Technologie de pointe. Comment le carbone est fabriqué pour les supercars : pourquoi est-il si bon de fabriquer des pièces en carbone pour le bricolage ?
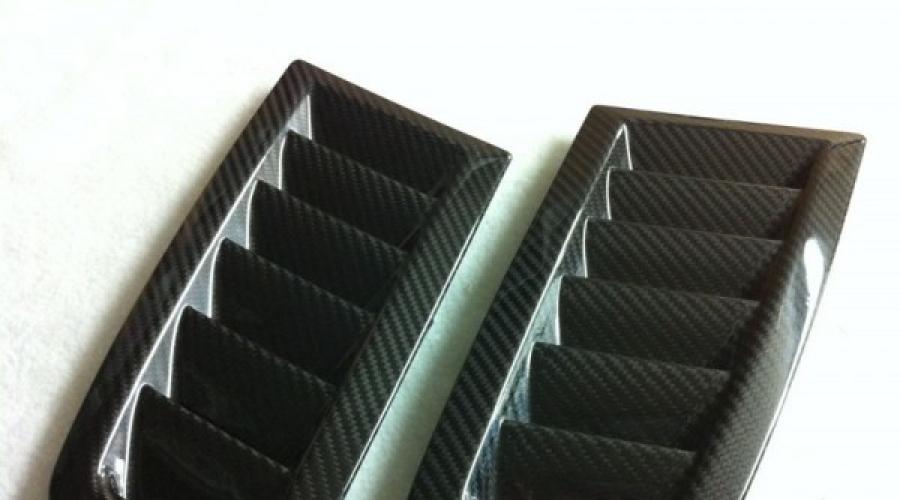
Lire aussi
Les matériaux composites polymères sont largement utilisés non seulement dans le monde de la production et du réglage des voitures de sport, mais également dans l'aviation et la construction navale. Plus tôt, nous avons examiné comment coller indépendamment une partie du corps avec un film de carbone. Voyons maintenant comment fabriquer de la fibre de carbone de vos propres mains.
Méthodes de fabrication
Les matériaux composites à base de fibres de carbone, également appelés matériaux composites à partir de filaments de fibres de carbone entrelacés, peuvent être fabriqués de 3 manières :
- méthode de moulage manuel ;
- procédé de formage sous vide ;
- production avec cuisson en autoclaves.
La production d'éléments en carbone à l'échelle industrielle nécessite un équipement coûteux. Par conséquent, à la maison, le carbone ne peut être produit qu'à la main ou par moulage sous vide.
Ce qu'il faut pour faire
Pour fabriquer du carbone, vous aurez besoin de :
- la fibre de carbone. Il diffère par le mode de tissage et la densité, mesurée en grammes par mètre carré (g / m2);
- séparateur (par exemple Loctite 770 NC). Il est utilisé pour séparer facilement l'élément carbone et la matrice après séchage. Le matériau est appliqué sur la matrice de la pièce ou sur une surface horizontale sur laquelle la couche avant de l'élément en carbone sera posée. La couche avant ne peut être qu'une seule, si sur verso pas besoin de créer une belle texture carbone ;
- matrice. Pour créer des parties horizontales, vous pouvez utiliser un morceau de verre ou un miroir. La surface doit être aussi lisse que possible, car tous les défauts de revêtement seront moulés sur la pièce fabriquée ;
- résine époxy (par exemple, EPR 320);
- durcisseur de résine (éventuellement EPH 294);
- outil de modèle de fibre de carbone. Vous pouvez utiliser des ciseaux ordinaires, mais préparez-vous au fait que couper la fibre émoussera rapidement l'outil. Si vous envisagez de produire en masse des pièces en carbone, nous vous recommandons d'acheter des ciseaux électriques (l'efficacité est montrée dans la vidéo).
Le besoin d'outils et de matériaux supplémentaires dépend de la méthode de fabrication choisie. Peu importe vos efforts, il ne fonctionnera pas de fabriquer du carbone durable par moulage à la main sans traitement thermique supplémentaire.
La méthode de fabrication est assez simple :
- la surface de la matrice est nettoyée de tous les contaminants ;
- un séparateur est appliqué uniformément sur toutes les surfaces, en plusieurs couches minces ;
- une couche de résine préparée est appliquée sur la surface;
- une couche de tissu de carbone est posée;
- la fibre est imprégnée de résine époxy. Il ne doit pas y avoir de bulles d'air entre la première couche et la matrice, ainsi qu'entre les couches suivantes. Vous pouvez répartir la résine avec un pinceau ordinaire, il est pratique de chasser les bulles d'air avec un rouleau;
- la couche suivante est appliquée, après quoi la procédure est répétée jusqu'à ce que l'épaisseur requise de la pièce soit atteinte;
- après la pose de la couche finale, les parties horizontales peuvent être pressées avec un morceau de verre ou de miroir correspondant. Dans ce cas, les deux côtés de la pièce recevront une surface brillante et une structure en carbone clair.
Le coût de la fibre de carbone ne pouvant être qualifié de démocratique, la fibre de verre peut être posée entre la première et la dernière couche de tissu de carbone. La fibre de verre ne doit pas être rugueuse pour ne pas casser la forme finale.
Pour réduire le coût de fabrication des pièces légères, l'élément n'est souvent laminé qu'avec de la fibre de carbone - il n'est posé que comme couche avant de l'élément de carrosserie.
Méthode de formage sous vide
En plus de l'ensemble standard de matériaux et d'outils, pour la fabrication d'éléments en carbone par infusion sous vide, vous aurez besoin de :
- tissu sacrificiel;
- maille conductrice. Utilisé pour la distribution de résine et l'extraction d'air ;
- film sous vide. Vous ne pouvez pas utiliser de film ordinaire, car il ne résiste pas aux températures élevées et n'a pas haute capacitéétirer;
- Pompe à vide. Pour la fabrication de petites pièces, une simple pompe à huile à un étage fera l'affaire;
- harnais d'étanchéité;
- tube en spirale pour l'alimentation en résine et l'admission d'air ;
- tuyau d'aspirateur;
- colliers pour tubes (colliers);
- piège à vide. Il est utilisé comme piège à résine époxy, qui endommagera la pompe à vide si elle pénètre dans la pompe à vide. Vous pouvez construire un piège de vos propres mains à partir de moyens improvisés.
Un four pour les éléments en carbone post-durcissement peut également être construit de vos propres mains. Veuillez noter que le traitement thermique doit être effectué à une certaine température, vous devez donc envisager la possibilité d'ajuster et de maintenir un degré donné.
La technologie d'infusion sous vide consiste à assembler un "sandwich" de tissu de carbone et à le placer dans un espace étanche. Après la pose, l'air est pompé et la résine est fournie à la pièce.
Le tissu imprégné de résine est laissé sous vide pendant 20 à 30 minutes, scellant les tubes d'alimentation en résine et de purge d'air. 24 heures suffisent pour le rejet initial et température ambiante, après quoi la pièce en carbone doit être envoyée pour une post-cuisson au four.
Nous n'avons pas décrit en détail la méthode d'infusion sous vide, car le processus est montré en détail dans la vidéo.
Source : http://AutoLirika.ru/tuning/karbon-svoimi-rukami.html
Comment fabriquer de la fibre de carbone de vos propres mains
La fibre d'hydrocarbure ou carbone est un matériau "tissé" à partir de filaments de carbone. Ils sont aussi fins qu'un cheveu humain, mais aussi solides que l'acier. Ils sont très difficiles à casser, mais il est tout à fait possible de les casser.
C'est pourquoi plusieurs couches de fibre de carbone sont utilisées dans la production de pièces. En appliquant des couches de carbone les unes sur les autres dans un ordre différent, les fabricants obtiennent la plus grande résistance à l'usure et aux chocs.
Malgré sa « jeunesse », le carbone est déjà solidement ancré sur le marché des matériaux de haute technologie.
Utilisation du carbone
Au début, des spécialistes de l'espace et de l'armée se sont intéressés à lui. Je le ferais encore ! Une substance qui vous permet de perdre du poids plusieurs fois et qui possède en même temps d'excellents indicateurs de force - n'est-ce pas un miracle?
Puis la fibre de carbone a progressivement commencé à conquérir l'industrie automobile. Au début, il s'agissait de pièces séparées qui nécessitaient des résultats élevés en matière de résistance à la déchirure, mais maintenant, le carbone sert le plus souvent de décoration exclusive d'une voiture, par exemple, de «jupe» en carbone.
Et maintenant, relativement récemment, les fibres d'hydrocarbures ont commencé à être utilisées au profit de réalisations sportives. En particulier, il est largement utilisé pour créer un cadre de vélo.
Un hommage à la mode ou un pas vers le futur ?
Depuis de nombreuses années, les cadres de vélo sont en acier ou en aluminium. Solide, léger, durable - il est idéal pour le cyclotourisme et les marathons professionnels. Mais peu à peu la place du fer est occupée par le carbone, nettement supérieur au métal à bien des égards.
De plus en plus, on trouve des vélos en carbone lors de tournois cyclistes, et les amateurs de promenades ordinaires dans le parc n'hésitent pas à acheter des modèles coûteux. Un tel engouement pour les nouvelles technologies est-il justifié ou s'agit-il simplement d'une autre mode ?
Le principal secret de la fibre de carbone réside dans sa fabrication. Difficile processus technologique la cuisson des pièces, leur sciage et leur raccordement donne un gage de fiabilité. Cependant, à la recherche de profits rapides, les entreprises d'un jour réduisent souvent les étapes et les délais de production, dégradant ainsi considérablement les performances techniques.
De tels cadres en carbone ne peuvent pas être distingués à l'œil nu de leurs homologues de haute qualité, mais avec tout dommage, même le plus insignifiant, le vélo s'effondrera littéralement sous le propriétaire.
Pourtant, c'est la demande qui crée l'offre.
Voulant être à la mode et économiser de l'argent en même temps, de nombreux cyclistes sont prêts à tenter leur chance et à acheter un vélo souterrain en carbone.
Acier ou carbone ?
Le principal concurrent de la fibre de carbone en termes de fiabilité et de durabilité est l'acier. De nombreux conservateurs pensent que le métal est beaucoup plus adapté à la fabrication de cadres de vélos. Et il y a de bonnes raisons à cela :
- Prix. Le coût d'un vélo typique en fibre de carbone de qualité douteuse est beaucoup plus élevé que le prix d'un cadre en acier sur mesure.
- Durabilité. Sur les sites Web et les pages de journaux, vous pouvez souvent voir des annonces pour la vente d'un «cheval d'acier» à la main. Même après 10, 20, 30 ans, le vélo ne perd pas ses principales caractéristiques. Juste fané avec le temps. Dans le même temps, la vente d'un vélo en fibre de carbone d'occasion est un cas rare. Le cadre d'un tel vélo ne trouve pas toujours un second propriétaire.
- Réparation. Et voilà, il est temps pour les amateurs de métal de se réjouir. Le fait est qu'avec un fort impact, le cadre en carbone ne se plie pas, mais se brise en morceaux. Comme un vase brisé sur des tuiles.
Comment fabriquer de la fibre de carbone automobile ou de la fibre de carbone de vos propres mains
Autrement dit, restaurer un ami à deux roues est inutile et coûteux. Cela n'a aucun sens de parler de la réparation de charpentes en acier. Chaque passionné de vélo ayant au moins une fois l'expérience de souder ou d'aligner des pièces par lui-même. Oui, apparence le vélo après, franchement, ce n'est pas festif, mais ça n'a plus vraiment d'importance.
Et pourtant, le cadre carbone trouve son consommateur. Après tout la dernière technologie les fabricants offrent des avantages indéniables de leur produit. Premièrement, le poids d'un cadre en fibre de carbone peut être inférieur à un kilogramme.
Peut-être pour faire le tour de la maison ou aller au magasin, cet argument n'est pas très pertinent. Mais la légèreté du vélo sera pleinement appréciée des amateurs de circuits touristiques au long cours.
Lorsqu'un vélo doit être transporté en montée, chaque gramme compte.
Deuxièmement, l'amortissement d'un tel véhicule est pensé dans les moindres détails. Pas une seule bosse ou butte ne résonnera plus désagréablement dans tous les organes du cavalier.
Le cadre en carbone reste immobile. C'est un plus indéniable. Et, troisièmement, grâce à la couleur et à la texture de la fibre de carbone, le vélo est élégant et à la mode.
Ce n'est pas une honte d'emmener une fille à un rendez-vous !
Les principaux fournisseurs de cadres en carbone bon marché sont des fabricants de Taiwan.
secrets de fabrication
De nombreux mastodontes de l'accastillage vélo choisissent de plus en plus de recentrer la production sur les pièces en fibre de carbone. Et cela est tout à fait compréhensible.
Tout d'abord, le cadre en carbone du vélo est fait à la main, avec un apport mécanique minimal. Et cela signifie que vous pouvez économiser le nombre de travaux et ne pas être gaspillé par la réparation d'équipements coûteux.
Deuxièmement, la demande pour les dernières technologies ne fait qu'augmenter, ce qui signifie qu'elle promet de gros profits. Et nous ne parlons pas seulement d'acheteurs ordinaires, mais aussi de stars du cyclisme de classe mondiale ! Alors, à quoi ressemble le processus de fabrication du carbone ?
- Le plus souvent, le CFRP entre dans l'usine sous forme de feuilles imprégnées de résine. Moins souvent - comme des bobines de fil;
- Le matériau est coupé en morceaux qui correspondent aux pièces du vélo. Cependant, déjà ici, les fabricants tiennent compte du fait que lors de l'application de couches, les fibres doivent «regarder» dans des directions différentes pour une plus grande fiabilité. Par conséquent, les bandes d'hydrocarbures ne s'adaptent pas toujours parfaitement à la forme souhaitée ;
- Ensuite, il y a la création réelle d'un miracle. La fibre de carbone est chauffée et, pour ainsi dire, moulée avec son aide un cadre de vélo. Ce processus nécessite la plus grande attention et concentration;
- Passons au chaud. Toutes les pièces sont fixées et placées sur un formulaire spécial. Destination : four ! ;
- Après plusieurs heures de languissement, le cadre en carbone est retiré et laissé refroidir. Au même stade, tous les joints, irrégularités et défauts sont vérifiés;
- Vous pouvez maintenant faire le ponçage. Toute la base du futur vélo sera nettoyée et peinte ;
- Le cadre est prêt !
DIY
Malgré le processus technologique assez laborieux, les artisans parviennent à recréer des cadres en carbone de leurs propres mains.
Sur Internet, vous pouvez trouver de nombreuses vidéos et instructions photo avec des descriptions sur ce sujet, allant des dessins à la température du four.
Étonnamment, ils font vraiment un super cadre! Peut-être que cela fonctionnera pour vous aussi? Après tout, créer son propre vélo de ses propres mains est vraiment un plaisir inestimable !
Le cadre en carbone d'un vélo fait l'objet de longues et houleuses discussions sur Internet. Certains considèrent que c'est kitsch cher mais dénué de sens.
D'autres sont convaincus que le temps de l'aluminium et de l'acier est révolu et que l'avenir est maintenant haute technologie. Que ce soit pour dépenser tout votre argent dans l'achat de carbone, c'est à vous de décider.
Cependant, cela vaut la peine de réfléchir à nouveau et de faire le bon choix.
Comment fabriquer de la fibre de carbone de vos propres mains | Plaque CFRP | Comment faire une plaque de fibre de carbone
Carbone (tissu carbone) (12)
Bref contenu de l'article : Tissu en fibre de carbone (Carbon), réglage de la voiture de vos propres mains, Envoi le jour de la commande Paiement à la livraison, reportage photo de l'emballage ! Ainsi que d'autres tissus de style - tissus hybrides, fibre de carbone, tissu de carbone, carbonisé, placer, ajouter, aramide, qu'est-ce que le carbone, biens, services, recherche, Kaliningrad et région de Kaliningrad, Russie, région de Moscou et Moscou. acheter carbone, carbone à faire soi-même, tissu carbone, fibre de carbone, noir de carbone 3d, réglage, fibre de carbone, tissu carbone, tissu aramide, fibre de carbone, technologie carbone, fibre de verre, acheter carbone, carbone, articles de réglage, résines, époxy , vide, pompes, Twill2x2, Twill4x4, Russie, prix, offre, catalogue, placer, ajouter, biens, services, recherche, Kaliningrad et région de Kaliningrad, Russie, région de Moscou et Moscou, Saint-Pétersbourg, Iekaterinbourg, Kazan, Iekaterinbourg, Krasnodar , Krasnoyarsk, Chelyabinsk, Magnitogorsk, Surgut, Naberezhnye Chelny, Vladimir, Volgograd bricolage fibre de carbone
Source : Carbone, bricolage, fabrication de tous produits à partir de Carbone, tissu Carbone, Kevlar, tissus hybrides. - -=Frères S.R.=-
En réalité nous parlerons pas sur la fabrication de pièces en fibre de carbone, mais sur l'application de fibre de carbone sur des pièces finies, des pièces de carrosserie ou des pièces intérieures. Décorer les pièces avec de la fibre de carbone si vous le souhaitez.
Si la fabrication d'une pièce entièrement en carbone est un processus plutôt compliqué, alors l'imposition de carbone sur pièce finie une procédure assez simple qui ne nécessite aucune compétence particulière. Tout ce dont tu as besoin c'est matériaux nécessaires, expérience élémentaire avec l'époxy et la précision.
Étape 1 : Nous retirons de la voiture les pièces que nous avons décidé de recouvrir de fibre de carbone. Il s'agira très probablement d'une sorte de partie en plastique de l'intérieur.
Nous traitons le détail sélectionné avec du papier de verre et le peignons dans la couleur principale du tissu en carbone. Il sera très probablement noir.
Cette peinture est nécessaire pour que la vraie couleur de la pièce (gris ou marron, comme dans les premiers Samars) ne transparaisse pas à travers la toile de carbone.
Étape 2 : Nous appliquons le tissu de carbone sur la pièce et déterminons comment nous allons le couper pour qu'il soit avec une marge. Nous collons avec du ruban adhésif où nous allons couper le tissu de carbone. Cela est nécessaire pour que le tissu ne fleurisse pas.
Étape 3 : Remuez l'époxy et appliquez-le uniformément sur la pièce. Après cela, nous commençons à appliquer progressivement du tissu de carbone sur la pièce. Assurez-vous que le tissu est bien ajusté contre la pièce et qu'il n'y a pas de bulles d'air.
Étape 4 : Nous attendons que le tissu adhère bien à la surface de la pièce, après quoi nous mélangeons plus d'époxy et commençons à bien en imbiber le tissu de carbone. L'époxy doit être bien absorbé par le tissu, qui peut prendre plusieurs couches de résine
Étape 5 : On attend que cette couche d'époxy sèche et on applique une autre couche, celle-ci est la dernière. Si vous avez des bulles d'air, vous pouvez les expulser avec chalumeau. Si l'air n'est pas expulsé, il détruira plus tard votre pièce.
Étape 6 : Une fois la dernière couche de résine durcie, nous prenons un papier de verre très fin et retirons la couche supérieure de résine légèrement jaunie du chalumeau. Ensuite, nous polissons la surface avec un polish et c'est tout. La pièce est prête à l'emploi. Au final, vous devriez obtenir quelque chose comme ça
C'est à quoi ils ressemblent pièces en plastique recouvert de carbone
D'ailleurs…
1.
Fabrication de carbone
Faites au moins 4 couches de résine, et encore plus c'est mieux. Cela évitera au tissu de se déchirer lorsque vous commencerez à le poncer. 2.
Essayez d'abord sur une petite pièce, et surtout plate, ce qui n'est pas si dommage, puis passez à des pièces plus complexes avec des coudes.
La partie la plus difficile de toute cette procédure consiste à poser le tissu de carbone sur la pièce.
Si, malgré tout, il vous arrivait de vous tromper, alors mettez votre pièce au congélateur pendant plusieurs heures. Ensuite, il suffit de tordre légèrement la pièce et la couche tombera.
Discutez de l'application de carbone aux pièces sur le forum
Comme nous l'avons déjà mentionné plus d'une fois, le modding informatique et le tuning automobile ont beaucoup en commun, ce qui explique probablement pourquoi de nombreux moddeurs sont constamment amenés à utiliser divers matériaux composites, tels que la fibre de verre, dans leurs projets de modding. Le matériau composite le plus emblématique dans le monde du tuning automobile est sans aucun doute la fibre de carbone ou simplement la fibre de carbone.
L'utilisation de vraie fibre de carbone est un processus beaucoup plus laborieux que l'utilisation de vinyle décoratif aspect carbone, c'est pourquoi la vraie fibre de carbone est si rare dans le modding.
Clin d'œil à faire soi-même en fibre de carbone, fibre de carbone, n'importe quelle longueur
Cependant, ce n'est pas une raison pour ne pas utiliser du vrai carbone dans le modding informatique.
Il y en a assez différentes options fabrication de pièces en fibre de carbone et peuvent facilement être couvertes par plusieurs articles, mais seuls deux d'entre eux conviennent à Utilisation à la maisonà moins, bien sûr, que vous ayez une pompe à vide et un autoclave à la maison
Source : https://stroyvolga.ru/%D1%83%D0%B3%D0%BB%D0%B5%D0%BF%D0%BB%D0%B0%D1%81%D1%82%D0%B8 %D0%BA-%D1%81%D0%B2%D0%BE%D0%B8%D0%BC%D0%B8-%D1%80%D1%83%D0%BA%D0%B0%D0%BC %D0%B8-%D0%BA%D0%B0%D0%BA-%D1%81%D0%B4%D0%B5%D0%BB%D0%B0/
Fabrication de pièces en carbone
La qualité des pièces en carbone dépend principalement de bon choix et la qualité de la toile de résine et de carbone. Si vous faites des erreurs dans le choix de la densité de la bande de fibres de carbone et du taux de solidification du mélange de résine, vous ne pourrez pas déposer soigneusement la pièce dans le moule, la presser fermement et éliminer complètement les bulles d'air.
Méthodes de base pour la fabrication de pièces en carbone
Les principales méthodes de fabrication de pièces en fibre de carbone comprennent:
- moulage à partir de préimprégnés, c'est-à-dire de produits semi-finis,
- moulage directement dans le moule,
- Procédé d'application.
Fabriquer de la fibre de carbone à la maison ne nécessite pas d'équipement sophistiqué et, avec certaines compétences, vous pouvez obtenir des pièces de qualité décente. Il est donc tout à fait possible de fabriquer soi-même du carbone de qualité satisfaisante.
Carbone pour le réglage de la voiture
Attention! Le soi-disant "3D-carbone", l'autovinyle n'a rien à voir avec le carbone, si ce n'est une excellente imitation de la surface du carbone. Ce sont des films colorés en vinyle et PVC avec des effets visuels uniquement pour finitions décoratives surface, mais pas pour le durcissement.
Mais pour la fabrication de certains éléments légers nécessitant une résistance élevée, par exemple pour les pare-chocs, les capots, les petites pièces de carrosserie, du carbone véritable coûteux peut être utilisé.
Vous pouvez même essayer de fabriquer vous-même des éléments de petite taille recouverts de fibre de carbone.
Mais il faut se rappeler que ce matériau est très sensible aux chocs ponctuels, et qu'il existe un risque d'endommagement par les petits cailloux et gravats sous les roues.
Si pour vous le rôle principal est joué par les paramètres esthétiques, et non l'allégement du poids d'une voiture ou d'une moto, alors regardez de plus près les films PVC aspect carbone, l'aqua-printing ou l'aérographe.
Production de préimprégnés de pièces en carbone
Le processus industriel de formation d'un produit à partir d'un préimprégné (formation d'ébauches) dans un autoclave est un flux simultané de processus complexes :
- polymérisation des composés,
- élimination sous vide de l'air et de l'excès de résine,
- la haute pression (jusqu'à 20 atm) presse toutes les couches sur la matrice, les compactant et les nivelant.
C'est un processus coûteux, par conséquent, pour un réglage à petite échelle à la maison, il est peu utile.
Mais la séparation de ces processus réduit le coût et allonge toute la procédure d'autoproduction de carbone. Dans le même temps, des modifications sont apportées à la technologie de préparation du préimprégné, vous devez donc toujours faire attention à la technologie à laquelle le préimprégné est destiné.
Dans ce cas, le préimprégné est préparé en sandwich. Après application de la résine, la pièce est recouverte des deux côtés d'un film de polyéthylène et passée entre deux axes.
Cela élimine l'excès de résine et l'air indésirable. Le préimprégné est pressé dans la matrice par un poinçon, et l'ensemble de la structure est placé dans une étuve.
Autrement dit, dans ce cas, le préimprégné est une préforme complètement prête pour le moulage, avec des couches comprimées et de l'air éliminé.
Cette méthode est le plus souvent utilisée par les ateliers de réparation automobile, achetant des ébauches de carbone, et les matrices sont en albâtre ou en gypse, parfois elles sont usinées à partir de métal, ou la pièce elle-même est utilisée comme modèle. que vous voulez répéter à partir du carbone. Parfois, les modèles sont découpés dans de la mousse et laissés à l'intérieur de la pièce finie.
La fibre de carbone à faire soi-même est le moyen le plus simple de réaliser la méthode de «recouvrement» ou l'application de fibre de carbone sur la pièce.
Méthode d'application (collage manuel)
Vous pouvez fabriquer de la fibre de carbone de vos propres mains en utilisant la méthode de collage, qui comprend cinq étapes principales :
- Préparation soignée de la surface encollée : ponçage, dégraissage, arrondissage des angles.
- Application d'adhésif.
- Collage de tissu carbone imprégné de résine époxy et de durcisseur.
- Séchage.
- Revêtement avec vernis protecteur ou peinture.
Les charges de résine sont utilisées à la fois à des fins décoratives et pour empêcher la résine de couler sur les surfaces verticales.
Matériel nécessaire
- Adhésif pour fixer le tissu de carbone à la surface.
- Tissu en fibre de carbone, qui est posé sur la résine en couches, avec un rouleau dur.
- Epoxy de viscosité moyenne avec durcisseur (parfois utilisé comme adhésif).
- Vernis de protection. Le polyuréthane est le meilleur pour la protection contre les rayures. Vous devez choisir imperméable et résistant à la lumière. Il ne s'estompe pas. La laque acrylique peut être utilisée comme couche de finition pour une brillance élevée.
La résine est appliquée 2 à 3 fois avec séchage intermédiaire et polissage.
Cette méthode diffère de la fabrication de carbone traditionnelle basée sur un modèle en appliquant un adhésif plutôt qu'un agent de démoulage pour un retrait facile du produit semi-fini résultant.
3M propose même des feuilles de carbone auto-adhésives, mais leur utilisation nécessite de bonnes compétences.
Et le carbone reste sur la partie collée, la renforçant. Cette production de fibre de carbone est le plus souvent utilisée pour coller des pare-chocs, des tableaux de bord, etc.
Méthode de moulage sous vide
Cette méthode nécessite équipement spécial et de bonnes compétences.
- Application d'un agent de démoulage sur la surface du modèle. Pour les surfaces mates et semi-brillantes, on utilise généralement une cire de démoulage, et pour les surfaces brillantes (plastique et métal), on utilise un agent de démoulage et des solutions d'apprêt de type WOLO, qui sont utilisés dans la production à petite échelle.
- Disposition du tissu de carbone dans une matrice, sans rides ni bulles.
- Imprégnation du tissu de carbone avec de la résine.
- Il peut y avoir plusieurs couches. Dans certains cas, le tissu de carbone peut être alterné avec de la fibre de verre.
- Superposer un film perforé pour faire sortir l'excès de résine et libérer l'air. Il est conseillé de se superposer.
- Tampon absorbant.
- Installation d'un tube à vide et d'un orifice pour le raccordement d'une pompe à vide.
- Mise en place de l'ensemble de la structure dans un film sous vide résistant, collage avec un harnais d'étanchéité sur l'outillage.
L'ensemble de la procédure ressemble au placement d'un objet dans sacs sous vide, qui sont vendus dans les magasins pour stocker des objets, puis en pomper l'air.
Au fait, vous pouvez expérimenter de tels sacs sous vide. Ils sont très résistants et sont disponibles dans une variété de tailles.
Une pompe à vide pour Utilisation à la maison coûtera en moyenne 150-200 $.
Méthode de formage avec pression (roulage manuel)
Il est appliqué pour auto-fabrication pièces en carbone et est similaire à la méthode de formage sous vide, mais sans l'utilisation d'outils coûteux. Les kits comprennent des pinceaux pour l'application de résine et des rouleaux pour l'extrusion à l'air et la stratification.
Pour un simple réglage de voiture, vous aurez besoin de:
- toile de carbone d'une densité de 200-300 g/m,
- époxy,
- durcisseur,
- rouleau dur et pinceau.
Sur Alibaba.com, 200 g/m². le sergé de tissage est offert à des prix allant de 10 $ à 25 $ par mètre carré. C'est vrai, et vous devez acheter à partir de 10 mètres. Mais vous pouvez accepter de recevoir des échantillons qui vous permettront de produire de manière indépendante de petits produits en carbone.
Une cire séparatrice, gelcoat est appliquée à la surface du moule pour former une couche protectrice et décorative sur la surface du produit fini. Après séchage, un mélange époxy pour fibre de carbone est appliqué au pinceau et la pose de la fibre de carbone commence.
Chaque couche est roulée pour éliminer les bulles d'air et obtenir une adhérence maximale. Après séchage complet à l'air ou en étuve, la pièce est retirée de la matrice, polie, recouverte d'un vernis protecteur.
Avec cette méthode, on obtient une consommation de résine élevée (trois fois supérieure à la densité de la fibre de carbone), mais c'est ainsi que l'on peut fabriquer n'importe quelle pièce en carbone de ses propres mains.
Les matériaux composites polymères sont largement utilisés non seulement dans le monde de la production et du réglage des voitures de sport, mais également dans l'aviation et la construction navale. Plus tôt, nous avons examiné comment coller indépendamment une partie du corps avec un film de carbone. Voyons maintenant comment fabriquer de la fibre de carbone de vos propres mains.
Méthodes de fabrication
Les matériaux composites à base de fibres de carbone, également appelés matériaux composites à partir de filaments de fibres de carbone entrelacés, peuvent être fabriqués de 3 manières :
- méthode de moulage manuel ;
- procédé de formage sous vide ;
- production avec cuisson en autoclaves.
La production d'éléments en carbone à l'échelle industrielle nécessite un équipement coûteux. Par conséquent, à la maison, le carbone ne peut être produit qu'à la main ou par moulage sous vide.
Ce qu'il faut pour faire
Pour fabriquer du carbone, vous aurez besoin de :
- la fibre de carbone. Il diffère par le mode de tissage et la densité, mesurée en grammes par mètre carré (g / m2);
- séparateur (par exemple Loctite 770 NC). Il est utilisé pour séparer facilement l'élément carbone et la matrice après séchage. Le matériau est appliqué sur la matrice de la pièce ou sur une surface horizontale sur laquelle la couche avant de l'élément en carbone sera posée. La couche avant ne peut être qu'une seule, si la face arrière ne nécessite pas la création d'une belle texture carbone ;
- matrice. Pour créer des parties horizontales, vous pouvez utiliser un morceau de verre ou un miroir. La surface doit être aussi lisse que possible, car tous les défauts de revêtement seront moulés sur la pièce fabriquée ;
- résine époxy (par exemple, EPR 320);
- durcisseur de résine (éventuellement EPH 294);
- outil de modèle de fibre de carbone. Vous pouvez utiliser des ciseaux ordinaires, mais préparez-vous au fait que couper la fibre émoussera rapidement l'outil. Si vous envisagez de produire en masse des pièces en carbone, nous vous recommandons d'acheter des ciseaux électriques (l'efficacité est montrée dans la vidéo).
Le besoin d'outils et de matériaux supplémentaires dépend de la méthode de fabrication choisie. Peu importe vos efforts, il ne fonctionnera pas de fabriquer du carbone durable par moulage à la main sans traitement thermique supplémentaire.
Méthode de moulage à la main
La méthode de fabrication est assez simple :
- la surface de la matrice est nettoyée de tous les contaminants ;
- un séparateur est appliqué uniformément sur toutes les surfaces, en plusieurs couches minces ;
- une couche de résine préparée est appliquée sur la surface;
- une couche de tissu de carbone est posée;
- la fibre est imprégnée de résine époxy. Il ne doit pas y avoir de bulles d'air entre la première couche et la matrice, ainsi qu'entre les couches suivantes. Vous pouvez répartir la résine avec un pinceau ordinaire, il est pratique de chasser les bulles d'air avec un rouleau;
- la couche suivante est appliquée, après quoi la procédure est répétée jusqu'à ce que l'épaisseur requise de la pièce soit atteinte;
- après la pose de la couche finale, les parties horizontales peuvent être pressées avec un morceau de verre ou de miroir correspondant. Dans ce cas, les deux côtés de la pièce recevront une surface brillante et une structure en carbone clair.
Le coût de la fibre de carbone ne pouvant être qualifié de démocratique, la fibre de verre peut être posée entre la première et la dernière couche de tissu de carbone. La fibre de verre ne doit pas être rugueuse pour ne pas casser la forme finale.
Pour réduire le coût de fabrication des pièces légères, l'élément n'est souvent laminé qu'avec de la fibre de carbone - il n'est posé que comme couche avant de l'élément de carrosserie.
Méthode de formage sous vide
En plus de l'ensemble standard de matériaux et d'outils, pour la fabrication d'éléments en carbone par infusion sous vide, vous aurez besoin de :

Un four pour les éléments en carbone post-durcissement peut également être construit de vos propres mains. Veuillez noter que le traitement thermique doit être effectué à une certaine température, vous devez donc envisager la possibilité d'ajuster et de maintenir un degré donné.
La technologie d'infusion sous vide consiste à assembler un "sandwich" de tissu de carbone et à le placer dans un espace étanche. Après la pose, l'air est pompé et la résine est fournie à la pièce. Le tissu imprégné de résine est laissé sous vide pendant 20 à 30 minutes, scellant les tubes d'alimentation en résine et de purge d'air. 24 heures et la température ambiante suffisent pour le durcissement initial, après quoi la pièce en carbone doit être envoyée pour post-durcissement au four. Nous n'avons pas décrit en détail la méthode d'infusion sous vide, car le processus est montré en détail dans la vidéo.
Les matériaux composites polymères sont largement utilisés non seulement dans le monde de la production et du réglage des voitures de sport, mais également dans l'aviation et la construction navale. Auparavant, nous avons examiné comment indépendamment. Voyons maintenant comment fabriquer de la fibre de carbone de vos propres mains.
Méthodes de fabrication
Les matériaux composites à base de fibres de carbone, également appelés matériaux composites à partir de filaments de fibres de carbone entrelacés, peuvent être fabriqués de 3 manières :
- méthode de moulage manuel ;
- procédé de formage sous vide ;
- production avec cuisson en autoclaves.
La production d'éléments en carbone à l'échelle industrielle nécessite un équipement coûteux. Par conséquent, à la maison, le carbone ne peut être produit qu'à la main ou par moulage sous vide.
Ce qu'il faut pour faire
Pour fabriquer du carbone, vous aurez besoin de :
- la fibre de carbone. Il diffère par le mode de tissage et la densité, mesurée en grammes par mètre carré (g / m2);
- séparateur (par exemple Loctite 770 NC). Il est utilisé pour séparer facilement l'élément carbone et la matrice après séchage. Le matériau est appliqué sur la matrice de la pièce ou sur une surface horizontale sur laquelle la couche avant de l'élément en carbone sera posée. La couche avant ne peut être qu'une seule, si la face arrière ne nécessite pas la création d'une belle texture carbone ;
- matrice. Pour créer des parties horizontales, vous pouvez utiliser un morceau de verre ou un miroir. La surface doit être aussi lisse que possible, car tous les défauts de revêtement seront moulés sur la pièce fabriquée ;
- résine époxy (par exemple, EPR 320);
- durcisseur de résine (éventuellement EPH 294);
- outil de modèle de fibre de carbone. Vous pouvez utiliser des ciseaux ordinaires, mais préparez-vous au fait que couper la fibre émoussera rapidement l'outil. Si vous envisagez de produire en masse des pièces en carbone, nous vous recommandons d'acheter des ciseaux électriques (l'efficacité est montrée dans la vidéo).
Le besoin d'outils et de matériaux supplémentaires dépend de la méthode de fabrication choisie. Peu importe vos efforts, il ne fonctionnera pas de fabriquer du carbone durable par moulage à la main sans traitement thermique supplémentaire.
Méthode de moulage à la main
La méthode de fabrication est assez simple :
- la surface de la matrice est nettoyée de tous les contaminants ;
- un séparateur est appliqué uniformément sur toutes les surfaces, en plusieurs couches minces ;
- une couche de résine préparée est appliquée sur la surface;
- une couche de tissu de carbone est posée;
- la fibre est imprégnée de résine époxy. Il ne doit pas y avoir de bulles d'air entre la première couche et la matrice, ainsi qu'entre les couches suivantes. Vous pouvez répartir la résine avec un pinceau ordinaire, il est pratique de chasser les bulles d'air avec un rouleau;
- la couche suivante est appliquée, après quoi la procédure est répétée jusqu'à ce que l'épaisseur requise de la pièce soit atteinte;
- après la pose de la couche finale, les parties horizontales peuvent être pressées avec un morceau de verre ou de miroir correspondant. Dans ce cas, les deux côtés de la pièce recevront une surface brillante et une structure en carbone clair.
Le coût de la fibre de carbone ne pouvant être qualifié de démocratique, la fibre de verre peut être posée entre la première et la dernière couche de tissu de carbone. La fibre de verre ne doit pas être rugueuse pour ne pas casser la forme finale.
Pour réduire le coût de fabrication des pièces légères, l'élément n'est souvent laminé qu'avec de la fibre de carbone - il n'est posé que comme couche avant de l'élément de carrosserie.
Méthode de formage sous vide
En plus de l'ensemble standard de matériaux et d'outils, pour la fabrication d'éléments en carbone par infusion sous vide, vous aurez besoin de :

Un four pour les éléments en carbone post-durcissement peut également être construit de vos propres mains. Veuillez noter que le traitement thermique doit être effectué à une certaine température, vous devez donc envisager la possibilité d'ajuster et de maintenir un degré donné.
La technologie d'infusion sous vide consiste à assembler un "sandwich" de tissu de carbone et à le placer dans un espace étanche. Après la pose, l'air est pompé et la résine est fournie à la pièce. Le tissu imprégné de résine est laissé sous vide pendant 20 à 30 minutes, scellant les tubes d'alimentation en résine et de purge d'air. 24 heures et la température ambiante suffisent pour le durcissement initial, après quoi la pièce en carbone doit être envoyée pour post-durcissement au four. Nous n'avons pas décrit en détail la méthode d'infusion sous vide, car le processus est montré en détail dans la vidéo.
- matériau composite polymère de brins de fibres de carbone entrelacés, situé dans une matrice de résines époxy. Les plus courants d'entre eux sont :
- méthode de moulage manuel ;
- méthode d'injection Résine de polyester;
- méthode d'infusion sous vide.
Où commence la production ?
Ainsi, pour créer une pièce par vous-même, vous devez d'abord créer une forme. Pour ce faire, vous pouvez utiliser presque tous les matériaux pouvant contenir une forme donnée et avec lesquels il vous convient de travailler. ça peut être du gypse mortier de ciment, et le plastique, le bois et le métal - tout dépend du type de pièce que vous fabriquez et de ce qu'il est plus facile pour vous de travailler personnellement.Une fois la forme prête (durcie, séchée - si nécessaire), nous appliquons du gelcoat sur sa surface à l'aide d'un rouleau, d'un pinceau ou d'un pulvérisateur - une substance à base de résine époxy vinylester. Il jouera le rôle d'une couche extérieure protectrice et décorative de notre futur produit, en raison de sa résistance suffisamment élevée et large couleurs, à partir de laquelle vous devez choisir la teinte dont vous avez besoin. Gelkonat protégera remarquablement la pièce des agressions environnement externe, y compris l'exposition à l'humidité et à la lumière du soleil.
Après le séchage du gelconate, vous pouvez commencer à mouler le produit lui-même. Pour ce faire, nous procédons à la découpe du matériau carbone (il peut s'agir de fibre de verre, de mat de verre ou de tissu en fibre de carbone) sous taille requise, placez dans la matrice préparée (notre formulaire) et appliquez au rouleau ou au pinceau un mélange de liant composé de résine polyester et de durcisseur. Cela doit être fait avec le plus de soin et d'efficacité possible, en veillant notamment à ce qu'il n'y ait pas de bulles d'air dans la structure de la pièce. Dans le même but, à la fin du moulage, mais avant qu'il ne durcisse, nous "roulons" la pièce avec un rouleau dur en en faisant sortir les bulles d'air (plus il reste d'air dans la matrice après séchage, moins votre pièce sera fiable être!
Fabriquer de la fibre de carbone à la maison

Lors de la création d'une surface en carbone, il est très important de faire attention au fait qu'il n'y a pas de bulles à la surface des pièces. Pour cela, il est nécessaire d'initialiser le processus d'infusion ou de moulage sous vide. L'équipement pour de telles opérations coûte environ 150 à 200 dollars, ce qui rend la production de fibre de carbone de vos propres mains et à la maison assez coûteuse, car l'achat équipement nécessaire et des matériaux, comme l'époxy et d'autres choses, vous devrez investir environ 15 000 roubles. Mais avec un tel équipement, vous pouvez vraiment produire des pièces de haute qualité qui peuvent rivaliser dans leurs performances avec celles vendues sur les marchés automobiles et dans les magasins. Avec un tel indicateur de qualité, vous pouvez sérieusement envisager de vendre vos propres pièces fabriquées via Internet ou sur les mêmes marchés spécialisés. L'essentiel n'est pas d'économiser de l'argent pour une pompe à vide et d'autres équipements.
Obtenir une forme, appliquer une pièce

Tout! La pièce est prête, vous pouvez la monter sur la voiture et profiter des résultats du réglage de vos propres mains !
En conclusion, je tiens à souligner que le principal avantage cette méthode est sa disponibilité à la maison et relativement faible coût composants initiaux, et le principal inconvénient, comme vous le devinez probablement, est la pénibilité du processus, et la plupart du temps n'est pas consacré à la production de la pièce, mais à la préparation de la forme. Mais si vous n'avez pas peur de ces problèmes, vous obtiendrez une pièce de réglage vraiment exclusive que personne d'autre n'aura !!!
Un de nos clients avait un tel projet : fabriquer une gamme de véhicules avec des caisses en fibre de carbone. Léger, durable, beau - des atouts solides. Seul le prix mord. Alors ils m'ont envoyé en reconnaissance : pour savoir comment faire la même chose, mais moins cher.
Pour être honnête, je n'avais jamais vu comment de telles choses étaient faites auparavant, et je n'imaginais même pas toute la technologie. Par conséquent, il a pris la tâche immédiatement et avec plaisir.
Mais il s'est avéré que se rendre à l'usine n'est pas si facile. Deux fabricants, sous divers prétextes, ont refusé de se rencontrer sur le site de production et ont constamment appelé à leur bureau. Le troisième bureau et la production se trouvaient dans le même bâtiment, et sans réfléchir à deux fois, je suis allé le voir.
L'usine a l'air plutôt décente, j'ai été emmené dans la salle d'exposition des négociations.
De la variété des échantillons, les yeux s'écarquillent: un vélo en carbone, des pièces pour le réglage de l'auto et de la moto, toutes sortes de gadgets à des fins incompréhensibles.
Capot monobloc pour BMW - le rêve des garçons du quartier.
Parfois, des fils de couleur sont tissés dans le tissu de carbone : rouge ou bleu, c'est très inhabituel.
Les détails, peints entièrement, immédiatement et ne peuvent être distingués de l'habituel. Habituellement, les athlètes font ceci : ils ont besoin faible poids, pas frimeur :)
Casque.
Et quelque chose, on ne sait pas pour quoi il faut.
Mais objectif principal ma visite était celle-ci :
Étui pour iPad. Je n'étais pas intéressé par le boîtier lui-même, bien sûr, mais par des choses similaires : pièces pour étuis de téléphone, ordinateurs portables, tablettes. Il était important de comprendre la technologie de production, de comprendre comment les concevoir correctement afin qu'elles soient aussi bon marché et technologiquement avancées que possible. Par conséquent, après de longues négociations et persuasion, j'ai quand même demandé une visite de la boutique.
La production occupe un étage du bâtiment, c'est propre, mais plutôt désert.
Le tissu de carbone avec la couche adhésive appliquée est livré en rouleaux. Il se décline en différentes épaisseurs, avec différents motifs de tissage. Stocké dans des réfrigérateurs spéciaux.
Le tissu est découpé en morceaux selon le motif et collé en plusieurs couches sur la matrice. Les matrices sont légères, faites d'un certain type de plastique et avec une ressource accrue, faites d'aluminium.
Des matrices allant travailler sont disposées à même le sol, chacune dans son secteur.
Le processus d'autocollant de carbone lui-même était situé derrière des portes en verre, mais ils ont catégoriquement refusé de me le montrer, disant que c'était un terrible secret commercial. Mais je ne pense pas qu'il y ait quoi que ce soit de secret là-dedans, il suffit de découper avec des ciseaux et de mettre les morceaux dans un moule.
Après cela, chaque pièce est emballée dans des sacs sous vide.
L'air est pompé hors des sacs et chargé dans l'un des deux fours, plus grand ou plus petit.
Les pièces finies sont retirées des matrices. Si la pièce a une forme complexe, sa matrice sera complexe et composée de plusieurs parties.
Contrôle qualité avant livraison à l'entrepôt.
Comme vous pouvez l'imaginer, ce n'est pas tout le processus. Maintenant, les pièces doivent couper les bords et les peindre avec du vernis. Mais cela se fait sur un autre site, par un sous-traitant. Ils ont proposé d'aller le voir, mais j'ai refusé - il n'y a certainement rien de nouveau là-bas.
Oh, vom même probablement intéressant de connaître les prix pro? Ainsi, un étui en carbone pour un iPad coûte 25 $ en usine. Un vélo - plusieurs milliers. Arrêtez de sourire, comme le dit un de mes amis. Et il n'y a pas d'options particulières pour réduire, une production trop petite, trop de travail manuel.
Mais tu souris toujours. Voici une dernière image de la vie chinoise ordinaire, que j'ai prise devant les portes de cette usine.