Four de fusion à induction pour la fusion des métaux. Fours à induction pour la fusion des métaux
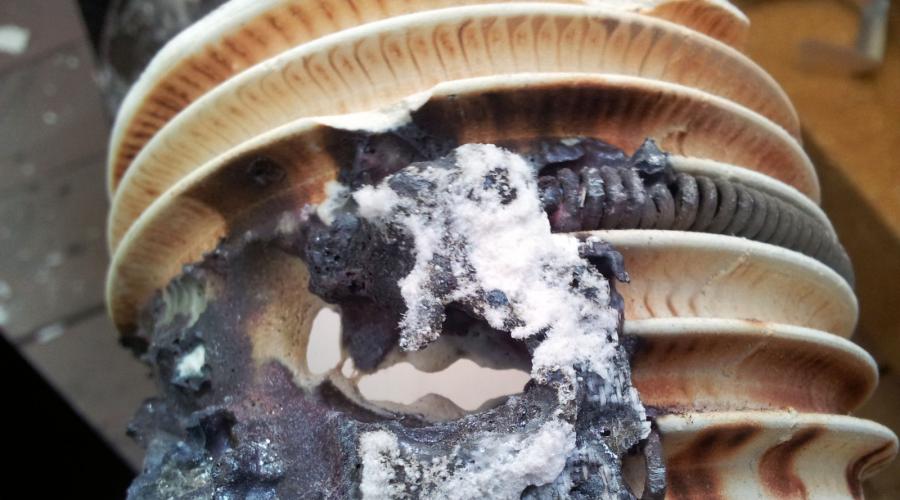
Lire aussi
Tout a commencé avec le fait que j'avais besoin d'un poêle pour... tout. J'avais envie de fondre et de chauffer de l'acier et de me brûler les mains, le tout en un mot. J'ai décidé d'emprunter la voie simple et j'ai commandé celui-ci chez Ali pour 10 000 (+5 000 frais d'expédition) :
J'ai travaillé exactement deux fois >_< после чего спираль потекла и попортила муфель:
En général, je recommande fortement de ne pas acheter de poêles aux Chinois ; ils mourront en un rien de temps. Cependant, j'ai réussi à obtenir un remboursement complet et Ali a pris mon parti. Mais hors frais de port. Il semble que j'en ai reçu 5 000, mais ce qui me restait entre les mains était ce qui restait du four, à savoir : un creuset en graphite, un tas de réfractaires, un thermocouple et un régulateur, ainsi que des pinces à la mode. Au final, c'est probablement un match nul.
Le four est mort, vive le nouveau four !
J'ai déjà assemblé celui-ci moi-même à partir de ceci :
Brique réfractaire ШЛ - 1 (je pense, je ne me souviens plus exactement quel numéro) :
Ce qu'il faut, c'est de la chamotte légère, car elle est très pratique pour découper des rainures pour la spirale, et elle est également très légère (très cassante, par contre). On découpe des rainures dans 4 briques pour obtenir une spirale montant de bas en haut afin de placer une autre spirale de féchral dans cette spirale. J'ai fait le fond avec quelques briques identiques et j'en ai coupé quelques autres en bouchons dans les coins du poêle. Vous pouvez coller le tout en place avec un composé ignifuge pour la pose de cheminées et poêles, du mastic ignifuge ou de la colle ignifuge.
Ensuite, il vous faut absolument un féchral, ou mieux encore un superféchral. Le nichrome ne fonctionnera pas ; il brûlera au contact de l'air. J'ai acheté cet écheveau à Novossibirsk (ne faites pas attention à ce qu'il y a dessus) :
Ils le vendent au poids et ici il fait 3 kg, la résistivité de ce fil est de 1,78 µOhm par mètre. Le calcul de la longueur de fil requise est très simple : le carré de la tension est divisé par la puissance (il me fallait 1,5 kW) et la résistivité. Autrement dit, dans mon cas : 220*220/1500 = 32 Ohms. 32/1,78=18 mètres. Au total, nous prenons 18 mètres de fil et l'enroulons sur une tige du diamètre requis - afin qu'il s'insère bien dans les rainures sciées dans les briques. Vous pouvez l'enrouler rapidement, par exemple à l'aide d'un tournevis. Je me suis serré la main %-)
La spirale devra être étirée pour que les spires ne se touchent pas et placée dans les rainures
Plus vous pouvez insérer étroitement la spirale dans les rainures et les coins, mieux c'est - lorsqu'il est chauffé, le féchral devient plus mou et peut s'affaisser et tomber des rainures. La spirale sort par le haut et par le bas (sur la photo ci-dessus vous pouvez voir la sortie par le haut). Il vaut la peine de tordre les sorties en deux pour que le fil ne devienne pas trop chaud. J'ai connecté les extrémités avec des fils de cuivre aux restes électroniques d'un four chinois. Je ne démonterai pas mon poêle pour les photographier, mais de tels régulateurs sont vendus dans les grands magasins de pièces détachées radio. Ils ressemblent à ceci (à gauche) :
En principe, vous pouvez déjà l'allumer et tout, en théorie, fonctionnera (il devrait y en avoir suffisamment pour faire fondre l'aluminium). Cependant, avec une utilisation à plus ou moins longue durée, il y aura d'importantes pertes de chaleur et il ne sera pas possible de développer la température de fusion du cuivre, par exemple. Dans ce cas, la laine de mullite-silice, le même feutre ou une sorte de fibre céramique seront utiles. Tout cela est vendu dans les magasins de produits réfractaires en ligne et est tout à fait abordable. Le coton coûte environ 200 roubles par kg. Il doit être enroulé autour de la chambre de travail et boucher généralement tous les trous afin que la chaleur ne s'échappe nulle part de la chambre. En théorie, il est préférable de refaire le couvercle avec de la chamotte légère et de rembourrer plus de coton pour qu'il s'ajuste mieux %-) En bref, rendre la chambre aussi isolée que possible du monde extérieur.
C'est vrai, mes mains ne peuvent toujours pas atteindre le couvercle, alors j'ai simplement mis de la fibre céramique provenant d'un four chinois en trois couches sur le dessus (à 1000 degrés à l'intérieur, vous pouvez facilement appuyer sur la fibre dessus avec une main non protégée).
Oh oui, j'ai oublié quelque chose - la laine de mullite-silice est imprégnée d'une sorte de non-sens huileux pour faciliter son installation. Lorsqu'il est chauffé, il brûle et pue assez sensiblement, au début le coton va fumer, puis tout ira bien.
Encore une chose : le thermocouple (alias thermomètre) ne doit absolument pas être placé dessus, comme le mien. Le fait est que dans cette position, la température est proche, indiquant, dans mon cas, environ 100 degrés de moins que dans la zone de travail où est suspendue la pièce sur la photo ci-dessus.
Et bien sûr, gardez à l’esprit que le courant circule en spirale. Avant d'entrer dans le four, coupez l'alimentation ou faites extrêmement attention à ne pas toucher la bobine sous tension.
Le type de chauffage le plus avancé est celui dans lequel la chaleur est créée directement dans le corps chauffé. Cette méthode de chauffage est très bien réalisée en faisant passer un courant électrique à travers le corps. Cependant, l'inclusion directe d'un corps chauffé dans un circuit électrique n'est pas toujours possible pour des raisons techniques et pratiques.
Dans ces cas, le type de chauffage parfait peut être obtenu en utilisant le chauffage par induction, dans lequel la chaleur est également créée dans le corps chauffé lui-même, ce qui élimine la consommation d'énergie inutile, généralement importante, dans les parois du four ou dans d'autres éléments chauffants. Par conséquent, malgré l'efficacité relativement faible de la génération de courants à hautes et hautes fréquences, l'efficacité globale du chauffage par induction est souvent supérieure.
La méthode d'induction permet également un chauffage rapide des corps non métalliques de manière uniforme sur toute leur épaisseur. La mauvaise conductivité thermique de tels corps exclut la possibilité d'un chauffage rapide de leurs couches internes de la manière habituelle, c'est-à-dire en fournissant de la chaleur de l'extérieur. Avec la méthode d'induction, la chaleur est générée de manière égale dans les couches externe et interne, et il peut même y avoir un risque de surchauffe de cette dernière si l'isolation thermique nécessaire des couches externes n'est pas réalisée.
Une propriété particulièrement précieuse du chauffage par induction est la possibilité d'une très forte concentration d'énergie dans le corps chauffé, qui se prête facilement à un dosage précis. Il n'est possible d'obtenir que le même ordre de densité énergétique, cependant, ce mode de chauffage est difficile à contrôler.
Les caractéristiques et les avantages bien connus du chauffage par induction ont créé de larges possibilités d'utilisation dans de nombreuses industries. De plus, cela permet de créer de nouveaux types de structures qui ne sont pas du tout réalisables avec les méthodes conventionnelles de traitement thermique.
Processus physique
Dans les fours et les appareils à induction, la chaleur dans un corps chauffé électriquement conducteur est libérée par les courants induits par un champ électromagnétique alternatif. Ainsi, un chauffage direct a lieu ici.
Le chauffage par induction des métaux est basé sur deux lois physiques : et la loi Joule-Lenz. Des corps métalliques (ébauches, pièces, etc.) y sont placés, ce qui y excite un vortex. La force électromotrice induite est déterminée par le taux de variation du flux magnétique. Sous l'influence de la force électromotrice induite, des courants de Foucault (enfermés à l'intérieur des corps) circulent dans les corps, libérant de la chaleur. Cet EMF se crée dans le métal, l'énergie thermique libérée par ces courants provoque un échauffement du métal. Le chauffage par induction est direct et sans contact. Il permet d'atteindre des températures suffisantes pour faire fondre les métaux et alliages les plus réfractaires.
Un chauffage par induction intense n'est possible que dans des champs électromagnétiques de haute intensité et fréquence, créés par des dispositifs spéciaux - des inducteurs. Les inducteurs sont alimentés à partir d'un réseau 50 Hz (réglages de fréquence industriels) ou de sources d'alimentation individuelles - générateurs et convertisseurs de moyennes et hautes fréquences.
L'inducteur le plus simple pour les appareils de chauffage par induction indirecte à basse fréquence est un conducteur isolé (allongé ou enroulé) placé à l'intérieur d'un tuyau métallique ou placé sur sa surface. Lorsque le courant circule à travers le conducteur inducteur, des éléments chauffants sont induits dans le tuyau. La chaleur du tuyau (il peut aussi s'agir d'un creuset, d'un récipient) est transférée au milieu chauffé (eau circulant dans le tuyau, air, etc.).
Chauffage par induction et trempe des métaux
Le plus largement utilisé est le chauffage par induction directe des métaux à moyennes et hautes fréquences. À cette fin, des inducteurs spécialement conçus sont utilisés. L'inducteur émet , qui tombe sur le corps chauffé et y est amorti. L'énergie de l'onde absorbée est convertie en chaleur dans le corps. Plus le type d'onde électromagnétique émise (plate, cylindrique, etc.) est proche de la forme du corps, plus l'efficacité de chauffage est élevée. Par conséquent, des inducteurs plats sont utilisés pour chauffer des corps plats et des inducteurs cylindriques (solénoïdes) sont utilisés pour chauffer des pièces cylindriques. En général, ils peuvent avoir une forme complexe, en raison de la nécessité de concentrer l’énergie électromagnétique dans la direction souhaitée.
Une caractéristique de l’apport d’énergie inductive est la capacité de réguler l’emplacement spatial de la zone d’écoulement.
Premièrement, des courants de Foucault circulent dans la zone couverte par l’inducteur. Seule la partie du corps qui est en connexion magnétique avec l'inducteur est chauffée, quelles que soient les dimensions hors tout du corps.
Deuxièmement, la profondeur de la zone de circulation des courants de Foucault et, par conséquent, la zone de libération d'énergie dépend, entre autres facteurs, de la fréquence du courant inducteur (augmente à basse fréquence et diminue avec l'augmentation de la fréquence).
L'efficacité du transfert d'énergie de l'inducteur au courant chauffé dépend de la taille de l'écart entre eux et augmente à mesure qu'il diminue.
Le chauffage par induction est utilisé pour le durcissement superficiel des produits en acier, par chauffage pour la déformation plastique (forgeage, estampage, pressage, etc.), la fusion des métaux, le traitement thermique (recuit, revenu, normalisation, durcissement), le soudage, le surfaçage et le brasage de les métaux.
Le chauffage indirect par induction est utilisé pour chauffer des équipements de traitement (conduites, conteneurs, etc.), chauffer des fluides liquides, sécher des revêtements et des matériaux (par exemple le bois). Le paramètre le plus important des installations de chauffage par induction est la fréquence. Pour chaque processus (durcissement superficiel, par chauffage), il existe une gamme de fréquences optimale qui offre les meilleures performances technologiques et économiques. Pour le chauffage par induction, des fréquences de 50 Hz à 5 MHz sont utilisées.
Avantages du chauffage par induction
1) Le transfert d’énergie électrique directement vers le corps chauffé permet un chauffage direct des matériaux conducteurs. Dans le même temps, la vitesse de chauffage augmente par rapport aux installations indirectes, dans lesquelles le produit n'est chauffé que depuis la surface.
2) Le transfert d'énergie électrique directement vers le corps chauffé ne nécessite pas de dispositifs de contact. Ceci est pratique dans les conditions de production en ligne de production automatisée, lors de l'utilisation d'équipements sous vide et de protection.
3) En raison du phénomène d’effet de surface, une puissance maximale est libérée dans la couche superficielle du produit chauffé. Par conséquent, le chauffage par induction pendant le durcissement permet un chauffage rapide de la couche superficielle du produit. Ceci permet d'obtenir une dureté élevée de la surface de la pièce à noyau relativement visqueux. Le processus de durcissement de surface par induction est plus rapide et plus économique que les autres méthodes de durcissement de surface d'un produit.
4) Le chauffage par induction permet dans la plupart des cas d'augmenter la productivité et d'améliorer les conditions de travail.
Fours de fusion à induction
Un four ou un appareil à induction peut être considéré comme une sorte de transformateur dans lequel l'enroulement primaire (inducteur) est connecté à une source de courant alternatif et le corps chauffé lui-même sert d'enroulement secondaire.
Le processus de travail des fours de fusion à induction est caractérisé par le mouvement électrodynamique et thermique du métal liquide dans un bain ou un creuset, ce qui contribue à l'obtention d'un métal de composition homogène et de sa température uniforme dans tout le volume, ainsi que de faibles déchets métalliques (plusieurs fois moins que dans les fours à arc).
Les fours de fusion par induction sont utilisés dans la production de pièces moulées, y compris de pièces façonnées, à partir d'acier, de fonte, de métaux et d'alliages non ferreux.
Les fours de fusion par induction peuvent être divisés en fours industriels à canal de fréquence et en fours à creuset industriels, moyenne et haute fréquence.
Un four à induction à canal est un transformateur, généralement de fréquence industrielle (50 Hz). L'enroulement secondaire du transformateur est une bobine de métal en fusion. Le métal est enfermé dans un canal annulaire réfractaire.
Le flux magnétique principal induit une FEM dans le métal du canal, la FEM crée un courant, le courant chauffe le métal, donc un four à canal à induction est similaire à un transformateur fonctionnant en mode court-circuit.
Les inducteurs des fours à canal sont constitués d'un tube de cuivre longitudinal, il est refroidi à l'eau, la partie canal de la pierre de foyer est refroidie par un ventilateur ou par un système d'air centralisé.
Les fours à canal à induction sont conçus pour un fonctionnement continu avec de rares transitions d'une qualité de métal à une autre. Les fours à induction à canal sont principalement utilisés pour fondre l'aluminium et ses alliages, ainsi que le cuivre et certains de ses alliages. D'autres séries de fours sont spécialisées comme mélangeurs pour contenir et surchauffer la fonte liquide, les métaux non ferreux et les alliages avant de les verser dans des moules.
Le fonctionnement d'un four à creuset à induction repose sur l'absorption de l'énergie électromagnétique d'une charge conductrice. La cage est placée à l'intérieur d'une bobine cylindrique - un inducteur. D'un point de vue électrique, un four à creuset à induction est un transformateur à air en court-circuit dont l'enroulement secondaire est une charge conductrice.
Les fours à creuset à induction sont utilisés principalement pour la fusion des métaux destinés aux pièces moulées façonnées en mode discontinu, ainsi que, quel que soit le mode de fonctionnement, pour la fusion de certains alliages, comme le bronze, qui ont un effet néfaste sur le revêtement des fours à canaux.
Un four à induction est utilisé pour faire fondre les métaux non ferreux et ferreux. Les unités de ce principe de fonctionnement sont utilisées dans les domaines suivants : de la fabrication de bijoux les plus raffinés à la fusion industrielle de métaux à grande échelle. Cet article abordera les caractéristiques de divers fours à induction.
Fours à induction pour la fusion des métaux
Principe d'opération
Le chauffage par induction constitue la base du fonctionnement du four. Autrement dit, le courant électrique crée un champ électromagnétique et de la chaleur est obtenue, qui est utilisée à l'échelle industrielle. Cette loi de la physique est étudiée dans les dernières années du secondaire. Mais il ne faut pas confondre la notion d'unité électrique et de chaudières à induction électromagnétique. Bien que la base du travail ici et là soit l'électricité.
Comment cela peut-il arriver
Le générateur est connecté à une source de courant alternatif, qui y pénètre via un inducteur situé à l'intérieur. Le condensateur est utilisé pour créer un circuit d'oscillation basé sur une fréquence de fonctionnement constante sur laquelle le système est réglé. Lorsque la tension dans le générateur augmente jusqu'à une limite de 200 V, l'inducteur crée un champ magnétique alternatif.
Le circuit est fermé, le plus souvent, grâce à un noyau en alliage ferromagnétique. Le champ magnétique alternatif commence à interagir avec le matériau de la pièce et crée un puissant flux d'électrons. Une fois que l'élément électriquement conducteur entre en action inductive, le système subit apparition de contraintes résiduelles, qui dans le condensateur contribue à l'apparition de courants de Foucault. L'énergie des courants de Foucault est convertie en énergie thermique de l'inducteur et le métal souhaité est chauffé à des températures de fusion élevées.
La chaleur produite par l'inducteur est utilisée :
- pour faire fondre les métaux mous et durs ;
- pour durcir la surface de pièces métalliques (par exemple des outils);
- pour le traitement thermique de pièces déjà produites ;
- besoins du ménage (chauffage et cuisine).
Brèves caractéristiques de divers fours
Types d'appareils
Fours à creuset à induction
Il s’agit du type de four à induction le plus courant. Une particularité qui diffère des autres types est qu'un champ magnétique alternatif y apparaît en l'absence de noyau standard. Creuset en forme de cylindre situé à l'intérieur de la cavité de l'inducteur. Le four, ou creuset, est constitué d'un matériau résistant parfaitement au feu et est relié au courant électrique alternatif.
Aspects positifs

Les unités à creuset comprennent à des sources de chaleur respectueuses de l'environnement, l'environnement n'est pas pollué par la fusion des métaux.
Il existe des inconvénients dans le fonctionnement des fours à creuset :
- lors du traitement technologique, des scories à basse température sont utilisées ;
- Le revêtement produit des fours à creuset a une faible résistance à la destruction, ce qui est particulièrement visible lors de changements brusques de température.
Les inconvénients existants ne posent pas de difficultés particulières ; les avantages d'une unité d'induction à creuset pour la fusion du métal sont évidents et ont rendu ce type d'appareil populaire et demandé par un large éventail de consommateurs.
Fours de fusion à induction à canaux
Ce type est largement utilisé dans la fusion des métaux non ferreux. Utilisé efficacement pour le cuivre et les alliages de cuivre à base de laiton, cupronickel, bronze. L'aluminium, le zinc et les alliages contenant ces métaux sont activement fondus dans les unités à canaux. L'utilisation généralisée de fours de ce type est limitée en raison de l'incapacité de fournir un revêtement résistant à la rupture sur les parois internes de la chambre.
Le métal en fusion dans les fours à induction à canaux subit mouvement thermique et électrodynamique, qui assure une homogénéité constante du mélange des composants de l'alliage dans le bain du four. L'utilisation de fours à canaux fonctionnant selon le principe de l'induction est justifiée dans les cas où des exigences particulières sont imposées au métal en fusion et aux lingots fabriqués. Les alliages sont de haute qualité en termes de coefficient de saturation des gaz et de présence d'impuretés organiques et synthétiques dans le métal.
Les fours à induction à canaux fonctionnent comme un mélangeur et sont conçus pour niveler la composition, maintenir une température de processus constante et sélectionner la vitesse de coulée dans les cristalliseurs ou les moules. Pour chaque alliage et composition de coulée, il existe des paramètres pour une charge spéciale.
Avantages
- l'alliage est chauffé dans la partie inférieure, à laquelle il n'y a pas d'accès à l'air, ce qui réduit l'évaporation de la surface supérieure, chauffée à une température minimale ;
- les fours à canaux sont classés comme fours à induction économiques, puisque la fusion qui se produit est assurée par une faible consommation d'énergie électrique ;
- le four a un rendement élevé grâce à l'utilisation d'un fil magnétique en boucle fermée ;
- La circulation constante du métal en fusion dans le four accélère le processus de fusion et favorise un mélange uniforme des composants de l'alliage.
Défauts
- la durabilité du revêtement interne en pierre diminue lorsque des températures élevées sont utilisées ;
- le revêtement est détruit lors de la fusion d'alliages chimiquement agressifs de bronze, d'étain et de plomb.
- lors de la fusion d'une charge contaminée de faible qualité, les canaux se bouchent ;
- les scories de surface dans le bain ne s'échauffent pas à une température élevée, ce qui ne permet pas d'effectuer des opérations dans l'interstice entre le métal et l'abri et de faire fondre les copeaux et ferrailles ;
- les unités à canaux ne tolèrent pas les interruptions de fonctionnement, ce qui les oblige à stocker en permanence une quantité importante d'alliage liquide dans la bouche du four.
L'élimination complète du métal en fusion du four entraîne sa fissuration rapide. Pour la même raison, il est impossible d'effectuer une analyse rapide conversion d'un alliage à un autre, il faut réaliser plusieurs fontes intermédiaires, appelées lest.
Fours à induction sous vide
Ce type est largement utilisé pour fondre des aciers de haute qualité et des alliages de nickel, de cobalt et de fer résistants à la chaleur. L'unité gère avec succès la fusion des métaux non ferreux. Le verre est bouilli dans des unités sous vide, les pièces sont traitées à haute température, produire des monocristaux.
Le four est classé comme un générateur haute fréquence situé dans un inducteur isolé de l'environnement extérieur, laissant passer un courant haute fréquence. Pour créer un vide, des masses d'air en sont pompées. Toutes les opérations d'introduction des additifs, de chargement de la charge et de distribution du métal sont réalisées par des mécanismes automatiques à commande électrique ou hydraulique. Les alliages avec de petits mélanges d'oxygène, d'hydrogène, d'azote et de matières organiques sont obtenus à partir de fours sous vide. Le résultat est bien supérieur aux fours à induction ouverts.
Acier résistant à la chaleur des fours sous vide utilisé dans la production d'outils et d'armes. Certains alliages de nickel contenant du nickel et du titane sont chimiquement actifs et il est problématique de les obtenir dans d'autres types de fours. Les fours sous vide effectuent la coulée du métal en faisant tourner le creuset dans l'espace interne du boîtier ou en faisant tourner la chambre avec un four fixe. Certains modèles ont un trou d'ouverture dans le fond pour évacuer le métal dans un conteneur installé.
Fours à creuset avec convertisseur à transistors
Utilisé pour les métaux non ferreux de poids limité. Ils sont mobiles, légers et peuvent être facilement déplacés d’un endroit à l’autre. L'ensemble du four comprend un transistor haute tension convertisseur universel. Permet de sélectionner la puissance recommandée pour la connexion au réseau et, par conséquent, le type de convertisseur nécessaire dans ce cas avec modification des paramètres de poids de l'alliage.
Four à induction à transistors Largement utilisé pour le traitement métallurgique. Avec son aide, les pièces sont chauffées en forge et les objets métalliques sont durcis. Les creusets des fours à transistors sont en céramique ou en graphite ; les premiers sont conçus pour faire fondre des métaux ferromagnétiques comme la fonte ou l'acier. Le graphite est installé pour faire fondre le laiton, le cuivre, l'argent, le bronze et l'or. Ils font fondre le verre et le silicium. L'aluminium fond bien à l'aide de creusets en fonte ou en acier.
Quel est le revêtement des fours à induction
Son objectif est de protéger l'enveloppe du four des effets destructeurs des températures élevées. Un effet secondaire est la conservation de la chaleur. l'efficacité du processus augmente.
Le creuset dans la conception d'un four à induction est réalisé de l'une des manières suivantes :
- par la méthode d'excavation dans des fours de petit volume ;
- par la méthode imprimée à partir d'un matériau réfractaire sous forme de maçonnerie ;
- combinés, associant céramique et couche tampon entre la maçonnerie et l'indicateur.
Le revêtement est composé de quartzite, corindon, graphite, graphite réfractaire, magnésite. Des additifs sont ajoutés à tous ces matériaux pour améliorer les caractéristiques du revêtement, réduire les changements de volume, améliorer le frittage et augmenter la résistance de la couche aux matériaux agressifs.
Pour sélectionner un matériau particulier pour la doublure prendre en compte un certain nombre de conditions d'accompagnement, à savoir le type de métal, le prix et les propriétés réfractaires du creuset, la durée de vie de la composition. Une composition de revêtement correctement sélectionnée doit fournir les exigences techniques du processus :
- obtenir des lingots de haute qualité ;
- la plus grande quantité de fusion complète sans travaux de réparation ;
- travail sûr des spécialistes;
- stabilité et continuité du processus de fusion ;
- obtenir du matériel de haute qualité en utilisant une quantité économique de ressources ;
- utilisation de matériaux courants pour le revêtement à bas prix ;
- impact minimal sur l'espace environnant.
L'utilisation de fours à induction permet d'obtenir alliages et métaux d'excellente qualité avec une teneur minimale en diverses impuretés et en oxygène, ce qui augmente leur utilisation dans des domaines de production complexes.
La fusion des métaux par induction est activement utilisée dans diverses industries, telles que l'ingénierie mécanique, la métallurgie et la production de bijoux. Le matériau est chauffé par courant électrique, ce qui permet d'utiliser la chaleur avec une efficacité maximale. Les grandes usines disposent d'unités industrielles spéciales à cet effet, tandis qu'à la maison, vous pouvez assembler de vos propres mains un four à induction simple et petit.
De tels fours sont populaires en production
Auto-assemblage du poêle
Il existe de nombreuses technologies et descriptions schématiques de ce processus présentées sur Internet et dans des magazines, mais lors du choix, il convient de choisir le modèle le plus efficace en fonctionnement, abordable et facile à mettre en œuvre.
Les fours de fusion faits maison ont une conception assez simple et se composent généralement de seulement trois parties principales logées dans un boîtier robuste. Ceux-ci inclus:
- élément générant un courant alternatif haute fréquence ;
- une pièce en forme de spirale créée à partir d'un tube de cuivre ou d'un fil épais, appelée inducteur ;
- creuset - un récipient dans lequel sera effectuée la calcination ou la fusion, en matériau réfractaire.
Bien entendu, un tel équipement n’est pas souvent utilisé dans la vie quotidienne, car tous les artisans n’ont pas besoin de telles unités. Mais les technologies présentes dans ces appareils se retrouvent dans les appareils électroménagers que de nombreuses personnes utilisent presque quotidiennement. Cela comprend les micro-ondes, les fours électriques et les cuisinières à induction. Vous pouvez fabriquer divers équipements à l'aide de schémas de vos propres mains si vous possédez les connaissances et les compétences nécessaires.
Dans cette vidéo, vous apprendrez en quoi consiste ce four
Le chauffage dans cette technique est réalisé grâce aux courants de Foucault par induction. L'augmentation de la température se produit instantanément, contrairement à d'autres appareils ayant un objectif similaire.
Par exemple, les cuisinières à induction ont un rendement de 90 %, mais les cuisinières à gaz et électriques ne peuvent pas se vanter de cette valeur, elles ne sont respectivement que de 30 à 40 % et de 55 à 65 %. Cependant, les cuisinières HDTV présentent un inconvénient : pour les utiliser, vous devrez préparer des plats spéciaux.
Conception de transistors
Il existe de nombreux schémas différents pour assembler des fondoirs à induction à la maison. Un four simple et éprouvé fabriqué à partir de transistors à effet de champ est assez facile à assembler ; de nombreux artisans connaissant les bases de l'ingénierie radio peuvent gérer sa fabrication selon le schéma présenté sur la figure. Pour créer une installation Vous devez préparer les matériaux et pièces suivants :
- deux transistors IRFZ44V ;
- fils de cuivre (pour le bobinage) en isolant émaillé, de 1,2 et 2 mm d'épaisseur (une pièce chacun) ;
- deux anneaux de selfs, ils peuvent être retirés de l'alimentation d'un vieil ordinateur ;
- une résistance de 470 Ohm pour 1 W (vous pouvez en connecter deux de 0,5 W chacune en série) ;
- deux diodes UF4007 (facilement remplaçables par le modèle UF4001) ;
- Condensateurs à film 250 W - une pièce d'une capacité de 330 nF, quatre - 220 nF, trois - 1 µF, 1 pièce - 470 nF.

L'assemblage s'effectue selon le dessin schématique ; il est également recommandé de vérifier les instructions étape par étape, cela vous protégera des erreurs et des dommages aux éléments. La création d'un four de fusion à induction de vos propres mains s'effectue selon l'algorithme suivant :
- Les transistors sont placés sur des dissipateurs thermiques assez grands. Le fait est que les circuits peuvent devenir très chauds pendant le fonctionnement, c'est pourquoi il est si important de sélectionner des pièces de taille appropriée. Tous les transistors peuvent être placés sur un seul radiateur, mais dans ce cas, vous devrez les isoler pour éviter qu'ils n'entrent en contact avec le métal. Des rondelles et des joints en plastique et en caoutchouc y contribueront. Le brochage correct des transistors est indiqué sur l'image.
- Ensuite, ils commencent à fabriquer des étranglements ; vous en aurez besoin de deux. Pour ce faire, prenez un fil de cuivre de 1,2 millimètres de diamètre et enroulez-le autour d'anneaux prélevés sur l'alimentation. Ces éléments contiennent du fer ferromagnétique sous forme de poudre, il est donc nécessaire d'effectuer au moins 7 à 15 tours en laissant une petite distance entre eux.
- Les modules résultants sont assemblés en une seule batterie d'une capacité de 4,6 μF et les condensateurs sont connectés en parallèle.
- Un fil de cuivre de 2 mm d'épaisseur est utilisé pour enrouler l'inducteur. Il est enroulé 7 à 8 fois autour de tout objet cylindrique, son diamètre doit correspondre à la taille du creuset. L'excédent de fil est coupé, mais il reste des extrémités assez longues : elles seront nécessaires à la connexion à d'autres pièces.
- Tous les éléments sont connectés sur la carte, comme indiqué sur la figure.
Si nécessaire, vous pouvez construire un boîtier pour l'unité ; à cet effet, seuls des matériaux résistants à la chaleur, tels que le textolite, sont utilisés. La puissance de l'appareil peut être réglée, pour laquelle il suffit de modifier le nombre de tours de fil sur l'inducteur et leur diamètre.

Avec des pinceaux en graphite
L'élément principal de cette conception est assemblé à partir de brosses en graphite dont l'espace est rempli de granit, broyé à l'état de poudre. Ensuite, le module fini est connecté à un transformateur abaisseur. Lorsque vous travaillez avec un tel équipement, vous n'avez pas à vous soucier des chocs électriques, car il n'est pas nécessaire d'utiliser du 220 volts.
Technologie de fabrication d'un four à induction à partir de brosses en graphite :
- Tout d'abord, le corps est assemblé ; pour cela, des briques réfractaires (argile réfractaire) mesurant 10 × 10 × 18 cm sont posées sur des carreaux pouvant résister à des températures élevées. La boîte finie est enveloppée dans du carton amiante. Pour donner à ce matériau la forme souhaitée, il suffit de l'humidifier avec une petite quantité d'eau. La taille de la base dépend directement de la puissance du transformateur utilisé dans la conception. Si vous le souhaitez, la boîte peut être recouverte de fil d'acier.
- Une excellente option pour les fours à graphite serait un transformateur de 0,063 kW provenant d'une machine à souder. S'il est conçu pour 380 V, pour des raisons de sécurité, il peut être soumis à un enroulement, bien que de nombreux techniciens radio expérimentés estiment que cette procédure peut être abandonnée sans aucun risque. Cependant, il est recommandé d'envelopper le transformateur avec de l'aluminium fin afin que l'appareil fini ne chauffe pas pendant le fonctionnement.
- Un substrat d'argile est placé au fond de la boîte afin que le métal liquide ne se propage pas, après quoi des brosses en graphite et du sable granitique sont placés dans la boîte.
Le principal avantage de tels dispositifs est considéré comme le point de fusion élevé, qui peut modifier l'état d'agrégation même du palladium et du platine. Les inconvénients incluent le chauffage trop rapide du transformateur, ainsi que la petite surface du four, qui ne permettra pas de fondre plus de 10 g de métal à la fois. Par conséquent, chaque maître doit comprendre que si l'appareil est assemblé pour traiter de gros volumes, il est préférable de fabriquer un four d'une conception différente.
Appareil basé sur une lampe
Un puissant poêle à fondre peut être assemblé à partir d'ampoules électroniques. Comme le montre le schéma, pour obtenir un courant haute fréquence, il est nécessaire de connecter des lampes à faisceau en parallèle. Au lieu d'un inducteur, cet appareil utilise un tube en cuivre d'un diamètre de 10 mm. La conception est également équipée d'un condensateur de réglage afin de pouvoir réguler la puissance du four. Pour le montage, vous devez préparer :
- quatre lampes (tétrodes) L6, 6P3 ou G807 ;
- condensateur ajustable;
- 4 selfs à 100-1000 µH ;
- voyant lumineux au néon;
- quatre condensateurs de 0,01 µF.
Pour commencer, le tube de cuivre est façonné en spirale - ce sera l'inducteur de l'appareil. Dans ce cas, une distance d'au moins 5 mm est laissée entre les spires et leur diamètre doit être compris entre 8 et 15 cm. Les extrémités de la spirale sont traitées pour être fixées au circuit. L'épaisseur de l'inducteur obtenu doit être supérieure de 10 mm à celle du creuset (il est placé à l'intérieur).
La pièce finie est placée dans le boîtier. Pour sa fabrication, vous devez utiliser un matériau qui assurera l'isolation électrique et thermique pour le remplissage de l'appareil. Ensuite, une cascade est assemblée à partir de lampes, de selfs et de condensateurs, comme le montre la figure, ces derniers étant connectés en ligne droite.
Il est temps de connecter l'indicateur au néon : il est nécessaire pour que le maître puisse savoir quand l'appareil est prêt à fonctionner. Cette ampoule est connectée au corps du four avec la poignée du condensateur variable.
Équipement du système de refroidissement
Les unités industrielles de fusion des métaux sont équipées de systèmes de refroidissement spéciaux utilisant de l'antigel ou de l'eau. L'équipement de ces installations importantes dans des poêles HDTV faits maison nécessitera des coûts supplémentaires, c'est pourquoi l'assemblage peut avoir un impact important sur votre portefeuille. Par conséquent, il est préférable de doter une unité domestique d'un système moins cher composé de ventilateurs.
Le refroidissement par air avec ces appareils est possible lorsqu'ils sont situés à distance du four. Sinon, les enroulements métalliques et les pièces du ventilateur peuvent servir de boucle pour court-circuiter les courants de Foucault, ce qui réduira considérablement l'efficacité de l'équipement.
Les tubes et les circuits électroniques ont également tendance à devenir chauds pendant le fonctionnement de l'appareil. Des dissipateurs thermiques sont généralement utilisés pour les refroidir.
Conditions d'utilisation
Pour les techniciens radio expérimentés, assembler un four à induction selon les schémas de vos propres mains peut sembler une tâche facile, donc l'appareil sera prêt assez rapidement et le maître voudra essayer sa création en action. Il convient de rappeler que lorsque l'on travaille avec une installation artisanale, il est important de suivre les précautions de sécurité et de ne pas oublier les principales menaces qui peuvent survenir lors du fonctionnement d'un four à inertie :
- Le métal liquide et les éléments chauffants de l'appareil peuvent provoquer de graves brûlures.
- Les circuits des lampes sont constitués de pièces à haute tension, donc lors du montage de l'unité, ils doivent être placés dans une boîte fermée, éliminant ainsi la possibilité de toucher accidentellement ces éléments.
- Le champ électromagnétique peut influencer même les éléments situés à l'extérieur du boîtier d'installation. Par conséquent, avant d'allumer l'appareil, vous devez ranger tous les appareils techniques complexes, tels que les téléphones portables, les appareils photo numériques, les lecteurs MP3, ainsi que tous les bijoux métalliques. Les personnes portant un stimulateur cardiaque courent également un risque : elles ne devraient jamais utiliser un tel équipement.
Ces fours peuvent être utilisés non seulement pour la fusion, mais également pour chauffer rapidement des objets métalliques pendant le formage et l'étamage. En modifiant le signal de sortie de l'installation et les paramètres de l'inducteur, vous pouvez configurer l'appareil pour une tâche spécifique.
Pour faire fondre de petits volumes de fer, des poêles faits maison sont utilisés ; ces appareils efficaces peuvent fonctionner à partir de prises ordinaires. L'appareil ne prend pas beaucoup de place, il peut être placé sur un bureau dans un atelier ou un garage. Si une personne sait lire des schémas électriques simples, elle n'a pas besoin d'acheter un tel équipement dans un magasin, car elle peut assembler un petit poêle de ses propres mains en quelques heures seulement.
Les radioamateurs ont découvert depuis longtemps qu'ils peuvent fabriquer de leurs propres mains des fours à induction pour faire fondre le métal. Ces schémas simples vous aideront à réaliser une installation HDTV pour un usage domestique. Cependant, il serait plus correct d’appeler toutes les conceptions décrites « les onduleurs de laboratoire de Kukhtetsky », car il est tout simplement impossible d’assembler indépendamment un poêle à part entière de ce type.
Les anciens potiers qui cuisaient des poteries dans des forges trouvaient parfois au fond des pièces dures et brillantes aux propriétés inhabituelles. À partir du moment où ils ont commencé à réfléchir à ce qu'étaient ces substances merveilleuses, comment elles y apparaissaient et où elles pouvaient être utilisées utilement, la métallurgie est née - l'artisanat et l'art du traitement des métaux.
Et le principal outil pour extraire de nouveaux matériaux extrêmement utiles du minerai est devenu les forges de thermofusion. Leurs conceptions ont parcouru un long chemin dans leur développement : depuis les dômes d'argile jetables primitifs chauffés au bois jusqu'aux fours électriques modernes avec contrôle automatique du processus de fusion.
Les unités de fusion des métaux ne sont pas seulement nécessaires aux géants de l'industrie métallurgique des métaux ferreux, qui utilisent des cubilots, des hauts fourneaux, des fours à sole et des convertisseurs régénératifs avec une production de plusieurs centaines de tonnes par cycle.
De telles valeurs sont typiques de la fusion du fer et de l'acier, qui représentent jusqu'à 90 % de la production industrielle de tous les métaux.
Dans la métallurgie des non-ferreux et le recyclage, les volumes sont bien moindres. Et le chiffre d’affaires mondial de la production de métaux des terres rares est généralement calculé à plusieurs kilogrammes par an.
Mais le besoin de fondre des produits métalliques ne se pose pas seulement lors de leur production en série. Un secteur important du marché de la métallurgie est occupé par la production de fonderie, qui nécessite des unités de fusion de métaux d'une production relativement faible - de plusieurs tonnes à des dizaines de kilogrammes. Et pour l'artisanat de pièces, la production artisanale et la fabrication de bijoux, des machines de fusion d'une capacité de production de plusieurs kilogrammes sont utilisées.
Tous les types d'appareils de fusion de métaux peuvent être divisés selon le type de source d'énergie pour eux :
- Thermique. Le liquide de refroidissement est du gaz de combustion ou de l'air très chauffé.
- Électrique. Différents effets thermiques du courant électrique sont utilisés :
- Étouffer. Chauffage de matériaux placés dans un boîtier isolé thermiquement avec un élément chauffant en spirale.
- Résistance. Chauffer un échantillon en y faisant passer un courant important.
- Arc. Utilisez la haute température de l’arc électrique.
- Induction. Fusion de matières premières métalliques par chaleur interne due à l'action des courants de Foucault.
- Streaming. Appareils exotiques à plasma et à faisceaux d'électrons.
Four de fusion à faisceau d'électrons à flux Four thermique à sole ouverte Four à arc électrique
Pour les petits volumes de production, le plus judicieux et le plus économique est l'utilisation d'appareils électriques, notamment fours de fusion à induction(IPP).
Construction de fours électriques à induction
En bref, leur action repose sur le phénomène des courants de Foucault – courants d'induction de Foucault dans un conducteur. Dans la plupart des cas, les ingénieurs électriciens les considèrent comme un phénomène nuisible.
Par exemple, c'est à cause d'eux que les noyaux des transformateurs sont constitués de plaques ou de rubans d'acier : dans un morceau de métal solide, ces courants peuvent atteindre des valeurs importantes, entraînant des pertes d'énergie inutiles pour le chauffer. Dans un four électrique de fusion par induction, ce phénomène est mis à profit. Essentiellement, il s'agit d'une sorte de transformateur dans lequel le rôle d'un enroulement secondaire court-circuité, et dans certains cas de noyau, est joué par un échantillon de métal en fusion. Il est métallique : seuls les matériaux conducteurs de l’électricité peuvent y être chauffés, tandis que les diélectriques resteront froids. Le rôle de l'inducteur - l'enroulement primaire du transformateur - est assuré par plusieurs tours d'un tube de cuivre épais enroulé dans une bobine à travers laquelle circule le liquide de refroidissement.
D'ailleurs, les plaques de cuisson de cuisine à chauffage par induction haute fréquence, devenues extrêmement populaires, fonctionnent sur le même principe. Un morceau de glace placé dessus ne fondra même pas, mais les ustensiles en métal placés chaufferont presque instantanément.
Caractéristiques de conception des fours thermiques à induction
Il existe deux principaux types d’IPP :

Pour les deux types d'unités de fusion de métaux, il n'y a pas de différences fondamentales dans le type de matières premières à travailler : elles fondent avec succès les métaux ferreux et non ferreux. Il suffit de sélectionner le mode de fonctionnement et le type de creuset appropriés.
Options de sélection
Ainsi, les principaux critères de choix de l'un ou l'autre type de four thermique sont les volumes et la continuité de production. Pour une petite fonderie, par exemple, dans la plupart des cas, un four électrique à creuset convient, et un four à canal convient pour une usine de recyclage.
De plus, l'un des principaux paramètres d'un four à creuset est le volume d'une masse fondue, sur la base duquel un modèle spécifique doit être sélectionné. Les caractéristiques importantes sont également la puissance maximale de fonctionnement et le type de courant : monophasé ou triphasé.
Choisir un emplacement pour l'installation
L'emplacement du four à induction dans un atelier ou un atelier doit permettre un libre accès pour l'exécution en toute sécurité de toutes les opérations technologiques pendant le processus de fusion :
- chargement de matières premières;
- manipulations pendant le cycle de travail ;
- décharger la masse fondue finie.
Le site d'installation doit être doté des réseaux électriques nécessaires avec la tension de fonctionnement et le nombre de phases requis, une mise à la terre de protection avec la possibilité d'un arrêt d'urgence rapide de l'unité. L'installation doit également être dotée d'une arrivée d'eau pour le refroidissement.
Les structures de table de petites dimensions doivent néanmoins être installées sur des supports individuels solides et fiables non destinés à d'autres opérations. Les unités au sol doivent également être dotées d’une fondation solide et renforcée.
Il est interdit de placer du feu et des matières explosives dans la zone de déchargement de la fonte. Un pare-feu avec des agents extincteurs doit être accroché à proximité de l'emplacement du poêle.
Instructions d'installation
Les unités de thermofusion industrielles sont des appareils à forte consommation d'énergie. Leur installation et leur installation électrique doivent être réalisées par des spécialistes qualifiés. Les petites unités avec une charge allant jusqu'à 150 kg peuvent être raccordées par un électricien qualifié, en suivant les règles normales d'installation électrique.
Par exemple, un four IPP-35 d'une puissance de 35 kW avec un volume de production de 12 kg de métaux ferreux et jusqu'à 40 métaux non ferreux a une masse de 140 kg. En conséquence, son installation comprendra les étapes suivantes :
- Sélection d'un emplacement approprié avec une base solide pour l'unité de thermofusion et l'unité d'induction haute tension refroidie par eau avec batterie de condensateurs. L'emplacement de l'unité doit être conforme à toutes les exigences opérationnelles et aux réglementations en matière d'électricité et de sécurité incendie.
- Doter l'installation d'une ligne de refroidissement par eau. Le four de fusion électrique décrit n'est pas fourni avec un équipement de refroidissement qui doit être acheté en plus. La meilleure solution pour cela serait une tour de refroidissement à cycle fermé à double circuit.
- Connexion d'une mise à la terre de protection.
Le fonctionnement de tout four de fusion électrique sans mise à la terre est strictement interdit.
- Alimenter une ligne électrique séparée avec un câble dont la section fournit la charge appropriée. Le panneau de puissance doit également fournir à la charge requise une réserve de marche
Pour les petits ateliers et l'usage domestique, des mini-fours sont produits, par exemple UPI-60-2, d'une puissance de 2 kW avec un volume de creuset de 60 cm³ pour la fusion des métaux non ferreux : cuivre, laiton, bronze ~ 0,6 kg , argent ~ 0,9 kg, or ~ 1,2 kg. Le poids de l'installation elle-même est de 11 kg, dimensions - 40x25x25 cm. Son installation consiste à la placer sur un établi en métal, à connecter le refroidissement par eau à circulation et à la brancher sur une prise de courant.
Technologie d'utilisation
Avant de commencer à travailler avec un four électrique à creuset, vous devez absolument vérifier l'état des creusets et du revêtement - l'isolation thermique de protection interne. S'il est conçu pour l'utilisation de deux types de creusets : céramique et graphite, vous devez sélectionner le matériau approprié au matériau chargé selon les instructions.
Généralement, les creusets en céramique sont utilisés pour les métaux ferreux, les creusets en graphite pour les métaux non ferreux.
Mode opératoire:
- Insérez le creuset à l'intérieur de l'inducteur et, après l'avoir chargé avec le matériau de travail, recouvrez-le d'un couvercle calorifuge.
- Allumez le refroidissement par eau. De nombreux modèles d’unités de fusion électriques ne démarreront pas s’il n’y a pas de pression d’eau requise.
- Le processus de fusion dans un creuset IPP commence par sa mise en marche et son entrée en mode de fonctionnement. S'il y a un régulateur de puissance, réglez-le sur la position minimale avant de l'allumer.
- Augmentez progressivement la puissance jusqu'à la puissance de fonctionnement correspondant au matériau chargé.
- Après avoir fondu le métal, réduisez la puissance au quart de la puissance de travail pour maintenir le matériau à l'état fondu.
- Avant de renverser, baissez le régulateur au minimum.
- Une fois la fusion terminée, coupez l’alimentation de l’installation. Éteignez le refroidissement par eau une fois qu'il a refroidi.
L'unité doit être sous surveillance tout au long du processus de fusion. Toute manipulation des creusets doit être effectuée à l'aide de pinces et avec des gants de protection. En cas d'incendie, l'installation doit être immédiatement mise hors tension et les flammes doivent être éteintes avec une bâche ou éteintes avec tout extincteur autre qu'à acide. Le remplissage d'eau est strictement interdit.
Avantages des fours à induction
- Haute pureté de la masse fondue résultante. Dans d'autres types de fours thermiques de fusion de métaux, il y a généralement un contact direct du liquide de refroidissement avec le matériau et, par conséquent, une contamination de ce dernier. En IPP, l'échauffement est produit par l'absorption du champ électromagnétique de l'inducteur par la structure interne des matériaux conducteurs. Par conséquent, ces fours sont idéaux pour la production de bijoux.
Pour les fours thermiques, le principal problème est de réduire la teneur en phosphore et en soufre des métaux ferreux fondus, ce qui détériore leur qualité.
- Haute efficacité des appareils de fusion par induction, atteignant jusqu'à 98 %.
- Vitesse de fusion élevée grâce au chauffage de l'échantillon de l'intérieur et, par conséquent, productivité élevée de l'IPP, en particulier pour les petits volumes de travail jusqu'à 200 kg.
Le chauffage d'un four à moufle électrique avec une charge de 5 kg se produit en quelques heures, tandis que l'IPP ne prend pas plus d'une heure.
- Les appareils d'une capacité de charge allant jusqu'à 200 kg sont faciles à placer, à installer et à utiliser.
Le principal inconvénient des appareils de fusion électriques, et ceux à induction ne font pas exception, est le coût relativement élevé de l'électricité comme liquide de refroidissement. Malgré cela, le rendement élevé et les bonnes performances des IPP les compensent largement pendant leur fonctionnement.
La vidéo montre un four à induction en fonctionnement.