Wie baut man ein Schweißgerät? Heimwerkergeräte zum Schweißen: Berechnung, Diagramme, Herstellung, Kontakt und Punkt
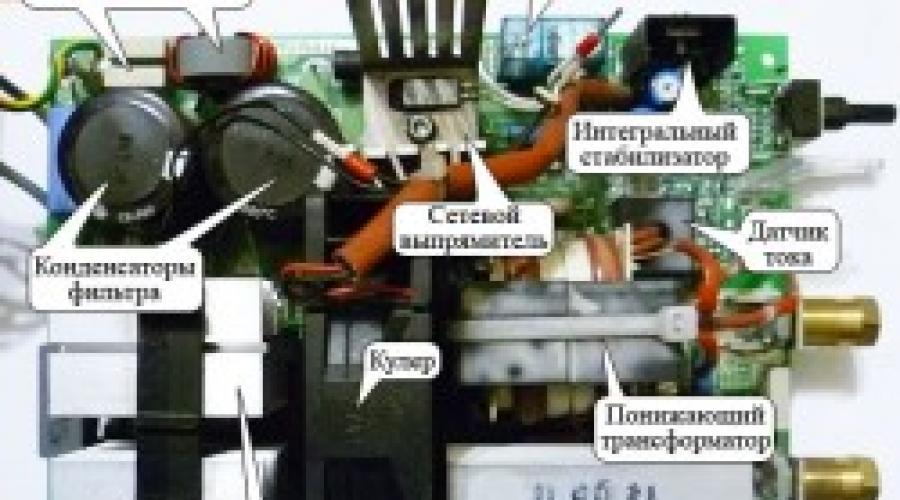
Beim Bau, bei der Installation und bei der Reparatur ist es schwierig, auf ein Schweißgerät zu verzichten. Normalerweise wird die Ausrüstung fertig gekauft. Sie können jedoch auch einen anderen Weg gehen: Bauen Sie selbst ein Schweißgerät, denn ein selbstgebautes Gerät spart erheblich Geld und wird zu einer unterhaltsamen Aktivität für diejenigen, die gerne basteln.
Über Verbindungsmethoden, Wicklungen und Elektroden
Existieren Verschiedene Arten Schweißgeräte. Der häufigste Fehler, den unerfahrene Handwerker machen, ist der Wunsch, sofort ein komplexes Gerät herzustellen. Schemata für die Herstellung einer Schweißmaschine können leicht im Internet gefunden werden; am besten gibt man der Art von Ausrüstung den Vorzug, deren Herstellung keine nennenswerten Schwierigkeiten bereitet und nicht viel Zeit in Anspruch nimmt. Die Reparatur Ihres eigenen Schweißgeräts wird für die Person, die das Gerät hergestellt hat, keine großen Probleme und erheblichen Kosten mit sich bringen.
Es stellt sich sofort die logische Frage: Welches Schweißgerät? wäre besser geeignet für die Arbeit zu Hause? Nur kleine Größe. Die optimale Lösung des Problems wäre, ein Gerät aus Geräten zu erstellen, die dem Handwerker bereits zur Verfügung stehen. Für die Arbeit benötigen Sie einen dreiphasigen Transformator. Die primären müssen verbunden werden. Bei einem Schweißgerät erfolgt dies am magnetischen Kreis mit einem „Dreieck“. Diese Methode wird nur für ein Gerät verwendet, das an ein Drehstromnetz mit einer Spannung von 380/220 V angeschlossen werden soll.
Die Stromversorgung und die konkrete Gestaltung des Gerätes sind die Aufgaben, die zunächst geklärt werden müssen. Wenn Essen und Interne Organisation Wenn Geräte nicht einander entsprechen, führt dies dazu, dass Geräte, deren Herstellung Zeit und Mühe gekostet hat, eine Gefahr für das Leben und die Gesundheit von Menschen darstellen. Soll das Schweißgerät aus einem einphasigen 220-V-Netz gespeist werden, muss der Anschluss der Primärwicklung des Transformators anders erfolgen. Die äußersten Stäbe der Magnetkerne des Geräts sind antiparallel verbunden. Für ein solches Schweißgerät wird ein anderes Prinzip der Befestigung der Sekundärwicklungen verwendet: ein fester Stromkreis.
Wird das Gerät aus einem einphasigen 220-V-Netz gespeist, unterscheidet es sich auch in den Merkmalen der Zusatzwicklung. Es wird auf alle Windungen des elektrischen Kabels gewickelt, über das das Schweißgerät verfügt. Wofür ist das? Beim Schweißen kommt es zu sprunghaften Änderungen des Schweißstroms. Sie benötigen einen Ballast, dessen Rolle die zusätzliche Wicklung übernimmt. Seine Besonderheit: 40-50 Umdrehungen. Für ein kleines Schweißgerät ist eine zweistufige Regelung der elektrischen Leistung am besten geeignet.
Anfänger wählen oft die falsche Elektrodengröße für das Gerät.
Um ein Gleichstromschweißgerät selbst herzustellen, benötigen Sie eine Hochleistungsstromquelle, die in der Lage ist, die Nennspannung eines herkömmlichen Einphasennetzes umzuwandeln und bereitzustellen konstanter Wert der entsprechende Strom. Dies ist notwendig, damit ein normaler Lichtbogen entstehen und aufrechterhalten werden kann.
Für ein Hochleistungsnetzteil sind folgende Komponenten erforderlich:
- Gleichrichter.
- Wechselrichter.
- Strom- und Spannungswandler.
- Strom- und Spannungsregler (zur Verbesserung der Qualitätsmerkmale des Lichtbogens selbst).
- Hilfsgeräte.
Es gibt eine einfache Regel, die Ihnen bei der richtigen Wahl hilft: Je stärker das Stromnetz und je dicker die elektrischen Leitungen, desto größer sollte die Elektrode sein.
Hauptkomponenten der Schweißmaschine:
- Magnetkreis des Transformators.
- Primärwicklungen.
- Sekundärwicklungen.
- Zusätzliche Wicklung.
- Fernkondensatoren.
- Schweißmodusschalter.
- Kontakttemperatursensor und Alarmtongerät.
- Schweißmodusschalter.
Zurück zum Inhalt
Warum wird Beton benötigt?
Das Gehäuse der Schweißmaschine ist ein wichtiges Thema. Für die Herstellung von Gehäusen solcher Geräte wird üblicherweise speziell vorbereiteter Beton verwendet. Er muss haben guter Indikator Plastizität. Geeignet ist diejenige, die am leichtesten die gewünschte Form annimmt und in kürzester Zeit aushärtet.
Für den Rumpf werden feiner Sand und Zement benötigt. Die erste sollte 75 % der Trockenbetonmischung ausmachen, die zweite sollte ein Fünftel davon ausmachen. Die restlichen 5 % der Trockenmischung sind PVA-Kleber und Glaswolle im Verhältnis 1:1. Anstelle von Kleber können Sie auch wasserlöslichen Latex verwenden.
Viele unerfahrene Handwerker glauben, dass die Herstellung einer Schweißmaschine viel einfacher ist als die Herstellung ihres Gehäuses. Tatsächlich ist es nichts Schwieriges, wenn Sie alle Aktionen nacheinander ausführen. Der Hauptfehler ist die falsch gewählte Körperdicke, sie sollte nicht weniger als 1 cm betragen. Das Schweißgerät muss gereinigt werden. Anschließend wird das Gerät getrocknet und erst dann beginnt die Herstellung des Gehäuses. Wenn der Beton ausgehärtet ist, muss die Schweißmaschine außen bearbeitet werden. Dies erfordert ein organisches Monomer.
Für diese Aufgabe eignen sich Styrol oder Methylmethacrylat. Sobald der Beton mit Monomer gesättigt ist, muss die Oberfläche wärmebehandelt werden. Die Temperatur muss hierfür mindestens 70 0 C betragen. In diesem Fall kommt es zur Polymerisation des Monomers. Durch diesen Vorgang bildet sich auf dem Gehäuse des Geräts selbst eine wasserdichte Schicht. Danach wird das Schweißgerät vor dem Einfluss der äußeren Umgebung geschützt.
Zurück zum Inhalt
Der einfachste Weg
Punktschweißen ist in der Branche am gefragtesten Alltagsleben, aber oft hat eine Person einfach nicht die Zeit, den komplexen Innenteil einer Schweißmaschine herzustellen. Wenn es Schwierigkeiten bereitet, können Sie auf die einfachste Lösung des Problems zurückgreifen. Überprüfen Sie, welches defekt ist Haushaltsgeräte ist im Haus.
Wenn ein Mikrowellenherd kaputt geht, werfen Sie ihn nicht überstürzt weg – wenn Sie neue elektrische Leitungen, Holzstücke, Klammern und Spitzen haben, wird das Gerät dies tun Punktschweißen kann sehr schnell hergestellt werden.
Du wirst brauchen:
- Unterlegscheiben.
- Selbstschneidende Schrauben.
- Heftklammern.
Sie müssen den vorgesehenen Abmessungen der Schweißmaschine entsprechen. Wenn der kaputte Mikrowelle Wenn der Transformator ordnungsgemäß funktioniert, wird er zur Grundlage der neuen selbstgebauten Ausrüstung.
Abbildung 1. Diagramm eines Brückengleichrichters für eine Schweißmaschine.
Schweißgeräte gibt es mit Gleich- und Wechselstrom.
S.A. Gleichstrom wird zum Niederstromschweißen von dünnen Blechen (Dachstahl, Automobil usw.) verwendet. Der Gleichstrom-Schweißlichtbogen ist stabiler, direktes und umgekehrtes Schweißen ist möglich. Sie können Gleichstrom mit Elektrodendraht ohne Beschichtung und Elektroden schweißen, die sowohl für das Schweißen mit Gleichstrom als auch mit Wechselstrom ausgelegt sind. Um den Lichtbogen bei niedrigen Strömen stabil brennen zu lassen, ist eine erhöhte Leerlaufspannung Uxx der Schweißwicklung (bis 70 - 75 V) wünschenswert. Zur Gleichrichtung von Wechselstrom werden einfachste „Brücken“-Gleichrichter auf leistungsstarken Dioden mit Kühlkörpern verwendet (Abb. 1).
Um Spannungswelligkeiten zu glätten, ist einer der Ausgänge von S.A. Und sie sind über die Induktivität L1 mit dem Elektrodenhalter verbunden, bei der es sich um eine Spule mit 10 - 15 Windungen eines Kupferbusses mit einem Querschnitt von S = 35 mm 2 handelt, die beispielsweise auf einen beliebigen Kern gewickelt ist. Um den Schweißstrom gleichzurichten und stufenlos zu regulieren, werden komplexere Schaltungen mit leistungsstarken gesteuerten Thyristoren verwendet. Eine der möglichen Schaltungen auf Basis von Thyristoren des Typs T161 (T160) ist im Artikel von A. Chernov „Es wird geladen und geschweißt“ (Model Designer, 1994, Nr. 9) beschrieben. Die Vorteile von Gleichstromreglern liegen in ihrer Vielseitigkeit. Der Bereich ihrer Spannungsänderungen liegt zwischen 0,1 und 0,9 Uxx, wodurch sie nicht nur zur stufenlosen Einstellung des Schweißstroms, sondern auch zum Laden verwendet werden können Batterien, Stromversorgung von elektrischen Heizelementen und anderen Zwecken.
Abbildung 2. Diagramm der fallenden äußeren Kennlinie der Schweißmaschine.
Reis. 1. Brückengleichrichter für Schweißgerät. Anschluss dargestellt S.A. zum Schweißen dünner Bleche mit „umgekehrter“ Polarität - „+“ an der Elektrode, „-“ am zu schweißenden Teil U2: - Ausgangswechselspannung des Schweißgeräts
Wechselstromschweißgeräte werden beim Schweißen mit Elektroden verwendet, deren Durchmesser mehr als 1,6 - 2 mm beträgt und die Dicke der geschweißten Produkte mehr als 1,5 mm beträgt. In diesem Fall ist der Schweißstrom erheblich (mehrere zehn Ampere) und der Lichtbogen brennt ziemlich gleichmäßig. Es werden ausschließlich Elektroden zum Schweißen mit Wechselstrom verwendet. Für den normalen Betrieb des Schweißgeräts ist Folgendes erforderlich:
- Stellen Sie eine Ausgangsspannung für eine zuverlässige Lichtbogenzündung bereit. Für Amateur S.A. Uxx = 60 - 65 V. Eine höhere Leerlauf-Ausgangsspannung wird vor allem aus Gründen der Betriebssicherheit nicht empfohlen (Uxxindustrial-Schweißgeräte - bis 70 - 75 V).
- Stellen Sie die für ein stabiles Brennen des Lichtbogens erforderliche Schweißspannung Usv bereit. Abhängig vom Durchmesser der Elektrode - Usv = 18 - 24 V.
- Geben Sie den Nennschweißstrom Iw = (30 - 40) de an, wobei Iw der Wert des Schweißstroms A ist; 30 - 40 - Koeffizient je nach Art und Durchmesser der Elektrode; dе - Elektrodendurchmesser, mm.
- Begrenzen Sie den Kurzschlussstrom Isk, dessen Wert den Nennschweißstrom nicht um mehr als 30 - 35 % überschreiten sollte.
Ein stabiles Lichtbogenbrennen ist möglich, wenn das Schweißgerät eine fallende äußere Kennlinie aufweist, die das Verhältnis zwischen Stromstärke und Spannung im Schweißkreis bestimmt (Abb. 2).
S.A. zeigt, dass für eine grobe (stufenweise) Überlappung des Schweißstrombereichs das Umschalten sowohl der Primär- als auch der Sekundärwicklung erforderlich ist (was aufgrund des darin fließenden großen Stroms strukturell schwieriger ist). Um den Schweißstrom innerhalb des ausgewählten Bereichs stufenlos zu ändern, werden außerdem mechanische Vorrichtungen zum Bewegen der Wicklungen verwendet. Wenn die Schweißwicklung relativ zur Netzwicklung entfernt wird, nehmen die magnetischen Verlustflüsse zu, was zu einer Verringerung des Schweißstroms führt.
Abbildung 3. Diagramm eines stabförmigen Magnetkreises.
Beim Entwurf einer Amateur-SA sollte man nicht danach streben, den Bereich der Schweißströme vollständig abzudecken. Es empfiehlt sich, im ersten Schritt ein Schweißgerät für das Arbeiten mit Elektroden mit einem Durchmesser von 2 - 4 mm zusammenzustellen und im zweiten Schritt, wenn mit niedrigen Schweißströmen gearbeitet werden muss, dieses durch ein separates Gleichrichtergerät mit zu ergänzen stufenlose Regelung des Schweißstroms. Amateur-Schweißgeräte müssen eine Reihe von Anforderungen erfüllen, von denen die wichtigsten die folgenden sind: relative Kompaktheit und geringes Gewicht; ausreichende Betriebszeit (mindestens 5 - 7 Elektroden dе = 3 - 4 mm) aus einem 220V-Netz.
Durch die Reduzierung der Leistung können Gewicht und Abmessungen des Gerätes reduziert und durch die Verwendung von Stahl mit hoher magnetischer Permeabilität und hitzebeständiger Isolierung der Wickeldrähte die Betriebszeit verlängert werden. Diese Anforderungen sind leicht zu erfüllen, wenn Sie die Grundlagen der Schweißmaschinenkonstruktion kennen und sich an die vorgeschlagene Technologie für deren Herstellung halten.
Reis. 2. Abfallende äußere Kennlinie der Schweißmaschine: 1 - Kennlinienfamilie für verschiedene Schweißbereiche; Isv2, Isvz, Isv4 – Schweißstrombereiche für Elektroden mit einem Durchmesser von 2, 3 bzw. 4 mm; Uxx – CA-Leerlaufspannung. Ist - Kurzschlussstrom; Ucv – Schweißspannungsbereich (18 – 24 V).
Reis. 3. Magnetkern vom Stabtyp: a - L-förmige Platten; b – U-förmige Platten; c - Platten aus Transformatorstahlbändern; S = axb – Querschnittsfläche des Kerns (Kern), cm 2 s, d – Fensterabmessungen, cm.
Wählen Sie also den Kerntyp. Für die Herstellung von Schweißgeräten werden hauptsächlich stabförmige Magnetkerne verwendet, da deren Konstruktion technologisch fortschrittlicher ist. Der Kern besteht aus Elektrostahlplatten beliebiger Konfiguration mit einer Dicke von 0,35–0,55 mm, die mit vom Kern isolierten Stiften festgezogen werden (Abb. 3). Bei der Auswahl eines Kerns müssen die Abmessungen des „Fensters“ berücksichtigt werden, damit es zu den Wicklungen der Schweißmaschine passt, und die Querschnittsfläche des Kerns (Kern) S =axb, cm 2. Wie die Praxis zeigt, sollten Sie nicht die Mindestwerte von S = 25 - 35 cm wählen, da das Schweißgerät nicht über die erforderliche Gangreserve verfügt und es schwierig wird, eine qualitativ hochwertige Schweißung zu erzielen. Und auch eine Überhitzung des Schweißgerätes nach kurzzeitigem Betrieb ist vorprogrammiert.
Abbildung 4. Diagramm eines toroidalen Magnetkreises.
Der Querschnitt des Kerns sollte S = 45 - 55 cm 2 betragen. Das Schweißgerät wird etwas schwerer sein, aber es wird Sie nicht im Stich lassen! Amateurschweißgeräte mit Ringkernen, die höhere elektrische Eigenschaften haben, etwa vier- bis fünfmal höher als die eines Stabtyps, und bei denen die elektrischen Verluste gering sind, werden immer weiter verbreitet. Die Arbeitskosten für ihre Herstellung sind höher und hängen hauptsächlich mit der Platzierung der Wicklungen auf dem Torus und der Komplexität der Wicklung selbst zusammen.
Mit dem richtigen Ansatz liefern sie jedoch gute Ergebnisse. Die Kerne bestehen aus Transformatorbandeisen, das zu einer torusförmigen Rolle gerollt ist. Ein Beispiel ist ein Kern eines 9-A-Spartransformators „Latr“. Zur Vergrößerung des Innendurchmessers des Torus („Fensters“) mit innen Wickeln Sie einen Teil des Stahlbandes ab und wickeln Sie es außen um den Kern. Doch wie die Praxis zeigt, reicht Latra allein nicht aus, um hochwertige SA herzustellen. (kleiner Abschnitt S). Selbst nach dem Arbeiten mit 1 - 2 Elektroden mit einem Durchmesser von 3 mm kommt es zu einer Überhitzung. Es ist möglich, zwei ähnliche Kerne gemäß dem in B. Sokolovs Artikel „Welding Baby“ (Sam, 1993, Nr. 1) beschriebenen Schema zu verwenden oder einen Kern durch Umspulen von zwei herzustellen (Abb. 4).
Reis. 4. Ringmagnetkern: 1.2 - Spartransformatorkern vor und nach dem Zurückspulen; 3 Design S.A. basierend auf zwei Ringkernen; W1 1 W1 2 - Netzwerkwicklungen parallel geschaltet; W 2 - Schweißwicklung; S = axb – Querschnittsfläche des Kerns, cm 2, s, d – Innen- und Außendurchmesser des Torus, cm; 4 - Elektrischer Schaltplan S.A. basierend auf zwei verbundenen Ringkernen.
Besondere Aufmerksamkeit verdienen Amateur-SAs, die auf der Basis von Statoren von asynchronen Dreiphasen-Elektromotoren mit hoher Leistung (mehr als 10 kW) hergestellt werden. Die Wahl des Kerns wird durch die Querschnittsfläche des Stators S bestimmt. Gestanzte Statorplatten entsprechen nicht vollständig den Parametern von Elektrotransformatorstahl, daher ist es nicht ratsam, den Querschnitt S auf weniger als 40 zu reduzieren - 45 cm.
Abbildung 5. Schema der Befestigung der Anschlüsse der CA-Wicklungen.
Der Stator wird vom Gehäuse befreit, die Statorwicklungen werden aus den Innennuten entfernt, die Nutbrücken werden mit einem Meißel abgeschnitten, die Innenfläche wird mit einer Feile oder einer Schleifscheibe geschützt, die scharfen Kanten des Kerns werden abgerundet und fest umwickelt und mit Baumwoll-Isolierband abgedeckt. Der Kern ist zum Wickeln von Wicklungen bereit.
Auswahl der Wicklungen. Für Primärwicklungen (Netzwicklungen) ist es besser, einen speziellen Kupferwicklungsdraht aus Kaltstahl zu verwenden. (Isolation aus Glaswolle. Auch Drähte mit Gummi- oder Gummigewebe-Isolierung weisen eine zufriedenstellende Hitzebeständigkeit auf. Drähte mit Polyvinylchlorid (PVC)-Isolierung sind für Arbeiten bei erhöhten Temperaturen (und dies ist bereits in der Konstruktion von Amateur-SA enthalten) aufgrund ihres möglichen Schmelzens, Leckagen aus den Wicklungen und ihres Kurzschlusses ungeeignet. Daher muss entweder die Polyvinylchlorid-Isolierung von den Drähten entfernt und die Drähte über die gesamte Länge mit Watte umwickelt werden. mit Isolierband oder entfernen Sie es nicht, sondern wickeln Sie den Draht über die Isolierung. Auch eine andere bewährte Wickelmethode ist möglich. Aber mehr dazu weiter unten.
Bei der Auswahl des Querschnitts der Wickeldrähte sind die Besonderheiten der Arbeit von S.A. zu berücksichtigen. (periodisch) erlauben wir eine Stromdichte von 5 A/mm 2. Bei einem Schweißstrom von 130 - 160 A (Elektrode dе = 4 mm) beträgt die Leistung der Sekundärwicklung P 2 = Isw x 160x24 = 3,5 - 4 kW, die Leistung der Primärwicklung unter Berücksichtigung von Verlusten etwa 5 - 5,5 kW betragen, und daher kann der maximale Strom der Primärwicklung 25 A erreichen. Folglich muss der Querschnitt des Drahtes der Primärwicklung S 1 mindestens 5 - 6 mm betragen. In der Praxis empfiehlt es sich, einen Draht mit einem Querschnitt von 6 - 7 mm 2 zu verwenden. Entweder handelt es sich um eine rechteckige Stromschiene oder um einen Wickeldraht aus Kupfer mit einem Durchmesser (ohne Isolierung) von 2,6 – 3 mm. (Berechnung mit der bekannten Formel S = piR 2, wobei S die Fläche des Kreises ist, mm 2 pi = 3,1428; R der Radius des Kreises, mm.) Wenn der Querschnitt eines Drahtes ist unzureichend, Wicklung in zwei Teile ist möglich. Beim Benutzen Aluminiumdraht sein Querschnitt muss um das 1,6- bis 1,7-fache vergrößert werden. Ist es möglich, den Querschnitt des Netzwerkwicklungsdrahtes zu reduzieren? Ja, du kannst. Aber gleichzeitig S.A. verliert die erforderliche Leistungsreserve, erwärmt sich schneller und der empfohlene Kernquerschnitt S = 45 - 55 cm wird in diesem Fall unangemessen groß. Die Anzahl der Windungen der Primärwicklung W 1 wird aus der folgenden Beziehung bestimmt: W 1 = [(30 – 50):S] x U 1 wobei 30–50 ein konstanter Koeffizient ist; S - Kernquerschnitt, cm 2, W 1 = 240 Windungen mit Biegungen von 165, 190 und 215 Windungen, d.h. alle 25 Umdrehungen.
Abbildung 6. Diagramm der Methoden zum Wickeln von CA-Wicklungen auf einen Stabkern.
Eine größere Anzahl von Netzwicklungsanzapfungen ist, wie die Praxis zeigt, unpraktisch. Und deshalb. Durch die Reduzierung der Windungszahl der Primärwicklung erhöhen sich sowohl die Leistung SA als auch Uxx, was zu einer Erhöhung der Lichtbogenspannung und einer Verschlechterung der Schweißqualität führt. Folglich ist es unmöglich, den Bereich der Schweißströme abzudecken, ohne die Schweißqualität zu verschlechtern, indem einfach die Anzahl der Windungen der Primärwicklung geändert wird. Dazu ist es erforderlich, die Windungen der Sekundärwicklung (Schweißwicklung) W 2 zu schalten.
Die Sekundärwicklung W 2 muss 65 - 70 Windungen einer isolierten Kupferschiene mit einem Querschnitt von mindestens 25 mm (vorzugsweise 35 mm) enthalten. Passend und flexibel Litzendraht(z. B. Schweißen) und mehradriges Dreiphasen-Stromkabel. Die Hauptsache ist, dass der Querschnitt der Leistungswicklung nicht kleiner als erforderlich sein sollte und die Isolierung hitzebeständig und zuverlässig sein sollte. Reicht der Drahtquerschnitt nicht aus, ist eine Wicklung in zwei oder sogar drei Drähten möglich. Bei Verwendung von Aluminiumdraht muss dessen Querschnitt um das 1,6- bis 1,7-fache vergrößert werden.
Reis. 5. Befestigung der Anschlüsse der CA-Wicklungen: 1 - CA-Gehäuse; 2 - Unterlegscheiben; 3 - Anschlussbolzen; 4 - Nuss; 5 - Kupferspitze mit Draht.
Die Anschaffung von Schaltern für hohe Ströme ist schwierig und die Praxis zeigt, dass es am einfachsten ist, die Schweißwicklungsleitungen durch Kupferfahnen unter Anschlussbolzen mit einem Durchmesser von 8 - 10 mm einzuführen (Abb. 5). Kupferkabelschuhe werden aus Kupferrohren mit geeignetem Durchmesser und einer Länge von 25 bis 30 mm hergestellt und durch Crimpen und vorzugsweise Löten an den Drähten befestigt. Konzentrieren wir uns insbesondere auf die Reihenfolge der Wicklungen. Allgemeine Regeln:
- Das Wickeln sollte entlang eines isolierten Kerns und immer in der gleichen Richtung (z. B. im Uhrzeigersinn) erfolgen.
- Jede Lage der Wicklung ist mit einer Lage Watte isoliert. Isolierung (Glasfaser, Elektrokarton, Pauspapier), vorzugsweise mit Bakelitlack imprägniert.
- Die Wicklungsklemmen sind verzinnt, markiert und mit Watte gesichert. Geflecht, zusätzlich Watte auf die Klemmen der Netzwicklung legen. Batist.
- Bei Zweifeln an der Qualität der Isolierung kann das Aufwickeln mit einer Baumwollschnur wie bei zwei Drähten erfolgen (der Autor verwendete Baumwollfaden zum Angeln). Nach dem Aufwickeln einer Schicht mit Baumwolle umwickeln. der Faden wird mit Leim, Lack etc. fixiert. und nach dem Trocknen die nächste Reihe aufwickeln.
Abbildung 7. Diagramm der Methoden zum Wickeln von CA-Wicklungen auf einen Ringkern.
Betrachten wir die Reihenfolge der Anordnung der Wicklungen auf einem stabförmigen Magnetkern. Die Netzwicklung kann im Wesentlichen auf zwei Arten positioniert werden. Mit der ersten Methode erhalten Sie einen „härteren“ Schweißmodus. Die Netzwerkwicklung besteht in diesem Fall aus zwei identischen Wicklungen W 1 W 2, die sich auf verschiedenen Seiten des Kerns befinden, in Reihe geschaltet sind und den gleichen Drahtquerschnitt haben. Zur Einstellung des Ausgangsstroms werden an jeder der Wicklungen Abgriffe vorgenommen, die paarweise geschlossen werden (Abb. 6a, c).
Bei der zweiten Methode wird die Primärwicklung (Netzwicklung) auf eine Seite des Kerns gewickelt (Abb. 6 c, d). In diesem Fall hat die SA eine steil abfallende Kennlinie, schweißt „sanft“, die Lichtbogenlänge hat weniger Einfluss auf die Höhe des Schweißstroms und damit auf die Schweißqualität. Nach dem Wickeln der Primärwicklung des CA muss das Vorhandensein kurzgeschlossener Windungen und die Richtigkeit der gewählten Windungszahl überprüft werden. Der Schweißtransformator wird über eine Sicherung (4 - 6A) und vorzugsweise ein Wechselstrom-Amperemeter an das Netzwerk angeschlossen. Wenn die Sicherung durchbrennt oder sehr heiß wird, liegt das daran ein klares Zeichen kurzgeschlossene Drehung. Folglich muss die Primärwicklung umgedreht werden Besondere Aufmerksamkeit auf die Qualität der Isolierung.
Reis. 6. Methoden zum Wickeln von CA-Wicklungen auf einen Stabkern: a – Netzwerkwicklung auf beiden Seiten des Kerns; b - die entsprechende Sekundärwicklung (Schweißwicklung), Rücken an Rücken angeschlossen; c - Netzwerkwicklung auf einer Seite des Kerns; g - die entsprechende Sekundärwicklung, in Reihe geschaltet.
Wenn das Schweißgerät laute Geräusche macht und die Stromaufnahme 2 - 3 A übersteigt, bedeutet dies, dass die Anzahl der Primärwicklungen unterschätzt wird und eine bestimmte Anzahl von Windungen aufgewickelt werden muss. Ein funktionierender CA verbraucht im Leerlauf nicht mehr als 1 - 1,5 A, erwärmt sich nicht und brummt nicht viel. Die Sekundärwicklung CA ist immer auf beiden Seiten des Kerns gewickelt. Bei der ersten Wickelmethode besteht die Sekundärwicklung ebenfalls aus zwei identischen Hälften, die zur Erhöhung der Stabilität des Lichtbogenbrennens (Abb. 6) gegenparallel geschaltet sind, und der Drahtquerschnitt kann etwas kleiner gewählt werden - 15 - 20 mm 2.
Abbildung 8. Anschlussplan für Messgeräte.
Bei der zweiten Wickelart wird die Hauptschweißwicklung W 2 1 auf der wicklungsfreien Seite des Kerns gewickelt und macht 60 - 65 % der Gesamtwindungszahl der Sekundärwicklung aus. Es dient hauptsächlich der Zündung des Lichtbogens und beim Schweißen sinkt die Spannung an ihm aufgrund eines starken Anstiegs des magnetischen Verlustflusses um 80 - 90 %. Auf die Primärwicklung wird eine zusätzliche Schweißwicklung W 2 2 gewickelt. Als Netzteil hält es die Schweißspannung und damit den Schweißstrom innerhalb der erforderlichen Grenzen. Die Spannung an ihm sinkt im Schweißbetrieb um 20 - 25 % gegenüber der Leerlaufspannung. Nach der Herstellung des SA ist es notwendig, ihn einzurichten und die Schweißqualität mit Elektroden unterschiedlichen Durchmessers zu überprüfen. Der Einrichtungsprozess ist wie folgt. Um Schweißstrom und -spannung zu messen, müssen Sie zwei elektrische Messgeräte kaufen – ein Wechselstrom-Amperemeter für 180–200 A und ein Wechselstrom-Voltmeter für 70–80 V.
Reis. 7. Methoden zum Wickeln von CA-Wicklungen auf einen Ringkern: 1.2 – gleichmäßige bzw. abschnittsweise Wicklung der Wicklungen: a – Netzwerk b – Leistung.
Ihr Anschlussplan ist in Abb. dargestellt. 8. Beachten Sie beim Schweißen mit unterschiedlichen Elektroden die Werte des Schweißstroms Iw und der Schweißspannung Uw, die innerhalb der erforderlichen Grenzen liegen müssen. Wenn der Schweißstrom klein ist, was am häufigsten vorkommt (die Elektrode bleibt hängen, der Lichtbogen ist instabil), werden in diesem Fall entweder durch Umschalten der Primär- und Sekundärwicklung die erforderlichen Werte oder die Anzahl der Windungen eingestellt Die Sekundärwicklung wird umverteilt (ohne sie zu erhöhen), um die Anzahl der Windungen zu erhöhen, die auf die obere Wicklung des Netzwerks gewickelt sind. Nach dem Schweißen können Sie einen Bruch machen oder die Kanten der geschweißten Produkte absägen, und die Qualität der Schweißnaht wird sofort deutlich: die Eindringtiefe und die Dicke der abgeschiedenen Metallschicht. Es ist sinnvoll, eine Tabelle basierend auf den Messergebnissen zu erstellen.
Abbildung 9. Diagramm von Schweißspannungs- und Strommessgeräten und Aufbau eines Stromwandlers.
Wählen Sie anhand der Daten in der Tabelle die optimalen Schweißmodi für die Elektroden aus verschiedene Durchmesser, wobei zu beachten ist, dass beim Schweißen mit Elektroden, beispielsweise mit einem Durchmesser von 3 mm, Elektroden mit einem Durchmesser von 2 mm geschnitten werden können, weil Der Schneidstrom ist 30-25 % höher als der Schweißstrom. Die Schwierigkeit, die oben empfohlenen Messgeräte zu kaufen, zwang den Autor dazu, auf die Herstellung einer Messschaltung (Abb. 9) zurückzugreifen, die auf dem gängigsten 1-10 mA DC-Milliamperemeter basiert. Es besteht aus Spannungs- und Strommessgeräten, die in einer Brückenschaltung aufgebaut sind.
Reis. 9. Schematische Darstellung von Schweißspannungs- und Strommessgeräten und Aufbau eines Stromwandlers.
Der Spannungsmesser ist an die Ausgangswicklung (Schweißwicklung) SA angeschlossen. Die Einstellung erfolgt mit jedem Tester, der die Schweißausgangsspannung kontrolliert. Über einen variablen Widerstand R.3 wird der Zeiger des Gerätes auf den letzten Skalenteil beim Maximalwert von Uxx eingestellt. Die Skala des Spannungsmessers ist recht linear. Für eine höhere Genauigkeit können Sie zwei oder drei Kontrollpunkte entfernen und kalibrieren Messgerät zum Messen von Spannungen.
Der Aufbau eines Strommessgeräts ist schwieriger, da es an einen selbstgebauten Stromwandler angeschlossen ist. Letzterer ist ein Ringkern mit zwei Wicklungen. Die Abmessungen des Kerns (Außendurchmesser 35-40 mm) sind nicht von grundsätzlicher Bedeutung, Hauptsache die Wicklungen passen. Kernmaterial - Transformatorstahl, Permalloy oder Ferrit. Die Sekundärwicklung besteht aus 600 - 700 Windungen isoliertem Kupferdraht der Marke PEL, PEV, vorzugsweise PELSHO, mit einem Durchmesser von 0,2 - 0,25 mm und ist an einen Strommesser angeschlossen. Die Primärwicklung ist ein Stromkabel, das im Ring verläuft und mit der Anschlussschraube verbunden ist (Abb. 9). Das Einrichten des Stromzählers erfolgt wie folgt. Zur Power (Schweiß-)Wicklung S.A. Schließen Sie einen kalibrierten Widerstand von dick an Nichromdraht 1 - 2 Sekunden lang laufen lassen (es wird sehr heiß) und die Spannung am SA-Ausgang messen. Es wird der in der Schweißwicklung fließende Strom ermittelt. Zum Beispiel beim Anschluss von Rн = 0,2 Ohm Uout = 30V.
Markieren Sie einen Punkt auf der Instrumentenskala. Drei bis vier Messungen mit unterschiedlicher relativer Luftfeuchtigkeit reichen aus, um das aktuelle Messgerät zu kalibrieren. Nach der Kalibrierung werden die Instrumente gemäß allgemein anerkannten Empfehlungen auf dem CA-Körper installiert. Beim Schweißen unter unterschiedlichen Bedingungen (Hoch- oder Schwachstromnetz, langes oder kurzes Versorgungskabel, dessen Querschnitt usw.) wird die SA durch Umschalten der Wicklungen angepasst. auf den optimalen Schweißmodus eingestellt und anschließend kann der Schalter in die Neutralstellung gebracht werden. Ein paar Worte zum Widerstandspunktschweißen. Auf dem Weg zum Design von S.A. Für diesen Typ gelten eine Reihe spezifischer Anforderungen:
- Die beim Schweißen abgegebene Leistung sollte maximal sein, jedoch nicht mehr als 5-5,5 kW. In diesem Fall wird der aus dem Netzwerk aufgenommene Strom 25 A nicht überschreiten.
- Der Schweißmodus muss „hart“ sein und daher die Wicklung der Wicklungen S.A. sollte gemäß der ersten Option durchgeführt werden.
- Die in der Schweißwicklung fließenden Ströme erreichen Werte von 1500-2000 A und höher. Daher sollte die Schweißspannung nicht mehr als 2–2,5 V und die Leerlaufspannung 6–10 V betragen.
- Der Querschnitt der Primärwicklungsdrähte beträgt mindestens 6-7 mm und der Querschnitt der Sekundärwicklung beträgt mindestens 200 mm. Dieser Drahtquerschnitt wird durch das Wickeln von 4-6 Windungen und deren anschließende Parallelschaltung erreicht.
- Es ist nicht praktikabel, zusätzliche Anzapfungen an der Primär- und Sekundärwicklung vorzunehmen.
- Aufgrund der kurzen Betriebsdauer des SA kann die Windungszahl der Primärwicklung als berechnetes Minimum angenommen werden.
- Es wird nicht empfohlen, einen Kernquerschnitt von weniger als 45-50 cm zu nehmen.
- Schweißspitzen und Unterwasserkabel müssen aus Kupfer sein und entsprechende Strömungen zulassen (Spitzendurchmesser 12–14 mm).
Eine besondere Klasse von Amateur-S.A. stellen Geräte dar, die auf Basis von Industriebeleuchtung und anderen Transformatoren (2-3 Phasen) mit einer Ausgangsspannung von 36 V und einer Leistung von mindestens 2,5-3 kW hergestellt werden. Vor der Änderung ist es jedoch erforderlich, den Kernquerschnitt, der mindestens 25 cm betragen sollte, sowie die Durchmesser der Primär- und Sekundärwicklungen zu messen. Es wird Ihnen sofort klar, was Sie von der Neugestaltung dieses Transformators erwarten können.
Und zum Schluss noch ein paar technische Tipps.
Das Schweißgerät muss mit einem Draht mit einem Querschnitt von 6–7 mm über einen Automaten mit einem Strom von 25–50 A, beispielsweise AP-50, an das Netzwerk angeschlossen werden. Der Durchmesser der Elektrode kann je nach Dicke des zu schweißenden Metalls nach folgender Beziehung gewählt werden: da= (1-1,5)L, wobei L die Dicke des zu schweißenden Metalls in mm ist.
Die Lichtbogenlänge wird je nach Elektrodendurchmesser gewählt und beträgt durchschnittlich 0,5-1,1 d3. Es wird empfohlen, mit einem kurzen Lichtbogen von 2-3 mm zu schweißen, dessen Spannung 18-24 V beträgt. Eine Vergrößerung der Lichtbogenlänge führt zu einer Verletzung der Stabilität seiner Verbrennung, erhöhten Verlusten durch Abfall und Spritzer, und eine Verringerung der Eindringtiefe des Grundmetalls. Je länger der Lichtbogen ist, desto höher ist die Schweißspannung. Die Schweißgeschwindigkeit wird vom Schweißer je nach Güte und Dicke des Metalls gewählt.
Beim Schweißen mit gerader Polarität wird der Pluspol (Anode) mit dem Teil und der Minuspol (Kathode) mit der Elektrode verbunden. Wenn eine geringere Wärmeentwicklung an den Teilen erforderlich ist, beispielsweise beim Schweißen dünner Blechstrukturen, kommt das Schweißen mit umgekehrter Polarität zum Einsatz (Abb. 1). In diesem Fall wird das Minus (Kathode) mit dem zu schweißenden Teil und das Plus (Anode) mit der Elektrode verbunden. Dies sorgt nicht nur für eine geringere Erwärmung des zu schweißenden Teils, sondern beschleunigt auch den Schmelzprozess des Elektrodenmetalls aufgrund der höheren Temperatur der Anodenzone und des größeren Wärmeeintrags.
Schweißdrähte werden über Kupferkabelschuhe unter den Anschlussbolzen an der Außenseite des Schweißmaschinengehäuses mit dem SA verbunden. Schlechte Kontaktverbindungen verringern die Leistungseigenschaften des SA, verschlechtern die Schweißqualität und können zu Überhitzung und sogar zu einem Brand der Drähte führen. Bei kurzen Schweißdrähten (4-6 m) sollte ihr Querschnitt mindestens 25 mm betragen. Bei Schweißarbeiten sind beim Arbeiten mit Elektrogeräten die Brand- und Elektroschutzvorschriften einzuhalten.
Schweißarbeiten sollten in einer speziellen Maske mit durchgeführt werden Schutzglas Klasse C5 (für Ströme bis 150-160 A) und Fäustlinge. Führen Sie alle SA-Umschaltungen erst durch, nachdem Sie das Schweißgerät vom Netzwerk getrennt haben.
Das Inverterschweißen ist ein modernes Gerät, das sich aufgrund seines geringen Gewichts und seiner Abmessungen großer Beliebtheit erfreut. Der Wechselrichtermechanismus basiert auf der Verwendung von Feldeffekttransistoren und Leistungsschaltern. Um Besitzer eines Schweißgeräts zu werden, können Sie in jedem Werkzeugladen ein so nützliches Ding erwerben. Aber es gibt einen viel wirtschaftlicheren Weg, der darin besteht, Inverterschweißen mit eigenen Händen herzustellen. Es ist die zweite Methode, auf die wir in diesem Material achten und uns überlegen, wie man zu Hause schweißt, was dafür benötigt wird und wie die Diagramme aussehen.
Merkmale des Wechselrichterbetriebs
Ein Inverter-Schweißgerät ist nichts anderes als ein Netzteil, wie es heute in modernen Computern verwendet wird. Worauf basiert die Funktionsweise des Wechselrichters? Im Wechselrichter ergibt sich folgendes Bild der elektrischen Energieumwandlung:
2) Strom mit konstanter Sinuskurve wird in Wechselstrom mit hoher Frequenz umgewandelt.
3) Der Spannungswert nimmt ab.
4) Der Strom wird gleichgerichtet, während die erforderliche Frequenz beibehalten wird.
Eine Auflistung solcher Stromkreisumwandlungen ist notwendig, um das Gewicht des Gerätes und seine Gesamtabmessungen reduzieren zu können. Schließlich handelt es sich, wie Sie wissen, um alte Schweißgeräte, deren Prinzip darauf beruht, die Spannung zu reduzieren und den Strom an der Sekundärwicklung des Transformators zu erhöhen. Aufgrund des hohen Stromwerts besteht daher die Möglichkeit des Lichtbogenschweißens von Metallen. Damit der Strom zunimmt und die Spannung abnimmt, verringert sich die Windungszahl der Sekundärwicklung, aber der Leiterquerschnitt nimmt zu. Als Ergebnis können Sie feststellen, dass ein Transformatorschweißgerät nicht nur erhebliche Abmessungen, sondern auch ein ordentliches Gewicht hat.
Um das Problem zu lösen, wurde eine Möglichkeit vorgeschlagen, ein Schweißgerät mit einer Wechselrichterschaltung zu implementieren. Das Prinzip des Wechselrichters basiert darauf, die Frequenz des Stroms auf 60 oder sogar 80 kHz zu erhöhen und dadurch das Gewicht und die Abmessungen des Geräts selbst zu reduzieren. Um ein Inverter-Schweißgerät zu implementieren, musste lediglich die Frequenz tausendfach erhöht werden, was durch den Einsatz von Feldeffekttransistoren möglich wurde.
Transistoren ermöglichen die Kommunikation untereinander mit einer Frequenz von etwa 60–80 kHz. Der Transistor-Stromversorgungskreis erhält einen konstanten Stromwert, der durch den Einsatz eines Gleichrichters gewährleistet wird. Als Gleichrichter dient eine Diodenbrücke, für den Spannungsausgleich sorgen Kondensatoren.
Wechselstrom, der nach Durchlaufen von Transistoren an einen Abwärtstransformator übertragen wird. Gleichzeitig wird aber eine um ein Hundertfaches kleinere Spule als Transformator verwendet. Warum eine Spule verwendet wird, weil die Frequenz des Stroms, der dem Transformator zugeführt wird, dank Feldeffekttransistoren bereits um das 1000-fache erhöht wird. Dadurch erhalten wir ähnliche Daten wie beim Transformatorschweißen, nur mit großer Unterschied in Gewicht und Abmessungen.
Was wird zum Zusammenbau eines Wechselrichters benötigt?
Um das Wechselrichterschweißen selbst zusammenzubauen, müssen Sie wissen, dass die Schaltung zunächst für eine Verbraucherspannung von 220 Volt und einen Strom von 32 Ampere ausgelegt ist. Nach der Energieumwandlung erhöht sich der Ausgangsstrom um fast das Achtfache und erreicht 250 Ampere. Dieser Strom reicht aus, um mit einer Elektrode im Abstand von bis zu 1 cm eine starke Naht zu erzeugen. Zur Realisierung einer Inverter-Stromversorgung müssen Sie folgende Komponenten verwenden:
1) Ein Transformator bestehend aus einem Ferritkern.
2) Wicklung des Primärtransformators mit 100 Drahtwindungen mit einem Durchmesser von 0,3 mm.
3) Drei Sekundärwicklungen:
— innen: 15 Windungen und Drahtdurchmesser 1 mm;
- mittel: 15 Windungen und Durchmesser 0,2 mm;
— außen: 20 Windungen und Durchmesser 0,35 mm.
Darüber hinaus benötigen Sie zum Zusammenbau des Transformators folgende Elemente:
- Kupferkabel;
- Glasfaser;
— Textolith;
— Elektrostahl;
- Material aus Baumwolle.
Wie sieht ein Inverter-Schweißkreis aus?
Um zu verstehen, was ein Inverter-Schweißgerät ist, ist es notwendig, das unten dargestellte Diagramm zu betrachten.
Stromkreis des Inverterschweißens
Alle diese Komponenten müssen kombiniert werden, um so ein Schweißgerät zu erhalten ein unverzichtbarer Helfer bei Schlosserarbeiten. Unten finden Sie ein schematisches Diagramm des Inverterschweißens.
Diagramm der Inverter-Schweißstromversorgung
Die Platine, auf der sich die Stromversorgung des Geräts befindet, ist getrennt vom Leistungsteil montiert. Der Trenner zwischen dem Leistungsteil und der Stromversorgung ist ein Metallblech, das elektrisch mit dem Gerätekörper verbunden ist.
Zur Steuerung der Gates werden Leiterbahnen verwendet, die in der Nähe der Transistoren angelötet werden müssen. Diese Leiter sind paarweise miteinander verbunden, wobei der Querschnitt dieser Leiter keine besondere Rolle spielt. Wichtig ist lediglich die Länge der Leiter, die 15 cm nicht überschreiten sollte.
Für jemanden, der mit den Grundlagen der Elektronik nicht vertraut ist, ist das Lesen dieser Art von Schaltung problematisch, ganz zu schweigen vom Zweck jedes Elements. Wenn Sie also keine Kenntnisse im Umgang mit Elektronik haben, ist es besser, einen vertrauten Spezialisten um Hilfe zu bitten. Unten sehen Sie beispielsweise ein Diagramm des Leistungsteils eines Inverter-Schweißgeräts.
Diagramm des Leistungsteils des Inverterschweißens
So montieren Sie das Inverterschweißen: Schritt-für-Schritt-Beschreibung + (Video)
Um ein Inverter-Schweißgerät zusammenzubauen, müssen Sie es abschließen Nächste Schritte funktioniert:
1) Rahmen. Es wird empfohlen, eine alte Computersystemeinheit als Gehäuse zum Schweißen zu verwenden. Es ist am besten geeignet, weil es hat erforderliche Menge Löcher zur Belüftung. Sie können einen alten 10-Liter-Kanister verwenden, in den Sie Löcher schneiden und den Kühler platzieren können. Um die Festigkeit der Struktur zu erhöhen, ist es notwendig, Metallecken am Systemgehäuse anzubringen, die mit Schraubverbindungen befestigt werden.
2) Zusammenbau des Netzteils. Ein wichtiges Element Das Netzteil ist genau ein Transformator. Es wird empfohlen, 7x7- oder 8x8-Ferrit als Basis des Transformators zu verwenden. Für die Primärwicklung des Transformators ist es notwendig, den Draht über die gesamte Breite des Kerns zu wickeln. Diese wichtige Funktion führt zu einem verbesserten Betrieb des Geräts bei Spannungsspitzen. Als Draht müssen unbedingt PEV-2-Kupferdrähte verwendet werden. Wenn keine Sammelschiene vorhanden ist, werden die Drähte zu einem Bündel verbunden. Zur Isolierung der Primärwicklung wird Glasfaser verwendet. Oben, nach der Glasfaserschicht, müssen Windungen aus Abschirmdrähten gewickelt werden.
Transformator mit Primär- und Sekundärwicklung zum Inverterschweißen
3) Leistungsteil. Als Leistungseinheit fungiert ein Abwärtstransformator. Als Kern für einen Abwärtstransformator werden zwei Arten von Kernen verwendet: Ш20х208 2000 nm. Es ist wichtig, zwischen beiden Elementen eine Lücke zu schaffen, die durch das Einlegen von Zeitungspapier gelöst wird. Die Sekundärwicklung eines Transformators zeichnet sich durch mehrlagige Wicklungswindungen aus. Auf der Sekundärwicklung des Transformators müssen drei Lagen Drähte verlegt und dazwischen Fluorkunststoffdichtungen angebracht werden. Es ist wichtig, zwischen den Wicklungen eine verstärkte Isolierschicht anzubringen, um einen Spannungsdurchbruch an der Sekundärwicklung zu vermeiden. Es ist notwendig, einen Kondensator mit einer Spannung von mindestens 1000 Volt zu installieren.
Transformatoren für die Sekundärwicklung alter Fernseher
Um die Luftzirkulation zwischen den Wicklungen zu gewährleisten, muss ein Luftspalt gelassen werden. Ein Stromwandler ist auf einem Ferritkern montiert, der mit dem Stromkreis an die Plusleitung angeschlossen ist. Der Kern muss mit Thermopapier umwickelt sein, daher ist es am besten, als Papier Kassenband zu verwenden. Auf der Aluminium-Kühlerplatte sind Gleichrichterdioden angebracht. Die Ausgänge dieser Dioden sollten mit blanken Drähten mit einem Querschnitt von 4 mm verbunden werden.
3) Wechselrichtereinheit. Der Hauptzweck eines Wechselrichtersystems besteht darin, Gleichstrom in hochfrequenten Wechselstrom umzuwandeln. Um eine Frequenzerhöhung zu gewährleisten, werden spezielle Feldeffekttransistoren verwendet. Schließlich sind es die Transistoren, die bei hohen Frequenzen öffnen und schließen.
Es wird empfohlen, mehr als einen leistungsstarken Transistor zu verwenden. Am besten ist es jedoch, eine Schaltung zu implementieren, die auf zwei weniger leistungsstarken Transistoren basiert. Dies ist notwendig, um die aktuelle Frequenz stabilisieren zu können. Die Schaltung kommt nicht ohne Kondensatoren aus, die in Reihe geschaltet sind und die Lösung folgender Probleme ermöglichen:
Wechselrichter aus Aluminiumplatte
4) Kühlsystem. An der Gehäusewand sollten Kühlventilatoren installiert werden, hierfür können Sie Computerkühler verwenden. Sie sind notwendig, um die Kühlung der Arbeitselemente sicherzustellen. Je mehr Ventilatoren Sie verwenden, desto besser. Insbesondere ist es unbedingt erforderlich, zwei Lüfter zu installieren, die den Sekundärtransformator überblasen. Ein Kühler bläst auf den Kühler und verhindert so eine Überhitzung der Arbeitselemente – Gleichrichterdioden. Am Strahler sind Dioden montiert auf die folgende Weise, wie auf dem Foto unten gezeigt.
Gleichrichterbrücke am Kühlkörper
Foto des Thermostats
Es wird empfohlen, es am Heizelement selbst zu installieren. Dieser Sensor wird ausgelöst, wenn die kritische Heiztemperatur des Arbeitselements erreicht ist. Wenn es ausgelöst wird, wird die Stromversorgung des Wechselrichtergeräts abgeschaltet.
Leistungsstarker Lüfter zur Kühlung des Wechselrichtergeräts
Während des Betriebs erwärmt sich das Inverterschweißen sehr schnell, weshalb zwei leistungsstarke Kühler vorhanden sind Voraussetzung. Diese Kühler oder Lüfter sind am Gerätegehäuse angebracht und dienen der Luftabsaugung.
Anwenden frische Luft dank der Löcher im Gerätekörper in das System integriert werden. Die Systemeinheit verfügt bereits über diese Löcher. Wenn Sie anderes Material verwenden, vergessen Sie nicht, für Frischluftzufuhr zu sorgen.
5) Löten der Platine ist ein entscheidender Faktor, da die gesamte Schaltung auf der Platine basiert. Es ist wichtig, Dioden und Transistoren in entgegengesetzter Richtung zueinander auf der Platine zu installieren. Die Platine wird direkt zwischen den Kühlkörpern montiert, mit deren Hilfe der gesamte Stromkreis der Elektrogeräte angeschlossen wird. Der Versorgungsstromkreis ist für eine Spannung von 300 V ausgelegt. Durch die zusätzliche Anordnung von Kondensatoren mit einer Kapazität von 0,15 μF ist es möglich, überschüssige Leistung wieder in den Stromkreis einzuspeisen. Am Ausgang des Transformators befinden sich Kondensatoren und Beschaltungselemente, mit deren Hilfe die Überspannungen am Ausgang der Sekundärwicklung unterdrückt werden.
6) Einrichtungs- und Debugging-Arbeiten. Nach dem Zusammenbau des Wechselrichterschweißgeräts müssen noch einige weitere Vorgänge durchgeführt werden, insbesondere die Inbetriebnahme des Geräts. Schließen Sie dazu eine Spannung von 15 Volt an den PWM (Pulsweitenmodulator) an und versorgen Sie den Kühler mit Strom. Zusätzlich über den Widerstand R11 mit dem Relaiskreis verbunden. Das Relais ist in den Stromkreis eingebunden, um Spannungsspitzen im 220-V-Netz zu vermeiden. Es ist unbedingt erforderlich, die Aktivierung des Relais zu überwachen und dann die PWM mit Strom zu versorgen. Dadurch sollte ein Bild beobachtet werden, bei dem rechteckige Bereiche im PWM-Diagramm verschwinden sollten.
Das Gerät eines selbstgebauten Wechselrichters mit einer Beschreibung der Elemente
Ob der Stromkreis richtig angeschlossen ist, können Sie beurteilen, wenn das Relais beim Einrichten 150 mA ausgibt. Für den Fall, dass es beobachtet wird Schwaches Signal, dann deutet dies darauf hin, dass die Platinenverbindung falsch ist. Möglicherweise liegt in einer der Wicklungen ein Fehler vor. Um Störungen zu vermeiden, müssen Sie daher alle Stromversorgungskabel kürzen.
Inverterschweißen im Gehäuse Systemeinheit vom Computer
Überprüfung der Funktionalität des Geräts
Nachdem alle Montage- und Fehlerbehebungsarbeiten abgeschlossen sind, bleibt nur noch die Überprüfung der Funktionsfähigkeit der resultierenden Schweißmaschine. Dazu wird das Gerät über ein 220-V-Netzteil mit Strom versorgt, anschließend werden hohe Stromwerte eingestellt und die Messwerte mit einem Oszilloskop überprüft. In der unteren Schleife sollte die Spannung innerhalb von 500 V liegen, jedoch nicht mehr als 550 V. Wenn bei einer strengen Auswahl der Elektronik alles richtig gemacht wird, wird die Spannungsanzeige 350 V nicht überschreiten.
Jetzt können Sie das Schweißen in Aktion überprüfen. Dazu verwenden wir die erforderlichen Elektroden und schneiden die Naht, bis die Elektrode vollständig durchbrennt. Danach ist es wichtig, die Temperatur des Transformators zu überwachen. Wenn der Transformator einfach kocht, hat der Stromkreis seine Mängel und es ist besser, den Arbeitsprozess nicht fortzusetzen.
Nach dem Schneiden von 2-3 Nähten erhitzen sich die Heizkörper auf eine hohe Temperatur, daher ist es wichtig, sie danach abkühlen zu lassen. Dazu reicht eine Pause von 2-3 Minuten, wodurch die Temperatur auf den optimalen Wert sinkt.
Überprüfung der Schweißmaschine
So verwenden Sie ein selbstgebautes Gerät
Nach dem Anschließen eines selbstgebauten Geräts an den Stromkreis stellt der Controller automatisch eine bestimmte Stromstärke ein. Wenn die Kabelspannung weniger als 100 Volt beträgt, deutet dies auf eine Fehlfunktion des Geräts hin. Sie müssen das Gerät zerlegen und den korrekten Zusammenbau noch einmal überprüfen.
Mit diesem Schweißmaschinentyp können Sie nicht nur Eisen-, sondern auch Nichteisenmetalle löten. Um ein Schweißgerät zusammenzubauen, benötigen Sie nicht nur Kenntnisse der Grundlagen der Elektrotechnik, sondern auch Freizeit für die Umsetzung der Idee.
Das Inverterschweißen ist in der Garage eines jeden Eigentümers unverzichtbar. Wenn Sie also noch kein solches Werkzeug erworben haben, können Sie es selbst herstellen.
Ohne Schweißgerät ist keine Arbeit mit Eisen möglich. Es ermöglicht das Schneiden und Verbinden von Metallteilen jeder Größe und Dicke. Gute Entscheidung- Schweißen Sie selbst, weil gute Modelle Sie sind teuer und billige sind von schlechter Qualität. Um die Idee zu verwirklichen, ein eigenes Schweißgerät herzustellen, müssen Sie es erwerben Spezialausrüstung So können Sie die Qualitätskompetenzen eines Spezialisten unter realen Bedingungen verbessern.
Arten und Eigenschaften des Werkzeugs
Nachdem alle notwendigen Voraussetzungen der Vorbereitungsphase erfolgreich erfüllt sind, eröffnet sich die Möglichkeit, mit eigenen Händen ein Modell des Schweißgerätes anzufertigen. Heute gibt es viele Schaltpläne, nach dem das Gerät hergestellt werden kann. Sie verfolgen einen der folgenden Ansätze:
- Gleich- oder Wechselstrom.
- Impuls oder Wechselrichter.
- Automatisch oder halbautomatisch.
Es lohnt sich, auf das Gerät zu achten, das zum Transformatortyp gehört. Wichtiges Merkmal Dieses Gerät wird mit Wechselstrom betrieben und kann daher in verwendet werden Lebensbedingungen. AC-Geräte sind in der Lage, die Standardqualität der Nähte in Schweißverbindungen sicherzustellen. Ein solches Gerät kann problemlos im Alltag Verwendung finden. bei der Betreuung von Immobilien im privaten Sektor.
Um ein solches Gerät zusammenzubauen, müssen Sie Folgendes haben:
- Etwa 20 Meter Kabel oder großflächiger Draht.
- Eine Metallbasis mit hoher magnetischer Permeabilität, die als Kern des Transformators verwendet wird.
Die optimale Kernkonfiguration hat eine U-förmige Kernbasis. Theoretisch könnte problemlos ein Kern mit jeder anderen Konfiguration geeignet sein, beispielsweise eine runde Form, die einem Stator entnommen wurde, der für einen Elektromotor unbrauchbar geworden ist. In der Praxis ist es jedoch viel schwieriger, eine Wicklung auf eine solche Basis zu wickeln.
Die Querschnittsfläche eines Kerns einer selbstgebauten Haushaltsschweißmaschine beträgt 50 cm 2. Dies reicht aus, um bei der Installation Stäbe mit einem Durchmesser von 3 bis 4 mm zu verwenden. Verwendung größerer Abschnitt führt nur zu einer Erhöhung der Masse der Struktur und die Effizienz des Geräts wird nicht höher.
Herstellungsanweisungen
Für die Primärwicklung muss Kupferdraht mit hoher Hitzebeständigkeit verwendet werden, da dieser bei Schweißarbeiten hohen Temperaturen ausgesetzt ist. Der verwendete Draht muss entsprechend der Glasfaser- oder Baumwollisolierung ausgewählt werden, bestimmt für den stationären Einsatz in Hochtemperaturzonen.
Für die Wicklung des Transformators dürfen keine Drähte mit PVC-Isolierung verwendet werden, die bei Erwärmung sofort unbrauchbar werden. In manchen Fällen erfolgt die Isolierung der Transformatorwicklung selbständig.
Um diesen Vorgang durchzuführen, müssen Sie ein Stück Baumwollstoff oder Glasfaser nehmen, es in etwa 2 cm breite Streifen schneiden, diese um den vorbereiteten Draht wickeln und den Verband mit einem beliebigen Lack mit elektrischen Eigenschaften imprägnieren. Eine solche Isolierung ist in Bezug auf die thermischen Eigenschaften keinem Werksanalog unterlegen.
Die Spulen werden nach einem bestimmten Prinzip gewickelt. Zuerst wird die Hälfte der Primärwicklung gewickelt, anschließend folgt die Hälfte der Sekundärwicklung. Fahren Sie dann mit der gleichen Technik mit der zweiten Spule fort. Um die Qualität der Isolierbeschichtung zu verbessern, werden Bruchstücke von Karton-, Glasfaser- oder Presspapierstreifen zwischen die Wicklungslagen eingelegt.
Geräteaufbau
Als nächstes müssen Sie konfigurieren. Dazu wird das Gerät an das Netzwerk angeschlossen und die Spannung an der Sekundärwicklung gemessen. Die Spannung sollte zwischen 60 und 65 Volt liegen.
Die genaue Einstellung der Parameter erfolgt durch Verkürzung oder Vergrößerung der Wicklungslänge. Um ein qualitativ hochwertiges Ergebnis zu erhalten, sollte die Spannung an der Sekundärwicklung auf die angegebenen Parameter eingestellt werden.
An die Primärwicklung des fertigen Schweißtransformators wird ein VRP-Kabel oder ein ShRPS-Draht angeschlossen, der für den Anschluss an das Netzwerk verwendet wird. Einer der Anschlüsse der Sekundärwicklung wird dem Anschluss zugeführt, an den später die Erde angeschlossen wird, und der zweite wird dem Anschluss zugeführt, an den das Kabel angeschlossen ist. Der letzte Vorgang ist abgeschlossen und das neue Schweißgerät ist einsatzbereit.
Produktion von Kleineinheiten
Ein Spartransformator aus einem Fernseher im sowjetischen Stil eignet sich problemlos für den Bau einer kleinen Schweißmaschine. Damit lässt sich leicht ein Voltaic-Lichtbogen erzeugen. Damit alles richtig funktioniert, werden Graphitelektroden zwischen den Anschlüssen des Spartransformators angeschlossen. Dieses einfache Design ermöglicht es Ihnen, mehrere auszuführen einfache Arbeit durch Schweißen, wie zum Beispiel:
- Herstellung oder Reparatur von Thermoelementen.
- Erhitzen von Produkten aus kohlenstoffreichem Stahl auf maximale Temperatur.
- Härten von Werkzeugstahl.
Ein selbstgebautes Schweißgerät, das auf der Basis eines Spartransformators hergestellt wurde, weist einen erheblichen Nachteil auf. Es muss mit zusätzlichen Vorsichtsmaßnahmen verwendet werden. Ohne galvanische Trennung vom Stromnetz handelt es sich um ein ziemlich gefährliches Gerät.
Als optimale Parameter eines zum Bau einer Schweißmaschine geeigneten Spartransformators gelten eine Ausgangsspannung im Bereich von 40 bis 50 Volt und geringer Strom von 200 bis 300 Watt. Dieses Gerät kann einen Betriebsstrom von 10 bis 12 Ampere liefern, was zum Schweißen von Drähten, Thermoelementen und anderen Elementen ausreicht.
Sie können Bleistiftminen als Elektroden für ein DIY-Mini-Schweißgerät verwenden. Die Anschlüsse verschiedener Elektrogeräte können als Halterungen für improvisierte Elektroden dienen.
Für Schweißarbeiten wird der Halter mit einem der Anschlüsse der Sekundärwicklung und das zu verschweißende Teil mit dem anderen verbunden. Der Griff für den Halter besteht am besten aus einer Glasfaserscheibe oder einem anderen hitzebeständigen Material. Es ist zu beachten, dass der Lichtbogen eines solchen Geräts nur für relativ kurze Zeit wirkt und so eine Überhitzung des verwendeten Spartransformators verhindert.
Bei manchen Karosseriearbeiten wird eine Schweißmaschine zum Verbinden von Metallteilen eingesetzt. Allerdings werden Arbeiten mit diesen Geräten meist bei schwerwiegenden Schäden am Körper durchgeführt, was relativ selten vorkommt. Von der Anschaffung eines neuen, relativ teuren Geräts zur einmaligen Nutzung ist daher abzuraten. Für den Hausgebrauch können Sie mit Ihren eigenen Händen ein Schweißgerät herstellen.
Besonderheiten
Es ist zu bedenken, dass der Eigenbau einer Schweißmaschine nur dann rentabel ist, wenn Sie über einige Ausgangskomponenten verfügen. Dies erklärt sich aus der Tatsache, dass zwar gesammelt das einfachste Modell Das betreffende Gerät ist einfach, die dafür benötigten Materialien sind sehr teuer. Wenn Sie sie daher separat erwerben, um dieses Gerät selbst herzustellen, kann es in Bezug auf die Endkosten in der Nähe eines neuen Markenwerkzeugs liegen, das natürlich die technischen Eigenschaften eines selbstgebauten Schweißgeräts übertrifft.
Design
Die Basis des jeweiligen Instruments ist ein Transformator, der als Energiequelle dient. Es besteht aus zwei Spulen aus Kupferdraht, die um einen Metallkern gewickelt sind. Darüber hinaus unterscheiden sich die Spulen in der Anzahl der Windungen. Derjenige, der an das Stromnetz angeschlossen ist, wird als primär bezeichnet. In diesem Fall entsteht in der Sekundärspule aufgrund der Induktion ein Strom geringerer Spannung, aber höherer Stromstärke.
Es ist zu berücksichtigen, dass ein Schweißgerät mit niedrigem Strom eine minderwertige Schweißung erzeugt, während ein zu hoher Strom zum Verbrennen der Elektroden und zum Schneiden des Metalls führt.
Das Schweißgerät kann mit einem Transformator beispielsweise aus einem Mikrowellenherd ausgestattet sein. Da an seiner Sekundärwicklung jedoch eine Spannung von etwa 2000 Volt auftritt, ist es notwendig, mit eigenen Händen einige Änderungen am Design vorzunehmen, um die Spannung zu senken, nämlich die Anzahl der Windungen zu reduzieren.
Um die Spannung zu reduzieren, wird die Sekundärwicklung an zwei Stellen zersägt und aus der Spule herausgezogen. Dabei ist darauf zu achten, dass die Primärwicklung nicht beschädigt wird. Anschließend wird die Sekundärwicklung mit einem dickeren Draht oder PEV-Draht mit Lackisolierung oder 0,05 mm dickem Thermopapier umwickelt. Es empfiehlt sich, die dritte Variante zu nutzen, da hierdurch der Skin-Effekt vermieden wird, der bei der Verwendung von herkömmlichem Draht auftritt. Es besteht darin, hochfrequente Ströme zu verdrängen, was zu einer Überhitzung des Leiters führt.
Die entstandene Wicklung wird mit dünnflüssigem Isolierlack überzogen. Für jedes Transformatormodell werden Parameter wie Windungszahl und Dicke berechnet. Es wurden jedoch auch die optimalen Werte abgeleitet: Wicklungsdicke – 0,3 mm, Breite – 40 mm, Drahtstärke – 0,5–0,7 mm.
Wenn Sie keinen Transformator aus einer Mikrowelle oder einem anderen Gerät haben, können Sie ihn selbst zusammenbauen. Dies erfordert einen Kern mit Querschnitt 25-55 cm² Transformatoreisen, gekennzeichnet durch hohe magnetische Permeabilität, mehrere Dutzend Meter langer Kupferdraht, Isoliermaterialien.
Was den Draht betrifft, gilt als beste Option hitzebeständiger Kupferdraht mit Glasfaser, Baumwolle oder als letztes Gummiisolierung. Sie können die Isolierung selbst durchführen. Dazu müssen Sie das Isoliermaterial in 2 cm lange Streifen schneiden und diese um den Draht wickeln.
Der letzte Schritt ist die Imprägnierung mit Elektrolack. Je besser die Isolierung, desto geringer ist die Gefahr einer Überhitzung des Instruments. Die Wicklungsparameter werden basierend auf berechnet technische Eigenschaften Gerät. Die Leerlauf-Ausgangsspannung eines selbstgebauten Schweißgeräts liegt zwischen 60 und 65 V, die Betriebsspannung zwischen 18 und 24 V. Bei der höchsten Leistung und einer Elektrode mit einem Durchmesser von 4 mm beträgt die Leistung in der Sekundärwicklung 3,5 -4 kW, im Primärbereich - etwa 5 kW unter Berücksichtigung der Verluste. Der Strom beträgt etwa 25 A.
Die Windungszahl wird anhand der Spannung unter Berücksichtigung der Querschnittsfläche des Magnetkerns von 2 cm ermittelt, für 1 V mit einem hochwertigen Draht sind es 0,9 - 1,1 Windungen. Die Summe ergibt sich aus der Division des Spannungspegels durch die Frequenz. Auf diese Weise werden Indikatoren für beide Wicklungen berechnet. Auf dieser Grundlage können Sie die erforderliche Drahtlänge ermitteln, indem Sie die Länge einer Windung mit der Gesamtzahl multiplizieren. In diesem Fall müssen Sie etwas Reserve mitnehmen.
Vor dem Wickeln der Spulen müssen Rahmen aus Leiterplatten oder Elektrokarton hergestellt werden, die lose auf den Kern gelegt werden. Zwischen der Primär- und Sekundärwicklung muss eine Isolierung in Form von Glasfaser, Elektro- oder gewöhnlichem Karton angebracht werden.
Rahmen
Das Schweißgerät sollte mit einem Gehäuse ausgestattet sein, in dem der Transformator untergebracht ist, um ihn vor äußeren Einflüssen zu schützen. Bei der Auswahl oder Herstellung müssen Sie dies berücksichtigen elektromagnetische Strahlung Nicht alle Materialien sind hierfür geeignet. Die besten Optionen sind ein solides, gebogenes, starres Stahlgehäuse oder ein Gehäuse aus dielektrischen Materialien. Die zweite Option ist schwieriger zu finden oder mit eigenen Händen zusammenzubauen und auch weniger langlebig, vermeidet jedoch Vibrationen und Energieverluste in den Strukturelementen von Transformatoren, die durch Wirbelströme verursacht werden, die durch starke magnetische Streufelder in der Nähe angeregt werden Wicklungen.
Bei Gehäusen aus anderen Materialien können diese negativen Phänomene etwas reduziert werden (um 30-50 %, je nach Design und Material des Gehäuses), wenn Längsschnitte am Gehäuse vorgenommen werden.
Die meisten selbstgebauten Schweißwerkzeuge haben keinen festen Körper. Dadurch werden damit verbundene Probleme wie Vibrationen, Wirbelströme und Energieverluste vermieden. Allerdings ist die Schweißmaschine in diesem Fall äußeren Einflüssen ausgesetzt, was zu einer starken Verschlechterung der Zuverlässigkeit und Arbeitssicherheit führt. Darüber hinaus ist zu berücksichtigen, dass die oben genannten Verluste mehrere Prozent betragen, was vor dem Hintergrund von Widerständen in Stromleitungen und Spannungsschwankungen im Netz kaum wahrnehmbar ist.
Darüber hinaus empfiehlt es sich, das Gerät mit einer Sekundärspannungsregelung zur stufenlosen Regelung des Schweißstroms auszustatten. Dadurch werden Verluste in langen Kabeln ausgeglichen, was besonders wichtig ist, wenn Sie abseits der Stromversorgung arbeiten. Markenwerkzeuge verfügen über eine stufenweise Spannungsregelung durch Schalten der Wicklungen. Ein elektrisches Heimschweißgerät kann mit einer Spannungsgleichrichterschaltung auf Basis von Thyristoren ausgestattet werden.
Zuverlässigkeitsproblem
Ein selbstgebautes Schweißgerät ist in den meisten Fällen nicht so zuverlässig wie ein Markenanalogon. Daher sollten bei der Herstellung einige Maßnahmen ergriffen werden, um ihn zu erhöhen.
Als Hauptursache für einen vorzeitigen Ausfall der betreffenden Geräte gilt die Überhitzung. Um die Wahrscheinlichkeit seines Auftretens zu verringern, ist zunächst eine wirksame Isolierung erforderlich. Dafür sind zuverlässige Wickeldrähte mit einer Stromdichte von bis zu 5-7 A/mm² erforderlich. Dies reicht jedoch möglicherweise nicht aus.
Um den Draht schnell abzukühlen, muss eine Wechselwirkung mit Luft gewährleistet sein. Dazu müssen Sie Schlitze in die Wicklungen einbringen. Nach der ersten Drahtschicht und alle zwei weiteren Schichten externe Teilnehmer Legen Sie Getenaks oder Holzbretter von 5-10 mm ein.
Dadurch wird sichergestellt, dass jede Drahtschicht auf einer Seite mit Luft in Kontakt steht. Verfügt das Schweißgerät nicht über Ventilatoren, sind die Schlitze vertikal ausgerichtet, um eine konstante Luftzirkulation zu gewährleisten. In diesem Fall kommt es von unten kalte Luft, der Warme geht hoch.
Mehr effektive Option Die Kühlung des Schweißgerätetransformators erfolgt selbstverständlich über einen Lüfter. Das Blasen hat nahezu keinen Einfluss auf die Aufheizgeschwindigkeit, beschleunigt aber die Abkühlung deutlich. Es muss jedoch berücksichtigt werden, dass bei einem Transformator mit geschlossenen Wicklungen das Problem der Überhitzung auch bei der Installation nicht gelöst werden kann leistungsstarker Ventilator. In diesem Fall lässt es sich nur durch moderaten Betrieb vermeiden.
Es gibt eine weitere Möglichkeit, das Problem der Transformatorüberhitzung zu lösen. Dabei wird es in Transformatorenöl getaucht. Diese Flüssigkeit leitet nicht nur Wärme ab, sondern dient auch als zusätzlicher Isolator. In diesem Fall muss das Transformatorgehäuse ein versiegelter Behälter sein.
Unter dem Gesichtspunkt der Überhitzung sind Ringkerntransformatoren am problematischsten. Sie erwärmen sich schnell und kühlen langsam ab. Vibrationen, die während des Betriebs aufgrund der Anziehung von Metallelementen durch die von ihnen erzeugten Variablen auftreten, gelten auch bei selbstgebauten Transformatoren als ziemlich ernstes Problem. Magnetfeld. Dadurch kommt es zu einer Reibung der Drähte, die zur Zerstörung der Isolierung sowie zur Zerstörung und zum Durchdrücken der Wicklungen an den Ecken des Rahmens führt. Um die Auswirkungen von Vibrationen zu reduzieren, ist eine hochwertige Isolierung erforderlich. Sie müssen außerdem alle festen Elemente fest befestigen.
Vermeiden Sie die Lagerung und Verwendung des Schweißgeräts bei hoher Luftfeuchtigkeit. In den Rissen der Isolierung kondensierendes Wasser fungiert als Stromleiter. Das Werkzeug muss vor der Verwendung überprüft werden. Wenn die Spannung 60 - 65 V überschreitet, erhöhen oder verringern Sie die Wicklung.