La composition du béton routier et les exigences de base pour la pose de la chaussée. Installation de sols en béton - l'ordre des travaux et leurs caractéristiques Installation de chaussées en béton armé
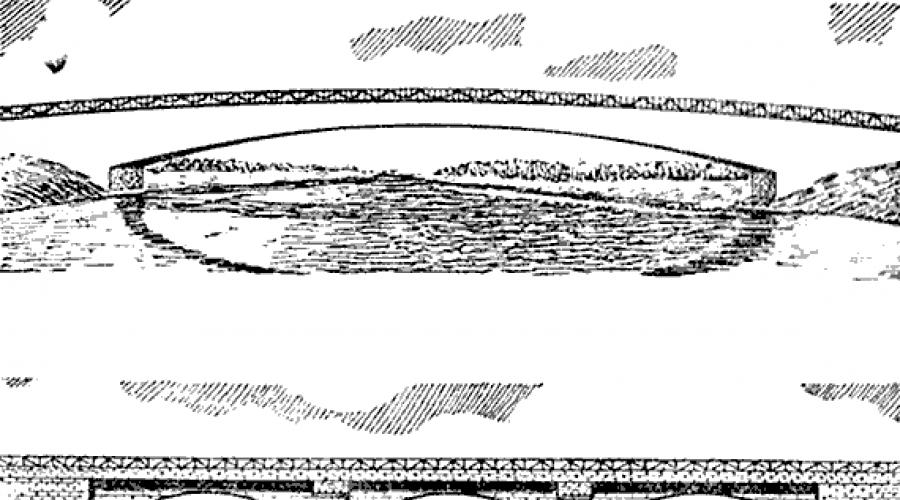
Lire aussi
Le béton est appelé matériaux artificiels résultant du collage (fixation) de matériaux en pierre naturelle - sable et gravier ou pierre concassée - en une pierre durable monolithique. Les bétons diffèrent par le liant, qui maintient ensemble les grains des matériaux en pierre naturelle. Le plus répandu est le béton de ciment, dans lequel les ciments sont un liant. Le béton bitumineux et le béton bitumineux sont largement utilisés dans la construction de routes ; le bitume et le goudron y servent de liant. Il existe d'autres types de béton : béton de gypse, béton de chaux, etc.
Notre brochure est dédiée à la description des propriétés du béton de ciment. Dans ce qui suit, nous l'appellerons simplement concret.
Le béton est un matériau de construction largement utilisé. Des constructions en sont souvent visibles sur les routes.
En apparence, une structure en béton, qu'il s'agisse d'une culée de pont, d'un ponceau ou d'un revêtement en béton d'une route, donne l'impression d'être faite de pierre grise. Au mot "pierre", nous associons généralement l'idée d'un matériau mort et immobile qui ne change pas ses propriétés pendant des décennies et des siècles.
L'idée du béton de ciment en tant que telle pierre n'est correcte qu'avec à l'extérieur. En fait, le béton est une pierre artificielle dans laquelle les processus de développement, de croissance, de vieillissement se poursuivent continuellement, une pierre qui grandit, se renforce, vieillit et meurt. En effet, la principale caractéristique du béton de ciment par rapport aux autres pierres est la formation de ses propriétés directement sur le chantier - dans la structure. Déjà cela donne à tous les travaux qui sont réalisés avec du béton, un caractère particulier. Le béton doit non seulement être préparé, mais également compacté, puis créer des conditions dans lesquelles il acquiert une résistance élevée.
La pâte de ciment dans la composition du béton, durcissant, fixe, colle des grains de sable individuels, du gravier individuel dans un monolithe à haute résistance, en fonction de la résistance de la pierre de ciment, de la résistance des matériaux en pierre et de la force d'adhérence de la cémentite et de la pierre avec des matériaux en pierre.
Un mélange de ciment, d'eau et de sable est appelé un mélange de mortier et, après durcissement, un mortier. Un mélange de ciment, d'eau, de sable et de pierre concassée ou de gravier en mouvement est appelé un mélange de béton. Le matériau semblable à de la pierre durcie, comme mentionné ci-dessus, est appelé béton.
La préparation du béton sur le chantier est effectuée par les constructeurs; par conséquent, ils ont la capacité d'influencer les propriétés du béton au cours de sa fabrication, ont la capacité de contrôler les propriétés du matériau résultant.
La propriété principale de tout matériau de construction est sa résistance.
Le béton a une résistance élevée, notamment en compression. Un cube en béton de 10 centimètres de côté peut supporter une charge de 20 à 40 tonnes, soit le poids d'un wagon de marchandises. Les bétons modernes ont une résistance encore plus grande, supportant une charge de 500 à 600 kilogrammes par centimètre carré de surface. La résistance à la traction du béton est bien moindre. Si un échantillon ou une structure en béton est étiré, la destruction se produira à des forces 10 à 15 fois inférieures à celles de la compression. C'est la différence entre les propriétés du béton de l'acier et d'autres métaux, qui ont approximativement la même résistance en traction et en compression.
De nombreuses structures de bâtiment sont soumises à des forces de flexion pendant le fonctionnement. Dans ce cas, dans la résistance du béton à l'action des forces destructrices, sa résistance à la traction est primordiale.
La découverte et l'utilisation généralisée dans la construction d'un nouveau matériau - le béton armé ont éliminé les défauts du béton en tant que matériau de structure. Le béton armé a gagné une place de choix dans la construction moderne. Dans ce document, les propriétés du béton - haute résistance à la compression, résistance à l'eau et à l'air, résistance au feu - sont combinées avec des propriétés de l'acier telles que la résistance à la traction, l'élasticité. À ouvrages en béton armé, où ces structures sont soumises à des forces de traction, des tiges d'acier sont installées, qui perçoivent l'action de ces forces. La quantité d'acier et son emplacement dans le béton sont déterminés par calcul. La figure 1 montre comment le béton et l'acier fonctionnent ensemble dans un nouveau matériau - le béton armé.
Fig. 1. Exemples de comparaison des propriétés du béton et du béton armé
Le béton armé est aujourd'hui très répandu ; des barrages et des ponts, des revêtements routiers d'autoroutes et des sites d'atterrissage pour aéronefs en sont construits, des tunnels, des tuyaux, des réservoirs sont en cours de construction, des structures de bâtiments résidentiels et industriels (colonnes, poutres, dalles de sol, escaliers, etc.) et même des rivières et les navires de mer. Le béton complètement sans acier, ou, comme on l'appelle, "barres d'armature", est maintenant rarement utilisé, mais les propriétés du béton de ciment déterminent en grande partie les propriétés du béton armé.
Dans la construction routière, l'utilisation du béton se développe rapidement, de sorte que chaque constructeur de routes doit être bien conscient des propriétés de ce matériau.
Le béton est très résistant aux influences naturelles telles que l'humidité et le séchage, le refroidissement et le chauffage, le gel et le dégel, l'abrasion et l'érosion. C'est un matériau indispensable pour des structures durables qui doivent exister pendant des dizaines et des centaines d'années.
Un avantage important du béton est la possibilité d'utiliser des matériaux locaux pour sa fabrication. Seul un dixième du béton (en poids) est un matériau artificiel - du ciment, les neuf dixièmes restants sont des matériaux en pierre naturelle et de l'eau, qui doivent seulement être extraits et livrés sur le chantier.
Le béton ne peut être comparé aux matériaux en bois, qui sont détruits par la décomposition, s'enflamment facilement et ne conviennent donc pas à la construction de structures durables. L'acier se décompose relativement rapidement lorsqu'il est exposé à l'air humide. Il ne peut pas être utilisé pour construire les murs des bâtiments, car il conduit facilement la chaleur ; compte tenu de cette propriété, les murs en acier devraient être 40 fois plus épais que le béton, l'acier étant trois fois plus lourd que le béton.
Le béton est un matériau indispensable pour la construction d'autoroutes, le long desquelles divers types de véhicules se déplacent rapidement. Les ponts, ponceaux, murs de soutènement et viaducs sont construits en béton armé. Les revêtements routiers sur les autoroutes et les bases pour les revêtements en béton bitumineux sont tous fabriqués en béton de ciment à grande échelle.
Par décision du parti et du gouvernement, la production en usine de béton armé préfabriqué est largement développée dans notre pays, dont l'utilisation conduit à l'industrialisation de la construction, ne permet que l'assemblage d'une structure à partir de pièces finies sur un chantier de construction.
Dans les revêtements routiers, le béton résiste à l'usure des véhicules passant sur la route, transfère et répartit la charge des roues de la voiture au sol. Dans les structures de pont, le béton résiste aux lourdes charges des voitures, des bus et des tramways passant sur le pont, et résiste également à l'action de décapage de l'eau sur les piles du pont ; de puissantes banquises sont brisées sur des taureaux en béton, que la rivière emporte dans la dérive des glaces. Maintenant, il est même difficile d'imaginer comment la construction serait réalisée si une personne n'avait pas de béton de ciment. De nombreuses structures construites aujourd'hui à partir de béton armé et de béton nécessiteraient beaucoup plus de travail et de dépenses lorsque l'on essaierait d'utiliser d'autres matériaux, et d'autres seraient totalement irréalisables.
Si l'on compare un pont en pierre avec un pont en béton armé moderne, on trouvera une énorme différence dans la quantité de matériaux, dans l'apparence des structures (Fig. 2). Il est clair pour tout le monde ce moins de matériaux va à la construction, moins la construction est chère, plus elle est rentable.
Fig.2. Pont en béton armé et pont en pierre naturelle
Les propriétés du béton et son application dans la construction routière sont décrites ci-dessous.
Préparation du mélange de béton
Afin d'obtenir un matériau aux propriétés bien définies - du béton à partir de substances hétérogènes telles que l'eau, le ciment, le sable et la pierre concassée ou le gravier, un certain nombre d'opérations doivent être effectuées. Dans le même temps, il est important de suivre les instructions des règles et instructions techniques. Bien que la production de béton ait souvent lieu directement sur le chantier, elle rappelle dans ce cas toute production en usine.
À partir de bons matériaux de ciment et de pierre, vous pouvez obtenir un béton solide et stable, mais vous pouvez également le gâcher si vous enfreignez les règles de préparation et de composition du béton. Tout d'abord, il est nécessaire de déterminer la composition du mélange de béton - le rapport de tous les matériaux pour celui-ci. La quantité de ciment et d'autres matériaux à prendre et dans quelle proportion est déterminée par le laboratoire qui existe sur chaque chantier de construction. Avant de choisir la composition du béton, les exigences relatives à ce béton doivent être connues. Dans le projet de construction, en fonction de la destination du béton, certaines exigences lui sont imposées en termes de résistance et d'autres propriétés techniques.
La résistance du béton est indiquée sous la forme d'une note. La durabilité du béton s'exprime dans la plupart des cas par l'exigence de sa résistance au gel. Pour les conditions climatiques de notre pays, un béton à très haute résistance au gel est nécessaire. Pour que le béton réponde à ces exigences, il faut utiliser du ciment Portland d'une certaine composition minéralogique et d'un grade d'au moins 500 ; les matériaux en pierre ne peuvent être utilisés que testés pour la résistance au gel, et le rapport eau-ciment du mélange ne doit pas dépasser 0,50. Si toutes ces exigences sont remplies, le béton aura une résistance élevée au gel. Il est également important lors de l'attribution de la composition du béton de prévoir que les propriétés du mélange de béton correspondent aux mécanismes disponibles pour son compactage et sa mise en place.
Cette correspondance est obtenue par une telle sélection de la composition du mélange, qui lui confère une certaine mobilité. Le taux de liquéfaction du mélange de béton lors des vibrations est également appelé maniabilité.
La mobilité du mélange de béton est déterminée de la manière suivante. Un coffrage métallique est rempli d'un mélange de béton - un cône sans fond et installé sur un support plat. Le cône est retiré et l'affaissement (inondation) du mélange de béton est mesuré après son retrait. La mobilité du mélange de béton est exprimée en centimètres du tirant d'eau du mélange par rapport à la hauteur d'origine.
Pour déterminer la maniabilité, le cône est placé sous la forme d'échantillons - des cubes d'une taille de côté de 20 centimètres. La forme avec un cône est fixée sur une plate-forme vibrante de laboratoire (Fig. 3). Le cône est rempli d'un mélange de béton, ainsi que lors de la détermination de la mobilité, le moule conique est retiré, la plate-forme vibrante est allumée et le temps d'étalement du mélange de béton dans le moule est déterminé. Une mesure de l'ouvrabilité est le temps en secondes nécessaire pour que le mélange s'étale dans le moule.
Fig.3. Détermination de l'ouvrabilité d'un mélange de béton :
à gauche - un moule avec un cône rempli de béton, avant de vibrer ;
à droite - une forme avec un mélange de béton après vibration
Pour le béton routier ordinaire, un mélange avec un affaissement de 2-3 cm et une maniabilité de 20-25 secondes est utilisé. Pour les structures à parois minces et densément renforcées, le tirage du cône de mélange de béton doit être de 5 à 6 centimètres avec une maniabilité de 5 à 10 secondes.
La principale exigence, qui est généralement suivie dans le choix de la composition du béton pour les chaussées et pour les structures renforcées, est le remplissage de tous les vides entre les particules d'un matériau plus gros. petites particules. De plus, il est nécessaire de créer une couche lubrifiante de pâte de ciment à la surface des particules de granulats pour obtenir un mélange mobile.
Fig.4. Schéma de sélection de la composition du béton
Ha Fig. 4 montre clairement le choix de la composition du béton. D'abord, on leur donne la quantité de ciment ou, à l'aide de tables auxiliaires, on calcule la quantité d'eau nécessaire pour un mélange donné. Déterminer ensuite le rapport eau-ciment - E/C. Ce rapport est très important pour caractériser la qualité et les propriétés de la pierre de ciment et du béton. Il est clair que plus le ciment-colle est dilué, plus sa résistance est faible. Dans la pratique de la sélection de la composition du béton d'une résistance donnée, des graphiques de la dépendance de la résistance du béton sur W / C sont utilisés, construits sur la base de données expérimentales. La figure 5 montre un exemple d'un tel graphique pour du béton sur des ciments de différentes qualités et de la pierre concassée. À grand volume travaux, il est recommandé de sélectionner la composition du béton à l'avance, en laboratoire, en déterminant la dépendance de la résistance du béton au rapport eau-ciment dans l'expérience pour ces matériaux. Après avoir déterminé la consommation de ciment et d'eau, la quantité de matériaux minéraux - sable et pierre concassée - est calculée de manière à ce que leur volume total avec le volume de pâte de ciment soit de 1000 litres (1 mètre cube). Après calculs préliminaires s'assurer de réaliser un essai de gâchage du mélange de béton avec vérification de sa maniabilité et avec fabrication d'échantillons témoins. Si, lors de la vérification, la maniabilité du mélange de béton s'avère différente de celle spécifiée, la composition du béton est corrigée en modifiant la teneur en ciment et en eau, en laissant le rapport eau-ciment inchangé.
Fig.5. Graphique de la dépendance de la qualité du béton au rapport eau-ciment pour les ciments de différentes qualités (les chiffres au-dessus des courbes indiquent la qualité du ciment).
Lorsque la composition du béton est définie, il est transféré à la centrale à béton. Pour un pesage précis des composants dans les centrales à béton modernes, des doseurs de pesage automatiques sont utilisés, qui sont installés pour peser une portion donnée de tout matériau en vrac ou d'eau. Dans les petites centrales à béton, des doseurs plus simples sont utilisés, tels que des trémies ou des boîtes montées sur des échelles centésimales conventionnelles.
Une mesure précise des éléments constitutifs du béton est nécessaire pour que ses propriétés correspondent à celles spécifiées et pour garantir l'homogénéité nécessaire du mélange. De plus, l'imprécision du dosage entraîne une surutilisation du ciment - le composant le plus cher du béton. Par conséquent, moderne règles techniques nécessitent l'utilisation obligatoire d'un dosage non négatif de tous les matériaux.
La prochaine opération consiste à mélanger le mélange de béton. Le mélange est effectué dans des machines spéciales - bétonnières. Notre industrie pour différentes conditions de travail produit des bétonnières mobiles et fixes de différentes capacités avec un volume de tambour de malaxage de 100 à 4500 litres. Pour la préparation de mélanges rigides, des bétonnières à mélange forcé sont produites. Les bétonnières conventionnelles mélangent le mélange de béton en le déplaçant avec des lames pendant que le tambour tourne. La figure 6 montre deux types de bétonnières les plus courantes. Après mélange, le mélange est déchargé en inclinant le tambour dans sa forme en forme de poire ou à travers un plateau qui est poussé à l'intérieur du tambour.
Fig.6. bétonnières divers modèles
Les bétonnières conventionnelles fonctionnent selon un tel cycle périodique. Mais il existe également des bétonnières continues, qui ont une productivité nettement plus élevée avec des dimensions plus petites.
performances de la bétonnière action périodique varie en fonction de leur capacité. D'une capacité moyenne, il contient 1200 litres de matériaux secs lorsqu'il est chargé et délivre environ 800 litres de béton prêt à l'emploi. Sa production horaire est d'environ 15 mètres cubes de mélange. La bétonnière continue est plus économique et est conçue pour une capacité de 100 à 200 mètres cubes par heure.
Dans la construction de routes, les bétonnières mobiles sont largement utilisées, car lorsque les matériaux sont reçus par transport ferroviaire ou maritime et à de grandes distances des bases au lieu de pose, le transport du mélange de béton devient difficile et devient techniquement inacceptable. Pendant le transport à long terme du mélange, sa mobilité change et la qualité se détériore ; par conséquent, les ouvriers routiers ont tendance à transporter des matériaux secs et à les mélanger sur place dans une bétonnière mobile.
La dernière réalisation technologique dans le domaine de la préparation du béton est constituée d'installations automatisées modernes pour les grands projets de construction. 24 heures sur 24 dans une telle usine, les volets des distributeurs fonctionnent, la pierre concassée et le sable se déversent avec un rugissement dans les bunkers, l'eau coule. Le béton prêt à l'emploi est déversé dans les caisses de puissants camions à benne basculante, qui l'amènent aux installations, le déchargent et retournent à nouveau à l'usine.
Les travaux d'amélioration des méthodes de préparation et de pose du mélange de béton se poursuivent.
Afin de poser étroitement le mélange de béton avec la plus faible teneur en eau, et donc avec la plus faible consommation de ciment, la vibration du mélange de béton est actuellement largement utilisée. Quelle est son action. Tout le monde sait que secouer un matériau granulaire, comme du sable sec, permet de placer beaucoup plus de matériau dans la même boîte que sans secouer : le matériau s'adapte plus densément. Si vous secouez le mélange de béton avec une grande fréquence, le mortier de ciment se liquéfie et le mélange acquiert les propriétés d'un liquide. Dans cet état, le mélange de béton remplit de manière dense le volume portant du coffrage, sans laisser de vides - des coquilles.
Pour transmettre des vibrations au smog de béton, des mécanismes spéciaux sont utilisés - des vibrateurs.
Le vibrateur effectue plusieurs milliers de vibrations par minute, et ces vibrations sont transmises au mélange de béton environnant. Le mélange, acquérant les propriétés d'un liquide lourd, se répand sur le coffrage, le remplissant et enveloppant l'armature. Twitter et le gravier se noient en même temps dans le mortier de ciment et sont uniformément répartis dans la masse de béton.
Grâce à la vibration, il est possible de déposer des mélanges beaucoup moins mobiles que manuellement. En réduisant la quantité d'eau pour de tels mélanges, nous améliorons les propriétés techniques du béton. Par conséquent, le béton vibré est de meilleure qualité que le béton placé à la main.
Notre industrie produit différents types de vibrateurs conçus pour couler du béton dans des structures massives et à parois minces, non renforcées et renforcées. La figure 7 montre l'apparence des vibrateurs internes et de surface pour compacter le mélange de béton.
Fig.7. Apparition des vibrateurs :
a - vibrateur interne ;
b - vibreur de surface
Le vibrateur interne est immergé dans la masse de béton pendant le fonctionnement. Pour une structure de faible épaisseur et avec une grande surface horizontale, telle que des surfaces de route, des dalles de pont et de sol, etc., on utilise des vibrateurs dits de surface (illustrés à la Fig. 7, b), fixés à une plate-forme qui est placée sur le béton superficiel. Les vibrations du site sont transmises au mélange de béton. Ils sont les plus largement utilisés dans la construction de routes. Pour compacter le béton dans les produits, le coffrage avec le produit est installé sur une table vibrante spéciale. Lorsque le vibreur est activé, tout le coffrage est soumis à des vibrations avec le mélange de béton ; en conséquence, un degré élevé de compactage est atteint. Il est possible de transmettre les vibrations du mélange de béton en fixant le vibreur sur le coffrage ; ces vibrateurs sont appelés vibrateurs externes ou étaux, car ils sont fixés au coffrage avec un étau.
La technique de compactage du béton, notamment dans la fabrication des produits préfabriqués en béton, s'améliore rapidement : la puissance et la fréquence des vibrations des vibrateurs augmentent, des vibrations simultanées sont introduites sur la table vibrante et un vibreur de surface, des vibrations avec chargement du mélange de béton sur l'ensemble domaine du produit. On peut supposer que dans les années à venir, la technologie de mise en place et de compactage du béton fera un pas en avant significatif sur la voie de nouveaux progrès techniques.
Dans la construction de routes, on utilise des machines de finition de béton complexes et complexes qui nivellent le mélange, le compactent par vibration et tassement, profilent la surface et la tassent. L'unité moderne pour le dispositif de chaussée en béton de ciment (Fig. 8) n'est pas inférieure à la complexité des opérations effectuées et à l'efficacité du travail aux céréales et au charbon.
Fig.8. Pavé
L'ensemble du cycle de pavage est réalisé par plusieurs machines. Des coffrages de rail sont installés sur la base profilée et compactée ; ils délimitent la bande du futur pavage de la chaussée, sont le coffrage de la dalle de pavage et servent en même temps de rails pour la circulation des machines à paver le béton. Une chaîne de camions à benne livre le mélange de béton de l'usine et le déverse dans le godet du distributeur. Depuis le godet, le mélange est rechargé dans la trémie de distribution et placé en vrac sur la base entre les coffrages avec une couche d'une certaine épaisseur. À la suite du répartiteur, une machine de finition du béton se déplace, compactant, nivelant et profilant le revêtement ; derrière elle déplacer des dispositifs pour couper les joints de dilatation. En une journée, un tel agrégat peut parcourir 300 mètres, laissant derrière lui une surface de route finie. Après la pose du béton, sa surface est recouverte d'une couche de sable ou d'un film d'une sorte de vernis ou de bitume, le protégeant ainsi du dessèchement. Dans le cas où l'abri est fait de sable, il est régulièrement arrosé. Après 20 jours, il est permis d'ouvrir la circulation sur la route si le temps était chaud avec une température de l'air d'au moins 15°.
Pour voie du milieu En Russie, la durée de la saison de construction est d'environ 200 jours. Pendant ce temps, un ensemble de machines pourra préparer 60 kilomètres d'une route de première classe. Et quelle énorme quantité de matériaux de construction doit être transportée pour cela ! Rien que pour la construction de la chaussée, plus de 3 500 tonnes de matériaux par kilomètre de route seront nécessaires, et plus de 200 000 tonnes pour toute la longueur de la route. Pour transporter toute cette masse de sable, de gravier, de mélange de béton, etc., environ 40 000 voyages de puissants camions à benne basculante seront nécessaires.
Maturation du béton
A partir du moment où le mélange de béton est réalisé jusqu'à son durcissement complet, une certaine période de maturation s'écoule, l'acquisition de la résistance, qui dure, selon le type de ciment et les conditions extérieures (température et humidité), de plusieurs jours à plusieurs mois et même des années. Pendant ce temps, le béton issu de la mobilité de la masse plastique se transforme en une pierre artificielle durable.
Cette transformation se fait progressivement. La première période de maturation du béton s'appelle la période de prise. Cela dure généralement plusieurs heures. A ce moment, la pâte de ciment perd sa mobilité. L'eau pénètre partiellement dans les composés chimiques et est partiellement répartie sur la surface des composés nouvellement formés, le mélange de béton perd sa mobilité et acquiert une résistance minimale.
La période de prise ne peut pas être nettement séparée de la période suivante - la période de durcissement. Cependant, quelques heures après la mise en place, il arrive un moment où le mélange de béton devient immobile et ne peut plus être vibré sans se casser. Ce moment peut être considéré comme la fin de la période de réglage.
Pour que les processus de combinaison chimique de l'eau avec les minéraux du ciment se déroulent de manière suffisamment efficace, il est nécessaire de maintenir le béton humide. Le durcissement s'arrête non seulement à basse température, mais également avec une humidité insuffisante. À cet égard, le béton est comme une plante : il doit être arrosé et maintenu au chaud pour qu'il se renforce. À température normale, le béton sur ciment Portland acquiert sa résistance principale dans les 20 à 30 jours suivant le durcissement. Un effet bénéfique sur la vitesse de durcissement est une augmentation de la température, qui est connue pour accélérer les réactions chimiques. Pour les calculs, la résistance atteinte par le béton au temps de durcissement de 28 jours est généralement prise en compte. L'augmentation de la température vous permet d'obtenir la même résistance en un temps beaucoup plus court.
Sur la base de l'étude du processus de durcissement, les conditions d'obtention d'un bon béton ont été élaborées : une quantité modérée d'eau lors du malaxage, des conditions de durcissement humides et chaudes. La qualité des ouvrages dépend du respect de ces conditions.
Travaux de béton en hiver
Des conditions climatiques relativement sévères sur presque tout le territoire de la Russie sont défavorables au durcissement du béton; par conséquent, les constructeurs doivent souvent créer artificiellement un environnement humide et chaud pour le béton posé. Les scientifiques et ingénieurs soviétiques ont développé des méthodes très efficaces pour couler le béton dans des conditions hivernales, permettant d'effectuer des travaux toute l'année.
En hiver, il est nécessaire de chauffer les matériaux pour le béton et de les protéger du refroidissement, voire de chauffer le béton posé dans la structure jusqu'à ce qu'il acquière la résistance souhaitée. Mais ces dernières années, une méthode a été développée qui permet de travailler à des températures négatives et sans chauffer les matériaux et le béton.
La méthode la plus simple pour créer des conditions favorables au durcissement du béton en hiver est la méthode "thermos a", développée il y a plus de 40 ans par le prof. I.A. Kireenko. Avec cette méthode, la structure est bien isolée de l'environnement de sorte qu'elle longue durée resté au chaud. Le principe de cette méthode est le même que celui d'un thermos classique. La chaleur dégagée lors du durcissement du ciment, en l'absence de pertes, chauffe la structure de l'intérieur. De cette manière, le béton peut être posé dans des structures massives dont la surface est petite par rapport au volume.
Pour les structures moins massives, un chauffage artificiel est utilisé : la structure est habillée d'une serre en bois (c'est la technique la moins rentable) ou chauffée à la vapeur, en installant un coffrage spécial autour du coffrage, sous lequel passe la vapeur, ou, enfin, le la structure est chauffée au courant électrique.
Une méthode basée sur l'introduction d'additifs salins dans le mélange de béton, qui abaisse le point de congélation du mélange de béton et accélère le durcissement du béton, est largement utilisée dans la production d'ouvrages en béton en hiver. Ces sels comprennent les sels de chlorure : chlorure de calcium et chlorure de sodium. Avec de petites additions de sels, il est possible de construire toutes les structures critiques dans des conditions de gel et de gel léger sans prendre de mesures spéciales pour chauffer le béton. Pour les ouvrages moins importants et temporaires, il est possible d'utiliser de gros ajouts de sels, qui permettent de réaliser des travaux de la même manière qu'en été, à des températures pouvant descendre jusqu'à -20°.
La figure 9 montre différentes manières de chauffer le béton des structures lors des travaux d'hiver. L'étuvage du béton est également utilisé l'été dans les bases pour la production de pièces préfabriquées en béton armé afin d'accélérer le durcissement du béton et d'augmenter le roulement des coffrages.
Fig.9. Façons de réchauffer le béton en hiver:
a - la méthode du "thermos" ; b - chauffage à la vapeur; c - chauffage électrique
Les méthodes de production d'ouvrages en béton en hiver, les méthodes accélérées de maturation du béton par chauffage et cuisson à la vapeur, ont trouvé la plus large diffusion dans la technologie de construction soviétique.
La production de travaux toute l'année, la fabrication de produits préfabriqués dans les usines deviennent les principales méthodes qui caractérisent la technique domestique du travail du béton, y compris la construction de routes.
Durabilité des structures en béton
Dans la construction de structures géantes, le béton de ciment joue un rôle important, en tant que l'un des matériaux de construction les plus durables de notre époque.
À première vue, les structures en béton mortes et immobiles vivent dans des conditions complexes et stressantes, subissant des changements destructeurs. Comprendre la vie du béton, ses propriétés et ses maladies, apprendre à gérer sa vie à volonté - telle est la tâche de celui qui a créé le béton.
En effet, pourquoi les structures individuelles construites en béton sont-elles détruites ?
Le béton, bien que très résistant, se « décrépit » avec le temps, se couvre de fissures, s'effrite et meurt. Le fait est que le béton durerait presque éternellement s'il n'était pas exposé aux influences environnementales. L'eau a le plus fort effet destructeur sur les structures en béton.
Il y a un ancien dicton latin "une goutte use une pierre". Ce proverbe est vrai non seulement au sens figuré, mais aussi littéralement. Il n'est pas rare de voir des dépressions sur un ancien dallage de pierre, formées dans la pierre aux endroits où des gouttes d'eau tombent constamment du toit. Ils sont apparus car il y a une lente dissolution de la pierre dans l'eau. Les particules d'eau qui tombent arrachent les molécules de la substance qui compose la pierre de sa surface, les entourent et les emportent. Sur une longue période, même le sable de rivière quartzeux se dissout progressivement dans de grandes quantités d'eau.
À conditions naturelles sur de longues périodes de temps, mesurées en dizaines et centaines de milliers d'années, les processus de dissolution de certaines roches et la formation de nouvelles se produisent continuellement.
La dissolution des matériaux en pierre naturelle et artificielle peut augmenter considérablement si l'eau contient du dioxyde de carbone et d'autres substances. Le dioxyde de carbone se trouve dans l'air en très faible quantité (0,03%) et est donc présent dans toute l'eau qui entre en contact avec l'air.
Un matériau de pierre naturelle aussi répandu que le calcaire se dissout encore plus dans l'eau que le quartz. Il faut environ 3 000 litres d'eau pour dissoudre 1 gramme de calcaire. La présence de dioxyde de carbone dans l'eau augmente considérablement la solubilité du calcaire. Dans les dépôts naturels de calcaire, à la suite de sa dissolution avec de l'eau, d'immenses grottes souterraines se forment.
Nous parlons en détail de la stabilité des roches, car le béton est essentiellement une roche artificielle et les processus de sa destruction sont similaires à la destruction des roches naturelles.
Le béton durci contient de la chaux, une substance très soluble dans l'eau. Oui, et d'autres substances qui composent la pierre de ciment peuvent se dissoudre progressivement dans l'eau.
Académicien A.A. Baikov, qui a étudié la durabilité du béton, a souligné que toutes les structures en béton en ciment Portland doivent inévitablement subir le processus de lessivage à la chaux et, après un certain temps, perdre toute cohérence et s'effondrer.
Dans les structures routières, le plus grand danger de dissolution concerne les supports de pont. Dans la chaussée, la couche de surface est exposée à l'action dissolvante de l'eau.
En plus de l'action dissolvante, l'eau est particulièrement dangereuse dans les cas où l'armement en béton est soumis à une alternance de mouillage dans l'eau et de congélation ultérieure. La répétition répétée de tels cycles conduit à la destruction rapide du béton.
Lorsque le béton saturé d'eau gèle, la destruction se produit en raison de l'anomalie de l'eau connue de la physique. Contrairement à la plupart des substances, l'eau, comme vous le savez, lorsqu'elle est congelée, c'est-à-dire lors du passage d'un état liquide à un état solide, il se dilate et de manière assez significative - d'environ 10%. Tout le monde sait qu'il est impossible de laisser au froid une bouteille remplie d'eau et une bouteille bouchée : l'eau gèle et la bouteille peut éclater, car la congélation de l'iode peut développer une pression de plus de 800 atmosphères (fig. 10). Même les conduites d'eau en acier posées dans le sol peuvent éclater lors de fortes gelées en raison du gel de l'eau qu'elles contiennent. L'augmentation du volume d'eau lors de la congélation était utilisée auparavant dans les carrières pour fendre la pierre extraite.
Fig.10. a - eau congelée dans un récipient ouvert (seau): la glace forme un "bouchon" sur les parois du récipient, occupant un plus grand volume;
b - lorsque l'eau est gelée dans un récipient hermétiquement fermé, la pression sur ses parois atteint 800 atmosphères
Les mêmes phénomènes se produisent dans le béton durci lorsqu'il est soumis au gel. L'eau contenue dans les pores du béton y gèle et, en se dilatant, provoque des contraintes pouvant détruire la structure en béton. La plus ou moins grande résistance du béton à l'action destructrice de l'eau et du gel dépend principalement de la structure de la pierre de ciment. La tâche d'un constructeur de routes érigeant des structures en béton est de créer toutes les conditions pour obtenir un béton durable et résistant au gel. Pour ce faire, le béton doit être le plus dense possible, ce qui signifie qu'il doit être préparé avec un minimum d'eau, bien tassé et durci dans des conditions favorables au durcissement.
Dans les parties sous-marines et souterraines des structures, il n'y a aucun danger de destruction du béton par le gel; ici, l'effet dissolvant de l'eau est possible, qui peut être renforcé par l'action chimique des sels dissous dans eaux naturelles Oh.
Les eaux naturelles (souterraines et fluviales) peuvent avoir une composition très différente selon la composition des roches avec lesquelles elles entrent en contact sur leur chemin.
Pour le béton, la teneur en sels de sulfate (sulfates) dans l'eau est particulièrement nocive. Le sulfate de calcium, le sulfate de magnésium, le sulfate de sodium sont dangereux car, pénétrant dans la solution aqueuse à l'intérieur du béton, ils entrent en interaction chimique avec parties constitutives pierre de ciment durcie, formant de nouveaux composés. Lorsque des réactions chimiques commencent dans la pierre de ciment durcie avec la formation de nouvelles substances, alors, naturellement, l'adhérence des particules de la pierre de ciment est rompue et sa résistance, et par conséquent, la résistance du béton diminue. De plus, les sulfates forment avec les constituants de la pierre de ciment - la chaux et les aluminates de calcium - un nouveau composé - le sulfoaluminate de calcium, qui occupe un volume 2,5 fois plus grand que les matériaux d'origine.
La cristallisation du sulfoaluminate de calcium entraîne un gonflement et une fissuration de la pierre de ciment et, par conséquent, des structures en béton de ciment.
Différentes sortes Les effets chimiques agressifs des eaux naturelles sur le béton peuvent être réduits à trois types principaux, illustrés à la Fig. 11.
Fig.11. Les principaux types de destruction du béton par les eaux agressives
Lors de la conception et de la construction de structures durables, les ingénieurs tiennent compte des conditions dans lesquelles ces structures seront situées et calculent leur durée de vie pendant une période prédéterminée.
Chaussées en béton
Le béton de ciment solide, durable et résistant à l'usure s'est révélé dès le meilleur côté comme matériau pour les fondations et les revêtements routiers. Les calculs confirment que l'utilisation du béton de ciment apporte de grandes économies à l'économie nationale.
En 1913, la première route en béton a été construite à Tiflis.
En plus des avantages économiques directs lors de la construction, la chaussée en béton offre des avantages techniques et économiques importants dans l'exploitation de la route. La grande durabilité du béton vous permet de réduire au minimum les coûts d'entretien et de réparation. La durée de vie d'une chaussée en béton est plusieurs fois supérieure à celle d'une chaussée en béton bitumineux. Une route bien construite avec une chaussée en béton de ciment (Fig. 20) peut servir pendant plusieurs décennies sans réparations majeures. La chaussée en béton de ciment est une dalle de 18 à 24 cm d'épaisseur.
Fig.12. Route avec chaussée en béton de ciment
Si la route est recouverte d'une bande continue de béton, puis avec les changements de température (jour et nuit, été et hiver), la dalle de béton changera de taille - se dilatera et se contractera, et des contraintes y apparaîtront, ce qui peut conduire à du béton fissuration. Tout le monde sait que lors de la construction de voies ferrées, les rails ne sont jamais étroitement liés pour éviter le gauchissement lors de la dilatation thermique, mais laissent un espace de plusieurs millimètres au niveau des joints. En été, cet espace est fermé et en hiver, les extrémités des rails divergent.
Sur une route en béton, les coutures sont également faites à une certaine distance - des lacunes. Pour que la dalle de béton ne s'effondre pas lorsqu'elle est chauffée, des joints de dilatation sont disposés - à travers les espaces entre les dalles de chaussée en béton adjacentes. Les coutures sont remplies de mastic de bitume élastique afin que l'eau ne pénètre pas dans la base sous la dalle. Les joints de dilatation dans un climat tempéré sont disposés après 20-30 mètres. Cette distance dépend de la température du mélange de béton au moment de la pose, ainsi que du climat de la zone.
Si un joint de dilatation n'est pas fourni, le revêtement, chauffé dans une fille chaude et ensoleillée, sera tellement sollicité que des morceaux entiers de béton peuvent se détacher de sa surface. Avec la force qui s'éloigne du revêtement, ils peuvent provoquer des accidents. De tels phénomènes ont été observés sur l'une des routes de Californie (États-Unis), où les coutures nécessaires n'étaient pas réalisées.
Lorsque le revêtement est refroidi à une température inférieure à la température du mélange de béton et au moment de la pose, le béton se rétracte et la dalle de béton peut se fissurer. Afin d'éviter l'apparition de telles fissures, le revêtement est séparé par des coutures à des distances inférieures à celles auxquelles apparaissent des contraintes dangereuses. Ces coutures sont généralement disposées à distance (5-10 mètres) et sont des coupes dont la profondeur est égale à un tiers de l'épaisseur de la dalle.Ces coutures sont appelées coutures de compression.La couture de compression est remplie de mastic, comme ainsi que le joint de dilatation.
Une couture de type coutures de compression est également disposée le long de l'axe de la route, sinon une fissure longitudinale peut se former.
Ainsi, la chaussée en béton de ciment est constituée, pour ainsi dire, de dalles séparées. Afin d'éviter de briser la solidité de l'ensemble du revêtement, ainsi que de transférer la charge des machines en mouvement d'une plaque à l'autre, des tiges métalliques spéciales sont installées dans les coutures.
La durée de vie du revêtement dépend de la qualité des performances de tous les travaux sur le dispositif de revêtement.
La construction de routes à chaussée en béton ne cesse d'augmenter, elles deviennent le principal type de routes principales.
Le béton est le plus couramment utilisé pour les revêtements de sol. Le matériau offre une résistance structurelle élevée, une résistance aux conditions de fonctionnement agressives. Les technologies de construction de sols sont bien étudiées, n'entraînent pas de coûts excessifs et se caractérisent par un large éventail d'applications.
Les couches sous-jacentes en béton sont disposées là où, pendant le fonctionnement, l'action d'huiles, de solutions, de solvants et de divers liquides agressifs est possible. Dans tous les autres cas, vous pouvez vous débrouiller avec l'installation de dalles de sable-gravier non rigides, de laitier, de béton bitumineux, de dalles de béton argileux.
L'épaisseur de la préparation dépend des charges de conception. Les caractéristiques des sols et des matériaux utilisés sont toujours pris en compte. Cependant, la réglementation en vigueur détermine l'épaisseur minimale des couches sous-jacentes. S'ils sont posés dans des locaux résidentiels et publics - c'est 80 mm, s'ils sont en production - 100 mm.
Sur les sols avec une pente, un ruissellement organisé, les joints coïncident avec le bassin versant, dans d'autres cas - avec les joints de dilatation du bâtiment
Le béton doit fournir la capacité portante de la préparation. En tant que matériau principal, un mélange de classe B22.5 est utilisé. Un béton moins durable (mais pas inférieur à B7.5) peut être pris à de faibles charges opérationnelles, en particulier à faible tension dans la couche sous-jacente.
Si les conditions de fonctionnement sont telles que le sol accepte des changements brusques de température, la coupe est toujours effectuée joints de dilatation. Ils sont placés avec un pas de 8-12 m dans des directions mutuellement perpendiculaires.
Préparation du sol
Avant de couler la préparation du béton, il est nécessaire de préparer une base de sol.
Le principe de travail est le suivant :
- si nécessaire, une excavation du sol végétal est effectuée;
- si révélé occurrence élevée aquifère, mener des activités pour abaisser le niveau des eaux souterraines ;
- les sols poussiéreux, argileux et limoneux doivent être asséchés. L'opération dure jusqu'à ce que la capacité portante soit restaurée ;
- si le sol est disposé dans des pièces non chauffées + une protection contre la déformation est mise en place sur des bases de soulèvement ;
- les sols poreux sont enlevés et remplacés par un sol à faible tirant d'eau, ou ils sont fixés;
- si la base a une structure brisée ou si elle est en vrac, elle doit être nettoyée des débris, des impuretés et compactée. Des pilonneuses mécaniques ou manuelles sont utilisées pour le travail. Le travail manuel n'est justifié que si l'équipement peut provoquer le déplacement des structures et des fondations adjacentes. Selon la technologie, les sols sont coulés en couches (10 cm chacune), en enfonçant chaque couche.
La surface du sol de fondation doit être conforme à toutes les élévations de conception prévues. Basé sur le niveau inférieur de la surface, le sol est nivelé, coulé, compacté. Si des mélanges de sols sont utilisés pour la construction de fondations, ils sont posés en couches de 50 à 75 mm avec un compactage couche par couche.
Remblayage des couches sous-jacentes
Lors du travail au sol, les couches sous-jacentes sont posées sous la préparation du béton.
Les travaux se déroulent comme suit :
- une couche de sable de construction est coulée sur la base (préparée et nivelée). Il est réparti sur toute la zone de travail en une couche continue et uniforme. L'épaisseur d'une couche doit être de 5 à 10 mm. Le compactage est effectué, pour lequel le sable est pré-humidifié;
- puis une couche de pierre concassée est disposée. Il est sélectionné par taille, composition, empilé et hydraté. En conséquence, une couche continue uniforme doit être formée, de 80 à 200 mm d'épaisseur. La pierre concassée est nivelée et enfoncée mécaniquement ou outil à main. Si du gravier est utilisé, il est posé de la même manière;
- sur des sols secs, il est permis de travailler avec des mélanges d'adobe. Le matériau est posé en couche jusqu'à 100 mm, compacté jusqu'à ce que l'humidité atteigne la surface.
Si une préparation multicouche est mise en œuvre, chaque couche suivante est posée après un traitement minutieux de la précédente.
Pour améliorer l'adhérence dans les couches sous-jacentes, une hydratation est appliquée entre elles.
Coulage de la préparation du béton
Le matériel peut être transporté sur le lieu de travail par des pompes à béton, des chariots, des camions à benne basculante. Si la structure ne nécessite pas de renforcement, le béton est posé directement à partir de chariots ou de camions à benne basculante au centre de la zone de coulée. Si une couche de renforcement est prévue, le béton est déchargé en basculant sur le côté.. Si nécessaire, le placement du treillis d'armature est réglable, mais l'armature ne doit pas être déplacée lors du coulage. Pour les gros volumes de travaux, il est conseillé d'utiliser une pompe à béton qui assure une répartition uniforme de la solution.
Le principe de fonctionnement est le suivant :
- des balises à contrôle horizontal strict sont placées sur la base. Les planches peuvent être utilisées comme matériau principal, dont la largeur correspond à l'épaisseur de la préparation du béton, de 4 à 6 cm d'épaisseur.Sur la base, les balises sont fixées avec des chevilles en bois martelées à une profondeur de 30 cm, par incréments de 1,5 m Au lieu de planches, il est permis de prendre un canal métallique;
- si une pente doit être organisée sur la surface du sol, elle est prévue au stade de la préparation en coupant le bord supérieur des balises au niveau requis ;
- avec une grande quantité de travail pour le dispositif de préparation du béton, la construction d'un coffrage pliable est nécessaire, avec une fixation fiable de tous les éléments;
- le béton est ramené à la surface. Le bétonnage est réalisé en bandes à travers une;
- tout d'abord, les bandes éloignées de l'entrée sont coulées, s'en rapprochant successivement;
- lorsque le béton a pris, procéder au traitement des bandes adjacentes non remplies. Les faces latérales des dalles finies sont prétraitées au bitume chaud. Couche d'application - 1,5-2 mm. Ces faces formeront des joints de dilatation ;
- procéder à la formation de coutures de retrait. Pour ce faire, un profilé métallique est approfondi dans une préparation fraîchement coulée, de 4 à 5 mm d'épaisseur et de 80 à 100 mm de largeur. Le profil doit être approfondi de 1/3 de l'épaisseur de la préparation. Le matériau est laissé pendant 20 à 40 minutes et retiré. Lorsque le béton a mûri, les joints de retrait sont coulés avec du mortier de ciment ou du mastic bitumineux chaud.
Une fois les travaux terminés, la surface est traitée à la truelle.
Étanchéité
La couche d'imperméabilisation est conçue pour la préparation du béton avec une intensité moyenne et élevée d'exposition à l'eau et à d'autres liquides sur le sol (+ alcalis, solutions, acides). Il peut s'agir de sols de locaux non chauffés, d'ouvrages construits sur des sols affaissés, de sols sur dalles de sol, de zones présentant un risque d'aspiration capillaire des eaux souterraines. Outre, une protection est nécessaire si la préparation du béton est placée sous le niveau de la zone aveugle.
Le choix du matériau est soumis aux principes suivants :
- s'il est nécessaire de fournir une protection contre l'action de l'eau, des liquides chimiquement agressifs, des matériaux tels qu'un film de polyéthylène, un film de chlorure de polyvinyle, un hydroisol peuvent être utilisés;
- dans le contexte de l'intensité moyenne de l'action des eaux usées, cela fonctionne avec succès coller l'imperméabilisation. Il est permis de travailler avec des matériaux bitumineux en les appliquant en 2 couches. ;
- dans le contexte de la forte intensité de l'action des liquides sur le sol, il est possible de réaliser une imperméabilisation en collage, mais avec un doublement du nombre de couches;
- lors de la préparation du béton, il est permis de réaliser une imperméabilisation à base de pierre concassée et d'autres matériaux en vrac, suivie d'une imprégnation au bitume chaud.
L'étanchéité par collage polymère est placée en 1 couche
Dans ce dernier cas, la protection est disposée après remplissage du coussin de pierre concassée. La couche est imprégnée avec un distributeur d'asphalte ou manuellement. Le bitume chaud est appliqué uniformément sur la base, avec une couche de 5 à 6 mm d'épaisseur. Si l'imprégnation bitumineuse est disposée en plusieurs couches, du sable (fractions jusqu'à 5 mm) ou des éclats de pierre sont autorisés à travers la première. Le compactage est effectué avec un rouleau, après quoi une deuxième couche jusqu'à 0,25 mm d'épaisseur est mise en œuvre, en utilisant de la poudre de sable.
Quels que soient les matériaux utilisés, la couche d'étanchéité doit être continue, étanche, en saillie au-dessus du sol sur une hauteur d'au moins 300 mm par rapport au niveau du revêtement.
Principes du dispositif d'étanchéité de revêtement:
- le fond doit être plat, sans poussière. Un primaire à base de mastics bitumineux ou de solutions à base de polymères est appliqué. La composition peut être distribuée manuellement avec des pinceaux ou au moyen de pulvérisateurs ;
- en conséquence, une épaisseur uniforme, la même couche d'apprêt doit être formée, dans laquelle il n'y a pas d'espace. L'épaisseur optimale est de 0,5 à 2 mm;
- les couches suivantes ne doivent être appliquées qu'après le séchage complet des précédentes, ce qui peut être déterminé par la cessation de la pégosité;
- lorsque vous travaillez avec des joints, ils sont recouverts de mastic et des bandes de matériau laminé de 10 à 20 cm de large sont collées, après quoi une autre couche de mastic est appliquée.
Principes de travail avec l'imperméabilisation de l'asphalte:
- le matériau peut être posé sur des mastics à chaud appliqués en une couche uniforme continue. La couche appliquée nécessite un nivellement, un compactage avec des truelles ou des rouleaux;
- le suivant est appliqué une fois que le fond est prêt, c'est-à-dire que le mastic est complètement refroidi;
- les joints sont espacés, un chevauchement de 200 mm est observé;
- la couche supérieure de protection doit être plane, avec l'épaisseur et la pente observées ;
- s'ils travaillent avec des mastics à froid, le principe de travail reste le même.
Principes de travail avec imperméabilisation roulée:
- le matériau peut être collé sur des mastics bitumineux à froid ou à chaud. Les exigences de préparation du substrat restent typiques ;
- lors de l'utilisation de mastics chauds, un ajustement des panneaux est nécessaire;
- le rouleau est déroulé sur la base de manière à obtenir un chevauchement de 100 mm ;
- le matériau posé est laissé pendant 24 heures pour éliminer les irrégularités et les vagues. La température dans la pièce ne doit pas être inférieure à +15 degrés;
- lorsque les panneaux se sont reposés, ils sont enroulés, ne laissant que la première rangée longitudinale et une ligne de guidage pour le collage est tracée;
- environ 0,5 m est plié du rouleau à coller et du mastic est appliqué. La base sous le rouleau est traitée avec le matériau;
- la zone avec du mastic est collée, en appuyant fermement sur la base, en roulant avec un rouleau du milieu vers les bords;
- puis éteignez le reste et agissez de la même manière ;
- les bords du matériau collé sont roulés avec un rouleau;
- le rouleau suivant est collé avec un chevauchement de 10 cm, en observant la lubrification des bords et en traitant avec un rouleau. Ensuite, ils agissent de la même manière, remplissant tout le domaine de travail;
- lorsque la première couche est prête, passez à l'appareil de la seconde en observant un chevauchement longitudinal de 20 mm. Contrôlez le placement des coutures à part.
Si la base n'a pas de pentes, les matériaux en rouleau sont déroulés sur la surface. S'il y en a un, ils travaillent des zones basses aux zones hautes.
isolation thermique
Appliquer efficacement matériaux d'isolation thermique Avec haute densité. Il peut s'agir de nattes ou de dalles à base de fibre de verre, de laine minérale ou de mousse de polystyrène plus moderne. L'épaisseur de couche optimale pendant le travail est de 100 mm.
L'isolation thermique est posée étroitement sur la base, assurant un ajustement parfait des joints. Comme alternative, il est permis d'utiliser une isolation thermique en vrac à base d'argile expansée. Il est appliqué sur la base en couches, suivi d'un nivellement et d'un compactage.
Dans les zones où la structure jouxte les murs et autres surfaces verticales, un espace doit être laissé, qui est fermé avec un ruban de matériau insonorisant.
Technologie des chaussées en béton
Les sols avec des revêtements en béton sont des structures à usage général qui sont utilisées avec succès à la fois dans la construction publique et dans la production. Un sol bien fait est capable de résister à des charges mécaniques élevées, à l'action de solutions, d'huiles, de sels et d'eau. En pratique le système fini est capable de résister à un chauffage jusqu'à 100 degrés.
L'enduit béton peut être posé au sol, sur la préparation béton sous-jacente, sur chapes ciment-sable M150 et plus, sur dalles béton armé. Sur le lieu de travail, optimal régime de température- pas inférieur à +5 degrés, jusqu'à une solution de la moitié de la résistance de conception.
Matériaux pour la préparation du béton:
- Le ciment Portland n'est pas inférieur à M400 en termes de résistance mécanique ;
- gravier ou gravats. La finesse ne doit pas dépasser 15 mm, soit 0,6 de l'épaisseur du revêtement. Il faut compter sur une consommation moyenne de l'ordre de 0,8 mètre cube par mètre cube de béton ;
- sable moyen ou grossier;
- l'eau.
Si un revêtement en béton anti-étincelles est requis, il convient d'utiliser du sable et de la pierre concassée à base de marbre ou de calcaire, qui ne produisent pas d'étincelles lorsqu'ils sont frappés par des objets métalliques.
La marque de béton ne peut être inférieure à M200. La mobilité de la solution est contrôlée - 2-4 cm. Il est permis d'introduire des plastifiants C-3 ou d'autres additifs modificateurs dans la formulation, ce qui réduira les coûts de main-d'œuvre lors de la pose.
Séquence de pose du béton :
- au début du travail, la base est nettoyée de la poussière et de la saleté;
- si des taches d'huile se sont formées sur la couche sous-jacente, elles doivent être éliminées avec des solutions spéciales prêtes à l'emploi ou une solution carbonate de sodium(5%). Après traitement, la zone est lavée à l'eau;
- si la pose est réalisée sur dalles préfabriquées, fissures. . Le remplissage s'effectue au ras de la surface des plaques.
Les évidements, les trous de montage sont soumis à l'étanchéité, pour lesquels un mortier ciment-sable M150 est préparé, pas inférieur à
Procédez à l'installation des balises en utilisant soit tubes d'acier, ou une barre en bois, ou un profilé métallique. Le diamètre et la hauteur du matériau doivent correspondre à l'épaisseur de conception du revêtement.
La première rangée de phares est disposée avec un retrait du mur égal à 0,5-0,6 m. Les suivants lui sont parallèles avec un pas allant jusqu'à 3 m. Il est permis de disposer la disposition immédiatement tout au long du travail. zone ou en fiches séparées, avec accostage dans l'axe et décalé de la largeur du rail.
Pour la fixation, prenez un mortier de ciment. Les guides sont alignés en fonction du niveau, conformément aux marquages précédemment appliqués. Pour corriger la position, de légers coups de marteau ou une pression de la main sont utilisés. L'horizontalité est vérifiée avec un rail ou des dispositifs spéciaux.
Le processus d'installation suivant est le suivant :
- avant de couler le béton, la base est abondamment humidifiée. Au moment de la pose du mortier, la surface doit être humide, mais sans excès d'eau;
- déterminer ensuite l'étendue des travaux, en calculant la vitesse de préparation du béton, la pose, la période de prise initiale;
- la solution est livrée sur le site à partir de l'unité de malaxage du béton par des camions malaxeurs. Si le coulage est effectué le long des premiers étages, la solution est déchargée directement sur la bande de bétonnage. Si des travaux sont effectués au deuxième étage et aux étages supérieurs, la solution est transférée dans des bacs de transfert et acheminée par portions sur le chantier par des ascenseurs, des grues;
- la solution est placée entre les balises, par une voie ;
- la couche est nivelée avec des pelles ou des grattoirs spéciaux de sorte qu'elle dépasse les balises de 3 à 5 mm;
- des bandes non remplies sont coulées après le démontage des balises, en utilisant des bandes prêtes à l'emploi comme guides et coffrages.
Le compactage est mis en œuvre avec la participation de chapes vibrantes, les déplaçant le long des phares. Si l'épaisseur de la structure est faible, le temps de vibration est minimisé, - agir jusqu'à ce que de l'humidité se forme à la surface. Une exposition excessive aux vibrations peut provoquer le tassement des granulats grossiers et la stratification du béton.
La vitesse de déplacement optimale de la table vibrante est réglée entre 0,5 et 1 mètre par minute. Lors du déplacement de l'outil, un rouleau de 2 à 5 cm de haut doit être assemblé à son bord inférieur.Dans les zones murales, dans les zones proches des colonnes, le compactage est effectué avec des pilonneuses manuelles pesant au moins 10 kg.
Si des cassures ont été faites lors du coulage, avant de reprendre la pose, les bords verticaux des enduits ayant eu le temps de durcir sont dépoussiérés, nettoyés et lavés à l'eau. Là où les coutures de travail sont placées, le scellement et le lissage sont effectués jusqu'à ce que la couture devienne invisible.
Technique du vide pour les sols en béton
Lors de la pose de chaussées en béton sur la préparation du béton, il est judicieux de se référer à la technique du vide. Dans ce cas, le revêtement est réalisé simultanément avec la couche sous-jacente. En conséquence, la résistance de la couche de surface est augmentée d'un tiers par rapport aux valeurs d'origine. Un sol de haute qualité avec d'excellentes caractéristiques physiques et mécaniques est formé.
Selon la technologie, une solution de béton liquide est posée sur la base, le compactage est effectué. Avec l'aide d'équipements spéciaux, ils extraient de l'épaisseur du béton l'excès d'eau qui travaille sur la résistance et la rigidité de la couche.
La formulation du béton est choisie en fonction de la qualité du ciment Portland et des granulats disponibles. Mais,
Pour assurer un effet d'étanchéité maximal, tout d'abord, une teneur accrue de la partie mortier est ajoutée à la composition du béton.
L'essence de la méthode du vide est la suivante:
- le mortier de béton est mélangé avec un excès d'eau de sorte que le tirant d'eau du cône atteigne 9-11 cm;
- le mélange est déchargé sur le lieu de pose et nivelé uniformément sur toute la surface;
- après coulée, la solution est compactée avec une chape vibrante si l'épaisseur de la couche ne dépasse pas 10 cm.Sur les chapes plus épaisses et en présence de renforcement, les vibrateurs profonds sont en outre attirés;
- des tapis d'aspiration sont placés sur la couche nivelée et compactée et reliés par le manchon à l'équipement d'aspiration ;
- le panneau inférieur filtré de tapis est placé directement sur le béton frais;
- le panneau supérieur est déroulé en lissant avec des brosses ou des rouleaux. Le travail commence au milieu de la bande, ce qui aura un bon effet sur l'étanchéité du système pendant le traitement sous vide.
Si deux panneaux ou plus sont posés sur la surface, ils doivent être placés avec un chevauchement d'au moins 3 cm.Le bord supérieur doit chevaucher le bord inférieur de 10 à 15 cm.Ensuite, l'aspiration commence. La durée de la technologie est calculée comme suit : 1-1,5 minutes par couche de béton de 1 cm.
Lorsqu'aucun mouvement d'eau n'est observé, le traitement est arrêté. Le béton doit gagner en densité, à laquelle il ne reste qu'une faible trace. Les tapis d'aspiration sont retirés.
Après le traitement sous vide, vous pouvez immédiatement commencer le lissage. Pour la première fois, ils travaillent avec des truelles à disques, la deuxième fois - avec des lames.
Traitement primaire des sols en béton
Lorsque la couche remplie est suffisamment compactée et gérée pour saisir, vous pouvez procéder au traitement primaire. L'état de préparation du revêtement peut être déterminé comme suit - lorsque vous marchez dessus, de légères traces doivent rester.
L'équipement de travail principal - truelles, truelles, avec disques de truelle installés. L'opération permet de corriger les défauts mineurs qui auraient pu se produire lors du coulage et du compactage ; après traitement, un horizon de finition se forme.
L'injection secondaire est possible après 1 à 6 heures. Au lieu de disques, les lames agissent comme le corps de travail. Pour les zones difficiles d'accès, ils travaillent manuellement ou avec une truelle pour le traitement chapes en ciment. Ces zones font l'objet d'un scellement prioritaire en raison de la prise rapide.
Se soucier
Le béton est un matériau qui doit mûrir dans des conditions humides. Pour fournir un tel environnement, la surface est recouverte de toile de jute humide, de sciure de bois humide, en maintenant le matériau dans cet état pendant 7 à 10 jours.
La fréquence de mouillage est choisie en fonction des conditions de température et d'humidité, cependant, le matériau ne doit pas sécher même partiellement
Ponçage et fraisage de sols en béton
Ce type de traitement nécessite la libération de la base des débris, mécanismes et dispositifs. Dans le processus de fraisage, des meules ou des fraises diamantées ordinaires d'un diamètre de 250 à 500 mm doivent être utilisées.
Le fraisage est effectué en bandes parallèles, chevauchant le bord de la bande dans l'approche suivante de 2 à 3 cm.En un seul passage, vous pouvez travailler à une profondeur de 2 à 7 mm, en vous concentrant sur les caractéristiques mécaniques et physiques du béton. Le but d'un tel traitement est l'exposition complète des grains de granulats, c'est-à-dire que la surface doit atteindre une résistance telle que son écaillage est impossible.
Les travaux se déroulent généralement en deux étapes. Lors de la première étape, la fraiseuse enlève une couche de 3 à 5 mm en un seul passage. Ensuite, le polissage est effectué en 1-2 passes, en utilisant Rectifieuses. Lors du traitement, il est nécessaire d'organiser un nettoyage en profondeur de la surface à temps.
Finition
La finition vous permet d'améliorer les performances des sols en béton. Lors du choix des matériaux, ils sont guidés par les conditions dans lesquelles la structure fonctionnera.
Vous pouvez agir comme suit :
- imprégnation de surface avec des fluates. Le revêtement est appliqué au plus tôt 10 jours après le versement de la solution. Le régime de température est observé dans la pièce - pas inférieur à +10 degrés. Avant le travail, la base doit être séchée et soigneusement nettoyée avec des aspirateurs de construction. Le matériau est appliqué jusqu'à ce que le béton cesse de l'absorber. La pratique montre que trois approches avec un intervalle de 24 heures suffisent pour cela;
- imprégnation de mastic. À ces fins, utilisez du verre liquide, des solutions aqueuses de chlorure de calcium. Le traitement est effectué en trois approches avec un intervalle quotidien. Lorsque le traitement est terminé, le béton doit être rincé à l'eau;
- ajouter des garnitures. Pour le durcissement, des mélanges secs spéciaux (corindon, quartz, métal) sont utilisés. Le type de matériau est sélectionné en fonction des charges de conception. Les chapes sont appliquées sur le béton frais après la prise initiale en deux passes à l'aide de machines de finition du béton ;
- comme couche de protection, vous pouvez utiliser du polyuréthane, du vernis époxy. Le matériau est appliqué sur le béton pendant la période de durcissement initial, immédiatement après la fin de l'opération de meulage. Avant les travaux, le sol est nettoyé avec un aspirateur industriel, traité avec un chiffon humidifié et apprêté avec le même vernis, mais avec un solvant dilué. Les compositions sont étalées au pinceau, au rouleau ou au pistolet. On observe un séchage couche par couche, au cours duquel la surface est protégée de l'humidité.
En plus des vernis polyuréthanes pour l'appareil de la couche supérieure, vous pouvez utiliser revêtements polymères(époxy, acrylique). Les couches de peinture sont appliquées en couche mince, pas plus de 0,3 mm d'épaisseur.. Si un effet décoratif est requis, les sols autonivelants qui forment une surface mate homogène sont un bon choix. Dans des conditions de charges élevées, vous pouvez vous tourner vers le dispositif de revêtements hautement chargés.
Dans les locaux résidentiels, le choix du revêtement de finition est pratiquement illimité - il peut s'agir de carrelage, de stratifié, de moquette, de liège, de linoléum ...
Sécurité
Lors de la construction de sols en béton, les règles de sécurité dans la construction sont toujours respectées. Tous les travailleurs doivent être familiarisés avec les conditions de travail, le briefing, la formation à la manutention du matériel et des outils.
Le dispositif des sols est réalisé à l'aide d'équipements technologiques. Des équipements de protection individuelle et collective, des outils de construction à main sont utilisés. Le lieu de travail dans les endroits difficiles d'accès doit être bien éclairé.
Lors de la pose d'imperméabilisation sur des mastics bitumineux chauds, une attention particulière est requise. La ventilation est assurée dans des espaces clos. Le contact prolongé des mélanges de ciment avec la peau est inacceptable.
prix d'un sol en béton
La technologie des sols en béton est disponible et ne nécessite pas de coûts trop élevés. En moyenne, les coûts financiers de la pose de 1 m². "clé en main" commence à partir de 850-1100 roubles. À ce coût, vous pouvez ajouter en toute sécurité le coût d'achat et d'expédition des matériaux.
Matériel, outil
Les travaux concrets sont effectués avec la participation d'un ensemble standard de machines et d'outils.
L'ensemble suivant doit être assemblé sur le chantier :
- en cas d'auto-préparation de solutions, des bétonnières sont nécessaires;
- le compactage préliminaire des sols, les couches sous-jacentes sont effectuées par des pilonneuses mécaniques;
- le remplissage est compacté par des rails vibrants, des vibrateurs profonds ;
- le traitement de finition est effectué avec la participation de truelles, de meuleuses;
- les aspirateurs industriels sont utilisés pour le nettoyage et le dépoussiérage ;
- niveau, niveau - un outil pour mesurer, contrôler l'horizontalité, la planéité de la structure;
- pelle, récipient propre, spatules.
conclusions
L'installation de revêtements de sol en béton doit être mise en œuvre dans le strict respect du processus technologique. Un résultat qualitatif est obtenu avec un travail professionnel, avec un contrôle qualité progressif du travail.
Le dispositif des sols industriels en béton est présenté en détail dans la vidéo :
La chaussée en béton de ciment est une chaussée de type capital dur conçue pour tout trafic lourd.
Ces revêtements sont différents:
- haute résistance;
- durabilité ;
- un niveau de circulation plus sûr la nuit ;
- coefficient d'adhérence élevé du revêtement, qui ne change pas lorsqu'il est humidifié;
— niveau élevé de mécanisation et d'automatisation ;
- la capacité à mener des travaux de construction dans des conditions défavorables;
- faible usure du revêtement (0,1-0,2 mm/an).
Avec tout ce qui précède et évident points positifs Il y a aussi des inconvénients à ces types de couverture :
- difficultés survenant lors de la réparation du revêtement;
– impossibilité d'ouvrir la circulation immédiatement après l'achèvement des travaux ;
- la nécessité de joints de dilatation.
Des chaussées en béton de ciment avec une hauteur de remblai de plus de 1,5 mètre sont construites la deuxième année.
Exigences pour les revêtements routiers c/w :
Le béton de ciment doit être solide et résistant au gel (F).
La résistance au gel est estimée par le nombre de cycles de congélation et de décongélation alternées d'échantillons saturés d'eau à l'âge de 28 jours sans diminution de résistance de plus de 25 % et perte de poids ne dépassant pas 5 %.
Les chaussées routières en béton de ciment sont divisées en grades qui caractérisent sa résistance à la traction en flexion et en compression.
La plate-forme en Russie et à l'étranger est différente: dans notre pays, les autoroutes à diverses fins sont en asphalte, tandis qu'en Europe et aux États-Unis, elles sont principalement en béton. C'est la différence évidente dans leur qualité. En Russie, les routes en béton ne se sont pas généralisées en raison de leur coût important - après tout, les vastes étendues du pays et la mise à jour de la toile coûteront à la population une nouvelle augmentation des impôts. Cependant, personne n'interdit aux propriétaires d'équiper les parkings et les porches en béton durable.
A quoi servent les routes en béton ?
La construction de routes en béton est opportune dans les endroits où il n'y a pas de possibilité de réparations fréquentes et où il est nécessaire d'avoir une plate-forme durable. En Russie c'est :
- Autodromes ;
- Pistes et atterrissages dans les aéroports ;
- Stationnement de voitures et autres équipements ;
- Sentiers piétonniers et trottoirs dans les villes;
- Routes côtières et remblais où prédominent une humidité élevée et une exposition à l'eau.
La durée de vie d'une dalle de béton dépasse la durée de vie de l'asphalte jusqu'à 2-3 fois. Pour cette raison, il est conseillé de remplacer partout les chaussées en béton bitumineux qui ne résistent pas aux conditions climatiques par du béton de ciment, ce qui se produit progressivement aux États-Unis.
La différence entre l'asphalte et le béton
Pourquoi la chaussée en asphalte n'est-elle pas aussi durable que la chaussée en béton? Tout est question de matériaux de base :
- L'asphalte est un composite de sable, de pierre concassée, de charges minérales et leur liant est constitué de polymères bitumineux.
- Le béton est un mélange de sable et de gravier mélangé avec du ciment et des additifs.
La principale différence entre le béton et l'asphalte est le liant dans leurs formulations. Le bitume, contrairement au ciment, ne forme pas une pierre durable, s'affaisse sous des sols faibles sous charge, se ramollit au soleil et hiverne mal. Le béton, soumis à la technologie de préparation et d'installation, est dépourvu de ces défauts.
La plate-forme se compose de plusieurs couches :
- Le sous-jacent est constitué de pierre concassée qui draine l'eau du sol et de sable qui compense les charges venant du dessus et du dessous du sol.
- Renforcement - cette couche de béton de qualité inférieure qui lie la literie.
- La plate-forme principale est une couche de béton.
Lors de la pose d'autoroutes à fort trafic de véhicules lourds, la route doit être en béton armé non contraint et contraint, la cage d'armature dans laquelle ne permet pas à la pierre de se fissurer sous le poids des poids lourds.
Dans la construction privée, ainsi que lors de l'aménagement d'une chaussée sur des sols saturés d'eau ou à forte teneur en eau, l'imperméabilisation de la chaussée est posée sur un remblai de sable et de gravier (des matériaux de toiture peuvent être utilisés). La couche empêche le mouillage constant du béton et, par conséquent, la corrosion de la pierre et de la cage d'armature.
Types de toile
Une route en béton convient aux autoroutes à grande vitesse à fort trafic et aux allées de village. Pour ces cas, choisissez différents types de toiles, de qualité et de coût différents :
- Une seule couche Haute qualité pour les routes de tout usage adaptées à la pose des couches supérieures et inférieures ;
- Le béton pour la couche inférieure de la toile est bon marché - il a une faible résistance, des exigences minimales sont imposées à ses composants. Un revêtement d'un tel matériau peut être utilisé dans l'aménagement de territoires adjacents avec un petit flux de voitures;
- Béton à performances moyennes pour chaussées lourdes et avancées. Peut être posé sur des routes importantes pour la colonisation ;
- Dans un groupe séparé, vous pouvez faire l'organisation de la route avec des dalles de béton prêtes à l'emploi.
Matériaux de remplissage
Le béton M400 est un matériau universel pour la pose de routes. Sa résistance est suffisante pour résister à la pression des roues des voitures et des camions sur les routes urbaines et rurales.
La base du béton est le ciment Portland, résistant à l'eau (1 partie). Des plastifiants sont également introduits dans la solution, ce qui augmente l'hydrophobicité du revêtement et sa résistance. La composition de la solution de travail comprend également:
- Pierre concassée - 5 parties;
- Sable - 2 parties.
Pour bétonner la route, il est rationnel de commander du béton prêt à l'emploi à l'usine - même pour un petit chantier, vous aurez besoin de beaucoup de mortier, qui doit être coulé rapidement, évitant ainsi le grippage des lots individuels.
Les propriétés des matériaux de chaussée peuvent varier en fonction de la charge prévue et des conditions de pavage.
Exigences relatives à la qualité des routes en béton
Lors du choix des composants pour la préparation du béton routier, ils sont guidés par le SNiP 3.06.03-85 "Routes". Le document réglemente les exigences relatives à la qualité de la toile finie:
- La résistance aux contraintes mécaniques est la principale exigence pour la surface de la route. Pour les routes à des fins différentes, l'indicateur est déterminé individuellement.
- Pas de fissures dans le revêtement après la pose et pendant le fonctionnement. Le respect de la technologie de construction des routes en béton et la bonne composition de la solution de travail aident à résoudre le problème.
- Résistance à l'eau et résistance chimique. Les autoroutes sont situées dans différentes conditions de relief et de qualité du sol, et en l'absence d'un système de drainage organisé (en cas de violation de la technologie de construction), l'eau s'accumule sur la toile, aggravant sa qualité.
exigences concrètes
La qualité de la toile est déterminée par les composants constitutifs, qui doivent également faire l'objet d'une sélection rigoureuse conformément aux profils GOST. Par exemple, la résistance de la pierre concassée, capable d'assurer un fonctionnement fiable et à long terme de la route, est d'au moins 1200 kg/cm 2 . Pour un oreiller, une pierre concassée moins durable de 800 à 1000 kg / cm 2 fera l'affaire.
Mobilité mortier de béton– 2 cm lors d'un test avec un cône. Un grand nombre d'inclusions minérales de différentes fractions permet d'éviter les écarts par rapport à ce paramètre.
Une autre exigence pour le béton est une résistance élevée à la flexion; pour cela, des plastifiants sont introduits dans la solution et la toile est en outre renforcée avec des armatures.
Avantages et inconvénients des routes en béton
Par rapport aux routes en asphalte, les routes en béton présentent de nombreux avantages :
- Haute résistance et rigidité du revêtement;
- Résistance à la chaleur, aux changements de température ;
- Longue durée de vie sans besoin de réparation ;
- Une bonne adhérence de la surface de la route et des roues automobiles augmente la sécurité routière.
Les inconvénients des routes sont moindres, mais ils sont importants :
- Coût de construction élevé;
- La nécessité d'un strict respect de la technologie dans la préparation des solutions et la sélection des composants ;
- La nécessité d'un ensemble complet de résistance du béton avant le début de la route.
Construction de routes en béton
Examinons en détail les étapes de la construction de routes en béton, car la durée de vie du revêtement dépend du respect de la technologie de pose.
Les travaux de terrassement sont parmi les plus coûteux et les plus complexes. Avant de commencer, un projet détaillé est établi sur la base d'une étude géologique du relief. Si possible, le plan de pose de la route est rendu horizontal - les monticules sont enlevés, une planche avec compactage de la roche est faite dans les évidements.
La couche de sol fertile est enlevée: pour la construction complète de l'autoroute à grande échelle, pour la pose privée de zones adjacentes, 15 à 20 cm suffisent.Les plus bas sont compactés avec des rouleaux et des plaques vibrantes d'un poids important. C'est l'une des étapes les plus importantes - la rigidité et l'intégrité du revêtement sous des charges dynamiques intenses dépendent du niveau de résistance de la base.
Au stade des travaux préparatoires avec le sol, un système de drainage est pensé pour drainer les eaux souterraines et les eaux pluviales. Pour ce faire, la base n'est pas réalisée dans un plan idéal, mais sous un léger angle de 2-4%. Le long de la route, des gouttières en béton ou des pentes naturelles peuvent être équipées, le long desquelles l'eau s'écoule dans le récepteur ou dans le sol.
Pose de literie
De la pierre concassée et du sable sont versés sur le sol compacté. Ils remplissent la fonction de compensateur de charge et de drainage de l'eau.
L'épaisseur des couches de litière dépend du type de relief et des propriétés des bases et fluctue autour de 20 à 40 cm.Lors de la pose de routes longue distance entre sable et gravier, le géotestile est souvent posé - il ne permet pas aux fractions de se mélanger et les remblais remplissent mieux leurs fonctions.
Sur les bases avec un niveau élevé d'eau souterraine, il est rationnel d'épaissir le remblai de gravats - il ne se lave pas et draine bien l'eau. Le sable doit être posé sous des couches de béton - il forme un coussin dense.
Les couches de sable et de pierre concassée doivent être compactées avec un rouleau ou des fosses vibrantes pour obtenir une résistance de coussin élevée.
Pour plus de commodité, la couche de litière est parfois recouverte d'une fine chape de béton jusqu'à 5 cm d'épaisseur, et une feuille d'étanchéité est posée sur le dessus.
Le béton étant faible aux charges de flexion, l'utilisation d'armatures n'est jamais superflue - le choix de son type dépend à nouveau des caractéristiques de la base. Dans certains cas, le renforcement peut ne pas être appliqué du tout.
Le diamètre de l'armature de la toile en béton n'est pris que de manière constructive selon les calculs. Ce sont généralement des barres de 10 mm soudées dans un treillis avec une cellule de 150 mm. Les produits de renforcement sont posés dans une couche de béton à une hauteur d'au moins 4 cm du plan inférieur. Il est important que le treillis se trouve dans la partie inférieure de la dalle, car c'est en elle que la charge de rupture se concentre et que des fissures se forment.
Le moyen le plus simple de réaliser un coffrage consiste à utiliser des panneaux épais d'une section de 50 × 150 mm (le choix de la hauteur dépend de la couche de conception de la base en béton et du revêtement). Convient également pour le contreplaqué épais. Les planches et le contreplaqué sont fixés avec des chevilles de renfort enfoncées dans le sol depuis l'extérieur de la toile. Lors de la pose de cheminements pour piétons et de parkings pour voitures, le coffrage peut être remplacé par une bordure de trottoir installée en préparation du coulage.
Chaussée en béton
Le coulage de la route avec du béton doit être effectué en continu, de sorte que les matériaux pour la toile sont préparés immédiatement dans la bonne quantité. Il est conseillé de commander le béton à l'usine; lors de la construction de grandes routes, des ateliers mobiles temporaires pour la production de mortier sont installés à proximité des installations, ce qui réduit les coûts de livraison.
Si nécessaire, du béton de faible qualité (par exemple, M200) est posé sur la base avec du remblai, puis avec du mortier de finition M400 avec des adjuvants.
La pose du revêtement de finition se déroule en 2 étapes: d'abord, un substrat de 30-40 mm est coulé, un treillis de renforcement est posé dessus et le reste de l'épaisseur est coulé.
L'épaisseur totale de la couche est d'environ 12 cm, parfois plus ou moins.
Le béton est coulé dans la préparation sans interruption et la surface est immédiatement nivelée. Le matériel est constamment mis à jour, le travail se poursuit 24 heures sur 24.
Après la pose, le béton doit être compacté par vibrocompression. La procédure expulse les bulles d'air et compacte la structure du revêtement fini.
Couper et sceller les joints de dilatation
Le dispositif d'une route en béton comprend la découpe de la toile en segments. C'est possible, alors le béton acquerra une résistance suffisante de 50 à 60% et résistera au poids d'une personne et d'un équipement de coupe.
Les coutures sont nécessaires pour compenser la dilatation thermique, qui dans divers degrés la pierre de béton est jetée. Avec les changements saisonniers du volume des dalles, les fissures ne se forment pas dans la chaussée.
Le sciage est effectué avec un outil spécial - le jointage.
Les joints de température sont réalisés à une distance déterminée par des calculs. L'une des formules de définition est l'épaisseur du revêtement × 30.
Pour empêcher l'eau de pénétrer dans la dalle à travers les joints, ils sont remplis de mastics bitume-polymère.
Entretien et prévention des chaussées en béton
Pour que le travail ne soit pas perdu, selon la technologie, la route en béton ne peut être ouverte à la circulation qu'après que le béton ait complètement gagné en résistance, c'est-à-dire après 28 jours.
Pour éviter la destruction de la toile, celle-ci est protégée par des imprégnations polymères, qui forment un film imperméable en surface. Certes, ceux-ci réduisent la rugosité de la route et son adhérence aux roues. Il s'agit d'une qualité négative pour les autoroutes à grande vitesse, donc dans la plupart des cas, la toile est laissée telle quelle. Si la préparation du sol et la technologie de pose ont été observées, les joints sont correctement coupés, rien ne menace l'intégrité des dalles pendant longtemps.
Une autre façon de prévenir et de réparer les routes en béton consiste à poser une couche d'usure. L'asphalte est appliqué sur le béton, ce qui assure l'adhérence des roues au revêtement et prolonge de plusieurs fois la durée de vie de l'autoroute elle-même. De plus, la réparation des chaussées en béton bitumineux est beaucoup moins chère.
Lorsque des fissures apparaissent, des mesures doivent être prises pour les éliminer. Pour sceller les petites violations, des mastics spéciaux sont utilisés, pour réparer les dommages plus profonds, un mortier de béton est utilisé. Dans tous les cas, la fissure est nettoyée et humidifiée avant l'introduction du granulat.
Si un défaut survient, vous devrez supprimer toute la section de la toile. La raison de ces déformations est un compactage insuffisant de la base du sol ou du remblai.
L'installation de planchers monolithiques en béton est souvent requise dans les installations qui impliquent des charges opérationnelles importantes. Il peut s'agir d'hypermarchés, de complexes commerciaux et d'expositions, de bâtiments industriels. Souvent, des sols monolithiques sont disposés dans des bâtiments résidentiels. Lors du choix des matériaux pour la fabrication de cette conception, il est nécessaire d'être guidé par les calculs de la résistance du sol préparé aux effets de divers facteurs destructeurs. Souvent le seul bonne décision dans ce cas, il reste des sols monolithiques.
Les propriétés distinctives des sols en béton sont une longue durée de vie, une résistance à l'usure extrêmement élevée, une facilité d'entretien. En raison de l'utilisation d'additifs de renforcement dans le mélange, la couche supérieure de la base devient résistante à l'humidité et aux produits chimiques.
Processus technologique de la chaussée en béton
À la base de ce type de sol industriel, un mélange ciment-sable contenant de la pierre concassée ou une dalle en béton armé prête à l'emploi est utilisé. La technologie de pose de béton présentée convient aux grands locaux industriels ou publics, ainsi qu'aux maisons privées.
Tous les travaux sont effectués dans le strict respect du SNiP et de toutes les exigences du processus technologique. dalle en béton doit être posé sur une base durcie et nettoyée. La raison de ces exigences est que si un mortier de mauvaise qualité est utilisé dans l'ancienne chape, l'adhérence du revêtement se détériore et, sous de forts impacts, la surface du béton commencera à s'effondrer. De plus, la cause d'un couplage faible est des taches de graisse ou d'huiles techniques non éliminées.
Pour préparer efficacement la base pour couler les sols monolithiques, il est nécessaire d'effectuer un certain nombre des activités suivantes:
- Élimine mécaniquement toutes les salissures, les taches de graisse, tout pelage et tout effritement. Pour éliminer les traces d'huile technique, un mortier de peinture est utilisé, le lavage à l'acide est efficace contre la colle à béton.
- Les irrégularités dans le niveau horizontal de la surface sont éliminées au moyen d'un mécanisme de fraisage. Si la différence de hauteur est jusqu'à 10%, il n'est pas nécessaire de l'éliminer.
- S'il y a des fissures ou des nids-de-poule sur la surface, ils doivent être dilatés et remplis d'un mélange contenant des polymères.
- Les zones qui ne se prêtent pas aux travaux de reconstruction doivent être démantelées et coulées avec du nouveau béton.
- La couche supérieure de l'ancienne chape doit également être nettoyée de la poussière. Sinon, la qualité du couplage diminuera, certains des contaminants flotteront, violant la douceur de la surface.
Après travail préparatoire entièrement mis en œuvre, le nivellement de la base est en cours. À la suite de cet événement, la note la plus élevée du revêtement est déterminée, et donc l'épaisseur de la chape en béton.
Les principaux types de sols monolithiques
Aujourd'hui, il existe trois principaux types de sols en béton :
- Sol ciment-sable monocouche. Utilisé pour les pièces avec une petite quadrature. Ce type d'enduit est peu résistant aux charges du fait de l'absence d'une couche supplémentaire d'enduit béton. L'option est pertinente pour les petits appartements, les immeubles résidentiels ou les locaux techniques.
- Plancher multicouche. La fabrication de cette conception est difficile, car le mélange de béton est posé en deux couches ou plus. Il est recommandé d'utiliser une méthode de revêtement similaire pour les travaux de reconstruction.
- Planchers monolithiques renforcés. Diffère par sa durabilité extrême de toutes les options des bases similaires. Grâce à l'utilisation de fers à béton, il devient possible de réduire l'épaisseur du revêtement et la masse des sols en béton. En tant que matériau de renforcement, des tiges ou des treillis en acier sont utilisés, si nécessaire, des éléments synthétiques. Cette conception est typique des locaux à forte charge sur le revêtement : ateliers de production, parkings, hangars agricoles, etc.
Le processus technologique de construction d'un sol en béton diffère selon but fonctionnel locaux. Dans ce cas, le but de cet événement est d'une importance considérable - niveler la surface du sol à l'intérieur de la pièce, isoler le revêtement en béton, augmenter la hauteur de la base, etc. En utilisant diverses méthodes de fabrication d'une chape ciment-sable, il est possible d'améliorer la qualité de la structure et la durée de la période de fonctionnement.
Il est important de noter que la préparation d'un plancher monolithique doit être conforme aux codes et règlements du bâtiment établis, c.-à-d. Couper. Leurs exigences peuvent varier en fonction des facteurs opérationnels du produit et du lieu de coulée.
Étanchéité de fondation
La surface nivelée et nettoyée est traitée avec du mastic (mélange imperméabilisant à base de colle). Cette étape fournit fonctionnellement :
- adhérence de haute qualité de l'ancienne chape en béton avec une nouvelle couche de ciment-sable;
- couche d'étanchéité supplémentaire.
Une alternative intéressante à une telle solution est l'hydrostekloizol. L'agent est appliqué en deux couches, la hauteur de chacune est d'au moins 5 mm. Possédant une plasticité élevée et une résistance aux charges atmosphériques, ce revêtement crée une barrière d'étanchéité durable pendant 10 à 15 ans.
La chaussée en béton monolithique est posée sur des "cartes" - des sections rectangulaires préparées pour la pose du mortier. La taille de ces parcelles est déterminée en fonction du potentiel de production. Des guides sont installés le long du périmètre des cartes, c'est-à-dire phares.
Renforcement et isolation thermique des sols en béton
Des éléments de renforcement sont posés pour éliminer le risque de fissures du sol pendant toute la période de fonctionnement, en particulier si une épaisseur de chape importante est obtenue. Ce type de travaux est réalisé en totale conformité avec les calculs de conception des charges futures.
À ces fins, un treillis en acier est souvent utilisé, le diamètre de la tige est de 5 mm et la taille d'une seule cellule est de 100 × 100 mm/150 × 150 mm. Le matériau pour la fabrication du treillis est la classe d'armature VR1.
Lorsque des charges importantes sont attendues sur le sol en béton, il est recommandé d'utiliser un armo-frame pour le renforcer. L'armature est raccordée directement sur le chantier, le diamètre de la tige varie de 8 à 18 mm.
Les raccords doivent être attachés ensemble avec du fil. Il est impossible de souder dans tous les cas, cela est dû aux différents degrés de retrait et de dilatation du métal et du béton lors des changements de température.
Installation de balises à faire soi-même
L'étape la plus critique dans la production de sols monolithiques, car la planéité du revêtement dépend du niveau des rails de balise exposés.
- En règle générale, la pièce est divisée en sections dont la largeur ne dépasse pas deux mètres. Des rails de balise spéciaux en forme de T sont utilisés comme guides, mais un profil régulier ou tuyau rond. Dans certaines situations, un simple bloc de bois, pré-calibré sur une surface plane.
- Les phares sont posés sur des collines de mortier frais de faible épaisseur. Après cela, en appuyant sur le rail dans la solution ou, au contraire, en élevant le niveau horizontal exact est défini. Le coulage de la première couche de béton n'est autorisé qu'après le durcissement complet des balises exposées.
- Lorsque la pièce a une grande quadrature et qu'il n'est pas possible de verser le sol une seule fois, la base est divisée en cartes rectangulaires ou carrées. Les limites de ces zones sont clôturées avec des coffrages en bois. Lorsque toutes les sections sont remplies et que le revêtement de béton durcit, les cloisons sont retirées et l'espace formé sous elles est rempli de mortier prêt à l'emploi.
Sol en béton, coulage du béton
Pour un travail réussi sur les sols coulés, il est fortement recommandé d'utiliser une bétonnière. Pour les gros volumes, des mélangeurs spéciaux pour automobiles sont utilisés. Cette approche offre la possibilité idéale d'un approvisionnement continu en mortier, ce qui affecte positivement la qualité des sols monolithiques.
- Le mélange fini est placé sur la base préparée dans des cellules, après quoi il est nivelé avec une pelle ordinaire pour éviter la formation de vides et augmenter la densité de la couche. Dans la mesure du possible, un compacteur vibrant est utilisé. Il est immergé dans la solution elle-même et maintenu jusqu'à ce que du lait apparaisse sur le revêtement.
- Lorsque l'épaisseur de la pose de béton dépasse légèrement les balises, elle est nivelée au moyen d'une règle. Dans ce cas, les mouvements doivent être dirigés vers soi et simultanément vers la gauche et vers la droite. Parfois, au lieu de la règle, un rail vibrant spécial est utilisé, installé le long des guides. Le principe de son fonctionnement est le même que celui de la règle manuelle, uniquement mécanisée.
- Une fois la chape prête, le revêtement est régulièrement humidifié avec de l'eau pour éviter un séchage et une fissuration intenses. Le délai jusqu'à ce que le sol soit entièrement prêt à fonctionner est d'au moins un mois.
Pour préparer les sols en béton de vos propres mains, vous devez utiliser la carte technologique pour l'installation d'un revêtement ciment-sable. Routage comprend prochaines étapes appareils au sol :
- préparation de base;
- après l'imperméabilisation de la base;
- puis pose de matériaux de renforcement ;
- installation de guides et cadre de coffrage;
- production de mélange ciment-sable et sa pose;
- alignement de la couche supérieure ;
- après séchage complet du sol, meulage de finition du revêtement fini.
Le revêtement de sol en béton n'est pas une tâche facile. diverses possibilités processus technologique. Grâce à la mise en œuvre de haute qualité de toutes les étapes processus de production une structure solide de planchers monolithiques est formée, capable de résister haute pression et ne pas se déformer même après une longue période de fonctionnement.