Exemples de joug Poka en mécanique. Les méthodes infaillibles sont divisées en trois niveaux par ordre d’efficacité croissante.
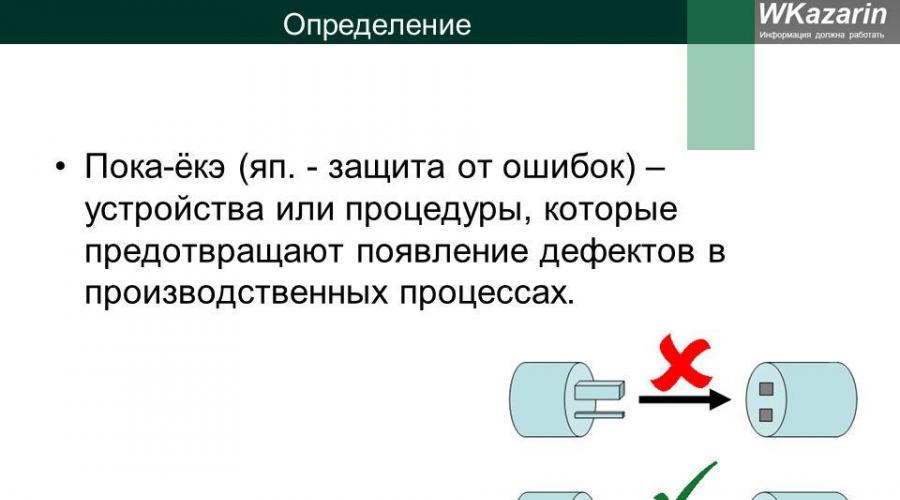
Lire aussi
Définition Poka-yoke (japonais - protection contre les erreurs) - dispositifs ou procédures qui empêchent l'apparition de défauts dans les processus de production.
Poka-yoke. Exemple 2. Une photocellule qui se déclenche si une personne franchit (ou vice versa, ne franchit pas) une ligne de contrôle invisible. Par exemple, un assembleur doit nécessairement prendre et utiliser une certaine pièce.
Types d'erreurs humaines Oubli Manque de compréhension des raisons Sous-estimation Inexpérience Réticence Inattention Lenteur Manque de normes Surprise Intentionnalité
Sources de défauts Opération manquée Erreurs d'usinage Erreur de positionnement des pièces Pièces manquantes Mauvaises pièces Usinage de la mauvaise pièce Opération incorrecte Erreurs de configuration Installation incorrecte de l'équipement Utilisation d'outils ou de montages incorrects Fukushima-1.
Exemple de solution : Traitement de la coulée Problème : Pièces non traitées Solution : Changement de la goulotte pour identifier les pièces défectueuses Description du processus : Les pièces coulées sont traitées sur une machine automatique et transférées au processus suivant via la goulotte. Avant amélioration : Si une pièce non traitée arrive par la goulotte, la machine suivante dans le processus s'arrête anormalement et peut être endommagée. Dessin tiré du livre « Poka-Yoke. Améliorer la qualité des produits en évitant les défauts"
Un exemple de solution à un problème : traitement de fonderie Après amélioration : Pour arrêter une pièce non traitée, une méthode a été développée qui prend en compte la différence de sa Forme géométrique de la pièce traitée. La goulotte a été modifiée pour que la pièce non usinée s'arrête dans un bloc installé dans la goulotte et ne coule pas dans la machine suivante. Cela a évité les pannes de machines. Dessin tiré du livre « Poka-Yoke. Améliorer la qualité des produits en évitant les défauts"
La présentation « ABC » est publiée dans la section Ressources. fabrication au plus juste. Qu’est-ce que le poka-yoke ? Les Poka-yoke (ou poka-yoke) sont des dispositifs ou des procédures qui empêchent l'apparition de défauts dans les processus de fabrication. La présentation donne une définition, répertorie les types d'erreurs humaines et les sources de défauts, et fournit plusieurs exemples.
Ci-dessous dans le texte de la note se trouve le texte d’accompagnement.
De plus, cette présentation en format vidéo avec mes commentaires est publiée sur Youtube.com et Rutube.ru.
Je vous demande de faire part de vos commentaires et suggestions sur les sites youtube et rutube, directement sur la page vidéo, ou via le formulaire présent sur mon site, afin que je puisse en tenir compte dans le futur.
Transcription du texte d'accompagnement
Les Poka-yoke (qui signifie « protection contre les erreurs » en japonais) sont des dispositifs ou des procédures qui empêchent l'apparition de défauts dans les processus de fabrication.
Regardons quelques exemples.
Exemple n°1. La forme du produit est telle qu'il ne peut pas être installé pour une manipulation ou une utilisation dans une position incorrecte (à l'envers ou à l'envers). Vous regardez une disquette de trois pouces qui ne peut être insérée complètement dans le lecteur que dans une seule position.
Exemple n°2. Photocellule qui se déclenche si une personne franchit (ou vice versa ne franchit pas) une ligne de contrôle invisible. Par exemple, un assembleur doit nécessairement prendre et utiliser une certaine pièce.
Les défauts sont dus à des erreurs humaines.
Il existe 10 types d’erreurs humaines qui entraînent des défauts. Ce:
- l'oubli,
- incompréhension des raisons (l'apparition de quelque chose)
- sous-estimation de toute situation (ou incapacité à identifier un objet)
- inexpérience
- réticence (à suivre les procédures et les règles)
- inattention
- lenteur (à prendre des décisions)
- manque de normes
- surprendre
- commettre intentionnellement une erreur (ou un sabotage)
Les sources des défauts sont les faits suivants :
- opération manquée
- erreurs de traitement
- erreurs de positionnement des pièces
- détail manquant
- mauvaise partie
- traiter la mauvaise pièce
- mauvais fonctionnement sur la bonne pièce
- erreurs de configuration
- installation incorrecte de l'équipement et
- utiliser le mauvais outil ou le mauvais accessoire
Regardons un exemple de résolution d'un problème.
Le problème réside dans les pièces brutes. La solution appliquée consistait à modifier la goulotte pour identifier les pièces défectueuses.
Regarde l'image.
Les pièces moulées sont traitées sur une machine automatique et transférées vers le processus suivant via une goulotte.
Avant l'amélioration, voici ce qui se produisait : si une pièce non traitée passe par les goulottes, la machine suivante dans le processus tombe en panne et peut être endommagée.
Pour arrêter une pièce non traitée, une méthode a été développée qui prend en compte la différence de sa forme géométrique par rapport à la pièce usinée. La goulotte a été modifiée pour que la pièce non usinée s'arrête dans un bloc installé dans la goulotte et ne se retrouve pas sur la machine suivante. Cela a évité les pannes de machines.
L'histoire de l'émergence du système « poke-eka »
En 1961, analysant structure de production Entreprises Yamaha Electric, Shingo a formulé la méthode baka-yoke (infaillible). Il est arrivé à la conclusion que le système de contrôle statistique généralement accepté ne prévient pas les défauts. Bien sûr, avec son aide, il était possible de prédire le degré de probabilité d'apparition du prochain défaut, mais ce ne serait qu'un exposé des faits. Shingo a décidé d'implémenter des contrôles dans le processus lui-même. Après tout, le mariage apparaît comme le résultat des erreurs des gens. Les erreurs sont bien sûr inévitables, mais elles peuvent être évitées en créant des machines et des outils avec retour d’information. Une tentative d'insertion incorrecte d'une pièce a immédiatement entraîné un arrêt des travaux. Un signal d'alarme a également été reçu lorsqu'un employé a oublié d'effectuer une opération. Lorsqu’une erreur s’est produite, elle a été identifiée, identifiée et complètement empêchée de se reproduire. Ainsi, Shigeo Shingo a séparé la cause de l'effet - l'erreur du défaut, garantissant une qualité de produit à 100 %. En effet, le contrôle qualité n'était plus effectué par prélèvement d'échantillons sur la table QD, mais directement sur la machine sur tous les produits sans exception. Les résultats ont été immédiats. Par exemple, en 1977 ateliers de fabrication La société Matsushita Electric, où le système Shingo a été introduit, a travaillé pendant 7 mois sans aucun défaut. S. Shingo a commencé à juste titre à utiliser le titre de « M. Amélioration » dans son pays et à l'étranger.
Certes, le nom « infaillible » n'a pas pu résister. Un jour, alors que Shingo présentait une nouvelle méthode aux ouvriers, l’un d’eux s’est écrié : « Je ne suis pas un imbécile ! » J'ai dû m'excuser et donner un nouveau nom à la méthode : le système poka-yoke (protection contre les défauts, ou 0-défaut). Ce système améliore considérablement l'efficacité processus de production, contribuant à réduire les déchets, à réduire les coûts et la perte de temps.
Le concept de la méthode bye-bye
La fabrication zéro défaut repose sur une méthode anti-erreur appelée Poka-Yoke. Le système « Poka-eka » peut être traduit en russe par « résistance insensée ».
L’idée de base est d’arrêter le processus dès qu’un défaut est détecté, d’en déterminer la cause et d’éviter que la source du défaut ne se reproduise. Aucun échantillonnage statistique n’est donc requis. Un élément clé de la procédure est que l'inspection de la source d'erreur est effectuée en tant que partie active du processus de fabrication afin d'identifier les erreurs avant qu'elles ne se transforment en défauts. La découverte d'une erreur arrête la production jusqu'à ce qu'elle soit corrigée, ou le processus est ajusté pour empêcher que le défaut ne se produise. Cela se fait à chaque étape du processus en surveillant les sources potentielles d’erreurs. De cette façon, les défauts sont identifiés et corrigés à leur source plutôt qu’à un stade ultérieur. Naturellement, ce processus est rendu possible par l'utilisation d'outils et de mécanismes avec retour d'information immédiat (le recours au personnel est évité dans le processus en raison de sa faillibilité). Cependant, le recours au personnel est essentiel pour identifier les sources potentielles d’erreur. A l'âge de 40 ans, Shingo apprend et utilise largement Méthodes statistiques contrôle qualité, mais 20 ans plus tard, en 1977, il se dit enfin libéré de leur envoûtement. Cela s'est produit lorsqu'il a observé de ses propres yeux comment, sur la chaîne de montage tuyaux de vidangeà l'usine machines à laver L'entreprise Matsushita de Shizuoka, qui employait 23 travailleurs, a réussi à fonctionner en continu sans aucun défaut pendant un mois, grâce à l'installation de dispositifs Poka-Yeke qui empêchaient l'apparition de défauts. Shingo soutient que le zéro défaut peut être atteint grâce à l'utilisation du contrôle de source et du système Poka-Yeke. Ensemble, ils constituent le « Contrôle Qualité Zéro ».
Ce concept de « zéro défaut » est différent de ce qui est habituellement associé au nom du mentor américain Philip Crosby. Le concept Shingo met l'accent sur l'atteinte du zéro défaut grâce à l'utilisation de bons matériaux. formation d'ingénieur production et la recherche sur les processus de production, plutôt qu'à travers les appels et les slogans associés aux campagnes de qualité menées par les entreprises américaines et d'Europe occidentale. Shingo lui-même, comme Deming et Juran, se montre préoccupé par cette approche américaine, arguant que la publication de statistiques sur les défauts est trompeuse et qu'il faut plutôt rechercher les éléments défectueux du processus de fabrication qui produisent la plupart des défauts des produits.
Le système « bye-bye » est la base d’une production sans défaut.
La plupart des défauts de production résultent d'une variabilité accrue des caractéristiques du processus, qui peut à son tour résulter de :
* des normes ou des procédures documentées mal élaborées ;
ѕ utilisation d'équipements de mauvaise qualité ou obsolètes ;
* utilisation de matériaux inadaptés ;
* usure des outils ;
* erreurs de l'opérateur.
Pour toutes ces causes de défauts, à l’exception de la dernière, des actions correctives et préventives peuvent être prises. Il est assez difficile d'éviter les erreurs des opérateurs.
L’idéologie sous-jacente du poke-eka est le fait qu’il est naturel que les gens commettent des erreurs dans le processus de travail. Et ce n’est pas un indicateur du manque de professionnalisme de l’opérateur. Le but du poke-ek est de trouver des moyens de se protéger contre les erreurs involontaires. Une liste des actions typiques de l'opérateur qui conduisent à des défauts est présentée dans le tableau.
La méthode poke-eka repose sur sept principes :
1 utiliser une conception robuste pour créer des processus efficaces ;
2 travailler en équipe : c’est le seul moyen de valoriser les connaissances de vos collaborateurs ;
3 éliminer les erreurs, également en utilisant une conception robuste : cela rapprochera le nombre d'erreurs de zéro ;
4 éliminer les causes profondes des défauts en utilisant la méthode des 5 Pourquoi ;
5 agir immédiatement, utiliser toutes les ressources possibles ;
6 éliminer les activités sans valeur ajoutée ;
7 mettre en œuvre des améliorations et réfléchir immédiatement à d'autres améliorations.
Lorsqu'ils utilisent poke-eka, ils ne comptent pas sur les opérateurs eux-mêmes pour trouver l'erreur. Par conséquent, lors de l'exécution de travaux, des capteurs tactiles et d'autres appareils sont utilisés. Cela permet d’identifier efficacement les défauts manqués par les opérateurs.
La méthode poke-ek doit être utilisée à la fois lors de l’inspection à l’arrivée et tout au long du processus. L'effet de sa mise en œuvre dépend de l'étape du processus - contrôle entrant ou contrôle en cours de processus - où cette méthode a été utilisée. Dans ce cas, si des incohérences sont identifiées, des signaux d'avertissement sont reçus ou même l'équipement peut être arrêté.
L'introduction de la méthode poke-ek lors du contrôle des entrées est appelée une approche proactive. Dans ce cas, la détection d'une erreur se produira avant que certaines opérations n'aient été effectuées, que des signaux d'avertissement soient utilisés ou même que l'équipement puisse être arrêté au niveau du contrôle de sortie.
L'approche dans laquelle la méthode poke-eka est appliquée à d'autres étapes du processus de production est dite réactive. Dans ce cas, cette méthode est utilisée :
* immédiatement après la fin du processus ;
* pendant le travail de l’opérateur ;
* lors d'un transfert vers étape suivante processus.
L'approche réactive est efficace car elle permet d'éviter que des produits défectueux ne soient transmis à l'étape suivante du processus, mais n'obtient néanmoins pas autant d'effets. haut degré protection contre les erreurs, comme c’est le cas avec l’approche proactive. L'utilisation de méthodes poke-ek dans le processus de recherche des causes des défauts ne donne pas de résultats élevés, mais en même temps, elle est beaucoup plus efficace qu'un contrôle sélectif.
Il existe d’autres approches pour utiliser la méthode poke-eka : le contrôle et l’avertissement. Avec une approche de surveillance, si un défaut est détecté, l'équipement s'arrête automatiquement. La démarche d'alerte repose sur l'utilisation de différents moyens de signalisation (signaux lumineux et sonores), qui informent l'opérateur sur erreur possible. L’arrêt des équipements n’est souvent pas une option dans l’approche préventive.
Les appareils utilisés dans le poke-eka, selon la méthode qui sous-tend leur fonctionnement, sont divisés en :
* contact;
* en lisant;
* mouvement séquentiel.
Les trois types de dispositifs peuvent être utilisés aussi bien dans une approche de contrôle que dans une approche préventive.
Le principe de fonctionnement des dispositifs à méthode de contact repose sur la détermination si l'élément sensible est en contact avec l'objet testé. Un exemple de tels dispositifs sont les interrupteurs de fin de course. Si le contact est rompu, un signal sonore est par exemple déclenché.
De plus, les appareils fonctionnant par contact comprennent les émetteurs et les récepteurs, les interrupteurs photoélectriques, les capteurs piézoélectriques, etc. Il n'est pas nécessaire que les appareils soient de haute technologie. De simples appareils passifs sont parfois les meilleurs. Ils empêchent que les pièces soient placées dans la mauvaise position pendant le processus.
Les lecteurs sont utilisés lorsqu'il y a un nombre fixe d'opérations dans un processus et un nombre fixe de pièces dans un produit. Le capteur compte les pièces plusieurs fois et transmet le produit au processus suivant uniquement si le nombre de pièces est correct.
Le troisième type d'appareil est constitué de capteurs qui déterminent si une opération de processus est terminée. Si l'opération n'est pas terminée ou n'est pas effectuée correctement, le capteur signale que l'équipement doit être arrêté. De nombreux capteurs et dispositifs photoélectriques connectés à une minuterie d'équipement fonctionnent sur ce principe. L'utilisation de tels dispositifs est plus efficace lorsque le processus utilise de nombreuses pièces similaires en forme et en taille.
L'application cohérente de la méthode poke-eka peut réduire considérablement le nombre d'erreurs commises par les opérateurs, ce qui contribue à réduire les coûts et à accroître la satisfaction des clients.
Un jour, il m'est arrivé d'observer situation similaire: le projet a été mal préparé et lancé très précipitamment. En conséquence, le processus mis en place s’est avéré totalement inadapté à la production de masse, ce qui a affecté la relation avec le client. Il était nécessaire d'agir immédiatement afin de ne pas "perdre" complètement le client. La première chose par laquelle la direction de l'organisation a commencé a été la réorganisation du département, en particulier, une décision a été prise pour remplacer le chef du département. cela vaut la peine de me corriger : j'ai dit que j'avais eu la chance d'observer cette situation, en fait, ce n'est qu'à partir de ce moment-là que j'ai été affecté à ce département, c'est-à-dire que je devais non pas observer la situation, mais la « pelleter ». Mais ce n'est plus le cas maintenant...
Il existe un tel concept dans langue anglaise« Réunion de lancement » peut être traduit de différentes manières – de « réunion de planification » à « débriefing ». Dans ce cas-ci, il s'agissait d'un discours introductif du nouveau patron, appelant à briser la situation actuelle et à dès que possible amener le niveau de qualité au niveau requis par le client. Permettez-moi de présenter brièvement la situation : 38 % de rendement du procédé (CFTY) et retard de 3 livraisons de produits (plus de 10 000 unités de produits finis). Dans la partie du discours qui concernait les ingénieurs, le nouveau patron a prononcé une phrase très intéressante :
- «Prenons Alex par exemple. Lors de la création de la conception de l'installation, il s'est basé sur son expérience, sa formation et sa connaissance du but de l'appareil. Mais s'il avait eu la chance de travailler avec lui pendant 12 heures en tant qu'opérateur sur un quart de travail, il aurait peut-être apporté quelques changements supplémentaires. Peut-être qu'on devrait te faire travailler par quarts ? Après tout, pendant long travail Des situations inhabituelles surgiront certainement… »
Voici un point intéressant : une personne n'est pas un robot, peu importe la façon dont vous l'enseignez, mais lors d'un travail à long terme, des erreurs ou des situations non standard surviennent inévitablement et conduisent à des erreurs. Il semblerait inutile de lutter contre le phénomène du facteur humain : tout processus auquel une personne participe est susceptible d'erreurs de la part des opérateurs. Cependant, vous pouvez réduire, ou essayer de réduire, la fréquence de ces erreurs au minimum. Créez un processus ou un ajout à celui-ci qui éliminera l'apparition d'erreurs.
Par exemple, le processus de tricotage des faisceaux automobiles : toutes les connexions sont conçues de telle manière qu'il est extrêmement difficile de mélanger les fils. Avec carte SIM téléphone mobile un des coins est "coupé", ce qui rend impossible une mauvaise installation. Les connecteurs des câbles sont à l'intérieur unité système ordinateur personnel avoir formes différentes, ce qui élimine la possibilité de connecter l'alimentation au connecteur du câble pour le transfert de données et vice versa.
Qu’ont en commun les exemples ci-dessus ? – Configuration du système qui élimine les erreurs humaines – Protection contre les erreurs – Poka Joug.
Poka Yoke est une philosophie de gestion de la qualité et d'amélioration continue des processus visant à éliminer la possibilité d'erreur humaine. Poka Yoke est une expression japonaise qui signifie littéralement « protection contre les erreurs ».
La mise en œuvre pratique du principe Poka Yoke peut être considérée sous deux angles :
- d'une part, et c'est la voie privilégiée, la protection contre les erreurs est un système dans lequel l'apparition d'une erreur est exclue ;
- d'autre part, c'est un système qui empêche qu'un produit défectueux n'atteigne la prochaine opération, station, site, ligne ou client.
Il convient de préciser que l'introduction d'un contrôle à 100 % signifie l'ajout d'une station ou d'une opération distincte à processus existant et n'est pas une mise en œuvre du principe Poka Yoke. Souvent, une telle solution nécessite des coûts supplémentaires, augmente la quantité de ressources consacrées à la fabrication des produits et augmente leur coût. Contrairement à un contrôle supplémentaire, l’application du principe anti-erreur pour empêcher l’entrée d’un produit défectueux ne nécessitera pas de ressources supplémentaires et n’affectera pas le coût de production.
Prenons exemple réel de la pratique. De temps en temps, le même défaut apparaissait sur les phares de voiture, qui étaient assemblés selon la méthode du convoyeur - une égratignure sur la lentille. Il s'est avéré que le phare avait été rayé sur l'un des dispositifs en forme de U du convoyeur. Cela ne se produisait que dans les cas où le phare était mal installé sur la base - le bord sous-pressé dépassait plus haut qu'il ne le devrait et, lors du déplacement le long du convoyeur, il s'accrochait au dispositif mentionné ci-dessus.
Comment éliminer ce défaut ?
- Achetez un appareil automatique qui installe le phare sur la base.
- Faites en sorte que tous les opérateurs contrôlent la position du phare sur une base.
- Placer une personne distincte chargée de surveiller la position des phares sur la base.
Il existe de nombreuses solutions et elles sont toutes variées, mais elles ont une chose en commun : le désir d'ajouter quelque chose au processus. Quelque chose qui nécessite des coûts supplémentaires et réduit éventuellement la productivité de la ligne.
Il est devenu possible d'éliminer ce défaut en mettant en œuvre le principe du Poka Yoke : une plaque en matériau souple, mais suffisamment dur pour ne pas rater le produit, a été installée sur l'appareil, ce qui a provoqué des rayures sur les phares. La plaque était trivialement vissée au cadre en forme de U de l'appareil et arrêtait simplement la pièce, l'empêchant de passer plus loin.
Autre exemple : tous les produits multimédia disposent d'une certaine quantité de mémoire. La partie « mémoire » du produit est fabriquée et programmée séparément de l'ensemble du produit. Le processus de configuration de l'appareil comprend les étapes suivantes :
- vérification de l'appareil ;
- programmation de « bas niveau » ;
- vérification du code du programme ;
- installation d'un code de sécurité ;
- tests fonctionnels de l'appareil (simulation de fonctionnement en conditions réelles).
Toutes ces étapes sont effectuées automatiquement en 40 à 70 s. et ne sont pas perceptibles par l'opérateur. Tout ce que l'opérateur voit, ce sont des indicateurs verts ou rouges, indiquant la réussite ou l'échec de l'opération. Guidé par la commande du programmateur, l’opérateur trie sur place les pièces ayant subi l’opération en « bonnes » et « mauvaises ». Veuillez noter qu'il est possible que l'opérateur se trompe et place la pièce dans le mauvais conteneur.
Sur le site d'assemblage final, le code de série du produit et le bloc mémoire sont scannés. Si une pièce ne passe pas par le programmateur, un message d’erreur apparaîtra sur l’écran de l’opérateur sur fond rouge, vous demandant de remplacer la pièce. La connexion de deux machines à une seule base de données sert de système pour empêcher les pièces de mauvaise qualité d'entrer dans le produit.
Malheureusement, Poka Yoke n'est qu'une philosophie d'assurance qualité et ne contient pas recommandations pratiques pour améliorer des processus spécifiques. Néanmoins, nous tenterons de formuler les postulats et principes de base de mise en œuvre de cette technique.
L’application de l’approche peut être divisée en plusieurs étapes :
- Déterminer les priorités des problèmes - cette étape est le début conditionnel du processus. Le but de cette étape est de classer tous les problèmes existants et d’orienter les efforts vers les plus fréquemment rencontrés.
- Effectuer une analyse - dès que possible problème important, les causes profondes de son apparition doivent être découvertes. L'approche Poka Yoke consiste à apporter des modifications qui éliminent complètement le défaut. La mise en œuvre d’une telle approche n’est possible qu’en luttant contre les causes des défauts. Par conséquent, le principe de protection contre les erreurs s'applique uniquement lorsque les efforts visent à prévenir l'erreur/la cause, et non le défaut, qui est le résultat de l'erreur.
- Mise en œuvre des changements - il est extrêmement difficile de décrire la phase créative du processus, mais il est très important de noter une caractéristique de cette étape : l'implication du personnel. Comme pour beaucoup d’autres démarches d’assurance qualité « à la japonaise », le facteur clé de succès est l’implication active du personnel dans le processus d’amélioration continue. Ainsi, à ce stade, le rôle principal est joué par les employés directement impliqués dans cette opération particulière. Cette approche présente deux avantages indéniables : -d'une part, seul l'opérateur connaît toutes les subtilités du travail sur un lieu de travail donné, d'autre part, la mise en œuvre des changements est beaucoup plus facile et plus rapide avec la participation directe des travailleurs.
Il existe trois manières (ou directions) principales d’introduire le changement :
- Changer le processus pour que l'échantillon défectueux soit définitivement remarqué par l'opérateur. Un exemple est une liste de contrôle remplie par l'opérateur pour chaque produit. Cet exemple très efficace lors de l'assemblage par une seule personne de produits complexes, notamment de moules, ainsi que sur les lignes de conditionnement de produits tels que les appareils électroménagers.
- Créer des conditions dans lesquelles un échantillon défectueux ne peut pas passer à l'étape suivante du processus, comme par exemple le cas décrit ci-dessus avec la création d'une base de données commune pour le programmeur et la station de numérisation de pièces.
- Créer un processus dans lequel les erreurs sont exclues. Un excellent exemple est décrit ci-dessus pour la chaîne de montage de phares d'automobiles - les rayures sur les lentilles de phares mal installés ne peuvent tout simplement pas se produire. Un tel phare ne pourra pas pénétrer dans la zone à risque potentiel.
Il existe de nombreux domaines d'application du principe de protection contre les erreurs, concentrons-nous sur l'un d'entre eux : la sécurité humaine. DANS la société moderne Nous utilisons de nombreux appareils et appareils pour nous aider à travailler ou à nous détendre. Les avantages de tous ces éléments sont à la limite du danger énorme qu'ils peuvent présenter pour la vie et la santé de l'utilisateur. Vous trouverez ci-dessous des exemples de la manière dont l’approche Poka Yoke a été mise en œuvre pour garantir la sécurité de la vie humaine :
- Sécurité enfants sur les portes de voiture : une porte sur laquelle cette option est installée ne peut pas être ouverte de l'intérieur.
- Doubles bouchons sur les flacons de pilules et Produits chimiques ménagers empêcher l’ouverture accidentelle et l’accès des enfants.
- Capteurs de flamme à proximité brûleurs à gaz cuisinières: lorsque la flamme du brûleur s'éteint, l'alimentation en gaz est automatiquement coupée.
- Le four à micro-ondes s'arrête automatiquement lorsque la porte est ouverte. Cela évite l'exposition aux ondes nocives et la possibilité de dommages aux membres.
- Pression manuelle à double bouton-poussoir : L'opérateur doit utiliser ses deux mains pour appuyer sur deux boutons. Cela élimine la possibilité de nuire à la santé de l'opérateur.
- Composants supplémentaires sur cartes de circuits imprimés, sensible aux décharges : lorsqu'une charge apparaît sur le boîtier ou sur une autre surface, le composant grille, ce qui évite à l'utilisateur de recevoir un choc électrique.
- Un excellent exemple de mise en œuvre du principe est montré dans la vidéo : une scie centrifuge s’arrête au moindre contact avec les doigts d’une personne.
La philosophie de gestion de la qualité, basée sur l'élimination de la possibilité d'erreurs du système, vise non seulement à réduire les défauts du processus, mais également à trouver des solutions qui ne nécessitent pas de coûts importants. Cette fonctionnalité distingue Poka Yoke des autres méthodes d’amélioration des processus. La méthodologie d'application de l'approche ne se limite pas à un ensemble spécifique d'outils ou de méthodes, ce qui la rend universelle et facilement applicable à n'importe quel domaine de l'activité humaine.