Fraiseuse à bois CNC de vos propres mains. Que sont les machines et appareils faits maison ? Auto-fabrication pour un atelier à domicile Dimensions machine CNC bricolage
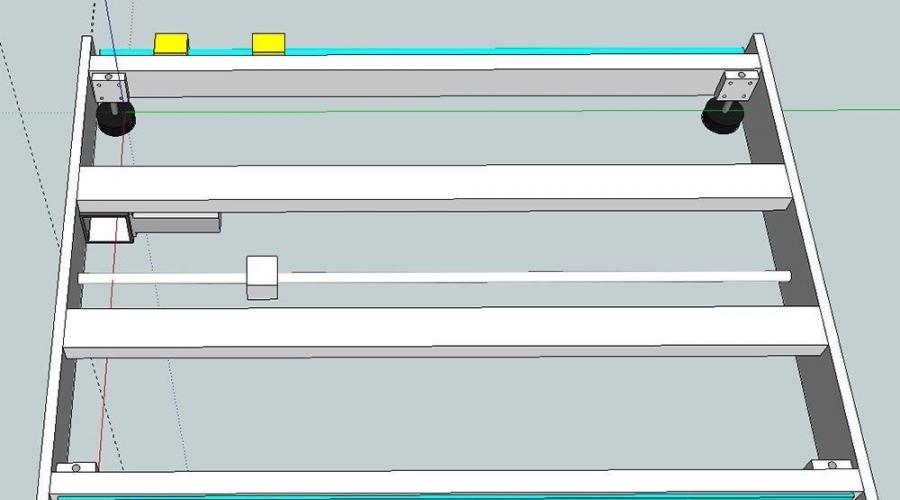
Lire aussi
Il a décrit en détail l'ensemble du processus de création d'une machine CNC pour travailler le bois et d'autres matériaux, en commençant par la conception.
1. Conception
Avant de construire une machine, vous devez au moins dessiner un croquis à la main, mais il est préférable de faire un dessin tridimensionnel plus précis à l'aide d'un programme de CAO. L'auteur du projet a utilisé google sketchup , un programme assez simple (gratuit pendant 30 jours). Pour un projet plus complexe, vous pouvez choisir Autocad.
Le but principal du dessin est de découvrir dimensions requises pièces à commander en ligne et assurez-vous que toutes les pièces mobiles de la machine s'emboîtent.
Comme vous pouvez le voir, l'auteur n'a pas utilisé de dessins détaillés avec des trous marqués pour le montage, il a décrit les trous dans le processus de construction de la machine, mais une telle conception initiale s'est avérée suffisante.
Dimensions hors tout de la machine : 1050 x 840 x 400 mm.
Course d'axe : X 730 mm, Y 650 mm, Z 150 mm
La longueur des rails et de la vis à billes dépend de la taille de la machine que vous avez en tête.
Lors de la conception d'une machine CNC, plusieurs questions se posent, dont la réponse dépend du résultat final.
Quel type de machine CNC souhaitez-vous choisir ?
Avec une table mobile ou avec un portail mobile ? Les conceptions de table coulissante sont souvent utilisées pour les machines-outils petite taille, jusqu'à 30x30 cm Ils sont plus faciles à construire, ils peuvent être rendus plus rigides que les voitures à portail mobile. L'inconvénient du déplacement de la table est qu'avec la même zone de coupe, la surface totale de la machine est deux fois plus grande que lors de l'utilisation de la conception avec un portail mobile. Dans ce projet, la zone de traitement est d'environ 65x65 cm, c'est pourquoi un portail mobile a été choisi.
Que voulez-vous traiter avec une machine CNC ?
Dans ce projet, la machine était destinée principalement au contreplaqué, bois franc bois et plastiques, ainsi que pour l'aluminium.
À partir de quoi la machine sera-t-elle construite ?
Cela dépend principalement du matériau qui sera traité sur la machine. Idéalement, le matériau utilisé pour fabriquer la machine doit être matériau plus solide, qui sera traité sur la machine ou, du moins, non moins durable. Par conséquent, si vous souhaitez couper de l'aluminium, la machine doit être construite en aluminium ou en acier.
De quelle longueur d'essieu avez-vous besoin ?
Selon l'idée originale, la machine CNC était censée traiter le contreplaqué et le MDF, qui sont produits aux Pays-Bas au format 62 x 121 cm.Par conséquent, pour Y, la distance de passage doit être d'au moins 620 mm. La longueur de déplacement le long de l'axe X est de 730 mm, car sinon la machine occuperait tout l'espace de la pièce. Par conséquent, l'axe X est plus court que la longueur de la feuille de contreplaqué (1210 mm), mais vous pouvez traiter la moitié, puis déplacer la feuille vers l'avant et traiter le reste. Avec cette astuce, il est possible d'usiner sur la machine des pièces bien plus grandes que la longueur de l'axe X. Pour l'axe Z, on a choisi 150 mm afin d'utiliser un quatrième axe à l'avenir.
Quel type de mouvement linéaire allez-vous utiliser ?
Il existe de nombreuses options pour un système de mouvement linéaire, la qualité du travail dépend en grande partie de son choix. Il est donc logique d'investir dans le meilleur système que vous pouvez vous permettre. L'auteur du projet a décidé que les rails linéaires étaient la meilleure option pour laquelle il avait assez d'argent. Si vous construisez un routeur CNC à 3 axes, vous devrez acheter un kit composé de trois ensembles de guides linéaires et de deux roulements linéaires par guide.
Quel système d'entraînement d'alimentation utiliserez-vous pour chaque essieu ?
Les principales options d'entraînement de l'alimentation sont les suivantes : courroies crantées, mécanismes à pignon et crémaillère et transmission vis-écrou. Pour les machines CNC artisanales, une transmission vis-écrou utilisant une paire de vis à billes est le plus souvent utilisée. L'écrou est fixé à la partie mobile de la machine, la vis est fixée aux deux extrémités. La vis est fixée au moteur. Si les moteurs tournent, l'écrou auquel est attachée la partie mobile de la machine se déplacera le long de la vis et mettra la machine en mouvement.
La vis à billes de cette machine est utilisée pour entraîner les axes X et Y. Les roulements à vis à billes offrent une conduite très douce, il n'y a pas de jeu et la qualité et la vitesse de coupe sont améliorées.
L'axe Z utilise une tige en acier inoxydable M10 de haute qualité avec un écrou Delrin fait maison.
Type de moteur et de contrôleur
Habituellement, les moteurs pas à pas sont utilisés dans les machines CNC maison. Les servomoteurs sont principalement utilisés pour les machines CNC industrielles de forte puissance, ils sont plus chers et nécessitent des contrôleurs plus coûteux. Des moteurs pas à pas de 3 Nm sont utilisés ici.
Type de broche
Le projet utilise un Kress d'origine et possède une belle bride de serrage de 43 mm ainsi qu'un contrôleur de vitesse intégré (mais la plupart des broches ont cette dernière caractéristique).
Si vous allez effectuer des coupes vraiment complexes, vous devez faire attention aux broches refroidies à l'eau - elles sont plus chères que les broches standard, mais elles sont beaucoup plus silencieuses, elles peuvent travailler à basse vitesse sans surchauffe et avec une variété de matériaux.
Dépenses
Cette machine CNC a coûté environ 1500 euros. Un routeur CNC pré-construit avec des spécifications similaires coûte beaucoup plus cher, vous pouvez donc économiser de l'argent en construisant le vôtre.
2. Accessoires pour créer une machine CNC
Matériel électrique et électronique :
- 3 moteurs pas à pas 3 Nm Nema 23 ;
- 3 pilotes de moteur pas à pas DM556 Leadshine ;
- Alimentation 36 V pour machines CNC ;
- carte d'interface 5 axes CNC Breakout Board pour contrôler les pilotes pas à pas ;
- Alimentation 5V pour carte d'interface;
- interrupteur à deux positions Marche/Arrêt ;
- câble toronné Blindé 4 conducteurs 18 AWG ;
- 3 interrupteurs de fin de course tactiles ;
- Broche : Kress FME 800 (également compatible Bosch Colt ou Dewalt Compact Router).
Optionnel:
- armoire/boîtier pour équipement électrique ;
- chemin de câbles en plastique mobile;
- Fiches de câble à 4 broches.
Parties mécaniques:
- guides linéaires : pour X - SBR 20 pour Y et Z - SBR 16 ;
- vis à billes (vis à billes) pour X et Y - diamètre 16 mm, pas 5 mm4
- comme vis de transmission pour l'axe Z : goupille en acier filetée M10 avec un écrou en Delrin fait maison ;
- profilé en aluminium : 30x60 mm, coupé en morceaux de 100 mm de long ;
- plaque en aluminium de 15 mm d'épaisseur;
- puissants pieds de nivellement anti-vibrations.
Programmes:
- logiciel CAO/FAO CamBam ;
- Programme de contrôle CNC Mach3
La machine est principalement construite avec des plaques en aluminium de 15 mm d'épaisseur et des profilés en aluminium de 30x60 mm. Les travaux ont été réalisés à l'aide de machines de perçage et de tournage. Les plaques et les profilés ont été commandés coupés sur mesure.
3. Axe X
Châssis de base composé de 4 pièces profilé en aluminium section 30x60 mm et deux panneaux latéraux de 15 mm d'épaisseur. À l'extrémité des profilés, il y a deux trous d'un diamètre de 6,8 mm, à l'aide d'un taraud, un filetage M8 est réalisé à l'intérieur des trous.
Filetage aux extrémités d'un profilé aluminium
Pour s'assurer que les trous sur les panneaux d'extrémité correspondent, les deux plaques ont été serrées ensemble lors du perçage. 4 trous sont percés au milieu de chaque plaque pour installer les roulements, et quatre trous supplémentaires dans l'une des plaques latérales pour le montage du moteur.
Leurs pièces en aluminium (50x50x20) formaient 4 blocs pour fixer les pattes de nivellement. Les blocs sont vissés aux profilés extérieurs avec quatre boulons M5 avec des écrous en T pour meubles.
Les guides linéaires s'adaptent directement sur les profilés en aluminium. Pour l'axe X, des rails d'un diamètre de 20 mm ont été utilisés. Les trous pré-percés dans la base des guides linéaires correspondent exactement aux rainures des profilés en aluminium. Pour l'installation, des boulons M5 et des écrous en T pour meubles ont été utilisés.
4. Plaques latérales du portail
Les plaques latérales du portail sont presque les mêmes, mais l'une d'elles comporte quatre trous supplémentaires percés pour le montage du moteur. L'ensemble du portail est constitué de plaques d'aluminium de 15 mm d'épaisseur. Pour que les trous soient exactement au bon endroit, des évidements ont été percés à des endroits soigneusement marqués avec un poinçon d'établi, et des trous ont été percés sur une perceuse le long de ces marques, d'abord avec une perceuse d'un diamètre plus petit, puis avec le nécessaire une.
En raison de la conception du portail, j'ai dû percer des trous aux extrémités des plaques latérales et faire des filetages M8 dans les trous.
5. Assemblage du portail
Portail assemblé et installé
Le reste du portail est réalisé de la même manière que les parties latérales. Le plus difficile était d'aligner correctement les rails linéaires, qui devaient s'aligner avec le bord de la plaque. Lors du marquage de l'emplacement exact des trous, j'ai pressé deux morceaux de profilés en aluminium contre les côtés de la plaque pour aligner les guides. À trous percés fileté M5. Lors de la fixation des rails au portail, assurez-vous que la distance entre les rails est la même sur toute la longueur, les rails doivent être parallèles.
Des roulements linéaires sont fixés à la paroi latérale du portail.
Plusieurs équerres donnent une rigidité supplémentaire à la structure.
La plaque au bas du portail comporte 6 trous percés pour la fixer aux plaques latérales. J'ai dû percer deux trous au milieu pour fixer le porte-écrou.
6. Chariot de l'axe Y
Le chariot de l'axe Y se compose d'une seule plaque sur laquelle sont fixés des roulements linéaires. Percer des trous était assez facile, mais une grande précision était nécessaire. Sur cette plaque sont fixés des roulements pour l'axe Y et l'axe Z. Comme les roulements linéaires sont proches les uns des autres, le moindre désalignement les fait se gripper. Le chariot doit glisser facilement d'un côté à l'autre. Les rails et les roulements doivent être ajustés. Des instruments numériques de haute précision ont été utilisés pour l'alignement. Lorsque l'écrou d'entraînement de l'axe Y a été fabriqué, deux trous supplémentaires ont dû être percés dans la plaque pour la fixer.
7. Axe Z
Les guides linéaires (rails) de l'axe Z sont fixés à la partie mobile de l'ensemble de l'axe Z. Les rails devaient être décalés de quelques millimètres du bord de la plaque. Pour les aligner, deux morceaux de plastique de l'épaisseur souhaitée ont été utilisés comme entretoises. On savait avec certitude que les bords de la plaque d'aluminium étaient parallèles, donc entre les côtés en aluminium attachés au bord de la plaque et les rails, l'auteur a inséré des morceaux de plastique, poussant les rails à la distance égale souhaitée, puis a marqué le trous, les percer et couper le filetage intérieur.
Pour monter la plaque supérieure sur l'assemblage de l'axe Z, trois trous sont percés à l'extrémité de la plaque de montage. Il n'était pas possible de fixer le moteur pas à pas directement sur la plaque, j'ai donc dû fabriquer un support en plastique séparé pour le moteur (voir point 12).
Deux blocs de logements de roulements sont fabriqués dans le même plastique. La vis d'entraînement est une tige en acier avec un filetage M10. La poulie de courroie de distribution est percée, filetée M10 et simplement boulonnée au sommet de la vis d'entraînement. Il est maintenu en place par trois vis de réglage. L'écrou d'entraînement Delrin se fixe au chariot de l'axe Y.
L'écrou d'entraînement Delrin se fixe au chariot de l'axe Y.
Le support de broche a été commandé à l'avance et possède une bague de serrage de 43 mm qui s'adapte au Kress utilisé dans le projet.
Si vous souhaitez utiliser une broche refroidie à l'eau, elle est souvent livrée avec un support prêt à l'emploi. Vous pouvez également acheter les supports séparément si vous souhaitez utiliser un boîtier Dewalt ou Bosch, ou les imprimer en 3D.
8. Courroies et poulies de distribution
Souvent, les moteurs sont montés à l'extérieur de la machine ou sur un support séparé. Dans ce cas, les moteurs peuvent être connectés directement à la vis à billes à l'aide d'un accouplement élastique. Mais, comme la machine est située dans une petite pièce, les moteurs sortis à l'extérieur interféreraient.
C'est pourquoi les moteurs sont placés à l'intérieur de la voiture. Il n'était pas possible de connecter directement les moteurs aux vis à billes, il a donc fallu utiliser des courroies de distribution et des poulies HTD5m de 9 mm de large.
Lorsque vous utilisez un entraînement par courroie, vous pouvez utiliser un réducteur pour connecter le moteur à la vis d'entraînement, ce qui vous permet d'utiliser des moteurs plus petits et d'obtenir toujours le même couple mais une vitesse plus lente. Comme les moteurs ont été choisis assez gros, il n'était pas nécessaire de rétrograder pour obtenir plus de puissance.
9. Supports moteur
Les supports moteur sont fabriqués à partir de tubes en aluminium de section carrée coupés à longueur sur commande. Vous pouvez également prendre un tube en acier et en découper des morceaux carrés. Les supports de moteur pour les axes X et Y doivent pouvoir coulisser vers l'intérieur et vers l'extérieur pour tendre les courroies de distribution. Des fentes ont été faites sur un tour et un grand trou a été percé sur un côté du support, mais vous pouvez également le faire sur une perceuse à colonne.
Un grand trou sur un côté de la monture a été scié avec une scie à bout. Cela permet au moteur de s'asseoir au ras du sol et maintient également l'arbre centré. Le moteur est monté avec des boulons M5. Il y a quatre fentes de l'autre côté du support pour que le moteur puisse glisser d'avant en arrière.
10. Blocs de roulement
Les blocs de support pour les axes X et Y sont en barre d'aluminium de 50 mm section ronde- quatre morceaux de 15 mm d'épaisseur chacun en ont été découpés. Après avoir marqué et percé quatre trous de montage, un grand trou est percé au centre de la pièce. Ensuite, une cavité pour les roulements a été réalisée. Les roulements doivent être enfoncés et les blocs boulonnés aux plaques d'extrémité et latérales.
11. Support pour écrou d'entraînement dans l'axe Z
Au lieu d'une vis à billes pour l'axe Z, j'ai utilisé une tige filetée M10 et un écrou fait maison à partir d'un morceau de Delrin. Le polyformaldéhyde Delrin est bien adapté à cet usage car il est autolubrifiant et ne s'use pas avec le temps. Si vous utilisez un taraud de bonne qualité pour le filetage, le jeu sera minime.
12. Supports pour écrous d'entraînement le long des axes X et Y
Pour les axes X et Y, le support d'entraînement est en aluminium. Les écrous à vis à billes ont deux petites brides avec trois trous de chaque côté. Un trou de chaque côté est utilisé pour fixer l'écrou au support. Le support est usiné sur un tour avec une grande précision. Une fois que vous avez fixé les écrous au portique et au chariot de l'axe Y, vous pouvez essayer de déplacer ces pièces d'un côté à l'autre en tournant les vis à billes à la main. Si les dimensions des supports sont incorrectes, l'écrou se bloquera.
Montage sur l'axe Y.
13. Support moteur axe Z
Le support moteur de l'axe Z est différent du reste. Il est découpé dans de l'acrylique de 12 mm. La tension de la courroie peut être ajustée en desserrant les deux boulons en haut et en faisant glisser l'ensemble du support moteur. Pour le moment, le support en acrylique fonctionne très bien, mais à l'avenir, on pense le remplacer par un support en aluminium, car lorsque la courroie est tendue, la plaque en acrylique se plie légèrement.
14. Plan de travail
Une table en aluminium avec des rainures en T serait préférable, mais c'est cher. L'auteur du projet a décidé d'utiliser un plateau de table perforé car il s'intègre dans le budget et offre de nombreuses options pour serrer la pièce.
La table est fabriquée à partir d'un morceau de contreplaqué de bouleau de 18 mm d'épaisseur et fixée, avec des boulons M5 et des écrous à rainure en T, à des profilés en aluminium. 150 écrous hexagonaux M8 ont été achetés. À l'aide du programme CAO, une grille a été dessinée avec des découpes hexagonales pour ces écrous. Ensuite, la machine CNC a découpé tous ces trous pour les écrous.
Un morceau de MDF de 25 mm d'épaisseur a été installé sur un morceau de contreplaqué de bouleau. Il s'agit d'une surface remplaçable. Un grand couteau de forme a été utilisé pour percer des trous dans les deux parties. Les trous dans le MDF sont alignés exactement avec le centre des trous hexagonaux découpés précédemment. Ensuite, un morceau de MDF a été retiré et tous les écrous ont été installés dans les trous du contreplaqué. Les trous étaient légèrement plus petits que les écrous, de sorte que les écrous y étaient martelés. Une fois terminé, le MDF est retourné à sa place.
La surface de la table est parallèle aux axes X et Y et est complètement plane.
15. Électronique
Les composants suivants ont été utilisés :
- Alimentation principale avec tension de sortie 48V DC et courant de sortie 6.6A;
- 3 pilotes de moteur pas à pas Leadshine M542 V2.0 ;
- 3 moteurs pas à pas 3Nm hybrides Nema 23 ;
- Tableau d'interface;
- relais - 4-32V CC, 25A/230 V CA;
- interrupteur principal;
- alimentation pour carte d'interface 5V DC;
- alimentation pour ventilateurs de refroidissement 12V DC;
- 2 ventilateurs Cooler Master Sleeve Bearing 80mm;
- 2 prises - pour broche et aspirateur ;
- bouton d'arrêt d'urgence et interrupteurs de fin de course (pas encore installés).
Si vous ne voulez pas dépenser beaucoup d'argent pour acheter du matériel séparément, vous pouvez l'acheter en un seul lot. Avant de commander, vous devez réfléchir à la taille des moteurs pas à pas dont vous avez besoin. Si vous construisez une petite machine pour couper du bois et du plastique, les moteurs pas à pas Nema 23, 1,9 Nm vous donneront suffisamment de puissance. Des moteurs de 3Nm sont choisis ici car la machine elle-même est assez grande et lourde, et l'usinage de matériaux comme l'aluminium était également prévu.
Pour les petits moteurs, vous pouvez charger trois moteurs, mais il est préférable d'utiliser des pilotes séparés. Les pilotes personnalisés de Leadshine sont micro-pas pour obtenir une douceur maximale et réduire les vibrations du moteur pas à pas. Les pilotes de ce projet peuvent gérer un maximum de 4,2 A et jusqu'à 125 micropas.
Une source de tension de 5 V CC est connectée à l'entrée d'alimentation principale. Les ventilateurs ont une prise électrique à l'intérieur de l'armoire, ils utilisent donc un adaptateur mural standard de 12 volts pour les alimenter. L'alimentation principale est allumée et éteinte avec un grand interrupteur.
Le relais 25A est contrôlé par un ordinateur via un disjoncteur. Les bornes d'entrée du relais sont connectées aux bornes de sortie du disjoncteur. Le relais est connecté à deux prises électriques, qui alimentent le Kress et l'aspirateur à copeaux. Lorsque le code G se termine par une commande M05, l'aspirateur et la broche s'éteignent automatiquement. Pour les activer, vous pouvez appuyer sur F5 ou utiliser la commande M03 G-code.
16. Armoire électronique
Pour l'équipement électrique, vous avez besoin d'un bon casier. L'auteur a dessiné des tailles et des emplacements approximatifs pour tous les composants sur une feuille de papier, en essayant de les disposer de manière à ce que toutes les bornes soient facilement accessibles lors de la connexion des fils. Il est également important qu'il y ait un flux d'air suffisant à travers l'armoire, car les contrôleurs pas à pas peuvent devenir très chauds.
De par leur conception, tous les câbles doivent avoir été connectés à l'arrière du boîtier. Des connecteurs spéciaux à 4 fils ont été utilisés afin qu'il soit possible de déconnecter l'électronique de la machine sans déconnecter aucune des bornes de fil. Deux prises ont été fournies pour alimenter la broche et l'aspirateur. Les prises de courant sont connectées à un relais pour allumer et éteindre automatiquement la broche par les commandes Mach3. Il aurait dû y avoir un gros interrupteur sur le devant du casier.
Les détails de l'armoire sont découpés sur la machine CNC elle-même
De plus, après une disposition approximative des pièces, les pièces de la coque ont été conçues dans le programme CAO. Ensuite, sur la machine elle-même, déjà assemblée, tous les côtés et la base sont découpés. Au-dessus de l'armoire se trouve un couvercle, avec un morceau de plexiglas au milieu. Après l'assemblage, tous les composants ont été installés à l'intérieur.
17. Logiciel
Mach3
Trois types de logiciels sont nécessaires pour contrôler une machine CNC.
- Programme de CAO pour créer des dessins.
- Programme CAM pour créer des trajectoires d'outils et une sortie de code G.
- Et un programme de contrôleur qui lit le code G et contrôle le routeur.
Ce projet utilise un programme CamBam simple. Il possède des fonctions de CAO de base et convient à la plupart des projets de bricolage. En même temps, c'est un programme CAM. Avant que CamBam puisse créer des chemins, quelques paramètres doivent être définis. Des exemples de paramètres sont le diamètre de l'outil utilisé, la profondeur de coupe, la profondeur par passe, la vitesse de coupe, etc. Après avoir créé le parcours d'outil, vous pouvez générer un code G qui indique à la machine quoi faire.
Dessin créé dans CamBam
Mach3 est utilisé pour le logiciel du contrôleur. Mach3 envoie des signaux via le port parallèle de l'ordinateur à la carte d'interface. Mach3 commande le zéro de l'outil de coupe et lance les programmes de coupe. Vous pouvez également l'utiliser pour contrôler la vitesse de la broche et la vitesse de coupe. Mach3 dispose de plusieurs assistants intégrés que vous pouvez utiliser pour générer des fichiers G-code simples.
Parcours d'outil créé par CamBam
18. Utilisation de la machine
Les premiers ont été fabriqués plusieurs pinces pour fixer les matériaux traités à la table de travail. Et le premier "gros" projet était l'armoire électronique (item 15).
Comme premiers échantillons, plusieurs divers types engrenages, boîtes pour médiators.
collecteur de poussière
Il s'est avéré que la machine CNC produit beaucoup de poussière et fait beaucoup de bruit. Pour résoudre le problème de la poussière, un dépoussiéreur a été fabriqué, auquel un aspirateur peut être fixé.
Routeur CNC 3 axes
Machine utilisateur SorenS7 .
Sans routeur CNC, de nombreux projets resteront non réalisés. L'auteur est arrivé à la conclusion que toutes les machines moins chères que 2000 euros ne peuvent pas donner la taille de la surface de travail et la précision dont il a besoin.
Ce qu'il fallait :
- zone de travail 900 x 400 x 120 mm ;
- broche relativement silencieuse, garantissant une puissance élevée à basse vitesse;
- dureté, autant que possible (pour le traitement pièces en aluminium);
- haut degré de précision;
- Interface USB;
- coûte moins de 2000 euros.
Ces exigences ont été prises en compte dans la conception 3D. L'attention principale a été accordée à l'emboîtement de toutes les pièces.
En conséquence, il a été décidé de construire un routeur avec un cadre profilé en aluminium, des vis à billes de 15 mm et des moteurs pas à pas NEMA 23, avec un courant de travail de 3A, parfaitement adaptés au système de montage fini.
Toutes les pièces s'adaptent parfaitement et il n'est pas nécessaire de fabriquer des pièces spéciales supplémentaires.
1. Fabrication du cadre
L'axe X a été assemblé en quelques minutes.
Les guides linéaires de la série HRC sont de très haute qualité, et immédiatement après l'installation, il est clair qu'ils fonctionneront parfaitement.
Puis le premier problème est survenu : les vis d'entraînement ne rentraient pas dans les roulements. Par conséquent, il a été décidé de refroidir les vis avec de la neige carbonique afin de réduire les dimensions.
2. Installation des vis d'entraînement
Une fois les extrémités des vis refroidies avec de la glace, elles s'intègrent parfaitement dans les supports.
3 : Électrique
L'assemblage de la partie mécanique est terminé, c'est maintenant au tour des composants électriques.
Étant donné que l'auteur connaissait bien Arduino et souhaitait fournir un contrôle total sur l'USB, le choix s'est porté sur Arduino Uno avec carte d'extension CNC Shield et pilotes de moteur pas à pas DRV8825. L'installation n'a pas été difficile du tout, et après avoir défini les paramètres, la machine a commencé à être contrôlée à partir d'un PC.
Mais comme le DRV8825 fonctionne principalement à 1,9 A et 36 V (et devient très chaud), un saut de pas se produit en raison d'une trop grande batterie faible. Un broyage long à des températures élevées ne se passerait guère bien.
Ensuite, il y avait des pilotes Tb6560 bon marché branchés sur une carte d'extension. La tension nominale s'est avérée pas trop adaptée à cette carte. Une tentative a été faite pour utiliser une alimentation 36V.
En conséquence, deux pilotes fonctionnent normalement, le troisième ne peut pas supporter une tension plus élevée et fait tourner le rotor du moteur pas à pas dans une seule direction.
J'ai encore dû changer de pilote.
Bien approché tbV6600. Il est presque entièrement recouvert d'un radiateur en aluminium et est facile à installer. Désormais, les moteurs pas à pas sur les axes X et Y fonctionnent avec un courant de 2,2 A et sur l'axe Z avec 2,7 A.
Il était nécessaire de protéger l'alimentation des moteurs pas à pas et le convertisseur de fréquence des petites puces en aluminium. Il existe de nombreuses solutions lorsque le transducteur est sorti assez loin de la fraiseuse. Le principal problème est que ces appareils génèrent beaucoup de chaleur et nécessitent refroidissement actif. Une solution originale a été trouvée : utiliser des morceaux de collants de 30 cm de long comme manchon de protection, bon marché et gai, et qui assure une circulation d'air suffisante.
4. Broche
Choisir la bonne broche n'est pas facile. L'idée originale était d'utiliser une broche Kress1050 standard, mais elle n'a que 1050 watts à 21000 tr/min, donc je ne m'attendais pas à beaucoup de puissance à des vitesses inférieures.
Le fraisage à sec de pièces en aluminium et en acier nécessite 6 000 à 12 000 tr/min. Une broche VFD de trois kilowatts avec un onduleur a été achetée, avec une livraison depuis la Chine, elle a coûté 335 euros.
C'est une broche assez puissante et facile à installer. Il est lourd - poids 9 kg, mais un cadre solide peut supporter son poids.
5. Assemblage terminé
La machine fait du bon boulot, j'ai dû bricoler les drivers du moteur pas à pas, mais en général le résultat est satisfaisant. Dépensé 1500 euros et construit une machine qui répond exactement aux besoins du créateur.
Le premier projet de fraisage était une encoche façonnée en POM.
6 : Finition pour le fraisage de l'aluminium
Déjà lors du traitement du POM, il était clair que le couple sur le support Y est trop important et que la machine se plie sous des charges élevées le long de l'axe Y. L'auteur a donc acheté un deuxième guide et mis à niveau le portail en conséquence.
Après cela, tout est revenu à la normale. Coût de réalisation 120 euros.
Maintenant, vous pouvez fraiser l'aluminium. L'alliage AlMg4.5Mn a donné de très bons résultats sans aucun refroidissement.
7. Conclusions
Pour créer votre propre machine CNC, vous n'avez pas besoin d'avoir sept travées dans le front, tout est entre nos mains.
Si tout est bien planifié, il n'est pas nécessaire d'avoir un tas de matériel et conditions idéales pour travailler, vous n'avez besoin que d'une certaine somme d'argent, d'un tournevis, d'une pince et d'une perceuse.
Il a fallu un mois pour développer la conception à l'aide du programme de CAO et pour commander et acheter des composants, quatre mois pour l'assemblage. La création de la deuxième machine aurait pris beaucoup moins de temps, car l'auteur n'avait aucune expérience dans le domaine des machines-outils, et il a dû en apprendre beaucoup sur la mécanique et l'électronique.
8. Accessoires
Électrique:
Toutes les pièces électriques sont achetées sur ebay.
- Arduino GRBL + CNC Shield : environ 20 euros
- Pilote de moteur pas à pas : 12 euros par pièce.
- Alimentation : 40 euros
- Moteurs pas à pas : environ 20 euros la pièce
- Broche + inverseur : 335 euros
Mécanique:
Roulements linéaires ARC 15 FN
Une photo: www.dold-mechatronics.de
Guidages linéaires AR/HR 15 - ZUSCHNITT
Une photo: www.dold-mechatronics.de
Vis à billes SFU1605-DM :
- 2x 1052mm
- 1x 600mm
- 1x 250mm
Une photo: www.dold-mechatronics.de
Support de roulement à vis à billes FLB20-3200 avec support de moteur NEMA23 :
Une photo: www.dold-mechatronics.de
Support de vis à billes LLB20
Une photo: www.dold-mechatronics.de
Accouplements moteur pas à pas-broche : provenance de Chine à 2,5 euros la pièce.
Cadre:
Profils de base 160x16 Écrou type I 8
Une photo: www.dold-mechatronics.de
Profils pour axe X 30x60 B-Type Nut 8
Une photo: www.dold-mechatronics.de
Profils de montage pas à pas axe Y 30x60 Écrou type B 8
Une photo: www.dold-mechatronics.de
Portail:
Profil 30x60 B-Type Écrou 8 pour roulement linéaire axe X 100 mm
Plaque arrière : plaque en aluminium de 5 mm d'épaisseur, 600x200.
Profil 30x60x60 B-Type Écrou 8 pour Y : 2 pcs.
Une photo: www.dold-mechatronics.de
Profil 30x30 B-Type Écrou 8
pour Z :
Plaque de montage - plaque aluminium épaisseur 5 mm, dimensions 250x160
Plaque coulissante pour montage broche - plaque aluminium épaisseur 5 mm, dimensions 200x160
9. Programme
Après une longue recherche d'une solution logicielle, le programme pratique Estlcam a été choisi, avec un coût de licence de 50 euros. La version d'essai du programme possède toutes les fonctionnalités de la version sous licence, mais est plus lente.
Ce logiciel est capable de reprogrammer l'Arduino et possède de nombreuses fonctionnalités, dont la possibilité de contrôler directement les moteurs pas à pas.
Exemple : Pour trouver le bord d'une pièce, vous devez connecter les fils aux contacts du micro-ordinateur Arduino et à la pièce. Si la pièce n'est pas conductrice, vous pouvez créer un revêtement conducteur temporaire à l'aide d'une feuille.
Après cela, le programme amène l'outil à la pièce de différents côtés et détermine ses limites au moment du contact.
10. Mise à niveau
Des supports en plastique temporaires ont été installés sur les axes Y et Z. Le plastique était assez solide, mais les agrafes pouvaient encore se casser. Par conséquent, l'auteur a fraisé des supports en aluminium pour les remplacer. Le résultat est montré sur la photo.
11. Machine en fonctionnement
Après un peu de pratique, la machine donne déjà de très bons résultats, pour du fait maison.
Ces photos montrent une pièce en alliage AlMg4.5Mn. Il est entièrement fraisé. Sur la deuxième photo - le résultat de la machine, sans autre traitement par d'autres moyens.
Une fraise VHM de 6 mm à 3 dents a été utilisée. Lors de l'utilisation de fraises de 4 et 6 mm, la machine obtient des résultats assez corrects. Pour sa classe d'équipement, bien sûr.
Table CNC
Pour le dessert - pas une machine, mais utile et intéressant fait maison pour la machine, à savoir un cadre solide et spacieux avec des étagères. Si vous n'avez pas encore de machine CNC, vous pouvez la construire plus tôt et l'utiliser comme établi.
Evan et Caitlin, propriétaires du site EvanAndKatelyn.com , a mis à jour sa table CNC avec fonctionnalité et espace.
Le produit a été entièrement assemblé sur des raccords à vis, sans l'utilisation de colle, afin de préserver la possibilité d'une modification et d'une mise à niveau faciles.
Outils et accessoires d'occasion :
- bouton d'arrêt ;
- Porte-rouleau ;
- Fraise et mèches ;
- Perceuse;
- Visseuse électrique;
- Vu;
- Machine X-Carve;
- Fraise en carbure 1/4 po ;
- Fraise à pointe sphérique à 4 canaux en carbure de 1/4 de pouce ;
- Protection auditive.
Étape 1 : préparation
La première étape consiste à tout retirer de l'ancienne table, en commençant par la machine et en terminant par un tas d'autres choses qui s'y trouvent, et à la démonter partiellement. Tout a été entièrement démonté, à l'exception de deux grandes étagères de 120 x 120 cm, qui ont été renforcées, constituant la base d'une nouvelle table.
Étape 2 : renforcer les étagères
Des supports d'angle ont été utilisés aux quatre coins intérieurs et des supports en L le long de la traverse qui longe le dessous.
Sur la photo ci-dessous: une comparaison d'une étagère renforcée avec une étagère inachevée.
Étape 3 : coupez l'excédent
A l'origine il y avait 4 casiers s'élevant au dessus du dessus de la table car une étagère supplémentaire était prévue au dessus de la machine. Cette idée a été rejetée, décidant de laisser deux racks sur quatre.
Ils ont été renforcés par des cornières.
Une étagère a été placée dessus et renforcée avec plus de supports.
Essai de force.
Étape 4 : Pegboard - Barre d'outils
Le meuble mis à jour devait ajouter autant d'espace de stockage que possible, et l'un des détails qui élargissait ses possibilités était un panneau perforé, dans les trous duquel des porte-outils sont fixés. Coupez les coins du panneau avec une scie sauteuse.
Étape 5 : Étagères inférieures
Pour le rangement en partie basse, il fallait laisser le plus de place possible, car. une scie à table et une meuleuse à tambour y sont entreposées. Il y avait aussi un besoin de beaucoup d'espace pour stocker les matériaux, il a donc été décidé d'ajouter une étagère, mais de la rendre facile à retirer. Des barres de bois préparées pour les pieds et une feuille de contreplaqué se sont avérées utiles.
Les pieds ont été fixés à la feuille de contreplaqué avec des équerres d'angle, l'étagère résultante a été insérée dans partie inférieure. Il est facile à retirer lorsqu'un stockage pleine hauteur est à nouveau nécessaire.
Étape 6 : Étagères du haut
L'ancien cadre avait une étagère supérieure pour un ordinateur travaillant avec la machine et pour diverses petites choses. Il restait encore de la place, et sous cette étagère ils décidèrent d'en faire une autre. Il a également aidé à couvrir les prises et le câblage de la machine.
L'étagère supérieure a été placée sur les extrémités des racks et vissée.
Dans la deuxième étagère, les coins des jambes ont été coupés avec une scie sauteuse.
Et aussi fixé avec des coins.
Étape 7 : finitions
Un panneau avec l'inscription "Appelez-moi" a été vissé à l'extrémité, qui sera plus tard remplacé par un nom inventé par les abonnés de YouTube.
Enfin, tout ce qui était dans son prédécesseur a été remis sur la table.
Il existe de nombreux projets impressionnants de machines artisanales, souvent les auteurs étonnent par leurs compétences et leurs solutions pleines d'esprit. Comme un passe-temps auto-assemblage Une machine CNC ou une imprimante 3D est supérieure à de nombreux autres passe-temps - à la fois en termes d'utilité du résultat, car de nombreuses choses merveilleuses peuvent être faites sur la machine, et en termes d'avantages du processus lui-même - ce n'est pas seulement passionnant, mais aussi activité cognitive pour aider à développer des compétences en ingénierie.
Nous ne répertorions pas les modèles individuels, car ils sont nombreux, et pour tous les buts, objectifs et conditions d'installation et de fonctionnement existantes, l'équipement doit être sélectionné individuellement, avec lequel des experts vous aideront. Contactez-nous!
Nous vous enverrons le matériel par e-mail
Avec un bon équipement, des processus technologiques complexes deviennent disponibles. Des équipements spécialisés à entraînement électrique simplifient grandement le traitement des ébauches de bois. Mais son acquisition est associée à des investissements importants. Pour résoudre ce problème avec succès, vous devez étudier attentivement les matériaux de cet article. Voici comment créer des machines à bois fonctionnelles pour votre atelier à domicile.
Certains échantillons d'équipements faits maison en termes de caractéristiques de consommation ne sont pas pires que les produits d'usine
Avant de passer directement aux équipements techniques, quelques remarques générales doivent être faites sur la salle spécialisée concernée :
- C'est pratique lorsque l'atelier est situé dans un bâtiment séparé. Cela implique un espace suffisant, l'absence de soucis inutiles, la possibilité d'un équipement complet et d'autres systèmes d'ingénierie.
- Si la chambre est en , ou Rez-de-chaussée, il doit être bien isolé de la zone résidentielle.
- La superficie d'un atelier standard ne doit pas être inférieure à 6-7 m². Hauteur - suffisante pour le libre passage et le niveau maximum de l'outil surélevé (à partir de 2,5 m et plus).
- Des systèmes de ventilation, de chauffage et d'éclairage de haute qualité seront utiles ici. Chaque système d'ingénierie doit être considéré séparément pour éviter des coûts excessifs pendant l'exploitation.
- Assurez-vous qu'il y a suffisamment de puissance électrique pour toutes les machines à bois pour l'atelier à domicile.
Noter! Si l'équipement comporte des composants électroniques, des disjoncteurs spéciaux seront utiles pour éviter les dommages causés par les surtensions, terre de protection. Il est nécessaire de s'assurer que les paramètres du réseau correspondent aux caractéristiques des unités de puissance (220 V, monophasé ; 380 V, triphasé).
L'utilisation d'une telle source réduira la fatigue et aidera à maintenir une bonne vision. Il est préférable d'installer un luminaire à DEL. Il ne chauffe pas l'espace environnant comme une lampe à incandescence conventionnelle. Contrairement à l'analogue à décharge gazeuse, il est difficile de l'endommager par action mécanique.
Machines à bois pour l'atelier à domicile et montages spéciaux: définitions de base, techniques de fabrication
- Chaque machine est conçue pour effectuer un ensemble limité d'opérations de travail avec des pièces de certaines tailles.
- En règle générale, les équipements spécialisés sont plus pratiques à utiliser que les modèles universels.
- Il sera plus facile de fabriquer une machine à bois de vos propres mains si vous dressez d'abord une liste exacte des exigences relatives à ses caractéristiques. Une puissance excessive n'est pas nécessaire. Le couple requis peut être fourni à l'aide d'une boîte de vitesses.
- De même, en réglant le mécanisme de transmission approprié, modifiez la vitesse de rotation de l'arbre de travail. Pour un traitement plus précis, un réglage en douceur est utile. paramètre donné sur une large gamme.
- Pour réduire les coûts, vous pouvez utiliser une perceuse à moteur électrique avec un corps cassé dans la conception et d'autres pièces de travail d'un équipement défectueux.
- Les composants mécaniques et électroniques les plus complexes devront être achetés séparément. Les coûts de reproduction de certaines technologies à domicile dépassent le coût des produits finis.
- La durée de vie des équipements à entraînement électrique sera augmentée s'ils sont protégés contre les charges excessives. En particulier, il est utile de s'équiper d'un équipement automatique qui coupe l'alimentation lorsque le moteur surchauffe.
Important! Les questions de sécurité ne doivent pas être négligées. Les poulies motrices sont recouvertes de carters. Des feuilles de plastique transparent sont installées devant les outils de travail.
Pour utilisation rationnelle l'espace libre, les étagères murales et de plafond, les étagères, les crochets et les supports spéciaux seront utiles. Le site d'installation exact des respectifs est choisi en tenant compte des particularités des processus technologiques, de l'emplacement des machines et des établis.
Article associé:
Notre examen vous aidera à choisir et à fabriquer des machines et des accessoires faits maison pour votre atelier à domicile, ainsi qu'à comprendre la technologie de leur fabrication.
Création d'un tour à bois pour un atelier à domicile
Les données techniques des produits respectifs, ainsi que les descriptions, peuvent être consultées sur Internet.
La partie principale est le cadre (1). D'autres parties du produit y sont attachées. Il fournit non seulement l'intégrité du cadre d'alimentation, mais également une bonne stabilité en surface. La machine de menuiserie est conçue pour traiter des pièces relativement légères, cette pièce peut donc être fabriquée à partir de bois dur.
Dans la partie centrale, il y a un pied à coulisse avec un support pour coupeur à main(2). Au lieu de cela, un support pour la fixation rigide de l'instrument peut être installé. La pièce est fixée entre les poupées avant (3) et arrière (4). Il est entraîné en rotation par un moteur électrique (6). Pour modifier le couple sur l'axe dans cette conception, un entraînement par courroie et une poulie (5) sont utilisés. L'étrier et la poupée mobile se déplacent horizontalement le long d'un arbre spécial (7), qui est installé à l'intérieur du châssis.
Important! Ces dessins peuvent être utilisés pour fabriquer une machine existante. Veuillez noter que toutes les dimensions ici sont en pouces.
Ce projet peut être utilisé pour fabriquer un tour à bois à faire soi-même. Il suffit de le compléter avec un appareil spécial, conçu pour créer systématiquement des produits identiques.
Pour le fixer au bon endroit, vous devez créer un support spécial. À cet exemple Du contreplaqué de 10 mm a été utilisé, à partir duquel une plate-forme de dimensions 480 × 180 mm a été découpée. Les dimensions données peuvent être modifiées en tenant compte des paramètres réels. Des trous dans le contreplaqué sont découpés de manière à ce que les boulons de fixation et les outils les traversent. Pour une fixation rigide le long du contour du site, des barres de bois sont fixées avec des vis.
Cette conception attire avec simplicité, accessibilité parties constitutives, prix raisonnable. Mais il y a quelques inconvénients à noter :
- Vous devrez utiliser vos deux mains pour déplacer le couteau. Cela est nécessaire pour générer une force suffisante et éviter les blocages.
- Le rayon minimum le long duquel les plis des pièces seront créés est limité par le diamètre de l'outil (fraise).
- Pour traiter les blancs de différentes races arbre nécessite un réglage précis de la vitesse de l'arbre, et dans cet exemple cette possibilité n'est pas prévue.
Cet exemple explique que même une conception qui a été testée par le temps et l'expérience pratique peut être améliorée grâce à une étude approfondie de l'équipement et du processus technologique.
Tour à bois fait maison à faire soi-même: vidéo avec instructions et commentaires de l'auteur du projet
Comment faire un tour à bois fait maison bon marché de vos propres mains
Avec l'aide de ce kit de menuiserie DIY, il ne sera pas difficile de le réaliser. Un tel lit peut être fixé sur une base en bois ou en métal. Les paramètres exacts de la poupée sont sélectionnés en tenant compte des dimensions et des sièges des supports de moteur. Les paramètres de puissance du moteur électrique seront plus que suffisants. Pour les équipements de menuiserie de ce type, une puissance de 250 à 300 kW suffit, si elle est transférée à l'arbre à l'aide d'une boîte de vitesses (poulie).
Le dernier exemple doit être étudié plus en détail. En choisissant le bon outil à entraînement électrique, vous pouvez obtenir la puissance et la vitesse de rotation nécessaires. Un mandrin standard est utile pour un serrage fiable et rapide de la pièce. Dans la technologie moderne de ce type, une protection contre la surchauffe, la pénétration de poussière dans le boîtier est assurée. Des commutateurs de haute qualité, une isolation efficace sont installés ici. Ce dessin suffit à lui seul pour comprendre comment fabriquer soi-même un tour.
Fabrication de fraises pour un tour à bois à partir de matériaux improvisés
Les limes, scies, clés et autres articles en acier à outils feront l'affaire. Il est plus facile de traiter des pièces de forme carrée (en coupe). Vous devez vous assurer qu'il n'y a pas de fissures ou d'autres défauts qui réduisent la résistance. Pour une fixation rigide des fraises traversantes, la machine doit être équipée d'un support spécial.
Composants importants pour une scie circulaire stationnaire DIY
Dans cet équipement, la table remplit les fonctions les plus importantes, ses paramètres doivent donc être étudiés avec attention particulière. Il est installé avec des mécanismes d'entraînement, des éléments du circuit de puissance et de commande. Il doit être dimensionné pour le poids des composants intégrés et des pièces de bois. Il ne faut pas oublier que pendant le fonctionnement, il y aura des charges statiques et dynamiques, des vibrations.
Lors de la spécification des paramètres de la machine, les facteurs suivants doivent être pris en compte :
- Pour cet équipement, la puissance du bloc d'alimentation doit être d'au moins 0,85 kW.
- Lors du calcul de la conception, il est nécessaire de vérifier la hauteur du bord saillant du disque. Il déterminera la profondeur de coupe maximale.
- La vitesse minimale de rotation de l'arbre de travail est limitée à 1,5 mille tours par minute. Il est souhaitable de l'augmenter pour que lors de l'exécution des opérations de travail, la couleur de la découpe en bois ne change pas.
Description d'une scie circulaire peu coûteuse d'une meuleuse de vos propres mains
Comme dans l'exemple précédent, lors de la création d'une telle machine, vous pouvez simplifier la solution du problème à l'aide d'outils électriques standard.
L'entraînement avec le disque de coupe est fixé sur la bascule rotative. Pour faciliter l'effort physique - installez un ressort ou un contrepoids. Le mouvement de l'outil n'est autorisé que dans le sens vertical le long d'un arc. Cette conception est mobile. Il peut être installé à l'intérieur et à l'extérieur sur un socle adapté. Si nécessaire, le broyeur peut être démonté. Il est fixé avec des éléments de raccordement vissés sur un joint amortisseur en bois (caoutchouc).
Lit de bricolage pour meuleuse d'angle: dessins, vidéos, algorithme de fabrication de pièces individuelles et assemblage:
Avantages et processus de création d'une simple fraiseuse à bois pour un atelier à domicile
Cet équipement est utilisé pour couper des rainures selon des dimensions données et un forage précis à différents angles. Avec lui, vous pouvez rapidement supprimer un quart, créer un évidement dans une pièce d'une certaine forme. Même sans explication détaillée, il est clair que de telles opportunités seront utiles au propriétaire d'une maison privée. Il reste à comprendre comment fabriquer une fraiseuse à bois maison. Une telle solution sera-t-elle économiquement viable ou est-il plus rentable d'acheter des équipements fabriqués en usine ?
Les réponses aux questions posées pourront être données après une étude détaillée des structures concernées.
Dans la partie centrale de la table, une unité d'alimentation est installée qui fait tourner la fraise. À l'aide de pinces et d'autres dispositifs, la pièce est fixée dans la position souhaitée et déplacée le long d'une trajectoire donnée. Tel lieu de travailéquipé d'un système d'aspiration des poussières.
Pour éliminer les erreurs lors de la mise en œuvre du projet, faites attention aux paramètres individuels des éléments structurels:
- Une table pour effectuer des opérations de travail est créée dans une version stationnaire. Ses dimensions et sa capacité de charge seront déterminées en tenant compte des caractéristiques des échantillons traités.
- Les experts recommandent d'installer des régulateurs à vis dans les parties inférieures des supports. Avec leur aide, vous pouvez établir la position horizontale exacte de la structure, même sur des surfaces inégales.
- Le châssis de puissance peut être assemblé à partir de tubes d'acier(profils rectangulaires). Pour la fabrication de plans de travail, un panneau de particules de haute qualité et assez épais convient. Une fine feuille de métal vibrera, ce qui dégradera la précision du traitement.
- Si vous choisissez un moteur d'une puissance de 500 à 900 W, les capacités de la fraise ne suffiront qu'à éliminer les couches minces, créant des dépressions relativement petites.
- Lors de l'installation d'un bloc d'alimentation de 900 à 1900 W, des opérations plus complexes sont autorisées. Cependant, certaines difficultés sont acceptables lors du traitement des ébauches de bois dur.
- Dans les machines puissantes (plus de 2000 W), vous pouvez installer des fraises de tout type. Un tel équipement appartient au niveau professionnel. Il est conçu pour un fonctionnement à long terme sans surchauffe du moteur.
- Pour la fabrication d'une plaque de montage à travers laquelle le moteur est fixé au plateau, vous pouvez utiliser une feuille de fibre de verre, de métal.
- Pour assurer une bonne visibilité dans la zone de travail, un rétroéclairage est monté au-dessus de la table.
Le tableau suivant fournit des informations sur le coût d'une fraiseuse à bois manuelle sur le marché intérieur.
Marque/modèle, photo | Puissance, W | Maxi- faible vitesse de rotation de la broche | Prix, frotter. | Remarques |
---|---|---|---|---|
![]() PROMA/SF-40 | 1500 | 24000 | 17500-18900 | Il est destiné à la création de rainures, pliage, fraisage. |
![]() Encore/Corvette-82 | 1500 | 2400 | 14200-15900 | Éléments de design distinctifs : accent type de coin avec une échelle qui simplifie le traitement sous un certain angle ; supports latéraux pour le maintien de grandes pièces. |
![]() Proxxon/ MT 400 | 100 | 25000 | 14200-15700 | Modèle léger et compact avec moteur de faible puissance. Conçu pour le traitement de petites pièces de bois tendre. |
![]() PROMA/TFS-120 | 5500 | 9000 | 175000-183000 | Matériel de niveau professionnel. Il est connecté à un réseau triphasé 380 V. Convient pour équiper les entreprises spécialisées dans le travail du bois. |
![]() X-CUT/ XC-3040 | 800 | 24000 | 188000-196000 | Machine compacte à commande numérique (CNC). Pour le confort de la gestion, il est équipé du panneau portable. Le téléchargement de nouveaux programmes à partir d'un ordinateur est autorisé à l'aide d'un "lecteur flash". |
La faisabilité de la mise en œuvre d'un projet de fraiseuse CNC à faire soi-même
L'utilisation du contrôle de programme vous permet de créer de grandes séries de pièces avec une grande précision, d'effectuer un traitement unique et particulièrement soigné. Pour démarrer un nouveau processus technologique, il suffit de télécharger un nouveau programme et de cliquer sur le bouton "Démarrer". Les tâches simples et complexes seront effectuées automatiquement par la fraiseuse à bois, sans intervention ni contrôle de l'utilisateur. Cette technique élimine les erreurs de l'opérateur et garantit la meilleure qualité.
Les avantages de cette classe d'équipements sont évidents. Il reste à savoir s'il est possible de créer une machine CNC pour le bois de vos propres mains. Voici les caractéristiques de cette classe d'équipement:
- Il faudra s'assurer de la possibilité de déplacer la fraise horizontalement dans toutes les directions. Cela nécessitera non seulement une conception appropriée des supports, mais également des moteurs électriques supplémentaires.
- Le positionnement précis de l'outil est assuré à l'aide de capteurs, de moteurs pas à pas.
- Ça prendra Logiciel, qui contrôlera le mouvement de la fraise, effectuera des fonctions de contrôle.
Important! Même s'il y a Description détaillée et les dessins d'une fraiseuse CNC pour le bois de vos propres mains seront très difficiles à réaliser.
Comment fabriquer ses propres fraises pour les machines à bois
Pour créer des produits silencieux, vous aurez besoin d'ébauches en acier à outils durable, résistant aux températures élevées et aux fortes contraintes mécaniques. Les perceuses, les raccords et les tiges endommagés feront l'affaire. La forme requise peut être créée à l'aide d'un disque diamanté installé dans une rectifieuse. L'affûtage des bords est effectué à un angle de 7 à 10 degrés. Trop étroit partie travaillante sera rapidement endommagé même lors du traitement du bois tendre.
Dessins et recommandations pour la création d'une machine à raboter à faire soi-même
La reproduction de haute qualité de ce type de traitement nécessite des efforts considérables. Par conséquent, il est recommandé d'utiliser moteur électrique triphasé d'une puissance de 5 kW ou plus avec une vitesse de rotor maximale de 4,5 mille tr/min.
L'arbre (1) avec un ou plusieurs couteaux est entraîné en rotation par un moteur électrique (4), deux poulies et une courroie. Pour presser et déplacer la pièce, des rouleaux (2, 3) et un entraînement manuel avec un mécanisme à chaîne sont installés ici. Le design est assemblé sur un cadre solide composé de coins en acier.
En tenant compte des préférences personnelles, il n'est pas difficile de préparer des dessins d'épaisseur à faire soi-même. Pour corriger les caractéristiques techniques, le volume des travaux futurs, les paramètres des ébauches et la taille de la pièce sont pris en compte.
Fabriquer une jauge d'épaisseur fonctionnelle à partir d'une raboteuse électrique de vos propres mains
Vous pouvez fabriquer rapidement et à peu de frais une machine basée sur un outil électrique standard.
L'image montre que l'outil électrique est fixé au-dessus de la pièce dans un cadre spécial. Ils offrent la possibilité de le déplacer dans les directions longitudinale et transversale en conservant strictement l'angle de 90° entre eux. Une raboteuse moderne est équipée d'une prise spéciale pour connecter un aspirateur. Par conséquent, il n'y aura pas de problèmes avec l'élimination des déchets.
La technologie de création d'une rectifieuse pour le bois de vos propres mains
Cet équipement remplit ses fonctions à l'aide d'arbres rigides et de toiles souples avec un abrasif appliqué sur la surface, des brosses et d'autres outils spéciaux.
Pour la fabrication d'équipements de niveau domestique, il est recommandé d'en choisir un relativement simple. Il peut être créé indépendamment après avoir déterminé la longueur requise, en tenant compte de l'emplacement exact des rouleaux de support. L'algorithme suivant est appliqué :
- La largeur du ruban est réglée de 15 à 25 cm.
- Les bandes sont découpées dans un grain de papier de verre approprié.
- Ils sont collés bout à bout sur une base souple en matériau dense, sans grandes coutures.
- Empêchez le patinage de la bande en augmentant de quelques millimètres le diamètre des galets de support dans la partie centrale. Il est également utile d'installer une couche de caoutchouc dessus.
Article
Sachant qu'une fraiseuse CNC est considérée comme un équipement technique et électronique sophistiqué, de nombreux artisans pensent qu'elle ne peut tout simplement pas être réalisée à la main.
Cependant, cette opinion n'est pas vraie: vous pouvez fabriquer un tel appareil de vos propres mains, mais pour cela, vous devez disposer non seulement de son dessin complet, mais également d'un ensemble de certains outils et composants appropriés.
Machine CNC DIY (dessins)
Décider de créer un fait maison machine spéciale CNC, rappelez-vous que cela peut prendre beaucoup de temps. De plus, vous aurez besoin de beaucoup d'argent.
Pour fabriquer une fraiseuse équipée d'un système CNC, vous pouvez utiliser 2 méthodes: acheter un ensemble prêt à l'emploi de pièces spécialement sélectionnées à partir desquelles un tel équipement est assemblé, ou trouver tous les composants et assembler indépendamment un appareil qui répond pleinement à tous vos exigences.
Préparation au travail
Si vous envisagez de fabriquer vous-même une machine CNC sans utiliser de kit prêt à l'emploi, la première chose à faire est de vous arrêter à régime spécial, sur lequel un tel mini-appareil fonctionnera.

Assemblage d'équipement
La base de l'équipement de fraisage assemblé peut être une poutre rectangulaire, qui doit être fermement fixée sur les rails.
La structure portante de l'équipement doit avoir une grande rigidité. Lors de son installation, il est préférable de ne pas utiliser de joints soudés, mais de fixer toutes les pièces uniquement avec des vis.
Dans l'équipement de fraisage que vous assemblerez vous-même, un mécanisme doit être fourni qui garantira que le dispositif de travail se déplace dans le sens vertical. Il est préférable de prendre pour cela un engrenage à vis dont la rotation sera transmise à l'aide d'une courroie crantée.
La partie principale de la machine
Une partie importante d'une telle machine est son axe vertical, qui, pour un appareil fait maison, peut être fabriqué à partir d'une plaque d'aluminium. Se souvenir de les dimensions d'un tel axe étaient précisément adaptées aux dimensions de l'appareil en cours de création.
Difficile à fabriquer, en plus des composants techniques, il dispose d'un dispositif électronique, qui ne peut être installé que par un spécialiste. Contrairement à cette opinion, la possibilité d'assembler une machine CNC de vos propres mains est excellente si vous préparez à l'avance les dessins, schémas et composants nécessaires.
Réalisation de travaux préparatoires
Lors de la conception d'une CNC de vos propres mains à la maison, vous devez décider selon quel schéma cela fonctionnera.
Souvent, un appareil d'occasion est pris comme base d'un futur appareil.
La perceuse peut être utilisée comme base pour une machine CNC
Cela nécessitera le remplacement de la tête de travail par une tête de fraisage.
La plus grande difficulté à concevoir une machine CNC de vos propres mains est la création d'un dispositif avec lequel l'outil de travail se déplace dans trois plans.
Résoudre partiellement le problème aidera les chariots provenant d'une imprimante conventionnelle. L'outil pourra se déplacer dans les deux plans. Il est préférable de choisir des chariots pour une machine CNC à partir d'une imprimante de grandes dimensions.
Un tel schéma vous permet de vous connecter ultérieurement au contrôle de la machine. L'inconvénient est que la fraiseuse CNC ne fonctionne qu'avec du bois, des produits en plastique, métal mince. Cela est dû au fait que les chariots de l'imprimante n'ont pas la rigidité nécessaire.
Il faut faire attention au moteur de la future unité. Son rôle se réduit au déplacement de l'outil de travail. La qualité du travail et la possibilité d'effectuer des opérations de fraisage en dépendent.
Une bonne option pour un routeur CNC fait maison est un moteur pas à pas.
Une alternative à un tel moteur est un moteur électrique, préalablement amélioré et ajusté aux normes de l'appareil.
Toute personne utilisant un moteur pas à pas vous permet de ne pas utiliser de vis, cela n'affecte en rien les capacités d'une telle CNC à bois. Il est recommandé d'utiliser des courroies crantées pour le fraisage sur une telle unité. Contrairement aux courroies standard, elles ne glissent pas sur les poulies.
Il est nécessaire de concevoir correctement la fraise de la future machine, pour cela, vous aurez besoin de dessins détaillés.
Matériaux et outils nécessaires au montage
L'ensemble général de matériaux pour une machine CNC comprend:
- câble de 14 à 19 m de long ;
- transformation du bois;
- mandrin de coupe;
- un convertisseur de fréquence ayant la même puissance que la broche ;
- roulements;
- tableau de contrôle;
- pompe à eau;
- tuyau de refroidissement ;
- trois moteurs pas à pas pour trois axes de mouvement de la structure ;
- boulons;
- câble de protection ;
- des vis;
- contreplaqué, aggloméré, dalle de bois ou structure métallique au choix comme corps du futur appareil;
- embrayage souple.
Il est recommandé d'utiliser une broche avec du liquide de refroidissement lors de la fabrication de vos propres mains. Cela vous permettra de ne pas l'éteindre toutes les 10 minutes pour refroidir. Une machine CNC faite maison convient au travail, sa puissance est d'au moins 1,2 kW. La meilleure option sera un appareil d'une puissance de 2 kW.
L'ensemble d'outils nécessaires à la fabrication de l'unité comprend:
- marteaux;
- ruban électrique;
- clés d'assemblage;
- colle;
- Tournevis
- fer à souder, mastic;
- broyeur, il est souvent remplacé par une scie à métaux;
- pinces, machine à souder, ciseaux, pinces.
Une simple machine CNC de bricolage
Procédure de montage de la machine
La fraiseuse CNC maison est assemblée selon le schéma:
- production de dessins et schémas de l'appareil indiquant le système électrique ;
- achat de matériel contenant une future machine CNC artisanale;
- l'installation d'un lit, de moteurs, d'une surface de travail, d'un portail, d'une broche y sera montée;
- installation de portail ;
- réglage de l'axe Z ;
- fixer la surface de travail;
- installation de broche ;
- installation d'un système de refroidissement par eau;
- installation du système électrique;
- connexion de la carte, avec son aide, l'appareil est contrôlé;
- configuration du logiciel ;
- démarrage de l'unité.
La base du lit est un matériau en aluminium.
Le cadre doit être en aluminium
Les profils de ce métal sont sélectionnés avec une section de 41 * 81 mm avec une épaisseur de plaque de 11 mm. Le corps du lit lui-même est relié à l'aide de coins en aluminium.
L'installation du portail déterminera l'épaisseur du produit pouvant être traité par la machine CNC. Surtout si c'est fait main. Plus le portail est haut, plus le produit qu'il peut traiter est épais. Il est important de ne pas l'installer trop haut, car cette conception sera moins durable et moins fiable. Le portail se déplace selon l'axe X et porte la broche sur lui-même.
Un profilé en aluminium est utilisé comme matériau pour la surface de travail de l'unité. Prenez souvent un profil avec des rainures en T. Pour un usage domestique, ils acceptent, son épaisseur est d'au moins 17 mm.
Une fois le cadre de l'appareil prêt, procédez à l'installation de la broche. Il est important de l'installer verticalement, car à l'avenir, il devra être ajusté, cela est fait pour fixer l'angle requis.
Pour installer le système électrique, la présence des composants suivants est requise :
- Unité de puissance;
- un ordinateur;
- moteur pas à pas ;
- Payer;
- bouton d'arrêt ;
- conducteurs de moteurs.
Le système nécessite un port LPT. De plus, il est installé qui contrôle le fonctionnement de l'appareil et vous permet de répondre à la question de savoir comment effectuer telle ou telle opération. La commande est reliée par des moteurs à la fraiseuse elle-même.
Une fois l'électronique installée sur la machine, vous devrez télécharger les pilotes et les programmes nécessaires au fonctionnement.
Erreurs de construction courantes
Une erreur courante lors de l'assemblage d'une machine CNC est l'absence de dessin, mais l'assemblage est effectué en fonction de celui-ci. En conséquence, il y a des omissions dans la conception et l'installation des structures de l'appareil.
Souvent, le mauvais fonctionnement de la machine est associé à un convertisseur de fréquence et à une broche mal sélectionnés.
Pour le bon fonctionnement de la machine, il est nécessaire de choisir la bonne broche
Dans de nombreux cas, les moteurs pas à pas ne reçoivent pas la puissance appropriée, une alimentation spéciale séparée doit donc être sélectionnée pour eux.
Il faut garder à l'esprit qu'un schéma de câblage et un logiciel correctement installés vous permettent d'effectuer de nombreuses opérations sur l'appareil. différents niveaux des difficultés. La machine CNC à faire soi-même peut être réalisée par un maître de niveau intermédiaire, la conception de l'unité présente un certain nombre de caractéristiques, mais en utilisant les dessins, il n'est pas difficile d'assembler les pièces.
Il est facile de travailler avec une CNC, compilée de vos propres mains, vous devez étudier la base informative, effectuer une série de travaux de formation et analyser l'état de l'unité et des pièces. Ne vous précipitez pas, ne tirez pas sur les pièces mobiles et n'ouvrez pas la CNC.
Pour faire un dessin en trois dimensions sur surface en bois ceux d'usine sont utilisés. Il est difficile de créer un mini-modèle similaire de vos propres mains à la maison, mais c'est possible avec une étude détaillée de la conception. Pour ce faire, vous devez comprendre les spécificités, choisir les bons composants et les configurer.
Le principe de fonctionnement de la fraiseuse
L'équipement de travail du bois moderne avec une unité de commande numérique est conçu pour former un motif complexe sur le bois. La conception doit contenir une partie électronique mécanique. Ensemble, ils automatiseront le processus de travail autant que possible.
Pour fabriquer un mini routeur à bois de bureau de vos propres mains, vous devez vous familiariser avec les principaux composants. L'élément de coupe est une fraise installée dans une broche située sur l'arbre du moteur. Cette conception est attachée au lit. Il peut se déplacer le long de deux axes de coordonnées - x ; y. Pour fixer la pièce, il est nécessaire de réaliser une table de support.
L'unité de commande électronique est connectée à moteurs pas à pas. Ils assurent le déplacement du chariot par rapport à la pièce. Grâce à cette technologie, vous pouvez réaliser des dessins 3D sur une surface en bois.
La séquence de fonctionnement du mini-équipement avec CNC, que vous pouvez fabriquer vous-même.
- Rédaction d'un programme selon lequel la séquence de mouvements de la pièce coupante sera effectuée. Pour ce faire, il est préférable d'utiliser des systèmes logiciels spéciaux conçus pour être adaptés à des modèles faits maison.
- Pose de la pièce sur la table.
- Sortie du programme vers la CNC.
- Mise sous tension des équipements, suivi de la mise en place des actions automatiques.
Pour obtenir une automatisation maximale du travail en mode 3D, vous devrez établir correctement un schéma et sélectionner les composants appropriés. Les experts recommandent d'étudier les modèles d'usine avant de fabriquer un mini.
Pour créer des motifs et des motifs complexes sur une surface en bois, vous aurez besoin de plusieurs types de fraises. Certains d'entre eux peuvent être faits vous-même, mais pour un travail soigné, vous devriez en acheter d'usine.
Schéma d'une fraiseuse artisanale à commande numérique
L'étape la plus difficile est le choix du schéma de fabrication optimal. Cela dépend des dimensions de la pièce et du degré de son traitement. Pour un usage domestique, il est souhaitable de fabriquer une mini fraiseuse CNC de bureau à faire soi-même qui aura le nombre optimal de fonctions.
La meilleure option consiste à créer deux chariots qui se déplaceront le long des axes de coordonnées x ; y. Il est préférable d'utiliser des barres d'acier rectifiées comme base. Des chariots y seront montés. Pour créer une transmission, des moteurs pas à pas et des vis à roulements sont nécessaires.
Pour une automatisation maximale du processus dans une construction en bois à faire soi-même, il est nécessaire de réfléchir en détail à la partie électronique. Classiquement, il se compose des composants suivants :
- Unité de puissance. Il est nécessaire d'alimenter en électricité les moteurs pas à pas et la puce du contrôleur. Utilisez souvent le modèle 12v 3A;
- manette. Il est conçu pour donner des commandes aux moteurs électriques. Pour le fonctionnement d'une mini fraiseuse CNC à faire soi-même, un simple circuit suffit pour contrôler le fonctionnement de trois moteurs;
- chauffeur. C'est aussi un élément de régulation du fonctionnement de la partie mobile de la structure.
L'avantage de ce complexe est la possibilité d'importer des fichiers exécutables des formats les plus courants. À l'aide d'une application spéciale, vous pouvez créer un dessin en trois dimensions d'une pièce pour analyse préliminaire. Les moteurs pas à pas fonctionneront à un certain taux de course. Mais pour cela, des paramètres techniques doivent être entrés dans le programme de contrôle.
Choix d'accessoires pour fraiseuse CNC
L'étape suivante consiste à sélectionner des composants pour l'assemblage d'équipements faits maison. La meilleure option est d'utiliser des moyens improvisés. Comme base pour les modèles de bureau d'une machine 3D, vous pouvez utiliser du bois, de l'aluminium ou du plexiglas.
Pour bon fonctionnement de l'ensemble du complexe, il est nécessaire de développer la conception des étriers. Pendant leur mouvement, il ne doit y avoir aucune vibration, cela peut entraîner un fraisage imprécis. Par conséquent, avant l'assemblage, tous les composants sont vérifiés pour la compatibilité les uns avec les autres.
- guides. Des barres d'acier polies d'un diamètre de 12 mm sont utilisées. La longueur pour l'axe x est de 200 mm, pour l'axe y elle est de 90 mm ;
- étrier. Textolite est la meilleure option. La taille habituelle de la plate-forme est de 25*100*45 mm ;
- moteurs pas à pas. Les experts recommandent d'utiliser des modèles d'une imprimante 24v, 5A. Contrairement aux lecteurs de disque, ils ont plus de puissance ;
- bloc de coupe. Il peut également être fabriqué à partir de textolite. La configuration dépend directement de l'outil disponible.
L'alimentation est mieux assemblée en usine. Dans l'auto-fabrication, des erreurs sont possibles, ce qui affecte par la suite le fonctionnement de tous les équipements.
La procédure de fabrication d'une fraiseuse CNC
Après avoir sélectionné tous les composants, vous pouvez créer vous-même une mini fraiseuse de bureau de vos propres mains. Tous les éléments sont à nouveau vérifiés au préalable, leurs dimensions et leur qualité sont vérifiées.
Pour fixer les éléments de l'équipement, il est nécessaire d'utiliser des attaches spéciales. Leur configuration et leur forme dépendent du schéma choisi.
La procédure d'assemblage d'un mini équipement CNC de bureau pour le bois avec une fonction de traitement 3D.
- Installation de guides d'étrier, leur fixation sur les parties latérales de la structure. Ces blocs ne sont pas encore installés sur la base.
- Rodage des étriers. Ils doivent être déplacés le long des guides jusqu'à ce qu'une conduite en douceur soit obtenue.
- Serrer les boulons pour fixer les étriers.
- Fixation des composants à la base de l'équipement.
- Installation de vis-mères avec accouplements.
- Installation de moteurs d'entraînement. Ils sont fixés aux vis d'accouplement.
La partie électronique est située dans un bloc séparé. Cela permet de réduire le risque de dysfonctionnement lors du fonctionnement du routeur. Un autre point important est le choix d'une surface de travail pour l'installation d'équipements. Il doit être de niveau, car les boulons de réglage de niveau ne sont pas prévus dans la conception.
Après cela, vous pouvez commencer les tests d'essai. Il est recommandé de configurer d'abord un programme de fraisage du bois simple. Pendant le fonctionnement, il est nécessaire de vérifier chaque passe de coupe - la profondeur et la largeur de traitement, en particulier en mode 3D.
La vidéo montre un exemple d'assemblage d'une grande fraiseuse CNC à faire soi-même: