Exemple de Poka Yoke în mecanică. Metodele de izolație sunt împărțite în trei niveluri în ordinea creșterii eficienței.
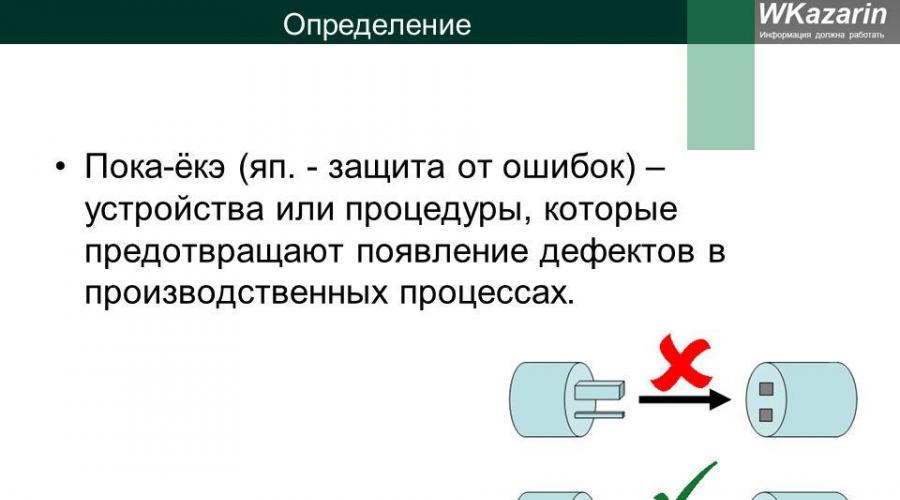
Citeste si
Definiție Poka-yoke (jap. - protecția erorilor) - dispozitive sau proceduri care previn apariția defectelor în procesele de fabricație.
Adio-jug. Exemplul 2. O fotocelulă care se declanșează dacă o persoană traversează (sau invers – nu traversează) o linie de control invizibilă. De exemplu, asamblatorul trebuie neapărat să ia și să folosească o anumită piesă.
Tipuri de eroare umană Uitare Înțelegerea greșită a cauzelor Subestimare Neexperiență Nedorință Neatenție Amânare Lipsa standardelor Surpriză Intenție
Surse de defecte Operare ratată Erori de prelucrare Eroare de poziționare a pieselor Piese lipsă Piese incorecte Prelucrarea piesei greșite Operare incorectă Erori de setare Instalare incorectă a echipamentului Folosind unealta sau scule greșite Fukushima-1.
Exemplu de soluție: Problemă de prelucrare prin turnare: Piese nefinisate Soluție: Schimbarea jgheabului pentru a identifica piesele defecte Descrierea procesului: Piesele turnate sunt prelucrate pe o mașină automată și trecute la următorul proces prin jgheab Înainte de îmbunătățire: Dacă o piesă nefinisată intră în jgheab, următoarea mașina se va prăbuși și poate fi deteriorată. Desen din cartea „Poka-Yoke. Îmbunătățirea calității produsului prin prevenirea defectelor»
Exemplu de rezolvare a problemelor: Prelucrarea unei piese turnate după îmbunătățire: Pentru a opri o piesă brută, a fost dezvoltată o metodă care ia în considerare diferența acesteia formă geometrică din piesa prelucrată. Jgheabul a fost modificat astfel incat piesa nefinisata sa se opreasca in blocul instalat in jgheab si sa nu cada in masina urmatoare. Acest lucru a ajutat la prevenirea defecțiunilor mașinii. Desen din cartea „Poka-Yoke. Îmbunătățirea calității produsului prin prevenirea defectelor»
Prezentarea „ABC of lean manufacturing. Ce este poka-yoke. Poka-yoke (sau poka-yoke) sunt dispozitive sau proceduri care previn defectele proceselor de fabricație. Prezentarea oferă o definiție, enumeră tipurile de erori umane și sursele de defecte și oferă câteva exemple.
Mai jos, în textul notei se află textul însoțitor.
În plus, această prezentare în format video cu comentariile mele este postată pe Youtube.comși Rutube.ru.
Vă rog să oferiți comentariile și sugestiile voastre pe site-urile youtube și rutube, direct pe pagina video, sau prin formularul de pe site-ul meu, pentru a le putea lua în considerare pe viitor.
Transcrierea textului însoțitor
Poka-yoke (care înseamnă „protecție împotriva erorilor” în japoneză) sunt dispozitive sau proceduri care împiedică apariția defectelor în procesele de fabricație.
Să ne uităm la câteva exemple.
Exemplul #1. Forma produsului este de așa natură încât nu poate fi instalat pentru prelucrare sau utilizare într-o poziție greșită (cu susul în jos sau cu spatele). Vedeți o dischetă de trei inchi care poate fi introdusă doar până la capăt în unitate într-o singură poziție.
Exemplul #2. O fotocelulă care se declanșează dacă o persoană traversează (sau invers - nu traversează) o linie de control invizibilă. De exemplu, asamblatorul trebuie neapărat să ia și să folosească o anumită piesă.
Defectele sunt cauzate de o eroare umană.
Există 10 tipuri de erori umane care duc la defecte. Acest:
- uitare,
- neînțelegere a motivelor (apariția a ceva)
- subestimarea oricărei situații (sau incapacitatea de a identifica orice obiect)
- lipsa de experiență
- nedorință (de a urma procedurile și regulile)
- nepăsare
- lentoare (în luarea unei decizii)
- lipsa standardelor
- surprinde
- comiterea intenționată a unei greșeli (sau sabotaj)
Sursele defectelor sunt următoarele fapte:
- operație ratată
- erori de procesare
- erori de poziție a pieselor
- detaliu lipsă
- element gresit
- manipularea piesei greșite
- operare incorectă pe partea corectă
- erori de configurare
- instalarea necorespunzătoare a echipamentelor și
- folosind o unealtă sau unealta greșită
Să luăm în considerare un exemplu de rezolvare a problemei.
Problema constă în detaliile brute. Soluția aplicată: schimbarea jgheabului pentru identificarea pieselor defecte.
Uitate la imagine.
Piesele turnate sunt procesate pe o mașină automată și transferate la următorul proces printr-un jgheab.
Înainte de îmbunătățire, s-a întâmplat următoarele: dacă o piesă nefinisată trece prin jgheab, următoarea mașină din proces se oprește anormal și poate fi deteriorată.
Pentru a opri o piesă brută, a fost dezvoltată o metodă care ține cont de diferența de formă geometrică a piesei prelucrate. Jgheabul a fost modificat astfel incat piesa nefinisata sa se opreasca in blocul instalat in jgheab si sa nu treaca la urmatoarea masina. Acest lucru a ajutat la prevenirea defecțiunilor mașinii.
Istoria apariției sistemului poke-eka
În 1961, analizând structura de productieÎntreprinderile Yamaha Electric, Shingo a formulat metoda baka-yoke (fool-proof). A ajuns la concluzia că sistemul general acceptat de control statistic nu împiedică căsătoria. Desigur, cu ajutorul său a fost posibil să se prezică gradul de probabilitate al următorului defect, dar aceasta ar fi doar o declarație de fapte. Shingo a decis să încorporeze controale în procesul în sine. La urma urmei, căsătoria apare ca urmare a greșelilor umane. Greșelile sunt, desigur, inevitabile, dar pot fi prevenite prin construirea de mașini și unelte cu feedback. O încercare de a introduce incorect o piesă a dus instantaneu la oprirea lucrării. S-a primit o alarma si in cazul in care un angajat a uitat sa faca o operatiune. După apariția unei erori, a urmat detectarea acesteia, identificarea și prevenirea completă a posibilității de reapariție. Astfel, Shigeo Shingo a separat cauza de efect - eroarea de defect, garantând calitatea produsului 100%. La urma urmei, controlul calității a fost efectuat de acum înainte nu prin prelevarea de mostre pe masa de control al calității, ci direct la mașina unealtă pe toate produsele fără excepție. Rezultatele nu au întârziat să apară. De exemplu, în 1977 magazine de producție de la Matsushita Elecric, unde a fost introdus sistemul Shingo, a funcționat timp de 7 luni fără defecte. S. Shingo a început să folosească pe bună dreptate titlul „Domnul Îmbunătățire” în țară și în străinătate.
Adevărat, denumirea de „protecție împotriva unui prost” nu a putut rezista. Odată, când Shingo le prezenta noua metodă muncitorilor, unul dintre muncitori a strigat: „Nu sunt prost!”. A trebuit să-mi cer scuze și să dau metodei un nou nume: sistemul poka-yoke (protecție împotriva defectelor, sau 0-defect). Acest sistem îmbunătățește foarte mult eficiența proces de producție contribuind la reducerea deșeurilor, reducerea costurilor și pierderea de timp.
Conceptul metodei bye-bye
Fabricarea fără defecte se bazează pe o metodă de protecție a erorilor numită Poka-Yoke. Sistemul „Poka-eka” poate fi tradus în rusă ca „fool-proof”.
Ideea de bază este de a opri procesul de îndată ce se găsește un defect, de a determina cauza și de a preveni reapariția sursei defectului. Prin urmare, nu este necesară eșantionarea statistică. O parte cheie a procedurii este că inspecția sursei erorii este efectuată ca parte activă a procesului de fabricație pentru a detecta erorile înainte ca acestea să devină defecte. Descoperirea unei erori fie oprește producția până când aceasta este corectată, fie procesul este corectat pentru a preveni apariția defectului. Acest lucru se realizează în fiecare etapă a procesului prin monitorizarea potențialelor surse de eroare. În acest fel, defectele sunt identificate și corectate chiar la sursă, și nu în etapele ulterioare. Desigur, acest proces a fost posibil prin utilizarea instrumentelor și mecanismelor cu feedback imediat (în acest proces, se evită utilizarea personalului datorită capacității acestora de a greși). Cu toate acestea, utilizarea personalului este esențială pentru identificarea potențialelor surse de eroare. La 40 de ani, Shingo a învățat și folosit în mare măsură metode statistice controlul calității, dar după 20 de ani, în 1977, a spus că în sfârșit s-a eliberat de farmecul lor de vrăjitorie. Acest lucru s-a întâmplat când a urmărit cu ochii săi cum era linia de asamblare tevi de scurgere la fabrica mașini de spălat Matsushita din Shizuoka, care a angajat 23 de muncitori, a reușit să funcționeze continuu fără un singur defect timp de o lună, datorită instalării dispozitivelor Poka-Yeke care preveniu defectele. Shingo susține că lipsa defectelor poate fi obținută prin utilizarea controlului sursei defectelor și a sistemului Poka-Yeke. Împreună, ele constituie „Zero Quality Control”.
Acest concept de „zero defecte” este diferit de ceea ce este asociat de obicei cu numele mentorului american Philip Crosby. Conceptul lui Shingo pune accent pe atingerea zero defecte prin folosirea bunului pregătire inginerească cercetarea de producție și proces, mai degrabă decât prin sloganurile și sloganurile asociate campaniilor de calitate ale firmelor americane și vest-europene. Shingo însuși, la fel ca Deming și Juran, arată îngrijorat față de această abordare americană, susținând că publicarea statisticilor defectelor este doar înșelătoare și că, în schimb, este necesar să se vâneze elementele defecte ale procesului de producție care cauzează majoritatea defectelor produsului.
Sistemul „poka-eka” este baza producției fără defecte.
Defectele de fabricație se datorează în mare parte variabilității crescute a caracteristicilor procesului, care, la rândul său, poate fi rezultatul:
- standarde elaborate incorect sau proceduri documentate;
* utilizarea echipamentelor de calitate scăzută sau învechite;
* folosirea materialelor necorespunzătoare;
* uzura sculelor;
* erori de operator.
Pentru toate aceste cauze de defecte, cu excepția ultimei, pot fi aplicate acțiuni corective și preventive. Este destul de dificil să preveniți erorile operatorului.
În centrul ideologiei poke-eka este faptul că este firesc ca oamenii să facă greșeli în procesul de muncă. Și acesta nu este un indicator al neprofesionalismului operatorului. Scopul poke-ek este de a găsi modalități de a vă proteja împotriva greșelilor neintenționate. Lista acțiunilor tipice ale operatorilor care duc la apariția defectelor este prezentată în tabel.
Metoda poke-eka se bazează pe șapte principii:
1 utilizați un design robust pentru a crea procese eficiente;
2 lucrul în echipă: doar așa se poate valorifica la maximum cunoștințele angajaților;
3 eliminați erorile, folosind și un design robust: acest lucru va aduce numărul de erori mai aproape de zero;
4 eliminați cauzele fundamentale ale defectelor prin aplicarea metodei 5 „De ce” (Cinci „de ce”);
5 acționează imediat, folosește toate resursele posibile;
6 eliminați activitățile care nu adaugă valoare;
7 implementați îmbunătățiri și gândiți-vă imediat la îmbunătățiri ulterioare.
Poké-eka nu se bazează pe operatorii înșiși pentru a găsi eroarea. Prin urmare, atunci când se lucrează, se folosesc senzori tactili și alte dispozitive. Acest lucru ajută la identificarea eficientă a defectelor trecute cu vederea de către operatori.
Metoda poke-eka trebuie aplicată atât la controlul intrării, cât și pe parcursul întregului proces. Efectul implementării sale depinde în ce stadiu al procesului - controlul intrării sau controlul în timpul procesului - această metodă a fost utilizată. În același timp, dacă au fost identificate neconcordanțe, se primesc semnale de avertizare sau chiar echipamentul poate fi oprit.
Introducerea metodei poke-eka la controlul de intrare se numește abordare proactivă. Detectarea erorilor în acest caz va avea loc înainte ca anumite operații să fi fost efectuate, să fie utilizate semnale de avertizare sau chiar și echipamentul poate fi oprit la controlul de ieșire.
Abordarea în care metoda poke-eka este aplicată altor etape ale procesului de producție se numește reactivă. În acest caz, se utilizează această metodă:
* imediat după finalizarea procesului;
* în timpul efectuării muncii de către operator;
* la transferul la următoarea etapă proces.
Abordarea reactivă este eficientă deoarece ajută la prevenirea transferului produselor defecte la următoarea etapă a procesului, dar, cu toate acestea, nu permite realizarea unui astfel de grad înalt protecție împotriva erorilor, ca în cazul unei abordări proactive. Utilizarea metodelor poke-eka în procesul de căutare a cauzelor defectelor nu dă rezultate ridicate, dar în același timp este mult mai eficientă decât controlul selectiv.
Există și alte abordări ale utilizării metodei poke-eka: control și avertizare. Cu o abordare de control, dacă este detectată un defect, echipamentul este oprit automat. Abordarea de avertizare se bazează pe utilizarea diferitelor mijloace de semnalizare (semnale luminoase și sonore) care informează operatorul despre posibilă eroare. Oprirea echipamentului nu face adesea parte din opțiunea abordării preventive.
Dispozitivele utilizate în poke-eka, în funcție de metoda care stă la baza activității lor, sunt împărțite în:
* a lua legatura;
* citind;
* miscare secventiala.
Toate cele trei tipuri de dispozitive pot fi utilizate atât într-o abordare de control, cât și într-o abordare de avertizare.
Principiul de funcționare al dispozitivelor cu metoda de contact se bazează pe determinarea dacă elementul sensibil este în contact cu obiectul testat. Întrerupătoarele de limită sunt un exemplu de astfel de dispozitive. Dacă contactul este rupt, atunci, de exemplu, se declanșează un semnal sonor.
De asemenea, dispozitivele care funcționează prin metoda contactului includ emițătoare și receptoare, întrerupătoare fotoelectrice, senzori piezoelectrici etc. Dispozitivele nu trebuie să fie de înaltă tehnologie. Dispozitivele pasive simple sunt uneori cele mai bune. Acestea nu permit pieselor să ia o poziție greșită în timpul procesului.
Cititoarele sunt folosite atunci când există un număr fix de operații într-un proces și un număr fix de piese într-un produs. Senzorul numără piesele de mai multe ori și trece piesa la următorul proces numai dacă numărul de piese este corect.
Al treilea tip de dispozitive sunt senzorii care determină dacă o operațiune de proces a fost finalizată. Dacă operațiunea nu este efectuată sau executată incorect, senzorul semnalează că echipamentul trebuie oprit. Multe dispozitive senzoriale și fotoelectrice funcționează pe acest principiu, care sunt asociate cu temporizatorul echipamentului. Utilizarea unor astfel de dispozitive este cea mai eficientă atunci când multe părți similare ca formă și dimensiune sunt utilizate în proces.
Aplicarea consecventă a metodei poke-eka poate reduce semnificativ numărul de erori făcute de operatori, ceea ce ajută la reducerea costurilor și la creșterea satisfacției clienților.
Odată s-a întâmplat să mă uit situație similară: proiectul a fost prost pregătit și lansat destul de grăbit. Ca urmare, procesul stabilit a fost complet nepotrivit pentru producția de masă, ceea ce a afectat relația cu clientul. A fost necesar să se ia măsuri imediate pentru a nu „pierde” complet clientul.Primul lucru cu care a început conducerea organizației a fost reorganizarea departamentului, în special, s-a decis înlocuirea șefului de departament.Probabil, tu ar trebui să te corectezi: am spus că am avut șansa să observ această situație, de fapt, abia din acel moment am fost repartizat la acest departament. Cu alte cuvinte, a trebuit să nu observ situația, ci să „răbesc.” Dar asta este nu despre asta acum...
Există un concept în Limba engleză„Ședința de lansare” - poate fi tradusă în diferite moduri - de la „planificare” la „debriefing”. În acest caz, acesta a fost discursul de deschidere al noului șef, care a cerut ruperea situației actuale și în cât mai repede posibil aduce nivelul de calitate cerut de client. Descrieți pe scurt situația: randament proces de 38% (CFTY) și o întârziere de 3 livrări de produse (mai mult de 10.000 de unități de produse finite). În partea din discurs care s-a ocupat de ingineri, șeful nou bătut a rostit o frază foarte interesantă:
- „Ia-l pe Alex, de exemplu. Când a proiectat instalația, s-a bazat pe experiența, educația și cunoștințele sale despre scopul dispozitivului. Dar, dacă ar fi putut lucra cu el timp de 12 ore ca operator în tură, ar fi putut face câteva modificări suplimentare. Poate ar trebui să fii forțat să lucrezi în tură? La urma urmei, în timpul muncă îndelungată sigur vor fi situații neprevăzute…”
Iată un punct interesant - o persoană nu este un robot, indiferent de modul în care predați, iar în timpul muncii îndelungate, vor apărea cu siguranță erori sau situații non-standard care duc la erori. Ar părea inutil să lupți împotriva fenomenului factorului uman - orice proces la care o persoană participă este supus erorilor operatorului. Cu toate acestea, este posibil să se reducă sau să se încerce să se minimizeze frecvența de apariție a unor astfel de erori la minimum. Creați un proces sau o adăugare la acesta care va exclude apariția unei erori.
De exemplu, procesul de tricotare a hamurilor de mașini: toate conexiunile sunt proiectate în așa fel încât să fie extrem de dificil să amestecați firele. La cartela SIM telefon mobil unul dintre colțuri este „tăiat”, ceea ce face imposibilă instalarea incorect.Conectori cabluri în interior bloc de sistem calculator personal avea formă diferită, ceea ce elimină posibilitatea conectării alimentării la conectorul cablului de date și invers.
Ce au exemplele de mai sus în comun? – Configurație de sistem care elimină apariția erorilor umane – protecție împotriva erorilor – Poka Jug.
Poka Yoke este o filozofie a managementului calității și îmbunătățirii continue a proceselor care vizează eliminarea posibilității erorii umane. Poka Yoke este o expresie japoneză care înseamnă literal „protecție împotriva erorilor”.
Implementarea practică a principiului Poka Yoke poate fi privită din două perspective:
- pe de o parte, și aceasta este modalitatea preferată, protecția împotriva erorilor este un sistem în care este exclusă apariția unei erori;
- pe de altă parte, este un sistem care împiedică un produs defect să intre în următoarea operațiune, stație, secțiune, linie sau client
Trebuie clarificat faptul că introducerea controlului 100% este adăugarea unei singure stații sau operațiuni la proces existentși nu este o implementare a principiului Poka Yoke. Adesea, o astfel de soluție necesită costuri suplimentare, crește cantitatea de resurse cheltuită pentru fabricarea produselor și crește costul acestora. Spre deosebire de controlul suplimentar, aplicarea principiului protecției împotriva erorilor pentru a preveni introducerea unui produs defect nu va implica resurse suplimentare și nu va afecta costul de producție.
Hai sa luam exemplu real din practica. Din când în când, pe farurile auto, a căror asamblare a fost efectuată prin metoda transportorului, a apărut același defect - o zgârietură pe lentilă. S-a dovedit că farul a fost zgâriat pe unul dintre dispozitivele în formă de U de pe transportor. Acest lucru s-a întâmplat numai în acele cazuri în care farul a fost instalat incorect pe bază - marginea necomprimată ieșea mai sus decât ar trebui și, atunci când se deplasa de-a lungul transportorului, se agăța de dispozitivul menționat mai sus.
Cum se remediază acest defect?
- Cumpărați un dispozitiv automat care instalează farul pe bază.
- Forțați toți operatorii să controleze poziția farului pe bază.
- Puneți o persoană separată responsabilă de controlul poziției farurilor pe bază.
Există multe soluții și toate sunt diverse, dar un lucru le unește - dorința de a adăuga ceva la proces. Ceva care implică costuri suplimentare și, eventual, scade productivitatea liniei.
A devenit posibilă eliminarea acestui defect prin implementarea principiului Poka Yoke: pe dispozitiv a fost instalată o placă din moale, dar suficient de tare pentru a nu rata produsul, care a provocat zgârieturi pe faruri. Placa a fost înșurubat trivial pe cadrul în formă de U al dispozitivului de fixare și a oprit pur și simplu piesa, împiedicând-o să treacă mai departe.
Un alt exemplu: toate produsele multimedia au o anumită cantitate de memorie. Partea „memorie” a produsului este fabricată și programată separat de întregul produs. Procesul de configurare a dispozitivului constă din următorii pași:
- verificarea dispozitivului;
- programare „nivel scăzut”;
- verificarea codului programului;
- instalarea unui cod de program de protecție;
- verificarea functionala a aparatului (imitarea muncii in conditii reale).
Toți acești pași se efectuează automat în 40 - 70 s. și invizibil pentru operator. Tot ceea ce vede operatorul sunt indicatori verzi sau roșii care indică succesul sau eșecul operațiunii. Ghidat de comanda programatorului, operatorul sortează pe loc piesele care au trecut operația în „bune” și „rele”. Vă rugăm să rețineți că operatorul are posibilitatea de a greși și de a plasa piesa în recipientul greșit.
La locul de asamblare finală sunt scanate codul de serie al produsului și blocul de memorie. În cazul lovirii unei piese care nu a trecut de programator, pe ecranul operatorului va apărea un mesaj de eroare pe fundal roșu, care vă va cere să înlocuiți piesa. Conectarea a două mașini la aceeași bază de date servește ca un sistem pentru a preveni intrarea pieselor de proastă calitate în produs.
Din păcate, Poka Yoke este doar o filozofie de asigurare a calității și nu conține sfaturi practice pentru a îmbunătăți procesele specifice. Cu toate acestea, să încercăm să formulăm postulatele și principiile de bază pentru implementarea acestei tehnici.
Aplicarea abordării poate fi împărțită în mai multe etape:
- Prioritizarea problemelor - această etapă este un început condiționat al procesului. Sensul acestei etape este de a clasifica toate problemele existente și de a direcționa eforturile către cele mai comune.
- Efectuarea analizei - o dată cel mai mult problema semnificativa, este necesar să se afle cauzele fundamentale ale apariției sale. Abordarea Poka Yoke presupune efectuarea de modificări care vor elimina complet apariția defectului. Implementarea unei astfel de abordări este posibilă numai în lupta împotriva cauzelor defectelor. În consecință, principiul protecției împotriva erorilor este valabil numai atunci când eforturile sunt îndreptate spre prevenirea erorii / cauzei, și nu a defectului - rezultatul erorii.
- Implementarea schimbării - este extrem de dificil de descris faza creativă a procesului, dar este foarte important de remarcat o caracteristică a acestei etape: implicarea personalului. Ca și în cazul multor alte abordări „japoneze” de asigurare a calității, factorul cheie de succes este implicarea activă a personalului în procesul de îmbunătățire continuă, astfel încât, în această etapă, rolul principal îl au angajații direct implicați în această operațiune. are două avantaje incontestabile: - în primul rând, numai operatorul cunoaște toate detaliile muncii la un anumit loc de muncă, în al doilea rând, implementarea modificărilor este mult mai ușoară și mai rapidă cu participarea directă a angajaților.
Există trei moduri (sau direcții) principale de a introduce schimbarea:
- Schimbarea procesului în așa fel încât proba defectă să fie neapărat observată de către operator. Un exemplu ar fi o listă de verificare completată de operator pentru fiecare produs. Acest exemplu foarte eficient în asamblarea unui singur om de produse complexe, cum ar fi matrițe, precum și în liniile de ambalare pentru produse precum aparatele electrice de uz casnic.
- Crearea unor astfel de condiții în care un eșantion defect nu poate ajunge la următorul pas al procesului, cum ar fi, de exemplu, cazul descris mai sus cu crearea unei baze de date comune pentru programator și stația de scanare a piesei.
- Crearea unui proces în care este exclusă apariția erorilor. Un exemplu excelent este descris mai sus pentru linia de asamblare a farurilor auto - zgârieturile pe lentilele farurilor instalate incorect pur și simplu nu pot apărea. Un astfel de far nu va putea intra în zona de risc potențial.
Există multe domenii de aplicare a principiului protecției împotriva erorilor, ne vom concentra pe unul dintre ele - securitatea umană. ÎN societate modernă folosim multe dispozitive și gadgeturi pentru a ne ajuta să lucrăm sau să ne jucăm. Beneficiile tuturor acestor articole se limitează la marele pericol pe care îl pot provoca pentru viața și sănătatea utilizatorului. Următoarele sunt exemple de implementare a abordării Poka Yoke pentru a asigura siguranța vieții umane:
- Blocare pentru copii la ușile mașinii: ușa cu opțiunea instalată nu poate fi deschisă din interior.
- Capacele duble pe borcanele de pastile si produse chimice de uz casnic preveni deschiderea accidentală și accesul copiilor.
- Detectoare de flacără aproape arzatoare pe gaz aragazele: când flacăra din arzător se stinge, alimentarea cu gaz se oprește automat.
- Cuptorul cu microunde se oprește automat când ușa este deschisă. Astfel, se previne expunerea la valuri dăunătoare și posibilitatea de deteriorare a membrelor.
- Apăsare manuală de pornire cu două butoane: operatorul trebuie să folosească ambele mâini pentru a apăsa două butoane. Astfel, este exclusă posibilitatea de a vătăma sănătatea operatorului.
- Componente suplimentare activate plăci de circuite imprimate Sensibil la șocuri: Când o încărcare este aplicată pe carcasă sau pe altă suprafață, componenta se va arde, împiedicând utilizatorul să fie electrocutat.
- Un exemplu excelent de implementare a principiului este prezentat în videoclip: ferăstrăul centrifugal se oprește la cel mai mic contact cu degetele unei persoane.
Filosofia managementului calității, bazată pe excluderea posibilității erorilor din sistem, vizează nu numai reducerea defectuosității procesului, ci și găsirea de soluții care nu necesită costuri semnificative. Această caracteristică diferențiază Poka Yoke de alte metode de îmbunătățire a procesului. Metodologia de aplicare a abordării nu se limitează la un set specific de instrumente sau metode, ceea ce o face universală și ușor de aplicat în orice domeniu al activității umane.