Silicone à base de verre liquide et d'alcool. Fabriquer des moules en silicone de vos propres mains
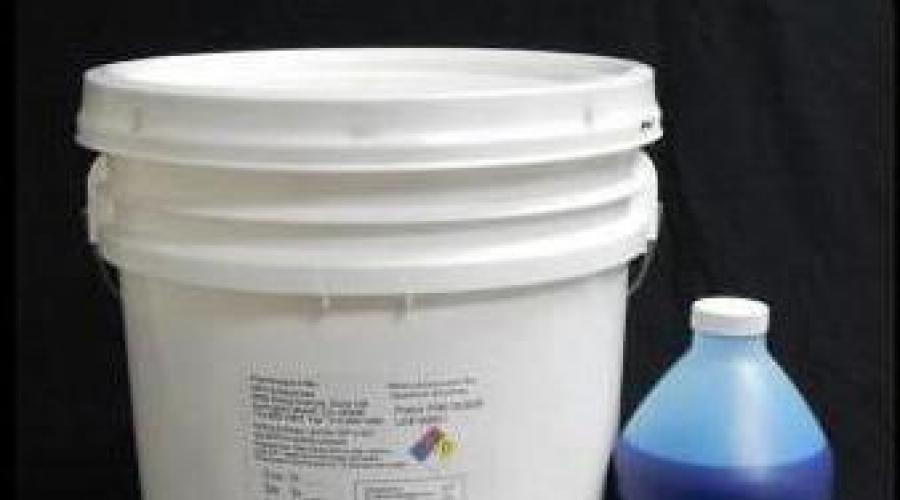
Lire aussi
Les moules en silicone sont récemment devenus extrêmement populaires. Ils sont fabriqués très simplement. Si vous le souhaitez, vous pouvez même les réaliser vous-même. Leur durée de vie est très longue par rapport, par exemple, au gypse. Cependant, bien sûr forme de haute qualité ne peut être fabriqué qu'à partir d'un matériau présentant de bonnes caractéristiques de performance. Quelles qualités doit avoir le silicone liquide pour moules et à quoi faut-il faire attention lors de son achat ?
Types de silicone et maîtres modèles
Bien entendu, lors de l'achat de matériel pour la fabrication de moules, vous devez tout d'abord faire attention à ses caractéristiques techniques. Aujourd'hui, seuls deux principaux types de silicone sont produits : l'enrobage et le remplissage.
Pour les deux matériaux, des maîtres-modèles en métal et en bois, ainsi qu'en plastique, en carton ou même simplement en papier, peuvent être utilisés dans la fabrication des formulaires.
Revêtement silicone
Cette variété est très adaptée à la confection de moules. Il s'agit d'un silicone très visqueux, appliqué sur le maître modèle avec un pinceau spécial. Un exemple d'un tel matériau est le mastic automobile résistant à la chaleur ABRO.
Silicone d'empotage
C'est aussi un bon matériau pour fabriquer des moules. Lors de son utilisation, le maître modèle est installé dans le flacon et versé par le haut. Le silicone liquide pour moules de cette variété se compose de deux composants : un durcisseur et une base. Avant de verser, ils sont soigneusement mélangés puis placés dans une chambre à vide pour éliminer les bulles d'air. Un matériau très populaire de ce type est, par exemple, le Pentelast-708S.
Facteur d'allongement
Quelles caractéristiques peuvent être considérées comme les plus importantes lors du choix d’un matériau tel que le silicone liquide ? En principe, presque toutes les variétés conviennent à la fabrication de moules. Cependant, il convient toujours de prêter attention à certains indicateurs lors de l'achat. Le paramètre le plus important caractérisant la qualité du silicone est le coefficient d'allongement. U matériaux modernes ce chiffre varie d'environ 200 à 1 300 %. Plus ce nombre est élevé, plus le silicone durci peut s'étirer et plus le nombre de moulages qu'un moule fabriqué à partir de celui-ci peut supporter est important.
Dans la pratique, on utilise généralement 700 à 800 pour cent de silicone liquide à un ou deux composants. Il est généralement idéal pour la production de moules. Les produits fabriqués à partir d'un matériau présentant ce coefficient d'allongement peuvent facilement résister jusqu'à 80 moulages. Ce chiffre peut être plus petit ou plus grand, en fonction de la complexité de la configuration du modèle maître.
Viscosité du silicone
C'est également un indicateur important qui a un impact énorme sur la qualité du formulaire fini. Le silicone liquide pour moules a une très faible viscosité. Pendant le fonctionnement, il remplit facilement les moindres recoins du maître modèle. Il est donc conseillé de l’utiliser pour la fabrication de moules de configurations très complexes.
La viscosité est mesurée en CPS. Pour les matériaux d'empotage, ce chiffre ne dépasse généralement pas 3 000 CPS. A titre de comparaison : l'eau a une viscosité de 0 CPS, huile de tournesol- 500, chérie - 10 000.
Autres indicateurs
En plus de la viscosité et du coefficient d'allongement, lors du choix du silicone, vous devez faire attention à :
Temps de travail. Plus cet indicateur est élevé, plus le matériau conserve sa viscosité longtemps.
Temps de polymérisation. Cette caractéristique est également très importante. Il montre combien de temps il faut pour que la forme coulée atteigne le facteur d'allongement indiqué.
Le silicone liquide à deux composants destiné à la fabrication de moules prend généralement plus de temps à durcir et à polymériser qu'il n'est visqueux. Cela peut être attribué aux avantages du matériau. Après tout, lorsqu'il travaille avec, le maître n'a pas besoin de se précipiter n'importe où.
Comment utiliser
Le silicone liquide est utilisé pour fabriquer les moules comme suit.
Le maître modèle est fixé au support avec une goutte de superglue et recouvert d'un agent de démoulage spécial. À la maison, il peut s'agir par exemple de vaseline ou d'huile pour machine.
Le support avec le modèle est fixé dans le flacon. Ces derniers peuvent être fabriqués à partir de presque n'importe quel matériau : bois, pâte à modeler, plastique, etc. Les flacons jetables sont en papier. Sa hauteur devrait être le double de celle de la future forme. Le fait est que pendant le processus de mise sous vide, le silicone mousse beaucoup. L'une des parois du flacon doit être amovible.
Le composé évacué est versé dans le flacon en un mince filet. Ceci est nécessaire pour garantir que le moins d'air possible pénètre dans le matériau liquide.
Le flacon est placé dans une installation sous vide pendant 1 à 2 minutes. Un traitement répété est nécessaire afin d'éliminer absolument tout l'air du silicone qui y est entré lors du versement.
La forme durcit en 5 à 6 heures environ. La polymérisation finale a lieu après un jour ou trois. Sur étape finale le formulaire est retiré du flacon et coupé en deux. Après cela, le modèle principal en est supprimé.
Moules en silicone visqueux
Dans ce cas, une technologie légèrement différente est utilisée. Le moule n’est pas utilisé dans la fabrication de moules en silicone. Le maître modèle est simplement enduit du matériau à l'aide d'un pinceau spécial en plusieurs couches (2-3 mm chacune) avec séchage intermédiaire pendant 2-3 heures.
Silicone liquide pour moules : prix
Les avantages de ce matériau ne concernent pas seulement la facilité de fabrication des moules. Il a acquis une grande popularité en raison de son faible coût. Le prix du silicone de haute qualité peut varier de seulement 450 à 750 roubles.
Dans les magasins spécialisés ou sur Internet, recherchez du silicone destiné spécifiquement à la fabrication de moules. Le fait est qu'aujourd'hui le plus différents types ce materiel. Par exemple, du silicone de pêche liquide est vendu. Il est utilisé pour lubrifier les fils tressés des engrenages, ce qui prolonge leur durée de vie et augmente la distance de lancer. Bien entendu, un tel silicone ne convient pas à la fabrication de moules.
Comment faire à la maison
Afin de fabriquer de vos propres mains du silicone liquide pour moules, vous devez acheter de l'alcool éthylique et du verre liquide. Vous aurez également besoin d'une bouteille en plastique et d'un bâton en bois. Étant donné que les composants du silicone sont des matériaux assez caustiques, vous devez porter des gants en caoutchouc épais sur vos mains. Le procédé de fabrication lui-même est le suivant :
DANS bouteille en plastique le verre liquide est versé à parts égales et éthanol.
Le mélange est soigneusement mélangé avec un bâton en bois.
Une fois qu'il a épaissi, vous devez le retirer de la bouteille et le pétrir soigneusement avec vos mains.
Le silicone ainsi préparé ressemble au plastique, au caoutchouc collant et peut prendre n'importe quelle forme.
Moules en silicone pour le four
Bien entendu, des matériaux dangereux pour l'environnement ne peuvent pas être utilisés pour fabriquer de tels moulages. Dans ce cas, le silicone liquide pour moules est fabriqué un peu différemment :
Trois cuillères à soupe de fécule de pomme de terre sont versées dans un pot de yaourt.
Ils le versent là mastic silicone dans la même quantité.
Mélangez le tout pendant dix minutes.
A partir du silicone ainsi préparé, vous pouvez facilement mouler forme simple pour la pâtisserie. Avant de verser la pâte, celle-ci doit être enduite d'huile végétale.
Utiliser des moules en silicone
Ainsi, le silicone liquide est souvent utilisé pour fabriquer des moules. L'utilisation de produits à base de matière « amidon » permet de réaliser des pâtisseries, des gâteaux, etc. originaux. Mais comment utilise-t-on des moules en silicone ordinaire ? Le plus souvent, ils sont utilisés pour fabriquer de beaux produits à partir de divers types de garnitures à deux composants. Les gros objets ne sont généralement pas fabriqués à l’aide de moules en silicone. Par conséquent, des seringues médicales ordinaires sont utilisées pour mélanger les composants des obturations à la maison. Ensuite, ils sont teintés avec une goutte de colorant et coulés dans le moule à travers le trou d'injection tendu par une entretoise.
Ils sont considérés comme l’un des types d’appâts non naturels les moins chers. Les silicones sont divisées en plusieurs types :
- Queue vibrante est un appât qui imite un petit poisson. Il y a un « sou » sur la queue de l'appât, qui donne au poisson son propre gibier.
- Tornade semblable à un vibrotail, cependant, au lieu d'un « centime », l'appât a une longue queue enroulée, semblable à un point d'interrogation.
- Vers en gros, ils n'ont pas leur propre jeu. Leur principale différence réside dans leur longueur, qui peut atteindre 30 centimètres.
- Par ailleurs, il existe des appâts en silicone qui imitent une variété de grenouilles, écrevisses et ainsi de suite.
Pour fabriquer des appâts en silicone de vos propres mains, vous aurez besoin de :
- appâts qui seront lancés
- cadre à remplir
- silicone
Comment faire fondre du silicone ?
Il existe plusieurs façons de faire fondre du silicone à la maison. Une fusion rapide du silicone est possible lors de l'utilisation d'une cuisinière à gaz. Pour faire fondre du silicone sur un feu, vous aurez besoin d’une boîte de conserve. Il peut s'agir d'une canette de bière coupée ou d'une canette de nourriture en conserve.
Cependant, la fusion par le feu pose plusieurs problèmes :
- le silicone brûle rapidement;
- fume;
- le silicone change de couleur et lorsqu'il est brûlé, il devient complètement noir ;
La fusion au micro-ondes est totalement exempte de ces inconvénients. Pour que les appâts aient la même couleur que la couleur originale du silicone, il faut le faire fondre au micro-ondes.
Lors de la fonte du silicone au micro-ondes, il y a une subtilité pour qu'il reste à l'état fluide le plus longtemps possible. Vous ne devez pas simplement attendre que le silicone fonde au micro-ondes, mais après la fusion, le conserver au micro-ondes pendant encore une minute et demie à deux minutes. Le récipient dans lequel le silicone est fondu doit être soigneusement réchauffé. Dans de telles conditions, le silicone reste beaucoup plus longtemps à l’état liquide.
Moule pour appâts en silicone
Le matériau le plus facilement disponible pour fabriquer des moules est le gypse. Ce formulaire est assez simple à réaliser. Il est nécessaire de diluer le plâtre jusqu'à obtenir la consistance d'une crème sure liquide et de le verser dans un moule en plastique ou en carton. Abaissez ensuite l'appât en silicone de la forme souhaitée dans le plâtre. Le plâtre devrait durcir en une heure et demie. Après quoi, vous pouvez retirer l'appât.
Cependant, l'utilisation de gypse pose également de nombreux problèmes.
- Premièrement, créer un tel formulaire prend beaucoup de temps, car Le plâtre doit être soigneusement séché. Si le moule n'est pas suffisamment séché, des bulles peuvent se former lors du coulage du silicone, ce qui endommagera considérablement le moule. apparence et la qualité de l'appât.
- Deuxièmement, il est assez difficile d'imprimer de petites parties de l'appât sur un moule en plâtre.
- Troisièmement, les coffrages en plâtre sont très fragiles ; si les coffrages en plâtre sont pressés un peu plus fort les uns contre les autres ou s'ils tombent accidentellement, ils éclateront instantanément.
- Le quatrième inconvénient est que les appâts sont difficiles à retirer du moule en plâtre.
Et si cette méthode convient toujours à la fabrication de queues et de vers vibrants, la fabrication de twisters sous forme de plâtre est problématique.
La résine époxy aidera à résoudre ces problèmes. Avec l'aide apportée une résine époxy pinceaux, il est nécessaire de lubrifier le moule en plâtre pour que la couche de résine soit la plus fine possible. Après quoi, le formulaire doit être soigneusement séché. Après avoir recouvert le moule en plâtre, les appâts en sont simplement retirés, les angles vifs sont lissés et le problème d'apparition de bulles d'air disparaît. Cependant, en raison du revêtement, la taille de l'appât sera légèrement réduite.
Fabriquer des appâts en silicone
La combinaison de couleurs idéale pour un appât artificiel est une combinaison de jaune et de rouge. Où jaune doit être très brillant et avoir une teinte vert clair.
Le processus étape par étape de fabrication des appâts ressemble à ceci :
- silicone fondant;
- verser du silicone dans un moule en plâtre ;
- refroidissement du silicone;
- tremper l'appât dans de l'eau froide;
Une fois le silicone refroidi, ce qui prend environ 5 à 10 minutes, il doit être plongé dans eau froide. Cette procédure est nécessaire pour que le silicone ne perde pas sa plasticité. Si cette étape est sautée, le silicone deviendra mou.
Comment augmenter vos prises de poissons ?

En 7 ans de pêche active, j'ai trouvé des dizaines de façons d'améliorer la morsure. Voici les plus efficaces :
- Activateur de morsure. Cet additif aux phéromones attire plus fortement les poissons par temps froid et eau chaude. Discussion sur l'activateur de morsure « Hungry Fish ».
- Promotion sensibilité des engrenages. Lisez les manuels appropriés pour votre type spécifique d’équipement.
- À base de leurres phéromones.
Méthodes d'installation des appâts en silicone

Pour monter l'appât, la méthode la plus couramment utilisée consiste à monter une tête plombée sur un hameçon. Le choix du poids de la tête doit être basé sur la profondeur du bassin. Lors du choix de la longueur de l'hameçon, vous devez vous concentrer sur la taille de l'appât. Les pêcheurs débutants croient que plus l'hameçon est gros, plus moins de quantité bouchées vides. C'est en partie vrai, mais il faut comprendre que si l'appât est placé sur l'hameçon avec tout le corps, alors ses vibrations sont considérablement limitées. L'appât en silicone peut glisser d'un tel hameçon. Certains pêcheurs utilisent de la super colle pour fixer solidement l'appât.
Une façon tout aussi populaire de monter un hameçon en silicone consiste à utiliser un hameçon double. L'hameçon doit être au centre du corps de l'appât. Pour attacher l'hameçon à l'appât, vous devez d'abord mesurer le niveau de l'endroit où le dard doit sortir. Après cela, l'un des doubles hameçons perce l'appât de part en part. Ensuite, la queue de l'hameçon est tirée à travers l'appât en silicone ; la queue doit être tirée à travers le corps de l'appât jusqu'à l'extrémité. L'hameçon doit être complètement enfoncé dans le corps de l'appât.
L'appât en silicone peut également être équipé d'hameçons décalés. Il existe deux formes de crochets décalés :
- forme oblongue incurvée;
- forme droite.
La forme du bol droit est utilisée avec des appâts de type ver et est récemment devenue obsolète. Pour attacher l'appât, vous devez percer l'extrémité avec la pointe de l'hameçon et la retirer immédiatement. Après quoi l'appât est passé au pas de l'hameçon et tourne légèrement. Pour fixer la pointe de l'hameçon dans l'appât, il est nécessaire de l'enlever par l'extrémité du corps de l'appât. Abaissez ensuite légèrement l'appât et insérez la pointe de l'hameçon dans le corps de l'appât. Le silicone ne doit pas être trop serré.
L'appât peut être équipé d'un tee. Dans le corps de l'appât, approximativement au milieu, vous devez faire un petit trou à l'aide d'un tube provenant d'une poignée. À l'aide d'un large cercle du manche, l'excès de silicone est expulsé, après quoi un trou reste dans l'appât. Ensuite, le corps de l'appât est percé avec la triple queue de l'hameçon et ressorti dans la bouche. Après cela, l'une des piqûres est enfilée dans le trou de sorte que l'hameçon soit situé exactement le long du corps de l'appât.
Choisir la bonne forme pour les futurs appâts en silicone - classement des meilleurs caoutchoucs comestibles des plus grandes marques.
— une revue des appâts comestibles les plus accrocheurs du segment économique.
Équipement pour appâts en silicone.
Appât en silicone Les clés sont l’un des types d’appâts artificiels les moins chers. Les fabriquer ne sera pas difficile. Pour fabriquer l'appât, vous n'avez besoin que d'un moule en plâtre et du silicone lui-même. La façon la plus simple de faire fondre le silicone est au micro-ondes. Après durcissement, le silicone doit être placé dans l'eau pendant deux heures pour préserver sa structure.
Silicone liquide DIY à la maison. Silicone liquide pour fabriquer des appâts et comment fabriquer des appâts de pêche. Les amis, je vais vous montrer une vidéo YouTube, je veux couler du silicone liquide dans des moules en plâtre, en le fabriquant moi-même. Je veux aussi expérimenter la couleur des colorants fluorescents. Je me suis fixé pour tâche de me rapprocher de la coloration uniforme comme une ventouse. Je souhaite également démontrer la zone de travail où je verse du silicone pour appâts, à savoir du silicone liquide pour appâts comestibles. L'endroit où l'appât est préparé est d'éliminer autant que possible la fumée chimique. Une fois fondu, le silicone liquide libère des vapeurs. Les gars, utilisez des équipements de protection : un masque à gaz, un respirateur. Et travaillez dans un endroit bien ventilé ou en plein air. J'ai préparé de mes propres mains des moules en plâtre et des appâts en silicone intéressants. Qu'un ami m'a donné pour le moulage. Ils ont une configuration inhabituelle et un complexe Forme géométrique. Avant de réaliser des moules en plâtre, vous devez préparer un modèle. Étonnamment, ils se sont avérés d’assez bonne qualité. Quand j’ai commencé à verser du silicone liquide, je pensais que je ne pourrais pas en retirer l’appât. Il est très côtelé et fin. En ouvrant les deux parties du moule, j'ai vu que toutes les pièces coulaient plutôt bien. Nous pouvons donc conclure qu'en principe, n'importe quel appât, même le plus lourd, peut être créé et lancé. Je vais vous montrer comment verser du silicone liquide de vos propres mains. Nous effectuerons également un test et vous verrez la couleur du silicone lors de l'ajout du pigment. Je prévois de mélanger du silicone liquide de mes propres mains. Colorants fluorescents en plastique souple. Que Konstantin m'a envoyé pour des expériences. Il est maintenant temps d'expérimenter et de servir pour vous-même et vos amis pour la saison. Je veux également créer les couleurs les plus réalisables pour les conditions que nous recherchons.
Commentaires sociaux Riquete
L'article décrit une expérience personnelle non professionnelle !
Les moules en silicone sont utilisés aussi bien dans la production que dans la vie quotidienne. Ils sont utilisés pour fabriquer des produits en gypse, tels que des pierres décoratives et des souvenirs, dans la production de savon, de bougies, de bijoux et en cuisine pour créer des plats et des pâtisseries. Pour certaines applications, les moules sont fabriqués à partir de types spéciaux de silicone, par exemple résistants à la chaleur, pour produits alimentaires et d'autres. En plus du silicone, des moules en polyuréthane sont également souvent utilisés. Nous n'avons pas travaillé avec du polyuréthane, nous allons donc sauter ce sujet.
Il existe de nombreux moules en silicone différents en vente, mais il n'est pas toujours possible de trouver ce dont vous avez besoin. Si vous le souhaitez vraiment, vous pouvez fabriquer vous-même un moule en silicone à la maison. Il existe plusieurs façons de fabriquer des moules de vos propres mains :
1. La plupart moyen abordable- Ce en utilisant du mastic silicone. Pas le meilleur la meilleure option, mais dans certains cas, cela peut être utile. Le seul avantage que l'on peut noter est la disponibilité du mastic. Le principal inconvénient est que les moules en mastic perdent rapidement et facilement leur forme (étirement). De plus, du mastic silicone dans forme pure Il n'est pas pratique d'appliquer le produit en raison de son caractère collant, il met beaucoup de temps à sécher, il doit être appliqué en fines couches et avant d'appliquer une nouvelle couche, il faut attendre que la précédente sèche complètement (environ 24 heures). ). La fabrication du moule prend plusieurs jours. Pour éviter que le mastic silicone ne colle aux mains et faciliter son application sur le relief souhaité, le mastic peut être mélangé à de la fécule de pomme de terre. Le mélange obtenu ressemblera un peu à une pâte épaisse et sera plus facile et plus rapide à mettre en forme. Pour les moules en silicone en mastic, ainsi que pour les moules fins en silicone de moulage, il faut réaliser un cadre rigide, par exemple en plâtre, afin que le moule ne se déforme pas lors du coulage. Le mastic acrylique ne convient pas à la fabrication de moules !
2. Utilisation d'un composé de silicone pour fabriquer des moules. C'est un ensemble de silicone liquide et d'un catalyseur (durcisseur). Le principe de fonctionnement est simple : 2 composants sont mélangés dans certaines proportions et le mélange obtenu est versé dans l'objet dont le moule doit être démoulé. Pour remplir le produit, vous devez réaliser un coffrage autour de celui-ci. Il peut être fabriqué à partir de n'importe quoi : pâte à modeler, plastique, bois et même boîtiers de CD, l'essentiel est qu'il ne fuit pas. Facile à sceller avec un pistolet à colle. Le produit lui-même n'a besoin d'être traité avec rien (s'il n'est pas en silicone) - le silicone ne colle pratiquement à rien et le moule s'enlève facilement. Si l'objet moulé présente des angles inversés ou si vous devez réaliser un moule 3D, vous devrez peut-être (selon la marque de silicone) réaliser un moule composite à partir de plusieurs parties. Pour ce faire, vous devez utiliser un agent de démoulage. Le silicone doit être coulé de manière à ce que les moules puissent être assemblés en douceur ; pour cela, il doit y avoir des trous dans la première partie et des saillies dans la seconde. Pour cela nous avons utilisé bâton de colleà partir d'un pistolet à colle chaude : les tiges ont été coupées en deux et fixées au bas du coffrage autour de l'objet à couler avant de couler la couche suivante, on les retire et on recouvre toute la surface de la partie résultante du moule avec un démoulage ; agent afin que la deuxième couche ne colle pas à la première.
La photo montre une forme réalisée à partir de Pentelast 710 après 45 à 50 coulées de plâtre.
Il existe de nombreuses variétés de composés silicones, nous n'avons eu l'occasion de travailler qu'avec 2 d'entre eux : le Pentelast 710M et le Pentelast 718. Ces deux composés production russe et sont disponibles en paquets de 1 kg, et ils sont également parmi les moins chers. Le Pentelast 710 M se distingue du 718 par sa plus grande fluidité et son temps de réaction plus long avec le catalyseur (reste fluide plus longtemps). Une fois guéri, le 718 est un peu plus dur, aucune autre différence n'a été remarquée. Mélangez le silicone avec le durcisseur strictement selon les instructions, rapidement mais soigneusement, afin qu'il y ait un minimum de bulles d'air. Si vous ajoutez moins de durcisseur que nécessaire ou si vous le mélangez mal, le silicone restera dans un état de « crème sure épaisse » ; si vous en ajoutez plus, vous n'aurez peut-être pas le temps de remplir le moule ; Après 24 heures, le formulaire obtenu peut être utilisé. En termes de résistance, ces silicones ne sont pas les meilleurs, donc pour les articles avec angles inversés Il vaut mieux faire des formes composées. Contrairement à certains moules commerciaux prêts à l'emploi, qui sont initialement découpés pour retirer les produits résultants et ne se déchirent pas lorsque vous les étirez, les moules fabriqués à partir des composés ci-dessus se déchireront facilement au niveau du site de découpe. Ils s'étirent bien sans dommage et vous n'avez pas à vous soucier de la rupture de la forme si vous faites tout avec soin.
Nous utilisons ces moules pour mouler des souvenirs et des figurines, et ils peuvent également être utilisés pour fabriquer du savon. Les moules fabriqués à partir de ces silicones ne peuvent pas être utilisés à des fins culinaires et ne peuvent pas y être cuits. pâte polymère dans le four.
Il existe des silicones spéciaux à cet effet. Ils ne sont pas non plus très adaptés à la fabrication pierre décorative, pour cela, il est préférable d'utiliser soit des formulaires de plus silicone résistant, ou en polyuréthane.
Des moules anciens et inutiles peuvent être utilisés en les ajoutant lors de la fabrication de nouveaux ; pour ce faire, les moules inutiles doivent être coupés en petits morceaux.
À propos, l'agent de démoulage a une durée de conservation de 6 mois (indiquée sur l'étiquette), mais il remplit ses fonctions tout à fait normalement après plus de 2 ans à compter de la date de production. Un flacon dure longtemps ; vous devez l'appliquer en couche fine.
Bien que nous décrivions ici les méthodes de fabrication de moules à la maison, il n'est toujours pas souhaitable de le faire à la maison, car le catalyseur est toxique et pue très fortement, et le scellant n'a pas non plus l'odeur la plus agréable. Tous les travaux doivent être effectués dans un endroit bien ventilé. DANS en dernier recours, vous pouvez utiliser le balcon (comme nous :)).
Le silicone est le matériau principal du 21ème siècle
Que font un avion de ligne et une éponge à vaisselle, une voiture et des lentilles de contact, un téléphone et station spatiale? Tous ces mécanismes, objets et appareils contiennent du silicone.
Il peut être liquide comme l'eau ou dur comme le verre - le polyorganosiloxane ou simplement le silicone, selon de nombreux experts scientifiques, est le matériau principal du 21e siècle, qui a radicalement changé nos vies. Tout composé contenant du silicium peut être classé parmi les silicones. En fait, l'ensemble du groupe de matériaux silicone tire son nom du nom anglais du silicium « Silicon ».
Les silicones revêtent une importance capitale dans l'industrie moderne. Si vous regardez autour de vous, presque n'importe quel objet monde moderne On ne l’a pas vu, chacun d’eux contient du silicone.
L'oxygène et le silicium sont les éléments les plus courants sur Terre. Le quartz, le cristal de roche et le sable de rivière ordinaire sont tous à base de silicium dont les réserves naturelles sont importantes et constamment renouvelées, ce qui signifie que la ressource pour produire des silicones est pratiquement inépuisable.
A partir d'un tel "gâteau" de silicone, le silicone peut être fabriqué par vulcanisation nouveau matériel avec absolument toutes les propriétés.
Pour comprendre pourquoi ce matériau est si populaire, il faut l’examiner au niveau moléculaire le plus profond.
Presque n’importe quel élément peut être ajouté à la chaîne principale silicium-oxygène-silicium (Si-O-Si) dans n’importe quel ordre. Il peut s'agir d'une structure non linéaire ou d'un réseau moléculaire. Capacité à organiser des multitudes diverses options liaison chimique - propriétés inhabituelles du silicone.
Les matériaux silicones apparaissent à travers une combinaison d’éléments apparemment incompatibles, grâce auxquels ils possèdent des propriétés particulières. Ce sont des silicones qui ont une plage de température très élevée et très bonne - de -120 à +300 degrés. Dans le même temps, n'importe quel type de ce matériau, même le plus courant, fonctionne de -60 à +200.
Une différence marquée entre ces températures réside dans les conditions extrêmes pour de nombreux matériaux. Mais pas pour les silicones, qui sont très simples à vérifier. Le point d’ébullition de l’eau est de 100 degrés et la chute instantanée jusqu’à zéro (au moment où la glace se forme) ne laisse aucune trace sur les échantillons de silicone. Cette capacité des silicones les a rendus indispensables dans l’aviation.
L'avion en est un exemple très clair. Lorsqu'il vole à une altitude de 10 000 mètres, où la température est de -60 degrés, et atterrit à l'aéroport, où il fait +30-50 degrés, les pièces en silicone ne réagissent en aucune façon à des changements de température aussi brusques et il y résiste facilement et scelle correctement tout ce dont vous avez besoin.
L’étanchéité d’une qualité étonnamment élevée des avions modernes est obtenue grâce à des joints en silicone.
Des silicones sont même ajoutées aux huiles d'aviation et au caoutchouc des trains d'atterrissage, ainsi que dans les moteurs d'avion - aux joints et joints en silicone. Dans le cockpit, il y a des boutons en silicone sur le panneau de commande, et toutes les coutures de la structure de l'avion sont également complètement scellées grâce au silicone.
Les mastics à base de silicone sont également utilisés dans la construction. Ils sont excellents pour sceller les fenêtres. L'ensemble de l'industrie actuelle des fenêtres produisant fenêtres en plastique n'a pu s'élever que parce qu'il était possible de sceller instantanément les fenêtres à double vitrage insérées. De plus, cela peut être fait de manière très fiable et pendant une longue période.
Utilisation du silicone dans la construction.
Quelle que soit leur apparence et leur application, la matière première de tous les produits en silicone est la même : elle est toujours liquide. Dans ce cas, le silicone devient facilement un matériau dur qui peut être facilement meulé, poli, coupé et généralement traité comme vous le souhaitez. Le silicone peut également ressembler à du caoutchouc – doux et élastique, qui peut être facilement compressé, plié et étiré.
L'aspect du silicone dépend entièrement du catalyseur. La première étape est la production de liquides, d’huiles et de caoutchoucs de silicone. Parallèlement, à partir de ces dernières, vous pouvez obtenir une variété de joints (anneaux, valves), de prothèses et différents types de silicones liquides et solides dont vous disposez.
La matière première liquide accepte le formulaire requis après avoir interagi avec le catalyseur et jusqu'à ce qu'il refroidisse, le futur silicone peut être peint de n'importe quelle couleur. La dernière étape est la vulcanisation, lorsque sous l'influence de l'air chaud la masse de silicone durcit, prenant la forme d'un produit fini.
Anneaux en silicone réguliers de différentes couleurs.
La température de vulcanisation du silicone est la limite supérieure de fonctionnement normal du futur produit. Une fois la vulcanisation terminée, la forme et les propriétés du matériau seront constantes, de sorte que la masse déjà formée entre dans le vulcanisateur.
Et le processus de moulage lui-même est appelé extrusion et est très similaire au travail d'un hachoir à viande conventionnel. Le mélange de silicone est chargé dans l'appareil dont le puissant piston en spirale presse littéralement le silicone dans le trou existant, qui représente le profil du futur produit. Pour réaliser une pièce d'une forme différente, il suffit de modifier l'attache du profil. C'est ainsi que toutes sortes de tubes et sondes médicales, tuyaux hydrauliques, rubans isolants pour fours et appareils ménagers, qui est désormais presque entièrement équipé de silicone.
Par exemple, une machine à café. Les compartiments pour les grains de café sont isolés avec du silicone pour préserver l'arôme et le goût du café frais. Même l'éponge à vaisselle contient du silicone - elle est faite de mousse de polyuréthane, ce qui lui confère une structure si poreuse. Et si vous regardez attentivement, vous verrez que les bulles de l'éponge sont presque identiques et situées exactement les unes par rapport aux autres. C’est le mérite des silicones, qui permettent de contrôler le moussage.
La mousse se forme lors de la réception du plus différentes substances– dans le raffinage du pétrole, dans l’industrie des pâtes et papiers, etc. Et plus il y a de mousse, plus moins d'espace pour le produit lui-même. Et pour le détruire, vous devez en retirer les particules qui font que les bulles de gaz n'éclatent pas, mais se trouvent dans un état mousse-air.
Mais comment ça fonctionne? Un des plus exemples illustratifs– une combinaison d’eau plate et d’huile végétale. En raison de la différence de densité de ces liquides, ils resteront toujours des couches indépendantes. Même si vous les mélangez, l’eau et l’huile se sépareront très rapidement. Un émulsifiant, un tensioactif qui stabilise les émulsions, peut forcer des molécules aussi différentes à se mélanger.
Ce n'est qu'alors qu'il y aura une répartition uniforme grâce au fait qu'il y aura un émulsifiant entre les liquides. Mais si vous le retirez, alors «l'effondrement» de ce système se produira à nouveau - les particules d'huile et d'eau se connecteront séparément les unes aux autres et les deux couches se sépareront à nouveau.
De la même manière, les matériaux silicones agissent sur les composants individuels des substances moussantes, contrôlant littéralement le diamètre des bulles. En raison de ces propriétés, le silicone est utilisé dans presque toutes les productions à base de mousse de polyuréthane, qu'il s'agisse d'une éponge à vaisselle ou d'une tresse pour volant de voiture.
D'ailleurs, Dans l'industrie automobile, le silicone a également réussi à prendre une position forte. Disons que dans les joints de voiture, il est utilisé en raison de sa capacité à bien se comprimer, grâce à laquelle il amortit tout, ce qui permet une meilleure préservation de la voiture.
La tresse en silicone pour volant de voiture aide à la conduite grâce à une meilleure adhérence des mains sur la jante du volant.
La longue durée de vie des pièces en silicone dans une voiture n'offre pas seulement une résistance à la déformation. Le fait est que les silicones automobiles ne sont pas sensibles aux huiles et à l'essence. Cette propriété leur est conférée par des catalyseurs spéciaux.
En général, il existe de nombreux types de caoutchouc de silicone, mais les différences entre eux - apparence, densité, ensemble de propriétés, etc., n'apparaissent qu'après vulcanisation. L'étape de vulcanisation à haute température est assez courte - en moyenne seulement 10 à 15 minutes d'exposition. Le temps d'exposition dépend du type de caoutchouc et de sa destination. Différents pneus ont des exigences différentes et chacun a ses propres exigences. spécifications techniques– se déchire-t-il facilement, s'étire-t-il bien, quelle est sa dureté et bien plus encore.
L'indicateur de dureté indique la capacité à conserver sa forme.
Par exemple, sur une télécommande de téléviseur, les boutons trop mous resteront collés et les boutons trop durs seront difficiles à appuyer. Mais le test le plus difficile est celui du caoutchouc dit isolant. Comme il doit durer longtemps et qu'il est très problématique d'effectuer des tests pendant toute la durée prévue de son service, les conditions lors des tests sont bien plus extrêmes qu'en réalité.
Les échantillons de caoutchouc de silicone sont exposés à un courant d'une tension de 3 000 à 4 000 volts - une telle charge est comparable à un coup de foudre. De l'arrière, une solution destructrice de chlorure d'homomonium est fournie aux plaques de caoutchouc pour renforcer l'effet du courant. Le test dure 6 heures, après quoi le degré d'endommagement du silicone est évalué. Et moins le courant qui passe a d'impact sur la plaque, meilleur est le caoutchouc.
Il est peu probable qu’une situation similaire se produise dans vrai vie. Pendant ce temps, certains silicones ne doivent fonctionner que dans des conditions extrêmes, par exemple dans l’espace.
Silicone comestible
Et ceux-ci sont déjà réels technologie de pointe et la production d'un tel silicone est spéciale. Il peut résister à des températures incroyables et est utilisé comme lubrifiant dans l’espace et dans les systèmes hydrauliques utilisés dans la technologie spatiale.
Les premiers pas de l'homme sur la Lune ont été rendus possibles grâce au silicone : c'est à partir de celui-ci qu'ont été fabriquées les bottes des astronautes. Un nouveau développement qui permettra de rapprocher un peu l'espace est la production de matériaux ultra durs et ultra résistants à la chaleur à partir de silicone.
Mais des matériaux fiables et résistants à la chaleur ne sont pas seulement nécessaires dans l’espace. Métallurgie, industrie automobile et agroalimentaire sont étroitement liées à des températures très élevées et celles-ci ne sont plus des centaines, mais des milliers de degrés. Mais les silicones peuvent aussi le faire.
Les matériaux nouvellement développés ont une résistance à la chaleur unique - jusqu'à 1 500 degrés et plus. Ainsi, un développement domestique à base de silicone possède des propriétés d'isolation thermique étonnantes. Lorsque la température d’un côté de l’échantillon dépasse 1 500 degrés, l’autre reste légèrement au-dessus de la température ambiante. Un tel matériau peut devenir une véritable protection, par exemple pour les métaux à bas point de fusion.
Plus récemment, un autre type de silicone a commencé à être produit en Russie, dont la tâche principale est la protection. Le nouveau caoutchouc de silicone peut littéralement sauver des vies. Dans le métro, les aéroports et les gares, en cas d'urgence, les locaux doivent être alimentés en électricité pendant au moins 3 heures. Et ce fil isolant en caoutchouc n'émet pas produits dangereux en cas d'incendie, mais au contraire, il forme une couche céramique assez résistante, qui permet au fil de fonctionner pendant au moins trois heures et protège les fils électriques des courts-circuits.
En fait, les silicones peuvent avoir toutes les propriétés, même les plus incroyables. Mais cela ne peut être fait qu'au stade du travail avec les matières premières, car le produit fini en silicone qui a subi la vulcanisation est bio et chimiquement inerte, c'est-à-dire qu'il ne forme pas de nouvelles liaisons chimiques. C’est pourquoi les silicones ne craignent pas de nombreux environnements agressifs.
Les silicones résistent facilement au contact à court terme avec des acides et des alcalis concentrés. Et ils peuvent rester dans des solutions faibles presque indéfiniment, là encore, sans perdre leurs propriétés.
C'est précisément à cause de son inertie les silicones sont activement utilisés en médecine. Il n’y a aucun endroit ni organe dans le corps qui ne puisse être temporairement remplacé ou aidé à fonctionner grâce au silicone.
Le silicone médical est produit à l’aide de catalyseurs au platine. La présence de métaux précieux rend le silicone absolument sans danger pour l'homme. Dans le milieu biologique dans lequel peuvent se trouver les implants et prothèses en caoutchouc de silicone ou où certains dispositifs ou instruments (sondes, drains) sont placés temporairement, ils ne provoquent pas de rejet dans l'organisme et sont totalement non toxiques.
Les implants mammaires en silicone ont fait le bonheur de milliers de femmes à travers le monde et ont apporté une grande renommée au matériau à partir duquel ils sont fabriqués.
En particulier, l’utilisation de silicone réduit considérablement le risque de complications après une intervention chirurgicale. À propos, certains types de silicones médicaux ne nécessitent pas de températures élevées lors de leur production. L'étape de leur vulcanisation (fixation de la forme) se déroule à température ambiante.
Grâce au silicone, les médecins ont réussi à vaincre la maladie du vieillissement la plus courante. Avec l’âge, une personne perd la vision, principalement en raison d’une opacification du cristallin. Les médecins installent désormais des lentilles en silicone chez ces patients. Pour la première fois, une telle opération a été réalisée par notre compatriote, le célèbre ophtalmologiste Svyatoslav Fedorov, qui, grâce à lentille artificielle redonne instantanément la vue aux personnes âgées.
Mais le silicone aide à restaurer la vision non seulement pendant la chirurgie.
Les lentilles de contact sont également en silicone. Malgré leur apparente fragilité, ces objectifs sont assez durables. Lorsqu'elles sont correctement sélectionnées, les lentilles en silicone hydrogel les plus fines ne causent aucun dommage aux yeux.
Et la petite présence de platine confère au silicone des propriétés cicatrisantes. Vous pouvez facilement vous débarrasser des brûlures et des cicatrices à l'aide de patchs en silicone, développés il y a longtemps par des scientifiques russes. Ils aident très bien en cas de brûlures, pour lisser les sutures chéloïdes après des brûlures et des opérations.
Si vous subissez accidentellement une brûlure mineure, il suffit d'appliquer une bande de plâtre de silicone sur le site de la brûlure. Et au bout de très peu de temps, vous constaterez que vous n'avez plus aucune trace de brûlure.
En même temps, le patch en silicone peut être retiré, lavé et réappliqué. Vous pouvez, par exemple, l'enlever la nuit ou le porter 24 heures sur 24 jusqu'à ce que vous obteniez des résultats complets. Un patch peut durer 2 à 3 mois, ce qui est un véritable record par rapport à un patch classique.
Cependant, presque tous les silicones peuvent se vanter de leur durabilité. Sous l'eau et dans l'espace, sur table de cuisine et dans le corps humain, les silicones fonctionnent partout pendant très longtemps et de manière tout aussi fiable. Et apparemment, le silicone ne fait que commencer sa grande marche à travers la planète.
Les scientifiques promettent d’obtenir bientôt du silicone capable de résister à des températures supérieures à 3000 degrés. Un tel matériau surpassera le titane en termes de résistance à la chaleur, et cela ne semble plus incroyable. Le silicone ouvre des perspectives si alléchantes qu'il ne fait aucun doute que de nouvelles découvertes avec sa participation active sont à nos portes.
Jusqu'à présent, il n'existe pas sur le marché un très large choix de silicone pour la fabrication de moules.
Appâts en silicone à la maison. Vidéo
De plus en plus d'artisans manifestent le désir de s'essayer à ce matériau relativement nouveau, mais dès les premiers pas, ils sont confrontés à des difficultés, ne sachant pas par où commencer, quel silicone utiliser et comment le manipuler. Ici, je vais essayer de résumer les points principaux, sur la base de ma propre expérience et des informations obtenues sur Internet. Je dirai tout de suite que je ne vous dirai rien de fondamentalement nouveau - tout ce qui sera discuté est bien connu des professionnels travaillant avec le silicone, mais j'espère que les informations recueillies en un seul endroit aideront les débutants à surmonter leurs premières difficultés.
Quels silicones sont nécessaires pour le moulage ?
Donc, tout d’abord, le silicone lui-même. Lors de la création de poupées, j'utilise des composés à base de platine (silicones à deux composants) de Smooth-On, fabriqués aux USA, car Nous parlerons exactement à leur sujet. Pour travailler, vous aurez besoin de deux types de silicones : pour couler les poupées elles-mêmes et pour réaliser le moule. Il n'y a pas beaucoup de premiers, principalement les séries Dragon Skin et Ecoflex. Ils ont haut degréélasticité et vous permettent de transmettre de la manière la plus réaliste l'effet de la chair humaine.
Les silicones de chacune de ces séries présentent des caractéristiques techniques différentes : douceur, durée de vie (durée pendant laquelle le silicone reste fluide), temps de durcissement, viscosité, etc. Quel type de silicone est-il préférable d’utiliser pour créer des poupées ? Je ne peux rien dire de précis ici - tout dépend du but ultime du maître. À mon avis, il est préférable de suivre le chemin de l'expérimentation, en essayant différentes séries afin de trouver en pratique le seul matériau qui permet d'obtenir l'effet souhaité.
Les silicones des séries Dragon Skin et Ecoflex sont incolores et translucides, donc pour obtenir une couleur de poupée réaliste, ils doivent être colorés à l'aide de pigments spéciaux Silc Pig.
Le deuxième type de silicones est utilisé pour réaliser le moule. Sois prudent - Les silicones à base de platine ne peuvent être coulées que dans des moules en silicone contenant du platine. Les silicones avec catalyseur à l'étain ne peuvent pas être utilisés. Sinon, le moulage ne durcira pas. Les silicones destinés au démoulage ont moins d’élasticité, une plus grande dureté et sont généralement de couleur vive ou transparents. Couleur vive l'un des composants vous permet de mélanger uniformément les composants A et B avant de couler, et les transparents vous permettent de voir le modèle dans le moule (cela est pratique si le moule est coulé dans son ensemble puis découpé en parties). Les silicones destinés au démoulage comprennent des séries telles que : la série E, la série Mold Star, la série Equinox, la série Rebound, etc.
Le moule peut être réalisé par coulage, ou en appliquant progressivement des couches de silicone avec un pinceau.
La première méthode est plus simple et plus rapide, mais nécessite plus de consommation de silicone. La seconde demande plus de travail et nécessite également divers Matériaux additionnels. Vous pouvez clairement voir le processus de création d'un formulaire « spread » sur la vidéo officielle de l'entreprise :
Un peu sur les formulaires
Le moule en silicone fini reste élastique, c'est son avantage absolu, mais il ne faut pas oublier qu'il peut se déformer facilement, il doit donc être placé dans un boîtier de protection spécial moulé en plâtre ordinaire.
Avant de verser du silicone dans un moule en silicone, vous devez utiliser un agent de démoulage spécial, Ease Release, sinon le moule et le moulage colleront étroitement ensemble. La couche de séparation doit être soigneusement séchée, car elle empêche dans certains cas le durcissement complet du moulage en silicone.
Les moules pour mouler des poupées peuvent être fabriqués non seulement en silicone, mais également en plâtre. Il est conseillé d'utiliser à cet effet un plâtre dentaire spécial, comme le Fuji Rock, qui a une résistance accrue, transmet parfaitement les petits détails en relief et sèche assez rapidement. Par rapport aux moules en silicone, les moules en plâtre ne nécessitent pas l'utilisation d'un agent de démoulage et absorbent l'excès d'huile de silicone pendant le processus de coulée. Cependant, les moules en plâtre présentent également des inconvénients importants - le maître-modèle est presque impossible à retirer du plâtre sans dommage, les moules s'ouvrent avec beaucoup de difficulté et se détachent assez rapidement, perdant la précision de l'alignement des moitiés. De plus, par rapport au silicone, un moule en plâtre doit être fabriqué à partir d'un plus grand nombre de pièces, ce qui augmente le nombre de coutures sur le moulage fini.
Règles de base pour travailler avec du silicone
Nous avons donc trié les matériaux pour le moulage, parlons maintenant du processus lui-même. Pour éviter les défauts et les pannes lors du travail du silicone, vous devez suivre deux règles d'or qui facilitent grandement la vie du maître :
- 1. Suivez toujours les instructions de manière stricte et pédante, en évitant toute activité amateur.
- 2. Testez toujours la compatibilité des nouveaux matériaux qui entrent en contact avec le silicone.
Pour le travail, il est conseillé d'acheter une chambre à vide avec une pompe qui pompe l'air du mélange avant de le verser. Certains types de silicones peuvent être utilisés sans dégazage préalable, cependant, le risque que des bulles d'air restent dans la masse gelée est assez élevé.
C’est également une bonne idée d’avoir un four ou une armoire de séchage pour le post-durcissement des produits finis. Le silicone ayant subi un traitement thermique acquiert rapidement les propriétés déclarées par le fabricant. caractéristiques physico-chimiques. Je ne risquerais pas de chauffer des produits dans un four destiné aux produits alimentaires, malgré le fait que les silicones à base de platine sont considérés comme des matériaux non toxiques.
Je voudrais noter que la fabrication de poupées en silicone nécessite des dépenses financières importantes, mais il est impossible d'économiser sur les matériaux et les équipements en recherchant des analogues bon marché et en effectuant un travail amateur - le résultat de telles expériences est généralement désastreux et entraîne des dommages inévitables aux pièces moulées et moules.
Lorsque vous travaillez avec du silicone, vous ne devez porter que des gants en vinyle ; les gants en latex ne peuvent pas être utilisés.
La salle de coulée doit être chauffée; la température ne doit pas descendre en dessous de 22-23 degrés. Nécessaire régime de température L'un des facteurs les plus importants est qu'à des températures inférieures à 18 degrés, le silicone peut tout simplement ne pas durcir et que des températures de l'air plus élevées réduisent légèrement la durée de vie du mélange de silicone fini.
Mais vous ne pouvez pas conserver le silicone à la chaleur. Le matériau a une durée de conservation limitée, qui diminue avec l'augmentation de la température. Un bidon ouvert doit être utilisé rapidement, car le contact avec environnement peut également affecter ses propriétés.
L'algorithme pour travailler le silicone doit être le suivant : sortez les pots de silicone d'un endroit frais, attendez qu'ils se réchauffent aux 23 degrés requis, mélangez soigneusement le contenu de chaque pot, combinez les composants A et B dans des proportions exactes. , soumettre le mélange fini au dégazage, verser dans le moule et remettre le silicone restant dans la chambre froide.
De manière générale, il faut rappeler que le silicone est un matériau très capricieux qui ne permet pas de libertés de manipulation.
Les aléas du silicone
En principe, le processus de fabrication des pièces moulées en silicone est élémentaire, mais cette simplicité est trompeuse.
Le silicone présente constamment des surprises désagréables, empêchant le maître de se détendre et de commettre des erreurs. Le principal danger du silicone non durci est l'inhibition (empoisonnement) par diverses substances incompatibles avec celui-ci. L'« ennemi » le plus redoutable et en même temps le plus commun du silicone est la pâte à modeler contenant du soufre. Pour travailler, vous devez acheter uniquement des pâtes à modeler marquées sans soufre, comme Monster Clay ou Chavant. Il est préférable de ne pas conserver du tout de pâte à modeler douteuse dans l'atelier - même toucher accidentellement un matériau contenant du soufre avec la main peut « infecter » le moule en silicone.
Le deuxième « ennemi » du silicone est le latex. N'utilisez pas de gants en latex, de seringues avec des buses en caoutchouc sur les pistons ou tout autre instrument comportant des pièces en latex dans leur conception.
Utilisez des bâtons de bois avec beaucoup de précaution pour remuer le mélange. Certains types de silicone ne tolèrent pas le contact avec le bois et peuvent être inhibés. Pour se prémunir des mauvaises surprises, il est conseillé de mélanger le silicone avec des agitateurs métalliques.
Les polyesters fraîchement durcis, les caoutchoucs époxy et polyuréthane sont également dangereux. Comme je l'ai déjà écrit ci-dessus, avant d'utiliser un nouveau matériau dans votre travail, vous devez le tester en le remplissant d'une petite portion de silicone. Si le mélange durcit complètement dans le temps habituel imparti pour une polymérisation complète et que la surface du silicone n'est pas collante, nous pouvons supposer que le nouveau matériau a réussi l'examen et peut être utilisé dans des travaux ultérieurs.
C'est essentiellement tout ce que je voulais vous dire sur les techniques de travail du silicone. J'ai moi-même souvent commis des erreurs, vécu de nombreux moments désagréables et j'espère que cette expérience durement gagnée aidera les artisans débutants à ne pas marcher sur le vieux râteau douloureusement familier et à économiser des nerfs, du temps et de l'argent. Bonne chance avec votre créativité!
Comment fabriquer du silicone à la maison
Le silicone est un matériau constitué d'une substance organique de silicium ; il possède des propriétés de plasticité et de douceur, c'est en raison de ces propriétés qu'il est utilisé pour créer des ébauches et des moules, ainsi que des figurines et des figurines. Avec absence outils spéciaux et des matériaux, vous pouvez fabriquer du polydiéthylsiloxane à la maison, ou si vous utilisez des formulations non scientifiques, du silicone à base de caoutchouc.
Ingrédients et mise en route
Pour préparer du silicone à partir de caoutchouc, vous ne devez utiliser que deux produits ménagers courants : le verre dit « liquide » et l'alcool éthylique.
Vous aurez également besoin d'une surface plane pour travailler et d'un récipient pour le silicone lui-même, de préférence peu profond et en plastique. Versez ensuite dans le récipient préparé dans des proportions égales, d'abord de l'alcool éthylique, puis du verre « liquide ». Mélangez la masse obtenue à l'aide de n'importe quel objet approprié, qu'il s'agisse d'une tige ordinaire ou d'une cuillère. Dès que le mélange commence à épaissir, vous pouvez remuer ou plutôt pétrir le silicone avec vos mains. Le résultat sera une substance dense dont la structure et l'apparence ressemblent à de la pâte à modeler et la couleur de cette substance sera blanche.
Dès que la substance durcit, vous pouvez donner au silicone la structure dont nous avons besoin ; il est préférable de déterminer à l'avance ce que vous allez sculpter. Ce sera très facile à faire, car la masse elle-même est molle et malléable, rappelant le caoutchouc, la pâte à modeler ou l'argile. Une fois le façonnage terminé, laissez reposer l'objet obtenu un certain temps pour permettre au silicone de durcir complètement. Le caoutchouc silicone durcira et le produit lui-même deviendra plus élastique et moins sensible à la déformation, aux chocs, etc.
Faire des copies à partir de silicone
Pour réaliser certaines copies d'objets ou d'objets, vous devez utiliser des silicones liquides, que vous pourrez trouver en magasin. Ces liquides silicones contiennent certaines impuretés et le processus de solidification est plus long, permettant ainsi d'en couler les objets nécessaires.
Avant de commencer la production, prenez un moule dans lequel vous placerez de la pâte à modeler pour les sculptures et l'objet lui-même à copier. Le moule doit être sans trous ni crevasses, et les côtés du moule doivent être amovibles pour retirer les flans de silicone eux-mêmes.
Versez le silicone dans le moule en commençant par le bord du moule. Dès que la partie supérieure de la pièce durcit, sortez la pâte à modeler pour sculptures, puis dans le moule vous verrez une figurine à moitié remplie de silicone.
Il est donc nécessaire de remplir le silicone avec verso, puis retirez la pièce en démontant le moule. L'élément lui-même pour la copie est retiré et il reste un espace vierge à partir duquel des copies peuvent être créées un nombre infini de fois.
Il y a quelques mois, je me suis fait prendre ici cette vidéo est sur YouTube, où un homme fabriquait un moule à partir de gélatine et de glycérine. J'ai beaucoup aimé la vidéo, d'autant plus que tous les composants de cette recette sont facilement accessibles et pas très chers, du moins pour de petits volumes de formulaires. La vidéo elle-même, bien qu'en langage bourgeois, n'a rien de spécial à approfondir ; il suffisait d'entendre cinquante-cinquante, après quoi il est devenu clair quelle quantité de glycérine et de gélatine devait être mélangée. Par conséquent, j'ai décidé d'essayer de répéter cette recette avec du silicone ou du caoutchouc fait maison, selon celui qui est le plus proche.
À la pharmacie et à l'épicerie la plus proche, plusieurs flacons de glycérine et le même nombre de sachets de gélatine ont été achetés. Ici, tout dépendra de la taille du moule ; si vous souhaitez fabriquer un moule pour quelque chose de grand, vous devrez alors acheter un peu plus de tous ces composants.
Mélangez le tout environ 50/50, c'est-à-dire à l'œil nu. Expérimentalement, j'ai découvert que si vous versez plus de glycérine, le mélange s'avère plus liquide et fluide. Mais s'il n'y a pas assez de glycérine, alors cette pâte de gélatine s'étirera comme de la colle Moment séchante et en même temps il est difficile de remuer même dans un bain-marie, encore moins de la verser dans un moule avec une partie aux détails complexes. En général, cela semble être du 50/50 Meilleure option. Je n'ai pas essayé d'ajouter de la glycérine plus de deux fois (pour connaître la limite à laquelle le mélange resterait fort et non collant après durcissement).
L’idéal est de chauffer le tout au bain-marie, car vous n’avez pas besoin de contrôler la température, mais cuisinière à gaz Il n'y a pas toujours d'accès, donc pour l'instant je me contente d'une bougie ordinaire. L'essentiel est de ne pas laisser bouillir la gélatine, sinon elle commencera à brûler et à sentir mauvais, comme si vous faisiez frire une sorte de carcasse d'animal :-) J'ai chauffé et agité cette substance pendant environ 10 minutes pour que le mélange soit homogène et sans grumeaux. Là, dans la vidéo, il chauffe le tout au micro-ondes, mais pour ne pas chercher de plats et ne pas évoquer le temps de chauffage requis, il a pour l'instant décidé de se contenter d'un chauffage ordinaire sur un feu ouvert.
J'ai arraché ce cristal de verre du lustre pendant toute la durée de l'expérience. J'ai également plié un moule à partir d'une bande de plastique à une taille légèrement plus grande que cette pierre.
J'ai versé un peu de ce silicone dans le fond du moule et je l'ai laissé refroidir pour faire une sorte de base pour une pierre. J'ai décidé de faire cela pour que l'épaisseur de ce caoutchouc soit plus ou moins uniforme sur toutes les faces du cristal. Sinon, si le moule est fin, il ne conservera pas bien la forme souhaitée et risque de se déchirer lorsque le prototype en sera retiré.
Après cela, plongez partiellement le cristal dans un bol de gélatine pour éliminer les bulles d'air du fond de la pierre. Puis on transfère rapidement ce galet et on le place au fond du moule, avec la gélatine collée dessus, comme pour le coller.
Maintenant, le plus simple est de remplir le formulaire de gélatine jusqu'aux bords du coffrage.
Ce qui est bien avec ce caoutchouc fait maison, c'est qu'il durcit littéralement sous vos yeux, dès qu'il refroidit vous pouvez le couper. Il n'est pas nécessaire d'attendre une semaine pour que cette forme prenne complètement, comme c'est généralement le cas avec le silicone de construction acide. Une fois la masse refroidie, déroulez le plastique de ce cube.
Nous faisons une coupe en haut et retirons soigneusement le cristal de verre de notre moule.
Mélangez ensuite et versez la résine époxy dans le moule.
Le moulage en résine époxy ne sortait plus du moule aussi facilement que le prototype en verre. J'ai donc dû découper soigneusement le moule en cercle et le déchirer afin de ne pas rayer le cristal époxy avec un couteau. Je ne sais pas encore à quoi cela est lié, mais le casting s'est avéré trouble et non transparent. Soit la présence d’eau quelque part dans la masse de gélatine l’affecte, soit autre chose. En revanche, si vous jetez quelque chose de coloré dans la masse, alors cela n’aura plus beaucoup d’importance.
Aussi, uniquement par souci d'expérimentation, j'ai essayé de couler un fragment de cette pierre, mais en plâtre (albâtre). Les résultats furent désastreux. La gélatine commence à absorber l'eau du gypse et nous obtenons ainsi une pierre de plâtre collante et une forme gâtée par l'eau. Peut-être que quelque chose de grossier et sans trop de détails peut être moulé à partir de plâtre dans un moule en gélatine, mais vous devrez alors d'une manière ou d'une autre nettoyer la surface du plâtre des fragments de gélatine collante.
En général, j'ai aimé le fait que ce moule en silicone fait maison permette de réaliser des moulages en résine époxy. Certes, il y a beaucoup de bruit avec l'acide (assemblage), et l'aspic reste cher. Une autre caractéristique positive de ces formes de gélatine est qu'elles peuvent être ajustées avec une spatule chaude, c'est-à-dire que s'il y a un trou inutile quelque part sur la forme, vous pouvez simplement le recouvrir en faisant fondre un fragment de cette masse de gélatine dans une cuillère. Vous pouvez également facilement fondre et remplir d’anciens moules dans de nouveaux. Je me souviens à quel point j'ai bricolé ce radiateur, même si avec l'aide de ce moule en gélatine, il aurait pu être copié encore plus rapidement et avec une meilleure qualité. Bien sûr, il y a aussi des inconvénients : ce moule a peur de l'eau et de la température (il fond), donc si un échauffement excessif se produit dans une coulée époxy massive, le moule peut simplement flotter avec la résine.
Postface 1
Après un certain temps, j'ai essayé de polir ce cristal époxy pour savoir exactement s'il était trouble en grande partie ou seulement superficiellement. J'ai également créé une page séparée sur le polissage époxy à la main, au cas où quelqu'un serait intéressé. Bien entendu, les résultats du polissage n’étaient pas particulièrement impressionnants, car je n’avais jamais vraiment poli la résine moi-même. Mais un peu de brillance est encore apparue sur ce galet, ceci est particulièrement visible dans la vidéo que j'ai ajoutée à la fin de ce sujet. En général, les moulages époxy dans des moules en gélatine ne sont troubles qu'à l'extérieur, du moins pour moi, alors gardez cela à l'esprit si vous souhaitez couler quelque chose dans un tel moule.
Une autre de mes formes, cette fois fabriquée à partir de ce type de silicone de construction. , mais il s'agissait principalement d'un projet ponctuel, puisqu'un seul clone était nécessaire. Si vous le souhaitez, bien sûr, vous pouvez en extraire quelques exemplaires, en protégeant le plâtre avec toutes sortes d'imprégnations et en utilisant divers lubrifiants de séparation. Mais même avec ces mesures, après la première utilisation, il a commencé à tomber en panne pour moi.
Cette fois, nous avons besoin d'environ 70 exemplaires d'obus, toujours pour ce char Tigre, nous avons donc dû abandonner le moule en plâtre et essayer d'utiliser silicone de construction. Sur Internet, ils écrivent que le silicone de construction peut résister à environ 5 à 8 moulages en résine époxy (EDP), puis il commence à s'effondrer. Par conséquent, il est recommandé d'utiliser de l'aspic, capable de produire plusieurs fois plus de copies. Mais quelque chose me rend confus à propos du prix des silicones coulés, j'ai donc décidé d'acheter le silicone de revêtement le moins cher pour tester et, pour ainsi dire, de sonder le processus de création de moules à partir de silicone, et il sera alors clair dans quelle direction creuser ensuite.
Pour commencer, j'ai fait un lit pour le silicone lui-même, afin que le silicone conserve la forme souhaitée lorsque de la résine époxy y est versée. J'ai suivi presque le même schéma que lors de la création du moule de ce radiateur. Un briquet ordinaire convenait parfaitement à la taille des projectiles, j'ai donc construit un coffrage en plastique autour de lui.
Je l'ai sculpté à la hâte, donc en le versant, il y avait beaucoup de fuites.
En fait, la moitié est déjà prête. J'ai trop rempli un peu de plâtre, de ce fait les rayons du moule vont dans le moins et ne libèrent pas le briquet, j'ai donc dû démonter le coffrage et meuler tout l'excédent pour retirer le briquet.
J'ai creusé les rainures des serrures, tout remonté, généreusement lubrifié avec de la graisse pour ne pas avoir à marteler quoi que ce soit comme la première fois, et en plus, la qualité de l'impression n'est pas requise ici.
Albâtre coulé.
Cette fois, les moitiés du moule se sont détachées comme sur des roulettes, sans même avoir besoin de frapper dessus.
J'ai broyé les bavures, enduit les moitiés de colle PVA et les ai envoyées sécher sur le radiateur.
Ensuite, pour être sûr, je les ai recouverts de paraffine.
En tant que lubrifiant séparateur, le cirage ordinaire a donné les meilleurs résultats, apparemment en raison du fait qu'il contient la même cire.
J'ai légèrement enduit les prototypes de projectiles avec ce cirage afin que le silicone lui-même ne colle pas aux projectiles.
J'ai soigneusement enduit les coques de silicone pour qu'il n'y ait pas de bulles d'air dessus. J'ai également rempli les deux moitiés du bouillon avec du silicone, puis j'ai mis les coquilles dans la moitié et j'ai fermé le couvercle en essorant l'excès de silicone. J'ai fait tout cela avec les mains sèches, sur Internet, ils écrivent qu'il vaut mieux se mouiller les mains, mais je ne l'ai pas fait, car je ne voulais pas me débarrasser des gouttelettes d'eau plus tard. D'ailleurs, l'odeur est indescriptible car le silicone est acide, on a l'impression d'avoir renversé une bouteille de vinaigre. Il est donc préférable de réaliser des moules en silicone avec la fenêtre ouverte ou même dehors.
J'ai serré le bloc avec des élastiques et je l'ai laissé sécher pendant quelques jours.
Deux jours plus tard, j'ai décidé de démonter le moule et de voir ce qui se passait. À première vue, tout semble normal, la seule chose qui m'a dérangé était la forte odeur acide lors du retrait du moule en silicone du plâtre.
J’avais hâte de faire une autopsie, alors je me suis armé d’instruments de perçage et de coupe et j’ai commencé l’opération. Il s'est avéré que la puanteur du moule n'était pas sans raison ; quelque part dans les profondeurs, le couteau a commencé à se salir sur le silicone qui n'avait pas séché. L’opération a donc dû être reportée de quelques jours. Mais cette fois, j'ai mis le moule dans la boîte, mais je ne l'ai pas fermé avec un couvercle, pour qu'il soit mieux aéré et sèche plus rapidement. Alors si vous réalisez un moule très épais, n'hésitez pas à le faire sécher pendant une semaine.
Deux jours plus tard, nous avons pu découper les coquilles. J'ai décidé de ne pas couper au milieu, mais plus près du bord, pour qu'il forme un bol avec un couvercle, à travers lequel je pourrais ensuite remplir le moule de résine. C'est difficile à voir sur la photo ici, mais le silicone collait très bien aux coques à plusieurs endroits. Par conséquent, une fois retiré, le silicone s'est déchiré et est resté sur les coques sous forme de petites pastilles.
Vous devez donc rechercher un autre lubrifiant séparateur ou appliquer davantage de cirage. Mais c'est une arme à double tranchant : si vous appliquez beaucoup de lubrifiant, vous perdrez le détail de la pièce, et en plus, il sera difficile d'appliquer le silicone lui-même sur le lubrifiant, car il est épais et collera n'importe où. , mais pas de la part.
J'ai lubrifié la crosse et en même temps le moule, mélangé la résine, préparé quelques clous pour un poids plus conséquent des projectiles à la sortie. En théorie, vous pouvez abandonner complètement le lit de plâtre car il s’agit d’une hémorroïde supplémentaire. À moins, bien sûr, que vous ne créiez dans un premier temps un moule en silicone sur quelque chose de plat, pour ne pas vous retrouver avec des bananes à la fin. Certes, il est possible que sans un ajustement serré, l'époxy s'écoule par la découpe du moule en silicone.
J'ai placé le moule légèrement incliné pour que la résine remplisse le moule par gravité, j'ai inséré des clous et j'ai progressivement rempli le moule de résine époxy. Comme il était rempli de résine, le moule était fermé, mais de manière à ce qu'il ne reste aucune bulle d'air à l'intérieur.
Après remplissage, j'ai fermé le couvercle et l'ai jeté sur la batterie. Au bout de 2-3 heures, la résine avait déjà durci. Après quoi j'ai retiré les coquilles du moule, à première vue, tout s'est bien passé. Un peu de ponçage et vous pourrez peindre.
Il s'est avéré que je me suis réjoui très tôt, à chaque coulée ultérieure, les coquilles étaient de plus en plus difficiles à démouler. L'époxy adhère de plus en plus étroitement à la chair, au point que le moule commence à se déchirer lorsque le projectile est retiré. Il devenait à chaque fois tout aussi difficile de nettoyer le moule lui-même des gouttes de résine. En général, plus près de la septième approche, le moule a cessé de se fermer hermétiquement, c'est pourquoi il y avait de plus en plus de défauts dans les pièces. Donc, si vous avez besoin de plusieurs copies de quelque chose, vous pouvez utiliser cette méthode, sinon cherchez un séparateur ou versez quelque chose de moins agressif (gypse).
Il semble qu’un autre lubrifiant de séparation soit nécessaire, et sans lui, le processus de clonage des munitions par cette méthode a été suspendu. Après un certain temps, j'ai fabriqué un tel moule composite en résine époxy et je l'ai utilisé pour couler des copies en plâtre des coquilles.
Postface 1
Je suis récemment tombé sur manière intéressante fabriquer du pseudo-silicone à partir de matériaux improvisés (gélatine, glycérine). Donc, si vous avez besoin de prendre rapidement un moulage d'une petite pièce et d'en couler une copie en résine époxy. C'est ici. Il est difficile d'y verser des pièces massives, car le moule a peur de chauffer (si soudainement il y a une réaction excessive dans la résine époxy), mais couler de petites choses est parfait.