An den Adressaten pünktlich ab. Logistiktechnik JIT - Just-in-time (Just in time)
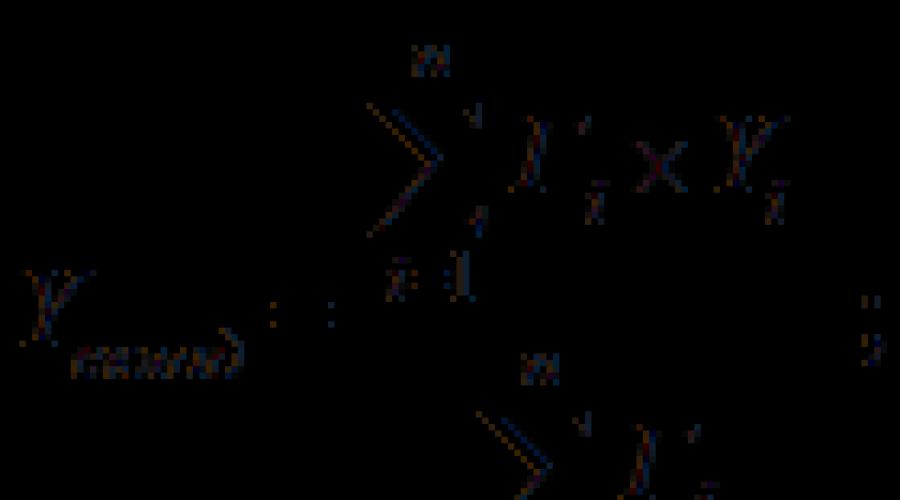
Eines der weltweit am weitesten verbreiteten Logistikkonzepte/-technologien ist das Konzept Gerade rechtzeitig - JIT (Pünktlich ) . Die Entstehung dieses Konzepts geht auf die späten 1950er Jahre zurück, als das japanische Unternehmen Toyota Motors und dann andere japanische Automobilhersteller begannen, das System aktiv umzusetzen. KANBAN.
Der ursprüngliche Slogan des Konzepts JIT potenzielle Bestände an Materialien, Komponenten und Halbzeugen im Produktionsprozess der Montage von Autos und ihren Haupteinheiten wurden ausgeschlossen. Die ursprüngliche Aufgabenstellung sah so aus: Liegt ein Produktionsplan vor, dann gilt es, die Bewegung der Materialflüsse so zu organisieren, dass alle Materialien, Komponenten und Halbzeuge in der richtigen Menge am richtigen Ort (auf der Baugruppe) ankommen Linie) und pünktlich zur Produktion bzw. Montage fertiger Produkte. Bei dieser Problemstellung erwiesen sich große Sicherheitsvorräte und das Einfrieren der Unternehmensmittel als unnötig.
Konzeptionell JIT-Der Ansatz diente als Grundlage für die spätere Einführung solcher Logistikkonzepte/-technologien wie Schlanke Produktion, („flache“ oder „dünne“ Produktion) und Mehrwertlogistik – „Wertschöpfungslogistik“.
Es gilt, die Grundidee der Methode hervorzuheben und zu charakterisieren, die auf drei Prämissen basiert (deren Richtigkeit mehrfach empirisch bestätigt wurde).
Erstens wird davon ausgegangen, dass die Nachfrage der Verbraucher nach Fertigprodukten nicht ihren vorab angesammelten Reserven entsprechen sollte, sondern den Produktionskapazitäten, die bereit sind, Rohstoffe und Materialien zu verarbeiten, die fast „von den Rädern“ kommen. Dadurch wird das Volumen der Produktionsbestände, die als eingefrorene Kapazität gelten, minimiert.
Zweitens ist bei minimalen Lagerbeständen eine kontinuierliche Rationalisierung der Organisation und Verwaltung der Produktion erforderlich, da ein hohes Lagerbestandsvolumen gewissermaßen Fehler und Mängel in diesem Bereich, Produktionsengpässe, unsynchronisierte Abläufe und ungenutzte Produktion verschleiert Kapazitäten, unzuverlässige Arbeit von Lieferanten und Vermittlern.
Drittens sollte man zur Beurteilung der Effizienz des Produktionsprozesses neben der Höhe der Kosten und der Produktivität der Mittel auch den Umsetzungszeitraum des Antrags, die sogenannte Dauer des gesamten Produktionszyklus, berücksichtigen. Kurze Fristen für die Implementierung von Anwendungen erleichtern die Unternehmensführung und tragen zu einer Steigerung der Wettbewerbsfähigkeit bei, da schnell und flexibel auf Änderungen der äußeren Bedingungen reagiert werden kann.
Im Gegensatz zu traditionellen Managementmethoden, nach denen das zentrale Glied in der Produktionsplanung Produktionsaufgaben an alle Abteilungen und Industrieeinheiten verteilt, mit der „ Pünktlich» Die zentrale Planung betrifft nur das letzte Glied der Logistikkette, also das Fertigproduktlager. Alle anderen Produktions- und Liefereinheiten erhalten Aufträge direkt von der nächsten Einheit, die näher am Ende der Lieferkette liegt. Hat beispielsweise ein Fertigwarenlager einen Antrag (was einer Erteilung eines Produktionsauftrags gleichkommt) für eine bestimmte Anzahl von Produkten an die Montagehalle gestellt, erteilt die Montagehalle Aufträge zur Produktion von Baugruppen an die Weiterverarbeitungshallen und die Kooperation Abteilung usw.
Dies bedeutet, dass der Fertigungsauftrag immer an die Abteilung erteilt wird, die das Teil verwendet (bzw. bearbeitet). Somit geht dem Materialfluss von der „Quelle“ zum „Verbraucher“ der Informationsfluss in die entgegengesetzte Richtung voraus, d. h. Produktion“ Pünktlich» vorangestellt mit Informationen « Pünktlich».
Methode " Pünktlich hat sich als so effektiv erwiesen, dass mittlerweile alle großen Organisationen Elemente dieses Ansatzes in gewissem Umfang nutzen. Der traditionelle Ansatz zur Arbeitsorganisation geht davon aus, dass das Inventar ein wichtiges Element des gesamten Systems ist und sicherstellt, dass der Betrieb nicht ausfällt. MRP reduziert den Lagerbestand, indem es den Masterplan so nutzt, dass eine bessere Übereinstimmung zwischen Materialvorräten und deren Nachfrage gewährleistet wird und dennoch ein gewisser Sicherheitsbestand für den Fall unvorhergesehener Probleme aufrechterhalten wird. Je höher der Grad der Übereinstimmung zwischen Angebot und Nachfrage ist, desto weniger Lagerbestände werden wir natürlich benötigen. Wenn wir das Missverhältnis zwischen Angebot und Nachfrage vollständig beseitigen können, benötigen wir überhaupt keine Lagerbestände. Darauf basiert die Arbeit“ Pünktlich".
Ein interessantes Beispiel, das die Essenz der Arbeit veranschaulicht. Pünktlich", besteht darin, einen Gasherd mit Flaschengas und Gas zu betreiben, das über eine Rohrleitung zugeführt wird. Im ersten Fall besteht manchmal eine Diskrepanz zwischen der Verfügbarkeit von Brennstoff in der Flasche und dem Bedarf daran. Um Unterbrechungen zu vermeiden, ist es notwendig, dies zu tun Gasflaschen im Voraus kaufen, also eine Reserve bilden Im zweiten Fall entspricht das Gasangebot genau der Nachfrage und der Verbraucher verfügt über keine Kraftstoffreserven.
Dieses Konzept basiert auf der Annahme, dass Vorräte durch schlechtes Management und schlechte Arbeitskoordination entstehen und daher Probleme in den Vorräten verborgen sind. Daraus folgt die Schlussfolgerung, dass es notwendig ist, die Gründe für die Differenz zwischen Angebot und Nachfrage zu finden, die Ausführung der Operationen zu verbessern, woraufhin die Bestände verschwinden. In einem weiteren Sinne JIT betrachtet das Unternehmen als eine Reihe von Problemen, die die effektive Ausführung von Vorgängen beeinträchtigen, z. B. lange Vorlaufzeiten, Instabilität der Auftragslieferung, unausgeglichene Abläufe untereinander, begrenzte Kapazität, Geräteausfälle, fehlerhafte Materialien, Arbeitsunterbrechungen, unzuverlässige Lieferanten , schlechte Qualität der fertigen Produkte, zu viel Papierkram und vieles mehr. Manager versuchen, diese Probleme zu lösen, indem sie Reserven schaffen, zusätzliche Kapazitäten kaufen, Ersatzausrüstung installieren, Feuerwehrleute einladen usw. In Wirklichkeit verbergen diese Maßnahmen jedoch nur die Ursachen der Probleme. Der konstruktive Ansatz besteht darin, die wirklichen Probleme zu identifizieren und zu lösen.
Konzept Gerade rechtzeitig(Pünktlich) führt zu einem Meinungswandel in folgenden Bereichen:
Vorräte. Organisationen müssen Probleme identifizieren und lösen, die zu Lagerbeständen führen und ein Minimum an Materialressourcen (Nullbestände), laufende Arbeiten und Fertigwaren anstreben.
Qualität. Es ist nicht notwendig, ein akzeptables Maß an Mängeln zu erreichen, sondern auf der Grundlage eines integrierten Qualitätsmanagements deren völlige Abwesenheit.
Lieferanten. Kunden müssen sich vollständig auf ihre Lieferanten verlassen und daher langfristige Partnerschaften mit einer kleinen Anzahl zuverlässiger Lieferanten und Spediteure aufbauen.
Volumen der Chargen. Es muss nach Möglichkeiten gesucht werden, das Volumen der Produktionschargen zu reduzieren, um kurze Produktionszyklen zu erreichen, damit sich keine Überproduktion in den Lagerbeständen der fertigen Produkte ansammelt.
Auftragserfüllungszeit. Es ist notwendig, die Durchlaufzeiten zu verkürzen, um Unsicherheiten zu reduzieren, die bei langen Lieferzeiten die Situation verändern können.
Zuverlässigkeit. Alle Vorgänge müssen kontinuierlich und fehlerfrei durchgeführt werden, d. h. Es sollte keine Geräteausfälle, Defekte, Fehlzeiten usw. geben.
Arbeitskräfte. Ein Geist der Zusammenarbeit ist notwendig, sowohl zwischen Arbeitnehmern als auch zwischen Managern und Arbeitnehmern, denn... Das Wohlergehen aller hängt vom Gesamterfolg bei der Arbeit ab; alle Mitarbeiter sollten gleich und fair behandelt werden. Jede kreative Initiative eines Mitarbeiters hinsichtlich möglicher Arbeitsverbesserungen wird gefördert.
Die Informationsunterstützung sollte einen schnellen Informationsaustausch und die Synchronisierung aller Prozesse der Materialversorgung, Produktion und Montage sowie der Lieferung fertiger Produkte ermöglichen.
Auf diese Weise, JIT- Dies ist nicht nur eine Möglichkeit, Lagerbestände zu minimieren, sondern auch die Verschwendung jeglicher Art von Ressourcen zu vermeiden, die Koordination zu verbessern und die betriebliche Effizienz zu steigern.
Eine flexible Arbeitsorganisation ist nur eine der notwendigen Voraussetzungen für die Umsetzung von JIT. Bevor überhaupt mit der Implementierung fortgefahren wird, muss festgestellt werden, ob JIT für das Unternehmen eine vorteilhafte Möglichkeit ist, die Produktion zu organisieren.
Wann ist das Just-in-Time-System von Vorteil? Häufiges Missverständnis: JIT ist nur auf Industrien mit hohem Volumen anwendbar. Das System hat sich zwar in der Massenproduktion als äußerst effektiv erwiesen, wird aber auch bei kleinen und mittleren Produktionsmengen erfolgreich eingesetzt. JIT basiert auf sich wiederholenden Abläufen und kann daher bei der Herstellung jedes Produkts verwendet werden, bei dem die Nachfrage eine Produktion in Zyklen wirtschaftlich sinnvoll macht. Um JIT anzuwenden, muss die Nachfrage zwei Anforderungen erfüllen:
- 1. Lautstärke. Das Verkaufsvolumen einer Produktlinie muss hoch genug sein, damit es sich lohnt, eine eigene Reihe miteinander verbundener Arbeitsstationen für die Produktion einzurichten, und stabil genug, um sicherzustellen, dass die Produktion über lange Zeiträume konstant bleibt.
- 2. Sortiment. Die Anzahl der Varianten bzw. Modelle innerhalb einer Produktlinie sollte gering sein, damit eine gemischte Produktlinie hergestellt werden kann.
Mengen- und Sortenanforderungen hängen vom einzelnen Unternehmen und seinen Bedingungen ab, wie z. B. Produktkomplexität, Komplexität des Herstellungsprozesses, Kapitalintensität, Kundenerwartungen und Ressourcenverfügbarkeit. Die Ermittlung der Rentabilität von JIT erfordert eine umfassende Analyse und kann nicht auf eine vereinfachte Auswahl nach den Kriterien Volumen – Sortiment – technischer Prozess reduziert werden.
Manchmal kann die Beschränkung der Anzahl an Modellen und Modifikationen durch modulare Designs umgangen werden. Die Produktion basiert auf einer kleinen Anzahl von Modulen, die in den meisten produzierten Modellen verwendet werden und den Großteil der Wertschöpfung während des Produktionsprozesses übernehmen. Aus diesen Modulen wird ein grundlegender Produktionsplan erstellt; Sobald der Käufer eine Bestellung für ein bestimmtes Modell erhält, werden diesem die entsprechenden Teile und Komponenten hinzugefügt. So stellte ein amerikanischer Schrankhersteller von der Serienfertigung auf die JIT-Produktion um, obwohl die jährliche Nachfrage nach seiner gesamten Produktpalette 2.400 Einheiten nicht überstieg. und bestand aus 1500 verschiedenen Konfigurationen. Nach der Neugestaltung des Produkts begann das Unternehmen mit der Produktion von 20 Modulen, aus denen dann 95 % aller fertigen Produkte hergestellt wurden. Die Produktion der Module ist nach dem JIT-System organisiert; ihre Modifikation auf Kundenwunsch erfolgt innerhalb eines Tages am Endmontageort. Die Lieferzeit der Bestellung wurde von 3 Wochen auf 1 Tag verkürzt und die Produktionskosten wurden um 25 % gesenkt. Durch den modularen Aufbau und die Einzigartigkeit in letzter Minute war das Unternehmen in der Lage, JIT in einer Umgebung mit geringem Volumen und hohem Mix zu implementieren.
Was verhindert JIT. Die Chancen auf eine erfolgreiche Implementierung von JIT sind gering. Im Jahr 1992 führte Arthur D. Little eine Umfrage unter 500 amerikanischen Fertigungsunternehmen durch und stellte fest, dass die meisten von ihnen erfolglose Versuche unternommen hatten, JIT-Prinzipien umzusetzen. Dafür gibt es viele Gründe. Das wichtigste Hindernis ist bereits aus Abb. ersichtlich. 4 ist eine große Anzahl von Programmen, die ordnungsgemäß entwickelt und in ein Ganzes integriert werden müssen. Dies gelingt nur den anpassungsfähigsten aller Organisationen. JIT stellt einen bedeutenden kulturellen Wandel gegenüber der traditionellen Produktionsweise dar. Früher als notwendig und höchst wünschenswert erachtete Faktoren wie Sicherheitsbestände werden heute als Verluste angesehen. Die systematische Beseitigung aller Arten von Nachlässigkeiten in der Produktion führt zu einem anspruchsvolleren und stressigeren Umfeld, und dazu kommt der ständige Verbesserungsbedarf. Zusätzlicher Stress entsteht durch die radikal neuen Rollen von Ingenieuren, Managern, Betriebsleitern, Betriebsgewerkschaftsführern und Produktionsarbeitern. Das Ersetzen veralteter Effizienzfaktoren wie menschlicher Arbeitskraft und Gerätenutzung durch neue Konzepte für Produktionszykluszeit, Wertschöpfung, Lagerbestandsvolumen und Qualität erfordert eine Änderung der Buchhaltungs- und Produktionssysteme.
Veränderungen in der Organisation, den Systemen, der Kultur und den Beziehungen können nur dann erfolgreich sein, wenn sie von der obersten Unternehmensspitze, also vom CEO, ausgehen. Nur auf dieser Ebene können Entscheidungen zur Zuweisung der erforderlichen Ressourcen, zur Einleitung der erforderlichen Änderungen in der Organisationsstruktur und den Betriebsprinzipien, zur Auswahl der am besten geeigneten Strategien und zur Erstellung geeigneter Kommunikationspläne getroffen werden. Der von oben kommende Prozess muss die Unterstützung der einfachen Arbeiter haben, und dafür müssen sie entsprechend geschult werden und die Möglichkeit erhalten, sich sinnvoll zu beteiligen.
Das ist eine schwierige, aber notwendige Aufgabe. Es erfordert ein sehr hohes Maß an Management- und Führungskompetenz – nur so können die technischen, organisatorischen und verhaltensbezogenen Probleme, die bei der Implementierung von JIT auftreten, überwunden werden. Wenn die Geschäftsleitung nicht bereit ist, sich voll und ganz auf die Seite von JIT zu stellen, ist es besser, die Umsetzung abzulehnen.
Just-In-Time-Implementierungssequenz. JIT sollte mit einem Pilotprogramm beginnen, das eine der Produktlinien des Unternehmens betrifft. Zuvor erfolgt eine umfassende Schulung von Führungskräften, Ingenieuren, Meistern, Bauleitern und direkten Werkstattmitarbeitern. Besonderer Wert sollte auf praktische Übungen gelegt werden, um allen das Verständnis des JIT-Systems und seiner Vorteile zu erleichtern. Um sicherzustellen, dass allen Mitarbeitern die Ziele der Innovation und deren Status bekannt sind, ist es notwendig, ein langfristiges Kommunikationsprogramm zu entwickeln und umzusetzen.
Änderungen in der Produktion sollten bereits in der Endmontagephase beginnen. In der Regel ist bereits ein gewisser Warenfluss vorhanden und es ist nicht schwierig, ihn neu zu organisieren, da hierfür voraussichtlich keine kapitalintensiven Geräte erforderlich sind. Montageabschnitte müssen im Kanban-System mithilfe von Karten oder Behältern miteinander verbunden werden. Als nächstes folgt die Abstimmung des Produktionsplans für die Pilotlinie, die Reduzierung der Umrüstzeiten und der Produktionsstart einer gemischten Modellreihe. Um den Ablauf zu synchronisieren, ist es notwendig, die Dauer der Vorgänge an verschiedenen Arbeitsplätzen auszugleichen und parallel dazu ein Programm zu starten, um die Rüstzeit der Ausrüstung in der Hauptproduktion zu verkürzen. Ladenmitarbeiter sollten möglichst direkt an allen Programmen teilnehmen. Die Erstellung eines effektiven JIT-Systems ist ein iterativer Prozess, der Versuch und Irrtum sowie die wichtigste Komponente – das Feedback der Mitarbeiter – umfasst. Wenn Arbeitnehmer durch Gewerkschaften vertreten werden, sollten sie als Partner im JIT-Umsetzungsprozess behandelt werden. Wenn in einem Unternehmen restriktive Arbeitsregeln gelten, müssen die Gewerkschaften in Verhandlungen zur Änderung der Arbeitspraktiken einbezogen werden.
Sobald JIT in der Endmontagephase reibungslos läuft, kann es auf die Vormontagephase ausgeweitet werden und so alle erfahrenen Montagevorgänge konsolidieren. Der letzte Schritt nach der Implementierung eines Programms zur Verkürzung der Umrüstzeit und damit der Möglichkeit der Produktion in kleinen Chargen ist die Synchronisierung des Ablaufs aller Vorgänge, einschließlich der Teilefertigung. Die erfolgreichen Prinzipien des Pilotprogramms müssen in allen verbleibenden Produktlinien repliziert werden, in denen JIT möglicherweise angewendet werden könnte.
Die für die Implementierung eines Systems erforderliche Zeit hängt von mehreren Faktoren ab: der Anzahl der Produktlinien, der Komplexität der Produkte, der Komplexität der technologischen Prozesse, den Fähigkeiten der vorhandenen Ausrüstung, dem Produktionsklima und der Verfügbarkeit von Ressourcen. Es ist wichtig, die richtige Geschwindigkeit der Veränderung zu wählen. Dies muss schrittweise erfolgen, damit Zeit für entsprechende Veränderungen in der Kultur der Organisation bleibt, und gleichzeitig schnell genug, um das Interesse und die Bereitschaft der Menschen, sich anzustrengen, aufrechtzuerhalten. Man muss sich auch damit abfinden, dass gemäß der JIT-Philosophie der kontinuierlichen Verbesserung die Implementierung eines Systems niemals vollständig abgeschlossen sein wird.
JIT ist eine effektive, aber fragile Form der Produktionsorganisation. Es erfordert kontinuierliche Verbesserungen in den Werkstätten und ständige Aufmerksamkeit seitens der Unternehmensleitung. Das Management muss sicherstellen, dass neue Marketingmöglichkeiten den JIT-Anforderungen entsprechen, damit zukünftiges Umsatzwachstum die Lebensfähigkeit des Systems nicht beeinträchtigt.
Gerade noch rechtzeitig und stressig. Kritiker nennen JIT „Stressmanagement“ und eine neue Form des „Sweatshops“. Die in diesem Rahmen durchgeführten Veränderungen basieren auf einem intensiven, extremen Arbeitstempo und einem anhaltenden Wunsch nach Kaizen – kontinuierlicher Verbesserung. Alle diese Beschwerden sind berechtigt und müssen von den Managern gelöst werden. Die potenziellen Vorteile von JIT sind zu groß, als dass sie durch unangemessen hohe Produktionsraten oder Kaizen-Programme beeinträchtigt werden könnten. Stressmanagement ist mit der starken Abhängigkeit von JIT und dem Bedarf an engagiertem Personal nicht vereinbar.
Kaizen-Widersprüche hängen hauptsächlich mit der Praxis zusammen, die Anzahl der Arbeiter oder der Kanban-Behälter zu reduzieren, d. h. mit gewaltsamen Methoden zur Wiederherstellung normaler Arbeitspraktiken. Der Autor dieses Artikels beobachtete einen fortschrittlicheren Ansatz in Japan. Über dem Arbeitsbereich des sechsköpfigen Teams hing ein Banner mit Kanjis Aussage und einer großen Zahl „5“. Ihr Ziel für das laufende Quartal war es, so viele kleine Verbesserungen vorzunehmen, dass nur fünf Personen auf der Website arbeiten konnten. Eine solche Zusammenarbeit steht im Einklang mit der Personalpolitik von JIT. Eine Reduzierung des Personalbestands erfolgt nach Veränderungen und nicht umgekehrt, wenn zunächst „zusätzliche“ Personen entlassen werden und dann von den verbleibenden Personen mehr Produktivität gefordert wird. Die Verringerung der Zahl sollte das Ergebnis einer Verbesserung und nicht deren treibende Kraft sein.
JIT ist eine anspruchsvolle und fragile Form der Produktionsorganisation, aber möglicherweise äußerst effektiv. Es sollte nicht durch den Einsatz von Managementpraktiken gefährdet werden, die gegenüber Arbeitnehmern missbräuchlich sind.
Rechnet sich Just-in-Time? Es kann durchaus sein. Wenn die notwendigen Markt- und Managementbedingungen erfüllt sind, hat JIT das Potenzial, die Produktion dramatisch zu verbessern. Das System hat wiederholt seine Fähigkeit unter Beweis gestellt, gleichzeitig den Lagerbestand zu reduzieren, die Kosten zu senken und die Qualität zu verbessern, was zusammen die Wettbewerbsfähigkeit und Rentabilität eines Unternehmens erheblich verbessern kann. Als Beispiel dafür, was mit JIT erreicht werden kann, siehe Daten der Antennenabteilung von Texas Instruments (Ellis & Conlon, 1992), siehe Tabelle. 2.
Diese beeindruckenden Ergebnisse wurden zwei Jahre nach dem Start des Just-in-Time-Programms erzielt. Ihr Einfluss wird in Abb. deutlicher dargestellt. 5 zeigt ein Diagramm des Anstiegs der Produktkosten während des Auftragsabwicklungsprozesses vor und nach der Implementierung dieses Systems.
Die Art der Kostenakkumulation während der kontinuierlichen Produktion in kleinen Chargen unter Verwendung des JIT-Systems ist tendenziell linear. Bei der Produktion in großen Mengen und mit sequentiellem Materialverbrauch und -verarbeitung, unterbrochen von Ausfallzeiten und Verzögerungen, ist das Muster der Kostenakkumulation diskontinuierlich. Verbesserungen bei Kosten und Durchlaufzeiten mit JIT sind offensichtlich. Weniger offensichtlich ist ein deutlicher Rückgang des Reservenvolumens, wie die Fläche unter den entsprechenden Kurven zeigt.
„Just-in-Time“, „Just-in-Time“ (JIT), Pull-System, Pull-System– vollständige Synchronisierung der Lieferungen mit den Produktions- und Verkaufsprozessen: Vorräte werden in kleinen Chargen direkt an die erforderlichen Punkte des Produktionsprozesses geliefert, das Lager umgehend, und fertige Produkte werden sofort an die Kunden versandt. Die Reihenfolge des Produktproduktionsmanagements ist umgekehrt: von der i-ten Stufe zur (i – 1)-ten.
Kurze Informationen zum Begriff |
Derzeit ist ein klarer Trend zu einem Anstieg der Lagerhaltungskosten zu erkennen, was zum Grund für die Entwicklung von „sofortigen“ Bestandsverwaltungssystemen geworden ist, zu denen auch das betrachtete „Just-in-Time“-System gehört.
Nach dem Just-in-Time-System wird die Bestellung von Fertigwaren an die letzte Stufe des Produktionsprozesses übermittelt, wo das erforderliche Volumen an unfertigen Arbeiten berechnet wird, das aus der vorletzten Stufe stammen sollte. Ebenso erfolgt ab der vorletzten Stufe eine Anfrage für die vorherige Produktionsstufe für eine bestimmte Anzahl von Halbzeugen. Somit besteht zwischen jeweils zwei benachbarten Stufen des Produktionsprozesses eine doppelte Verbindung:
- Von der i-ten Stufe bis zur (i – 1)-ten Stufe wird die erforderliche Menge an laufenden Arbeiten angefordert („gezogen“);
- Von der (i – 1) Stufe werden materielle Ressourcen in der erforderlichen Menge an die i-te Stufe gesendet.
Darüber hinaus werden Materialressourcen aus der externen Umgebung in kleinen Mengen direkt an die erforderlichen Stellen im Produktionsprozess geliefert und fertige Produkte sofort an Kunden versandt. Somit gibt es in einem Just-in-Time-System überhaupt keine Lagerbestände als solche, was es ermöglicht, auf den Aufbau eines Lagersystems zu verzichten. Es gibt auch keine Versicherungen oder Saisonvorräte.
Um Verzögerungen bei der Versorgung mit Lagerbeständen und beim Verkauf von selbst hergestellten Produkten zu vermeiden, werden Einkaufs-/Verkaufsbeziehungen mit einer kleinen Anzahl zuverlässiger, vertrauenswürdiger Lieferanten, Spediteure und Käufer aufgebaut.
Die Hauptvorteile des Just-in-Time-Systems:
- kurzer Produktionszyklus, hoher Vermögensumschlag, einschließlich Lagerbestände;
- Es fallen keine oder nur äußerst geringe Lagerkosten für Produktion und Lagerhaltung an.
Die Hauptnachteile des Just-in-Time-Systems sind:
- die Schwierigkeit, eine hohe Konsistenz zwischen den Produktproduktionsstufen sicherzustellen;
- erhebliches Risiko einer Unterbrechung der Produktion und des Verkaufs von Produkten.
Veröffentlichungen
Funktionales Management. Fragment aus dem Buch „Theory of System Management“
Als Haupteffizienzbereiche der Produktionsaktivitäten des Unternehmens im Allgemeinen und der Bestandsverwaltung im Besonderen gelten das „Just-in-Time“-Pround seine Variante CANBAN. Darüber hinaus werden das Konzept und die Grundprinzipien der Bestandsverwaltung sowie die Struktur und Funktionen der Logistikdienstleistung des Unternehmens besprochen. Es werden Methoden zur Berechnung des Bedarfs an materiellen Ressourcen bereitgestellt.
Komaha A. Bestandsverwaltung
Bewertet werden die Erfahrungen im Bestandsmanagement der Toyota- und Kmart-Unternehmen: Just-in-Time-System, statistische Prozesskontrolle, Gesamtqualitätsmanagement, Neugestaltung von Geschäftsprozessen, Gesamtgeldmanagement, optimales Bestellgrößenmodell, Bestandsbewertung und Buchhaltung.
Just-in-Time-Inventar-Replenishment-System (JIT).
Berücksichtigt werden die Philosophie des Konzepts, Schlüsselelemente, Vorteile des „Just-in-Time“-Systems und die Hauptfehler bei seiner Anwendung.
Just-In-Time (JIT)-System
Das „Just in time“-System, wörtlich übersetzt „just in time oder just in time“, wurde vom japanischen Automobilkonzern Toyota entwickelt. Der Autor war Taiishi Ohno (der schließlich Vizepräsident des Unternehmens wurde) und mehrere seiner Kollegen. Das System beinhaltet die Lieferung der notwendigen Materialressourcen in der erforderlichen Menge und zum richtigen Zeitpunkt an den Ort ihres Produktionsverbrauchs unter Umgehung von Zwischenlagern. Dies trägt dazu bei, unerwünschte Lagerbestände auf ein Minimum zu reduzieren.
Mit diesem System wird die Aufgabe unter Umgehung anderer Unternehmensbereiche auf das letzte Glied der Produktionskette verlagert – das Fertigproduktlager. Vom Fertigproduktlager aus wird die Aufgabe nacheinander an die Abteilungen gesendet, die Vorgänge in den vorherigen Phasen des Technologiezyklus ausführen. Der Hersteller verfügt nicht über einen vollständigen Arbeitsplan und Zeitplan und ist an eine bestimmte Verbraucherbestellung gebunden. Die Detaillierung der Pläne erfolgt durch die direkten Ausführenden der Arbeiten unter Berücksichtigung des Umfangs der erhaltenen Aufgabe und des Zeitpunkts ihrer Ausführung. Das „Justin Time“-System beinhaltet die Zusammenarbeit mit einer einzigen Bezugsquelle auf Basis eines langfristigen Vertrags. Der Einkauf erfolgt in der Regel in kleinen Mengen. Die Hauptanforderung an den Lieferanten besteht darin, eine hohe Qualität der gelieferten Produkte sicherzustellen, da die Produkte hauptsächlich „von den Rädern“ an den industriellen Verbrauch geliefert werden.
Das Just-in-Time-System ist ein Logistikkonzept für ein Unternehmen, bei dem die Produktbewegungen während des Produktionsprozesses und die Lieferungen von Lieferanten sorgfältig und rechtzeitig geplant werden – so dass in jeder Phase des Prozesses die nächste (meist kleine) Charge eintrifft zur Verarbeitung genau in dem Moment, in dem die vorherige Charge abgeschlossen ist.
Insgesamt vermeidet das Just-in-Time-Versorgungssystem das Problem der Überproduktion, reduziert die Lagerbestände auf das geringstmögliche Maß und eliminiert unverhältnismäßige Lagerkosten. Ein solches System ermöglicht es Ihnen unter anderem, die Produktion mit einem Minimum an Fehlern zu organisieren. Schließlich sind Unternehmen mit Just-in-Time-Lieferungen stets bestrebt, die Produktionsqualität zu verbessern und suchen immer nach neuen Wegen, um effizienter zu arbeiten.
Es wird allgemein angenommen, dass Just-in-Time lediglich eine angemessene Produktionsplanung ist, die zu einem Mindestmaß an unfertigen Erzeugnissen und Lagerbeständen führt. Aber im Wesentlichen handelt es sich bei dem System um eine spezifische Philosophie, die jeden Aspekt des Produktionsprozesses abdeckt, von der Entwicklung über den Produktverkauf bis hin zum Kundendienst. Diese Philosophie zielt darauf ab, ein System zu schaffen, das mit minimalem Lagerbestand, minimalem Platzbedarf und minimalem Papieraufwand gut funktioniert. Es muss ein System sein, das keinen Ausfällen und Störungen unterliegt und flexibel (hinsichtlich Änderungen im Produktsortiment und Produktionsvolumen) ist. Das ultimative Ziel ist ein ausgewogenes System mit einem reibungslosen und schnellen Materialfluss durch das System. Im System ist Qualität sowohl in das Produkt als auch in den Produktionsprozess „eingebaut“. Unternehmen, die das System nutzen, haben ein Qualitätsniveau erreicht, das es ihnen ermöglicht, mit kleinen Produktionsläufen und engen Zeitplänen zu arbeiten. Diese Systeme sind äußerst zuverlässig, die Hauptursachen für Ineffizienz und Störungen werden beseitigt und die Mitarbeiter werden nicht nur für die Arbeit im System geschult, sondern auch für die kontinuierliche Verbesserung des Systems.
Eine Reihe von Unternehmen, darunter Toyota als eines der ersten, verbrachten in den 1970er Jahren Jahre damit, das Just-in-Time-Konzept oder JIT, eine andere Bezeichnung für Just-in-Time, zu entwickeln. Diese Methoden haben sich als so effektiv erwiesen, dass mittlerweile alle großen Organisationen Elemente dieses Ansatzes in gewissem Umfang nutzen. Der traditionelle Ansatz zur Arbeitsorganisation geht davon aus, dass das Inventar ein wichtiges Element des gesamten Systems ist und sicherstellt, dass der Betrieb nicht ausfällt. MRP reduziert den Lagerbestand, indem es den Masterplan so nutzt, dass eine bessere Übereinstimmung zwischen Materialvorräten und deren Nachfrage gewährleistet wird und dennoch ein gewisser Sicherheitsbestand für den Fall unvorhergesehener Probleme aufrechterhalten wird. Je höher der Grad der Übereinstimmung zwischen Angebot und Nachfrage ist, desto weniger Lagerbestände werden wir natürlich benötigen. Wenn wir das Missverhältnis zwischen Angebot und Nachfrage vollständig beseitigen können, benötigen wir überhaupt keine Lagerbestände. „Just in time“ basiert darauf.
Ein interessantes Beispiel, das die Essenz der „Just-in-Time“-Arbeit verdeutlicht, ist der Betrieb eines Gasherds mit Flaschengas und Gas, das über eine Rohrleitung zugeführt wird. Im ersten Fall besteht manchmal eine Diskrepanz zwischen der Verfügbarkeit von Kraftstoff im Zylinder und dem Bedarf daran. Um Unterbrechungen zu vermeiden, müssen Sie Gasflaschen im Voraus kaufen, d.h. einen Vorrat anlegen. Im zweiten Fall entspricht das Gasangebot genau der Nachfrage und der Verbraucher verfügt über keine Brennstoffreserven. Dieses Konzept basiert auf der Annahme, dass Vorräte durch schlechtes Management und schlechte Arbeitskoordination entstehen und daher Probleme in den Vorräten verborgen sind. Daraus folgt die Schlussfolgerung, dass es notwendig ist, die Gründe für die Differenz zwischen Angebot und Nachfrage zu finden, die Ausführung der Operationen zu verbessern, woraufhin die Bestände verschwinden. Im weiteren Sinne betrachtet Just in Time das Unternehmen als eine Reihe von Problemen, die die effiziente Ausführung von Vorgängen beeinträchtigen, zum Beispiel lange Vorlaufzeiten, Instabilität der Auftragslieferung, unausgeglichene Abläufe untereinander, begrenzte Kapazität, Geräteausfälle, Defekte Materialien, Arbeitsunterbrechungen, unzuverlässige Lieferanten, schlechte Qualität des Hausarztes, zu viel Papierkram und vieles mehr. Manager versuchen, diese Probleme zu lösen, indem sie Reserven schaffen, zusätzliche Kapazitäten kaufen, Ersatzausrüstung installieren, Feuerwehrleute einladen usw. In Wirklichkeit verbergen diese Maßnahmen jedoch nur die Ursachen der Probleme. Der konstruktive Ansatz besteht darin, die wirklichen Probleme zu identifizieren und zu lösen. Das Just-in-Time-Konzept führt zu Meinungsveränderungen in folgenden Bereichen:
Lagerbestände just in time. Unternehmen müssen Probleme, die zu Lagerbeständen führen, identifizieren und lösen und dabei eine Mindestbestandsaufnahme (Nullbestand) für unfertige Erzeugnisse anstreben.
Qualität just in time. Es ist nicht notwendig, ein akzeptables Maß an Mängeln zu erreichen, sondern auf der Grundlage eines integrierten Qualitätsmanagements deren völlige Abwesenheit.
Lieferanten in Just-in-time. Kunden müssen sich vollständig auf ihre Lieferanten verlassen und daher langfristige Partnerschaften mit einer kleinen Anzahl zuverlässiger Lieferanten und Spediteure aufbauen.
Umfang der Spiele im Just-in-time. Es muss nach Möglichkeiten gesucht werden, das Volumen der Produktionschargen zu reduzieren, um kurze Produktionszyklen zu erreichen, damit sich keine Überproduktion in den SOE-Beständen ansammelt.
Auftragserfüllungszeit in Just-in-Time. Es ist notwendig, die Durchlaufzeiten zu verkürzen, um Unsicherheiten zu reduzieren, die bei langen Lieferzeiten die Situation verändern können.
Zuverlässigkeit just in time. Alle Vorgänge müssen kontinuierlich und fehlerfrei durchgeführt werden, d. h. Es sollte keine Geräteausfälle, Defekte, Fehlzeiten usw. geben.
Arbeiter bei Just in time. Ein Geist der Zusammenarbeit ist notwendig, sowohl zwischen Arbeitnehmern als auch zwischen Managern und Arbeitnehmern, denn... Das Wohlergehen aller hängt vom Gesamterfolg bei der Arbeit ab; alle Mitarbeiter sollten gleich und fair behandelt werden. Jede kreative Initiative eines Mitarbeiters hinsichtlich möglicher Arbeitsverbesserungen wird gefördert.
Die Informationsunterstützung in Just-in-Time soll einen schnellen Informationsaustausch und die Synchronisierung aller Prozesse der MR-Lieferung, Produktion und Montage sowie der GP-Versorgung ermöglichen.
Somit ist Just-in-Time nicht nur eine Möglichkeit, Lagerbestände zu minimieren, sondern auch Verschwendung für jede Art von Ressource zu vermeiden, die Koordination zu verbessern und die betriebliche Effizienz zu steigern.
Das ultimative Ziel des Systems ist ein ausgewogenes System; Das bedeutet, dass ein reibungsloser und schneller Materialfluss durch das System gewährleistet ist. Die Hauptidee besteht darin, den Prozess so kurz wie möglich zu gestalten und die Ressourcen optimal zu nutzen. Der Grad der Zielerreichung hängt davon ab, inwieweit weitere (Hilfs-)Ziele erreicht werden, wie zum Beispiel:
Beseitigen Sie Ausfälle und Störungen im Produktionsprozess.
Machen Sie das System flexibel.
Reduzieren Sie die Vorbereitungszeit für den Prozess und alle Produktionszeiten.
Lagerbestand minimieren.
Eliminieren Sie unnötige Kosten.
Ausfälle und Störungen im Prozess wirken sich negativ auf das System aus und stören den reibungslosen Produktfluss und müssen daher behoben werden. Störungen werden durch eine Vielzahl von Faktoren verursacht: schlechte Qualität, Geräteausfall, Änderungen in den Zeitplänen, verspätete Lieferungen. Alle diese Faktoren sollten nach Möglichkeit ausgeschlossen werden. Vorbereitungszeit und Produktionsvorlaufzeiten verlängern den Prozess, ohne die Produktkosten zu erhöhen. Darüber hinaus wirkt sich die Länge dieser Fristen negativ auf die Flexibilität des Systems aus. Daher ist ihre Reduzierung sehr wichtig und eines der Ziele der kontinuierlichen Verbesserung.
Vorräte sind ungenutzte Ressourcen, die Platz beanspruchen und die Produktionskosten erhöhen. Sie sollten minimiert oder wenn möglich ganz beseitigt werden. Unnötige Ausgaben stellen unproduktive Ressourcen dar; Durch deren Beseitigung können Ressourcen freigesetzt und die Produktion ausgeweitet werden. In der Just-in-Time-Philosophie gehören zu den unnötigen Ausgaben:
Überproduktion;
Wartezeit;
unnötiger Transport;
Lagerung von Vorräten;
Mängel und Verschwendung;
ineffektive Arbeitspraktiken;
Produktmängel.
Das Vorhandensein solcher diskretionärer Ausgaben weist auf eine Verbesserungsmöglichkeit hin, oder die Liste der diskretionären Ausgaben identifiziert potenzielle Ziele für eine kontinuierliche Verbesserung.
Vorteile von Just-in-Time-Systemen.
„Just-in-Time“-Systeme haben eine Reihe wichtiger Vorteile, die die Aufmerksamkeit von Unternehmen mit einem traditionellen Produktionsansatz auf sich ziehen. Die Hauptvorteile sind:
- - reduzierte Lagerbestände im Produktionsprozess (unfertige Erzeugnisse), Einkäufe und Fertigwaren.
- - kleinere Anforderungen an die Größe der Produktionsflächen.
- - Verbesserung der Produktqualität, Reduzierung von Fehlern und Nacharbeiten.
- - Reduzierung der Produktionszeit.
- - größere Flexibilität beim Wechsel der Produktpalette.
- - reibungsloserer Produktionsablauf mit sehr seltenen Ausfällen aufgrund von Qualitätsproblemen, kürzere Vorbereitungszeiten für den Produktionsprozess; Vielseitig qualifizierte Arbeitskräfte, die sich gegenseitig helfen oder ersetzen können.
- - höhere Produktivität und Geräteauslastung.
- - Beteiligung der Arbeitnehmer an der Lösung von Problemen.
- - die Notwendigkeit guter Beziehungen zu Lieferanten.
- - weniger Bedarf an nicht produktionsbezogenen Arbeiten, wie etwa der Lagerung und dem Transport von Materialien.
Derzeit wird das System von den größten japanischen, amerikanischen und europäischen Unternehmen in verschiedenen Branchen eingesetzt. Das System basiert auf dem Prinzip: Produkte nur dann produzieren, wenn sie in geringerer Menge als erforderlich benötigt werden. Die Just-in-Time-Methode basiert auf dem Logistikgedanken: „Es wird nichts produziert, bis es gebraucht wird.“ Weigerung, Produkte in großen Mengen herzustellen. Die Versorgung der Produktion erfolgt bedarfsgerecht in Kleinserien, wodurch eine Reduzierung der Lagerbestände erreicht wird.
Der Einsatz dieser Technik ermöglicht es dem Unternehmen, unnötige Kosten zu vermeiden, indem unproduktive Kosten reduziert werden, die insbesondere aus der Produktion überschüssiger Produkte, Ausfallzeiten von Ausrüstung und Personal, Wartung überschüssiger Lagerflächen und mit der Präsenz verbundenen Verlusten bestehen von Produktmängeln. Gleichzeitig begleitet die Nachfrage die Produkte über das gesamte Produktionsvolumen. Vorräte werden zum Zeitpunkt ihrer Verwendung im Produktionsprozess geliefert. Ein Teil der indirekten Kosten wird in die Kategorie der direkten Kosten überführt. Der Schwerpunkt liegt auf der Qualität, Verfügbarkeit und den Gesamtkosten der Produkte und nicht auf der Höhe der Einkaufspreise. Mit dem Begriff Just-in-Time (JIT) werden Industriesysteme bezeichnet, in denen die Bewegung von Produkten während der Produktion und die Lieferungen von Lieferanten sorgfältig und rechtzeitig geplant werden – so dass in jeder Phase des Prozesses die folgende, meist kleine, Charge entsteht kommt genau dann zur Verarbeitung, wenn die vorherige Charge abgeschlossen ist. Daher der Name Just-in-Time (just in time, nur pünktlich). Das Ergebnis ist ein System, in dem es keine passiven Einheiten gibt, die auf die Verarbeitung warten, oder ungenutzte Arbeiter oder Geräte, die auf die Verarbeitung von Artikeln warten.
Das Just-in-Time-Phänomen (JIT) ist charakteristisch für Fertigungssysteme, die mit sehr wenig „Fett“ arbeiten (z. B. überschüssiger Lagerbestand, überschüssige Arbeitskräfte, überschüssige Produktionsfläche). JIT bezieht sich auf den zeitlichen Ablauf der Bewegung durch ein System von Teilen und Materialien sowie Dienstleistungen. Unternehmen, die einen JIT-Ansatz verwenden, haben in der Regel einen erheblichen Vorteil gegenüber ihren Konkurrenten, die einen traditionelleren Ansatz verwenden. Sie haben niedrigere Produktionskosten, weniger Fehler, größere Flexibilität und die Fähigkeit, neue oder verbesserte Produkte schnell auf den Markt zu bringen. In dieser Veröffentlichung betrachten wir das Just-in-Time-System (JIT), einschließlich seiner Hauptelemente und der Faktoren, die für einen effektiven Betrieb erforderlich sind.
Implementierungsprobleme.
- - Hohe Anfangsinvestitions- und Implementierungskosten Just in time.
- - Unfähigkeit, mit unvorhergesehenen Umständen umzugehen (Ausfälle, Streiks von Zulieferern usw.);
- - Abhängigkeit von qualitativ hochwertigen gelieferten Materialien. · Notwendigkeit, in einer stabilen Produktionsumgebung zu arbeiten, obwohl die Nachfrage oft schwankt.
- - Reduzierte Flexibilität bei der Erfüllung sich ändernder Verbraucheranforderungen.
- - Schwierigkeiten bei der Reduzierung der Umrüstzeit und der damit verbundenen Kosten.
- - Unfähigkeit einzelner Lieferanten, im Just-in-Time-Modus zu arbeiten.
- - Probleme bei der Just-in-Time-Anbindung an andere Informationssysteme von Partnern.
- - Die Notwendigkeit, die allgemeine Anordnung von Strukturen zu ändern.
- - Arbeiten der Mitarbeiter in einem Umfeld mit erhöhtem Stress.
- - Mangelnde Zusammenarbeit und Vertrauen zwischen den Mitarbeitern.
- - Unfähigkeit einzelner Mitarbeiter, größere Verantwortung zu übernehmen.
Das Konzept der effektiven Reaktion auf Verbraucheranfragen. Just in Time zwingt Lieferanten dazu, ihre Arbeitsweise zu ändern, um schnellere Lieferungen, höhere Qualität, kleinere Losgrößen und absolute Zuverlässigkeit zu gewährleisten. Eine offensichtliche Möglichkeit, diesen Anforderungen gerecht zu werden, besteht darin, dass die Lieferanten selbst Just-in-Time-Methoden anwenden. Dadurch wird sichergestellt, dass das gesamte LC koordiniert und auf der Grundlage derselben Ziele und Prinzipien arbeitet. Notwendige Voraussetzungen für die Umsetzung des Just-in-Time-Konzepts. Verfügbarkeit zuverlässiger Lieferanten im Wirtschaftssystem. Beispielsweise konnten amerikanische und europäische Hersteller dieses Konzept aufgrund der geringen Lieferzuverlässigkeit 10–15 Jahre später als die Japaner einführen.
Partnerschaftliche Beziehungen zwischen Organisationen in der Lieferkette. Einsatz von Systemen zum Austausch von Informationen über die erforderliche Warenbeschaffung, zum Beispiel Kanban für Just in Time und elektronischer Datenaustausch für ECR. Hohe Geschwindigkeit der physischen Lieferung von MR, unter anderem durch Verkürzung der Zeit der Zwischenlagerung und des Wartens auf die Frachtabfertigung. Genaue Informationen über den aktuellen Produktionsstand, genaue Prognosen für die nahe Zukunft. Um dies zu erreichen, müssen zuverlässige Telekommunikationssysteme sowie Informations- und Computerunterstützung bei der Organisation und Betriebsführung von Produktionsprozessen eingesetzt werden. Eines der weltweit am weitesten verbreiteten Logistikkonzepte/-technologien ist das JIT-Konzept. Die Entstehung dieses Konzepts geht auf die späten 1950er Jahre zurück, als das japanische Unternehmen Toyota Motors und dann andere japanische Automobilhersteller begannen, das KANBAN-System aktiv einzuführen. Das ursprüngliche Motto des JIT-Konzepts war die Eliminierung potenzieller Bestände an Materialien, Komponenten und Halbzeugen im Produktionsprozess der Montage von Autos und ihren Haupteinheiten.
Die ursprüngliche Aufgabenstellung sah so aus: Liegt ein Produktionsplan vor, dann gilt es, die Bewegung der Materialflüsse so zu organisieren, dass alle Materialien, Komponenten und Halbzeuge in der richtigen Menge am richtigen Ort (auf der Baugruppe) ankommen Linie) und pünktlich zur Produktion bzw. Montage fertiger Produkte. Bei dieser Problemstellung erwiesen sich große Sicherheitsvorräte und das Einfrieren der Unternehmensmittel als unnötig. Das ELA Terminology Dictionary definiert JIT als Konzept und als Technologie: „Im Großen und Ganzen handelt es sich um einen Erfolgsansatz, der auf der konsequenten Eliminierung von Verschwendung basiert (Verschwendung ist jede Aktivität, die dem Produkt keinen Mehrwert verleiht). Im engeren Sinne geht es um die Lieferung von Materialien zur richtigen Zeit an den richtigen Ort.“
Konzeptionell diente der JIT-Ansatz als Grundlage für die spätere Umsetzung von Logistikkonzepten/-technologien wie Lean Production („flache“ oder „dünne“ Produktion) und Value Added Logistics. Aus logistischer Sicht handelt es sich bei JIT um eine relativ einfache binäre Bestandsverwaltungslogik ohne Einschränkung des Mindestbestandsbedarfs, nach der die Materialflüsse sorgfältig mit dem im Produktionsplan festgelegten Bedarf für die Freigabe fertiger Produkte synchronisiert werden. Eine solche Synchronisierung ist nichts anderes als die Koordination zweier Funktionsbereiche der Logistik: Versorgung und Produktionsunterstützung. Anschließend wurde die JIT-Ideologie erfolgreich in den Produktvertrieb und nun in Makrologistiksysteme auf verschiedenen Ebenen und für verschiedene Zwecke übertragen.
Die wesentlichen Vorteile von Just-in-Time-Technologien, die ihren breiten Einsatz in der Logistikpraxis erklären, sind:
Geringe Lagerbestände.
Reduzierung der Produktionsfläche.
Verbesserung der Produktqualität, Reduzierung von Fehlern und Nacharbeiten.
Reduzierte Produktionszeit.
Erhöhte Flexibilität bei Sortimentswechseln.
Reibungsloser Produktionsablauf mit seltenen Ausfällen aufgrund von Qualitätsproblemen; kürzere Vorbereitungszeiten für den Produktionsprozess; Vielseitig qualifizierte Arbeitskräfte, die sich gegenseitig helfen oder ersetzen können.
Hohe Produktivität und effizienter Geräteeinsatz.
Beteiligung der Arbeitnehmer an der Lösung von Produktionsproblemen.
Gute Beziehungen zu Lieferanten.
Weniger produktionsfremde Arbeiten wie Lagerhaltung und Materialtransport.
JIT ist ein modernes Konzept/eine moderne Technologie zum Aufbau von Arzneimitteln als Ganzes oder zur Organisation des Logistikprozesses in einem separaten funktionalen Geschäftsbereich: Produktion, Lieferung und Vertrieb, basierend auf der Synchronisierung der Lieferprozesse von MR, GP, GP im Die erforderlichen Mengen bis zum Zeitpunkt, zu dem die Arzneimittelelemente/-verbindungen benötigt werden, zu ermitteln, um die mit Sicherheitsbeständen verbundenen Kosten zu minimieren. Das JIT-Konzept steht in engem Zusammenhang mit funktionalen Logistikkreisläufen und deren Komponenten. Im Idealfall sollten MR, IR oder GP genau dann an einen bestimmten Punkt in der Lieferkette (Kanal) geliefert werden, wenn sie benötigt werden (nicht früher und nicht später), wodurch Überbestände in den Funktionsbereichen des Unternehmens eliminiert werden. Viele moderne Medikamente, die auf dem JIT-Ansatz basieren, konzentrieren sich auf kurze Komponenten der Logistikzyklen, was eine schnelle Reaktion des Werks auf Nachfrageänderungen und dementsprechend ein flexibles Produktionsprogramm erfordert.
Das JIT-Logistikkonzept zeichnet sich durch folgende Hauptmerkmale aus:
Mindestgarantie-/Versicherungsbestände (null) von MR, NP, GP;
kurze Produktions-(Logistik-)Zyklen;
kleine Mengen GP-Produktion und Auffüllung der Lagerbestände (Vorräte);
Beziehungen (für die MR-Beschaffung) mit einer kleinen Anzahl zuverlässiger Lieferanten und Spediteure;
effektive Informationsunterstützung.
Der Just-in-Time-Ansatz (oder Kanban-Ansatz) wurde vom japanischen Automobilkonzern Toyota entwickelt. Der Autor war Taiishi Ohno (der schließlich Vizepräsident für Produktion des Unternehmens wurde) und mehrere seiner Kollegen.
Just-in-Time (Just-in-Time) ist ein System der Warenlieferung, das es einem Unternehmen ermöglicht, große Lagerbestände abzubauen. Beim Einsatz eines Just-in-Time-Liefersystems wird ein spezieller Zeitplan erstellt, der angibt, wann und wie viele Waren geliefert werden. Darüber hinaus erfolgen die Lieferungen oft täglich. Der Hauptvorteil eines solchen Systems liegt offensichtlich in seiner Flexibilität und der Möglichkeit, die Lagerkosten zu senken. Das ultimative Ziel ist ein ausgewogenes System mit einem reibungslosen und schnellen Materialfluss durch das System. Ein interessantes Beispiel, das die Essenz von Just-in-Time-Arbeit verdeutlicht, ist der Betrieb eines Gasherds mit Flaschengas und Gas, das über eine Pipeline zugeführt wird. Im ersten Fall besteht manchmal eine Diskrepanz zwischen der Verfügbarkeit von Kraftstoff im Zylinder und dem Bedarf daran. Um Unterbrechungen zu vermeiden, müssen Sie Gasflaschen im Voraus kaufen, d.h. einen Vorrat anlegen. Im zweiten Fall entspricht das Gasangebot genau der Nachfrage und der Verbraucher verfügt über keine Brennstoffreserven.
In Abb. 1 zeigt ein Diagramm der traditionellen Produktionsorganisation und Abb. 2 – Diagramm der Produktionsorganisation nach der „Just-in-Time“-Methode. Das traditionelle Planungssystem basiert auf dem Prinzip, eine vorgegebene Charge von Teilen oder Baugruppen in Folgeoperationen zu „schieben“, ohne zu berücksichtigen, ob sie dort tatsächlich in solchen Mengen und zu einem bestimmten Zeitpunkt benötigt werden. Das Just-in-Time-System basiert auf dem genau entgegengesetzten Prinzip.
Produktbestellung
Komponenten
Material
Abb.1 Schema der traditionellen Produktionsorganisation
Bestellung von Materialien, Bestellung von Komponenten, Bestellung von Produkten
Abb.2 Organisationsschema nach der „Just-in-Time“-Methode
Der Arbeitsrhythmus, die Menge und der Umfang der Teile und Baugruppen in der Produktion werden nicht durch das Beschaffungsglied (das erste Glied der Produktionskette), sondern durch das Generalmontageband (das letzte Glied der Produktionskette) bestimmt. „Input“ und „Output“ im System scheinen die Plätze zu tauschen. Wenn im traditionellen Schema der „Output“ nur das ist, was im „Input“ enthalten war, wird bei Kanban nur das, was am „Output“ benötigt wird, in die Produktion „einbezogen“. Anfragen nach „Input“ gehen von den allgemeinen Montagelinien entlang der gesamten Technologiekette ein.
In der Praxis bedeutet dies, dass Produkte just-in-time zum Verkauf hergestellt werden: fertige Autos – zum Zeitpunkt des Verkaufs, Komponenten und Baugruppen – zum Zeitpunkt der Montage des fertigen Produkts, Einzelteile – zum Zeitpunkt der Montage von Einheiten, Materialien – zum Zeitpunkt der Herstellung von Teilen.
Wenn das Just-in-Time-System unternehmensweit funktioniert, ist eine Materialbevorratung überflüssig. Sie können vollständig liquidiert werden, was zur Liquidation von Lagerbeständen und Lagereinrichtungen führt. Aus ökonomischer Sicht spielen Materialbestände die Rolle von Kostenträgern, „eingefrorenem Geld“. Die Kosten für die Lagerhaltung werden reduziert und damit auch das Produktionskostenvolumen. Dadurch erhöht sich der Kapitalumschlag.
Es stellt sich sofort ein bestimmtes Problem ein. Es ist ziemlich schwierig, ein Versorgungssystem zu organisieren, das ohne Ausfälle funktioniert. Denn es stellt sich heraus, dass das Unternehmen bei Just-in-Time-Lieferungen in eine Abhängigkeit von seinem Lieferanten gerät. Sollten auf seiner Seite unerwartete Probleme auftreten, wird auch das Unternehmen darunter leiden. Es kann sogar erforderlich sein, die Produktion oder den Verkauf von Produkten vorübergehend einzustellen. Schließlich können steigende Transportkosten dazu führen, dass Just-in-Time für eine bestimmte Anwendung ein ineffektives System ist.
Es ist durchaus möglich, dass es rentabler ist, Waren in einem Lagerhaus zu lagern, als sie ständig auszuliefern. Beispielsweise verwendet das Unternehmen Euro Trade Rus kein Just-in-Time-System. Das Unternehmen beschäftigt sich mit dem Großhandel mit Badaccessoires, die wiederum in China hergestellt werden. Um jedoch einen Produktionsauftrag zu erteilen, muss dieser ein Mindestvolumen erreichen. Das heißt, um Seifenschalen bestellen zu können, muss die Bestellmenge mindestens 29 Würfel betragen und es müssen mindestens 432 Stück jeder Seifenschalenfarbe bestellt werden. Nur dann ist die Produktion der Bestellung wirtschaftlich gerechtfertigt und die Lieferung wirtschaftlich rentabel, andernfalls werden die Logistikkosten dieses Geschäft unrentabel machen.
Das Unternehmen Euro Trade Rus arbeitet mit Einzelhandelsketten zusammen und ist deren Lieferant. Und Einzelhandelsketten geben, um die Kosten für die Lagerhaltung zu senken, jede Woche Bestellungen auf, sobald das Produkt das Regal verlässt, mit einem genau festgelegten Liefertermin und einer genau festgelegten Uhrzeit. Infolgedessen kann der Mindestbestellwert in Geld 20.000 Rubel betragen. Darüber hinaus liegt zwischen der Bestellung beim Hersteller und der tatsächlichen Lieferung im Lager eine sehr große Zeitspanne von 3,5 Monaten, und es kommt häufig zu Verzögerungen bei der Lieferzeit von bis zu 4,5 Monaten. Es liegt auf der Hand, dass in diesem Fall unter allen gegebenen Voraussetzungen nicht nach dem JIT-System gearbeitet werden kann. Dazu ist es notwendig, das gesamte Organisationssystem neu aufzubauen. Daher ist es für das Unternehmen Euro Trade Rus rentabler, Waren in einem Lagerhaus zu lagern, als sie regelmäßig in kleinen Mengen zu liefern.
Daher wird Just-in-Time (JIT) heute nicht nur in der Produktion eingesetzt, wo die Technologie eingeführt wurde, sondern auch im Einzelhandel. Darüber hinaus kann dieses System auch von kleinen Unternehmen problemlos genutzt werden. Stimmt, nicht immer und nicht überall. Hier ist alles sehr individuell. Es muss immer abgewogen werden, ob es für das Unternehmen rentabel ist, ein solches Versorgungssystem zu nutzen, oder ob es besser ist, die Lagerbestände weiterhin zu lagern. In Russland beispielsweise gibt es bei Just-in-Time-Lieferungen viele Probleme, da unsere Lieferanten laut Statistik bei weitem nicht so verpflichtend sind.
Die Erfolgsgeschichte von Dell ist wahrscheinlich die berühmteste und am häufigsten zitierte, wenn es um das Konzept der Just-in-Time-Lieferung geht.
Der Aufstieg des Unternehmens Dell gelang einst vor allem der kompetenten Organisation des Just-in-Time-Systems. Zu Beginn seiner Reise entschied sich Michael Dell für den Direktvertrieb, wodurch er die Kosten des Unternehmens deutlich senken konnte. Während Tausende von Komponenten in den Lagern anderer Computerhersteller verstaubten, organisierte Dell ein System, das es ermöglichte, nur die benötigten Waren auf Lager zu haben. Der Zusammenbau des Computers begann erst nach der Bestellung. Dadurch verkaufte Dell den Computer günstiger als seine Konkurrenten und konnte sein Komponentensortiment viel schneller aktualisieren. Zum Vergleich: Dell begann 85 Tage vor HP mit der Installation des Pentium 4-Prozessors in seinen Computern. Es gab einfach nicht so viele unverkaufte P3 in den Lagerhäusern des Unternehmens.
Ein weiteres Beispiel kann angeführt werden: Der berühmte amerikanische Motorradhersteller Harley-Davidson sah sich in den 1970er Jahren einer zunehmenden Konkurrenz mit japanischen Unternehmen ausgesetzt: Honda, Yamaha, Suzuki und Kawasaki. Die meisten zuvor stabilen Unternehmen dieser Branche sind bankrott gegangen. Die vier japanischen Unternehmen könnten ihre Motorräder fast überall auf der Welt mit höherer Qualität und niedrigeren Preisen als ihre Konkurrenten liefern. 1978 versuchte Harley-Davidson vor Gericht nachzuweisen, dass japanische Unternehmen Motorräder zu Dumpingpreisen verkauften, d. h. unter ihren Kosten. Doch bei Gerichtsverhandlungen stellte sich heraus, dass die Betriebskosten japanischer Unternehmen 30 % niedriger sind als die von Harley-Davidson. Einer der Hauptgründe für diesen Zustand war die Verwendung der JIT-Betriebsart. Daher begann Harley-Davidson 1982 mit der Entwicklung und Implementierung eines Material-nach-Bedarf-Programms, ähnlich dem JIT. Das Unternehmen hatte anfangs Schwierigkeiten, aber im Laufe von fünf Jahren konnte es die Rüstzeit um 75 %, die Garantie- und Abfallkosten um 60 % sowie die Bestände an unfertigen Erzeugnissen um 22 Millionen US-Dollar reduzieren. Im gleichen Zeitraum stieg die Produktivität des Unternehmens um 30 % und das Unternehmen behauptet sich nun gut am Markt.
Einige Organisationen, die JIT implementiert haben, konnten Bestandsreduzierungen von bis zu 90 % verzeichnen; Bereiche, in denen gearbeitet wird – bis zu 40 %; Lieferkosten - bis zu 15 % usw. Zu den Vorteilen von JIT gehören:
Reduzierung der Materialbestände und unfertigen Arbeiten;
Reduzierte Lagervorlaufzeit;
Verkürzung der Produktionszeit;
Produktivitätssteigerung;
Verwendung von Geräten mit höherer Belastung;
Reduzierung des Abfallvolumens;
Verantwortungsbewusstere Einstellung der Mitarbeiter zur Arbeit;
Verbesserung der Beziehungen zu Lieferanten;
Die Gewohnheit entwickeln, Probleme, die während der Arbeit auftreten, konstruktiv zu lösen.
Tabelle 1
Berechnung der Auswirkung des Kaufs von Waren bei einem entfernten Lieferanten (in der Stadt R)
Indikatorname |
Einheit Messungen |
Bedeutung |
|
Kosten für die Lieferung von Waren von Stadt P nach Stadt N |
Rub./Kubikmeter |
||
Zinsen für die Gutschrift von Transportbeständen |
Rub./Kubikmeter |
||
Versandkosten |
Rub./Kubikmeter |
||
Versicherungskosten |
Rub./Kubikmeter |
||
Zusätzliche Kosten insgesamt |
Rub./Kubikmeter |
||
Der Kostenunterschied beträgt 1 Kubikmeter. Ladung |
Rub./Kubikmeter |
||
Auswirkung des Einkaufs in der Stadt R |
Rub./Kubikmeter |
||
Stadt, in der die Ware gekauft werden soll |
Einkäufer im Vertrieb von Konsumgütern
Versandkosten:
1. Tarif -400 RUR/Kubikmeter.
2. Der jährliche Zinssatz für ein zur Bezahlung von Waren aufgenommenes Darlehen beträgt 10 %, die Reisezeit beträgt 15 Tage.
13000 * 0,10 * (15: 365) = 546 RUR/Kubikmeter.
3. Zusätzliche Kosten für die Spedition 200 RUR/Kubikmeter.
4. Zusätzliche Kosten für die Transportversicherung 1,1 %
1,1 * 13000: 100 = 143 Rubel.
5. Kosten für die Frachtlieferung: 400+546+200+143=1289
6. 1000-1289=289
Als Ergebnis der Berechnungen kann der Kauf von Waren bei einem Lieferanten in der Stadt N empfohlen werden, weil Die Kosten sind um 289 RUB/Kubik niedriger als in der Stadt R.
Finden Sie einen Standort für das Auslieferungslager einer Einzelhandelskette, der es ermöglicht, den Transportaufwand für die Lieferung von Waren an die belieferten Filialen zu minimieren.
Tabelle 2
Koordinaten der Filialen (Verbraucher des Materialflusses)
Shop-Nr. |
Frachtumschlag, t/Monat. |
||
Die Kosten für die Lieferung von Waren von Lagern zu Filialen sind einer der Hauptfaktoren, die die Wahl des Standorts für ein Distributionslager beeinflussen. Diese Kosten können minimiert werden, indem ein Lager in der Nähe des Schwerpunkts der Güterströme platziert wird.
Die Koordinaten des Schwerpunkts von Güterströmen werden durch die Formeln bestimmt:

wobei Г i der Frachtumsatz des i-ten Verbrauchers ist;
X i, Y i - Koordinaten des i-ten Verbrauchers.
Durch die Platzierung eines Distributionslagers in der Nähe des gefundenen Schwerpunkts der Frachtströme werden die Kosten für die Lieferung von Waren vom Lager zu den bedienten Filialen minimiert.
Koordinaten des Schwerpunkts der Güterströme (X-Lager, Y-Lager), d. h. Der Ort, an dem sich ein Auslieferungslager befinden kann, wird durch die Formeln bestimmt:
In Abbildung 3 ist Punkt C (7;9) der Standort des Auslieferungslagers.

Abb. 3.
Antwort: Der Schwerpunkt der Frachtströme liegt in den folgenden Koordinaten: Y - 9, X - 7.