Enduit terrazitique et pierre. Enduits terrazit Application des enduits terrazit
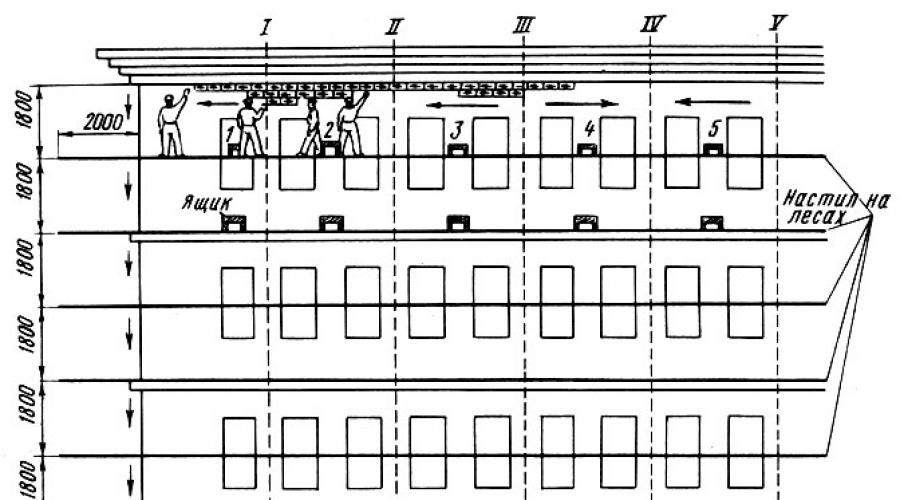
Lire aussi
Enduits décoratifs. Les enduits décoratifs sont faits pour l'extérieur et décoration d'intérieur bâtiments, ainsi que pour la finition des façades panneaux muraux et blocs. Finir avec une solution colorée permet de diversifier solution de couleur façades et imiter des types de finitions plus coûteux, tels que le revêtement en pierre naturelle.
Enduits décoratifs colorés.
Les principaux types d'enduits décoratifs colorés sont :
- chaux-sable;
- terrazite;
- pierre;
- sgraffite.
Les enduits chaux-sable sont les enduits colorés les plus économiques. Les charges qu'ils contiennent sont généralement du sable de quartz et, beaucoup moins souvent, des déblais rocheux. Après finition, un tel plâtre imite la roche sédimentaire - le grès.
Postuler diverses méthodes l'application d'une couche de revêtement plastique et les méthodes de finition dans un état plastique ou semi-durci permettent d'obtenir une variété de textures de surface du plâtre fini. Par exemple, une surface imitant la pierre naturelle - le travertin - peut être obtenue.
Enduits de pierre.
Enduits de pierre. Les enduits de pierre sont les plus exigeants en main-d'œuvre et vue complexe travaux de plâtrage. La charge dans la solution pour eux est une miette de pierre d'une certaine roche. Les surfaces durcies sont traitées avec des outils spéciaux de travail de la pierre à percussion. Après traitement, la surface d'un tel plâtre imite une certaine roche - granit, marbre, etc. Au lieu de travailler avec des instruments à percussion, les enduits de pierre sont gravés avec une solution à 10% après durcissement. d'acide chlorhydrique suivi d'un lavage à l'eau. L'acide détruit la couche superficielle du ciment durci, exposant la surface des éclats de pierre.
Enduits terrazitiques.
Enduits terrazitiques. Les enduits Terrazit sont obtenus à partir de mélanges de terrasite spécialement préparés. En tant que charge, en plus du sable de quartz, des éclats de pierre de différentes tailles sont utilisés. Un tel plâtre est traité à l'état semi-durci avec une sableuse, le grattage d'un cycleur denté et des brosses à ongles. À la suite du traitement, une texture de surface à grain fin ou moyen est obtenue, imitant le tuf ou le grès traité.
Plâtre sgraffite.
Plâtre sgraffite (de l'italien - rayé). Le plâtre Sgraffite est un type spécial de plâtre décoratif et artistique utilisé pour la finition des bâtiments. Lors du plâtrage de la surface de cette manière, 2 couches ou plus sont d'abord appliquées. couleur différente, puis coupez partiellement (grattez) la ou les couches supérieures, créant ainsi un motif ornemental ou de tracé coloré en relief.
Le plâtrage avec des mortiers décoratifs est réalisé en 2-3 couches. Le but de la première couche, faite de mortier de plâtre ordinaire, est de niveler la surface. La deuxième couche - sol (préparatoire) sert de base à la troisième - couche décorative. Avec des surfaces suffisamment planes, elles se limitent à deux couches - au sol et décoratives.
À enduit décoratif s'est avéré de haute qualité, la base sous la couche décorative doit répondre à certaines exigences: la composition et la consistance de la couche de sol doivent être constantes, car lors de l'application de la couche décorative, sa phase liquide (eau, liant, pigment) est aspirée dans les pores de la couche de sol. Avec une porosité inégale de la couche de sol, des taches apparaissent à la surface de la couche décorative. Pour éviter cela, le sable de la couche de fond doit avoir une composition de grain constante et le dosage des composants doit être strictement maintenu sur toute la surface enduite.
Pour la couche de sol, il est conseillé d'utiliser des mélanges secs, qui sont produits dans la quantité requise en un seul lot. Dans ce cas, lors de la préparation de la solution, seul le dosage du lait de chaux est surveillé, qui est préparé immédiatement dans le volume requis. Dans le même but, la couche d'apprêt est humidifiée uniformément sur toute la surface avant d'appliquer la couche décorative. Il est préférable de le faire la nuit et d'appliquer une couche de finition sur l'apprêt humide le lendemain.
Le sable pour la couche de sol doit être à grain moyen, de préférence du sable de rivière avec une teneur de 35 ... 40% de grains avec une granulométrie de 0,6 ... La chaux est utilisée Haute qualité. La pâte à la chaux après trempe se conserve au moins un mois. Avec une exposition plus courte, la pâte est nettoyée des particules non éteintes en la faisant passer à travers un tamis vibrant.
La résistance de la couche de sol ne doit pas être inférieure à la résistance de la couche décorative. Pour les enduits en pierre forgés, il est préférable d'augmenter quelque peu la résistance de la couche d'apprêt, car cela empêchera les éclats de pierre d'y être pressés.
Préparé pour la couche de sol les files d'attente suivantes: chaux-ciment, ciment-chaux, ciment, chaux. La composition exacte de la solution pour la couche de sol est définie dans le laboratoire de construction.
Les enduits décoratifs doivent répondre à certaines exigences opérationnelles, artistiques et esthétiques. La composition des mortiers décoratifs, le type et la taille des agrégats doivent correspondre au projet, ainsi que la texture et la couleur - à la norme établie par le projet. Les enduits colorés doivent être uniformes sur toute la surface, sans taches, joints et autres défauts, et la rugosité de leur texture doit être la même sur toute la surface.
La composition de travail de la solution décorative est sélectionnée de manière empirique afin d'établir les paramètres optimaux garantissant la qualité requise de la solution. Pour ce faire, des cartes de test de taille 25 x 40 ou 50 x 50 cm sont plâtrées, en modifiant légèrement le rapport des composants.
Les cartes sont numérotées, enregistrant la composition adoptée pour chacune d'elles. Après approbation de l'échantillon, la composition acceptée du mélange est strictement observée.
Comme liants dans la préparation des mortiers décoratifs pour le plâtrage des façades, les mélanges hydrauliques ou les ciments Portland (unis, blancs ou colorés) sont le plus souvent utilisés. Pour les enduits colorés à l'intérieur des bâtiments - liants à la chaux et au gypse. Dans les ciments Portland ordinaires, en règle générale, des additifs sont introduits pour l'amincissement sous forme de calcaire finement broyé, de marbre, de dolomite, de diatomite, d'oxyde de titane dans une quantité allant jusqu'à 25% en poids du ciment. La marque de ciment blanchi ne doit pas être inférieure à 300. Le ciment Portland blanc donne parfois une teinte verdâtre, pour l'enlever, on ajoute au ciment 5% d'ocre doré ou 1% d'ocre ordinaire.
La chaux de haute qualité est vieillie pendant au moins un mois. Il ne doit pas contenir de cendres, ce qui réduit la blancheur de la chaux. Le lait de chaux est filtré à travers un tamis à cellules de 0,5 ... 1,0 mm. Les particules de chaux caillée tombées lors du traitement de la couche de revêtement provoqueront la formation de taches blanches. En tant qu'additifs colorants dans les solutions, des pigments naturels et artificiels résistants aux alcalis et à la lumière sont utilisés - ocre, plomb rouge de fer, momie, oxyde de chrome, outremer. Lait de chaux avant mesure dose requise bien mélanger. Les ingrédients secs sont d'abord chargés dans le malaxeur à mortier et mélangés, puis ajoutés eau propre ou du lait de citron vert et mélanger à nouveau pendant 5...7 minutes. La solution est préparée en une quantité telle qu'elle peut être utilisée en une heure.
N'ajoutez pas de lait de chaux ou d'eau à la solution préparée, car cela changerait sa couleur.
Compositions de couleur chaux-sable. Les compositions colorées à la chaux et au sable additionnées de ciment Portland sont principalement utilisées pour le plâtrage des façades. Beaucoup moins souvent, les solutions colorées sont utilisées pour la décoration intérieure des bâtiments.
Dans les solutions pour enduits colorés, le liant principal est de la chaux séchée bien trempée. Pour augmenter la résistance et la résistance à l'eau du mortier, jusqu'à 10% du poids de la pâte de chaux y sont ajoutés avec du ciment Portland ordinaire, avec des tons sombres de la couche de plâtre, ou du ciment Portland blanc avec des tons clairs. Pour les travaux extérieurs, en règle générale, les mortiers purement à la chaux ne sont pas utilisés.
La couleur souhaitée de la solution est obtenue en y ajoutant des pigments résistants aux alcalis et à la lumière. La teinte souhaitée est obtenue en introduisant un pigment blanc ou de la farine de pierre de marbre, de calcaire dans la solution en tant que diluant. Le sable de quartz pur est utilisé comme charge pour les solutions de sable coloré. Dans certains cas, pour obtenir du plâtre certaine couleur, utilisez du marbre, du calcaire, des sculptures en tuf.
La plus grande taille de sable ne doit pas dépasser 1,25 mm avec une prédominance de grains de 0,3 ... soit au moins 50%. Le mélange sec est préparé immédiatement en quantité suffisante pour l'ensemble de la portée des travaux. La mobilité du mortier chaux-sable pour les couches de sol doit correspondre à l'immersion du cône de référence de 6 ... 10 cm lors de l'application mécanisée et de 8 ... 9 cm
La plasticité de la solution à l'installation est vérifiée de la manière suivante: la solution est appliquée avec une spatule en plâtre ou une truelle avec une couche de 5 ... 10 mm. La présence de lacunes indique sa plasticité insuffisante.
La consistance du mortier plastique dépend du type de finition, de la texture et de la méthode d'application. Cela peut aller de la densité de la crème sure à la pâte. Pour chaque type de finition, il est nécessaire de respecter strictement le rapport accepté entre la quantité d'enrobé sec et d'eau ou de lait de chaux. Avant utilisation, la solution est soigneusement mélangée.
Solutions pour enduit terrazitique.
Solutions pour enduit terrazitique. Dans la plupart des cas, les mortiers sont préparés à partir de mélanges terrazitiques secs prêts à l'emploi, constitués de l'agrégat approprié (marbre, granit ou calcaire), de ciment et de chaux hydratée. Dans l'établissement, ils ne sont mélangés qu'avec de l'eau, en respectant le dosage d'eau accepté.
Les mélanges Terrazit sont produits dans les couleurs suivantes : bleu, blanc, gris clair, crème, jaune, rose, bleu, turquoise, vert, etc. Si la teinte obtenue ne correspond pas au projet, vous pouvez obtenir la teinte souhaitée en mélangeant 2 -3 mélanges de couleurs primaires. Les mélanges doivent être secs, exempts de grumeaux et de matières étrangères, et la couleur et le ton de chaque lot doivent être uniformes. Les liants et agrégats de différentes tailles et de différentes couleurs doivent être répartis uniformément dans le mélange. Le mélange doit être exempt de grumeaux de pigments, ce qui peut être vérifié en lissant la surface du mélange avec une spatule. Si l'approvisionnement en enrobés secs pour terrasite est difficile, les enrobés sont préparés sur place.
Préparation du mélange de terrazite. L'agrégat est obtenu à partir de carrières de pierre ou d'usines de traitement de pierre à proximité. La mie d'enduit terrazitique utilisé pour les façades doit être résistante au gel.
Le sable de différentes roches donne les couleurs souhaitées des enduits de terrazite :
- les couleurs blanches donnent des sables blancs et clairs de quartz, de marbre et de calcaire;
- jaune clair - sable de quartz jaune naturel, calcaire jaune et sables dolomitiques;
- rose clair - sable composé de granit rouge, de marbre et de tuf;
- jaune pâle clair - sables lavés d'argile de montagne, sables de rivière, sables de marbre rouge-jaune;
- vert clair et turquoise - sables de syénite, diorites et autres roches de couleur et d'ombre vertes;
- terre cuite - sables de tuiles et de briques concassées;
- gris clair - sables et granits gris concassés, marbres, calcaire, sable lavé au laitier.
Pour préparer un mélange de mortier de terrazite, l'agrégat et le mélange de ciment avec des pigments sont d'abord chargés dans le mélangeur de mortier et soigneusement mélangés. L'eau et le lait de chaux sont introduits à des doses strictement mesurées après avoir mélangé le mélange sec et mélangé à nouveau. Les plastifiants sont introduits avec de l'eau et du lait de chaux. Avec une petite quantité de travail, les composants sont mélangés manuellement. Tout d'abord, des portions exactement mesurées d'agrégat et un mélange de ciment et de pigments sont mélangés avec une pelle dans une boîte. Le mélange est fermé en le mouillant avec de l'eau ou du lait de chaux d'un arrosoir et en pelletant simultanément. Il n'est pas recommandé de verser de l'eau ou du lait de chaux d'un seau.
La mobilité du mélange de mortier peut être déterminée par son glissement à partir d'une lame inclinée : le mélange ne doit pas coller à la lame. Le mélange de mortier ne doit pas s'étaler lorsqu'il est posé sous forme de cône. Le mélange serré dans un poing ne doit pas être pressé entre les doigts, et lorsque les doigts ne sont pas serrés, il ne doit pas s'effriter. Le mélange de mortier fini ne doit pas être collecté en tas, car une grande partie de la miette tombera nécessairement.
Mortiers pour enduits de pierre. Les solutions préparées imitent le revêtement des bâtiments en pierre naturelle - marbre, granit, tuf, labradorite, etc. Moins souvent, elles finissent les surfaces des espaces intérieurs.
Le ciment Portland ordinaire ou coloré est utilisé comme liant dans les mortiers pour enduits de pierre. De la chaux est ajoutée pour donner au mélange de mortier la plasticité souhaitée. Dans le même but, des additifs plastifiants sont introduits.
Pour donner au plâtre de pierre la structure et la couleur de la pierre naturelle, il est nécessaire de choisir le bon enduit. A cet effet, une miette de roche imitée est utilisée comme charge. Ce n'est pas sufisant. Ainsi, si pour du plâtre imitant le marbre, on prend du marbre avec un grand nombre de veines,
alors le plâtre se révélera inégal et ne ressemblera pas à du marbre. Par conséquent, pour les enduits de marbre, il est préférable de prendre des miettes obtenues à partir de marbre unicolore.
Pour un enduit imitant le grès, il faut prendre plus de granulat fin et moins de granulat grossier. Si des roches profondes (granit, labradorite) sont simulées, la structure de surface doit être plus uniformément granuleuse et avec des grains plus gros que lors de la simulation de roches sortantes (basalte, porphyre), qui ont une structure de surface finement cristalline entrecoupée de gros grains individuels.
Le type d'agrégat utilisé est déterminé par la méthode de traitement de surface ultérieur. Dans les mélanges destinés au sablage, il doit y avoir au moins 50% de grains d'une taille de 2,5 ... 5 mm. Des mélanges à gros grains sont utilisés pour les textures en relief. Pour une texture finement rainurée obtenue par ponçage, la granulométrie de l'enduit ne doit pas dépasser 1,2 mm.
Pour que lors du traitement du plâtre à l'aide de copeaux de roche dure, les outils ne deviennent pas rapidement ternes, une partie des copeaux de granit doit être remplacée par une miette de plus roches tendres, à condition que le nécessaire apparence plâtres. Lors du décapage à l'acide, la dureté de la mie peut être quelconque, mais les minéraux de la mie ne doivent pas interagir avec l'acide.
L'enduit sgraffito nécessite très peu de mortier, il est donc préparé sur place à partir de chaux en pâte, de granulats et de pigments. Pour augmenter la résistance et la résistance à l'eau de la solution, ajoutez 10 ... 15% de ciment en poids de pâte de chaux. Des pigments de haute qualité (oxyde de chrome, cobalt, etc.), qui donnent des tons purs, sont ajoutés à la pâte de chaux qui, après mélange, est filtrée à travers un tamis fin.
En tant que charge, du sable de quartz bien lavé ou du marbre concassé avec des grains de plus de 1 mm est utilisé. Pour les solutions appliquées au pinceau, de la poudre de marbre ou de la farine est utilisée comme charge.
Composition pour sgraffite en plâtre. Dans la composition pour enduit sgraffito, un mortier de chaux-sable est pris comme base dans un rapport de 1: 3 (pâte de chaux: sable blanc en parties en volume).
La couleur désirée est obtenue en ajoutant des pigments (parties volumiques de la pâte de chaux): jaune - ocre 0,5; rouge - momies 0,1; rose - clous de girofle 0,3 ; bleu - outremer 0,1 ; brun - terre d'ombre 0,1, ocre 0,1 et ciment Portland grade 400 - 0,1.
Matériaux de plâtre.
Sgraffite en stuc multicolore.
Informations générales. Les enduits de sgraffite multicolores (de l'italien - rayé) sont obtenus en appliquant séquentiellement de fines couches de solutions colorées les unes sur les autres, suivies d'un grattage, en découpant un motif dessus.
Types de plâtres . Les enduits décoratifs sont divisés en trois types : calcaire-sable, terrazitique et pierre.
Utilisé pour la finition Mur de briques, ainsi que des surfaces constituées de matériaux de grade 50 et inférieur, tels que le béton léger, le tuf, la roche coquillière, les blocs céramiques poreux. Ces enduits sont appliqués sur des sols avec une petite quantité de ciment. Ils ne doivent pas être appliqués sur des surfaces de béton denses car ils peuvent s'écailler avec le temps.
Enduits de terrazit utilisé pour la finition des murs, des colonnes, des plinthes et d'autres parties des édifices capitaux.
Enduits de pierre imiter la pierre naturelle de parement (granit, marbre, calcaire, tuf). Ces enduits sont utilisés pour la finition de surfaces en béton lourd et dense, en brique, c'est-à-dire des matériaux d'une note d'au moins 100. Lors de l'application d'enduits en pierre sur des surfaces en moins de matériau résistant, ils s'écaillent. Les enduits de pierre sont appliqués sur des sols en ciment.
Séquence d'exécution . Les enduits colorés décoratifs sont fabriqués à partir de mélanges préparés en usine ou sur le chantier. Les mélanges sont préparés à partir de liants, de granulats et de pigments.
Les mélanges sont servis sur les lieux de travail dans des boîtes à solutions, divisées en deux. Un mélange sec est versé dans une moitié de la boîte et la solution est diluée par portions dans l'autre moitié. La solution peut être diluée dans toute la boîte, mais dans une quantité telle qu'elle doit être utilisée dans l'heure, c'est-à-dire avant que le ciment ne commence à prendre.
La solution est préparée comme suit. Le mélange sec est agité. Puis les doses de ce mélange et de lait de chaux sont dosées et mélangées jusqu'à obtention d'une masse homogène. Afin de ne pas changer la couleur de la solution, ni eau ni lait de chaux ne doivent être ajoutés à l'avenir. Lors de la préparation de solutions colorées grande importance a la précision du dosage de tous les composants; un dosage incorrect affecte non seulement la qualité du plâtre, mais, en règle générale, conduit à une violation de ses propriétés décoratives spécifiées.
Un apprêt ciment-chaux ou mortier de ciment est appliqué mécaniquement ou manuellement. Pour améliorer l'adhérence de la couche de revêtement à la surface, sur une solution de sol fraîche et bien nivelée, des rainures ondulées de 5 mm de profondeur sont rayées avec une lame de scie à une distance de 20 à 30 mm les unes des autres. Après 2-3 heures après avoir gratté les sillons, le sol est humidifié avec de l'eau d'un œil de craie. Après 10 à 12 heures, lorsque la solution prend, elle est fortement arrosée avec un jet d'eau dispersé pendant 5 à 7 jours, 3 à 5 fois par jour (selon la météo).
Après l'application de l'apprêt, la surface de la façade est divisée en prises afin de lieux ouverts il n'y avait pas de joints formés aux jonctions des couches de revêtement appliquées dans temps différent. Cela se produit parce que lorsqu'une solution de revêtement fraîche est combinée avec une solution précédemment appliquée et déjà séchée, l'eau de la solution nouvellement appliquée est absorbée par la solution séchée. Ainsi, en raison de la quantité supplémentaire de peinture, une bande se forme à la jonction des première et deuxième poignées, qui est plus foncée par rapport à la couleur du reste de l'enduit de façade. Si la façade a des pilastres, des rebords, des ceintures, alors elle est divisée de sorte que les joints des poignées se trouvent dans les coins près des rebords, alors ils seront à peine perceptibles. Si la façade a des tiges ou des corniches entre les planchers, les joints peuvent être sous ces tiges. Si la façade est complètement lisse, les prises sont cassées de manière à ce que leurs bordures passent le long des pentes de la fenêtre, là où le joint est moins visible.
Les captures peuvent être brisées à la fois horizontalement et verticalement. Les bords des poignées doivent être réguliers et lisses. Un joint lisse et uniforme peut être obtenu en installant une règle le long des bords de la poignée sur toute sa longueur, qui est retirée après l'application et le nivellement de la solution de revêtement colorée.
Si des taches blanches apparaissent sur le sol aux endroits où il a séché, elles sont abondamment humidifiées avec de l'eau toutes les 4 à 5 heures et toute la surface est humidifiée 1 à 1,5 heure avant l'application du revêtement. Il n'est pas recommandé de mouiller ultérieurement la surface avec de l'eau afin d'éviter le glissement de la solution de revêtement. Après 7 à 12 jours après l'application de l'apprêt, une solution colorée y est appliquée - un revêtement (couche de revêtement décorative).
L'épaisseur des couches décoratives colorées dans les enduits de pierre et de terrazitic dépend principalement de la finesse de l'agrégat (mie) et de la nature de la finition. L'épaisseur totale des couches de revêtement décoratif est en moyenne de 6 à 15 mm avec des agrégats de taille moyenne. Avec des agrégats plus gros, l'épaisseur peut atteindre jusqu'à 25 mm. La solution est appliquée en deux ou trois couches ou plus, selon sa densité et l'épaisseur du revêtement. Habituellement, une couche de pulvérisation et un apprêt d'un mortier décoratif sont d'abord appliqués, mais il est parfois nécessaire d'appliquer une autre couche de revêtement décoratif pour le nivellement. Ceci est fait lorsque le sol est fait avec négligence.
La procédure d'application de la solution est la suivante. Tout d'abord, une couche de pulvérisation est appliquée à partir d'une solution décorative, que l'on laisse épaissir, saisir de manière à ce qu'elle cesse de glisser de la surface, ce qui prend 1 à 1,5 heure.
Ensuite, le sol est appliqué en une ou plusieurs couches, nivelé et compacté à la truelle. Après épaississement du mortier décoratif appliqué et nivelé, il est ensuite compacté à la truelle, au pilon ou au bord d'une règle jusqu'à l'apparition d'une laitance de ciment en surface, puis enfin lissé à la spatule à plâtre. Ces opérations sont effectuées de manière à ce qu'il n'y ait pas de vides dans le plâtre, qui, lors du traitement, peuvent s'affaisser et former des coquilles, ainsi que pour rendre la surface lisse, de sorte qu'il soit plus facile à traiter et à obtenir une finition plus propre.
Lorsque des solutions avec des granulats fins sont utilisées, un revêtement décoratif est appliqué sur le sol pris, nivelé, lissé (frotté) avec une truelle, puis frotté avec une râpe.
Les fissures formées dans le plâtre sont scellées avec la même solution et doivent être écrasées. Cela devrait être fait avant que le mortier ne sèche. Si les fissures ne sont pas réparées, la solution le long de leurs bords tombera une fois séchée et, lors du scellement de ces fissures, des taches se forment après le séchage du revêtement.
Pour donner à la couche décorative de revêtement la résistance nécessaire, après la prise, elle est humidifiée avec de l'eau pendant 6 à 8 jours. Le premier jour, il est humidifié uniquement avec une brosse pétrifiée afin de ne pas laver la solution, et tous les deux jours, il est arrosé à partir d'arrosoirs ou d'un tuyau avec un pulvérisateur. La surface est mouillée 2 à 4 fois par jour, en fonction de la température extérieure.
Le plâtre au niveau des joints doit être maintenu humide en tout temps. Pour ce faire, les joints d'une largeur de 200 à 300 mm sont aspergés d'eau de la pierre et suspendus avec un tapis humide ou une toile de jute. Le joint doit être scellé avant de procéder à l'application du revêtement le long des limites de l'ancienne prise. Jusqu'à ce moment, le joint est humidifié. Cela aide à éliminer les traces de joints, car le plâtre humide absorbe moins d'eau du mortier frais.
Organisation du travail . Nous considérerons l'organisation du travail sur le plâtrage avec des solutions colorées et la décomposition des façades en sections à l'aide d'exemples.
Exemple 1. La façade avec des pilastres sur toute la hauteur du bâtiment, mais sans ceintures inter-étages, est divisée en prises (Fig. 105), qui vont du coin au premier pilastre, du premier pilastre au second, etc. Chaque prise est divisé par les forêts en cartes 1-6, selon deux par étage. Lors du plâtrage, après avoir retiré la corniche, un revêtement est appliqué sur le reste de la surface de la façade, mais de manière à ce qu'il n'y ait pas de joints visibles.
Après avoir plâtré la carte 1, les plâtriers passent à la carte 2, où des boîtes avec un mélange sec doivent être installées à l'avance et de l'eau doit être préparée. Si une solution prête à l'emploi est fournie, les boîtes doivent en être remplies 5 à 10 minutes avant l'arrivée des plâtriers.
Lorsque les plâtriers appliquent du mortier sur la carte 2, les ouvriers dédiés retirent les caisses de la carte 1 et les déplacent sur la carte 3, et ainsi de suite.
Fenêtre et pentes de porte il est recommandé de plâtrer immédiatement sur toute la surface de la poignée. Si des plateaux, des sandriks en forme de tiges sont fournis pour les fenêtres, ils peuvent être retirés après avoir fini toute la surface. Dans ce cas, les pentes sont taillées simultanément avec le dispositif de traction.
Les pilastres peuvent être finis avant ou après le plâtrage des deux prises adjacentes. Dans les deux cas, les joints ne seront pas visibles, car ils seront alignés avec les enveloppes.
Exemple 2. S'il n'y a pas de pilastres sur la façade, mais qu'il y a des ceintures entre les étages, les prises sont réalisées étage par étage (Fig. 106). Le sol est divisé par des échafaudages en deux en hauteur. Les captures sont divisées dans le sol en cartes. Les lignes de séparation I-I, II-II, etc., sont tracées à la craie. Pour effectuer le travail, un lien est attribué à chaque carte.
Pour qu'il n'y ait pas de joints visibles, les liens organisent le travail de cette manière. Le premier maillon applique la solution à gauche de la ligne I-I, le second à droite de cette ligne vers la ligne II-II, le troisième maillon va de la ligne III-III vers la gauche, le quatrième de cette ligne vers la droit. Avec cet ordre de travail, la solution est appliquée sur les joints en même temps.
Les courroies interfloor sont retirées ou coupées à la main. Pour effectuer ce travail, plusieurs plâtriers sont affectés.
Si la façade est brisée en pierres avec rustication, il est souhaitable de la plâtrer de manière à ce que chaque partie de la solution soit appliquée sur les pierres à différents endroits de la façade (par exemple, en damier). S'il y a une subtile différence de couleur entre les différentes parties du mortier, dans ce cas, les joints ne seront pas visibles et la façade donne l'impression d'être faite de pierres de différentes nuances.
Lorsqu'il est nécessaire de plâtrer une poignée étroite en une seule fois, les postes de travail des plâtriers sont placés les uns en dessous des autres et le mortier est jeté comme indiqué sur la Fig. 105.
Lors de travaux sur des échafaudages, des planches sont posées près des murs, sur lesquelles le mortier rebondissant tombera. Toutes les 20 à 30 minutes, il est collecté, ajouté à la portion suivante de la solution et mélangé.
Préparation de surface, application d'apprêt . Avant la préparation, les surfaces sont inspectées, puis entaillées, les coutures sont sélectionnées, nettoyées avec un balai, éliminant la poussière, la saleté et toutes les particules qui ne sont pas tombées, mais pas tombées. Les surfaces des enduits décoratifs doivent être particulièrement bien préparées, car les enduits de pierre sont traités avec des outils à percussion et, si la surface est de mauvaise qualité, lors du traitement du revêtement, elle peut tomber avec l'apprêt. Après avoir corrigé les endroits cassés, il reste des taches qui gâchent la façade.
Après préparation, ils procèdent à l'accrochage, au martelage des clous, à la disposition des timbres et des balises. Dans les endroits aux encoches épaisses, les ongles sont bourrés et tressés avec du fil.
Deux à trois heures avant la pulvérisation, la surface est humidifiée avec de l'eau. Après la pulvérisation, le sol est appliqué au niveau des phares, en nivelant et en grattant les cellules à l'aide d'une coupe, d'une brosse à ongles ou d'un râteau. Si les balises sont fabriquées à partir de la même solution que le sol, elles ne sont pas coupées, mais laissées dans le sol. Les phares sont coupés de gypse, la base est dégagée sous eux et enduite du même mortier que celui utilisé pour le sol.
Le spray et l'apprêt sous les enduits terrazitiques sont appliqués avec un mortier ciment-chaux avec un rapport de 1:1:6. Sous les enduits de pierre, un mortier de ciment de composition 1: 3 ou 1: 4 est utilisé, sous chaux-sable coloré - la même composition que l'enduit lui-même, c'est-à-dire 0,1 heure de ciment, 1 heure de chaux en pâte et 3 heures de sable.
Pour que les solutions appliquées ne sèchent pas rapidement, elles sont humidifiées avec de l'eau 3 à 4 fois par jour pendant 3 à 5 jours.
Enduits couleur chaux-sable . Des enduits à la chaux et au sable sont préparés, la pâte de chaux est utilisée comme liant. 10 à 15% de ciment et de pigments appropriés y sont ajoutés. La charge est du sable de quartz pur. Pour le revêtement de couches d'enduits de couleur chaux-sable à texture lisse, du sable de quartz est nécessaire avec une prédominance de grains de 0,3 à 0,6 mm, ne contenant pas de grains supérieurs à 1 mm. Pour les textures pulvérisées, on utilise du sable à gros grains, dans lequel environ 50 % des grains ont une taille de 0,6 à 2 mm. Le sable de quartz pour les tons clairs de plâtre doit être blanc. Pour les liants colorants, pas plus de 7% de peintures de construction sèches sont ajoutées à partir de la masse de pâte de chaux et de ciment. Pour la brillance, du mica peut être ajouté, pas plus de 5% du volume de ciment. Les compositions des enduits chaux-sable sont données dans le tableau. quatre.
Les enduits à l'état semi-durci ou non (plastique) sont traités pour obtenir la texture souhaitée avec des cycles, un tampon, un rouleau.
Cycles - plaques d'acier avec dents, pas plus de 2-3 mm de haut. Les dents sont larges, étroites, disposées en rangée ou à une certaine distance les unes des autres. Avant de commencer les travaux, la surface est divisée en rectangles, en carrés ou les axes des pierres y sont marqués. Ensuite, les règles sont appliquées au bon endroit, selon lesquelles les cycles sont guidés, en appuyant dessus avec une telle force que les dents coupent la surface du plâtre (Fig. 107, a, b).
La finition au tampon et au rouleau permet d'obtenir des figures répétées identiques sur le plâtre. Les timbres et les rouleaux sont en bois, en caoutchouc, en métal, ils peuvent être coulés en plomb, en régule. Leurs dimensions sont déterminées par le dessin. La profondeur du relief du motif ne doit pas dépasser 5 mm. La poignée est fixée rigidement au tampon, le rouleau est librement fixé à l'axe. Lors du laminage du motif avec un rouleau (Fig. 108), une règle ou une truelle est appliquée sur la solution lissée, qui sert de guide pour le mouvement du rouleau. Pour que la solution ne colle pas aux tampons et aux rouleaux, il est recommandé de les lubrifier avec une émulsion savonneuse ou de l'huile liquide pour machine.
La finition par pulvérisation est effectuée dans l'ordre suivant. La surface destinée à ce type de finition est nivelée avec de la terre, puis des rainures y sont rayées. Pour la pulvérisation, une solution de consistance crémeuse est préparée. Pour qu'il ne s'écoule pas de la surface, ajoutez du sable grossier, du gravier fin, des miettes. Pour obtenir un spray coloré, des peintures sèches résistantes aux alcalis sont introduites dans la solution.
Vaporiser à travers le maillage effectuer comme ceci (Fig. 109, a). Un treillis métallique avec des cellules de 2,5 x 2,5 à 10 x 10 mm (selon la taille de la texture requise) est tendu et cloué sur cadre en bois 1 x 2 m Pour que le treillis ne vibre pas, un fil est tiré sur le cadre en deux ou trois rangées et un treillis y est attaché. Dans les angles de la charpente, des planches de 100 à 200 mm de long sont clouées afin que le treillis puisse être installé strictement à la même distance de la surface à traiter.
La solution est jetée avec une spatule du faucon à travers le filet. En passant à travers le maillage, la solution est coupée et répartie sur la surface avec des tubercules; selon la fréquence de la grille, une texture fine ou grossièrement rugueuse se forme. La solution est lancée en jets uniformes, une ou plusieurs fois. La boîte à mortier doit être légère, petite, de préférence sur roues, car elle doit souvent être déplacée. La pulvérisation peut être obtenue en appliquant la solution avec la buse de la pompe à mortier.
Une pulvérisation à partir d'un balai (Fig. 109, b) est effectuée comme suit. Avant de prélever une solution sur un balai, mélangez-la afin que les grosses particules ne se déposent pas. À main droite ils prennent un balai coupé, à gauche - un bâton ou un morceau de règle. Un balai avec une solution est amené au mur et frappé sur un bâton, secouant la solution. Une texture grande ou moyenne "sous un manteau de fourrure" se forme à la surface. La solution est appliquée au même endroit une ou plusieurs fois.
Les textures combinées (Fig. 110) sont obtenues en appliquant des mortiers colorés de chaux et de sable et en effectuant un traitement de surface supplémentaire: découpe dans différentes directions avec une spatule à plâtre, estampage et pulvérisation.
Enduits de terrazit . Terrazit est livré sur le chantier sous la forme d'un mélange coloré sec prêt à l'emploi, qui est mélangé avec de l'eau sur le chantier. La couleur et la texture de la terrasite sont les mêmes que celles du grès ou du tuf, mais avec une brillance obtenue grâce à l'introduction de mica. Le liant des enduits terrazitiques est la chaux en flocons additionnée de 20 à 30 % de ciment. En tant que charge, des copeaux de marbre et du sable de quartz sont utilisés. Pour colorer la terrazite, on introduit des pigments, et parfois uniquement de la farine minérale colorée (marbre, pierre, granit).
Les mélanges de terrazite produits sont divisés par des chiffres ou des lettres : n° 1, ou M (grain fin), avec des grains agrégés de 1-2 mm, n° 2, ou C (grain moyen), avec des grains agrégés de 2-4 mm et n° 3, ou K (à gros grains), avec des grains agrégés de 4 à 6 mm. Ainsi, lors de l'utilisation du mélange n ° 1, une texture fine est obtenue, n ° 2 - moyenne et n ° 3 - grande.
Le terrasite avec des granulats fins est utilisé pour tirer les tiges.
Les compositions des mélanges pour enduits terrazitiques sont données dans le tableau. 5.
Les mortiers Terrazit sont un peu plus difficiles à appliquer que les mortiers chaux-sable, car les premiers sont préparés dans la plupart des cas avec de grosses miettes. Parfois, le mortier de terrasite est rendu liquide et appliqué sur la surface en 3-4 couches avec une spatule en plâtre d'un faucon à côtés.
Lors du plâtrage de la surface, une pulvérisation de mortier de terrasite liquide est d'abord appliquée sur le sol préparé et après sa prise (après 1-1,5 heures), 2-3 couches de sol, en fonction de la taille du terrasite et de l'épaisseur du couche de plâtre. Le sol est nivelé, compacté à coups de truelle ou d'un bord de la règle. Si des coquilles apparaissent à la surface du sol, elles sont corrigées avec une solution; puis appliquez un revêtement et nivelez-le.
Après avoir fixé la couche appliquée de plâtre terrazitique, elle est parfois écrasée. Dans la plupart des cas, le jointoiement est nécessaire si la surface est enduite de terrazzo fin, et elle sera traitée avec des grattoirs à dents fines. Frottez la surface soigneusement et rapidement.
Une fois la solution durcie (généralement après 3 à 6 heures), le raclage commence. Avec une légère pression sur le grattoir, les éclats de marbre et le sable s'effritent, laissant des nids plus ou moins grands et formant ainsi une surface rugueuse. La surface du plâtre est traitée à l'état semi-durci. Si vous commencez à faire du vélo plus tôt, la solution collera au cycle. Un tel grattage ne fera qu'aggraver l'apparence de la surface traitée. Si le plâtre est excessivement durci, il est plus difficile à gratter.
La texture lors du grattage du plâtre terrazitique dépend de la taille des dents du grattoir ou de la brosse à ongles, ainsi que de la finesse des agrégats.
En cours de grattage (Fig. 111, a, b), le plâtrier tient le grattoir, selon sa taille, avec une ou deux mains et le gratte sur la surface du plâtre. Il n'est pas recommandé d'appuyer fort sur le cycle ; il doit se déplacer en douceur, sans à-coups. Le cycle à dents coupe la surface et élimine le film usé ; en même temps, le mica et la mie sont exposés. Vous devez faire du vélo dans une direction, sinon des taches resteront à la surface, gâchant l'apparence du plâtre (cela est particulièrement visible les jours ensoleillés), et selon la règle; dans ce cas, des rayures uniformes sont obtenues et la surface grattée ressemble à la texture "sous un manteau de fourrure". La facture "sous un manteau de fourrure" peut être obtenue et plus d'une manière simple- application mécanisée d'enduit coloré directement sur la surface à enduire.
Pour obtenir la texture "sous grès taillé" à partir de la surface d'une épaisse couche de terrazite, la couche supérieure de plâtre est ébréchée au ciseau. Pour obtenir la texture "sous une pierre déchirée", la pierre concassée est incrustée dans une couche de terre fraîchement appliquée à divers endroits et jetée avec un mortier de terrazite, qui est ensuite traité avec un cycle ou un pinceau.
Après traitement, la surface est balayée avec un balai ou une brosse à poils durs.
Le plâtrage avec terrasite sans grattage est le suivant. Après avoir pulvérisé la surface, du sol y est appliqué à partir d'une solution ordinaire d'une épaisseur telle qu'elle n'atteint pas les balises de 5 à 7 mm, puis un sol coloré est appliqué sur ce sol frais jusqu'au plan des balises, qui est nivelé avec une règle ou une truelle. Après le sol coloré avec un balai, un revêtement crémeux de 5 à 7 mm d'épaisseur est appliqué sous forme de pulvérisation, en couches uniformes, sans lacunes, de sorte que des épaississements et des bosses ne se forment pas à la surface. Une fois le revêtement séché, la surface est nivelée avec le bord d'une truelle ou d'une règle, repoussant les particules saillantes et faiblement adhérentes. Ensuite, la surface est balayée avec un balai, exposant le mica, et une sorte de surface grattée est obtenue. Après avoir appliqué le revêtement, il est nécessaire de couper les balises, car même avec sa couche la plus épaisse, elles dépasseront du plan principal. Si, toutefois, une fine couche de terre est appliquée sur les balises, les particules de miettes adhèrent faiblement à la solution des balises et se décollent facilement au moment de la règle ou lors du balayage avec un balai. Le besoin de terrazite lors du plâtrage de cette manière est réduit de 25%, c'est-à-dire sur la quantité de déchets générés lors du grattage, et la productivité du travail augmente.
Pour effectuer la finition de la terrasite, l'équipe est divisée en sections, chacune étant chargée d'un certain processus: une section applique un spray et un sol simple, la deuxième - sol coloré, la troisième - revêtement, la quatrième - coupe les balises et les ferme avec terrasite, le cinquième - traite le revêtement.
Lors du cyclage des surfaces, de la poussière se dégage sur le plâtre durci, vous devez donc travailler avec des lunettes de sécurité.
Enduits de pierre . Ces enduits (Fig. 112) sont appelés marbres, car ils comportent une charge sous forme d'éclats de marbre et de granit ou de miettes d'autres roches, qui, une fois fendus, donnent un éclat étincelant. La couleur des miettes, ainsi que la farine de marbre ou de pierre, est choisie pour correspondre à la couleur du plâtre. Le liant principal est le ciment, parfois additionné de 10 à 20 % de chaux en pâte, qui est ajoutée pour rendre la solution plastique. Les grains de mie occupent la partie prédominante de la surface et, après forgeage, créent principalement la couleur et la texture du plâtre. Dans le même temps, le ciment coloré, pour ainsi dire, complète la couleur de la mie.
Les enduits de pierre sont les plus chers et les plus exigeants en main-d'œuvre, mais en même temps les plus durables, les plus durables et les plus décoratifs. Les mortiers d'enduits de pierre (tableau 6) sont plus rigides que les terrazitiques, ils sont donc plus difficiles à appliquer.
L'influence principale sur la couleur du plâtre est rendue par le blanchiment et la coloration des liants. Pour les enduits de marbre blanc et de calcaire, il est préférable d'utiliser du ciment blanc (le ciment ordinaire est blanchi). Pour blanchir le ciment ordinaire, on utilise de la chaux, de la farine ou de la poudre de marbre blanc. Afin de ne pas réduire la résistance du plâtre, des additifs de chaux et de farine de marbre sont introduits dans les quantités suivantes: pour les grades de ciment 200 et 300 - jusqu'à 20-25% du volume de ciment, pour les grades de ciment 300-400 jusqu'à à 40-50%.
Les solutions d'enduits en pierre sont appliquées avec une spatule en plâtre en 2 à 4 étapes, car il est impossible d'appliquer une couche d'enduit d'une épaisseur de 10 mm en une seule étape.
Les mortiers pour enduits de pierre s'appliquent de la même manière que les terrazitiques : première pulvérisation. après 1-1,5 heures une couche de sol, qui est compactée et nivelée. Si le sol a un grand nombre de coquilles, puis elles sont corrigées avec la même solution, mais plus liquide, la surface est lissée à la truelle ou légèrement frottée à la râpe.
La surface plâtrée est humidifiée avec de l'eau pendant 6 à 8 jours, le premier jour 3 à 4 fois, les jours suivants 5 à 6 fois. Puis sous 1 à 2 jours. le plâtre sèche et acquiert une résistance suffisante. Pendant ce temps, un forgeage d'essai est effectué sur une petite surface. Si la miette ne se sépare pas de l'impact, mais est enfoncée, cela signifie que la solution n'a pas encore acquis la force nécessaire et doit être maintenue en plus. Si la miette se brise et que le mortier s'effrite, le plâtre convient au forgeage.
Les plâtres sont traités avec un marteau à boucharder, une troyanka, un rouage, un ciseau ou frottés avec des barres, des râpes.
Le marteau-piqueur pendant le travail est tenu à deux mains et la surface du plâtre est coupée avec des coups uniformes. Dès l'impact, les dents de la boucharde coupent la surface, ébrèchent la couche supérieure du mortier et une partie des grains de miettes, qui commencent à scintiller et à briller. Le forgeage est effectué jusqu'à ce que la couche supérieure de la solution et une partie des grains de chapelure soient complètement ébréchées. Pour obtenir une surface uniformément finie, l'uniformité des coups est d'une grande importance.
Troyanka ou un ciseau pendant le travail est maintenu à un angle de 45 ° par rapport à la surface, ils enlèvent également le film supérieur du plâtre. Les coups de marteau doivent être de la même force.
Lors du traitement du plâtre pas complètement durci, le mortier est souvent bourré entre les dents des outils. Dans ce cas, l'outil ne coupe pas le plâtre et ne fend pas la mie, mais l'écrase, ce qui réduit les qualités décoratives du plâtre. Les outils doivent être nettoyés périodiquement avec une brosse métallique de la solution qui s'est accumulée entre les dents. Si les dents deviennent émoussées, l'outil est remplacé par un neuf. La barre et la râpe pour faciliter l'utilisation doivent être insérées dans une poignée en bois.
Souvent, les surfaces du plâtre sont divisées en pierres, repoussant les lignes avec une corde, qui est frottée avec de la craie ou un pigment. À l'aide d'un cordon frotté, des sangles et d'autres profils droits sont appliqués. Les bandes sont frottées selon la règle, sur laquelle un clip avec une râpe ou une barre est pressé.
Garniture de manteau de fourrure le plus souvent réalisé à la boucharde. La taille de la texture dépend de la taille des miettes et des dents de la boucharde. Plus les dents et la mie sont grandes, plus l'encoche est grande.
Finition hachurée(sous les rainures) produisent un cheval de Troie. Selon la taille des dents de l'outil, les rainures peuvent être grandes, moyennes, petites. Les premiers coups sont faits le long de la ligne battue avec une corde, et le suivant - parallèlement à la première rainure.
Finition en damier effectuer comme ça. La surface est divisée en cellules à l'aide d'un cordon ou d'une règle. Après cela, chaque cellule est traitée avec un cheval de Troie dans une direction mutuellement perpendiculaire, mais de telle manière que la texture terminée ne capture pas d'autres cellules. Les cellules peuvent être traitées de manière combinée: une cage est coupée avec un marteau "sous un manteau de fourrure", l'autre - avec un cheval de Troie en forme de rainures.
Garniture d'écoutille rayée est réalisé de la manière suivante. La surface est divisée en pierres avec un cordon. Des rustines rectangulaires sont percées entre les pierres avec une règle en acier sur un mortier tendre non encore durci ou avec un ciseau sur un mortier durci. Ensuite, les lignes délimitant les rubans et les lignes indiquant une série de traits sont repoussées. Après avoir fait une entaille de traits, des rouilles sont percées à travers toutes les pierres. La ligne de rouille est traitée avec un ciseau ordinaire ou un escarpin étroit. Le ciseau et l'escarpin doivent être maintenus à un angle de 60 à 70 ° par rapport à la surface afin d'obtenir des rustications propres et uniformes.
Finition pierre brisée et grès il est réalisé comme suit: une couche de mortier de plâtre d'une épaisseur de 40 à 50 mm est appliquée sur la surface, puis le mortier appliqué est brisé en pierres, les rouilles sont coupées et le traitement commence.
Un ciseau est enfoncé dans le plâtre durci à divers endroits et des coups latéraux sont appliqués avec un marteau le long de son extrémité, arrachant des morceaux de mortier : des irrégularités importantes (éclats) se forment à la surface du plâtre.
Texture de grès taillé obtenu en ébréchant de petits morceaux de plâtre avec un ciseau ou une langue.
Le plâtre de pierre semi-durci peut être traité avec des grattoirs à encoches serrés dans une cage. Le cycle est déplacé selon la règle et il raye de petites rainures verticales sur la surface.
Installation de rouille, finition des bords, coins, pentes et autres détails . L'un des types les plus courants de plinthes et de façades de finition consiste à les diviser en pierres séparées.
Les rouilles entre les pierres peuvent avoir différents profils (Fig. 113, a-g): triangulaires, carrées, en forme de tiges. Le plus souvent, ils fabriquent des rouilles de forme rectangulaire. Pour la rustication, la surface du socle ou de la façade est divisée en pierres avec un cordon ou une règle. Le long des lignes de séparation sur le plâtre fraîchement appliqué, la rustication est poinçonnée ou retirée avec des gabarits.
Poinçonner les rouilles avec une règle(Fig. 114, a). Une règle en acier de 5 à 15 mm d'épaisseur est appliquée sur la ligne prévue et avec un coup de marteau, elle est approfondie de 5 à 10 mm dans le plâtre fraîchement appliqué. Ensuite, la règle est soigneusement retirée afin de ne pas déchirer les bords des rouilles. Pour travailler, vous devez disposer de deux règles : une sur la longueur des rouilles, la seconde en largeur ou en hauteur. Les règles doivent être légèrement effilées en forme de cône afin qu'elles sortent plus facilement de la solution.
Couper les rouilles avec une scie(Fig. 114, b). Les rouilles sont coupées le long du plâtre durci avec un morceau de scie de 1 200-300 mm de long avec une poignée fixée au sommet. La règle 2 est appliquée aux lignes marquées, le long desquelles les rouilles sont sciées à la scie. En bourrant et en coupant, vous pouvez créer des rouilles ne dépassant pas 15 mm.
Dispositif de rouille utilisant des rails. Lorsque les rustications doivent avoir une largeur considérable et des profils simples (carré, triangle), elles sont disposées à l'aide de lattes (Fig. 115, a). Le Reiki doit être bien aiguisé. Les lames quadrangulaires ont généralement une section trapézoïdale pour faciliter leur retrait de la solution. Selon la profondeur de rouille requise, les lattes sont installées dans le sol ou dans la couche de couverture. Avant d'installer les rails, il est préférable de les recouvrir de graisse. La solution appliquée près des rails est compactée avec une truelle ou un pilon afin qu'il n'y ait pas de coquilles. Selon la forme de la pierre, soit tout l'espace entre les lattes est recouvert d'une solution, soit seulement près des lattes.
Pour la formation de rouilles profilées (Fig. 115, b), des lattes profilées sont utilisées (Fig. 115, c), rabotées sous forme de rouille. Les lattes longues sont faites pour les lignes horizontales, les lattes courtes pour les lignes verticales. Les lattes courtes sont coupées en longues avec une pointe droite. Ils s'enlèvent facilement après le réglage de la solution. L'utilisation de rails vous permet d'augmenter la productivité.
Étirer et couler les rouilles . Les rouilles sont retirées selon les règles accrochées (Fig. 116, a). Cependant, ils peuvent également être installés à partir de pièces préfabriquées dans des moules.
Les détails de rouille sont coulés à partir de gypse ou de mortier de ciment. Le mortier de ciment est préparé sous forme d'un mélange semi-sec, puis il est coulé dans un moule et compacté. Cette méthode de fabrication de produits s'appelle le battage. Pour la résistance des pièces, des renforts y sont insérés. La forme pour battre les produits est fabriquée en morceaux - à partir de gypse ou de béton. Les produits en plâtre peuvent également être coulés dans des moules en plâtre ou en plastique. Pour installer les détails de la rustication, la surface du mur est accrochée, des balises et des marques sont disposées, un spray et de la terre sont appliqués, qui, après nivellement, sont coupés dans une cage avec un outil de coupe ou autre. Ensuite, à l'aide d'un cordon crayeux, des lignes sont poinçonnées pour installer les pièces moulées et elles sont congelées dans la solution. L'espace entre les rouilles qui forment la pierre est ensuite rempli de mortier et traité à la texture requise.
Au lieu de couler, vous pouvez retirer des morceaux de tiges sur l'établi, qui sont ensuite coupés en parties bonne taille et congeler avec une solution sur le site d'installation. Cependant, la coulée de moules est plus productive que l'extraction de moules.
Finition des bords des coins, des pentes et d'autres détails. Ces détails sont finis différemment. Dans un cas, ils reçoivent la même texture que toute la surface, dans l'autre, ils sont encadrés d'un ruban d'une largeur maximale de 30 à 50 mm, qui reçoit une texture complètement différente. Bandes de plâtres de mortiers de ciment ils sont laissés lisses, en les frottant avec une râpe ou une demi-râpe sur un mortier fraîchement appliqué, ou après durcissement du mortier, ils sont frottés avec des barres sur des enduits en pierre. Les rubans sont le plus souvent coupés avec un ciseau ou une troyanka, en disposant des rainures, ou on leur donne une texture «manteau de fourrure». Pour que les rubans soient complètement droits et aient la même largeur, ils sont d'abord battus avec un cordon à la craie ou des lignes sont tracées selon la règle ci-jointe.
Il est recommandé de frotter les bandes avec une truelle selon la règle pressée sur le plâtre. Le frottement des bandes avec une barre ou une râpe est également effectué selon la règle, qui sert de guide. En frottant avec une barre, on obtient une texture lisse, avec une râpe sur du terrazzo - gratté, et sur du plâtre de pierre - scié. Si la bande sur les bords est traitée avec un cheval de Troie, elle doit être dirigée depuis angle aiguà l'intérieur, c'est-à-dire vers le milieu (Fig. 116, b). Dans la direction opposée, la troyanka ébréchera les moustaches et des nids-de-poule apparaîtront dessus. En forgeant le même endroit avec un cheval de Troie dans des directions mutuellement perpendiculaires, la texture "sous un manteau de fourrure" est obtenue. Pendant l'entaillage, le cheval de Troie ou le ciseau doit être maintenu à un angle de 60 à 70 ° par rapport à la surface.
Application de copeaux de pierre sur un sol frais . En plus du forgeage du plâtre de pierre, une méthode de sa texture est également utilisée, qui ne nécessite pas de traitement avec des outils. Ce type de traitement de texture est effectué de la manière suivante.
Les éclats de pierre sont triés par taille. Si nécessaire, du mica et d'autres agrégats sont ajoutés à la chapelure et le tout est mélangé. Après cela, les sols d'une solution colorée en plastique sont appliqués sur la surface et nivelés. Ensuite, sur une couche de plâtre fraîche, une miette de pierre est jetée avec une spatule d'un faucon, préalablement humidifiée avec de l'eau pour son adhérence plus fiable à la solution.
Le bébé est lancé rapidement, avec des mouvements brusques (lancements) et sans lacunes. À partir de lancers nets, la mie humide est mieux intégrée dans le sol fraîchement appliqué et adhère fermement à la solution. Lorsqu'il est appliqué correctement, une belle texture rugueuse et scintillante est obtenue.
Les miettes tombées sont collectées, lavées à l'eau et réutilisées.
Pour l'application de copeaux de pierre sur un sol frais, le travail s'organise comme suit. La surface est divisée en sections. La brigade est divisée en deux unités. Le premier maillon applique la terre et la nivelle, le second jette les miettes sur la solution de terre fraîche, récupère les chutes (rebondies), rince et réutilise. Si l'extérieur de la mie est contaminé par la solution, elle peut être lavée après une semaine avec une solution d'acide chlorhydrique à 10 %.
Finition de surface avec des pierres de différentes nuances . Pour obtenir une surface rustiquée avec des pierres de différentes nuances de couleurs, rappelant le revêtement en pierre naturelle, des solutions multicolores sont utilisées. Les pierres sont recouvertes d'une solution de la même couleur, par exemple jaune, mais de tons différents - jaune clair, jaune et jaune vif.
Lors du plâtrage, une solution d'une teinte est d'abord préparée et appliquée à la première série de pierres, puis une solution d'une teinte différente est préparée et appliquée à la deuxième série de pierres marquées, la troisième série de pierres est finie avec une solution de une troisième teinte, etc. La solution doit être appliquée de manière à ne pas éclabousser le plâtre précédemment appliqué.
Le plâtrage de cette manière ne nécessite pas de casser la surface en prises, ce qui simplifie grandement la production et l'organisation du travail.
Finition au mortier chaux-gypse avec éclats de marbre . Ce type de finition s'utilise aussi bien en intérieur qu'en extérieur, bien protégé de la pluie. L'apprêt est appliqué à partir d'un mortier chaux-gypse classique. Le mélange de revêtement est préparé à partir de gypse et de copeaux de marbre, du mica est ajouté pour la brillance. Pour le plâtre coloré, un pigment résistant aux alcalis est introduit dans le mélange.
Le mélange sec est fermé avec du lait de chaux jusqu'à la consistance d'une pâte semi-liquide. Une couche de couverture d'une épaisseur de 10 à 20 mm est appliquée sur le sol, nivelée et frottée. Le revêtement durci est nettoyé avec des brosses en acier : un film de gypse et de chaux est gratté des grains de miettes et de mica. Après le nettoyage, la surface est balayée avec un balai ou une brosse. Le lavage des surfaces à l'eau n'est pas autorisé. Il doit être nettoyé avec soin afin de ne pas nettoyer toute la couche de revêtement. Les mouvements de la brosse doivent se faire dans le même sens afin que la surface ne prenne pas l'aspect d'une rayure. La surface ainsi finie a une agréable texture scintillante.
Lors de l'entretien d'une telle surface, elle est balayée avec une brosse à poils doux et très sale est nettoyée avec une brosse en acier doux.
Exigences pour la qualité du plâtre . La surface traitée doit avoir le même aspect et le même ton, les petits nids de poule sont autorisés, à peine perceptibles à une distance de 3 m.Avec des nids de poule fréquents et des endroits inégalement traités, visibles à une distance de 5 m, le plâtre est rejeté. La profondeur de l'encoche lors du traitement avec un burin est autorisée jusqu'à 5 mm. La profondeur des lignes de grattage et la distance entre elles lors du traitement avec une brosse en métal ou à ongles doivent être de 1 à 2 mm, la distance entre les rainures est de 5 à 10 mm. Les traces de joints de plâtre ne doivent pas être visibles à une distance de 5 m.Les écarts par rapport aux normes ci-dessus ne sont pas autorisés.
Enduits terrazitiques. Terrazit est livré sur le chantier sous la forme d'un mélange coloré sec prêt à l'emploi, qui est mélangé avec de l'eau sur le chantier. La couleur et la texture de la terrasite sont les mêmes que celles du grès ou du tuf, mais avec une brillance obtenue grâce à l'introduction de mica. Le liant des enduits terrazitiques est la chaux en flocons additionnée de 20 à 30 % de ciment. En tant que charge, des copeaux de marbre et du sable de quartz sont utilisés. Pour colorer la terrazite, on introduit des pigments, et parfois uniquement de la farine minérale colorée (marbre, pierre, granit).
Les mélanges de terrazite produits sont divisés par des numéros ou par des désignations de lettres : n° 1 ou M(à grains fins) avec des grains de remplissage de 1-2 millimètre, n° 2 ou DE(à grain moyen) avec grains agrégés 2-4 millimètre et n ° 3 ou À(gros grains) avec grains agrégés 4-6 millimètre. Ainsi, lors de l'utilisation du mélange n ° 1, une texture fine est obtenue, n ° 2 - moyenne et n ° 3 - grande.
Le mica utilisé pour la décoration est tamisé sur les mêmes tamis que la charge.
Les compositions des mélanges pour enduits terrazitiques sont données dans le tableau. huit.
Tableau 8
Composition des enduits de terrazite (en parties en volume)
matériaux | Couleur du plâtre et taille de la texture |
|||||
blanche K | jaune C | lumière | brun- | lumière | foncé- |
|
Ciment Portland |
1 |
1,5 |
1 |
1,5 |
1 |
1 |
Noter. Pour la solution K, une grosse miette est prise (4-6 millimètre), pour la solution C - milieu (2-4 millimètre), pour la solution M - fin (1-2 millimètre).
Il est un peu plus difficile d'appliquer des mortiers de terrasite que des mortiers de chaux et de sable, car les premiers sont préparés dans la plupart des cas avec de grosses miettes. Parfois, le mortier de terrasite est rendu liquide et appliqué sur la surface en 3-4 couches avec une spatule en plâtre d'un faucon à côtés. Le terrasite avec des granulats fins est utilisé pour tirer les tiges.
Lors du plâtrage de la surface avec des mortiers de terrasite, un spray est d'abord appliqué sur le sol préparé à partir d'un mortier de terrasite liquide et après sa prise (après 1-5 h), appliquer l'apprêt en 2-3 couches, en fonction de la taille de la terrazite et de l'épaisseur de la couche de plâtre. Le sol est bien nivelé, compacté à coups de truelle ou d'un bord de la règle. Si des coquilles apparaissent à la surface du sol, elles sont corrigées avec une solution; puis appliquez un revêtement et nivelez-le bien.
Après avoir fixé la couche appliquée de plâtre terrazitique, elle est parfois écrasée. Dans la plupart des cas, le jointoiement est nécessaire si la surface est enduite de terrazzo fin, et elle sera traitée avec des grattoirs à dents fines. Il faut frotter soigneusement et en même temps rapidement.
Après la prise du mortier (habituellement après 3-6 h) commencer à faire du vélo. Avec une légère pression sur le cycle, les éclats de marbre et le sable commencent à s'effriter, laissant des nids plus ou moins grands et formant ainsi une surface rugueuse. Lors du raclage de la terrasite, les déchets atteignent 25% de la matière consommée.
La surface du plâtre est traitée à l'état semi-durci. Si vous commencez à faire du vélo plus tôt, la solution collera au cycle. Un tel grattage ne fera qu'aggraver l'apparence de la surface traitée. Si le plâtre est excessivement durci, il est plus difficile à gratter.
La texture lors du grattage du plâtre terrazitique dépend de la taille des dents du grattoir ou des ongles de la brosse, ainsi que de la finesse des agrégats.
En cours de grattage (Fig. 145), le plâtrier tient le grattoir, selon sa taille, avec une ou deux mains et le racle sur la surface du plâtre. Il n'est pas recommandé d'appuyer fort sur le cycle, il doit se déplacer en douceur, sans à-coups. Le cycle à dents coupe la surface et élimine le film usé ; en même temps, le mica et la mie sont exposés.

Vous devez faire du vélo dans une direction, sinon des taches resteront sur la surface, gâchant l'apparence du plâtre (ceci est particulièrement visible les jours ensoleillés).
Le grattage est recommandé selon la règle, dans ce cas même des rayures sont obtenues, et la surface grattée ressemble à la texture «sous un manteau de fourrure». La texture «sous un manteau de fourrure» peut également être obtenue de manière plus simple - par application mécanisée d'un revêtement coloré directement sur la surface à enduire.
Pour obtenir la texture "sous grès taillé", la couche supérieure de plâtre est ébréchée à la surface d'une épaisse couche de terrasite avec un ciseau.
Pour obtenir la texture "sous une pierre déchirée", la pierre concassée est incrustée dans une couche de terre fraîchement appliquée à divers endroits et jetée avec un mortier de terrazite, qui est ensuite traité avec un cycle ou une brosse.
Après le traitement, la surface est balayée avec un balai ou une brosse à poils durs.
Le plâtrage avec terrasite sans grattage est le suivant. Après avoir pulvérisé la surface, un apprêt y est appliqué à partir d'une solution ordinaire d'une épaisseur telle qu'elle n'atteint pas les phares de 5 à 7 millimètre, puis de la terre colorée est appliquée sur cette terre fraîche jusqu'au plan des phares, qui est nivelé avec une règle ou une truelle.
Après le sol coloré avec un balai, un enduit crémeux d'une épaisseur de 5-7 millimètre. Le revêtement est appliqué en couches uniformes, sans lacunes, de sorte que l'épaississement et les bosses n'apparaissent pas sur la surface. Une fois le revêtement séché, la surface est nivelée avec le bord d'une truelle ou d'une règle, repoussant les particules saillantes et faiblement adhérentes. Ensuite, la surface est balayée avec un balai, exposant le mica, et une sorte de surface grattée est obtenue.
Après avoir appliqué le revêtement, il est nécessaire de couper les balises, car même avec sa couche la plus épaisse, elles dépasseront du plan principal. Si, toutefois, une fine couche de terre est appliquée sur les balises, les particules de miettes adhèrent faiblement à la solution des balises et se décollent facilement au moment de la règle ou lors du balayage avec un balai.
Le besoin de terrazite lors du plâtrage de cette manière est réduit de 25%, c'est-à-dire de la quantité de déchets générés lors du grattage. Dans le même temps, la productivité du travail augmente.
Pour effectuer la finition de la terrasite, l'équipe est divisée en sections, chacune étant chargée d'un certain processus: une section applique un spray et un sol simple, la deuxième - sol coloré, la troisième - revêtement, la quatrième - coupe les balises et les ferme avec terrasite, le cinquième - traite le revêtement.
Lors du cyclage des surfaces, de la poussière se dégage sur le plâtre durci, vous devez donc travailler avec des lunettes de sécurité.
Le plâtre Terrazit est plus souvent utilisé dans la finition décorative des façades de bâtiments, mais peut également être utilisé sur les surfaces des murs intérieurs. bâtiments publiques. Il s'agit d'un mortier de chaux-ciment additionné de mélanges de terrazite - ciment blanc, sable de quartz, copeaux de pierre et de marbre, chaux en peluche, mica et autres.
Une solution de plâtre terrazitique est préparée dans des mélangeurs de mortier en petites portions, car. elle se rattrape rapidement. En ajoutant un pigment de couleur au mélange (de 0,5 à 2% du poids sec du mélange), vous pouvez modifier l'intensité de la couleur. Il est nécessaire de s'assurer que toutes les portions de la solution ont la même consistance et la même gamme de couleurs.
L'apprêt pour plâtre est appliqué et nivelé sur la surface du mur. Ensuite, des sillons de 3 mm de profondeur sont grattés ou coupés à une distance de 3 cm les uns des autres. Cela garantit un réglage sûr de la couche de terrasite lourde, qui est appliquée sur une couche d'apprêt bien fixée.
Avant d'appliquer la couche de couverture, le sol est bien humidifié. Lorsque l'eau est absorbée, un plâtre décoratif est appliqué et un jointoiement est effectué. Pour le traitement de surface final, des cycles, des fraises (un outil similaire à une fraise pour traiter la surface de la pierre et du plâtre), des brosses avec des clous enfoncés sont utilisés. Ensuite, la surface est balayée avec un balai ou une brosse douce. Il est nécessaire d'humidifier la surface du plâtre de terrazite avec de l'eau plusieurs fois par jour pendant 3-4 jours.
Pour obtenir une texture à grain fin ou à grain moyen, 30 minutes - 1 heure après l'application de l'enduit, lorsqu'il est encore semi-plastique, sa surface est traitée avec un cycle ou une brosse à ongles. Il est nécessaire de maintenir des intervalles de temps égaux entre le moment de l'application du plâtre et le début du traitement de ses cycles. Ensuite, la surface du plâtre de terrazite sera uniforme sur toute la surface du mur. Si cette période est trop longue, les zones traitées deviendront plus claires que le ton général. Si certains endroits se distinguent par des taches sombres, alors le cycle a commencé tôt.
Il convient également de rappeler que lors du grattage précoce, le mortier non durci peut coller à l'outil, et lors du grattage tardif, le mortier durcit fortement et le processus de grattage devient plus difficile. Appuyez légèrement le grattoir sur la surface du plâtre en le tenant avec une ou deux mains. En douceur, sans mouvements brusques, déplacez le grattoir le long de la surface dans une direction, en s'écrasant dans le plâtre et en enlevant le film usé et en exposant le mica et les éclats de pierre. En conséquence, vous obtiendrez des rayures uniformes et la surface acquerra une texture «manteau de fourrure».
Lors de l'utilisation d'un mélange de ciment dans lequel au moins la moitié des grains ont des tailles de 2,5 à 5 mm, une texture semblable à de la pierre à grains grossiers est obtenue. Dans ce cas, des bouchardes ou d'autres instruments de percussion sont utilisés pour traiter le revêtement après son durcissement.
Pour créer une texture "sous du grès taillé", utilisez un ciseau, qui ébréchera la couche supérieure de plâtre. La texture "sous une pierre déchirée" est obtenue en incrustant des éclats de pierre (pierre concassée) dans une couche de terre fraîche et en la jetant avec du mortier de terrazite. Après séchage, la surface est traitée avec des cycles ou une brosse à dents. Après le cycle, le plâtre doit être nettoyé avec un balai ou une brosse à cheveux.
Terrazit est livré sur le chantier sous la forme d'un mélange coloré sec prêt à l'emploi, qui est mélangé avec de l'eau sur le chantier. La couleur et la texture de la terrasite sont généralement les mêmes que celles du grès ou du tuf, mais avec un éclat dû à l'ajout de mica. Le liant des enduits terrazitiques est la chaux en flocons additionnée de 20 à 30 % de ciment. En tant que charge, des copeaux de marbre et du sable de quartz sont utilisés. La coloration de la terrasite est obtenue en y introduisant des pigments, et parfois uniquement de la farine minérale colorée.
Les mélanges de terrazit produits sont divisés par des nombres indiquant la finesse de l'agrégat. La chambre a désignation de la lettre: K - grande texture, C - moyenne et M - petite.
La surface du plâtre est traitée dans un état semi-durci, semi-plastique par grattage, nettoyage avec des brosses à ongles, etc. La texture de la terrasite dépend de la taille des copeaux de marbre, qui tombent pendant le traitement de surface, laissant plus ou moins petits nids. Lors du raclage de la terrasite, les déchets atteignent 25% du matériau déposé.
Il est un peu plus difficile d'appliquer des mortiers de terrasite que des mortiers de chaux et de sable, car les premiers sont fabriqués dans la plupart des cas avec de grosses miettes. Parfois, le mortier de terrasite est rendu liquide et appliqué sur la surface en 3-4 couches avec une spatule en plâtre d'un faucon à côtés. Le terrasite avec des granulats fins est utilisé pour tirer des tiges.
La recette des mélanges de terrazite est donnée dans le tableau. Dix.
Nom des matériaux | La couleur du plâtre et la taille de la texture : grand K, moyen C et petit M | |||||
blanche À |
jaune DE |
jaune clair DE |
brun M |
gris clair M |
gris foncé M |
|
ciment Portland Citron vert moelleux Quartz de sable miettes de marbre Marbre en poudre Mica Peinture (en % du poids de ciment et chaux floconneuse) |
2 6 - 12 3 1 |
1,5 4 9 4 1 0,5 Ocre 2% |
1 3 5,5 3,5 - 0,5 Ocre 2% |
1,5 3 11 - - 0,5 Ombre 0.5% |
1 2,5 - 9 3 0,5 |
9 2,5 4 - 4 0,5 Suie 0,3% |
Noter. Pour la solution K, une grosse miette est prise (corsage 4-b pour la solution C - moyen (2-4 mm), pour la solution M-petit (1-2 mm).
Application de mortiers de terrazite. Un spray est d'abord appliqué sur la surface à enduire, et après sa prise (après 1-1,5 heures), l'apprêt est appliqué en 2-3 couches, en fonction de la taille du terrasite et de l'épaisseur de la couche de plâtre. Le sol est bien nivelé et compacté avec une truelle ou une règle. Si des coquilles apparaissent à la surface du sol, elles sont couvertes.
S'il y a beaucoup de petits coquillages au sol, ils font une couverture et la nivellent bien.
Après avoir fixé la couche appliquée de plâtre terrazitique, elle est parfois écrasée. Le jointoiement est dans la plupart des cas nécessaire lorsque la surface est enduite de terrasite fine, et le traitement sera effectué avec des grattoirs à dents fines. Le jointoiement doit être fait soigneusement et rapidement.
Grattage de terrazite. Après avoir réglé la solution, ce qui prendra 3 à 6 heures ou plus, ils commencent à gratter. Il doit être démarré lorsque, avec une légère pression sur le cycle, la surface du plâtre de terrasite commence à s'effriter, c'est-à-dire que des copeaux de marbre et du sable tombent de la masse totale de la couche de plâtre, formant une surface rugueuse. Si le grattage est commencé plus tôt, la solution se froissera et collera au cycle. Un tel grattage ne fera qu'aggraver l'apparence de la surface traitée. Si le plâtre est surexposé (sec), il est difficile à gratter.
Lors du grattage de la terrazite, la texture obtenue dépend de la taille des dents du grattoir et des clous de la brosse, ainsi que de la finesse des agrégats.
Lors du grattage de la terrasite, le plâtrier tient le grattoir, selon sa taille, d'une ou deux mains et l'enfonce le long de la surface de l'enduit (Fig. 193). Il n'est pas recommandé d'appuyer fort sur le cycle ; il doit se déplacer en douceur, sans à-coups.
Riz. 193. Grattage de terrasite
Le cycle à dents coupe la surface et élimine le film usé, exposant le mica ou. Vous devez faire du vélo dans une direction, sinon des taches resteront à la surface, gâchant l'apparence du plâtre (ceci est particulièrement visible les jours ensoleillés). Il est préférable de gratter selon la règle; dans ce cas, des rayures uniformes sont obtenues et la surface grattée ressemble à la texture «sous un manteau de fourrure». Pour obtenir la texture "sous grès taillé", la couche supérieure de plâtre est ébréchée à la surface d'une épaisse couche de terrasite avec un ciseau.
Pour obtenir la texture «sous une pierre déchirée», un ciseau, un support ou une languette est enfoncé dans le plâtre et des morceaux de plâtre sont retirés avec eux; tandis que les outils doivent être martelés dans des directions différentes. Afin d'économiser des matériaux, la texture d'une pierre déchirée peut être obtenue en posant du gravier dans du plâtre dans différentes directions et en le jetant avec du mortier de terrazite, qui est ensuite traité avec des cycles.
Après le traitement, la surface est balayée avec un balai ou une brosse à poils durs.
Enduit avec terrasite sans ponçage. Il existe une méthode plus économique, plus rapide et simplifiée pour appliquer et traiter la terrasite, proposée par l'ingénieur A. M. Shepelev. C'est comme suit. Un mélange sec de terrazite est préparé de la manière habituelle. Mais pour le sol, en plus du mélange habituel, ils préparent également un mélange sec de la même couleur que la terrasite.
Après pulvérisation, un apprêt est appliqué à partir d'une solution ordinaire d'une épaisseur telle qu'il n'atteint pas les balises de 5 à 7 mm, puis un apprêt coloré est appliqué sur cet apprêt frais au plan des balises. Le sol coloré est nivelé avec une règle ou une truelle.
Après l'apprêt coloré, un spray est appliqué avec un balai - un revêtement crémeux d'une épaisseur de 5-7 mm. Le spray est appliqué avec précaution, en couches uniformes, sans lacunes, de sorte que l'épaississement et les bosses n'apparaissent pas sur la surface. Une fois le revêtement séché, la surface est nivelée avec le bord d'une truelle ou d'une règle, repoussant les particules de miettes saillantes et faiblement adhérentes. Ensuite, la surface est balayée avec un balai, exposant le mica et obtenant, pour ainsi dire, une surface grattée.
Pour effectuer des travaux avec une telle finition, l'équipe est divisée en maillons, chacun étant chargé d'un certain processus: un maillon applique un spray et un sol simple, le deuxième - sol coloré, le troisième - revêtement, le quatrième - coupe balises et les ferme avec terrasite, le cinquième - traite le revêtement.
Les phares doivent être coupés après l'application du revêtement, car même avec sa couche la plus épaisse, ils dépasseront du plan principal. Si, cependant, une fine couche de terre est appliquée sur les balises, les particules de miettes adhèrent faiblement à la solution des balises et tomberont facilement lors de l'exécution d'une règle ou du balayage avec un balai.
Le besoin de terrazite lors du plâtrage de cette manière est réduit de 25%, c'est-à-dire de la quantité de déchets générés lors du raclage. Dans le même temps, la productivité du travail augmente.