessert werden kann.
Selbstgebaute Holzdrehmaschine zum Selbermachen: Video mit Anweisungen und Kommentaren des Autors des Projekts
Wie man mit eigenen Händen eine preiswerte hausgemachte Holzdrehmaschine herstellt
Mit diesem DIY-Holzbearbeitungsset wird es nicht schwer sein, es selbst zu tun. Dieser Rahmen kann auf einem Holz- oder Metallsockel montiert werden. Die genauen Parameter des Spindelstocks werden unter Berücksichtigung der Abmessungen und Montageorte der Motorlager ausgewählt. Die Leistungsparameter des Elektromotors von . Für Schreinereigeräte dieser Art reicht eine Leistung von 250-300 kW aus, wenn diese über ein Getriebe (Riemenscheibe) auf die Welle übertragen wird.
Das letzte Beispiel muss genauer untersucht werden. Durch die Auswahl eines geeigneten Elektrowerkzeugs erhalten Sie die erforderliche Leistung und Drehzahl. Um das Werkstück sicher und schnell zu fixieren, ist ein handelsübliches Spannfutter sinnvoll. Moderne Technologien dieser Art bieten Schutz vor Überhitzung und dem Eindringen von Staub in das Gehäuse. Hier sind hochwertige Schalter und eine wirksame Isolierung verbaut. Allein diese Zeichnung reicht aus, um zu verstehen, wie man eine Drehmaschine selbst herstellt.
Herstellung von Fräsern für eine Holzdrehmaschine aus Abfallmaterialien
Geeignet sind Feilen, Sägen, Schraubenschlüssel und andere Produkte aus Werkzeugstahl. Es ist einfacher, quadratische Werkstücke (im Querschnitt) zu bearbeiten. Sie sollten darauf achten, dass keine Risse oder andere Mängel vorhanden sind, die die Festigkeit beeinträchtigen. Zur starren Fixierung der Fräser durch den Durchgang muss die Maschine mit einer speziellen Halterung ausgestattet sein.
Wichtige Komponenten für eine DIY-Stationärkreissäge
Bei diesem Gerät werden die wichtigsten Funktionen vom Tisch ausgeführt, daher müssen seine Parameter untersucht werden besondere Aufmerksamkeit. Es ist mit Antriebsmechanismen, Stromversorgung und Steuerelementen ausgestattet. Es muss so ausgelegt sein, dass es das Gewicht von Einbauteilen und Holzstücken tragen kann. Wir dürfen nicht vergessen, dass im Betrieb statische und dynamische Belastungen und Vibrationen auftreten.
Bei der Festlegung der Maschinenparameter müssen folgende Faktoren berücksichtigt werden:
- Bei diesem Gerät muss die Leistung des Aggregates mindestens 0,85 kW betragen.
- Bei der Berechnung der Struktur ist es notwendig, die Höhe des überstehenden Scheibenrandes zu überprüfen. Dadurch wird die maximale Schnitttiefe bestimmt.
- Die Mindestdrehzahl der Arbeitswelle ist auf 1,5 Tausend Umdrehungen pro Minute begrenzt. Es empfiehlt sich, ihn zu erhöhen, damit sich die Farbe des Holzwerkstücks während des Arbeitsvorgangs nicht verändert.
Beschreibung einer preiswerten Kreissäge aus einer Schleifmaschine mit eigenen Händen
Wie im vorherigen Beispiel können Sie beim Erstellen einer solchen Maschine die Aufgabe mit Standard-Elektrowerkzeugen vereinfachen.
Der Antrieb mit der Trennscheibe ist auf einem Drehkipphebel montiert. Um die körperliche Anstrengung zu erleichtern, ist eine Feder oder ein Gegengewicht eingebaut. Das Werkzeug kann nur in vertikaler Richtung entlang eines Bogens bewegt werden. Dieses Design ist mobil. Es kann im Innen- oder Außenbereich auf einem geeigneten Untergrund installiert werden. Bei Bedarf kann das Mahlwerk demontiert werden. Die Befestigung erfolgt mit Schraubverbindungselementen auf einer dämpfenden Holz-(Gummi-)Dichtung.
Do-it-yourself-Ständer für einen Winkelschleifer: Zeichnungen, Videos, Algorithmus zur Herstellung von Einzelteilen und Montage:
Vorteile und Herstellungsprozess einer einfachen Holzfräsmaschine für eine Heimwerkstatt
Diese Ausrüstung wird zum Schneiden von Nuten auf bestimmte Größen und zum präzisen Bohren in verschiedenen Winkeln verwendet. Mit seiner Hilfe können Sie schnell ein Viertel entfernen und eine Aussparung für ein Werkstück einer bestimmten Form schaffen. Auch ohne ausführliche Erläuterung ist klar, dass solche Möglichkeiten für den Eigentümer eines Privathauses von Nutzen sein werden. Es bleibt abzuwarten, wie man eine selbstgebaute Holzfräsmaschine herstellt. Wäre eine solche Lösung wirtschaftlich machbar oder wäre es rentabler, fabrikgefertigte Geräte zu kaufen?
Die aufgeworfenen Fragen können nach einer detaillierten Untersuchung der relevanten Strukturen beantwortet werden.
Im mittleren Teil des Tisches ist eine Antriebseinheit installiert, die den Fräser dreht. Mithilfe von Zwingen und anderen Vorrichtungen fixieren sie das Werkstück in der gewünschten Position und bewegen es entlang einer vorgegebenen Bahn. Das Arbeitsplatz Ausgestattet mit einem funktionsfähigen Staubentfernungssystem.
Um Fehler bei der Projektumsetzung auszuschließen, achten Sie auf die einzelnen Parameter der Strukturelemente:
- Der Tisch zur Durchführung von Arbeitsvorgängen wird in stationärer Ausführung erstellt. Seine Abmessungen und Tragfähigkeit werden unter Berücksichtigung der Eigenschaften der zu verarbeitenden Proben bestimmt.
- Experten empfehlen den Einbau von Schraubenreglern in die unteren Teile der Stützen. Mit ihrer Hilfe können Sie auch auf unebenen Oberflächen die exakte horizontale Position der Struktur ermitteln.
- Der Kraftrahmen kann daraus zusammengebaut werden Stahl Röhren(Rechteckprofile). Für die Herstellung einer Arbeitsplatte eignet sich eine hochwertige und ziemlich dicke Spanplatte. Ein dünnes Blech vibriert, was die Verarbeitungsgenauigkeit beeinträchtigt.
- Wenn Sie sich für einen Motor mit einer Leistung von 500–900 W entscheiden, reicht die Leistung des Fräsers nur aus, um dünne Schichten abzutragen und relativ kleine Vertiefungen zu erzeugen.
- Bei der Installation eines 900-1900-W-Netzteils sind komplexere Vorgänge zulässig. Bei der Bearbeitung von Werkstücken aus Hartholz sind jedoch gewisse Schwierigkeiten akzeptabel.
- Leistungsstarke Maschinen (mehr als 2000 W) können Fräser aller Art einbauen. Solche Geräte gehören zum professionellen Niveau. Es ist für einen Langzeitbetrieb ohne Überhitzung des Motors ausgelegt.
- Um eine Montageplatte herzustellen, durch die der Motor an der Tischplatte befestigt wird, können Sie eine Glasfaser- oder Metallplatte verwenden.
- Um eine gute Sicht im Arbeitsbereich zu gewährleisten, ist oberhalb des Tisches eine Beleuchtung angebracht.
Die folgende Tabelle gibt Auskunft darüber, wie viel eine manuelle Holzfräse auf dem heimischen Markt kostet.
Marke/Modell, Foto | Kraft, W | Maxi- Niedrige Spindeldrehzahl U/min | Preis, reiben. | Anmerkungen |
---|---|---|---|---|
![]() PROMA/SF-40 | 1500 | 24000 | 17500-18900 | Entwickelt zum Erstellen von Nuten, Falten und Fräsen. |
![]() Enkor/ Corvette-82 | 1500 | 2400 | 14200-15900 | Markante Designelemente: Stop Ecktyp mit einer Skala, die die Bearbeitung in einem bestimmten Winkel vereinfacht; Seitenständer zur Abstützung großer Werkstücke. |
![]() Proxxon/MT 400 | 100 | 25000 | 14200-15700 | Kompaktes, leichtes Modell mit Motor mit geringer Leistung. Konzipiert für die Bearbeitung kleiner Weichholzstücke. |
![]() PROMA/TFS-120 | 5500 | 9000 | 175000-183000 | Ausrüstung auf professionellem Niveau. Anschluss an ein dreiphasiges 380-V-Netz. Geeignet für die Ausstattung spezialisierter Holzverarbeitungsbetriebe. |
![]() X-CUT/ XC-3040 | 800 | 24000 | 188000-196000 | Kompakte Maschine mit numerischer Steuerung (CNC). Zur einfachen Steuerung ist es mit einer Fernbedienung ausgestattet. Das Laden neuer Programme von einem Computer ist mit einem Flash-Laufwerk möglich. |
Die Machbarkeit, ein CNC-Fräsmaschinenprojekt mit eigenen Händen umzusetzen
Durch den Einsatz von Softwaresteuerung ist es möglich, große Teileserien mit hoher Präzision zu erstellen und eine einzigartige und besonders sorgfältige Bearbeitung durchzuführen. Um einen neuen technologischen Prozess zu starten, laden Sie einfach ein neues Programm herunter und klicken Sie auf die Schaltfläche „Start“. Einfache und komplexe Aufgaben werden von einer Holzfräsmaschine automatisch erledigt, ohne dass der Benutzer eingreifen oder steuern muss. Diese Technik eliminiert Bedienfehler und gewährleistet höchste Qualität.
Die Vorteile von Geräten dieser Klasse liegen auf der Hand. Es bleibt abzuwarten, ob es möglich ist, mit eigenen Händen eine CNC-Maschine für Holz zu bauen. Die folgenden Merkmale zeichnen diese Geräteklasse aus:
- Es muss sichergestellt werden, dass sich der Fräser horizontal in alle Richtungen bewegen kann. Dazu benötigen Sie neben einer entsprechenden Befestigungskonstruktion auch zusätzliche Elektromotoren.
- Die präzise Positionierung des Werkzeugs wird durch Sensoren und Schrittmotoren gewährleistet.
- Wird benötigt Software, das die Bewegung des Fräsers steuert und Steuerfunktionen ausführt.
Wichtig! Auch wenn es welche gibt detaillierte Beschreibung und Zeichnungen einer CNC-Fräsmaschine für Holz mit eigenen Händen werden sehr schwierig anzufertigen sein.
So stellen Sie Ihre eigenen Fräser für Holzbearbeitungsmaschinen her
Für die Herstellung dieser Produkte benötigen Sie Rohlinge aus langlebigem Werkzeugstahl, der hohen Temperaturen und starker mechanischer Beanspruchung standhält. Beschädigte Bohrer, Beschläge und Stangen reichen aus. Die gewünschte Form kann mit einer Diamantscheibe erzeugt werden, die in eine Schärfmaschine eingebaut ist. Die Kante wird in einem Winkel von 7 bis 10 Grad geschärft. Zu schmal Arbeitsteil wird auch bei der Bearbeitung von Weichholz schnell beschädigt.
Zeichnungen und Empfehlungen zum Erstellen eines Dickenhobels mit eigenen Händen
Eine qualitativ hochwertige Reproduktion dieser Art der Verarbeitung erfordert einen erheblichen Aufwand. Daher wird die Verwendung empfohlen Dreiphasen-Elektromotor Leistung ab 5 kW bei einer maximalen Rotordrehzahl von 4,5 Tausend U/min.
Die Welle (1) mit einem oder mehreren Messern dreht sich über einen Elektromotor (4), zwei Riemenscheiben und einen Riemen. Zum Andrücken und Bewegen des Werkstücks sind hier Rollen (2, 3) und ein Handantrieb mit Kettenmechanismus verbaut. Die Struktur ist auf einem robusten Rahmen aus Stahlecken montiert.
Unter Berücksichtigung persönlicher Vorlieben ist es nicht schwer, Zeichnungen einer Dickenhobelmaschine mit eigenen Händen anzufertigen. Zur Korrektur technischer Eigenschaften werden das zukünftige Arbeitsvolumen, Werkstückparameter und Raumabmessungen berücksichtigt.
Mit eigenen Händen aus einem Elektrohobel einen funktionsfähigen Abrichthobel herstellen
Sie können schnell und kostengünstig eine Maschine auf Basis eines Standardwerkzeugs mit Elektroantrieb herstellen.
Das Bild zeigt, dass das Elektrowerkzeug in einem speziellen Rahmen über dem Werkstück befestigt ist. Sie ermöglichen eine Bewegung in Längs- und Querrichtung unter strikter Einhaltung eines Winkels von 90° zwischen ihnen. Ein modernes Flugzeug ist mit einem speziellen Ausgang zum Anschluss eines Staubsaugers ausgestattet. Daher wird es keine Probleme bei der Abfallentsorgung geben.
Technologie zum Erstellen einer Holzschleifmaschine mit eigenen Händen
Dieses Gerät erfüllt seine Funktionen mithilfe von starren Wellen und flexiblen Klingen mit auf die Oberfläche aufgetragenem Schleifmittel, Bürsten und anderen Spezialwerkzeugen.
Für die Herstellung von Haushaltsgeräten empfiehlt es sich, relativ einfache Geräte zu wählen. Sie können es nach Ermittlung der benötigten Länge unter Berücksichtigung der genauen Lage der Stützrollen selbst erstellen. Der folgende Algorithmus wird verwendet:
- Die Breite des Bandes ist auf 15 bis 25 cm eingestellt.
- Aus Schleifpapier geeigneter Körnung werden Streifen geschnitten.
- Sie werden durchgehend und ohne große Nähte auf eine flexible Unterlage aus dichtem Material geklebt.
- Ein Verrutschen des Bandes wird dadurch verhindert, dass der Durchmesser der Stützrollen im Mittelteil um mehrere Millimeter vergrößert wird. Es ist auch sinnvoll, eine Gummischicht darauf anzubringen.
Artikel
Da viele Handwerker wissen, dass eine CNC-Fräsmaschine als kompliziertes technisches und elektronisches Gerät gilt, denken sie, dass dies einfach nicht mit eigenen Händen möglich ist.
Diese Meinung entspricht jedoch nicht der Realität: Sie können ein solches Gerät mit Ihren eigenen Händen herstellen, dafür benötigen Sie jedoch nicht nur die vollständige Zeichnung, sondern auch einen Satz bestimmter Werkzeuge und geeigneter Komponenten.
DIY CNC-Maschine (Zeichnungen)
Ich habe mich entschieden, ein hausgemachtes zu kreieren Spezialmaschine Bedenken Sie bei CNC, dass dies lange dauern kann. Darüber hinaus benötigen Sie viel Geld.
Um eine Fräsmaschine herzustellen, die mit einem CNC-System ausgestattet ist, können Sie zwei Methoden anwenden: Kaufen Sie einen fertigen Satz speziell ausgewählter Teile, aus denen diese Ausrüstung zusammengebaut wird, oder suchen Sie alle Komponenten und bauen Sie unabhängig ein Gerät zusammen, das alle Anforderungen erfüllt Deine Anforderungen.
Vorbereitung auf die Arbeit
Wenn Sie vorhaben, eine CNC-Maschine selbst zu bauen, ohne einen vorgefertigten Bausatz zu verwenden, müssen Sie als Erstes anhalten Sonderregelung, wonach ein solches Mini-Gerät funktionieren wird.

Gerätemontage
Die Basis der zusammengebauten Fräsausrüstung kann ein rechteckiger Balken sein, der fest auf den Führungen befestigt werden muss.
Die tragende Struktur der Ausrüstung muss eine hohe Steifigkeit aufweisen. Bei der Montage ist es besser, keine Schweißverbindungen zu verwenden, sondern alle Teile nur mit Schrauben zu verbinden.
Die von Ihnen selbst zusammengebaute Fräsausrüstung muss über einen Mechanismus verfügen, der die Bewegung des Arbeitsgeräts in vertikaler Richtung gewährleistet. Am besten nehmen Sie dafür ein Schraubengetriebe, dessen Drehung über einen Zahnriemen übertragen wird.
Hauptteil der Maschine
Ein wichtiger Teil einer solchen Maschine ist ihre vertikale Achse, die bei einem selbstgebauten Gerät aus einer Aluminiumplatte hergestellt werden kann. Erinnere dich an Die Abmessungen einer solchen Achse wurden genau auf die Abmessungen des zu erstellenden Geräts abgestimmt.
Die Herstellung ist schwierig, da es neben den technischen Komponenten auch über ein elektronisches Gerät verfügt, das nur ein Fachmann einbauen kann. Entgegen dieser Meinung ist die Möglichkeit, eine CNC-Maschine mit eigenen Händen zusammenzubauen, großartig, wenn Sie im Voraus die erforderlichen Zeichnungen, Diagramme und Komponentenmaterialien vorbereiten.
Vorbereitende Arbeiten durchführen
Wenn Sie zu Hause eine CNC mit Ihren eigenen Händen entwerfen, müssen Sie entscheiden, nach welchem Schema sie funktionieren soll.
Oftmals dient ein gebrauchtes Gerät als Basis für ein zukünftiges Gerät.
Die Bohrmaschine kann als Basis für eine CNC-Maschine verwendet werden
Der Arbeitskopf muss durch einen Fräskopf ersetzt werden.
Die größte Schwierigkeit beim Entwerfen einer CNC-Maschine mit eigenen Händen besteht darin, ein Gerät zu erstellen, mit dem sich das Arbeitswerkzeug in drei Ebenen bewegt.
Wagen, die einem herkömmlichen Drucker entnommen wurden, helfen teilweise, das Problem zu lösen. Das Werkzeug kann sich in beiden Ebenen bewegen. Es ist besser, Schlitten für eine CNC-Maschine von einem Drucker mit großen Abmessungen zu wählen.
Ein solches Schema ermöglicht es Ihnen, die Steuerung später an die Maschine anzuschließen. Der Nachteil ist, dass eine CNC-Fräsmaschine nur Holz, Kunststoff usw. bearbeitet dünnes Metall. Dies liegt daran, dass die Druckerschlitten nicht über die erforderliche Steifigkeit verfügen.
Auf den Motor des zukünftigen Aggregats muss geachtet werden. Seine Rolle beschränkt sich auf die Bewegung des Arbeitswerkzeugs. Davon hängen die Qualität der Arbeit und die Fähigkeit zur Durchführung von Fräsarbeiten ab.
Eine gute Option für einen selbstgebauten CNC-Fräser ist ein Schrittmotor.
Eine Alternative zu einem solchen Motor ist ein zuvor verbesserter und an die Standards des Geräts angepasster Elektromotor.
Wer einen Schrittmotor verwendet, darf auf den Einsatz eines Schraubenantriebs verzichten; die Leistungsfähigkeit einer solchen CNC-Maschine für Holz wird dadurch in keiner Weise beeinträchtigt. Es wird empfohlen, zum Fräsen auf einem solchen Gerät Zahnriemen zu verwenden. Im Gegensatz zu Standardriemen rutschen sie nicht auf den Riemenscheiben.
Es ist notwendig, den Fräser der zukünftigen Maschine richtig zu konstruieren; hierfür benötigen Sie detaillierte Zeichnungen.
Für die Montage benötigte Materialien und Werkzeuge
Der allgemeine Materialsatz für eine CNC-Maschine umfasst:
- Kabel 14–19 m lang;
- , Holzverarbeitung;
- Spannfutter für Fräser;
- Frequenzumrichter mit der gleichen Leistung wie die Spindel;
- Lager;
- Steuerplatine;
- Wasserpumpe;
- Kühlschlauch;
- drei Schrittmotoren für drei Achsen der Strukturbewegung;
- Bolzen;
- Schutzkabel;
- Schrauben;
- als Korpus des zukünftigen Geräts stehen Sperrholz, Spanplatten, Holzplatten oder Metallkonstruktionen zur Auswahl;
- weiche Kupplung.
Beim Eigenbau empfiehlt es sich, eine Spindel mit Kühlmittel zu verwenden. Dadurch können Sie es nicht alle 10 Minuten ausschalten, um es abzukühlen. Für die Arbeit eignet sich eine selbstgebaute CNC-Maschine, deren Leistung mindestens 1,2 kW beträgt. Die beste Option wird ein 2-kW-Gerät.
Der für die Herstellung des Geräts erforderliche Werkzeugsatz umfasst:
- Hämmer;
- Isolierband;
- Montageschlüssel;
- Kleber;
- Schraubendreher;
- Lötkolben, Dichtmittel;
- Schleifmaschine, sie wird oft durch eine Bügelsäge ersetzt;
- Zange, Schweißgerät, Schere, Zange.
Einfache DIY-CNC-Maschine
Vorgehensweise beim Zusammenbau der Maschine
Eine selbstgebaute CNC-Fräsmaschine wird nach folgendem Schema zusammengebaut:
- Erstellung von Zeichnungen und Geräteplänen zur Darstellung des elektrischen Anlagensystems;
- Kauf von Materialien für eine zukünftige selbstgebaute CNC-Maschine;
- Installation des Rahmens, auf dem die Motoren, die Arbeitsfläche, das Portal und die Spindel montiert werden;
- Portalinstallation;
- Einstellen der Z-Achse;
- Fixieren der Arbeitsfläche;
- Spindelinstallation;
- Installation eines Wasserkühlsystems;
- Installation elektrischer Systeme;
- Anschließen der Platine, mit deren Hilfe das Gerät gesteuert wird;
- Softwarekonfiguration;
- Startstart der Einheit.
Die Basis für den Rahmen ist ein Material aus Aluminium.
Der Rahmen muss aus Aluminium bestehen
Aus diesem Metall hergestellte Profile werden mit einem Querschnitt von 41*81 mm und einer Plattendicke von 11 mm ausgewählt. Der Rahmenkörper selbst wird über Aluminiumecken verbunden.
Die Installation des Portals bestimmt, wie dick das Produkt von der CNC-Maschine verarbeitet werden kann. Vor allem, wenn es selbst hergestellt wird. Je höher das Portal, desto dicker kann das Produkt verarbeitet werden. Es ist wichtig, es nicht zu hoch zu installieren, da diese Konstruktion sonst weniger langlebig und zuverlässig ist. Das Portal bewegt sich entlang der X-Achse und trägt die Spindel.
Als Material für die Arbeitsfläche des Gerätes wird ein Aluminiumprofil verwendet. Oftmals nehmen sie ein Profil an, das über T-Nuten verfügt. Für den Heimgebrauch wird es akzeptiert; seine Dicke beträgt mindestens 17 mm.
Nachdem der Rahmen des Geräts fertig ist, beginnen Sie mit der Installation der Spindel. Es ist wichtig, es vertikal zu installieren, da es in Zukunft angepasst werden muss; dies geschieht, um den erforderlichen Winkel festzulegen.
Zur Installation der elektrischen Anlage müssen folgende Komponenten vorhanden sein:
- Netzteil;
- Computer;
- Schrittmotor;
- zahlen;
- Stopptaste;
- Autofahrer.
Für den Betrieb des Systems ist ein LPT-Anschluss erforderlich. Darüber hinaus ist eine Installation installiert, die den Betrieb des Geräts steuert und die Beantwortung der Frage ermöglicht, wie dieser oder jener Vorgang ausgeführt wird. Die Steuerung ist über Motoren mit der Fräsmaschine selbst verbunden.
Nachdem die Elektronik in der Maschine installiert ist, müssen Sie die für den Betrieb erforderlichen Treiber und Programme herunterladen.
Häufige Montagefehler
Ein häufiger Fehler beim Zusammenbau einer numerisch gesteuerten Maschine ist das Fehlen einer Zeichnung, die Montage erfolgt jedoch danach. Dadurch kommt es zu Versäumnissen bei der Konstruktion und Installation von Apparatekonstruktionen.
Oft ist ein falscher Betrieb der Maschine mit einem falsch ausgewählten Frequenzumrichter und einer falsch ausgewählten Spindel verbunden.
Für den korrekten Betrieb der Maschine ist es notwendig, die richtige Spindel auszuwählen
In vielen Fällen erhalten Schrittmotoren nicht die richtige Stromversorgung, sodass für sie eine spezielle separate Stromversorgung ausgewählt werden muss.
Es muss berücksichtigt werden, dass Sie mit einem korrekt installierten Stromkreis und einer korrekt installierten Software zahlreiche Vorgänge am Gerät ausführen können verschiedene Level Schwierigkeiten. Ein Handwerker mittleren Niveaus kann eine CNC-Maschine mit eigenen Händen herstellen; das Design der Einheit weist eine Reihe von Merkmalen auf, aber mit Hilfe von Zeichnungen ist es nicht schwierig, die Teile zusammenzubauen.
Es ist einfach, mit einer selbstgebauten CNC zu arbeiten; Sie müssen die Informationsbasis studieren, eine Reihe von Schulungsarbeiten durchführen und den Zustand der Einheit und der Teile analysieren. Beeilen Sie sich nicht, rütteln Sie nicht an beweglichen Teilen und öffnen Sie die CNC nicht.
Zum Anfertigen einer dreidimensionalen Zeichnung Holzoberfläche Es werden werkseitige Exemplare verwendet. Es ist schwierig, ein ähnliches Minimodell mit eigenen Händen zu Hause herzustellen, aber mit einer detaillierten Untersuchung des Designs ist es möglich. Dazu müssen Sie die Besonderheiten verstehen, die richtigen Komponenten auswählen und konfigurieren.
Funktionsprinzip einer Fräsmaschine
Moderne Holzbearbeitungsgeräte mit numerischer Steuerung sind darauf ausgelegt, ein komplexes Muster auf Holz zu erzeugen. Das Design muss ein mechanisches elektronisches Teil enthalten. Zusammen ermöglichen sie es Ihnen, den Arbeitsprozess so weit wie möglich zu automatisieren.
Um eine Desktop-Mini-Holzfräsmaschine mit Ihren eigenen Händen herzustellen, sollten Sie sich mit den Hauptkomponenten vertraut machen. Das Schneidelement ist ein Fräser, der in einer auf der Welle des Elektromotors befindlichen Spindel eingebaut ist. Dieses Design ist am Rahmen befestigt. Es kann sich entlang zweier Koordinatenachsen bewegen – x; j. Um das Werkstück zu fixieren, ist die Anfertigung eines Auflagetisches erforderlich.
Die elektronische Steuereinheit ist angeschlossen Schrittmotoren. Sie ermöglichen eine Verschiebung des Schlittens relativ zum Teil. Mit dieser Technologie können Sie 3D-Zeichnungen auf einer Holzoberfläche erstellen.
Der Betriebsablauf von Minigeräten mit CNC, die Sie selbst herstellen können.
- Schreiben eines Programms, nach dem eine Abfolge von Bewegungen des Schneidteils ausgeführt wird. Hierzu nutzen Sie am besten spezielle Softwarepakete, die für die Anpassung an selbstgebaute Modelle konzipiert sind.
- Legen Sie das Werkstück auf den Tisch.
- Ausgabe des Programms an die CNC.
- Einschalten der Ausrüstung, Überwachung der Umsetzung automatischer Aktionen.
Um eine maximale Automatisierung der Arbeit im 3D-Modus zu erreichen, müssen Sie ein Diagramm korrekt erstellen und die entsprechenden Komponenten auswählen. Experten empfehlen, Fabrikmodelle zu studieren, bevor man ein Mini-Modell baut.
Um komplexe Designs und Muster auf einer Holzoberfläche zu erstellen, benötigen Sie verschiedene Arten von Fräsern. Einige davon können unabhängig hergestellt werden, aber für feine Arbeiten sollten Sie Fabrikmodelle kaufen.
Diagramm einer selbstgebauten numerisch gesteuerten Fräsmaschine
Die schwierigste Phase ist die Auswahl des optimalen Fertigungsschemas. Sie hängt von den Abmessungen des Werkstücks und dem Grad seiner Bearbeitung ab. Für den Heimgebrauch ist es ratsam, eine DIY-Desktop-Mini-CNC-Fräsmaschine zu bauen, die über die optimale Anzahl an Funktionen verfügt.
Die beste Option besteht darin, zwei Schlitten zu bauen, die sich entlang der x-Koordinatenachsen bewegen; j. Als Unterlage verwenden Sie am besten polierte Stahlstäbe. Darauf werden Kutschen montiert. Um ein Getriebe zu erstellen, werden Schrittmotoren und Spindeln mit Wälzlagern benötigt.
Für eine maximale Automatisierung des Prozesses im DIY-Holzbau ist es notwendig, den elektronischen Teil im Detail zu durchdenken. Konventionell besteht es aus folgenden Komponenten:
- Netzteil. Notwendig für die Stromversorgung der Schrittmotoren und des Controller-Chips. Häufig wird das 12V 3A-Modell verwendet;
- Regler. Es dient dazu, Befehle an Elektromotoren zu senden. Um eine selbstgebaute Mini-CNC-Fräsmaschine zu betreiben, reicht eine einfache Schaltung aus, um die Funktion von drei Motoren zu steuern;
- Treiber. Es ist auch ein Element zur Regulierung des Betriebs des beweglichen Teils der Struktur.
Der Vorteil dieses Komplexes ist die Möglichkeit, ausführbare Dateien der gängigsten Formate zu importieren. Mit einer speziellen Anwendung können Sie eine dreidimensionale Zeichnung eines Teils erstellen Voruntersuchung. Schrittmotoren arbeiten mit einer bestimmten Geschwindigkeit. Dazu müssen jedoch technische Parameter in das Steuerungsprogramm eingegeben werden.
Auswahl von Komponenten für eine CNC-Fräsmaschine
Der nächste Schritt besteht darin, Komponenten für den Zusammenbau selbstgebauter Geräte auszuwählen. Die beste Option ist der Einsatz improvisierter Mittel. Als Basis für Desktop-3D-Maschinenmodelle können Holz, Aluminium oder Plexiglas verwendet werden.
Für ordnungsgemäße Bedienung des gesamten Komplexes ist es notwendig, das Design der Bremssättel zu entwickeln. Während ihrer Bewegung sollten keine Vibrationen auftreten, da dies zu ungenauen Fräsvorgängen führen kann. Daher werden vor der Montage alle Komponenten auf Kompatibilität untereinander überprüft.
- Führer. Es werden polierte Stahlstäbe mit einem Durchmesser von 12 mm verwendet. Die Länge für die x-Achse beträgt 200 mm, für die y-Achse 90 mm;
- Bremssattel Die beste Option ist Textolith. Die übliche Größe der Plattform beträgt 25*100*45 mm;
- Schrittmotoren. Experten empfehlen die Verwendung von Modellen eines 24-V-5-A-Druckers. Im Gegensatz zu Diskettenlaufwerken verfügen sie über mehr Leistung;
- Fräserfixierungsblock. Es kann auch aus Textolith hergestellt werden. Die Konfiguration hängt direkt vom verfügbaren Tool ab.
Am besten bauen Sie ein Werksnetzteil zusammen. Beim Selbermachen sind Fehler möglich, die sich anschließend auf die Funktion aller Geräte auswirken.
Herstellungsablauf einer CNC-Fräsmaschine
Nachdem Sie alle Komponenten ausgewählt haben, können Sie mit Ihren eigenen Händen eine Mini-Tischfräsmaschine selbst bauen. Alle Elemente werden zunächst noch einmal überprüft und auf Größe und Qualität überprüft.
Zur Befestigung von Ausrüstungselementen ist die Verwendung spezieller Befestigungselemente erforderlich. Ihre Konfiguration und Form hängen vom gewählten Schema ab.
Verfahren zum Zusammenbau von Desktop-Mini-CNC-Geräten für Holz mit 3D-Bearbeitungsfunktion.
- Einbau von Bremssattelführungen, deren Befestigung an den Seitenteilen der Struktur. Diese Blöcke sind noch nicht auf der Basis installiert.
- Bremssättel einschleifen. Sie müssen entlang der Führungen bewegt werden, bis eine reibungslose Bewegung erreicht ist.
- Ziehen Sie die Schrauben fest, um die Bremssättel zu sichern.
- Anbringen von Komponenten an der Gerätebasis.
- Einbau von Leitspindeln samt Kupplungen.
- Einbau von Antriebsmotoren. Sie werden an den Kupplungsschrauben befestigt.
Der elektronische Teil befindet sich in einem separaten Block. Dies trägt dazu bei, die Wahrscheinlichkeit von Fehlfunktionen während des Betriebs des Routers zu verringern. Ein weiterer wichtiger Punkt ist die Wahl der Arbeitsfläche für die Geräteinstallation. Es muss eben sein, da die Konstruktion keine Schrauben zur Niveauregulierung vorsieht.
Danach können Sie mit den Probeversuchen beginnen. Zunächst empfiehlt es sich, ein einfaches Holzfräsprogramm einzurichten. Während der Arbeit ist es notwendig, jeden Durchgang des Fräsers zu überprüfen – die Tiefe und Breite der Bearbeitung, insbesondere im 3D-Modus.
Das Video zeigt ein Beispiel für den Zusammenbau einer großen CNC-Fräsmaschine aus Eigenbau: