Flüssiges Holz mit eigenen Händen – wir schaffen Holz-Kunststoff zu Hause. Entformen und Fertigstellen
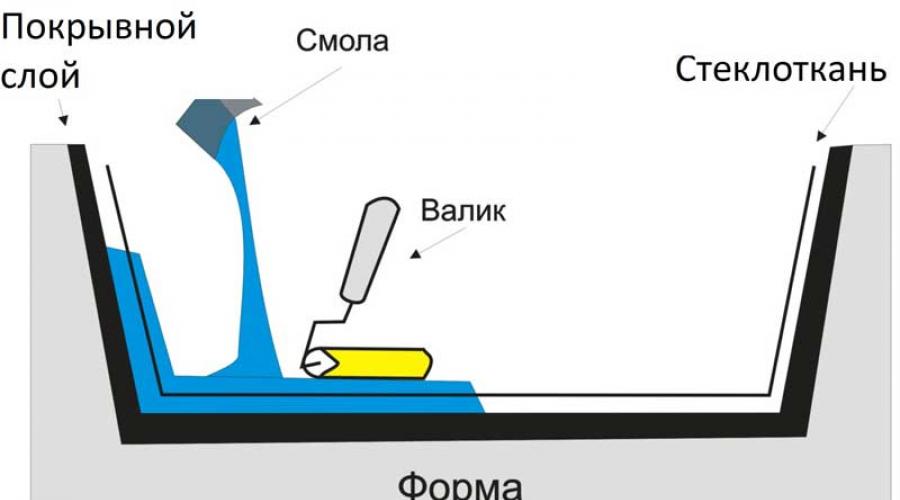
Lesen Sie auch
Bestimmt für die Herstellung einfacher Teile für den Haushaltsbedarf sowie von Elementen komplexer Maschinen und Mechanismen. Insbesondere langlebig und leichtes Material Wird zur Herstellung von Yachtrümpfen, Bodykits für Autos und Motorräder sowie Flugzeughäuten verwendet.
Glasfaser besteht aus einem Verstärkungselement, Glasfaser, und einem Füllstoff, Polymerharz. Fiberglas ist eine Ansammlung von Fasern, die auf besondere Weise angeordnet sind. durchnässt Epoxidharz . Abhängig von der Dicke kann das Material Gewicht haben Quadratmeter von 300 bis 900 Gramm.
Handformverfahren
Im modernen industrielle Produktion Es kommen verschiedene Technologien zur Glasfaserherstellung zum Einsatz.
Für die Herstellung von Glasfaserteilen mit eigenen Händen eignet sich am besten das Handformen. Die Arbeitstechnologie erfordert keinen Einsatz komplexer Geräte und teurer Materialien.
Um Glasfaser mit der manuellen Formmethode mit Ihren eigenen Händen herzustellen, müssen Sie eine konsequente Leistung erbringen Nächste Schritte funktioniert:
- Materialauswahl;
- Schneiden von Glasfaser;
- Erzeugen einer Trennschicht in der Matrix;
- Schaffung einer Deckschicht;
- Glasfaser in die Matrix einlegen;
- Auftragen einer Polymerzusammensetzung;
- Wiederholen Sie die beiden vorherigen Schritte erforderliche Menge Zeiten (abhängig von der Dicke des Produkts);
- Trocknen des Produkts;
- Entfernen des Produkts aus der Form;
- Endbearbeitung (falls erforderlich).
Das Hauptmerkmal der Handformmethode ist hochgradig Qualitätsabhängigkeiten fertiges Teil vom Können des Darstellers ab. Um ein möglichst vollständiges Bild der Selbstherstellung zu erhalten, ist es notwendig, jeden Schritt im Detail zu betrachten.
Auswahl an Materialien
Die Art des Matrixmaterials wird abhängig von der Anzahl der seriengefertigten Teile gewählt. Für die einmalige Formgebung kann die Matrize aus Gips bestehen. Wenn mehr als tausend Proben hergestellt werden müssen, wird eine Stahlmatrix bestellt. Zu Hause ist die Matrize oft ein Abguss des Originalmodells. Am bequemsten ist es, mit der oben beschriebenen Technologie einen Gipsverband aus Glasfaser herzustellen.
Die Wahl des Glasfasertyps hängt von den Anforderungen an die Festigkeit und ästhetischen Eigenschaften des Endprodukts ab. Stoffe mit feinen Fasern verleihen der Oberfläche ein glattes, glänzendes Aussehen und die Verwendung von grobem Fiberglas sorgt für eine hohe Festigkeit.
Die Zusammensetzung des Polymerharzes wird ebenfalls basierend auf dem Zweck und den Betriebsbedingungen des Teils bestimmt. Dafür ist der Polymerfüllstoff verantwortlich technische Eigenschaften Glasfaser, wie zum Beispiel:
- Produktfarbe;
- Grad der Wasserdichtigkeit;
- Betriebstemperaturbereich;
- Exposition gegenüber chemischen Reagenzien und Umgebungen;
- Empfindlichkeit gegenüber ultravioletter Strahlung;
- Grad der Zerbrechlichkeit, Weichheit und Schlagfestigkeit des Produkts.
Vorbereitung von Glasfaser
Der Zuschnitt von Glasfaser erfolgt nach einer Schablone aus dickem Karton entsprechend den Abmessungen der Matrize. Wenn das Produkt eine komplexe Form hat, ist es ausnahmsweise zulässig, Glasfaserzuschnitte zu verwenden, die aus mehreren einzelnen Elementen bestehen.
Abhängig von der Dicke des Teils wird es vorbereitet erforderliche Anzahl an Materialschichten, die an einem bequemen, leicht zugänglichen Ort in der Reihenfolge ihrer Entstehung in der Matrix gespeichert werden. Wenn zwischen dem Schneiden von Glasfaser und dem Formen von Produkten eine Pause von mehreren Tagen liegt, müssen die Lagerbedingungen des Materials genau eingehalten werden.
Trennschicht
Die auf der Oberfläche der Matrizenform aufgebrachte Trennschicht dient dazu, die Möglichkeit einer sicheren Entnahme des fertigen Produkts nach der Festigkeitssteigerung zu gewährleisten. Das Material, aus dem die Trennschicht besteht, ist häufig Gel oder Autowachs.
Deckschicht
Zum Verlegen der oberen und nachfolgenden Glasfaserschichten wird Epoxid- oder Polyesterharz verwendet. Die Komponenten werden nach den technischen Vorschriften des Herstellers gemischt und infundiert. Die vorbereitete Zusammensetzung muss innerhalb von 15 Minuten verbraucht werden, daher wird das Harz für jede weitere Schicht neu vorbereitet.
Die Deckschicht ist die erste in die Matrix eingebrachte Schicht und gleichzeitig die oberste Schutzschicht des Produkts. Seine Dicke sollte nicht mehr als 0,4 mm betragen, um Risse während des Trocknungsprozesses zu vermeiden. Der Trocknungsprozess der Beschichtungsschicht dauert so lange, bis eine gelatineartige, klebrige Masse entsteht.
Glasfaser verlegen und mit Harz imprägnieren
Nach Erreichen der erforderlichen Konsistenz der Deckschicht wird das geschnittene Glasgewebe in die Matrizenform eingelegt. Die erste Glasfaserschicht ist die dünnste (300 g/m2), was für die glatteste Oberfläche des Produkts sorgt.
Das Glasfasergewebe muss allen Biegungen der Matrixform exakt folgen, ohne dass es zu Delaminierungen und zur Bildung von Lufteinschlüssen kommt.
Nach dem Verlegen wird eine Schicht Polymerharz auf die Glasfaser aufgetragen und die resultierende Form zur besseren Imprägnierung und zum Ausdrücken von Luftblasen mit einer speziellen Walze gerollt. Die nächste Glasfaserschicht wird aufgetragen, ohne auf das Trocknen des Harzes zu warten. Anschließend wird der Vorgang des Vorbereitens und Auftragens der Polymerzusammensetzung wiederholt.
Abhängig von der Dicke und der erforderlichen Festigkeit des Produkts wird eine unterschiedliche Anzahl von Glasfaser- und Imprägnierungsschichten gebildet. Als letzte Schicht wird Glasfilz oder dünnes Glasfaservlies verwendet.
Entformen und Fertigstellen
Das Entfernen des Produkts aus der Matrix muss erfolgen, nachdem das Material an Festigkeit gewonnen hat, um Verformung und Delaminierung zu vermeiden. IN normale Bedingungen Die Trocknungszeit für Glasfaser beträgt 12 bis 24 Stunden. Diese Zeit kann durch Aufwärmen der Matrix verkürzt werden Infrarot-Strahler, oder indem man es in eine Trockenkammer legt.
Die Endbearbeitung umfasst das Beschneiden und Schleifen der Kanten des Produkts.
Bei Bedarf kann das Produkt mit Grundfarbe im gewünschten Farbton lackiert werden. Fertige Materialien können mit Polymerklebstoffen zusammengeklebt werden.
Regeln für die Arbeitsausführung
Zum Erhalten hochwertige Glasfaserprodukte Bei der Durchführung der Arbeiten ist Folgendes zu berücksichtigen:
- die Oberflächen der Matrix und der Behälter zur Herstellung des Polymerharzes müssen sauber sein;
- Luftblasen, die mit einer Rolle nicht herausgedrückt werden konnten, müssen durch Schneiden mit einer Klinge entfernt werden;
- die verwendeten Werkzeuge (Rollen, Pinsel) sowie Behälter zum Mischen der Komponenten müssen unmittelbar nach Gebrauch mit Aceton gewaschen werden, um Harzreste zu entfernen;
- Zur Einhaltung sollte die Temperatur im Arbeitsraum nicht unter 20 Grad liegen die richtige Technologie Harzpolymerisationsprozess;
- Polymerkomponenten können giftige Dämpfe enthalten, daher müssen die Arbeiten in einem gut belüfteten Bereich durchgeführt werden;
- Zum Schutz der Hände sollten Handschuhe getragen werden;
- Das Rauchen und die Verwendung offener Flammen sind in den Räumlichkeiten verboten.
Das Video unten erklärt gut, wie man Glasfaser mit eigenen Händen herstellt. Als Beispiel stellt der Autor des Videos „Wimpern“ für Autoscheinwerfer her.
Leider enthält das uns allen bekannte und weltweit verbreitete Plastik gesundheitsschädliche Stoffe. Darüber hinaus werden bei der Herstellung Erdölprodukte verwendet. Allerdings gab es bis vor Kurzem kaum eine Alternative zu diesem günstigen Material. Sicherlich, neue Baumaterialien erscheinen ständig. Dabei handelt es sich um Sperrholz, Spanplatten und Faserplatten. Auch in der Betonindustrie, Metallurgie und Glasindustrie gibt es Neuheiten. Allerdings sind sie hinsichtlich der Kosten und damit der Verfügbarkeit noch weit von Kunststoff entfernt.
Zu Beginn des neuen Jahrtausends gelang es Wissenschaftlern, ein grundlegend neues Strukturmaterial zu schaffen, das in den kommenden Jahrzehnten den üblichen Kunststoff fast vollständig ersetzen kann. Das thermoplastischer Holz-Polymer-Verbundwerkstoff(DPKT oder DPK) und bei gewöhnlichen Menschen - „flüssiger Baum“. Zur Herstellung werden primäre (sekundäre) Rohstoffe PP, PE oder PVC sowie Holzzusätze (Holzmehl, andere Pflanzenfasern) und Hilfsstoffe verwendet. Die Wirkung übertraf alle Erwartungen. Neuestes Material nicht nur umweltfreundlich (Schwefelgehalt um 90 % reduziert), sondern auch kombinativ beste Eigenschaften Holz und Kunststoff hielten die Kosten relativ niedrig.
Laut Experten beträgt das jährliche Wachstum des WPC-Umsatzes weltweit etwa 20 %. Was ist also dieses Wunder, auf das Architekten, Designer und Produktionsmitarbeiter so lange gewartet haben? Versuchen wir es herauszufinden.
Bewerbung und Abwicklung
Aufgrund seiner Eigenschaften wird Holz-Polymer-Verbundwerkstoff hervorragend in den unterschiedlichsten Bereichen eingesetzt. Die Materialien zeichnen sich durch Gleichmäßigkeit und Glätte der Oberfläche, Plastizität, Beständigkeit gegen atmosphärische und biologische Einflüsse aus und ihre Lebensdauer selbst unter rauen Außenbedingungen beträgt 50 Jahre.
All dies ermöglicht die Verwendung von WPC bei der Herstellung verschiedener Architektur- und Baumaterialien: Sockelleisten, Verkleidungen, Fensterbänke, Profile, dekorative Elemente sowie Füllstoffe.
Sie stellen gebrauchsfertige Produkte aus WPC her: Laminat, Bodenbeläge, Möbelbleche, Möbel, Kabelkästen, Mehrkammerfensterprofile und sogar Terrassendielen – ein Profil für die Herstellung von Liegeplätzen und Piers.
Die physikalischen und mechanischen Eigenschaften des Holz-Polymer-Verbundwerkstoffs bieten zahlreiche Möglichkeiten für seine Verarbeitung. Material verliert nicht seine Form und Festigkeit, nimmt bis zu 4 % Feuchtigkeit auf. Daraus lassen sich leichte, hohle Dinge herstellen. Die Montage erfolgt mit Nägeln und Schrauben sowie speziellen Riegeln.
Darüber hinaus kann WPC mit Furnier furniert, mit Folien und Kunststoffplatten laminiert, mit beliebigen Farben und Lacken bemalt werden, um verschiedene Arten zu erhalten dekorative Effekte, Hinzufügen von Pigmenten zur Zusammensetzung usw.
Aus WPC gewonnene Produkte sind leicht zu bearbeiten. Sie lassen sich leicht sägen, bohren, schneiden, kleben, miteinander verschweißen, biegen (nach dem Vorwärmen mit einem Brenner) und, wenn dem Material Mehl hinzugefügt wird, weiches Gestein Holz oder zellulosehaltige Abfälle verleihen dem Produkt zusätzlich eine erhöhte Plastizität.
Schließlich WPC, zusätzlich zu der Ästhetik, die es verleiht Aussehen Es ist auch angenehm für die Sinne und hat einen leicht holzigen Duft.
Produktionstechnologie
Zur Herstellung eines Holz-Polymer-Verbundwerkstoffs werden mehrere Komponenten verwendet. In erster Linie handelt es sich dabei natürlich um zerkleinertes Holz oder zellulosehaltige Rohstoffe. Das heißt, es kann sich nicht nur um Holz, sondern auch um Mais, Reis, Sojabohnen, Stroh, Papier, Sägemehl usw. handeln. Der zweite Hauptbestandteil von WPC sind synthetische Bindemittel. Dazu gehören: Polyethylen, PVC-Propylen usw. Die übrigen Komponenten sind zusätzliche Zusatzstoffe, deren Zusammensetzung je nach Verwendungszweck des zukünftigen Produkts variiert. Zu den gebräuchlichsten gehören: Farbstoffe, Pigmente, Antioxidantien, stoßfeste Modifikatoren, Licht- und Wärmestabilisatoren, Flammschutzmittel und Antiseptika zum Schutz vor Feuer und Fäulnis, hydrophobe Zusätze zur Widerstandsfähigkeit gegen Feuchtigkeit, Schaummittel zur Reduzierung der Dichte von WPC.
Holzpartikelvolumen im Material können zwischen 30 und 70 % liegen und ihre Größe beträgt 0,7 bis 1,5 mm. Feinfraktionen werden bei der Herstellung fertiger Profile verwendet, die keiner zusätzlichen Oberflächenbehandlung bedürfen. Mittlere Modelle eignen sich zum Bemalen oder Veredeln mit Furnier. Grob – aus technischen Gründen.
Volumen synthetischer Bindemittel x variiert ebenfalls und kann zwischen 2 und 55 % liegen. Dies hängt wiederum vom Zweck des zukünftigen Produkts ab. Was zusätzliche Zusatzstoffe betrifft, so darf ihr Volumen im Material 15 % nicht überschreiten.
Übrigens ist es deutschen Entwicklern vor nicht allzu langer Zeit gelungen, zu produzieren „flüssiges Holz“ von idealer Qualität. Spezialisten des Fraunhofer-Instituts haben es aus Lignin hergestellt. Dieses Material wird aus Holz gewonnen. DPK hat angerufen Arboform ist ein völlig ungiftiges Produkt. Wenn außerdem ein gewöhnlicher Holz-Polymer-Verbundstoff 3-4 Mal verarbeitet werden kann, dann kann dieser bis zu 10 Mal verarbeitet werden. Warum machen wir das? Tatsache ist, dass in China die WPC-Industrie wächst wie nirgendwo sonst auf der Welt. Und wenn in Europa und den USA die hergestellten Materialien einer Reihe von Tests unterzogen werden, dann kümmert man sich im Reich der Mitte nicht darum und beliefert den Markt, auch den internationalen, mit einem Produkt von nicht bester Qualität.
Nun ungefähr Anlagen zur Herstellung von WPC. Zur Standardausstattung gehören: ein Doppelschneckenextruder, eine Formdüse, ein Kalibrier- und Kühltisch, eine Zugvorrichtung, eine Längenschneidevorrichtung, eine Breitenteilung (falls erforderlich) und ein Stapler. Die gesamte Linie ist kompakt und die Steuerung erfolgt in der Regel vollautomatisch. Einige Modelle umfassen außerdem: eine Mühle (Rohstoffmühle), einen Rohmaterial-Autoloader und einen Mischer.
Hersteller solcher Leitungen und Module sind vor allem Chinesische Unternehmen. Die Spitzenreiter unter ihnen sind WPC, Zhangjiagang City Boxin Machinery usw. Die Qualität der Ausrüstung ist auf einem ordentlichen Niveau, zumal die Hauptkomponenten dafür von europäischen Maschinenbaubetrieben hergestellt werden.
In diesem Artikel verraten wir Ihnen, wie Sie einen beliebten machen können Baumaterial Sie können es mit Ihren eigenen Händen als flüssigen Baum bezeichnen, und wir werden auch alle seine Vorteile beschreiben.
Jeder Heimwerker weiß, dass Holzprodukte Angst haben negative Auswirkungen verschiedene Betriebsfaktoren, was ihre Lebensdauer verkürzt. Gleichzeitig wird der Baum von vielen Menschen und professionellen Bauherren geliebt. Es ist umweltfreundlich, sieht gut aus, lädt den Menschen mit positiver Energie auf und hat viele weitere Vorteile.
Flüssiges Holzprodukt
Aus diesen Gründen versuchen Experten seit längerem, einen Ersatz für Naturholz zu finden, der optisch und physisch nicht von Holz zu unterscheiden ist und dieses in Qualität und Widerstandsfähigkeit gegen Einflüsse übertrifft Naturphänomen. Die Recherche war erfolgreich. Modern chemische Industrie war in der Lage, ein einzigartiges Material zu schaffen – Flüssigkeit künstlicher Baum. Es brach buchstäblich in die Baumärkte auf der ganzen Welt ein. Mittlerweile wird solches Holz unter der Abkürzung WPC (Wood-Polymer-Composite) verkauft. Das Material, an dem wir interessiert sind, besteht aus folgenden Komponenten:
- Bei der geschredderten Holzbasis handelt es sich im Wesentlichen um Verarbeitungsabfälle Naturholz. Ein gegebener Verbundstoff kann 40 bis 80 % davon enthalten.
- Thermoplastische chemische Polymere – Polyvinylchloride, Polypropylene und so weiter. Mit ihrer Hilfe wird der Holzsockel zu einer einzigen Komposition zusammengesetzt.
- Zusatzstoffe werden Zusatzstoffe genannt. Dazu gehören Farbstoffe (färben das Material im gewünschten Farbton), Schmiermittel (erhöhen die Feuchtigkeitsbeständigkeit), Biozide (schützen Produkte vor Schimmel und Schädlingen), Modifikatoren (erhalten die Form des Verbundwerkstoffs und sorgen für seine hohe Festigkeit), Schaummittel (ermöglichen, dass Sie können das Gewicht von WPC reduzieren).
Diese Komponenten werden in bestimmten Anteilen gemischt, stark erhitzt (bis die Zusammensetzung flüssig wird), die Mischung polymerisiert und dann in spezielle Formen gefüllt hoher Druck und cool. Das Ergebnis all dieser Maßnahmen ist eine Zusammensetzung mit Flexibilität und ausgezeichneter Korrosionsbeständigkeit, Elastizität und Schlagfestigkeit. Und was am wichtigsten ist: WPC hat ein magisches Aroma von Naturholz sowie eine Farbe und Textur, die mit echtem Holz identisch sind.
Wir hoffen, dass Sie in unserem kurzen Testbericht verstanden haben, wie flüssiges Holz hergestellt wird und was es ist. Die beschriebenen Holz-Polymer-Produkte zeichnen sich durch eine Reihe betrieblicher Vorteile aus. Im Folgenden stellen wir die wichtigsten vor:
- erhöhte Widerstandsfähigkeit gegen mechanische Beschädigungen;
- Temperaturwechselbeständigkeit (WPC-Produkte können sowohl bei +150 °C als auch bei -50 °C verwendet werden);
- hohe Feuchtigkeitsbeständigkeit;
- Leichtigkeit Selbstverarbeitung und Installation (zu diesem Zweck wird ein Werkzeug verwendet, um mit Naturholz zu arbeiten);
- lange Lebensdauer (mindestens 25–30 Jahre);
- große Farbauswahl;
- Resistenz gegen Pilze;
- einfache Wartung (der Verbundwerkstoff ist leicht zu reinigen, er kann abgekratzt, lackiert und in jeder Farbe gestrichen werden).
Dekoration aus Holz und Kunststoff
Ein wichtiger Vorteil von Holz-Kunststoff ist, dass es einen sehr günstigen Preis hat. Dies wird durch die Verwendung recycelter Produkte (zerkleinertes Sperrholz, Sägemehl, Späne) bei der Herstellung von WPC erreicht. Es ist schwierig, in dem von uns betrachteten Material Mängel zu finden, aber es gibt sie. Was würden wir ohne es tun? Holz-Kunststoff hat nur zwei Nachteile. Erstens ist beim Einsatz in Wohnräumen auf eine hochwertige Belüftung zu achten. Zweitens wird WPC nicht für den Einsatz empfohlen, wenn gleichzeitig und dauerhaft hohe Luftfeuchtigkeit und erhöhte Lufttemperatur im Raum vorhanden sind.
Die besonderen Eigenschaften eines Verbundstoffs aus Holz und Kunststoff ermöglichen die Herstellung verschiedener Bauprodukte daraus. Dieses Material wird für die Herstellung von Außenverkleidungen, glatten, hohlen, gewellten und massiven Terrassendielen (d. h. Terrassendielen) verwendet. Aus WPC werden schicke Balustraden, aufwendige Geländer, sichere Zäune, luxuriöse Pavillons und viele andere Konstruktionen hergestellt. Mit Holz-Kunststoff können Sie die Innenräume Ihres Wohnraums luxuriös gestalten und individuell gestalten Vorort wahrhaft schön.
Die Kosten des beschriebenen Verbundwerkstoffs hängen davon ab, welches Polymer für seine Herstellung verwendet wird. Wenn ein Hersteller WPC aus Polyethylen-Rohstoffen herstellt, ist der Preis des fertigen Produkts minimal. Es ist jedoch zu beachten, dass solche Produkte nicht UV-beständig sind. Aber Polyvinylchlorid-Polymere verleihen Holzkunststoff eine hohe Beständigkeit gegen Feuer und UV-Strahlen und machen ihn zudem sehr langlebig. Produkte aus WPC (insbesondere Terrassendielen) werden üblicherweise in nahtlose und mit Nähten unterteilt. Die ersten werden ohne Klammern, Schrauben und andere Hardware montiert. Solche Platten haften einfach aneinander und bilden eine dauerhafte, durchgehende Oberfläche.
Holz-Kunststoff-Material
Um jedoch Produkte mit Nähten zu installieren, müssen Sie Kunststoff oder verwenden Metallverschluss(Am häufigsten fungieren Verschlüsse als solche). WPC-Platten oder -Bretter können hohl oder massiv sein. Für die Gestaltung von Veranden in Privathäusern ist es besser, Produkte mit Hohlräumen zu verwenden. Sie sind leicht und lassen sich ganz einfach selbst bearbeiten. Für den Einbau eignet sich eher Massivholz-Kunststoff, der erheblichen Belastungen standhält an öffentlichen Orten(Böschungen, Sommerrestaurants und -bars, Schiffsdecks), wo ein hohes Verkehrsaufkommen herrscht.
Achten Sie bei der Auswahl von WPC-Platten auf die Dicke ihrer Wände (sie sollte mindestens 4–5 mm betragen), die Höhe der Versteifungsrippen (je höher sie sind, desto zuverlässiger sind die Produkte im Betrieb) und deren Anzahl (Je mehr Rippen, desto stärker das Ergebnis. Design).
Auch die Breite Ihrer Verbundplatten und -bretter sollten Sie mit Bedacht wählen. Hier muss ein Punkt verstanden werden. H Je breiter die von Ihnen gekauften Produkte sind, desto einfacher wird es für Sie, damit zu arbeiten, da für die Installation solcher Dielen deutlich weniger Befestigungsmittel erforderlich sind . Noch mehrere nützliche Tipps Für Sie. Erkundigen Sie sich bei den Verkäufern, aus welchem Sägemehl das WPC hergestellt wurde. Wenn der Hersteller für diese Zwecke Nadelholz verwendet, ist es besser, nach einem anderen Material zu suchen. Warum? Aus dem Grund, dass Verbundwerkstoffe auf Nadelholzbasis als feuergefährlich gelten. Und die Festigkeitseigenschaften solcher Produkte lassen zu wünschen übrig. WPC auf Basis von Recyclingabfällen Laubbäume frei von diesen Nachteilen.
Wenn auf Verbundplatten (Bretter, Platten) deutlich leichte Adern oder Bereiche zu erkennen sind, ist die Betriebssicherheit der Produkte gering. Höchstwahrscheinlich verwendete der Hersteller Holzmehl von geringer Qualität und darüber hinaus schlecht gemahlen. Solche Platten weisen in der Regel eine geringe Wasserbeständigkeit auf. Sie können nicht im Freien verwendet werden. Die unzureichende Qualität des WPC wird auch durch das Vorhandensein einer uneinheitlichen Farbe auf seiner Oberfläche (Flecken, deutlich sichtbare Farbübergänge) angezeigt.
Jetzt kommt der spaßige Teil. Wenn Sie möchten, können Sie zu Hause ganz einfach mit Ihren eigenen Händen ein würdiges Analogon von WPC herstellen. Selbstgemachter Holz-Kunststoff wird aus Sägemehl und gewöhnlichem PVA-Kleber hergestellt und zur Restaurierung verwendet Parkettbrett, Reparatur von Laminatböden, Restaurierung anderer Holzbeläge. Es kann auch zur Herstellung von Rohböden in Pavillons und Nebenräumen verwendet werden.
Verbundmaterial aus Sägemehl und Leim
WPC wird nach folgendem Schema von Hand hergestellt:
- Schleifen Sägespäne in einer Kaffeemühle oder einer Handküchenmühle staubig mahlen.
- Fügen Sie dem zerkleinerten Sägemehl PVA-Kleber hinzu (Anteile - 30 bis 70 %) und mischen Sie diese Komponenten, bis Sie eine Mischung mit der Konsistenz einer Paste erhalten.
- Gießen Sie Farbstoff in die vorbereitete Zusammensetzung (es wird empfohlen, für gewöhnliche Zusätze zu verwenden). Farbe auf Wasserbasis). Alles noch einmal vermischen.
Sie haben also selbstgemachten Holz-Kunststoff hergestellt! Fühlen Sie sich frei, mit dieser Mischung Löcher in die Löcher zu füllen. Holzboden. Nach dem Aushärten des WPC muss die restaurierte Stelle nur noch mit feinkörnigem Schleifpapier angeschliffen werden. Die mit Ihren eigenen Händen erstellte Komposition kann auch für die Gestaltung neuer Böden verwendet werden. Sammeln und stellen Sie selbstgemachtes WPC her benötigte Mengen und die Schalungskonstruktion damit verfüllen. Dicke selbstgemachte Bretter in diesem Fall sollten es mindestens 5 cm sein. Los geht's!
Das Spielvideo „“ kann kostenlos in den Formaten mp4, x-flv, 3gpp heruntergeladen werden. Klicken Sie dazu oben auf die Schaltfläche „Video herunterladen“.
Beschreibung:
Typ – Handwerkszutat; Wo suchen – machen Sie es selbst; Faltbar – ja, 64 Stück pro Stapel. Beschreibung und Funktionen. Jetzt wissen Sie nicht nur, wie man in Minecraft ein Komposit herstellt, sondern auch alle Bastelarbeiten, bei denen es als Zutat involviert ist, daher IndustrialCraft 2 Composite - Minecraft Wiki minecraft -ru Industriehandwerk 2 Komposit-Materialien vom Typ Verbundwerkstoff Stärke Nein Faltbar Ja64 Erster Auftritt. -Minecraft-Wissensdatenbank -Industrial Craft 2 Composite. Wie erstelle ich ein Komposit in Minecraft mir Minecraft Wie erstelle ich ein Komposit in Minecraft? Wie erstelle ich ein Komposit in Minecraft? Überprüfung des Minecraft 1.8.8-Updates – Was ist neu in Minecraft 1.8.8? Wie erstelle ich einen Sattel in Minecraft 1.8.8? Industrial Craft 2 Composite in Minecraft Minecraft Forum Wie man in Minecraft ein Komposit erstellt. Komposit in Minecraft kann durch Komprimieren von Kompositbarren mit einem Kompressor erhalten werden. So erstellen Sie ein Komposit in Minecraft Allin Minecraft Komposit ist ein Gegenstand, der vom IndustrialCraft²-Mod hinzugefügt wurde. Es wird durch Komprimieren von Verbundwerkstoffbarren in einem Kompressor hergestellt. Wird bei der Herstellung vieler hochtechnologischer und langlebiger Blöcke und Gegenstände verwendet. Industrial Craft 2 Composite – Minecraft Wiki m craft Forum für Gamer und Betrüger: Cheats, Mods, Anleitungen. World of Tanks, Warface, Armored Empfehlen Sie ein Spiel ähnlich wie Trove oder Minecraft 3 Nachrichten 19. Januar 2016 Was ist Wipe in Minecraft Server? Was ist Wipe 2-Nachrichten 19. Januar 2016 Wie man Bronze und Komposit herstellt! - Wie erstelle ich ein Komposit in Minecraft? Wir stellen Nano-Rüstungen, Jetpack-Elektro und Nano-Säbel her – ProFIT31ru. Wie man in Minecraft IC2+BC3 eine Iridium-Verbundpflanze herstellt – GameCity. So erstellen Sie eine Startnummer in Minecraft. So erstellen Sie eine Startnummer in Minecraft. Minecraft in seiner klassischen Form ist ein „Mining“-Spiel, bei dem eines der meisten wichtige Aufgaben Es handelt sich um eine Variante des Bergbaus. Die restlichen vier Plätze werden mit Iridium-Verbundplatten belegt. Wie erstelle ich ein Komposit in Minecraft? - Crafting in Minecraft az Minecraft Composite ist ein Gegenstand, der vom Industrial Craft²-Mod hinzugefügt wurde. Es wird durch Komprimieren von Verbundwerkstoffbarren in einem Kompressor hergestellt. Wird bei der Herstellung vieler hochtechnologischer und langlebiger Blöcke und Gegenstände verwendet. Wie man in Minecraft Verbundwerkstoffe herstellt - 14
Video für Mobiltelefon, Smartphone, Tablet etc. können online, kostenlos und ohne Registrierung eingesehen werden. Und auch herunterladen mobiles Video im mp4-, x-flv- und 3gpp-Format!
Bitte hinterlassen Sie Ihren Kommentar oder Ihre Bewertung zu diesem Video! Es wird den Autor sehr interessieren, was Sie über sein Werk denken.