Exzentrischer Schraubstock mit Schnellverschluss. DIY Exzenterklemme aus Metall
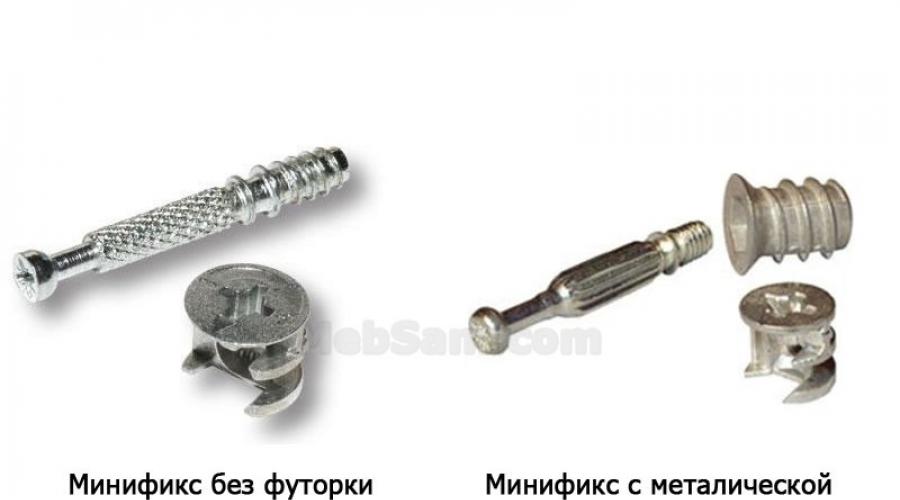
Lesen Sie auch
Ein Exzenterbefestiger (Ratexes, Minifixes, Exzenterspanner – wer auch immer das nennt) ist eine der häufigsten Arten von Möbelbefestigern.
Minifixes sind gut, weil die mit ihrer Hilfe befestigten Teile viele Male demontiert und wieder zusammengebaut werden können, ohne dass die Steifigkeit verloren geht, was nicht passieren würde, da die Befestigung bei jeder Montage/Demontage ihre Steifigkeit verliert.
Minifix-Möbel haben nur einen Nachteil: Der Einbau ist mühsam. Wenn Sie nicht über teure Spachtelausrüstung verfügen, müssen Sie für die Installation selbst drei verschiedene Löcher in drei verschiedenen Ebenen sehr sorgfältig markieren und genau bohren, was normalerweise viel Aufwand und Zeit erfordert.
Diese Arbeit duldet keine Fehler bei der Markierung. Schließlich wird man die Verbindung am Ende nicht anpassen können.
Auch die Kosten können nicht als völlig günstig bezeichnet werden. Der Preis für einen Minifix ist in der Regel 3-4 mal teurer als für eine Bestätigung.
Daher sollte es in den notwendigsten Fällen eingesetzt werden.
Ein Exzenterspanner wird an Stellen eingesetzt, an denen Teile befestigt werden (T- oder L-förmig), deren Verbindung vor neugierigen Blicken verborgen bleiben muss. Sie befestigen zum Beispiel:
- Tischplatten für Computer- und andere Tische aus Spanplatten
- Kommodenoberteile
- Böden, Dächer und andere Teile, bei denen es nicht möglich ist, Löcher an der Vorderseite des Teils zu bohren.
Die verbaute Minifix-Stange des Exzenterspanners ist vollständig im Spanplattenkorpus verborgen, sichtbar bleibt nur der Exzenter, mit dem verbaut wird innen Produkte.
Arten von Exzenterkupplungen
Je nach Hersteller gibt es mehrere Modifikationen des Minifix, darunter:
- Stab (Rastex)
- Exzentrisch (Minifix)
- Kunststoff- oder Metallbuchse (je nach Hersteller)
- Minifix-Stummel (optional)
Es gibt auch Eck- (Scharnier-) und doppelseitige Kupplungen. Aber um sie zu benutzen, muss man ein völliger Perverser sein und auch sorgfältig darüber nachdenken, wo sie verwendet werden können. Heutzutage werden sie aufgrund ihrer Nutzlosigkeit praktisch nicht mehr verwendet.
Bis heute beliebt ist die Exzenterklemme, deren Stange es ist bereits im Gange mit Spanplattengewinde, ohne Kunststoffhülse. Das heißt, es besteht nur aus zwei Teilen: der Stange und dem Exzenter.
Aber für alle Fälle analysieren wir in diesem Artikel die Installation von zwei Arten dieses Befestigungselements – sowohl mit als auch ohne Buchse.
Einbauanleitung für Exzenterkupplung (ohne Buchse)
Benötigtes Werkzeug:
- Schraubendreher
- Forstnerschneider 15 mm
- Bohrer 7 mm (für Stangenkörper)
- Bohrer 5 mm oder Bestätigung (zum Einschrauben der Stange)
- Lineal, Ahle, Bleistift
Die Standarddicke des Spurstangenkörpers beträgt 6 mm und die Länge beträgt 44 mm. Der Exzenterdurchmesser beträgt 15 mm und seine Tiefe 12,5 mm. Foto von Exzenter und Stab:
Wie oben erwähnt, müssen für die Installation eines Minifix drei Löcher mit unterschiedlichen Durchmessern in die zu verbindenden Teile gebohrt werden.
Beginnen wir also mit dem Zusammenbau.
Damit der Exzenter den Stangenkopf sicher erfasst, sollte er 6 mm überstehen:
Под вкручивание штока в ДСП делается отверстие сверлом 5 мм (или конфирматным), если это боковина, его центр должен располагаться на расстоянии 8 мм от края, глубиной 10-11 мм (шток должен вкручиваться плотно и до самого конца, по отметку, это видно auf dem Foto).
An einem anderen Teil werden Markierungen für zwei Löcher angebracht.
Der erste befindet sich im Mittenabstand von 34 mm vom Rand, unter dem Loch mit einem Forstnerfräser mit einem Durchmesser von 15 mm. Seine Tiefe muss der Dicke des Exzenters entsprechen (ca. 12 mm), damit der Exzenter bündig in das Teil passt.
Das zweite Loch wird am Ende des Teils genau in der Mitte mit einem 7-mm-Bohrer (bei 1 mm) gebohrt mehr Körper Stange).
Anbringen eines Kabelbinders mit Kunststoffhülse
Das Prinzip der Montage eines Minifix mit einer Buchse ist genau das gleiche wie bei der Montage eines Metall-Minifix, mit dem einzigen Unterschied, dass: Sie benötigen ein weiteres Loch für die Stange.
Video: Installation einer exzentrischen Möbelkupplung
Ein Schraubstock ist aus einer Autowerkstatt oder Heimwerkstatt nicht mehr wegzudenken, egal mit welchem Material Sie arbeiten müssen: Metall, Kunststoff oder Holz. Üblicherweise kommt überall ein klassischer Schraubstock mit Kurbel zum Einsatz, der Teile langsam spannt und wieder löst.
Es ist absolut einfach und in kurzer Zeit, einen selbstgebauten Metallschraubstock mit Exzenterspanner herzustellen, der kompakt ist und zudem eine schnelle und zuverlässige Fixierung von Werkstücken ermöglicht. Die Geschwindigkeit des Schraubstocks ist besonders nützlich, wenn große Arbeitsmengen ausgeführt werden, die durch Gleichmäßigkeit und Monotonie gekennzeichnet sind.
Den einfachsten Metallschraubstock mit Exzenterspanner können Sie mit Ihren eigenen Händen aus kostengünstigem Schrottmaterial herstellen – übrig gebliebenem Altmetall, das fast immer in einer Heimwerkstatt oder Garage zu finden ist. Daher werden wir uns nicht mit den Materialien befassen. Sofern Bedarf zur Spezifizierung der Merkmale besteht, klären wir dies im Rahmen des Arbeitsprozesses.
Für die Arbeit benötigen wir die gängigsten Werkzeuge:
- Schweißvorrichtung;
- Schleifmaschine mit Trennscheibe;
- Bohrmaschine oder Bohrmaschine;
- Gewindebohrer:
- Hammer;
- Milben;
- Schraubstock usw.
Beginnen wir mit der Herstellung eines Schraubstocks
Damit die Arbeit reibungslos verläuft, kann es nicht schaden, sich das Endergebnis der gerade begonnenen Arbeit im Kopf vorzustellen: ein fertiger Schnellspann-Exzenterschraubstock, der uns durch seine Kompaktheit, Farbvielfalt und erstaunliche Fähigkeit zum schnellen und schnellen Spannen begeistert jedes Werkstück zuverlässig spannen.Nun machen wir uns an die Arbeit, damit der Traum Wirklichkeit wird. Wir finden den Rest des nutzlosen Kanals, markieren ihn mit Lineal und Marker und schneiden das benötigte Stück mit einer Schleifmaschine ab. Es wird die Basis für die beweglichen und festen Backen unseres Schraubstocks.
Von einer geeigneten Ecke mit gleichem Winkel schneiden wir nach dem Markieren zwei gleich lange Stücke ab, die in einem Schraubstock die Basis der Backen unseres hausgemachten Schraubstocks bilden.
In der Mitte des Regals einer der Ecken – der zukünftigen beweglichen Backe des Schraubstocks – markieren wir die Mitte des Lochs, das wir auf einer Bohrmaschine bohren.
Auf dem Querstück des Kanalrohlings markieren wir entlang seiner Mittelachse, näher an einem Ende, die Grenzen des Schlitzes, entlang dem sich die bewegliche Backe unseres Schraubstocks bewegen wird. Markieren Sie die markierten Punkte und bohren Sie Löcher, die die Enden des Schlitzes bilden.
Mit einer Schleifmaschine schneiden wir im Kanalsteg zwischen diesen beiden Löchern einen Metallstreifen aus und schlagen ihn mit dem spitz zulaufenden Hammerkopf heraus. Dieser Schlitz legt die Bewegungsgrenzen der beweglichen Backe des Schraubstocks fest.
Mit einer Schleifmaschine schneiden wir aus einem geeigneten Metallstreifen zwei Stücke, deren Länge der Breite des Eckregals entspricht. Sie dienen als Begrenzer für die Bewegung der beweglichen Backe entlang des Schlitzes.
Als nächstes verbinden wir den Winkel und den Kanal mit einer Schraube und einer Mutter in der Position, die sie im fertigen Schraubstock einnehmen werden.
Wir spannen diese Struktur in einen Schraubstock und schweißen auf beiden Seiten des Kanals Begrenzer quer an die Ecke und halten sie mit einer Zange fest. Um ein versehentliches Verschweißen mit den Kanalflanschen zu vermeiden, legen wir beim Schweißen ein dünnes Stück Gummi, Kunststoff oder anderes dielektrisches Material dazwischen.
Dann schneiden wir aus einem gebrauchten Hammer mit rundem Kopf mit einem Schleifer einen zylindrischen Rohling ab, dessen Höhe ungefähr dem Durchmesser entspricht – der Rohling für die zukünftige Exzenterklemme.
Wir markieren an seinem Ende einen Punkt mit einer gewissen Exzentrizität – einer Vertiefung gegenüber der Mittellängsachse des Zylinders. Anhand der Markierung bohren wir ein Durchgangsloch parallel zur Achse unseres Werkstücks.
Aus einem dicken Metallstreifen schneiden wir nach dem Markieren zwei Stücke mit Länge und Höhe aus, die dem Regal des gleichen Flanschwinkels entsprechen. Dies sind zukünftige Backenauflagen für Schnellspannschraubstöcke.
Wir bohren zwei Löcher in diese Pads in der Mitte, näher an den Kanten. Wir klappen sie von der Vorderseite unter den Köpfen der Befestigungsschrauben auf. Mit einer Mühle machen wir eine Kerbe und reinigen sie. Wir testen die Qualität der Befestigung der Beläge an den Eckflanschen (Backen) mit zwei Schrauben und Muttern.
Eine Ecke (Festbacke) schweißen wir quer zum Kanalsteg auf der dem Schlitz gegenüberliegenden Seite an. Wir montieren die Pads wieder an den festen und beweglichen Backen und schrauben sie schließlich mit einem Schraubenschlüssel und einem Schraubendreher fest.
Aus ziemlich dickem Metall schneiden wir einen Streifen aus, dessen Größe der Länge der Ecke und der Breite dem Abstand zwischen den Enden der Regale diagonal entspricht. Wir schweißen es auch, um die Festigkeit und Steifigkeit der festen Backe zu gewährleisten.
Nun nehmen wir einen dickeren Metallstreifen, bohren an einem Ende ein Loch und schneiden mit einem Gewindebohrer ein Gewinde hinein. Dann schneiden wir davon ein Stück mit einem rechteckigen Gewindeloch ab, das sich etwas vom Quadrat unterscheidet.
Diese selbstgemachte rechteckige Mutter hält den Exzenter an der beweglichen Backe und ermöglicht es ihm, sich entlang des Kanalstegs (Führung) in die eine oder andere Richtung zu bewegen.
Um zu verhindern, dass sich die Mutter unter der Kanalbrücke dreht, schneiden wir auf beiden Seiten davon zwei Begrenzungsführungsstangen in Längsrichtung entlang des gesamten Schlitzes mit einem kleinen Spalt ab und schweißen sie an.
Im Exzenter an der Seite, etwa in der Mitte seiner Höhe, bohren wir Sackloch und schneiden Sie einen Faden hinein, um den Griff zu montieren.
Wir montieren die bewegliche Backe des Schraubstocks mit vorgeschweißten Anschlägen und schrauben die fertige Abdeckung mit Kerben mit zwei Schrauben an der Ecke fest.
Wir finden ein Stück Eisenblech mit ausreichender Dicke, um die Steifigkeit zu gewährleisten. Wir markieren darauf die Konturen einer achteckigen Basis mit zwei Markierungen für Löcher zur Befestigung. Mit einer Mühle schneiden wir es aus.
Daran schweißen wir einen Kanal (Führung) mit fester Backe. Wir bearbeiten Schweißnähte und Oberflächen mit einer Schleifmaschine, um Rost, Metallablagerungen, Rauheiten und Kantenverrundungen zu entfernen.
Die Schwammauflage und den Längsschlitz mit seitlichem Rand verschließen wir mit Bauklebeband.
Mit ihrer Hilfe können Sie mit einer Bewegung des Exzentergriffs jedes Werkstück schnell, zuverlässig und ohne Zeitaufwand darin befestigen extra Aufwand.
Anmerkungen am Ende
Da Sie mit einem Winkelschleifer arbeiten müssen, Schweißgerät, Bohrmaschine, dann ist es notwendig, persönliche Schutzausrüstung zu verwenden, mindestens eine Schutzbrille als Augenschutz und Handschuhe für die Hände.Damit die beweglichen Teile des Exzenterspanners klemmfrei arbeiten, können sie von Zeit zu Zeit mit Graphitfett geschmiert werden und der Exzenterhebel kann bequem mit einem Holzgriff ausgestattet werden.
Der Exzenterspanner ist ein weiterentwickeltes Spannelement. Exzenterspanner (ECC) werden zum direkten Spannen von Werkstücken und in komplexen Spannsystemen eingesetzt.
Manuelle Schraubzwingen sind einfach im Aufbau, haben aber einen erheblichen Nachteil: Um das Teil zu sichern, muss der Arbeiter etwas tun große Menge Rotationsbewegungen Schlüssel, der zusätzlichen Zeit- und Arbeitsaufwand erfordert und dadurch die Arbeitsproduktivität verringert.
Die oben genannten Überlegungen zwingen dazu, manuelle Schraubzwingen nach Möglichkeit durch Schnellspannzwingen zu ersetzen.
Am weitesten verbreitet sind auch.
Obwohl es schnell ist, liefert es nicht große Stärke Spannen des Teils, daher kommt es nur bei relativ geringen Schnittkräften zum Einsatz.
Vorteile:
- Einfachheit und Kompaktheit des Designs;
- weit verbreitete Verwendung standardisierter Teile im Design;
- einfache Einrichtung;
- Fähigkeit zur Selbstbremsung;
- Geschwindigkeit (Ansprechzeit des Laufwerks beträgt etwa 0,04 Minuten).
Mängel:
- die konzentrierte Natur der Kräfte, die den Einsatz exzentrischer Mechanismen zur Sicherung nicht starrer Werkstücke nicht zulässt;
- die Spannkräfte bei runden Exzenternocken sind instabil und hängen stark von der Größe der Werkstücke ab;
- verminderte Zuverlässigkeit durch starken Verschleiß der Exzenternocken.
Reis. 113. Exzenterspanner: a – das Teil ist nicht gespannt; b - Position mit eingespanntem Teil
Exzentrisches Klemmdesign
Der runde Exzenter 1, eine Scheibe mit einem gegenüber der Mitte versetzten Loch, ist in Abb. dargestellt. 113, a. Der Exzenter ist frei auf der Achse 2 montiert und kann um diese rotieren. Der Abstand e zwischen dem Mittelpunkt C der Scheibe 1 und dem Mittelpunkt O der Achse wird Exzentrizität genannt.
Am Exzenter ist ein Griff 3 befestigt, durch dessen Drehung das Teil am Punkt A festgeklemmt wird (Abb. 113, b). Aus dieser Abbildung ist ersichtlich, dass der Exzenter wie ein gebogener Keil wirkt (siehe schattierter Bereich). Um zu verhindern, dass sich die Exzenter nach dem Spannen wegbewegen, müssen sie selbstbremsend sein. Die selbstbremsende Eigenschaft der Exzenter ist gewährleistet die richtige Entscheidung das Verhältnis des Durchmessers D des Exzenters zu seiner Exzentrizität e. Das Verhältnis D/e wird als Kennlinie des Exzenters bezeichnet.
Bei einem Reibungskoeffizienten f = 0,1 (Reibungswinkel 5°43") sollte die Exzenterkennlinie D/e ≥ 20 und bei einem Reibungskoeffizienten f = 0,15 (Reibungswinkel 8°30") D/e ≥ 14 betragen.
So verfügen alle Exzenterspanner, deren Durchmesser D 14-mal größer ist als die Exzentrizität e, über die Eigenschaft der Selbstbremsung, d. h. sie sorgen für eine zuverlässige Klemmung.
Abbildung 5.5 – Schemata zur Berechnung exzentrischer Nocken: a – rund, nicht standardmäßig; b- hergestellt nach der Archimedes-Spirale.
Exzentrische Spannmechanismen umfassen Exzenternocken, Halterungen dafür, Zapfen, Griffe und andere Elemente. Es gibt drei Arten von Exzenterbacken: rund und zylindrisch Arbeitsfläche; gekrümmt, deren Arbeitsflächen entlang einer archimedischen Spirale (seltener - entlang einer Evolventen- oder logarithmischen Spirale) umrissen sind; Ende
Runde Exzenter
Aufgrund der einfachen Herstellung sind runde Exzenter am weitesten verbreitet.
Ein runder Exzenter (gemäß Abbildung 5.5a) ist eine Scheibe oder Walze, die um eine Achse gedreht wird, die gegenüber der geometrischen Achse des Exzenters um einen Betrag A, Exzentrizität genannt, verschoben ist.
Gekrümmte Exzenternocken (gemäß Abbildung 5.5b) sorgen im Vergleich zu runden für eine stabile Spannkraft und einen größeren Drehwinkel (bis zu 150°).
Nockenmaterialien
Exzenternocken bestehen aus 20X-Stahl, sind auf eine Tiefe von 0,8 bis 1,2 mm aufgekohlt und auf eine Härte von HRCe 55–61 gehärtet.
Exzenterbacken werden wie folgt unterschieden: Entwürfe: Rundexzenter (GOST 9061-68), Exzenter (GOST 12189-66), Doppelexzenter (GOST 12190-66), Gabelexzenter (GOST 12191-66), Doppelexzenter (GOST 12468-67).
Der praktische Einsatz von Exzentermechanismen in verschiedenen Spannvorrichtungen ist in Abbildung 5.7 dargestellt
Abbildung 5.7 – Arten von exzentrischen Spannmechanismen
Berechnung von Exzenterspannern
Die Ausgangsdaten zur Bestimmung der geometrischen Parameter der Exzenter sind: Toleranz δ der Werkstückgröße von der Montagebasis bis zum Angriffsort der Spannkraft; Winkel a der Drehung des Exzenters aus der Nullposition (Anfangsposition); erforderliche Kraft FZ zum Spannen des Teils. Die wichtigsten Konstruktionsparameter von Exzentern sind: Exzentrizität A; Durchmesser dc und Breite b des Exzenterzapfens (Achse); Außendurchmesser exzentrisch D; Breite des Arbeitsteils des Exzenters B.
Berechnungen exzentrischer Spannmechanismen werden in der folgenden Reihenfolge durchgeführt:
Berechnung von Klemmen mit einer standardmäßigen exzentrischen runden Nocke (GOST 9061-68)
1. Bestimmen Sie den Umzug HZu Exzenternocke, mm:
Wenn der Drehwinkel des Exzenters nicht begrenzt ist (a ≤ 130°), dann
wobei δ die Toleranz der Werkstückgröße in Spannrichtung ist, mm;
Dgar = 0,2…0,4 mm – garantierter Abstand zum bequemen Ein- und Ausbau des Werkstücks;
J = 9800…19600 kN/m – Steifigkeit des exzentrischen EZM;
D = 0,4...0,6 hk mm – Gangreserve unter Berücksichtigung von Verschleiß und Herstellungsfehlern des Exzenternockens.
Wenn der Drehwinkel des Exzenters begrenzt ist (a ≤ 60°), dann
2. Wählen Sie anhand der Tabellen 5.5 und 5.6 einen Standard-Exzenternocken aus. In diesem Fall müssen folgende Bedingungen erfüllt sein: Fz ≤ FH max und HZu≤ H(Abmessungen, Material, Wärmebehandlung und andere technische Bedingungen gemäß GOST 9061-68. Es ist nicht erforderlich, die Festigkeit des Standard-Exzenternockens zu testen.
Tabelle 5.5 – Standard-Rundexzenter-Nocken (GOST 9061-68)
Bezeichnung | Äußere Exzenter Nocke, mm | Exzentrizität, | Nockenhub h, mm, nicht weniger | |||
Drehwinkel begrenzt auf a≤60° | Drehwinkel begrenzt auf a≤130° |
|||||
Hinweis: Für die Exzenterzapfen 7013-0171...1013-0178 werden die Werte von F3 max und Mmax anhand des Festigkeitsparameters berechnet, im Übrigen unter Berücksichtigung ergonomischer Anforderungen mit einer maximalen Grifflänge von L = 320 mm. |
3. Bestimmen Sie die Länge des Exzentermechanismusgriffs, mm
Werte M max und P z max werden gemäß Tabelle 5.5 ausgewählt.
Tabelle 5.6 – Runde Exzenternocken (GOST 9061-68). Abmessungen, mm
Zeichnung - Zeichnung einer Exzenterkurve
DIY Exzenterklemme
Das Video zeigt Ihnen, wie Sie eine hausgemachte Exzenterklemme zum Fixieren eines Werkstücks herstellen. Exzenterklemme zum Selbermachen.
/ 13.06.2019
DIY Exzenterklemme aus Metall. Exzenterspanner
Exzenterspanner sind einfach herzustellen und werden daher häufig in Werkzeugmaschinen eingesetzt. Durch den Einsatz von Exzenterspannern kann die Zeit zum Spannen eines Werkstücks deutlich verkürzt werden, allerdings ist die Spannkraft geringer als bei Gewindespannern.
Exzenterspanner werden in Kombination mit und ohne Spanner hergestellt.
Betrachten Sie eine Exzenterklemme mit Klemme.
Exzenterspanner können bei erheblichen Toleranzabweichungen (±δ) des Werkstücks nicht arbeiten. Bei großen Toleranzabweichungen muss die Klemme ständig mit Schraube 1 nachjustiert werden.
Exzentrische Berechnung |
Die zur Herstellung des Exzenters verwendeten Materialien sind U7A, U8A Mit Wärmebehandlung bis HR von 50...55 Einheiten, Stahl 20X mit Aufkohlung bis zu einer Tiefe von 0,8...1,2 mit Härten HR von 55...60 Einheiten.
Schauen wir uns das exzentrische Diagramm an. Die KN-Linie teilt den Exzenter in zwei Teile? symmetrische Hälften, die sozusagen bestehen aus 2x Auf den „Anfangskreis“ aufgeschraubte Keile.
Die exzentrische Rotationsachse ist gegenüber ihrer geometrischen Achse um den Betrag der Exzentrizität „e“ verschoben.
Der Abschnitt Nm des unteren Keils wird üblicherweise zum Spannen verwendet.
Betrachtet man den Mechanismus als eine Kombination bestehend aus einem Hebel L und einem Keil mit Reibung an zwei Flächen auf der Achse und dem Punkt „m“ (Klemmpunkt), erhält man eine Kraftbeziehung zur Berechnung der Klemmkraft.
wobei Q die Klemmkraft ist
P – Kraft auf den Griff
L – Griffschulter
r – Abstand von der exzentrischen Rotationsachse zum Kontaktpunkt Mit
Werkstück
α - Anstiegswinkel der Kurve
α 1 - Reibungswinkel zwischen Exzenter und Werkstück
α 2 - Reibungswinkel auf der Exzenterachse
Um ein Weglaufen des Exzenters während des Betriebs zu vermeiden, ist es notwendig, den Zustand der Selbstbremsung des Exzenters zu beachten
wobei α -
Gleitreibungswinkel am Kontaktpunkt mit dem Werkstück ø -
Reibungskoeffizient
Betrachten Sie für ungefähre Berechnungen von Q - 12P das Diagramm einer doppelseitigen Klemme mit Exzenter
|
Keilklemmen
Keilspannvorrichtungen werden häufig in Werkzeugmaschinen eingesetzt. Ihr Hauptelement sind ein-, zwei- und dreikeile. Der Einsatz solcher Elemente beruht auf der Einfachheit und Kompaktheit der Konstruktionen, der Schnelligkeit und Zuverlässigkeit im Betrieb, der Möglichkeit, sie beispielsweise als Spannelement, das direkt auf das zu fixierende Werkstück einwirkt, und als Zwischenglied zu verwenden. eine Verstärkerverbindung in anderen Spannvorrichtungen. Typischerweise werden selbstbremsende Keile verwendet. Die Bedingung für die Selbstbremsung eines einfach abgeschrägten Keils wird durch die Abhängigkeit ausgedrückt
α > 2ρ
Wo α - Keilwinkel
ρ - der Reibungswinkel auf den Kontaktflächen G und H zwischen dem Keil und den Gegenteilen.
Im Winkel α ist die Selbstbremsung gewährleistet = 12° Um jedoch zu verhindern, dass Vibrationen und Lastschwankungen beim Einsatz der Zwinge das Werkstück schwächen, werden häufig Keile mit einem Winkel α verwendet.
Aufgrund der Tatsache, dass eine Verringerung des Winkels zu einer Vergrößerung führt
Aufgrund der selbstbremsenden Eigenschaften des Keils ist es bei der Auslegung des Antriebs des Keilmechanismus erforderlich, Vorrichtungen vorzusehen, die das Entfernen des Keils aus dem Arbeitszustand erleichtern, da das Lösen eines belasteten Keils schwieriger ist, als ihn in den Arbeitszustand zu bringen.
Dies kann durch die Verbindung der Betätigungsstange mit einem Keil erreicht werden. Wenn sich die Stange 1 nach links bewegt, passiert sie den Weg „1“ in den Leerlauf und drückt dann beim Auftreffen auf den Stift 2, der in den Keil 3 gedrückt wird, diesen heraus. Wenn sich die Stange zurückbewegt, drückt sie durch Auftreffen auf den Stift auch den Keil in die Arbeitsposition. Dies sollte in Fällen berücksichtigt werden, in denen der Keilmechanismus durch einen pneumatischen oder hydraulischen Antrieb angetrieben wird. Um einen zuverlässigen Betrieb des Mechanismus zu gewährleisten, sollten dann auf verschiedenen Seiten des Antriebskolbens unterschiedliche Flüssigkeits- oder Druckluftdrücke erzeugt werden. Dieser Unterschied bei der Verwendung von pneumatischen Antrieben kann durch den Einsatz eines Druckminderventils in einem der Rohre erreicht werden, die den Zylinder mit Luft oder Flüssigkeit versorgen. In Fällen, in denen keine Selbstbremsung erforderlich ist, empfiehlt es sich, Rollen an den Kontaktflächen des Keils mit den Gegenstücken der Vorrichtung zu verwenden, um das Einsetzen des Keils in seine ursprüngliche Position zu erleichtern. In diesen Fällen ist es notwendig, den Keil zu verriegeln.
Für große Produktionsprogramme werden häufig Schnellspannklemmen verwendet. Eine Art solcher Handspanner sind Exzenterspanner, bei denen Spannkräfte durch Drehen der Exzenter erzeugt werden.
Erhebliche Kräfte bei einer kleinen Kontaktfläche der Arbeitsfläche des Exzenters können zu Schäden an der Oberfläche des Teils führen. Daher wirkt der Exzenter normalerweise über die Auskleidung, Drücker, Hebel oder Stangen auf das Teil.
Spannexzenter können unterschiedliche Arbeitsflächenprofile haben: in Form eines Kreises (Rundexzenter) und mit Spiralprofil (in Form einer logarithmischen oder archimedischen Spirale).
Ein runder Exzenter ist ein Zylinder (Rolle oder Nocke), dessen Achse exzentrisch zur Drehachse liegt (Abb. 176, a, b). Solche Exzenter sind am einfachsten herzustellen. Zum Drehen des Exzenters dient ein Griff. Exzenterspanner werden häufig in Form von Kurbelwellen mit einer oder zwei Stützen hergestellt.
Exzenterspanner sind immer manuell, daher die Hauptbedingung ordnungsgemäße Bedienung Ihr Zweck besteht darin, die Winkelposition des Exzenters nach dem Drehen zum Spannen beizubehalten – „Selbstbremsung des Exzenters“. Diese Eigenschaft des Exzenters wird durch das Verhältnis des Durchmessers O der zylindrischen Arbeitsfläche zur Exzentrizität e bestimmt. Dieses Verhältnis wird als Exzentercharakteristik bezeichnet. Ab einer bestimmten Übersetzung ist die Bedingung für eine Selbstbremsung des Exzenters erfüllt.
Typischerweise wird der Durchmesser B eines runden Exzenters aus Konstruktionsgründen festgelegt und die Exzentrizität e auf Grundlage der Selbstbremsbedingungen berechnet.
Die Symmetrielinie des Exzenters teilt ihn in zwei Teile. Man kann sich zwei Keile vorstellen, von denen einer das Teil beim Drehen des Exzenters sichert. Die Position des Exzenters, wenn er mit der Oberfläche eines Teils minimaler Größe in Kontakt kommt.
Typischerweise wird die Position des an der Arbeit beteiligten Abschnitts des Exzenterprofils wie folgt gewählt. so dass bei horizontaler Lage der Linien 0\02 der Exzenter die eingespannte mittelgroße Fliege mit dem Punkt c2 berühren würde. Beim Spannen von Teilen mit maximaler und Mindestgrößen Die Teile berühren jeweils die Punkte cI und c3 des Exzenters, die symmetrisch relativ zum Punkt c2 liegen. Dann ist das aktive Profil des Exzenters der Bogen C1C3. In diesem Fall kann der Teil des Exzenters, der in der Abbildung durch die gestrichelte Linie begrenzt ist, entfernt werden (in diesem Fall muss der Griff an eine andere Stelle verschoben werden).
Der Winkel a zwischen der aufgespannten Fläche und der Normalen des Rotationsradius wird Elevationswinkel genannt. Dies ist für verschiedene Winkelpositionen des Exzenters unterschiedlich. Aus dem Scan geht hervor, dass der Winkel a gleich Null ist, wenn das Teil und der Exzenter die Punkte a und B berühren. Sein Wert ist am größten, wenn der Exzenter den Punkt c2 berührt. Bei kleinen Keilwinkeln ist ein Verklemmen möglich, bei großen Winkeln ist ein spontanes Lösen möglich. Daher ist ein Klemmen, wenn die Exzenterpunkte a und b das Teil berühren, unerwünscht. Für eine ruhige und zuverlässige Befestigung des Teils ist es erforderlich, dass der Exzenter im Abschnitt C\C3 mit dem Teil in Kontakt kommt, wenn der Winkel a ungleich Null ist und nicht in weiten Grenzen schwanken kann.
Eine Kreissäge ist aus einer Schreinerei nicht mehr wegzudenken, denn der einfachste und häufigste Arbeitsschritt ist das Längssägen von Werkstücken. In diesem Artikel wird erläutert, wie man eine selbstgemachte Kreissäge herstellt.
Einführung
Die Maschine besteht aus drei Hauptstrukturelementen:
- Base;
- Sägetisch;
- Parallelanschlag.
Die Basis und der Sägetisch selbst sind nicht sehr kompliziert Strukturelemente. Ihr Design ist offensichtlich und nicht so kompliziert. Daher betrachten wir in diesem Artikel das komplexeste Element – den Parallelanschlag.
Der Parallelanschlag ist also ein bewegliches Teil der Maschine, das als Führung für das Werkstück dient und entlang dessen sich das Werkstück bewegt. Dementsprechend hängt die Schnittqualität vom Parallelanschlag ab, denn wenn der Anschlag nicht parallel ist, kann es zu einem Verklemmen des Werkstücks oder des Sägeblatts kommen.
Darüber hinaus muss der Parallelanschlag einer Kreissäge eine recht steife Konstruktion haben, da der Meister versucht, das Werkstück gegen den Anschlag zu drücken, und wenn der Anschlag verschoben wird, führt dies zu einer Nichtparallelität mit den oben genannten Folgen .
Existieren verschiedene Designs Parallelanschläge abhängig von der Art der Befestigung am Rundtisch. Hier ist eine Tabelle mit den Eigenschaften dieser Optionen.
Parallelzaun-Design | Vorteile und Nachteile |
Zweipunktmontage (vorne und hinten) | Vorteile:· Ziemlich steifes Design. · Ermöglicht die Platzierung des Anschlags an einer beliebigen Stelle auf dem Rundtisch (links oder rechts vom Sägeblatt); Erfordert nicht die Massivität der Führung selbst Mangel:· Um es zu befestigen, muss der Meister ein Ende vor der Maschine festklemmen, außerdem um die Maschine herumgehen und das gegenüberliegende Ende am Anschlag befestigen. Dies ist bei der Wahl der gewünschten Position des Anschlags sehr umständlich und bei häufigem Nachjustieren ein erheblicher Nachteil. |
Einpunktmontage (vorne) | Vorteile:· Weniger starre Konstruktion als bei der Anbringung des Anschlags an zwei Punkten. · Ermöglicht die Platzierung des Anschlags an einer beliebigen Stelle auf dem Rundtisch (links oder rechts vom Sägeblatt); · Um die Position des Anschlags zu ändern, genügt es, ihn auf einer Seite der Maschine zu befestigen, wo sich der Master während des Sägevorgangs befindet. Mangel:· Der Anschlag muss massiv ausgeführt sein, um die erforderliche Steifigkeit der Konstruktion zu gewährleisten. |
Befestigung in der Nut eines Rundtisches | Vorteile:· Schnelle Umstellung. Mangel:· Komplexität des Designs, · Schwächung der kreisförmigen Tischstruktur, · Feste Position gegenüber der Linie des Sägeblatts, · Ziemlich komplexes Design für selbstgemacht, insbesondere aus Holz (nur aus Metall). |
In diesem Artikel untersuchen wir die Möglichkeit, eine Parallelanschlagkonstruktion für eine Kreissäge mit einem Befestigungspunkt zu erstellen.
Vorbereitung auf die Arbeit
Bevor Sie beginnen, müssen Sie sich für die notwendigen Werkzeuge und Materialien entscheiden, die während des Arbeitsprozesses benötigt werden.
Für die Arbeit werden folgende Werkzeuge verwendet:
- Kreissäge oder Kreissäge können verwendet werden.
- Schraubendreher.
- Schleifer (Winkelschleifer).
- Handwerkzeuge: Hammer, Bleistift, Winkel.
Während der Arbeit benötigen Sie außerdem folgende Materialien:
- Sperrholz.
- Massive Kiefer.
- Stahlrohr mit einem Innendurchmesser von 6-10 mm.
- Stahlstab mit einem Außendurchmesser von 6-10 mm.
- Zwei Unterlegscheiben mit vergrößerter Fläche und einem Innendurchmesser von 6-10 mm.
- Selbstschneidende Schrauben.
- Holzkleber.
Entwurf eines Kreissägenanschlags
Die gesamte Struktur besteht aus zwei Hauptteilen – längs und quer (also relativ zur Ebene des Sägeblatts). Jedes dieser Teile ist fest mit dem anderen verbunden und stellt eine komplexe Struktur dar, die aus mehreren Teilen besteht.
Die Anpresskraft ist groß genug, um die Festigkeit der Struktur zu gewährleisten und den gesamten Parallelanschlag sicher zu fixieren.
Aus einem anderen Blickwinkel.
Die allgemeine Zusammensetzung aller Teile ist wie folgt:
- Die Basis des Querteils;
- Längsteil
- , 2 Stk.);
- Die Basis des Längsteils;
- Klemme
- Exzentrischer Griff
Eine Kreissäge herstellen
Vorbereitung der Rohlinge
Ein paar Punkte, die Sie beachten sollten:
- Flache Längselemente bestehen aus massivem Kiefernholz und nicht wie andere Teile.
Am Ende bohren wir ein 22 mm großes Loch für den Griff.
Dies geschieht am besten durch Bohren, Sie können es aber auch einfach mit einem Nagel einschlagen.
Die für die Arbeit verwendete Kreissäge verwendet einen selbstgebauten beweglichen Schlitten aus (oder optional können Sie einen falschen Tisch zusammenbauen), der nicht zu schlecht ist, um sich zu verformen oder zu beschädigen. Wir schlagen an der markierten Stelle einen Nagel in diesen Wagen und beißen den Kopf ab.
Als Ergebnis erhalten wir ein glattes zylindrisches Werkstück, das mit einem Band- oder Exzenterschleifer bearbeitet werden muss.
Wir stellen einen Griff her – es ist ein Zylinder mit einem Durchmesser von 22 mm und einer Länge von 120–200 mm. Dann kleben wir es in den Exzenter.
Querteil der Führung
Beginnen wir mit der Herstellung des Querteils der Führung. Es besteht, wie oben erwähnt, aus folgenden Details:
- Die Basis des Querteils;
- Obere Querklemmstange (mit schrägem Ende);
- Untere Querklemmstange (mit schrägem Ende);
- Endstreifen (Befestigungsstreifen) des Querteils.
Obere Querklemmleiste
Beide Klemmleisten – die obere und die untere – haben ein Ende, das nicht gerade im 90°-Winkel, sondern im Winkel von 26,5° (genauer gesagt 63,5°) geneigt („schräg“) ist. Diese Winkel haben wir bereits beim Schneiden der Werkstücke beobachtet.
Die obere Querklemmleiste dient dazu, sich entlang der Basis zu bewegen und die Führung durch Drücken gegen die untere Querklemmleiste weiter zu fixieren. Es wird aus zwei Rohlingen zusammengesetzt.
Beide Klemmleisten sind fertig. Es ist notwendig, die Laufruhe zu überprüfen und alle Mängel zu beseitigen, die das reibungslose Gleiten beeinträchtigen; außerdem müssen Sie die Dichtheit der geneigten Kanten überprüfen; Es dürfen keine Lücken oder Risse vorhanden sein.
Bei festem Sitz ist die Festigkeit der Verbindung (Fixierung der Führung) maximal.
Zusammenbau des gesamten Querteils
Längsteil der Führung
Der gesamte Längsteil besteht aus:
- , 2 Stk.);
- Die Basis des Längsteils.
Dieses Element wird dadurch hergestellt, dass die Oberfläche laminiert und glatter ist – dies verringert die Reibung (verbessert das Gleiten) und ist außerdem dichter und fester – langlebiger.
Bei der Umformung der Rohlinge haben wir diese bereits zugesägt, es müssen nur noch die Kanten verfeinert werden. Dies geschieht mit Kantenband.
Die Kantentechnik ist einfach (man kann sie sogar mit einem Bügeleisen kleben!) und verständlich.
Die Basis des Längsteils
Wir befestigen es zusätzlich mit selbstschneidenden Schrauben. Vergessen Sie nicht, einen 90°-Winkel zwischen den Längs- und Vertikalelementen einzuhalten.
Montage von Quer- und Längsteilen.
Genau hier SEHR!!! Es ist wichtig, einen Winkel von 90° einzuhalten, da davon die Parallelität der Führung zur Ebene des Sägeblattes abhängt.
Einbau des Exzenters
Anleitung installieren
Es ist Zeit, unsere gesamte Struktur zu sichern Kreissäge. Dazu müssen Sie die Queranschlagstange am Rundtisch befestigen. Die Befestigung erfolgt wie auch anderswo mit Leim und selbstschneidenden Schrauben.
... und wir betrachten die Arbeit als erledigt – die Kreissäge ist mit Ihren eigenen Händen fertig.
Video
Video, auf dem dieses Material erstellt wurde.
Die Geräte verwenden zwei Arten von Exzentermechanismen:
1. Kreisexzenter.
2. Krummlinige Exzentriker.
Die Art des Exzenters wird durch die Kurvenform im Arbeitsbereich bestimmt.
Arbeitsfläche kreisförmige Exzenter– ein Kreis mit konstantem Durchmesser und verschobener Rotationsachse. Der Abstand zwischen dem Mittelpunkt des Kreises und der Drehachse des Exzenters wird als Exzentrizität bezeichnet ( e).
Betrachten wir das Diagramm eines Kreisexzenters (Abb. 5.19). Linie, die durch den Mittelpunkt eines Kreises verläuft UM 1 und Drehpunkt UM 2 kreisförmige Exzenter, teilen Sie es in zwei symmetrische Abschnitte. Jeder von ihnen ist ein Keil, der sich auf einem Kreis befindet, der vom Drehzentrum des Exzenters aus beschrieben wird. Der exzentrische Hubwinkel α (der Winkel zwischen der aufgespannten Fläche und der Normalen des Rotationsradius) bildet den Radius des exzentrischen Kreises R und Rotationsradius R, gezeichnet von ihren Mittelpunkten bis zum Kontaktpunkt mit dem Teil.
Der Höhenwinkel der exzentrischen Arbeitsfläche wird durch die Beziehung bestimmt
Exzentrizität; - Drehwinkel des Exzenters.
Abbildung 5.19 – Berechnungsschema Exzenter
Wo ist der Spalt zum freien Einführen des Werkstücks unter dem Exzenter ( S 1= 0,2...0,4 mm); T - Werkstückgrößentoleranz in Spannrichtung; - exzentrische Gangreserve, die es vor dem Durchlaufen des Totpunkts schützt (= 0,4...0,6 mm); j– Verformung in der Kontaktzone;
wobei Q die Kraft am Kontaktpunkt des Exzenters ist; - Steifigkeit der Spannvorrichtung,
Zu den Nachteilen kreisförmiger Exzenter gehört die Änderung des Höhenwinkels α beim Drehen des Exzenters (und damit der Spannkraft). Abbildung 5.20 zeigt das Entwicklungsprofil der Arbeitsfläche des Exzenters, wenn dieser um einen Winkel gedreht wird ρ . IN Erstphase bei ρ = 0° Elevationswinkel α = 0°. Bei weiterer Drehung des Exzenters vergrößert sich der Winkel α steigt und erreicht ein Maximum (α Max) bei ρ = 90°. Eine weitere Drehung führt zu einer Winkelverkleinerung α , und bei ρ = 180° ist der Elevationswinkel wieder Null α =0°
Reis. 5.20 – Exzenter reiben.
Die Kräftegleichungen in einem kreisförmigen Exzenter können mit ausreichender Genauigkeit für praktische Berechnungen geschrieben werden, analog zur Berechnung der Kräfte eines flachen Keils mit einer einzigen Abschrägung und einem Winkel am Kontaktpunkt. Dann lässt sich mit der Formel die Kraft auf die Länge des Griffs ermitteln
Wo l– Abstand von der exzentrischen Rotationsachse zum Kraftangriffspunkt W; R– Abstand von der Drehachse zum Berührungspunkt ( Q); - Reibungswinkel zwischen Exzenter und Werkstück; - Reibungswinkel auf der exzentrischen Rotationsachse.
Die Selbstbremsung des Kreisexzenters ist im Verhältnis zu seinem Außendurchmesser gewährleistet D zur Exzentrizität. Dieses Verhältnis wird als Exzenterkennlinie bezeichnet.
Runde Exzenter werden aus 20X-Stahl hergestellt, bis zu einer Tiefe von 0,8...1,2 mm verkittet und anschließend auf eine Härte von HRC 55...60 gehärtet. Die Abmessungen des runden Exzenters müssen unter Berücksichtigung von GOST 9061-68 und GOST 12189-66 verwendet werden. Standard-Rundexzenter haben die Abmessungen D = 32–80 mm und e = 1,7–3,5 mm. Zu den Nachteilen von Kreisexzentern zählen ein kleiner Linearhub, eine Unbeständigkeit des Hubwinkels und damit der Spannkraft beim Spannen von Werkstücken mit großen Größenschwankungen in Spannrichtung.
Abbildung 5.21 zeigt einen normierten Exzenterspanner zum Spannen von Teilen. Das Werkstück 3 ist auf festen Trägern 2 montiert und wird durch eine Stange 4 gegen diese gedrückt. Beim Spannen des Werkstücks wird eine Kraft auf den Exzentergriff 6 ausgeübt W, und es dreht sich um seine Achse und ruht auf der Ferse 7. Die Kraft entsteht auf der exzentrischen Achse Rüber Takt 4 an den Part übertragen.
Abbildung 5.21 – Normalisierte Exzenterklemme
Abhängig von der Größe der Leiste ( l 1 Und l 2) erhalten wir die Klemmkraft Q. Die Stange 4 wird durch eine Feder gegen den Kopf 5 der Schraube gedrückt. Der Exzenter 6 mit der Stange 4 bewegt sich nach der Freigabe des Teils nach rechts.
Gebogene Backen Sie zeichnen sich im Gegensatz zu Kreisexzentern durch einen konstanten Hubwinkel aus, der bei jedem Drehwinkel der Nocke die gleichen Selbstbremseigenschaften gewährleistet.
Die Arbeitsfläche solcher Nocken ist in Form einer logarithmischen oder archimedischen Spirale ausgeführt.
Bei einem Arbeitsprofil in Form einer logarithmischen Spirale ist der Radiusvektor der Nocke ( R) wird durch die Abhängigkeit bestimmt
p = Ce a G
Wo MIT- Konstante; e - Basis natürlicher Logarithmen; A - Proportionalitätsfaktor; G- Polarwinkel.
Wenn ein Profil entlang einer archimedischen Spirale verwendet wird, dann
p=aG .
Wenn die erste Gleichung in logarithmischer Form dargestellt wird, stellt sie wie die zweite Gleichung eine Gerade in kartesischen Koordinaten dar. Daher kann die Konstruktion von Nocken mit Arbeitsflächen in Form einer logarithmischen oder archimedischen Spirale mit ausreichender Genauigkeit durchgeführt werden, wenn einfach die Werte berücksichtigt werden R, entnommen aus dem Diagramm in kartesischen Koordinaten, abgesetzt vom Mittelpunkt des Kreises in Polarkoordinaten. In diesem Fall wird der Durchmesser des Kreises in Abhängigkeit vom erforderlichen Hubwert des Exzenters ausgewählt ( H) (Abb. 5.22).
Abbildung 5.22 – Profil einer gebogenen Nocke
Diese Exzenter bestehen aus den Stählen 35 und 45. Die äußeren Arbeitsflächen sind auf eine Härte von HRC 55...60 wärmebehandelt. Die Hauptabmessungen gebogener Exzenter wurden normalisiert.
Guten Tag an die Fans selbstgemachte Geräte. Wenn keine Laster zur Hand sind oder diese einfach nicht verfügbar sind, dann einfache Lösung Sie können etwas Ähnliches selbst zusammenbauen, da für die Montage der Klemme keine besonderen Fähigkeiten und schwer zu findenden Materialien erforderlich sind. In diesem Artikel erkläre ich Ihnen, wie Sie eine Holzklammer herstellen.
Um Ihre Klemme zusammenzubauen, müssen Sie eine starke Holzart finden, damit sie hohen Belastungen standhält. In diesem Fall eignet sich ein Eichenbrett gut.
Um mit der Herstellungsphase zu beginnen notwendig:
*Schraube, deren Größe am besten etwa 12–14 mm beträgt.
*Mutter für Schraube.
*Schleifsteine aus Eichenholz.
*Ein Teil des Profils besteht aus Holz mit einem Querschnitt von 15 mm.
*Zimmermannsleim oder Parkettleim.
*Epoxid.
*Lack, kann durch Beize ersetzt werden.
*Metallstab 3 mm.
*Bohrer mit kleinem Durchmesser.
*Meißel oder Meißel.
*Bügelsäge für Holz.
*Hammer.
*Elektrische Bohrmaschine.
*Schleifpapier mittlerer Körnung.
*Schraubstock und Klemme.
Erster Schritt. Je nach Wunsch kann die Größe der Klammer unterschiedlich gestaltet werden; in diesem Fall schneidet der Autor Blöcke mit den Maßen 3,5 x 3 x 3,5 cm – einteilig und 1,8 x 3 x 7,5 cm – zweiteilig aus.
Danach spannen wir einen 75 mm langen Block in einen Schraubstock und bohren mit einem Bohrer ein Loch, wobei wir 1–2 cm von der Kante zurücktreten.
Passen Sie als Nächstes das Loch, das Sie gerade gemacht haben, an das Loch in der Mutter an und zeichnen Sie den Umriss mit einem Bleistift nach. Schneiden Sie nach dem Markieren mit Meißel und Hammer bewaffnet einen sechseckigen Senkkopf für die Mutter aus.
Zweiter Schritt. Um die Mutter im Block zu befestigen, müssen Sie die bearbeitete Nut im Inneren mit Epoxidharz bestreichen und dort dieselbe Mutter eintauchen und sie ein wenig im Block versenken.
Normalerweise völlig trocken Epoxidharz nach 24 Stunden erreicht, danach können Sie fortfahren nächste Stufe Versammlungen.
Dritter Schritt. Der Bolzen, der idealerweise zu unserer festen Mutter im Balken passt, muss modifiziert werden; nehmen Sie dazu einen Bohrer und bohren Sie ein Loch in der Nähe seines Sechskantkopfes.
Danach gehen wir zu den Stäben über. Sie müssen so zusammengefügt werden, dass an den Seiten längere Stäbe und dazwischen ein kürzerer Stab entstehen. Bevor die drei Balken zusammengespannt werden, müssen Sie mit einem dünnen Bohrer Löcher an der Befestigungsstelle bohren, damit das Werkstück nicht splittert, da diese Anordnung für uns nicht geeignet ist.
Mit einem Schraubendreher ziehen wir die Schrauben an den vorbereiteten Bohrstellen fest, nachdem wir die Fugen zuvor mit Klebstoff bestrichen haben.
Den fast fertigen Spannmechanismus sichern wir mit einer Klammer und warten, bis der Kleber getrocknet ist. Zur bequemen Nutzung der Zwinge benötigen Sie einen Hebel, mit dem Sie Ihre Werkstücke festklemmen können; dazu dienen ein Metallstab und ein in zwei Teile gesägtes Rundholzstück mit einem Querschnitt von 15 mm; in beide Teile müssen Sie Bohren Sie ein Loch für die Stange und kleben Sie alles auf.
Die letzte Etappe. Um die Montage abzuschließen, benötigen Sie Lack oder Beize. Wir schleifen unsere selbstgemachte Klammer und beschichten sie anschließend mit mehreren Lackschichten.
An diesem Punkt ist die Herstellung Ihrer eigenen Klemme fertig und sie wird in einen betriebsbereiten Zustand versetzt, wenn der Lack vollständig getrocknet ist. Danach können Sie mit diesem Gerät mit vollem Vertrauen arbeiten.
Eine relativ kompakte Exzenterklemme, bei der es sich um eine Art Nockenmechanismus handelt, ist einfach herzustellen und hat eine hohe Verstärkung. Sie hat zweifellos einen weiteren Hauptvorteil ...
... – sofortige Leistung. Wenn es zum „Ein- und Ausschalten“ einer Schraubzwinge oft notwendig ist, mindestens ein paar Umdrehungen in die eine und dann in die andere Richtung zu machen, reicht es bei Verwendung einer Exzenterzwinge aus, den Griff nur um ein Viertel zu drehen drehen. Natürlich sind sie den Exzentern hinsichtlich Spannkraft und Arbeitshub überlegen, aber bei einer konstanten Dicke der befestigten Teile in der Massenproduktion ist der Einsatz von Exzentern äußerst komfortabel und effektiv. Der weit verbreitete Einsatz von Exzenterspannern, beispielsweise in Lagerbeständen zum Zusammenbauen und Schweißen kleiner Metallkonstruktionen und Elemente nicht standardmäßiger Ausrüstung, erhöht die Arbeitsproduktivität erheblich.
Die Arbeitsfläche der Nocke besteht meist aus einem Zylinder mit einem Kreis oder einer Archimedes-Spirale an der Basis. Weiter im Artikel wir werden redenüber die gebräuchlichere und technologisch fortschrittlichere runde Exzenterklemme.
Die Abmessungen exzentrischer runder Nocken für Werkzeugmaschinen sind in GOST 9061-68* genormt. Die Exzentrizität der runden Nocken ist in diesem Dokument auf 1/20 des Außendurchmessers eingestellt, um Selbstbremsbedingungen über den gesamten Betriebsdrehwinkelbereich bei einem Reibungskoeffizienten von 0,1 oder mehr zu gewährleisten.
Das Bild unten zeigt geometrisches Diagramm Klemmmechanismus. Durch Drehen des Exzentergriffs gegen den Uhrzeigersinn um eine gegenüber der Stütze starr fixierte Achse wird das feste Teil gegen die Auflagefläche gedrückt.
Die dargestellte Position des Mechanismus ist durch den maximal möglichen Winkel gekennzeichnet α , während die gerade Linie, die durch die Drehachse und den Mittelpunkt des exzentrischen Kreises verläuft, senkrecht zu der geraden Linie ist, die durch den Kontaktpunkt des Teils mit der Nocke und den Mittelpunkt des äußeren Kreises gezogen wird.
Wenn Sie die Nocke um 90 ° im Uhrzeigersinn relativ zu der im Diagramm gezeigten Position drehen, entsteht zwischen dem Teil und der Arbeitsfläche des Exzenters ein Spalt, dessen Größe der Exzentrizität entspricht e. Dieser Freiraum ist für den freien Ein- und Ausbau des Teils erforderlich.
Programm in MS Excel:
In dem im Screenshot gezeigten Beispiel wird anhand der angegebenen Abmessungen des Exzenters und der auf den Griff ausgeübten Kraft das Montagemaß von der Drehachse des Nockens bis zur Auflagefläche unter Berücksichtigung der Dicke des Teils ermittelt , der Selbstbremszustand wird überprüft, die Klemmkraft und der Kraftübertragungskoeffizient werden berechnet.
Der Wert des Reibungskoeffizienten „Teil – Exzenter“ entspricht dem Fall „Stahl auf Stahl ohne Schmierung“. Für die Option „Stahl auf Stahl mit Schmierung“ wird der Wert des Reibungskoeffizienten „Achse – Exzenter“ gewählt. Die Verringerung der Reibung an beiden Stellen erhöht die Leistungseffizienz des Mechanismus, die Verringerung der Reibung im Kontaktbereich zwischen dem Teil und der Nocke führt jedoch zum Verschwinden der Selbstbremsung.
Algorithmus:
9. φ 1 =arctg (f 1 )
10. φ 2 =arctg (f 2 )
11. α =arctg (2*e /D )
12. R =D/ (2*cos (α ))
13. A =s +R *cos (α )
14. e ≤ R*f 1+ (d/2)* f 2
Ist die Bedingung erfüllt, ist eine Selbstbremsung gewährleistet.
15. F = P * L * cos(α )/(R * tg(α +φ 1 )+(D /2)* tg(φ 2 ))
1 6 . k = F/P
Abschluss.
Die für die Berechnungen gewählte und im Diagramm dargestellte Position der Exzenterklemme ist im Hinblick auf Selbstbremsung und Kraftgewinn die „ungünstigste“. Aber diese Wahl ist kein Zufall. Wenn in einer solchen Arbeitsposition die berechneten Kraft- und Geometrieparameter den Konstrukteur zufriedenstellen, weist der Exzenterspanner in allen anderen Positionen einen noch größeren Kraftübertragungskoeffizienten auf bessere Konditionen selbstbremsend.
Beim Entwerfen geht es weg von der betrachteten Position hin zur Reduzierung der Größe A Wenn andere Abmessungen unverändert bleiben, verringert sich der Abstand zum Einbau des Teils.
An Größe zunehmen A kann dazu führen, dass der Exzenter während des Betriebs verschleißt und die Dicke stark schwankt S, wenn es einfach unmöglich ist, das Teil einzuspannen.
Zu den Materialien, aus denen die Nocken gefertigt werden können, wurde im Artikel bisher bewusst nichts erwähnt. GOST 9061-68 empfiehlt die Verwendung von verschleißfestem oberflächenbetoniertem Stahl 20X, um die Haltbarkeit zu erhöhen. In der Praxis wird ein Exzenterspanner jedoch je nach Verwendungszweck, Betriebsbedingungen und verfügbaren technologischen Möglichkeiten aus den unterschiedlichsten Materialien hergestellt. Mit der obigen Berechnung in Excel können Sie die Parameter von Klemmen für Nocken aus beliebigen Materialien bestimmen. Denken Sie jedoch daran, die Werte der Reibungskoeffizienten in den Ausgangsdaten zu ändern.
Wenn sich der Artikel für Sie als nützlich erwiesen hat und die Berechnung notwendig ist, können Sie die Entwicklung des Blogs unterstützen, indem Sie einen kleinen Betrag auf eine beliebige (je nach Währung) der angegebenen Wallets überweisen Internetgeld: R377458087550, E254476446136, Z246356405801.
Respekt vor der Arbeit des AutorsIch flehe herunterladen Datei mit Berechnungsprogrammnach dem Abonnement zu Artikelankündigungen im Fenster am Ende des Artikels oder im Fenster oben auf der Seite!