Warum wird eine Destillationskolonne benötigt? Wie ist eine Destillationskolonne aufgebaut und nach welchem Prinzip funktioniert sie? Bewertung der Besten mit Beschreibungen und Preisen Funktionsprinzip des Destillationskolonnengeräts
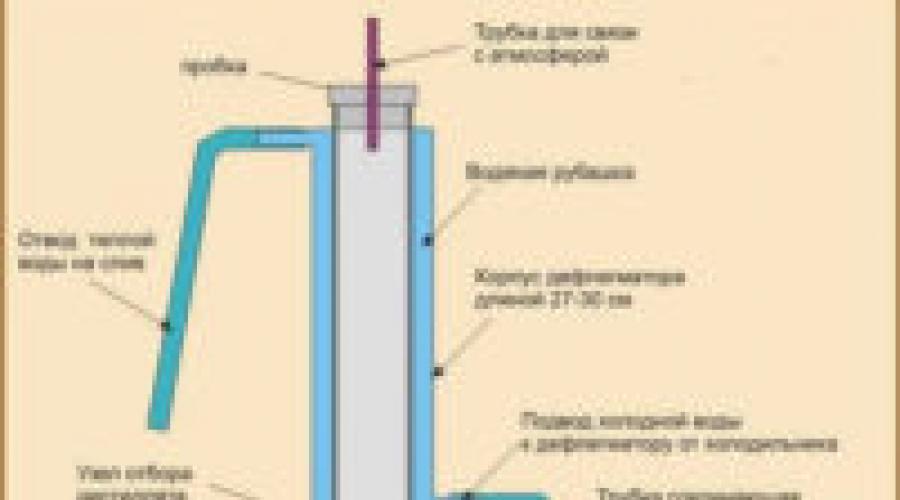
Lesen Sie auch
Wir alle behandeln mit großem Stolz und Liebe das, was mit unseren eigenen Händen angebaut und hergestellt wird, und bezeichnen diese Produkte als umweltfreundlich. Der Anziehungskraft auf Natürlichkeit und Reinheit bin ich nicht aus dem Weg gegangen.
Das Produkt ist auf jeden Fall von hoher Qualität und in angemessenen Mengen gesund. Für die Meister der Spirituosenherstellung bleibt die Frage jedoch weiterhin akut: darauf, das Produkt von schädlichen Verunreinigungen zu befreien.
Wissen Sie, wie man Mondschein reinigt? Schließlich sind Fuselöle selbst in einer „tränenreinen“ Flüssigkeit enthalten, die dünn aus dem Röhrchen eines gewöhnlichen Öls ohne Destillationssäule in ein Ersatzgefäß fließt.
Fertiger Wodka, den wir alle regelmäßig in Geschäften kaufen, ist frei davon Schadstoffe, hauptsächlich aus Fuselölen. Und das Geheimnis ist ganz einfach.
In produzierenden Fabriken alkoholische Getränke Sie verwenden keine Destillation (wie beim Mondschein), sondern Berichtigung, eine grundlegend andere Methode.
Daher ist der „Steiß“ frei von Verunreinigungen und hat in der Regel eine mildere Wirkung auf den Körper. Natürlich handelt es sich um hochwertigen Wodka.
Schauen wir uns an, was eine Destillationskolonne ist und warum ein Mondscheindock sie braucht. Zunächst einmal ist dies eine Art Überbau über dem Destillationstank Sie dienen als Filter, in dem sie sich absetzen. Detailliertes Diagramm Die Destillationskolonne ist unten dargestellt.
Das Grundprinzip der Kolonne ist mechanische Reinigung Mondschein aus verschiedenen Verunreinigungen noch in der Produktionsphase.
Bei der gewöhnlichen Destillation (Destillation) wird der gesamte Alkohol sowie andere Dämpfe beim Erhitzen aus der Maische freigesetzt, miteinander vermischt, um dann gemeinsam durch das Auslassrohr in den Kühlschrank und dann zu entweichen in eine Flüssigkeit verwandeln, die in einen nahegelegenen Behälter tropft.
Trennung dieser Dämpfe in Alkohol und Fusel im Normalfall Lebensbedingungen schwierig.
Nur ein Teil des Ergebnisses kann durch Kontrolle erreicht werden Temperaturregime, Und Trennung von „Kopf“ und „Zahl“.
Und so funktioniert eine Destillationskolonne: Bei der Rektifikation werden nach oben aufsteigende gemischte Dämpfe in Flüssigkeit umgewandelt, die in spezielle „Platten“ fließt, die mit der Rektifikations- und Reinigungskolonne der Destillationsapparatur ausgestattet sind.
Im Schleim (Flüssigkeit in Platten) verbleiben leicht flüchtige Verbindungen (Siedepunkt bei sehr niedriger Temperatur). niedrige Temperaturen) und höher, in das Kühlsystem, steigen schwerflüchtige auf, wo sie sich in eine alkoholhaltige Flüssigkeit verwandeln – gereinigten Mondschein.
Fuselöle und andere schädliche Verbindungen verbleiben im Schleim, und der Alkohol kondensiert frei im platzierten Behälter und fließt in ihn hinein.
Bei selbstgebauten Geräten bleibt das Funktionsprinzip der Destillationskolonne gleich, die Funktion der Rückflussverzögerung wird jedoch nicht von Platten, sondern von mehreren kleinen Federn aus Küchenschwämmen aus Edelstahl übernommen.
Wie macht man das zu Hause?
Es gibt fertige Moonshine-Destillierapparate mit Destillationskolonne, die online gekauft werden können. In der Regel sind sie praktisch und von recht hoher Qualität, aber die Preise der Gleichrichter halten viele davon ab, Mondschein von außergewöhnlich hoher Qualität herzustellen.
Geben Sie also auf und verwenden Sie die „altmodischen“ Methoden zur Reinigung des Produkts: Watte, Aktivkohle, Kaffeefilter? Natürlich nicht, Volkshandwerker haben einen Ausweg aus dieser Situation gefunden.
Wir zeigen Ihnen, wie Sie im wahrsten Sinne des Wortes eine Destillationskolonne selbst bauen können aus Schrottmaterialien. Doch bevor Sie mit der Umsetzung Ihrer Idee beginnen, wägen Sie die Vor- und Nachteile dieses Geräts sorgfältig ab.
Profis Berichtigung:
- Praktisch perfekte Reinigung Mondschein vor schädlichen Verunreinigungen.
- Mit Mondschein, der aus einem Gerät gewonnen wird, das mit einer selbstgebauten Mondschein-Reinigungssäule ausgestattet ist, können Sie verschiedene Getränke von sehr hoher Qualität mit hohem Alkoholgehalt zubereiten.
- Die Qualität des resultierenden Produkts entspricht den GOST-Standards für die industrielle Produktion.
- Nur mit Hilfe einer Destillationskolonne kann man es erhalten wirklich sauberes und hochwertiges Endprodukt. Mit einer gewöhnlichen Destillation kann selbst ein solches Ergebnis nicht erreicht werden.
Minuspunkte:
- Vielen erfahrenen Schwarzbrennern zufolge wird das Endprodukt nach dem Durchlaufen einer Destillationskolonne „entmannt“ und verliert nicht nur Fusel, sondern auch den größten Teil der aromatischen Komponente (z. B. den Geschmack der Marmelade, die Sie hinzugefügt haben).
- Der Herstellungsprozess des Endprodukts ist zeitaufwändiger und erfordert daher mehr Energie (Strom, Gas, Brennholz).
- Sie benötigen die Säule selbst, die Sie entweder kaufen oder selbst herstellen müssen.
Um eine Destillationskolonne mit eigenen Händen herzustellen, ist es notwendig, eine solche zu bauen, nachdem man das Funktionsprinzip verstanden hat Gerät.
Denken Sie daran, dass es sich bei der Destillationskolonne um eine Mondscheindestille handelt erfordert hochwertige Rohstoffe damit es seinen Hauptzweck erfüllen kann.
Du wirst brauchen:
- Edelstahlrohr mit einem Durchmesser von 30 bis 50 mm und einer Höhe von 1,3 – 1,4 Metern. Es empfiehlt sich, genau diesen Durchmesser einzuhalten, um das Maximum zu erreichen ordnungsgemäße Bedienung Ausrüstung. Edelstahl ist ein chemisch inertes Material, unterliegt keiner Korrosion und gibt keine Fremdgerüche oder chemischen Verunreinigungen ab.
- Viele glauben, dass es noch besser ist, eine Destillationskolonne zu bauen aus Kupfer, aber dies liegt in Ihrem Ermessen und Ihren Möglichkeiten;
- Verbindungselemente sowie Silikon- und/oder Kupferrohre;
- Isolierung(ein Stück Schaumgummi reicht aus);
- Klemme von einer medizinischen Infusion (nicht notwendig, aber bequemer);
- 2 Metallgitterklammern– entlang des Innendurchmessers des Rohrs und Anlaufscheiben dafür;
- Kontaktelemente, das Alkoholdämpfe von Verunreinigungen reinigt. Kleine Glasperlen sind in dieser Hinsicht einfach hervorragend, aber die Frage ist, wo man sie bekommt die richtige Menge(Sie sollten 2/3 oder mindestens die Hälfte der Innenseite der Säule ausfüllen). Daher wurde ein Ersatz gefunden - Metallschwämme zum Reinigen von Geschirr in einer Menge von 30 - 40 Stück.
Auswahl an Federschwämmen aus Metall - die wichtigste Etappe Herstellung des Gleichrichters. Du kannst shoppen gehen nur mit Magnet. Edelstahl in Lebensmittelqualität (der für die Verwendung in der Lebensmittelindustrie zugelassen ist) IST NICHT MAGNETISCH!
Andernfalls können Sie einen Schwamm kaufen, der im Inneren der Säule rostet, oder einen aus technischem Edelstahl, der schädliche Verbindungen freisetzt.
Das ist eigentlich alles. optionale Ausrüstung, wobei zu berücksichtigen ist, dass Sie bereits über eine Mondscheindestille verfügen, einschließlich eines Würfels und eines Kühlschranks.
Herstellungsprozess
Wie Ihre eigene Destillationskolonne aussehen soll, bleibt Ihnen überlassen. Auch das Montageprinzip bietet mehrere Lösungsmöglichkeiten:
- Schneiden Sie das ausgewählte Rohr in zwei Teile (das obere beträgt 0,5 – 1/3 der Gesamthöhe).
- Nach dem Anfasen die Kanten verbinden. Sie können einen Adapter oder eine Gewindeverbindung verwenden.
- Am Boden des Rohres muss ein Metallgitter angebracht werden, um zu verhindern, dass Füllstoffpartikel in den Würfel fallen. Mit diesem Teil wird eine selbstgebaute Destillationskolonne auf dem Destillationswürfel installiert.
- Schneiden Sie Ihre vorhandenen Edelstahlschwämme in kleine Stücke von etwa einem halben Zentimeter. Füllen Unterteil(Denken Sie daran, es sollte mindestens 0,5 der Gesamthöhe des Gleichrichters betragen, jedoch nicht mehr als 2/3) mit Metallschwammstücken. Anschließend das Rohr mit einem Netz abdecken und mit einer Anlaufscheibe sichern.
- Verbinden Sie den unteren Teil des Rohrs direkt mit dem Tank und isolieren Sie die Verbindung.
- Das allgemeine Design der Destillationskolonne sieht das Vorhandensein eines Wassermantels vor, sodass ein Wassergehäuse mit zwei Rohren für den Einlass und Auslass von Wasser zur Kühlung hermetisch an den oberen Teil des Rohrs angelötet ist.
- Die Oberseite des Rohrs muss mit einem Deckel verschlossen oder verlötet werden, sodass ein Loch für das atmosphärische Rohr entsteht.
- Über der Verbindungsstelle mit dem unteren Rohr, 1,5–2 cm, ein Loch für das Rohr bohren, durch das das Destillat (Mondschein) abgelassen wird. Befestigen Sie darunter einen Teller, auf dem sich Kondenswasser sammelt – Schleim.
- Verbinden Sie die Rohrabschnitte miteinander. Hier ist eine Säule, die zum Reinigen von Mondschein mit eigenen Händen entwickelt wurde, und sie ist fertig.
Wichtig! Die Rohrverbindung muss dicht, aber zusammenlegbar sein. Wenn Sie es auf Dichtmittel auftragen, verschwindet die Waschbarkeit Innenfüllung, und ggf. auch austauschen.
Wichtig ist, dass sich die Federstücke nicht ineinander verschränken, sondern kompakt verdichtet. Drücken Sie den Füller nicht mit Gewalt ein; es ist besser, das Rohr zu schütteln und zu klopfen, um den gesamten Abschnitt zu füllen.
Der letzte Schritt besteht darin, den Kühlschrank bereits in der Mondscheindestille anzuschließen. Dies kann bequem über einen Silikonschlauch mit darin angebrachter Tropfklemme erfolgen. Auf diese Weise können Sie die Geschwindigkeit der Flüssigkeitsbewegung jederzeit anpassen.
Nützliche Videos zum Gerät und zum Selbermachen
Funktionsprinzip der Destillationskolonne:
Neue Destillationskolonne „Prima“, Prinzip Schnellverschlussverbindung, sehen:
Praktische Arbeit an der Säule vom Eingießen des Rohalkohols bis zum Abtrennen der Schwänze:
Nachdem Sie sich die Zeichnung der Destillationskolonne angesehen haben, werden Sie verstehen, wie man sie richtig zusammenbaut. Und nachdem Sie es in Aktion getestet haben, werden Sie verstehen, dass Sie jetzt starken und perfekt gereinigten Mondschein herstellen. Teilen Sie Informationen mit Freunden über soziale Netzwerke!
§ 13.2 Destillationskolonnen: ihre Konstruktion und Funktionsweise
Wie oben erwähnt, erfolgt die Berichtigung in speziellen Geräten - Destillationskolonnen Ah, das sind die Hauptelemente von Rektifikationsanlagen.
Berichtigungsprozess kann periodisch und kontinuierlich durchgeführt werden, unabhängig von der Art und Ausführung der Destillationskolonnen. Betrachten wir den Prozess der kontinuierlichen Rektifikation, der in der Industrie zur Trennung von Flüssigkeitsgemischen eingesetzt wird.
Destillationskolonne- Vertikale zylindrischer Apparat mit geschweißtem (oder(vorgefertigtes) Gehäuse, in dem sich Massen- und Wärmeaustauschvorrichtungen (horizontale Platten) befinden 2 oder Düse). Am unteren Ende der Säule (Abb. 13.3) befindet sich ein Würfel 3, in dem die untere Flüssigkeit kocht. Die Erwärmung im Würfel erfolgt durch Totdampf in einer Rohrschlange oder in einem Rohrbündelheizkessel. Ein integraler Bestandteil der Destillationskolonne ist der Rückflusskühler 7, der dazu dient, den die Kolonne verlassenden Dampf zu kondensieren.
Die Rektifikationsbodenkolonne funktioniert wie folgt. Der Würfel wird ständig erhitzt und die noch vorhandene Flüssigkeit kocht. Der im Würfel erzeugte Dampf steigt die Säule hinauf. Das zu trennende Ausgangsgemisch wird zum Sieden vorgeheizt. Serviert wird auf einem Nährteller 5, der die Säule in zwei Teile teilt: untere (erschöpfende) 4 und Obermaterial (Stärkung) 6. Die anfängliche Mischung von der Nährstoffplatte fließt auf die darunter liegenden Platten und interagiert auf ihrem Weg mit dem Dampf, der sich von unten nach oben bewegt. Durch diese Wechselwirkung wird der Dampf mit der leicht flüchtigen Komponente angereichert und die herabströmende Flüssigkeit, die an dieser Komponente verarmt ist, wird mit der leicht flüchtigen Komponente angereichert. Am Boden der Kolonne findet der Prozess der Extraktion (Absaugung) der leicht flüchtigen Komponente aus der Ausgangsmischung und deren Umwandlung in Dampf statt. Ein Teil des Endprodukts (rektifiziertes Produkt) wird zur Bewässerung des oberen Teils der Kolonne zugeführt.
Die Flüssigkeit, die zur Bewässerung oben in die Kolonne eintritt und von oben nach unten durch die Kolonne fließt, wird als Rückfluss bezeichnet. Dampf, der mit dem Rückfluss auf allen Böden des oberen Teils der Kolonne interagiert, wird mit einer leicht flüchtigen Komponente angereichert (verstärkt). Der die Kolonne verlassende Dampf wird zum Rückflusskühler 7 geleitet, wo er kondensiert. Das resultierende Destillat wird in zwei Ströme aufgeteilt: Einer wird als Produkt zur weiteren Kühlung und zum Lager für Fertigprodukte geschickt, der andere wird als Rückfluss zurück zur Kolonne geleitet.
Das wichtigste Element einer Bodendestillationskolonne ist der Boden, da auf ihm die Wechselwirkung von Dampf mit Flüssigkeit stattfindet. In Abb. 13.4 zeigt ein Diagramm des Geräts und der Bedienung Kappenplatte. Sie hat einen Hintern 1, hermetisch mit dem Säulenkörper verbunden 4, Dampfrohre 2 und Abflussrohre 5. Dampfrohre sind so konzipiert, dass sie von der Bodenplatte aufsteigende Dämpfe weiterleiten. Durch die Abflussrohre fließt Flüssigkeit von der darüber liegenden Platte zur darunter liegenden. Auf jedem Dampfrohr ist eine Kappe montiert 3, Dabei werden Dämpfe in eine Flüssigkeit geleitet, durch diese hindurchgeperlt, abgekühlt und teilweise kondensiert. Der Boden jeder Platte wird durch die Dämpfe der darunter liegenden Platte erhitzt. Darüber hinaus wird beim teilweisen Kondensieren von Dampf Wärme freigesetzt. Aufgrund dieser Hitze siedet die Flüssigkeit auf jeder Platte und bildet dabei eigene Dämpfe, die sich mit den Dämpfen der darunter liegenden Platte vermischen. Der Flüssigkeitsstand auf der Platte wird über Abflussrohre aufrechterhalten.
Reis. 13.3. Diagramm der Destillationskolonne: / - Körper; 2 - Gerichte; 3 - Würfel; 4, 6 - erschöpfende und verstärkende Teile der Säule; 5 -Ernährungsteller; 7 - Rückflußkühler
Die auf der Platte ablaufenden Prozesse lassen sich wie folgt beschreiben (siehe Abb. 13.4). Lassen Sie Dämpfe der Zusammensetzung A von der unteren Platte auf die Platte strömen, und Flüssigkeit der Zusammensetzung strömt von der oberen Platte durch das Überlaufrohr IN. Durch die Wechselwirkung von Dampf A mit Flüssigkeit IN(Dampf, der durch die Flüssigkeit sprudelt, verdampft diese teilweise und kondensiert teilweise.) Es entsteht ein neuer Dampf der Zusammensetzung MIT und neue Flüssigkeitszusammensetzung D, sind im Gleichgewicht. Durch den Betrieb der Platte entsteht neuer Dampf MIT reicher an flüchtigen Substanzen als der Dampf, der von der unteren Platte kommt A, das heißt, es befindet sich Dampf auf dem Teller MIT angereichert mit einer leicht flüchtigen Substanz. Neue Flüssigkeit D, im Gegenteil, es wurde ärmer an flüchtigen Bestandteilen im Vergleich zur Flüssigkeit, die von der oberen Platte kam IN, Das heißt, auf der Platte wird die Flüssigkeit an der leicht flüchtigen Komponente abgereichert und an der leicht flüchtigen Komponente angereichert. Kurz gesagt besteht die Arbeit der Platte darin, den Dampf anzureichern und die Flüssigkeit von flüchtigen Bestandteilen zu befreien.
Reis. 13.4. Diagramm des Aufbaus und der Funktionsweise einer Kappenplatte: / - Unterseite der Platte; 2 - Wasserdampfrohr;
3 - Deckel; 4 - Säulenkörper; 5 - Abflussrohr
Reis. 13.5. Darstellung der Funktionsweise der Destillationsplatte im Diagramm bei-x: 1- Gleichgewichtskurve;
2 - Linie der Arbeitskonzentrationen
Als Platte bezeichnet man eine Platte, auf der sich ein Gleichgewichtszustand zwischen den von ihr aufsteigenden Dämpfen und der herabströmenden Flüssigkeit einstellt theoretisch. Unter realen Bedingungen wird aufgrund der kurzfristigen Wechselwirkung von Dampf mit Flüssigkeit auf den Platten kein Gleichgewichtszustand erreicht. Die Trennung des Gemisches auf einer realen Platte ist weniger intensiv als auf einer theoretischen. Um die Arbeit einer theoretischen Platte zu leisten, sind daher mehr als eine reale Platte erforderlich.
In Abb. Abbildung 13.5 zeigt anhand eines Diagramms die Funktionsweise einer Destillationsplatte bei-X. Die theoretische Platte entspricht einem schattierten rechtwinkligen Dreieck, dessen Schenkel dem Konzentrationszuwachs der flüchtigen Komponente im Dampf entsprechen Schnurrbart-j A , und das Ausmaß der Abnahme der Konzentration der flüchtigen Komponente in der Flüssigkeit ist gleich X B - X D . Die Segmente, die den angegebenen Konzentrationsänderungen entsprechen, konvergieren auf der Gleichgewichtskurve. Dies setzt voraus, dass sich die die Platte verlassenden Phasen im Gleichgewichtszustand befinden. In Wirklichkeit wird der Gleichgewichtszustand jedoch nicht erreicht und die Konzentrationsänderungsabschnitte erreichen nicht die Gleichgewichtskurve. Das heißt, die Arbeitsplatte (real) entspricht einem kleineren Dreieck als dem abgebildeten
in Abb. 13.5.
Die Ausführungen der Böden von Destillationskolonnen sind sehr vielfältig. Betrachten wir kurz die wichtigsten.
Säulen mit Kopfplatten in der Industrie weit verbreitet. Die Verwendung von Kappen sorgt für einen guten Kontakt zwischen Dampf und Flüssigkeit, eine effektive Durchmischung auf der Platte und einen intensiven Stoffaustausch zwischen den Phasen. Die Form der Kappen kann rund, facettiert und rechteckig sein, die Platten können ein- oder mehrkappenförmig sein.
Eine Platte mit gerillten Kappen ist in Abb. dargestellt. 13.6. Dampf aus der unteren Wanne strömt durch die Lücken und gelangt in die oberen (umgekehrten) Rinnen, die ihn zu den mit Flüssigkeit gefüllten unteren Rinnen leiten. Hierbei perlt Dampf durch die Flüssigkeit und sorgt so für einen intensiven Stoffaustausch. Der Flüssigkeitsspiegel auf der Platte wird durch eine Überlaufvorrichtung aufrechterhalten.
Kolonnen mit Siebböden sind in Abb. dargestellt. 13.7. Die Platten haben eine große Anzahl von Löchern mit kleinem Durchmesser (von 0,8 bis 3 mm). Der Druck des Dampfes und die Geschwindigkeit seines Durchgangs durch die Löcher müssen dem Druck der Flüssigkeit auf der Platte entsprechen: Der Dampf muss den Druck der Flüssigkeit überwinden und verhindern, dass diese durch die Löcher auf die darunter liegende Platte austritt. Daher erfordern Siebböden eine entsprechende Regulierung und reagieren sehr empfindlich auf Veränderungen im Regime. Sinkt der Dampfdruck, sinkt die Flüssigkeit aus den Siebböden. Siebböden reagieren empfindlich auf Verunreinigungen (Niederschläge), die die Löcher verstopfen und so Bedingungen für die Bildung von Siebböden schaffen können Bluthochdruck. All dies schränkt ihre Verwendung ein.
Gepackte Säulen(Abb. 13.8) unterscheiden sich darin, dass die Rolle der Platten in ihnen die sogenannte „Düse“ spielt. Als Düse werden spezielle Keramikringe (Raschig-Ringe), Kugeln, kurze Röhren, Würfel, sattelförmige, spiralförmige usw. Körper aus verschiedenen Materialien (Porzellan, Glas, Metall, Kunststoff usw.) verwendet.
Dampf tritt von einem entfernten Kessel in den unteren Teil der Kolonne ein und bewegt sich in der Kolonne nach oben in Richtung der fließenden Flüssigkeit. Über eine große Oberfläche aus gepackten Körpern verteilt, kommt der Dampf in intensiven Kontakt mit der Flüssigkeit und tauscht dabei Komponenten aus. Die Düse muss haben große Oberfläche pro Volumeneinheit, haben einen geringen hydraulischen Widerstand, sind beständig gegen die chemische Wirkung von Flüssigkeit und Dampf, haben eine hohe mechanische Festigkeit und sind kostengünstig.
Füllkörpersäulen haben einen geringen hydraulischen Widerstand und sind einfach zu verwenden: Sie können leicht entleert, gewaschen, gespült und gereinigt werden.
Das Design der Destillationskolonne ist komplexer aufgebaut als das einer herkömmlichen Mondscheindestille. Darüber hinaus impliziert die Arbeit mit einer Kolonne im Gegensatz zu einem Gerät, beispielsweise mit einem Dampfgarer, eine Art „Vorbereitungsmodus“, bevor die eigentliche Destillation beginnt. Wenn Sie Glück haben (wir empfehlen die Wahl eines Markengeräts), finden Sie wahrscheinlich eine mitgelieferte Anleitung. Lesen Sie dieses wichtige Dokument unbedingt durch, da dort alle Anweisungen für die Arbeit mit diesem speziellen Modell enthalten sind. Tatsächlich ist die Verwendung einer Destillationskolonne keine schwierige Aufgabe; die Hauptsache ist, genau zu verstehen, was getan wird und warum.
So verwenden Sie eine Destillationskolonne
Zunächst ist anzumerken, dass es nicht ganz richtig ist, die Maische sofort im Rektifikationsmodus zu destillieren. In diesem Fall spielt es keine Rolle. Es besteht die Gefahr, dass die Düse innerhalb kürzester Zeit verstopft und die Reinigung von Alkoholdämpfen unmöglich wird. Allerdings ist fast jede Haushaltsdestillationskolonne in der Lage, im Destillationsmodus zu arbeiten, wodurch Sie bereits in der ersten Stufe Rohalkohol gewinnen können. Es kann aber bereits einer Berichtigung unterzogen werden.
Als Vorbereitungsphase gilt der Betrieb der Kolonne „allein“ für 15-20 Minuten. Dies ist zum Aufwärmen notwendig, wodurch Sie Alkoholverluste vermeiden. In diesem Modus werden keine Fraktionen ausgewählt, dem Rückflusskühler wird maximale Kühlung zugeführt, alle Dämpfe kondensieren darin und der sogenannte „wilde Rückfluss“ fließt vollständig in den Destillationswürfel.
Denken Sie immer daran, dass die Temperaturanpassung durch Hinzufügen/Reduzieren von Heizung oder Kühlung sanft und schrittweise erfolgen sollte, da das System träge ist und die Etablierung eines neuen stabilen Temperaturregimes innerhalb der Säule nicht sofort, sondern innerhalb von 20–30 Sekunden erfolgt.
Zu Beginn des Betriebs der Destillationskolonne „von selbst“ ist ein leichtes „Seufzen“ zu hören, was normal ist. Dies ist die Freisetzung der Luft, die sich vor dem Eintritt des Dampfes in der Säule befand. Sobald die Säule den Betriebsmodus erreicht (Beginn des Prozesses des Flüssig-Dampf-Phasenaustauschs durch Masse und Wärme), kann die Säule beginnen, leichte Geräusche zu machen, was ebenfalls normal ist.
Wenn die Kolonne aufgewärmt ist, beginnt direkt die Rektifikationsstufe. Mach dich sauber Ethanol Ohne fremde Verunreinigungen hilft nur eine Destillationskolonne.
Wie nutzt man eine Destillationskolonne im „Betriebsmodus“?
Hier ist eine Kurzanleitung:
- Die Temperatur im oberen Teil der Kolonne wird (durch Anpassung der Kühlung des Rückflusskühlers und Erwärmung des Würfels) so eingestellt, dass die Kopffraktionen zu verdampfen beginnen. In der Regel beträgt sie 65-68°C. In finden Sie Informationen darüber, dass die Thermometerwerte einen leichten „Kamm“ ergeben können. Aber die Hauptsache ist, dass sie sich in engen Grenzen bewegt und das Temperaturregime insgesamt stabil bleibt.
- Die Köpfe werden mit einer Geschwindigkeit von maximal einem Tropfen pro Sekunde abgenommen. Ansonsten gelten dieselben Kriterien wie beim Destillieren in einem herkömmlichen Destillierapparat (das Kopfvolumen kann berechnet werden oder sich am Geruch orientieren).
- Nach Auswahl der Köpfe wird die Temperatur in der Säule auf 77–78 °C erhöht. Die Auswahlgeschwindigkeit kann hier etwas erhöht werden. Erhöhen Sie die Kühlung leicht und erhöhen Sie die Hitze.
- Sobald die Temperatur in der Kolonne während der Auswahl des „Körpers“ zu steigen begann, ist es an der Zeit, den Auffangtank zu wechseln und die Rückstände auszuwählen, wenn Sie daran interessiert sind, natürlich.
Im Allgemeinen ist klar, dass die Arbeit mit einer Destillationskolonne nicht so schwierig ist; es ist wichtig, sich daran zu gewöhnen, das Temperaturregime einzeln oder zwei gleichzeitig anzupassen, da die Qualität der ausgewählten Fraktionen weitgehend davon abhängt. Was die Verwendung des resultierenden Getränks angeht, entscheidet jeder Besitzer selbst: Wird reines Ethanol für medizinische oder technische Zwecke verwendet?
Für die Eigenproduktion von Starkgetränken benötigt man modernes Equipment aus Qualitätsmaterial. Im Handel bieten Hersteller Modelle an, die in Brenner und Gleichrichter unterteilt sind. Viele unerfahrene Destillerien quälen sich mit der Frage: Was ist besser für das Heimbrauen – eine Kolonne oder eine Mondscheindestille?
Das Funktionsprinzip ist nicht viel anders, aber das Endprodukt aus der Destillationskolonne ist besser und sauberer und in Bezug auf die Stärke sucht es seinesgleichen, da es sich um fast reinen Alkohol handelt. Um herauszufinden, wie sich diese Geräte unterscheiden, welche technischen Parameter sie haben, welche individuellen Nuancen es gibt und ob es Nachteile gibt, müssen Sie diesen Artikel lesen.
Der gesamte Destillationsprozess besteht aus einem Wärmeaustausch, der im Produkt stattfindet; während des Abkühlvorgangs wird das Rohmaterial abgetrennt und die gereinigte Substanz erscheint am Ausgang des Geräts. Bei unterschiedlichen Erhitzungstemperaturen erhält man unterschiedliche Stoffe:
- t=+56 C – wir bekommen Aceton;
- t=+65 C – Methylalkohol kann isoliert werden;
- und erst bei t=+78 C wird rektifizierter Alkohol erhalten;
- Wenn wir weiter bis zum Siedepunkt von Wasser und höher, beispielsweise bis zu 100 Grad, erhitzen, erhalten wir am Ausgang Wasser, das mit Fuselölen und allen möglichen Verunreinigungen aromatisiert ist.
Grundlage des gesamten in der Kolonne ablaufenden Prozesses ist der Kontakt der flüssigen und dampfförmigen Zustände verschiedene Substanzen, wodurch verschiedene Dämpfe freigesetzt werden, die sich im Rückflusskühler absetzen und nur alkoholhaltige Dämpfe weiterströmen.
Im Verdampfer erfolgt eine zusätzliche Erwärmung, jedoch nur bis zu +78 Grad, sodass alle schädlichen Verunreinigungen und Wasser kondensieren und im Gerät verbleiben. In verschiedenen Bereichen des Produkts kommt es zu einer individuellen Wechselwirkung von Dampf und Kondensat, wobei sich Fraktionen unterschiedlicher Temperaturniveaus zu Kondensat niederschlagen und in den unteren Teil fließen.
Eine Kolonne ist ein Gerät mit einer bestimmten Höhe und einem über die gesamte Länge verlängerten Behälter, sodass unterschiedliche Temperaturen erreicht werden: Nur alkoholhaltige Dämpfe gelangen ganz nach oben, alle anderen Fraktionen fallen ins Kondensat, da die Temperatur niedriger ist wird benötigt, damit sie kochen. Der Geschmack und die Stärke des Endprodukts unterscheiden sich je nach Sorte deutlich bessere Seite aus Mondschein, der durch einen Standardbrenner geleitet wurde.
Moderne Kolonnenmodelle zeichnen sich durch eine sehr hohe Produktivität aus und der bei der Rektifikation entstehende Alkohol weist keinen Fuselgeruch oder Fremdverunreinigungen auf.
Was ist der Unterschied zwischen einer Moonshine-Destille und einer Destillationskolonne?
Der wichtigste Unterschied: Ein Standardgerät für das Heimbrauen besteht aus einem Destillationswürfel und einer Kühlschlange, in der alkoholhaltige Dämpfe kondensiert werden. Einige Modelle verfügen über einen Trockendampfer, in dem Verunreinigungen hochwertig abgetrennt und Dämpfe aromatisiert werden, um erstklassigen Alkohol in Form von Brandy oder Whisky herzustellen.
Die Säule ist ein ziemlich komplexes Gerät; sie dient hauptsächlich der Reinigung von bereits hergestelltem Mondschein, um alle kleinsten Fremdeinschlüsse zu entfernen und reinen Alkohol zu erhalten. Die Konstruktion besteht aus Edelstahl, Kupfer oder Messing, da im Inneren sehr komplexe Hochtemperaturprozesse ablaufen und die Korrosionsbeständigkeit recht hoch sein sollte.
Der untere Teil der Kolonne wird Schublade genannt, der obere Teil Kühler oder Rückflusskühler, da hier die endgültige Trennung der verschiedenen Schleime erfolgt. In seiner Hülle befindet sich eine Röhre zur Kommunikation Umfeld damit der Innendruck den zulässigen Wert nicht überschreitet. Wir haben bereits alle Nuancen der Arbeit besprochen und lassen sie daher weg.
Das Produkt wird auf einem Destillationstank oder -würfel installiert und alle Verbindungen müssen perfekt abgedichtet sein. Ganz oben befindet sich ein Auslassrohr für Alkoholdampf, am besten ist es, wenn zusätzlich ein Kühlschrank vorhanden ist. Die Höhe des Produkts ist ordentlich, einige Proben sind bis zu 2 m hoch, daher passt dieses Design möglicherweise nicht in den Innenbereich: 2 m + Tank + Herd. Die beste Option- Erhitzen Sie den Tank auf einem speziellen Mondscheinofen: Er hat kleine Abmessungen, wie ein elektrischer Tischherd.
Es wird nicht empfohlen, Maische durch eine Kolonne zu destillieren, obwohl die Hersteller heute bereits die Herstellung verbesserter Proben beherrschen, die dieser Anwendung gewachsen sind. Das Urteil ist einfach: Moonshine-Destillierapparate sind für die Destillation von Rohalkohol konzipiert und die Kolonne kann ihn fast vollständig von Gerüchen und schädlichen Verunreinigungen reinigen.
Erinnern! Um reinen Alkohol zu erhalten, wird eine Destillationskolonne verwendet. Wenn Sie Rakia oder Brandy herstellen möchten, bei dem Sie das Aroma und den spezifischen Geschmack des Originalprodukts benötigen, verwenden Sie nur eine Destille mit Mondschein.
Arten von Moonshine-Destillierapparaten und Destillationskolonnen
Insgesamt gibt es weltweit zwei Haupttypen von Geräten zum praktischen Mondscheinbrauen:
- Alkoholhaltige Dämpfe werden zur Kühlung seitlich abgeführt – direkt in die Spule oder durch eine Dampfkammer.
- Die Dämpfe werden nach oben in eine Destillationseinrichtung abgeleitet, wo Verunreinigungen abgetrennt werden. Komplettreinigung vor Gerüchen und anschließender Abkühlung.
Klassische Geräte werden nach dem Kühlsystem unterteilt: mit Spule oder Direktstrom, wobei das Kühlelement der Kühlschrankkörper ist.
Die Spalten sind nach der Menge des erhaltenen Endprodukts unterteilt:
- einfach, Gewährleistung der Trennung des Ausgangsmaterials in zwei Endprodukte – rektifiziertes Produkt und Sediment;
- komplex – sie ermöglichen die Trennung in mehr als zwei Produkte, Kolonnen mit der Auswahl zusätzlicher Fraktionen in Form von Seitenströmen und aus speziellen Strippern.
Es gibt auch eine Unterteilung nach Zweck, Druckhöhe, Funktionsprinzip oder Kontaktorganisation innerhalb der Struktur.
Darüber hinaus werden die Spalten in vollständige und unvollständige Spalten unterteilt. Unvollständige Produkte werden in zwei weitere Typen unterteilt:
- Eine Maische- oder Destillationskolonne, die nach folgendem Prinzip funktioniert: Alkoholhaltiger Dampf tritt in die obere Platte ein und verlässt den Würfel reines Wasser. Im Kühlschrank fällt Kondenswasser aus, aber der Rückflusskühler ist nicht installiert.
- In Alkoholsäulen geschieht alles spiegelbildlich: Unter der unteren Platte wird Dampf zugeführt. Der Alkohol wird im oberen Teil entfernt, der Rest mit Wasser wird im unteren Teil entfernt; der Rückflusskühler übernimmt die Funktion der Zufuhr eines flüssigen Mediums. Solche Säulen werden auf Alambiks installiert.
Die ersten sind nicht für die Herstellung von reinem Alkohol gedacht und die zweite Option dient nicht der Herstellung von reinem Wasser.
Eigenschaften beider Geräte
Jeder weiß, dass der Hauptzweck einer Mondscheindestille darin besteht, durch Destillation und anschließende Reinigung alkoholhaltige Flüssigkeit aus der Maische zu gewinnen. Die wichtigsten technischen Parameter sind:
Volumen
Dieser Faktor beeinflusst den Produktionsumfang zu Hause, daher basiert die Produktauswahl auf diesem Parameter: Je mehr Maische, desto mehr Liter Rohalkohol werden gereinigt verschiedene Methoden oder eine erneute Destillation durchgeführt wird.
Material
Im Grunde alle Details moderne Modelle aus lebensmittelechtem oder medizinischem Edelstahl. In der Produktion werden folgende Marken verwendet:
- AISI 304 wird aufgrund seiner relativ hohen Reinigungseigenschaften in der Medizin, in Milchviehbetrieben und ähnlichen Fabriken eingesetzt;
- 430-Stahl ist von geringer Qualität, aber daraus hergestellte Produkte können auf Induktionsherden erhitzt werden;
- Legierungen mit Kupfer und Kombinationen von Stählen verschiedene Marken findet sich in vielen Modellen von Mondscheindestillierapparaten aus in- und ausländischer Produktion.
IN selbstgemachte Geräte Aluminium wird immer noch verwendet, aber es wird fast durch zuverlässigere Materialien ersetzt. Spulen bestehen aus Kupfer oder Messing; nur Elite-Geräte, sogenannte Alambiks, die zur Herstellung von selbstgemachtem Elite-Alkohol verwendet werden, bestehen vollständig aus Kupfer.
Zusätzliche Geräte
Dazu gehören ein Thermometer, ein Alkoholmessgerät, ein Dampfgarer, ein Rückflusskühler und andere, die bei der Steuerung des Destillationsprozesses helfen. Eine wiederholte Reinigung führt zu einem guten Ergebnis, wird jedoch nicht durchgeführt, wenn Sie ein aromatisches Getränk mit Duft benötigen.
Der Übersichtlichkeit halber ist es besser, die technischen Eigenschaften von Universaldestillationskolonnen in Form einer kleinen Tabelle darzustellen:
Alle Dichtungsverbindungen in der Säule bestehen aus lebensmittelechtem Hochtemperatursilikon Garantiezeit Betrieb mindestens 10-20 Jahre, zulässige Temperatur bis +150°C.
Vorteile und Nachteile
Eine Standardanlage zur Herstellung von Mondschein hat folgende Vorteile:
- Das einfachste Design, das Funktionsprinzip ist für alle Benutzer klar, kann ohne großen finanziellen Aufwand unabhängig hergestellt werden.
- Es gibt eine Vielzahl an Rezepten, die dem fertigen Modell beiliegen, Sie können diese jedoch durch das Studium des Rezepts im Internet deutlich erweitern.
- Hohe Zuverlässigkeit des Designs und aller Materialien.
- Niedrige Kosten, was sich insbesondere auf die breite Verfügbarkeit für alle Bevölkerungsgruppen auswirkt.
Destillationskolonnen haben ihre Vorteile:
- Erhalten Sie ein reines Produkt ohne Geruch und Fremdverunreinigungen.
- Die Festigkeit des Endprodukts ist viel höher als die eines einfachen Geräts.
- Es wird verwendet, um alkoholhaltige Flüssigkeiten von zuckerhaltiger Maische zu trennen, da dort viele Fremdverunreinigungen und Gerüche vorhanden sind.
Im Vergleich dazu weist das klassische Gerät weitere negative Eigenschaften auf:
- geringe Produktivität;
- geringer Alkoholgehalt – nicht mehr als 70 %;
- geringer Reinigungsgrad bei der Primärdestillation;
- Gefahr besteht, wenn die Sicherheitsvorkehrungen nicht befolgt werden.
Destillationskolonnen haben nur einen Nachteil – die große Höhe der Struktur.
Was ist besser zu wählen
Wenn wir das Design eines klassischen Mondscheinprodukts und einer Destillationskolonne vergleichen, fällt der Unterschied auf, und sie werden für unterschiedliche Zwecke verwendet. Daher hängt Ihre Wahl direkt von Ihren Zielen sowie davon ab, was Sie destillieren möchten:
- Für Weinmaische sowie Maische auf der Basis von Beeren und Früchten ist es besser, eine Mondscheindestille zu verwenden.
- Für Zuckermaische ist es besser, eine Säule zu verwenden, da das Endprodukt sauber und geruchlos ist.
Heutzutage werden Modelle universeller Produkte angeboten, die als einfacher Destillierapparat oder als leistungsstarke Destillationskolonne eingesetzt werden können.
Besonders gefragt bei erfahrenen Brennern sind Geräte deutscher Hersteller, die über eine zusätzliche Schublade verfügen, die in den Brenner eingeschraubt wird. Beispielsweise haben die Kolonne und der Apparat die gleiche Produktivität von 2 l/h, aber das Produkt ist ganz anders:
- die Dichte bzw. Festigkeit eines klassischen Produkts beträgt nur 60 % und die einer Säule 96 %;
- Der Reinigungsgrad einer Destillerie ist 60-mal niedriger als der einer Kolonne.
Moonshine-Destillierapparate sind aufgrund ihrer Abmessungen praktischer und die Säulen sind viel höher – die kompakteste wird etwa einen Meter hoch sein.
Wenn wir die Produktivität verschiedener Produkte vergleichen, dann produziert der Klassiker 2 Liter Rohalkohol pro Stunde und die Kolonne 2 Liter reinen Alkohol 96,6 %, oder in Bezug auf 60 % Mondschein 6-7 Liter. Daher müssen Sie beim Kauf entscheiden, was Ihnen wichtiger ist – die Reinheit des Endprodukts oder die einfache Verwendung des Produkts überall. Auch die finanzielle Leistungsfähigkeit spielt eine wichtige Rolle.
Schlussfolgerungen
Wenn wir über die Reinheit des Endprodukts sprechen, dann sind Destillationskolonnen einer einfachen Mondscheindestille um Längen überlegen, aber sehr wichtig hat eine finanzielle Seite. Jeder Benutzer wählt das gewünschte Modell für sich aus, aber wir stellen nüchtern fest, dass die Klassiker des Genres immer noch verlieren technischer Fortschritt dargestellt durch eine produktivere Destillationskolonne in Bezug auf die wichtigsten technischen Indikatoren.
§ 13.2 Destillationskolonnen: ihre Konstruktion und Funktionsweise
Wie oben erwähnt, erfolgt die Rektifikation in speziellen Geräten – Rektifikationskolonnen, die die Hauptelemente von Rektifikationsanlagen sind.
Berichtigungsprozess kann periodisch und kontinuierlich durchgeführt werden, unabhängig von der Art und Ausführung der Destillationskolonnen. Betrachten wir den Prozess der kontinuierlichen Rektifikation, der in der Industrie zur Trennung von Flüssigkeitsgemischen eingesetzt wird.
Destillationskolonne- Vertikale zylindrischer Apparat mit geschweißtem (oder(vorgefertigtes) Gehäuse, in dem sich Massen- und Wärmeaustauschvorrichtungen (horizontale Platten) befinden 2 oder Düse). Am unteren Ende der Säule (Abb. 13.3) befindet sich ein Würfel 3, in dem die untere Flüssigkeit kocht. Die Erwärmung im Würfel erfolgt durch Totdampf in einer Rohrschlange oder in einem Rohrbündelheizkessel. Ein integraler Bestandteil der Destillationskolonne ist der Rückflusskühler 7, der dazu dient, den die Kolonne verlassenden Dampf zu kondensieren.
Die Rektifikationsbodenkolonne funktioniert wie folgt. Der Würfel wird ständig erhitzt und die noch vorhandene Flüssigkeit kocht. Der im Würfel erzeugte Dampf steigt die Säule hinauf. Das zu trennende Ausgangsgemisch wird zum Sieden vorgeheizt. Serviert wird auf einem Nährteller 5, der die Säule in zwei Teile teilt: untere (erschöpfende) 4 und Obermaterial (Stärkung) 6. Die anfängliche Mischung von der Nährstoffplatte fließt auf die darunter liegenden Platten und interagiert auf ihrem Weg mit dem Dampf, der sich von unten nach oben bewegt. Durch diese Wechselwirkung wird der Dampf mit der leicht flüchtigen Komponente angereichert und die herabströmende Flüssigkeit, die an dieser Komponente verarmt ist, wird mit der leicht flüchtigen Komponente angereichert. Am Boden der Kolonne findet der Prozess der Extraktion (Absaugung) der leicht flüchtigen Komponente aus der Ausgangsmischung und deren Umwandlung in Dampf statt. Ein Teil des Endprodukts (rektifiziertes Produkt) wird zur Bewässerung des oberen Teils der Kolonne zugeführt.
Die Flüssigkeit, die zur Bewässerung oben in die Kolonne eintritt und von oben nach unten durch die Kolonne fließt, wird als Rückfluss bezeichnet. Dampf, der mit dem Rückfluss auf allen Böden des oberen Teils der Kolonne interagiert, wird mit einer leicht flüchtigen Komponente angereichert (verstärkt). Der die Kolonne verlassende Dampf wird zum Rückflusskühler 7 geleitet, wo er kondensiert. Das resultierende Destillat wird in zwei Ströme aufgeteilt: Einer wird als Produkt zur weiteren Kühlung und zum Lager für Fertigprodukte geschickt, der andere wird als Rückfluss zurück zur Kolonne geleitet.
Das wichtigste Element einer Bodendestillationskolonne ist der Boden, da auf ihm die Wechselwirkung von Dampf mit Flüssigkeit stattfindet. In Abb. 13.4 zeigt ein Diagramm des Geräts und der Bedienung Kappenplatte. Sie hat einen Hintern 1, hermetisch mit dem Säulenkörper verbunden 4, Dampfrohre 2 und Abflussrohre 5. Dampfrohre sind so konzipiert, dass sie von der Bodenplatte aufsteigende Dämpfe weiterleiten. Durch die Abflussrohre fließt Flüssigkeit von der darüber liegenden Platte zur darunter liegenden. Auf jedem Dampfrohr ist eine Kappe montiert 3, Dabei werden Dämpfe in eine Flüssigkeit geleitet, durch diese hindurchgeperlt, abgekühlt und teilweise kondensiert. Der Boden jeder Platte wird durch die Dämpfe der darunter liegenden Platte erhitzt. Darüber hinaus wird beim teilweisen Kondensieren von Dampf Wärme freigesetzt. Aufgrund dieser Hitze siedet die Flüssigkeit auf jeder Platte und bildet dabei eigene Dämpfe, die sich mit den Dämpfen der darunter liegenden Platte vermischen. Der Flüssigkeitsstand auf der Platte wird über Abflussrohre aufrechterhalten.
Reis. 13.3. Diagramm der Destillationskolonne: / - Körper; 2 - Gerichte; 3 - Würfel; 4, 6 - erschöpfende und verstärkende Teile der Säule; 5 -Ernährungsteller; 7 - Rückflußkühler
Die auf der Platte ablaufenden Prozesse lassen sich wie folgt beschreiben (siehe Abb. 13.4). Lassen Sie Dämpfe der Zusammensetzung A von der unteren Platte auf die Platte strömen, und Flüssigkeit der Zusammensetzung strömt von der oberen Platte durch das Überlaufrohr IN. Durch die Wechselwirkung von Dampf A mit Flüssigkeit IN(Dampf, der durch die Flüssigkeit sprudelt, verdampft diese teilweise und kondensiert teilweise.) Es entsteht ein neuer Dampf der Zusammensetzung MIT und neue Flüssigkeitszusammensetzung D, sind im Gleichgewicht. Durch den Betrieb der Platte entsteht neuer Dampf MIT reicher an flüchtigen Substanzen als der Dampf, der von der unteren Platte kommt A, das heißt, es befindet sich Dampf auf dem Teller MIT angereichert mit einer leicht flüchtigen Substanz. Neue Flüssigkeit D, im Gegenteil, es wurde ärmer an flüchtigen Bestandteilen im Vergleich zur Flüssigkeit, die von der oberen Platte kam IN, Das heißt, auf der Platte wird die Flüssigkeit an der leicht flüchtigen Komponente abgereichert und an der leicht flüchtigen Komponente angereichert. Kurz gesagt besteht die Arbeit der Platte darin, den Dampf anzureichern und die Flüssigkeit von flüchtigen Bestandteilen zu befreien.
Reis. 13.4. Diagramm des Aufbaus und der Funktionsweise einer Kappenplatte: / - Unterseite der Platte; 2 - Wasserdampfrohr;
3 - Deckel; 4 - Säulenkörper; 5 - Abflussrohr
Reis. 13.5. Darstellung der Funktionsweise der Destillationsplatte im Diagramm bei-x: 1- Gleichgewichtskurve;
2 - Linie der Arbeitskonzentrationen
Als Platte bezeichnet man eine Platte, auf der sich ein Gleichgewichtszustand zwischen den von ihr aufsteigenden Dämpfen und der herabströmenden Flüssigkeit einstellt theoretisch. Unter realen Bedingungen wird aufgrund der kurzfristigen Wechselwirkung von Dampf mit Flüssigkeit auf den Platten kein Gleichgewichtszustand erreicht. Die Trennung des Gemisches auf einer realen Platte ist weniger intensiv als auf einer theoretischen. Um die Arbeit einer theoretischen Platte zu leisten, sind daher mehr als eine reale Platte erforderlich.
In Abb. Abbildung 13.5 zeigt anhand eines Diagramms die Funktionsweise einer Destillationsplatte bei-X. Die theoretische Platte entspricht einem schattierten rechtwinkligen Dreieck, dessen Schenkel dem Konzentrationszuwachs der flüchtigen Komponente im Dampf entsprechen Schnurrbart-j A , und das Ausmaß der Abnahme der Konzentration der flüchtigen Komponente in der Flüssigkeit ist gleich X B - X D . Die Segmente, die den angegebenen Konzentrationsänderungen entsprechen, konvergieren auf der Gleichgewichtskurve. Dies setzt voraus, dass sich die die Platte verlassenden Phasen im Gleichgewichtszustand befinden. In Wirklichkeit wird der Gleichgewichtszustand jedoch nicht erreicht und die Konzentrationsänderungsabschnitte erreichen nicht die Gleichgewichtskurve. Das heißt, die Arbeitsplatte (real) entspricht einem kleineren Dreieck als dem abgebildeten
in Abb. 13.5.
Die Ausführungen der Böden von Destillationskolonnen sind sehr vielfältig. Betrachten wir kurz die wichtigsten.
Säulen mit Kopfplatten in der Industrie weit verbreitet. Die Verwendung von Kappen sorgt für einen guten Kontakt zwischen Dampf und Flüssigkeit, eine effektive Durchmischung auf der Platte und einen intensiven Stoffaustausch zwischen den Phasen. Die Form der Kappen kann rund, facettiert und rechteckig sein, die Platten können ein- oder mehrkappenförmig sein.
Eine Platte mit gerillten Kappen ist in Abb. dargestellt. 13.6. Dampf aus der unteren Wanne strömt durch die Lücken und gelangt in die oberen (umgekehrten) Rinnen, die ihn zu den mit Flüssigkeit gefüllten unteren Rinnen leiten. Hierbei perlt Dampf durch die Flüssigkeit und sorgt so für einen intensiven Stoffaustausch. Der Flüssigkeitsspiegel auf der Platte wird durch eine Überlaufvorrichtung aufrechterhalten.
Kolonnen mit Siebböden sind in Abb. dargestellt. 13.7. Die Platten haben eine große Anzahl von Löchern mit kleinem Durchmesser (von 0,8 bis 3 mm). Der Druck des Dampfes und die Geschwindigkeit seines Durchgangs durch die Löcher müssen dem Druck der Flüssigkeit auf der Platte entsprechen: Der Dampf muss den Druck der Flüssigkeit überwinden und verhindern, dass diese durch die Löcher auf die darunter liegende Platte austritt. Daher erfordern Siebböden eine entsprechende Regulierung und reagieren sehr empfindlich auf Veränderungen im Regime. Sinkt der Dampfdruck, sinkt die Flüssigkeit aus den Siebböden. Siebböden reagieren empfindlich auf Verunreinigungen (Niederschläge), die die Löcher verstopfen und so Bedingungen für die Entstehung hoher Drücke schaffen können. All dies schränkt ihre Verwendung ein.
Gepackte Säulen(Abb. 13.8) unterscheiden sich darin, dass die Rolle der Platten in ihnen die sogenannte „Düse“ spielt. Als Düse werden spezielle Keramikringe (Raschig-Ringe), Kugeln, kurze Röhren, Würfel, sattelförmige, spiralförmige usw. Körper aus verschiedenen Materialien (Porzellan, Glas, Metall, Kunststoff usw.) verwendet.
Dampf tritt von einem entfernten Kessel in den unteren Teil der Kolonne ein und bewegt sich in der Kolonne nach oben in Richtung der fließenden Flüssigkeit. Über eine große Oberfläche aus gepackten Körpern verteilt, kommt der Dampf in intensiven Kontakt mit der Flüssigkeit und tauscht dabei Komponenten aus. Die Düse muss eine große Oberfläche pro Volumeneinheit haben, einen geringen hydraulischen Widerstand aufweisen, beständig gegen die chemische Wirkung von Flüssigkeit und Dampf sein, eine hohe mechanische Festigkeit aufweisen und kostengünstig sein.
Füllkörpersäulen haben einen geringen hydraulischen Widerstand und sind einfach zu verwenden: Sie können leicht entleert, gewaschen, gespült und gereinigt werden.
Reis. 13.6. Platte mit gerillten Kappen: A- generelle Form; B- Längsschnitt; V- Diagramm der Plattenbedienung
Reis. 13.7. Schematische Darstellung der Siebplattenstruktur: / - Kolonnenkörper; 2 - Platte; 3 - ein Abflussrohr; 4 - hydraulischer Verschluss; 5 - Löcher
Reis. 13.8. Schema einer gepackten Destillationskolonne: 1 - rahmen; 2 - Eingabe der Ausgangsmischung; 3 - Dampf; 4 - Bewässerung; 5 - Gitter; 6 - Düse; 7-Auslass für hochsiedendes Produkt j-. 8 - Fernkessel