Самодельный компрессор из холодильника для накачки колес. Как сделать компрессор из холодильника: пошаговое руководство
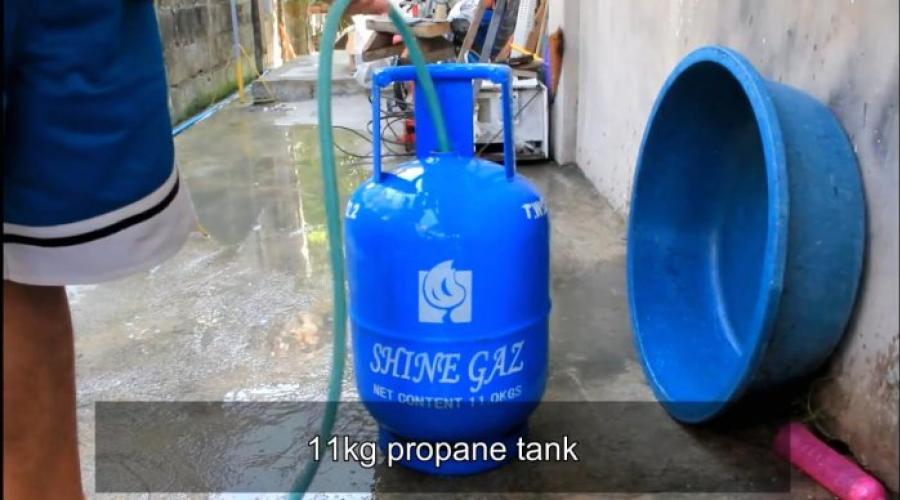
Читайте также
С недавних пор компрессоры снискали популярность среди любителей мастерить. Их делают на базе практически любых двигателей, рассчитывая мощность базового агрегата в зависимости от количества потребителей. Для домашних мастерских пользуются спросом самодельные компрессорные установки, сделанные своими руками.
Компрессоры от холодильников часто остаются работоспособными после поломки или устаревания самого холодильника. Они маломощны, но зато неприхотливы в работе. И многие мастера из них делают вполне достойные самодельные установки. Давайте и мы посмотрим, как это можно сделать своими руками.
Детали и материалы
Необходимые детали:- 11-килограммовый пропановый баллон;
- Муфта на 1/2 дюйма с внутренней резьбой и заглушкой;
- Металлические пластины, ширина – 3-4 см, толщина – 2-4 мм;
- Два колеса с монтажной платформой;
- Холодильный компрессор от холодильника;
- Переходник на 1/4 дюйма;
- Соединитель обратного клапана из латуни;
- Медная муфта-соединитель трубы на ¼ дюйма – 2 шт;
- Аппаратура для регулировки давления компрессора;
- Болты, винты, гайки, фумлента.
- Сварочный инвертор;
- Шуруповерт или дрель;
- Фрезы по металлу с титановым покрытием;
- Турбинка или бормашина с абразивными насадками;
- Щетка по металлу;
- Вальцеватель для медных трубок;
- Разводные ключи, плоскогубцы.
Собираем компрессор
Шаг первый – готовим ресивер
Пустой баллон от сжиженного пропана промываем хорошенько водой. Очень важно удалить таким образом все остатки взрывоопасной газовой смеси.
В торцевое отверстие баллона выставляем внахлест переходник на 1/4 дюйма. Обвариваем его со всех сторон сваркой, и заглушаем винтом.
Ресивер ставим на колеса и подпору. Для этого берем отрезки металлических пластин, сгибаем их под углом и навариваем на корпус со стороны днища. К уголкам привариваем колеса с монтажной платформой. В передней части ресивера монтируем скобу-подпору.Шаг второй – монтируем компрессор
Сверху ресивера выставляем крепежные рамки для компрессора из металлических пластин. Проверяем их положение пузырьковым уровнем, и обвариваем. Компрессор садим на прижимные болты через резиновые амортизирующие прокладки. У данного типа компрессора будет задействован всего один отвод, через который воздух нагнетается в ресивер. Остальные два, всасывающих воздух, останутся нетронутыми.Шаг третий – закрепляем обратный клапан и переходник на аппаратуру
Выбираем подходящую по диаметру фрезу по металлу, и проделываем шуруповертом или дрелью отверстие в корпусе под муфту. Если на корпусе муфты имеются выступающие формы, стачиваем их бормашиной (можно для этого применить обычный электронаждак или болгарку с шлифовальным диском).
Выставляем муфту в отверстие и обвариваем ее по окружности. Внутренняя резьба ее должна соответствовать по шагу и диаметру посадочной резьбе на обратном клапане.
Используем латунный обратный клапан для небольших компрессоров. Отвод для спуска давления заглушаем подходящим болтом, поскольку на регулировочной сборке уже предусмотрен спускной клапан.
Для установки реле давления или прессостата со всей регулирующей аппаратурой монтируем еще один переходник на 1/4 дюйма. Отверстие под него делаем по центру ресивера, недалеко от компрессора.
Закручиваем обратный клапан с переходником на 1/2 дюйма.
Соединяем медной трубкой отвод цилиндра компрессора и обратный клапан. Для этого специальным инструментом развальцовываем концы медных трубок, и соединяем их латунными резьбовыми переходниками. Подтягиваем соединение разводными ключами.Шаг четвертый – устанавливаем регулировочную аппаратуру
Сборка регулировочной аппаратуры состоит из реле давления (прессостат) с регулирующим датчиком, предохранительного клапана или клапана сброса давления, переходника-муфты с наружной резьбой и нескольких кранов и манометров.
Первым делом монтируем реле давления. Его необходимо слегка приподнять до уровня компрессора. Применяем удлинитель-муфту с наружной резьбой, и закручиваем реле через уплотнительную фумленту.
Через переходник устанавливаем датчик регулировки давления с манометрами. Завершаем сборку клапаном сброса давления и двумя кранами под выходы шлангов.Шаг пятый – подключаем электрику
Отверткой разбираем корпус реле давления, открывая доступ к контактам. Подводим 3-х жильный кабель к контактной группе, и распределяем каждый из проводов согласно схеме подключения (включая заземление).
Аналогичным образом делаем подводку питающего кабеля, оснащенного вилкой под силовую розетку. Закручиваем крышку реле обратно, на ее место.Шаг шестой – доработка и пробный запуск
Для переноски компрессорной установки прикрепляем к рамкам компрессора специальную рукоять. Делаем ее из обрезков профильной квадратной и круглой трубы. Крепим ее на прижимные болты и красим в цвет компрессора.
Подключаем установку к сети 220 В, и проверяем ее работоспособность. По заверениям автора, для получения давления в 90 psi или 6 Атм, этому компрессору необходимо 10 минут. С помощью регулировочного датчика, включение компрессора после падения давления также регулируется от определенного показателя, отображаемого на манометре. В своем случае, автор настроил установку так, чтобы компрессор снова включался от 60 psi или 4 Атм.
Осталась последняя операция – замена масла. Это немаловажная часть технического обслуживания таких установок, ведь ревизионного окошка в них не предусмотрено. А без масла такие машины могут проработать совсем недолго.
Откручиваем сливной болт в нижней части компрессора, и сливаем отработку в бутылку. Перевернув компрессор на бок, заливаем немного чистого масла, и закручиваем заглушку обратно. Теперь все в порядке, можно пользоваться нашим компрессорным агрегатом!
Не нужно лишний раз говорить о том, для чего нужен компрессор, ведь это и так ясно. Но из холодильника своими руками сделать не каждому под силу. Тем не менее, запасшись терпением, необходимым инструментом и теоретическими знаниями, с этим заданием можно справиться, и довольно быстро. Использовать такое оборудование можно вместе с аэрографом, пульверизатором и т.п. инструментом. Ключевые его особенности в том, что работа практически бесшумна, а габариты малы. Но вот давление такой компрессор создает очень даже неплохое.
Почему самодельный, а не профессиональный?
Вы наверняка уже знаете ответ на этот вопрос. Зачастую дело в цене. Профессиональные компрессоры имеют высокую цену. А если у вас есть старенький холодильник, который стоит без дела, то почему бы не занять себя на несколько часов и не сделать компрессор самому. Что касается конструкции, она отличается, но не очень. Покупные модели имеют электродвигатель, который передает работу через ременную передачу. В нашем случае электродвигатель и рабочая камера будут находиться в одном корпусе, но ременной передачи нет.
Меньше в самодельном изделии и автоматики. Хотя вот защиту от перегрева нужно установить. Такая релешка спасет ваш мотор от высоких температур и предотвратит поломку. Что касается смазки, то профессиональные компрессоры могут быть и сухими, то есть не иметь смазки. Такие модели работают за счет графитовых колец. В нашем же случае смазки будет много, что непосредственным образом влияет на долговечность оборудования.
Стоит заметить, что самодельный компрессор из холодильника своими руками сделать не так уж и сложно. Но необходимо понимать, что тут требуется внимание к деталям. В любом случае, если у вас все получится, то на выходе вы будете иметь функциональную станцию, которую можно отрегулировать как вам хочется и компоновать так, как вам удобно. Всего этого, к сожалению, нельзя сделать с покупным оборудованием.
Демонтажные работы
Прежде чем использовать компрессор, его необходимо снять с холодильника и соответствующим образом оборудовать. Но об этом несколько позже. Сейчас собственно о том, как выполнить демонтажные работы. Сложного тут ничего нет. Вам понадобится небольшой набор инструментов: плоскогубцы, две отвертки (плоская и крестовая), пара накидных ключей. Наверное, все знают, где располагается компрессор. Обычно это нижняя задняя часть холодильника.
Теперь можно приступать к снятию. Вы увидите медные трубки, которые ведут к системе охлаждения. С помощью плоскогубцев их необходимо откусить. Желательно с максимальным отпуском. В дальнейшем вы сможете их использовать в своих целях. Стоит обратить ваше внимание на то, что нужно откусывать трубки, а не пытаться пилить их с помощью напильника. "Почему?" - спросите вы. Все просто, при пилении обязательно образуется мелкая стружка, которая в том или ином размере попадает в компрессор, что может привести к ухудшению его технического состояния вплоть до поломки.
На этом работы не закончены, нам нужно снять не менее ответственный элемент - пусковое реле. Обычно это белый или черный небольшой коробок с входящими и выходящими из него проводками. Аккуратно необходимо открутить крепления и откусить провода, ведущие к вилке. Заранее пометьте, где у реле верх, а где низ. Это может быть указано на корпусе, проверьте. нужны для того, чтобы снять тушку компрессора. Вот мы и сняли компрессор из холодильника своими руками. Еще один момент, забирайте все крепежные элементы с собой, они вам пригодятся.
Проверяем работоспособность оборудования
Первым делом после снятия необходимо убедиться в том, что компрессор не «сдох» и его можно использовать в своих целях. Для этого необходимо расплющить медные трубки с помощью плоскогубец. Делается это для того, чтобы через них свободно выходил и заходил воздух. На следующем этапе нам нужно поставить пусковое реле в такое положение, в котором оно было еще до снятия. Это крайне важно. Дело в том, что реле работает по принципу нагрева пластин и земного притяжения. Неверная ориентация приведет к его поломке. Даже может сгореть обмотка компрессора, что не есть хорошо.
На реле имеются входящие провода. К ним нужно прикрутить провод с вилкой. Место соединения, во избежание поражения током, необходимо закрутить изолентой. После этого вы можете втыкать вилку в розетку. Если компрессор тихо себе тарахтит, а из трубки идет воздух, значит, вы все сделали правильно и оборудованием можно пользоваться. На этом этапе рекомендуется пометить трубки, чтобы знать, из какой выходит воздух, а в какую входит. Если же во время работы появились проблемы, скажем, компрессор не включается или выключается через некоторое время, то придется выполнять прозвонку реле и находить слабое звено. Данная процедура требует минимальных знаний электрических цепей и электротехники в целом.
Необходимые для работ материалы
Перед тем как сделать компрессор из холодильника, необходимо обзавестись всем нужным для работы. Во-первых, это компрессор. Мы уже разобрались, как снять двигатель (компрессор) с холодильника, поэтому он должен быть у вас под рукой. Кстати, на разных моделях холодильной техники установлены различные компрессоры. Обычно они представляют собой изделие цилиндрической формы или так называемый горшок.
Для того чтобы изготовить качественный компрессор, который выполнял бы свое назначение на все 100%, необходимо обзавестись ресивером. По сути, это емкость, в которую двигатель с холодильника будет накачивать воздух. В принципе, нет каких-то определенных требований, предъявляемых к ресиверу. Подойдет старый пустой огнетушитель, ресивер с грузового авто. Объем может быть разным - от 3 литров и больше. Также перед тем как сделать компрессор из холодильника, нужно найти подходящие шланги. Длина двух из них должна быть 10 см и более, последний должен быть не менее 50-60 см. Тут очень удобно брать автомобильные шланги. Дело в том, что они будут крепиться к фильтрам, а размер их отлично подходит для этих целей.
Что касается расходников, то это два фильтра - бензиновый и дизельный, хомуты, проволока, эпоксидная смола, манометр. Что касается инструмента, то это найдется у каждого хозяина в мастерской. Нужны дрель, нож, отвертка и плоскогубцы. После того как вы все это собрали в кучу, можно приступать к выполнению работ.
из холодильника: пошаговая инструкция
Большинство компрессоров на выходе имеют три медных трубки. Две из них открытые, те, которые вы откусывали плоскогубцами, и одна запаянная. Обычно она самая короткая. Соответственно, трубка, из которой дует воздух, - выходная, а та, которая всасывает - входная. Третьей пока не касаемся, но немного позже мы разберемся, для чего она и что с ней делать. Так вот, после проверки выхода и входа сделайте соответствующие отметки и отключите компрессор от сети. Дальше берем заранее подготовленную доску. Она будет нашей основой. С помощью саморезов крепим компрессор к доске. Трубки перед соединением необходимо дополнительно обработать. Желательно не использовать пилку по металлу, лучше возьмите плоскогубцы.
Один важный момент: компрессор необходимо крепить к основе ровно так же, как он был установлен на холодильнике. Монтаж боком или вверх ногами недопустим. Это связано с уже знакомым нам пусковым реле, которое работает за счет сил гравитации. Наш компрессор своими руками из холодильника еще не сделан. Теперь нам нужно изготовить ресивер. Подойдет пластиковая емкость. В её верхней части сверлим два отверстия под трубочки соответствующего диаметра. Затем вставляем их туда и заливаем все это эпоксидной смолой для герметизации. Одна из трубок (входная) должна не доставать до дна ресивера пару сантиметров. Короткая трубка (выходная) запускается примерно на 10 см. Такие манипуляции нужны для более удобного смешивания воздуха.
Железный ресивер
"Как сделать из холодильника?" - спросите вы. Да очень просто, для этого необходимо воспользоваться инструкцией, описанной выше. Но есть одно но, для таких целей лучше всего взять железный ресивер. Между пластмассой и металлом особой разницы нет, но только на железный ресивер мы можем установить манометр. Кроме того, шланги запаиваются или завариваются, а не заливаются смолой. Это обеспечивает лучшую герметичность емкости.
Чтобы установить манометр, необходимо просверлить отверстие соответствующего диаметра, установить прибор и запаять это место. Хотя более гуманно было бы пойти следующим путем. Просверливаем отверстие в подходящем месте и на это место завариваем гайку. Дальше остается только прикрутить манометр, и дело сделано. В принципе, особой разницы нет, только замена вышедшего из строя манометра производится значительно проще. После того как все сделано, можно крепить ресивер к основе. Для этого используйте стальную ленту или проволоку. По сути, компрессор из холодильника своими руками мы почти сделали. Осталось несколько небольших деталей.
Как сделать мини-компрессор: последняя часть монтажа
Большую часть пути мы уже прошли. Теперь осталось несколько штрихов. Для начала берем отрезок шланга (10 см) и надеваем на него бензиновый фильтр. Если вы используете автомобильный шланг, то проблем с надеванием возникнуть не должно. Если шланги тонкие и на штуцер не надеваются, то как вариант их можно подогреть. Свободный конец шланга нужно надеть на входное отверстие компрессора. Если соединения прочные, то хомуты можно не использовать, тем более что давления тут практически нет. Несложно догадаться, что фильтр необходим для того, чтобы исключить попадание пыли в компрессор. Второй отрезок шланга соединяется с выходным отверстием компрессора и входным ресивера. Тут уже будет большое давление, поэтому ставим хомуты. На третий шланг надеваем дизельный фильтр, а второй конец вставляем в выходное отверстие ресивера. Выходящий штуцер фильтра (дизельного) присоединяется к рабочему шлангу пульверизатора, аэрографа или другого оборудования. Вы наверняка и сами определитесь, как можно использовать компрессор от холодильника и в каких целях.
Технические характеристики и обслуживание оборудования
Что касается создаваемого компрессором давления, то тут сложно говорить о конкретных цифрах. Многое зависит от модели и возраста оборудования. Кстати, «древние» компрессоры более мощные. Они способны давать порядка 2-3 бар. Как импортные, так и советские модели работают практически бесшумно, правда, есть и исключения.
Что касается обслуживания, то это довольно важный момент, если вы не хотите, чтобы вскоре потребовался ремонт компрессора холодильника. Своими руками ухаживать за таким оборудованием не сложно. Главное правило заключается в том, что необходимо периодически менять бензиновый и дизельный фильтры. Помимо этого, желательно сливать накопившее в ресивере масло. Решающую роль же в долговечности оборудования играет высокая частота замены масла в компрессоре. Делать это нужно не сколько часто, сколько в назначенный срок. Чтобы слить отработку, необходимо отрезать кусок запаянной трубки. Помните, о ней мы упоминали еще в самом начале статьи. Через неё сливается старое масло и заливается новое.
Стоит ли ремонтировать компрессор?
Нередко двигатель холодильника выходит из строя. Как ни странно, но зачастую смысла в ремонте нет. Но когда дело в хладгене, то вопрос решается его заменой. Что же касается других случаев, например, попадание пыли вовнутрь или сгорание обмотки, это лучше оставить без внимания. Реально проще и дешевле купить новый двигатель. А вот своими руками имеет смысл. Сложного в этом ничего нет. Тем более, что о том, как снимать компрессор с холодильника, вы уже знаете. Устанавливается он в обратном порядке. Значение имеет то, чтобы монтаж был выполнен правильно. То есть места соединений трубок должны быть герметичными, а проводов - надежными, то есть изолированными. В целом же сам процесс замены занимает не более 20 минут. Если вы все же решили выполнить ремонт компрессора холодильника своими руками, то приготовьтесь к трудностям. Сначала прозвоните реле, возможно, дело именно в нем, и поэтому оборудование не запускается. Затем в компрессоре. Если это не помогло, то оборудование можно выбросить, особенного смысла с ним возиться нет.
Заключение
Вот мы и разобрались с тем, как изготовить компрессор от холодильника своими руками. Вообще, во время выполнения работ могут возникнуть самые различные трудности. Начиная с того, что на фильтр не налезают шланги, и заканчивая плохими соединениями или отсутствием реакции со стороны компрессора. Но большинство проблем можно устранить. В целом же такой компрессор - штука весьма полезная. С его помощью вы можете заниматься покраской и другими полезными делами. Большее значение имеет то, какой аэрограф или пульверизатор вы используете, нежели компрессор. Основное назначение такого оборудования - обеспечивать постоянное давление. Если появилась необходимость в большом давлении, скажем 3,5 бар и выше, то отыскать подходящий компрессор будет не сложно. Скорее всего, это советская модель. Обусловлено это тем, что современные двигатели холодильников, хоть и не являются мощными, весьма производительны. Вот и все по данной теме теперь вы можете приступать к делу.
Нередко у старого неиспользуемого холодильника остается вполне работоспособный компрессор. Его можно немного модернизировать, чтобы в результате получить полноценную установку, пригодную для использования в различных целях - чаще всего их используют для покраски, накачки автомобильных шин, выполнения аэрографии или питания пневматических приборов. Рассмотрим, как изготовить компрессор своими руками из старого холодильника.
Детали и инструменты, необходимые для изготовления компрессора
Чтобы сделать компрессор из холодильника своими руками, потребуются следующие инструменты:
- Сварочный аппарат (инвертор).
- Электродрель, шуруповерт.
- Бормашина, гравировальная мини-дрель с набором фрез.
- Щетка с металлическим ворсом для удаления ржавчины.
- Пассатижи, набор гаечных ключей, разводной ключ.
Из материалов надо приготовить:
- Пластины из стали толщиной 2–3 мм шириной 3–4 см.
- Две опоры на колесиках.
- Переходник на 1/4 дюйма.
- Глухую полудюймовую муфту с внутренней резьбой.
- Обратный клапан и соединитель под него.
- Две медных полудюймовых муфты-соединителя под медную трубку.
- Прижимные болты, гайки, другие крепежные элементы, фум-ленту.
В процессе работы может возникнуть необходимость в использовании других инструментов или материалов. Так, вместо пропанового баллона может быть использован корпус от огнетушителя или готовый автомобильный ресивер. Некоторые мастера предлагают устанавливать пластиковые емкости, от чего следует воздержаться, поскольку компрессора от холодильников могут создавать высокое давление, способное разорвать такой ресивер.
Процесс изготовления компрессора из холодильника
Технология изготовления самодельного компрессора из холодильника состоит из нескольких этапов.
Ресивер
Чтобы сделать компрессор из холодильника, необходим качественный ресивер. Для этого используется металлическая емкость с герметичным выходом - пустой газовый баллон на 11 литров. Прежде всего, надо избавиться от остатков газовой смеси в баллоне, для чего его изнутри хорошенько промывают водой. Затем к отверстию в торце прикладывается переходник на 1/4 дюйма и обваривается встык с максимальной герметичностью шва. Готовый переходник следует заглушить болтом.
В нижней части баллона сварным способом устанавливаются опоры с колесиками. Для устойчивости приваривается опора в верхней части, обеспечивающая горизонталь. В результате получается баллон, опирающийся на три точки (два колеса и опорная скоба), снабженный выходным штуцером.
Монтаж компрессора
Следующий шаг - установка компрессора на ресивер. Для этого понадобится приварить сверху горизонтально расположенного баллона две монтажных скобы. Расстояние между ними соответствует положению крепежных отверстий на компрессоре, который будут фиксировать на скобах прижимные болты. Для обеспечения бесшумной работы, которой отличаются самодельные компрессорные установки, сделанные из старых холодильников, между корпусом устройства и скобами следует установить резиновые прокладки.
Важно! Перед установкой компрессора надо заменить масло, находящееся внутри него, на другое, нейтральное к действию воздуха (подойдет лукойловское 10 W-40). Замену масла производят через запаянный отвод, который после этого следует вновь загерметизировать. Для исключения попадания масла в воздух необходимо на выходе из компрессора установить фильтр.
Обратный клапан и переходник на аппаратуру
Установка обратных клапанов - схема
Следующий этап изготовления самодельного компрессора - монтаж обратного клапана и переходника для присоединения регулировочной аппаратуры. Для этого понадобится просверлить в корпусе ресивера соответствующие отверстия - под обратный клапан удобнее расположить сбоку, а под аппаратуру - сверху, поблизости от компрессора.
В корпус ресивера вваривается муфта с внутренней резьбой, такой же, как у обратного клапана. На нем необходимо заглушить отверстие для сброса давления, поскольку подобное устройство имеется в блоке аппаратуры управления, взятого у старого холодильника.
Отверстие глушится винтом, под который предварительно нарезается резьба. Винт обматывается фум-лентой и плотно завинчивается в отверстие. Затем обратный клапан соединяется с отводом компрессора, для чего используется медная полудюймовая муфта-соединитель. Концы трубок с предварительно вставленными частями муфты развальцовывают, после чего муфта плотно соединяется.
Монтаж регулировочной аппаратуры
Лучше всего использовать регулировочную аппаратуру, которая была установлена на холодильнике в комплекте с компрессором. Они оптимальным образом подходят друг к другу. В состав регулировочной сборки обычно входит реле давления, клапаны сброса давления, манометры и нескольких регуляторов.
Сначала устанавливается реле давления. Это черная коробочка с манометром, ее присоединяют через удлинитель с наружной резьбой к выходу в верхней части баллона рядом с компрессором. Затем к реле присоединяются все остальные части сборки.
Регулировочная аппаратура на компрессоре
Подключение электрики
Провода питания компрессора от холодильника подключаются к соответствующим контактам реле давления. Для этого надо снять с реле крышку, после чего станут видны контакты. Трехжильный провод компрессора (с заземлением) подключается к соответствующим контактам (они отмечены специальной маркировкой), подобным образом подключается провод питания, оснащенный вилкой для силовой розетки. Проверяется прочность соединения контактов, крышка реле устанавливается на место.
Проверка работы самодельного компрессора
После соединения всех деталей и подключения проводов питания производится пробный запуск и настройка режима работы. Компрессор включается в сеть, с помощью регулировочной сборки настраивается режим включения/отключения устройства при наборе определенного давления.
Не рекомендуется сразу устанавливать высокие значения, поскольку может обнаружиться негерметичность сварного соединения на каком-нибудь из штуцеров. Найденные изъяны подлежат устранению, для чего устройство отключается от сети, давление, набранное во время пробного запуска, сбрасывается, обнаруженные недоработки устраняются. После этого устройство вновь подключается к сети и запускается в эксплуатацию.
статья о применение старого компрессора от холодильника, для использования в аэрографе.
Итак глава первая: добыча.
Обычно в наших широтах ареал обитания диких или одичавших компрессоров довольно невелик, хотя случаются исключения. Чаще всего их можно встретить возле мусорок во дворах домов либо в подвалах, где хранят всякий хлам. Обычно они крепко прикручены к большому белому ящику, который в простонародье именуют холодильник и хранят в нём пиво. Охотиться на дикого компрессора голыми руками не выйдет, он вам просто так не дастся. А пока вы будете бегать за вооружением, дикий компрессор вполне может стать домашним, но уже чужим.
При себе надо обязательно иметь специальный комплект оружия - плоскогубцы,отвёртки плоскую и крестик, 2 ключа на 12Х14. При обнаружении большого белого ящика необходимо внимательно осмотреть его, обычно компрессор прячется в его нижней части сзади. Если компрессор обнаружен и при вас есть необходимый комплект оружия можно приступать к добыче.
Добыча компрессора - процесс несложный, но надо к нему подойти внимательно и аккуратно, иначе в последствии могут быть проблемы. Первое что надо сделать - плоскогубцами или бокорезами откусить медные трубки, которые идут к решётке охлаждения, с припуском не меньше 10 см., а лучше – по максимуму, потом лишние трубки пригодятся (на некоторых типов компрессоров на трубках закреплена металлическая табличка с выбитыми цифрами - не выбрасывайте её, она тоже может пригодиться). Причём трубки надо именно откусить! Не в коем случае нельзя пилить, стружка обязательно попадёт внутрь, тогда ваш компрессор может сильно заболеть и умереть. При откусывании трубки заплющатся, можно этого не бояться, да и поможет не облиться маслом при транспортировке.
На этом этапе могу порекомендовать на кусочек чистой бумаги вылить каплю масла из компрессора и посмотреть его на наличие металлических частиц. Если в масле замечаются пылинки серебрянки - можно дальше не продолжать, и почтить минутой молчания светлую память погибшего агрегата.
Второе и самое главное - компрессор состоит не только из железяки, у него есть ещё один и очень важный орган - пусковое реле. Реле выглядит как маленькая чёрненькая (иногда беленькая) коробочка, отдельно прикрученная винтиками рядом с компрессором,в неё и из неё идут проводки. Нужно аккуратно отвинтить реле от холодильника, и точно так же аккуратно отсоединить разъём который идёт от реле к тушке компрессора (это относится к старым горшкам, у других типов компрессоров реле может быть несъёмным). Входящие 2 провода скорее всего придётся откусить, они всё равно не идут на прямую к вилке. Есть ещё один важный момент - надо запомнить или пометить в каком положении было прикручено реле, где верх и низ, оно бывает и подписано, но не всегда. Почему важно - об этом ниже.
Ну и наконец третье - с помощью 2 ключей на 12 откручиваем тушку компрессора от холодильника. Он обычно прикручен 4 болтами с гайками, через резиновые прокладочки. Желательно весь этот комплект крепежа и резинок забрать с собой, может пригодиться при последующей подготовке к работе.
Глава вторая: подготовка (одомашнивание).
Итак, вы только что добыли свой компрессор, перемазанные грязью и маслом, с исцарапанными и оттянутыми до колен руками, уставшие но довольные наконец дотянули до его дома. Теперь можно приступать к подготовке компрессора к работе. Первое что нужно сделать - контрольный пуск. Одеваем разъём реле на контакты в корпусе компрессора. Ориентируем и временно закрепляем реле на горизонтальной поверхности, можно даже скотчем приклеить. Главное - закрепить реле так,как оно стояло в холодильнике,оно работает на прицепе земного притяжения и нагрева пластин. Если неправильно сориентировать его, или просто бросить на весу - оно не сработает правильно, и это может кончиться фатально как для реле, так и для обмоток мотора компрессора.
Аккуратно и с помощью изоленты прикручиваем к входящим в реле проводам временный провод с вилкой. Настоятельно рекомендую замотать место скрутки изолентой, от этого зависит ваша безопасность и жизнь. Моделистов и так мало, давайте дорожить ими и собой. Заплющенные трубки нужно обжать плоскогубцами, они разойдутся в стороны и освободят проход воздуха.
Когда всё готово и закреплено - можно втыкать вилку в розетку. Обычно это сопровождается небольшим искрением и хлопком, нагрузка всё-таки немалая. Если всё в порядке - компрессор должен включиться и тихонько тарахтеть. Из трубки должен идти воздух, нужно пометить кто из них «вдох», а кто «выдох». Долго гонять не нужно, главное убедиться в работоспособности агрегата в сборе. Если не в порядке и компрессор не запускается, либо запускается и через некоторое время выключается - дело плоховато. Для небольшого обследования нужно дружить с электротехникой и тестером. Если вы с этими вещами не дружите - не рекомендую ковыряться дальше.
Ну а если дружите или имеете представление - продолжим. Надо снять разъём реле с компрессора и прозвонить обмотки мотора. Они должны звониться с небольшим сопротивлением между собой в любой комбинации. Если одна из обмоток не звониться - мы держим в руках тело погибшего агрегата. Если звониться, значит надо осмотреть и почистить реле. Аккуратно вскрыть коробочку, и мелкой наждачной бумагой подчистить контакты. Главное их не погнуть и не отломать, сильно тереть тоже не надо.
Затем собираем всё обратно, закрепляем как положено и пробуем включать вновь. Если снова не запускается или выключается – увы, не повезло… (Это при условии, что реле родное и шло в комплекте с этим компрессором. Аварийное отключение может происходить и из-за того, что мотор мощнее, чем тот, на который рассчитано реле, тогда придётся искать другое реле, а в этом поможет табличка на трубке.) Впрочем, не будем о грустном, надеемся, что всё заработало.
Теперь предстоит собрать ваш агрегат в более приспособленное и компактное устройство. Конечно, я не претендую на истину, у каждого свои возможности и средства для достижения этой цели, но изложу свой подход к сборке всего устройства. Для этого нужно посетить ближайший магазин автозапчастей, авторынок или ларёк с запчастями. Там нужно приобрести:
Литр моторного масла для замены,10w40 или другое минеральное или полусинтетическое. обычно литр минимальная тара, но если повезёт – бывает разливное, хватит и 500 грамм. На худой конец можно смазать все скрипучие петли в доме.
Резиновую армированную маслобензостойкую трубку, около метра длинной и 4мм внутреннего диаметра.Неплохо иметь с собой отрезок медной трубки от компрессора, к ней можно примерить нужную резиновую трубку.
Металлические стяжные хомуты, 6 штук. Их надо примерять к свежекупленной резиновой трубке. Они должны быть немного большего диаметра.
Хлорвиниловую трубку для омывателей стёкол. Они полупрозрачные, есть и армированные, но нам такие не нужны. Длину нужно выбирать в зависимости от места расположения компрессора и комфорта работы, но не менее 2 метров.
2 фильтра тонкой очистки – один для бензина, второй для дизельного топлива. Визуально отличаются – для бензина внутри стоит бумажная гармошка, для дизеля – внутри синтетическая сеточка.
Тюбик маслобензостойкого силиконового герметика, лучше густой консистенции и серого цвета, более жидкий и чёрный хуже.
После приобретения всего этого надо направить свои стопы в ближайший хозяйственный магазин. В нём вы должны приобрести:
Шнур с вилкой на конце, для запитывания компрессора в сеть. Длинной не менее 1,5 метров, желательно в двойной изоляции.
Одноклавишный выключатель света в корпусе закрытого типа, для внешнего монтажа.
Мебельные шурупы по дереву 3,5 х 16 или 3х16.
Теперь всю эту кучу надо объединить вместе, и мы получим вожделенный агрегат.
Первый и самый важный пункт подготовки, от которого зависит дальнейшая работа и долговечность компрессора - замена масла. Немало копий было сломано по этому поводу, надо менять, не надо, какое масло лить, а какое нет.
Мнений может быть много, но правильное - моё ! Дабы не возникало потом пустых вопросов типа "а у меня на подсолнечном работает и хорошо!", распишу свою точку зрения на этот момент.
Внутрь компрессора на заводе заливается чистое "веретённое” (фреонное, компрессорное - как его не называли) масло. На самом деле оно минеральное. Оно не содержит в себе никаких присадок, потому что компрессор в холодильнике работает в замкнутом и безвоздушном (безкислородном) пространстве, и не подвергается ни какому воздействию внешней среды. Когда мы начинаем его использовать в наших целях ситуация кардинально меняется. На масло начинает воздействовать кислород воздуха, микрочастицы пыли, влага и прочее. Минеральное масло довольно быстро засоряется и окисляется, теряет свои свойства. Это приводит к сильному нагреву компрессора при работе, шуму, износу поршневой системы и, в конце концов, к заклиниванию. И это притом, что масла было достаточно. Более того - в связи с небольшими связующими и смачивающими свойствами минерального масла оно будет интенсивно лететь на выход, засоряя парами воздух и уменьшая рабочий уровень в компрессоре.
Автомобильное (моторное) масло лишено большинства из этих проблем, в первую очередь за счёт содержания в нём пакета присадок компенсирующих или полностью устраняющих плохие факторы, влияющие на качество и долговечность масла. Тем более что оно рассчитано на гораздо более жёсткие условия эксплуатации, чем те, которые будут в вашем компрессоре. Я например использую моторную полусинтетику 10w40, потому что она остаётся после замены масла в моей машине. Можно использовать и минеральное, и полусинтетическое масло с другими индексами, но использовать синтетические масла не рекомендую. Во-первых дороже значительно, во-вторых они более жидкие и менее долговечные.
Надеюсь, что написал убедительно, хотя конечно найдутся неверующие, которые будут упорно заливать любое попавшееся под руки масло, ну да и флаг им.
Вернёмся к нашему железному другу. Тут возникает некоторый технический момент, а именно - какой тип компрессора попал в ваши руки. Визуально они разделяются на 2 основных типа - цилиндр и горшок (напоминает ночную вазу, прикрытую выпуклой крышкой). Первые - практически вымерший вид, применялся в очень старых типах холодильников, перестал производиться в конце 70х годов. Но если вам удалось добыть такой тип компрессора живьём - вам здорово повезло. Давление на выходе они могут дать гораздо больше остальных. Чаще всего в руки попадает именно второй тип компрессоров - горшки.
Главное для нас отличие на данном этапе - это куда менять масло. В цилиндрах чаще всего на боку корпуса вкручен огромный болт, он закрывает собой заливную горловину. Нужно открутить его с помощью гаечного ключа, слить из компрессора старое масло в какую-нибудь одноразовую посуду.Желательно замерить сколько этого масла было. В зависимости от типа цилиндра в них надо залить от 300 до 500 грамм масла. Затем аккуратно завернуть болт обратно, желательно намазав его маслобензостойким герметиком.
С горшком несколько сложнее. Из него обычно торчит 3 трубки – вдох, выдох и запаянная заливная трубочка. Масло менять желательно через неё. Для этого нам надо вскрыть эту трубочку, можно немного надрезать надфилем по кругу ниже заплющенного места, но не в коем случае не пилить насквозь. Потом по надрезу трубочку нужно надломить и полностью отломать, покачивая в стороны. Образовавшийся по краю заусенец надо слегка прибить молотком. Затем просто слить масло из горшка, наклонив его в сторону трубочек, в любую одноразовую тару. Запомните – после слива масла компрессор не в коем случае не включать!
Заправлять компрессор придётся шприцом, понемногу вливая масло в заливную трубочку, можно надеть резиновую трубку в виде импровизированной воронки. Масла в горшок требуется около 250-350 грамм. После заправки трубочку надо заглушить, иначе воздух будет уходить через неё (либо наоборот – входить мимо фильтра, зависит от типа компрессора). Можно конечно заплющить, но это не удобно, потом ведь масло придётся менять. Я рекомендую вкрутить небольшой саморезный винтик подходящего диаметра, под шляпкой которого будет резиновая шайбочка-прокладочка.
Как и в случае с маслом найдутся отчаянные или ленивые товарищи, которые будут пытаться кормить компрессор маслом на ходу, подливая его к засасывающей трубке - я крайне не рекомендую поступать так. Во-первых – масло желательно менять всё и сразу, а включать компрессор со слитым маслом – это значит убить его. Во-вторых - есть такое явление в поршневых устройствах - гидроудар. Это когда в пространство над поршнем попадает жидкость, в объёме большем, чем позволяет объём камеры сжатия. Жидкости, как мы знаем, почти не сжимаются, а мотор компрессора будет пытаться это сделать. В результате мы можем получить разрушение поршневой системы. Надеюсь, что и в этом я убедил.
И так продолжим. Теперь будем складывать всё в кучу, по приведённой схеме.
Эта схема предназначена для аэрографов одинарного действия, типа нашего любимого "Этон" – он же – белорус, либо переделанных на однократное действие аэрографов двойного действия.
Можно конечно соединить это всё и оставить на весу, но эта конструкция будет постоянно ломаться и разваливаться. Думаю, если немного потратить сил и объединить всё на какой либо платформе или в корпусе – это будет надёжнее и доставит большее удовольствие от работы. Не претендую на стандартизацию, но мой тип сборки абсолютно не требует применения станков, сварки или специального инструмента. Все материалы так же доступны, и стоимость их небольшая. Для самого простого и надёжного результата можно собрать конструкцию на листе фанеры или ДСП. Размеры этого листа в основном зависят от типа выбранного или добытого ресивера. Ресивер нужен для минимум двух функций – он сглаживает пульсации давления воздуха, неизбежные при работе компрессора, служит уловителем паров и капелек масла. Для недорогих аэрографов одинарного действия, к которым относится широко распространённый "Этон" – он же – белорус, ресивер большой ёмкости совершенно не нужен, достаточно объёма около 1-2 литров.
Как показывает практика, в качестве ресивера используют практически любые герметично закрывающиеся ёмкости – от пластиковых бутылок для напитков и пива до промышленных ресиверов от грузовиков и оборудования. На мой взгляд, использовать пластиковые бутылки и уж тем более стеклянные несколько небезопасно, эти материалы не обладают хорошей механической прочностью, и даже небольшое давление в ресивере может разорвать его при повреждении и нанести травмы. Можно конечно использовать и такие вещи как баллон от огнетушителя, но это несколько укрупняет и утяжеляет всю конструкцию.
Наиболее оптимальными ёмкостями под ресивер являются небольшие пищевые канистры для воды из полупрозрачного белого полиэтилена, либо как в моём примере – расширительный бачок от жигулей. Полиэтилен, из которого сделаны эти ёмкости, довольно толстый и вязкий, не боится механических повреждений от упавших мелких предметов и довольно долго сохраняет свои свойства. Даже если и произойдёт разрыв - он не даёт осколков или обрывков материала. Тем, кто не хочет применять такие материалы под давлением, могу посоветовать присмотреться к небольшим сварным металлическим канистрам для топлива, объёмом 5 литров.
Приспособить канистру или бачок для ресивера довольно просто – надо взять 2 трубочки, например медные, отрезанные от компрессора, длинной около 15 см каждая. Не забудьте, на компрессоре должны остаться трубки не менее 10 см длинной. В крышке канистры сверлятся 2 отверстия, в которые должны плотно входить эти трубочки. Затем с внутренней стороны крышки место вхождения трубок заливается эпоксидной смолой, полностью заливать не надо, надо оставить ещё место для вкручивания горлышка. Когда всё высыхает – нужно смазать горлышко и пробку герметиком и плотно закрутить. В этом моменте важно правильно разместить трубки – их кончики не должны быть рядом, и выходящая трубка должна быть выше входящей (как на схеме).
Теперь, когда всё подготовлено, можно прикинуть, каких размеров нужен лист фанеры. Сильно в обтяжку собирать не стоит, так будет сложнее обслуживать, да и компрессор должен иметь некоторое пространство вокруг для обдува воздухом и охлаждения. В моём случае хватило куска 30х40 см. Фанеру нужно брать толщиной не менее 9 мм, лист ДВП – 15 мм. Обрезка уголков и обработка грубой шкуркой – это уже на вкус. Но занозы в пальцах удовольствие не доставят.
По углам листа на его будущей нижней части необходимо шурупами закрепить ножки, резиновые или, например, пробки от пластиковых бутылок (хороший повод взять 4 «полторашки» пива). Главное шурупами не прикрутить насквозь к полу или столу. Ножки необходимы для снижения шума при работе компрессора, предотвращают его «уползание» с места, да и поцарапать пол тоже неприятно.
Далее сверлятся 4 отверстия под крепления компрессора, болты, надеюсь, не забыли взять с собой? Возможно, при использовании толстого листа фанеры или ДСП может не хватить длины штатных болтов, тогда придётся купить более длинные в комплекте с гайками, в хозяйственном или авто магазине.
Самое сложное – закрепить ресивер. Устанавливать его надо первым, что бы потом не мешали остальные детали агрегата. Протыкать ресивер насквозь крепежом не стоит, здесь нужен творческий подход – например, использовать резиновую трубку или полоску, прочную ткань или кожу, перфорированную ленту для упаковки тяжёлых грузов и т.д. Один край крепящей ленты прикручивается шурупом к фанере, перекидывается через ресивер и с натягом прикручивается с другой стороны.
Компрессор закрепляется болтами, желательно трубками к краю листа фанеры, так в дальнейшем будет проще менять масло. Резьбу болтов при привинчивании желательно смазать герметиком, так они в последствии не будут откручиваться из-за вибраций. Рядом с ним шурупами привинчиваем пусковое реле, правильно его сориентировав. Дальше – выключатель света, на его контакты присоединяем реле и шнур питания. Сам шнур желательно закрепить хомутиком или петелькой к листу фанеры, так он не вырвется из выключателя.
Когда с электрической частью закончено – приступаем к монтажу остальной пневматической системы. На входе компрессора с помощью отрезка резиновой трубки и 2 хомутов закрепляем фильтр тонкой очистки для бензина. Возможно, кому-то покажется лишней эта деталь, но это ведь не дорого, и всяческая пыль не будет попадать внутрь компрессора, тогда оттуда её уже не извлечь. Главное при всех последующих операциях не залить этот фильтр маслом, он потеряет от этого свои свойства. Далее отрезком резиновой трубки и 2 хомутами соединяем выход компрессора со входом ресивера. Действовать надо аккуратно, дабы не выломать трубки из крышки. На выход ресивера так же натягиваем резиновую трубку с 2 хомутами, закрепляем фильтр для дизельного топлива. Этот фильтр можно заполнить силикагелем, тогда он будет выполнять 2 функции – уловитель влаги и переходник для закрепления резиновой и хлорвиниловой трубок. Можно конечно обойтись и без него, хлорвиниловую трубку натянуть прямо на выход ресивера, но такое соединение не будет полностью герметично и прочно, с гладкой медной трубки шланг будет срываться.
Хлорвиниловая трубка обычно меньше диаметром, чем штуцер фильтра и аэрографа, растягивается не очень хорошо, и насадить её довольно сложно. Для этого есть маленькая хитрость – кончик трубки погружается в растворитель 647 на несколько минут. Неглубоко, больше 5 мм не стоит, иначе она будет слишком гибкая, и не будет упора для её насаживания на штуцер. Желательно закрепить фильтр и хлорвиниловую трубку на листе фанеры, так она не будет болтаться и расшатывать трубки ресивера.
Ну вот практически и всё. Можно включать, послушать, как шипит воздух. Только кидаться сразу в работу не стоит, если применялся силиконовый герметик – ему надо просохнуть пару дней.
Глава третья: эксплуатация.
Здесь ничего сложного нет. Главное при эксплуатации компрессора – не допускать его перегрева. Обычно компрессор нагревается до температуры 40-45С за 25-30 минут непрерывной работы. Дольше работать не стоит, это уже может плохо отразиться на его ресурсе и качестве работы.
При дальнейшей эксплуатации, возможно, придётся регулировать давление воздуха. Например, некоторые типы компрессоров могут выдать гораздо большее количество воздуха, чем это нужно для аэрографа, либо это связано с покрасочными моментами. В этом случае компрессор будет создавать излишне большое давление в трубках, фильтрах и ресивере, да и сам он будет работать с перегрузкой и быстро нагреваться. В этом случае нам потребуется редуктор. Самое важное – редуктор в этой системе нужно устанавливать на ВХОДЕ компрессора, если он будет устанавливаться на выходе – это также будет вызывать перегрузку компрессора и его быстрый нагрев.
Устанавливая редуктор на входе, мы ограничиваем количество воздуха, проходящее через компрессор, тем самым регулируется и давление. Самым простым и доступным редуктором являются калиброванные трубочки, которые можно закрепить на входе фильтра через резиновую трубку, например от стержней авторучек, или толстые иглы от шприцов. Можно и самому насверлить разными свёрлами. Либо можно посетить ближайший зоомагазин, в товарах для аквариума можно найти очень даже подходящие маленькие краники и редукторы. И по посадочным диаметрам они как раз, и стоят копейки. В отличие от калиброванных трубочек они позволят регулировать давление в некоторых пределах по ходу работы.
Глава четвёртая: обслуживание.
Обслуживание компрессора дело не сложное, хотя для этого придётся частично снимать некоторые детали. Можно конечно и вовсе не обслуживать агрегат, но поверьте – он ответит тем же.
В обслуживание входят:
Замена масла.
Замена фильтров.
Слив накопившегося масла из ресивера.
Масло, какое бы оно не было хорошее, всё равно со временем теряет свои свойства и загрязняется. В компрессоре вне зависимости от режима и количества времени его работы масло желательно менять не реже раза в год.
Для этого необходимо снять с него все трубки, вывинтить из заправочной трубочки заглушку – винтик, и наклонив компрессор вылить из него всё масло. Запомните – после этого включать его нельзя не в коем случае! Далее, как и при первой замене масла, шприцом заливаем необходимое количество масла внутрь. Пока сняты трубки – можно заодно снять старые фильтры, вылить накопившееся масло из ресивера. Вливать это масло обратно в компрессор не стоит.
Потом установить все новые фильтры на место, трубки вернуть обратно на компрессор. В этом хорошо помогают металлические хомуты, они позволяют неоднократно проводить подобные операции.
Ну вот вроде и всё, удачной работы. Думаю возникшие дополнительные вопросы можно будет разрешить на форуме.
Компрессорная техника становится все более популярной и востребованной, ведь ее делают самых различных модификаций и размеров. Силу сжатого воздуха широко используют в мастерских, на производствах и заводах. Домашние мастера также не обходят эту тему стороной.
Самодельные компрессорные установки на базе штатного компрессора от холодильника явление далеко не новое. Чтобы получить из них оборудование близкое к профессиональному, их модернизируют, дополняя различными вспомогательными элементами – датчиками, реле, манометрами, ресиверами и т.д. Однако чаще всего останавливаются на бюджетных вариантах, один которых мы хотим сегодня предложить вашему вниманию.
Принцип работы устройства компрессора от холодильника
Штатный компрессор от холодильника представляет собой компрессорную установку без накопительной емкости, которая заключена в металлический корпус. От него отходят две медные трубки, через которые воздух всасывается вовнутрь и выходит наружу под давлением. Электрическая схема подключения практически не меняется, поскольку является готовой. На входящий, и выходящий патрубки монтируются воздушные фильтры, а следом и кислородный шланг с переходником для потребителя.Ресурсы для сборки компрессора
Материалы:- Компрессор от холодильника;
- Кабель подключения с вилкой;
- Воздушный фильтр автомобильный – 2 шт;
- Кислородный шланг для патрубков;
- Спиральный кислородный шланг с быстросъемными переходниками;
- Воздушный пистолет для подкачки колес;
- Хомуты, провода.
Собираем компрессорную установку
Компрессор от холодильника снабжен пусковым реле, к которому изначально подведен термостат. В данной сборке он не участвует, поэтому его необходимо отключить, предварительно отметив контакты на пусковом реле, и замкнуть их отрезком изолированного провода.Подбираем кислородный шланг по диаметру патрубка, и монтируем воздушный фильтр на вход компрессора. Один его пластиковых патрубков для отбора воздуха можно обрезать, оставив свободным отверстие. В соединении можно обойтись без хомутов, поскольку этот элемент нашей установки не находится под давлением.
Патрубок для него не стоит делать длинным. Отрезаем его ножом, и насаживаем фильтр от руки. Чтобы медные трубки компрессора не находились на одной линии, и не мешали друг другу, их можно отогнуть в разные стороны.
Следом крепим второй воздушный фильтр на выход. При необходимости медный патрубок под него можно укоротить кусачками.
Как показала практика самого автора, даже при сравнительно небольшом давлении такая сборка не может обойтись без прижимных хомутов. Насаживаем их на патрубки, и поджимаем соединение. Второй выходящий из компрессора медный патрубок автор заглушил саморезом и изолентой.
Прикрепляем к воздушному фильтру небольшой отрезок кислородного шланга, и подключаем спиральный шланг для компрессорных работ. Это можно сделать и через быстросъемный переходник.
Теперь можно подключить к спиральному шлангу воздушный пистолет для подкачки колес, и проверить работоспособность нашей установки. Чтобы избежать избыточного давления в шлангах и фильтре, можно обжать курок воздушного пистолета нейлоновой стяжкой.