Dessins de diagramme de machine cnc à faire soi-même. Machine de gravure simple faite maison de routeur de commande numérique par ordinateur
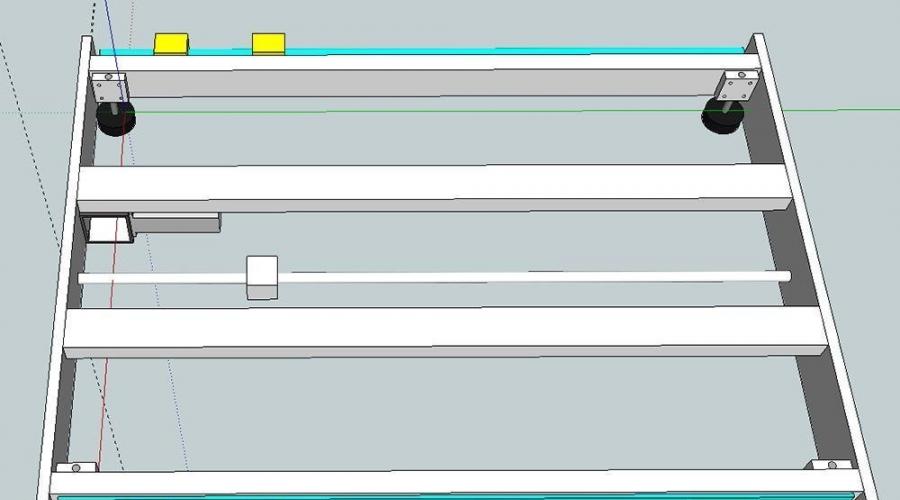
Lire aussi
Il a décrit en détail l'ensemble du processus de création d'une machine CNC pour travailler le bois et d'autres matériaux, en commençant par la conception.
1. Conception
Avant de construire une machine, vous devez au moins dessiner un croquis à la main, mais il est préférable de faire un dessin tridimensionnel plus précis à l'aide d'un programme de CAO. L'auteur du projet a utilisé google sketchup , un programme assez simple (gratuit pendant 30 jours). Pour un projet plus complexe, vous pouvez choisir Autocad.
Le but principal du dessin est de découvrir dimensions requises pièces à commander en ligne et assurez-vous que toutes les pièces mobiles de la machine s'emboîtent.
Comme vous pouvez le voir, l'auteur n'a pas utilisé de dessins détaillés avec des trous marqués pour le montage, il a décrit les trous dans le processus de construction de la machine, mais une telle conception initiale s'est avérée suffisante.
Dimensions hors tout de la machine : 1050 x 840 x 400 mm.
Course d'axe : X 730 mm, Y 650 mm, Z 150 mm
La longueur des rails et de la vis à billes dépend de la taille de la machine que vous avez en tête.
Lors de la conception d'une machine CNC, plusieurs questions se posent, dont la réponse dépend du résultat final.
Quel type de machine CNC souhaitez-vous choisir ?
Avec une table mobile ou avec un portail mobile ? Les conceptions de table coulissante sont souvent utilisées pour les machines-outils petite taille, jusqu'à 30x30 cm Ils sont plus faciles à construire, ils peuvent être rendus plus rigides que les voitures à portail mobile. L'inconvénient du déplacement de la table est qu'avec la même zone de coupe, la surface totale de la machine est deux fois plus grande que lors de l'utilisation de la conception avec un portail mobile. Dans ce projet, la zone de traitement est d'environ 65x65 cm, c'est pourquoi un portail mobile a été choisi.
Que voulez-vous traiter avec une machine CNC ?
Dans ce projet, la machine était destinée principalement au contreplaqué, bois franc bois et plastiques, ainsi que pour l'aluminium.
À partir de quoi la machine sera-t-elle construite ?
Cela dépend principalement du matériau qui sera traité sur la machine. Idéalement, le matériau utilisé pour fabriquer la machine doit être plus résistant que le matériau qui sera usiné, ou au moins aussi résistant. Par conséquent, si vous souhaitez couper de l'aluminium, la machine doit être construite en aluminium ou en acier.
De quelle longueur d'essieu avez-vous besoin ?
Selon l'idée originale, la machine CNC était censée traiter le contreplaqué et le MDF, qui sont produits aux Pays-Bas au format 62 x 121 cm.Par conséquent, pour Y, la distance de passage doit être d'au moins 620 mm. La longueur de déplacement le long de l'axe X est de 730 mm, car sinon la machine occuperait tout l'espace de la pièce. Par conséquent, l'axe X est plus court que la longueur de la feuille de contreplaqué (1210 mm), mais vous pouvez traiter la moitié, puis déplacer la feuille vers l'avant et traiter le reste. Avec cette astuce, il est possible d'usiner sur la machine des pièces bien plus grandes que la longueur de l'axe X. Pour l'axe Z, on a choisi 150 mm afin d'utiliser un quatrième axe à l'avenir.
Quel type de mouvement linéaire allez-vous utiliser ?
Il existe de nombreuses options pour un système de mouvement linéaire, la qualité du travail dépend en grande partie de son choix. Il est donc logique d'investir dans le meilleur système que vous pouvez vous permettre. L'auteur du projet a décidé que les rails linéaires étaient la meilleure option pour laquelle il avait assez d'argent. Si vous construisez un routeur CNC à 3 axes, vous devrez acheter un kit composé de trois ensembles de guides linéaires et de deux roulements linéaires par guide.
Quel système d'entraînement d'alimentation utiliserez-vous pour chaque essieu ?
Les principales options d'entraînement de l'alimentation sont les suivantes : courroies crantées, mécanismes à pignon et crémaillère et transmission vis-écrou. Pour les machines CNC artisanales, une transmission vis-écrou utilisant une paire de vis à billes est le plus souvent utilisée. L'écrou est fixé à la partie mobile de la machine, la vis est fixée aux deux extrémités. La vis est fixée au moteur. Si les moteurs tournent, l'écrou auquel est attachée la partie mobile de la machine se déplacera le long de la vis et mettra la machine en mouvement.
La vis à billes de cette machine est utilisée pour entraîner les axes X et Y. Les roulements à vis à billes offrent une conduite très douce, il n'y a pas de jeu et la qualité et la vitesse de coupe sont améliorées.
L'axe Z utilise une tige en acier inoxydable M10 de haute qualité avec un écrou Delrin fait maison.
Type de moteur et de contrôleur
Habituellement, les moteurs pas à pas sont utilisés dans les machines CNC maison. Les servomoteurs sont principalement utilisés pour les machines CNC industrielles de forte puissance, ils sont plus chers et nécessitent des contrôleurs plus coûteux. Des moteurs pas à pas de 3 Nm sont utilisés ici.
Type de broche
Le projet utilise un Kress d'origine et possède une belle bride de serrage de 43 mm ainsi qu'un contrôleur de vitesse intégré (mais la plupart des broches ont cette dernière caractéristique).
Si vous allez effectuer des coupes vraiment complexes, vous devez faire attention aux broches refroidies à l'eau - elles sont plus chères que les broches standard, mais elles sont beaucoup plus silencieuses, elles peuvent travailler à basse vitesse sans surchauffe et avec une variété de matériaux.
Dépenses
Cette machine CNC a coûté environ 1500 euros. Un routeur CNC pré-construit avec des spécifications similaires coûte beaucoup plus cher, vous pouvez donc économiser de l'argent en construisant le vôtre.
2. Accessoires pour créer une machine CNC
Matériel électrique et électronique :
- 3 moteurs pas à pas 3 Nm Nema 23 ;
- 3 pilotes de moteur pas à pas DM556 Leadshine ;
- Alimentation 36 V pour machines CNC ;
- carte d'interface 5 axes CNC Breakout Board pour contrôler les pilotes pas à pas ;
- Alimentation 5V pour carte d'interface;
- interrupteur à deux positions Marche/Arrêt ;
- câble toronné Blindé 4 conducteurs 18 AWG ;
- 3 interrupteurs de fin de course tactiles ;
- Broche : Kress FME 800 (également compatible Bosch Colt ou Dewalt Compact Router).
Optionnel:
- armoire/boîtier pour équipement électrique ;
- chemin de câbles en plastique mobile;
- Fiches de câble à 4 broches.
Parties mécaniques:
- guides linéaires : pour X - SBR 20 pour Y et Z - SBR 16 ;
- vis à billes (vis à billes) pour X et Y - diamètre 16 mm, pas 5 mm4
- comme vis de transmission pour l'axe Z : goupille en acier filetée M10 avec un écrou en Delrin fait maison ;
- profilé en aluminium : 30x60 mm, coupé en morceaux de 100 mm de long ;
- plaque en aluminium de 15 mm d'épaisseur;
- puissants pieds de nivellement anti-vibrations.
Programmes:
- logiciel CAO/FAO CamBam ;
- Programme de contrôle CNC Mach3
La machine est principalement construite avec des plaques en aluminium de 15 mm d'épaisseur et des profilés en aluminium de 30x60 mm. Les travaux ont été réalisés à l'aide de machines de perçage et de tournage. Les plaques et les profilés ont été commandés coupés sur mesure.
3. Axe X
Châssis de base composé de 4 pièces profilé en aluminium section 30x60 mm et deux panneaux latéraux de 15 mm d'épaisseur. À l'extrémité des profilés, il y a deux trous d'un diamètre de 6,8 mm, à l'aide d'un taraud, un filetage M8 est réalisé à l'intérieur des trous.
Filetage aux extrémités d'un profilé aluminium
Pour s'assurer que les trous sur les panneaux d'extrémité correspondent, les deux plaques ont été serrées ensemble lors du perçage. 4 trous sont percés au milieu de chaque plaque pour installer les roulements, et quatre trous supplémentaires dans l'une des plaques latérales pour le montage du moteur.
Leurs pièces en aluminium (50x50x20) formaient 4 blocs pour fixer les pattes de nivellement. Les blocs sont vissés aux profilés extérieurs avec quatre boulons M5 avec des écrous en T pour meubles.
Les guides linéaires s'adaptent directement sur les profilés en aluminium. Pour l'axe X, des rails d'un diamètre de 20 mm ont été utilisés. Les trous pré-percés dans la base des guides linéaires correspondent exactement aux rainures des profilés en aluminium. Pour l'installation, des boulons M5 et des écrous en T pour meubles ont été utilisés.
4. Plaques latérales du portail
Les plaques latérales du portail sont presque les mêmes, mais l'une d'elles comporte quatre trous supplémentaires percés pour le montage du moteur. L'ensemble du portail est constitué de plaques d'aluminium de 15 mm d'épaisseur. Pour que les trous soient exactement au bon endroit, des évidements ont été percés à des endroits soigneusement marqués avec un poinçon d'établi, et des trous ont été percés sur une perceuse le long de ces marques, d'abord avec une perceuse d'un diamètre plus petit, puis avec le nécessaire une.
En raison de la conception du portail, j'ai dû percer des trous aux extrémités des plaques latérales et faire des filetages M8 dans les trous.
5. Assemblage du portail
Portail assemblé et installé
Le reste du portail est réalisé de la même manière que les parties latérales. Le plus difficile était d'aligner correctement les rails linéaires, qui devaient s'aligner avec le bord de la plaque. Lors du marquage de l'emplacement exact des trous, j'ai pressé deux morceaux de profilés en aluminium contre les côtés de la plaque pour aligner les guides. Les trous percés sont filetés M5. Lors de la fixation des rails au portail, assurez-vous que la distance entre les rails est la même sur toute la longueur, les rails doivent être parallèles.
Des roulements linéaires sont fixés à la paroi latérale du portail.
Plusieurs équerres donnent une rigidité supplémentaire à la structure.
La plaque au bas du portail comporte 6 trous percés pour la fixer aux plaques latérales. J'ai dû percer deux trous au milieu pour fixer le porte-écrou.
6. Chariot de l'axe Y
Le chariot de l'axe Y se compose d'une seule plaque sur laquelle sont fixés des roulements linéaires. Percer des trous était assez facile, mais une grande précision était nécessaire. Sur cette plaque sont fixés des roulements pour l'axe Y et l'axe Z. Comme les roulements linéaires sont proches les uns des autres, le moindre désalignement les fait se gripper. Le chariot doit glisser facilement d'un côté à l'autre. Les rails et les roulements doivent être ajustés. Des instruments numériques de haute précision ont été utilisés pour l'alignement. Lorsque l'écrou d'entraînement de l'axe Y a été fabriqué, deux trous supplémentaires ont dû être percés dans la plaque pour la fixer.
7. Axe Z
Les guides linéaires (rails) de l'axe Z sont fixés à la partie mobile de l'ensemble de l'axe Z. Les rails devaient être décalés de quelques millimètres du bord de la plaque. Pour les aligner, deux morceaux de plastique de l'épaisseur souhaitée ont été utilisés comme entretoises. On savait avec certitude que les bords de la plaque d'aluminium étaient parallèles, donc entre les côtés en aluminium attachés au bord de la plaque et les rails, l'auteur a inséré des morceaux de plastique, poussant les rails à la distance égale souhaitée, puis a marqué le trous, les percer et couper le filetage intérieur.
Pour monter la plaque supérieure sur l'assemblage de l'axe Z, trois trous sont percés à l'extrémité de la plaque de montage. Il n'était pas possible de fixer le moteur pas à pas directement sur la plaque, j'ai donc dû fabriquer un support en plastique séparé pour le moteur (voir point 12).
Deux blocs de logements de roulements sont fabriqués dans le même plastique. La vis d'entraînement est une tige en acier avec un filetage M10. La poulie de courroie de distribution est percée, filetée M10 et simplement boulonnée au sommet de la vis d'entraînement. Il est maintenu en place par trois vis de réglage. L'écrou d'entraînement Delrin se fixe au chariot de l'axe Y.
L'écrou d'entraînement Delrin se fixe au chariot de l'axe Y.
Le support de broche a été commandé à l'avance et possède une bague de serrage de 43 mm qui s'adapte au Kress utilisé dans le projet.
Si vous souhaitez utiliser une broche refroidie à l'eau, elle est souvent livrée avec un support prêt à l'emploi. Vous pouvez également acheter les supports séparément si vous souhaitez utiliser un boîtier Dewalt ou Bosch, ou les imprimer en 3D.
8. Courroies et poulies de distribution
Les moteurs sont souvent montés sur à l'extérieur machine ou sur un rack séparé. Dans ce cas, les moteurs peuvent être connectés directement à la vis à billes à l'aide d'un accouplement élastique. Mais, comme la machine est située dans une petite pièce, les moteurs sortis à l'extérieur interféreraient.
C'est pourquoi les moteurs sont placés à l'intérieur de la voiture. Il n'était pas possible de connecter directement les moteurs aux vis à billes, il a donc fallu utiliser des courroies de distribution et des poulies HTD5m de 9 mm de large.
Lorsque vous utilisez un entraînement par courroie, vous pouvez utiliser un réducteur pour connecter le moteur à la vis d'entraînement, ce qui vous permet d'utiliser des moteurs plus petits et d'obtenir toujours le même couple mais une vitesse plus lente. Comme les moteurs ont été choisis assez gros, il n'était pas nécessaire de rétrograder pour obtenir plus de puissance.
9. Supports moteur
Les supports moteur sont fabriqués à partir de tubes en aluminium de section carrée coupés à longueur sur commande. Vous pouvez également prendre un tube en acier et en découper des morceaux carrés. Les supports de moteur pour les axes X et Y doivent pouvoir coulisser vers l'intérieur et vers l'extérieur pour tendre les courroies de distribution. Sur le tour des fentes ont été faites et un grand trou percé sur un côté du support, mais vous pouvez également le faire sur une perceuse à colonne.
Un grand trou sur un côté de la monture a été scié avec une scie à bout. Cela permet au moteur de s'asseoir au ras du sol et maintient également l'arbre centré. Le moteur est monté avec des boulons M5. Il y a quatre fentes de l'autre côté du support pour que le moteur puisse glisser d'avant en arrière.
10. Blocs de roulement
Les blocs de support pour les axes X et Y sont en barre d'aluminium de 50 mm section ronde- quatre morceaux de 15 mm d'épaisseur chacun en ont été découpés. Après avoir marqué et percé quatre trous de montage, un grand trou est percé au centre de la pièce. Ensuite, une cavité pour les roulements a été réalisée. Les roulements doivent être enfoncés et les blocs boulonnés aux plaques d'extrémité et latérales.
11. Support pour écrou d'entraînement dans l'axe Z
Au lieu d'une vis à billes pour l'axe Z, j'ai utilisé une tige filetée M10 et un écrou fait maison à partir d'un morceau de Delrin. Le polyformaldéhyde Delrin est bien adapté à cet usage car il est autolubrifiant et ne s'use pas avec le temps. Si vous utilisez un taraud de bonne qualité pour le filetage, le jeu sera minime.
12. Supports pour écrous d'entraînement le long des axes X et Y
Pour les axes X et Y, le support d'entraînement est en aluminium. Les écrous à vis à billes ont deux petites brides avec trois trous de chaque côté. Un trou de chaque côté est utilisé pour fixer l'écrou au support. Le support est usiné sur un tour avec une grande précision. Une fois que vous avez fixé les écrous au portique et au chariot de l'axe Y, vous pouvez essayer de déplacer ces pièces d'un côté à l'autre en tournant les vis à billes à la main. Si les dimensions des supports sont incorrectes, l'écrou se bloquera.
Montage sur l'axe Y.
13. Support moteur axe Z
Le support moteur de l'axe Z est différent du reste. Il est découpé dans de l'acrylique de 12 mm. La tension de la courroie peut être ajustée en desserrant les deux boulons en haut et en faisant glisser l'ensemble du support moteur. Sur le ce moment le support acrylique fonctionne très bien, mais à l'avenir je pense le remplacer par un support en aluminium, car lorsque la courroie est tendue, la plaque acrylique se plie légèrement.
14. Plan de travail
Une table en aluminium avec des rainures en T serait préférable, mais c'est cher. L'auteur du projet a décidé d'utiliser un plateau de table perforé car il s'intègre dans le budget et offre de nombreuses options pour serrer la pièce.
La table est fabriquée à partir d'un morceau de contreplaqué de bouleau de 18 mm d'épaisseur et fixée, avec des boulons M5 et des écrous à rainure en T, à des profilés en aluminium. 150 écrous hexagonaux M8 ont été achetés. À l'aide du programme CAO, une grille a été dessinée avec des découpes hexagonales pour ces écrous. Ensuite, la machine CNC a découpé tous ces trous pour les écrous.
Un morceau de MDF de 25 mm d'épaisseur a été installé sur un morceau de contreplaqué de bouleau. Il s'agit d'une surface remplaçable. Un grand couteau de forme a été utilisé pour percer des trous dans les deux parties. Les trous dans le MDF sont alignés exactement avec le centre des trous hexagonaux découpés précédemment. Ensuite, un morceau de MDF a été retiré et tous les écrous ont été installés dans les trous du contreplaqué. Les trous étaient légèrement plus petits que les écrous, de sorte que les écrous y étaient martelés. Une fois terminé, le MDF est retourné à sa place.
La surface de la table est parallèle aux axes X et Y et est complètement plane.
15. Électronique
Les composants suivants ont été utilisés :
- Alimentation principale avec tension de sortie 48V DC et courant de sortie 6.6A;
- 3 pilotes de moteur pas à pas Leadshine M542 V2.0 ;
- 3 moteurs pas à pas 3Nm hybrides Nema 23 ;
- Tableau d'interface;
- relais - 4-32V CC, 25A/230 V CA;
- interrupteur principal;
- alimentation pour carte d'interface 5V DC;
- alimentation pour ventilateurs de refroidissement 12V DC;
- 2 ventilateurs Cooler Master Sleeve Bearing 80mm;
- 2 prises - pour broche et aspirateur ;
- bouton d'arrêt d'urgence et interrupteurs de fin de course (pas encore installés).
Si vous ne voulez pas dépenser beaucoup d'argent pour acheter du matériel séparément, vous pouvez l'acheter en un seul lot. Avant de commander, vous devez réfléchir à la taille des moteurs pas à pas dont vous avez besoin. Si vous construisez une petite machine pour couper du bois et du plastique, les moteurs pas à pas Nema 23, 1,9 Nm vous donneront suffisamment de puissance. Des moteurs de 3Nm sont choisis ici car la machine elle-même est assez grande et lourde, et l'usinage de matériaux comme l'aluminium était également prévu.
Pour les petits moteurs, vous pouvez charger trois moteurs, mais il est préférable d'utiliser des pilotes séparés. Les pilotes personnalisés de Leadshine sont micro-pas pour obtenir une douceur maximale et réduire les vibrations du moteur pas à pas. Les pilotes de ce projet peuvent gérer un maximum de 4,2 A et jusqu'à 125 micropas.
Une source de tension de 5 V CC est connectée à l'entrée d'alimentation principale. Les ventilateurs ont une prise électrique à l'intérieur de l'armoire, ils utilisent donc un adaptateur mural standard de 12 volts pour les alimenter. L'alimentation principale est allumée et éteinte avec un grand interrupteur.
Le relais 25A est contrôlé par un ordinateur via un disjoncteur. Les bornes d'entrée du relais sont connectées aux bornes de sortie du disjoncteur. Le relais est connecté à deux prises électriques qui alimentent le Kress et le nettoyeur de copeaux. Lorsque le code G se termine par une commande M05, l'aspirateur et la broche s'éteignent automatiquement. Pour les activer, vous pouvez appuyer sur F5 ou utiliser la commande M03 G-code.
16. Armoire électronique
Pour l'équipement électrique, vous avez besoin d'un bon casier. L'auteur a dessiné des tailles et des emplacements approximatifs pour tous les composants sur une feuille de papier, en essayant de les disposer de manière à ce que toutes les bornes soient facilement accessibles lors de la connexion des fils. Il est également important qu'il y ait un flux d'air suffisant à travers l'armoire, car les contrôleurs pas à pas peuvent devenir très chauds.
De par leur conception, tous les câbles doivent avoir été connectés à l'arrière du boîtier. Des connecteurs spéciaux à 4 fils ont été utilisés afin qu'il soit possible de déconnecter l'électronique de la machine sans déconnecter aucune des bornes de fil. Deux prises ont été fournies pour alimenter la broche et l'aspirateur. Les prises de courant sont connectées à un relais pour allumer et éteindre automatiquement la broche par les commandes Mach3. Il aurait dû y avoir un gros interrupteur sur le devant du casier.
Les détails de l'armoire sont découpés sur la machine CNC elle-même
De plus, après une disposition approximative des pièces, les pièces de la coque ont été conçues dans le programme CAO. Ensuite, sur la machine elle-même, déjà assemblée, tous les côtés et la base sont découpés. Au-dessus de l'armoire se trouve un couvercle, avec un morceau de plexiglas au milieu. Après l'assemblage, tous les composants ont été installés à l'intérieur.
17. Logiciel
Mach3
Trois types de logiciels sont nécessaires pour contrôler une machine CNC.
- Programme de CAO pour créer des dessins.
- Programme CAM pour créer des trajectoires d'outils et une sortie de code G.
- Et un programme de contrôleur qui lit le code G et contrôle le routeur.
Ce projet utilise un programme CamBam simple. Il possède des fonctions de CAO de base et convient à la plupart des projets de bricolage. En même temps, c'est un programme CAM. Avant que CamBam puisse créer des chemins, quelques paramètres doivent être définis. Des exemples de paramètres sont le diamètre de l'outil utilisé, la profondeur de coupe, la profondeur par passe, la vitesse de coupe, etc. Après avoir créé le parcours d'outil, vous pouvez générer un code G qui indique à la machine quoi faire.
Dessin créé dans CamBam
Mach3 est utilisé pour le logiciel du contrôleur. Mach3 envoie des signaux via le port parallèle de l'ordinateur à la carte d'interface. Mach3 commande le zéro de l'outil de coupe et lance les programmes de coupe. Vous pouvez également l'utiliser pour contrôler la vitesse de la broche et la vitesse de coupe. Mach3 dispose de plusieurs assistants intégrés que vous pouvez utiliser pour générer des fichiers G-code simples.
Parcours d'outil créé par CamBam
18. Utilisation de la machine
Les premiers ont été fabriqués plusieurs pinces pour fixer les matériaux traités à la table de travail. Et le premier "gros" projet était l'armoire électronique (item 15).
Comme premiers échantillons, plusieurs divers types engrenages, boîtes pour médiators.
collecteur de poussière
Il s'est avéré que la machine CNC produit beaucoup de poussière et fait beaucoup de bruit. Pour résoudre le problème de la poussière, un dépoussiéreur a été fabriqué, auquel un aspirateur peut être fixé.
Routeur CNC 3 axes
Machine utilisateur SorenS7 .
Sans routeur CNC, de nombreux projets resteront non réalisés. L'auteur est arrivé à la conclusion que toutes les machines moins chères que 2000 euros ne peuvent pas donner cette taille surface de travail et la précision dont il a besoin.
Ce qu'il fallait :
- zone de travail 900 x 400 x 120 mm ;
- broche relativement silencieuse, garantissant une puissance élevée à basse vitesse;
- dureté, autant que possible (pour le traitement pièces en aluminium);
- haut degré précision;
- Interface USB;
- coûte moins de 2000 euros.
Ces exigences ont été prises en compte dans la conception 3D. L'attention principale a été accordée à l'emboîtement de toutes les pièces.
En conséquence, il a été décidé de construire un routeur avec un cadre profilé en aluminium, des vis à billes de 15 mm et des moteurs pas à pas NEMA 23, avec un courant de travail de 3A, parfaitement adaptés au système de montage fini.
Toutes les pièces s'adaptent parfaitement et il n'est pas nécessaire de fabriquer des pièces spéciales supplémentaires.
1. Fabrication du cadre
L'axe X a été assemblé en quelques minutes.
Les guides linéaires de la série HRC sont de très haute qualité, et immédiatement après l'installation, il est clair qu'ils fonctionneront parfaitement.
Puis le premier problème est survenu : les vis d'entraînement ne rentraient pas dans les roulements. Par conséquent, il a été décidé de refroidir les vis avec de la neige carbonique afin de réduire les dimensions.
2. Installation des vis d'entraînement
Une fois les extrémités des vis refroidies avec de la glace, elles s'intègrent parfaitement dans les supports.
3 : Électrique
L'assemblage de la partie mécanique est terminé, c'est maintenant au tour des composants électriques.
Étant donné que l'auteur connaissait bien Arduino et souhaitait fournir un contrôle total sur l'USB, le choix s'est porté sur Arduino Uno avec carte d'extension CNC Shield et pilotes de moteur pas à pas DRV8825. L'installation n'a pas été difficile du tout, et après avoir défini les paramètres, la machine a commencé à être contrôlée à partir d'un PC.
Mais comme le DRV8825 fonctionne principalement à 1,9 A et 36 V (et devient très chaud), un saut de pas se produit en raison d'une trop grande batterie faible. Un broyage long à des températures élevées ne se passerait guère bien.
Ensuite, il y avait des pilotes Tb6560 bon marché branchés sur une carte d'extension. La tension nominale s'est avérée pas trop adaptée à cette carte. Une tentative a été faite pour utiliser une alimentation 36V.
En conséquence, deux pilotes fonctionnent normalement, le troisième ne peut pas supporter une tension plus élevée et fait tourner le rotor du moteur pas à pas dans une seule direction.
J'ai encore dû changer de pilote.
Bien approché tbV6600. Il est presque complètement fermé. radiateur en aluminium et facile à mettre en place. Désormais, les moteurs pas à pas sur les axes X et Y fonctionnent avec un courant de 2,2 A et sur l'axe Z avec 2,7 A.
Il était nécessaire de protéger l'alimentation des moteurs pas à pas et le convertisseur de fréquence des petites puces en aluminium. Il existe de nombreuses solutions lorsque le transducteur est sorti assez loin de la fraiseuse. Le principal problème est que ces appareils génèrent beaucoup de chaleur et nécessitent un refroidissement actif. A été trouvé solution originale: Utilisez des morceaux de collants de 30 cm comme manchon de protection, bon marché et gai, et fournissez une circulation d'air suffisante.
4. Broche
Choisir la bonne broche n'est pas facile. L'idée originale était d'utiliser une broche Kress1050 standard, mais elle n'a que 1050 watts à 21000 tr/min, donc je ne m'attendais pas à beaucoup de puissance à des vitesses inférieures.
Le fraisage à sec de pièces en aluminium et en acier nécessite 6 000 à 12 000 tr/min. Une broche VFD de trois kilowatts avec un onduleur a été achetée, avec une livraison depuis la Chine, elle a coûté 335 euros.
C'est une broche assez puissante et facile à installer. Il est lourd - poids 9 kg, mais un cadre solide peut supporter son poids.
5. Assemblage terminé
La machine fait du bon boulot, j'ai dû bricoler les drivers du moteur pas à pas, mais en général le résultat est satisfaisant. Dépensé 1500 euros et construit une machine qui répond exactement aux besoins du créateur.
Le premier projet de fraisage était une encoche façonnée en POM.
6 : Finition pour le fraisage de l'aluminium
Déjà lors du traitement du POM, il était clair que le couple sur le support Y est trop important et que la machine se plie sous des charges élevées le long de l'axe Y. L'auteur a donc acheté un deuxième guide et mis à niveau le portail en conséquence.
Après cela, tout est revenu à la normale. Coût de réalisation 120 euros.
Maintenant, vous pouvez fraiser l'aluminium. L'alliage AlMg4.5Mn a donné de très bons résultats sans aucun refroidissement.
7. Conclusions
Pour créer votre propre machine CNC, vous n'avez pas besoin d'avoir sept travées dans le front, tout est entre nos mains.
Si tout est bien planifié, il n'est pas nécessaire d'avoir un tas de matériel et conditions idéales pour travailler, vous n'avez besoin que d'une certaine somme d'argent, d'un tournevis, d'une pince et d'une perceuse.
Il a fallu un mois pour développer la conception à l'aide du programme de CAO et pour commander et acheter des composants, quatre mois pour l'assemblage. La création de la deuxième machine aurait pris beaucoup moins de temps, car l'auteur n'avait aucune expérience dans le domaine des machines-outils, et il a dû en apprendre beaucoup sur la mécanique et l'électronique.
8. Accessoires
Électrique:
Toutes les pièces électriques sont achetées sur ebay.
- Arduino GRBL + CNC Shield : environ 20 euros
- Pilote de moteur pas à pas : 12 euros par pièce.
- Alimentation : 40 euros
- Moteurs pas à pas : environ 20 euros la pièce
- Broche + inverseur : 335 euros
Mécanique:
Roulements linéaires ARC 15 FN
Une photo: www.dold-mechatronics.de
Guidages linéaires AR/HR 15 - ZUSCHNITT
Une photo: www.dold-mechatronics.de
Vis à billes SFU1605-DM :
- 2x 1052mm
- 1x 600mm
- 1x 250mm
Une photo: www.dold-mechatronics.de
Support de roulement à vis à billes FLB20-3200 avec support de moteur NEMA23 :
Une photo: www.dold-mechatronics.de
Support de vis à billes LLB20
Une photo: www.dold-mechatronics.de
Accouplements moteur pas à pas-broche : provenance de Chine à 2,5 euros la pièce.
Cadre:
Profils de base 160x16 Écrou type I 8
Une photo: www.dold-mechatronics.de
Profils pour axe X 30x60 B-Type Nut 8
Une photo: www.dold-mechatronics.de
Profils de montage pas à pas axe Y 30x60 Écrou type B 8
Une photo: www.dold-mechatronics.de
Portail:
Profil 30x60 B-Type Écrou 8 pour roulement linéaire axe X 100 mm
Plaque arrière : plaque en aluminium de 5 mm d'épaisseur, 600x200.
Profil 30x60x60 B-Type Écrou 8 pour Y : 2 pcs.
Une photo: www.dold-mechatronics.de
Profil 30x30 B-Type Écrou 8
pour Z :
Plaque de montage - plaque aluminium épaisseur 5 mm, dimensions 250x160
Plaque coulissante pour montage broche - plaque aluminium épaisseur 5 mm, dimensions 200x160
9. Programme
Après une longue recherche d'une solution logicielle, le programme pratique Estlcam a été choisi, avec un coût de licence de 50 euros. La version d'essai du programme possède toutes les fonctionnalités de la version sous licence, mais est plus lente.
Ce logiciel est capable de reprogrammer l'Arduino et possède de nombreuses fonctionnalités, dont la possibilité de contrôler directement les moteurs pas à pas.
Exemple : Pour trouver le bord d'une pièce, vous devez connecter les fils aux contacts du micro-ordinateur Arduino et à la pièce. Si la pièce n'est pas conductrice, vous pouvez créer un revêtement conducteur temporaire à l'aide d'une feuille.
Après cela, le programme amène l'outil à la pièce de différents côtés et détermine ses limites au moment du contact.
10. Mise à niveau
Des supports en plastique temporaires ont été installés sur les axes Y et Z. Le plastique était assez solide, mais les agrafes pouvaient encore se casser. Par conséquent, l'auteur a fraisé des supports en aluminium pour les remplacer. Le résultat est montré sur la photo.
11. Machine en fonctionnement
Après un peu de pratique, la machine donne déjà de très bons résultats, pour du fait maison.
Ces photos montrent une pièce en alliage AlMg4.5Mn. Il est entièrement fraisé. Sur la deuxième photo - le résultat de la machine, sans autre traitement par d'autres moyens.
Une fraise VHM de 6 mm à 3 dents a été utilisée. Lors de l'utilisation de fraises de 4 et 6 mm, la machine obtient des résultats assez corrects. Pour sa classe d'équipement, bien sûr.
Table CNC
Pour le dessert - pas une machine, mais un produit maison utile et intéressant pour une machine, à savoir un lit durable et spacieux avec des étagères. Si vous n'avez pas encore de machine CNC, vous pouvez la construire plus tôt et l'utiliser comme établi.
Evan et Caitlin, propriétaires du site EvanAndKatelyn.com , a mis à jour sa table CNC avec fonctionnalité et espace.
Le produit a été entièrement assemblé sur des raccords à vis, sans l'utilisation de colle, afin de préserver la possibilité d'une modification et d'une mise à niveau faciles.
Outils et accessoires d'occasion :
- bouton d'arrêt ;
- Porte-rouleau ;
- Fraise et mèches ;
- Perceuse;
- Visseuse électrique;
- Vu;
- Machine X-Carve;
- Fraise en carbure 1/4 po ;
- Fraise à pointe sphérique à 4 canaux en carbure de 1/4 de pouce ;
- Protection auditive.
Étape 1 : préparation
La première étape consiste à tout retirer de l'ancienne table, en commençant par la machine et en terminant par un tas d'autres choses qui s'y trouvent, et à la démonter partiellement. Tout a été entièrement démonté, à l'exception de deux grandes étagères de 120 x 120 cm, qui ont été renforcées, constituant la base d'une nouvelle table.
Étape 2 : renforcer les étagères
Des équerres ont été utilisées sur les quatre coins intérieurs et des supports en L le long traverse courant le long du côté inférieur.
Sur la photo ci-dessous: une comparaison d'une étagère renforcée avec une étagère inachevée.
Étape 3 : coupez l'excédent
A l'origine il y avait 4 casiers s'élevant au dessus du dessus de la table car une étagère supplémentaire était prévue au dessus de la machine. Cette idée a été rejetée, décidant de laisser deux racks sur quatre.
Ils ont été renforcés par des cornières.
Une étagère a été placée dessus et renforcée avec plus de supports.
Essai de force.
Étape 4 : Pegboard - Barre d'outils
Le meuble mis à jour devait ajouter autant d'espace de stockage que possible, et l'un des détails qui élargissait ses possibilités était un panneau perforé, dans les trous duquel des porte-outils sont fixés. Coupez les coins du panneau avec une scie sauteuse.
Étape 5 : Étagères inférieures
Pour le rangement en partie basse, il fallait laisser le plus de place possible, car. il y a entreposé une scie circulaire à table et un tambour Rectifieuse. Il y avait aussi un besoin de beaucoup d'espace pour stocker les matériaux, il a donc été décidé d'ajouter une étagère, mais de la rendre facile à retirer. Handy préparé pour les jambes barres en bois et une feuille de contreplaqué.
Les pieds ont été fixés à la feuille de contreplaqué avec des équerres d'angle, l'étagère résultante a été insérée dans partie inférieure. Il est facile à retirer lorsqu'un stockage pleine hauteur est à nouveau nécessaire.
Étape 6 : Étagères du haut
L'ancien cadre avait une étagère supérieure pour un ordinateur travaillant avec la machine et pour diverses petites choses. Il restait encore de la place, et sous cette étagère ils décidèrent d'en faire une autre. Il a également aidé à couvrir les prises et le câblage de la machine.
L'étagère supérieure a été placée sur les extrémités des racks et vissée.
Dans la deuxième étagère, les coins des jambes ont été coupés avec une scie sauteuse.
Et aussi fixé avec des coins.
Étape 7 : finitions
Un panneau avec l'inscription "Appelez-moi" a été vissé à l'extrémité, qui sera plus tard remplacé par un nom inventé par les abonnés de YouTube.
Enfin, tout ce qui était dans son prédécesseur a été remis sur la table.
Il existe de nombreux projets impressionnants de machines artisanales, souvent les auteurs étonnent par leurs compétences et leurs solutions pleines d'esprit. En tant que passe-temps, l'auto-assemblage d'une machine CNC ou d'une imprimante 3D surpasse de nombreux autres passe-temps - à la fois en termes d'utilité du résultat, car de nombreuses choses merveilleuses peuvent être faites sur la machine, et en termes d'avantages du processus lui-même - ce n'est pas seulement excitant, mais aussi activité cognitive pour aider à développer des compétences en ingénierie.
Nous ne répertorions pas les modèles individuels, car ils sont nombreux, et pour tous les buts, objectifs et conditions d'installation et de fonctionnement existantes, l'équipement doit être sélectionné individuellement, avec lequel des experts vous aideront. Contactez-nous!
Traitement complexe divers matériaux a depuis longtemps cessé d'être le lot des magasins d'usine. Il y a vingt ans, le maximum que les artisans à domicile pouvaient se permettre était de scier avec une scie sauteuse.
Aujourd'hui, les routeurs portatifs et les lasers de découpe peuvent être facilement achetés à la quincaillerie. Divers guides sont fournis pour le traitement linéaire. Mais qu'en est-il de la découpe de formes complexes ?
Les tâches élémentaires peuvent être réalisées à l'aide d'un modèle. Cependant cette méthode présente des inconvénients: premièrement, il est nécessaire de créer le gabarit lui-même, et deuxièmement, le motif mécanique a des restrictions sur la taille des arrondis. Et enfin, l'erreur de tels appareils est trop grande.
Une solution a été trouvée depuis longtemps: une machine CNC vous permet de découper de vos propres mains des formes aussi complexes dans du contreplaqué, ce dont les «opérateurs de puzzle» ne peuvent que rêver.
Le dispositif est un système de positionnement de coordonnées de l'outil de coupe, contrôlé Programme d'ordinateur. C'est-à-dire que la tête de traitement se déplace le long de la pièce, selon une trajectoire donnée. La précision n'est limitée que par la taille de l'accessoire de coupe (cutter ou faisceau laser).
Les possibilités de ces machines sont infinies. Il existe des modèles avec un positionnement bidimensionnel et tridimensionnel. Cependant, leur coût est si élevé que l'acquisition ne peut être justifiée que par une utilisation commerciale. Il reste à assembler la machine CNC de vos propres mains.
Fonctionnement du système de coordonnées
La base de la machine est un châssis puissant. La base est une surface parfaitement plane. Il sert également de bureau. Le deuxième élément de base est le chariot sur lequel l'outil est fixé. Il peut s'agir d'un dremel, d'un routeur manuel, d'un pistolet laser - en général, de tout appareil capable de traiter une pièce. Le chariot doit se déplacer strictement dans le plan du châssis.
Commençons par une configuration 2D.
En tant que cadre (base) pour une machine CNC à faire soi-même, vous pouvez utiliser la surface de la table. Surtout, après réglage de tous les éléments, la structure ne bouge plus, restant rigidement vissée à la base.
Pour se déplacer dans une direction (appelons-la X), deux guides sont placés. Ils doivent être strictement parallèles entre eux. Une structure de pont est installée en travers, également constituée de guides parallèles. Le deuxième axe est Y.
En définissant les vecteurs de mouvement le long des axes X et Y, vous pouvez définir le chariot (et avec lui l'outil de coupe) sur n'importe quel point du plan du bureau avec une grande précision. En choisissant le rapport des vitesses de déplacement le long des axes, le programme fait en sorte que l'outil se déplace en continu le long de n'importe quelle trajectoire, la plus complexe.
Le châssis de la machine CNC est fabriqué par les mains d'un artisan, vidéo
Il existe une autre notion : le chariot avec l'outil est fixe immobile, la table de travail se déplace avec la pièce. Il n'y a pas de différence fondamentale. A moins que les dimensions du socle (et donc de la pièce) ne soient limitées. Mais le circuit d'alimentation de l'outil de travail est simplifié, il n'y a pas lieu de se soucier des câbles d'alimentation souples.
Lors du choix des composants électroniques pour votre machine de bricolage, il est important de faire attention à leur qualité, car la précision des opérations technologiques qui y seront effectuées en dépendra. Après avoir installé et connecté tous les composants électroniques du système CNC, vous devez télécharger le logiciel et les pilotes nécessaires. Ce n'est qu'après cela qu'un test de fonctionnement de la machine suit, vérifiant le bon fonctionnement de la machine sous le contrôle des programmes téléchargés, identifiant les défauts et les éliminant rapidement.
Toutes les actions ci-dessus et les composants répertoriés conviennent à la fabrication d'une fraiseuse de vos propres mains, non seulement pour un groupe d'alésage coordonné, mais également pour un certain nombre d'autres types. Sur de tels équipements, il est possible de traiter des pièces avec une configuration complexe, puisque le corps de travail de la machine peut se déplacer dans trois plans : 3d.
Votre désir d'assembler de vos propres mains une telle machine à commande numérique doit être soutenu par la présence de certaines compétences et de dessins détaillés. Il est également fortement souhaitable de visionner un certain nombre de vidéos de formation thématiques, dont certaines sont présentées dans cet article.
21 , note moyenne : 3,52
sur 5)
Pour la plupart des artisans à domicile, la fabrication d'un tel assemblage en tant que fraiseuse CNC à faire soi-même est quelque chose au niveau d'une intrigue fantastique, car ces machines et mécanismes sont complexes dans la conception, la compréhension constructive et électronique de l'appareil.
Cependant, ayant à portée de main la documentation nécessaire, ainsi que les matériaux et accessoires requis, il est tout à fait possible de fabriquer de vos propres mains une mini-fraiseuse artisanale équipée d'une CNC.
Ce mécanisme se distingue par la précision du traitement effectué, la facilité de contrôle des processus mécaniques et technologiques, ainsi que d'excellents indicateurs de productivité et de qualité du produit.
Principe d'opération
Fraiseuses de blocs innovantes commandées par ordinateur conçues pour des modèles complexes sur des produits semi-finis. La conception doit avoir un composant électronique. Ensemble, cela vous permettra d'automatiser au maximum les processus de travail.
Pour modéliser des mécanismes de fraisage, vous devez d'abord vous familiariser avec les éléments fondamentaux. Le rôle de l'élément d'actionnement est une fraise, qui est montée dans une broche située sur l'arbre d'un moteur électrique. Cette partie est fixée sur la base. Il est capable de se déplacer selon deux axes de coordonnées : X et Y. Concevoir et installer une table de support pour fixer les pièces.
L'unité de réglage électrique s'articule avec les moteurs électriques de propulsion. Ils assureront le déplacement du chariot par rapport aux pièces ou produits semi-finis en cours de traitement. En utilisant une technologie similaire, une image graphique 3D est réalisée sur des avions en bois.
La séquence de travail effectuée par ce mécanisme CNC:
- L'écriture programme de travail, grâce à quoi le mouvement du corps de travail sera effectué. Pour cette procédure, il est préférable d'utiliser des systèmes électroniques spécialisés conçus pour s'adapter aux copies "artisanales".
- Montage des produits semi-finis sur la table.
- Sortie logicielle vers la CNC.
- Mécanismes de démarrage, contrôlant le passage des manipulations automatiques des équipements.
Pour obtenir le niveau maximum d'automatisation en mode 3D, complétez correctement le schéma et étiquetez certains composants. Les experts conseillent fortement d'étudier d'abord les instances de production avant de commencer à construire une fraiseuse de mes propres mains.
Schéma et dessin
Schéma d'une fraiseuse CNC
La phase la plus critique de la fabrication d'un analogue fait maison est la recherche du déroulement optimal de la fabrication de l'équipement. Cela dépend directement des caractéristiques globales des pièces à traiter et de la nécessité d'atteindre une certaine qualité de traitement.
Afin d'obtenir tout fonctions nécessaireséquipement, la meilleure option est la fabrication d'une mini-fraiseuse de leurs propres mains. Ainsi, vous serez sûr non seulement de l'assemblage et de sa qualité, mais aussi des propriétés technologiques, on saura à l'avance comment l'entretenir.
Composants de transmission
L'option la plus réussie consiste à concevoir 2 chariots se déplaçant le long d'axes perpendiculaires X et Y. Il est préférable d'utiliser des tiges de métal poli comme cadre. Les chariots mobiles mobiles sont "habillés" dessus. Pour la fabrication correcte de la transmission, préparez des moteurs pas à pas, ainsi qu'un jeu de vis.
Pour une meilleure automatisation des flux de travail des fraiseuses CNC, conçues par soi-même, il est nécessaire de compléter immédiatement le composant électronique dans les moindres détails. Il est divisé en les composants suivants :
- utilisé pour conduire l'énergie électrique vers les moteurs pas à pas et alimenter la puce du contrôleur. Le fonctionnement est considéré comme une modification 12v 3A ;
- son but est de donner des commandes aux moteurs. Pour l'exécution correcte de toutes les opérations spécifiées d'une fraiseuse CNC, il suffira d'utiliser un schéma simple pour surveiller les performances de 3 moteurs;
- pilotes (logiciels). C'est aussi un élément de réglage du mécanisme mobile.
Vidéo: fraiseuse CNC à faire soi-même.
Accessoires pour une fraiseuse maison
L'étape suivante et cruciale dans la construction d'équipements de broyage est la sélection des composants pour la construction d'une unité faite maison. Le meilleur moyen de sortir de cette situation est l'utilisation de pièces et d'appareils improvisés. Il est possible de prendre des essences de bois massif (hêtre, charme), aluminium/acier ou verre organique comme base pour des copies de bureau de machines 3D.
Pour le fonctionnement normal du complexe dans son ensemble, le développement de la conception des étriers est nécessaire. Au moment de leur mouvement, les oscillations ne sont pas inacceptables, cela entraînera un fraisage incorrect. Par conséquent, avant l'assemblage, les composants sont vérifiés pour un fonctionnement fiable.
Conseils pratiques selon le choix des composants de la fraiseuse CNC :
- guides - des barres d'acier bien polies de Ø12 mm sont utilisées. La longueur de l'axe X est d'environ 200 mm, Y - 100 mm ;
- mécanisme de soutien, matériau optimal- textolite. Les dimensions standard du chantier sont de 30×100×50 mm ;
- moteurs pas à pas - les experts en ingénierie conseillent d'utiliser des échantillons d'un périphérique d'impression 24v, 5A. Ils ont un pouvoir assez important ;
- un bloc pour fixer le corps de travail, il peut également être construit à l'aide de textolite. La configuration dépend directement de l'outil disponible.
La procédure de construction d'équipement de fraisage CNC
Après avoir terminé la sélection de tous les composants nécessaires, vous pouvez facilement construire de vos propres mains un mécanisme de fraisage surdimensionné équipé d'une CNC. Avant de procéder à la conception directe, nous vérifions à nouveau les composants, contrôlons leurs paramètres et leur fabrication. Cela contribuera en outre à éviter une défaillance prématurée de la chaîne de mécanismes.
Pour une fixation fiable des composants de l'équipement, des attaches spécialisées sont utilisées. Leur conception et leur exécution dépendent directement du futur schéma.
La liste des étapes nécessaires pour assembler un petit équipement CNC pour effectuer le processus de fraisage:
- Montage des axes de guidage de l'élément de support, fixation sur les parties extrêmes de la machine.
- Étriers de meulage. Il est nécessaire de se déplacer le long des guides jusqu'à ce qu'un mouvement fluide se forme.
- Serrage des vis pour fixer le dispositif de support.
- Fixation des composants à la base du mécanisme de travail.
- Montage des vis-mères et des accouplements.
- Installation de moteurs de marche. Ils sont fixés aux boulons d'attelage.
Les composants électroniques sont situés dans une armoire autonome. Cela garantit la minimisation des défaillances de performance lors de la réalisation d'opérations technologiques avec une fraise. Plan de montage machine de travail doit être sans gouttes, car la conception ne prévoit pas de vis de contrôle de niveau.
Après avoir terminé ce qui précède, procédez aux tests d'essai. Vous devez d'abord installer un programme léger pour effectuer le fraisage. En cours de travail, il est nécessaire de vérifier en permanence toutes les passes du corps de travail (coupe). Paramètres soumis à un contrôle constant: la profondeur et la largeur du traitement. Cela s'applique particulièrement au traitement 3D.
Ainsi, en se référant aux informations écrites ci-dessus, la fabrication d'équipements de fraisage de vos propres mains offre toute une liste d'avantages par rapport aux homologues achetés conventionnels. Premièrement, cette conception sera adaptée aux volumes et aux types de travaux attendus, deuxièmement, la maintenabilité est assurée, car elle est construite à partir de matériaux et d'accessoires improvisés, et, troisièmement, cette option d'équipement est peu coûteuse.
Ayant de l'expérience dans la conception de tels équipements, les réparations ultérieures ne prendront pas beaucoup de temps, les temps d'arrêt seront réduits au minimum. Un tel équipement peut être utile à vos voisins dans leur chalet d'été pour effectuer leur propre travaux de réparation. En louant un tel équipement, vous aiderez votre ami proche au travail, comptez sur son aide à l'avenir.
Après avoir traité les questions constructives et caractéristiques fonctionnelles fraiseuses, ainsi que la charge qui lui incombera, vous pouvez prendre en charge sa fabrication en toute sécurité, sur la base des informations pratiques fournies le long du texte. Concevez et accomplissez des tâches sans aucun problème.
Vidéo : fraiseuse à bois CNC maison.
De nos jours, la production de petites pièces en bois, pour diverses structures, devient de plus en plus fréquente. Aussi dans les magasins, vous pouvez trouver une variété de belles peintures en trois dimensions réalisé sur toile de bois. Ces opérations sont effectuées à l'aide de fraiseuses à commande numérique.La précision des pièces ou des images en bois est obtenue grâce à la commande par ordinateur, un programme spécialisé.
La défonceuse à bois à commande numérique est une machine hautement professionnelle conçue selon dernier mot La technologie.
Tout le travail consiste à traiter avec un coupe-bois spécial, qui peut être utilisé pour couper de petites pièces en bois, créer beaux dessins. Le travail est effectué en fournissant des signaux aux moteurs pas à pas, qui, à leur tour, déplacent le routeur le long de trois axes.
Pour cette raison, un traitement de haute précision se produit. En règle générale, un tel travail ne peut pas être effectué manuellement avec une qualité aussi élevée. Par conséquent, les fraiseuses à bois CNC sont une excellente trouvaille pour les menuisiers.
objectif
Depuis l'Antiquité, le fraisage était destiné aux travaux de rabotage du bois. Mais le moteur du progrès avance strictement à notre époque, la commande numérique a été créée pour de telles machines. A ce stade, la fraiseuse peut effectuer diverses actions liées à la transformation du bois :
- Découpe de diverses pièces en bois massif.
- Couper les parties excédentaires de la pièce.
- Possibilité de faire des rainures et des trous de différents diamètres.
- Dessiner des ornements complexes à l'aide d'un cutter.
- 3D Images tridimensionnelles sur bois massif.
- Complet fabrication de meubles et beaucoup plus.
Quelle que soit la tâche, elle sera effectuée avec une grande précision et exactitude.
Astuce : lorsque vous travaillez sur un équipement CNC fait maison, vous devez retirer en douceur l'épaisseur du bois, sinon votre pièce sera endommagée ou brûlée par la fraise !
Variété
Dans le monde technologique moderne, on distingue les types suivants de fraiseuses à bois CNC:
Stationnaire
Ces machines sont placées dans les industries, car elles sont énormes en taille et en poids. Mais un tel équipement est capable de fabriquer des produits en gros volumes.
Manuel
Ce sont des appareils faits maison ou des appareils à partir de kits prêts à l'emploi. Ces machines peuvent être installées en toute sécurité dans votre garage ou votre propre atelier. Ceux-ci incluent les sous-espèces suivantes:
Equipement utilisant un portique, à commande numérique
Directement, la fraise elle-même est capable de se déplacer le long de deux axes cartésiens X et Z. Ce type de machine présente une grande rigidité lors de la flexion. La conception de la fraiseuse à portique à commande numérique est assez simple dans son exécution. De nombreux charpentiers commencent leur connaissance des machines CNC à partir de ce sous-type. Cependant, dans ce cas, la taille de la pièce sera limitée par la taille du portail lui-même.
Portique à commande numérique et mobile
La construction de ce sous-type est un peu plus compliquée.
portail mobile
C'est ce type qui déplace le routeur le long des trois axes cartésiens, le long de X, Z et Y. Dans ce cas, il sera nécessaire d'utiliser un guide solide pour l'axe X, car toute la charge lourde lui sera dirigée.
Avec un portail mobile, il est très pratique pour créer des circuits imprimés. Sur l'axe Y, il est possible d'usiner des pièces longues.
La fraise se déplace le long de l'axe Z.
Machine sur laquelle la partie fraisante peut se déplacer dans le sens vertical
Ce sous-type est généralement utilisé lors du raffinage d'échantillons de production ou lors de la conversion d'équipements de forage en gravure et fraisage.
Le champ de travail, c'est-à-dire le plateau lui-même, a des dimensions de 15x15 centimètres, ce qui rend impossible le traitement de grandes pièces.
Ce type n'est pas très pratique à utiliser.
Sans portail à commande numérique
Ce type de machine est très complexe dans sa conception, mais c'est la plus productive et la plus pratique.
Les pièces peuvent être usinées jusqu'à cinq mètres de long, même si l'axe X mesure 20 centimètres.
Ce sous-type est extrêmement inadapté à la première expérience, car il nécessite des compétences sur cet équipement.
Ci-dessous, nous examinerons la conception d'une fraiseuse à bois CNC portative, nous analyserons les principes de son fonctionnement. Nous apprenons comment faire cette idée originale et comment cet équipement est ajusté.
Appareil et principe de fonctionnement
Les pièces principales du dispositif de fraisage sont les pièces suivantes :
lit
Directement la conception de la machine elle-même, sur laquelle se trouvent toutes les autres pièces.
étrier
Un nœud qui est un support pour supporter le mouvement d'un outil automatique.
Bureau
La zone où tous les travaux nécessaires sont effectués.
Arbre de broche ou toupie
Un outil qui effectue des travaux de fraisage.
Fraise pour la transformation du bois
Un outil, ou plutôt un dispositif pour une fraise, de différentes tailles et formes, à l'aide duquel le bois est traité.
CNC
Disons simplement le cerveau et le cœur de toute la structure. Le logiciel effectue un contrôle précis de tous les travaux.
Le travail est dans la gestion de programme. Un programme spécialisé est installé sur l'ordinateur, c'est elle qui convertit les circuits qui y sont chargés en codes spéciaux, que le programme distribue au contrôleur, puis aux moteurs pas à pas. Les moteurs pas à pas, à leur tour, déplacent la fraise le long des axes de coordonnées Z, Y, X, grâce auxquels le traitement de la pièce en bois a lieu.
Choix d'accessoires
L'étape principale de l'invention fait maison fraiseuse est le choix des pièces constitutives. Après tout, en choisissant un mauvais matériel, quelque chose peut mal tourner
Un exemple d'assemblage à partir d'un cadre en aluminium.
le travail lui-même. Utilise habituellement matériaux simples tels que : aluminium, bois (massif, MDF), plexiglas. Pour le fonctionnement correct et précis de l'ensemble de la structure, il est important de développer l'ensemble de la conception des étriers.
Astuce : Avant le montage fais le toi-même, il est nécessaire de vérifier la compatibilité de toutes les pièces déjà préparées.
Vérifiez s'il y a des accrocs qui interfèrent. Et surtout, pour éviter divers types de fluctuations, car cela conduirait directement à un broyage de mauvaise qualité.
Il existe certaines affectations pour la sélection des éléments de travail qui aideront à la création, à savoir :
Guides
Schéma de guides CNC pour une fraise.
Pour eux, des tiges d'un diamètre de 12 millimètres sont utilisées. Pour l'axe X, la longueur de la tige est de 200 millimètres et pour l'axe Y, la longueur est de 90 millimètres.
L'utilisation de guides permettra une installation de haute précision des pièces mobiles
étrier
Support pour fraiseuse CNC.
Assemblage des supports.
Le matériau Textolite peut être utilisé pour ces composants. Suffisant matériau résistant d'un genre. En règle générale, les dimensions du tampon textolite sont de 25x100x45 millimètres.
Bloc de verrouillage du routeur
Un exemple de cadre pour la fixation d'un routeur.
Vous pouvez également utiliser un cadre en textolite. Les dimensions dépendent directement de l'outil dont vous disposez.
Moteurs pas à pas ou servomoteurs
Source de courant
Manette
Une carte électronique qui distribue l'électricité aux moteurs pas à pas pour les déplacer le long des axes.
Astuce : lors du soudage de la carte, il est nécessaire d'utiliser des condensateurs et des résistances dans des boîtiers SMD spéciaux (l'aluminium, la céramique et le plastique sont utilisés pour fabriquer des boîtiers pour ces pièces). Cela réduira les dimensions de la planche, ainsi que l'espace interne dans la conception sera optimisé.
Assemblée
Schéma d'une machine artisanale à commande numérique
Le montage ne vous prendra pas trop de temps. La seule chose est que le processus de réglage sera le plus long de tout le processus de fabrication.
Commencer
Il est nécessaire de développer un schéma et des dessins de la future machine à commande numérique.
Si vous ne souhaitez pas le faire, vous pouvez télécharger des dessins sur Internet. Pour tous tailles préparer tous les détails nécessaires.
Faire tous les trous nécessaires
Conçu pour les roulements et les guides. L'essentiel est de respecter toutes les dimensions nécessaires, sinon le fonctionnement de la machine sera perturbé. Un schéma avec une description de l'emplacement des mécanismes est présenté. Elle vous laissera obtenir idée générale surtout si vous le collectionnez pour la première fois.
Lorsque tous les éléments et pièces du mécanisme sont prêts pour vous, vous pouvez procéder au montage en toute sécurité. La première étape consiste à assembler le cadre de l'équipement.
Cadre
Doit être géométriquement correct. Tous les coins doivent être réguliers et égaux. Lorsque le cadre est prêt, vous pouvez monter les axes de guidage, le bureau, les étriers. Lorsque ces éléments sont installés, vous pouvez installer un routeur ou une broche.
La dernière étape reste - l'électronique. L'installation de l'électronique est l'étape principale de l'assemblage. Un contrôleur est connecté aux moteurs pas à pas installés sur la machine, qui sera responsable de leur fonctionnement.
Ensuite, le contrôleur est connecté à un ordinateur sur lequel un programme de contrôle spécial doit déjà être installé. Marque largement utilisée Arduino, qui fabrique et fournit des équipements matériels.
Avec tout connecté et prêt, il est temps d'exécuter une pièce de test. Tout bois qui ne dépassera pas le bureau convient à cela. Si votre pièce a été traitée et que tout est en ordre, vous pouvez procéder à la fabrication à part entière de l'un ou l'autre produit de fraisage.
Sécurité
La sécurité avec les équipements de fraisage est la base des bases. Si vous ne prenez pas soin de vous, vous pouvez vous retrouver à l'hôpital avec des blessures graves. Toutes les règles de sécurité sont les mêmes, mais les plus élémentaires seront énumérées ci-dessous :
- Vous devez mettre votre équipement à la terre pour éviter les chocs électriques.
- Tenez les enfants éloignés de la machine.
- Ne pas manger ni boire sur le bureau.
- Les vêtements doivent être appropriés.
- Ne traitez pas de pièces volumineuses qui dépassent la taille du bureau, de l'équipement de la machine.
- Ne jetez pas divers outils sur la zone de travail de la machine.
- Ne pas utiliser de matériel (métal, plastique, etc.).
Revues vidéo
Examen vidéo des pièces de la machine et où les obtenir :
Examen vidéo de la fraiseuse à bois:
Examen vidéo de l'électronique