Selbstgemachter magnetischer Schlüsselhalter. Steckdosenhalter Wie man einen Steckdosenhalter herstellt
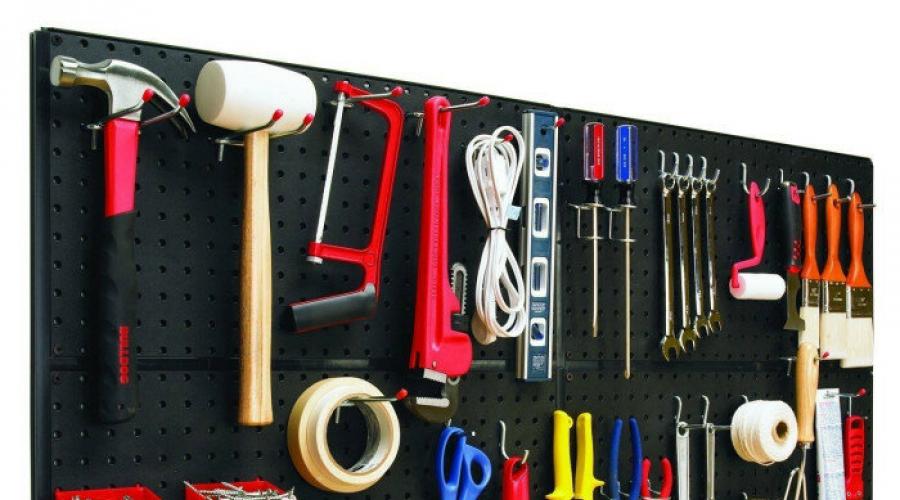
Im Winter ist das Tischlerhandwerk in einer ungeheizten Werkstatt ein unterdurchschnittliches Vergnügen. Aber meine Hände jucken. Also beschloss ich, ein Wochenendprojekt umzusetzen, das etwas gröbere Arbeit erforderte – die Installation einer Werkzeugtafel neben der Werkbank.
Platz für das zukünftige Panel:
Dieses Problem lässt sich mit Lochplatten (aus Blech oder HDF) oder Economy-Platten (MDF mit Rillen über die gesamte Länge) lösen. In thematischen Foren findet man oft Themen, in denen Leute damit prahlen, dass ihre Werkstätten mit solchen Panels ausgestattet sind. Es sieht wirklich beeindruckend aus.
Diese Option ist jedoch nicht für jeden geeignet. Obwohl die Paneele selbst nicht billig sind, müssen Sie auch zusätzliche Kleiderbügel und Haken kaufen, deren Gesamtkosten um ein Vielfaches höher sind als die Kosten des Paneels selbst. Darüber hinaus wirft die Benutzerfreundlichkeit von Haken ohne starre Fixierung Fragen auf. Und es ist nicht klar, wie man einen selbstgemachten Kleiderbügel aus Sperrholz an einer solchen Platte anbringt?
Lassen Sie mich Ihnen ein Beispiel geben.
Sehen Sie auf dem Foto einen roten Gasschrauber mit einem schmalen Loch im Griff? Wenn Sie ihn beim Abnehmen versehentlich ein wenig nach oben schieben, kann es passieren, dass der Haken von der Platte springt. Nun ja, oder der Haken muss repariert werden. Natürlich eine Kleinigkeit, aber Sie müssen Zeit (wenn auch nur für den Bruchteil einer Sekunde), Aufmerksamkeit und einen Sekundenzeiger ablenken, der höchstwahrscheinlich beschäftigt sein wird. Natürlich kann man versuchen, den Gasschlüssel vorsichtig abzuziehen, damit er nichts verfängt, aber erfordert dieser Haken nicht zu viel Aufmerksamkeit?
Das Gleiche wird höchstwahrscheinlich passieren, wenn Sie versuchen, Zangen mit roten und blauen Griffen zu entfernen. Weil die Gummigriffe wie ein Morsekegel in der Halterung einrasten.
Obwohl ich mich natürlich irren könnte und meine Zweifel vergebens sind.
Noch ein Detail: Kleiderbügel für nur eine Zange und einen Hammer kosten fast 500 Rubel. Wie sie sagen, zählen Sie es.
Ich bin für einfache und zuverlässige Lösungen. Daher wurde beschlossen, als Platte eine Platte aus gewöhnlichem 15-mm-Sperrholz zu verwenden. Als Aufhänger und Haken können Sie gewöhnliche selbstschneidende Schrauben unterschiedlicher Länge zum Preis von zwei Kopeken pro Kilogramm verwenden, die ohne Ihren anhaltenden Wunsch nirgendwo hingehen. Die gleichen selbstschneidenden Schrauben können zur Befestigung jeder selbstgebauten Aufhängung verwendet werden. In diesem Fall kann die Länge des aus der Platte herausragenden Teils der Schraube vor Ort genau eingestellt werden, indem die Schraube sogar durchgängig in das Sperrholz eingeschraubt wird. Dafür muss aber zwischen Sperrholz und Wand ein Spalt vorhanden sein.
Der Spalt kann mit Kunststoffscheiben für Lochplatten hergestellt werden. Es ist jedoch sicherer, das Panel auf einem speziell geschweißten Rahmen zu installieren. Dadurch werden die Unebenheiten der Wand ausgeglichen, die gesamte Struktur wird steifer und Sie können einen Spalt beliebiger Größe einstellen.
Natürlich ist diese Methode auch nicht kostenlos und nicht so glamourös, dafür aber deutlich praktischer.
Ich glaube, dass sich nur wenige Menschen für den Schweißprozess interessieren. Das Ergebnis ist wichtig. Der Rahmen ist aus meiner liebsten fünfzigsten Ecke geschweißt. Alle Befestigungslöcher sind 8 mm groß.
Wir richten den Rahmen auf einer Sperrholzplatte aus und markieren die Befestigungspunkte.
Die Löcher im Sperrholz sind einige Millimeter breiter als im Rahmen, um kleinere Ungenauigkeiten auszugleichen.
Habe den Rahmen lackiert Autofarbe aus einer Dose. Farbe - Die Schneekönigin(mit Metallic). In der Anleitung steht, dass die Farbe bei einer bestimmten Temperatur aufgetragen werden sollte Umfeld nicht niedriger als +15. Allerdings gibt es in der Werkstatt keine Heizung und wir mussten bei -1 mal lackieren. Die Qualität der Beschichtung wurde dadurch nicht beeinträchtigt. Der einzige Unterschied besteht höchstwahrscheinlich in der Trocknungszeit.
Der Rahmen wird mit acht 8x80-Dübeln an der Wand befestigt. Tatsache ist, dass die Garagenwand, an der das Paneel installiert werden soll, nur einen halben Ziegelstein dick ist. Wie geplant große Menge Befestigungspunkte sollen die Last gleichmäßig verteilen. Zudem blieben die Dübel teilweise zwischen den Ziegeln hängen, sodass ihre Zuverlässigkeit geringer ist.
Wenn ich mir nun das fertige Ergebnis ansehe, verstehe ich, dass man mit der Hälfte der Dübel auskommen konnte. Aber hier gilt: Vorsicht ist besser als Nachsicht.
Die Sperrholzplatte wird mit dreizehn 8x45-Ankern am Rahmen befestigt.
Anker eignen sich hervorragend für diese Aufgabe. Um eine normale Mutter und Schraube festzuziehen, benötigen Sie Zugang sowohl zur Mutter als auch zur Schraube. Wenn der Rahmen jedoch bereits an der Wand befestigt ist, ist ein solcher Zugang nicht möglich (insbesondere bei der Befestigung von Sperrholz an der mittleren Querstange des Rahmens). Allerdings muss der Anker nur von einer Vorderseite aus zugänglich sein.
Ich kann mir gar nicht vorstellen, was schief gehen könnte. Das einzige Problem, das bei einer solchen Verbindung theoretisch auftreten kann, ist, dass die Mutter und der Lochrand in der Ecke die Ankerhülse durchbeißen. Aber das ist unwahrscheinlich. Daher erscheint mir diese Verbindung sehr zuverlässig.
Wenn das Panel fertig ist, können Sie mit der Platzierung des Werkzeugs beginnen. An erster Stelle steht der Vorschlaghammer. Da sie keine eigene Wohnung hatte, war sie ständig im Weg. Gleichzeitig ist die Aussicht, es in meiner Werkstatt einzusetzen, vage. Aber man kann es auch nicht wegwerfen. Es ist ein Werkzeug! Deshalb habe ich kurzerhand eine spezielle Halterung dafür angeschweißt,
Ich habe alles mit Sprühfarbe dekoriert
und platzierte es in der hintersten Ecke unter der Decke. Endlich werde ich nicht mehr über sie stolpern und sie ist immer verfügbar, wenn ich sie brauche.
Dank eines leistungsstarken Rahmens und einer Vielzahl von Befestigungspunkten müssen Sie sich keine Gedanken über die zulässige Belastung des Panels machen.
Die Panelfläche ist etwas größer Quadratmeter- nicht wenig und es gibt eine gewisse Reserve.
Ich habe vor ein paar Jahren die gleichen Werkzeugtafeln in meiner Landgarage installiert. Ich habe genau die gleichen Anker verwendet. Dort entstand die Idee, einen Rahmen unter das Paneel zu schweißen – dies ist der Gestaltung der Wände geschuldet. Aber die Idee hat sich durchgesetzt.
In all den Jahren könnte ich mit den Panels einfach nicht zufriedener sein. Auf der Datscha benutze ich das Werkzeug nicht sehr oft, also vergesse ich etwas. Manchmal war es einfacher zu kaufen neues Werkzeug als ein altes in den Trümmern zu finden. Deshalb habe ich mehrere Gebäudeebenen, mehrere Lotlinien, Gasschlüssel, Äxte und andere Dinge. Natürlich wird sich auf dem Bauernhof alles als nützlich erweisen. Aber jetzt weiß ich immer genau und vergesse nicht, welche Werkzeuge ich habe, wie viele und wo sie sich befinden. In den ersten Wochen muss man sich daran gewöhnen, dass jedes Ding seinen eigenen Platz haben sollte. Und wenn es zur Gewohnheit wird, ist die Arbeit in der Werkstatt kein ständiges Suchen mehr. das richtige Werkzeug und über unnötige Dinge stolpern.
Kurz gesagt, ich empfehle es.
Der ganze Job dauerte eineinhalb Tage frei. Es war möglich, eines zu machen, aber ohne zu malen (ich musste eine Pause machen, um die Farbe trocknen zu lassen). Insgesamt bin ich mit dem Ergebnis zufrieden.
Hallo an alle DIY-Liebhaber!
Um mit Gewindebefestigungen zu arbeiten, ist jedoch neben Gabelschlüsseln häufig auch die Verwendung von Innensechskantschlüsseln erforderlich. Deshalb habe ich beschlossen, auch für sie einen Wandhalter anzufertigen.
Ich muss sagen, dass ich diesen Satz Innensechskantköpfe mit Schlüssel und Kunststoffhalter habe.
Das Problem besteht jedoch darin, dass sich einige Köpfe nur recht schwer aus den Löchern in diesem Halter entfernen lassen, andere dagegen kaum halten und manchmal herausfallen, da die Löcher dafür bereits locker sind. Und die an den Seiten der Köpfe angegebenen Maße sind aufgrund der hohen Wände des Halters überhaupt nicht sichtbar. Die Praxis hat gezeigt, dass dieser Halter bei Bedarf bequem mitgenommen werden kann, für die Arbeit in der Werkstatt jedoch nicht sehr praktisch ist.
Rückblickend Verschiedene Optionen hausgemacht Wandhalter, beschloss ich zunächst, bei dem zu verweilen, was zu sein schien optimale Option, bei dem die Innensechskantköpfe einfach in in die Platine gebohrte Löcher gesteckt werden.
Da sich die Durchmesser benachbarter Köpfe jedoch nicht sehr unterscheiden (im wahrsten Sinne des Wortes um 0,5 bis 2 mm), ist es sehr schwierig, Bohrer oder Kronen für Holz auszuwählen, um Löcher dafür zu bohren.
Natürlich war es möglich, einige Löcher mit einer Rundholzfeile zu bohren, aber dann kam ich auf eine bessere Idee.
Ich habe mich für einen Halter entschieden, bei dem die Steckdosen einfach auf die vertikalen Stifte geschoben werden. Darüber hinaus können als solche Stifte Schrauben mit aufgesetzten Kunststoffrohren verwendet werden. Natürlich ist die Herstellung eines solchen Halters auch viel einfacher als der eines Halters mit Löchern.
Um einen solchen Halter herzustellen, benötigte ich folgende Materialien:
Materialien und Befestigungselemente:
Ein Holzbrett mit einer Dicke von 1,5 bis 2 cm, einer Breite von 4,5 cm und einer Länge von etwa 30 cm;
- Neun Schrauben 3x35 mm;
Zwei Holzschrauben 4x60 mm;
Plastikstrohhalme.
Werkzeuge:
Zeichen- und Messwerkzeuge (Bleistift, Maßband und Winkel);
Eine Stichsäge mit Feile zum Kurvenschneiden;
Elektrischer Bohrschrauber;
Metallbohrer mit einem Durchmesser von 2,5 mm;
Metallbohrer mit einem Durchmesser von 4 mm;
Kugelfräser für Holz;
Lochsäge für Holz, Durchmesser 19 mm;
Halbrunder Meißel;
Schere;
Schraubendreherbits PZ1 und PH2, zum Eindrehen von Schrauben;
Schleifpapier.
Herstellungsprozess
Zuerst markieren wir das Holzbrett - den zukünftigen Halter, stechen mit einer Ahle in die Mitte der zukünftigen Löcher für die Stiftschrauben und bohren die Löcher selbst (können durch) mit einem Durchmesser von 2,5 mm.
Anschließend mit einer Lochsäge durchtrennen Sackloch mit einem Durchmesser von 19 mm, für einen Schlüssel.
Reinigen Sie dieses Loch mit einem halbrunden Meißel und entfernen Sie überschüssiges Holz.
Wir bohren quer durch die Diele zwei Löcher mit einem Durchmesser von 4 mm, für lange Holzschrauben, zur späteren Befestigung unseres Halters an der Wand.
Diese Löcher versenken wir mit einem Kugelholzfräser für Schraubenköpfe.
Dann schneiden wir mit einer Schere Stücke aus Kunststoffrohren ab, die wir auf die Schrauben stecken. Die Länge jedes Stücks beträgt ca. 25 mm.
Ich habe Plastikstrohhalme aus gebrauchten Flüssigseifenflaschen genommen.
Jetzt stecken wir auf jede Schraube ein Stück Rohr.
Und diese Schrauben schrauben wir im Vorfeld fest gebohrte Löcher mit einem Durchmesser von 2,5 mm, bis die Kunststoffrohre fest zusammengepresst sind (aber nicht zu fest anziehen).
Hier möchte ich besonders darauf hinweisen, dass unbedingt Schrauben mit kleinem Kopf (nicht mehr als 6 mm Durchmesser) verwendet werden müssen, da sonst die Innensechskantköpfe nicht darauf passen.
Anschließend führen wir alle notwendigen Schnittarbeiten mit einer Stichsäge durch. Das heißt, wir schneiden eine Nut in das Schlüsselloch, schneiden auch den Halter selbst aus und runden seine Enden ab.
Danach bearbeiten wir unseren Halter mit Schleifpapier und schleifen ihn ab Besondere Aufmerksamkeit Kanten und Enden.
Und jetzt ist unser Halter fast fertig!
Für eine einfachere Handhabung müssen nur noch Etiketten mit der Aufschrift der Kopfgrößen darauf geklebt werden.
Diese Etiketten können am Computer erstellt und mit einem Drucker ausgedruckt, dann ausgeschnitten und auf den Halter geklebt werden.
Jetzt ist es sehr praktisch, die Innensechskantköpfe zu entfernen und auf die Haltestifte zu stecken. Und sie halten sehr sicher und fallen nie herunter.
Zudem sitzen die Innensechskantköpfe dank der Kunststoffröhrchen an den Stiften und Schrauben sehr weich und geschmeidig darauf und verkratzen nicht.
Nun, das ist wahrscheinlich alles, was ich habe!
Tschüss für alle, nützlichere und notwendigere hausgemachte Produkte!
Aufgrund eines Lecks Wasserrohr Am 20. Rohr musste das Gewinde um die Hälfte gekürzt werden. Die Matrize wurde für 230 Rubel gekauft, im Prinzip vernünftiges Geld, ein Besuch beim Klempner wäre teurer gewesen:
Und dann tauchte ein Problem auf: Wie dreht man es, wie greift man es? Fertige Matrizenhalter für 45 mit Ratsche kosten weniger als 1000 Rubel. Vom Kauf wird abgeraten, da 1-2 Fäden abgeschnitten werden müssen. Ich fing an, über Optionen nachzudenken, entschied mich für diese und kauften einen 22-Innensechskant (Kosten 60 Rubel):
Und sägen Sie mit einer Schleifmaschine die Zähne entsprechend der Größe der Löcher in der Matrize durch:
Es stellt sich dieses coole Design heraus:
Mit einer Schleifmaschine lässt sich ein Innensechskopf problemlos bearbeiten, allerdings muss man ihn langsam abschneiden und an den Stellen, an denen die Matrize aufliegt, entfernen. Die resultierende Befestigung erwies sich als sehr zuverlässig; zum Drehen des Innensechskantkopfes verwendete ich einen fehlerhaften Drehmomentschlüssel mit einer Ratsche von einem halben Meter Länge:
Das Design weist zwei Nachteile auf. Der erste Nachteil besteht darin, dass die Löcher in der Matrize nicht für ihren vorgesehenen Zweck verwendet werden, sondern lediglich zum Entfernen von Spänen dienen. Daher muss beim Schneiden von Gewinden zumindest regelmäßig der Innensechskantkopf entfernt werden , und die Matrize höchstens öfter abschrauben. Der zweite Nachteil besteht darin, dass aufgrund der Tatsache, dass die Kraft mit einer Verschiebung von einigen Zentimetern vom Gewinde auf die Matrize ausgeübt wird und die Kraft dort ziemlich groß ist, das Gewinde selbst relativ zum Rohr geneigt ist. Bei einem dünnen Rohr führt dies dazu, dass ein Loch in das Rohr geschnitten wird, d. h. das Gewinde passt in das Rohr. Um diesen Effekt zu minimieren, wechseln Sie die Krafteinwirkung in entgegengesetzten Schlüsselpositionen ab. Zum gemütlichen Schneiden von 2-3 Fäden ist das Design durchaus geeignet.
In diesem Artikel erzähle ich Ihnen, wie der Autor ein nützliches Gerät in Form eines Halters für Schlüsselköpfe hergestellt hat. Da die Aufbewahrung von Werkzeugen, nämlich Kleinteilen, beispielsweise Schlüsselköpfen oder Bolzen, schwierig sein kann, wurde diese Idee umgesetzt. Profis kaufen Werkzeuge separat und bewahren sie in einem speziellen Koffer auf, aber dieser zusätzliche Kosten. Warum also nicht einen selbstgemachten magnetischen Schlüsselhalter herstellen, der ein guter Ersatz für die kostengünstigste Aufbewahrungsmöglichkeit sein kann? Ein weiterer Pluspunkt ist, dass jeder einzelne Kopf an seinem richtigen Platz bleibt und Sie keine Angst haben müssen, ihn während des Transports zu verlieren.
Um dieses nützliche hausgemachte Produkt herzustellen, benötigen Sie folgende Materialien:
*Programm zum Entwerfen eines Vektorbildes (Corel Draw).
*Laserschneider.
*Plattenstärke 130 mm, 5 x 20 cm (Pappel).
*Plattenstärke 64 mm, 5 x 40 cm (Nussbaum).
*Magnetstreifen 40 cm lang.
*Epoxidharz.
*Schleifpapier.
*Acryllack.
Schritt eins. Erstellen eines Projekts in Corel Draw
Zunächst müssen Sie ein Muster erstellen, aus dem dieser Halterrohling lasergeschnitten wird. Dazu müssen Sie zumindest über einige Grundkenntnisse im Erstellen von Vektorbildern verfügen.
Zuerst tun erforderliche Menge Kreise Dabei entstehen Löcher, in die die Köpfe der Schlüssel gesteckt werden. Machen Sie die Kreise mit einem Spielspiel von + 0,05 cm, damit Sie Ihre Köpfe während des Gebrauchs problemlos in die fertigen Zellen stecken können.
Platzieren Sie die Kreise gleichmäßig und lassen Sie zwischen ihnen einen Abstand von einigen Millimetern. Wenn alle Kreise fertig sind, markieren Sie den Umriss eines Rechtecks um sie herum, das als Basis dienen soll. Die Winkel können unterschiedlich sein, sowohl regelmäßig als auch geschweift, wie in unserem Projekt.
Schritt zwei. Entwicklung des Frameworks
Nach der Abdeckung müssen Sie die Basis entwickeln. Die Form bleibt dieselbe – rechteckig mit geschweiften Ecken, wie der Durchgang nach dem Fräsen. Anstelle der Kreise müssen schwarze Trennstreifen angebracht werden. Die Breite des Streifens sollte dem Durchmesser des größten Kreises entsprechen. Die Linien auf dem Grundlayout müssen in Schwarz gezeichnet werden, damit der Laser sie nicht ausschneidet, sondern eingraviert.
Schritt drei. Den Hauptteil erstellen
Auch das Layout für den Hauptteil des Halters ist im Wesentlichen fertig (analog zum ersten Schritt). Aber von der Seite wird es besonders anders aussehen. Für besseren Nutzen und Informationsgehalt markieren wir die Maße der Köpfe am Endteil des Halters. Wir machen das an jedem geeigneten Ort, Hauptsache, die Abmessungen stimmen überein.
Schritt vier. Schneiden
In diesem Schritt werden entsprechend den vorbereiteten Layouts die Halterrohlinge ausgeschnitten, von denen wir drei haben.
Der Prozess ist sehr langwierig und erfordert Geduld.
Schritt fünf. Schleifen
Alle fertigen Teile müssen mit Schleifpapier geschliffen werden. Beseitigen Sie dazu alle Unregelmäßigkeiten und Mängel.
Schritt sechs. Seitliche Gravur
Wir nehmen den breitesten Pappelrohling und gravieren ihn mit Zahlen.
Schritt sieben: Magnetstreifen aufkleben
Wir schneiden den Streifenmagneten in Streifen und kleben ihn auf die Basis des Halters. Magnete dieser Art verfügen über eine selbstklebende Rückseite. Um sie sicher anzubringen, ist es jedoch besser, einen zusätzlichen Schritt durchzuführen Epoxidharz. Nachdem alles mit Leim bedeckt ist, drücken Sie es zur besseren Festigkeit 5 - 10 Minuten lang mit einer Presse. Seien Sie vorsichtig beim Kleben.
Schritt acht. Verklebung aller Teile des Halters
Mit Epoxidharz beschichten wir alle Teile des Werkstücks, kleben sie zusammen und drücken es dann einige Dutzend Minuten lang mit einer Presse.
Die Aufbewahrung von Werkzeugen, insbesondere von Kleinteilen wie Steckschlüsseleinsätzen, Schrauben usw., kann manchmal schwierig sein. Laien kaufen Werkzeuge häufig separat und die Aufbewahrung in einem speziellen Koffer oder einer speziellen Box ist mit zusätzlichen Kosten verbunden. Ein praktischer, selbstgemachter magnetischer Schlüsselhalter kann jedoch eine hervorragende Alternative zu mehr sein teure Option Lagerung Darüber hinaus wird jeder Kopf sicher in seiner eigenen Zelle befestigt und die gesamte Box kann transportiert werden, ohne befürchten zu müssen, sie zu verlieren.
Material
- Programm zur Erstellung von Vektorbildern (Corel Draw);
- Laserschneider;
- Brett 130 mm stark, 5 x 20 cm (Pappel);
- Brett 64 mm stark, 5 x 40 cm (Nussbaum);
- Magnetstreifen 40 cm lang;
- Epoxidharz;
- Schleifpapier;
- Acryllack.
Schritt 1: Erstellen Sie ein Projekt in Corel Draw
Zunächst muss ein Layout erstellt werden, nach dem der exakte Rohling des Halters mit einem Laser ausgeschnitten wird. Um ein Layout zu erstellen, müssen Sie über Kenntnisse im Erstellen von Vektorbildern verfügen.
Erstellen Sie zunächst die Anzahl der Kreise, die Sie benötigen. Diese werden zu den Löchern, in die Sie die Buchsen für die Schlüssel stecken. Machen Sie Kreise in der Größe des Durchmessers der Köpfe selbst + 0,05 cm. Dies ist notwendig, damit Sie Ihre Köpfe während des Betriebs frei in die vorbereiteten Zellen einführen können.
Verteilen Sie die Kreise gleichmäßig und lassen Sie zwischen ihnen einen Abstand von einigen Millimetern. Wenn Sie alle Kreise platziert haben, zeichnen Sie ein Rechteck um sie herum. Die Ecken können Sie wie gewohnt belassen oder wie in diesem Projekt figurativ gestalten.
Schritt 2: Entwickeln Sie das Framework
Nach dem Deckel muss die Basis des Halters entwickelt werden. Die Grundform bleibt dieselbe – rechteckig mit geschweiften Ecken. Anstelle der Kreise müssen Sie jedoch schwarze Streifen auftragen. Die Breite des Streifens sollte dem Durchmesser des größten Kreises entsprechen. Die Linien auf dem Grundlayout müssen schwarz markiert sein, damit der Laser sie nicht ausschneidet, sondern eingraviert.
Schritt 3: Erstellen Sie das Hauptteil
Auch das Layout für den Hauptteil des Halters ist im Wesentlichen fertig (analog zum ersten Schritt). Aber von der Seite wird es besonders aussehen. Um den weiteren Betrieb zu erleichtern, müssen die Abmessungen der Köpfe am Ende des Halters markiert werden. Tun Sie dies in jeder für Sie passenden Form. Hauptsache, die Größen passen.
Schritt 4. Schneiden
In diesem Stadium werden die Halterrohlinge gemäß den vorbereiteten Layouts ausgeschnitten. Insgesamt wird es drei davon geben.
Schritt 5: Schleifen
Alle Werkstücke müssen geschliffen werden. Nehmen Sie dazu Schleifpapier und glätten Sie alle Unregelmäßigkeiten.
Schritt 6: Gravur der Seite
Nehmen Sie das breiteste Stück (Pappel) und gravieren Sie darauf Zahlen.
Schritt 7. Magnetstreifen aufkleben
Der vorhandene Magnet muss in Streifen geschnitten und auf die Basis des Halters geklebt werden. Magnete dieser Art haben eine Klebebasis, für eine sichere Befestigung ist es jedoch besser, sie zusätzlich mit Epoxidharz zu beschichten. Geklebt Magnetstreifen, legen Sie sie für 5 – 10 Minuten unter die Presse. Seien Sie beim Kleben vorsichtig.
Schritt 8. Alle Teile des Halters verkleben