Контрольные карты. X и R карты
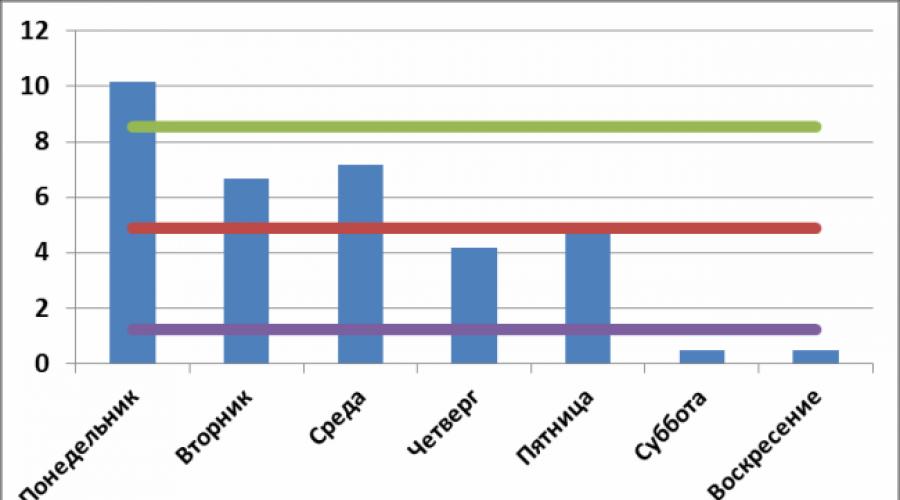
Читайте также
Недавно я публиковал здесь свой , где достаточно простым языком, местами злоупотребляя сквернословием, под 20-ти минутный хохот слушателей рассказывал о том, как отделить системные вариации от вариаций, вызванных особыми причинами.
Теперь хочу подробно разобрать пример построения контрольной карты Шухарта на основе реальных данных. В качестве реальных данных я взял историческую информацию о завершенных личных задачах. Эта информация у меня есть благодаря адаптации под себя модели личной эффективности Дэвида Аллена Getting Things (про это у меня тоже есть старый слайдкаст в трех частях: Часть 1 , Часть 2 , Часть 3 + Excel-табличка с макросами для анализа задач из Outlook).
Постановка задачи выглядит так. У меня имеется распределение среднего числа завершенных задач в зависимости от дня недели (ниже на графике) и нужно ответить на вопрос: «есть ли что-то особенное в понедельниках или это всего лишь погрешность системы?»
Ответим на этот вопрос при помощи контрольной карты Шухарта – основного инструмента статистического управления процессами.
Итак, критерий Шухарта наличия особой причины вариации достаточно прост: если какая-то точка выходит за контрольные пределы, рассчитанные особым образом, то она свидетельствует об особой причине. Если точка лежит внутри этих пределов, то отклонение обусловлено общими свойствами самой системы. Грубо говоря, является погрешностью измерений.
Формула для вычисления контрольных пределов выглядит так:
Где
- среднее значение средних значений по подгруппе,
- средний размах,
- некоторый инженерный коэффициент, зависящий от размера подгруппы.
Все формулы и табличные коэффициенты можно найти, например, в ГОСТ 50779.42-99 , где кратко и понятно изложен подход к статистическому управлению (честно, сам не ожидал, что есть такой ГОСТ. Более подробно тема статистического управления и его места в оптимизации бизнеса раскрыта в книге Д. Уилера).
В нашем случае мы группируем количество выполненных задач по дням недели – это и будет подгруппами нашей выборки. Я взял данные о числе завершенных задач за 5 недель работы, то есть, размер подгруппы равен 5. При помощи таблицы 2 из ГОСТа находим значение инженерного коэффициента:
Вычисление среднего значения и размаха (разницы между минимальным и максимальным значениями) по подгруппе (в нашем случае по дню недели) задача достаточно простая, в моем случае результаты такие:
Центральной линией контрольной карты будет являться среднее групповых средних, то есть:
Так же вычисляем средний размах:
Теперь мы знаем, что нижний контрольный предел для числа выполненных задач будет равен:
То есть, те дни, в которые я в среднем завершаю меньшее число задач, с точки зрения системы являются особенными.
Аналогично получаем верхний контрольный предел:
Теперь нанесем на график центральную линию (красная), верхний контрольный предел (зеленая) и нижний контрольный предел (фиолетовая):
И, о, чудо! Мы видим три явно особенные группы, выходящие за контрольные пределы, в которых присутствуют явно не системные причины вариаций!
По субботам и воскресеньям я не работаю. Факт. А понедельник оказался действительно особенным днем. И теперь можно думать и искать что же такого реально особенного в понедельниках.
Однако если бы среднее число выполненных в понедельник задач находилось внутри контрольных пределов и пусть даже сильно выделялось на фоне остальных точек, то с точки зрения Шухарта и Деминга искать какие-то особенности в понедельниках было бы бессмысленным занятием, так как подобное поведение обуславливается исключительно общими причинами. Например, я построил контрольную карту для других 5-ти недель в конце прошлого года:
И вроде как есть какое-то ощущение того, что понедельник как-то выделяется, но согласно критерию Шухарта - это всего-лишь флуктуация или погрешность самой системы. Согласно Шухарту, в данном случае можно сколь угодно долго исследовать особые причины понедельников - их просто нет. С точки зрения статистического управления, на этих данных понедельник ничем не отличается от любого другого рабочего дня (даже воскресенья).
40. 7 Инструментов контроля качества. Контрольные карты Шухарта по альтернативному признаку: виды, методика построения, анализ, рекомендации.
Карта для доли дефектных изделий (p-карта). В p-карте подсчитывается доля дефектных изделий в выборке. Она применяется, когда объем выборки - переменный.
Карта для числа дефектных изделий (np-карта). В np-карте подсчитывается число дефектных изделий в выборке. Она применяется, когда объем выборки - постоянный.
Карта для числа дефектов в выборке (с-карта). В с-карте подсчитывается число дефектов в выборке.
Карта для числа дефектов на одно изделие (u-карта). В u-карте подсчитывается число дефектов на одно изделие в выборке.
41. Статистический приемочный контроль: понятие, уровни дефектности, риски поставщика и потребителя.
Приёмочный статистический контроль , совокупность статистических методов контроля массовой продукции с целью выявления её соответствия заданным требованиям.П. с. к. - действенное средство обеспечения доброкачественности массовой продукции.
П. с. к . проводится на основе системы (стандарта) правил контроля, предписывающих использование определённого плана контроля в зависимости от количества изделий в контролируемой партии, результатов контроля предыдущих партий, трудоёмкости контроля и т.д. Основным методом отбора изделий для контроля является случайный выбор (без возвращения), при котором изделия наудачу отбираются для контроля, причём любой из возможных составов выборки имеет одинаковую вероятность.
Если по результатам контроля изделия классифицируются на годные и дефектные , то говорят, чтоконтроль проводится по альтернативному признаку . В практикеП. с. к. широко используются одноступенчатые планы контроля по альтернативному признаку, определяемые заданием числа n отбираемых для контроля изделий (n - объём выборки) и т. н. приёмочного числа с, смысл которого в следующем: если d - число обнаруженных в выборке дефектных изделий - больше с, то партия бракуется, если же d £ c, то принимается. Иногда выгодно использовать двухступенчатые планы П. с. к. по альтернативному признаку, определяемые объёмами n1 и n2 первой и второй выборок. Если d1 - число дефектных изделий, обнаруженных в первой выборке, - не более c1, то партия принимается, если же d1 ³ r1(r1 > c1), то бракуется. В тех случаях, когда c1 < d1 < r1, берётся вторая выборка, включающая n2. изделий. Если же общее число d1 + d2 дефектных объектов, обнаруженных в первой и второй выборках, не более c2, то партия принимается, если же d1 + d2 > c2, то бракуется. В некоторых случаях рекомендуется использовать многоступенчатые планы контроля, последовательные планы (см. Последовательный анализ) и др.
Для одних условий производства браковка партии влечёт за собой сплошную проверку всех изделий партии с целью устранения из неё всех дефектных изделий, для других означает уничтожение изделий или их использование в качестве сырья для повторного производства (металлические изделия идут в переплавку) и т.д. При использовании П. с. к. решение о приёмке или браковке проводится на основе контроля лишь части случайно отбираемых изделий. Поэтому всегда имеется не равная нулю вероятность приёмки партий, содержащих дефектные изделия. Когда контроль изделий носит разрушительный характер (испытания на разрыв и т.п.), П. с. к. является единственно возможным способом приёмочного контроля. Если при контроле свойства изделий не меняются, то в принципе возможен сплошной контроль. Тщательная выборочная проверка изделий может дать более объективные результаты, чем неизбежно менее тщательная (из-за увеличения объёма работы) сплошная проверка.
Если изделия отбираются для контроля на основе случайного выбора, то можно вычислить оперативную характеристику плана контроля, равную вероятности P (D) приёмки партии, содержащей D дефектных изделий.
В стандартах П. с. к. указывается, какие типы планов целесообразно использовать для контроля массовой продукции. Переход от контроля с одноступенчатыми планами к более сложным может уменьшить вероятность ошибочного принятия партий, содержащих большое число дефектных объектов (рис.). Однако планы, отличные от одноступенчатых, сложнее как с точки зрения их реализации, так и по методам получения на их основе статистических оценок для уровня качества массовой продукции.
Проблема текущего мониторинга качества продукции в процессе ее производства всегда остро стояла перед производителями. Если под мониторингом качества понимать не только непосредственную проверку пригодности выпускаемого изделия, но и наблюдение за тенденциями изменения качества, то поставленная задача представляется достаточно трудоемкой.
Для решения подобных вопросов в условиях современного производства менеджеры по контролю качества используют методики и процедуры, основанные на статистическом анализе характеристик изделий.
Одним из таких инструментов являются незаменимые при поточном мониторинге качества контрольные карты (или контрольные карты Шухарта)
, визуализирующие статистические характеристики исследуемого производственного процесса.
В данном материале рассматриваются модельные примеры контрольных карт и на их основе демонстрируются способы выявления нарушений качества.
Общий подход к текущему контролю качества достаточно прост. В процессе производства проводятся выборочные измерения изделий. После этого на графике (карте) строятся диаграммы изменчивости выборочных значений плановых спецификаций в выборках, и рассматривается степень их близости к заданным значениям. Если диаграммы обнаруживают наличие тренда выборочных значений или оказывается, что выборочные значения находятся вне заданных пределов, то считается, что процесс вышел из-под контроля, и предпринимаются необходимые действия для того, чтобы найти причину его разладки.
Критерии серий служит для выделения систематических тенденций в расположении точек контрольной карты, которые могут указать на разладку контролируемого процесса.
Контроль по непрерывному признаку
Для контроля качества по непрерывному признаку (анализа изменчивости параметров) обычно применяются X-bar, R или S карты.
На X-bar карту наносятся значения выборочных средних для того, чтобы контролировать отклонение непрерывной переменной от среднего значения.
На контрольную R-карту наносятся значения размахов выборок для контроля за степенью изменчивости непрерывного параметра, на S и S2 картах строятся соответственно графики выборочных стандартных отклонений и дисперсий.
Рисунок 1
Данный пример (см. Рисунок 1) демонстрирует контрольные карты «хорошего» процесса. Точки на обеих контрольных картах находятся внутри контрольных пределов. При этом не наблюдается ни систематических смещений (трендов), ни каких-либо других признаков выхода процесса из-под контроля: точки обеих карт равномерно (во всяком случае, на основе визуального анализа) колеблются относительно соответствующих средних линий.
Среднее значение шестой выборки находится достаточно близко к нижнему контрольному пределу, однако на фоне общей положительной картины, это не является тревожным событием. Управляемость процесса также подтверждается хорошей подгонкой гистограмм наблюдаемых выборочных средних и размахов теоретическим нормальным распределением (гистограммы в левой части рисунка).
Рисунок 2
В следующем примере, на рисунке выше приводятся «плохие» контрольные карты. Явно видно, что процесс плохо управляем: выборочные средние 1-й и 4-й выборок находится вне контрольных пределов. Также настораживает то, что шесть из семи выборочных средних находятся по одну сторону средней линии.
Дополнительно на разладку производственного процесса указывает гистограмма распределения выборочных средних (левый верхний график), показывающая явное отличие распределения средних от нормального.
Стоит также отметить, что при явных выбросах на X-bar карте, значения выборочных размахов (R-карта) лежат в рамках контрольных пределов.
Рисунок 3
В данном примере контрольных карт (см. Рисунок 3) демонстрируется обратная ситуация. Средние значения по выборкам (точки на X-bar карте) находятся в контрольных пределах, при этом на R-карте размахов имеется выброс (размах второй выборки выше верхнего контрольного предела). Большие значения в выборке с критическим размахом сокращаются с малыми значениями, в результате чего, выборочное среднее значение находится в пределах нормы. Также стоит отметить небольшое систематическое смещение на карте средних, но его при малом количестве выборок и критическом размахе значений такое смещение можно считать не существенным на данном этапе исследования.
В итоге в такой ситуации требуется проведение мероприятий по снижению разброса значений исследуемого параметра, после чего перейти к более глубокому анализу выборочных средних.
Рисунок 4
В следующем примере (см. Рисунок 4) снова можно наблюдать наличие выбросов на X-bar карте и их отсутствие на карте размахов. Однако наиболее показательным результатом в данном примере является наличие заметного тренда на обеих картах: положительного на карте средних и отрицательного на карте размахов. Систематическое снижение значений выборочных размахов означает сходимость процесса (уменьшение разброса значений). Казалось бы, это - положительное явление. Но, при положительном тренде значений средних, процесс, скорее всего, сходится к значению, лежащему вне контрольных пределов. В итоге, в скором времени, все измерения исследуемого параметра могут оказаться вне значений спецификаций.
Контроль качества по атрибуту
Другим типом контрольных карт являются карты по атрибутивному признаку (атрибуту) – например, по числу дефектных деталей в партии, по числу отклонений характеристик изделия от стандарта в расчете на выборку.
Преимущество контрольных карт по атрибутивному признаку состоит в возможности быстро получить общее представление о различных аспектах качества анализируемого изделия; то есть, на основании различных критериев качества инженер может сразу принять или забраковать продукцию.
Контрольные карты по атрибутивному признаку иногда позволяют обойтись без применения дорогих точных приборов и требующих значительных затрат времени для измерительных процедур. Кроме того, этот тип контрольных карт более понятен менеджерам, которые не разбираются в тонкостях методов контроля качества. Таким образом, с помощью этих карт можно более убедительно продемонстрировать руководству наличие проблем с качеством изделий.
Однако, по сравнению с контрольными картами по атрибутивному признаку, карты для непрерывных переменных обладают большей чувствительностью. Благодаря этому, контрольные карты для непрерывных переменных могут указать на существование проблемы ухудшения качества, прежде чем в потоке продукции появятся настоящие бракованные изделия, выделяемые с помощью контрольной карты по атрибутивному признаку.
Контрольные карты для непрерывных переменных можно считать предвестниками проблем ухудшения качества, которые предупреждают об их наличии задолго до того, как в процессе производства резко возрастет доля бракованных изделий.
Для контроля качества продукции по атрибутивному признаку обычно используются следующие типы карт:
- С-карта
- U-карта
- Np-карта
- P-карта
При использовании С- и U-карт принимается предположение о том, что дефекты контролируемой характеристики продукции встречаются сравнительно редко и контрольные пределы для данных типов карт рассчитываются на основе свойств распределения Пуассона (распределения редких событий).
В свою очередь контрольные пределы для Np- и P-карт рассчитываются на основе биномиального распределения , а не распределения редких событий. Поэтому данный тип карт должен использоваться в том случае, когда обнаружение дефекта не является редким событием (например, происходит более чем у 5% проверенных единиц продукции).
При этом на С- и Np-картах отображается число дефектов (в партии, в день, на один станок), а на U- и P-картах отображается относительная частота дефектов, то есть отношение числа обнаруженных дефектов к числу проверенных единиц продукции.
Рисунок 5
На рисунке выше представлен пример P-карты по атрибуту. На основе визуального анализа графика можно заключить, что данный процесс является управляемым: не наблюдается значений вне контрольных пределов (выбросов), нет заметного тренда, а также не наблюдаются систематические тенденции в расположении точек на карте.
Рисунок 6
В противовес предыдущему графику на данной P-карте (см. Рисунок 6) демонстрируется «плохой» процесс. В шестой и седьмой выборках встречается более 80% бракованных изделий, что выше предопределенных контрольных пределов. Естественно такой высокий процент отбраковки продукции свидетельствует о наличии серьезных проблем качества данного производственного процесса.
Рисунок 7
На следующей P-карте (см. Рисунок 7) также представлен пример «плохого» процесса. Причем, помимо выброса в последней выборке (80% брака), можно наблюдать систематическое увеличение процента бракованных изделий.
Аналогично продемонстрированным методам проводится визуальный анализ качества на основе других карт по атрибуту. Далее приводятся некоторые примеры текущего контроля качества на основе C-карты.
Рисунок 8
На этой С-карте показан хорошо управляемый технологический процесс: количество бракованной продукции в каждой выборке находится в рамках контрольных пределов.
Рисунок 9
А в этом примере (см. Рисунок 9) на C-карте наблюдается выброс (первая выборка). Однако соответствующие статистики по остальным выборкам находятся в рамках контрольных пределов. Таким образом, на основании этой карты, исключив первую выборку, можно считать процесс управляемым. Если проблемная выборка отражает начало реального технологического процесса, то, скорее всего, ее неудовлетворительное качество связано с первоначальной настройкой процесса. В этом случае рекомендуется провести дополнительный анализ качества продукции, выпущенной на начальном этапе и, исключив имеющийся выброс, признать процесс управляемым.
Резюме
В заключение еще раз хочется подчеркнуть высокую эффективность применения контрольных карт в управлении качеством. Используя подходящие средства графического отображения, человеческий глаз способен отлавливать признаки ухудшения качества и тревожные тенденции в режиме поточного конвейерного производства.
При этом мощный аналитический пакет, такой как STATISTICA , способен взять на себе практически всю работу по обнаружению признаков разладки технологического процесса в online режиме, оставив оператору лишь анализ наиболее изощренных критериев визуальной проверки качества (малых трендов).
Прежде чем приступать к непосредственному построению контрольных карт, ознакомимся с основными этапами поставленной задачи. Итак, ввиду того, что разные авторы преследуют свои цели, описывая построение контрольных карт, ниже будет представлено оригинальное видение этапов построения контрольных карт Шухарта.
Алгоритм построения контрольных карт Шухарта:
I. Анализ процесса.
В первую очередь необходимо задаться вопросом о существующей проблеме, потому что, при отсутствии оных, проведение анализа не будет иметь смысла. Для большей наглядности, можно воспользоваться причинно-следственной диаграммой Исикавы (упоминалась выше, гл. 2). Для ее составления рекомендуется привлечение сотрудников из разных отделов и использование мозгового штурма. Проведя доскональный анализ проблемы, и выяснив факторы, на нее влияющие переходим ко второму этапу.
II. Выбор процесса.
Прояснив в предыдущем этапе влияющие на процесс факторы, нарисовав детальный скелет «рыбы», необходимо выбрать процесс, который будет подвержен дальнейшему исследованию. Этот этап очень важен, потому что, выбор неверных показателей сделает всю контрольную карту менее эффективной, ввиду исследования малозначительных показателей. На этом этапе стоит осознавать, что выбор соответственного процесса и показателя определяет исход всего исследования и затрат, связанного с ним.
Приведем некоторые примеры, возможных показателей:
Таблица 1. Применение контрольных кар в сервисных организациях
Источник Эванс Дж. Управление качеством: учебн. Пособие/Дж. Эванс.-М.: Юнити-Дана, 2007.
При этом, показатель следует выбирать, руководствуясь главной целью компании, а именно, удовлетворение потребностей покупателей. Когда выбран процесс и показатель, его характеризующий можно переходить к сбору данных.
III. Сбор данных.
Цель данного этапа - сбор данных о процессе. Для этого, необходимо спроектировать наиболее пригодный способ для сбора данных, выяснить, кто и в какое время будет проводить замеры. Если процесс не оснащен техническими средствами, позволяющими автоматизировать занесение и обработку данных, возможно применение одного из семи простых способов Исикавы - контрольных листков. Контрольные листки, фактически, представляют собой бланки, для регистрации исследуемого параметра. Их преимущество заключается в простоте использования и легкости обучения сотрудников. Если же на рабочем месте имеется компьютер, возможно занесение данных через соответствующие программные продукты.
В зависимости от специфики показателя, определяется частота, время сбора и объем выборки для обеспечения репрезентативности данных. Собранные данные являются основой для проведения дальнейших операций и вычислений.
После сбора информации, исследователь должен принять решение о необходимости группировки данных. Разбиение на группы зачастую определяет работоспособность контрольных карт. Здесь, с помощью уже проведенного анализа с применением причинно-следственной диаграммы можно установить факторы, по которым можно будет наиболее рационально сгруппировать данные. Следует учесть, что данные внутри одной группы должны обладать небольшой изменчивостью, в ином случае, данные могут быть ложно интерпретированы. Также, если процесс делится с помощью стратифицирования на части, следует проанализировать каждую их частей в отдельности (пример: изготовление одинаковых деталей, разными работниками).
Изменение способа группирования, будет приводить к изменению факторов, которые образуют внутригрупповые вариации. Следовательно, необходимо изучить факторы, влияющие на изменение показателя, чтобы суметь применить правильную группировку.
IV. Вычисление значений контрольной карты.
Контрольные карты Шухарта делятся на количественные и качественные (альтернативные) в зависимости от измеримости исследуемого показателя. Если значение показателя измеримо (температура, вес, размер, и др.) применяют карты значения показателя, размахов и двойные карты Шухарта. Напротив, если показатель не позволяет применять числовые измерения, используют типы карт, для альтернативного признака. Фактически, показатели, исследуемые по такому признаку, определяются как соответствующие или не соответствующие предъявляемым требованиям. Отсюда и использование карт для доли (числа) дефектов и числа соответствий (несоответствий) на единицу продукции.
Для любого типа карт Шухарта предполагается определение центральной и контрольных линий, где центральная линия (CL-control limit), фактически представляет собой среднее значение показателя, а контрольные границы (UCL-upper control limit; LCL-lower control limit) - допустимые значения допуска.
Значения верхней и нижней контрольных границ определяются по формулам для разных типов карт, как можно видеть из схемы в приложении 1. Для их вычисления, с целью замены громоздких формул, используют коэффициенты из специальных таблиц для построения контрольных карт, где значение коэффициента зависит от объема выборки (приложение 2). Если же объем выборки велик, то используют карты, дающие наиболее полную информацию.
На данном этапе исследователь должен вычислить значения CL, UCL, LCL.
V. Построение контрольной карты.
Итак, мы и подошли к наиболее интересному процессу - графическое отражение полученных данных. Итак, если данные заносились в компьютер, то с помощью среды программ Statistica или Excel, можно, быстро графически изобразить данные. Однако можно построить контрольную карту и, не имея специальных программ, тогда, по оси OY контрольных карт откладываем значения показателя качества, а по OX - моменты времени регистрации значений, в такой последовательности:
1. наносим на контрольную карту центральную линию (CL)
2. наносим границы (UCL; LCL)
3. отражаем, полученные в ходе исследования данные, путем нанесения соответствующего маркера в точку пересечения значения показателя и времени его регистрации. Рекомендуется использование разных типов маркеров для значений, находящихся внутри границ допуска и выходящих за эти границы.
4. в случае использования двойных карт, повторите пункты 1-3 для второй карты.
VI. Проверка стабильности и управляемости процесса.
Этот этап призван показать нам то, ради чего и проводились исследования - стабилен ли процесс. Под стабильностью (статистической управляемостью) понимают состояние, при котором гарантирована повторяемость параметров. Таким образом, процесс будет стабилен, только в том случае, если не происходят нижеперечисленные случаи.
Рассмотрим основные критерии нестабильности процесса:
1. Выход за контрольные границы
2. Серия - определенное число точек, неизменно оказывающееся по одну сторону от центральной линии - (сверху)снизу.
Серия длиной в семь точек рассматривается как ненормальная. Кроме того, ситуацию следует рассматривать как ненормальную, если:
а) не менее 10 из 11 точек оказываются по одну сторону от центральной линии;
б) не менее 12 из 14 точек оказываются по одну сторону от центральной линии;
в) не менее 16 из 20 точек оказываются по одну сторону от центральной линии.
3. тренд - непрерывно повышающаяся или понижающаяся кривая.

4. приближение к контрольным границам. Если 2 или 3 точки оказываются очень близки к контрольным границам, это свидетельствует о ненормальности распределения.

5. приближение к центральной линии. Если значения концентрируются около центральной линии, это может свидетельствовать о неверном выборе способа группировки, что делает размах слишком широким и приводит к смешиванию данных различным распределений.

6. периодичность. Когда, спустя, определенные равные промежутки времени, кривая идет то на «спад», то на «подъем».

VII. Анализ контрольных карт.
Дальнейшие действия основываются на выводе о стабильности или нестабильности процесса. Если процесс не отвечает критериям стабильности, следует уменьшить влияние неслучайных факторов и, собрав новые данные, построить контрольную карту. Но, если процесс отвечает критериям стабильности, необходимо оценить возможности процесса (Cp). Чем меньше разброс параметров внутри границ допуска, тем выше значение показателя возможности процесса. Показатель отражает отношение ширины параметра и степень его разброса. Круглов М.Г., Шишков Г.М. Менеджмент качества как он есть/М.Г. Круглов, Г.М. Шишков.- М.: Эксмо, 2006. Индекс возможности рассчитывается как, где можно вычислить как.

Если вычисленный показатель меньше 1, то исследователю нужно усовершенствовать процесс, либо остановить изготовление продукции, либо изменить требования к продукции. При значении индекса:
Cр<1 возможности процесса неприемлемы,
Cр=1 процесс находится на грани требуемых возможностей,
Cр>1 процесс удовлетворяет критерию возможности.

В случае отсутствия смещения относительно центральной линии Cp=Cpk , где. Два этих показателя используют всегда совместно, для определения статуса процесса, так, в машиностроении считается нормой, что означает, что вероятность несоответствия не превышает 0,00006.
Теперь, рассмотрев алгоритм построения контрольных карт, разберем конкретный пример.
Задание: Контролируется содержание хрома в стальных отливках. Проводят замеры в четырех плавках. В таблице 2 приведены данные по 15 подгруппам. Необходимо построить карту.
Решение: Поскольку уже заранее известно, какой тип карты необходимо построить, вычислим значения
номер подгруппы |
||||||

Следующим шагом будет вычисление, где, в соответствии с вышеуказанной схемой, а. Теперь, имея, значения центральной линии, среднего значения показателя и среднего отклонения, найдем значения контрольных границ карт.
Где находится по таблице коэффициентов для вычислений линий контрольных карт и равно 0,729. Тогда UCL=0,880 , LCL=0,596.
Для значений нижние и верхние контрольные границы определяются по формулам:
где и находятся по таблице коэффициентов для вычислений линий контрольных карт и равны 0,000 и 2,282 соответственно. Тогда UCL=0,19*2,282=0,444 и LCL=0,19*0,000=0.
Построим контрольные карты для средних значений и размахов данной выборки, при помощи Excel:


Как мы можем удостовериться, контрольные карты не выявили неслучайные значения, выходы за контрольные границы, серии или тренды. Однако, график средних значений тяготеет к центральному положению, что может свидетельствовать как о неверно выбранных границах допуска, так и о ненормальности распределения и нестабильности процесса. Дабы удостоверится, вычислим индекс возможности процесса. , где можно вычислить как, по таблице коэффициентов, найдем значение, равное;


Так как, вычисленный индекс <1, что свидетельствует о неприемлемости возможностей процесса, его статистической неуправляемости и не стабильности. Необходимо провести усовершенствования процесса, установить контроль над его протеканием, с целью уменьшения влияния не случайных факторов.