Arbre liquide à faire soi-même - nous créons du bois-plastique à la maison. Démoulage et finition
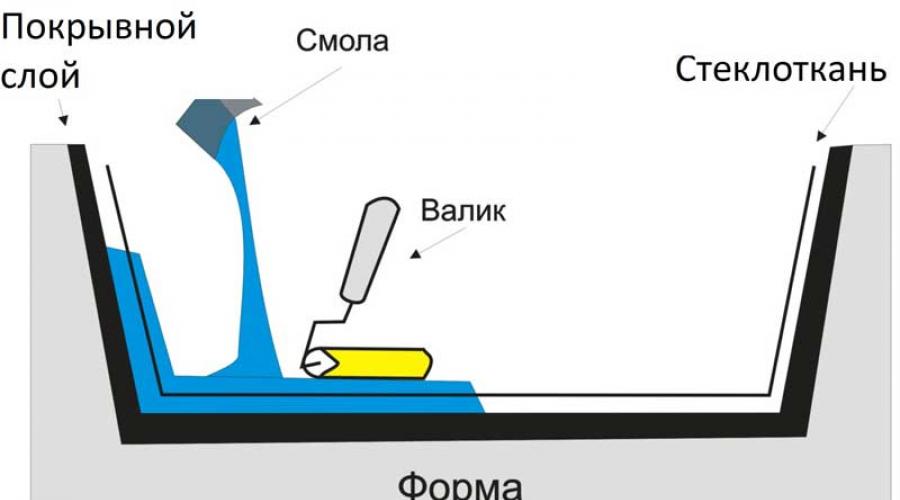
Lire aussi
Conçu pour la production de pièces simples utilisées pour les besoins domestiques et d'éléments de machines et de mécanismes complexes. Particulièrement résistant et matériau léger utilisé pour la fabrication de coques de yachts, kit carrosserie pour voitures et motos, peaux d'avions.
La fibre de verre se compose d'un élément de renforcement, la fibre de verre, et d'une charge, la résine polymère. La fibre de verre est une collection de fibres ordonnées de manière spéciale, imprégné une résine époxy . Selon l'épaisseur, le matériau peut avoir un poids mètre carré de 300 à 900 grammes.
Méthode de moulage à la main
En moderne production industrielle diverses technologies de fabrication de fibre de verre sont utilisées.
Pour créer des pièces en fibre de verre de vos propres mains, la méthode la plus appropriée est le moulage manuel. La technologie de production ne prévoit pas l'utilisation d'équipements complexes et de matériaux coûteux.
Afin de fabriquer de la fibre de verre de vos propres mains par moulage à la main, vous devez effectuer séquentiellement prochaines étapesœuvres:
- choix des matériaux;
- couper la fibre de verre;
- création d'une couche séparatrice dans la matrice ;
- création d'une couche de couverture;
- pose de fibre de verre dans la matrice;
- appliquer une composition polymère ;
- répétition des deux étapes précédentes quantité requise fois (en fonction de l'épaisseur du produit);
- séchage du produit;
- retirer le produit du moule;
- traitement final (si nécessaire).
La principale caractéristique de la méthode de moulage à la main est haut degré dépendances de qualité pièce finie sur le niveau de compétence de l'interprète. Afin d'obtenir l'image la plus complète de la fabrication de bricolage, vous devez considérer chacune des étapes en détail.
Sélection des matériaux
Le type de matériau de matrice est adopté en fonction du nombre de pièces produites en série. Pour un moulage unique, la matrice peut être en gypse. Si plus d'un millier d'échantillons sont nécessaires, une matrice en acier est commandée. À la maison, la matrice est souvent un moulage du modèle original. Il est plus pratique de faire une impression également à partir de fibre de verre en utilisant la technologie décrite ci-dessus.
Le choix du type de fibre de verre dépend des exigences de résistance et des caractéristiques esthétiques du produit fini. Un tissu à grain fin donnera à la surface un aspect lisse et brillant, tandis que l'utilisation d'un tissu en fibre de verre grossier fournira une résistance élevée.
La composition de la résine polymère est également déterminée en fonction de l'objectif et des conditions de fonctionnement de la pièce. La charge polymère est responsable de tels Caractéristiques fibre de verre comme:
- couleur du produit ;
- degré de résistance à l'eau;
- Plage de température de fonctionnement ;
- sensibilité à l'influence des réactifs chimiques et des environnements;
- sensibilité au rayonnement ultraviolet;
- le niveau de fragilité, de douceur, de résistance aux chocs du produit.
Préparation de la fibre de verre
La découpe de la fibre de verre est réalisée selon un gabarit en carton épais selon la taille de la matrice. Si le produit a une forme complexe, il est permis, à titre exceptionnel, d'utiliser une découpe de tissu de verre constituée de plusieurs éléments distincts.
En fonction de l'épaisseur de la pièce est préparée le nombre requis de couches de matériau, qui sont stockés dans un endroit pratique et facilement accessible, dans l'ordre de leur moulage dans la matrice. Si une pause de plusieurs jours est prévue entre les processus de découpe du tissu de verre et de moulage des produits, il est nécessaire de respecter strictement les conditions de stockage du matériau.
Couche de séparation
La couche de séparation appliquée à la surface du moule à matrice sert à assurer le retrait en toute sécurité du produit fini après qu'il ait gagné en résistance. En tant que matériau à partir duquel la couche de séparation est fabriquée, un gel ou une cire automatique est souvent utilisé.
Couche de couverture
La résine époxy ou polyester est utilisée pour la pose des couches supérieures et suivantes de fibre de verre. Les composants sont mélangés et infusés selon les réglementations technologiques du fabricant. La composition préparée doit être utilisée dans les 15 minutes, et donc, pour chaque couche suivante, la résine est préparée à nouveau.
La couche supérieure est la première couche placée dans la matrice et, en même temps, la couche supérieure protectrice du produit. Son épaisseur ne doit pas dépasser 0,4 mm afin d'éviter les fissures lors du processus de séchage. Le processus de séchage de la couche supérieure dure jusqu'à ce qu'elle se transforme en une masse collante gélatineuse.
Pose de fibre de verre et imprégnation de résine
Après avoir atteint la consistance requise de la couche supérieure, la découpe de fibre de verre est posée sous la forme d'une matrice. La première couche de fibre de verre est la plus fine (300 g/m2), ce qui assure la surface la plus lisse du produit.
La fibre de verre doit répéter exactement toutes les courbures de la forme de la matrice sans délaminage ni formation de poches d'air.
Après la pose, une couche de résine polymère est appliquée sur la fibre de verre et la forme obtenue est roulée avec un rouleau spécial afin de mieux imprégner et extruder les bulles d'air. La couche suivante de fibre de verre est posée sans attendre que la résine sèche. Ensuite, le processus de préparation et d'application de la composition polymère est répété.
Selon l'épaisseur et la résistance requise du produit, un nombre différent de couches de fibre de verre et d'imprégnation est moulé. Comme dernière couche, un feutre de verre ou une fine toile de verre de finition est utilisée.
Démoulage et finition
Il est nécessaire de retirer le produit de la matrice après que le matériau a gagné en résistance afin d'éviter sa déformation et son délaminage. À conditions normales le temps de séchage de la fibre de verre est de 12 à 24 heures. Ce temps peut être réduit en réchauffant la matrice émetteur infrarouge, ou en le plaçant dans une chambre de séchage.
La finition comprend le rognage et le ponçage des bords du produit.
Si nécessaire, le produit peut être peint dans la couleur souhaitée avec de la peinture sur la base. Les matériaux finis peuvent être collés ensemble à l'aide d'adhésifs polymères.
Règles d'exécution du travail
Pour obtenir produits en fibre de verre de qualité lors de l'exécution des travaux, les éléments suivants doivent être pris en compte:
- les surfaces de la matrice et des récipients pour la préparation de la résine polymère doivent être propres ;
- les bulles d'air qui n'ont pas pu être expulsées avec un rouleau doivent être éliminées avec une coupe avec une lame;
- les outils utilisés (rouleaux, pinceaux), ainsi que les récipients pour mélanger les composants, doivent être lavés à l'acétone immédiatement après utilisation pour éliminer les résidus de résine ;
- la température dans la salle de travail ne doit pas être inférieure à 20 degrés pour se conformer à bonne technologie processus de polymérisation de résine;
- les composants en polymère peuvent dégager des vapeurs toxiques, le travail doit donc être effectué dans un endroit bien ventilé ;
- des gants doivent être utilisés pour protéger les mains;
- Il est interdit de fumer et d'utiliser des sources de flammes nues dans la chambre.
Il explique bien comment fabriquer de la fibre de verre de vos propres mains dans la vidéo ci-dessous. A titre d'exemple, l'auteur de la vidéo fabrique des "cils" pour les phares de voiture.
Malheureusement, le plastique connu de nous tous et si répandu dans le monde entier contient des substances nocives pour la santé humaine. De plus, des produits pétroliers sont utilisés dans sa production. Cependant, jusqu'à récemment, il n'y avait pratiquement pas d'alternative à ce matériau bon marché. Bien sûr, nouveaux matériaux de construction apparaissent constamment. Ce sont le contreplaqué, les panneaux de particules et les panneaux de fibres. Il y a aussi des nouveautés dans l'industrie du béton, la métallurgie et l'industrie du verre. Néanmoins, en termes de coût, et donc d'accessibilité, ils sont encore loin du plastique.
Au début du nouveau millénaire, les scientifiques ont réussi à créer un matériau structurel fondamentalement nouveau qui, dans les décennies à venir, pourra presque complètement remplacer le plastique habituel. ce en composite bois-polymère thermoplastique(DPKT ou DPK), et chez les gens ordinaires - "arbre liquide". Dans sa production, des matières premières primaires (secondaires) PP, PE ou PVC sont utilisées, ainsi que des additifs de bois (farine de bois, autres fibres végétales) et des additifs auxiliaires. L'effet a dépassé toutes les attentes. Dernier matériel non seulement respectueux de l'environnement (teneur en soufre réduite de 90%), mais aussi, associant meilleures propriétés le bois et le plastique, ont maintenu le coût relativement bas.
Selon les experts, la croissance annuelle des ventes de WPC dans le monde est d'environ 20 %. Quel est donc ce miracle que les architectes, les designers et les ouvriers de production attendent depuis si longtemps ? Essayons de comprendre.
Demande et traitement
En raison de ses propriétés, le composite bois-polymère est parfaitement utilisé dans une grande variété de domaines. Les matériaux se distinguent par l'uniformité et la douceur de la surface, la plasticité, la résistance aux influences atmosphériques et biologiques, et la durée de vie même dans des conditions extérieures difficiles atteint 50 ans.
Tout cela permet d'utiliser WPC dans la production de divers matériaux architecturaux et de construction : plinthes, panneaux muraux, appuis de fenêtre, profilés, éléments décoratifs ainsi que des charges.
Fabriqué à partir de WPC et de produits prêts à l'emploi : stratifié, revêtements de sol, tôles de meubles, meubles, boîtes à câbles, profilés de fenêtres à plusieurs chambres et même platelage - un profilé pour la fabrication de piliers et de piliers.
Les propriétés physiques et mécaniques du composite bois-polymère offrent de nombreuses opportunités pour sa transformation. Matériel ne perd pas sa forme et sa force, prenant en soi jusqu'à 4% d'humidité. Des objets légers et creux peuvent en être fabriqués. Il est monté à la fois à l'aide de clous et de vis, et sur des loquets spéciaux.
Et pourtant, WPC peut être plaqué avec du placage, laminé avec des films et des feuilles de plastique, peint avec toutes les peintures et vernis, obtenir divers effets décoratifs en ajoutant des pigments à la composition, etc.
Les produits obtenus à partir de WPC sont facilement usinés. Ils sont facilement sciés, percés, coupés, collés, soudés les uns aux autres, pliés (après préchauffage au chalumeau), et si la farine de roches tendres du bois ou des déchets contenant de la cellulose, cela confère au produit une plasticité également accrue.
Enfin, le WPC, en plus de l'esthétique que lui confère apparence, agréable à sentir, avec une légère odeur boisée.
Technologie de production
Un certain nombre de composants sont utilisés pour fabriquer un composite bois-polymère. Tout d'abord, il s'agit bien sûr de bois broyé ou de matières premières contenant de la cellulose. Autrement dit, il peut s'agir non seulement de bois, mais aussi de maïs, de riz, de soja, de paille, de papier, de sciure de bois, etc. Le deuxième composant principal du WPC est les liants synthétiques. Ceux-ci incluent: polyéthylène, PVC propylène, etc. Les composants restants sont des additifs supplémentaires dont la composition varie en fonction de la destination du futur produit. Les plus courants comprennent : les colorants, les pigments, les antioxydants, les modificateurs de choc, les stabilisants à la lumière et à la chaleur, les retardateurs de flamme et les antiseptiques pour protéger contre le feu et la pourriture, les additifs hydrophobes pour résister à l'humidité, les agents moussants pour réduire la densité du WPC.
Volume de particules de bois dans le matériau peut être de 30 à 70 %, et leur taille est de 0,7 à 1,5 mm. Les fractions fines sont utilisées dans la production de profilés finis qui ne nécessitent pas de traitement de surface supplémentaire. Les moyennes conviennent à la peinture ou au placage. Rugueux - à des fins techniques.
Volume de liants synthétiques x varie également et peut aller de 2 à 55 %. Encore une fois, cela dépend de l'objectif du futur produit. Quant aux additifs supplémentaires, leur volume dans le matériau ne dépasse pas 15%.
Soit dit en passant, il n'y a pas si longtemps, les développeurs allemands ont réussi à faire "bois liquide" de qualité parfaite. Les spécialistes de l'Institut Fraunhofer l'ont créé à partir de lignine. Ce matériau est obtenu à partir de bois. DPK a appelé Arboforme est un produit absolument non toxique. De plus, si un composite bois-polymère conventionnel peut être recyclé 3 à 4 fois, alors celui-ci peut être recyclé jusqu'à 10 fois. Pourquoi fait-on ça? Le fait est qu'en Chine, l'industrie de la production de WPC se développe comme nulle part ailleurs dans le monde. Et, si en Europe et aux États-Unis, les matériaux créés subissent une série de tests, alors dans le Céleste Empire, ils ne s'en soucient pas et fournissent au marché, y compris international, un produit de qualité médiocre.
Maintenant environ Équipement de production WPC. Son ensemble standard comprend : une extrudeuse à double vis, une matrice de moulage, une table de calibrage et de refroidissement, un dispositif de tirage, un dispositif de coupe dans le sens de la longueur, une division dans le sens de la largeur (si nécessaire) et un empileur. Toute la ligne est compacte et généralement entièrement automatisée. Dans la configuration de certains modèles, il y a aussi : un broyeur (hachoir de matières premières), un chargeur automatique de matières premières et un mélangeur.
Les fabricants de ces lignes et modules sont principalement Entreprises chinoises. Les leaders parmi eux sont WPC, Zhangjiagang City Boxin Machinery, etc. La qualité des équipements est d'un niveau décent, d'autant plus que leurs principaux composants sont produits par des usines d'ingénierie européennes.
Dans cet article, nous vous dirons comment vous pouvez faire un populaire materiel de construction appelé un arbre liquide à faire soi-même, et décrit également tous ses avantages.
Tout artisan à domicile sait que les produits en bois ont peur impacts négatifs une variété de facteurs opérationnels, ce qui réduit leur durée de vie. En même temps, l'arbre est aimé par de nombreuses personnes et constructeurs professionnels. Il est respectueux de l'environnement, a fière allure, charge une personne d'énergie positive et présente de nombreux autres avantages.
produit en bois liquide
Pour ces raisons, les experts tentent depuis longtemps de trouver un substitut au bois naturel, qui ne serait visuellement et physiquement différent du bois, surpassant ce dernier par sa qualité et sa résistance à l'influence. phénomène naturel. La recherche a été couronnée de succès. Moderne industrie chimique a pu créer un matériau unique - liquide arbre artificiel. Il a littéralement fait irruption sur les marchés de la construction du monde entier. Maintenant, un tel arbre est vendu sous l'abréviation WPC (composite bois-polymère). Le matériau qui nous intéresse est composé des composants suivants :
- Base en bois déchiqueté - en fait, traitement des déchets bois naturel. Dans l'un ou l'autre composite, ils peuvent contenir de 40 à 80 %.
- Polymères chimiques thermoplastiques - polychlorures de vinyle, polypropylènes, etc. Avec leur aide, la base en bois est assemblée en une seule composition.
- Additifs appelés additifs. Ceux-ci comprennent des colorants (colorent le matériau dans la teinte souhaitée), des lubrifiants (augmentent la résistance à l'humidité), des biocides (protègent les produits contre les moisissures et les insectes nuisibles), des modificateurs (conservent la forme du composite et garantissent sa haute résistance), des agents gonflants ( permettent de réduire le poids du WPC).
Ces composants sont mélangés dans certaines proportions, chauffés fortement (jusqu'à ce que la composition devienne liquide), le mélange est polymérisé, puis il est introduit dans des formes spéciales sous haute pression et super. À la suite de toutes ces actions, on obtient une composition qui présente une flexibilité et une excellente résistance à la corrosion, élasticité et résistance aux chocs. Et le plus important - WPC a un arôme magique de bois naturel, ainsi qu'une couleur et une texture identiques au vrai bois.
Nous espérons qu'à partir de notre courte revue, vous avez compris comment le bois liquide est produit et compris ce que c'est. Les produits en bois-polymère décrits se caractérisent par un certain nombre d'avantages opérationnels. Voici les principales ci-dessous :
- résistance accrue aux dommages mécaniques;
- résistance aux changements de température (les produits en WPC peuvent fonctionner à la fois à +150 ° С et à -50 °);
- haute résistance à l'humidité;
- faciliter auto-traitement et installation (à ces fins, un outil est utilisé qui fonctionne avec du bois naturel);
- longue durée de vie (au moins 25-30 ans);
- un grand choix de couleurs;
- résistance aux champignons;
- facilité d'entretien (le composite est facile à nettoyer, il peut être gratté, verni, peint de n'importe quelle couleur).
décoration bois plastique
Un avantage important du bois plastique est qu'il a un coût très abordable. Ceci est réalisé grâce à l'utilisation de produits de transformation secondaire (contreplaqué déchiqueté, sciure de bois, copeaux) dans la production de WPC. Il est difficile de trouver des lacunes dans le matériel que nous examinons, mais elles existent. Et comment sans ça ? Il n'y a que deux inconvénients au bois plastique. Premièrement, lors de son utilisation dans les pièces à vivre, il est nécessaire d'équiper une ventilation de haute qualité. Deuxièmement, WPC n'est pas recommandé pour une utilisation dans les cas où une humidité élevée et une température de l'air élevée sont constamment et simultanément présentes dans la pièce.
Les caractéristiques particulières d'un composite de bois et de plastique permettent de fabriquer divers produits de construction à partir de celui-ci. Ce matériau est utilisé pour la réalisation de revêtements extérieurs, de platelages lisses, creux, ondulés et pleins (autrement dit, decking). Des balustrades chics, des garde-corps artistiques, des clôtures fiables, des gazebos luxueux et de nombreuses autres structures sont fabriqués à partir de WPC. Le bois-plastique vous permettra d'équiper luxueusement les intérieurs d'un quartier résidentiel et de créer le vôtre zone suburbaine Vraiment magnifique.
Le coût du composite décrit dépend du polymère utilisé pour sa fabrication. Si le fabricant fabrique du WPC à partir de matières premières en polyéthylène, le prix du produit fini sera minime. Mais il convient de noter que ces produits ne résistent pas aux rayons ultraviolets. Mais les polymères de chlorure de polyvinyle confèrent au plastique du bois une haute résistance au feu et aux rayons UV, et le rendent également très durable. Les produits de WPC (en particulier les terrasses) sont généralement divisés en sans soudure et avec coutures. Les premiers sont montés sans pinces, vis et autre matériel. Ces panneaux s'emboîtent simplement les uns dans les autres, formant une surface solide solide.
matière plastique bois
Mais pour installer des produits avec des coutures, vous devez utiliser du plastique ou attaches métalliques(le plus souvent dans le rôle de telles sont les pinces). Les panneaux ou panneaux WPC peuvent être creux ou pleins. Pour aménager les vérandas des maisons privées, il est préférable d'utiliser des produits avec des vides. Ils sont légers et très faciles à travailler. Le bois-plastique corsé, capable de supporter des charges importantes, convient mieux à la pose dans dans des lieux publics(remblais, restaurants et bars d'été, ponts de navires), où il y a un fort trafic de personnes.
Lors du choix des panneaux de WPC, faites attention à l'épaisseur de leurs parois (elle doit être d'au moins 4-5 mm), à la hauteur des raidisseurs (plus ils sont hauts, plus les produits seront fiables en fonctionnement) et à leur nombre (plus il y a de nervures, plus la conception est solide).
Vous devez également choisir judicieusement la largeur des panneaux composites et des planches. Il y a un point à comprendre ici. H Plus vous achetez de produits larges, plus il vous sera facile de travailler avec eux, car pour l'installation de telles planches, vous aurez besoin de beaucoup moins de fixations . Plusieurs encore conseils utiles Pour toi. Vérifiez auprès des vendeurs à partir de quelle sciure le WPC a été fabriqué. Si le fabricant a utilisé du bois tendre à ces fins, il est préférable de rechercher un autre matériau. Pourquoi? Pour la raison que les composites à base de conifères sont considérés comme dangereux pour le feu. Et les caractéristiques de résistance de ces produits laissent beaucoup à désirer. WPC basé sur le recyclage des déchets arbres à feuilles caduques dépourvu de ces défauts.
Dans les cas où des stries ou des zones claires sont clairement visibles sur les panneaux composites (planches, dalles), la fiabilité opérationnelle des produits sera faible. Très probablement, le fabricant a utilisé de la farine de bois de mauvaise qualité et, de plus, mal moulue. En règle générale, ces panneaux ont un faible indice de résistance à l'eau. Ils ne peuvent pas être utilisés à l'extérieur. La présence d'une couleur non uniforme à sa surface (taches, transitions de nuances clairement visibles) témoigne également de la qualité insuffisante du WPC.
Et maintenant le plus intéressant. Si vous le souhaitez, vous pouvez facilement créer chez vous un analogue digne du WPC. Le bois plastique fait maison est fabriqué à partir de sciure de bois et de colle PVA ordinaire et est utilisé pour restaurer planche de parquet, réparation de sols stratifiés, restauration d'autres revêtements en bois. Il peut également être utilisé pour la fabrication de revêtements de sol bruts pour les sols de gazebos et de locaux auxiliaires.
Matériau composite à base de sciure de bois et de colle
WPC se fait à la main selon le schéma suivant :
- moudre sciure dans un moulin à café ou un moulin à main jusqu'à ce qu'il soit poussiéreux.
- Ajoutez de la colle PVA à la sciure broyée (proportions - 30 à 70%) et mélangez ces composants jusqu'à obtenir un mélange de consistance pâteuse.
- Versez le colorant dans la composition réalisée (il est recommandé d'utiliser des additifs utilisés pour les peinture à base d'eau). Mélangez à nouveau le tout.
Alors vous avez fait un bois-plastique maison ! N'hésitez pas à combler les trous dans cette composition Sol en bois. Une fois le WPC durci, la zone restaurée n'aura besoin d'être poncée qu'avec de l'émeri à grain fin. Une composition à faire soi-même peut également être utilisée pour équiper de nouveaux sols. Collectez, faites un KDP maison en les bonnes quantités et remplissez-en la structure de coffrage. Épaisseur planches maison dans ce cas, il doit être d'au moins 5 cm.
La vidéo du jeu "" peut être téléchargée gratuitement aux formats mp4, x-flv, 3gpp, pour cela, cliquez sur le bouton "Télécharger la vidéo" situé en haut.
La description:
Type - ingrédient d'artisanat ; Où chercher - faites-le vous-même; Empilable - oui, 64 par pile. Descriptif et fonctionnalités. Maintenant, vous savez non seulement comment faire un composite dans minecraft, mais aussi tout le métier où il est impliqué en tant qu'ingrédient, donc IndustrialCraft 2 Composite - Minecraft Wiki minecraft -fr fabrication industrielle 2 Composite Composite Type Matériaux Résistance Non Empilable Oui64 Première apparition. -Base de connaissances Minecraft -Composite Industrial Craft 2. Comment faire un composite dans minecraft mir minecraft Comment fabriquer un composite dans minecraft ? Comment fabriquer un composite dans minecraft? Examen de la mise à jour de Minecraft 1.8.8 - quoi de neuf dans minecraft 1.8.8 ? Comment faire une selle dans minecraft 1.8.8 ? Artisanat industriel 2 Composite dans minecraft minecraft Forum Comment faire un composite dans minecraft. Le composite dans minecraft peut être obtenu en comprimant des lingots composites à l'aide d'un compresseur. Comment faire un composite dans minecraft allin minecraft Un composite est un élément ajouté par le mod IndustrialCraft². Il est fabriqué en comprimant des lingots composites dans un compresseur. Utilisé dans la fabrication de nombreux blocs et objets de haute technologie et durables. Industrial Craft 2 Composite - Minecraft Wiki m craft Forum pour les joueurs et les tricheurs : astuces, mods, guides. World of Tanks, Warface, Armored Recommander un jeu similaire à Trove ou Minecraft 3 posts 19 janvier 2016 serveur minecraft? Qu'est-ce que wipe 2 posts 19 janvier 2016 Comment faire du bronze et du composite ! Comment faire un composite dans minecraft ? Nous fabriquons des nano-armures, des jet packelectro et des nano sabres - ProFIT31ru. Comment faire une usine de composite d'iridium dans minecraft ic2+bc3 - GameCity. Comment faire un bavoir dans Minecraft Comment faire un bavoir dans Minecraft Minecraft dans son incarnation classique est un jeu de "minage", où l'un des plus tâches importantes considéré comme une variété d'exploitation minière.Les quatre places restantes seront occupées par des plaques composites d'iridium. Comment faire un composite dans minecraft ? - Craft in Minecraft az minecraft Composite est un élément ajouté par le mod Industrial Craft ². Il est fabriqué en comprimant des lingots composites dans un compresseur. Utilisé dans la fabrication de nombreux blocs et objets de haute technologie et durables. comment faire un composite dans minecraft - 14
Vidéo pour téléphone mobile, smartphone, tablette, etc. sont consultables en ligne, gratuitement et sans inscription. Et aussi télécharger vidéo mobile au format mp4, x-flv et 3gpp !
N'hésitez pas à laisser votre commentaire ou votre avis sur cette vidéo ! L'auteur sera très intéressé de savoir ce que vous pensez de son travail.