Formlos geformte Pfähle, Betonzusammensetzung. Ausrüstung zur Herstellung von Hohlkörperdecken
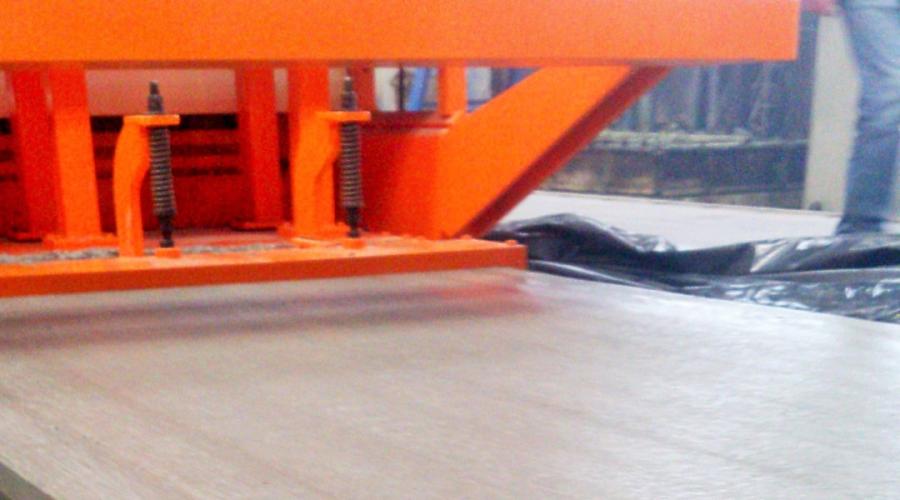
4./2011 VESTNIK _7/202J_MGSU
MODERNE TECHNOLOGISCHE LINIEN ZUR HERSTELLUNG VON BODENPLATTEN
MODERNE PROZESSLINIEN FÜR DIE BODENPLATTENFERTIGUNG
E.C. Romanova, P.D. Kapyrin
E.S. Romanova, P.D. Kapyrin
Staatliche Bildungseinrichtung für höhere Berufsbildung MGSU
Der Artikel diskutiert moderne technologische Linien zur Herstellung von Bodenplatten im formlosen Formverfahren. Der technologische Prozess, die Zusammensetzung der Linie werden analysiert und die Eigenschaften der verwendeten Ausrüstung angegeben.
Im aktuellen Artikel werden die modernen Prozesslinien zur Herstellung von Schalungsdecken untersucht. Der gesamte technologische Prozess wird ebenso untersucht wie die Zusammensetzung der Linien. Die Eigenschaften und Qualitäten der gebrauchten Geräte werden erwähnt.
Der Schlüssel zum Erfolg eines Unternehmens, das Betonprodukte herstellt, liegt derzeit in der Herstellung einer breiten Produktpalette. Folglich benötigt ein modernes Unternehmen, eine Anlage, eine Anlage automatisierte Produktionslinien, leicht rekonfigurierbare Ausrüstung, Universalmaschinen, Anwendung energiesparender und energieeffizienter Technologien.
Technologien zur Herstellung von Stahlbetonprodukten und -konstruktionen lassen sich in traditionelle (Förderer, Zuschlagstofffluss, Kassette) und moderne Technologien unterteilen, wobei das kontinuierliche formlose Formen einen besonderen Platz einnimmt.
Die formlose Formgebungstechnologie wurde während der Sowjetunion entwickelt und als „Mähdrescher-Technologie“ bezeichnet. Heute ist die Technologie in Russland gefragt; mit jeder Betriebserfahrung wird sie von unseren Spezialisten verbessert, wobei die Erfahrung ausländischer Unternehmen genutzt wird.
Der technologische Prozess des formlosen Formverfahrens ist wie folgt: Die Produkte werden auf einem beheizten Metallboden (ca. 60 °C) geformt, der mit vorgespannten hochfesten Drähten oder Litzen verstärkt ist. Die Formmaschine bewegt sich entlang von Schienen und hinterlässt eine kontinuierliche Form Streifen aus geformtem Stahlbeton.
Es gibt drei bekannte Verfahren zum kontinuierlichen formlosen Formen: Vibrationspressen, Extrudieren und Verdichten.
Stopfmethode
Der Kern der Verdichtungsmethode besteht darin, dass sich die Formmaschine beim Verdichten auf Schienen bewegt Betonmischung In der Umformanlage erfolgt dies mit Spezialhämmern. In Abb. In Abb. 1 ist eine schematische Darstellung einer Formanlage zum kontinuierlichen Stopfen dargestellt.
Reis. 1 Schema einer Formanlage zum kontinuierlichen Formen im Stampfverfahren
Die untere Schicht der Betonmischung wird aus Trichter 1 auf die Formbahnen gelegt und mit einem Hochfrequenz-Vibrationsverdichter 3 verdichtet. Die oberste Schicht der Betonmischung wird aus Trichter 2 zugeführt und ebenfalls mit einem Hochfrequenz-Verdichter 6 verdichtet Zusätzlich wird die Oberfläche der Platte mit einem Stoß-Vibrations-Stampfer verdichtet. Nach beiden Flächenverdichtern werden Stabilisierungsplatten 4 eingebaut, um die Verdichtung der Betonmischung zu verbessern. Die Methode findet keine breite Anwendung, da die Anlage sowohl im Betrieb als auch in der Wartung äußerst aufwändig ist.
Extrusionsmethode
Der technologische Prozess besteht aus mehreren aufeinanderfolgenden Phasen:
1. Eine spezielle Gleisreinigungsmaschine reinigt zunächst die Metallbeschichtung und schmiert anschließend die Gleise mit Öl.
2. Die zur Verstärkung verwendeten Bewehrungsseile werden gedehnt, wodurch Spannung entsteht.
3. Anschließend beginnt die Bewegung des Extruders 1 (Abb. 2), wodurch ein Streifen geformten Stahlbetons 2 (Abb. 2) zurückbleibt.
Reis. 2 Extruder
4/2011 VESTNIK _4/2011_MGSU
Die Betonmischung im Schneckenextruder wird entgegen der Maschinenbewegung durch die Löcher der Formanlage gepumpt. Das Formen erfolgt horizontal und die Formmaschine scheint sich vom fertigen Produkt wegzudrücken. Dies gewährleistet eine gleichmäßige Verdichtung in der Höhe und macht die Extrusion beim Formen großformatiger Produkte mit einer Höhe von mehr als 500 mm unverzichtbar.
4. Anschließend wird das Produkt einer Wärmebehandlung unterzogen – es wird mit wärmeisolierendem Material abgedeckt und der Ständer selbst wird von unten erhitzt.
5. Nachdem der Beton die erforderliche Festigkeit erreicht hat, wird die Platte nach vorheriger Entspannung mit einer Diamantsäge mit Lasersicht auf die vorgesehene Länge zugeschnitten.
6. Nach dem Sägen werden die Hohlkörperplatten mittels Hebegriffen aus der Produktionslinie entnommen.
Die Technologie ermöglicht die Herstellung von Platten, die 5–10 % leichter sind als herkömmliche Platten. Durch die hohe Verdichtung der Betonmischung durch die Schnecken können etwa 20 kg Zement pro Kubikmeter Mischung eingespart werden.
Neben den Vorteilen hat die Technologie auch erhebliche Nachteile:
Die Betriebskosten sind hoch. Harte Betonmischung ist abrasiv, was zu einem Verschleiß der Schnecken führt
Die Extrusionsausrüstung ist nur für Zement und inerte Materialien höchster Qualität (normalerweise der Güteklasse M500) ausgelegt.
Begrenzte Produktpalette. Die Extrusion ist nicht zum Formen von Balken, Säulen, Querträgern, Pfeilern und anderen Produkten mit kleinem Querschnitt vorgesehen.
Vibrokompressionsmethode
Das Vibrationspressverfahren ist optimal für die Herstellung aller Produkte mit einer Höhe von nicht mehr als 500 mm. Die Formmaschine ist mit Rüttlern ausgestattet, um die Betonmischung zu verdichten. Es ist zuverlässig und langlebig, enthält keine Verschleißteile. Die Palette der hergestellten Produkte ist vielfältig; Hohlbodenplatten, Rippenplatten, Balken, Querriegel, Pfeiler, Absenkpfähle, Stürze usw. werden gleichermaßen erfolgreich hergestellt. Ein wichtiger Vorteil der Formmaschine ist ihre Unprätentiösität gegenüber der Qualität der Rohstoffe und die damit verbundene Wirtschaftlichkeit. Hochwertige Produkte werden durch die Verwendung von Zement der Güteklasse 400, Sand und Schotter mittlerer Qualität erzielt.
Betrachten wir einen modernen Komplex zur formlosen Herstellung von Hohlkörperbodenplatten (Abb. 3) und beschreiben wir detailliert den technologischen Prozess.
Der Produktionszyklus des formlosen Formens umfasst die folgenden Vorgänge: Reinigen und Schmieren der Formschiene, Auslegen der Bewehrung, Spannen der Bewehrung, Vorbereiten einer Betonmischung, Formen von Produkten, Wärmebehandlung, Entlasten der Bewehrung, Schneiden von Produkten in Stücke einer bestimmten Länge, und Export fertiger Produkte.
Der Komplex umfasst:
Industriebodenbelag
Slipformer
Betonsauger
Multifunktionaler Trolley
Automatischer Plotter (Markiergerät)
Universelle Sägemaschine
Frische Betonsäge
Reis. 3 Technologielinie zur Herstellung vorgespannter Hohlplatten
Technische Eigenschaften und Vorteile der hergestellten Produkte:
1. Hohe Festigkeitseigenschaften.
2. Hohe Genauigkeit der Gesamtabmessungen.
4. Möglichkeit der Herstellung verschiedener Standardgrößen entlang der Länge mit beliebiger Teilung.
5. Möglichkeit der Herstellung schräger Produktenden (Schnitte sind in jedem Winkel möglich).
6. Die Möglichkeit, durch die Verwendung gekürzter Platten Löcher in den Decken für den Durchgang von Lüftungs- und Sanitärblöcken zu bilden und diese Löcher herzustellen Standardbreite und Position im Plan beim Formen von Produkten.
7. Produktionstechnik sorgt dafür strikte Einhaltung spezifizierte geometrische Parameter.
8. Geschätzte gleichmäßig verteilte Last ohne Berücksichtigung des Eigengewichts für den gesamten Bereich von 400 bis 2000 kgf/m2.
Produktauswahl
Tabelle 1
Bodenplatten 1197 mm breit
Dicke, mm Länge, m Gewicht, kg
120 mm Von 2,1 bis 6,3 Von 565 BIS 1700
Von 1,8 bis 9,6
Von 705 bis 3790
Von 2850 bis 5700
Bodenplatten 1497 mm breit
Von 1,8 bis 9,6
Von 940 bis 5000
Von 3700 bis 7400
Von 7,2 bis 14
Von 5280 bis 10260
Kurzbeschreibung und Ausstattungsmerkmale
1. Industriebodenbelag (Abb. 4)
Reis. 4 Aufbau des Technikbodens: 1 - Gewindestange; 2 - Basis (Fundament); 3 - Kanal; 4 - Verstärkungsnetz; 5 - Metall-Kunststoff-Rohr zum Heizen; 6 - Betonestrich; 7 - Isolierung und Betonestrich; 8 - Blechabdeckung
Betonsockel unter dem Technikboden sollte vollkommen eben sein und ein leichtes Gefälle zum Abwasserkanal aufweisen. Die Fußbodenheizung erfolgt über ein Elektrokabel bzw heißes Wasser bis zu einer Temperatur von +60°C. Für Unternehmen, die über ein eigenes Kesselhaus verfügen, ist die Warmwasserbereitung rentabler. Darüber hinaus erwärmt sich der Boden bei der Warmwasserbereitung schneller. Ein technischer Boden ist eine komplexe technische Struktur, die dem Gewicht von geformten Stahlbetonprodukten standhalten muss. Daher beträgt die Dicke des Blechs 12–14 mm. Aufgrund thermischer Längenänderungen des Blechs (bis zu 10 cm auf einer 100-Meter-Strecke) wird das Blech mit Metallplatten im Millimeterabstand fixiert. Die Vorbereitung und das Schweißen von Blechen sollte bei durchgeführt werden Höchststufe Denn je sauberer die Plattenoberfläche bearbeitet wird, desto glatter ist die Deckenoberfläche der Platte.
2. Slipformer (Abb. 5)
Reis. 5 Slipformer
Formmaschine – Slipformer (B=6200 kg) – konzipiert für die Herstellung von Hohldecken. Das Auto ist mit allem ausgestattet notwendige Ausrüstung, einschließlich Zubehör wie Elektrokabel, Kabeltrommel, Wasserbehälter und Gerät zum Glätten der Oberfläche – Finisher.
Die erforderliche Deckenstärke wird durch Austausch des Rohrschalungssatzes erreicht (Austausch dauert ca. 1 Stunde). Die elektrohydraulische Steuerung der Maschine ist für die Arbeit eines Bedieners ausgelegt.
Die Maschine ist mit vier elektrischen Antriebsrädern und einem Variator ausgestattet, der abhängig von der Art der herzustellenden Bodenplatte und der verwendeten Betonmischung unterschiedliche Fahr- und Formgeschwindigkeiten ermöglicht. Typischerweise variiert die Geschwindigkeit zwischen 1,2 und 1,9 m/min.
Die Maschine ist mit einem stationären vorderen und einem hydraulischen hinteren Aufnahmetrichter für Betonmischung ausgestattet. Es verfügt außerdem über zwei Vibratoren mit einstellbarer Leistung. Die Maschine verfügt über eine hydraulisch angetriebene Kabeltrommel komplett mit Elektrokabel (maximale Länge 220 m). Der Finisher ist mit einer Montagevorrichtung und einem Elektroanschluss ausgestattet.
Der Rohrschalungsbausatz ist mit einem hydraulischen Antrieb ausgestattet, die seitlichen Schalungselemente sind aufgehängt, was eine gute Haftung an den Führungen gewährleistet. Der Beton wird durch einen Doppeltrichter mit zwei kontrollierten Auslässen zugeführt
VESTNIK _MGSU
manuell (das Betonvolumen pro Steckdose beträgt 2 Kubikmeter). Es gibt einen verzinkten Wassertank.
Die Maschine wird an die im Werk verfügbare Betonsorte angepasst.
3. Betonsauger (Abb. 6)
Reis. 6 Betonsauger
Der Absauger dient zum Entfernen von ungehärtetem (frischem) Beton (B=5000 kg, 6000 x 1820 x 2840) und wird zum Schneiden von Profilen in Platten und zur Herstellung von Platten mit hervorstehender Bewehrung verwendet. Der Sauger kann auch zum Reinigen des Bodens entlang der Führungen sowie zwischen Produktionsständen verwendet werden. Der Elektroantrieb verfügt über zwei Vorwärtsgänge und zwei Rückwärtsgänge. Die niedrige Geschwindigkeit beträgt 6,6 m/min, die hohe Geschwindigkeit 42 m/min.
Der Absauger beinhaltet:
1. Ein eingebauter Filter und Filtergehäuse, einschließlich:
Filterfläche von 10 m2
Nadel- und Filzfilter aus Polyester mit mikroporöser wasser- und ölabweisender Außenschicht
Automatisches Ventil, das alle 18 Sekunden die Beutelfilter durch Einblasen von Luft wechselt
Abfallbehälter unter dem Filter
Betonabscheider vor dem Auslass.
2. Aspirationsgerät in einem schalldämmenden Gehäuse. Maximale Luftzufuhr - 36 kPa, Motor 11 kW.
3. Kreiselpumpe und ein zusätzlicher Tank für die Wasserdüse.
4. Ein verzinkter Wassertank mit einem Fassungsvermögen von 500 Litern.
Saugdüse mit integrierter handbetätigter Wasserdüse und
Eine am Querträger angebrachte Federausgleichsvorrichtung ermöglicht Quer- und Längsbewegungen. Abfallbehälter mit einem Fassungsvermögen von 1090 l. ausgestattet mit zwei pneumatischen Verschlussventilen. Der Behälter verfügt über einen Haken, der das Anheben erleichtert, sowie über eine Vorrichtung zum Reinigen des Behälters durch Anheben. Die höhenverstellbare Arbeitsplattform dient der Reinigung der Führungen. Der Sauger verfügt über einen Ösenhaken, einen Luftkompressor mit einem Fassungsvermögen von 50 Litern, einen elektrischen Schalter und eine Steuereinheit mit der Möglichkeit, bis zu 4 Fernbedienungen zu installieren.
4. Multifunktionswagen (Abb. 7)
Reis. 7 Multifunktionswagen
Der Trolley (B=2450kg, 3237x1646x2506) wird mit Batterie betrieben und erfüllt die folgenden drei Funktionen:
1. Spannen von Verstärkungsseilen und -drähten entlang von Produktionsständen
2. Schmierung von Produktionsständen
3. Reinigung der Produktionsstände
Die Maschine ist ausgestattet mit: einer Ankerplatte zum Befestigen von Kabeln und Armaturen, einem Schaber zum Reinigen von Produktionsständern, einer Sprühflasche zum Auftragen eines Schmiermittels und einer Handbremse.
5. Automatischer Plotter (Markierungsgerät) (Abb. 8)
Reis. 8 Plotter
Der Plotter (B = 600 kg, 1600 x 1750 x 1220) ist zum automatischen Markieren von Platten und Zeichnen von Zeichnungen darauf gemäß beliebigen geometrischen Daten im EXG-Format (Arbeitsgeschwindigkeit 24 m/min), beispielsweise Schnittwinkel, Ausschnittflächen, konzipiert und Projektidentifikationsnummer. Das Bedienfeld des Plotters ist berührungsempfindlich. Plattendaten können mit jedem tragbaren Gerät auf den Plotter übertragen werden –
VESTNIK _MGSU
für oder über eine drahtlose Netzwerkverbindung. Für Messungen mit einer Genauigkeit von ±1 mm wird ein Laser eingesetzt.
6. Universalsägemaschine (Abb. 9)
Reis. 9 Universal-Sägemaschine
Mit dieser Sägemaschine (B = 7500 kg, 5100 x 1880 x 2320) können Sie gehärtete Platten in der erforderlichen Länge und in jedem Winkel sägen. Die Maschine verwendet 900-1300-mm-Scheiben mit Diamantschneide; Die Scheiben sind zum Schneiden von Platten mit einer maximalen Dicke von 500 mm ausgelegt. Die Maschinengeschwindigkeit beträgt 0-40 m/min. Sägegeschwindigkeit 0-3 m/min, verschiedene Einstellungen möglich. Die Schnittgeschwindigkeit wird automatisch durch eine sparsame Leistungsanpassung des Sägemotors eingestellt. Die Kühlwassermenge beträgt 60 Liter pro Minute. Die Kühlung der Trennscheibe erfolgt auf beiden Seiten durch Düsen, die über einen im Wasserversorgungssystem installierten Druck- und Durchflusssensor gesteuert werden. Die vorderen Düsen können für einen schnellen Sägeblattwechsel einfach gedreht werden. Für eine optimale Arbeitsleistung ist die Schnittgeschwindigkeit einstellbar.
Die Sägemaschine hat die folgenden Eigenschaften:
1. Elektromotoren für präzise Bewegungen.
2. Die Sägemaschine ist vollautomatisch.
3. Der Bediener muss lediglich den Schnittwinkel eingeben.
4. Die manuelle Positionierung erfolgt mittels Laserstrahl.
7. Säge für Frischbeton (Abb. 10)
Reis. 10 Säge für Frischbeton
Handbetriebene Säge (m = 650 kg, 2240 x 1932 x 1622) zum Längsschneiden von frisch verlegter Betonmischung zur Herstellung von Platten mit nicht standardmäßiger Breite, die von den in der Formmaschine angegebenen abweichen. Die maximale Plattenhöhe beträgt 500 mm. Das Sägeblatt verfügt über einen elektrischen Antrieb. Um Geld zu sparen, kann die gebrauchte Diamanttrennscheibe (1100-1300) recycelt werden. Die Positionierung und Bewegung der Maschine erfolgt manuell. Die Säge bewegt sich auf Rollen am Ständer entlang und wird über ein Kabel mit Strom versorgt.
Benutze dies technologischer Prozess erlaubt:
Sorgen Sie für eine erhöhte Tragfähigkeit der Bodenplatten (da die Bewehrung durch vorgespannte Bewehrung erfolgt)
Sorgen Sie für eine hohe Ebenheit der Oberfläche, indem Sie die Oberfläche der Platten kräftig glätten
Achten Sie auf die strikte Einhaltung der vorgegebenen geometrischen Parameter
Herstellung von Platten mit hohen Festigkeitseigenschaften durch Zwangsverdichtung der Unter- und Unterseite oberste Schichten Beton usw.
Wir haben moderne technologische Linien zur Herstellung von Bodenplatten untersucht. Diese Technologien erfüllen die meisten Anforderungen an die moderne Herstellung von Betonprodukten. Daher sind sie vielversprechend, d.h. Ihre Verwendung ermöglicht Unternehmen der Effizienz, Stahlbeton usw. Seien Sie wettbewerbsfähig und erfüllen Sie die Kundenbedürfnisse vollständig.
Literatur
1. Utkin V.L. Neue Technologien in der Bauindustrie. - M.: Russischer Verlag, 2004. - 116 S.
2. http://www.echo-engineering.net/ – Gerätehersteller (Belgien)
3. A. A. Borshchevsky, A. S. Iljin; Mechanische Ausrüstung zur Herstellung von Baustoffen und Produkten. Lehrbuch für Universitäten zum Thema Spezial. „Die Produktion baut sich auf. Hrsg. und Strukturen.“ – M: Alliance Publishing House, 2009. – 368 Seiten: Abb.
1. Utkin V. L. Neue Technologien der Bauindustrie. - M: der russische Verlag, 2004. - 116 mit.
2. http://www.echo-engineering.net/ – der Hersteller der Ausrüstung (Belgien)
3. A.A.Borschevsky, A.S.Ilyin; die mechanische Ausrüstung für die Herstellung von Baumaterialien und Produkten. Das Lehrbuch für Gymnasien zum Thema „Pr-in-Builds. Hrsg. Und Designs". Veröffentlichung Haus das Alliance, 2009. - 368c.: Schlick.
Schlüsselwörter: Böden, Formen, Technologien, Schalung, Ausrüstung, technologische Linien, Platten
Schlüsselwörter: Überlappung, Bildung, Technologien, Balkenwerk, Ausrüstung, technologische Linien, Platten
Der Artikel wurde von der Redaktion des MGSU Bulletins vorgestellt
Der multifunktionale Betonmischkomplex ist mit sechs ausgestattet Betonmischer SICOMA unterschiedlicher Volumina mit einer Gesamtproduktivität von 360 Kubikmetern Beton pro Stunde. Zur Herstellung einer Mischung wird ein Dehnungsmessstreifensensor als Wägeinstrument verwendet, dessen Signal durchläuft Software-Logiksteuerung SIEMENS verarbeitet es in Sekundenbruchteilen und gibt Befehle zur Durchführung von Aktionen an Aktoren (Motoren, Sektorventile, Absperrventile mit Antrieb). Dadurch erhalten die Dosierbehälter die im Labor ermittelte Bedarfsmenge an Materialien. Der Prozess der Materialsammlung wird automatisch gesteuert. Die Mischer sind mit Optionen ausgestattet, um das Mischen der Betonmischung zu optimieren. Von der Betonmischanlage kann Beton an sieben stationäre Stationen geliefert werden. Der werkseigene Betonmischkomplex deckt den Bedarf für die Herstellung kommerzieller Mischungen und Stahlbetonprodukte vollständig ab.
Werkstatt zur Herstellung von FBS-Blöcken
DSK Kolovrat verfügt über selbstfahrende Formmaschinen zum Vibrationspressen von FBS-Blöcken. Blöcke können in hergestellt werden kurze Zeit in großen Mengen gemäß der in GOST 13579-78 vorgesehenen Nomenklatur.
formlose Formanlagen
Auf langen Ständen formlose Formanlagen von TECNOSPAN Es werden vorgespannte Stahlbetonprodukte hergestellt. Heute ist dies die fortschrittlichste Formmethode. Es ist wichtig, dass der Einsatz formloser Technologien die Umweltleistung des Unternehmens im Vergleich zu Aggregatproduktionslinien um etwa eine Größenordnung verbessert (Lärm, Staubgehalt usw. werden reduziert). Wir produzieren Hohlplatten, Pfähle, Säulen, Querträger, Balken und Stürze. Alle Produkte verfügen über ein obligatorisches staatliches Zertifikat und entsprechen den GOST-Standards.
technisches Labor
Das Material wird auf Einhaltung der Normen überprüft und die Produktqualitätskontrolle erfolgt in unserem Labor, das mit hochwertiger europäischer Ausrüstung ausgestattet ist. Die Qualitätskontrolle erfolgt in allen Phasen – von der Eingangskontrolle der Materialien bis zum Versand der fertigen Produkte an den Verbraucher.
Ausrüstung zur Herstellung von Hohlkörperdecken. Unser Unternehmen wählt und liefert diese Ausrüstung entsprechend den vom Kunden gestellten Aufgaben. Unsere zwei Hauptanforderungen bei der Lieferung einer Leitung:
- Produktionsraum, in dem eine formlose Formanlage für Hohlkörperdecken installiert wird, muss mindestens 90 Meter lang sein. Diese Abmessungen ermöglichen Gleise mit einer Länge von 72 Laufmetern. Wir halten den Bau von Gleisen kürzerer Länge aus folgenden Gründen für ungeeignet:
- Bei der formlosen Formgebungstechnologie kommt es zu geringen technologischen Verlusten an Betonmischung und Bewehrung am „Eingang/Ausgang“ der Formmaschine. Auf 4 Gleisen mit 60 linearen Linien. m. Diese Verluste werden 2-mal größer sein als auf 2 Gleisen von 120 Laufmetern. M.
- Nach einem Formzyklus auf einer Bahn müssen wir das Formmodul spülen und die Maschine zur nächsten Bahn bewegen. In der Praxis dauert dieser Vorgang etwa 40 Minuten. Dementsprechend auf 4 Gleisen mit 60 linearen Linien. m. Der Produktionszeitverlust ist doppelt so groß wie bei 2 Gleisen mit 120 Laufmetern. M.
Ein Beispiel für die „Einfahrt“ einer Formmaschine in ein Gleis. LBF-Formteil
- Verfügbarkeit unserer eigenen Betonmischanlage. Weil Für die Arbeit an der Linie zum formlosen Formen von Hohlplatten wird eine „harte“ Betonmischung benötigt; diese Mischung können wir nicht in Mischern liefern. Es ist auch nicht ratsam, zwischen der Vorbereitung der Betonmischung und dem Einbringen auf die Formstrecke einen langen Zeitraum (maximal 20 Minuten) zu verstreichen. Dieser Umstand schließt die Anlieferung des benötigten Gemisches auf der Ladefläche eines Muldenkippers praktisch aus.
Der Hauptunterschied in der Ausstattung der formlosen Formanlage ist die Formmaschine. Es gibt drei Arten von Formmaschinen: Extruder, Vibrationsformmaschine Und Slipformer. Unser Unternehmen liefert formlose Formanlagen mit Extruder, oder Vibrationsformmaschinen. Was erklärt diese Variabilität?
Linie zum formlosen Formen von Hohlkernplatten, ausgestattet mit einer Vibroformmaschine. Erstens ist es dort angebracht, wo das jährliche Produktionsvolumen von Hohlplatten 100.000 m2 nicht überschreitet oder sich ein angenehmes Wettbewerbsumfeld entwickelt hat. eines der Features Vibrationsformmaschine- Hierbei handelt es sich um einen erhöhten Zementverbrauch in der verwendeten Betonmischung. Im Durchschnitt sind das 70 „zusätzliche“ Kilogramm pro 1 m3 Beton im Vergleich zur verwendeten Mischung Extruder.
Für die Herstellung von 100.000 m2 Hohlkörperplatten mit einer Breite von 1.200 mm und einer Höhe von 220 mm werden pro Jahr etwa 11.000 m3 Betonmischung benötigt. Bei durchschnittlich 70 „zusätzlichen“ kg/m3 Beton wird der jährliche Mehrverbrauch an Zement etwa 750 Tonnen betragen.
Wie profitiert eine Vibroformmaschine von einem Extruder?
- weniger Investitionen. Mit anderen Worten, der Preis des Sets formlose Formanlagen mit Vibroformmaschine, etwa 1,5- bis 2-mal niedriger als bei einem ähnlichen Kit mit Extruder.
- Die Kosten für jede Ersatzdüse betragen Vibrationsformmaschine um das 5- bis 8-fache geringer als bei einem Extruder.
- Es gibt so etwas wie das Verhältnis der Kosten für Verbrauchsmaterialien und Ersatzteile pro 1 m2 produzierter Bramme pro Jahr. U Vibrationsformmaschine dieses Verhältnis überschreitet nicht 0,08 Euro/m2. Mindestwert Extruder, die wir in unserer Praxis angetroffen haben - 0,18 Euro/m2. Der Unterschied zwischen diesen Indikatoren ist zunächst einmal darauf zurückzuführen Vibrationsformmaschinen Es gibt keine Verschleißteile wie Schnecken, die darauf stehen Extruder.
An Video, Nachfolgend finden Sie die Technologie des formlosen Formens mit einer Vibrationsformmaschine „Resimart“(Spanien), einschließlich der von unserem Unternehmen gelieferten.
Ingenieure V. I. IVANOV (Gosstroy UdSSR), A. A. FOLOMEEV (NIIZhB)
In den letzten Jahren hat in Kanada, den USA, Deutschland, England, Italien, Frankreich und anderen Ländern die formlose Produktion von vorgefertigten Stahlbetonkonstruktionen für Wohn-, öffentliche und öffentliche Gebäude begonnen Industriegebäude sowie einige Arten von Ingenieurbauwerken. Auf diese Weise entstehen Mehrfachhohlplatten, massive Belagplatten, lineare Elemente aus T-, I-Träger-, Vierkant- und Sechskantprofilen sowie Außenwandplatten mit geprägten Vorderflächen.
Merkmale der meisten durch formloses Formen hergestellten Strukturen sind ein konstanter Querschnitt über die Länge des Produkts, eine erhebliche Vereinfachung ihrer Verstärkungselemente, was zu einer Reduzierung des Stahlverbrauchs und einer Erhöhung der Betonqualität im Vergleich zu Produkten für die gleichen Produkte führt Zweck hergestellt von inländischen Unternehmen. Die charakteristischen Unterschiede dieser Produktionstechnologie sind: der Einsatz spezieller Formeinheiten, die gleichzeitig die Vorgänge des Verlegens und Verdichtens der Betonmischung unter dem Einfluss von Vibration und statischem Druck durchführen; die Verwendung von Wasser zur Plastifizierung der Betonmischung auf einer vorgewärmten Standfläche; vollständige Ablehnung von Formularen; maschinelles Auslegen von Armierungsgewebe oder Querstangen; die Möglichkeit, auf einem Ständer Strukturen unterschiedlicher Länge zu erhalten, indem das ausgehärtete Produkt mit einer Kreissäge geschnitten wird oder kombinierte Methode- Vorschneiden eines frisch geformten Elements mit vibrierenden Messern und Endschneiden des ausgehärteten Teils des Betons mit vorgespannter Bewehrung mit einer Kreissäge.
Die Wärmebehandlung erfolgt durch Zufuhr von Kühlmittel (Dampf, heißes Wasser oder erhitztes Öl) in Teilregister der Stände, während die Produkte mit Plane oder synthetischen Materialien abgedeckt sind.
Die Hauptausrüstung technologischer Linien für formloses Formen sind spezialisierte Formeinheiten mit unterschiedlichen Funktionsprinzipien und Designlösungen, die sich auch in der Palette der hergestellten Elemente unterscheiden. Aufgrund ihres Funktionsprinzips lassen sie sich in zwei Gruppen einteilen. Die erste sind Maschinen mit einem Extrusionsarbeitskörper, der gleichzeitig die Betonmischung über den gesamten Produktquerschnitt verdichtet. Die zweite Methode besteht aus vibrationsziehenden Arbeitskörpern, die den Prozess der Formung von Elementen in mehreren Schritten durchführen, abhängig von der Höhe des Produktquerschnitts oder der Notwendigkeit, Hohlräume darin zu erhalten.
Einheiten mit einem Extrusionskörper (Spyrol – Kanada, Daikor – USA, Elematic – Finnland usw.) sind für das Formen von Hohlkernplatten mit einer Breite von 1,2 m und einer Länge von bis zu 12 m ausgelegt und auf die Herstellung von Produkten durch jede Maschine spezialisiert nur eine Höhe - 150, 200, 250 oder 300 mm. Ihr Arbeitskörper (Abb. 1) besteht aus mehreren Schrauben, deren Anzahl der Anzahl der Hohlräume in der Platte entspricht. Im Inneren jeder Schnecke sind Hochfrequenzvibratoren eingebaut. Die Schnecken enden mit Hohlkörpern, deren Enden durch Gummimanschetten von ihrem Hauptteil getrennt sind, was die Übertragung von Vibrationen von den Rüttlern auf die Endteile der Hohlkörper und damit auf den frisch geformten Beton der Schnecken deutlich reduziert Produkte. Um Produkte mit konstanter Höhe zu erhalten, ist im Gerät ein Oberflächenrüttler eingebaut, der die Funktion einer Kalibriervorrichtung übernimmt.
Die Maschine verfügt über keinen Fahrantrieb; ihre Bewegung während des Formvorgangs erfolgt durch die Wirkung der Reaktionskräfte der verdichteten Betonmischung.
Die Platten werden in Längsrichtung nur mit vorgespannten hochfesten Drähten oder Seilen verstärkt.


Die Anordnung und Spannung der Bewehrung erfolgt mit hydraulischen Hebern. Zum Verlegen der Querbewehrung im oberen Bereich der Produkte ist eine spezielle Vorrichtung vorgesehen. Die Platten bestehen aus einer Betonmischung mit BJLltv 0,28. Bei einer Betonfestigkeit von 250 kgf/cm2 wird die Bewehrungsspannung gelöst und die Produkte werden mit einer Festigkeit von 350 kgf/cm2 an den Verbraucher versandt.
Die Herstellung von Hohldecken wird in der Regel in einer Spannweite von 18 m und einer Länge von 165 m organisiert, wobei 6 Gerüste mit je 108 m Länge aufgestellt werden, drei in jede Richtung von der Spannweitenachse. Alle Stände werden von einer Formeinheit bedient. Am Stand arbeiten zwei Arbeiterteams, bestehend aus 9 Personen pro Schicht, die nach Abschluss der angegebenen Arbeiten nach 3-4 Stunden von einem Stand zum anderen wechseln. Das erste Team beginnt mit dem Schneiden der Platten, dem Entfernen aus dem Stand und endet mit der Vorbereitung des Standes für die Produktbildung. Das zweite Team befasst sich hauptsächlich mit der Formung von Produkten und Arbeiten im Zusammenhang mit deren beschleunigter Aushärtung.
Der Standumsatz beträgt 18 Stunden mit einer Produktaushärtungszeit von 8–10 Stunden. Die Produktformgeschwindigkeit beträgt 0,8–1,2 m/min. Der durchschnittliche Betriebszyklus einer Kreissäge zum Schneiden eines gehärteten Produkts beträgt 4 Minuten. Bei 260 Arbeitstagen beträgt die jährliche Produktivität einer Spanne mit sechs Ständen etwa 38.000 m3 oder 250.000 m2 Produkte.
Die Produktion pro Arbeiter beträgt ca. 1400 m3 pro Jahr.
Zu den Einheiten mit einem vibrobräumenden Arbeitskörper gehören Spezialmaschinen von Hastings Dynamould (USA) zum formlosen Formen von Hohlkernplatten und Platten aus massivem Profil mit einer Breite von 1,2 oder 2,4 m, einer Plattenhöhe von 150, 200, 250 oder 300 mm und Platten - 50 und 100 mm. Produkte jeder Standardgröße können nur von einer Maschine geformt werden, die auf die Herstellung dieses Elements spezialisiert ist.
Die Platten werden im unteren Bereich mit vorgespannten Seilen und im oberen Bereich mit Armierungsgewebe verstärkt, das während des Formprozesses maschinell ausgelegt wird. Bei Bedarf kann ein Netz entsprechender Breite verlegt werden, das entlang der Längsseite des Produkts Auslässe bildet.
Hohlkernplatten werden mithilfe von Vibrationsmechanismen in zwei Schritten geformt. Der letzte Arbeitsgang ist die Kalibrierung der oberen Oberfläche der Produkte. Zuerst legt und verdichtet die Maschine die Betonmischung auf den unteren Teil der Platte und formt ihre vertikalen Elemente (Abb. 2), dann auf den oberen Teil des Produkts und bearbeitet anschließend die Oberseite der Platte mit Walzen.
Um ein Produkt mit zwei Oberflächen zu erhalten, die zum Tünchen oder Streichen bereit sind (zur Verwendung von Platten als Wandpaneele) wird seine Oberfläche zusätzlich mit einer Scheibenglättmaschine bearbeitet.
Das Unternehmen, das die Ausrüstung herstellt, ist der Ansicht, dass die Hauptvoraussetzung für eine qualitativ hochwertige Formung der Produkte die ununterbrochene Versorgung der Bunker mit Betonmischung ist. Die Arbeitsgeschwindigkeit der Maschine wird je nach Produktquerschnitt zwischen 1 und 3,6 m/min gewählt. Leerlaufgeschwindigkeit - 35 m/min. Zum Einsatz kommt eine Betonmischung mit einem Setzkegel bis 5 cm und einer Grobkorngröße bis 19 mm sowie Sand mit einem Kornmodul von 2,5. Betonsorte M 350 mit einem Zementverbrauch von 420 kg/m3 und einer Wassermenge von 140 l/m3, was die Verwendung einer Betonmischung mit W/Z = = 0,32 ermöglicht.
Eine Formanlage kann vier Stände mit einer Länge von 120 m bedienen. Sie beschäftigt 8 Mitarbeiter pro Schicht. Bei einem Einschichtbetrieb und einer Wärmebehandlung von 8 bis 9 Stunden (bei einer Standoberflächentemperatur von 60 bis 70 °C) erreicht die jährliche Produktivität von zwei Ständen 180.000 m2 Paneele.
Die Firma „Sienkrit“ (USA) bewirbt im Formprinzip ähnliche Anlagen zur Herstellung von Hohlkörperdecken mit einer Höhe von 7,5, 10, 20 und 30 cm, mit einer Spannweite von bis zu 12 m und Leichtbaudecken mit einer Höhe von 20, 30, 35 und 40 cm, mit einer Spannweite von bis zu 20 m. Die Platten werden in drei Schritten geformt und in drei Schichten auf jeden Ständer gelegt, mit einem Abstandshalter zwischen den Schichten aus Polymergewebe. Formgeschwindigkeit 2,4-3-3,6 m/min. Die Breite der Platten beträgt 1,2; 1,5; 2 und 2,4 m.

Vertreter der Firma Spandake (USA) behaupten, dass sie die leichtesten Platten mit einer Höhe von 15 bis 40 cm und einer Breite von 1,2 oder 2,4 m produzieren. Sie werden mit zwei Maschinen und einer Vorrichtung geformt. Die erste Maschine, die sich entlang des Ständers bewegt, formt aus Leichtbeton die untere Platte des Produkts. Anschließend wird eine Trommel mit 4–5 cm breiten Rippen darüber gerollt, deren Anzahl der Anzahl der gespannten Seile der Produkte entspricht. In die geformten Rillen werden Seile gelegt, die zweite Maschine formt vertikale Rippen aus schwerem Beton, gießt leichtes wärmedämmendes Material (Schlackenbimsstein, Blähton etc.) in den Freiraum dazwischen und formt die obere Platte des Produkts. Nach dem Aushärten wird die Platte in Stücke einer bestimmten Länge geschnitten.
Universeller sind Einheiten zum formlosen Formen von Stahlbetonprodukten von Max Roth (Deutschland). Mit ihrer Hilfe ist es möglich, Hohlkammerbodenplatten mit einer Länge von bis zu 12 m, einer Höhe von 80, 160, 220 und 300 mm und einer Breite von 0,8 mm herzustellen. 1,2; 1,5; 1,8; 2,4; 3 und 3,6 m, Massivdecken und Wandelemente mit einer Höhe von 140, 240 und 300 mm; lineare Elemente mit T-, I-Träger-, Trog- und anderen Querschnitten. Mit einer 3,6 m breiten Plattenherstellungsmaschine können Sie beispielsweise gleichzeitig eine 3,6 m breite Platte oder zwei 2,4 m breite und 1,2 m breite Platten oder drei 1,2 m breite Platten oder zwei 1,8 m breite Platten herstellen Hohlkammerplatten und Elemente von Außenwänden können aus Leicht- und Schwerbeton hergestellt werden. Die Festigkeit schwerer Betonprodukte erreicht 450-550 kgf//cm2. Der Zementverbrauch liegt im Bereich von 350–420 kg/m3 und der W/Z = 0,36–0,4. Es werden 2 bis 4 Fraktionen von Zuschlagstoffen mit einer Partikelgröße von bis zu 8 mm (die massivste) und die größte 10-12 mm verwendet. Zuschlagstoffe größer als 15 mm werden nicht verwendet. Die Produkte werden im unteren Bereich mit einer in üblicher Weise gespannten Vorspannarmierung und einem Armierungsgewebe verstärkt, das von der Maschine während des Formvorgangs eingelegt wird. Durch die Verwendung von Armierungsgeweben mit ausreichender Breite ist es möglich, Produkte mit Austrittsöffnungen entlang der Längskanten herzustellen. Im oberen Bereich der Produkte wird das Armierungsgewebe durch eine mit geringem Kraftaufwand gespannte Längsarmierung ersetzt, auf die die Maschine während des Formvorgangs Querstäbe mit vorgegebener Teilung legt. .
Diese Maschinen führen das Formen je nach Produkttyp in 14 bis 3 Schritten durch (Abb. 3). Im ersten Schritt wird der untere Teil der Platte einer bestimmten Dicke betoniert, wobei die Betonmischung über die Breite des Produkts verteilt wird. Anschließend wird der Mittelteil der Bramme geformt, in dem die mit der Maschine bewegten Hohlräumer runde oder ovale Hohlräume formen. Im dritten Schritt wird der obere Teil der Platte geformt. Zur Vorbereitung des Tünchens oder Streichens wird die Oberfläche zusätzlich mit einer Scheibenkelle bearbeitet. Die Formmaschine bewegt sich je nach Dicke des Formprodukts mit einer Geschwindigkeit von 1–2,5 m/min.
Nach Angaben der Firma Max Roth empfiehlt es sich, die Produktion von Hohlkern-Massivdecken mit einer Breite von 3,6 m auf drei Gerüsten mit einer Länge von 150 m und einer Breite von 3,85 m zu organisieren, die sich in einer Spannweite von 16 m befinden beträgt 1600 m2 Platten pro Tag, die Anzahl der Mitarbeiter beträgt 8 Personen. pro Schicht, jährliche Produktivität - 400.000 m2.
Im Werk Lavenir en Gene/Lyon (Frankreich) werden Außenwandpaneele und vorgespannte Rippendecken mit einer Breite von 3,6 m und einer Länge von 5,76 m auf zwei Gerüsten mit einer Spannweite von 105 m Länge und 20 m Breite hergestellt. Die Gerüste sind mit Registern ausgestattet für Kühlöl und haben eine Oberflächentemperatur von ca. 60°C. Die Bewegungsgeschwindigkeit der Formmaschine beträgt 2 m/min. Die Spannenproduktivität beträgt 1400–1800 m2 Platten pro Tag.
Die beschriebenen Einheiten werden in Deutschland, Frankreich, Österreich, England, der Schweiz, Italien, Spanien und einer Reihe weiterer Länder betrieben.
NIIZHB abgeschlossen vergleichende Analyse Indikatoren für die Herstellung von Hohlkammerplatten mit einer Breite von 1,2 m auf Linien und Gerüsten mit einer Extrusionseinheit sowie flache Platten 3 m breit auf Förderstrecken und Banklinie. Gleichzeitig wurden Einsparungen auf Baustellen durch den Einsatz hochwertiger Produkte sowie Einsparungen bei Bewehrungsstahl für Scharniere und Endrahmen nicht berücksichtigt. Herkömmlicherweise ging man davon aus, dass ihre Kosten die mit der Verwendung höherer Betonqualitäten verbundenen Kosten decken sollten.
Die Analyse ergab, dass die formlose Methode zur Herstellung von Stahlbetonkonstruktionen mit Einheiten der beschriebenen Typen eine Reduzierung der Arbeitsintensität der Produktion um das 1,7- bis 1,8-fache ermöglicht; Der Metallverbrauch der Ausrüstung beträgt das 3,2- bis 9,6-fache. Die Herstellungskosten betragen das 1,1- bis 1,2-fache.
Basierend auf der Effizienz der formlosen Produktion sollten die beschriebenen Technologien in mehrere Richtungen umgesetzt werden, wodurch spezielle Einheiten und Liniendesigns für deren Verwendung geschaffen werden. Dazu gehören Maschinen und Linien zur Herstellung raumgroßer Schwerbetonplatten mit Umstellung für die Herstellung von Produkten unterschiedlicher Breite in einer Breite von maximal 3,6 m; Leichtbeton-Außenwandplatten mit Reliefoberflächen in verschiedenen architektonischen Designs; Bodenplatten aus Blähtonbeton für Wohngebäude und öffentliche Gebäude; lineare Elemente, einschließlich T-Pfetten zur Abdeckung von Vieh- und Geflügelställen, Zaunpfosten für Weiden, Pfähle und andere Produkte.
Die Umsetzung dieser Maßnahmen erfordert eine gewisse Überarbeitung der Produktion derzeit hergestellter Strukturen und die Schaffung neuer Strukturen im Verhältnis zu den Fähigkeiten der beschriebenen Technologie.
Moskau 1981
Veröffentlicht durch Beschluss der Abteilung für Fabriktechnologie für Beton und Stahlbeton NTS NIIZHB des Staatlichen Baukomitees der UdSSR vom 6. März 1981.
Die Technologie zur Herstellung von vorgespannten Stahlbetonkonstruktionen im formlosen Verfahren in allen Phasen (Vorbereitung der Betonmischung, Vorbereitung der Stahlständer, Verlegen und Spannen der Bewehrung, Formen, Wärmebehandlung, Schneiden von Festbetonstreifen in Produkte und deren Transport) beschrieben. Die Anforderungen an die Qualität der fertigen Produkte sind gegeben.
VORWORT
In den letzten Jahren hat sich in der UdSSR die formlose Produktion von Stahlbetonkonstruktionen auf linearen Ständern entwickelt, auf denen mit der Methode des kontinuierlichen Formens Produkte mit konstantem Querschnitt über die Länge des Ständers hergestellt werden können: Hohlkammerbodenplatten, Flach- und Wannenplatten, einschichtige und dreischichtige Wandpaneele usw.
Diese Empfehlungen sind für den praktischen Einsatz in vorgefertigten Stahlbetonfabriken bestimmt, wo die formlose Produktion von Stahlbetonkonstruktionen auf linearen Gerüsten eingeführt wird, die mit selbstfahrenden Formeinheiten und anderen Geräten ausgestattet sind, die von Max Roth (Deutschland) gekauft oder in der UdSSR unter a reproduziert wurden Lizenz dieser Firma und beschreiben Sie auch die Reihenfolge des technologischen Prozesses.
Das formlose Produktionsverfahren mit selbstfahrenden Formeinheiten stellt besondere Anforderungen an die Qualität der Betonmischungen, deren Transport zu den Formeinheiten, die Steuerung einer kontinuierlich bewegten Formeinheit, das Verlegen und Spannen der Bewehrung, die Wärmebehandlung, das Ausschalen und den Transport der Produkte .
Die Empfehlungen wurden auf der Grundlage einer praktischen Überprüfung der Bestimmungen der technischen Dokumentation von Max-Roth-Geräten unter Produktionsbedingungen im Seversky-Stahlbetonwerk des Glavsreduralstroy-Ministeriums für Schwerbau der UdSSR erstellt.
Die Empfehlungen wurden vom Forschungsinstitut für Stahlbetonbau des Staatlichen Baukomitees der UdSSR (Kandidaten der technischen Wissenschaften S. P. Radoshevich, E. Z. Akselrod, M. V. Mladova, V. N. Yarmakovsky, N. N. Kupriyanov) unter Beteiligung von Glavsreduralstroy vom Ministerium für Schwerbau der UdSSR entwickelt (Ingenieure E.P. Varnavsky, S.N. Poish, V.N. Khlybov) und UralpromstroyNIIproekt des Staatlichen Baukomitees der UdSSR (Kandidaten der technischen Wissenschaften A.Ya. Epp, R.V. Sakaev, T.V. Kuzina, I.V. Filippova, Yu. N. Karnet, Ingenieur V.V. Anishchenko).
Direktion des NIIZhB
ALLGEMEINE BESTIMMUNGEN
1.1. Diese Empfehlungen gelten für die Herstellung von vorgespannten Stahlbetonprodukten mit einer Breite bis zu 1,5 m und einer Höhe bis zu 30 cm (Hohlkammer-Bodenplatten und Wandplatten) aus Schwer- und Leichtbeton im formlosen Verfahren.
1.3. Merkmale der formlosen Fertigung in Lizenz von Max Roth sind:
mehrstufiges kontinuierliches Formen von Produkten aus starren Betonmischungen;
Umsetzung der Vibrationseinwirkung auf die Betonmischung durch Arbeitsteile allein durch Kontakt mit der Mischung (oberflächenschichtige Verdichtung);
kontinuierliche Bewegung der Verdichtungselemente der Maschine relativ zur zu verlegenden Betonmischung.
Die technologische Linie zur formlosen Herstellung von vorgespannten Stahlbetonprodukten muss über folgende Ausstattung verfügen:
Stahlständer Größe 150´ 4 m mit Ölheizregistern darunter (Prozesslinien mit in der UdSSR nachgebildeten Geräten können kleinere Ständer haben);
hydraulische Spannvorrichtungen zum Gruppenspannen der Bewehrung und zum Ausgleich von Spannungsverlusten beim Aufheizen des Gerüstes und der Bewehrung während der Wärmebehandlung (Gruppen-Hydraulikheber);
Hydraulikheber vom Typ „Paul“ zum einmaligen Spannen der Bewehrung (Einzelhydraulikheber);
Selbstfahrender Betonstahlverteiler mit Umlenk- und Schneidvorrichtung;
Spulenhalter zur Draht- oder Litzenverstärkung;
selbstfahrende Formeinheit mit Dosiertrichtern;
Wagen mit einer wärmeisolierenden Decke zum Abdecken des frisch geformten Betonstreifens während der Wärmebehandlung;
Vibrationsmesser zum Schneiden von massivem Rohbeton;
Sägen mit Diamanttrennscheibe zum Schneiden von Hartbeton;
eine selbstfahrende Hebe- und Transportmaschine mit pneumatischen Saugnäpfen zum Entnehmen fertiger Produkte vom Ständer und zum Transportieren;
Standreinigungsmaschine;
Anlage für Heizöl (Kühlmittel) Typ MT-3000 (Heinz) oder HE-2500 (Kärcher).
Darüber hinaus muss die Produktionslinie über einen speziellen Posten zum Waschen der Formeinheit verfügen.
1.4. Die Besonderheit des Formens besteht darin, dass die Formeinheit in Form eines Portals hergestellt ist, auf dem sich Abgabetrichter, dreistufige Verdichtungsvibrationselemente, bewegliche Hohlraumbildner, formbildende und trennende bewegliche Elemente, ein Schmier- und Plastifizierungssystem des Ständers usw. befinden steuert, ist montiert und lässt sich mithilfe einer einstellbaren hydraulischen Seilspannvorrichtung reibungslos bewegen. In diesem Fall platziert und drückt die Formeinheit mithilfe einer automatischen Vorrichtung die obere Querstabverstärkung und glättet die offene Oberfläche des Produkts.
1.5. Die Formeinheit ermöglicht durch entsprechende Nachjustierung die Herstellung von Produkten unterschiedlicher Breite und Dicke. In diesem Fall darf die Gesamtbreite der geformten Produkte 3,6 m nicht überschreiten, die Höhe 30 cm nicht überschreiten.
1.6. Für die Herstellung von Produkten können Betonmischungen mit einer Härte von 20 - 40 s (GOST 10181 -81) verwendet werden.
2. TECHNOLOGIE ZUR HERSTELLUNG VON STAHLBETONSTRUKTUREN MITTELS FORMLOSER VERFAHREN
Anforderungen an die Betonmischung
2.1. Das Formen von Hohlkammerplatten und Massivplatten erfolgt aus einer Betonmischung auf einem dichten Zuschlagstoff mit einer Betonqualität für eine Druckfestigkeit von 300 – 500.
2.2. Zum Formen von Hohlkernplatten und Massivplatten können Betonmischungen mit einer Härte von (25 ± 5) s gemäß GOST 10181-81 bei einer Formgeschwindigkeit (1,0) verwendet werden± 0,2) m/min.
2.3. Zur Herstellung von Beton sollten Sie Zement mit einer normalen Zementleimdichte (NGCT) von nicht mehr als 27 % verwenden. Die Verwendung von Zementen mit einem höheren NGCT kann zu einer Verletzung des Sand-Zement-Verhältnisses und damit zu einer schlechten Formbarkeit der Mischung führen.
2.4. Sand muss den Anforderungen von GOST 10268-70 entsprechen. Das Vorhandensein von Körnern größer als 10 mm im Sand ist nicht zulässig.
Die Festigkeit des Zuschlagstoffs muss mindestens das Zweifache der Festigkeit von Beton betragen.
2.6. Um die Anforderungen an die Steifigkeit der Betonmischung und die Festigkeit des Betons zur Berechnung und Anpassung der Zusammensetzung der Betonmischung zu erfüllen, ist es notwendig, folgende Eigenschaften der Rohstoffe zu ermitteln:
für Zement
Aktivität R c , MPa - in jeder Charge;
NGNT,% - 1 Mal pro Schicht;
Dichte ρ, g/cm 3 – für jede Zementart;
für Sand
Schüttdichte G , kg/m 3 - 1 Mal pro Schicht;
Standard (Standardabweichung) von Körnern größer als 5 mm pro Schicht, % – in jeder Charge;
Größenmodul Mcr - 1 Mal pro Schicht;
Kontamination (Auswaschung), % – einmal pro Schicht;
natürliche Luftfeuchtigkeit, % – einmal pro Schicht;
für Schotter
Dichte ρ, g/cm 3 – für jeden Steinbruch;
Schüttdichte G , kg/m 3 - 1 Mal pro Schicht;
Standard für Körner größer als 5 mm pro Schicht, % – in jeder Charge;
Verschmutzung, % – einmal pro Schicht;
Festigkeit (Krümelbarkeit), MPa – in jeder Charge;
natürliche Luftfeuchtigkeit, % - einmal pro Schicht.
Basierend auf den erhaltenen Eigenschaften berechnet das Werkslabor die Zusammensetzung der Betonmischung unter Berücksichtigung der in den Absätzen dargelegten Bestimmungen. - diese Empfehlungen.
Ш = Шр - 0,01 Ш р · (к + F), (2)
wohin und F- Standards für Körner größer als 5 mm pro Schicht in Schotter und Sand, %;
Шр – geschätzte Menge Schotter, kg.
In diesem Fall wird der Verbrauch an gemischtem Sand P cm und gemischtem Schotter Sh cm durch die Formeln bestimmt
(3)
wo mit und D- bzw. die Menge an Sand in Schotter und Schotter in Sand, %;
Ø cm = Ø + П - П cm. (4)
2.10. Anpassung des Materialverbrauchs in Abhängigkeit vom Feuchtigkeitsgehalt der Zuschlagstoffe W, dem Vorhandensein von Sand im Schotter und Schotter im Sand sowie der Aktivität von Zement R ts , NGCT, Schotterhohlräume A wird durchgeführt, wenn der bei der Prüfung neu ermittelte Wert wie folgt vom zuvor verwendeten Wert abweicht:
W - um ± 0,2 %; R - um ± 2,5 MPa; NGCT – um ± 0,5 %;
a - um ± 1,0; M cr - um ± 0,1.
2.11. Die Festigkeit von Beton wird durch die Ergebnisse der Prüfung von Würfelproben bestimmt, die aus einer Kontrollbetonprobe mit einem Gewicht geformt wurden, dessen spezifischer Druck 4 × 10 –3 MPa beträgt. Die volumetrische Masse frisch geformter Proben muss mit einer Toleranz der theoretischen (berechneten) volumetrischen Masse entsprechen± 2 %. Kontrollwürfel werden zusammen mit dem Produkt auf dem Ständer gedämpft.
Die Prüfung der Proben zur Festigkeitsbestimmung erfolgt im heißen Zustand (3 Proben pro Stand).
2.12. Das Formen von Wandpaneelen und Blöcken erfolgt aus Betonmischungen auf porösem Zuschlagstoff, wobei folgende Betone verwendet werden: Baubeton – Güteklassen M150 – M200, Bau- und Wärmedämmung – Güteklassen M50 – M100 und Wärmedämmung – Güteklassen M15 – M25.
2.13. Bei der Herstellung von strukturellem und wärmedämmendem Leichtbeton der Sorten M50 – M100 wird eine Mischung aus Blähtonkies mit einem Anteil von 5 – 10 mm einer Sorte mit einer Rohdichte von nicht mehr als 500 und einem Anteil von 10 – 20 mm einer Sorte verwendet Es sollte Blähtonsand mit einer Schüttdichte von höchstens 800 verwendet werden, der den Anforderungen von GOST 9759-76 entspricht.
Für die Herstellung einer Wärmedämmschicht aus grobporigem Beton M15 - M25 wird die Verwendung von Blähtonkies der Fraktionen 10 - 20 mit einer Rohdichte von maximal 350 empfohlen.
Bei der Herstellung von strukturellem Blähtonbeton der Sorten M150 – M200 ist es erforderlich, Blähtonkies mit einer Fraktion von 5 – 10 mm und einer Güteklasse von nicht geringerer Festigkeit zu verwenden H125.
2.14. Die Verarbeitbarkeit der Betonmischung für strukturellen Blähtonbeton sollte durch eine Härte im Bereich von 20 - 40 s gemäß GOST 10181-81 gekennzeichnet sein.
2.15. Die Arbeitsdosierung der zu mischenden Materialien wird vom Werkslabor mindestens einmal pro Schicht ausgegeben, wobei eine Überprüfung der Härte der Betonmischung der ersten Chargen obligatorisch ist.
2.16. Die Dosierung von Zement, Wasser und Zuschlagstoffen muss gemäß GOST 7473-76 erfolgen.
Die Dosierung von Blähtonkies und porösem Sand sollte nach der volumetrischen Gewichtsmethode erfolgen, wobei die Mischungszusammensetzung auf der Grundlage der Überwachung der Schüttdichte von groben porösen Zuschlagstoffen und Sand in einem Wiegespender angepasst werden muss.
2.17. Es wird empfohlen, die Betonmischung für schweren Konstruktions- und strukturwärmedämmenden Leichtbeton in Zwangsmischern vorzubereiten.
Die Vorbereitung der Betonmischung für die Wärmedämmschicht aus grobporigem Beton sollte in schwerkraftbetriebenen Betonmischern erfolgen.
2.18. Die Mischdauer einer Betonmischung einer bestimmten Härte wird vom Werkslabor gemäß GOST 7473-76 ermittelt und genau eingehalten± 0,5 Min.
2.19. Der Mischbetrieb wird mindestens zweimal pro Schicht überwacht.
2.20. Die Härte der aus jedem Betonmischer kommenden Betonmischung wird während der Bildung eines Bestandes mindestens dreimal überprüft.
Vorbereitung der Stände
2.21. Nach der Entnahme der fertigen Produkte erfolgt die Reinigung des Standes, indem eine Reinigungsmaschine entlanggefahren wird, die mit einem Kran am Stand montiert ist.
2.22. Die Reinigungsmaschine kann in zwei Modi betrieben werden:
„normale Reinigung“ – beim Reinigen des Standes ohne getrockneten Beton;
„Vollbürstenmodus“ – wenn sich Reste von getrocknetem Beton auf dem Ständer befinden.
2.23. Für die Reinigung große Menge Um den restlichen Rohbeton zu entfernen, wird ein spezieller Schaber in Form eines Eimers mit Seitenwänden an die Reinigungsmaschine gehängt. Zur Reinigung von Festbeton, der stark am Untergrund haftet, wird ein an der Maschine aufgehängter Abstreifbalken eingesetzt. Die Geschwindigkeit der Maschine ist so gewählt, dass der Ständer in einem Durchgang der Maschine gereinigt wird.
2.24. Ein Bestand mit einer kleinen Menge kleiner Reste von Betonkrümeln wird mit einem Wasserstrahl gereinigt, der aus einem unter Druck stehenden Schlauch zugeführt wird.
Bewehrung verlegen und spannen
2,25. Nach der Standreinigung werden die Beschläge verlegt. Der Draht (Litzen) wird mit einem selbstfahrenden Bewehrungsspreizer gezogen, der aus drei oder sechs Spulenhaltern besteht, die sich hinter den Ständern an der Seite der Gruppenhydraulikheber befinden.
Der selbstfahrende Bewehrungsverteiler muss sich mit einer Geschwindigkeit von 30 m/min über den Ständer bewegen.
Die Bewehrung wird manuell an den Anschlägen an den Ständerenden befestigt.
2.26. Ein am Ständer befestigter Drahtstrang (Litzen) wird mit einem einzigen hydraulischen Wagenheber am passiven Ende des Ständers angezogen, bis die Installationsspannung der Bewehrung 90 % der angegebenen Kraft beträgt.
Der Vorgang wird wiederholt, bis die Einbauspannung aller Bewehrungselemente erreicht ist.
2.27. Nach dem Spannen der Bewehrung müssen Schutzklammern am Ständer angebracht werden, falls die Bewehrungselemente beim endgültigen Spannen brechen.
2.28. Die Spannung des gesamten Bewehrungspakets auf 100 % der vorgegebenen Kraft erfolgt über einen Gruppen-Hydraulikheber am aktiven Ende des Ständers, nachdem darauf eine selbstfahrende Formeinheit montiert und für den Betrieb vorbereitet wurde.
Der gesamte Vorgang muss gemäß den Anweisungen von Max Roth durchgeführt werden.
Formen
2.29. Die Umformeinheit wird mit einem Kran am passiven Ende des Standes montiert; Auf dem Gerät sind Aufnahmetrichter installiert, und das Stromversorgungskabel und das Kabel des Seilspannsystems werden mit einem Bewehrungswagen zum aktiven Ende des Ständers geführt und jeweils am elektrischen Anschluss und der dahinter befindlichen speziellen Anschlaghalterung befestigt die hydraulischen Heber der Gruppe.
2.30. Die Einstellung und Einstellung der Umformeinheit erfolgt auf der Grundlage der Anweisungen zur Wartung der Umformeinheit, die in der technischen Dokumentation der vom Hersteller gelieferten Geräte enthalten sind, sowie gemäß diesen Empfehlungen.
2.31. Die Hohlkörper müssen so eingebaut werden, dass der Abstand von der Standfläche bis zur Unterkante des hinteren Teils der Hohlkörper dem Design im Produkt entspricht und im vorderen Teil 2 mm höher ist. Die Rückseite der Seiten- und Trennwände sollte 1 mm über dem Ständer angebracht werden, die Vorderseite 2 mm.
2.32. Vibrationsverdichter der Stufe 1 werden entsprechend der Dicke der Basis der herzustellenden Platten installiert. Der vordere Teil der durch Gummistoßdämpfer gestützten Stangen sollte 5 mm höher angebracht werden als der hintere Teil. In diesem Fall sollte der hintere Teil der Vibrationsverdichter der 1. Stufe 5 mm von der Unterseite der ihnen folgenden Hohlraumbildner abgesenkt werden.
2.33. Die Vibrationsverdichter der 2. Stufe werden so eingebaut, dass sich ihr hinterer Teil in einem Abstand von 5 mm über den Hohlraumbildnern befindet.
Der Neigungswinkel der Vibrationsverdichter wird in Abhängigkeit von der Plattendicke und der Konsistenz der Betonmischung gewählt.
2.34. Eine mechanische Stopfvorrichtung zum Einbetten der Querbewehrung muss in der unteren Position 10 mm über der Oberkante des Formprodukts installiert werden. Die Kontrollmarke ist in diesem Fall der hintere Teil der Vibrationsverdichter der 3. Stufe oder die Oberfläche des Stahlblechs der Ständer.
2,35. Die Platten, auf denen die Vibrationsverdichter der 3. Stufe befestigt sind, müssen horizontal installiert und durch Gummistoßdämpfer abgestützt werden. In diesem Fall nimmt die Arbeitsverdichtungsplatte im Kontakt mit der Betonmischung die vorgesehene Schräglage ein.
2.36. Ein Bunkerblock mit einer Gesamtkapazität von 10 m 3 mit einer automatischen Vorrichtung zum Laden der Betonmischung und zum Zuführen der Mischung in Dosierbunker wird mit einem Laufkran auf dem Portal der Formmaschine installiert und mit Bolzen befestigt.
2.37. Vor Beginn des Formens muss die Funktionsfähigkeit aller drei Stufen der Vibrationsverdichtung, der Hohlraumformer, der Seiten- und Trennwände sowie des Mechanismus zur automatischen Zufuhr der Betonmischung im Leerlauf überprüft werden.
2,38. Die Rotation der Rüttler aller drei Verdichtungsstufen sollte in Richtung der Bewegung der Formmaschine erfolgen. Stimmt die Drehrichtung nicht überein, müssen die Phasen getauscht werden.
2.39. Beim Anpassen der Position der Seiten und Trennwände, die die Seitenkanten der Produkte bilden, muss ausgeschlossen werden, dass die Seiten während des Formvorgangs mit dem Ständer in Berührung kommen. Der Einbau von Seitenwänden und Trennwänden erfolgt individuell Hochpunkt aller Gerüste, um zu bestimmen, welche Formeinheit sich nach deren Installation vor dem Probeformen nacheinander über alle Gerüste bewegt.
2,40. Der Abstand zwischen den Vibrationsverdichtern der 2. Stufe und der gespannten oberen Bewehrung sollte (20) betragen± 5) mm.
2.41. Bevor mit dem Formen begonnen wird, wird das Gerät in seiner ursprünglichen Position am Anfang des passiven Endes des Ständers installiert; Die Trichter des automatischen Lademechanismus werden mithilfe eines Brückenkrans mit Betonmischung gefüllt, die aus einem Eimer zugeführt wird.
2.42. Vor Beginn der Umformung wird eine Vorrichtung zur Abstützung und Fixierung der beanspruchten Bewehrung installiert. Der Einbau erfolgt in einer solchen Position der Formeinheit, wenn der Abstand zwischen dem Einfülltrichter der 1. Verdichtungsstufe und den Bewehrungsabstandshaltern 100 - 150 mm beträgt. Die Richtung der Drähte (Litzen) muss mit der Richtung der Ständerachse übereinstimmen; Passen Sie ggf. die Position der Führungsschienen an.
2.43. Während des Formvorgangs muss die Betonmischung den Vorratstrichtern aller drei Verdichtungsstufen in einer Menge zugeführt werden, die 1/3 des Trichtervolumens entspricht, was eine konstante Unterstützung bietet, die für die gleichmäßige Zufuhr der Mischung während der Verdichtung erforderlich ist Elemente der Maschine. Wenn in den Vorratsbehältern kein Mischungsstau vorhanden ist, wird die Mischung in unzureichenden Mengen unter die Verdichtungselemente geliefert, was zu einer Unterverdichtung des Betons in den Produkten führt.
2.44. Die Dosierung der Mischung aus den Vorratsbehältern erfolgt über Schieber an der Rückwand der Behälter mit Schiebehebeln.
Die Hin- und Herbewegung der Dosiertrichter der 2. und 3. Stufe sollte auf 20–30 Zählimpulse/Minute eingestellt werden. In diesem Fall muss der 3. Verdichtungsstufe eine solche Menge Betonmischung zugeführt werden, dass vor den Vibrationsverdichtern eine kleine Walze entsteht. Dieser Anforderung wird durch die Dosierung des Gemisches aus dem Trichter der 3. Stufe sowie durch eine Neuanordnung der mechanischen Verdichtungsvorrichtung in der Höhe entsprochen.
2,45. Das Formen der Produkte muss kontinuierlich über den gesamten Stand erfolgen, ohne dass die Formeinheit angehalten werden muss. Die Formgeschwindigkeit sollte je nach Steifigkeit der Mischung und Höhe des Formprodukts experimentell ausgewählt werden und kann mit 0,5 - 2,0 m/min angenommen werden.
Beim Formen von Hohlkammerplatten aus Betonmischungen mit der Härte (25± 5) mit empfohlener Geschwindigkeit (1,0± 0,2) m/min. Beim Formen von dreischichtigen Wandplatten mit einer Dicke von 250 – 300 mm aus Betonmischungen mit einer Härte von 20 – 40 s wird eine Geschwindigkeit von 1,0 – 1,5 m/min empfohlen.
Die Gesamtdauer der Formung eines 150 m langen Ständerstreifens sollte 3 Stunden nicht überschreiten und die Festigkeit der zu Beginn des Betonierens geformten Würfelproben vor der Wärmebehandlung sollte 0,5 MPa nicht überschreiten.
2.46. Bei der Bildung von Mehrschichtplatten aus Blähtonbeton wird der hintere Teil der Vibrationsverdichter der 1. Stufe gemäß der Produktzeichnung über der Standfläche in einem Abstand installiert, der der Dicke der unteren Strukturschicht des Produkts entspricht; Der Schieber des Dosiertrichters sollte 100 - 120 mm über der unteren Bauschicht angebracht werden.
2.47. Der hintere Teil der Vibrationsverdichter der 2. Stufe wird 10 mm über der vorgeschriebenen Wärmedämmschicht installiert, und der Schieber des Dosiertrichters wird 50 - 60 mm installiert.
In diesem Fall müssen die Rüttler der 2. Verdichtungsstufe abgeschaltet werden.
2,48. Der hintere Teil der Vibrationsverdichter der 3. Stufe wird über der Ständeroberfläche in einem Abstand installiert, der der Dicke des Produkts entspricht, und das Tor des Dosiertrichters befindet sich 100 - 120 mm über der Produktoberfläche.
2,49. Die Behandlung des Ständers mit OE-2-Schmiermittel und die Plastifizierung der unteren Schicht der Betonmischung mit Wasser erfolgt mit speziellen Geräten, die im vorderen Teil der Formeinheit installiert sind.
2,50. Vor Abschluss der Ausformung, 2 m vor der Ständerkante, ist es notwendig, die Leisten der Führungsvorrichtungen der Bewehrung zu entfernen. Die Betonmischung muss gleichmäßig in die Trichter der Beschickungseinrichtung und die Vorratstrichter eingefüllt werden, sodass sie am Ende des Formens vollständig verbraucht ist.
2.51. Nach Abschluss des Formvorgangs wird das Gerät in die Nähe der Spannseil-Drehvorrichtung bewegt, seine Bewegung stoppt und alle Funktionskomponenten des Geräts werden ausgeschaltet.
2,52. Nach Abschluss des Formvorgangs an jedem Stand wird die Formeinheit an einer speziell ausgestatteten Waschstation mit einem Hochdruckwasserstrahl gewaschen.
Nach der Arbeitsschicht wird die Formeinheit gründlich gewaschen. Zuvor empfiehlt es sich, die 2. und 3. Stufe der Dichtung zu demontieren. Mechanische Einwirkungen (Klopfen) sind verboten. Alle Mechanismen und Motoren müssen vor dem Waschen abgedeckt werden.
Formfehler und deren Beseitigung
2.53. Gebrochener Draht (Litze). Überprüfen Sie, ob eine der drei Dichtungsstufen Kontakt mit dem Draht hat. Andernfalls besteht die Gefahr, dass sich der Draht im verdichteten Beton verfängt und bricht.
2.54. Verlust der Haftung der Litze am Beton oder Abweichung von der Sollposition. Es ist zu prüfen, ob sich die Drähte (Litzen) und Vibrationsverdichter der 2. Stufe nicht berühren und ob Füllstoffe mit einer Fraktion von mehr als 10 mm in die Betonmischung gelangen.
2.55. Rauheit der Plattenoberseite und Querrisse. Es wird empfohlen, die Konsistenz der Betonmischung mit der erforderlichen Konsistenz sowie die Einhaltung der erforderlichen Geschwindigkeiten beim Formen und Dosieren der Betonmischung für die 3. Verdichtungsstufe zu überprüfen.
2.56. Risse auf der Unterseite der Paneele. Beim Einbau der Vibrationsverdichter der 1. Stufe muss der Neigungswinkel überprüft werden. Bei einem großen Neigungswinkel nimmt die horizontale Komponente bei der Bewegung des Arbeitselements zu und kann zu Unstetigkeiten führen (übersteigt die Haftkraft der Betonmischung am Ständer).
Die Position der Vibrationsverdichter der 1. Stufe im Verhältnis zu den Hohlraumbildnern sollte überprüft werden. Bei falscher Montage zerstören Hohlraumbildner den bereits verdichteten Plattenuntergrund.
2.57. Bildung von Rissen an den Seitenkanten der Paneele. Es empfiehlt sich, die Bewegungsgeschwindigkeit der Seiten- und Trennelemente zu überprüfen und ggf. anzupassen.
Sie sollten prüfen, ob die Seiten und Trennelemente Kontakt zum Ständer haben.
2.58. Unzureichende Verdichtung der Wände zwischen Hohlräumen. In der 2. Verdichtungsstufe sollten Sie die Dosierung der Betonmischung überprüfen. Es wird empfohlen, den Neigungswinkel der Vibrationsverdichter der 2. Stufe und deren Funktion zu überprüfen.
2,59. Bei der Überprüfung der Funktion von Vibrationsverdichtern müssen Sie sicherstellen, dass alle Rüttler funktionstüchtig sind.
Die Schwingungsamplitude der Dichtungen sollte betragen:
für die 1. Stufe - 0,9 - 1,0 mm;
für die 2. Stufe - 0,7 - 0,8 mm;
für die 3. Stufe - 0,3 - 0,35 mm.
Wärmebehandlung
2,60. Während der Formungszeit sorgt das in einer Ölheizanlage auf 100 °C erhitzte und in den Registern des Ständers zirkulierende Öl dafür, dass die Temperatur der Stahlbleche des Ständers mindestens 20 °C beträgt.
2.61. Nach Abschluss der Formung und Beschichtung des frisch geformten Betons mit einer wärmeisolierenden Decke wird die Öltemperatur für 7 Stunden auf 170 – 200 °C erhöht, was eine Standtemperatur von etwa 90 °C gewährleistet, und der Beton wird auf 65 °C erhitzt - 70 °C.
Die Betontemperatur während der Wärmebehandlungsperiode wird anhand von Diagrammen der Beziehung zwischen der Öltemperatur im System und der Betontemperatur basierend auf den Öltemperaturmesswerten auf dem Bedienfeld der Ölheizeinheit gesteuert.
2,62. Die isotherme Erwärmung erfolgt 7 Stunden lang, wobei die Öltemperatur allmählich auf 100 °C absinkt.
2,63. Das Abkühlen von Produkten vor der Spannungsübertragung auf den Beton ist nicht zulässig [siehe. „Leitfaden zur Wärmebehandlung von Beton und Stahlbetonprodukten“ (Moskau, 1974)]. Es wird empfohlen, die Druckkräfte spätestens 0,5 Stunden nach Ende der Isotherme und Prüfung der Kontrollproben auf den Beton zu übertragen. In diesem Fall sollte die Temperatur des Betons um nicht mehr als 15 – 20 °C gegenüber der Temperatur des Betons bei isothermer Erwärmung gesenkt werden.
2,64. Während der Wärmebehandlung werden der Ständer und die Bewehrung beim Ausfahren durch eine automatische Vorrichtung gespannt, die an Gruppenhydraulikzylindern montiert ist, und zwar durch die Aktivierung eines Endschalters und einer automatischen Vorrichtung zur Aufrechterhaltung der Spannkraft der Bewehrung. Es wird empfohlen, die Betriebszeit der Maschine über ein Zeitrelais auf 3 Minuten einzustellen.
Produkte schneiden und transportieren
2,65. Die Spannung wird mithilfe eines Gruppenhydraulikhebers am aktiven Ende des Ständers gelöst und anschließend wird die Bewehrung am passiven Ende des Ständers abgeschnitten.
2,66. Das Schneiden eines Betonstreifens in Produkte einer bestimmten Länge erfolgt mit einer Säge mit Diamanttrennscheibe, beginnend am passiven Ende des Ständers. Es besteht die Möglichkeit, Schleifscheiben zu verwenden. Die Zeit für einen Querschnitt einer 3,6 m breiten Betonmasse beträgt 5 Minuten.
2,67. Mit einer selbstfahrenden Hebe- und Transportmaschine mit pneumatischen Saugnäpfen werden die Produkte aus dem Ständer entnommen und am freien Ende des Ständers bzw. dessen Verlängerung gelagert.
2,68. Der Weitertransport der Produkte zu einem Umzugswagen oder -fahrzeug erfolgt mit einem Laufkran unter Verwendung einer speziellen balkenlosen Hebetraverse.
Qualitätskontrolle der fertigen Produkte
2,69. Die Qualitätskontrolle der fertigen Produkte erfolgt durch die technische Kontrollabteilung des Werks auf Basis der aktuellen Regulierungsdokumente(Spezifikationen, Ausführungszeichnungen) und diese Empfehlungen.
2,70. Die Abweichung der Abmessungen von Hohlkammerplatten sollte Folgendes nicht überschreiten:
in Länge und Breite -± 5 mm;
Dicke - ± 3 mm.
2,71. Die Dicke der Betonschutzschicht bis zur Arbeitsbewehrung muss mindestens 20 mm betragen.
2,72. Die Platten müssen gerade Kanten haben. Bei einzelnen Paneelen darf die Krümmung der Boden- oder Seitenfläche auf einer Länge von 2 m nicht mehr als 3 mm und auf der gesamten Länge des Paneels nicht mehr als 8 mm betragen.
2,73. An der Unterseite (Decke) der Paneele dürfen sich keine Senken befinden. Auf der Ober- und Seitenfläche der Paneele sind separate kleine Aussparungen mit einem Durchmesser von höchstens 10 mm und einer Tiefe von bis zu 5 mm zulässig.
2,74. Einstürzen der Paneele sowie das Verfüllen von Hohlräumen mit Beton sind nicht zulässig.
2,75. Die Paneele werden ohne verstärkte Enden hergestellt.
2,76. Das Aussehen der Paneele muss folgende Anforderungen erfüllen:
die untere (Decken-)Oberfläche muss glatt und zum Streichen ohne zusätzliche Nachbearbeitung vorbereitet sein;
auf der unteren (Decken-)Oberfläche der Paneele, lokales Durchhängen, Fett und Rostflecken und offene Luftporen mit einem Durchmesser und einer Tiefe von mehr als 2 mm;
Späne und Durchhängen entlang der Längsunterkanten der Platten sind nicht zulässig;
An den horizontalen Kanten der Plattenenden sind Betonsplitter mit einer Tiefe von mehr als 10 mm und einer Länge von 50 mm pro 1 m Platte nicht zulässig;
Risse sind nicht zulässig, mit Ausnahme von Schwindrissen an der Oberfläche mit einer Breite von nicht mehr als 0,1 mm;
Ein Verrutschen der beanspruchten Bewehrung ist nicht akzeptabel.
2,77. Abweichungen von den Konstruktionsmaßen der Wandpaneele sollten Folgendes nicht überschreiten:
nach Länge
für Paneele bis 9 m Länge - +5, -10 mm;
für Paneele länger als 9 m - ± 10 mm;
in Höhe und Dicke - ± 5 mm.
2,78. Der Unterschied in den Paneldiagonalen sollte Folgendes nicht überschreiten:
für Paneele bis 9 m Länge - 10 mm;
für Paneele länger als 9 m - 12 mm.
2,79. Die Nichtebenheit der Paneele, die durch die größte Abweichung einer der Ecken des Paneels von der durch drei Ecken verlaufenden Ebene gekennzeichnet ist, sollte Folgendes nicht überschreiten:
für Paneele länger als 9 m - 10 mm.
2,80. Die Platten müssen gerade Kanten haben. Die Abweichung von der Geraden des tatsächlichen Oberflächenprofils und der Plattenkanten sollte auf einer Länge von 2 m 3 mm nicht überschreiten.
Über die gesamte Plattenlänge sollte die Abweichung nicht größer sein als:
für Paneele bis 9 m Länge - 6 mm;
für Platten länger als 9 und - 10 mm.
2,81. Dolinen, Luftporen, lokale Durchbiegungen und Vertiefungen auf der zu lackierenden Plattenoberfläche sollten nicht größer sein als:
im Durchmesser - 3 mm;
in der Tiefe - 2 mm.
2,82. Fett- und Rostflecken auf der Oberfläche der Produkte sind nicht zulässig.
2,83. Betonrippen mit einer Tiefe von mehr als 5 mm auf den Stirnflächen und 8 mm auf den Nicht-Stirnflächen und einer Gesamtlänge von mehr als 50 mm pro 1 m der Platte sind nicht zulässig.
2,84. Risse in den Platten sind nicht zulässig, mit Ausnahme lokaler einseitiger Schwindrisse mit einer Breite von nicht mehr als 0,2 mm.
2,85. Der Feuchtigkeitsgehalt von Beton in Platten (in Gewichtsprozent) sollte 15 % für Beton auf porösem Kies und 20 % für Beton auf porösem Schotter nicht überschreiten.
Der Feuchtigkeitsgehalt des Betons in den Platten wird vom Hersteller mindestens einmal im Monat überprüft.
Wandpaneele fertigstellen
2,86. Die Textur von Wandpaneelen wird mit speziellen Geräten erzielt. Das Auftragen eines Zement-Sand-Endmörtels auf die Oberfläche eines Betonstreifens und die Erzielung einer glatten Vorderseite der Produkte erfolgt mithilfe einer an der Formeinheit angebrachten Endbearbeitungseinheit, die aus einem Mörteltrichter und Glättstangen besteht.
2,87. Bei der dekorativen Reliefveredelung von Produkten mit Zementsandmörtel sind die „Anleitungen zur Veredelung der Fassadenoberflächen von Paneelen für Außenwände“ (VSN 66-89-76) zu beachten.
3. SICHERHEIT
3.1. Im Werk, in dem die Produktion von vorgefertigten Stahlbetonkonstruktionen im formlosen Verfahren auf linearen Gerüsten organisiert ist, werden alle Arbeiten gemäß den „Regeln für Sicherheit und Betriebshygiene in Fabriken und Werksgeländen für Stahlbetonprodukte“ (M ., 1979) sowie Kapitel SNiP III-16-80 „Beton und Stahlbetonkonstruktionen vorgefertigt.“
3.2. Besondere Sicherheitsregeln bei der Durchführung einzelner technologischer Arbeiten (Heizen von Öl, Verlegen und Spannen von Bewehrungen auf einem Ständer, Schneiden von Fertigprodukten usw.) sind in besonderen Anweisungen für die Durchführung dieser Arbeiten festgelegt, die in der technischen Dokumentation der Ausrüstung enthalten sind und mitgeliefert werden mit der Ausrüstung vom Werk - dem Hersteller.
3.3. Besondere Sicherheitsregeln müssen auf Plakaten in der Werkstatt vermerkt sein.
3.4. Das Personal, das das Werk betritt, muss eine spezielle Schulung zur Technik der Durchführung von Arbeiten am Stand absolvieren, eine Prüfung bestehen und sich vierteljährlich einer Unterweisung unterziehen.
3.5. Bei Arbeiten an einer Ölheizungsanlage sind die „Empfehlungen zur Reduzierung“ zu beachten Feuergefahr Anlagen mit aromatisiertem Kühlöl AMT-300“ (M., 1967).