Zusammensetzung des Straßenbetons und Grundvoraussetzungen für die Verlegung von Straßenbelägen. Einbau von Betonböden – Arbeitsablauf und ihre Merkmale Einbau von Stahlbetondecken
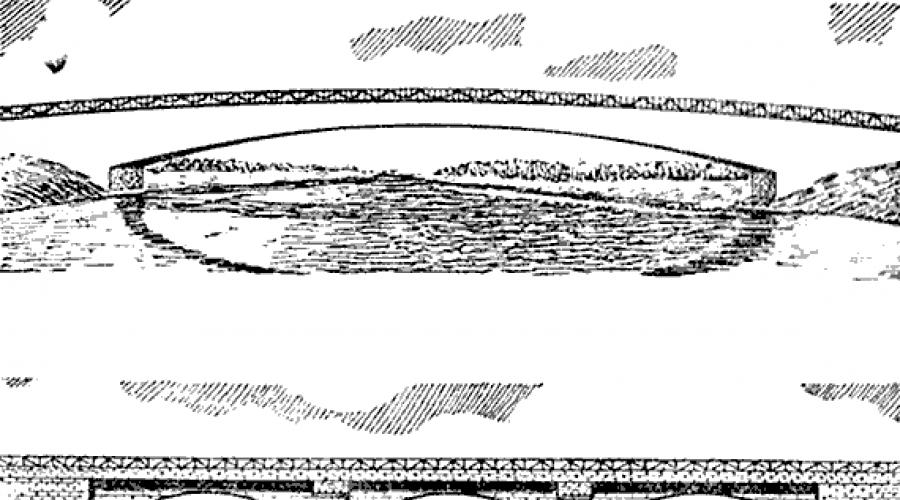
Betone sind künstliche Materialien, die durch das Kleben (Befestigen) von Natursteinmaterialien – Sand und Kies oder Schotter – zu einem monolithischen, haltbaren Stein gewonnen werden. Beton unterscheidet sich durch das Bindemittel, das die Körner von Natursteinmaterialien zusammenhält. Die gebräuchlichste Art ist Zementbeton, bei dem Zement das Bindemittel ist. Asphaltbeton und Teerbeton werden häufig im Straßenbau verwendet; Als Bindemittel dienen darin Bitumen und Teer. Es gibt noch andere Betonarten: Gipsbeton, Kalkbeton usw.
Unsere Broschüre widmet sich der Beschreibung der Eigenschaften von Zementbeton. In Zukunft nennen wir es einfach Beton.
Beton ist ein weit verbreiteter Baustoff. Daraus hergestellte Strukturen sind oft auf Straßen zu sehen.
Eine Betonkonstruktion, sei es eine Brückenstütze, ein Durchlass oder eine Betonfahrbahndecke, erweckt optisch den Eindruck, aus grauem Stein zu bestehen. Mit dem Wort „Stein“ verbinden wir meist die Vorstellung eines toten, unbeweglichen Materials, das seine Eigenschaften über Jahrzehnte und Jahrhunderte hinweg nicht verändert.
Die Vorstellung von Zementbeton als einem solchen Stein ist nur mit richtig draußen. Tatsächlich ist Beton ein künstlicher Stein, in dem die Prozesse der Entwicklung, des Wachstums und des Alterns kontinuierlich ablaufen; ein Stein, der wächst, stärker wird, altert und stirbt. Tatsächlich ist das Hauptmerkmal von Zementbeton im Vergleich zu anderen Steinen die Ausbildung seiner Eigenschaften direkt auf der Baustelle – im Bauwerk. Dies allein verleiht allen mit Beton ausgeführten Arbeiten einen einzigartigen Charakter. Beton muss nicht nur vorbereitet, sondern auch verdichtet werden und dann müssen Bedingungen geschaffen werden, unter denen er eine hohe Festigkeit erhält.
Der Zementleim in der Zusammensetzung Beton härtet aus, hält zusammen, verklebt einzelne Sandkörner, einzelne Schotter zu einem Monolithen, der je nach Festigkeit des Zementsteins, der Festigkeit der Steinmaterialien und der Haftung eine hohe Festigkeit aufweist Festigkeit von Zementit und Stein-zu-Stein-Materialien.
Die Mischung aus Zement, Wasser und Sand wird Mörtelmischung genannt, nach dem Aushärten Mörtel. Eine Mischung aus Zement, Wasser, Sand und Schotter oder Kies in bewegtem Zustand wird als Betonmischung bezeichnet. Das ausgehärtete steinartige Material wird, wie oben erwähnt, Beton genannt.
Die Betonvorbereitung auf der Baustelle erfolgt durch Bauherren; Daher haben sie die Fähigkeit, die Eigenschaften von Beton während seines Herstellungsprozesses zu beeinflussen und die Eigenschaften des resultierenden Materials zu regulieren.
Die Haupteigenschaft jedes Baumaterials ist seine Festigkeit.
Beton hat eine hohe Festigkeit, insbesondere unter Druck. Ein Betonwürfel mit einer Seitenlänge von 10 Zentimetern hält einer Belastung von 20-40 Tonnen stand, also dem Gewicht eines Güterwaggons. Moderner Beton weist eine noch höhere Festigkeit auf und hält einer Belastung von 500 bis 600 Kilogramm pro Quadratzentimeter Fläche stand. Die Zugfestigkeit von Beton ist deutlich geringer. Wenn eine Betonprobe oder -struktur gedehnt wird, erfolgt die Zerstörung mit 10-15-mal geringeren Kräften als beim Komprimieren. Dies ist der Unterschied zwischen den Eigenschaften von Beton und Stahl und anderen Metallen, die sowohl bei Zug als auch bei Druck ungefähr die gleiche Festigkeit aufweisen.
Viele Gebäudestrukturen unterliegen im Betrieb Biegekräften. In diesem Fall ist für die Widerstandsfähigkeit des Betons gegen die Einwirkung zerstörerischer Kräfte seine Zugfestigkeit von größter Bedeutung.
Die Entdeckung und weit verbreitete Verwendung eines neuen Materials im Bauwesen – Stahlbeton – beseitigte die Nachteile von Beton als Baustoff. Stahlbeton hat im modernen Bauwesen einen festen Platz erobert. Es vereint die Eigenschaften von Beton – hohe Druckfestigkeit, Wasser- und Luftbeständigkeit, Feuerbeständigkeit – mit Eigenschaften von Stahl wie Zugfestigkeit und Elastizität. IN Stahlbetonkonstruktionen Dort, wo diese Bauwerke Zugkräften ausgesetzt sind, werden Stahlstangen eingebaut, die die Wirkung dieser Kräfte wahrnehmen. Die Stahlmenge und ihre Lage im Beton werden rechnerisch ermittelt. Abbildung 1 zeigt, wie Beton und Stahl in einem neuen Material, Stahlbeton, zusammenwirken.
Abb.1. Beispiele zum Vergleich der Eigenschaften von Beton und Stahlbeton
Mittlerweile ist Stahlbeton weit verbreitet; Es wird zum Bau von Dämmen und Brücken, Straßenbelägen für Autobahnen und Flächen für Flugzeuglandebahnen, Tunneln, Rohren, Tanks, Strukturen von Wohn- und Industriegebäuden (Säulen, Balken, Bodenplatten, Treppen usw.) und sogar Flüssen und Meeren verwendet Gefäße. Beton ganz ohne Stahl, sogenannte „Bewehrungsstäbe“, wird heute nur noch selten verwendet, die Eigenschaften von Zementbeton bestimmen jedoch weitgehend die Eigenschaften von Stahlbeton.
Der Einsatz von Beton im Straßenbau nimmt rasant zu, daher sollte jeder Straßenbauer die Eigenschaften dieses Materials genau kennen.
Beton weist eine hohe Beständigkeit gegenüber natürlichen Einflüssen wie Benetzung und Trocknung, Abkühlung und Erwärmung, Gefrieren und Auftauen, Abrieb und Erosion auf. Es ist ein unverzichtbares Material für langlebige Bauwerke, die Dutzende und Hunderte von Jahren halten sollen.
Ein wichtiger Vorteil von Beton ist die Möglichkeit, für seine Herstellung lokale Materialien zu verwenden. Nur ein Zehntel des Betons (nach Gewicht) besteht aus künstlichem Material – Zement, die restlichen neun Zehntel sind Natursteinmaterialien und Wasser, die nur abgesaugt und auf die Baustelle geliefert werden müssen.
Beton ist in keiner Weise mit Holzwerkstoffen zu vergleichen, die durch Verrottung zerstört werden, leicht Feuer fangen und daher für den Bau dauerhafter Bauwerke ungeeignet sind. Stahl zersetzt sich relativ schnell, wenn er feuchter Luft ausgesetzt wird. Es kann nicht für den Bau von Gebäudewänden verwendet werden, da es Wärme leicht leitet; Angesichts dieser Eigenschaft müssten Stahlwände 40-mal dicker als Betonwände gebaut werden; Stahl ist dreimal schwerer als Beton.
Für den Bau von Autobahnen, auf denen sich Fahrzeugströme verschiedener Art schnell bewegen, ist Beton ein unverzichtbarer Werkstoff. Brücken, Durchlässe, Stützmauern und Viadukte werden aus Stahlbeton gebaut. Fahrbahnbeläge auf Autobahnen und Untergründe für Asphaltbetondecken werden zunehmend aus Zementbeton hergestellt.
Auf Beschluss der Partei und der Regierung wird in unserem Land die Fabrikproduktion von vorgefertigtem Stahlbeton weit verbreitet, deren Verwendung zur Industrialisierung des Bauwesens führt und nur den Zusammenbau einer Struktur aus vorgefertigten Teilen auf einer Baustelle ermöglicht.
In Straßenoberflächen widersteht Beton der Abnutzung durch vorbeifahrende Fahrzeuge und überträgt und verteilt die Last von den Fahrzeugrädern auf den Boden. Bei Brückenkonstruktionen hält Beton hohen Belastungen durch über die Brücke fahrende Autos, Busse und Straßenbahnen stand und widersteht auch der erodierenden Wirkung von Wasser auf die Brückenstützen. An den Betonbullen brechen mächtige Eisschollen, die vom Fluss in die Eisdrift getragen werden. Jetzt ist es schwer vorstellbar, wie der Bau durchgeführt würde, wenn die Menschen keinen Zementbeton hätten. Viele Bauwerke, die heute aus Stahlbeton und Beton gebaut werden, würden viel mehr Arbeit und Kosten erfordern, wenn man versuchen würde, andere Materialien zu verwenden, und andere wären völlig undurchführbar.
Vergleicht man eine Steinbrücke mit einer Brücke aus modernem Stahlbeton, so stellt man einen großen Unterschied in der Materialmenge und im Erscheinungsbild der Bauwerke fest (Abb. 2). Es ist jedem klar, was was ist weniger Materialien Je billiger die Struktur ist, desto rentabler ist sie.
Abb.2. Stahlbetonbrücke und Natursteinbrücke
Im Folgenden werden die Eigenschaften von Beton und seine Verwendung im Straßenbau beschrieben.
Vorbereitung der Betonmischung
Um aus Stoffen mit unterschiedlichen Eigenschaften wie Wasser, Zement, Sand und Schotter oder Kies ein Material mit genau definierten Eigenschaften – Beton – zu erhalten, müssen eine Reihe von Arbeitsgängen durchgeführt werden. Es ist wichtig, die technischen Regeln und Anweisungen zu befolgen. Obwohl die Herstellung von Beton oft direkt auf der Baustelle stattfindet, erinnert sie auch in diesem Fall an eine Fabrikproduktion.
Aus guten Zement- und Steinmaterialien können Sie starken und stabilen Beton erhalten, aber Sie können ihn ruinieren, wenn Sie gegen die Regeln für die Vorbereitung und Herstellung von Beton verstoßen. Zunächst muss die Zusammensetzung der Betonmischung bestimmt werden – das Verhältnis aller Materialien dafür. Wie viel Zement und andere Materialien in welchem Verhältnis entnommen werden müssen, bestimmt das auf jeder Baustelle vorhandene Labor. Vor der Auswahl der Betonzusammensetzung müssen die Anforderungen an diesen Beton bekannt sein. Bei der Gestaltung eines Bauwerks werden je nach Verwendungszweck des Betons bestimmte Anforderungen an die Festigkeit und andere technische Eigenschaften gestellt.
Die Festigkeit von Beton wird als Güteklasse angegeben. Die Dauerhaftigkeit von Beton drückt sich in den meisten Fällen in der Anforderung an seine Frostbeständigkeit aus. Die klimatischen Bedingungen unseres Landes erfordern Beton mit sehr hoher Frostbeständigkeit. Damit Beton diese Anforderungen erfüllt, muss Portlandzement mit einer bestimmten mineralogischen Zusammensetzung und einer Güteklasse von mindestens 500 verwendet werden; Es dürfen nur Steinmaterialien verwendet werden, die auf Frostbeständigkeit geprüft sind und das Wasser-Zement-Mischungsverhältnis sollte nicht höher als 0,50 sein. Wenn alle diese Anforderungen erfüllt sind, weist Beton eine hohe Frostbeständigkeit auf. Ebenso wichtig ist es bei der Festlegung einer Betonzusammensetzung, sicherzustellen, dass die Eigenschaften der Betonmischung mit den verfügbaren Mechanismen für ihre Verdichtung und Platzierung übereinstimmen.
Diese Übereinstimmung wird durch die Wahl der Zusammensetzung der Mischung erreicht, die ihr eine gewisse Beweglichkeit verleiht. Die Verflüssigungsgeschwindigkeit einer Betonmischung beim Rütteln wird auch Verarbeitbarkeit genannt.
Die Mobilität der Betonmischung wird auf folgende Weise bestimmt. Die Betonmischung wird in eine Metallform gefüllt – ein Kegel ohne Boden, der auf einem flachen Ständer installiert ist. Der Kegel wird entfernt und das Absinken (Sinken) der Betonmischung nach dem Entfernen gemessen. Die Beweglichkeit einer Betonmischung wird in Zentimetern des Setzmaßes der Mischung im Vergleich zur ursprünglichen Höhe ausgedrückt.
Um die Verarbeitbarkeit zu bestimmen, wird der Kegel in die Form von Proben gebracht – Würfel mit einer Seitenlänge von 20 Zentimetern. Die Form mit Kegel wird auf einer Laborvibrationsplattform befestigt (Abb. 3). Der Kegel wird wie bei der Bestimmung der Mobilität mit Betonmischung gefüllt, die Kegelform entfernt, die Rüttelplattform eingeschaltet und die Zeit der Ausbreitung der Betonmischung in der Form bestimmt. Der Verarbeitbarkeitsindikator ist die Zeit in Sekunden, die die Mischung benötigt, um sich in der Form zu verteilen.
Abb. 3. Bestimmung der Verarbeitbarkeit einer Betonmischung:
Auf der linken Seite ist eine Form mit einem Kegel zu sehen, der vor dem Vibrieren mit Betonmischung gefüllt wird.
rechts - eine Form mit einer Betonmischung nach dem Rütteln
Für gewöhnlichen Straßenbeton wird eine Mischung mit einem Kegelausbreitmaß von 2–3 Zentimetern und einer Verarbeitbarkeit von 20–25 Sekunden verwendet. Bei dünnwandigen und dicht bewehrten Konstruktionen sollte das Setzmaß des Betonmischungskegels 5–6 Zentimeter bei einer Verarbeitbarkeit von 5–10 Sekunden betragen.
Die Hauptanforderung, die normalerweise bei der Auswahl der Betonzusammensetzung für Straßenoberflächen und für verstärkte Konstruktionen beachtet wird, ist das Ausfüllen aller Hohlräume zwischen Partikeln größeren Materials kleine Partikel. Darüber hinaus ist es notwendig, eine Gleitschicht aus Zementleim auf der Oberfläche der Zuschlagstoffpartikel zu erzeugen, um eine bewegliche Mischung zu erhalten.
Abb.4. Auswahlschema für die Betonzusammensetzung
Abbildung 4 zeigt deutlich den Fortschritt bei der Auswahl der Betonzusammensetzung. Zunächst wird die Zementmenge angegeben oder anhand von Hilfstabellen die benötigte Wassermenge für eine bestimmte Mischung berechnet. Anschließend wird das Wasser-Zement-Verhältnis W/Z bestimmt. Dieses Verhältnis ist sehr wichtig für die Charakterisierung der Qualität und Eigenschaften von Zementstein und Beton. Es ist klar, dass die Festigkeit des Zementklebers umso geringer ist, je stärker er verdünnt ist. Bei der Auswahl der Betonzusammensetzung einer bestimmten Festigkeit werden Diagramme der Abhängigkeit der Betonfestigkeit vom W/Z verwendet, die auf der Grundlage experimenteller Daten erstellt wurden. Abbildung 5 zeigt ein Beispiel für ein solches Diagramm für Beton auf Basis von Zement unterschiedlicher Qualität und Schotter. Bei großes Volumen Während der Arbeiten wird empfohlen, die Betonzusammensetzung vorab im Labor auszuwählen und für diese Materialien experimentell die Abhängigkeit der Betonfestigkeit vom Wasser-Zement-Verhältnis zu bestimmen. Nachdem der Zement- und Wasserverbrauch ermittelt wurde, wird die Menge der mineralischen Materialien – Sand und Schotter – so berechnet, dass ihr Volumen zusammen mit dem Volumen des Zementleims 1000 Liter (1 Kubikmeter) beträgt. Nach vorläufige Berechnungen Es ist notwendig, eine Probemischung der Betonmischung durchzuführen, ihre Verarbeitbarkeit zu überprüfen und Kontrollproben anzufertigen. Wenn sich bei der Prüfung herausstellt, dass die Verarbeitbarkeit der Betonmischung von der angegebenen abweicht, wird die Zusammensetzung des Betons durch Änderung des Zement- und Wassergehalts korrigiert, wobei das Wasser-Zement-Verhältnis unverändert bleibt.
Abb.5. Diagramm der Abhängigkeit der Betonsorte vom Wasser-Zement-Verhältnis für Zemente verschiedener Qualitäten (die Zahlen über den Kurven geben die Zementsorte an).
Sobald die Zusammensetzung des Betons festgelegt ist, wird er in das Betonwerk überführt. Um die Komponenten genau zu wiegen, werden in modernen Betonwerken automatische Wiegespender eingesetzt, die eine bestimmte Portion eines beliebigen Schüttguts oder Wassers abwiegen. In kleinen Betonmischanlagen werden einfachere Spender verwendet, beispielsweise Behälter oder Kisten, die auf gewöhnlichen Hundertstelwaagen montiert sind.
Eine genaue Messung der Betonbestandteile ist notwendig, um sicherzustellen, dass seine Eigenschaften mit den angegebenen übereinstimmen und die erforderliche Homogenität der Mischung gewährleistet ist. Darüber hinaus führt eine Ungenauigkeit bei der Dosierung zu einem übermäßigen Verbrauch von Zement – dem teuersten Bestandteil von Beton. Daher modern Technische Regeln erfordern die obligatorische Verwendung einer nicht massenhaften Dosierung aller Materialien.
Der nächste Arbeitsgang ist das Mischen der Betonmischung. Das Mischen erfolgt in speziellen Maschinen – Betonmischern. Unsere Branche produziert mobile und stationäre Betonmischer unterschiedlicher Kapazität für unterschiedliche Arbeitsbedingungen mit einem Mischtrommelvolumen von 100 bis 4500 Litern. Zur Herstellung starrer Mischungen werden Betonmischer mit Zwangsmischung hergestellt. Herkömmliche Betonmischer mischen die Betonmischung, indem sie sie mit Schaufeln drehen, während die Trommel rotiert. Abbildung 6 zeigt die beiden gängigsten Betonmischertypen. Nach dem Mischen wird die Mischung durch Kippen der birnenförmigen Trommel oder durch eine in die Trommel eingeschobene Wanne ausgetragen.
Abb.6. Betonmischer verschiedene Designs
Herkömmliche Betonmischer arbeiten nach diesem periodischen Zyklus. Es gibt aber auch Durchlaufbetonmischer, die bei kleineren Baugrößen eine deutlich höhere Produktivität aufweisen.
Leistung des Betonmischers periodische Aktion variiert je nach Kapazität. Bei einem durchschnittlichen Fassungsvermögen fasst er im beladenen Zustand 1200 Liter Trockenmaterial und produziert etwa 800 Liter Transportbeton. Die stündliche Produktivität beträgt etwa 15 Kubikmeter Mischung. Ein kontinuierlicher Betonmischer ist wirtschaftlicher und für eine Produktivität von 100-200 Kubikmetern pro Stunde ausgelegt.
Im Straßenbau sind mobile Betonmischer weit verbreitet, da der Transport der Betonmischung schwierig und technisch inakzeptabel wird, wenn die Materialien per Bahn oder Wassertransport ankommen und große Entfernungen von den Fundamenten bis zur Einbaustelle zurückgelegt werden. Bei längerem Transport des Gemisches verändert sich seine Mobilität und seine Qualität verschlechtert sich; Daher neigen Straßenarbeiter dazu, trockene Materialien zu transportieren und sie am Einbauort in einem mobilen Betonmischer zu mischen.
Die neueste technologische Errungenschaft im Bereich der Betonaufbereitung sind moderne automatisierte Anlagen für große Bauprojekte. In einer solchen Anlage arbeiten die Zapfventile rund um die Uhr, Schotter und Sand werden mit Brüllen in die Bunker geschüttet und Wasser wird eingegossen. Die fertige Betonmischung wird auf leistungsstarke Muldenkipper gekippt, die sie zu den Bauwerken transportieren, entladen und zum Werk zurückbringen.
Die Arbeiten zur weiteren Verbesserung der Methoden zur Herstellung und Verlegung von Betonmischungen werden fortgesetzt.
Um die Betonmischung mit möglichst geringem Wassergehalt und damit geringstem Zementverbrauch dicht zu verlegen, wird derzeit häufig das Rütteln der Betonmischung eingesetzt. Was ist seine Wirkung? Jeder weiß, dass man durch das Schütteln eines körnigen Materials, wie etwa trockenem Sand, viel mehr Material in die gleiche Kiste packen kann als ohne ein solches Schütteln: Das Material wird dichter gepackt. Wenn Sie die Betonmischung häufig schütteln, verdünnt sich der Zementmörtel und die Mischung erhält die Eigenschaften einer Flüssigkeit. In diesem Zustand füllt die Betonmischung dicht das gesamte Volumen der Schalung aus und hinterlässt keine Hohlräume darin – Schalen.
Um dem Betonsmog Vibrationen zu verleihen, werden spezielle Mechanismen verwendet – Vibratoren.
Der Rüttler erzeugt mehrere tausend Schwingungen pro Minute und überträgt diese Schwingungen auf die umgebende Betonmischung. Die Mischung, die die Eigenschaften einer schweren Flüssigkeit annimmt, verteilt sich über die Schalung, füllt sie und umhüllt die Bewehrung. Chill und Kies versinken im Zementmörtel und verteilen sich gleichmäßig in der gesamten Betonmasse.
Durch Vibration ist es möglich, deutlich weniger bewegliche Mischungen zu verlegen als manuell. Durch die Reduzierung des Wasseranteils solcher Mischungen verbessern wir die technischen Eigenschaften des Betons. Daher weist Rüttelbeton eine höhere Qualität im Vergleich zu Handbeton auf.
Unsere Industrie produziert verschiedene Arten von Rüttlern, die zum Verlegen von Beton in massiven und dünnwandigen, unbewehrten und bewehrten Strukturen bestimmt sind. Abbildung 7 zeigt das Aussehen der Innen- und Oberflächenrüttler zur Verdichtung der Betonmischung.
Abb.7. Aussehen der Vibratoren:
a - Innenvibrator;
b - Oberflächenvibrator
Während des Betriebs taucht der Innenrüttler in die Betonmasse ein. Für Bauwerke geringer Dicke und mit großer horizontaler Fläche, wie Straßendecken, Brücken- und Bodenplatten usw., werden sogenannte Flächenrüttler eingesetzt (dargestellt in Abb. 7, b), die an einer aufgesetzten Plattform befestigt sind der Oberflächenbeton. Die Vibrationen der Baustelle werden auf die Betonmischung übertragen. Am häufigsten werden sie im Straßenbau eingesetzt. Um Beton in Produkten zu verdichten, wird die Form mit dem Produkt auf einem speziellen Rütteltisch installiert. Beim Einschalten des Rüttlers wird die gesamte Form samt Betonmischung Vibrationen ausgesetzt; Dadurch wird ein hoher Verdichtungsgrad erreicht. Sie können Vibrationen auf die Betonmischung übertragen, indem Sie den Rüttler an der Schalung befestigen; Solche Rüttler werden als Außenrüttler oder Schraubstockrüttler bezeichnet, da sie mit einem Schraubstock an der Schalung befestigt werden.
Die Technik der Betonverdichtung, insbesondere bei der Herstellung von vorgefertigten Betonprodukten, verbessert sich rasant: Leistung und Vibrationsfrequenz der Rüttler werden erhöht, gleichzeitige Vibrationen auf einem Rütteltisch und einem Flächenrüttler werden eingeführt, Vibrationen mit Belastung der Betonmischung über den gesamten Bereich des Produkts. Es ist davon auszugehen, dass die Technik des Betoneinbaus und der Betonverdichtung in den kommenden Jahren einen deutlichen Schritt in Richtung weiterer technischer Fortschritte machen wird.
Im Straßenbau werden komplexe Betonbearbeitungsmaschinen eingesetzt, um das Gemisch zu ebnen, durch Rütteln und Verdichten zu verdichten, die Oberfläche zu profilieren und zu verdichten. Eine moderne Einheit zum Bau einer Straßendecke aus Zementbeton (Abb. 8) steht in puncto Komplexität und Betriebseffizienz Getreide- und Kohlemähdreschern in nichts nach.
Abb.8. Fertiger
Der gesamte Zyklus des Pflasterbaus wird von mehreren Maschinen durchgeführt. Schienenschalungen werden auf einem profilierten und verdichteten Untergrund montiert; Sie begrenzen den Streifen zukünftiger Fahrbahndecken, dienen als Schalung für die Fahrbahnplatte und dienen gleichzeitig als Schienen für die Fortbewegung von Betoniermaschinen. Eine Reihe von Muldenkippern liefert die Betonmischung aus der Anlage und kippt sie in eine Verteilerschaufel. Aus dem Eimer wird die Mischung in einen Verteilertrichter umgeladen und in lockerem Zustand in einer Schicht einer bestimmten Dicke auf dem Untergrund zwischen den Schienenformen platziert. Nach dem Verteiler bewegt sich eine Betonbearbeitungsmaschine, die die Beschichtung verdichtet, nivelliert und profiliert; Dahinter bewegen sich Vorrichtungen zum Schneiden von Dehnungsfugen. An einem Tag kann eine solche Einheit 300 Meter zurücklegen und hinterlässt eine fertige Straßenoberfläche. Nach dem Verlegen des Betons wird dessen Oberfläche mit einer Sandschicht oder einem Lack- oder Bitumenfilm bedeckt und so vor dem Austrocknen geschützt. Wenn der Unterstand aus Sand besteht, wird er regelmäßig bewässert. Nach 20 Tagen darf der Verkehr auf der Straße wieder freigegeben werden, wenn das Wetter warm ist und die Lufttemperatur mindestens 15° beträgt.
Für Mittelzone In Russland beträgt die Dauer der Bausaison etwa 200 Tage. In dieser Zeit kann ein Maschinensatz 60 Kilometer erstklassige Straße präparieren. Und wie viel Baumaterial muss dafür transportiert werden! Allein für den Bau des Straßenbelags werden pro Straßenkilometer über 3.500 Tonnen Material benötigt, für die gesamte Straßenlänge sind es über 200.000 Tonnen. Um all diese Massen an Sand, Schotter, Betonmischung usw. zu transportieren, sind etwa 40.000 Fahrten leistungsstarker Muldenkipper erforderlich.
Reifung von Beton
Von der Herstellung der Betonmischung bis zur vollständigen Aushärtung findet eine gewisse Reifungs- und Festigkeitsphase statt, die je nach Zementart und äußeren Bedingungen (Temperatur und Luftfeuchtigkeit) mehrere Tage bis mehrere Monate und sogar mehrere Monate dauern kann Jahre. In dieser Zeit verwandelt sich Beton von einer flexiblen Kunststoffmasse in einen haltbaren Kunststein.
Diese Transformation erfolgt schrittweise. Die erste Phase der Betonreifung wird als Abbindezeit bezeichnet. Es dauert normalerweise mehrere Stunden. Zu diesem Zeitpunkt verliert der Zementleim seine Beweglichkeit. Wasser geht teilweise chemische Verbindungen ein und verteilt sich teilweise über die Oberfläche der neu gebildeten Verbindungen, die Betonmischung verliert ihre Beweglichkeit und erhält eine minimale Festigkeit.
Die Abbindeperiode kann nicht scharf von der nächsten Periode, der Aushärtungszeit, getrennt werden. Einige Stunden nach dem Verlegen kommt jedoch der Punkt, an dem die Betonmischung bewegungslos wird und nicht mehr zerstörungsfrei gerüttelt werden kann. Dieser Moment kann als Ende des Abbindezeitraums betrachtet werden.
Damit die Prozesse der chemischen Verbindung von Wasser mit Zementmineralien ausreichend effektiv ablaufen, ist es notwendig, den Beton in einem feuchten Zustand zu halten. Die Aushärtung stoppt nicht nur bei niedrigen Temperaturen, sondern auch bei unzureichender Luftfeuchtigkeit. In dieser Hinsicht ist Beton wie eine Pflanze: Damit er gut wachsen kann, muss er bewässert und warm gehalten werden. Bei normalen Temperaturen erreicht Portlandzementbeton seine Hauptfestigkeit innerhalb von 20 bis 30 Tagen nach dem Aushärten. Eine Temperaturerhöhung, die bekanntermaßen chemische Reaktionen beschleunigt, wirkt sich günstig auf die Aushärtegeschwindigkeit aus. Zur Berechnung wird üblicherweise die Festigkeit herangezogen, die der Beton nach der Aushärtezeit von 28 Tagen erreicht. Durch eine Erhöhung der Temperatur ist es möglich, die gleiche Festigkeit in viel kürzerer Zeit zu erreichen.
Basierend auf der Untersuchung des Aushärtungsprozesses wurden die Bedingungen für die Erzielung eines guten Betons entwickelt: eine mäßige Wassermenge beim Mischen, feuchte und warme Aushärtungsbedingungen. Die Qualität von Bauwerken hängt von der Einhaltung dieser Bedingungen ab.
Betonarbeiten im Winter
Relativ raue klimatische Bedingungen auf fast dem gesamten Territorium Russlands sind für die Betonhärtung ungünstig; Daher müssen Bauherren häufig künstlich eine feuchte und warme Umgebung für den verlegten Beton schaffen. Sowjetische Wissenschaftler und Ingenieure haben hocheffiziente Methoden zum Betonieren unter winterlichen Bedingungen entwickelt, die es ermöglichen, das ganze Jahr über zu arbeiten.
Im Winter ist es notwendig, die Betonmaterialien zu erwärmen und vor Auskühlung zu schützen oder sogar den im Bauwerk verlegten Beton zu erhitzen, bis er die erforderliche Festigkeit erreicht. Doch in den letzten Jahren wurde eine Methode entwickelt, die es ermöglicht, bei Minustemperaturen und ohne Heizmaterial und Beton zu arbeiten.
Der einfachste Weg, günstige Bedingungen für die Betonerhärtung im Winter zu schaffen, ist die „Thermos a“-Methode, die vor über 40 Jahren von Prof. I.A. Kireenko. Mit dieser Methode ist die Struktur gut von der Umgebung isoliert, so dass sie lange Zeit blieb warm. Das Prinzip dieser Methode ist das gleiche wie das einer normalen Thermoskanne. Die beim Aushärten des Zements freigesetzte Wärme erwärmt verlustfrei die Struktur von innen. Auf diese Weise kann Beton in massive Bauwerke eingebaut werden, deren Oberfläche im Verhältnis zum Volumen klein ist.
Bei weniger massiven Bauwerken kommt eine künstliche Beheizung zum Einsatz: Das Bauwerk wird mit einem Holzwärmer abgedeckt (dies ist die am wenigsten rentable Technik) oder mit Dampf erhitzt, wobei um die Schalung ein spezielles Gehäuse angebracht wird, unter dem Dampf geleitet wird, oder schließlich das Struktur wird mit elektrischem Strom erhitzt.
Bei der Herstellung von Betonarbeiten im Winter wird häufig ein Verfahren eingesetzt, das auf dem Einbringen von Salzzusätzen in die Betonmischung basiert, die den Gefrierpunkt der Betonmischung senken und die Aushärteprozesse des Betons beschleunigen. Zu diesen Salzen gehören Chloridsalze: Calciumchlorid und Natriumchlorid. Durch geringe Zugabe von Salzen ist es möglich, kritische Bauwerke bei Frost und milden Frostbedingungen ohne besondere Maßnahmen zur Betonerwärmung zu errichten. Bei weniger kritischen und temporären Bauwerken können große Salzzusätze verwendet werden, die ein Arbeiten wie im Sommer bei Temperaturen bis zu -20° ermöglichen.
Abbildung 9 zeigt verschiedene Methoden zum Erhitzen von Beton in Bauwerken während der Arbeit im Winter. Dampfbeton wird im Sommer auch an Stützpunkten zur Herstellung von Stahlbetonfertigteilen eingesetzt, um die Aushärtung des Betons zu beschleunigen und den Formenumschlag zu erhöhen.
Abb.9. Möglichkeiten, Beton im Winter aufzuwärmen:
a - „Thermos“-Methode; b - Dampfheizung; c - elektrische Heizung
Methoden zur Herstellung von Betonarbeiten im Winter, beschleunigte Methoden zur Betonreifung durch Erhitzen und Dämpfen, fanden in der sowjetischen Bautechnik die weiteste Verbreitung.
Die ganzjährige Arbeitsproduktion und die Herstellung vorgefertigter Produkte in Fabriken werden zu den Haupttechniken, die die heimische Betonarbeitstechnologie, auch auf Straßenbaustellen, charakterisieren.
Haltbarkeit von Betonkonstruktionen
Beim Bau riesiger Bauwerke spielt Zementbeton als einer der langlebigsten Baustoffe unserer Zeit eine entscheidende Rolle.
Auf den ersten Blick leben tote, bewegungslose Betonkonstruktionen unter komplexen und stressigen Bedingungen und unterliegen zerstörerischen Veränderungen. Das Leben von Beton, seine Eigenschaften und Krankheiten zu verstehen, zu lernen, sein Leben nach Belieben zu kontrollieren – das ist die Aufgabe des Menschen, der Beton geschaffen hat.
Warum werden einzelne Bauwerke aus Beton zerstört?
Obwohl Beton sehr widerstandsfähig ist, wird er mit der Zeit „altersschwach“, wird mit Rissen bedeckt, bröckelt und stirbt ab. Tatsache ist, dass Beton fast ewig halten würde, wenn er keinen Umwelteinflüssen ausgesetzt wäre. Wasser hat die stärkste zerstörerische Wirkung auf Betonkonstruktionen.
Es gibt ein altes lateinisches Sprichwort: „Ein Tropfen höhlt einen Stein.“ Dieses Sprichwort gilt nicht nur im übertragenen Sinne, sondern auch im wörtlichen Sinne. Auf einem alten Bürgersteig aus Stein sieht man oft Vertiefungen im Stein an Stellen, an denen ständig Wassertropfen vom Dach fallen. Sie entstanden, weil sich der Stein langsam im Wasser auflöst. Partikel des fallenden Wassers reißen die Moleküle der Substanz, aus der der Stein besteht, von seiner Oberfläche ab, umgeben sie und tragen sie mit sich. Selbst Quarzflusssand löst sich im Laufe der Zeit in großen Mengen Wasser nach und nach auf.
IN natürliche BedingungenÜber lange Zeiträume, gemessen in Zehntausenden und Hunderttausenden von Jahren, finden kontinuierlich Prozesse der Auflösung einiger Gesteine und der Bildung neuer Gesteine statt.
Die Auflösung von Natur- und Kunststeinmaterialien kann erheblich zunehmen, wenn das Wasser Kohlendioxid und einige andere Stoffe enthält. Kohlendioxid ist in sehr geringen Mengen (0,03 %) in der Luft enthalten und daher in allem Wasser vorhanden, das mit der Luft in Kontakt kommt.
Ein übliches Natursteinmaterial, Kalkstein, löst sich in noch größeren Mengen in Wasser als Quarz. Um 1 Gramm Kalkstein aufzulösen, benötigt man etwa 3000 Liter Wasser. Das Vorhandensein von Kohlendioxid im Wasser erhöht die Löslichkeit von Kalkstein stark. In natürlichen Kalksteinvorkommen entstehen durch die Auflösung durch Wasser riesige unterirdische Höhlen.
Wir sprechen ausführlich über die Stabilität von Gesteinen, da Beton im Wesentlichen ein künstliches Gestein ist und seine Zersetzungsprozesse dem Verfall natürlicher Gesteine ähneln.
Festbeton enthält Kalk, einen Stoff, der gut wasserlöslich ist. Und andere Stoffe, aus denen Zementstein besteht, können sich nach und nach in Wasser auflösen.
Akademiker A.A. Baikov, der die Haltbarkeit von Beton untersuchte, wies darauf hin, dass alle Betonkonstruktionen aus Portlandzement zwangsläufig dem Prozess der Kalkauslaugung unterliegen und nach einer gewissen Zeit jeglichen Zusammenhalt verlieren und zusammenbrechen.
Bei Straßenbauwerken besteht die größte Auflösungsgefahr für Brückentragwerke. Bei einem Straßenbelag ist die Oberflächenschicht der auflösenden Wirkung von Wasser ausgesetzt.
Neben seiner lösenden Wirkung ist Wasser vor allem dann gefährlich, wenn der Beton abwechselnd in Wasser eingeweicht und anschließend gefriert wird. Die wiederholte Wiederholung solcher Zyklen führt zu einer schnellen Zerstörung des Betons.
Wenn mit Wasser gesättigter Beton gefriert, kommt es aufgrund einer aus der Physik bekannten Wasseranomalie zur Zerstörung. Im Gegensatz zu den meisten Stoffen ist Wasser bekanntlich im gefrorenen Zustand, d.h. Beim Übergang vom flüssigen in den festen Zustand dehnt es sich deutlich aus, und zwar um etwa 10 %. Jeder weiß, dass man eine mit Wasser gefüllte und verschlossene Flasche nicht in der Kälte stehen lassen darf: Das Wasser gefriert und die Flasche kann platzen, da beim Einfrieren von Jod ein Druck von über 800 Atmosphären entstehen kann (Abb. 10). Selbst im Erdreich verlegte Wasserleitungen aus Stahl können bei starkem Frost durch das Gefrieren des darin befindlichen Wassers platzen. Die Wasservolumenzunahme beim Gefrieren wurde früher in Steinbrüchen zur Spaltung des Bruchsteins genutzt.
Abb. 10. a - in einem offenen Gefäß (Eimer) gefrorenes Wasser: Das Eis bildet eine „Kappe“ über den Wänden des Gefäßes und nimmt ein größeres Volumen ein;
b - Wenn Wasser in einem dicht verschlossenen Gefäß gefriert, erreicht der Druck an seinen Wänden 800 Atmosphären
Die gleichen Phänomene treten bei Festbeton auf, wenn dieser gefriert. In den Poren des Betons befindliches Wasser gefriert darin und verursacht durch seine Ausdehnung Spannungen, die die Betonstruktur zerstören können. Die größere oder geringere Widerstandsfähigkeit von Beton gegenüber den zerstörerischen Einwirkungen von Wasser und Frost hängt in erster Linie von der Struktur des Zementsteins ab. Die Aufgabe eines Straßenbauers beim Bau von Betonbauwerken besteht darin, alle Voraussetzungen für die Herstellung von frostbeständigem und haltbarem Beton zu schaffen. Um dies zu erreichen, muss der Beton so dicht wie möglich sein, was bedeutet, dass er mit minimalen Wassermengen hergestellt, dicht eingebaut und unter günstigen Bedingungen für die Aushärtung gehalten werden muss.
In Unterwasser- und Untergrundteilen von Bauwerken besteht keine Gefahr der Betonzerstörung durch Gefrieren; hier ist die lösende Wirkung von Wasser möglich, die durch die chemische Wirkung der darin gelösten Salze verstärkt werden kann natürliche Gewässer Oh.
Natürliche Gewässer (Grundwasser und Fluss) können je nach Beschaffenheit der Gesteine, mit denen sie auf ihrem Weg in Kontakt kommen, völlig unterschiedliche Zusammensetzungen aufweisen.
Besonders schädlich für Beton ist der Gehalt an Schwefelsäuresalzen (Sulfaten) im Wasser. Calciumsulfat, Magnesiumsulfat und Natriumsulfat sind gefährlich, da sie, wenn sie in wässriger Lösung in Beton gelangen, eine chemische Wechselwirkung mit ihnen eingehen Komponenten Zementstein erhärtet und bildet neue Verbindungen. Wenn im erhärteten Zementstein chemische Reaktionen unter Bildung neuer Stoffe beginnen, dann wird naturgemäß die Haftung der Partikel des Zementsteins gestört und seine Festigkeit und damit die Festigkeit des Betons nimmt ab. Darüber hinaus bilden Sulfate mit den Bestandteilen des Zementsteins – Kalk und Calciumaluminate – eine neue Verbindung – Calciumsulfoaluminat, die ein 2,5-mal größeres Volumen als die Ausgangsstoffe einnimmt.
Die Kristallisation von Calciumsulfoaluminat führt zum Quellen und Reißen von Zementstein und damit auch von Konstruktionen aus Zementbeton.
Verschiedene Arten Die aggressiven chemischen Auswirkungen natürlicher Wässer auf Beton lassen sich auf drei Haupttypen reduzieren, die in Abb. 11 dargestellt sind.
Abb. 11. Hauptarten der Betonzerstörung durch aggressives Wasser
Beim Entwurf und Bau langlebiger Bauwerke berücksichtigen Ingenieure die Bedingungen, unter denen diese Bauwerke errichtet werden, und berechnen ihre Lebensdauer für vorgegebene Zeiträume.
Straßenbeläge aus Beton
Am besten hat sich starker, haltbarer und verschleißfester Zementbeton bewährt die beste Seite als Material für Straßenuntergründe und -beläge. Berechnungen bestätigen, dass die Verwendung von Zementbeton der Volkswirtschaft große Einsparungen bringt.
Bereits 1913 wurde in Tiflis die erste Betonstraße gebaut.
Zusätzlich zu den direkten wirtschaftlichen Vorteilen während des Baus bietet der Betonbelag erhebliche technische und wirtschaftliche Vorteile beim Straßenbetrieb. Durch die hohe Dauerhaftigkeit von Beton können Sie Wartungs- und Reparaturkosten auf ein Minimum reduzieren. Die Lebensdauer einer Betonfahrbahn ist im Vergleich zu einer Asphaltbetondecke um ein Vielfaches höher. Eine gut ausgebaute Straße mit Zementbetonbelag (Abb. 20) kann mehrere Jahrzehnte ohne größere Reparaturen halten. Der Straßenbelag aus Zementbeton ist eine 18 bis 24 Zentimeter dicke Platte.
Abb. 12. Straße mit Zementbetondecke
Wenn die Straße mit einem durchgehenden Betonband bedeckt ist, ändert sich bei Temperaturänderungen (Tag und Nacht, Sommer und Winter) die Größe der Betonplatte – sie dehnt sich aus und zieht sich zusammen, und es entstehen Spannungen darin, die zu Rissen führen können des Betons. Jeder weiß, dass beim Bau von Eisenbahnschienen die Schienen nie eng miteinander verbunden werden, um Verformungen bei Wärmeausdehnung zu vermeiden, sondern an den Stößen ein Spalt von mehreren Millimetern gelassen wird. Im Sommer schließt sich diese Lücke und im Winter laufen die Schienenenden auseinander.
Auf einer Betonstraße werden in einem gewissen Abstand auch Nähte angebracht – Lücken. Um zu verhindern, dass die Betonplatte bei Erwärmung zusammenbricht, werden Dehnungsfugen eingebaut – durch Lücken zwischen benachbarten Betondeckenplatten. Damit kein Wasser in den Untergrund unter der Platte eindringt, werden die Nähte mit elastischem Bitumenmastix verfüllt. Dehnungsfugen werden in gemäßigten Klimazonen alle 20–30 Meter installiert. Dieser Abstand hängt von der Temperatur der Betonmischung zum Zeitpunkt der Verlegung sowie vom Klima der Umgebung ab.
Wenn Sie keine Dehnungsfuge vorsehen, wird die Beschichtung durch die Erwärmung bei heißer Sonneneinstrahlung so stark beansprucht, dass ganze Betonstücke von der Oberfläche abbrechen können. Wenn sie mit Gewalt von der Oberfläche abfliegen, kann es zu Unfällen kommen. Solche Phänomene wurden auf einer Straße in Kalifornien (USA) beobachtet, wo die notwendigen Nähte nicht hergestellt wurden.
Wenn die Beschichtung auf eine Temperatur abgekühlt wird, die unter der Temperatur der Betonmischung und dem Zeitpunkt des Verlegens liegt, schrumpft der Beton und die Betonplatte kann reißen. Um das Auftreten solcher Risse zu vermeiden, wird die Beschichtung durch Nähte in Abständen getrennt, die kleiner sind als die, bei denen gefährliche Spannungen auftreten. Solche Nähte werden normalerweise in einem Abstand von 5 bis 10 Metern hergestellt und sind Schlitze, deren Tiefe einem Drittel der Plattendicke entspricht. Diese Nähte werden als Drucknähte bezeichnet. Wenn beim Abkühlen Druckspannungen im Beton auftreten, die Betonplatte reißt an der schwächsten Stelle – entlang des durch den Schnitt geschwächten Querschnitts. Die Drucknaht wird ebenso wie die Dehnungsnaht mit Mastix verfüllt.
Entlang der Straßenachse wird ebenfalls eine Naht nach Art der Drucknähte hergestellt, da sonst die Bildung eines Längsrisses möglich ist.
Somit besteht eine Straßendecke aus Zementbeton aus einzelnen Platten. Um zu verhindern, dass die Festigkeit der gesamten Beschichtung beschädigt wird, und um die Last von beweglichen Maschinen von einer Platte auf eine andere zu übertragen, werden in den Nähten spezielle Metallstangen installiert.
Die zukünftige Lebensdauer der Beschichtung hängt von der Qualität aller Arbeiten zum Einbau der Beschichtung ab.
Der Bau von Betonstraßen nimmt kontinuierlich zu und sie entwickeln sich zum Haupttyp der Autobahnen.
Beton wird am häufigsten für Bodenbeläge verwendet. Das Material bietet eine hohe strukturelle Festigkeit und Beständigkeit gegenüber aggressiven Betriebsbedingungen. Technologien für den Bau von Bodenkonstruktionen sind gut untersucht, verursachen keine übermäßigen Kosten und zeichnen sich durch ein breites Anwendungsspektrum aus.
Betonunterschichten werden dort eingebaut, wo während des Betriebs die Einwirkung von Ölen, Lösungen, Lösungsmitteln und verschiedenen aggressiven Flüssigkeiten möglich ist. In allen anderen Fällen können Sie mit dem Einbau von weichen Sandschotter-, Schlacken-, Asphaltbeton- und Tonbetonplatten auskommen.
Die Dicke der Vorbereitung richtet sich nach den Bemessungslasten. Dabei werden stets die Eigenschaften der verwendeten Böden und Materialien berücksichtigt. Aktuelle Normen legen jedoch die Mindestdicke der darunter liegenden Schichten fest. Bei der Installation in Wohn- und öffentlichen Räumen beträgt sie 80 mm, in Industrieräumen 100 mm.
Bei Böden mit Gefälle und organisierter Entwässerung müssen die Fugen mit der Wasserscheide übereinstimmen, in anderen Fällen mit den Dehnungsfugen des Gebäudes
Der Beton muss die Tragfähigkeit der Zubereitung gewährleisten. Als Hauptmaterial wird eine Mischung der Klasse B22,5 verwendet. Weniger haltbarer Beton (jedoch nicht niedriger als B7,5) kann bei geringen Betriebslasten, insbesondere bei geringer Spannung in der darunter liegenden Schicht, verwendet werden.
Wenn die Betriebsbedingungen so sind, dass der Boden plötzlichen Temperaturschwankungen ausgesetzt ist, führen Sie das Schneiden immer durch Dehnungsfugen. Sie werden in Schritten von 8–12 m in zueinander senkrechten Richtungen angebracht.
Bodenvorbereitung
Vor dem Gießen des Betons muss der Bodengrund vorbereitet werden.
Das Funktionsprinzip ist wie folgt:
- bei Bedarf wird Pflanzenerde ausgehoben;
- wenn enthüllt hohes Vorkommen Grundwasserleiter, Maßnahmen zur Absenkung des Grundwasserspiegels durchführen;
- Staubige, tonige und lehmige Böden müssen getrocknet werden. Die Operation dauert bis zur Wiederherstellung der Tragfähigkeit;
- wenn der Boden in unbeheizten Räumen + auf wogenden Untergründen verlegt wird, ist ein Schutz gegen Verformung gegeben;
- poröse Böden werden entfernt und durch Böden mit geringer Setzung ersetzt oder verfestigt;
- Wenn der Untergrund eine gebrochene Struktur aufweist oder sperrig ist, sollte er von Schmutz und Verunreinigungen gereinigt und verdichtet werden. Es werden mechanische oder manuelle Stampfer verwendet. Handarbeit ist nur dann gerechtfertigt, wenn die Ausrüstung zu einer Verschiebung benachbarter Bauwerke und Fundamente führen kann. Gemäß der Technologie werden Böden in Schichten (10 cm) gegossen, wobei jede Schicht verdichtet wird.
Die Oberfläche des Bodengrundes muss allen geplanten Bemessungshöhen entsprechen. Basierend auf dem unteren Niveau der Oberfläche wird der Boden eingeebnet, hinzugefügt und verdichtet. Werden Erdmischungen für den Bau von Fundamenten verwendet, werden diese in Schichten von 50–75 mm mit schichtweiser Verdichtung verlegt.
Hinterfüllung darunter liegender Schichten
Bei Arbeiten am Boden werden Unterschichten unter die Betonvorbereitung gelegt.
Die Arbeiten werden wie folgt durchgeführt:
- Auf den Untergrund wird eine Schicht Bausand gegossen (vorbereitet und eingeebnet). Es wird in einer durchgehenden, gleichmäßigen Schicht über den gesamten Arbeitsbereich verteilt. Die Dicke einer Schicht sollte 5-10 mm betragen. Es erfolgt eine Verdichtung, bei der der Sand vorbefeuchtet wird;
- Als nächstes wird eine Schotterschicht ausgelegt. Es wird nach Größe, Zusammensetzung ausgewählt, verlegt und angefeuchtet. Dadurch sollte eine gleichmäßige durchgehende Schicht mit einer Dicke von 80-200 mm entstehen. Schotter wird mechanisch eingeebnet und verdichtet Handwerkzeuge. Wenn Kies verwendet wird, erfolgt die Verlegung auf ähnliche Weise;
- Auf trockenen Untergründen ist das Arbeiten mit Lehmmischungen zulässig. Das Material wird in einer Schicht von bis zu 100 mm verlegt und verdichtet, bis Feuchtigkeit an die Oberfläche gelangt.
Wenn eine mehrschichtige Vorbereitung durchgeführt wird, wird jede weitere Schicht nach sorgfältiger Bearbeitung der vorherigen Schicht verlegt.
Um die Haftung in den darunter liegenden Schichten zu verbessern, wird Feuchtigkeit zwischen ihnen verwendet
Betonvorbereitung gießen
Das Material kann mit Betonpumpen, Karren und Muldenkippern zur Baustelle transportiert werden. Wenn die Struktur keine Verstärkung erfordert, wird der Beton direkt von Karren oder Muldenkippern in die Mitte des Betonierbereichs eingebracht. Ist eine Bewehrungsschicht vorgesehen, erfolgt das Entladen des Betons durch seitliches Kippen.. Bei Bedarf kann die Platzierung des Bewehrungsnetzes angepasst werden, die Bewehrung kann jedoch beim Gießen nicht von ihrem Platz verschoben werden. Bei großen Arbeitsmengen empfiehlt sich der Einsatz einer Betonpumpe, die eine gleichmäßige Verteilung der Lösung gewährleistet.
Das Funktionsprinzip ist wie folgt:
- Auf der Basis sind Leuchtfeuer mit strenger horizontaler Kontrolle angebracht. Als Hauptmaterial können Bretter verwendet werden, deren Breite der Dicke der Betonvorbereitung entspricht, 4-6 cm dick. Auf dem Sockel werden die Baken mit Holzdübeln befestigt, die in Schritten bis zu einer Tiefe von 30 cm eingetrieben werden von 1,5 m. Anstelle von Brettern ist es zulässig, einen Metallkanal zu verwenden;
- Wenn auf der Bodenfläche ein Gefälle vorgesehen werden muss, erfolgt dies in der Vorbereitungsphase durch Abschneiden der Oberkante der Baken auf das erforderliche Niveau.
- Bei einem großen Arbeitsaufwand erfordert die Installation der Betonvorbereitung den Bau einer vorgefertigten Schalung mit zuverlässiger Befestigung aller Elemente.
- Beton wird der Oberfläche zugeführt. Das Betonieren erfolgt streifenweise nacheinander;
- Zunächst werden die Streifen gefüllt, die am weitesten vom Eingang entfernt sind, und sich nacheinander diesem nähern;
- Sobald der Beton ausgehärtet ist, beginnen sie mit der Bearbeitung angrenzender unbefüllter Streifen. Die Seitenkanten der fertigen Platten werden mit Heißbitumen vorbehandelt. Auftragsschicht – 1,5–2 mm. Diese Kanten bilden Dehnungsfugen;
- beginnen Schrumpfnähte zu bilden. Dazu wird ein 4-5 mm dickes und 80-100 mm breites Metallprofil in die frisch gegossene Zubereitung vertieft. Das Profil sollte 1/3 der Präparationsdicke eingegraben werden. Das Material wird 20–40 Minuten belassen und dann entfernt. Wenn der Beton ausgereift ist, werden die Schwindfugen mit Zementmörtel oder heißem Bitumenmastix verfüllt.
Nach Abschluss der Arbeiten wird die Oberfläche mit Glättmaschinen bearbeitet.
Abdichtung
Die Abdichtungsschicht wird unter der Betonvorbereitung bei mittlerer und hoher Einwirkung von Wasser und anderen Flüssigkeiten auf dem Boden (+ Laugen, Lösungen, Säuren) angeordnet. Dies können Böden unbeheizter Räume, Bauwerke auf absinkenden Böden, Böden auf Bodenplatten, Bereiche mit der Gefahr einer kapillaren Ansaugung von Grundwasser sein. Außerdem, Ein Schutz ist erforderlich, wenn die Betonvorbereitung unterhalb des Blindbereichs platziert wird.
Bei der Materialauswahl gelten folgende Grundsätze:
- Wenn ein Schutz vor der Einwirkung von Wasser und chemisch aggressiven Flüssigkeiten erforderlich ist, können Sie Materialien wie Polyethylenfolie, Polyvinylchloridfolie und Abdichtungen verwenden.
- funktioniert erfolgreich vor dem Hintergrund der durchschnittlichen Intensität der Abwassereinwirkung Klebeabdichtung. Es ist zulässig, mit bituminösen Materialien zu arbeiten und diese in 2 Schichten aufzutragen. ;
- vor dem Hintergrund der hohen Intensität der Einwirkung von Flüssigkeiten auf den Boden ist eine Klebeabdichtung möglich, jedoch mit einer Verdoppelung der Anzahl der Schichten;
- Zur Betonvorbereitung ist der Einbau einer Abdichtung auf Basis von Schotter und anderen Schüttgütern mit anschließender Imprägnierung mit Heißbitumen zulässig.
Die Polymerklebstoffabdichtung wird in einer Schicht aufgetragen
Im letzteren Fall wird der Schutz nach dem Auffüllen des Schotterkissens angebracht. Die Imprägnierung der Schicht erfolgt mit einem Asphaltverteiler oder manuell. Heißbitumen wird gleichmäßig in einer 5-6 mm dicken Schicht auf den Untergrund aufgetragen. Wenn die Bitumenimprägnierung in mehreren Schichten angeordnet ist, wird die erste Schicht mit Sand (Fraktionen bis 5 mm) oder Steinschlägen übergossen. Die Verdichtung erfolgt mit einer Walze, anschließend wird mit Sand eine zweite Schicht mit einer Dicke von bis zu 0,25 mm aufgetragen.
Unabhängig von den verwendeten Materialien muss die Abdichtungsschicht durchgehend und dicht sein und mindestens 300 mm über der Beschichtungsebene über den Boden hinausragen.
Grundsätze der Beschichtungsabdichtung:
- Der Untergrund sollte glatt und staubfrei sein. Es wird eine Grundierung auf Basis von Bitumenmastix oder Lösungen auf Basis von Polymeren aufgetragen. Die Zusammensetzung kann manuell mit Pinseln oder mit Sprühgeräten verteilt werden;
- Dadurch soll eine gleichmäßig dicke, identische Grundierungsschicht entstehen, in der es keine Lücken gibt. Optimale Dicke – 0,5–2 mm;
- Die folgenden Schichten sollten erst aufgetragen werden, nachdem die vorherigen vollständig getrocknet sind, was durch das Aufhören der Klebrigkeit festgestellt werden kann.
- Bei der Arbeit mit Fugen werden diese mit Mastix abgedeckt und 10-20 cm breite Streifen aus Rollenmaterial aufgeklebt, anschließend wird eine weitere Mastixschicht aufgetragen.
Grundsätze für die Arbeit mit Asphaltabdichtungen:
- Das Material kann auf heißen Mastix aufgetragen und in einer durchgehenden, gleichmäßigen Schicht aufgetragen werden. Die aufgetragene Schicht erfordert eine Nivellierung, Verdichtung mit Kellen oder Walzen;
- der nächste wird aufgetragen, nachdem der untere fertig ist, d. h. der Mastix ist vollständig abgekühlt;
- die Stöße sind versetzt angeordnet, eine Überlappung von 200 mm wird eingehalten;
- die oberste Schutzschicht muss glatt sein und die erforderliche Dicke und Neigung aufweisen;
- Wenn mit Kaltmastix gearbeitet wird, bleibt das Funktionsprinzip dasselbe.
Prinzipien der Arbeit mit Rollabdichtungen:
- Das Material kann auf Kalt- oder Heißbitumenmastix geklebt werden. Die Anforderungen an die Untergrundvorbereitung bleiben typisch;
- bei Verwendung von Heißmastix ist eine Anpassung der Paneele erforderlich;
- die Rolle wird auf dem Untergrund ausgerollt, um eine Überlappung von 100 mm zu gewährleisten;
- Das verlegte Material wird 24 Stunden lang belassen, um Unebenheiten und Wellen zu beseitigen. Die Raumtemperatur sollte nicht unter +15 Grad liegen;
- Wenn die Platten ruhen, werden sie zurückgerollt, so dass nur die erste Längsreihe übrig bleibt und eine Klebelinie gezeichnet wird.
- Etwa 0,5 m von der zu verklebenden Rolle abbiegen und Mastix auftragen. Der Untergrund unter der Rolle wird mit dem Material bearbeitet;
- der Bereich wird mit Mastix verklebt, fest an den Untergrund gedrückt und mit einer Rolle von der Mitte bis zu den Rändern gerollt;
- dann wenden Sie den restlichen Teil ab und verfahren Sie genauso;
- die Kanten des geklebten Materials werden mit einer Rolle gerollt;
- Die nächste Rolle wird mit einer Überlappung von 10 cm verklebt, dabei ist darauf zu achten, dass die Kanten beschichtet und mit einer Rolle bearbeitet werden. Dann verhalten sie sich ähnlich und füllen den gesamten Arbeitsbereich aus;
- Wenn die erste Schicht fertig ist, fahren Sie mit der Installation der zweiten fort und achten Sie dabei auf eine Längsüberlappung von 20 mm. Kontrollieren Sie die versetzte Platzierung der Nähte.
Wenn der Untergrund keine Gefälle aufweist, werden Rollenmaterialien über die Oberfläche ausgerollt. Wenn es einen gibt, arbeiten sie von niedrigen zu hohen Bereichen
Wärmedämmung
Effektiv bewerben Wärmedämmstoffe Mit Hohe Dichte. Dies können Matten oder Platten auf Basis von Glasfaser, Mineralwolle oder moderner Polystyrolschaum sein. Die optimale Schichtdicke während der Arbeit beträgt 100 mm.
Die Wärmedämmung wird eng am Untergrund verlegt und sorgt so für einen festen Sitz der Fugen. Alternativ ist der Einsatz einer losen Wärmedämmung auf Blähtonbasis zulässig. Es wird schichtweise auf den Untergrund aufgetragen, anschließend egalisiert und verdichtet.
In Bereichen, in denen die Struktur an Wände und andere vertikale Flächen angrenzt, sollte ein Spalt gelassen werden, der mit einem Band aus schalldämmendem Material abgedeckt wird.
Betonpflastertechnik
Böden mit Betonbeschichtung sind Allzweckkonstruktionen, die sowohl im öffentlichen Bau als auch in der Produktion erfolgreich eingesetzt werden. Ein richtig verarbeiteter Boden hält hohen mechanischen Belastungen, der Einwirkung von Lösungen, Ölen, Salzen und Wasser stand. Zur Praxis Das fertige System hält einer Hitze von bis zu 100 Grad stand.
Der Betonbelag kann auf dem Boden, auf der darunter liegenden Betonvorbereitung, auf Zementsandestrichen M150 und höher, auf Stahlbetonbodenplatten verlegt werden. Am Arbeitsplatz müssen optimale Standards eingehalten werden Temperaturregime– nicht niedriger als +5 Grad, bis die Lösung die Hälfte ihrer vorgesehenen Festigkeit erreicht.
Materialien zur Betonvorbereitung:
- Portlandzement mit einer Festigkeit von mindestens M400;
- Kies oder Schotter. Die Größe sollte nicht mehr als 15 mm oder 0,6 der Beschichtungsdicke betragen. Sie müssen mit einem durchschnittlichen Verbrauch von rund 0,8 Kubikmeter pro Kubikmeter Beton rechnen;
- mittlerer oder grober Sand;
- Wasser.
Wenn eine funkenfreie Betonbeschichtung erforderlich ist, müssen Sand und Schotter auf Marmor- oder Kalksteinbasis verwendet werden, die beim Auftreffen von Metallgegenständen keinen Funken erzeugen.
Die Betongüte darf nicht unter M200 liegen. Die Beweglichkeit der Lösung wird kontrolliert – 2–4 cm. Es ist zulässig, C-3-Weichmacher oder andere modifizierende Zusatzstoffe in die Formulierung einzubringen, was die Arbeitskosten während der Installation senkt.
Reihenfolge der Betonpflasterung:
- Bei Arbeitsbeginn wird der Untergrund von Staub und Schmutz gereinigt;
- Sollten sich auf der darunter liegenden Schicht bereits Ölflecken gebildet haben, sollten diese mit speziellen Fertiglösungen oder einer Lösung entfernt werden Soda(5 %). Nach der Behandlung wird der Bereich mit Wasser gewaschen;
- bei Verlegung auf vorgefertigten Bodenplatten entstehen Lücken. . Die Verfüllung erfolgt oberflächenbündig mit den Platten.
Aussparungen und Befestigungslöcher müssen abgedichtet werden, wofür ein Zement-Sand-Mörtel M150 vorbereitet wird, mindestens
Beginnen Sie mit der Installation von Beacons Stahl Röhren, entweder ein Holzbalken oder ein Metallprofil. Durchmesser und Höhe des Materials müssen der Auslegungsdicke der Beschichtung entsprechen.
Die erste Leuchtfeuerreihe wird mit einem Abstand von 0,5-0,6 m zur Wand ausgelegt. Die weiteren Reihen werden parallel dazu in Schritten von bis zu 3 m ausgelegt. Es ist zulässig, den gesamten Arbeitsbereich auf einmal anzulegen oder mit getrennten Karten, mit axialer Verbindung und versetzt um die Breite der Leiste.
Nehmen Sie zur Fixierung einen Zementmörtel. Die Führungen werden entsprechend der zuvor angebrachten Markierungen nivelliert. Um die Position anzupassen, verwenden Sie leichte Hammerschläge oder Handdruck. Die Horizontalität wird mit einem Stab oder speziellen Instrumenten überprüft.
Der anschließende Installationsvorgang läuft wie folgt ab:
- Vor dem Gießen des Betons wird der Untergrund reichlich angefeuchtet. Zum Zeitpunkt des Auftragens der Lösung sollte die Oberfläche feucht sein, jedoch ohne überschüssiges Wasser;
- Als nächstes wird der Arbeitsumfang bestimmt, indem die Geschwindigkeit der Betonvorbereitung, des Verlegens und die anfängliche Abbindezeit berechnet werden;
- Die Lösung wird von der Betonmischanlage mit Betonmischwagen zur Baustelle geliefert. Wenn im ersten Stockwerk gegossen wird, wird die Lösung direkt auf den Betonierstreifen aufgetragen. Bei Arbeiten im zweiten und oberen Stockwerk wird die Lösung in Übergabetrichter transportiert und mit Aufzügen und Kränen portionsweise zur Baustelle gebracht;
- die Lösung wird durch einen Streifen zwischen den Beacons platziert;
- die Schicht wird mit Schaufeln oder Spezialschabern so eingeebnet, dass sie die Baken um 3-5 mm überragt;
- Ungefüllte Streifen werden nach der Demontage der Baken gegossen, wobei vorgefertigte Streifen als Führung und Schalung dienen.
Die Verdichtung erfolgt unter Beteiligung vibrierender Lamellen, die entlang der Baken bewegt werden. Wenn die Dicke der Struktur gering ist, wird die Vibrationszeit auf ein Minimum reduziert, - einwirken, bis sich auf der Oberfläche Feuchtigkeit bildet. Übermäßige Vibrationen können zum Absetzen grober Gesteinskörnungen und zur Delaminierung des Betons führen.
Die optimale Bewegungsgeschwindigkeit des Rüttelbohlens wird auf 0,5-1 Meter pro Minute eingestellt. Beim Bewegen des Gerätes sollte an dessen Unterkante eine Walze mit einer Höhe von 2-5 cm montiert werden. Im Wandbereich, im säulennahen Bereich erfolgt die Verdichtung mit Handstampfern von mindestens 10 kg Gewicht.
Sollte es beim Gießen zu Unterbrechungen kommen, werden vor der Wiederaufnahme des Einbaus die vertikalen Kanten der ausgehärteten Beschichtungen abgestaubt, gereinigt und mit Wasser abgewaschen. Wo sich Arbeitsnähte befinden, wird so lange verdichtet und geglättet, bis die Naht unsichtbar wird.
Vakuumverfahren zur Herstellung von Betonböden
Beim Verlegen von Betondecken zur Betonvorbereitung ist es sinnvoll, auf das Vakuumverfahren zurückzugreifen. In diesem Fall erfolgt die Beschichtung gleichzeitig mit der darunter liegenden Schicht. Dadurch erhöht sich die Festigkeit der Oberflächenschicht im Vergleich zu den ursprünglichen Indikatoren um ein Drittel. Es entsteht ein hochwertiger Boden mit hervorragenden physikalischen und mechanischen Eigenschaften.
Je nach Technologie wird eine flüssige Betonlösung auf den Untergrund aufgetragen und verdichtet. Mit speziellen Geräten extrahieren sie aus der Dicke des Betons überschüssiges Wasser, was sich auf die Festigkeit und Steifigkeit der Schicht auswirkt.
Die Betonrezeptur wird auf der Grundlage der Qualität des Portlandzements und der verfügbaren Zuschlagstoffe ausgewählt. Aber,
Um eine maximale Verdichtungswirkung zu gewährleisten, wird der Betonzusammensetzung zunächst ein höherer Anteil des Mörtelanteils zugesetzt
Das Wesen der Vakuummethode ist wie folgt:
- die Betonlösung wird mit einer überschüssigen Menge Wasser gemischt, so dass die Kegelsetzung 9-11 cm erreicht;
- die Mischung wird auf den Aufstellungsort entladen und über die gesamte Fläche gleichmäßig eingeebnet;
- Nach dem Gießen wird die Lösung mit einer Rüttellatte verdichtet, wenn die Schichtdicke 10 cm nicht überschreitet. Bei dickeren Estrichen und bei Vorhandensein einer Bewehrung werden zusätzlich Tiefenrüttler eingesetzt;
- Saugmatten werden auf die eingeebnete und verdichtete Schicht gelegt und über einen Schlauch mit der Vakuumanlage verbunden;
- die gefilterte Bodenmatte wird direkt auf den Frischbeton gelegt;
- Die obere Platte wird ausgerollt und mit Bürsten oder Rollen geglättet. Die Arbeit beginnt in der Mitte der Leinwand, was sich positiv auf die Abdichtung des Systems während der Vakuumverarbeitung auswirkt.
Wenn zwei oder mehr Platten auf der Fläche verlegt werden, sollten diese mit einer Überlappung von mindestens 3 cm platziert werden. Die Oberkante sollte die Unterkante um 10-15 cm überlappen. Anschließend beginnt das Absaugen. Die Dauer der Technologie berechnet sich wie folgt: 1-1,5 Minuten pro 1 cm Betonschicht.
Wenn keine Wasserbewegung beobachtet wird, wird die Behandlung beendet. Der Beton muss eine Dichte erreichen, bei der nur noch schwache Spuren darauf zurückbleiben. Die Saugmatten werden entfernt.
Nach der Vakuumbehandlung können Sie sofort mit dem Glätten beginnen. Das erste Mal arbeiten sie mit Kellen mit Scheiben, das zweite Mal mit Klingen.
Primärbehandlung von Betonböden
Wenn die gegossene Schicht ausreichend verdichtet ist und Zeit zum Abbinden hat, können Sie mit der Primärverarbeitung beginnen. Die Bereitschaft der Beschichtung lässt sich wie folgt feststellen: Beim Begehen sollten leichte Spuren zurückbleiben.
Hauptarbeitsgeräte – Glätt- und Glättmaschinen mit eingebauten Glättscheiben. Der Vorgang hilft, kleinere Mängel zu korrigieren, die beim Gießen und Verdichten entstanden sein könnten; nach der Verarbeitung wird ein Endhorizont gebildet.
Eine Nachverfugung ist nach 1-6 Stunden möglich. Anstelle von Scheiben fungieren Schaufeln als Arbeitskörper. An schwer zugänglichen Stellen arbeiten sie manuell oder mit einer Kelle zur Bearbeitung Zementestriche. Aufgrund der schnellen Erhärtung sollten solche Flächen zunächst verfugt werden.
Pflege
Beton ist ein Material, das unter feuchten Bedingungen reifen muss. Um eine solche Umgebung zu schaffen, wird die Oberfläche mit feuchtem Sackleinen und nassem Sägemehl bedeckt, wodurch das Material 7–10 Tage lang in diesem Zustand gehalten wird.
Die Häufigkeit der Befeuchtung richtet sich nach den Temperatur- und Feuchtigkeitsbedingungen, das Material darf jedoch nicht einmal teilweise austrocknen
Schleifen und Fräsen von Betonböden
Diese Art der Verarbeitung erfordert die Befreiung der Basis von Schmutz, Mechanismen und Geräten. Beim Fräsvorgang sollten gewöhnliche Diamantscheiben oder Fräser mit einem Durchmesser von 250-500 mm verwendet werden.
Das Fräsen erfolgt in parallelen Streifen, wobei beim nächsten Ansatz die Streifenkante um 2-3 cm überlappt wird. In einem Durchgang kann bis zu einer Tiefe von 2-7 mm gearbeitet werden, wobei der Schwerpunkt auf den mechanischen und physikalischen Eigenschaften des Betons liegt. Der Zweck dieser Behandlung besteht darin, die Spachtelkörner vollständig freizulegen, d. h. die Oberfläche muss eine solche Festigkeit erreichen, dass sie nicht abplatzen kann.
Die Arbeiten werden in der Regel in zwei Schritten durchgeführt. Im ersten Schritt trägt eine Fräsmaschine in einem Durchgang eine Schicht von 3-5 mm ab. Anschließend wird in 1-2 Durchgängen geschliffen Schleifmaschinen. Bei der Verarbeitung sollten Sie rechtzeitig eine gründliche Reinigung der Oberfläche veranlassen.
Abschluss
Durch die Endbearbeitung können die Leistungseigenschaften von Betonböden verbessert werden. Bei der Auswahl der Materialien orientieren sie sich an den Bedingungen, unter denen die Struktur betrieben wird.
Sie können wie folgt vorgehen:
- Oberflächenimprägnierung mit Fluaten. Die Beschichtung wird frühestens 10 Tage nach dem Ausgießen der Lösung aufgetragen. Die Temperatur im Raum wird aufrechterhalten – nicht unter +10 Grad. Vor der Arbeit muss der Untergrund getrocknet und gründlich mit Baustaubsaugern gereinigt werden. Das Material wird so lange aufgetragen, bis der Beton es nicht mehr aufnimmt. Die Praxis zeigt, dass hierfür drei Anläufe im Abstand von 24 Stunden ausreichend sind;
- Imprägnierung mit Dichtungsmassen. Zu diesem Zweck werden flüssiges Glas und wässrige Lösungen von Calciumchlorid verwendet. Die Behandlung erfolgt in drei Ansätzen in täglichen Abständen. Nach Abschluss der Behandlung muss der Beton mit Wasser gewaschen werden;
- Toppings hinzufügen. Zur Aushärtung werden spezielle Trockenmischungen (Korund, Quarz, Metall) verwendet. Die Materialart wird anhand der Bemessungslasten ausgewählt. Auf Frischbeton werden nach dem ersten Aushärten in zwei Ansätzen mit Betonbearbeitungsmaschinen Belägen aufgetragen;
- Als Schutzschicht kann Polyurethan- oder Epoxidlack verwendet werden. Das Material wird während der ersten Aushärtungszeit unmittelbar nach Abschluss des Schleifvorgangs auf den Beton aufgetragen. Vor der Arbeit wird der Boden mit einem Industriestaubsauger gereinigt, mit einem angefeuchteten Lappen behandelt und mit dem gleichen Lack, jedoch mit verdünntem Lösungsmittel, grundiert. Die Zusammensetzungen werden mit Pinseln, Rollen oder Sprühen aufgetragen. Es wird eine schichtweise Trocknung beobachtet, bei der die Oberfläche vor Feuchtigkeit geschützt wird.
Zusätzlich zu Polyurethanlacken können Sie verwenden Polymerbeschichtungen(Epoxidharz, Acryl). Farbschichten werden in einer dünnen Schicht aufgetragen, die nicht dicker als 0,3 mm ist.. Wenn ein dekorativer Effekt gewünscht ist, sind selbstnivellierende Böden, die eine nahtlose, matte Oberfläche erzeugen, eine gute Wahl. Bei hohen Belastungen können Sie auf den Aufbau hochgefüllter Beschichtungen zurückgreifen.
In Wohngebäuden ist die Auswahl an Endbeschichtungen praktisch unbegrenzt – es können Fliesen, Laminat, Teppich, Kork, Linoleum usw. sein.
Sicherheitstechnik
Bei der Verlegung von Betonböden sind stets die Bausicherheitsvorschriften einzuhalten. Alle Arbeitnehmer müssen mit den Arbeitsbedingungen vertraut sein, Anweisungen und Schulungen im Umgang mit Geräten und Werkzeugen erhalten.
Die Verlegung der Böden erfolgt mit technologischen Geräten. Zum Einsatz kommen individuelle und kollektive Schutzausrüstung sowie handgeführte Bauwerkzeuge. Der Arbeitsplatz an schwer zugänglichen Stellen sollte gut beleuchtet sein.
Beim Verlegen von Abdichtungen auf Heißbitumenmastix ist besondere Vorsicht geboten. Die Belüftung erfolgt in geschlossenen Räumen. Ein längerer Kontakt von Zementmischungen mit der Haut ist nicht akzeptabel.
Kosten für die Verlegung von Betonbodenbelägen
Die Technik zur Verlegung von Betonbodenbelägen ist vorhanden und erfordert keine allzu hohen Kosten. Im Durchschnitt betragen die finanziellen Kosten für die Verlegung von 1 qm. „schlüsselfertig“ beginnt bei 850-1100 Rubel. Zu diesen Kosten können Sie getrost die Kosten für den Einkauf und die Lieferung von Materialien hinzufügen.
Ausrüstung, Werkzeuge
Die Betonarbeiten werden mit einem Standardsatz an Maschinen und Werkzeugen ausgeführt.
Auf der Baustelle sollte folgendes Set zusammengestellt werden:
- bei selbstzubereitenden Lösungen sind Betonmischer erforderlich;
- Die Vorverdichtung des Bodens und der darunter liegenden Schichten erfolgt mit mechanischen Stampfern.
- Die Verdichtung der Füllung erfolgt mittels Rüttelleisten und Tiefenrüttlern;
- Die Endbearbeitung erfolgt mit Glätt- und Schleifmaschinen.
- Zur Reinigung und Staubentfernung werden Industriestaubsauger eingesetzt;
- Ebene, Ebene - ein Werkzeug zum Messen und Kontrollieren der Horizontalen und Ebenheit der Struktur;
- Schaufel, sauberer Behälter, Spatel.
Schlussfolgerungen
Die Verlegung von Betonbodenbelägen muss unter strikter Einhaltung des technologischen Prozesses erfolgen. Mit professioneller Arbeit und schrittweiser Qualitätskontrolle der Arbeit wird ein qualitativ hochwertiges Ergebnis erzielt.
Der Aufbau von Industriebetonböden wird im Video ausführlich gezeigt:
Zementbetonpflaster ist ein dauerhafter Hartbelag, der für starken Verkehr ausgelegt ist.
Ähnliche Beschichtungen unterscheiden sich:
- hohe Festigkeit;
— Haltbarkeit;
— sichereres Verkehrsaufkommen in der Nacht;
— hoher Haftkoeffizient der Beschichtung, der sich bei Befeuchtung nicht verändert;
— hoher Grad an Mechanisierung und Automatisierung;
— die Fähigkeit, Bauarbeiten unter ungünstigen Bedingungen durchzuführen;
— geringer Verschleiß der Beschichtung (0,1-0,2 mm/Jahr).
Mit all dem oben Gesagten und Offensichtlichen positive Aspekte Diese Beschichtungsarten haben auch Nachteile:
- Schwierigkeiten bei der Reparatur der Beschichtung;
— Unmöglichkeit der Verkehrsfreigabe unmittelbar nach Abschluss der Bauarbeiten;
— die Notwendigkeit, Dehnungsfugen zu installieren.
Zementbetondecken mit einer Böschungshöhe von mehr als 1,5 Metern werden im zweiten Jahr gebaut.
Anforderungen an Straßenbeläge:
Zementbeton muss fest und frostbeständig sein (F).
Die Frostbeständigkeit wird anhand der Anzahl der Zyklen abwechselnden Einfrierens und Auftauens wassergesättigter Proben im Alter von 28 Tagen beurteilt, ohne dass die Festigkeit um mehr als 25 % abnimmt und das Gewicht um nicht mehr als 5 % abnimmt.
Straßenbeläge aus Zementbeton werden in Güteklassen eingeteilt, die ihre Zugfestigkeit bei Biegung und Druck charakterisieren.
Der Straßenbelag in Russland und im Ausland ist unterschiedlich: In unserem Land bestehen Autobahnen für verschiedene Zwecke aus Asphalt, während sie in Europa und den USA hauptsächlich aus Beton bestehen. Dies ist der offensichtliche Unterschied in ihrer Qualität. In Russland haben sich Betonstraßen aufgrund ihrer erheblichen Kosten nicht durchgesetzt – schließlich werden die riesigen Flächen des Landes und die Erneuerung des Straßenbelags die Bevölkerung eine weitere Steuererhöhung kosten. Allerdings verbietet niemand Hausbesitzern, Parkplätze und Einfahrten aus langlebigem Beton zu bauen.
Warum werden Betonstraßen benötigt?
Der Bau von Betonstraßen empfiehlt sich dort, wo keine häufigen Reparaturen möglich sind und eine dauerhafte Straßenoberfläche erforderlich ist. In Russland ist es:
- Autodrome;
- Start- und Landebahnen und Landeplätze auf Flughäfen;
- Parken von Autos und anderen Geräten;
- Fußgängerwege und Gehwege in Städten;
- Küstenstraßen und Böschungen, wo hohe Luftfeuchtigkeit und Wassereinwirkung vorherrschen.
Die Lebensdauer einer Betonplatte übersteigt die Lebensdauer von Asphalt um das 2- bis 3-fache. Aus diesem Grund empfiehlt es sich überall, Straßenbeläge aus Asphaltbeton, die den klimatischen Bedingungen nicht standhalten, durch solche aus Zementbeton zu ersetzen, was in den USA nach und nach geschieht.
Der Unterschied zwischen Asphalt und Beton
Warum ist der Straßenbelag aus Asphalt nicht so langlebig wie der Straßenbelag aus Beton? Auf die Qualität der Grundmaterialien kommt es an:
- Asphalt ist ein Verbundwerkstoff aus Sand, Schotter und mineralischen Füllstoffen. Als Bindemittel dienen Bitumenpolymere.
- Beton ist eine Mischung aus Sand und Kies, gemischt mit Zement und Zusatzstoffen.
Der Hauptunterschied zwischen Beton und Asphalt ist das Bindemittel in ihrer Zusammensetzung. Bitumen bildet im Gegensatz zu Zement keine starken Steine, sackt bei Belastung unter schwachen Böden ab, wird in der Sonne weich und überwintert nicht gut. Beton weist diese Nachteile nicht auf, wenn die Vorbereitungs- und Installationstechnologie befolgt wird.
Der Straßenbelag besteht aus mehreren Schichten:
- Der Untergrund besteht aus Schotter, der das Wasser aus dem Boden ableitet, und Sand, der die Belastungen von oben und unten aus dem Boden ausgleicht.
- Verstärkung – dabei handelt es sich um eine Schicht minderwertigen Betons, die die Bettung bindet.
- Der Hauptfahrbahnbelag besteht aus einer Betonschicht.
Bei der Verlegung von Autobahnen mit starkem Schwerlastverkehr muss die Straße aus unbelastetem und gespanntem Stahlbeton bestehen, dessen Bewehrungskorb verhindert, dass der Stein unter dem Gewicht schwerer Lastkraftwagen reißt.
Im Privatbau sowie bei der Gestaltung eines Straßenbelags auf wassergesättigten oder hochgelegenen Böden wird die Abdichtung des Straßenbelags auf einem Sand- und Kiesdamm verlegt (Dachpappenmaterialien können verwendet werden). Die Schicht verhindert eine ständige Benetzung des Betons und damit eine Korrosion des Steins und des Bewehrungsrahmens.
Arten von Leinwand
Die Betonstraße eignet sich sowohl für stark befahrene Autobahnen als auch für Ortseinfahrten. Für diese Fälle werden verschiedene Leinwandtypen gewählt, die sich in Qualität und Kosten unterscheiden:
- Einschichtige Beschichtung Gute Qualität für Straßen jeglicher Art, geeignet zum Verlegen von Ober- und Unterschichten;
- Beton für die untere Schicht der Leinwand ist billig – er hat eine geringe Festigkeit und an seine Komponenten werden nur minimale Anforderungen gestellt. Eine Beschichtung aus einem solchen Material kann bei der Gestaltung lokaler Bereiche mit einem geringen Personenverkehr verwendet werden;
- Grundbeton mit durchschnittlichen Eigenschaften für schwere und anspruchsvolle Beschichtungen. Kann auf Dorfstraßen verlegt werden;
- Die Gestaltung von Straßen mit Fertigbetonplatten kann in einer eigenen Gruppe zusammengefasst werden.
Materialien zum Füllen der Leinwand
Das universelle Material für den Straßenbau ist M400-Beton. Seine Festigkeit reicht aus, um dem Druck der Räder von Pkw und Lkw auf Stadt- und Dorfeinfahrten standzuhalten.
Die Basis des Betons ist wasserbeständiger Portlandzement (1 Teil). Der Lösung werden außerdem Weichmacher zugesetzt, die die Hydrophobie der Beschichtung und ihre Festigkeit erhöhen. Die Arbeitslösung umfasst außerdem:
- Schotter – 5 Teile;
- Sand – 2 Teile.
Für das Betonieren einer Straße ist es sinnvoll, Fertigbeton im Werk zu bestellen – selbst für eine kleine Baustelle benötigen Sie viel Mörtel, der schnell gegossen werden muss, ohne dass einzelne Chargen aushärten.
Straßenbelagmaterialien können je nach erwarteter Belastung und Einbaubedingungen unterschiedliche Eigenschaften aufweisen.
Anforderungen an die Qualität von Betonstraßen
Bei der Auswahl von Komponenten für die Vorbereitung von Straßenbeton orientieren sie sich an SNiP 3.06.03-85 „Autobahnen“. Das Dokument regelt die Qualitätsanforderungen an den fertigen Stoff:
- Die Widerstandsfähigkeit gegenüber mechanischen Belastungen ist die Hauptanforderung an einen Straßenbelag. Für Straßen mit unterschiedlichem Verwendungszweck wird der Indikator individuell ermittelt.
- Keine Risse in der Beschichtung nach der Montage und im Betrieb. Die Einhaltung der Technologie zum Bau von Betonstraßen und die richtig ausgewählte Zusammensetzung der Arbeitslösung tragen zur Lösung des Problems bei.
- Wasserbeständigkeit und Beständigkeit gegenüber chemischen Reagenzien. Autobahnen befinden sich in unterschiedlichen Reliefbedingungen und Bodenqualitäten, und ohne organisierte Entwässerung (bei Verstößen gegen die Bautechnik) sammelt sich Wasser auf der Straßenoberfläche und verschlechtert deren Qualität.
Konkrete Anforderungen
Die Qualität des Stoffes wird durch die Bestandteile bestimmt, die ebenfalls einer sorgfältigen Auswahl gemäß den einschlägigen GOSTs unterzogen werden müssen. Beispielsweise beträgt die Festigkeit von Schotter, der einen zuverlässigen und langfristigen Betrieb der Straße gewährleisten kann, mindestens 1200 kg/cm². Für ein Kissen reicht weniger haltbarer Schotter mit einem Gewicht von 800–1000 kg/cm 2 aus.
Mobilität Betonmörtel– 2 cm beim Testen mit einem Kegel. Eine große Anzahl mineralischer Einschlüsse unterschiedlicher Fraktionen trägt dazu bei, Abweichungen von diesem Parameter zu vermeiden.
Eine weitere Anforderung an Beton ist eine hohe Biegefestigkeit; dazu werden Weichmacher in die Lösung eingebracht und die Leinwand zusätzlich mit Bewehrung verstärkt.
Vor- und Nachteile von Betonstraßen
Im Vergleich zu Asphaltstraßen haben Betonstraßen eine Reihe von Vorteilen:
- Hohe Festigkeit und Steifigkeit der Beschichtung;
- Beständigkeit gegen Hitze und Temperaturwechsel;
- Lange Lebensdauer ohne Reparaturbedarf;
- Eine gute Haftung der Fahrbahnoberfläche und der Autoräder erhöht die Verkehrssicherheit.
Die Straßen haben zwar weniger Nachteile, sind aber erheblich:
- Hohe Baukosten;
- Die Notwendigkeit einer strikten Einhaltung der Technologie bei der Vorbereitung von Lösungen und der Auswahl von Komponenten;
- Die Notwendigkeit, dass der Beton seine volle Festigkeit erreicht, bevor mit der Straße begonnen wird.
Bau einer Betonstraße
Betrachten wir die Phasen des Baus von Betonstraßen im Detail, da die Lebensdauer der Beschichtung von der Einhaltung der Verlegetechnik abhängt.
Aushubarbeiten gehören zu den teuersten und komplexesten. Vor Beginn wird ein detailliertes Projekt erstellt, das auf einer geologischen Untersuchung des Reliefs basiert. Wenn möglich, wird die Verlegeebene der Straße horizontal gemacht – die Hügel werden entfernt und in die Aussparungen wird ein Brett mit Felsverdichtung eingebracht.
Die fruchtbare Bodenschicht wird abgetragen: für den großflächigen Bau einer Autobahn komplett; für die private Verlegung angrenzender Flächen genügen 15-20 cm. Die unteren werden mit Walzen und Rüttelplatten mit großem Gewicht verdichtet. Dies ist eine der kritischsten Phasen – die Steifigkeit und Integrität der Beschichtung unter intensiven dynamischen Belastungen hängt vom Festigkeitsniveau des Untergrunds ab.
In der Phase der Vorarbeiten mit dem Boden wird über ein Entwässerungssystem zur Ableitung von Grund- und Regenwasser nachgedacht. Dazu wird die Basis nicht in einer idealen Ebene, sondern in einem leichten Winkel von 2-4 % hergestellt. Entlang der Straße können Betonrinnen oder natürliche Böschungen installiert werden, über die das Wasser in einen Auffangbehälter oder in den Boden fließt.
Verlegen der Bettungsschicht
Auf den verdichteten Boden werden Schotter und Sand geschüttet. Sie übernehmen die Funktion des Lastausgleichs und der Wasserableitung.
Die Dicke der Bettungsschichten hängt von der Art des Reliefs und den Eigenschaften des Fundaments ab und liegt zwischen 20 und 40 cm. Bei der Verlegung von Überlandstraßen wird Geotest häufig zwischen Sand und Schotter verlegt - es verhindert eine Vermischung der Fraktionen und die Dämme erfüllen ihre Funktion besser.
Bei Fundamenten mit hohem Grundwasserspiegel ist es sinnvoll, den Schotterhügel dicker zu machen – er wäscht sich nicht aus und leitet das Wasser gut ab. Sand muss unter Betonschichten gelegt werden – er bildet ein dichtes Kissen.
Sowohl Sand- als auch Schotterschichten müssen mit einer Walze oder Rüttelgruben verdichtet werden, um eine hohe Polsterfestigkeit zu erreichen.
Der Einfachheit halber wird die Bettungsschicht manchmal mit einem bis zu 5 cm dicken dünnen Betonestrich abgedeckt und darauf eine Abdichtungsbahn gelegt.
Beton ist gegenüber Biegebelastungen schwach, daher ist der Einsatz von Bewehrung nie überflüssig – die Wahl der Bewehrung hängt wiederum von den Eigenschaften des Untergrunds ab. In einigen Fällen kann es sein, dass überhaupt keine Verstärkung verwendet wird.
Der Durchmesser der Bewehrung für die Betonplatte wird nur statisch nach Berechnungen ermittelt. Normalerweise handelt es sich dabei um Stäbe ab 10 mm, eingeschweißt in ein Netz mit einer Zelle ab 150 mm. Die Bewehrungsprodukte werden in einer Betonschicht in einer Höhe von mindestens 4 cm von der Bodenebene verlegt. Es ist wichtig, dass sich das Netz im unteren Teil der Platte befindet, da sich dort die zerstörerische Belastung konzentriert und Risse entstehen.
Am einfachsten lässt sich die Schalung mit dicken Brettern mit einem Querschnitt von 50x150 mm herstellen (die Wahl der Höhe hängt von der Konstruktionsschicht des Betonsockels und der Beschichtung ab). Dickes Sperrholz funktioniert auch. Bretter und Sperrholz werden mit Verstärkungsstiften befestigt, die von der Außenseite der Platte in den Boden gesteckt werden. Bei der Verlegung von Gehwegen und Parkplätzen für Autos kann die Schalung durch einen Bordstein ersetzt werden, der bereits in der Phase der Betoniervorbereitung eingebaut wird.
Betonpflaster verlegen
Das Gießen der Straße mit Beton muss kontinuierlich erfolgen, damit die Materialien für das Straßenbett sofort in der erforderlichen Menge vorbereitet werden. Es empfiehlt sich, Beton im Werk zu bestellen; beim Bau großer Straßen werden in der Nähe der Standorte temporäre mobile Werkstätten zur Herstellung von Mörtel installiert, was die Lieferkosten senkt.
Bei Bedarf wird minderwertiger Beton (z. B. M200) mit Bettung auf den Untergrund gelegt, anschließend mit Oberputzmörtel M400 mit Zusatzstoffen.
Das Verlegen des Oberbelags erfolgt in 2 Schritten: Zuerst wird ein 30-40 mm dicker Untergrund gegossen, ein Armierungsgewebe darauf gelegt und die restliche Dicke gegossen.
Die Gesamtschichtdicke beträgt etwa 12 cm, manchmal mehr oder weniger.
Zur Vorbereitung wird ohne Unterbrechung Beton gegossen und die Oberfläche sofort eingeebnet. Ständig wird Material angeliefert, rund um die Uhr wird gearbeitet.
Nach dem Einbau muss der Beton mittels Vibrationskompression verdichtet werden. Das Verfahren verdrängt Luftblasen und verdichtet die Struktur der fertigen Beschichtung.
Dehnungsfugen schneiden und abdichten
Beim Bau einer Betonstraße wird die Straßenoberfläche in Segmente zerlegt. Dies ist möglich, dann erreicht der Beton eine ausreichende Festigkeit von 50-60 % und hält dem Gewicht von Personen und Schneidgeräten stand.
Um die Wärmeausdehnung auszugleichen, sind Nähte erforderlich unterschiedliche Grade ein Betonstein wird heruntergeworfen. Wenn sich das Plattenvolumen saisonal ändert, bilden sich keine Risse in der Straßenoberfläche.
Das Sägen erfolgt mit einem Spezialwerkzeug – einem Abrichthobel.
Dehnungsfugen werden in einem durch Berechnungen ermittelten Abstand hergestellt. Eine der Bestimmungsformeln ist Schichtdicke × 30.
Um zu verhindern, dass Wasser durch die Nähte in die Platte eindringt, werden diese mit Bitumen-Polymer-Dichtstoffen gefüllt.
Pflege und Vorbeugung von Betondecken
Damit die Arbeiten nicht umsonst sind, darf eine Betonstraße laut Technik erst dann für den Verkehr freigegeben werden, wenn der Beton seine volle Festigkeit erreicht hat, also nach 28 Tagen.
Um eine Zerstörung der Leinwand zu verhindern, wird diese mit Polymerimprägnierungen geschützt, die auf der Oberfläche einen wasserfesten Film bilden. Diese verringern zwar die Unebenheit der Straße und die Haftung an den Rädern. Dies ist eine negative Eigenschaft für Autobahnen, daher wird das Straßenbett in den meisten Fällen so belassen, wie es ist. Wenn die Bodenvorbereitungs- und Verlegetechnik befolgt wird und die Nähte richtig geschnitten sind, gefährdet nichts die Unversehrtheit der Platten für lange Zeit.
Eine weitere Möglichkeit zur Vorbeugung und Sanierung von Betonstraßen ist die Verlegung einer Nutzschicht. Auf den Beton wird Asphalt aufgetragen, der für Traktion zwischen den Rädern und der Oberfläche sorgt und die Lebensdauer der Autobahn selbst um ein Vielfaches verlängert. Darüber hinaus ist die Reparatur von Asphaltbetondecken deutlich kostengünstiger.
Wenn Risse auftreten, müssen Maßnahmen zu deren Beseitigung ergriffen werden. Zur Reparatur kleinerer Schäden werden spezielle Spachtelmassen und zur Reparatur tieferer Schäden Betonmörtel verwendet. In allen Fällen wird der Riss vor dem Einbringen der Spachtelmasse gereinigt und angefeuchtet.
Tritt ein Fehler auf, muss der gesamte Teil der Leinwand entfernt werden. Die Ursache solcher Verformungen ist eine unzureichende Verdichtung des Bodengrundes oder der Böschung.
Der Einbau von monolithischen Betonböden ist häufig in Einrichtungen erforderlich, die hohe Betriebsbelastungen erfordern. Dies können Verbrauchermärkte, Einkaufs- und Ausstellungskomplexe, Industriegebäude sein. In Wohngebäuden werden häufig monolithische Böden verlegt. Bei der Auswahl der Materialien für die Herstellung dieser Struktur muss man sich an Berechnungen der Widerstandsfähigkeit des vorbereiteten Bodens gegenüber dem Einfluss verschiedener zerstörerischer Faktoren orientieren. Oft das Einzige die richtige Entscheidung in diesem Fall verbleiben monolithische Böden.
Die besonderen Eigenschaften von Betonböden sind eine lange Lebensdauer, eine extrem hohe Verschleißfestigkeit und eine einfache Wartung. Durch die Verwendung festigender Zusätze in der Mischung wird die oberste Schicht des Untergrundes beständig gegen Feuchtigkeit und Chemikalien.
Technologischer Prozess zum Einbau von Betondecken
Als Untergrund für diesen Industriebodentyp wird ein Zement-Sand-Gemisch mit Schotter oder eine vorgefertigte Stahlbetonplatte verwendet. Die vorgestellte Betonverlegetechnik eignet sich sowohl für große Industrie- oder öffentliche Räumlichkeiten als auch für Privathäuser.
Alle Arbeiten werden unter strikter Einhaltung von SNiP und allen Anforderungen des technologischen Prozesses durchgeführt. Betonplatte muss auf einem verstärkten und gereinigten Untergrund verlegt werden. Der Grund für diese Anforderungen besteht darin, dass bei Verwendung einer minderwertigen Lösung in einem alten Estrich die Haftung der Beschichtung nachlässt und die Betonoberfläche bei starken Stößen zu bröckeln beginnt. Ursache für eine schwache Haftung sind auch ungelöste Fett- oder technische Ölflecken.
Um den Untergrund effektiv für das Gießen monolithischer Böden vorzubereiten, müssen eine Reihe der folgenden Maßnahmen durchgeführt werden:
- Entfernen Sie mechanisch sämtlichen Schmutz, Fettflecken, eventuelle Abblätterungen und Krümel. Um Spuren von technischem Öl zu entfernen, wird eine Malerlösung verwendet; Säurewaschen wirkt gegen Betonkleber.
- Unebenheiten im horizontalen Oberflächenniveau werden durch ein Fräswerk beseitigt. Beträgt der Höhenunterschied bis zu 10 %, muss dieser nicht beseitigt werden.
- Sollten Risse oder Schlaglöcher auf der Oberfläche vorhanden sein, sollten diese aufgeweitet und mit einer Mischung gefüllt werden, die Polymere enthält.
- Bereiche, die nicht saniert werden können, müssen zurückgebaut und mit neuem Beton gefüllt werden.
- Auch die oberste Schicht des alten Estrichs sollte von Staub befreit werden. Andernfalls nimmt die Qualität der Haftung ab und ein Teil der Verunreinigungen schwimmt nach oben und beeinträchtigt die Glätte der Oberfläche.
Nachdem Vorarbeit vollständig fertiggestellt, der Sockel wird eingeebnet. Als Ergebnis dieses Ereignisses wird die höchste Höhe der Beschichtung und damit die Dicke des Betonestrichs ermittelt.
Haupttypen monolithischer Böden
Heutzutage gibt es drei Haupttypen von Betonböden:
- Einschichtiger Zement-Sand-Boden. Wird für Räume mit kleiner Quadratmeterzahl verwendet. Aufgrund des Fehlens einer zusätzlichen Betonbeschichtung ist diese Art der Beschichtung nicht sehr belastbar. Diese Option ist für kleine Wohnungen, Wohngebäude oder Hauswirtschaftsräume relevant.
- Mehrschichtiger Boden. Die Herstellung dieser Konstruktion ist aufwendig, da die Betonmischung in zwei oder mehr Schichten verlegt wird. Es wird empfohlen, bei Sanierungsarbeiten eine ähnliche Beschichtungsmethode zu verwenden.
- Verstärkte monolithische Böden. Es zeichnet sich durch die extreme Festigkeit aller Varianten ähnlicher Basen aus. Durch den Einsatz von Bewehrungsstäben ist es möglich, die Beschichtungsdicke und das Gewicht von Betonböden zu reduzieren. Als Verstärkungsmaterial werden Stahlstäbe oder -geflecht, bei Bedarf auch Kunststoffelemente verwendet. Dieses Design ist typisch für Räumlichkeiten mit hoher Belastung der Beschichtung: Produktionshallen, Fahrzeugparks, landwirtschaftliche Hangars usw.
Der technologische Prozess zum Verlegen eines Betonbodens unterscheidet sich je nach funktionaler Zweck Firmengelände. In diesem Fall ist das Ziel dieser Maßnahme von erheblicher Bedeutung – die Oberfläche des Bodens im Raum zu nivellieren, die Betondecke zu isolieren, die Höhe des Sockels zu erhöhen usw. Durch verschiedene Verfahren zur Herstellung von Zementsandestrichen ist es möglich, die Bauqualität und die Lebensdauer zu verbessern.
Es ist wichtig zu beachten, dass die Vorbereitung eines monolithischen Bodens den geltenden Bauvorschriften und -vorschriften entsprechen muss, d. h. SNiP. Ihre Anforderungen können je nach den Betriebsfaktoren des Produkts und dem Ort des Gießens variieren.
Abdichtung des Untergrundes
Die nivellierte und gereinigte Oberfläche wird mit Mastix (einer wasserfesten Mischung auf Klebstoffbasis) behandelt. Dieser Schritt stellt funktional Folgendes bereit:
- hochwertige Haftung des alten Betonestrichs mit der neuen Zement-Sand-Schicht;
- zusätzliche Abdichtungsebene.
Eine würdige Alternative zu einer solchen Lösung ist die Hydroglasisolierung. Das Produkt wird in zwei Schichten aufgetragen, jede Schichthöhe beträgt mindestens 5 mm. Diese Beschichtung verfügt über eine hohe Plastizität und Beständigkeit gegen atmosphärische Belastungen und bildet eine dauerhafte wasserdichte Barriere für 10–15 Jahre.
Die monolithische Betondecke wird nach „Karten“ verlegt – rechteckigen Flächen, die zum Verlegen des Mörtels vorbereitet sind. Die Größe solcher Flächen wird auf der Grundlage des Produktionspotenzials bestimmt. Entlang des Kartenumfangs sind Führungen angebracht, d.h. Leuchtfeuer.
Verstärkung und Wärmedämmung von Betonböden
Das Verlegen von Bewehrungselementen erfolgt, um die Bildung von Bodenrissen während der gesamten Betriebszeit, insbesondere bei großen Estrichdicken, auszuschließen. Diese Art von Arbeiten wird in voller Übereinstimmung mit den Entwurfsberechnungen zukünftiger Belastungen durchgeführt.
Für diese Zwecke wird häufig Stahlgewebe verwendet, der Durchmesser des Stabes beträgt 5 mm und die Größe einer einzelnen Zelle beträgt 100 × 100 mm / 150 × 150 mm. Das Material für die Herstellung des Netzes ist eine Bewehrung der Klasse BP1.
Wenn starke Belastungen des Betonbodenbelags zu erwarten sind, empfiehlt es sich, zur Verstärkung einen verstärkten Rahmen zu verwenden. Die Bewehrung wird direkt auf der Baustelle angebunden, der Stabdurchmesser variiert zwischen 8 und 18 mm.
Die Bewehrung sollte mit Draht zusammengebunden werden. Das Schweißen ist unter keinen Umständen möglich, da Metall und Beton bei Temperaturschwankungen unterschiedlich stark schrumpfen und sich ausdehnen.
DIY-Beacon-Installation
Dies ist der kritischste Schritt bei der Herstellung monolithischer Böden, da die Höhe der freigelegten Bakenlamellen die Ebenheit der Beschichtung bestimmt.
- In der Regel wird der Raum in Abschnitte mit einer Breite von maximal zwei Metern unterteilt. Als Führungen werden spezielle T-förmige Leuchtturmlamellen verwendet, aber auch ein regelmäßiges Profil bzw rundes Rohr. In manchen Situationen einfach Holzblock, zuvor auf einer ebenen Fläche überprüft.
- Leuchtfeuer werden auf kleine, dicke Hügel aus frischem Mörtel gelegt. Anschließend wird durch Eindrücken der Lamellen in die Lösung oder umgekehrt durch Anheben die exakte horizontale Ebene eingestellt. Das Gießen der ersten Betonschicht ist erst nach vollständiger Aushärtung der freigelegten Baken zulässig.
- Wenn der Raum eine große Fläche hat und eine einmalige Füllung des Bodens nicht möglich ist, wird die Basis in rechteckige oder quadratische Karten unterteilt. Die Grenzen solcher Flächen werden mit Holzschalungen eingezäunt. Wenn alle Abschnitte gegossen sind und die Betonbeschichtung ausgehärtet ist, werden die Trennwände entfernt und der darunter gebildete Raum mit Fertigmörtel verfüllt.
Betonböden verlegen, Beton gießen
Für eine erfolgreiche Bodenbetonierung wird die Verwendung eines Betonmischers dringend empfohlen. Für große Mengen werden spezielle Automischer verwendet. Dieser Ansatz bietet die ideale Möglichkeit einer kontinuierlichen Lösungsversorgung, was sich positiv auf die Qualität monolithischer Böden auswirkt.
- Die fertige Mischung wird in Zellen auf den vorbereiteten Untergrund gelegt und anschließend mit einer gewöhnlichen Schaufel eingeebnet, um die Bildung von Hohlräumen zu verhindern und die Dichte der Schicht zu erhöhen. Wenn möglich, wird ein Vibrationsverdichter verwendet. Es wird in die Lösung selbst eingetaucht und gehalten, bis Milch auf der Beschichtung erscheint.
- Wenn die Dicke des Betons die Baken leicht überschreitet, wird er mit einem Lineal nivelliert. Die Bewegungen sollten auf Sie selbst und gleichzeitig nach links und rechts gerichtet sein. Manchmal wird anstelle einer Regel ein spezieller Rüttelestrich verwendet, der entlang von Führungen installiert wird. Das Funktionsprinzip ist das gleiche wie beim manuellen Lineal, nur mechanisiert.
- Nachdem der Estrich fertig ist, wird die Beschichtung regelmäßig mit Wasser angefeuchtet, um einer starken Austrocknung und Rissbildung vorzubeugen. Die Zeitspanne bis zur vollständigen Gebrauchsbereitschaft des Bodens beträgt mindestens einen Monat.
Um Betonböden selbst vorzubereiten, müssen Sie eine technologische Karte zum Verlegen einer Zement-Sand-Beschichtung verwenden. Routenführung beinhaltet Nächste Schritte Bodengeräte:
- Vorbereiten der Basis;
- dann wird die Basis wasserdicht gemacht;
- dann Verstärkungsmaterialien verlegen;
- Installation von Führungen und Schalungsrahmen;
- Herstellung einer Zement-Sand-Mischung und deren Einbau;
- Nivellieren der obersten Schicht;
- Nachdem der Boden vollständig getrocknet ist, erfolgt der abschließende Schleifvorgang der fertigen Beschichtung.
Das Verlegen von Betonböden ist eine anspruchsvolle Aufgabe Verschiedene Optionen technologischer Prozess. Als Ergebnis einer qualitativ hochwertigen Umsetzung aller Phasen Fertigungsprozess Es entsteht eine starke Struktur aus monolithischen Böden, die standhält Hoher Drück und verformen sich auch nach längerem Gebrauch nicht.