Шесть сигм как инструмент управления изменениями. Проектная парадигма «Шести сигм
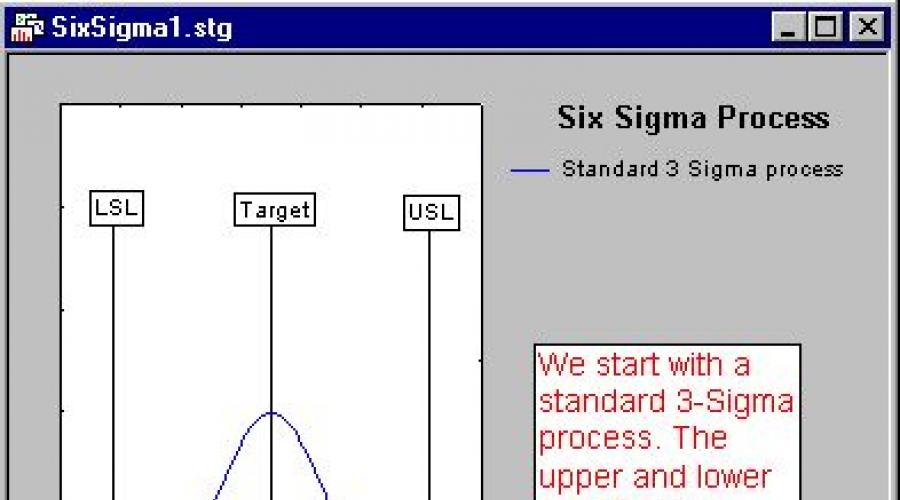
Читайте также
Шесть сигма - хорошо структурированная методология управления данными, различных областях производства, сфере услуг, менеджмента и другой деловой активности. Технология "шесть сигма" базируется на хорошо изученных и апробированных статистических методах контроля качества, анализа данных и систематическом тренинге всего персонала на фирме, вовлеченного в деловую активность или процесс, который получил статус "процесс шесть сигма".
Рис. 1. Калькулятор Шесть Сигма
Методология "шесть сигма" и стратегия менеджмента обеспечивают надежную основу для организации корпоративного контроля качества. В последние годы интерес к "шесть сигма" значительно вырос, поскольку появилось множество примеров успешного внедрения подхода как на предприятиях США, так и в Европе.
Процесс "шесть сигма" обеспечивает всего лишь 3.4 дефекта на 1 миллион произведенных деталей. Достижение подобных результатов является целью, заложенной в концепцию "шесть сигма". Подобные улучшения не могут произойти без внесения изменений во все аспекты деловой активности, связанные с реформируемым процессом. Именно поэтому программы по внедрению методологии "шесть сигма" обращают особое внимание на предварительную подготовку персонала на предприятии.
Основная идея концепции может быть проиллюстрирована следующим образом:
Рассмотрим процесс, в котором распределение отклонений от среднего значения предполагается нормальным и контрольные пределы установлены на интервалах 3*сигма (такой процесс носит название "процесс три сигма").
Рис. 2. Нормальный процесс распределения отклонений
Рис. 3. Отклонение процесса от прежнего среднего на 1.5 сигма
Предположим, что мы произвели один миллион деталей и хотим подсчитать их число, оказавшееся за верхним контрольным пределом. На рисунке это закрашенная область под графиком распределения процесса:
Рис. 4. Заштрихованная область - число деталей, оказавшихся за верхним контрольным пределом
Для процесса "три сигма" число деталей вне контрольного предела будет 66.807 (для реального процесса на практике, конечно, такая точность не будет достигаться, но порядок величины будет сохраняться).
Рис. 5. Заштрихованая область - число деталей вне контрольного предела 66,807
Для процесса "четыре сигма", контрольные пределы для которого установлены на 4*сигма от средней линии, число "бракованных" деталей будет 6.210.
Рис. 6. Заштрихованная область - число "бракованных" деталей для процесса "четыре сигма"
Для процесса "шесть сигма" мы обнаружим всего 3.4 детали, которые оказались вне верхнего контрольного предела:
Рис. 7. Для процесса "Шесть Сигма" 3, 4 бракованных детали
Термин "шесть сигма" произошел от стремления добиться такой дисперсии для процесса, чтобы ± 6 сигма уложилось в интервале от нижнего контрольного предела до верхнего.
В этом случае, если даже смещение процесса достигнет 1.5 сигма, то число дефектов будет все равно очень низким. Причины смещения могут быть разными и зависеть от многих факторов на производстве. Значение 1.5 для смещения тоже не было взято случайно.
Корпорация Моторола, которая считается одним из пионеров успешного внедрения концепции "шесть сигма", в результате тщательного исследования дала заключение о том, что со временем даже хорошо отрегулированный процесс может давать сдвиги в среднем значении до 1.5 сигма.
В проиллюстрированном выше примере мы предположили сдвиг в направлении верхнего контрольного предела. Для нижнего контрольного предела ситуация будет аналогичной.
Отметим, что часто на производстве не рассматривают один из концов нормального распределения, поскольку из-за особенностей технологии важен лишь один из контрольных пределов.
Например, при заточке болта большие значения его толщины являются не таким страшным браком, как слишком маленькие, поскольку брак можно исправить, если повторной заточкой уменьшить толщину (в то же время слишком маленькая толщина окончательно бракует деталь).
Другим примером может служить число покупателей в магазине - если их слишком мало, то это плохо, но если вдруг наблюдается всплеск активности, то это достаточно приятное событие для владельца.
В STATISTICA имеются набор модулей Промышленная STATISTICA , которые заключают в себе все статистические методы, на которые делается упор в концепции "шесть сигма": Карты контроля качества, Анализ процессов, Планирование эксперимента .
Удобным инструментом специалиста по качеству является встроенный в STATISTICA "Вероятностный калькулятор", который позволяет проводить вычисление критических точек для различных распределений. Если раньше при расчете доверительных интервалов и контрольных пределов специалисту приходилось каждый раз искать в толстых томах нужную цифру, то сейчас, пользуясь "Вероятностным калькулятором", вычисления производятся автоматически с помощью пары кнопок мыши.
Методология Шесть сигм опирается на сочетание статистических , различных методов анализа данных и системы постоянного повышения квалификации специалистов, так или иначе вовлеченных в процессы, организованные с учетом Шести сигм.
На вопросы читателей журнала Darwin об опыте использования методологии Six Sigma отвечает Деннис Сестер, директор по вопросам качества корпорации Motorola.
Отвлекаясь от поддержки бизнес-инициатив, направленных на достижение уровня качества Шесть сигм, каким образом, с вашей точки зрения, система Шесть сигм применима для таких функций информационной инфраструктуры, как поддержка внутренних пользователей, сетевое администрирование, администрирование информационных систем?
Есть следующие основания для применения системы качества Шесть сигм.
- Потребность в идентификации предоставляемого продукта или услуги.
- Способность определять процессы, используемые для доставки продукта или услуги, и отображать их.
- Возможность находить потенциальные ошибки для каждого шага процесса.
Если существует возможность подсчитать дефекты и ошибки, то можно установить уровень отклонений от нормального распределения. Например, оценивая поддержку внутреннего пользователя Internet в терминах «время работы» или «время реакции», пользователь становится объектом получения данных о текущих показателях своей работы. В «рабочем году» примерно 525 000 минут (число возможностей), для того чтобы время работы соответствовало уровню 6 сигма, время простоя (число дефектов) не должно превышать 1,5 минуты в год. Как только метрика определена и собраны данные о дефектах, можно составлять графики Парето и выявлять первопричины отклонения качества.
Каким должен быть первый шаг для достижения требуемого уровня качества? Допустим, сейчас наша компания сертифицирована по ISO 9001 и мы пытаемся достичь третьего уровня зрелости по SEI-CMM. Какими должны быть типичные метрики?
Я могу предположить, исходя из стремления достичь третьего уровня по CMM, что ваша основная работа состоит в производстве программного обеспечения. Первым шагом должно быть определение базы изменений, допустим, строк кода, а затем установление способности находить дефекты или ошибки на каждой фазе разработки кода. Обычно это делается в форме инспекции. Если вы действительно близко подошли к третьему уровню по CMM, эти процессы у вас налажены. Затем надо измерить число дефектов на каждой фазе разработки. Получив данные о дефектах, можно приступать к анализу данных, то есть применить метод Парето, выполнить анализ первопричин и т. д.
Почему нет отраслей, в которых был бы превышен уровень 6 сигма? Если бы не было дефектов вовсе, то не было бы и самого понятия «сигма». Согласны ли вы со мной?
Концепция Шесть сигм - это концепция постоянного совершенствования. Данные испытаний показывают, что в случаях, когда формальная программа качества отсутствует, большинство организаций не выходят за рамки 3 или 4 сигма. Поэтому первый этап - это определение места компании в данной классификации, после чего начинается движение к совершенству. Six Sigma характеризует качество, близкое к совершенству. Вместе с тем во многих приложениях, особенно в разработке сложного программного обеспечения, состоящего из миллионов строк кода, уровень 6 сигма недостаточен для достижения высокого уровня удовлетворенности клиентов.
Мне много раз приходилось слышать лозунг «Затраты на качество окупаются сторицей», суть которого сводится к тому, что организация может получить огромную отдачу от вложения средств в повышение качества. Инициативы Six Sigma собирают важные данные о процессах. Собирают ли они также данные, требуемые для количественного выражения отдачи от инвестиций в повышение качества?
Напрямую - нет. Большинство компаний, располагающих зрелыми системами качества, собирают данные о «цене качества». На ранних стадиях «цена качества» (Cost of Quality) может достигать 20% оборота. Для тех же компаний, которые имеют развитые эффективные программы качества, это, как правило, 5-10% или даже меньше. Существенную отдачу от вложений в повышение качества на промышленных предприятиях можно ожидать спустя многие годы. Причины очевидны. В большинстве случаев проект продукта или системы служит основным фактором, влияющим на уровень качества. Для получения заметного повышения отдачи продукт, процесс или система должны быть соответствующим образом запроектированы. Поэтому часто требуется несколько итераций модернизации продукта или системы.
Я понимаю, что Шесть сигм можно применить к любому процессу, а не только к производственным процессам. Можно ли, например, таким способом соотнести известные ограничения надежности современных компонентов (серверов, межсетевых экранов, маршрутизаторов, Internet и т. д.) с качеством ИТ-услуг в целом (например, к доступности определенной базы данных для бизнес-партнера)?
Я считаю важным измерять «сквозное» качество системы или процесса. Не менее важно оценивать каждый этап процесса. В моей практике было и такое, что оценивались все компоненты, составлялся график Парето и проводился анализ первопричин на базе собранных данных для определения причин недостаточной надежности или готовности. Затем основное внимание обращалось на элементы, оказывающие наибольшее влияние на работу всей системы, но усовершенствования вносились постепенно, после чего процесс повторялся. В сложных системах влияние одного элемента на другие носит характер сложной зависимости. Либо, как часто бывает, надежность можно увеличить за счет избыточности, если это позволяет цена. На деле же каждый компонент нельзя оценить досконально полно, выявляются только наиболее узкие места. Клиентов - внутренних или внешних - не интересует, какой компонент «виноват» в недостаточной готовности, они хотят, чтобы система работала, оправдывая их ожидания.
В чем заключается роль руководства в достижении уровня 6 сигма? Должен ли руководитель придерживаться командного стиля или выступать в качестве лидера? В чем состоит различие?
Не исключено, что командный стиль руководства позволяет быстро получить определенные результаты, но на него нельзя опираться в течение долгого времени, во всяком случае, если это не армия. Лидерство состоит в том, что руководитель выводит компанию на такой уровень, какого бы она не достигла без него. Как правило, этого добиваются делами, а не словами. Некоторое время люди подчиняются распоряжениям, то есть словам, но это не может длиться долго, если слова не подкреплены делами самого руководителя. Одна из легенд, связанных с достижением компанией Motorola лидерства в области качества, связана с именем Боба Кальвина, председателя совета директоров и бывшего генерального директора. В начале 80-х компания вышла в «поход за качеством». Боб каждый раз ставил вопрос об анализе результатов работы по качеству в повестку дня заседаний совета директоров и уходил только после обсуждения этих вопросов. Так продолжалось несколько лет. До сих пор вопрос о качестве - это первый пункт повестки дня всех бизнес-мероприятий в Motorola. Вот пример того, что я называю лидерством.
Каких бизнес-преимуществ добилась Motorola благодаря меньшему числу дефектов? Как достигнутый пятый уровень сертификации по SEI-CMM помог вашему подразделению Motorola?
Motorola добилась существенного роста эффективности, причем это выразилось в целом ряде аспектов. Есть данные о том, что суммарная экономия за 11 лет превысила 15 млрд. долл. Мы существенно снизили производственные затраты на единицу продукции и на гарантийное обслуживание, а также капиталовложения в оборудование. Есть результаты, которые не поддаются количественной оценке, хотя также крайне важны. Мы повысили авторитет своей торговой марки, значительно увеличив уровень удовлетворенности клиентов. Это произошло благодаря высокому качеству и надежности продуктов. В Motorola есть несколько подразделений, занятых разработкой программного обеспечения, которые соответствуют пятому уровню по CMM, большинство же из них находится на уровне 3 или 4. Вы знаете, что первый уровень характеризуется как «хаос». Организации, соответствующие третьему уровню, существенно снизили количество дефектов и сократили цикл разработки, их также отличает высокая степень предсказуемости показателей работы. Но, должен добавить, сам по себе уровень зрелости по CMM - недостаточное условие высокого качества работы. У нас есть несколько подразделений, выпускающих программное обеспечение с уровнем качества выше 6 сигма, если брать за показатель число дефектов на тысячу строк кода.
Допустим, я менеджер в государственном ведомстве, занимающемся выделением льгот. В целом по стране около 10% льгот предоставляется незаслуженно. Как можно применить подход Шесть сигм для снижения числа ошибок?
Прежде всего должен сказать, что 10% ошибок соответствуют уровню 2 сигма, что весьма характерно для организаций, не имеющих формальных . И это крайне огорчительно. Но в этом можно увидеть определенную долю оптимизма - достижение должного уровня качества сулит гигантские преимущества, которые выражаются в снижении затрат и сокращении цикла обработки того или иного рода. Требуется внесение значительных усовершенствований в систему качества.
- Постоянное, многолетнее стремление к усовершенствованиям, проявленное на самом «верху» организации.
- Обучение руководства и сотрудников некоторым базовым аспектам Шесть сигм.
- Выполнение отображения всех процессов от начала до конца и формирование карты «как есть». Анализ процессов с целью выявления излишних действий, а также действий, не ведущих к достижению результата (инспекции и проверки, например, отнюдь не ведут к достижению результата).
- Создание карты процесса «как должно быть». «Очистка» рабочих процессов.
- Подсчет дефектов или ошибок для каждого шага процесса.
- Выполнение категоризации и составление диаграммы Парето для основных дефектов.
- Анализ первопричин дефектов и внедрение решения, устраняющего эти причины.
- Возможность узаконить решения, выбрав какие-либо из них в качестве долговременных (это не касается обучения или добавления инспекционных проверок);
- Повторение описанной процедуры для очередного уровня по числу дефектов.
Из сказанного становится понятно, что внесение основополагающих усовершенствований требует многолетних усилий.
Главную трудность в реализации Six Sigma в сервисных компаниях представляет разнообразие выполняемых процессов. Большинство процессов зависят от клиентов, а на качество конечного продукта оказывает влияние множество непредвиденных обстоятельств. В чем состоят основные особенности разработки программы качества для сервисной отрасли?
Везде, где есть процессы, есть возможность и измерить отклонения от заданных пределов. При наличии достаточного объема информации не имеет значения, идет ли речь о производстве или об индустрии обслуживания. В данной ситуации объемы показательных данных малы, а необходимость в устранении ошибок велика. Мне известно, что корпорация Boeing пользуется услугами специализированной компании для технического обслуживания самолетов, я бы предложил изучить опыт этой фирмы. Кроме того, военно-воздушные силы США применяют к операциям обслуживания на протяжении многих лет, они также могут послужить примером.
Вы занимались внедрением Шести сигм? Расскажите нам о своем опыте.
Ключевая идея и история

Основу системы качества Шесть сигм составляет оценка отклонений фактических показателей процесса от кривой нормального распределения отклонений. Если те или иные показатели процесса находятся в определенных пределах отклонений, качество результатов процесса также остается высоким. Единицу измерения отклонений в статистике принято называть «сигмой». Заметный эффект наблюдается при отклонении не более 4,5 сигма; в этом случае показатель числа дефектов на миллион единиц продукции составляет 3,4. Но это условие выполняется для стабильных процессов. Производственные процессы не отличаются стабильностью. Изобретатели методологии пришли к выводу, что отклонения процесса, вызванные его естественной нестабильностью, дают отклонения качества на уровне 1,5 сигма. Таким образом, если целевой уровень качества составляет 4,5 сигма, то с учетом 1,5 сигма на отклонения необходимо обеспечивать уровень качества в 6 сигма.
В большинстве компаний обеспечивается уровень качества 3 или 3,5 сигма. Уровень 3 сигма соответствует 93-процентному уровню качества, то есть 66 800 дефектов на миллион единиц продукции.
Методология Шесть сигм была разработана в 1986 году в компании Motorola. Концепцию предложил старший инженер подразделения средств связи Билл Смит. Его побудили к этому жалобы торговых агентов на местах, сообщавших об участившихся случаях предъявления претензий по гарантийным обязательствам. Смит создал новый подход к стандартизации методов учета дефектов. В идеале производство, организованное с учетом методологии Шесть сигм, должно было выпускать продукты, практически не имеющие изъянов.
Смит разработал необходимый статистический аппарат и представил его руководству компании. Идея была принята на «ура», и в Motorola развернулась работа по документированию основных процессов, их согласованию с критически важными требованиями пользователей и установке систем измерения и аналитических систем, позволявших постоянно вносить усовершенствования в процессы.
В результате компания в 1988 году стала первым лауреатом премии за качество продукции Malcolm Baldridge National Quality Award. Компания за четыре года добилась экономии в 2 млрд. долл. Подобная сумма не могла не привлечь внимание отрасли, и у методологии Шесть сигм начали появляться адепты, например компании General Electric и AlliedSignal (теперь Honeywell International). Но со временем интерес к Шесть сигм стал угасать. На авансцену вышли идеи реинжиниринга бизнес-процессов, захватившие умы многих руководителей предприятий. Однако в самый разгар увлечения этими теориями в General Electric внедрили методологию Шесть сигм, и результаты оказались впечатляющими. Произошло это так. Генеральный директор AlliedSignal Ларри Боссиди, занимавший прежде один из руководящих постов в General Electric, внедрил Six Sigma и остался доволен результатами. В 1995 году генеральный директор корпорации General Electric Джек Уэлч оказался на больничной койке и предложил Боссиди выступить на очередном заседании совета директоров корпорации с любой темой по его собственному выбору. Неудивительно, что выбор Боссиди пал на Six Sigma. Его речь произвела впечатление, и спустя месяц General Electric уже активно формировала штат специалистов по этой методологии. На следующий год корпорация отчиталась о значительной экономии, достигнутой благодаря Six Sigma. За два года экономия составила 330 млн. долл. Уэлч стал ярым приверженцем этой методологии.
Развертывание Six Sigma
Сила Six Sigma заключена в «эмпирическом», управляемом данными подходе и в использовании количественных показателей. Цель Six Sigma - сокращение отклонений в ходе производственного процесса и его совершенствование путем реализации так называемого «проекта совершенствования Six Sigma», который распадается на последовательность шагов DMAIC (define, measure, analyze, improve, control): определение, измерение, анализ, совершенствование и контроль.
На первом этапе, «определения» (define), ставятся цели и рамки проекта, выявляются проблемы, которые должны быть решены для достижения определенного уровня отклонений. Цели могут различаться на разных уровнях организации - так, например, на уровне высшего руководства это может быть большая отдача от инвестиций или завоевание большей доли рынка. На уровне операций целью может быть увеличение объемов выпуска какого-либо цеха. На проектном уровне - снижение количества брака или увеличение эффективности отдельного процесса. Для выявления потенциальных возможностей для улучшений используются методы добычи данных.
На втором этапе, «измерения» (measure), происходит сбор информации о текущем состоянии дел для получения данных, характеризующих базовый уровень показателей работы, и выявления участков, требующих наибольшего внимания. На этом этапе также определяются метрики, позволяющие оценить степень приближения к намеченным целям.
На третьем этапе, «анализа» (analyze), выявляются основные причины проблем в обеспечении качества, после чего правильность выбора этих причин проверяется при помощи специальных инструментов анализа данных.
На четвертом этапе, «совершенствования» (improve), внедряются решения, ориентированные на устранение проблем (основных причин), определенных на этапе анализа. В числе таких решений могут быть средства управления проектами и другие инструменты управления и планирования.
Цель пятого этапа, «контроля» (control), - оценка и мониторинг результатов предшествующих этапов. На этом этапе улучшения подкрепляются модификацией системы стимулов и поощрений, наборов правил, процедур, систем MRP, бюджетов, инструкций персоналу и других рычагов управления. Для гарантии корректности документации можно обеспечить, например, ее соответствие спецификации ISO 9000.
В инструментарий Six Sigma входит множество статистических методов. Один только их список выглядит весьма внушительно: мнение клиента, реализация функции качества, графики выполнения, диаграммы Парето, гистограммы, отображения процессов, определения процессов, частичные факториалы и др. Эти методы используются в реализации стратегии совершенствования процессов Шесть сигм.
Каждый из перечисленных выше этапов предполагает применение специальных аналитических численных методов из широкого набора методов, рекомендованных для Six Sigma. Выбор конкретных методов определяется природой процесса.
Еще одним важным моментом реализации проекта Six Sigma является распределение ролей среди специалистов. Должны быть назначены «исполнители» на следующие ключевые роли. «Лидер» (Champion) - член высшего руководства предприятия, который, собственно, и должен принять решение о запуске проекта Six Sigma и затем обеспечивать его реализацию, устраняя все возможные препятствия и предоставляя требуемые ресурсы. «Черный пояс» (Black Belt) - это, в соответствии со своим званием, высококлассный специалист, эксперт в области Six Sigma. Он инструктирует проектную группу, руководит и проводит обучение использованию методов и инструментария Six Sigma. Он отвечает за выполнение полной программы повышения квалификации. И наконец, конкретную работу по внедрению проводит проектная группа Шесть сигм. В нее входят специалисты в тех областях, которые затрагиваются в рамках проекта Six Sigma, прошедшие обучение основам методологии. Они предоставляют необходимую поддержку в ходе реализации проекта и делятся своими знаниями.
Будьте внимательны!
Six Sigma - это инициатива, ориентированная не на технологов, а на руководителей высшего звена, они несут ответственность за проект по ее реализации. Кроме того, внедрение Six Sigma предполагает целый ряд запретов на те уловки, а также вполне законные приемы, к которым наиболее часто прибегают руководители, когда речь идет об освоении новой технологии.
Нельзя игнорировать клиента, даже если трудно четко сформулировать его требования и перевести их в термины Six Sigma. Нельзя начинать внедрение Six Sigma с нижних или средних уровней организации. Six Sigma - это забота руководителей самого высокого уровня, как бы ни были они заняты, в противном случае не стоит надеяться на успех. Нельзя пытаться внедрить Six Sigma «по дешевке», какими бы бессмысленными на первый взгляд ни казались 160-240 часов обучения под руководством очень высоко оплачиваемого «черного пояса».
Нельзя «для еще более лучших результатов» объединять Шесть сигм с другими инициативами. Нельзя, да и бесполезно пытаться внедрить Шесть сигм начиная с небольшого пилотного проекта. Пилотный проект - это нечто слишком мелкое для внимания высшего руководства. Ради него не будут изменены основные производственные процессы, не будет сформирована инфраструктура поддержки - результатом станет разочарование в идее, и компания навсегда - или до смены руководства - лишится возможности повысить собственную эффективность.
Нельзя, наконец, реализовывать проекты Six Sigma для улучшения работы какого-либо одного подразделения, когда все остальная организация не готова к переменам. Система Six Sigma требует высокого качества руководства - тогда предприятие может рассчитывать на значительные преимущества.
Сильные стороны и ограничения Six Sigma
Первым и наиболее очевидным преимуществом методологии Six Sigma является повышение рентабельности за счет сокращения прямых затрат. Благодаря участию в проектах Six Sigma квалифицированных и хорошо обученных специалистов это сокращение может быть весьма значительным.
Впрочем, список достоинств этим не ограничивается. Вскоре после внедрения Шесть сигм многие организации добивались повышения прибыли и улучшения других финансовых показателей. Кроме того, поднимался уровень удовлетворенности клиентов. Снижалось число дефектов, сокращался производственный цикл, росла производительность труда и выход готовой продукции.
Но определение качества от противного, то есть как отсутствие некачественного, грешит ограниченностью. Исходной целью методологии Six Sigma было именно сокращение дефектных продуктов. Впрочем, методология развивается, и сейчас Six Sigma направлена на выявление и совершенствование так называемых «критических характеристик качества» (critical to quality, CTQ). Эти характеристики определяют все ожидания пользователя в отношении того или иного продукта или услуги. Правильное определение всех таких характеристик и их достижение с помощью Шесть сигм позволяет добиваться полной удовлетворенности клиентов. И все же этого недостаточно. Компании могут рассчитывать на успех в длительной перспективе, только если смогут удивлять своих клиентов новаторскими предложениями. Более того, компании должны непрерывно совершенствовать свою деятельность. Повышенное внимание, уделяемое в методологии Six Sigma жесткости процесса, его соответствию установленным нормам, противоречит новаторству, которое, по существу, является отклонением от нормы. Инновационный подход означает отклонения в производственном процессе, избыточность, необычные решения, недостаточную проработку - все то, с чем борется Six Sigma. Об этом придется помнить руководителям, решившим внедрить эту методологию.
Есть и еще одно, весьма существенное именно для руководителей обстоятельство, о котором необходимо помнить. Six Sigma - не просто модификация старых технологических методов обеспечения качества; это принципиально новый подход к руководству предприятием. Руководители Motorola расширили идею гарантии качества далеко за рамки собственно производства. Шесть сигм превратилась в способ организации труда на всем предприятии.
Взгляд из России
По собирательному мнению российских экспертов в области систем качества, Six Sigma - интересный, эффективный метод, но достаточно дорогой, как с точки зрения внедрения (его развертыванию нередко сопутствуют изменения организационной структуры предприятия, реструктуризация, перестройка технологических процессов и т. д.), так и обучения персонала. Наши собеседники в большинстве своем утверждали, что его использование целесообразно прежде всего на больших производственных предприятиях. Судя по всему, Шесть сигм если и применяется в России, то очень мало: эта жесткая методология не очень ложится на российский менталитет.
Эксперты, с которыми мы побеседовали, не склонны противопоставлять Шесть сигм и ISO 9001. Ряд специалистов рассматривает метод «Шести сигм» просто как один из статистических методов анализа и измерения качества, который можно использовать в качестве одного из возможных при внедрении ISO 9001. Этот стандарт качества предписывает обязательное применение статистических методов на производственных предприятиях, но жестких рекомендаций придерживаться какого-то конкретного метода не содержит, допуская использование любого необходимого и достаточного метода.
Методика Шесть сигм
Проблема, с которой столкнулась компания Motorola в середине 80х годов, заключалась в слишком высоком проценте бракованных транзисторов, получавшихся в результате производственного процесса. Чтобы исправить ситуацию компания разработала методику статистического анализа процесса, в которой учитывался процент бракованных изделий в динамике.
Постоянный сбор данных о статистике дефектов позволил установить среднестатистический процент брака, и определить количественные цели по повышению качества процесса. Иными словами, было проведено нормирование процесса по числу бракованных изделий и были поставлены задачи по снижению этой нормы.
Анализ динамики изменения числа дефектов позволил определить процессы с большим числом дефектов, и адресно направить усилия по исправлению именно этих процессов. Кроме того, удалось спрогнозировать и спланировать динамику улучшения качества производственного процесса и тем самым обеспечить снижение ее себестоимости.
Сегодня методика Шесть сигм успешно применяется по всему миру в самых разных областях: производственных, здравоохранении, разработке программного обеспечения и т.д. Разработан ряд программных продуктов, с помощью которых можно проводить статистический анализ процессов.
Даже самые эффективные и проверенные временем инструменты со временем должны меняться, становиться лучше, адаптируясь к реалиям рынка и компаний, представленных на нем.
Яркий пример тому — Lean Six Sigma. Это — в чем-то инновационное сочетание методов управления процессами, основанных на принципах Six Sigma, с упором на то, что могут быть с успехом использованы не только в производстве, но в любой сфере бизнеса.
Lean Six Sigma: что это?
Lean Six Sigma (LSS, Лин 6 сигм, Лин шесть сигм) — интегрированная методология, в основу которой легли американская и японская методологии:
(иными словами, Бережливое производство) — действия, направленные на сокращение потерь (отходов) производства и ускорение процессов выпуска готовой продукции; всячески приветствуются стандартизованные решения;
(Шесть сигм) — действия, назначение которых — повышение качества выпускаемой продукции и, как следствие, — повышение лояльности клиентов; основа решений, зачастую, совершенно нестандартных — анализ информации.
Немного истории: что такое «Lean manufacturing»?
Также эту философию называют методологией бережливого производства, lean-методологией, lean production. Основоположником данного метода работы стал Тайити Оно , идеолог производственной системы компании «Тойота» (хотя сам термин Оно не использовал, наименование lean production ввел американец Джон Крафчик (ныне — главный исполнительный директор Waymo, компании создающей самоуправляемые автомобили)).
Над алгоритмом lean production также работали Джеймс Вумек и Майкл Вейдер, Сигэо Синга, Джеффри Лайкер, Дэннис Хоббс , которые внесли многое в ту концепцию, которой сегодня пользуются ведущие мировые компании. При этом сама концепция трансформировалась и расширилась. Если изначально речь шла о бережливом производстве, то сегодня правильнее говорить о бережливом предприятии.
Одним из главных моментов, который часто забывается, является то, что идеально налаженный процесс производства — ничто, если в остальных аспектах деятельности компании царит хаос. Приоритетная задача руководителя — разобраться в происходящем и выявить скрытые потери.
Чтобы в дальнейшем свести их к минимуму, выстроив правильный климат в компании:
Как лидер в своей организации, будь она большая или небольшая, вы сможете сделать самый большой вклад в развитие компании, если обеспечите мотивацию и поддержку тем, кто возьмется за преобразования по системе Бережливого производства. Подобно дирижеру оркестра, у вас нет необходимости играть на всех инструментах, но вам нужно досконально знать ноты и руководить оркестром...Майкл Вейдер
Несмотря на то, что в Японии lean-методология используется более 60-лет, а в США эта философия была принята в 1990-е годы, ее ключевые принципы актуальны и сегодня:
- рабочие — не просто сменные винтики системы, они должны быть по-настоящему вовлечены во все производственные процессы, начиная от самых простых, заканчивая самыми сложными; такое возможно только при искреннем уважении руководства к сотрудникам и понимании необходимости постоянного профессионального роста каждого работника компании;
- системы менеджмента и управления должны, прежде всего, объединять: технологии, регламенты, человеческие ресурсы;
- ключевой фактор успеха — изменение корпоративной культуры.
Lean — это культура постоянного операционного совершенствования компании. Это непрерывная работа над устранением потерь и повышением эффективности. Это личное отношение каждого сотрудника к тому, насколько эффективно он выполняет свои функции и как процессы на его рабочем месте приносят дополнительную ценность клиентам. Для того чтобы достичь максимальной операционной эффективности, необходимо совершенствовать все процессы не только с точки зрения компании, но и с точки зрения клиента...Илья Польшаков, директор по трансформации компании "Киевстар«
В каких компаниях используют lean-методологию:
- General Motors
- VALEO
- Ford Motor Company
- New Balance
- Caltex
- Тиккурила
- «ЕВРАЗ УКРАИНА» и др.
Радует, что в Украине также активизировались процессы, направленные на широкое внедрение этой практики:
Сегодня lean — это одна из лучших мировых практик повышения эффективности любых организаций, независимо от их размера или сферы деятельности. Мы верим, что более глубокое понимание и применение культуры бережливого производства будет способствовать серьезной трансформации украинского бизнеса, усилению его конкурентоспособности на европейских и мировых рынках, и в результате станет весомым вкладом в социальное и экономическое развитие страны...Сергей Комберянов, президент Lean Institute Ukraine
Немного истории: что такое «Six Sigma» (Шесть сигм)?
Можно сказать, что история развития концепции началась с этой фразы, сказанной в 1979 году на заседании совета директоров компании «Моторола»:
Реальная проблема компании заключается в том, что качество нашей продукции отвратительное!Арт Сандри
Именно это высказывание заставило руководителей пересмотреть методы и принципы работы, ведь 5-20% доходов компании (до 900 миллионов долларов) уходило на ликвидацию брака в продукции.
Изменить ситуацию было сложно, ведь путь от производственных линий до конечного потребителя — долгий и извилистый. В результате была применена статистика, которая позволила добиться искомого результата.
Основа концепции Шести сигм:
- Сигма (греческая литера σ) — среднеквадратическое отклонение, демонстрирующее величину отклонений для определенной выборки (измерения результатов процесса при разных исходных данных).
- Чем больше возможностей для варьирования внутренних и внешних факторов производства, тем выше уровень отклонений качества.
- Чем меньше разброс значений по определенной характеристике, тем выше качество произведенной продукции.
Чем больше числа — тем очевиднее преимущество использования метода Шести сигм. Так, для компании «Моторола» правило 6 сигм стало способом сэкономить около 14 миллиардов долларов и увеличить продажи в 5 раз (за 10 лет с момента внедрения метода 6 сигм).
Если процесс функционирует на уровне одной сигмы, значит, он производит больше дефектной, чем годной, продукции, с точки зрения внешнего потребителя.Грегори Ватсон,
президент и управляющий партнер компании Business Systems Solutions, Inc
Чтобы стандартизировать работу с системой 6 сигм был разработан специальный пошаговый алгоритм, названный DMAIC:
- define (определение)
- measure (измерение)
- analyze (анализ)
- improve (совершенствование)
- control (контроль).
Визуально процесс работы с концепцией 6 сигм можно представить так:
Методология реально работает для разных сфер и стран, ведь:
- средняя зарплата для профессионалов с сертификатом Six Sigma Yellow Belt составляет 68 294 долларов США (по данным Burning Glass).
- те, кто овладел принципами Six Sigma, заработали больше, чем те, кто этого не сделал: + 12 475 долларов США в Канаде (по данным ASQ.org).
Кроме того, методику используют такие компании, как:
- General Electric
- Ford Motor Company
- FedEx
- Caterpillar Inc
- Honeywell.
Преимущества использования Lean Six Sigma (Лин 6 сигм)
Если говорить о глобальных выгодах использования симбиоза бережливого производства и Шести сигм, то их список будет выглядеть подобно пазлу, где недостатки, свойственные lean-методологии, с успехом восполняет методика 6 сигм (и наоборот):
- Основа бережливого производства — устранение такого вида потерь, как брак (дефектная продукция). При этом не идет речи о том, чтобы искать и просчитывать варианты того, откуда может взяться этот брак. И, конечно, не ведется работа над поиском способов уменьшения возможностей для варьирования внутренних и внешних факторов производства. А вот в концепции 6 сигм во главу угла ставится именно это.
- Исходя их того, что методика 6 сигм изначально разрабатывалась в направлении того, чтобы повысить уровень удовлетворенности клиентов, все ее ключевые моменты завязаны на отслеживании взаимосвязи «особенности процесса производства — уровень удовлетворенности конечного пользователя». В бережливом же производстве такая взаимосвязь метрик не отслеживается.
- Методика 6 сигм требует изначального построения формализованных процедур реализации концепции. Первым делом описываются обязанности руководства, особенности и время обучения, метрики, по которым отслеживается прогресс или регресс и пр.
- Бережливое производство борется с несколькими видами потерь, характерных для производства, а вот Six Sigma фокусируется на войне с дефектами.
- Время и «замороженные» активы — очень важные факторы, которые оптимизируются при бережливом производстве, а вот в методологии Шести сигм эти критерии не берутся во внимание.
Принципы, которые помогают добиться успеха проекту, основанному на Lean Six Sigma (LSS)
- Главный фокус — удовлетворение потребностей клиента. Изначально необходимо установить планку, ниже которой не позволяют опускаться требования клиента и рынка в целом. Также надо понять, что в вашем продукте ценно для клиента и развивать это. То, что ценности не представляет — отбросить.
- Залог успеха — сбор данных для выявления конкретной проблемы и борьбы с ней. Статистика — важна! Причины дефектов и неудовлетворенности клиентов часто не очевидны. Не стоит хвататься за все и сразу. Это породит только хаос.
- Налаживайте коммуникации. Все участники рабочего процесса должны знать принципы LSS, иначе быть беде, а не прогрессу. Обучение — наше все!
- Отслеживайте результаты и корректируйте их. Мотивируйте личностный и профессиональный рост сотрудников, не превращая их в бессловесных исполнителей инициативы свыше.
Уровни квалификации в Lean Six Sigma
- «Черный пояс»: человек, который станет стратегом компании и будет глобально руководить процессом внедрения LSS;
- «Зеленый пояс»: те, кто становятся главной движущей силой внедрения концепции 6 сигм, оптимально если перед началом обучения работник, претендующий на звание выбрал в компании мини-задачу, которая требует практической проработки в рамках тренинга;
- «Желтый пояс»: работают под началом «Зеленого пояса», выполняя узкие специфические задачи, в решении которых могут и должны быть настоящими экспертами;
- «Белый пояс»: признак того, что человек овладел базовым набором знаний и понимает, что такое методика 6 сигм.
Результат применения Lean Six Sigma выглядит впечатляюще:
Кому выгодно использование Lean Six Sigma?
По сути — всем. Хотя, конечно, часто можно услышать разговоры не о том, как поставить эту методику на службу своей компании, а как раз о том, почему не стоит даже пробовать.
Есть две основные причины по которым люди начинают внедрять 6 Sigma. Первая — компания в кризисе и нужно что-то делать чтобы вылезти из «дыры» или, когда конкуренты съедают вас живьем. Вторая — когда компания хочет улучшить качество своей продукции и быть всегда в ТОП...Рино Доменико, Президент и Исполнительный Директор Sterling Business School
Итак, кто может использовать данную методологию:
Какие компании уже используют методику:
- АО «Новый стиль»
- Wal-Mart
- Agrogeneration
- Starbucks
- ДТЕК Энерго
- Merck
- Киевстар
- ПАТ «Маріупольський металургійний комбінат імені Ілліча»
- Coca-Cola.
Инструменты, которые пригодятся для развития Lean Six Sigma на предприятии:
Методология Lean Six Sigma — решение для тех, кто привык использовать передовые наработки, получая результат уже тогда, когда остальные участники рынка еще раздумывают над целесообразностью внедрения той или иной методики.
Как показывает практика, данную концепцию берут на вооружение специалисты высокого уровня, достигающие впечатляющих показателей роста, независимо от исходных условий.
6 сигм — это сложная часть объединенной технологии Lean 6 Sigma (бережливого управления и 6 сигм) . Долгое время, объясняя ее на вводных тренингах по Lean Six Sigma , мы показывали кривую распределения данных и пытались пояснить используя математические и статистические материалы.
Наш коллега, Хавьер Гиен Мадрид (на фото), нашел способ объяснять 6 сигм просто, чем с вами сегодня и делимся!
Начнем с основ
Шесть сигм (англ. six sigma) - концепция управления производством, разработанная в корпорации Motorola в 1986 году и популяризированная в середине 1990-х после того, как Джек Уэлш применил её как ключевую стратегию в General Electric. Суть концепции сводится к необходимости улучшения качества выходов каждого из процессов, минимизации дефектов и статистических отклонений в операционной деятельности. Концепция использует методы управления качеством, в том числе, статистические методы, требует использования измеримых целей и результатов, а также предполагает создание специальных рабочих групп на предприятии, осуществляющих проекты по устранению проблем и совершенствованию процессов («чёрные пояса», «зелёные пояса»).
Почему, собственно «6 сигм», а не, скажем, 3 или 5?
Название происходит от статистического понятия среднеквадратичного отклонения, обозначаемого греческой буквой σ. Зрелость производственного процесса в этой концепции описывается как σ-рейтинг отклонений, или процентом бездефектной продукции на выходе, так, процесс управления качеством 6σ на выходе даёт 99,99966 % выходов без дефектов, или не более 3,4 дефектных выходов на 1 млн операций. Motorola установила в качестве цели достижение показателя качества 6σ для всех производственных процессов, и именно этот уровень и дал наименование концепции.
На этом можно было бы завершить нашу статью. Но нет, по-моему, по-прежнему мало что понятно, верно?
Давайте перейдем к примеру.
Все хотя бы раз в жизни играли в дартц? Если не играли поясню: цель игрока попасть в центр. Чем дальше от центра попадает игрок, тем ниже баллы он/она получает. На картинке ниже расположились результаты 4 различных игроков.
Какой игрок лучше?
Какой игрок лучше?
4-й, это очевидно. Он всегда попадает в цель и получает наивысший бал. Такой результат — всегда цель наших процессов.
А что мы можем сказать про 1 игрока? Он откровенно плох, правда ведь? Он никогда не попадает в цель, его результат разбросан. Ты не хотим для своих процессов таких результатов.
Отлично, с худшим лучшим результатом мы разобрались. А что скажете про 2-го и 3-го игрока? Кто из этих двоих предпочтителен для наших с вами процессов?
August 3rd, 2017Шесть Сигм позволяет перестроить и восстановить бизнес-процессы. Используя определенные инструменты и техники, Пояса Шести Сигм помогают избавиться от потерь и вариативности, отлаживая процессы до достижения лучшего результата. Шесть Сигм стоит за успехом многих крупнейших корпораций мира. Таких как Microsoft.
Но задавались ли вы когда-нибудь вопросом, как такие корпорации достигают такого успеха? В сегодняшней статье проанализируем путь корпорации Microsoft и посмотрим, каким образом там используются методы Шести Сигм. Хотите понять, каким образом им удается оставаться лучшими в своей отрасли? Как они стали одной из ведущих компаний в сфере цифровых технологий? В этой статье вы найдете ответы на эти вопросы.
История Шести Сигм в Microsoft
Ведущая корпорация в сфере цифровых технологий, Microsoft постоянно трудится для достижения все новых и новых вершин. Даже став именем нарицательным во всем мире, Microsoft никогда не останавливается на достигнутом. Они также работают над инновациями в сфере технологий для “умного дома” и облачных решений. Во всех направлениях они добиваются успеха в мировом масштабе.
Но знали ли вы, что Microsoft в своих операциях применяет инструменты Лин Шесть Сигм? Хотя их успех уже не на том уровне, как в середине 90-х, в связи с появлением таких конкурентов, как Apple, Microsoft внедрил очень значимые перемены, чтобы удержать свои позиции и оставаться на первом месте. В первую очередь, они сменили фокус на создание программных решений для веб-приложений для организаций. Мы также не можем не упомянуть о все большей роли Интернета в мире технологий, что заставило Microsoft реорганизовать свои операции с учетом появления новых продуктов и переналадки имеющихся процессов.
Такой инструмент Лин Шесть Сигм, как карта потока создвания ценности позволяет проанализировать потребительский спрос и выстроить свою работу так, чтобы соответствовать требованиям потребителей. Так Microsoft разработал свою платформу Windows CE OS. Это был один из самых успешных продуктов, совместимый с сетевыми устройствами для работы не только на компьютере, но и телевизорами и персональными цифровыми помощниками. Платформа CE OS также послужила первым шагом на пути к цепочке других успешных проектов. За большинством успешных проектов корпорации стоит успешное применение методов и техник Шести Сигм.
Microsoft / Шесть Сигм Сегодня
Уже ближе к настоящему моменту Microsoft использовал подход Шести Сигм для очередного гигантского скачка в операционной эффективности. На протяжении поздних 2010-х годов они начали реорганизацию структуры Лидерства. Это позволило им получить максимальные преимущества от постоянно возникающих возможностей в мире технологий. Также их целью было внедрить культуру непрерывного совершенствования во все свои организационные структуры.
Во главе с новым менеджментом (Шесть Сигм делает ставки на лучших из лучших), Microsoft трансформировал свою корпоративную культуру. Microsoft всегда был рефлексирующей и отзывчивой на любые изменения конъюнктуры компанией, приспосабливаясь к появляющимся тенденциям и новым возможностям рынка. Более того, реорганизация структуры лидерства не случайно совпала с увеличением продаж по портативным гаджетам, таким как смартфоны и планшеты. (Более того, это произошло также благодаря компания Amazon и Apple.) В результате реструктуризации Лидерства в корпорации появилось лучшее понимание рынка и его тенденций, что привело к увеличению прибыли и удовлетворенности клиентов.
Существует множество техник Шести Сигм. Применение методов Шести Сигм для устранения факторов неэффективности процессов вместе с реструктуризацией Лидерства и устранением ненужных слоев иерархии позволило Microsoft понять тенденции потребительского спроса и быстрее на них реагировать. Одним из основополагающих принципов Шести Сигм является соответствие требованиям потребительского спроса. И именно на этом Microsoft и сделал ставку для достижения результата, также как и на другие факторы достижения внутренней эффективности – устранение потерь, например. Microsoft это только одна из многих корпораций, которые на своем примере демонстрируют эффективность методов Шести Сигм.