Hightech. Wie Kohlefaser für Supersportwagen hergestellt wird: Warum sie so gut ist. Carbonteile mit eigenen Händen herstellen
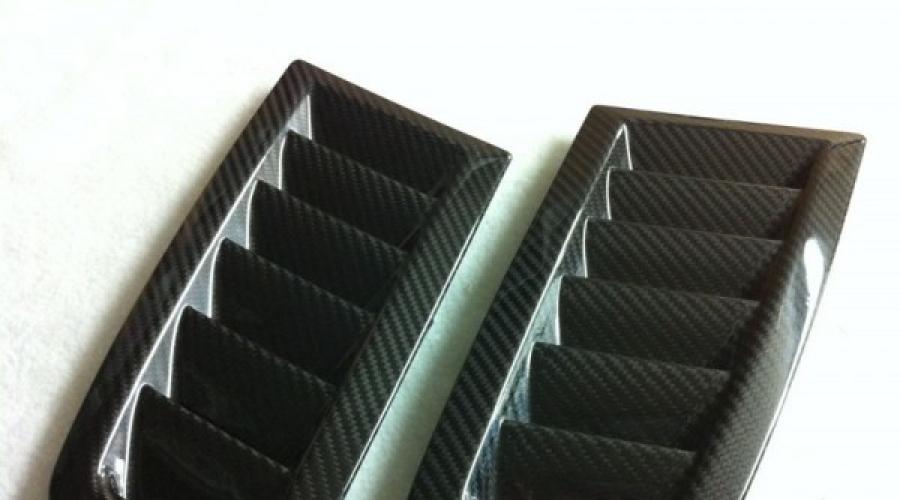
Lesen Sie auch
Polymerverbundwerkstoffe werden nicht nur in der Welt der Produktion und des Tunings von Sportwagen, sondern auch in der Luftfahrt und im Schiffbau häufig eingesetzt. Zuvor haben wir uns angeschaut, wie man ein Karosserieteil selbst mit Carbon-Look-Folie bekleben kann. Schauen wir uns nun an, wie man Kohlefaser mit eigenen Händen herstellt.
Herstellungsmethoden
Carbon-Kunststoffe, wie auch Verbundwerkstoffe aus verwobenen Kohlenstofffaserfäden genannt werden, können auf drei Arten hergestellt werden:
- Handformverfahren;
- Vakuumformverfahren;
- Produktion mit Backen in Autoklaven.
Die Herstellung von Kohlenstoffelementen im industriellen Maßstab erfordert teure Ausrüstung, sodass Kohlenstoff zu Hause nur durch Hand- oder Vakuumformen hergestellt werden kann.
Was für die Produktion benötigt wird
Zur Herstellung von Kohlefaser benötigen Sie:
- Kohlefaser. Es unterscheidet sich in der Webmethode und der Dichte, gemessen in Gramm pro Quadratmeter (g/m2);
- Trennmittel (zum Beispiel Loctite 770 NC). Wird zur einfachen Trennung des Kohlenstoffelements und der Matrix nach dem Trocknen verwendet. Das Material wird auf die Matrix des Teils oder die horizontale Fläche aufgetragen, auf der die vordere Schicht des Kohlenstoffelements verlegt wird. Es kann nur eine Frontschicht geben, wenn Rückseite es ist nicht nötig, eine schöne Carbon-Textur zu erzeugen;
- Matrix. Um horizontale Details zu erzeugen, können Sie ein Stück Glas oder einen Spiegel verwenden. Die Oberfläche sollte möglichst glatt sein, da alle Beschichtungsfehler auf das gefertigte Teil abgeformt werden;
- Epoxidharz (zum Beispiel EPR 320);
- Härter für Harz (optional EPH 294);
- Kohlefaser-Schneidwerkzeug. Sie können eine normale Schere verwenden, aber seien Sie darauf vorbereitet, dass das Werkzeug durch das Schneiden der Faser schnell stumpf wird. Wenn Sie planen, Carbonteile in Massenproduktion herzustellen, empfehlen wir die Anschaffung einer elektrischen Schere (die Wirksamkeit wird im Video demonstriert).
Der Bedarf an zusätzlichen Werkzeugen und Materialien hängt von der gewählten Herstellungsmethode ab. Ganz gleich, wie sehr Sie sich auch anstrengen, ohne zusätzliche Wärmebehandlung wird es Ihnen nicht gelingen, durch Handformen langlebiges Carbon herzustellen.
Die Herstellungsmethode ist ganz einfach:
- die Oberfläche der Matrix wird von allen Verunreinigungen gereinigt;
- ein Separator wird in mehreren dünnen Schichten gleichmäßig auf alle Oberflächen aufgetragen;
- auf die Oberfläche wird eine Schicht aus vorbereitetem Harz aufgetragen;
- eine Schicht Carbongewebe wird gelegt;
- Die Faser ist mit Epoxidharz imprägniert. Zwischen der ersten Schicht und der Matrix sowie zwischen den nachfolgenden Schichten dürfen sich keine Luftblasen befinden. Sie können das Harz mit einem normalen Pinsel verteilen; Luftblasen lassen sich bequem mit einer Rolle entfernen;
- die nächste Schicht wird aufgetragen, danach wird der Vorgang wiederholt, bis die erforderliche Dicke des Teils erreicht ist;
- Nach dem Auftragen der letzten Schicht können die horizontalen Teile mit einem Gegenstück aus Glas oder Spiegel verpresst werden. In diesem Fall erhalten beide Seiten des Teils eine glänzende Oberfläche und eine klare Carbonstruktur.
Da die Kosten für Kohlefaser nicht als erschwinglich bezeichnet werden können, kann Glasfaser zwischen der ersten und letzten Lage des Kohlefasergewebes verlegt werden. Das Glasfasergewebe sollte nicht rau sein, um die endgültige Form nicht zu beeinträchtigen.
Um die Herstellungskosten von Leichtbauteilen zu senken, wird das Element oft nur mit Kohlefaser laminiert – es wird nur als vordere Schicht des Karosserieelements platziert.
Vakuumformverfahren
Zusätzlich zum Standardsatz an Materialien und Werkzeugen benötigen Sie zur Herstellung von Kohlenstoffelementen im Vakuuminfusionsverfahren:
- Opfertuch;
- leitfähiges Netz. Wird zur Harzverteilung und Luftentfernung verwendet;
- Vakuumfolie. Sie können keine gewöhnliche Folie verwenden, da diese hohen Temperaturen nicht standhält und dies nicht der Fall ist hohe Fähigkeit zum Dehnen;
- Vakuumpumpe. Für die Herstellung von Kleinteilen eignet sich eine einfache einstufige Ölpumpe;
- Dichtungsgeschirr;
- Spiralrohr für Harzzufuhr und Luftansaugung;
- Vakuumröhre;
- Klemmen für Rohre (Klemmen);
- Vakuumfalle. Wird als Falle für Epoxidharz verwendet, das, wenn es in die Vakuumpumpe gelangt, diese beschädigt. Sie können aus verfügbaren Materialien mit Ihren eigenen Händen eine Falle bauen.
Sie können auch selbst einen Ofen zum Nachhärten von Kohlenstoffelementen bauen. Bitte beachten Sie, dass die Wärmebehandlung bei einer bestimmten Temperatur durchgeführt werden muss. Daher sollten Sie die Möglichkeit in Betracht ziehen, einen bestimmten Grad anzupassen und beizubehalten.
Bei der Vakuuminfusionstechnologie wird ein „Sandwich“ aus Kohlenstoffgewebe zusammengestellt und in einem geschlossenen Raum platziert. Nach der Installation wird die Luft abgepumpt und dem Werkstück Harz zugeführt.
Das mit Harz imprägnierte Gewebe wird 20 bis 30 Minuten lang unter Vakuum belassen, wodurch die Harzzufuhr- und Lufteinlassschläuche verschlossen werden. Für die erste Aushärtung reichen 24 Stunden aus Zimmertemperatur Danach sollte das Carbonteil zum Nachhärten in den Ofen geschickt werden.
Wir haben die Vakuuminfusionsmethode nicht im Detail beschrieben, da der Vorgang im Video ausführlich gezeigt wird.
Quelle: http://AutoLirika.ru/tuning/karbon-svoimi-rukami.html
Wie man mit eigenen Händen kohlenstofffaserverstärkten Kunststoff herstellt
Kohlenwasserstofffasern oder Kohlenstoff sind ein aus Kohlenstoffsträngen „gewebtes“ Material. Sie sind so dünn wie menschliches Haar, aber so stark wie Stahl. Sie sind sehr schwer zu zerreißen, aber es ist durchaus möglich, sie zu zerbrechen.
Deshalb werden bei der Herstellung von Teilen mehrere Kohlenstoffschichten verwendet. Durch das Übereinanderschichten von Kohlenstoffschichten in unterschiedlicher Reihenfolge erreichen Hersteller die höchste Verschleißfestigkeit und Schlagfestigkeit.
Trotz seiner „Jugend“ hat sich Carbon bereits fest im Markt der Hightech-Materialien etabliert.
Verwendung von Kohlenstoff
Zunächst interessierten sich Weltraum- und Militärspezialisten dafür. Würde es trotzdem tun! Eine Substanz, die eine mehrfache Gewichtsreduzierung ermöglicht und gleichzeitig hervorragende Festigkeitseigenschaften aufweist – ist das nicht ein Wunder?
Dann begann Carbonfaser nach und nach die Automobilindustrie zu erobern. Waren es zunächst Einzelteile, die eine hohe Reißfestigkeit erforderten, dient Carbon heute meist als exklusive Dekoration für ein Auto, beispielsweise als Carbon-„Rock“.
Und so begann man vor relativ kurzer Zeit, Kohlenwasserstofffasern zu nutzen sportliche Erfolge. Insbesondere wird es häufig zur Herstellung von Fahrradrahmen verwendet.
Eine Hommage an die Mode oder ein Schritt in die Zukunft?
Fahrradrahmen wurden viele Jahre lang aus Stahl oder Aluminium hergestellt. Langlebig, leicht, verschleißfest – ideal für Radsport und professionelle Marathons. Doch an die Stelle von Eisen tritt nach und nach Kohlenstoff, der dem Metall in vielerlei Hinsicht deutlich überlegen ist.
Bei Radsportturnieren findet man zunehmend Carbon-Fahrräder und wer gerne regelmäßig im Park spazieren geht, scheut sich nicht, teure Modelle zu kaufen. Ist diese große Leidenschaft für neue Technologien gerechtfertigt oder handelt es sich nur um einen weiteren Modetrend?
Das Hauptgeheimnis der Kohlenwasserstofffaser liegt in ihrer Herstellung. Schwierig technologischer Prozess Teile backen, aussägen und zusammenfügen garantiert Zuverlässigkeit. Im Streben nach schnellen Gewinnen verkürzen Nachtflugunternehmen jedoch häufig die Produktionsschritte und -zeiten, wodurch sich die technischen Eigenschaften erheblich verschlechtern.
Solche Carbonrahmen sind optisch nicht von hochwertigen Gegenstücken zu unterscheiden, aber bei jeder noch so kleinen Beschädigung wird das Fahrrad unter dem Besitzer buchstäblich auseinanderfallen.
Und doch ist es die Nachfrage, die das Angebot schafft.
Um im Trend zu liegen und gleichzeitig Geld zu sparen, sind viele Radsportbegeisterte bereit, ein Risiko einzugehen und ein im Untergrund hergestelltes Carbonfahrrad zu kaufen.
Stahl oder Carbon?
Der Hauptkonkurrent von Kohlefaser in Bezug auf Zuverlässigkeit und Haltbarkeit ist Stahl. Viele Konservative glauben, dass Metall für die Herstellung von Fahrradrahmen viel besser geeignet sei. Und dafür gibt es überzeugende Argumente:
- Preis. Die Kosten für ein typisches Carbonfaser-Fahrrad zweifelhafter Qualität übersteigen den Preis eines maßgeschneiderten Stahlrahmens deutlich.
- Haltbarkeit. Auf Websites und Zeitungsseiten sieht man oft Anzeigen für den Verkauf eines „Stahlpferdes“ aus zweiter Hand. Auch nach 10, 20, 30 Jahren verliert ein Fahrrad nicht seine Grundeigenschaften. Außer, dass es mit der Zeit verblasst ist. Gleichzeitig ist der Verkauf eines gebrauchten Carbonfaser-Fahrrads ein seltener Fall. Der Rahmen eines solchen Fahrrades findet nicht immer einen zweiten Besitzer.
- Reparatur. Und hier ist es Zeit für Metal-Liebhaber, sich zu freuen. Die Sache ist, dass sich der Carbonrahmen bei einem starken Aufprall nicht verbiegt, sondern in Stücke zerbricht. Wie eine Vase, die auf einer Fliese zerbricht.
Wie man mit eigenen Händen Automobil-Kohlefaser oder Kohlefaser herstellt
Das heißt, die Restaurierung eines zweirädrigen Freundes ist sinnlos und teuer. Es macht keinen Sinn, über die Reparatur von Stahlrahmen zu sprechen. Jeder erfahrene Radsportler hat schon einmal selbständig Teile gelötet oder ausgerichtet. Ja, Aussehen Die Geschichte danach ist ehrlich gesagt nicht festlich, aber das spielt keine Rolle mehr.
Und doch finden Carbonrahmen ihre Abnehmer. Schließlich Neueste Technologien Hersteller bieten unbestreitbare Vorteile ihres Produkts. Erstens kann das Gewicht eines Carbonfaserrahmens weniger als ein Kilogramm betragen.
Vielleicht ist dieses Argument für das Fahren im Haus oder zum Laden nicht sehr relevant. Aber die Leichtigkeit des Fahrrads wird vor allem Fans von touristischen Fernrouten zu schätzen wissen.
Wenn Sie Ihr Fahrrad auf einen Berg tragen müssen, zählt jedes Gramm.
Zweitens ist der Wertverlust eines solchen Fahrzeugs bis ins kleinste Detail durchdacht. Keine einzige Beule und kein Hügel wird mehr unangenehm in allen Organen des Reisenden widerhallen.
Der Carbonrahmen bleibt stationär. Das ist ein unbestreitbares Plus. Und drittens sieht das Fahrrad dank der Farbe und Textur der Kohlefaser stilvoll und modisch aus.
Es ist keine Schande, ein Mädchen bei einem Date mitzunehmen!
Die Hauptlieferanten für günstige Carbonrahmen sind Hersteller aus Taiwan.
Geheimnisse der Produktion
Viele Mastodons in der Herstellung von Fahrradteilen entscheiden sich zunehmend dafür, die Produktion auf die Herstellung von Carbonteilen umzustellen. Und das ist durchaus verständlich.
Erstens wird der Kohlenwasserstoff-Fahrradrahmen von Hand gefertigt, wobei nur minimaler Maschinenaufwand erforderlich ist. Das bedeutet, dass Sie die Zahl der Arbeitsplätze einsparen können und kein Geld für die Reparatur teurer Geräte verschwenden müssen.
Zweitens wächst die Nachfrage nach neuesten Technologien immer weiter, was höhere Gewinne verspricht. Und wir sprechen nicht nur von gewöhnlichen Kunden, sondern auch von Weltklasse-Radsportstars! Wie sieht also der Carbon-Herstellungsprozess aus?
- Am häufigsten kommen Kohlefasern in Form von mit Harz imprägnierten Platten in die Fabrik. Seltener - wie Garnrollen;
- Das Material wird in Stücke geschnitten, die den Teilen des Fahrrads entsprechen. Allerdings berücksichtigen die Hersteller bereits hier, dass die Fasern beim Auftragen von Schichten für eine höhere Zuverlässigkeit in verschiedene Richtungen „blicken“ müssen. Daher passen Kohlenwasserstoffstreifen nicht immer perfekt in die vorgesehene Form;
- Dann geschieht die eigentliche Erschaffung eines Wunders. Carbonfasern werden erhitzt und sozusagen zu einem Fahrradrahmen geformt. Dieser Vorgang erfordert höchste Aufmerksamkeit und Konzentration;
- Kommen wir zum „heißen“. Alle Teile werden fixiert und auf eine spezielle Form gelegt. Ziel: Ofen!;
- Nach mehrstündigem Sieden wird der Carbonrahmen entfernt und abkühlen gelassen. Gleichzeitig werden alle Fugen, Unregelmäßigkeiten und Mängel überprüft;
- Jetzt können Sie mit dem Schleifen beginnen. Die gesamte Basis des zukünftigen Fahrrads wird gereinigt und lackiert;
- Der Rahmen ist fertig!
Mit seinen eigenen Händen
Trotz des recht mühsamen technologischen Prozesses gelingt es den Handwerkern, Carbonrahmen mit eigenen Händen nachzubilden.
Im Internet findet man zu diesem Thema jede Menge Videos und Fotoanleitungen mit Beschreibungen, angefangen von Zeichnungen bis hin zur Ofentemperatur.
Überraschenderweise ergeben sie tatsächlich einen tollen Rahmen! Vielleicht klappt es auch bei dir? Schließlich ist es wirklich ein unschätzbares Vergnügen, mit eigenen Händen ein eigenes Fahrrad zu bauen!
Carbon-Fahrradrahmen sind Gegenstand langer und hitziger Diskussionen im Internet. Manche halten es für teuren, aber bedeutungslosen Kitsch.
Andere sind zuversichtlich, dass die Zeit von Aluminium und Stahl vorbei ist und die Zukunft jetzt liegt hohe Technologie. Ob Sie Ihr gesamtes Geld für den Kauf von Kohlefaser ausgeben, liegt bei Ihnen.
Es lohnt sich jedoch, noch einmal darüber nachzudenken und die richtige Wahl zu treffen.
Wie man Kohlefaser mit eigenen Händen herstellt | Kohlefaserplatte | wie man eine Kohlefaserplatte herstellt
Carbon (Carbongewebe) (12)
Kurzer Inhalt des Artikels: Kohlefaser (Carbon) Carbongewebe, Autotuning zum Selbermachen, Versand am Tag der Bestellung, Nachnahme, Fotobericht der Verpackung! Sowie andere Stoffe für das Styling – Hybridstoffe, Kohlefaser, Kohlenstoffgewebe, karbonisiert, Place, Add, Aramid, was ist Kohlenstoff, Waren, Dienstleistungen, Suche, Kaliningrad und die Region Kaliningrad, Russland, Region Moskau und Moskau. Carbon kaufen, Carbon zum Selbermachen, Carbongewebe, Carbonfaser, 3D-Ruß, Tuning, Carbonfaser, Carbongewebe, Aramidgewebe, Carbonfaser, Carbontechnologie, Fiberglas, Carbon kaufen, Carbon, Artikel über Tuning, Harze, Epoxid, Vakuum, Pumpen, Twill2x2, Twill4x4, Russland, Preise, Angebot, Katalog, Ort, hinzufügen, Waren, Dienstleistungen, Suche, Kaliningrad und Kaliningrader Gebiet, Russland, Moskauer Gebiet und Moskau, St. Petersburg, Jekaterinburg, Kasan, Jekaterinburg, Krasnodar, Krasnojarsk, Tscheljabinsk, Magnitogorsk, Surgut, Nabereschnyje Tschelny, Wladimir, Wolgograd, Kohlenstoff zum Selbermachen
Quelle: Carbon, Do-it-yourself, Herstellung aller Produkte aus Carbon, Carbon, Kevlar, Hybridgewebe. - -=S.R.Brothers=-
Tatsächlich wir werden reden Dabei geht es nicht darum, Teile aus Kohlefaser herzustellen, sondern darum, Kohlefaser auf fertige Teile, Karosserie- oder Innenteile aufzubringen. Wenn Sie möchten, können Sie Teile auch mit Kohlefaser verzieren.
Wenn die Herstellung eines Teils, das vollständig aus Kohlenstoff besteht, ein recht komplexer Prozess ist, dann ist die Anwendung von Kohlenstoff darauf angebracht fertiges Teil ein ziemlich einfaches Verfahren, das keine besonderen Fähigkeiten erfordert. Alles was Sie brauchen ist alles notwendige Materialien, Grunderfahrung im Umgang mit Epoxidharz und Genauigkeit.
Schritt 1: Entfernen Sie die Teile aus dem Auto, die Sie mit Kohlefaser verkleiden möchten. Höchstwahrscheinlich handelt es sich um eine Art Innenteil aus Kunststoff.
Wir bearbeiten das ausgewählte Teil mit Schleifpapier und lackieren es in der Hauptfarbe des Carbongewebes. Höchstwahrscheinlich wird es schwarz sein.
Diese Lackierung ist notwendig, damit die tatsächliche Farbe des Teils (grau oder braun, wie bei frühen Samaras) nicht durch das Carbongewebe hindurchscheint.
Schritt 2: Wir tragen das Carbongewebe auf das Teil auf und überlegen, wie wir es schneiden, wobei wir berücksichtigen, dass ein Spielraum vorhanden ist. Wir kleben es mit Klebeband an die Stelle, an der wir das Carbongewebe schneiden werden. Dies ist notwendig, um zu verhindern, dass sich der Stoff auflöst.
Schritt 3: Mischen Sie den Epoxidkleber und tragen Sie ihn gleichmäßig auf das Teil auf. Dann beginnen wir, nach und nach Carbongewebe auf das Teil aufzutragen. Stellen Sie sicher, dass der Stoff eng am Teil anliegt und keine Luftblasen vorhanden sind.
Schritt 4: Wir warten, bis das Gewebe gut an der Oberfläche des Teils haftet, rühren dann weiteres Epoxidharz ein und beginnen, das Carbongewebe gründlich damit zu tränken. Das Epoxidharz muss gut vom Stoff aufgenommen werden, wozu mehrere Schichten Harz erforderlich sein können.
Schritt 5: Wir warten, bis diese Epoxidschicht getrocknet ist, und tragen eine weitere Schicht auf, dies ist die letzte. Sollten sich Luftblasen gebildet haben, können Sie diese mit austreiben Lötlampe. Wenn die Luft nicht ausgestoßen wird, wird Ihr Teil anschließend zerstört.
Schritt 6: Nachdem die letzte Harzschicht ausgehärtet ist, nehmen Sie sehr feines Schleifpapier und entfernen Sie die oberste Harzschicht, die leicht vergilbt ist, mit der Lötlampe. Anschließend polieren wir die Oberfläche mit Politur und fertig. Das Teil ist einsatzbereit. Am Ende sollten Sie so etwas bekommen
So sehen sie aus Kunststoffteile Kohlenstoffbeschichtet
Übrigens…
1.
Kohlenstoffproduktion
Machen Sie mindestens 4 Schichten Harz, besser noch mehr. Dadurch wird verhindert, dass der Stoff reißt, wenn Sie mit dem Schleifen beginnen. 2.
Probieren Sie es zunächst an einem kleinen und vor allem flachen Teil aus, das, wenn etwas passiert, nicht so schlimm ist, und gehen Sie dann zu komplexeren Teilen mit Kurven über.
Der schwierigste Teil dieser ganzen Prozedur ist das Auflegen des Carbongewebes auf das Teil.
Sollte Ihnen doch einmal ein Fehler unterlaufen, legen Sie Ihr Teil für mehrere Stunden in den Gefrierschrank. Dann drehen Sie das Teil einfach leicht und die Schicht fällt ab.
Diskutieren Sie im Forum über die Anwendung von Kohlefaser auf Teilen
Wie wir bereits mehrfach erwähnt haben, haben Computer-Modding und Autotuning viele Gemeinsamkeiten, was wahrscheinlich der Grund dafür ist, dass viele Modder bei ihren Modding-Projekten immer wieder verschiedene Verbundmaterialien wie Glasfaser verwenden. Das kultigste Verbundmaterial in der Welt des Autotunings ist zweifellos Kohlefaser oder einfach Carbon.
Die Verwendung von echten Carbonfasern ist ein viel arbeitsintensiverer Prozess als die Verwendung von dekorativem Carbonfaser-Vinyl, weshalb echte Carbonfasern beim Modding so selten sind.
Do-it-yourself-Knoten aus Kohlefaser, Kohlefaser in beliebiger Länge
Dies ist jedoch kein Grund, beim Computer-Modding kein echtes Carbon zu verwenden.
Es gibt ziemlich viele verschiedene Optionen Herstellung von Kohlefaserteilen und könnte leicht Gegenstand mehrerer Artikel sein, aber nur zwei davon sind dafür geeignet Heimgebrauch, es sei denn natürlich, Sie haben zu Hause eine Vakuumpumpe und einen Autoklaven
Quelle: https://stroyvolga.ru/%D1%83%D0%B3%D0%BB%D0%B5%D0%BF%D0%BB%D0%B0%D1%81%D1%82%D0%B8 %D0%BA-%D1%81%D0%B2%D0%BE%D0%B8%D0%BC%D0%B8-%D1%80%D1%83%D0%BA%D0%B0%D0%BC %D0%B8-%D0%BA%D0%B0%D0%BA-%D1%81%D0%B4%D0%B5%D0%BB%D0%B0/
Herstellung von Carbonteilen
Die Qualität von Carbonteilen hängt in erster Linie davon ab die richtige Entscheidung und die Qualität des Harz- und Carbongewebes. Wenn Sie bei der Auswahl der Dichte der Kohlefaserplatte und der Aushärtegeschwindigkeit der Harzmischung Fehler machen, können Sie das Werkstück nicht vorsichtig in die Form legen, fest andrücken und Luftblasen vollständig entfernen.
Grundlegende Methoden zur Herstellung von Carbonteilen
Zu den wichtigsten Methoden zur Herstellung von Carbonteilen gehören:
- Formen aus Prepregs, also Halbzeugen,
- direkt in die Form formen,
- Anwendungsverfahren.
Für die Herstellung von Kohlefaser zu Hause ist keine komplexe Ausrüstung erforderlich, und mit bestimmten Fähigkeiten können Sie Teile von angemessener Qualität erhalten. Daher ist es durchaus möglich, Kohlefaser in zufriedenstellender Qualität selbst herzustellen.
Carbon für Autotuning
Aufmerksamkeit! Das sogenannte „3D-Carbon“, Auto-Vinyl, hat nichts mit Carbon zu tun, außer einer hervorragenden Imitation der Oberfläche von Carbon. Hierbei handelt es sich ausschließlich um mehrfarbige Vinyl- und PVC-Folien mit optischen Effekten dekorative Veredelung Oberflächen, jedoch nicht zum Härten.
Aber für die Herstellung einiger Leichtbauelemente, bei denen eine hohe Festigkeit erforderlich ist, beispielsweise für Stoßfänger, Motorhauben und kleine Karosserieteile, kann teures Echtcarbon verwendet werden.
Sie können sogar versuchen, kleine Elemente selbst mit Kohlefaser zu bedecken.
Es ist jedoch zu bedenken, dass dieses Material sehr empfindlich gegenüber punktuellen Stößen ist und die Gefahr einer Beschädigung durch kleine Steine und Geröll unter den Rädern besteht.
Wenn für Sie ästhetische Parameter im Vordergrund stehen und nicht die Gewichtsreduzierung eines Autos oder Motorrads, dann werfen Sie einen genaueren Blick auf PVC-Folien in Carbon-Optik, Aquadruck oder Airbrush.
Herstellung von Carbonteilen im Prepreg-Verfahren
Der industrielle Prozess des Formens eines Produkts aus Prepreg (Rohlingen zum Formen) in einem Autoklaven ist ein gleichzeitiger Ablauf komplexer Prozesse:
- Polymerisation der Verbindung,
- Vakuumentfernung von Luft und überschüssigem Harz,
- Hochdruck (bis zu 20 atm) drückt alle Schichten gegen die Matrix, verdichtet und nivelliert sie.
Dies ist ein teurer Prozess und daher für das Tuning im kleinen Maßstab zu Hause kaum von Nutzen.
Die Trennung dieser Prozesse senkt jedoch die Kosten und verlängert den gesamten Prozess zur Herstellung von Kohlenstoff selbst. In diesem Fall werden Änderungen an der Prepreg-Aufbereitungstechnologie vorgenommen, sodass immer darauf geachtet werden muss, für welche Technologie das Prepreg bestimmt ist.
In diesem Fall wird das Prepreg in Form eines Sandwiches hergestellt. Nach dem Auftragen des Harzes wird das Werkstück beidseitig mit Kunststofffolie abgedeckt und zwischen zwei Wellen geführt.
Dadurch werden überschüssiges Harz und unerwünschte Luft entfernt. Das Prepreg wird mit einem Stempel in die Matrix gepresst und die gesamte Struktur in einen Wärmeschrank gelegt.
Das heißt, in diesem Fall stellt das Prepreg ein vollständig formbereites Werkstück dar, bei dem komprimierte Schichten und Luft entfernt wurden.
Diese Methode wird am häufigsten von Autowerkstätten beim Kauf von Carbonrohlingen verwendet. Die Matrizen bestehen aus Alabaster oder Gips, manchmal aus Metall, oder das Teil selbst wird als Modell verwendet. die Sie in Kohlenstoff nachbilden möchten. Manchmal werden Modelle aus Schaumstoff ausgeschnitten und verbleiben im fertigen Teil.
Der einfachste Weg, Kohlefaser mit eigenen Händen herzustellen, besteht darin, das Werkstück zu „bedecken“ oder mit Kohlefaser zu versehen.
Auftragungsmethode (Handkleben)
Mit der Klebemethode können Sie Kohlefaser selbst herstellen. Sie umfasst fünf Hauptschritte:
- Sorgfältige Vorbereitung der Klebefläche: Schleifen, Entfetten, Ecken abrunden.
- Auftragen von Kleber.
- Mit Epoxidharz und Härter imprägnierte Kohlefaserverklebung.
- Trocknen.
- Beschichtung mit Schutzlack oder Farbe.
Harzfüllstoffe werden sowohl zur dekorativen Wirkung als auch zur Verhinderung des Tropfens von Harz von vertikalen Flächen verwendet.
Notwendige Materialien
- Klebstoff zum Befestigen von Carbonfasern auf einer Oberfläche.
- Kohlefasergewebe, das schichtweise auf das Harz gelegt und mit einer harten Walze gerollt wird.
- Mittelviskoses Epoxidharz mit Härter (wird manchmal als Klebstoff verwendet).
- Schutzlack. Für den Kratzschutz ist Polyurethan die beste Wahl. Sie müssen wasserdicht und lichtdicht wählen. Es wird nicht bewölkt. Für hohen Glanz kann Acryllack als Decklack verwendet werden.
Das Auftragen des Harzes erfolgt 2-3 mal mit Zwischentrocknung und Anschleifen.
Diese Methode unterscheidet sich von der traditionellen Herstellung von Kohlenstoffprodukten nach Modellen durch die Verwendung eines Klebstoffs anstelle eines Separators, um das resultierende Halbzeug leicht entfernen zu können.
Die Firma 3M bietet sogar selbstklebende Kohlefaser an, allerdings erfordert die Verarbeitung gute Kenntnisse.
Und der Kohlenstoff verbleibt am zu verklebenden Teil und verstärkt ihn. Diese Art der Kohlenstoffproduktion wird am häufigsten zur Verkleidung von Stoßfängern, Armaturenbrettern usw. verwendet.
Vakuumformverfahren
Diese Methode erfordert Spezialausrüstung und gute Fähigkeiten.
- Auftragen eines Trennmittels auf die Oberfläche des Modells. Für matte und halbglänzende Oberflächen wird üblicherweise ein Trennwachs verwendet, für glänzende Oberflächen (Kunststoff und Metall) werden Trennmittel und Grundierungslösungen vom Typ WOLO verwendet, die in der Kleinserienproduktion zum Einsatz kommen.
- Falten- und blasenfreies Einlegen von Carbongewebe in die Matrix.
- Imprägnierung von Kohlefaser mit Harz.
- Es kann mehrere Schichten geben. In einigen Fällen kann Kohlefaser mit Glasfaser abgewechselt werden.
- Anbringen einer perforierten Folie, um überschüssiges Harz herauszudrücken und Luft entweichen zu lassen. Es empfiehlt sich eine Überlappung.
- Verlegen der Saugschicht.
- Installation des Vakuumschlauchs und Anschluss zum Anschluss der Vakuumpumpe.
- Legen Sie die gesamte Struktur in eine haltbare Vakuumfolie und kleben Sie sie mit einem Dichtungsband an das Gerät.
Der gesamte Vorgang ähnelt dem Einlegen eines Objekts Vakuumverpackung, die in Geschäften zum Aufbewahren von Dingen verkauft werden, mit anschließendem Abpumpen von Luft.
Mit solchen Vakuumbeuteln kann man übrigens experimentieren. Sie sind sehr langlebig und in verschiedenen Größen erhältlich.
Eine Vakuumpumpe für Heimgebrauch wird durchschnittlich 150-200 $ kosten.
Druckformverfahren (Handwalzen)
Es ist beantragt selbstgemacht Kohlenstoffteile und ähnelt dem Vakuumformverfahren, jedoch ohne den Einsatz teurer Geräte. Die Kits enthalten Pinsel zum Auftragen von Harz und Rollen zum Herausdrücken von Luft und zum Rollen von Schichten.
Für einfaches Autotuning benötigen Sie:
- Carbongewebe mit einer Dichte von 200-300 g/m,
- Epoxidharz,
- Härter,
- harte Rolle und Pinsel.
Auf Alibaba.com Carbongewebe mit einer Dichte von 200 g/m2. Köperbindungen kosten zwischen 10 und 25 US-Dollar pro Stück Quadratmeter. Es stimmt, Sie müssen ab 10 Metern kaufen. Sie können jedoch zustimmen, Muster zu erhalten, mit denen Sie selbst kleine Kohlenstoffprodukte herstellen können.
Trennwachs und Gelcoat werden auf die Oberfläche der Form aufgetragen, um eine schützende und dekorative Schicht auf der Oberfläche des fertigen Produkts zu bilden. Nach dem Trocknen wird mit einem Pinsel eine Epoxidmischung für Carbonfasern aufgetragen und mit dem Auslegen des Carbongewebes begonnen.
Jede Schicht wird mit einer Walze abgerollt, um Luftblasen zu entfernen und eine maximale Haftung zu erreichen. Nach vollständiger Trocknung an der Luft oder im Wärmeschrank wird das Teil aus der Matrize entnommen, geschliffen und mit einem Schutzlack überzogen.
Bei dieser Methode wird ein hoher Harzverbrauch erzielt (dreimal höher als die Dichte von Kohlefaser), aber auf diese Weise können Sie jedes Carbonteil mit Ihren eigenen Händen herstellen.
Polymerverbundwerkstoffe werden nicht nur in der Welt der Produktion und des Tunings von Sportwagen, sondern auch in der Luftfahrt und im Schiffbau häufig eingesetzt. Zuvor haben wir uns angeschaut, wie man ein Karosserieteil selbst mit Carbon-Look-Folie bekleben kann. Schauen wir uns nun an, wie man Kohlefaser mit eigenen Händen herstellt.
Herstellungsmethoden
Carbon-Kunststoffe, wie auch Verbundwerkstoffe aus verwobenen Kohlenstofffaserfäden genannt werden, können auf drei Arten hergestellt werden:
- Handformverfahren;
- Vakuumformverfahren;
- Produktion mit Backen in Autoklaven.
Die Herstellung von Kohlenstoffelementen im industriellen Maßstab erfordert teure Ausrüstung, sodass Kohlenstoff zu Hause nur durch Hand- oder Vakuumformen hergestellt werden kann.
Was für die Produktion benötigt wird
Zur Herstellung von Kohlefaser benötigen Sie:
- Kohlefaser. Es unterscheidet sich in der Webmethode und der Dichte, gemessen in Gramm pro Quadratmeter (g/m2);
- Trennmittel (zum Beispiel Loctite 770 NC). Wird zur einfachen Trennung des Kohlenstoffelements und der Matrix nach dem Trocknen verwendet. Das Material wird auf die Matrix des Teils oder die horizontale Fläche aufgetragen, auf der die vordere Schicht des Kohlenstoffelements verlegt wird. Es kann nur eine Vorderschicht vorhanden sein, wenn auf der Rückseite keine schöne Carbonstruktur erzeugt werden muss;
- Matrix. Um horizontale Details zu erzeugen, können Sie ein Stück Glas oder einen Spiegel verwenden. Die Oberfläche sollte möglichst glatt sein, da alle Beschichtungsfehler auf das gefertigte Teil abgeformt werden;
- Epoxidharz (zum Beispiel EPR 320);
- Härter für Harz (optional EPH 294);
- Kohlefaser-Schneidwerkzeug. Sie können eine normale Schere verwenden, aber seien Sie darauf vorbereitet, dass das Werkzeug durch das Schneiden der Faser schnell stumpf wird. Wenn Sie planen, Carbonteile in Massenproduktion herzustellen, empfehlen wir die Anschaffung einer elektrischen Schere (die Wirksamkeit wird im Video demonstriert).
Der Bedarf an zusätzlichen Werkzeugen und Materialien hängt von der gewählten Herstellungsmethode ab. Ganz gleich, wie sehr Sie sich auch anstrengen, ohne zusätzliche Wärmebehandlung wird es Ihnen nicht gelingen, durch Handformen langlebiges Carbon herzustellen.
Handformverfahren
Die Herstellungsmethode ist ganz einfach:
- die Oberfläche der Matrix wird von allen Verunreinigungen gereinigt;
- ein Separator wird in mehreren dünnen Schichten gleichmäßig auf alle Oberflächen aufgetragen;
- auf die Oberfläche wird eine Schicht aus vorbereitetem Harz aufgetragen;
- eine Schicht Carbongewebe wird gelegt;
- Die Faser ist mit Epoxidharz imprägniert. Zwischen der ersten Schicht und der Matrix sowie zwischen den nachfolgenden Schichten dürfen sich keine Luftblasen befinden. Sie können das Harz mit einem normalen Pinsel verteilen; Luftblasen lassen sich bequem mit einer Rolle entfernen;
- die nächste Schicht wird aufgetragen, danach wird der Vorgang wiederholt, bis die erforderliche Dicke des Teils erreicht ist;
- Nach dem Auftragen der letzten Schicht können die horizontalen Teile mit einem Gegenstück aus Glas oder Spiegel verpresst werden. In diesem Fall erhalten beide Seiten des Teils eine glänzende Oberfläche und eine klare Carbonstruktur.
Da die Kosten für Kohlefaser nicht als erschwinglich bezeichnet werden können, kann Glasfaser zwischen der ersten und letzten Lage des Kohlefasergewebes verlegt werden. Das Glasfasergewebe sollte nicht rau sein, um die endgültige Form nicht zu beeinträchtigen.
Um die Herstellungskosten von Leichtbauteilen zu senken, wird das Element oft nur mit Kohlefaser laminiert – es wird nur als vordere Schicht des Karosserieelements platziert.
Vakuumformverfahren
Zusätzlich zum Standardsatz an Materialien und Werkzeugen benötigen Sie zur Herstellung von Kohlenstoffelementen im Vakuuminfusionsverfahren:

Sie können auch selbst einen Ofen zum Nachhärten von Kohlenstoffelementen bauen. Bitte beachten Sie, dass die Wärmebehandlung bei einer bestimmten Temperatur durchgeführt werden muss. Daher sollten Sie die Möglichkeit in Betracht ziehen, einen bestimmten Grad anzupassen und beizubehalten.
Bei der Vakuuminfusionstechnologie wird ein „Sandwich“ aus Kohlenstoffgewebe zusammengestellt und in einem geschlossenen Raum platziert. Nach der Installation wird die Luft abgepumpt und dem Werkstück Harz zugeführt. Das mit Harz imprägnierte Gewebe wird 20 bis 30 Minuten lang unter Vakuum belassen, wodurch die Harzzufuhr- und Lufteinlassschläuche verschlossen werden. Für die erste Aushärtung genügen 24 Stunden und Raumtemperatur, danach sollte das Carbonteil zur Nachhärtung in den Ofen geschickt werden. Wir haben die Vakuuminfusionsmethode nicht im Detail beschrieben, da der Vorgang im Video ausführlich gezeigt wird.
Polymerverbundwerkstoffe werden nicht nur in der Welt der Produktion und des Tunings von Sportwagen, sondern auch in der Luftfahrt und im Schiffbau häufig eingesetzt. Zuvor haben wir uns angeschaut, wie man es selbstständig macht. Schauen wir uns nun an, wie man Kohlefaser mit eigenen Händen herstellt.
Herstellungsmethoden
Carbon-Kunststoffe, wie auch Verbundwerkstoffe aus verwobenen Kohlenstofffaserfäden genannt werden, können auf drei Arten hergestellt werden:
- Handformverfahren;
- Vakuumformverfahren;
- Produktion mit Backen in Autoklaven.
Die Herstellung von Kohlenstoffelementen im industriellen Maßstab erfordert teure Ausrüstung, sodass Kohlenstoff zu Hause nur durch Hand- oder Vakuumformen hergestellt werden kann.
Was für die Produktion benötigt wird
Zur Herstellung von Kohlefaser benötigen Sie:
- Kohlefaser. Es unterscheidet sich in der Webmethode und der Dichte, gemessen in Gramm pro Quadratmeter (g/m2);
- Trennmittel (zum Beispiel Loctite 770 NC). Wird zur einfachen Trennung des Kohlenstoffelements und der Matrix nach dem Trocknen verwendet. Das Material wird auf die Matrix des Teils oder die horizontale Fläche aufgetragen, auf der die vordere Schicht des Kohlenstoffelements verlegt wird. Es kann nur eine Vorderschicht vorhanden sein, wenn auf der Rückseite keine schöne Carbonstruktur erzeugt werden muss;
- Matrix. Um horizontale Details zu erzeugen, können Sie ein Stück Glas oder einen Spiegel verwenden. Die Oberfläche sollte möglichst glatt sein, da alle Beschichtungsfehler auf das gefertigte Teil abgeformt werden;
- Epoxidharz (zum Beispiel EPR 320);
- Härter für Harz (optional EPH 294);
- Kohlefaser-Schneidwerkzeug. Sie können eine normale Schere verwenden, aber seien Sie darauf vorbereitet, dass das Werkzeug durch das Schneiden der Faser schnell stumpf wird. Wenn Sie planen, Carbonteile in Massenproduktion herzustellen, empfehlen wir die Anschaffung einer elektrischen Schere (die Wirksamkeit wird im Video demonstriert).
Der Bedarf an zusätzlichen Werkzeugen und Materialien hängt von der gewählten Herstellungsmethode ab. Ganz gleich, wie sehr Sie sich auch anstrengen, ohne zusätzliche Wärmebehandlung wird es Ihnen nicht gelingen, durch Handformen langlebiges Carbon herzustellen.
Handformverfahren
Die Herstellungsmethode ist ganz einfach:
- die Oberfläche der Matrix wird von allen Verunreinigungen gereinigt;
- ein Separator wird in mehreren dünnen Schichten gleichmäßig auf alle Oberflächen aufgetragen;
- auf die Oberfläche wird eine Schicht aus vorbereitetem Harz aufgetragen;
- eine Schicht Carbongewebe wird gelegt;
- Die Faser ist mit Epoxidharz imprägniert. Zwischen der ersten Schicht und der Matrix sowie zwischen den nachfolgenden Schichten dürfen sich keine Luftblasen befinden. Sie können das Harz mit einem normalen Pinsel verteilen; Luftblasen lassen sich bequem mit einer Rolle entfernen;
- die nächste Schicht wird aufgetragen, danach wird der Vorgang wiederholt, bis die erforderliche Dicke des Teils erreicht ist;
- Nach dem Auftragen der letzten Schicht können die horizontalen Teile mit einem Gegenstück aus Glas oder Spiegel verpresst werden. In diesem Fall erhalten beide Seiten des Teils eine glänzende Oberfläche und eine klare Carbonstruktur.
Da die Kosten für Kohlefaser nicht als erschwinglich bezeichnet werden können, kann Glasfaser zwischen der ersten und letzten Lage des Kohlefasergewebes verlegt werden. Das Glasfasergewebe sollte nicht rau sein, um die endgültige Form nicht zu beeinträchtigen.
Um die Herstellungskosten von Leichtbauteilen zu senken, wird das Element oft nur mit Kohlefaser laminiert – es wird nur als vordere Schicht des Karosserieelements platziert.
Vakuumformverfahren
Zusätzlich zum Standardsatz an Materialien und Werkzeugen benötigen Sie zur Herstellung von Kohlenstoffelementen im Vakuuminfusionsverfahren:

Sie können auch selbst einen Ofen zum Nachhärten von Kohlenstoffelementen bauen. Bitte beachten Sie, dass die Wärmebehandlung bei einer bestimmten Temperatur durchgeführt werden muss. Daher sollten Sie die Möglichkeit in Betracht ziehen, einen bestimmten Grad anzupassen und beizubehalten.
Bei der Vakuuminfusionstechnologie wird ein „Sandwich“ aus Kohlenstoffgewebe zusammengestellt und in einem geschlossenen Raum platziert. Nach der Installation wird die Luft abgepumpt und dem Werkstück Harz zugeführt. Das mit Harz imprägnierte Gewebe wird 20 bis 30 Minuten lang unter Vakuum belassen, wodurch die Harzzufuhr- und Lufteinlassschläuche verschlossen werden. Für die erste Aushärtung genügen 24 Stunden und Raumtemperatur, danach sollte das Carbonteil zur Nachhärtung in den Ofen geschickt werden. Wir haben die Vakuuminfusionsmethode nicht im Detail beschrieben, da der Vorgang im Video ausführlich gezeigt wird.
– ein Polymerverbundwerkstoff aus verwobenen Kohlenstofffaserfäden, die sich in einer Matrix aus Epoxidharzen befinden. Die häufigsten sind die folgenden:
- Handformverfahren;
- Injektionsmethode Polyester Harz;
- Vakuuminfusionsmethode.
Wo beginnt die Produktion?
Um also ein Teil selbst herzustellen, müssen Sie zunächst eine Form herstellen. Dazu können Sie fast jedes Material verwenden, das eine bestimmte Form behält und mit dem Sie bequem arbeiten können. Es könnte Gips sein oder Zementmörtel und Kunststoff und Holz und Metall – alles hängt davon ab, welche Art von Teil Sie herstellen und was für Sie persönlich einfacher zu bearbeiten ist.Nachdem die Form fertig ist (ausgehärtet, ggf. getrocknet), tragen Sie Gelcoat – eine Substanz auf Basis von Epoxid-Vinylesterharz – mit einer Rolle, einem Pinsel oder einem Spray auf die Oberfläche auf. Aufgrund seiner relativ hohen Festigkeit und Breite wird es als schützende und dekorative Außenschicht unseres zukünftigen Produkts dienen Farbspektrum, aus dem Sie den gewünschten Farbton auswählen müssen. Gelconate schützt das Teil perfekt vor aggressiven Einflüssen Außenumgebung, auch durch Einwirkung von Feuchtigkeit und Sonnenlicht.
Nachdem das Gelkonat getrocknet ist, können Sie mit dem Formen des Produkts selbst beginnen. Dazu schneiden wir Carbonmaterial (es kann Glasfaser, Glasmatte oder Kohlefasergewebe sein) darunter erforderliche Größe, legen Sie es in die vorbereitete Matrize (unsere Form) und tragen Sie mit einer Rolle oder einem Pinsel eine Bindemittelmischung bestehend aus Polyesterharz und Härter auf. Dies muss so sorgfältig und effizient wie möglich erfolgen und insbesondere darauf achten, dass sich keine Luftblasen in der Struktur des Teils befinden. Aus dem gleichen Grund „rollen“ wir das Teil nach Abschluss des Formens, aber bevor es aushärtet, mit einer harten Walze und drücken dabei Luftblasen aus ihm heraus (je mehr Luft nach dem Trocknen in der Matrix verbleibt, desto weniger zuverlässig wird Ihr Teil sein !
Kohlefaser zu Hause herstellen

Beim Erstellen einer Carbonoberfläche ist es sehr wichtig, darauf zu achten, dass keine Blasen auf der Oberfläche der Teile entstehen. Hierzu muss der Vakuuminfusions- bzw. Formprozess initialisiert werden. Die Ausrüstung für solche Arbeiten kostet etwa 150 bis 200 US-Dollar, was die Herstellung von Kohlefaser mit eigenen Händen und zu Hause seit dem Kauf zu einer ziemlich teuren Aufgabe macht notwendige Ausrüstung und Materialien wie Epoxidharz und andere Dinge müssen Sie etwa 15.000 Rubel investieren. Aber mit einer solchen Ausrüstung können Sie wirklich hochwertige Teile herstellen, die in ihrer Leistung mit denen konkurrieren können, die auf Automärkten und in Geschäften verkauft werden. Mit einem solchen Qualitätsindikator können Sie ernsthaft darüber nachdenken, Ihre selbst hergestellten Ersatzteile über das Internet oder auf denselben spezialisierten Märkten zu verkaufen. Die Hauptsache ist, kein Geld für eine Vakuumpumpe und andere Geräte zu verschwenden.
Das Formular erhalten, das Teil anwenden

Alle! Das Teil ist fertig, Sie können es am Auto montieren und die Ergebnisse des Tunings selbst genießen!
Abschließend möchte ich darauf hinweisen, dass der Hauptvorteil darin liegt diese Methode ist seine Verfügbarkeit zu Hause und relativ niedrige Kosten Der Hauptnachteil besteht, wie Sie wahrscheinlich erraten haben, in der Arbeitsintensität des Prozesses, und die meiste Zeit wird nicht für die Herstellung des Teils, sondern für die Vorbereitung der Form aufgewendet. Wer diese Probleme aber nicht scheut, erhält ein wirklich exklusives Tuningteil, das sonst niemand haben wird!!!
Einer unserer Kunden hatte das folgende Projekt: eine Geräteserie mit Kohlefaserkarosserien herzustellen. Leicht, langlebig, schön – alles Pluspunkte. Nur der Preis sticht. Also schickten sie mich auf eine Erkundungsmission, um herauszufinden, wie man dasselbe, aber billiger, machen kann.
Ehrlich gesagt hatte ich noch nie zuvor gesehen, wie solche Dinge hergestellt werden, und ich konnte mir die ganze Technologie noch nicht einmal vorstellen. Deshalb habe ich die Aufgabe sofort und gerne übernommen.
Es stellte sich jedoch heraus, dass der Weg zur Anlage nicht so einfach ist. Zwei Hersteller weigerten sich unter verschiedenen Vorwänden, sich am Produktionsstandort zu treffen und riefen mich beharrlich in ihr Büro. Der Dritte hatte ein Büro und eine Produktion im selben Gebäude, und ohne lange nachzudenken ging ich zu ihm.
Die Anlage sieht ganz ordentlich aus, ich werde in den Besprechungsraum/Ausstellungsraum geführt.
Die Vielfalt der Beispiele ist schwindelerregend: ein Carbon-Fahrrad, Teile für Auto- und Motorrad-Tuning, alle möglichen Spielereien mit unbekanntem Zweck.
Eine einteilige Motorhaube für BMW ist der Traum der Jungs vom Himmel.
Manchmal werden farbige Fäden in Carbongewebe eingewebt: rot oder blau, das sieht sehr ungewöhnlich aus.
Vollständig lackierte Teile sind von gewöhnlichen Teilen nicht sofort zu unterscheiden. Normalerweise tun Sportler dies: Sie brauchen geringes Gewicht, keine Angeber :)
Motorradhelm.
Und etwas Unbekanntes für das, was es braucht.
Aber Hauptziel Bei meinem Besuch gab es Folgendes:
Ipad hülle. Mich interessierte natürlich nicht das Gehäuse selbst, sondern ähnliches: Teile für Handyhüllen, Laptops, Tablets. Es war wichtig, die Produktionstechnologie zu verstehen und zu verstehen, wie man sie richtig gestaltet, damit sie so kostengünstig und technologisch fortschrittlich wie möglich ist. Deshalb habe ich nach langem Verhandeln und Überreden schließlich um eine Führung durch die Werkstatt gebeten.
Die Produktion nimmt eine Etage des Gebäudes ein, es ist sauber, aber eher verlassen.
Kohlefaserplatten mit aufgetragener Klebeschicht werden in Rollen geliefert. Es gibt ihn in verschiedenen Stärken und mit unterschiedlichen Webmustern. In speziellen Kühlschränken gelagert.
Der Stoff wird nach dem Muster in Stücke geschnitten und in mehreren Schichten auf die Matrize geklebt. Die Matrizen sind leicht, etwa aus Kunststoff und ressourcenschonender aus Aluminium.
Die zu verarbeitenden Matrizen werden jeweils in einem eigenen Bereich direkt auf dem Boden ausgelegt.
Der Carbon-Klebeprozess selbst befand sich dahinter Glastüren, aber sie weigerten sich rundweg, es mir zu zeigen, mit der Begründung, es sei ein schreckliches Geschäftsgeheimnis. Aber ich glaube nicht, dass da irgendetwas Geheimnisvolles ist, sie haben es einfach mit einer Schere ausgeschnitten und die Reste in eine Form gegeben.
Anschließend wird jedes Teil in Vakuumbeutel verpackt.
Die Luft wird aus den Beuteln abgepumpt und in einen von zwei größeren oder kleineren Öfen geladen.
Fertigteile werden aus den Formen entnommen. Wenn das Teil eine komplexe Form hat, ist die Matrix dafür komplex und besteht aus mehreren Teilen.
Qualitätskontrolle vor der Lieferung an das Lager.
Wie Sie vielleicht vermuten, ist dies nicht der gesamte Prozess. Jetzt müssen Sie die Kanten der Teile beschneiden und mit Lack lackieren. Dies erfolgt jedoch an einem anderen Standort, bei einem Subunternehmer. Sie boten an, vorbeizukommen und einen Blick darauf zu werfen, aber ich lehnte ab – da gibt es definitiv nichts Neues.
Oh, Sie interessieren sich wahrscheinlich für die Preise? Eine Carbonhülle für ein iPad kostet ab Werk also 25 US-Dollar. Ein Fahrrad kostet mehrere Tausend. Du wirst aufhören zu lächeln, wie einer meiner Freunde sagt. Und Reduktionsmöglichkeiten gibt es eigentlich nicht, zu kleine Stückzahlen, zu viel Handarbeit.
Aber du wirst trotzdem lächeln. Hier ist ein letztes Bild des gewöhnlichen chinesischen Lebens, das ich vor den Toren dieser Fabrik aufgenommen habe.